2025年の3Dプリンティング金属粉末
目次
3Dプリンティング 金属粉末は、航空宇宙、医療、自動車などの業界全体で製造に革命をもたらしている。この高度な積層造形技術は、微細な金属粉末の層を選択的に溶融することにより、3D CADデータから複雑な金属部品を直接作成することを可能にする。
この包括的なガイドでは、金属粉末3Dプリンティングのあらゆる側面を検証し、技術とアプリケーションを理解するのに役立ちます。
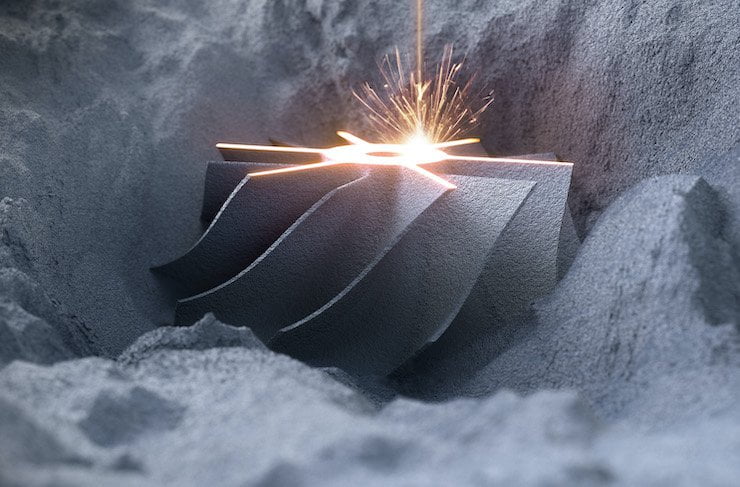
3Dプリンティング金属粉末の概要
直接金属レーザー焼結(DMLS)または選択的レーザー溶融(SLM)としても知られる金属3Dプリンティングは、高出力レーザーを使用して微細な金属粉末を固体の3Dオブジェクトに融合する積層造形プロセスです。
3Dプリンターは、アルミニウム、チタン、ニッケル合金、ステンレス鋼のような粉末状の金属材料から層ごとに金属部品を作り上げる。この技術は、比類のない設計の自由度と、従来の製造にはない印象的な材料特性を提供します。
3Dプリンティング金属粉末に関する主な詳細:
パラメータ | 詳細 |
---|---|
テクノロジー | レーザーを用いて金属粉末を選択的に溶融する粉末床溶融プロセス |
材料 | アルミニウム、チタン、ニッケル、ステンレス鋼、コバルトクロム、貴金属 |
ハードウェア | 高出力レーザー、パウダーベッド、レーキシステムを備えた3Dプリンター |
プロセス | パウダーを薄く広げ、レーザーで選択的に溶かし、レイヤーを重ねてパーツを作る |
プロパティ | 高強度、均一な材料、複雑な内部形状 |
アプリケーション | 航空宇宙、医療用インプラント、自動車、工具、宝飾品 |
メリット | 設計の自由度、軽量化、部品の統合、ラピッドプロトタイピング |
制限事項 | 装置コストが高い、サイズに制限がある、後処理が必要 |
この積層造形法は、設計の自由度の向上、部品の統合、迅速なプロトタイピング、大幅な軽量化など、CNC機械加工のような従来の減法的手法と比較して多くの利点をもたらします。複雑な金属部品を3Dプリントできるようになったことで、各業界で重要なイノベーションが実現しています。
3Dプリンター用金属粉末の種類
3Dプリンティング金属粉末は、航空宇宙、自動車、医療、エネルギーなど様々な産業向けにユニークな特性を提供する、積層造形に不可欠な材料です。以下は、3Dプリンティング金属粉末の主なカテゴリーと一般的な種類の概要で、分かりやすいように表形式で表示しています。
関連商品
1.チタン合金
チタン粉末は軽量、高強度、耐腐食性で、航空宇宙や医療用途に理想的です。
タイプ | 説明 | アプリケーション |
---|---|---|
Ti6Al4V(グレード5) | 強度重量比が高く、広く使用されているチタン合金。 | 航空宇宙、自動車、医療用インプラント |
Ti6Al4V ELI | グレード5を精製したもので、生体適合性のために格子間物質が極めて少ない。 | 医療用インプラント、補綴物 |
純チタン | グレード1~4、優れた耐食性と生体適合性。 | 化学処理、医療用インプラント |
2.ステンレス鋼
ステンレス鋼粉末は耐久性、耐食性に優れ、構造部品や機能部品に広く使用されている。
タイプ | 説明 | アプリケーション |
---|---|---|
316Lステンレス鋼 | 優れた耐食性と機械的特性。 | 医療器具、食品加工、海洋 |
17-4PHステンレス鋼 | 高い強度と耐摩耗性を持つ析出硬化鋼。 | 航空宇宙、自動車、産業用工具 |
304ステンレス鋼 | コストパフォーマンスが高く、適度な耐食性。 | 消費財、構造部品 |
3.アルミニウム合金
アルミニウム粉末は軽量で熱伝導性に優れ、航空宇宙や自動車用途に最適です。
タイプ | 説明 | アプリケーション |
---|---|---|
AlSi10Mg | 優れた機械的特性と耐熱性。 | 航空宇宙、自動車、工業部品 |
AlSi12 | 熱伝導率が高く、耐摩耗性に優れている。 | 熱交換器、軽量部品 |
アルミニウム 7075 | 高強度かつ軽量で、ヘビーデューティー用途に適している。 | 航空宇宙、構造部品 |
4.ニッケル基合金
ニッケル合金は、過酷な環境下で優れた耐高温性と耐食性を発揮します。
タイプ | 説明 | アプリケーション |
---|---|---|
インコネル718 | 高い強度と耐酸化性を持ち、過酷な条件に適している。 | タービンブレード、ジェットエンジン、エネルギー分野 |
インコネル625 | 海洋を含む過酷な環境に対する卓越した耐性。 | 海洋、化学処理 |
ハステロイX | 優れた耐熱性と耐薬品性。 | 航空宇宙、高温環境 |
5.コバルトクロム合金
コバルト・クロム粉末は耐摩耗性に優れ、生体適合性に優れているため、医療や歯科用途に最適です。
タイプ | 説明 | アプリケーション |
---|---|---|
CoCrMo | 強度、耐摩耗性、生体適合性を兼ね備えている。 | 歯科インプラント、矯正器具 |
CoCrW | 高い硬度と耐熱性で、要求の厳しい用途に適している。 | タービンブレード、高摩耗部品 |
6.工具鋼
工具鋼はその硬度と耐摩耗性で知られ、一般的に工具や金型の製造に使用される。
タイプ | 説明 | アプリケーション |
---|---|---|
H13工具鋼 | 工具や金型に最適な耐熱鋼。 | 射出成形、ダイカスト |
マレージング鋼 | 強度と靭性に優れ、高応力部品に適している。 | 航空宇宙、工具 |
7.貴金属
貴金属は、その審美性と導電性の特性から、高級品、宝飾品、電子機器に使用されている。
タイプ | 説明 | アプリケーション |
---|---|---|
金(Au) | 高価で耐食性に優れ、装飾用途に使用される。 | ジュエリー、エレクトロニクス |
銀(Ag) | 優れた熱伝導性と電気伝導性。 | エレクトロニクス、導電性部品 |
プラチナ (Pt) | 高い耐久性と耐性があり、高級用途に使用される。 | ジュエリー、触媒コンバーター |
8.銅合金
銅ベースの粉末は、特殊な用途向けに卓越した熱伝導性と電気伝導性を提供します。
タイプ | 説明 | アプリケーション |
---|---|---|
純銅 | 導電性に優れ、電気用途に適している。 | エレクトロニクス、熱交換器 |
銅合金 | 良好な導電性(例えばCuCrZr)を持つ強化された機械的特性。 | 電気部品、工具 |
3Dプリンティング 金属粉末プロセス
金属3Dプリントに使用される同様の粉末床融合技術はいくつかある:
金属粉末床溶融プロセス
プロセス | 詳細 |
---|---|
ダイレクトメタルレーザー焼結(DMLS) | レーザーを用いて不活性ガス雰囲気中で金属粉末を選択的に溶融する。 |
選択的レーザー溶融(SLM) | DMLSと非常によく似ており、粉末を完全に溶融して固体部品にする。 |
電子ビーム溶解(EBM) | レーザーの代わりに電子ビームを使用することで、より高いビルドレートを実現 |
選択的レーザー焼結(SLS) | 粉体を完全に溶融させることなく、一緒に固形部分に焼結する。 |
ダイレクトメタルレーザー溶融(DMLM) | DMLSプロセスの別称 |
レーザーカッティング | コンセプトレーザーが開発したプロセス |
ラスフォーム | DMG MORIによるプロセス |
最も一般的に使用される技術はDMLSとSLMである。どちらも高出力のイッテルビウムファイバーレーザーを使用して金属粉末を完全に溶融・融合させ、CADデータから3Dオブジェクトを成長させる。
SLMとDMLSの主な違いは、SLMは完全な溶融と高密度のパーツの実現を目指すのに対し、DMLSは粉末粒子間に若干の空隙があるパーツを製造する可能性があることである。しかし、この用語はしばしば同じ意味で使われる。
電子ビーム溶解(EBM)は、レーザーではなく電子ビーム熱源を使用するため、造形速度が速くなる。しかし、EBMはチタンやニッケル合金のような導電性材料にしか使えない。
選択的レーザー焼結(SLS)は、完全な融点に達することなく、より低い温度で粉末を固体部品に融合させる。これにより、より多孔質の金属部品ができる。
粉末床3Dプリンティング用金属材料
様々な金属や合金を、粉末床融合3Dプリンティング技術で使用する微粉末に加工することができる:
粉末床3Dプリンティング用金属
素材 | 詳細 | アプリケーション |
---|---|---|
チタン | 高い強度対重量比、生体適合性 | 航空宇宙、医療用インプラント |
アルミニウム | 軽量、高強度 | 自動車、航空宇宙 |
ニッケル合金 | 耐食性、高強度 | 航空宇宙、海洋 |
ステンレス鋼 | 耐食性、高硬度 | 工業用工具、金型 |
コバルトクロム | 生体適合性、摩耗性 | 歯科、医療用インプラント |
貴金属 | ジュエリー、耐久性 | ジュエリー、高級品 |
工具鋼 | 耐熱性、硬度 | 金属成形、射出成形金型 |
合金鋼 | 高強度、耐衝撃性 | 工業用磨耗部品 |
最も広く使用されている金属は、強度対重量比が高いチタン合金とアルミニウムである。インコネルのような不活性ニッケル合金は航空宇宙用途で人気があります。ステンレス鋼と工具鋼の粉末は、優れた硬度と耐摩耗性を持つ耐久性のある金属部品を作ります。
金、銀、プラチナなどの貴金属は、宝飾品や高級品を直接3Dプリントできる。カスタム医療用インプラントには、チタンやコバルトクロムのような生体適合合金がよく使われる。
AM用の金属粉末は、ガスまたは水の噴霧化によって、粉末床印刷の解像度に最適なサイズの精密な粒子サイズに製造される。
金属粉末床3Dプリンティングの用途
金属積層造形は、航空宇宙、医療、歯科、自動車、工業の各分野で、複雑で軽量な部品の製造を可能にする。
金属粉末床3Dプリンティングの産業用途:
産業 | アプリケーション | メリット |
---|---|---|
航空宇宙 | 航空機部品、タービン、ロケット部品 | 軽量化、ジオメトリーの最適化 |
メディカル | 整形外科用インプラント、手術器具 | 生体適合性、個別化 |
自動車 | 軽量部品、カスタム金型 | より迅速な開発、統合 |
インダストリアル | 射出成形金型、治具、固定具 | 最適化されたコンフォーマル冷却 |
ジュエリー | 指輪、ペンダント、時計 | ユニークな幾何学模様、ゴールド/シルバー |
歯科 | クラウン、ブリッジ、アライナー | カスタムフィット、迅速な生産 |
航空宇宙分野では、強度対重量特性が最適化されたチタン製ブラケットやステンレス製ランディングギア部品のような、より軽量な航空機構造部品の製造に金属AMが使用されている。
この技術は、患者の解剖学的構造に適合し、荷重をより分散させる股関節のような、カスタマイズされた医療用インプラントに理想的である。メタルプリンティングは、部品の統合と軽量最適化設計によって自動車製造を合理化する。
射出成形のような業界では、金型に3Dプリントされたコンフォーマル冷却チャンネルが生産性を大幅に向上させます。ジュエラーは、このプロセスを活用して、貴金属で世界に一つだけのジュエリーを制作しています。
金属粉末床3Dプリンティングの利点
プロトタイプから最終用途の生産部品に至るまで、金属AMは機械加工や金属鋳造のような従来の製造プロセスよりも大きな利点を提供する:
金属粉末床3Dプリンティングの主な利点
- 設計の自由度 - 減法法では不可能な複雑な有機的形状や内部格子を作成する。
- より高速なプロセス - ツールを使用しない積層造形プロセス、低廃棄物 - CADから金属部品へ直接移行
- 軽量化 - トポロジーを最適化し、より軽く、より強い金属部品を実現
- 部品の統合 - アセンブリを1つの3Dプリント部品に統合し、製造工程を削減します。
- ラピッドプロトタイピング - 開発中の金属部品設計を迅速にテスト
- カスタマイズ部品 - 医療用インプラントやその他の金属部品を簡単にカスタマイズできます。
- 高強度 - アズプリント金属部品は、鋳造のような従来の方法に匹敵する。
- 在庫の削減 - 金属スペアパーツをオンデマンドで印刷。
- 廃棄物削減 - アディティブ・プロセスの材料廃棄率は5%以下
金型のコンフォーマル冷却チャンネルやインプラントの複雑な格子構造など、金属AM部品の最適化された特性は、フライス加工や鋳造プロセスでは製造不可能である。
複雑な金属部品やカスタマイズされた金属部品をCADデータから直接3Dプリントすることで、大がかりな金型製作、機械加工、組み立てを必要とするサブトラクティブ方式に比べて、製造工程を最小限に抑えることもできます。時間とコストを大幅に節約できるため、少量生産に最適です。
金属粉末床印刷の限界と課題
多くの利点がある一方で、金属粉末床3Dプリントを採用する際に注意すべき制限もある:
金属粉末床3Dプリンティングの限界
- 高い機械コスト - 金属3Dプリンタは$100,000程度から。大型システムは$1Mを超える
- 部品サイズに制限 - 現在、500mm x 500mm x 500mm以下の数量に対応
- 後処理 - サポート除去、表面仕上げのための追加工数
- 異方性材料 - 造形方向によって機械的特性が異なる
- 必要な規格 - 航空宇宙および医療用には、粉体およびプロセスの規格が不足している。
- 材料の選択肢が限られる - 鋳造やMIM粉末冶金に比べて利用可能な合金が少ない。
- 気孔率の問題 - パラメータによっては、プロセス中に小さな内部空隙が生じる可能性がある。
- 未使用粉の管理 - 金属粉の取り扱い、リサイクル要件
プリンターのコストと造形サイズの制約から、金属AMの採用は比較的少量生産に限られるかもしれない。サポート構造やビルドプレートのオーバーハングも、機械加工のような後処理を必要とする。
規制の厳しい分野に採用が広がるにつれ、材料、プロセス、粉末の取り扱いに関する業界標準の開発が進んでいる。現在、AM用に最適化されたプレアロイ粉末として利用できるのは、一部の金属合金に限られている。
X/Y方向とZ方向で強度が異なる異方性材料特性は、設計とプロセス補正を必要とする。内部ボイドや空隙の問題も、理想的な加工パラメータを設定することで軽減する必要があります。
金属粉末ベッド3Dプリントプロセス
金属用の粉末床融合3Dプリントプロセスでは、金属粉末の薄い層を広げ、それを選択的に溶かしてパーツを作り上げる:
金属粉末床融合3Dプリントプロセス:
ステップ | 説明 |
---|---|
1.3Dモデル | CADモデルをレイヤーに3Dスライス |
2.スプレッドパウダー | 機械が金属粉の薄い層(~20~100μm)を広げる |
3.レーザー溶融 | 高出力レーザーが粉体を選択的に溶融し、層を溶かす |
4.下のベッド | ビルドプレートが下がり、新しいパウダー層が上に広がる |
5.ステップを繰り返す | フルパートが出来上がるまで、ステップ2~4を繰り返す。 |
6.部品を取り外す | 未溶融のパウダーが部品を支え、その後取り除かれる |
7.ポストプロセス | 追加の洗浄と表面仕上げ |
このプロセスは、通常STL形式の3D CADモデルから始まり、スライサー・ソフトウェアによって処理される。これはモデルをレイヤーにスライスし、基本的に各レイヤーの2Dプロファイルを作成し、プリンター用の造形指示を生成します。
プリンターは、ワイパーシステムを使って金属粉末の薄い層をパウダーベッド全体に広げます。その後、レーザービームが層の上をなぞり、その層のプロファイルに従って選択的に金属粉末を溶かす。
高出力レーザーが金属粒子を完全に融合させ、固化層にする。その後、ビルドプレートが下がり、新しい粉末の次の層が前の層の上に広がる。
未焼結の粉末は、造形中にサポートとして機能する。プリント後、このパウダーはブラシで払い落とされ、完成した金属部品が現れる。多くの場合、3Dプリントされた表面を滑らかにするために、機械加工や表面仕上げが行われる。
パウダーベッド・フュージョン・プリンター・ハードウェア
専門の金属3Dプリントシステムは、金属粉末を処理するために粉末床融合技術を使用しています。コアコンポーネントは以下の通り:
パウダーベッド融合プリンターコンポーネント:
コンポーネント | 説明 |
---|---|
レーザーシステム | 金属粉末溶融用高出力ファイバーレーザー ~100-400W |
粉体床 | 可動式ベッドに薄く敷き詰められた金属粉 |
パウダーディスペンサー | パウダーをベッドにスムーズに散布 |
パウダーコレクション | 余分な粉を回収して再利用 |
不活性ガス流量 | アルゴンまたは窒素で満たされた密閉チャンバー |
ビルドプレート | レイヤーが上に印刷されるにつれて低くなる |
光学系 | 粉体ベッド上にレーザービームを集光・照射 |
制御システム | レーザー、光学系、パウダーベッドを協調制御 |
金属粉末を完全に溶融して緻密な部品に融合させるには、高出力のイッテルビウムファイバーレーザーが必要である。理想的な溶融プールと接合を達成するためには、レーザーのエネルギー密度と焦点を厳密に制御する必要がある。
レーザーは数十ミクロンまで集光し、各層の形状をトレースします。ガルボミラー光学系は、ベッド上でレーザーを正確に照射します。
金属粉末は、レーキシステムによってカートリッジから吐出され、約20~100ミクロンの厚さで印刷エリア全体に均一に広げられる。パウダーはシステムの前部から吐出され、余剰分は後部で回収される。
アルゴンや窒素のような不活性ガスがビルドチャンバーを満たし、アルミニウムやチタンのような反応性の金属の酸化を防ぐ。システム全体は、レーザー、パウダーベッド、その他のアクチュエーターを統合した専用ソフトウェアによって制御される。
粉末床溶融プロセス・パラメーター
粉末溶融に関わる様々なプロセスパラメーターを最適化することは、高品質の金属部品を製造する上で非常に重要である:
主要な粉末床溶融プロセスパラメータ:
パラメータ | 典型的な範囲 | 部品品質への影響 |
---|---|---|
レーザー出力 | 100-400W | メルトプールの大きさに影響、ボンディングをコントロール |
ビームサイズ | ~50-100μm | フォーカススポットのサイズは解像度、精度に影響する |
スキャン速度 | 最大10,000 mm/s | より速いスキャンは熱勾配に影響する |
ハッチの間隔 | ~50~200μm | スキャントラック間の距離、高密度化 |
レイヤーの高さ | 20-100μm | より薄い層が解像度と表面仕上げを向上 |
パウダー層 | 20-50μm | 粉体層の均一性と厚さ |
ビルドプレート温度 | 60-200°C | 予熱がストレスとカールを軽減 |
レーザー出力は、金属粉末粒子を完全に溶かして固体部品にするには十分高くなければならない(通常100W~400W)。しかし、出力が高すぎるとキーホーリング現象が発生する可能性がある。
レーザーのスキャンを高速化すると、生産速度は向上しますが、残留応力や材料の異方性が生じやすくなります。ハッチ間隔は、隣接するスキャントラック間の距離を設定します。
20~50ミクロン程度の薄いパウダー層は、解像度、微細なディテール、表面仕上げを向上させる。また、ビルドプレートを予熱することで、ストレスを軽減することができます。
パラメーターの最適化は、粉末材料、レーザー光学系、不活性ガスフロー、その他の相互依存的な要因に特有のものです。理想的な設定を行うには、微調整が必要です。
金属AM部品の後処理ステップ
粉末溶融法を用いて複雑な金属部品を印刷した後は、通常、追加の後処理が必要になる:
金属AM部品の一般的な後処理ステップ:
- サポート除去 - 未焼結粉末サポートを振動、ブラストなどで除去する。
- 熱応力除去 - 部品にアニール処理を施し、プロセスによる内部応力を除去します。
- 表面加工 - フライス加工、旋盤加工、研削加工など、表面を滑らかにする伝統的な方法。
- 熱間静水圧プレス - 高熱と圧力を加え、材料の密度を高める。
- 熱処理 - 制御された加熱・冷却サイクルを用いて微細構造を変化させる。
- 表面仕上げ - コーティングの塗布、希望する表面特性を得るための研磨仕上げ
サポートパウダーは、振動、ビーズやエアによるブラスト、真空吸引を組み合わせて慎重に除去される。このパウダーはふるい分けして再利用できることが多い。
アニーリング熱処理は、レーザー溶融時の激しい局所加熱によって誘発される応力を緩和するのに役立ちます。追加の表面加工は、寸法精度と表面仕上げを向上させます。
用途によっては、高温で均一な高いガス圧をかけ、部品をさらに高密度化する熱間静水圧プレスが有効です。これにより、印刷されたままの部品の空隙を最小限に抑えることができます。
溶体化処理、時効処理、または合金に合わせたその他の熱処理によって、望ましい材料の微細構造と特性を達成することができる。研磨やコーティングのような追加の表面仕上げ工程は、要求される表面特性を提供します。
積層造形用工業用金属粉末
特殊な金属粉末は、流動性、充填密度、粉末床溶融3Dプリンティングで加工する際のレーザー吸収といった理想的な特性を提供するために開発された:
金属粉末の特性と製造方法
パウダー・プロパティ | 代表的な仕様 | 製造方法 |
---|---|---|
サイズ範囲 | 15-45 μm | 不活性ガスによるガスアトマイズ |
形態学 | 球形 | 良好なパウダーフローとパッキング |
不純物 | <100 ppm O2 | 合金の機械的特性を維持 |
見かけ密度 | 最大80%の材料密度 | 粉体の充填と散布を示す |
流量 | ホール流量計 >15s/50g | 印刷時のスムーズなパウダーの広がり |
高解像度の印刷、良好な表面仕上げ、適切な流動特性を得るためには、約15~45ミクロンの精密な粒度分布が必要である。球状のパウダー形態は、パウダーのスムーズな供給とベッド全体への広がりを可能にします。
化学的純度は、意図した印刷ままの材料性能を達成するために非常に重要です。酸化や汚染は強度や延性を低下させます。
流量はASTM B213規格に基づき、ホールフローメーター漏斗を用いて試験される。安定した粉体層を形成するためには、約4g/cc以上の良好な見掛け粉体密度が必要です。
ガスアトマイズと水アトマイズは、付加製造の要件を満たす球状の金属粉末を製造するための一般的な技術である。粉末はふるい分けされ、均一な粒子径が確保される。
金属粉末床3Dプリントサービスの選択
適切な金属AMサービスプロバイダーを選択することは、高品質のプリントパーツを得るための鍵です。以下は考慮すべき要素です:
金属3Dプリントサービスの評価と選び方
- 経験 - 専門性を評価するために、特に金属AMの経験年数を調べる。
- 材料 - チタン、工具鋼、貴金属など、必要な金属を確実に提供する。
- 部品サイズ - 必要な部品寸法に合わせて、製造ボリュームのあるサービスを選択します。
- 品質プロセス - すべての段階で厳格な品質管理プロトコルに従うこと。
- 後加工 - CNC機械加工などの二次加工を提供できるかどうかを確認する。
- アプリケーションに関する専門知識 - 航空宇宙、医療などの規制の厳しい分野で重要な役割を果たします。
- 認証 - プロセスに関するISOおよび業界固有の認証を探す。
- カスタマーサービス - 設計やアプリケーションのアドバイスに欠かせない、迅速な技術サポートチーム
- 納期 - 標準的なリードタイムとお急ぎ注文のオプションを理解する。
- 価格 - 素材と形状の複雑さ、後処理、量を考慮する。
- NDA/IP保護 - 独自の設計データは契約により保護されるべきである。
金属AM部品の設計ガイドライン
金属積層造形の利点を十分に活用するためには、設計はDfAM(Design for Additive Manufacturing)の原則に従うべきである:
主要なメタルAM設計ガイドライン:
- 格子構造による軽量化の最適化
- アセンブリを単一の複雑な部品に統合
- コンフォーマル・クーリング・チャンネルのような内部機能の設計
- 機械加工では不可能な、有機的で自由な形状を使用する。
- オーバーハングを最小限に抑え、角度をつけたサポートを設計する。
- 部品の高さを低くし、大きな平らな部分を避けるための方向付け
- サポートの取り外しの問題を回避するためのネジ穴の設計
- 気孔ができやすい薄い壁には、厚みを増す。
- 異なる方向の異方性材料特性を補正する
- 有益であれば、制御された多孔性を表面にデザインする
部材を薄くした複雑な格子構造は、3Dプリントすると強度を保ったまま軽量化できる。アセンブリを単一部品に統合することは、従来の製造と比較して大きな利点です。
冷却水路やその他の有用な内部空洞は、もはや穴を開ける必要がなく、最適な有機的経路をたどることができる。弛みやすいオーバーハングは、角度のついた格子や傾斜のあるデザインによって避けることができる。
部品の向きは、残留応力を減らすために、印刷中のZ高さを最小にすることを目指すべきである。気孔が発生しやすい薄い壁は、目標の材料密度を達成するために余分な厚みが必要になる場合があります。
金属AMのコスト・モデリングと経済性
金属添加剤が経済的に実行可能かどうかを判断するには、すべてのコストを評価する必要がある:
金属粉末床AMのコスト要因:
- 機械の減価償却 - 高額なプリンターコストを耐用年数にわたって分散
- 材料費 - 粉末金属は$100~$500/kg
- 労力 - オペレーターの労力、デザイン、後処理
- エネルギー消費 - 高出力レーザーやその他のシステムは、かなりの電力を必要とする。
- 生産速度 - パラメータ、機械限界に基づく1時間当たりの印刷量
- 後処理 - 機械加工、仕上げ工程はダウンタイムとコストを増加させる。
- 設備コスト - 必要な粉体処理システム、不活性ガス、スペース
- 品質管理 - 生産中の部品の検査と工程の適格性確認
- 安全性とコンプライアンス - 規制の対象となるアプリケーションの場合、文書化は広範囲にわたります。
金属プリンターのコストが高いということは、生産量を増やすことで最適な利用ができるよう、機械の耐用年数を評価することを意味する。材料費もまた、特にエキゾチック合金の場合には重要である。
オペレーター、エンジニア、設計者、品質技術者など、すべての労働力を計算に入れなければならない。エネルギー消費は大きい。後工程のダウンタイムが生産速度を低下させる。
航空宇宙や医療用途では、文書化や品質システムのようなコンプライアンス・コストが広範囲に及ぶ。入念なコスト・モデリングにより、金属AMがコスト効率の良い時期を決定します。
金属積層造形の動向と未来
金属粉末床溶融炉は急速に発展し、採用が進んでいる:
金属粉末床3Dプリンティングの将来動向:
- より大きな容積 - 500mm立方以上のエンクロージャーを開発中
- 製造速度の向上 - スキャニング戦略とマルチレーザーシステムの改善
- 新しい材料オプション - アルミニウムF357やM300マルエージング鋼など、より多くの合金
- ハイブリッド製造 - 印刷、フライス加工、検査を1つのシステムで実現
- 粉体ハンドリングの自動化 - 粉体管理のためのクローズドループリサイクルシステム
- 新たな用途 - 石油・ガス、エレクトロニクス分野への拡大
- システムコストの低下 - 工業化により、プリンターのコストは長期的に低下する。
- 材料特性の向上 - プロセスの改良とHIPによる高密度化を通じて
- 拡張冶金-微細構造と特性の特性評価の向上
- 業界標準 - 航空宇宙および医療におけるプロセスおよび材料品質について
造形量が大きくなれば、より複雑で大量生産が可能になる。マルチレーザー光学系は、造形速度を劇的に向上させます。
クローズドループ粉体ハンドリングシステムは、品質と安全性を向上させながら、リサイクルと再利用を自動化する。新しいエキゾチック合金のオプションが毎年導入されている。ハイブリッド製造は、アディティブプロセスとサブトラクティブプロセスを組み合わせ、完全なその場加工を実現します。
技術の成熟に伴うコストの低下は、用途を拡大し続けるだろう。さらなる材料研究とベンチマークは、加工合金を拡大し、材料性能を向上させる。航空宇宙、医療、自動車分野での採用を加速するため、業界標準に関する広範な取り組みが行われる。
結論
このガイドでは、印刷プロセスや材料からアプリケーション、利点、制限、トレンドまで、金属粉末床融合3D印刷の主要な側面をカバーしています。
金属を使った積層造形は、そのユニークな機能により、産業界全体で破壊的なイノベーションを可能にしている。この技術は、軽量化、部品の統合、設計の自由度、ラピッドプロトタイピング、カスタマイズされた金属部品の製造を可能にします。
プリンターのコスト、造形サイズの制約、後処理、材料オプションなどの制約にもかかわらず、金属AMの採用は、航空宇宙、医療、自動車、産業分野のミッションクリティカルなアプリケーションの拡大に向けて加速している。
継続的なプロセスの改良、新素材、造形量の増加、ハイブリッドシステム、自動化されたパウダーハンドリング、コストの低下により、最終用途の生産部品に金属3Dプリンティングの利用が拡大することが予想されます。このガイドでは、この変革的な製造技術の現状と軌跡を取り上げます。
金属粉末3Dプリントに関するよくある質問
ここでは、金属粉末床溶融積層造形に関するよくある質問にお答えします:
Q: 金属粉末床溶融法で3Dプリントできる材料は何ですか?
A: 一般的な合金には、チタン、アルミニウム、ニッケル、ステンレス鋼、工具鋼、コバルトクロム、金や銀などの貴金属、銅などがあります。新しい合金は常に開発されています。
Q:現在、どのような産業で金属AMが使われていますか?
A: 航空宇宙、医療、歯科、自動車、石油・ガス、産業機械、宝飾品は、金属AMの主要な採用企業です。この技術は複雑で少量生産の部品に最適です。
Q: 金属粉末床3Dプリントの精度はどのくらいですか?
A: 寸法精度は±0.1-0.2%まで可能で、パラメータと後処理により±50μm程度の高分解能も可能です。
Q: メタルAMには特別な設備が必要ですか?
A: 印刷中は不活性ガス雰囲気が必要で、通常はアルゴンです。ベントとふるいを備えたパウダーハンドリングシステムも推奨されます。その他の特別な設備は必要ありません。
Q: 表面仕上げに影響する要因は何ですか?
A: 層高、レーザーパラメーター、粉末サイズ分布、研磨などの後処理はすべて表面仕上げに影響します。Ra値は10μm以下が可能です。
Q: 機械的特性は何で決まるのですか?
A: 合金組成、粉末の品質と形態、プロセス・パラメーター、熱処理、HIPはすべて、最終的な印刷金属部品の特性に影響します。
Q: 金属粉末床印刷の価格はどのくらいですか?
A: プリンターシステムは$100,000から$1,000,000以上です。材料費は合金によって異なり、通常$100~$500/kgです。操業コストも高い。
Q: 中型部品の印刷にかかる時間は?
A: 造形速度は、パーツの形状、材料、パラメーター、プリンターモデルによって異なりますが、通常5~20cm3/時間です。靴箱サイズのパーツで5~15時間かかることもあります。
Q: 金属プリンターで作れる部品のサイズは?
A: 現在の最大造形量は500 x 500 x 500 mm程度ですが、より大きなシステムも開発中です。大きな部品は複数に分割することができます。
Q: 金属AMの後処理には何が必要ですか?
A: サポート除去、応力除去、機械加工、穴あけ、表面仕上げ、熱処理、時には熱間静水圧プレス。
シェアする
MET3DP Technology Co., LTDは、中国青島に本社を置く積層造形ソリューションのリーディングプロバイダーです。弊社は3Dプリンティング装置と工業用途の高性能金属粉末を専門としています。