金属粉末の3Dプリント:プラズマアトマイズ装置の選択
目次
それぞれが砂粒ほどの大きさしかない溶けた金属粒子の流れから、複雑なオブジェクトを直接作ることを想像してみてください。これはサイエンスフィクションではない。 金属粉.しかし、この小さな金属の驚異はどこから来るのだろうか?溶けた金属を3Dプリントの傑作の構成要素に変える技術、プラズマアトマイゼーションの魅惑的な世界に足を踏み入れてみよう。
プラズマアトマイゼーションを深く掘り下げる
プラズマアトマイゼーションの核心は、ハイテク金属精錬プロセスである。その仕組みはこうだ:
- 原料の準備: その旅は、一般的にインゴットやロッドの形をした高純度の金属原料を選ぶことから始まります。これらの原料は、最終的な粉末が特定の材料特性と組成要件を満たすよう、細心の注意を払って選択されます。
- 溶融とプラズマ生成: 選択された原料は高温炉に供給され、そこで溶融され、溶融金属ストリームとなる。同時に、アルゴンなどの不活性ガスが電気アークでイオン化され、高温・高速のプラズマ流が発生する。
- 霧化: このプロセスの核心は、溶融金属とプラズマ流の相互作用にある。プラズマは高出力の切断トーチのように作用し、溶融金属の流れを破壊して小さな液滴に分解する。これらの液滴は、周囲のガス環境による極端な冷却によって、飛行中に急速に凝固する。
- 粉の収集と分類: その結果 金属粉その後、サイクロンやフィルターを使って、粒径と形状の分布を持つ粉体を回収する。最後に、粉体は分級工程を経て、ふるい分けまたは気流分級技術を用いて、粒径と形態に基づいて粒子が分離される。
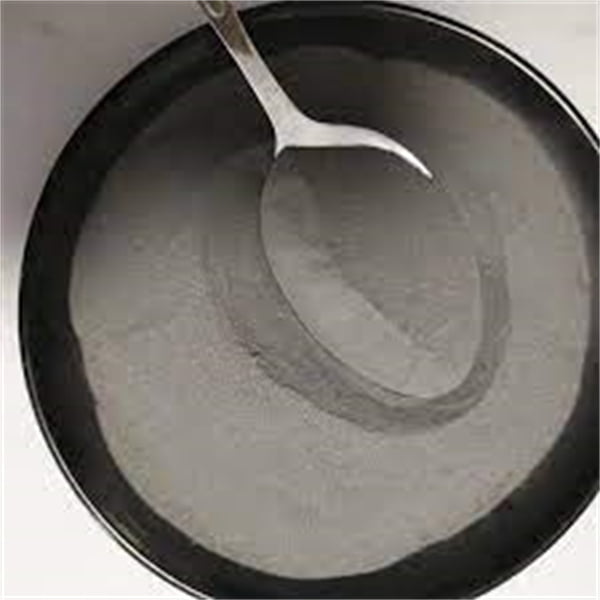
プラズマアトマイズ装置
プラズマ霧化の魔法は、それだけで起こるものではない。複雑な専門機器のオーケストラが必要で、それぞれがプロセスで重要な役割を果たしている。では、そのキーパーソンを掘り下げてみよう:
1.プラズマトーチ: この特殊な装置が導体として機能し、電気アークと不活性ガスを用いて高温プラズマ流を発生させる。さまざまな設計のトーチが存在し、それぞれプラズマ温度、速度、制御性などの点でさまざまな利点がある。
2.誘導炉: ハイテク鍋溶解機を想像してください。誘導炉は電磁誘導を利用して金属原料を効率的に加熱し、目的の温度まで溶融させ、プロセス全体を通して一貫した均一な溶融を実現します。
3.霧化チャンバー: ここはドラマが展開される舞台である。チャンバーにはプラズマ・トーチと溶融金属原料が収納され、霧化プロセスのための制御された環境が提供される。
4.粉体回収システム: 霧化の後、金属粒子を捕捉する必要がある。そこでサイクロンやフィルターを用いた捕集システムが活躍し、ガス流から粉体を効率的に分離する。
5.分類システム: 金属粉末の粒子はすべて同じではありません。分級システムは、多くの場合、ふるい分けまたは気流分級技術を使用し、粒径と形態に基づいて粉末を綿密に選別し、3Dプリンティング用途に一貫した望ましい粉末分布を確保します。
6.制御システム: プロセス全体は、高度な制御システムによって綿密に監視・制御されている。このシステムにより、プラズマトーチ、炉、その他の機器の最適な動作パラメータが保証され、安定した高品質の粉末生産が保証されます。
ポピュラーを探る 金属粉
プラズマアトマイゼーションの素晴らしさは、その多様性にある。さまざまな金属を3Dプリント可能な粉末に変えることができる。ここでは、積層造形で使用される最も一般的な金属粉末をいくつか紹介する:
1.ステンレス鋼粉末: これらの汎用性の高い粉末は、強度、耐食性、手頃な価格を兼ね備えており、医療用インプラントから航空宇宙部品まで、さまざまな用途に理想的です。
2.チタン粉末: その卓越した強度対重量比と生体適合性で有名なチタン粉末は、航空宇宙、医療、歯科産業で広く使用されています。
3.アルミニウム粉末: 軽量でリサイクルしやすいアルミニウム粉末は、自動車や航空宇宙分野など、軽量化と優れた熱伝導性を必要とする用途によく選ばれています。
4.ニッケル基合金粉末 優れた高温性能と耐食性を提供するニッケル基合金粉末は、エネルギー、航空宇宙、化学処理産業などの要求の厳しい用途に対応しています。
5.コバルトクロム粉: これらの生体適合性粉末は、その優れた耐摩耗性と生体適合性により、人工関節や歯科補綴物などの用途に医療・歯科分野で広く使用されている。
6.インコネル粉末: これらの高性能ニッケル・クロム系合金粉末は、卓越した強度、耐熱性、耐食性で知られており、ガスタービン、ロケットエンジン、化学処理装置などの要求の厳しい用途に最適です。
7. 銅粉:優れた電気伝導性と熱伝導性で知られる銅粉は、電気部品や熱交換器、さらには3Dプリントアンテナなど、さまざまな用途に使われています。
8. 耐火金属粉末:タングステンやタンタルなどの高融点粉末は、極端な耐熱性と耐摩耗性が要求される環境で優れた性能を発揮します。炉の部品、るつぼ、ロケットエンジンのノズルなどにも使用されています。
9. プレシャス 金属粉: 金、銀からプラチナ、パラジウムに至るまで、プラズマアトマイゼーションは、宝飾品、電子機器、さらには歯科修復を含む多様な用途のための微細な金属粉末の製造を可能にする。
10. マルチ・マテリアル・パウダー: 技術革新の限界を押し広げるプラズマアトマイゼーションは、異なる材料を組み合わせて独自の特性を実現する複合粉末の製造にも利用できる。例えば、チタンとタンタルを組み合わせることで、医療用インプラントの強度と生体適合性を向上させた粉末を作ることができる。
プラズマ霧化とガス霧化の比較
高性能の特殊金属粉末の分野ではプラズマアトマイゼーションが頂点に君臨していますが、ガスアトマイゼーションも3Dプリントに適した粉末を作るための一般的な技術です。その主な違いを探ってみよう:
プラズマ霧化:
- メリット
- より細かく、より球状の粉末粒子: 高精度と表面仕上げを必要とする用途に最適。
- パウダーの特性をよりよくコントロールできる: 特定のニーズに合わせて粒度分布と形態を調整できる。
- より幅広い金属材料に適している: 高融点金属や反応性金属を扱うことができる。
- デメリット
- エネルギー消費量が多い: 高温プラズマ生成プロセスには、大きなエネルギー投入が要求される。
- より複雑で高価な機器: プラズマ霧化システムの設置と維持には、より大きな投資が必要である。
ガス霧化:
- メリット
- より低いエネルギー消費: プラズマアトマイゼーションに比べ、ガスアトマイゼーションはよりエネルギー効率の高いプロセスを提供する。
- 設備コストの低減: ガス噴霧システムの設置は一般に安価である。
- デメリット
- より粗く、より球形でない粉末粒子: 高精度と表面仕上げを必要とする用途には適さない場合がある。
- 材料の互換性には制限がある: 高融点金属や反応性金属との闘い。
最終的に、プラズマとガスアトマイゼーションのどちらを選択するかは、アプリケーションの具体的なニーズによって決まります。より微細な粉末と優れた特性制御を必要とする高性能で要求の厳しい用途では、プラズマアトマイゼーションが優位に立つ。しかし、より粗い粉末で十分なコスト重視の用途では、ガスアトマイズが有効な選択肢となります。
メリットとデメリットを明らかにする
どの技術にも言えることだが、プラズマ霧化には利点と欠点がある。さらに掘り下げてみよう:
メリット
- 高品質のパウダー: パウダー粒子をより細かく球状にすることで、最終的な3Dプリントパーツの印刷性、表面仕上げ、機械的特性を向上させます。
- 物件に対するコントロールの強化: 粒子径分布、形態、さらには化学組成を特定の用途に合わせて調整することができる。
- 汎用性がある: 高融点金属や反応性金属を含む幅広い金属材料に対応し、多様な材料の3Dプリントの可能性を広げる。
デメリット
- 高いエネルギー消費: このプロセスでは、プラズマ生成のために多大なエネルギーを投入する必要があり、運用コストと環境フットプリントに影響を与える。
- 資本コストと運用コストが高い: プラズマ霧化システムの設置や維持には、他の粉末製造技術に比べて多額の投資が必要である。
- 技術的な複雑さ: このプロセスでは、安定した高品質の粉末を製造するために、専門知識とさまざまなパラメーターの慎重な管理が必要となる。
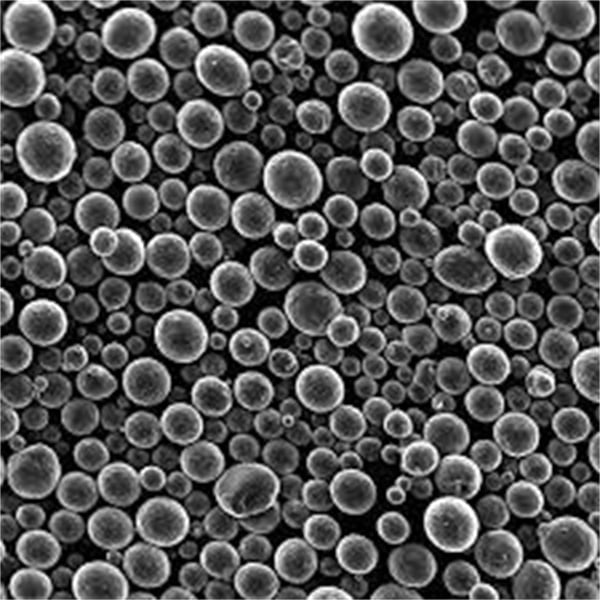
追加の考慮事項を探る
ここまで、プラズマアトマイゼーションの核心的な側面と、金属粉末の3Dプリントにおけるその役割について説明してきたが、さらにいくつかの要素を考慮する価値がある:
- 環境への影響: プラズマ霧化はエネルギー消費量が大きいため、環境への影響が懸念される。現在進行中の研究では、よりエネルギー効率の高いプロセスを開発し、再生可能エネルギー源を利用することに重点を置いている。
- 安全性への配慮: 溶融金属や高温プラズマを扱う作業には、固有の安全リスクが伴う。安全な操業には、適切な安全プロトコルの導入と人員のトレーニングが不可欠です。
- 将来の進歩: プラズマアトマイゼーションの分野は常に進化している。より微細で均一な粉末を製造するための新たな技術を開発するための研究が進められており、優れた特性を持つ3Dプリント部品の作成が可能になり、積層造形の新たな可能性が開かれている。
よくあるご質問
Q: プラズマアトマイズで生成される金属粉末の典型的なサイズは?
A: プラズマアトマイズによって生成される金属粉末の粒径は、特定の材料やプロセスパラメータによって異なります。しかし、一般的には直径が10~150マイクロメートルで、用途によってはさらに細かいものや粗いものもあります。
Q: 原料金属の品質は、最終的な粉末特性にどのような影響を与えますか?
A: 最終的な粉末の特性には、原料金属の品質が重要な役割を果たします。原料の不純物や不均一性は、粉末粒子の欠陥やばらつきにつながり、印刷性や最終的な3Dプリント部品の機械的特性に影響を与えます。従って、安定した高品質の粉末を製造するためには、高純度でよくキャラクタライズされた原料を使用することが不可欠です。
Q: プラズマアトマイズ粉末を使った3Dプリント金属部品には、どのような用途がありますか?
A: プラズマアトマイズ粉末を使用した3Dプリント金属部品の用途は多岐にわたり、急速に拡大しています。代表的な例をいくつかご紹介します:
- 航空宇宙 航空機部品、宇宙船部品、ロケットエンジン部品は、3Dプリント金属が提供する軽量、高強度、高温耐性の恩恵を受けている。
- メディカルだ: カスタムインプラント、手術器具、歯科補綴物は、3Dプリント金属の生体適合性と優れた機械的特性を活用し、個別の医療ソリューションを実現します。
- 自動車: 自動車部品やレーシングコンポーネントなど、高い強度対重量比を必要とするコンポーネントは、性能向上と軽量化のために金属粉末を使用して3Dプリントすることができます。
- 消費財: ハイエンドのスポーツ用品からカスタマイズされたジュエリーに至るまで、3Dプリントされた金属部品は、ユニークなデザインの可能性とパーソナライゼーションオプションを提供し、さまざまな消費財に進出しています。
Q: 3Dプリンティング業界におけるプラズマアトマイゼーションの将来性は?
A: プラズマアトマイズは、3Dプリンティング用の高性能金属粉末を製造するための重要な技術であり続けると予想されます。3Dプリンティングにおける先端材料や複雑な形状の需要が高まるにつれて、より微細で均一なオーダーメイドの粉末のニーズが高まるでしょう。よりエネルギー効率の高いプロセスの開発や新しい粉末製造技術の探求など、プラズマアトマイゼーション技術の進歩により、3Dプリンティングの分野での地位はさらに強化されると予想される。
結論として プラズマアトマイズは、金属粉末の3Dプリンティング領域における基礎技術です。その多用途性、高品質の粉末を製造する能力、応用範囲の拡大により、付加製造の限界を押し広げ、さまざまな業界で3Dプリンティングの可能性を引き出すために不可欠なツールとなっています。研究開発がプロセスを改良し、新たな可能性を追求し続ける中で、プラズマアトマイゼーションは3Dプリンティングの未来を形作る上で重要な役割を果たすことになるでしょう。
シェアする
MET3DP Technology Co., LTDは、中国青島に本社を置く積層造形ソリューションのリーディングプロバイダーです。弊社は3Dプリンティング装置と工業用途の高性能金属粉末を専門としています。
関連記事
Met3DPについて
最新情報
製品
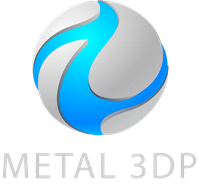
3Dプリンティングと積層造形用金属粉末