3D Printed Intake Manifolds for High-Performance Vehicles
目次
Introduction: Revolutionizing Performance with 3D Printed Intake Manifolds
The relentless pursuit of performance in the automotive industry demands constant innovation. Engineers and designers are perpetually seeking ways to extract more power, enhance efficiency, reduce weight, and optimize every component for maximum effect. Within the intricate dance of engine components, the intake manifold plays a critical, often underestimated, role. It’s the crucial conduit responsible for distributing the vital air-fuel mixture (or just air in direct-injection engines) to each cylinder. The efficiency, flow dynamics, and thermal management characteristics of this component directly impact engine output, throttle response, and overall vehicle performance. For decades, traditional manufacturing methods like casting and CNC machining have been the standard for producing intake manifolds. While reliable, these methods often impose significant constraints on design complexity, material choices, and production lead times, particularly for low-volume, high-performance applications or rapid prototyping cycles. Enter the disruptive power of 金属積層造形(AM), commonly known as metal 3D printing. This transformative technology is rapidly changing the landscape of automotive component design and production, offering unprecedented freedom and capabilities. Specifically for intake manifolds, metal AM unlocks the potential to create highly optimized, lightweight, and complex geometries that were previously impossible or prohibitively expensive to manufacture. Imagine intake runners precisely tuned for specific RPM ranges, integrated mounting points reducing assembly complexity, or internal structures designed for superior thermal management – all fabricated directly from robust, high-performance metal powders. This isn’t science fiction; it’s the reality enabled by technologies like Selective Laser Melting (SLM), Direct Metal Laser Sintering (DMLS), and Electron Beam Melting (EBM). Companies at the forefront of this revolution, like メット3dp, are providing the advanced equipment and high-quality materials necessary to turn these complex digital designs into functional, high-performance hardware. This introductory section sets the stage, exploring how metal 3D printing is not just an alternative but often a superior solution for producing next-generation intake manifolds, pushing the boundaries of what’s achievable in engine performance and design for the demanding high-performance vehicle sector. We will delve into the specific advantages, material considerations, design principles, and procurement strategies relevant to engineers, designers, and procurement managers looking to leverage this cutting-edge technology for competitive advantage in the 自動車の付加製造 space. The ability to rapidly iterate designs, customize manifolds for specific engine builds or racing series, and achieve significant weight reduction without compromising strength makes metal AM an indispensable tool for manufacturers aiming for the pinnacle of automotive engineering and performance. The integration of advanced simulation tools like Computational Fluid Dynamics (CFD) with the geometric freedom of AM allows for the creation of manifolds that are not just manufactured differently, but fundamentally より良い in terms of airflow efficiency and distribution, leading to tangible gains in horsepower and torque across the desired operating range. Furthermore, the potential for part consolidation – integrating features like fuel rail mounts, sensor bosses, or vacuum ports directly into the manifold structure – simplifies assembly, reduces potential leak points, and contributes further to overall system optimization. As we explore the nuances of this technology throughout this post, it will become clear why メタル 3Dプリンティング introduction into the workflow for performance vehicle components like intake manifolds is no longer a niche experiment but a strategic imperative for innovation and speed-to-market. The demand for bespoke solutions in motorsport, hypercars, and specialized tuning markets perfectly aligns with the capabilities of AM, allowing for tailored performance characteristics that mass production techniques struggle to accommodate efficiently or cost-effectively.
Unlocking Performance: The Role of Intake Manifolds in High-Performance Engines
To fully appreciate the impact of 3D printing, one must first understand the critical function of the intake manifold within a high-performance internal combustion engine. It’s far more than just a simple pipe; it’s a highly engineered component designed to manage and optimize the flow of air (or air-fuel mixture) from the throttle body to the individual cylinder intake ports. The effectiveness of this delivery process profoundly influences several key performance metrics:
- Volumetric Efficiency (VE): This measures how effectively the engine cylinders fill with the air-fuel mixture compared to their theoretical maximum volume. A well-designed intake manifold maximizes VE, especially within the engine’s target operating RPM range, by minimizing flow restrictions and utilizing pressure wave dynamics (acoustic tuning). Higher VE translates directly to more potential power output. In high-performance engines, maximizing VE across a broad RPM range, or specifically tuning it for peak power at high RPMs, is paramount. The intricate runner lengths, diameters, plenum volume, and runner transitions achievable with メタルAM allow for unprecedented control over these automotive airflow dynamics.
- Air/Fuel Distribution: Ensuring each cylinder receives an equal quantity and quality of the air-fuel mixture is vital for smooth operation, consistent power delivery, and engine longevity. Uneven distribution can lead to cylinders running too lean (risking detonation) or too rich (wasting fuel, reducing power), causing imbalances, vibrations, and potential engine damage. The complex internal geometries possible with 3D printing enable designs that promote symmetrical and homogenous mixture distribution, overcoming limitations often seen in cast or fabricated manifolds where core shifts or welding inconsistencies can compromise flow paths.
- Throttle Response: The volume of the intake manifold (specifically the plenum) and the length/diameter of the runners influence how quickly the engine responds to throttle inputs. Larger plenums can sometimes dampen throttle response, while optimized runner designs can enhance intake velocity at lower RPMs, improving immediacy. High-performance driving demands instantaneous response, and AM allows designers to fine-tune these volumes and shapes with incredible precision, balancing peak power requirements with sharp transient behaviour.
- Torque Curve Shaping: The length and diameter of the intake runners play a significant role in determining the engine’s torque characteristics. Longer, narrower runners generally favor low-to-mid-range torque production by utilizing intake pulse tuning (Helmholtz resonance) effectively at lower engine speeds. Conversely, shorter, wider runners typically benefit high-RPM horsepower by reducing flow restriction when the engine is demanding large volumes of air quickly. Variable-length intake runners (VLIM) are a complex mechanical solution to this compromise. However, 金属3Dプリンティング allows for the creation of fixed-geometry manifolds meticulously optimized through CFD simulation to achieve a specific desired torque curve shape – perhaps a broad, flat torque curve for driveability or a sharply rising curve for peak power in racing applications – without the mechanical complexity of VLIM systems.
- 熱管理: Intake air temperature significantly affects engine performance and detonation resistance. Cooler, denser air allows for more fuel to be burned, increasing power. Intake manifolds, especially in turbocharged or supercharged applications, can absorb significant heat from the engine block and cylinder heads. The choice of material (e.g., lower thermal conductivity alloys where appropriate) and the ability to design integrated heat shields or optimized airflow paths around the manifold using AM can help manage intake air temperatures (IATs). Certain designs might even explore integrating channels for liquid cooling within the manifold structure itself, a feat difficult to achieve with traditional methods.
Traditional Manufacturing Limitations:
- キャスティング: While cost-effective for high volumes, casting (sand casting, investment casting) limits the complexity of internal passages due to core requirements. Achieving thin walls consistently can be challenging, surface finishes are often rough requiring secondary machining, and porosity can be a concern. Runner lengths and plenum shapes are often compromises dictated by the casting process itself.
- CNC Machining: Machining from billet offers excellent precision and material properties but is incredibly wasteful (high buy-to-fly ratio) and time-consuming, making it very expensive, especially for complex shapes requiring multi-axis machining. Internal features are particularly difficult and costly to machine. Creating truly optimized, curved runner paths is often impractical.
- Fabrication (Welding): Fabricating manifolds by welding tubes and flanges allows for some customization but introduces potential failure points at welds, can create internal turbulence, and makes achieving perfectly consistent runner lengths and smooth transitions difficult. It’s often labor-intensive.
という文脈では high-performance vehicle tuning そして internal combustion engine parts optimization, the intake manifold is a prime candidate for innovation. Whether it’s for naturally aspirated engines seeking maximum VE, or forced induction setups needing robust construction and optimized flow under pressure, the design freedom offered by 3D printing provides a powerful tool. Engineers can leverage engine performance optimization techniques like CFD simulation to iterate through numerous virtual designs, testing different runner lengths, tapers, plenum volumes, and velocity stack integrations before committing to a physical print. This rapid iteration capability, combined with the ability to produce complex, organic shapes perfectly tailored to the airflow requirements, is why 金属積層造形 is becoming the go-to solution for teams and manufacturers seeking the ultimate edge in engine performance. The quest for higher specific outputs, broader powerbands, and sharper responses in everything from race cars to hypercars and specialized aftermarket builds drives the adoption of technologies that overcome the inherent limitations of older manufacturing paradigms.
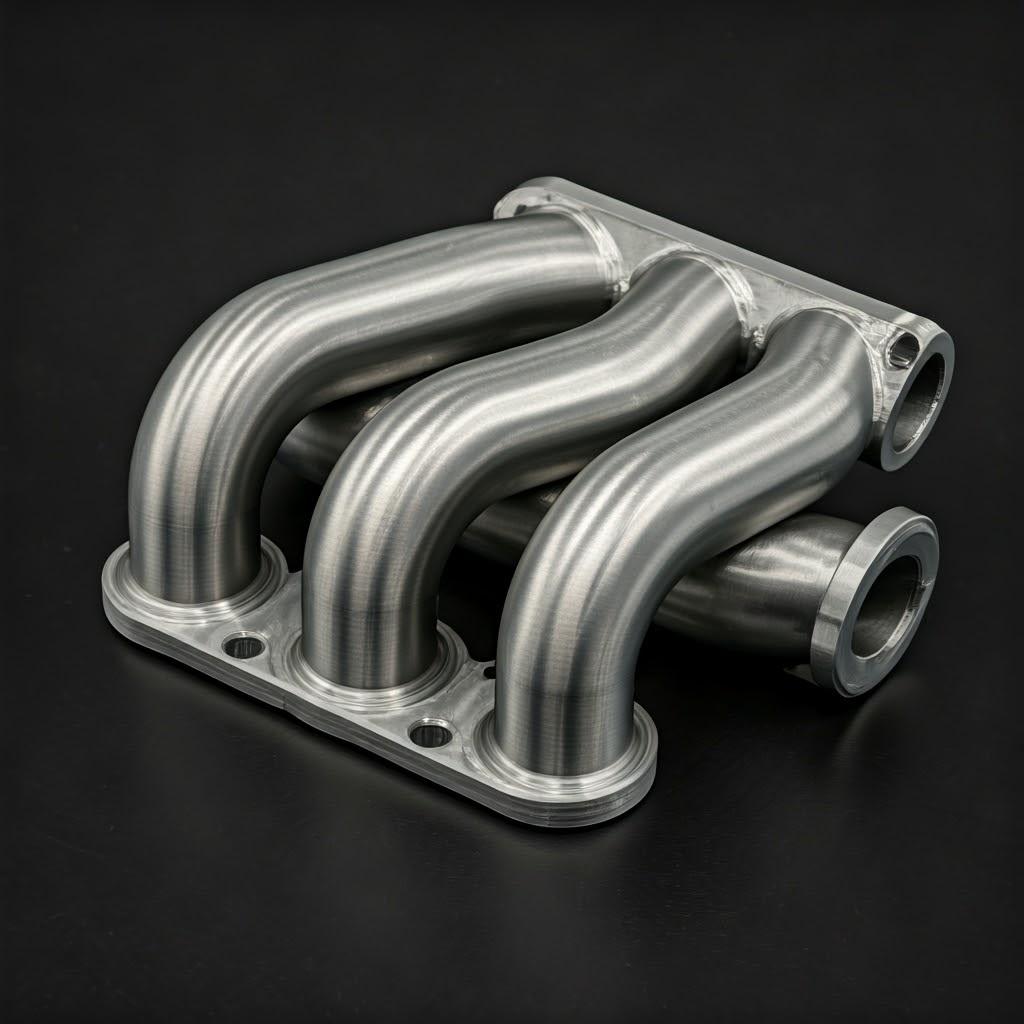
Why Metal Additive Manufacturing for Intake Manifolds? Advantages Over Traditional Methods
The transition towards 金属積層造形(AM) for producing intake manifolds, particularly in the high-performance automotive sector, is driven by a compelling set of advantages that directly address the limitations of traditional methods like casting, CNC machining, and fabrication. These benefits extend beyond mere novelty, offering tangible improvements in performance, design flexibility, weight, and development speed. For automotive procurement specialists and engineers evaluating manufacturing options, understanding these metal AM benefits automotive applications is crucial.
Key Advantages of Metal AM for Intake Manifolds:
- Unparalleled Design Freedom & Complexity: This is arguably the most significant advantage. AM builds parts layer by layer directly from a 3D CAD model, freeing designers from the constraints imposed by molds, cores, or cutting tool access.
- Optimized Airflow: Designers can create incredibly complex internal geometries, including smoothly curving runners, precisely calculated tapers, optimized plenum shapes, and integrated velocity stacks, all tailored through CFD analysis for maximum volumetric efficiency and balanced cylinder distribution. This level of complex geometry manufacturing is simply unattainable or prohibitively expensive with conventional methods.
- Topology Optimization: Software can be used to remove material from non-critical areas while maintaining structural integrity, resulting in organic-looking, highly efficient structures that minimize weight while meeting all functional requirements.
- パーツの統合: Features like sensor bosses, vacuum ports, fuel rail mounts, and bracketry can be integrated directly into the manifold design, reducing part count, assembly time, potential leak points, and overall system weight.
- 軽量化: High-performance vehicles constantly strive for weight reduction. Metal AM excels here:
- 材料効率: Unlike subtractive manufacturing (CNC machining), AM uses material only where needed, significantly reducing waste.
- Optimized Structures: As mentioned above, topology optimization allows for significant weight savings compared to bulky cast or machined parts, without compromising strength. Using inherently lighter alloys like Aluminum Silicon Magnesium (AlSi10Mg) further enhances this benefit. Even when using denser materials like IN625 for high-temperature applications, the ability to create thin-walled, optimized structures keeps weight lower than comparable traditionally manufactured parts. Lightweighting automotive components is a key driver for AM adoption.
- Rapid Prototyping & Iteration: The speed from digital design to physical part is drastically reduced.
- Faster Development Cycles: Engineers can design, print, test, and revise manifold designs in days or weeks, rather than the months often required for casting tooling or complex CNC programming. This accelerates development and allows for more performance refinement before final production.
- Customization & Low Volumes: AM is ideal for producing bespoke manifolds for specific engine builds, racing series with unique regulations, or limited-production performance vehicles. The cost per part is less dependent on volume compared to tooling-intensive methods like casting.
- Material Variety & Performance: Metal AM offers access to a growing range of high-performance alloys suitable for demanding intake manifold applications.
- 先進合金: Materials like AlSi10Mg (lightweight, good thermal conductivity) and IN625 (excellent high-temperature strength and corrosion resistance, ideal for extreme boost or exhaust-gas-adjacent components) can be readily processed. Companies like Met3dp specialize in producing high-quality powders, including innovative alloys, optimized for AM processes.
- Consistent Properties: When processed correctly using quality-controlled equipment and powders (like those from trusted 金属粉サプライヤー), AM parts can achieve mechanical properties comparable or even superior to cast equivalents, with excellent density and integrity.
- Improved Performance Potential: The culmination of design freedom, lightweighting, and material options directly translates to potential performance gains.
- Enhanced VE & Power: Optimized airflow paths lead to better cylinder filling and potentially higher horsepower and torque.
- Improved Throttle Response: Fine-tuned plenum volumes and runner designs contribute to quicker engine response.
- 熱安定性: Material choice and design features can help manage intake air temperatures more effectively, especially crucial in forced induction setups.
Comparison Table: Metal AM vs. Traditional Methods for Intake Manifolds
特徴 | 金属積層造形(AM) | キャスティング | CNC Machining (Billet) | Fabrication (Welding) |
---|---|---|---|---|
デザインの複雑さ | Very High (Complex internal/external geometries) | Moderate (Limited by cores/molds) | Moderate (Limited by tool access) | Low-Moderate (Geometric limitations) |
軽量化 | Excellent (Topology optimization, thin walls) | Fair (Can be bulky, wall thickness limits) | Good (But high material waste) | Fair (Depends on design/material) |
Prototyping Speed | Very Fast | Slow (Tooling required) | Slow-Moderate (Programming/setup time) | 中程度 |
Low Volume Cost | Moderate-High (No tooling cost amortization) | Very High (Tooling cost dominates) | Very High (Material waste, machine time) | High (Labor intensive) |
High Volume Cost | High (Slower build rates per part) | Low (Tooling amortized) | 非常に高い | 高い |
廃棄物 | 非常に低い | Low-Moderate (Gates, risers) | Very High (Buy-to-fly ratio) | 低い |
部品の統合 | 素晴らしい | 限定 | 限定 | 貧しい |
Internal Surface Finish | Fair-Good (Requires post-processing) | Poor-Fair (Requires post-processing) | Excellent (Where accessible) | Fair (Weld beads impact flow) |
代表的な素材 | Al Alloys, Ti Alloys, Ni Superalloys, Steels | Al Alloys, Cast Iron, Magnesium Alloys | Al Alloys, Ti Alloys, Steels | Al Alloys, Steels, Ti Alloys |
Export to Sheets
一方 casting limitations intake manifold design and the cost/waste of CNC machining vs 3D printing are significant drawbacks, AM isn’t without its considerations. Initial equipment investment can be high (though service bureaus mitigate this), build speeds for single parts can be slower than mass production casting, and post-processing is often required to achieve final tolerances and surface finishes. However, for the target application – high-performance vehicles where performance optimization, customization, and speed-to-market are paramount – the advantages offered by metal AM often outweigh these factors. Partnering with an experienced service provider like メット3dp, which possesses not only advanced printing technology but also deep materials science expertise, ensures that these benefits are fully realized, delivering intake manifolds that push the boundaries of engine performance. The ability to rapidly translate CFD-optimized designs into functional hardware makes metal AM a transformative force in the development and production of critical performance vehicle components.
Material Selection for Peak Performance: AlSi10Mg and IN625 Intake Manifolds
Choosing the right material is fundamental to the success of any engineering project, and 3D printed intake manifolds are no exception. The operating environment of an intake manifold – involving airflow dynamics, connection to a vibrating engine, exposure to fuel vapors (in port injection), and significant temperature fluctuations (especially in boosted applications or proximity to hot engine components) – dictates specific material property requirements. Metal additive manufacturing offers a versatile palette of materials, but for high-performance automotive intake manifolds, two alloys frequently stand out: AlSi10Mg そして IN625 (Inconel 625). Understanding their respective properties and application suitability is key for engineers and procurement managers sourcing these components.
AlSi10Mg: The Lightweight Champion
AlSi10Mg is an aluminum alloy containing silicon and magnesium, widely used in both traditional casting and additive manufacturing. It’s often considered the workhorse aluminum alloy for powder bed fusion processes like SLM and DMLS.
- キー・プロパティ
- 密度が低い: (~2.67 g/cm³) This is its primary advantage, contributing significantly to vehicle lightweighting efforts. Reducing mass, especially high up in the engine bay, improves handling dynamics.
- 優れた強度対重量比: Offers respectable mechanical strength and stiffness, especially after appropriate heat treatment, making it suitable for the structural demands of an intake manifold.
- 優れた熱伝導性: Helps dissipate heat, which can be advantageous in keeping intake air temperatures lower, although this can be a double-edged sword if absorbing too much heat from the engine block. Design considerations can mitigate unwanted heat transfer.
- 良好な耐食性: Generally resistant to atmospheric corrosion and automotive fluids.
- 溶接性: Can be welded if necessary for repairs or modifications, though less common with AM parts.
- 加工性: It is one of the most common and well-understood alloys for laser powder bed fusion, making it widely available from 3D printing materials suppliers and service providers.
- Applications for Intake Manifolds:
- Naturally aspirated engines.
- Moderately boosted applications (turbocharged or supercharged) where peak temperatures remain within the alloy’s operating range.
- Applications where minimizing weight is the absolute top priority (e.g., motorsport).
- Rapid prototyping and design validation due to its cost-effectiveness relative to superalloys.
- 検討する:
- Temperature Limitation: AlSi10Mg loses significant strength at elevated temperatures (typically above 150-200°C or 300-390°F), making it unsuitable for extremely high-boost applications or locations experiencing excessive heat soak from exhaust components or the engine block without careful thermal management design.
- 延性: Can be less ductile than some other aluminum alloys or steels, requiring careful design to avoid stress concentrations.
IN625 (Inconel 625): The High-Temperature Heavyweight
IN625 is a nickel-chromium-molybdenum-niobium superalloy renowned for its exceptional performance in extreme environments. While significantly denser and more expensive than aluminum alloys, its properties are essential when conditions exceed the capabilities of AlSi10Mg.
- キー・プロパティ
- Outstanding High-Temperature Strength: Maintains excellent mechanical properties (tensile strength, creep resistance, fatigue life) at very high temperatures (up to 800-900°C or 1470-1650°F and beyond for short durations).
- Excellent Corrosion and Oxidation Resistance: Highly resistant to a wide range of corrosive environments, including combustion byproducts and high-temperature oxidation.
- High Fatigue Strength: Crucial for components subjected to engine vibrations and pressure cycles.
- Good Weldability (Relative to other superalloys): Can be processed effectively using AM technologies like SLM and EBM.
- Applications for Intake Manifolds:
- Extreme Forced Induction: High-pressure turbocharging or supercharging systems where intake air temperatures and manifold surface temperatures can become significantly elevated due to heat soak and compressed air heat.
- Integrated Exhaust Gas Recirculation (EGR) Components: If EGR passages are integrated into the manifold design, IN625 can withstand the high temperatures of exhaust gases.
- Proximity to Hot Components: Situations where the manifold is very close to exhaust manifolds or turbochargers, leading to high radiant and conductive heat transfer.
- Maximum Durability Requirements: Applications demanding the utmost reliability and longevity under severe operating conditions (e.g., endurance racing).
- 検討する:
- 高密度: (~8.44 g/cm³) Significantly heavier than aluminum, impacting lightweighting goals. The design freedom of AM can help mitigate this by optimizing geometry, but it will inherently be heavier than an equivalent AlSi10Mg part.
- より高いコスト: Both the raw powder and the printing process are considerably more expensive than for aluminum alloys.
- Lower Thermal Conductivity: Compared to aluminum, IN625 conducts heat less readily. This can be beneficial in insulating intake air from engine heat but might require consideration for heat dissipation if the manifold itself gets excessively hot.
- 処理の課題: Requires higher energy input and careful parameter control during the AM process.
Material Selection Guide: Key Factors
ファクター | Priority Favors AlSi10Mg | Priority Favors IN625 | 考察 |
---|---|---|---|
動作温度 | Lower (< 150-200°C / 300-390°F) | Higher (> 200°C / 390°F) | Accurately predict peak temperatures via simulation or testing. |
軽量化 | Highest Priority | Lower Priority (Strength/Temp is key) | AM design optimization helps minimize weight penalty for IN625. |
予算 | Lower Budget | Higher Budget Available | Factor in powder cost, print time, and post-processing complexity. |
Boost Level / Pressure | Naturally Aspirated / Moderate Boost | High / Extreme Boost | Higher pressures often correlate with higher temperatures and stress. |
Proximity to Heat Sources | More distant from exhaust/turbo | Very close proximity | Thermal shielding or coatings might be needed regardless of material. |
Corrosion Concerns | Standard Automotive Environment | Aggressive Chemical Exposure / EGR | Both offer good resistance, but IN625 is superior in extreme conditions. |
生産量 | Prototyping / Lower Volume / Cost-Sensitive | Performance-Critical / Lower Volume | Cost difference becomes more significant at scale (though AM is often low vol). |
Export to Sheets
The Met3dp Advantage:
Choosing the right material is only part of the equation. The quality of the metal powder itself is paramount for achieving dense, defect-free parts with predictable mechanical properties. Companies like メット3dp play a crucial role as high-quality metal powder suppliers. Met3dp utilizes advanced powder production techniques, such as industry-leading gas atomization and Plasma Rotating Electrode Process (PREP) technologies, to manufacture metallic powders like AlSi10Mg and IN625 with:
- 高い真球度: Ensures good powder flowability and dense packing in the powder bed, critical for print quality.
- Controlled Particle Size Distribution (PSD): Optimized PSD leads to better melting characteristics and finer feature resolution.
- Low Impurity Levels: High purity materials result in superior mechanical properties and consistency.
- Batch-to-Batch Consistency: Essential for reliable and repeatable manufacturing processes.
By sourcing high-performance powders like AlSi10Mg そして IN625 from reputable manufacturers such as Met3dp, engineers and procurement managers can have greater confidence in the final integrity and performance of their 3D printed intake manifolds. Met3dp’s expertise extends beyond just supplying powder; their understanding of the interaction between materials and metal AM processes ensures that customers receive powders optimized for specific printing technologies like SLM, DMLS, or their own specialized Selective Electron Beam Melting (SEBM) systems, further enhancing the quality and reliability of these critical 高性能部品. Consulting with material experts and AM service providers early in the design phase is crucial for making the optimal material selection based on the specific performance requirements, operating conditions, and budget constraints of the project. Sources and related content
Design for Additive Manufacturing (DfAM): Optimizing Intake Manifolds for 3D Printing
Simply taking a CAD model designed for casting or machining and sending it to a metal 3D printer rarely yields optimal results. To truly unlock the potential of additive manufacturing for components like high-performance intake manifolds, designers must embrace 積層造形設計 (DfAM) principles. DfAM isn’t just about ensuring a part できる be printed; it’s about leveraging the unique capabilities and understanding the constraints of the AM process to create parts that are lighter, stronger, perform better, and are more cost-effective to produce. For intake manifolds, this means focusing on fluid dynamics, structural integrity, thermal management, and printability simultaneously. Implementing DfAM principles automotive applications like this requires a shift in thinking.
Key DfAM Considerations for Intake Manifolds:
- Optimize for Flow AND Printability: The primary function is airflow. CFD simulation is invaluable for optimizing runner lengths, diameters, tapers, plenum volume, and bellmouth entries for target VE and distribution. However, these ideal flow paths must be manufacturable.
- Self-Supporting Angles: Design internal channels and runner curves with overhang angles typically greater than 45 degrees from the horizontal plane (relative to the build direction) to minimize the need for internal support structures, which are difficult and costly to remove. Where supports は necessary inside runners, design them for easy removal or consider processes like abrasive flow machining for finishing.
- Smooth Transitions: Avoid sharp corners or abrupt changes in cross-section within flow paths, as these create turbulence and can be difficult to print accurately. Use generous fillets and smooth splines.
- Internal Features: Consider how internal features like flow straighteners or dividers will be built and supported. Sometimes, splitting the manifold into sections that are printed separately and then joined (e.g., via welding or bolting) can be more practical for complex internal geometries, although this adds assembly steps.
- Leverage Topology Optimization and Generative Design: These computational tools are revolutionary for lightweighting and performance enhancement.
- Structural Optimization: Apply topology optimization to the plenum body, mounting flanges, and any integrated brackets. The software identifies areas where material is not contributing significantly to stiffness or strength under defined load cases (engine vibration, mounting forces, boost pressure) and removes it, leaving an organic, load-path-optimized structure. This can yield significant weight savings for the manifold structure itself.
- Flow Path Guidance: While topology optimization is primarily structural, generative design tools can sometimes assist in finding novel, efficient flow path routing within defined boundary conditions, working synergistically with CFD.
- 格子構造: Consider infilling thicker sections of the plenum or mounting areas with internal lattice structures. These can provide excellent stiffness and strength at a fraction of the weight of solid material, while also potentially aiding in vibration damping.
- Minimize Support Structures: Support structures are often necessary in metal AM (especially PBF processes) to anchor the part to the build plate, support overhanging features, and manage thermal stress. However, they add material cost, build time, and significant post-processing effort for removal.
- Build Orientation: Carefully select the build orientation to minimize overhangs and the total volume of required supports. Orienting large flat surfaces (like plenum tops) horizontally can increase warping risk, so often a slight angle is preferred. Orienting cylindrical runners vertically often minimizes internal supports but may increase build height and time. There’s always a trade-off.
- Design Modifications: Slightly modify angles, add sacrificial ribs or fillets (chamfers) to make features self-supporting. Redesign sharp overhangs into conical or teardrop shapes where functionally acceptable.
- Support Optimization: Use specialized software to generate optimized support structures (e.g., tree supports, block supports with perforation) that are strong enough during the build but easier to remove afterwards. Ensure adequate access for support removal tools, especially around flanges and ports. Planning support structure design metal AM が重要だ。
- Wall Thickness and Feature Size: AM processes have limitations on minimum wall thickness and feature resolution.
- Minimum Wall Thickness: Typically around 0.4-1.0 mm, depending on the material, machine, and geometry. Ensure walls are thick enough to withstand operating pressures (especially under boost) and vibration, and for handling during post-processing. Thicker walls may be needed near flanges for sealing. Consult your AM service provider, like Met3dp, for specific wall thickness guidelines 3D printing based on their equipment and chosen material.
- Hole Sizes: Small holes (e.g., for vacuum lines or sensors) may need to be drilled or reamed after printing for accuracy, as small as-printed holes can be slightly irregular or undersized. Design them slightly undersized for subsequent machining or allow for sufficient stock.
- Feature Resolution: Fine details like logos or surface textures can be incorporated but are limited by the laser/electron beam spot size and powder particle size.
- Part Consolidation Strategy: Identify opportunities to integrate adjacent components or features.
- Bracketry: Integrate mounting brackets for sensors, actuators, or cable routing directly into the manifold body.
- Fluid Ports: Design threaded or O-ring sealing ports for sensors, vacuum lines, or fuel injectors directly into the print, potentially eliminating separate fittings. Ensure sufficient material is designed around ports for sealing and strength.
- Flange Design: Optimize flange designs for sealing (consider adding grooves for O-rings) and bolt access, ensuring adequate clearance for tools during assembly.
- Thermal Management Considerations:
- Heat Dissipation/Insulation: Depending on the goal (keep air cool vs. withstand high heat), use thin walls and fins (AlSi10Mg) to dissipate heat or leverage topology optimization for minimal contact area and potentially lower conductivity materials like IN625 where insulation is key.
- Warping Prevention: Large, flat sections (like plenum surfaces) are prone to warping due to thermal stresses during the build. Consider adding temporary stiffening ribs (removed later) or using build strategies that minimize stress accumulation. Careful orientation is key.
DfAM Workflow for Intake Manifolds:
- Define Requirements: Clearly outline performance targets (flow rate, pressure handling, temperature range), weight targets, mounting points, interfaces, and cost constraints.
- Initial Design & Simulation: Create an initial CAD model based on traditional design principles or intuition. Perform CFD analysis to evaluate airflow characteristics (fluid dynamics simulation CFD).
- Topology Optimization (Optional but Recommended): Apply topology optimization to structural elements based on simulated or expected loads (pressure, vibration).
- DfAM Refinement: Modify the geometry based on DfAM principles (self-supporting angles, support minimization, wall thickness, feature integration). Iterate with CFD to ensure performance isn’t compromised.
- Build Simulation (Recommended): Use specialized software to simulate the AM build process, predicting potential stress concentrations, warping, and support needs. Refine orientation and supports based on simulation results.
- Final Design & Pre-processing: Finalize the CAD model and prepare the build file (STL or other format), including optimized orientation and support structures.
By proactively incorporating these DfAM strategies, engineers can move beyond simply replicating existing manifold designs and start creating truly optimized components that fully exploit the transformative capabilities of metal additive manufacturing. Partnering with an experienced AM provider like Met3dp, who understands the nuances of 印刷方法 and materials, during the design phase can provide invaluable feedback and ensure a successful outcome.
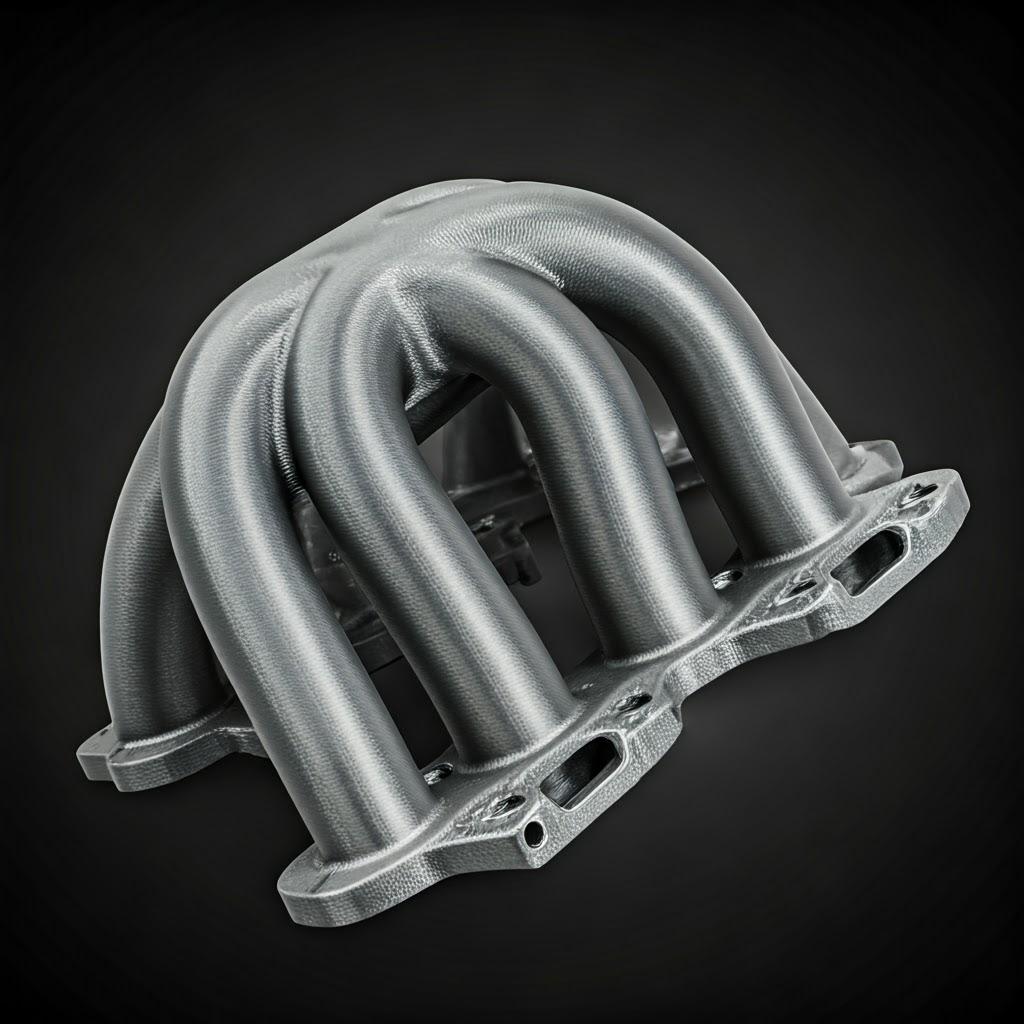
Achieving Precision: Tolerances, Surface Finish, and Dimensional Accuracy in 3D Printed Manifolds
While metal additive manufacturing offers incredible design freedom, it’s crucial for engineers and procurement managers to understand the levels of precision achievable in terms of dimensional tolerances, surface finish, and overall accuracy. Unlike the highly controlled environment of multi-axis CNC machining, AM involves complex thermal processes that can influence the final geometry and surface characteristics of the printed part. However, with proper process control, high-quality materials, and often post-processing, 3D printed intake manifolds can meet the demanding requirements of high-performance automotive applications.
Dimensional Tolerances:
Dimensional tolerance refers to the permissible variation in the size of a part feature. In metal AM, particularly Powder Bed Fusion (PBF) processes like SLM, DMLS, and EBM, typical ‘as-built’ tolerances are often in the range of:
- General Tolerances: ±0.1 mm to ±0.3 mm (±0.004″ to ±0.012″) for smaller features (e.g., up to 50-100 mm).
- Larger Features: Tolerance might increase proportionally with size, potentially ±0.2% of the nominal dimension for larger parts due to accumulated thermal effects.
Factors Influencing Dimensional Accuracy:
- Thermal Stress & Warpage: The repeated heating and cooling cycles inherent in AM can cause internal stresses, leading to distortion or warpage, especially in large or complex geometries like intake manifolds with large flat plenum sections or long runners. Careful orientation, robust support structures, and post-build stress relief are crucial for mitigation.
- Machine Calibration: The accuracy of the laser or electron beam positioning system, scanner calibration, and layer thickness control directly impacts part accuracy. Well-maintained, high-quality machines are essential.
- パウダーの質: Consistent particle size distribution and morphology of the metal powder (like the high-quality AlSi10Mg and IN625 powders produced by Met3dp using advanced atomization techniques) contribute to predictable melting behaviour and dimensional stability.
- Process Parameters: Laser/electron beam power, scan speed, hatch spacing, and layer thickness must be meticulously optimized for the specific material and geometry to ensure accurate melting and solidification.
- Shrinkage: Metals shrink upon cooling and solidification. This shrinkage is compensated for in the build preparation software, but variations can still occur.
- Support Structure Interaction: The way supports connect to the part and how they are removed can slightly affect the dimensions of the surfaces they touched.
Achieving Tighter Tolerances:
For critical interfaces like engine head flanges, throttle body mounts, sensor ports, and injector bores, the as-built tolerances of AM may not be sufficient. In these cases:
- Machining Allowances: Design the part with extra material (e.g., 0.5 mm to 1.5 mm) specifically on these critical surfaces.
- Post-Process CNC Machining: After printing and stress relief, use CNC machining to achieve final tolerances, often reaching ±0.025 mm (±0.001″) or better, comparable to fully machined parts. This hybrid approach combines the geometric freedom of AM with the precision of subtractive manufacturing for critical interfaces.
Surface Finish (Roughness):
Surface finish, typically measured as Ra (average roughness), is another key characteristic. As-built metal AM parts generally have a rougher surface compared to machined parts due to the layer-by-layer process and partially melted powder particles adhering to the surface.
- Typical As-Built Ra:
- Top Surfaces: Often smoother, potentially Ra 5-10 µm (200-400 µin).
- Vertical Walls: Ra 8-15 µm (315-590 µin) is common, showing layer lines.
- Down-facing/Supported Surfaces: Tend to be the roughest, potentially Ra 15-25 µm (590-980 µin) or higher, depending on support type and removal method. Internal channels relying on supports will be particularly rough.
- EBM vs. Laser PBF: Electron Beam Melting (EBM) typically produces rougher surfaces than laser-based systems (SLM/DMLS) due to higher energy input and different powder characteristics but can sometimes manage internal stresses better.
Impact on Intake Manifolds:
- Internal Surfaces: Rough internal surfaces within the runners and plenum can increase friction losses and slightly disrupt airflow compared to a perfectly smooth passage. While the impact might be minor in some cases, optimizing for smoothness is desirable for peak performance.
- Sealing Surfaces: As-built surfaces are generally unsuitable for critical sealing flanges. Machining or specialized post-processing is required.
表面仕上げの改善:
Various post-processing techniques can significantly improve the surface finish of 3D printed manifolds:
- CNC Machining: Provides the best finish on accessible surfaces.
- Abrasive Blasting (Bead Blasting, Sand Blasting): Creates a uniform matte finish, removing loose powder and slightly smoothing surfaces (Ra 5-10 µm achievable).
- Tumbling/Vibratory Finishing: Uses abrasive media in a tumbling barrel or vibratory bowl to smooth external surfaces and break sharp edges. Effective for batches of smaller parts or rugged designs.
- Abrasive Flow Machining (AFM): Forces an abrasive putty through internal channels under pressure. Excellent for smoothing internal runners and passages that are inaccessible by other means.
- Electropolishing: An electrochemical process that removes a thin layer of material, resulting in a very smooth, bright finish. More common for specific alloys like stainless steels or certain superalloys.
- Manual Polishing: Labor-intensive but can achieve mirror finishes where required for aesthetics or specific flow requirements.
Quality Control and Inspection:
Ensuring the final intake manifold meets specifications requires robust quality control additive manufacturing protocols:
- 寸法検査: Coordinate Measuring Machines (CMMs) for high-accuracy point measurements on critical features. 3D laser scanning provides a comprehensive comparison of the entire part geometry against the original CAD model, creating deviation maps.
- Surface Finish Measurement: Profilometers are used to quantify surface roughness (Ra).
- 非破壊検査(NDT): Techniques like CT scanning (Computed Tomography) can inspect internal geometries, detect voids or porosity, and verify internal channel integrity without damaging the part. Dye penetrant testing or magnetic particle inspection can check for surface cracks.
- Pressure Testing: Essential for intake manifolds, especially boosted applications, to verify integrity and check for leaks at operating pressures.
Supplier Role:
Achieving consistent precision relies heavily on the capabilities and quality systems of the metal AM service bureau. Providers like Met3dp, with their focus on industry-leading print volume, accuracy and reliability, invest in high-end equipment, rigorous calibration schedules, optimized process parameters developed through extensive R&D, and robust quality management systems (often certified to standards like ISO 9001 or AS9100 for aerospace). When evaluating potential suppliers, inquiring about their dimensional accuracy standards automotive parts, typical achievable tolerances, surface finish capabilities, and available inspection methods is crucial for procurement teams. Clear communication of critical dimensions and required tolerances on engineering drawings is essential for ensuring the final part meets expectations.
Beyond the Print: Essential Post-Processing for 3D Printed Intake Manifolds
The journey of a 3D printed metal intake manifold doesn’t end when the printer stops. The ‘green’ part, fresh off the build plate, requires several crucial post-processing metal AM steps to transform it into a functional, reliable, high-performance component. These steps are not optional extras; they are integral to achieving the desired mechanical properties, dimensional accuracy, surface finish, and overall quality. Understanding these requirements is vital for planning production timelines and costs associated with additive manufacturing procurement.
Common Post-Processing Steps for Metal AM Intake Manifolds:
- Powder Removal (De-Powdering):
- プロセス Immediately after the build finishes and the chamber cools, the build job (part attached to the build plate, surrounded by unfused powder) is removed. Excess powder is carefully recovered, often through manual brushing, vacuuming, or automated sieving stations for recycling. Internal channels within the manifold require particular attention to ensure all loose powder is removed, sometimes involving vibration or compressed air.
- Importance: Residual powder, especially in internal passages, can restrict airflow, contaminate engine internals, or interfere with subsequent processes. Thorough de-powdering is critical.
- Stress Relief Heat Treatment:
- プロセス This is typically the first step after de-powdering, often performed while the part is still attached to the build plate. The part/plate assembly is heated in a furnace to a specific temperature below the material’s critical transformation point, held for a period, and then slowly cooled. Parameters (temperature, time, atmosphere) are material-specific (e.g., heat treatment AlSi10Mg differs significantly from IN625).
- Importance: The rapid heating/cooling cycles during printing induce significant internal stresses. Stress relief reduces these stresses, preventing distortion or cracking during support removal or machining, and improving dimensional stability and mechanical properties (especially fatigue life). It is absolutely essential for reliable parts.
- Part Removal from Build Plate:
- プロセス Once stress-relieved, the intake manifold is separated from the build plate. This is commonly done using wire EDM (Electrical Discharge Machining) or a bandsaw. Care must be taken to avoid damaging the part.
- Importance: Frees the part for subsequent handling and processing. The base surface where it was attached will require finishing.
- 支持構造の撤去:
- プロセス The support structures, designed to anchor the part and support overhangs during printing, must now be removed. This can be done manually using pliers, cutters, grinders, or CNC machining. Access can be challenging, especially for internal supports within runners or complex plenum geometries. Support removal techniques require skill and care to avoid damaging the part surface.
- Importance: Supports are non-functional and obstruct airflow or assembly. Their complete removal is necessary. Marks or ‘witness lines’ left by supports often require further finishing.
- CNC Machining (for Critical Features):
- プロセス As discussed previously, critical interfaces like head flanges, throttle body mounts, sensor ports, and injector bores are often CNC machined to achieve tight tolerances and specific surface finishes required for sealing and precise alignment. This involves setting up the AM part on a milling machine or lathe.
- Importance: Guarantees dimensional accuracy and proper sealing/mating with other engine components. CNC finishing 3D prints is standard practice for high-precision applications.
- Surface Finishing / Smoothing:
- プロセス Depending on requirements, various methods are used to improve the as-built surface finish:
- Bead Blasting: Provides a uniform matte finish, cleans surfaces.
- Tumbling/Vibratory Finishing: Smooths external surfaces and edges.
- Abrasive Flow Machining (AFM): Ideal for smoothing internal runners to improve airflow characteristics.
- Manual Grinding/Polishing: For specific aesthetic requirements or targeted smoothing.
- Electropolishing: For compatible alloys, achieves very smooth, clean surfaces.
- Importance: Improves aesthetics, can enhance airflow (smoother internal passages), removes surface imperfections, and prepares surfaces for coatings if needed. Surface polishing metal parts can be crucial for performance.
- プロセス Depending on requirements, various methods are used to improve the as-built surface finish:
- Further Heat Treatments (Optional):
- プロセス Depending on the material (especially AlSi10Mg) and desired properties, additional heat treatments like solution treatment and aging (e.g., T6 condition for aluminum) may be performed その後 stress relief and potentially machining. These treatments significantly enhance strength and hardness but can sometimes cause slight dimensional changes that need to be accounted for. IN625 typically requires specific solution annealing or aging treatments to optimize its properties for high-temperature service.
- Importance: Tailors the final mechanical properties (strength, hardness, ductility) to meet the specific demands of the application.
- Cleaning and Inspection:
- プロセス Thorough cleaning to remove any machining fluids, abrasive media, or debris. Final inspection includes dimensional checks (CMM, scanning), surface finish verification, visual inspection, and potentially NDT (CT scanning, pressure testing) as per the quality plan.
- Importance: Ensures the final part is clean, meets all specifications, and is free from critical defects before delivery or assembly.
- Coating or Surface Treatments (Optional):
- プロセス Application of specialized coatings:
- Thermal Barrier Coatings (TBCs): Ceramic coatings applied (often via plasma spray) to exterior or interior surfaces to reduce heat transfer – useful for keeping intake air cool or protecting the manifold material from extreme heat.
- Anodizing (for Aluminum): Improves corrosion resistance and surface hardness, allows for coloring.
- Powder Coating/Painting: For aesthetics and basic environmental protection.
- Dry Film Lubricants: Applied internally to potentially improve airflow.
- Importance: Enhances performance (thermal management), durability (corrosion/wear resistance), or aesthetics. Coating options automotive components should be considered based on the operating environment.
- プロセス Application of specialized coatings:
Planning for Post-Processing:
It’s crucial to factor post-processing into the initial design, budget, and lead time calculations. Complex internal supports that are impossible to remove, or designs requiring extensive manual polishing, will significantly increase costs and delays. Collaborating with an experienced AM service provider like Met3dp, who can offer guidance on DfAM for minimizing post-processing effort and has in-house or established partnerships for performing these necessary steps efficiently, is highly beneficial. Their comprehensive solutions, spanning from advanced powders and SEBM プリンター to application development services, encompass an understanding of the entire workflow, including these critical finishing stages. Failure to properly plan and execute post-processing can negate the benefits gained from using AM in the first place, resulting in a component that fails to meet performance or reliability standards.
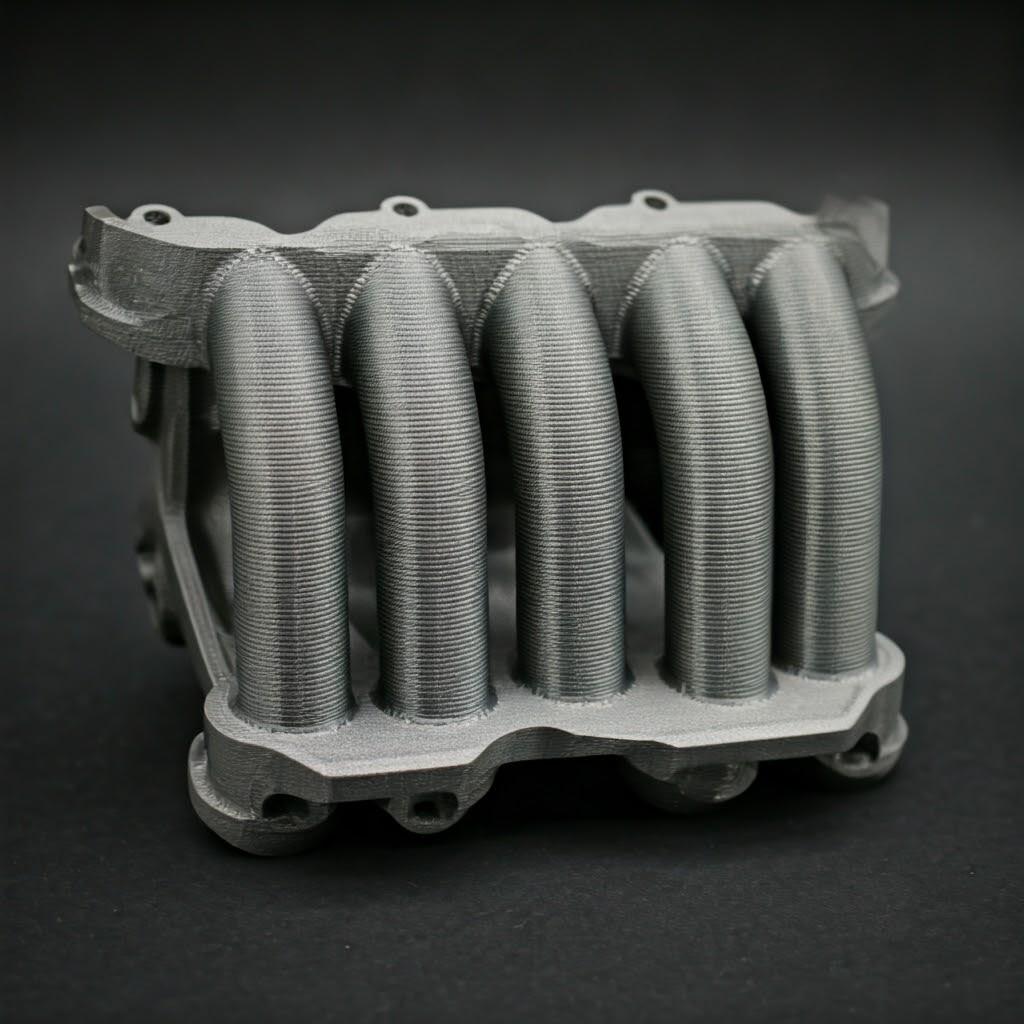
Navigating Challenges in Metal AM for Intake Manifolds: Solutions and Best Practices
While metal additive manufacturing offers tremendous advantages for producing high-performance intake manifolds, the technology is not without its challenges. Understanding potential metal 3D printing defects, process difficulties, and quality control hurdles is essential for both designers and procurement teams engaging with metal AM service bureaus. Proactive planning, robust process control, and adherence to best practices are key to mitigating these issues and ensuring the delivery of high-quality, reliable components.
Common Challenges and Mitigation Strategies:
- Warping and Distortion:
- チャレンジ: Significant temperature gradients during the PBF process create internal stresses that can cause the part, especially large flat sections like plenum surfaces or long runners, to warp or distort during the build or after removal from the build plate. This is a major concern for maintaining flange flatness and overall dimensional accuracy.
- Solutions & Best Practices:
- Optimized Build Orientation: Avoid orienting large flat surfaces parallel to the build plate. A slight tilt can help.
- Robust Support Structures: Use well-designed supports, particularly near edges and corners of large features, to anchor the part firmly and counteract thermal stresses. Consider thermal supports designed specifically to conduct heat away.
- Build Plate Heating: Pre-heating the build plate (common in EBM, increasingly used in laser PBF) reduces thermal gradients between the part and the plate, lowering stress.
- プロセスパラメータの最適化 Fine-tuning laser/beam power, scan speed, and scan strategy (e.g., island scanning, chessboard patterns) can minimize localized heat buildup and residual stress.
- Stress Relief Heat Treatment: Performing stress relief before removing the part from the build plate is critical for stabilizing the geometry.
- Design Modifications: Introduce slight crowns to large flat surfaces or add temporary stiffening ribs (removed post-print) to resist warping.
- 多孔性:
- チャレンジ: Small voids or pores within the printed material can compromise its structural integrity, fatigue life, and pressure-holding capability. Porosity can arise from trapped gas (gas porosity) or incomplete melting/fusion between layers or scan tracks (lack of fusion porosity).
- Solutions & Best Practices:
- High-Quality Powder: Use spherical, dry, high-purity metal powders with optimized particle size distribution (like those from Met3dp). Poor quality or contaminated powder is a common source of gas porosity. Proper powder handling and storage are essential.
- Optimized Process Parameters: Ensure sufficient energy density (power/speed ratio) to fully melt the material. Incorrect parameters are the primary cause of lack of fusion. Extensive parameter development for each material/machine combination is crucial.
- Shielding Gas Atmosphere: Maintain a high-purity inert gas atmosphere (Argon or Nitrogen) in the build chamber to prevent oxidation and displace process byproducts that could cause gas porosity. Monitor oxygen levels.
- 熱間静水圧プレス(HIP): A post-processing step involving high temperature and high pressure inert gas. HIP can effectively close internal pores (both gas and lack of fusion), significantly improving density and mechanical properties. It adds cost but may be necessary for critical applications.
- NDT Inspection: Use CT scanning to detect internal porosity levels and ensure they are within acceptable limits based on application requirements.
- Cracking (Solidification/Liquation Cracking):
- チャレンジ: Cracks can form during solidification or in the heat-affected zone due to thermal stresses, particularly in alloys with a wide solidification range or those susceptible to segregation (like some aluminum alloys if not processed correctly).
- Solutions & Best Practices:
- 素材の選択: Choose alloys known for good printability or understand the specific challenges associated with chosen alloys (e.g., certain high-strength aluminum alloys are more prone to cracking).
- プロセスパラメータの最適化 Control cooling rates through scan strategy and parameter adjustments.
- Build Plate Heating: Reduces thermal gradients, lowering cracking susceptibility.
- ストレス解消: Prompt stress relief after printing is vital.
- デザイン: Avoid sharp internal corners or features that act as stress concentrators.
- Support Removal Difficulties:
- チャレンジ: Removing support structures, especially dense or internal supports within complex manifold runners or plenums, can be time-consuming, costly, and risk damaging the part surface. Inaccessible internal supports may be impossible to remove completely.
- Solutions & Best Practices:
- DfAM for Support Minimization: Design parts with self-supporting angles (>45°) wherever possible.
- Optimized Build Orientation: Choose an orientation that minimizes the need for critical internal supports.
- Optimized Support Design: Use support structures (e.g., thin-walled, perforated, tree-like) designed for easier removal. Ensure adequate access points for tools.
- Specialized Removal Techniques: Consider wire EDM for precise support cutting near the part surface, or abrasive flow machining for internal channel finishing which can also help remove internal support remnants.
- Design for Access: If internal supports are unavoidable, design access ports or consider splitting the part into printable sections.
- Residual Stress Management:
- チャレンジ: Even if warping is controlled, significant residual stress can remain within the part, potentially affecting fatigue life, long-term dimensional stability, or leading to unexpected failures in service.
- Solutions & Best Practices:
- Comprehensive Stress Relief: Implement appropriate stress relief cycles based on material and geometry. This is non-negotiable.
- Process Simulation: Use simulation tools to predict residual stress patterns and optimize build strategy (orientation, scan pattern) to minimize peak stresses.
- Machining Strategy: Consider the potential for distortion when machining parts with residual stress. Sometimes staged machining with intermediate stress relief steps is needed.
- Build Plate Heating: As mentioned, this significantly reduces stress accumulation during the build.
- Quality Assurance and Consistency:
- チャレンジ: Ensuring consistent quality and properties from part-to-part and batch-to-batch requires rigorous process control and monitoring. Variations in powder batches, machine calibration, or atmospheric conditions can impact results.
- Solutions & Best Practices:
- Robust Quality Management System (QMS): Partner with suppliers like Met3dp who operate under strict QMS (e.g., ISO 9001, AS9100) ensuring traceability, process control, and documentation. Information about Met3dp’s commitment to quality can often be found exploring their company profile (About Met3dp).
- Powder Management: Strict procedures for powder handling, storage, testing (chemistry, PSD), and traceability. Powder recycling requires careful monitoring to prevent degradation.
- インプロセスモニタリング: Advanced AM systems incorporate sensors to monitor melt pool characteristics, temperature, oxygen levels, etc., providing real-time quality indicators.
- Post-Build Qualification: Implement a clear plan for part inspection and testing (dimensional, NDT, mechanical property testing on witness coupons) to verify requirements are met.
Conclusion on Challenges:
Successfully manufacturing high-performance 3D printed intake manifolds requires acknowledging and proactively addressing these potential challenges. It necessitates a combination of smart design (DfAM), careful material selection, precisely controlled metal AM processes, thorough post-processing, and stringent quality assurance additive manufacturing protocols. Collaboration between designers, engineers, procurement teams, and experienced AM service providers is paramount. By leveraging expertise, advanced technology, and best practices, the challenges can be effectively managed, allowing the automotive industry to fully capitalize on the performance, lightweighting, and customization benefits offered by metal additive manufacturing for critical components like intake manifolds.
Choosing Your Partner: Selecting the Right Metal 3D Printing Service Provider
Selecting the appropriate 金属積層造形(AM) service provider is arguably as critical as optimizing the design or choosing the right material for your 3D printed intake manifold. The quality, performance, reliability, and cost-effectiveness of the final component are directly influenced by the capabilities, expertise, and quality systems of your chosen partner. With the rapid growth of the AM industry, numerous providers offer metal printing services, but not all are created equal, especially when dealing with demanding applications like high-performance automotive components. Engineers and procurement specialists need a structured approach to evaluate and select a supplier that aligns with their technical requirements, quality standards, and project goals. Choosing wisely involves looking beyond just the price quote and assessing a range of critical factors.
Key Criteria for Evaluating Metal AM Service Providers:
- Technical Capabilities & Equipment:
- 印刷技術: Do they offer the specific PBF process (SLM, DMLS, EBM) best suited for your chosen material (AlSi10Mg, IN625) and design complexity? Different technologies have nuances in surface finish, feature resolution, and internal stress management. Companies like Met3dp offer specialized technologies like Selective Electron Beam Melting (SEBM) alongside laser-based systems, providing broader options.
- Machine Fleet & Build Volume: Do they have sufficient machine capacity to meet your lead time requirements, especially for potential series production or multiple prototypes? Verify their maximum build envelope can accommodate the size of your intake manifold design. Providers with industry-leading print volumes offer more flexibility.
- マテリアル・ポートフォリオ Do they regularly process the specific alloy you need (AlSi10Mg, IN625)? Do they have experience and validated parameters for these materials? Can they source high-quality, certified powders? Look for providers like Met3dp who not only use but also manufacture 高性能金属粉末, ensuring deep material expertise. Do they offer other relevant alloys if design requirements change?
- Accuracy & Resolution: What are their documented typical tolerances and achievable minimum feature sizes for the relevant materials and machines? Can they demonstrate evidence of achieving the precision required for your critical features?
- Expertise, Experience & Engineering Support:
- Application Experience: Have they successfully produced similar components, particularly intake manifolds or other complex automotive parts? Can they share case studies or demonstrate relevant experience in the high-performance automotive sector?
- DfAM Expertise: Do they offer design consultation or feedback based on DfAM principles? Can their engineers review your design and suggest modifications to improve printability, reduce cost, or enhance performance? This collaborative approach is invaluable.
- Material Science Knowledge: Does the team possess deep understanding of metallurgy, heat treatments, and material properties specific to AM parts? This is crucial for ensuring optimal material performance and selecting appropriate post-processing. Met3dp, with its decades of collective expertise in metal additive manufacturing, exemplifies this depth.
- Problem Solving: How do they approach potential challenges like warping or support removal for complex geometries? Experienced providers have developed robust solutions and troubleshooting protocols.
- Quality Management Systems & Certifications:
- 認定: Are they certified to relevant quality standards, such as ISO 9001 (general quality management) or AS9100 (aerospace, often adopted by high-performance automotive sectors)? Certification indicates adherence to rigorous process control, documentation, and continuous improvement.
- プロセス制御: What measures do they take to ensure process stability and repeatability? This includes machine calibration, environmental controls, powder handling protocols, and potentially in-process monitoring.
- Traceability: Can they provide full traceability for materials (powder batches) and processes used for your specific part? This is critical for quality assurance and root cause analysis if issues arise.
- Inspection Capabilities: What NDT and metrology equipment do they have in-house (CMM, 3D scanning, CT scanning, surface profilometry, material testing)? Can they provide comprehensive inspection reports tailored to your requirements?
- Post-Processing Capabilities:
- In-House vs. Outsourced: Do they perform critical post-processing steps like stress relief, heat treatment, CNC machining, and surface finishing in-house, or do they manage a network of trusted subcontractors? In-house capabilities often offer better control over quality and lead times.
- Range of Services: Can they provide the specific post-processing needed for your intake manifold (e.g., AFM for internal channels, precision machining of flanges, specific coatings)? Verify their expertise in these secondary operations.
- Customer Service, Communication & Project Management:
- Responsiveness: How quickly and thoroughly do they respond to inquiries and requests for quotes?
- Communication: Is communication clear, professional, and proactive? Will you have a dedicated point of contact for your project?
- Collaboration: Are they willing to work collaboratively to solve design or manufacturing challenges?
- Project Management: Do they have clear processes for order tracking, progress updates, and managing deadlines?
- Cost, Value & Lead Time:
- Transparent Pricing: Is the quote detailed and easy to understand, breaking down costs where possible? Be wary of quotes that seem too low, as they may compromise on quality or omit necessary post-processing.
- Value Proposition: Consider the overall value, including expertise, quality assurance, support, and reliability, not just the upfront price. A slightly higher cost from a reputable provider can save significant time and expense downstream by avoiding failures or delays.
- Quoted Lead Times: Are the quoted lead times realistic given the complexity of the part and required processes? How reliable are their lead time estimations based on past performance or references?
Why Consider Met3dp?
Based on these criteria, a provider like メット3dp presents a compelling case for companies seeking high-quality 3D printed intake manifolds:
- Comprehensive Solutions: Offering a synergistic combination of advanced SEBM printers, high-quality metal powder manufacturing (AlSi10Mg, IN625, custom alloys), and application development services.
- Technical Leadership: 雇用 industry-leading print volume, accuracy and reliability across their systems, backed by deep materials science and process expertise.
- Quality Focus: Utilizing advanced powder production (Gas Atomization, PREP) for superior powder characteristics and likely operating under rigorous quality control standards for both powders and printing services.
- Partnership Approach: Positioning themselves as partners to help organizations implement AM and accelerate digital manufacturing transformations, suggesting a collaborative and supportive customer relationship.
Supplier Evaluation Checklist (Example):
基準 | Weighting (1-5) | Provider A Score (1-5) | Provider B Score (1-5) | Met3dp Score (1-5) | 備考 |
---|---|---|---|---|---|
Technology Match (SLM/EBM) | 5 | 4 | 5 | 5 | Met3dp offers SEBM, potentially beneficial |
Material Expertise (AlSi10Mg/IN625) | 5 | 3 | 4 | 5 | Met3dp manufactures these powders |
ビルド・ボリューム | 4 | 5 | 4 | 5 | Verify specific dimensions |
DfAM Support | 4 | 3 | 3 | 4 | Look for proactive design feedback |
Automotive Experience | 4 | 2 | 4 | 4 | Ask for relevant case studies |
Quality Certifications (ISO/AS) | 5 | 3 | 5 | 5 | Verify current certifications |
Post-Processing (In-house Machining) | 4 | 2 | 5 | 4 | Check specific capabilities (e.g., AFM) |
Inspection Capabilities (CT Scan) | 4 | 1 | 4 | 4 | Confirm availability for internal checks |
Lead Time Reliability | 4 | 3 | 4 | 4 | Check references if possible |
Cost (Quoted Price) | 3 | 5 | 3 | 3 | Balance with quality/value |
Communication/Support | 3 | 4 | 4 | 5 | Assess responsiveness during quoting |
Weighted Score Total | — | 126 | 156 | 168 | Illustrative scoring |
Export to Sheets
Ultimately, the selection process may involve obtaining quotes and potentially sample parts from shortlisted providers. Conducting audits or site visits (if feasible) can also provide valuable insights. Investing time in thorough metal AM service bureau evaluation is crucial for mitigating risks and ensuring a successful partnership for producing critical high-performance parts manufacturer collaborations like 3D printed intake manifolds.
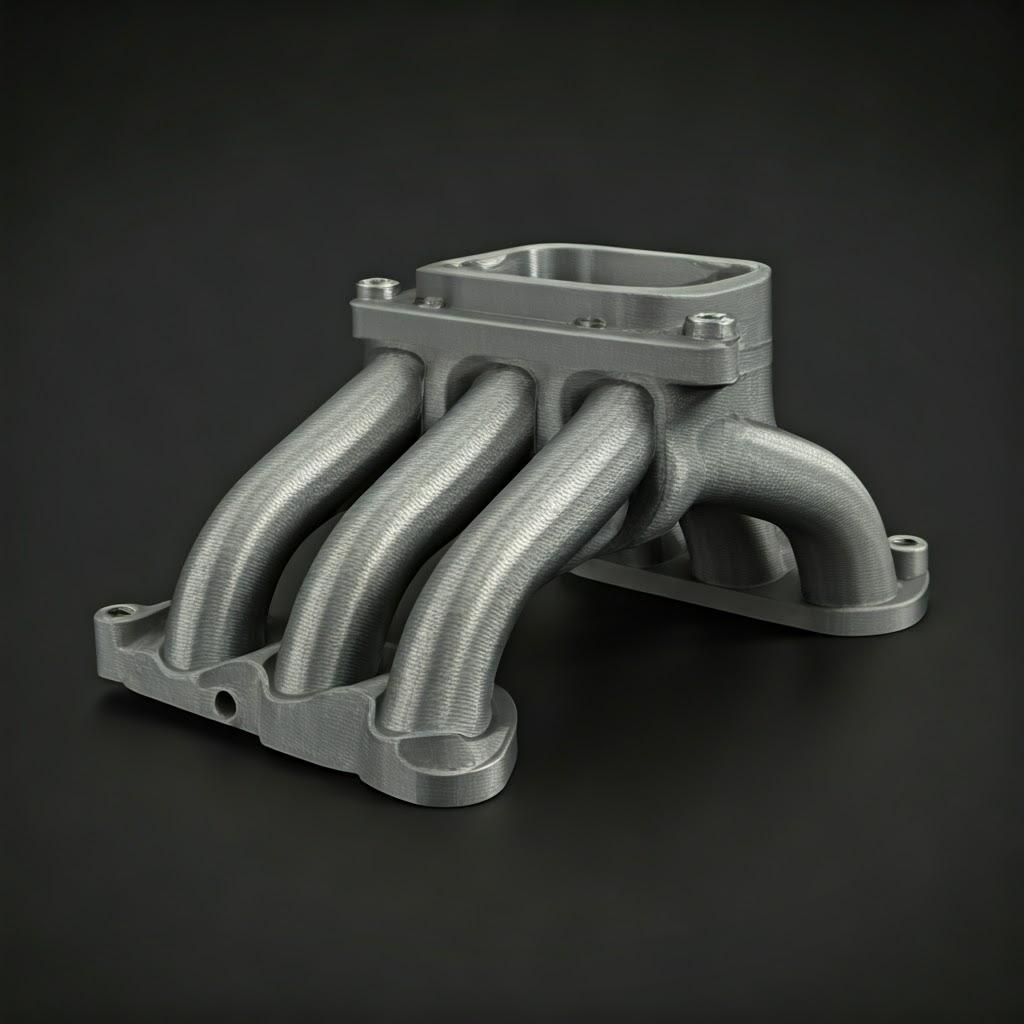
Understanding the Investment: Cost Factors and Lead Times for 3D Printed Intake Manifolds
One of the most frequent questions from engineers and procurement managers considering metal additive manufacturing concerns the cost and time required to produce a part like an intake manifold. While AM eliminates tooling costs associated with casting, the metal 3D printing cost analysis involves several different factors. Similarly, lead times can be significantly faster than traditional tooling cycles but are influenced by various elements. Understanding these drivers is key to budgeting effectively and setting realistic project timelines.
Key Cost Factors for Metal AM Intake Manifolds:
- 材料費:
- Powder Type: This is a major differentiator. High-performance nickel superalloys like IN625 are significantly more expensive per kilogram than aluminum alloys like AlSi10Mg. Exotic or custom alloys will command even higher prices.
- Powder Consumption: The total volume of the part, including any necessary support structures, directly impacts the amount of powder consumed. Designs optimized via DfAM (topology optimization, reduced supports) can lower material usage.
- パウダーの質: High-quality, spherical powders with controlled PSD from reputable suppliers like Met3dp may have a higher initial cost but contribute to better print quality, fewer failures, and more consistent results, potentially lowering overall cost.
- リサイクル: While unfused powder is largely recyclable, the recycling process itself has associated costs and quality control measures.
- Machine Time (Build Time):
- Part Volume & Height: Larger parts or taller builds (oriented vertically) take longer to print layer by layer.
- 複雑さ: Highly complex geometries may require slower scan speeds or more intricate scan strategies, increasing time.
- 層の厚さ: Thinner layers provide better resolution and surface finish but significantly increase the number of layers and thus build time.
- Machine Type & Efficiency: Different machines (e.g., multi-laser systems) have varying build rates. The machine’s hourly operating rate (covering depreciation, energy, maintenance, consumables) is a key cost component.
- Nesting: If multiple parts (or multiple copies of the same part) can be efficiently nested onto a single build plate, the machine time cost per part can be reduced.
- 人件費:
- Pre-Processing: CAD file preparation, build simulation, orientation optimization, and support generation require skilled engineering time.
- Machine Setup & Teardown: Preparing the machine, loading powder, unloading the build, and basic cleaning involve operator time.
- De-Powdering: Manual removal of unfused powder, especially from internal channels, can be labor-intensive.
- サポートの取り外し: This is often a significant manual labor component, requiring careful work with hand tools, grinders, or EDM.
- Post-Processing & Finishing: Labor associated with machining, tumbling, polishing, cleaning, and inspection.
- 後処理費用:
- 熱処理: Furnace time, energy consumption, and potentially controlled atmosphere costs for stress relief or property-enhancing treatments.
- 機械加工: Costs associated with CNC machine time, tooling, and programming for finishing critical features.
- 表面仕上げ: Costs of specialized processes like AFM, electropolishing, or extensive manual polishing.
- HIP (Hot Isostatic Pressing): If required for maximum density and fatigue life, HIP adds a significant cost step due to the specialized equipment involved.
- Inspection & QA: Costs related to CMM measurements, 3D scanning, NDT (CT scanning is particularly expensive), and quality documentation.
- Supplier Overheads & Profit: Service providers factor in their operational costs (facility, administration, R&D) and profit margin.
Factors Influencing Lead Time:
- ビルドタイム: As described above, this is often the largest single component of the timeline, ranging from hours to several days depending on the manifold’s size and complexity.
- Machine Availability: The service provider’s current workload and machine scheduling queue will impact when your part can start printing. High-demand periods can lead to longer queues.
- Post-Processing Duration: Each step adds time:
- Stress Relief: Typically 8-24 hours (including controlled cooling).
- Machining: Hours to days, depending on complexity and setup.
- Support Removal/Finishing: Hours to days, highly variable based on design.
- HIP/Specialized Coatings: Can add several days due to logistics and batch processing.
- Inspection: Hours to days.
- 配送: Time required for transit from the service provider to your facility.
- Iterations: If prototypes require design changes and re-prints, this adds significantly to the overall project timeline.
Typical Lead Time Ranges (Estimates):
- Simple Prototype (Minimal Post-Processing): 5~10営業日
- Complex Manifold (AlSi10Mg, Standard Post-Processing): 2~4週間
- Complex Manifold (IN625, Extensive Post-Processing + HIP): 4-8 weeks+
Cost vs. Traditional Methods:
- プロトタイピング: Metal AM is often faster and more cost-effective than creating prototype tooling for casting or extensive CNC programming for machining complex manifolds from billet.
- Low Volume Production (1-100 units): AM can be very competitive, especially for complex designs where casting tooling is expensive to amortize over few parts, or machining is excessively wasteful/time-consuming.
- Medium to High Volume Production (100s-1000s+): Traditional casting typically becomes more cost-effective per part due to tooling amortization and faster cycle times, unless the unique performance or lightweighting benefits enabled only by AM justify a higher per-part cost, or if the design complexity makes casting infeasible.
Obtaining Accurate Quotes:
To get an accurate quote and lead time estimate for your intake manifold project, provide potential suppliers with:
- 3D CADモデル: In a standard format (STEP, STL).
- Material Specification: AlSi10Mg, IN625, or other.
- Quantity Required: Including potential future volumes.
- Critical Tolerances: Clearly defined on drawings for essential features.
- 表面仕上げの要件: Specify Ra values for critical internal/external surfaces.
- 後処理の必要性: Detail required heat treatments, machining, finishing, inspection (NDT), or coatings.
- Application Details: Understanding the operating conditions (pressure, temperature) helps the supplier assess feasibility and recommend best practices.
Wholesale 3D Printing Services: For companies needing regular production or higher volumes of AM parts, exploring 卸売3Dプリントサービス or establishing ongoing partnerships with providers like Met3dp can lead to optimized pricing structures, dedicated capacity, and streamlined workflows compared to one-off orders. Discussing volume forecasts and long-term needs can unlock potential efficiencies. The ROI additive manufacturing automotive projects often realize comes from faster development, superior performance, and lightweighting, which can outweigh a potentially higher per-part cost compared to conventional methods in specific scenarios.
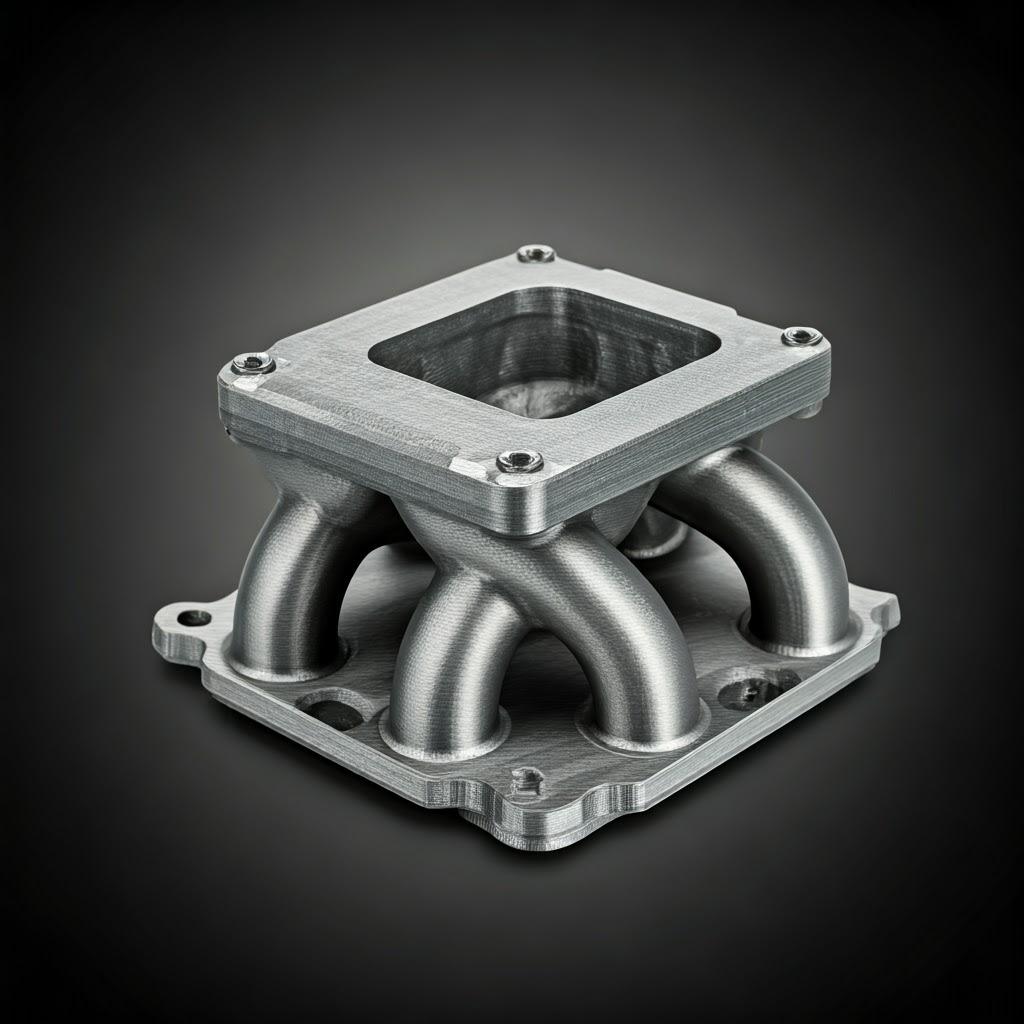
Frequently Asked Questions (FAQ) about 3D Printed Intake Manifolds
Here are answers to some common questions regarding the use of metal additive manufacturing for intake manifolds:
1. How durable are 3D printed metal intake manifolds compared to cast or machined ones?
When designed correctly, manufactured using high-quality materials and processes, and subjected to appropriate post-processing (especially stress relief and potentially HIP), 3D printed metal intake manifolds can exhibit durability comparable or even superior to traditional counterparts.
- 素材の特性: AM parts made from alloys like AlSi10Mg or IN625 can achieve densities exceeding 99.5% and mechanical properties (tensile strength, yield strength, fatigue life) that meet or exceed casting standards for the same alloys, especially after optimized heat treatments.
- デザインの最適化: The ability to optimize the design using topology optimization and DfAM principles allows for material placement precisely where needed for strength, potentially creating stronger structures at similar or lower weights compared to design-compromised cast parts.
- Potential Weaknesses: Improperly processed parts can suffer from porosity or residual stress, which could reduce durability. Choosing a reputable provider with robust quality control, like Met3dp, is crucial to mitigate these risks. Internal surface roughness, if not addressed via post-processing like AFM, could theoretically influence long-term fatigue life under high cycle conditions, although this is often secondary to bulk material properties.
- 比較する: Compared to fabricated/welded manifolds, monolithic AM parts eliminate potential failure points at weld seams. Compared to billet machined parts, AM part properties depend heavily on process control but can be very close, especially after HIP.
2. Is 3D printing intake manifolds cost-effective?
The cost-effectiveness depends heavily on the specific application, production volume, design complexity, and the value placed on performance gains or accelerated development.
- Prototyping & Low Volume: Highly cost-effective. It avoids the high upfront cost and long lead times of casting tooling and is often cheaper and faster than complex multi-axis CNC machining from billet for one-offs or small batches (1-50 units).
- 複雑なデザイン: For manifolds with intricate internal geometries optimized for flow, AM may be the のみ feasible manufacturing method, making cost a secondary factor to achieving the desired performance.
- Performance Value: If the AM-enabled design provides measurable gains in horsepower, torque, throttle response, or crucial weight savings (especially in motorsport or high-performance vehicles), the higher per-part cost compared to high-volume casting can be easily justified by the competitive advantage gained.
- High Volume: For standard designs in mass production (thousands of units), traditional casting usually remains more cost-effective per part.
- Summary: Consider the total cost of ownership, including development time savings, performance benefits, and potential for part consolidation, not just the manufacturing cost per piece. For high-performance, low-to-medium volume, or highly customized intake manifolds, 金属3Dプリンティング often provides excellent value.
3. What information is essential to provide a metal AM service provider for an accurate quote?
To receive a timely and accurate quote, you should provide as much detail as possible. Key information includes:
- 3D CAD Data: A well-defined solid model in a neutral format like STEP is preferred over mesh files like STL for manufacturing quotes, although STL is often used for printing itself. Include 2D drawings if specific tolerances or features need clear callouts.
- 素材の選択: Clearly specify the desired alloy (e.g., AlSi10Mg, IN625) and any required material certifications.
- 数量: Number of parts needed for this order and any projected future volumes (helps assess potential for volume pricing).
- Critical Dimensions & Tolerances: Highlight features requiring tight tolerances (e.g., flange flatness, bore diameters) and specify the required values. Use Geometric Dimensioning and Tolerancing (GD&T) where appropriate.
- 表面仕上げの要件: Specify desired Ra values for critical surfaces (e.g., internal runners, sealing faces).
- 後処理の要件: List all necessary steps: specific heat treatment cycles (e.g., stress relief, T6 temper), required machining operations, finishing (e.g., bead blast, AFM, polishing), inspection needs (e.g., pressure test, CT scan), and any coatings.
- Application Context: Briefly describe the engine type (NA, turbo, supercharged), expected operating pressures and temperatures, and primary performance goals. This helps the provider offer relevant advice.
4. Can the internal passages of a 3D printed intake manifold be made perfectly smooth for optimal airflow?
Achieving perfectly smooth internal passages requires specific attention during design and post-processing.
- As-Built Finish: The internal surfaces of AM parts, especially those requiring support structures or oriented unfavorably, will have a degree of roughness (typically Ra 10-25 µm or more). Down-facing surfaces are usually the roughest.
- DfAM Impact: Designing runners with self-supporting angles (>45°) minimizes the need for internal supports, resulting in comparatively smoother surfaces than supported sections. Vertical orientation of runners can also help.
- Post-Processing Solutions:
- Abrasive Flow Machining (AFM): This is often the most effective method for smoothing complex internal passages by flowing an abrasive putty through them. It can significantly reduce roughness (potentially reaching Ra < 5 µm).
- Tumbling/Vibratory Finishing: Can provide some smoothing if the media can effectively reach internal areas, but less targeted than AFM.
- Electropolishing: Effective for certain alloys and geometries, providing very smooth finishes.
- トレードオフ: Achieving ultra-smooth internal finishes adds cost and lead time due to the extra post-processing steps. The performance benefit of incremental smoothness improvements needs to be weighed against this cost. While smoother is generally better for ideal laminar flow, the complex geometries enabled by AM often provide larger performance gains through optimized shapes, even with a slightly rougher surface than a mirror-polished tube.
Conclusion: Driving the Future of Automotive Performance with Metal Additive Manufacturing
The intake manifold, a critical component governing engine breathing and performance, stands as a prime example of how 金属積層造形 is reshaping the landscape of high-performance automotive engineering. As we’ve explored, the limitations inherent in traditional casting and machining – constraints on design complexity, lengthy tooling processes, material waste, and difficulties in low-volume customization – are effectively overcome by the layer-by-layer precision and freedom offered by metal 3D printing technologies like SLM, DMLS, and SEBM.
The advantages are compelling: unparalleled デザインの自由 allowing for CFD-optimized runner paths and integrated features; significant 軽量化 potential through topology optimization and efficient material use; the ability to utilize 高性能素材 like lightweight AlSi10Mg and high-temperature IN625 tailored to specific operating conditions; and drastically accelerated prototyping and development cycles. These benefits translate directly into tangible performance gains – enhanced volumetric efficiency, improved throttle response, optimized torque curves, and greater overall engine output – giving manufacturers and racing teams a crucial competitive edge.
However, realizing this potential requires a holistic approach. Success hinges on embracing 積層造形設計 (DfAM) principles, carefully selecting the appropriate 材料, understanding and planning for essential 後処理 steps (from stress relief to precision machining and surface finishing), and navigating potential manufacturing 課題 through robust process control and quality assurance.
Critically, the journey relies on selecting the right manufacturing partner. A provider like メット3dp embodies the necessary combination of cutting-edge technology, deep materials expertise (as both a powder manufacturer and printing service provider), rigorous quality systems, and a collaborative approach. Their 包括的なソリューション, spanning advanced printers, optimized metal powders, and application development support, position them as a key enabler for companies looking to leverage メタルAM for demanding applications like intake manifolds.
について future of automotive manufacturing, particularly in the performance, motorsport, and specialized vehicle sectors, will undoubtedly see increased adoption of additive manufacturing. For components like intake manifolds, where airflow optimization, weight reduction, and customization are paramount, metal 3D printing is no longer just a viable alternative; it is rapidly becoming the benchmark for innovation and performance. By partnering with knowledgeable suppliers and strategically integrating AM into their design and production workflows, automotive companies can continue to push the boundaries of engine performance and drive the next generation of high-performance vehicles.
シェアする
MET3DP Technology Co., LTDは、中国青島に本社を置く積層造形ソリューションのリーディングプロバイダーです。弊社は3Dプリンティング装置と工業用途の高性能金属粉末を専門としています。
関連記事
Met3DPについて
最新情報
製品
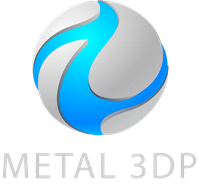
3Dプリンティングと積層造形用金属粉末