3D Printed Strut Mounts
Índice
Introduction – The Evolution of Automotive Suspension: Embracing 3D Printed Strut Mounts
The automotive industry is in constant pursuit of innovation, striving for enhanced performance, improved safety, and more efficient manufacturing processes. At the heart of a vehicle’s ride quality and handling lies its suspension system, and a seemingly small yet critical component within this system is the strut mount. Traditionally manufactured through conventional methods like casting and machining, strut mounts are now undergoing a revolution, spearheaded by the transformative capabilities of metal Impresión 3D. This advanced manufacturing technique offers unprecedented design freedom, material optimization, and the potential for significant performance enhancements. At Metal3DP, we understand the intricate demands of the automotive sector and are at the forefront of providing cutting-edge additive manufacturing solutions. Our expertise in high-performance metal powders and advanced 3D printing technologies enables the production of strut mounts that meet and exceed the stringent requirements of modern vehicles. This blog post will explore the myriad benefits of utilizing 3D printed strut mounts, the ideal materials for their production, and how this technology is reshaping the future of automotive manufacturing. To learn more about our comprehensive metal 3D printing services, visit our Impresión 3D en metal página.
What are 3D Printed Strut Mounts Used For? – Critical Components for Vehicle Dynamics and Comfort
Strut mounts are integral components in a vehicle’s suspension system, serving several crucial functions that directly impact ride comfort, handling precision, and overall vehicle safety. Primarily, they act as the interface between the vehicle’s chassis and the suspension struts. Their key roles include:
- Dampening Vibrations and Noise: Strut mounts incorporate elastomeric or rubber elements that absorb road vibrations and noise generated by the suspension system, preventing them from being transmitted directly into the vehicle’s cabin. This contributes significantly to a smoother and quieter ride for passengers.
- Supporting the Strut Assembly: They provide a secure mounting point for the entire strut assembly, which typically includes the shock absorber and coil spring. This ensures the structural integrity and proper functioning of the suspension system.
- Allowing for Steering Pivot: In the front suspension, strut mounts often incorporate a bearing that allows the strut to pivot as the steering wheel is turned. This ensures smooth and responsive steering.
- Isolating Suspension Movement: They help isolate the movements of the suspension from the vehicle’s body, preventing excessive stress and wear on both the suspension components and the chassis.
The applications of strut mounts are vast, spanning across various vehicle types, including:
- Passenger Cars: Ensuring a comfortable and controlled driving experience.
- Light Trucks and SUVs: Providing robust support for heavier loads and varied terrains.
- High-Performance Vehicles: Contributing to precise handling and responsiveness.
- Vehículos eléctricos (VE): Aiding in noise reduction and optimizing for weight efficiency.
By leveraging metal 3D printing, manufacturers can tailor the design and material properties of strut mounts to meet the specific demands of each application. This level of customization is often challenging to achieve with traditional manufacturing methods. For insights into the diverse applications of metal 3D printing, explore our Producto showcase.
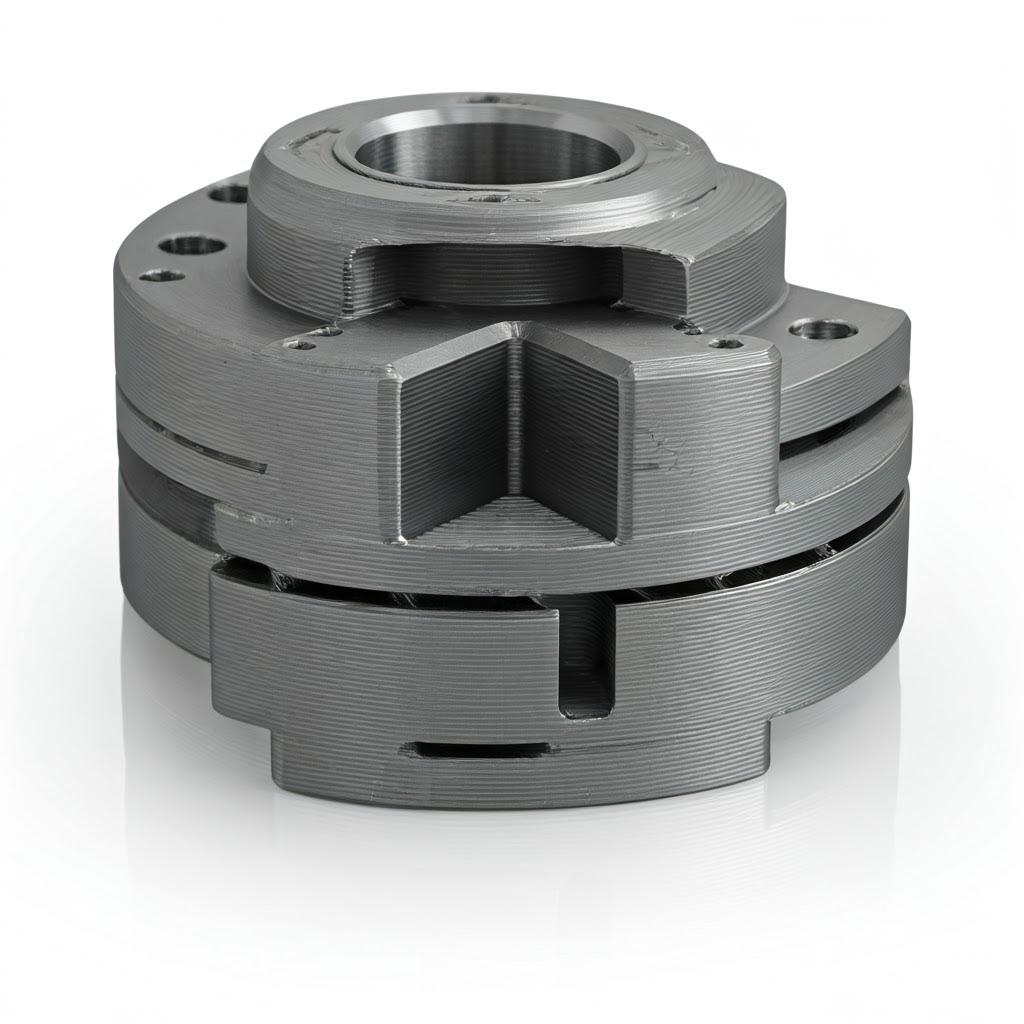
Why Use Metal 3D Printing for Strut Mounts? – Unlocking Innovation in Automotive Manufacturing
Adopting metal 3D printing for the production of automotive strut mounts offers a multitude of compelling advantages over conventional manufacturing techniques. These benefits are particularly attractive to engineers and procurement managers seeking enhanced performance, efficiency, and innovation:
- Design Flexibility and Optimization: Metal 3D printing allows for the creation of complex geometries and intricate internal structures that are simply not feasible with traditional methods like casting or machining. This design freedom enables engineers to optimize the strut mount for weight reduction (lightweighting), improved stiffness, and enhanced vibration damping through techniques like topology optimization and lattice structures.
- Eficiencia de materiales y reducción de residuos: Additive manufacturing processes build parts layer by layer, using only the material needed for the component. This significantly reduces material waste compared to subtractive methods where material is removed from a larger block. For industries focused on sustainability and cost-effectiveness, this is a crucial advantage.
- Creación rápida de prototipos e iteración: Metal 3D printing drastically accelerates the prototyping process. Engineers can quickly iterate on designs, produce functional prototypes, and test them in real-world conditions, leading to faster development cycles and reduced time-to-market.
- On-Demand Manufacturing and Customization: 3D printing enables the production of strut mounts on demand, eliminating the need for large production runs and warehousing. This is particularly beneficial for low-volume production, specialized vehicles, or aftermarket parts. Furthermore, it allows for customization of strut mounts to specific vehicle models or performance requirements.
- Integración de características: Additive manufacturing can facilitate the integration of multiple components into a single 3D printed part, reducing the number of assembly steps and potential failure points. For example, damping features or sensor integration could be incorporated directly into the strut mount design.
- Rendimiento y durabilidad mejorados: By selecting advanced metal powders and optimizing the design for additive manufacturing, it is possible to produce strut mounts with superior mechanical properties, such as higher strength-to-weight ratios and improved fatigue resistance, leading to enhanced vehicle performance and component durability.
En Metal3DP, our state-of-the-art Selective Electron Beam Melting (SEBM) printers are ideally suited for producing complex and high-performance automotive components like strut mounts. Discover more about our advanced printing methods on our Métodos de impresión página.
Recommended Materials and Why They Matter – A7075 and AlSi10Mg: High-Performance Alloys for Strut Mounts
The choice of material is paramount in determining the performance and longevity of automotive strut mounts. For metal 3D printing applications, specific metal powders offer a unique combination of properties that make them ideal for this critical component. Metal3DP recommends A7075 and AlSi10Mg aluminum alloys for 3D printed strut mounts due to their exceptional characteristics:
A7075 Aluminum Alloy:
- Alta relación resistencia-peso: A7075 is renowned for its exceptionally high strength, often comparable to some steels, while being significantly lighter. This is crucial for automotive applications where weight reduction directly translates to improved fuel efficiency and handling.
- Excelente resistencia a la fatiga: Strut mounts are subjected to cyclic loading and vibrations. A7075 exhibits excellent fatigue resistance, ensuring the longevity and reliability of the component under demanding conditions.
- Buena maquinabilidad: While 3D printing offers near-net-shape manufacturing, some post-processing might be required. A7075 has good machinability, facilitating any necessary finishing operations.
- Resistencia a la corrosión: While generally good, A7075 may require surface treatments like anodizing to enhance corrosion resistance in certain environments.
AlSi10Mg Aluminum Alloy:
- Buena resistencia y ductilidad: AlSi10Mg offers a good balance of strength and ductility, making it a versatile material for structural automotive components.
- Excelente imprimibilidad: This alloy is well-suited for powder bed fusion 3D printing processes like Selective Laser Melting (SLM) and Direct Metal Laser Sintering (DMLS), exhibiting good flowability and consistent melting behavior.
- Buena conductividad térmica: AlSi10Mg possesses good thermal conductivity, which can be beneficial in dissipating heat generated within the suspension system.
- Buena resistencia a la corrosión: AlSi10Mg offers good resistance to corrosion, making it suitable for the often harsh operating conditions of automotive components.
The selection of either A7075 or AlSi10Mg will depend on the specific performance requirements of the strut mount and the overall vehicle design. Metal3DP offers a comprehensive range of high-quality metal powders, including these advanced aluminum alloys, specifically optimized for additive manufacturing. Our advanced powder making system ensures high sphericity and flowability, critical for producing dense, high-quality 3D printed parts. Learn more about our commitment to quality on our Quiénes somos página.
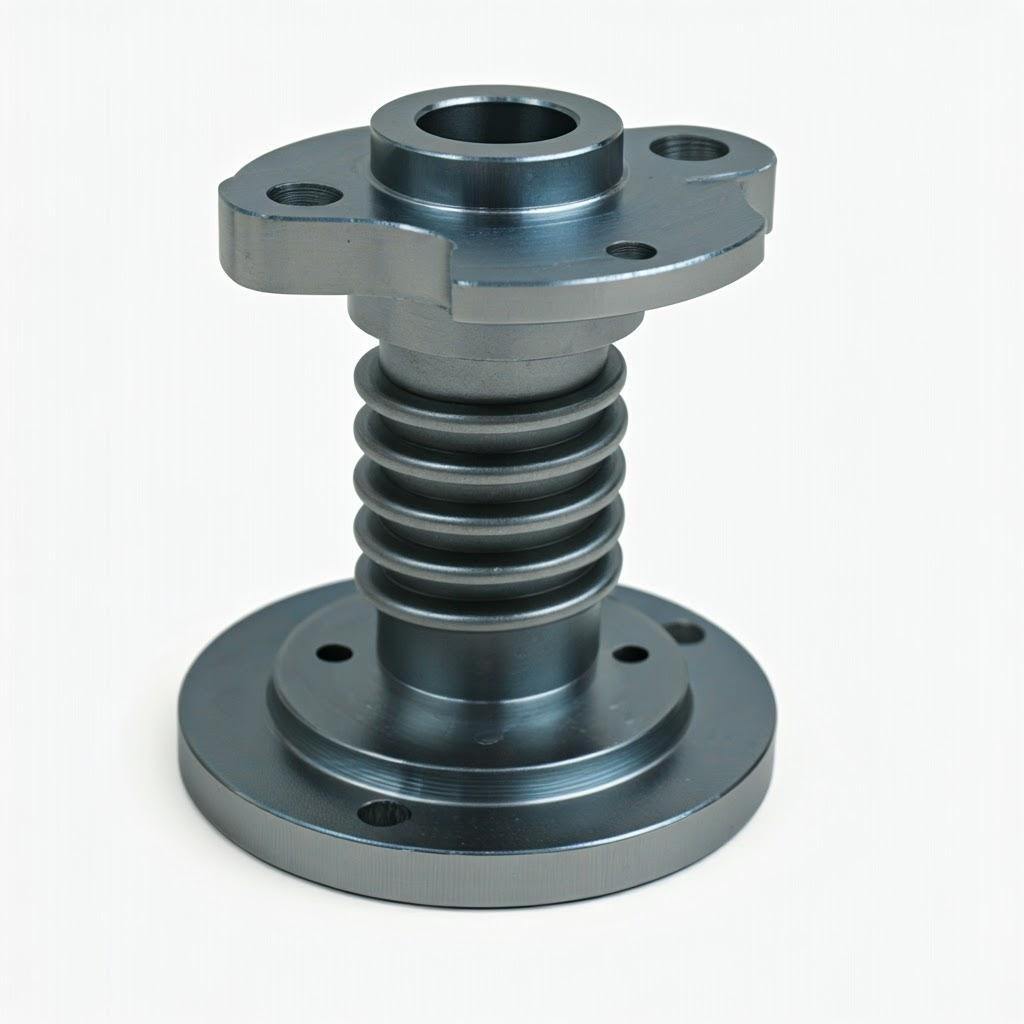
Design Considerations for Additive Manufacturing – Optimizing Strut Mounts for 3D Printing
Designing for additive manufacturing (DfAM) is crucial to fully leverage the capabilities of metal 3D printing and produce high-performance, cost-effective strut mounts. Unlike traditional manufacturing methods with their inherent limitations, 3D printing offers design freedom that can be exploited to enhance functionality and reduce material usage. Here are key design considerations for 3D printed strut mounts:
- Optimización de la topología: This computational method can be employed to identify and remove material from low-stress areas of the strut mount while maintaining its structural integrity. This results in lightweight yet strong components, crucial for improving vehicle efficiency and handling.
- Estructuras reticulares: Incorporating lattice or cellular structures within the non-critical volumes of the strut mount can significantly reduce weight without compromising stiffness. These intricate internal geometries are only achievable through additive manufacturing.
- Consolidación de piezas: Where traditional designs might require multiple assembled components, 3D printing allows for the consolidation of these parts into a single, integrated design. This reduces assembly time, potential failure points, and overall part count.
- Orientation and Support Structures: The orientation of the part during the printing process can significantly impact surface finish, support material requirements, and overall build time. Careful consideration of the optimal orientation is essential. Support structures are often necessary to support overhanging features and prevent collapse during printing. Designing with self-supporting angles and minimizing overhangs can reduce the need for extensive support structures, simplifying post-processing.
- Wall Thickness and Ribbing: Optimizing wall thickness and incorporating strategically placed ribs can enhance the stiffness and strength of the strut mount without adding excessive weight. These features can be tailored precisely to the load-bearing requirements of the component.
- Internal Channels and Features: Additive manufacturing allows for the creation of internal channels or features that can be used for cooling, wiring, or even integrated sensors within the strut mount. This level of functional integration is a significant advantage of 3D printing.
- Textura de la superficie: The surface texture of a 3D printed part can be controlled to some extent during the printing process. Designing for specific surface finishes can impact the need for post-processing and the component’s interaction with other parts.
By embracing these DfAM principles, engineers can design strut mounts that are not only functional replacements for traditionally manufactured parts but also offer enhanced performance and efficiency. Metal3DP‘s team of experienced engineers can provide valuable insights and support in optimizing your designs for metal additive manufacturing. Contact us to explore how our expertise can benefit your automotive applications.
Tolerance, Surface Finish, and Dimensional Accuracy – Achieving Precision in 3D Printed Strut Mounts
In the automotive industry, precision and accuracy are paramount. Strut mounts must adhere to strict dimensional tolerances to ensure proper fit, function, and safety within the suspension system. Metal 3D printing technologies have advanced significantly in their ability to produce parts with high levels of accuracy and controlled surface finishes.
- Precisión dimensional: The dimensional accuracy achievable with metal 3D printing depends on several factors, including the printing technology (e.g., DMLS, SLM, SEBM), the material used, and the size and complexity of the part. With careful process control and optimized parameters, tolerances of ±0.1 mm or even finer can be achieved for critical dimensions of strut mounts.
- Acabado superficial: The as-printed surface finish of metal 3D printed parts is typically rougher than that achieved by machining. The surface roughness is influenced by the powder particle size, layer thickness, and printing parameters. For strut mount applications where smooth surfaces are required for mating with other components or for fatigue performance, post-processing techniques like machining, grinding, polishing, or shot peening can be employed to achieve the desired surface finish.
- Factores que afectan a la precisión: Several factors can influence the dimensional accuracy of 3D printed strut mounts:
- Thermal Distortion: Residual stresses built up during the printing process can lead to warping or distortion. Proper process parameters, stress relief heat treatments, and optimized part orientation can mitigate these issues.
- Encogimiento: Metal powders undergo solidification and shrinkage during the printing process. Accurate compensation for this shrinkage in the design and process parameters is crucial for achieving dimensional accuracy.
- Calibración y Mantenimiento: Regular calibration and maintenance of the 3D printing equipment are essential to ensure consistent and accurate results.
- Retirada de la estructura de soporte: The removal of support structures can sometimes affect the surface finish and dimensional accuracy of the supported areas. Careful design and optimized support strategies can minimize these effects.
Metal3DP utilizes advanced 3D printing equipment and rigorously controlled processes to ensure the production of strut mounts with high dimensional accuracy and consistent quality. We understand the critical importance of precision in automotive components and employ stringent quality control measures throughout the manufacturing process.
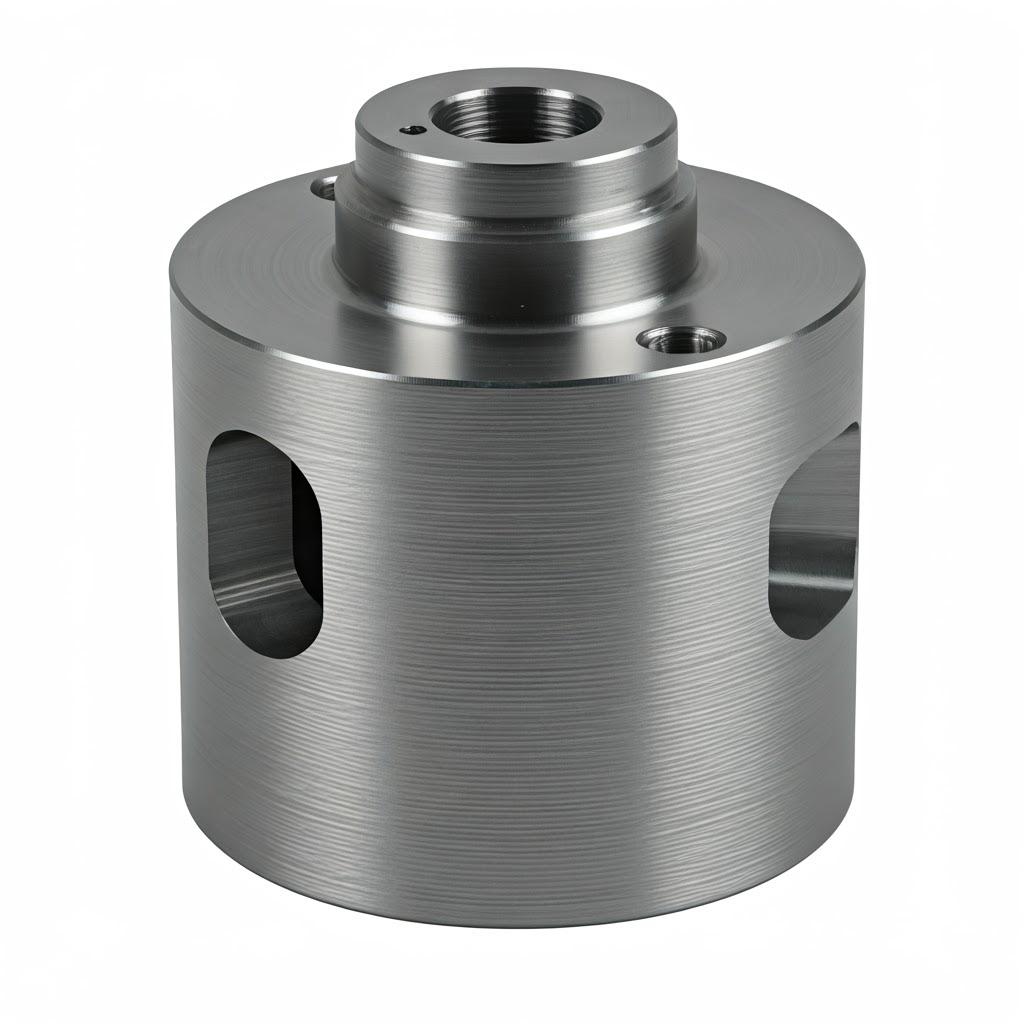
Post-Processing Requirements – Enhancing Performance and Finish of 3D Printed Strut Mounts
While metal 3D printing can produce near-net-shape parts, post-processing steps are often necessary to achieve the final desired properties, surface finish, and dimensional accuracy for automotive strut mounts. Common post-processing requirements include:
- Retirada de la estructura de soporte: Support structures, essential for printing complex geometries, need to be carefully removed after the build is complete. This can be done manually or using automated methods, depending on the complexity and material.
- Tratamiento térmico antiestrés: To alleviate residual stresses built up during the rapid heating and cooling cycles of the printing process, a stress relief heat treatment is often performed. This improves the mechanical properties and dimensional stability of the strut mount.
- Acabado superficial: Depending on the application and required surface roughness, various finishing techniques can be employed:
- Mecanizado: Precision machining can be used to achieve tight tolerances and smooth surface finishes on critical mating surfaces.
- Grinding and Polishing: These processes can further refine the surface finish for improved aesthetics or performance.
- Granallado: This surface treatment can enhance fatigue resistance by introducing compressive stresses on the surface.
- Heat Treatment for Property Enhancement: Specific heat treatments can be applied to optimize the mechanical properties of the 3D printed material, such as increasing hardness or strength. The specific heat treatment will depend on the alloy used (e.g., age hardening for A7075).
- Surface Coatings: Coatings can be applied to enhance corrosion resistance, wear resistance, or other functional properties. Common coatings for automotive components include anodizing, powder coating, or specialized protective films.
- Inspección y control de calidad: Rigorous inspection processes, including dimensional measurements and non-destructive testing (NDT) methods, are crucial to ensure that the 3D printed strut mounts meet the required quality standards.
Metal3DP offers comprehensive post-processing services to ensure that our 3D printed strut mounts meet the exact specifications of our automotive clients. Our expertise in material science and manufacturing processes allows us to select and apply the most appropriate post-processing techniques to achieve optimal performance and durability.
Common Challenges and How to Avoid Them – Ensuring Successful 3D Printing of Strut Mounts
While metal 3D printing offers numerous advantages, there are potential challenges that can arise during the production of strut mounts. Understanding these challenges and implementing appropriate strategies to avoid them is crucial for successful outcomes:
- Deformación y distorsión: Thermal gradients and residual stresses during the printing process can lead to warping or distortion of the part.
- Solución: Optimize part orientation, use support structures effectively, control process parameters (e.g., laser power, scan speed, build plate temperature), and implement stress relief heat treatments.
- Porosidad: Internal voids or pores within the printed part can compromise its mechanical strength and fatigue resistance.
- Solución: Optimize printing parameters, ensure high-quality metal powder with good flowability (a key characteristic of Metal3DP‘s powders), and employ appropriate shielding gas to prevent oxidation.
- Dificultades para retirar la estructura de soporte: Aggressively attached support structures can be challenging to remove and may leave surface defects.
- Solución: Design parts with self-supporting angles where possible, optimize support structure design for easy removal, and use appropriate removal tools and techniques.
- Rugosidad superficial: The as-printed surface finish may not meet the requirements for certain applications.
- Solución: Optimize printing parameters to minimize surface roughness, and employ post-processing techniques like machining, grinding, or polishing.
- Material Property Variations: Inconsistent material properties throughout the printed part can occur if process parameters are not well-controlled.
- Solución: Utilize well-calibrated and maintained 3D printing equipment (like Metal3DP‘s industry-leading printers), optimize and consistently monitor process parameters, and ensure the use of high-quality, homogeneous metal powders.
- Cost Optimization: While 3D printing can be cost-effective for certain applications, it’s essential to optimize the design and printing process to minimize costs.
- Solución: Design for material efficiency (e.g., topology optimization, lattice structures), optimize build time through part orientation and nesting, and select the most appropriate printing technology and material for the application.
By proactively addressing these potential challenges through careful design, optimized process parameters, and the use of high-quality materials and equipment (such as those provided by Metal3DP), manufacturers can successfully leverage metal 3D printing to produce high-performance automotive strut mounts.
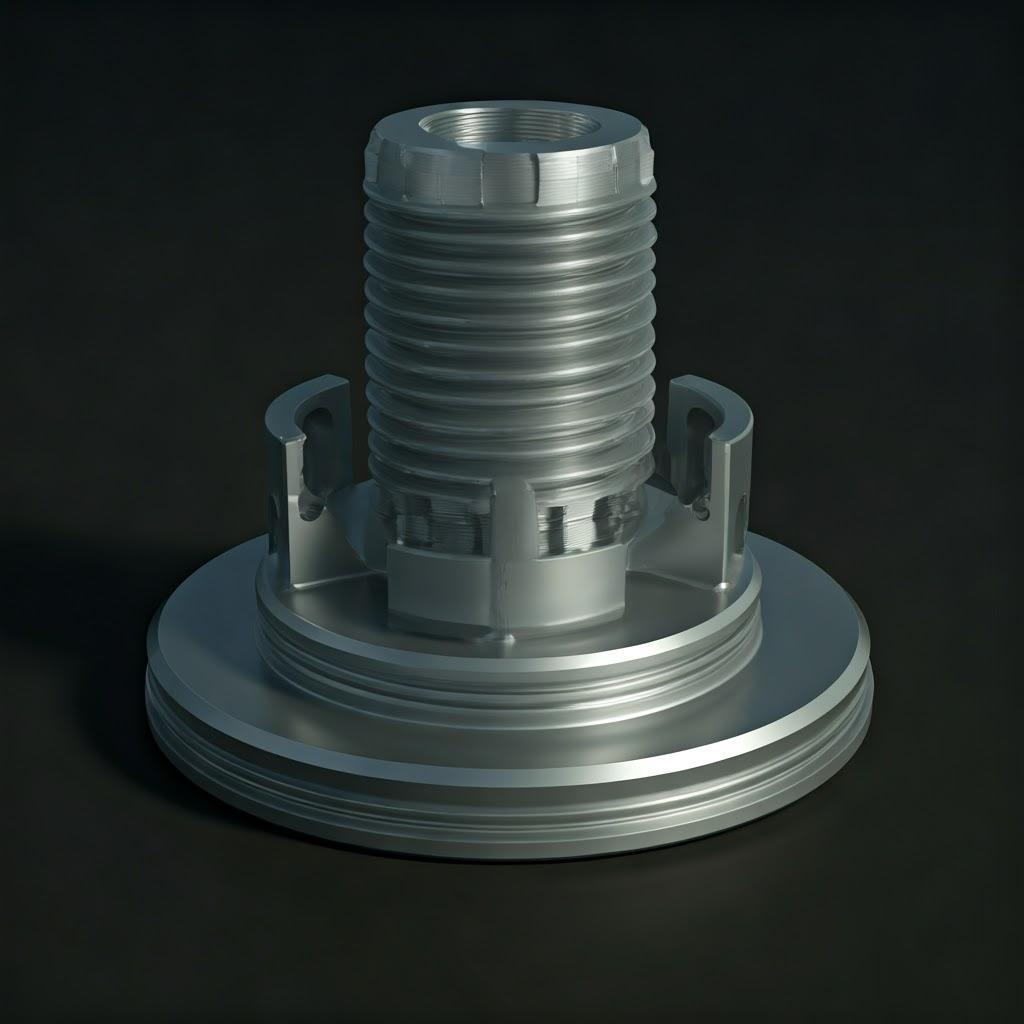
How to Choose the Right Metal 3D Printing Service Provider – Selecting a Partner for Automotive Innovation
Choosing the right metal 3D printing service provider is a critical decision that can significantly impact the success of your automotive strut mount project. A reliable partner will possess the expertise, equipment, and quality control processes necessary to deliver high-performance components that meet your specific requirements. Here are key factors to consider when evaluating potential metal 3D printing service providers:
- Capacidades de los materiales: Ensure the provider has experience working with the recommended materials (A7075 and AlSi10Mg) and possesses the necessary material certifications and expertise in handling these alloys for automotive applications. Metal3DP offers a wide range of high-quality metal powders, including these advanced aluminum alloys, specifically optimized for additive manufacturing.
- Printing Technology and Equipment: Understand the types of metal 3D printing technologies the provider utilizes (e.g., DMLS, SLM, SEBM). Each technology has its own strengths and limitations in terms of accuracy, surface finish, and build volume. Metal3DP‘s industry-leading SEBM printers offer exceptional accuracy and reliability for mission-critical parts.
- Quality Control and Certifications: Inquire about the provider’s quality management system and certifications (e.g., ISO 9001, AS9100 for aerospace). Robust quality control processes, including material traceability, in-process monitoring, and post-printing inspection, are essential for ensuring the reliability of automotive components.
- Design and Engineering Support: A valuable service provider will offer design and engineering support to help optimize your strut mount design for additive manufacturing. This includes expertise in topology optimization, material selection, and design for manufacturability. Metal3DP‘s team possesses decades of collective expertise in metal additive manufacturing and provides comprehensive application development services.
- Capacidades de postprocesado: Determine if the provider offers the necessary post-processing services, such as support removal, heat treatment, surface finishing, and coatings, to meet your final part requirements. A one-stop-shop for printing and post-processing can streamline the production process.
- Production Capacity and Scalability: Assess the provider’s production capacity and their ability to scale up production if your volumes increase. Consider their lead times and manufacturing capabilities.
- Industry Experience and Reputation: Look for a provider with a proven track record in the automotive industry or similar demanding sectors. Review case studies and testimonials to gauge their experience and customer satisfaction.
- Communication and Customer Support: Effective communication and responsive customer support are crucial for a smooth and successful collaboration. Choose a provider that is proactive, transparent, and willing to work closely with you throughout the project.
By carefully evaluating these factors, you can select a metal 3D printing service provider like Metal3DP that can be a valuable partner in your automotive innovation journey.
Cost Factors and Lead Time – Understanding the Economics of 3D Printed Strut Mounts
Understanding the cost drivers and typical lead times associated with metal 3D printing is essential for budget planning and project scheduling. Several factors influence the cost of 3D printed strut mounts:
- Coste del material: The cost of the metal powder (e.g., A7075, AlSi10Mg) is a significant factor. Specialized alloys and high-performance powders typically have higher costs. Metal3DP manufactures a wide range of high-quality metal powders to meet various application needs.
- Tiempo de construcción: The time it takes to print a strut mount depends on its size, complexity, and the chosen printing technology. Longer build times translate to higher machine operating costs. Optimizing part orientation and design for faster printing can help reduce costs.
- Costes de postprocesamiento: The extent of post-processing required (e.g., support removal, heat treatment, machining, coatings) will impact the overall cost. Minimizing the need for extensive post-processing through design optimization can be beneficial.
- Costes laborales: The expertise required for design, printing, and post-processing contributes to the overall cost. Experienced service providers with skilled technicians may have higher labor costs but can also ensure higher quality.
- Machine Depreciation and Maintenance: The cost of owning and maintaining the 3D printing equipment is factored into the pricing.
- Volume of Production: While 3D printing can be cost-effective for low to medium volumes and customized parts, the cost per part may decrease with larger production runs due to economies of scale.
Plazo de entrega: The lead time for 3D printed strut mounts depends on factors such as:
- Design Complexity and Optimization: Initial design and optimization for additive manufacturing may take time.
- Disponibilidad de material: The availability of the chosen metal powder can affect lead times. Metal3DP maintains a stock of its high-quality metal powders to ensure timely production.
- Tiempo de impresión: The actual printing duration is a key component of the lead time.
- Tiempo de post-procesamiento: The time required for post-processing steps will add to the overall lead time.
- Control de Calidad e Inspección: Thorough quality checks can also influence the final delivery time.
It’s important to discuss cost and lead time expectations with your chosen metal 3D printing service provider early in the project to ensure alignment with your budget and schedule. Metal3DP is committed to providing transparent cost breakdowns and realistic lead times for our additive manufacturing services.
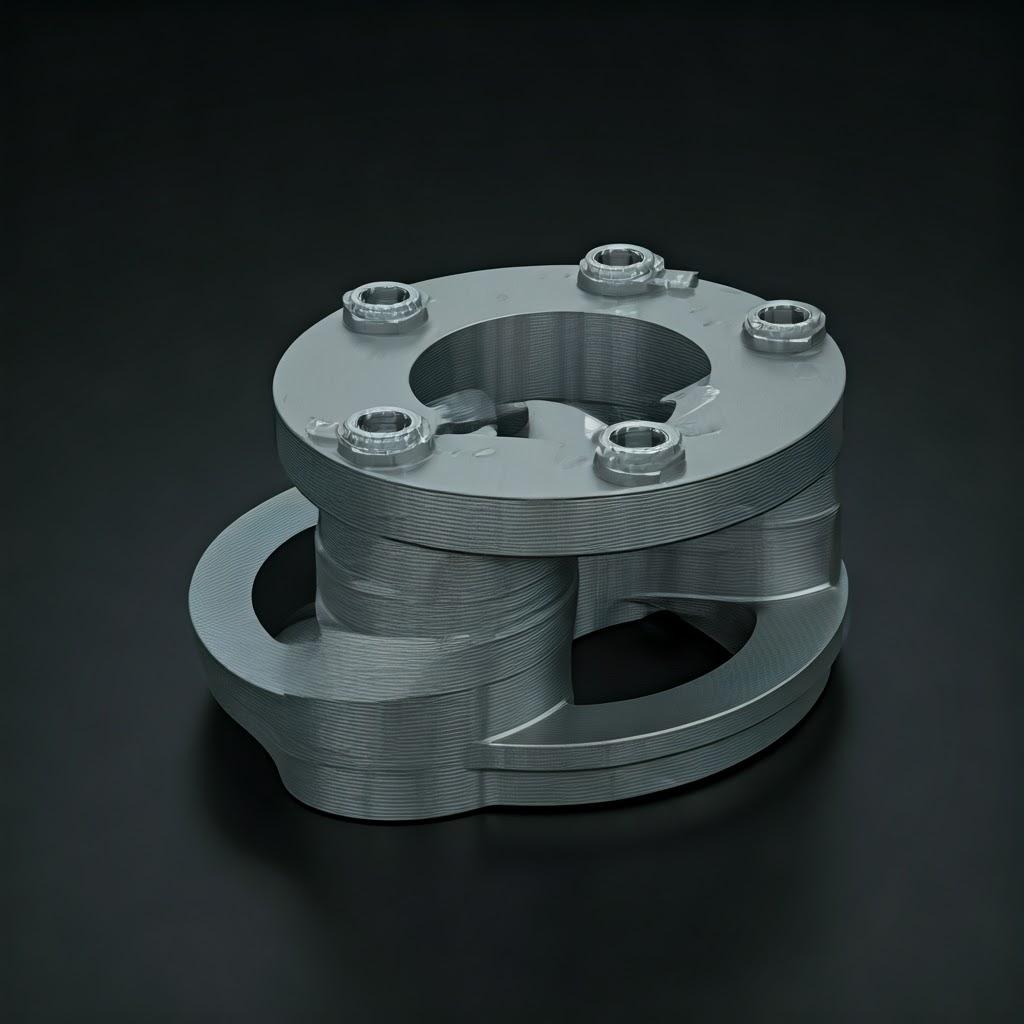
Frequently Asked Questions (FAQ) – Addressing Common Inquiries about 3D Printed Strut Mounts
- Are 3D printed metal strut mounts as strong and durable as traditionally manufactured ones?
- Yes, when the design is optimized for additive manufacturing and the correct high-performance metal powder (like A7075 or AlSi10Mg from Metal3DP) is used with appropriate post-processing, 3D printed strut mounts can achieve comparable or even superior strength-to-weight ratios and durability compared to traditionally manufactured parts.
- Can metal 3D printing be cost-effective for producing strut mounts in larger volumes?
- While 3D printing excels in low to medium volume production and customization, advancements in technology and process optimization are making it increasingly competitive for larger volumes as well. Factors like design complexity, material efficiency, and reduced assembly costs can contribute to its cost-effectiveness. Consulting with Metal3DP can help assess the cost-effectiveness for your specific volume requirements.
- What are the typical tolerances achievable with metal 3D printing for strut mounts?
- Depending on the printing technology and material, tolerances of ±0.1 mm or even finer can be achieved for critical dimensions. Post-processing techniques like machining can further enhance dimensional accuracy when required. Metal3DP‘s advanced printing equipment is capable of achieving high levels of precision.
Conclusion – Driving Automotive Excellence with 3D Printed Strut Mounts
Metal 3D printing is revolutionizing the design and manufacturing of automotive components, and strut mounts are a prime example of this transformative potential. By leveraging the design freedom, material optimization, and rapid prototyping capabilities of additive manufacturing, engineers and procurement managers can unlock significant benefits, including lightweighting, enhanced performance, on-demand production, and customization. Materials like A7075 and AlSi10Mg, available in high quality from Metal3DP, offer the ideal combination of strength, durability, and printability for these critical suspension components. As the automotive industry continues to push the boundaries of innovation, metal 3D printing will undoubtedly play an increasingly vital role in shaping the future of vehicle design and manufacturing. Contact Metal3DP today to explore how our cutting-edge systems and high-performance metal powders can empower your organization’s additive manufacturing goals.
Compartir
MET3DP Technology Co., LTD es un proveedor líder de soluciones de fabricación aditiva con sede en Qingdao, China. Nuestra empresa está especializada en equipos de impresión 3D y polvos metálicos de alto rendimiento para aplicaciones industriales.
Solicite información para obtener el mejor precio y una solución personalizada para su empresa.
Artículos relacionados
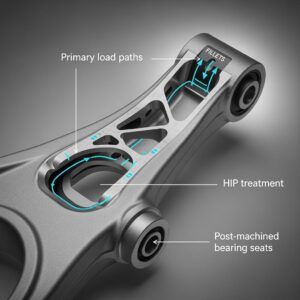
Metal 3D Printing for U.S. Automotive Lightweight Structural Brackets and Suspension Components
Leer Más "Acerca de Met3DP
Actualización reciente
Nuestro producto
CONTACTO
¿Tiene alguna pregunta? ¡Envíenos un mensaje ahora! Atenderemos su solicitud con todo un equipo tras recibir su mensaje.