Impresión 3D de polvo metálico: elección del equipo de atomización por plasma
Índice
Imagine crafting intricate objects directly from a stream of molten metal particles, each no bigger than a grain of sand. This isn’t science fiction; it’s the reality of 3D printing with polvos metálicos. But where do these tiny metallic marvels come from? Enter the fascinating world of plasma atomization, a technology that transforms molten metal into the building blocks of 3D printed masterpieces.
A Deep Dive into Plasma Atomization
Plasma atomization, at its core, is a high-tech metal refining process. Here’s how it works:
- Preparación de la materia prima: The journey begins with the selection of high-purity metal feedstock, typically in the form of ingots or rods. These are meticulously chosen to ensure the final powder meets specific material properties and composition requirements.
- Melting and Plasma Generation: The chosen feedstock is then fed into a high-temperature furnace, where it’s melted into a molten metal stream. Simultaneously, an inert gas, like argon, is ionized using an electric arc, creating a high-temperature, high-velocity plasma stream.
- Atomización: The heart of the process lies in the interaction between the molten metal and the plasma stream. The plasma, acting like a high-powered cutting torch, disrupts the molten metal stream, breaking it down into tiny droplets. These droplets rapidly solidify in-flight due to the extreme cooling provided by the surrounding gas environment.
- Powder Collection and Classification: The resulting polvo metálico, with a distribution of particle sizes and shapes, is then collected using cyclones or filters. Finally, the powder undergoes a classification process, where particles are separated based on their size and morphology using sieving or air classification techniques.
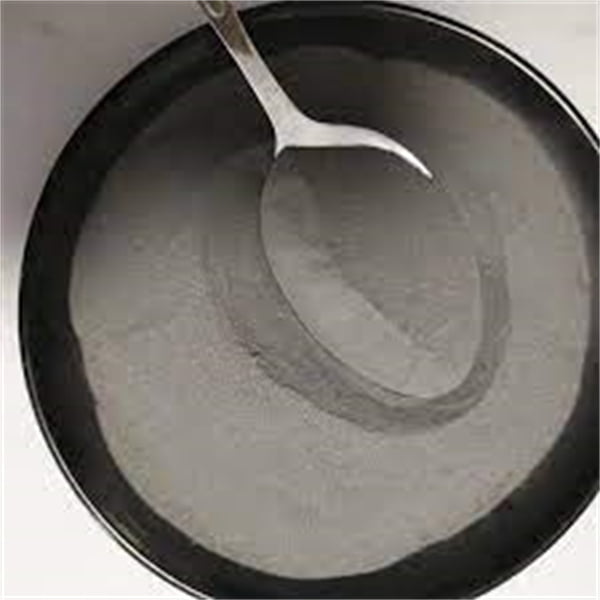
Equipment of Plasma Atomization
The magic of plasma atomization doesn’t happen by itself. It requires a complex orchestra of specialized equipment, each playing a crucial role in the process. Let’s delve into the key players:
1. Plasma Torch: This specialized device acts as the conductor, generating the high-temperature plasma stream using an electric arc and an inert gas. Different torch designs exist, each offering various advantages in terms of plasma temperature, velocity, and controllability.
2. Induction Furnace: Imagine a high-tech pot melter. The induction furnace uses electromagnetic induction to efficiently heat and melt the metal feedstock to the desired temperature, ensuring consistent and uniform melting throughout the process.
3. Atomization Chamber: This is the stage where the drama unfolds. The chamber houses the plasma torch and the molten metal feedstock, providing a controlled environment for the atomization process.
4. Powder Collection System: After atomization, the metal particles need to be captured. This is where the collection system, employing cyclones or filters, comes into play, efficiently separating the powder from the gas stream.
5. Classification System: Not all metal powder particles are created equal. The classification system, often using sieving or air classification techniques, meticulously sorts the powder based on particle size and morphology, ensuring a consistent and desirable powder distribution for 3D printing applications.
6. Control System: The entire process is meticulously monitored and controlled by a sophisticated control system. This system ensures optimal operating parameters for the plasma torch, furnace, and other equipment, guaranteeing consistent and high-quality powder production.
Exploring Popular Polvos metálicos
The beauty of plasma atomization lies in its versatility. It can transform a wide range of metals into 3D printing-ready powders. Here are some of the most popular metal powders used in additive manufacturing:
1. Polvos de acero inoxidable: These versatile powders offer a combination of strength, corrosion resistance, and affordability, making them ideal for diverse applications, from medical implants to aerospace components.
2. Titanium Powders: Renowned for their exceptional strength-to-weight ratio and biocompatibility, titanium powders are extensively used in the aerospace, medical, and dental industries.
3. Polvos de aluminio: Lightweight and readily recyclable, aluminum powders are popular choices for applications requiring weight reduction and good thermal conductivity, such as in the automotive and aerospace sectors.
4. Nickel-based Alloy Powders: Offering superior high-temperature performance and corrosion resistance, nickel-based alloy powders cater to demanding applications in the energy, aerospace, and chemical processing industries.
5. Cobalt-Chrome Powders: These biocompatible powders are widely used in the medical and dental fields for applications like joint replacements and dental prosthetics due to their excellent wear resistance and biocompatibility.
6. Inconel Powders: These high-performance nickel-chromium-based alloy powders are known for their exceptional strength, heat resistance, and corrosion resistance, making them ideal for demanding applications in gas turbines, rocket engines, and chemical processing equipment.
7. Polvos de cobre:Renowned for their excellent electrical conductivity and thermal conductivity, copper powders are used in various applications, including electrical components, heat exchangers, and even 3D printed antennas.
8. Polvos de metales refractarios:These high-melting-point powders, such as tungsten and tantalum, excel in environments requiring extreme heat resistance and wear resistance. They find applications in furnace components, crucibles, and even rocket engine nozzles.
9. Precious Polvos metálicos: From gold and silver to platinum and palladium, plasma atomization allows for the creation of fine metal powders for diverse applications, including jewelry, electronics, and even dental restorations.
10. Polvos multimaterial: Pushing the boundaries of innovation, plasma atomization can also be used to create composite powders, combining different materials to achieve unique properties. For example, combining titanium and tantalum can create powders with improved strength and biocompatibility for medical implants.
Comparing Plasma Atomization with Gas Atomization
While plasma atomization reigns supreme in the realm of high-performance, specialty metal powders, gas atomization is another popular technique for creating 3D printing-ready powders. Let’s explore the key differences:
Atomización por plasma:
- Ventajas:
- Partículas de polvo más finas y esféricas: Ideal for applications requiring high precision and surface finish.
- Better control over powder properties: Allows for tailoring particle size distribution and morphology for specific needs.
- Suitable for a wider range of metal materials: Can handle high-melting-point and reactive metals.
- Desventajas:
- Higher energy consumption: The high-temperature plasma generation process demands significant energy input.
- More complex and expensive equipment: Setting up and maintaining a plasma atomization system requires greater investment.
Atomización de gases:
- Ventajas:
- Lower energy consumption: Compared to plasma atomization, gas atomization offers a more energy-efficient process.
- Lower equipment cost: Setting up a gas atomization system is generally less expensive.
- Desventajas:
- Coarser and less spherical powder particles: May not be suitable for applications demanding high precision and surface finish.
- Compatibilidad de materiales limitada: Struggles with high-melting-point and reactive metals.
Ultimately, the choice between plasma and gas atomization depends on the specific needs of the application. For high-performance, demanding applications requiring finer powders and superior control over properties, plasma atomization reigns supreme. However, for cost-sensitive applications where coarser powders suffice, gas atomization can be a viable option.
Unveiling the Advantages and Disadvantages
Like any technology, plasma atomization offers a unique blend of benefits and drawbacks. Let’s delve deeper:
Ventajas:
- Polvos de alta calidad: Produces finer and more spherical powder particles, leading to improved printability, surface finish, and mechanical properties of the final 3D printed parts.
- Greater control over properties: Allows for tailoring particle size distribution, morphology, and even chemical composition for specific applications.
- Versatilidad: Handles a wide range of metal materials, including high-melting-point and reactive metals, expanding the possibilities for 3D printing diverse materials.
Desventajas:
- Alto consumo de energía: The process requires significant energy input for plasma generation, impacting operational costs and environmental footprint.
- Costes operativos y de capital elevados: Setting up and maintaining a plasma atomization system demands substantial investment compared to other powder production techniques.
- Technical complexity: The process requires expertise and careful control of various parameters for consistent and high-quality powder production.
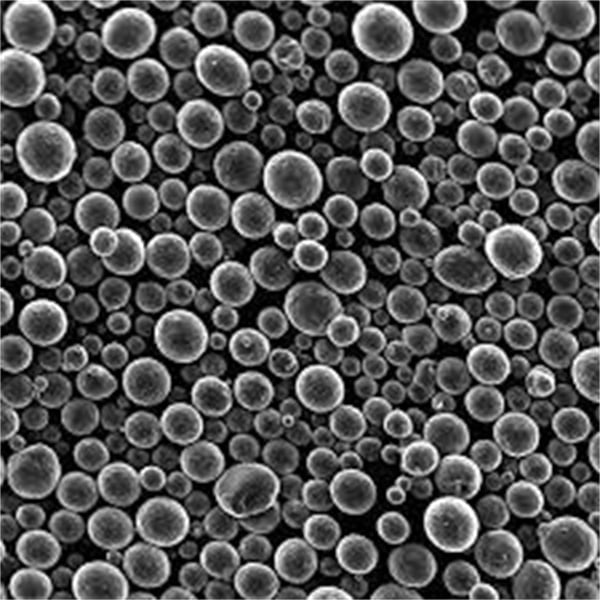
Exploring Additional Considerations
While we’ve explored the core aspects of plasma atomization and its role in 3D printing metal powders, several additional factors are worth considering:
- Impacto medioambiental: The high energy consumption of plasma atomization raises concerns about its environmental footprint. Ongoing research focuses on developing more energy-efficient processes and utilizing renewable energy sources.
- Consideraciones de seguridad: Working with molten metal and high-temperature plasma involves inherent safety risks. Implementing proper safety protocols and training personnel are crucial for safe operation.
- Future advancements: The field of plasma atomization is constantly evolving. Research is underway to develop new techniques for even finer and more uniform powder production, enabling the creation of 3D printed parts with superior properties and unlocking new possibilities for additive manufacturing.
PREGUNTAS FRECUENTES
Q: What are the typical sizes of metal powder particles produced by plasma atomization?
A: The size of metal powder particles produced by plasma atomization can vary depending on the specific material and process parameters. However, they typically range from 10 to 150 micrometers in diameter, with some reaching even finer or coarser sizes depending on the application.
Q: How does the quality of the feedstock metal impact the final powder properties?
A: The quality of the feedstock metal plays a crucial role in the final powder properties. Impurities and inconsistencies in the feedstock can translate into defects and variations in the powder particles, affecting their printability and the mechanical properties of the final 3D printed parts. Therefore, using high-purity and well-characterized feedstock is essential for consistent and high-quality powder production.
Q: What are some of the applications of 3D printed metal parts produced using plasma-atomized powders?
A: The applications of 3D printed metal parts produced using plasma-atomized powders are diverse and rapidly expanding. Here are some prominent examples:
- Aeroespacial: Aircraft components, spacecraft parts, and rocket engine components benefit from the lightweight, high-strength, and high-temperature resistance offered by 3D printed metals.
- Médico: Custom implants, surgical instruments, and dental prosthetics leverage the biocompatibility and excellent mechanical properties of 3D printed metals for personalized medical solutions.
- Automóvil: Components requiring high strength-to-weight ratio, such as car parts and racing components, can be 3D printed using metal powders for improved performance and weight reduction.
- Bienes de consumo: From high-end sporting equipment to customized jewelry, 3D printed metal parts are finding their way into various consumer goods, offering unique design possibilities and personalization options.
Q: What are the future prospects of plasma atomization in the 3D printing industry?
A: Plasma atomization is expected to remain a critical technology for producing high-performance metal powders for 3D printing. As the demand for advanced materials and complex geometries in 3D printing grows, the need for finer, more uniform, and tailored powders will rise. Advancements in plasma atomization technology, including the development of more energy-efficient processes and the exploration of novel powder production techniques, are expected to further strengthen its position in the 3D printing landscape.
En conclusión, plasma atomization stands as a cornerstone technology in the realm of 3D printing metal powders. Its versatility, ability to produce high-quality powders, and expanding range of applications make it a vital tool for pushing the boundaries of additive manufacturing and unlocking the potential of 3D printing across diverse industries. As research and development continue to refine the process and explore new possibilities, plasma atomization is poised to play a significant role in shaping the future of 3D printing.
Compartir
MET3DP Technology Co., LTD es un proveedor líder de soluciones de fabricación aditiva con sede en Qingdao, China. Nuestra empresa está especializada en equipos de impresión 3D y polvos metálicos de alto rendimiento para aplicaciones industriales.
Solicite información para obtener el mejor precio y una solución personalizada para su empresa.
Artículos relacionados
Acerca de Met3DP
Actualización reciente
Nuestro producto
CONTACTO
¿Tiene alguna pregunta? ¡Envíenos un mensaje ahora! Atenderemos su solicitud con todo un equipo tras recibir su mensaje.
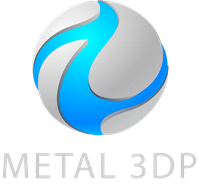
Polvos metálicos para impresión 3D y fabricación aditiva
PRODUCTO
cONTACT INFO
- Ciudad de Qingdao, Shandong, China
- [email protected]
- [email protected]
- +86 19116340731