3D Printed Test Coupons for Aerospace Certification
目次
Introduction: The Critical Role of Test Coupons in Aerospace Qualification and the Rise of Additive Manufacturing
The aerospace industry operates at the pinnacle of engineering, where performance, reliability, and safety are non-negotiable. Every component, from the smallest fastener to the largest structural element, undergoes rigorous scrutiny to ensure it can withstand the extreme conditions of flight. Central to this assurance process is the humble yet indispensable test coupon. These standardized specimens, often taking the form of tensile bars, fatigue samples, or fracture toughness specimens, are the bedrock upon which material properties are verified, manufacturing processes are validated, and ultimately, flight components receive their airworthiness certification from regulatory bodies like the Federal Aviation Administration (FAA) and the European Union Aviation Safety Agency (EASA). Without reliable data derived from test coupons, demonstrating compliance with stringent aerospace material specifications and performance requirements would be impossible. They are the empirical proof linking material science to safe and reliable flight.
Traditionally, these critical test coupons have been manufactured through subtractive methods – meticulously machined from larger blocks of wrought, forged, or cast materials. While this approach has served the industry for decades, it presents inherent challenges, particularly as aerospace manufacturing evolves. Machining is time-consuming, generates significant material waste (especially with expensive aerospace alloys like titanium), and, crucially, may not fully represent the nuanced microstructural characteristics of components made using newer, advanced manufacturing techniques.
入力 金属積層造形(AM), commonly known as metal 3Dプリンティング. This transformative technology, encompassing processes like Laser Powder Bed Fusion (L-PBF) and Electron Beam Melting (EBM), builds parts layer by layer directly from metal powder. Initially utilized for rapid prototyping, metal AM has rapidly matured into a viable production method for complex, high-performance aerospace components. Its adoption offers tantalizing possibilities: lightweight structures optimized through topology, consolidated part designs reducing assembly needs, and the ability to work with novel high-performance alloys.
However, the adoption of AM components in safety-critical aerospace applications necessitates an equally advanced approach to qualification and certification. This is where the synergy between metal AM and test coupon production becomes incredibly powerful. Utilizing metal 3D printing to create the very test coupons needed to validate the process offers significant advantages. It allows for:
- Accelerated Testing Cycles: Coupons can be printed rapidly, often alongside prototype parts or even embedded within production builds, drastically shortening the time required to generate crucial material data.
- Cost-Effective Development: Printing near-net-shape coupons reduces material waste and machining time, making iterative testing and material characterization more economically viable, especially during the development and qualification phases.
- Truly Representative Properties: Critically, AM-produced test coupons inherently possess the unique microstructure – including grain orientation, potential micro-porosity, and surface characteristics – that results from the layer-by-layer building process. This provides data that is far more representative of the final AM component’s actual performance compared to coupons machined from bulk material, which has a different thermomechanical history.
For aerospace engineers, procurement managers, and component certification suppliers, understanding how metal AM revolutionizes test coupon production is vital. It’s not just about printing a shape; it’s about leveraging a sophisticated manufacturing process to generate reliable, relevant data faster and more efficiently. As a leader in metal additive manufacturing solutions, Met3dp provides not only industry-leading 3D printing equipment known for accuracy and reliability but also the high-performance metal powders essential for producing dependable aerospace components and their corresponding test coupons. Embracing 3D printed test coupons is a strategic step towards streamlining additive manufacturing qualification and accelerating the adoption of innovative AM parts in the demanding aerospace sector. This blog post will delve into the specifics of using metal AM for aerospace test coupon production, focusing on recommended materials like AlSi10Mg and Ti-6Al-4V, design considerations, process control, and how to partner with the right aerospace material testing service provider.
What Are 3D Printed Aerospace Test Coupons Used For? Applications & Industries
3D printed metal test coupons are not merely replicas of their machined counterparts; they are purpose-built tools designed to interrogate and validate the specifics of the additive manufacturing process itself, providing critical data for engineers, designers, quality assurance teams, and regulatory bodies. Their applications within the aerospace and aviation industries are diverse and fundamental to the safe implementation of AM components. Key uses include:
- Material Characterization: This is perhaps the most fundamental application. AM processes create unique microstructures that differ significantly from traditional wrought or cast materials. 3D printed coupons are essential for establishing the baseline mechanical properties of a specific material (e.g., AlSi10Mg, Ti-6Al-4V) as produced by a specific AM machine using a defined set of process parameters. This includes determining:
- Tensile Properties: Ultimate Tensile Strength (UTS), Yield Strength (YS), Elongation (ductility), Reduction of Area. Tested according to standards like ASTM E8/E8M.
- Fatigue Properties: High Cycle Fatigue (HCF) and Low Cycle Fatigue (LCF) life under cyclic loading, crucial for components experiencing vibration or repeated stress cycles (e.g., engine parts, airframe structures). Tested according to standards like ASTM E606.
- 破壊靭性: Resistance to crack propagation, vital for damage tolerance assessments in critical structures. Tested using specific notched coupon geometries (e.g., Compact Tension specimens per ASTM E399).
- クリープ抵抗: Deformation under sustained load at elevated temperatures, relevant for engine components and hypersonic applications.
- 硬度: Surface hardness measurements (Rockwell, Vickers).
- Impact Toughness: Energy absorption capacity (Charpy, Izod tests).
- Process Validation & Optimization: Metal AM involves a complex interplay of variables – laser/electron beam power, scan speed, layer thickness, hatch spacing, build chamber atmosphere, powder characteristics, and more. Test coupons serve as a quantifiable output to validate that a chosen parameter set consistently produces material meeting the required specifications. They are used iteratively during process development to:
- Optimize parameters for desired density, microstructure, and mechanical properties.
- Establish Process Control Windows (PCWs).
- Compare results between different machines or facilities.
- Assess the effect of changes in powder batches or machine maintenance.
- Generate data for statistical process control (SPC).
- Lot Acceptance Testing (LAT): For production runs of AM aerospace components, test coupons are often built alongside the actual parts on the same build plate, or as part of a dedicated build using powder from the same batch. These “witness coupons” undergo testing to verify that the specific production lot meets the minimum acceptance criteria defined in the material or part specification. This ensures ongoing quality control and traceability for certified aerospace suppliers. Failure of LAT coupons can trigger investigation and potential rejection of the entire build batch.
- Equivalency Demonstrations: A significant hurdle for AM adoption is demonstrating that AM components can reliably meet or exceed the performance of legacy parts made from traditional materials. Test coupon data is used to compare the properties of the AM material against established databases (like the Metallic Materials Properties Development and Standardization – MMPDS handbook). While direct “equivalence” is complex due to microstructural differences, coupon testing provides the quantitative basis for substantiating performance claims and building confidence for AM material qualification.
- Certification Support: Ultimately, the data generated from 3D printed test coupons forms a critical part of the documentation package submitted to regulatory authorities (FAA, EASA, etc.) for type certification or supplemental type certification of aircraft incorporating AM parts. This data demonstrates compliance with airworthiness standards and provides objective evidence that the material and process are controlled and capable of producing safe, reliable components. Rigorous, statistically significant test coupon data is non-negotiable for achieving flight qualification.
- Research and Development (R&D): AM opens doors to new alloy development and complex geometries. Test coupons are indispensable tools for researchers exploring novel materials, understanding process-structure-property relationships in AM, and developing next-generation aerospace solutions.
対象業界:
The primary industries leveraging 3D printed aerospace test coupons are:
- 航空宇宙・防衛 Manufacturers of commercial aircraft, military aircraft, helicopters, missiles, satellites, and space launch vehicles. OEMs (Original Equipment Manufacturers like Boeing, Airbus, Lockheed Martin, Northrop Grumman, SpaceX) and their tiered suppliers heavily rely on this data.
- Aviation MRO (Maintenance, Repair, and Overhaul): Companies involved in repairing or replacing aircraft components can use AM for obsolete parts or improved repair solutions. Test coupons are essential for validating the quality and properties of these AM repairs or replacement parts.
For procurement managers and supply chain professionals within these industries, identifying capable test coupon manufacturers そして aerospace testing services proficient in metal AM is crucial. They need partners who understand the nuances of AM processes, possess the necessary quality certifications (like AS9100), and can reliably deliver accurate test specimens and data compliant with stringent aerospace requirements. Companies like Met3dp, with their focus on high-quality powders and advanced printing systems, play a vital role in enabling the production of reliable test coupons that underpin the qualification process.
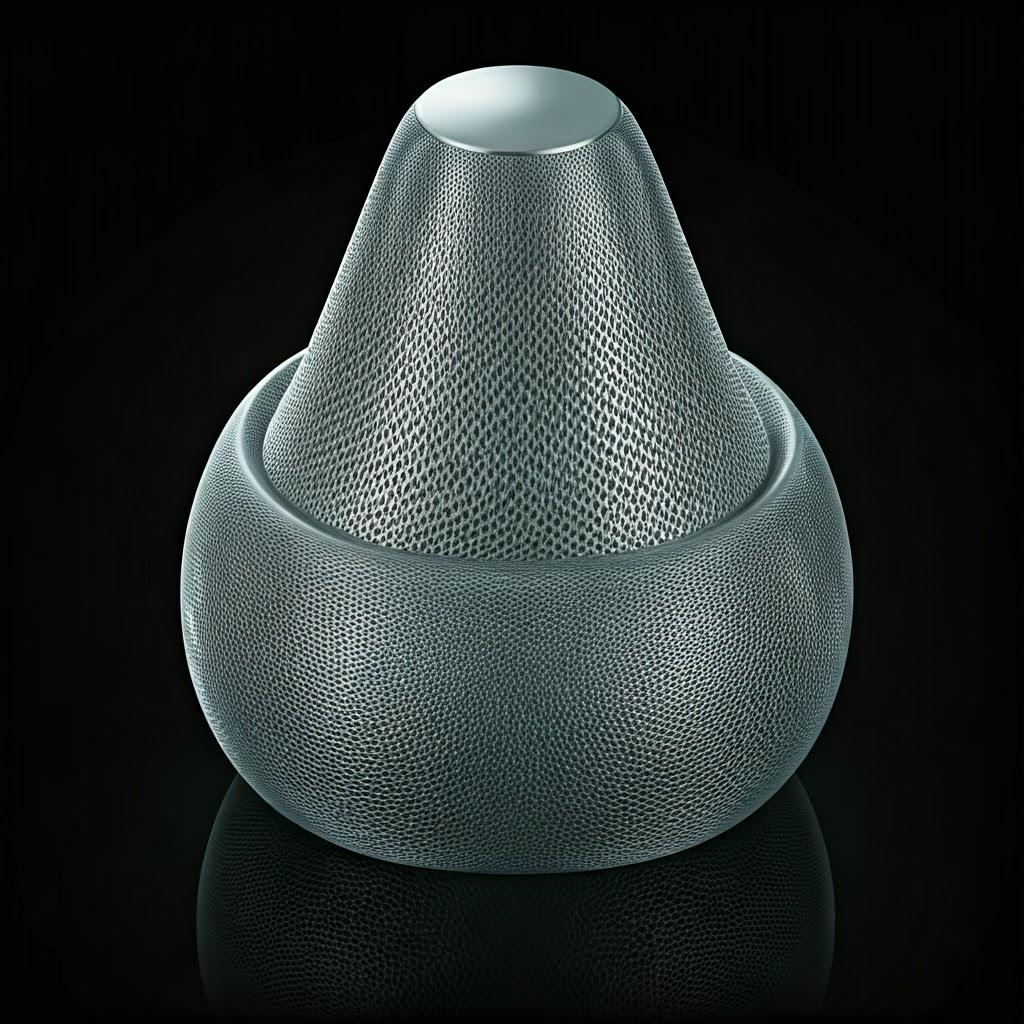
Why Use Metal 3D Printing for Aerospace Test Coupon Production? Key Advantages
While traditional machining of test coupons from wrought or cast stock remains a valid method, leveraging metal additive manufacturing specifically for coupon production offers a compelling suite of advantages, particularly relevant to the pace, cost pressures, and technical demands of the modern aerospace industry. These benefits streamline the path towards component qualification and unlock efficiencies throughout the development and production lifecycle.
- Speed and Lead Time Reduction: This is often the most immediate and impactful advantage.
- Traditional: Procuring bulk material, setting up complex machining operations, and producing coupons can take weeks or even months, especially for specialized alloys or geometries.
- アディティブ・マニュファクチャリング Test coupons can often be designed and printed within days. Furthermore, they can frequently be included directly on the build plate alongside prototype parts or even within the support structures of larger components (“in-situ witnesses”). This parallel processing drastically cuts down the total time required to get from design iteration to actionable material property data. For rapid prototyping aerospace projects, this acceleration is invaluable, allowing engineers to make faster decisions based on empirical results.
- Cost-Effectiveness (Especially for Specific Scenarios): While the cost-per-part in AM can be higher than traditional mass production, it often proves more economical for test coupon applications due to:
- 廃棄物の削減: AM is a near-net-shape process, using only the material needed for the coupon and its supports. Machining from bulk stock, conversely, can result in significant material loss (buy-to-fly ratio), which is particularly costly for expensive aerospace alloys like titanium or nickel superalloys.
- Lower Tooling Costs: AM requires no specific tooling, jigs, or fixtures beyond the build plate and standard post-processing equipment. Machining requires setup, potentially custom fixtures, and tool wear.
- Small Batch Efficiency: AM excels at producing small, customized batches efficiently. Running numerous small test matrices with varying parameters or orientations is far more cost-effective with AM than setting up multiple machining runs. This facilitates more comprehensive cost-effective material testing during development.
- Representative Material Properties: This is arguably the most significant technical advantage for qualifying actual AM components.
- Reflecting the As-Built State: Metal AM processes involve rapid melting and solidification, creating unique microstructures often characterized by columnar grains aligned with the build direction, potential for minor anisotropy (direction-dependent properties), and specific surface textures. Coupons printed using the exact same parameters, material batch, and machine as the final component will inherently possess these characteristics.
- Inaccurate Comparisons: Testing coupons machined from wrought or cast bar stock, which have undergone vastly different thermomechanical processing, provides data on the bulk material but not necessarily on how that material behaves after being processed through AM. Using AM coupons gives engineers and certification authorities higher confidence that the test data accurately reflects the performance of the actual AM part in service.
- Design Flexibility for Advanced Testing: AM’s layer-by-layer approach allows for the creation of complex geometries that are difficult or impossible to machine conventionally. While many standard coupons (like tensile bars) are geometrically simple, AM enables:
- Integrated Features: Printing coupons with specific notch geometries for fracture mechanics testing without the need for secondary machining steps like EDM (Electrical Discharge Machining).
- Lattice or Topology Optimized Coupons: Testing the specific properties of lightweight lattice structures intended for use in final components.
- Coupons with Internal Channels: For testing materials intended for applications like conformal cooling channels in tooling or heat exchangers.
- Material Efficiency and Sustainability: Beyond just cost savings from reduced waste, using less raw material aligns with increasing sustainability goals within the aerospace industry. AM’s near-net-shape capability minimizes the environmental footprint associated with material extraction and processing compared to subtractive methods. This contributes to aerospace supply chain optimization efforts.
- Process Monitoring Integration (“Witness Coupons”): Including test coupons within a production build serves as an integrated quality control check. These “witness coupons” experience the exact same build conditions as the parts they accompany. Testing these coupons provides direct validation of that specific build cycle’s quality, supplementing other process monitoring techniques (e.g., melt pool monitoring). This capability is highly valued by additive manufacturing service bureaus focused on production quality.
In summary, while machining remains relevant, producing aerospace test coupons via metal 3D printing offers compelling advantages in speed, cost (especially for development and small batches), and, most importantly, the ability to generate data that truly represents the material characteristics of the final additively manufactured component. Partnering with an experienced AM provider like Met3dp, who understands the intricacies of process control and offers high-quality materials, ensures that these advantages can be fully realized, accelerating innovation and certification in the demanding aerospace sector. Explore Met3dp’s metal 3D printing solutions to see how advanced AM technology can benefit your qualification process.
Recommended Materials (AlSi10Mg, Ti-6Al-4V) and Why They Matter for Aerospace Coupons
The choice of material for any aerospace component, including test coupons used for its qualification, is dictated by the performance requirements of the application – strength, weight, temperature resistance, corrosion resistance, and fatigue life are key considerations. Metal additive manufacturing offers a growing portfolio of aerospace-relevant alloys, but two stand out as workhorses for both components and the test coupons used to qualify them: AlSi10Mg (an aluminum-silicon-magnesium alloy) そして Ti-6Al-4V (a high-strength alpha-beta titanium alloy, often referred to as Grade 5).
The quality of the metal powder used in AM is paramount to achieving reliable, repeatable results, both in the final parts and in the test coupons. Key powder characteristics influencing printability and final material properties include:
- 真球度: Highly spherical powder particles flow easily and pack densely, leading to more uniform layers and reduced porosity.
- 流動性: Good flow ensures consistent powder deposition across the build plate. Measured using Hall Flowmeter or similar techniques.
- 粒度分布(PSD): A controlled PSD is crucial for dense packing and predictable melting behavior. Too many fine particles can impede flow and pose safety hazards, while too many coarse particles can lead to incomplete melting and porosity.
- Purity & Chemistry: Strict control over alloy composition and minimizing impurities (like oxygen and nitrogen, especially for titanium) is essential for achieving desired mechanical properties and consistency.
- Absence of Satellites: Small, irregular particles attached to larger spherical ones can negatively impact flowability and packing density.
Companies like Met3dp invest heavily in advanced powder production techniques, such as Vacuum Induction Melting Gas Atomization (VIGA) そして プラズマ回転電極プロセス(PREP). VIGA uses inert gas jets to atomize a stream of molten metal, creating spherical powders suitable for many alloys including AlSi10Mg. PREP involves rotating a consumable electrode at high speed within a plasma torch, melting the tip and centrifugally ejecting fine, highly spherical droplets, particularly effective for reactive materials like titanium alloys (Ti-6Al-4V) and ensuring high purity and sphericity. Sourcing powder from manufacturers with robust production and quality control systems, like Met3dp, is a critical first step for any aerospace AM supplier.
Let’s examine the two recommended materials in detail:
1. AlSi10Mg (Aluminum Alloy)
- 構成: Primarily aluminum, with significant additions of silicon (~9-11%) and magnesium (~0.2-0.45%).
- キー・プロパティ
- 軽量だ: Density around 2.68 g/cm³. Excellent for weight-sensitive aerospace applications.
- 優れた強度対重量比: Offers respectable strength, particularly after appropriate heat treatment.
- 優れた印刷適性: The silicon content improves fluidity in the melt pool, making it one of the easier aluminum alloys to process via L-PBF with high density.
- Good Thermal Properties: Decent thermal conductivity.
- 耐食性: Generally good, though can be further improved with surface treatments.
- Typical Aerospace Applications: While not typically used for highly critical primary structures, AlSi10Mg finds use in:
- Housings and enclosures for electronics.
- Brackets, clamps, and fixtures.
- Environmental Control System (ECS) ducting.
- Heat exchangers.
- Prototype parts.
- Drone components.
- Why Use AlSi10Mg for Test Coupons?:
- Process Validation: As one of the most common AM aluminum alloys, printing AlSi10Mg coupons is essential for validating the L-PBF process for a wide range of non-critical structural and thermal management parts.
- Cost-Effective Testing: Aluminum powder is significantly less expensive than titanium or nickel alloys, making AlSi10Mg coupons a cost-effective way to conduct extensive process optimization, parameter development, and routine quality control testing.
- Baseline Comparison: Provides a well-understood baseline for comparing new aluminum alloy developments.
- B2B Focus: Procurement managers looking for AlSi10Mg powder suppliers または aluminum AM services need partners who can demonstrate consistent powder quality and printing expertise for reliable component and coupon production.
2. Ti-6Al-4V (Titanium Alloy – Grade 5 / UNS R56400)
- 構成: Primarily titanium, with ~6% aluminum and ~4% vanadium. This alpha-beta alloy is the most widely used titanium alloy across industries.
- キー・プロパティ
- 卓越した強度対重量比: Superior to most steels and aluminum alloys, making it ideal for reducing structural weight while maintaining strength.
- 優れた耐食性: Forms a stable passive oxide layer, providing outstanding resistance in many aggressive environments (including saltwater).
- Good High-Temperature Performance: Retains useful strength up to around 300-400°C (approx. 600-750°F), suitable for certain engine components and airframe structures experiencing elevated temperatures.
- 疲労強度: Exhibits good resistance to fatigue loading, critical for long-service-life components.
- 生体適合性: Widely used in medical implants (though typically requires specific certifications not always relevant for aerospace coupons).
- Typical Aerospace Applications: Ti-6Al-4V is extensively used for critical, load-bearing components:
- Airframe structures (bulkheads, wing components, pylons).
- Engine components (blades, discs, casings – often in cooler sections).
- Landing gear components.
- High-strength fasteners.
- Hydraulic system components.
- Satellite components.
- Why Use Ti-6Al-4V for Test Coupons?:
- Qualifying Critical Parts: Given its use in safety-critical applications, rigorous testing using representative coupons is absolutely mandatory for qualifying any AM Ti-6Al-4V component for flight.
- Process Sensitivity: Titanium alloys are sensitive to process parameters and atmospheric contamination (oxygen, nitrogen). Coupon testing is vital for ensuring the AM process consistently delivers the required microstructure, low porosity, and mechanical properties.
- Understanding Anisotropy: Ti-6Al-4V often exhibits more pronounced anisotropy in AM compared to AlSi10Mg. Coupons built in different orientations (X, Y, Z, and potentially 45 degrees) are needed to fully characterize its directional properties.
- Validating Post-Processing: Heat treatments (like stress relief, beta annealing, and HIP) are critical for optimizing Ti-6Al-4V properties. Coupons must undergo the same treatments as the final parts to validate the effectiveness of these steps.
- B2B Focus: ソーシング Ti-6Al-4V Grade 5 powder specifically optimized for AM (low interstitials, controlled PSD) and partnering with an AS9100 certified titanium printing specialist is paramount for companies producing or procuring critical titanium components. A titanium additive manufacturing specialist like Met3dp understands the nuances of handling and processing this demanding material.
Material Property Comparison (Typical AM Values – Post-Processed):
プロパティ | 単位 | AlSi10Mg (Heat Treated – T6) | Ti-6Al-4V (Stress Relieved / HIP’d) | 備考 |
---|---|---|---|---|
密度 | g/cm3 (lb/in3) | ~2.68 (0.097) | ~4.43 (0.160) | Ti-6Al-4V is ~65% denser |
極限引張強さ(UTS) | MPa (ksi) | 300 – 480 (44 – 70) | 900 – 1150 (130 – 167) | Ti-6Al-4V significantly stronger |
Yield Strength (YS) | MPa (ksi) | 200 – 320 (29 – 46) | 800 – 1050 (116 – 152) | Ti-6Al-4V significantly higher YS |
破断伸度 | % | 3 – 10 | 6 – 18 | Alloy dependent, higher better ductility |
弾性係数 | GPa (Msi) | ~70 (10.2) | ~110-120 (15.9 – 17.4) | Ti-6Al-4V is stiffer |
最高使用温度 | °C (°F) | ~150-200 (300-390) | ~350-400 (660-750) | Approximate, application dependent |
Strength-to-Weight Ratio (UTS/Density) | Arbitrary Units | ~112 – 179 | ~203 – 260 | Ti-6Al-4V is superior |
Export to Sheets
Note: These are typical ranges. Actual properties depend heavily on specific AM process parameters, build orientation, heat treatment, and testing conditions. Always refer to specific material data sheets and qualification data.
In conclusion, AlSi10Mg and Ti-6Al-4V represent two pillars of current aerospace additive manufacturing. Using 3D printed test coupons made from these materials is not just recommended; it is essential for validating processes, ensuring quality, and ultimately achieving the rigorous certification standards demanded by the aerospace industry. Leveraging high-quality powders and advanced printing systems from providers like Met3dp is fundamental to generating the reliable coupon data needed to qualify next-generation aerospace components.
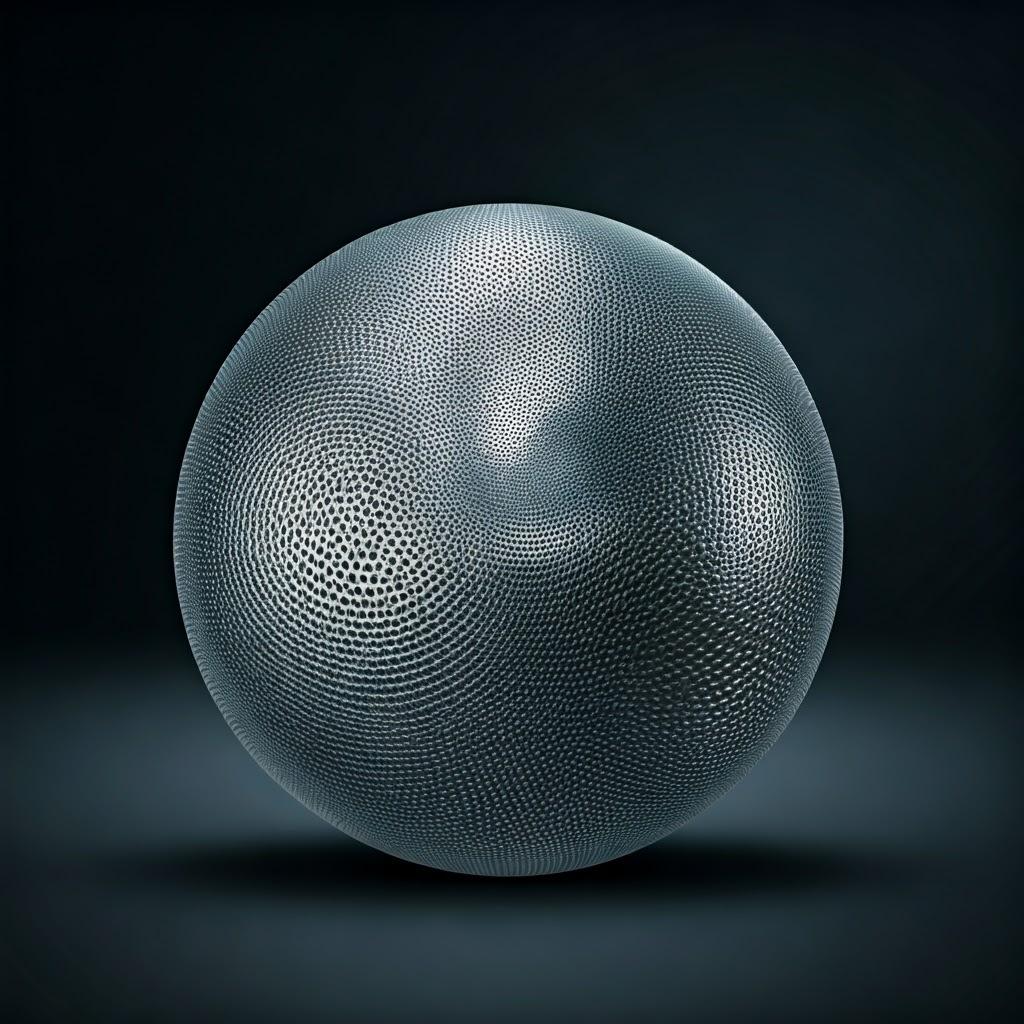
Design Considerations for Additive Manufacturing of Aerospace Test Coupons
While the fundamental purpose of a test coupon is standardized – to provide a specimen for measuring specific material properties under controlled conditions – designing coupons specifically for additive manufacturing requires careful consideration beyond merely replicating a traditional drawing. The layer-by-layer nature of AM introduces unique factors that influence the final microstructure, dimensional accuracy, surface condition, and ultimately, the validity of the test results. Effective AM design guidelines for test coupons focus on ensuring representativeness, printability, and testability. Engineers and designers involved in DFAM (Design for Additive Manufacturing) aerospace applications must address several key aspects:
- Adherence to Established Standards: The starting point for any test coupon design remains the internationally recognized standards. These documents dictate critical dimensions, geometries, and tolerances required for consistent and comparable testing across different labs and organizations. Key standards include:
- Tensile Testing: ASTM E8/E8M (Standard Test Methods for Tension Testing of Metallic Materials), ISO 6892-1. These define the geometry of round or flat tensile bars, including gauge length, grip section dimensions, and transition radii, ensuring stress concentration is minimized within the gauge section where measurement occurs.
- Fatigue Testing: ASTM E606 (Standard Test Method for Strain-Controlled Fatigue Testing), ASTM E466 (Standard Practice for Conducting Force Controlled Constant Amplitude Axial Fatigue Tests of Metallic Materials), ISO 1099. Fatigue specimens often require highly polished gauge sections and specific fillet radii to prevent premature failure initiation outside the area of interest.
- Fracture Toughness Testing: ASTM E399 (Standard Test Method for Linear-Elastic Plane-Strain Fracture Toughness K(Ic) of Metallic Materials), ASTM E1820 (Standard Test Method for Measurement of Fracture Toughness). These require precise notch geometries (e.g., in Compact Tension (CT) or Single Edge Notch Bend (SENB) specimens).
- AM Specific Standards: ASTM F3122 (Standard Guide for Evaluating Mechanical Properties of Metal Materials Made via Additive Manufacturing Processes), ISO/ASTM 52921 (Standard Terminology for Additive Manufacturing). The CAD model for the coupon must accurately reflect these standard geometries. Any deviation must be justified and documented, as it could affect the test outcome.
- Build Orientation and Anisotropy: This is arguably the most critical AM-specific design consideration. Due to the directional nature of heat input and solidification during processes like L-PBF and EBM, metal AM parts often exhibit anisotropic microstructures (typically columnar grains elongated in the build direction – Z-axis) and, consequently, anisotropic mechanical properties.
- 影響: Tensile strength, ductility, and fatigue life can vary significantly depending on whether the load is applied parallel (Z-direction), perpendicular (X or Y directions), or at an angle (e.g., 45 degrees) to the build direction.
- Design Strategy: Test coupons must be designed and oriented on the build plate to capture the material properties relevant to the loading conditions of the actual component being qualified. This often means printing coupons in multiple orientations:
- Vertical (Z): Load axis parallel to the build direction.
- Horizontal (X/Y): Load axis perpendicular to the build direction, lying in the build plane. Often X and Y are assumed similar but may be tested separately.
- 45 Degrees: Load axis at 45 degrees to the build direction, often representing an intermediate or potentially worst-case scenario for certain properties.
- について test specimen CAD preparation phase must include defining these build orientations clearly for the AM service provider. Understanding and characterizing this anisotropy is fundamental for reliable aerospace component design.
- サポート体制: Most metal AM processes require support structures for features overhanging the build plate beyond a certain angle (typically <45 degrees from horizontal) and to anchor the part firmly to the build plate, managing thermal stresses.
- Necessity: Cylindrical coupons printed horizontally (X/Y orientation) require extensive support along their length. Even vertically oriented coupons need support at the base connected to the build plate.
- Design Implications:
- Minimizing Contact on Critical Surfaces: Supports should ideally not contact the gauge length or critical radii of the coupon, as removal can damage the surface and affect test results (especially fatigue). Supports are typically placed on grip sections or sacrificial material.
- Ease of Removal: Supports should be designed for relatively easy removal without excessive force or heat input that could alter the coupon’s properties. Techniques include using smaller contact points or specialized support geometries (e.g., lattice or tree supports).
- 熱管理: Dense supports can act as heat sinks, potentially influencing the local microstructure. Support strategy should be consistent for comparable results.
- Collaboration between the designer and the additive manufacturing engineering services provider is key to optimizing support strategy.
- Thermal Management and Layout: Residual stress accumulation and potential warping are inherent challenges in metal AM due to intense, localized heating and cooling.
- 影響: Excessive residual stress can lead to distortion (making the coupon unusable or dimensionally inaccurate), cracking during the build or post-processing, and can significantly affect fatigue performance.
- Design/Layout Strategies:
- Optimized Nesting: Arranging coupons efficiently on the build plate to maximize throughput while ensuring adequate spacing to manage thermal load and allow for powder removal.
- Orientation Effects: Vertical orientations often experience different stress profiles than horizontal ones.
- Thermal Simulation: Advanced simulation tools can predict thermal gradients and stress accumulation, informing optimal orientation and support strategies, although this adds complexity and cost.
- Consistent Placement: For comparative studies, placing coupons in similar locations on the build plate across different builds can help minimize variability due to thermal location effects.
- Feature Resolution and Printability: AM processes have limitations on the minimum size of features they can accurately produce.
- Minimum Wall Thickness: Typically around 0.3-0.5 mm, depending on the machine and material.
- Hole Diameters: Small holes can be challenging to print accurately and may require subsequent drilling/reaming.
- Fillet Radii: Sharp internal corners can be difficult to print accurately and act as stress risers; appropriate fillet radii per standards must be achievable.
- Notch Geometry: For fracture toughness or notched fatigue specimens, the AM process must be capable of accurately reproducing the specified notch root radius, as this is critical to the stress concentration factor. Post-process machining (e.g., wire EDM) may be required for very sharp notches. The design must respect the chosen AM system’s capabilities.
- CAD File Preparation and Documentation: High-quality input data is essential.
- File Format: STL is common but can have resolution issues. 3MF is becoming preferred as it carries more information (e.g., orientation, material).
- Watertight Geometry: CAD models must be manifold (“watertight”) with no errors (e.g., inverted normals, non-manifold edges).
- Associated Drawings: A traditional 2D drawing should accompany the CAD file, clearly specifying critical dimensions, tolerances (using GD&T), required surface finishes (especially on gauge sections), material specification, required post-processing (heat treatments, HIP), and importantly, the intended build orientation(s).
Successfully designing AM test coupons requires a blend of understanding material testing standards, the nuances of the AM process, and the specific requirements of the aerospace component being qualified. Close collaboration with experienced additive manufacturing engineering services providers, who understand the interplay between design, process, and material outcomes, is highly recommended.
Achieving Precision: Tolerance, Surface Finish, and Dimensional Accuracy in AM Coupons
While AM offers design freedom and speed, achieving the dimensional accuracy, tight tolerances, and specific surface finishes required for reliable aerospace test coupons demands careful process control and often necessitates post-processing. The precision of the final coupon directly impacts the validity of the derived mechanical property data, as inaccuracies in dimensions affect stress calculations, and surface condition heavily influences fatigue life. Stakeholders involved in aerospace dimensional control must understand the capabilities and limitations of metal AM in this regard.
- Typical Tolerances in Metal AM: The achievable dimensional accuracy in metal AM processes like L-PBF and EBM depends on numerous factors but generally falls within these ranges for as-built parts:
- General Tolerances: Often cited as approximately +/- 0.1 mm to +/- 0.2 mm (0.004″ to 0.008″) for smaller dimensions, or +/- 0.1% to +/- 0.2% of the nominal dimension for larger parts.
- Factors Influencing Accuracy:
- Machine Calibration: Accuracy of laser/beam positioning, galvo systems, and Z-axis movement.
- Thermal Effects: Shrinkage during cooling, residual stress causing minor warping or distortion.
- スキャン戦略: The pattern used to melt the powder can influence local shrinkage and stress.
- パウダーの特徴 Layer packing density and consistency.
- Part Size and Geometry: Larger parts or complex geometries may exhibit greater deviation.
- Location on Build Plate: Thermal variations across the plate can lead to minor differences.
- While AM providers like Met3dp strive for industry-leading print volume, accuracy and reliability, inherent process physics impose limits on as-built tolerances compared to precision machining. For standard test coupons requiring tolerances tighter than these typical values (e.g., on gauge diameter or width), post-machining is usually necessary.
- Surface Finish (Roughness – Ra, Rz): The as-built surface finish of metal AM parts is significantly rougher than machined surfaces.
- Typical Values: As-built surface roughness (Ra) can range widely, often from 5 µm to 25 µm (200 µin to 1000 µin) or even higher, depending on the process, material, parameters, and surface orientation relative to the build direction.
- Orientation Dependence:
- Up-skin Surfaces: Top-facing surfaces tend to be smoother.
- Down-skin Surfaces: Surfaces facing downwards (supported) are typically rougher due to contact with support structures and partially melted powder particles adhering.
- Vertical Walls: Show roughness related to layer lines.
- Curved/Angled Surfaces: Exhibit a “stair-stepping” effect, contributing to roughness.
- Parameter Influence: Layer thickness (thicker layers = rougher), beam energy input, and scan speed all affect the final surface topography.
- Critical Importance for Fatigue: Surface roughness is a major factor influencing fatigue life. Rough surfaces contain microscopic notches and valleys that act as stress concentrators, leading to premature crack initiation and significantly lower fatigue strength compared to smooth, polished surfaces. Therefore, as-built surfaces are generally unsuitable for generating reliable fatigue data representative of a component’s intrinsic material capability. Gauge sections of fatigue coupons must typically be machined and/or polished to a specified low Ra value (e.g., < 0.4 µm or as defined by the standard/specification). Understanding surface finish additive manufacturing capabilities and limitations is crucial for test program planning.
- Achieving Tighter Tolerances and Finishes: When as-built tolerances or surface finish do not meet the requirements specified in the test standard or component drawing (which is common for critical dimensions like gauge diameter/width and grip sections), post-processing is essential:
- CNC Machining: Turning (for round bars), milling (for flat bars or features), or grinding can achieve tolerances of +/- 0.01 mm (0.0004″) or better and surface finishes (Ra) well below 0.8 µm (32 µin). This ensures:
- Accurate cross-sectional area for stress calculations.
- Proper fit and alignment in test machine grips.
- Smooth gauge surface required for valid fatigue testing.
- ハイブリッド製造: Some workflows integrate AM and machining in sequence, potentially machining critical features between AM steps or using AM to create near-net shapes that are then finish-machined.
- CNC Machining: Turning (for round bars), milling (for flat bars or features), or grinding can achieve tolerances of +/- 0.01 mm (0.0004″) or better and surface finishes (Ra) well below 0.8 µm (32 µin). This ensures:
- Dimensional Inspection and Metrology: Verification of the final coupon dimensions before destructive testing is a critical quality step.
- 方法:
- Coordinate Measuring Machines (CMM): High-accuracy tactile or optical measurement for verifying dimensions against the CAD model or drawing.
- Structured Light / Laser Scanning: Capturing the full 3D geometry for comparison to CAD, useful for complex shapes or overall form deviation.
- Hand Tools: Calipers and micrometers for quick checks of basic dimensions (use with caution for final acceptance).
- GD&T: Geometric Dimensioning and Tolerancing should be used on coupon drawings to define not just size tolerances but also form, orientation, and location tolerances where critical (e.g., parallelism of grip flats, concentricity of gauge section).
- Pre-Test Verification: Ensures that any dimensional deviations are known and documented, or that non-conforming coupons are rejected before costly testing proceeds. Robust metrology for 3D printing is a key capability for any serious aerospace AM supplier.
- 方法:
Achieving the required precision for aerospace test coupons using AM often involves a combination of optimized printing strategies and planned post-processing steps, particularly machining. Understanding the interplay between as-built capabilities and finishing operations is key to obtaining accurate, reliable, and certifiable material property data that meets stringent aerospace tolerance standards.
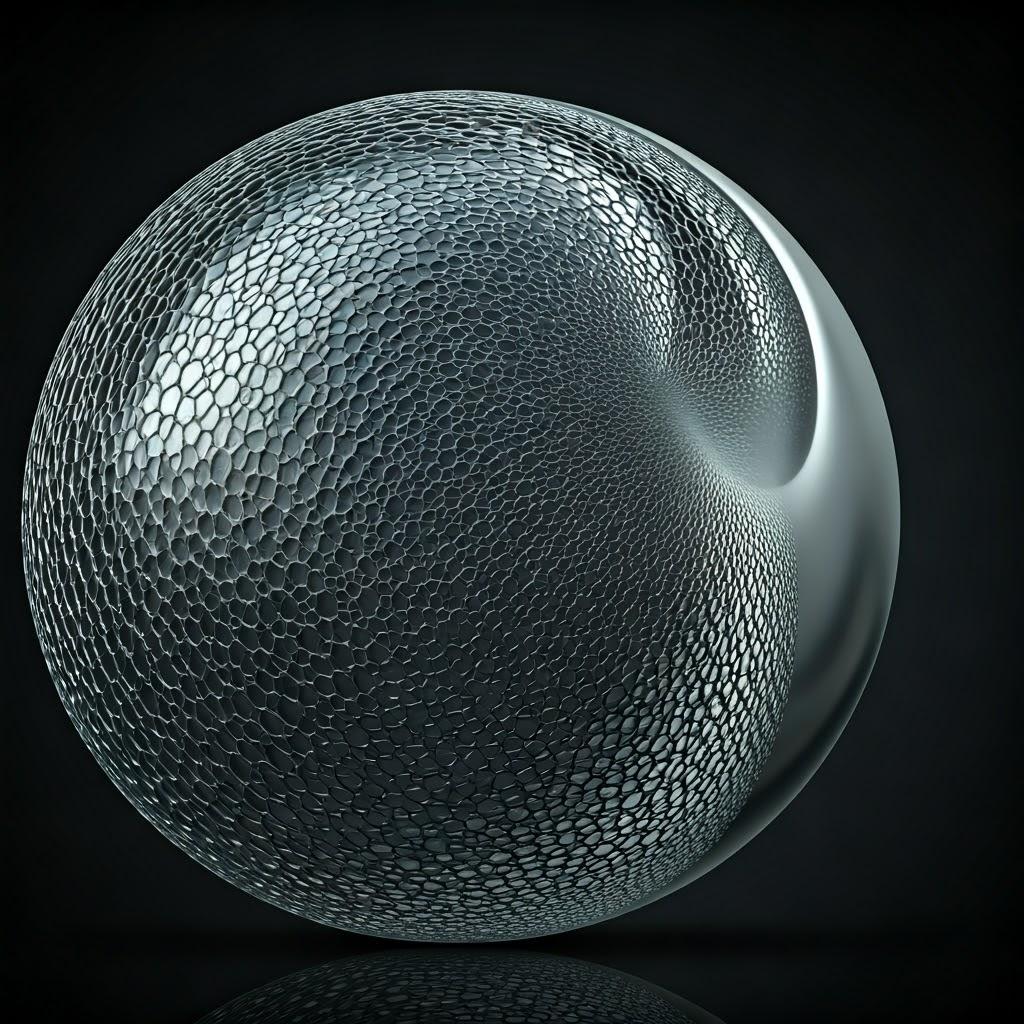
Post-Processing Requirements for 3D Printed Aerospace Test Coupons
Producing a dimensionally accurate test coupon via metal AM is only the first step. The as-built part, directly off the printer, often possesses internal stresses, potential micro-porosity, rough surfaces, and attached support structures that make it unsuitable for immediate, reliable testing, especially for demanding aerospace applications. A sequence of carefully controlled post-processing steps is typically mandatory to relieve stress, consolidate the material, remove supports, achieve final dimensions and surface finish, and verify internal quality. These steps are not optional extras; they are integral to achieving the desired material properties and ensuring the test coupon accurately represents a properly processed aerospace component. Leading providers of metal AM post-processing solutions offer these critical services.
- 1. Stress Relief (SR): This is almost universally the first critical step after the build finishes and before removing parts from the build plate (especially for high-stress materials like Ti-6Al-4V).
- 目的 The rapid heating/cooling cycles inherent in AM induce significant internal residual stresses. SR heat treatment heats the part uniformly to a temperature below its transformation point, holds it for a specific time, and then slowly cools it. This allows stresses to relax through microscopic plastic deformation, significantly reducing the risk of:
- Distortion or cracking when parts are cut from the build plate.
- Warping during subsequent machining.
- Premature failure under load due to superimposed residual stresses.
- Typical Cycles:
- AlSi10Mg: Often ~2 hours at 300°C (572°F).
- Ti-6Al-4V: Often 1-4 hours at 600-800°C (1112-1472°F) in a vacuum or inert atmosphere to prevent oxidation.
- Importance: Skipping or improperly performing SR can compromise the entire part and subsequent test results.
- 目的 The rapid heating/cooling cycles inherent in AM induce significant internal residual stresses. SR heat treatment heats the part uniformly to a temperature below its transformation point, holds it for a specific time, and then slowly cools it. This allows stresses to relax through microscopic plastic deformation, significantly reducing the risk of:
- 2. Support Structure Removal: Once stress-relieved (and typically cooled), the coupons need to be separated from the build plate and have their support structures removed.
- 方法:
- Mechanical: Wire EDM (precise but slower), bandsaw (faster but less precise), manual breaking/cutting (requires care).
- Build Plate Cutting: Often done first using wire EDM or sawing to separate the entire build job.
- 検討する: Removal methods must avoid damaging the coupon itself, particularly the gauge section. Nicks, scratches, or excessive localized heat input during removal can act as failure initiation sites. Careful manual finishing or follow-up machining of removal witness marks is often needed.
- 方法:
- 3. Heat Treatment (Beyond Stress Relief): Depending on the alloy and application requirements, further heat treatments are often necessary to optimize microstructure and mechanical properties.
- 熱間静水圧プレス(HIP): This is standard practice for critical aerospace components, especially those made from Ti-6Al-4V or nickel superalloys, and thus essential for the corresponding test coupons.
- プロセス Parts are subjected to high temperature (just below melting point) and high-pressure inert gas (e.g., Argon at 100 MPa / 15 ksi or higher) in a specialized HIP vessel.
- 目的 The combination of heat and pressure causes internal voids (gas porosity, lack-of-fusion defects) to collapse and diffusion bond shut, significantly increasing material density, ductility, fatigue life, and property consistency (reducing scatter in test results).
- Requirement: Often mandated by aerospace specifications for fatigue-critical or fracture-critical AM parts. HIP services AM providers with aerospace qualifications (e.g., NADCAP) are essential.
- Solution Annealing & Aging: Applicable to precipitation-hardenable alloys like AlSi10Mg (T6 treatment) or certain titanium/nickel alloys.
- プロセス Involves heating to dissolve alloying elements into solid solution, quenching (rapid cooling) to lock them in, and then aging (re-heating to a lower temperature) to allow controlled precipitation of fine strengthening phases.
- 目的 Significantly increases strength and hardness compared to the as-built or stress-relieved state. The specific cycle (temperatures, times) is alloy-dependent and must match the treatment applied to the final component.
- Annealing (e.g., for Ti-6Al-4V): Various annealing cycles (e.g., mill anneal, duplex anneal, beta anneal) can be used to modify the alpha-beta microstructure to optimize for specific properties like fracture toughness, creep resistance, or fatigue strength.
- 熱間静水圧プレス(HIP): This is standard practice for critical aerospace components, especially those made from Ti-6Al-4V or nickel superalloys, and thus essential for the corresponding test coupons.
- 4. Machining to Final Dimensions: As discussed previously, machining is frequently required to achieve the tight tolerances and smooth surface finishes needed for reliable testing.
- Areas: Primarily grip sections (for proper test machine interfacing) and gauge sections/lengths (for accurate stress calculation and required surface finish, especially for fatigue).
- Operations: CNC turning, milling, grinding. Care must be taken to avoid excessive heat input or surface damage during machining 3D printed parts.
- 5. Surface Finishing: Beyond machining, additional surface treatments may be specified depending on the test type.
- Bead Blasting/Grit Blasting: Creates a uniform matte finish, cleans the surface, and can introduce beneficial compressive residual stresses (depending on media and parameters).
- ショットピーニング: A controlled process using spherical media to bombard the surface, inducing significant compressive residual stress, which markedly improves fatigue life. Often applied to fatigue coupons after final machining.
- 研磨: Mechanical or electrochemical polishing to achieve very low surface roughness (e.g., Ra < 0.2 µm) required for high-cycle fatigue (HCF) testing, minimizing surface-initiated failure.
- Chemical Etching: Sometimes used to reveal microstructure for metallographic examination after testing, or potentially as part of a cleaning/inspection process.
- 6. Non-Destructive Testing (NDT): Before destructive mechanical testing, NDT is often performed on the finished coupons (or representative samples) as a final quality check, especially for critical qualification programs.
- X-Ray Computed Tomography (CT Scanning): Provides a 3D view of the coupon’s internal structure, capable of detecting, locating, and sometimes quantifying internal defects like porosity or inclusions without destroying the sample. Essential for understanding defect populations that HIP may not fully close or for verifying HIP effectiveness.
- Fluorescent Penetrant Inspection (FPI): A surface inspection method used after machining/polishing to detect surface-breaking cracks or defects that could invalidate a test. Requires meticulous cleaning and inspection processes, often under NADCAP control for aerospace heat treatment NADCAP and NDT certified providers.
The specific sequence and parameters of these post-processing steps must be carefully defined, controlled, documented, and aligned with the processing route of the actual aerospace component being qualified. Partnering with an AM service provider who offers comprehensive, aerospace-certified post-processing capabilities, or has strong relationships with qualified NDT inspection additive manufacturing partners, is crucial for obtaining meaningful and certifiable test coupon results.
Common Challenges in AM Test Coupon Production and Mitigation Strategies
While metal additive manufacturing offers transformative potential for producing aerospace test coupons, the process is complex and not without its challenges. Achieving consistent, reliable coupons that accurately reflect the properties of a well-controlled AM process requires vigilance and proactive mitigation strategies. Understanding these potential pitfalls is crucial for both AM service providers and the engineers or procurement managers relying on the resulting data. Many challenges relate directly to achieving optimal metal AM quality assurance.
- 1. Porosity (Internal Voids): This is one of the most common defects in metal AM.
- 種類だ:
- Lack of Fusion (LoF): Irregularly shaped voids occurring between scan tracks or layers due to insufficient energy input (low power, high speed) failing to fully melt and fuse the powder.
- Keyhole Porosity: Spherical voids caused by excessive energy density, leading to metal vaporization and instability in the melt pool, trapping gas.
- Gas Porosity: Spherical voids caused by dissolved gas (e.g., Argon from the build chamber, or Hydrogen in the powder) coming out of solution during solidification, or trapped within hollow powder particles.
- 影響: Porosity reduces the effective load-bearing cross-section and acts as a stress concentrator, significantly degrading mechanical properties, especially ductility and fatigue life (often the life-limiting factor).
- Mitigation Strategies:
- プロセスパラメータの最適化 Rigorous Design of Experiments (DoE) to establish robust parameter sets (power, speed, hatch spacing, layer thickness) that ensure full melting and stable melt pool dynamics. Use of advanced melt pool monitoring システムである。
- High-Quality Powder: Using powder with high sphericity, controlled PSD, good flowability, and low internal gas content minimizes potential sources of porosity. Sourcing from reputable suppliers like Met3dp, known for their advanced powder making system, is key.
- 熱間静水圧プレス(HIP): Highly effective at closing LoF and gas porosity through high temperature and pressure, significantly improving internal soundness. (Note: HIP may not close pores open to the surface).
- 種類だ:
- 2. Anisotropy (Directional Properties): As previously mentioned, the inherent layer-wise solidification often leads to columnar grain growth aligned with the thermal gradient (typically the Z-axis), resulting in properties that vary with build direction.
- 影響: Tensile strength, yield strength, ductility, and fatigue properties can differ between the build (Z) and transverse (X/Y) directions, sometimes substantially (e.g., ductility can be lower in Z).
- Mitigation Strategies:
- 特徴づけ: Test coupons must be built and tested in multiple orientations (X, Y, Z, 45°) relevant to the component’s loading to fully understand and quantify the anisotropy.
- Design Allowables: Use direction-specific material property allowables in component design and analysis.
- Process Development: Advanced strategies (e.g., modifying scan patterns, using beam modulation) might aim to promote more equiaxed (non-directional) grain structures, but this is complex and often alloy-specific.
- 熱処理: Certain heat treatments can modify the microstructure and potentially reduce (but rarely eliminate) anisotropy.
- 3. Residual Stress, Distortion, and Cracking: The intense thermal cycles generate significant residual stresses.
- 影響: Can cause distortion (warping) during the build or after removal from the build plate, lead to parts detaching from supports or the plate, cause cracking (especially in brittle alloys or complex geometries), and negatively impact fatigue life.
- Mitigation Strategies:
- Optimized Scan Strategies: Using techniques like island/checkerboard scanning breaks up long scan vectors, reducing stress build-up.
- 熱管理: Preheating the build plate or chamber reduces thermal gradients.
- Robust Support Structures: Proper supports anchor the part and help manage stress.
- Stress Relief (SR): Performing an appropriate SR heat treatment immediately after the build and before plate removal is critical.
- Simulation: Process simulation tools can help predict stress distribution and optimize build layout and supports.
- 4. Surface Roughness Variability and Defects: As-built surfaces are inherently rougher than machined ones and can contain defects.
- 影響: High or inconsistent roughness significantly affects fatigue performance. Surface defects like partially melted particles or witness marks from support removal can act as crack initiation sites.
- Mitigation Strategies:
- Parameter Optimization: Fine-tuning parameters (e.g., contour passes, smaller layer thickness) can improve surface finish, often at the cost of build speed.
- Orientation Control: Avoid placing critical surfaces in down-skin or heavily supported orientations if possible.
- 後処理: Plan for machining, blasting, or polishing of critical surfaces (especially for fatigue coupons) to achieve the required finish. Careful support removal techniques.
- 5. Consistency and Repeatability: Ensuring that coupons produced in different builds, on different machines, or even at different facilities yield statistically equivalent results is paramount for qualification and production control. This requires robust additive manufacturing process validation.
- 影響: Lack of repeatability undermines confidence in the process and the validity of the data for certification.
- Mitigation Strategies:
- Strict Quality Management System (QMS): Implementing and adhering to rigorous QMS procedures (e.g., AS9100) covering all aspects from powder handling to post-processing and inspection.
- Machine Calibration & Maintenance: Regular, documented calibration and preventative maintenance of AM machines.
- Process Monitoring & Control: Utilizing melt pool monitoring, sensor data, and SPC to track process stability. Defining and locking down validated process parameters.
- Powder Management: Strict protocols for powder receiving inspection, storage, handling, blending/recycling, and batch traceability. Regular powder testing.
- Operator Training: Ensuring operators are well-trained and follow standard operating procedures (SOPs).
- Environmental Control: Maintaining stable temperature and humidity in the operating environment.
- Leveraging Met3dp technical support and their focus on reliable printing systems contributes to achieving higher consistency.
- 6. Material Contamination: Particularly critical for reactive alloys like Ti-6Al-4V.
- 影響: Pickup of oxygen, nitrogen, or hydrogen from the build atmosphere or contaminated powder can lead to embrittlement, reducing ductility and fracture toughness. Cross-contamination between different alloy types if machines are not properly cleaned.
- Mitigation Strategies:
- Atmospheric Control: Maintaining high-purity inert gas (Argon) atmosphere with low O2 levels (<100-1000 ppm, depending on spec). Continuous monitoring.
- パウダーハンドリング: Using dedicated equipment, sealed containers, inert gas handling for reactive powders. Strict powder traceability and testing for contaminants.
- Machine Cleaning: Thorough cleaning protocols between different material builds.
Successfully navigating these challenges requires deep process understanding, meticulous control, advanced equipment, and a strong quality culture. Partnering with an experienced AM service provider like Met3dp, committed to reducing defects in metal 3D printing through advanced technology and expertise, significantly increases the probability of producing high-quality, reliable aerospace test coupons essential for certification.
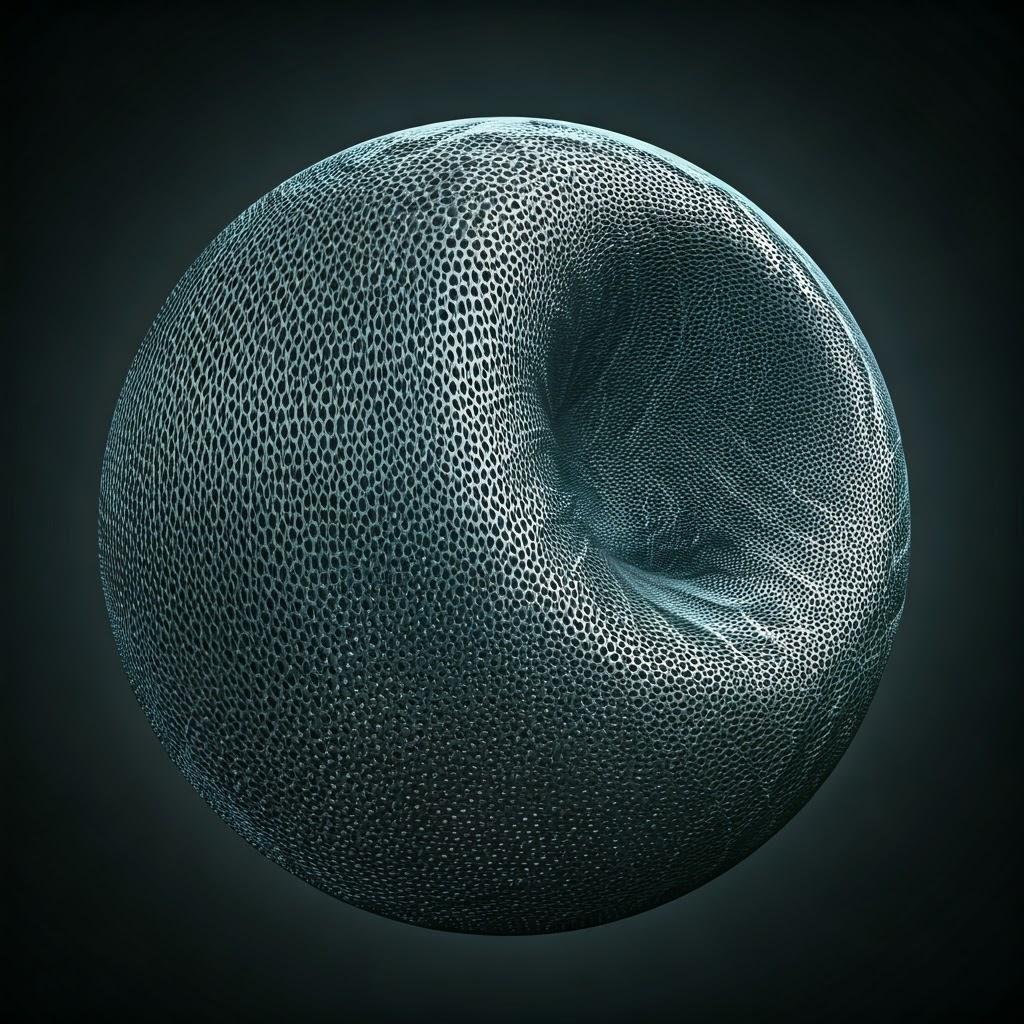
How to Choose the Right Metal 3D Printing Service Provider for Aerospace Coupons
Selecting a partner for producing critical aerospace test coupons via metal additive manufacturing is a decision that extends far beyond simply finding a vendor with a 3D printer. The stakes are incredibly high; the data generated from these coupons underpins component airworthiness and flight safety. Therefore, aerospace engineers, quality managers, and procurement professionals must conduct rigorous due diligence to qualify aerospace AM suppliers. Choosing the right partner involves evaluating a combination of technical capabilities, quality systems, material expertise, process control, and a proven track record within the demanding aerospace sector. Here’s a comprehensive guide on what to look for when undertaking metal AM service bureau evaluation:
- 1. Aerospace Certifications (AS9100 is Mandatory): This is the non-negotiable starting point.
- AS9100: This standard builds upon ISO 9001 but includes specific, stringent requirements for quality management systems within the aviation, space, and defense industries. Certification to AS9100 demonstrates a provider’s commitment to:
- Rigorous configuration management and traceability.
- Risk management processes.
- Specific process controls relevant to aerospace manufacturing.
- Formalized procedures for non-conformance management and corrective action.
- Verification of purchased products (including critical materials like metal powders).
- NADCAP Accreditation: While AS9100 covers the overall QMS, NADCAP (National Aerospace and Defense Contractors Accreditation Program) provides specific accreditation for special processes. For AM providers, relevant NADCAP accreditations might include Heat Treating, Non-Destructive Testing (NDT), Materials Testing Laboratories, and potentially Welding (which AM is sometimes considered under). If a provider performs these critical post-processing or testing steps in-house, NADCAP accreditation provides an extra layer of assurance regarding their process control and technical competence.
- Action: Always request copies of current AS9100 certificates and any relevant NADCAP accreditations. Verify their scope covers additive manufacturing and the specific materials you require.
- AS9100: This standard builds upon ISO 9001 but includes specific, stringent requirements for quality management systems within the aviation, space, and defense industries. Certification to AS9100 demonstrates a provider’s commitment to:
- 2. Proven Material Expertise (AlSi10Mg, Ti-6Al-4V, and Beyond): The provider must demonstrate deep knowledge of the specific aerospace alloys you intend to use.
- 経験: How long have they been processing AlSi10Mg and Ti-6Al-4V via AM? Do they have established, validated parameter sets?
- Powder Management: What are their procedures for sourcing, inspecting, handling, storing, and recycling metal powders? How do they ensure powder quality and prevent contamination or degradation over time? Do they test powder chemistry and properties regularly? Providers like Met3dp, who manufacture their own high-quality powders using advanced methods like Gas Atomization and PREP, often have a deeper understanding of material characteristics.
- Metallurgical Support: Do they have metallurgists or materials scientists on staff who understand the process-structure-property relationships in AM? Can they provide guidance on heat treatment and expected properties?
- 3. Machine Capabilities, Technology, and Maintenance: The quality of the equipment and its upkeep is crucial.
- テクノロジー: Do they utilize appropriate AM technology (L-PBF, EBM) suitable for your material and application? Are their machines from reputable manufacturers?
- Condition & Calibration: Are the machines well-maintained according to OEM recommendations? Is there documented evidence of regular calibration (e.g., laser power, scanner accuracy, oxygen sensors)?
- Capacity & Redundancy: Do they have sufficient machine capacity to meet your lead time requirements? Do they have multiple machines capable of running your materials, providing redundancy in case of equipment failure? Companies offering industry-leading print volume, accuracy and reliability, like Met3dp, invest heavily in their machine technology. Explore Met3dp’s product range to understand their equipment offerings.
- 4. Robust Process Control and Quality Management System (QMS): Go beyond the certificate and probe the details of their QMS implementation for AM.
- Traceability: Can they demonstrate end-to-end traceability from the raw powder batch through build parameters, post-processing steps, inspection, testing, and final coupon identification?
- Build Documentation: What data is recorded for each build (e.g., machine parameters, sensor data like melt pool monitoring, gas quality, temperature logs)? How is this data stored and linked to the produced parts/coupons?
- Parameter Control: How are validated process parameters controlled and deployed? How are changes managed?
- Statistical Process Control (SPC): Do they utilize SPC techniques to monitor process stability and capability?
- Non-Conformance: What is their documented process for handling non-conforming material or build deviations?
- 5. Comprehensive Post-Processing and Testing Network: AM coupons almost always require post-processing.
- In-House vs. Subcontracted: Understand which steps (SR, HIP, machining, finishing, NDT, mechanical testing) are performed in-house versus subcontracted.
- Subcontractor Qualification: If subcontracted, how does the provider qualify and manage these vendors? Are the subcontractors also AS9100/NADCAP certified for the relevant processes?
- Integrated Management: Does the provider manage the entire workflow seamlessly, ensuring proper handling and process control between steps?
- Testing Capabilities: Can they perform or manage the required mechanical tests (tensile, fatigue, fracture toughness, etc.) according to ASTM/ISO standards? Are their testing labs (in-house or external) accredited to ISO 17025 (General requirements for the competence of testing and calibration laboratories)? Can they provide certified test reports?
- 6. Experience, Track Record, and Technical Support: Look for evidence of successful execution.
- Aerospace Focus: Have they worked with other aerospace OEMs or suppliers? Can they provide relevant (non-confidential) case studies or references?
- Qualification Support: Do they have experience supporting material or process qualification programs according to aerospace standards (e.g., MMPDS data generation)?
- Engineering Collaboration: How capable is their engineering team? Can they provide Design for Additive Manufacturing (DFAM) support, help optimize coupon design for printability, or troubleshoot build issues? A provider like Met3dp, with decades of collective expertise and offering 医療、航空宇宙、自動車などの業界向けアプリケーション開発サービス, brings significant value here.
- 7. Lead Time, Capacity, and Communication: Practical considerations are important.
- Realistic Timelines: Can they provide clear and realistic lead time estimates based on your requirements (quantity, material, post-processing, testing)?
- Capacity Planning: How do they manage machine scheduling and workload to meet promised delivery dates?
- Communication: Are they responsive, transparent, and easy to communicate with?
- 8. Cost vs. Overall Value: When involved in procurement aerospace 3D printing, resist the temptation to select solely based on the lowest price per coupon.
- Total Cost of Ownership: Consider the potential costs associated with poor quality, delays, failed tests, or lack of proper documentation. The cost of a failed qualification program far outweighs minor savings on coupon production.
- Value Proposition: Evaluate the provider’s overall value, including their expertise, reliability, quality systems, risk mitigation, and ability to serve as a true partner in your qualification efforts.
正しい選択 AM partner is a strategic decision that directly impacts the success and timeline of aerospace component qualification. A thorough evaluation based on these criteria will help ensure you partner with a provider capable of delivering high-quality, reliable, and fully traceable test coupons that meet the stringent demands of the aerospace industry.
Understanding Cost Factors and Lead Times for AM Test Coupon Production
Budgeting and planning for additive manufacturing projects, including the production of essential test coupons, requires a clear understanding of the factors that drive costs and influence delivery timelines. While AM offers speed advantages, the production of high-quality, aerospace-compliant coupons involves multiple process steps, each contributing to the overall expense and schedule. A detailed metal 3D printing cost analysis considers the following elements:
Key Cost Drivers:
- 材料費:
- Powder Price: This varies significantly by alloy. Aerospace-grade Ti-6Al-4V powder is substantially more expensive (often 5-10x or more) per kilogram than AlSi10Mg powder due to raw material costs and complex production processes (like PREP) needed to ensure purity and quality. Costs for nickel superalloys or other exotic materials can be even higher.
- Powder Usage & Waste: While AM is near-net-shape, some powder is inevitably lost during handling, becomes non-recyclable after multiple uses (due to morphology changes or contamination limits), or remains unfused in the build chamber. Buy-to-fly ratios are much better than machining, but material consumption is still a factor. Powder refresh strategies (mixing used powder with virgin powder) impact overall cost.
- AM Machine Time: This is often the most significant cost component in the AM process itself.
- Calculation: Typically charged based on the total build time ($/hour or $/build). Build time is primarily determined by the height of the tallest part on the build plate (more layers = more time) and the time per layer (recoating time + laser/beam scanning time).
- Influencing Factors:
- Coupon Orientation: Vertically oriented coupons generally result in taller builds and thus longer machine times compared to horizontally oriented coupons (though horizontal coupons may require more support).
- Nesting Density: How efficiently coupons are packed onto the build plate. More coupons per build generally reduce the allocated machine time cost per coupon.
- 層の厚さ: Thinner layers improve surface finish but significantly increase the number of layers and thus build time.
- Scan Speed & Strategy: Parameters used to melt the powder affect the time spent scanning each layer.
- Machine Rate: The hourly operational cost of the AM machine (including depreciation, energy, maintenance, inert gas, software licenses, facility overhead).
- Build Preparation & Setup Labor:
- CAD Processing: Time spent by engineers/technicians to slice the CAD models, generate appropriate support structures, plan the build layout (nesting), and create the machine instruction files.
- Machine Setup: Labor involved in cleaning the build chamber, loading powder, installing the build plate, running machine calibrations/checks.
- Amortization: These setup costs are relatively fixed per build, so they are spread across more coupons in larger batch sizes, reducing the cost per coupon.
- 後処理費用: These steps can collectively represent a substantial portion (often 50% or more) of the final coupon cost.
- ストレス解消: Furnace cycle time, energy consumption, cost of vacuum or inert gas atmosphere.
- サポートの取り外し: Labor time (manual removal) or machine time (wire EDM, sawing). Requires careful handling.
- 熱間静水圧プレス(HIP): A specialized and relatively expensive process due to equipment cost, long cycle times (often 8-12+ hours including ramp-up/cool-down), high pressures, and inert gas consumption. Often priced per cycle, with costs shared among parts within the HIP vessel.
- Heat Treatment (Other): Costs similar to stress relief, dependent on cycle complexity and duration.
- 機械加工: CNC machine time (turning, milling, grinding), tooling costs, programming time, labor. Cost depends heavily on the extent of machining required (grips only vs. full gauge section).
- 表面仕上げ: Labor and consumable costs for bead blasting, shot peening, polishing, etc. Polishing fatigue specimens to a mirror finish can be labor-intensive.
- NDT: Equipment usage (CT scanner time can be expensive) and cost of certified inspectors/analysts. FPI involves chemical consumables and inspection time.
- Testing Costs (If Bundled):
- Destructive Testing: Costs per test for tensile, fatigue (can be very high cost/long duration, especially for HCF), fracture toughness, hardness, metallography, chemical analysis. Requires calibrated test equipment and skilled technicians.
- Reporting: Time to compile and generate certified test reports.
- Quantity and Batch Size:
- 規模の経済: Producing coupons in larger batches generally reduces the cost per coupon by optimizing machine utilization (denser nesting), amortizing setup costs, and potentially filling post-processing equipment (furnaces, HIP) more efficiently.
- Complexity and Certification:
- Coupon Design: While most standard coupons are simple, unique geometries might require more complex support strategies or machining setups.
- Documentation: The cost associated with generating the extensive documentation, traceability records, and certification packages required for aerospace compliance adds overhead.
Typical Lead Times:
Lead time is the total time from order placement to final coupon delivery (or test report delivery). It is highly variable and depends on the specific processing route required. Expect realistic timelines – AM lead time estimation requires considering all steps:
- Simple Coupons (e.g., Tensile Bars, As-Built or Stress-Relieved + Machined Grips): 1-3 weeks might be achievable, depending on machine availability and batch size.
- Complex Processing (e.g., Fatigue Coupons requiring SR, HIP, Full Machining, Polishing, NDT, and Testing): 4-8 weeks or longer is common. HIP cycles, extensive machining, and especially long-duration fatigue testing significantly extend the timeline.
- Key Factors Influencing Lead Time:
- Machine Availability: Provider’s current backlog and machine scheduling.
- ビルドタイム: As discussed under cost factors.
- Post-Processing Queues: Waiting times for furnaces, HIP units (often run in batches), machining centers, NDT equipment, and testing labs can create bottlenecks.
- Testing Duration: Tensile tests are quick, but fatigue tests can run for days or weeks per coupon.
- Shipping & Logistics: Time for transport between facilities if post-processing or testing is subcontracted.
- Expedited Services: Often possible but usually come at a significant cost premium.
いつ budgeting AM projects, it’s crucial to obtain detailed quotes outlining all included steps and associated costs and to discuss lead times upfront, factoring in potential delays in complex post-processing or testing phases. Understanding the various Met3dp printing methods and their associated process chains helps in planning.
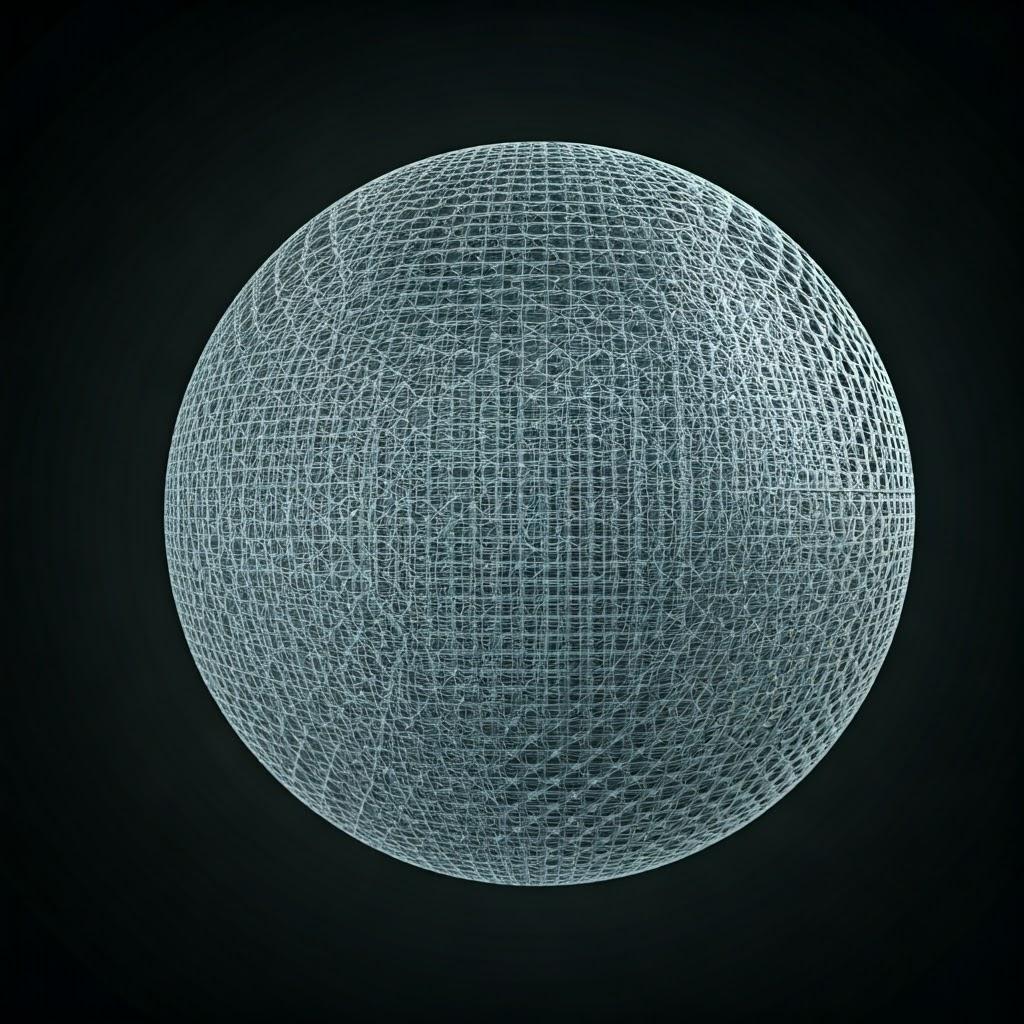
Frequently Asked Questions (FAQ) about 3D Printed Aerospace Test Coupons
As metal additive manufacturing becomes more prevalent in aerospace, engineers, designers, and procurement specialists often have questions about using 3D printed test coupons for qualification and certification. Here are answers to some common inquiries:
- Q1: Are the mechanical properties measured from 3D printed coupons directly comparable to traditional wrought or cast material properties found in handbooks like MMPDS?
- A1: Not directly, and it’s critical to understand why. 3D printed coupons represent the properties of the material as processed by additive manufacturing. AM creates unique microstructures (e.g., finer grain structures, potential anisotropy, different defect populations) compared to wrought or cast products, which undergo different thermomechanical processing. Therefore, AM coupon data reflects the performance achievable via the specific AM process, parameters, and post-processing used. While the goal is often to meet or exceed minimums specified for traditional materials, direct substitution based solely on handbook values is generally not appropriate without specific equivalency studies or the development of dedicated AM material property allowables based on statistically significant AM coupon test data (following guidelines like CMH-17). The primary purpose of AM coupons is to validate the AMプロセス and qualify the AM part.
- Q2: How repeatable and reliable are the results obtained from 3D printed test coupons? Can we trust the data for certification?
- A2: High repeatability and reliability are achievable but depend heavily on rigorous process control and quality management throughout the entire workflow. Key factors include:
- Consistent AM Process: Using validated and locked parameters on well-calibrated and maintained machines.
- High-Quality Powder: Consistent powder chemistry, PSD, and morphology from reputable suppliers like Met3dp. Strict powder handling and recycling protocols.
- Controlled Post-Processing: Precisely executing required steps like stress relief, HIP, heat treatment, and machining according to qualified procedures.
- Robust QMS: Adherence to AS9100 standards ensures traceability, documentation, and control.
- Standardized Testing: Performing mechanical tests according to relevant ASTM/ISO standards in accredited labs (ISO 17025).
- When these elements are in place, the data generated from AM test coupons is considered reliable and forms the basis for aerospace component certification worldwide. Statistical analysis of coupon data is used to establish design allowables with high confidence levels.
- A2: High repeatability and reliability are achievable but depend heavily on rigorous process control and quality management throughout the entire workflow. Key factors include:
- Q3: Is 3D printing test coupons generally more expensive or cheaper than conventionally machining them from wrought/cast bar stock?
- A3: The cost comparison is nuanced and depends on the specific scenario:
- AM Can Be More Cost-Effective For:
- Rapid Prototyping & Development: Quickly producing small batches for iterative testing or parameter optimization.
- Material Representativeness: When the goal is to test the as-built AM microstructure, printing coupons is the only way.
- Expensive Materials: Reduced material waste (better buy-to-fly ratio) for alloys like titanium or Inconel can lead to savings compared to machining from large blocks.
- 複雑な幾何学: If specialized coupon geometries are needed.
- Machining May Be Cheaper For:
- Very Large Quantities: For extremely high-volume production of standard coupon geometries (e.g., thousands of tensile bars) from common, readily available bar stock, traditional CNC machining might achieve a lower cost per part if the AM-specific microstructure is not the primary concern.
- Overall: For aerospace qualification, where speed, material representativeness, and validating the AM process are paramount, the benefits of 3D printing coupons often outweigh potential cost differences, especially during development and for moderate production volumes.
- AM Can Be More Cost-Effective For:
- A3: The cost comparison is nuanced and depends on the specific scenario:
- Q4: What specific industry standards govern the production and testing of metal additive manufacturing test coupons for aerospace?
- A4: A growing body of standards specifically addresses metal AM for aerospace applications. Key documents include:
- ASTM F3301: Standard Guide for Additive Manufacturing – Post-Processing Methods: Standard Specification for Thermal Post-Processing Metal Parts Made Via Powder Bed Fusion.
- ASTM F3055: Standard Specification for Additive Manufacturing Nickel Alloy (UNS N07718) with Powder Bed Fusion. (Similar specs exist for other alloys).
- ASTM F3056: Standard Specification for Additive Manufacturing Titanium-6 Aluminum-4 Vanadium ELI (Extra Low Interstitial) with Powder Bed Fusion.
- ASTM F3187: Standard Guide for Qualifying Materials Made by Additive Manufacturing Processes for Spaceflight Hardware.
- AMS Standards: SAE Aerospace Material Specifications are increasingly being developed for AM materials (e.g., AMS700x series).
- ISO/ASTM Standards: The 529xx series covers general AM terminology, processes, and data requirements.
- Core Mechanical Testing Standards: ASTM E8/E8M (Tensile), ASTM E606 (LCF Fatigue), ASTM E466 (HCF Fatigue), ASTM E399/E1820 (Fracture Toughness), etc., remain applicable for the actual testing methods.
- OEM/Prime Specifications: Major aerospace companies often have their own internal standards and specifications that suppliers must adhere to.
- A4: A growing body of standards specifically addresses metal AM for aerospace applications. Key documents include:
Conclusion: Accelerate Aerospace Innovation and Certification with Metal AM Test Coupons
In the relentless pursuit of lighter, stronger, and more efficient aircraft and spacecraft, metal additive manufacturing has emerged as a cornerstone technology. However, realizing the full potential of AM in safety-critical aerospace applications hinges upon rigorous validation and certification – a process fundamentally reliant on data derived from meticulously produced and tested aerospace test coupons.
As we’ve explored, leveraging metal AM itself to create these vital specimens offers compelling advantages over traditional methods. The ability to rapidly produce coupons with material properties truly representative of the final AM component, coupled with potential cost efficiencies (especially during development and for complex alloys like AlSi10Mg そして Ti-6Al-4V) and design flexibility, significantly accelerates the qualification pathway. Utilizing AM for coupons allows engineers to iterate faster, optimize processes more effectively, and generate the high-fidelity data needed to satisfy regulatory requirements and build confidence in additively manufactured parts.
However, the journey is not without its technical demands. Success requires navigating considerations from coupon design aligned with AM principles and testing standards, achieving stringent tolerance and surface finish requirements (often via integrated post-processing like machining and HIP), and proactively mitigating common challenges such as porosity, anisotropy, and residual stress. This underscores the critical importance of robust process control, meticulous quality management (AS9100), and comprehensive post-processing and testing.
Ultimately, the reliability of the data derived from AM test coupons is inextricably linked to the capabilities and expertise of the manufacturing partner. Choosing the right metal 3D printing service provider – one with proven aerospace experience, certified quality systems, deep material knowledge, advanced equipment, and a commitment to technical excellence – is paramount.
メット3dp stands ready to be that partner. As a leading provider of aerospace additive manufacturing solutions, headquartered in Qingdao, China, Met3dp offers a comprehensive approach. We specialize in both state-of-the-art 3D printing equipment delivering industry-leading print volume, accuracy, and reliability, and the production of high-performance metal powders optimized for AM. Our advanced powder manufacturing, employing Gas Atomization and PREP technologies, ensures the high sphericity, flowability, and purity essential for printing dense, high-quality metal parts and reliable test coupons from innovative alloys including TiNi, TiTa, TiAl, TiNbZr, CoCrMo, stainless steels, superalloys, and the workhorse AlSi10Mg and Ti-6Al-4V grades.
With decades of collective expertise, Met3dp provides comprehensive solutions spanning SEBM printers, advanced metal powders, and application development services. We partner with organizations to implement 3D printing, navigate the complexities of qualification, and accelerate digital manufacturing transformations.
Don’t let the challenges of qualification slow your aerospace innovation. Leverage the power of metal AM test coupons produced with expertise and precision. Contact Met3dp today to explore how our cutting-edge systems, high-quality powders, and extensive knowledge can support your aerospace testing and certification needs, powering your organization’s additive manufacturing goals.
シェアする
MET3DP Technology Co., LTDは、中国青島に本社を置く積層造形ソリューションのリーディングプロバイダーです。弊社は3Dプリンティング装置と工業用途の高性能金属粉末を専門としています。
関連記事
Met3DPについて
最新情報
製品
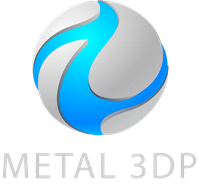
3Dプリンティングと積層造形用金属粉末