Complex Actuator Housings for Valves via Metal AM
目次
Introduction: Defining Industrial Valve Actuator Housings and Their Critical Role
Industrial valve actuators are the workhorses of countless fluid control systems across numerous sectors. They provide the necessary force and motion – whether pneumatic, hydraulic, electric, or manual – to operate valves like ball, butterfly, gate, or globe valves, regulating the flow of liquids, gases, slurries, or steam. At the heart of these actuators lies the housing: a critical structural component that performs several vital functions.
The actuator housing serves as the protective enclosure for the internal mechanisms – motors, gears, pistons, springs, sensors, and electronics – shielding them from harsh operating environments, contaminants, impacts, and corrosion. It also provides the necessary mounting points for connecting the actuator to the valve and potentially to other control system components. Furthermore, the housing must withstand the internal pressures and stresses generated during actuation and maintain its structural integrity under demanding conditions, which can include extreme temperatures, high pressures, vibrations, and exposure to corrosive media.
Traditionally, actuator housings have been manufactured using methods like casting (sand, investment, die), forging, or machining from billet stock. While effective for high-volume production of standardized designs, these methods often face limitations when dealing with:
- 複雑な幾何学: Internal features, intricate passageways, or optimized shapes for weight reduction or improved performance can be difficult or impossible to achieve cost-effectively.
- 廃棄物: Subtractive processes like machining generate significant scrap material, increasing costs, especially with expensive alloys.
- Long Lead Times: Tooling creation (molds, dies) for casting or forging can take weeks or months, delaying prototyping and production.
- Design Iteration Challenges: Modifying a design often requires expensive tooling adjustments or new tooling altogether, hindering rapid innovation.
- Supply Chain Vulnerabilities: Reliance on traditional foundries or machine shops can introduce bottlenecks, especially for specialized or low-volume orders.
In this context, 金属積層造形(AM), commonly known as metal 3Dプリンティング, emerges as a transformative technology for producing industrial valve actuator housings. Metal AM builds parts layer by layer directly from digital models using high-performance metal powders. This approach unlocks unprecedented design freedom, enables rapid prototyping and production, reduces material waste, and allows for the creation of highly optimized, complex components that were previously unmanufacturable. For procurement managers, engineers, and system designers seeking enhanced performance, shorter lead times, and greater supply chain resilience for critical valve components, exploring metal AM for actuator housings is becoming increasingly crucial. Companies seeking B2B procurement solutions or identifying a reliable industrial distributor for specialized components find metal AM offers competitive advantages.
Applications: Where are Metal AM Valve Actuator Housings Used? Industries and Functions
The versatility and benefits of metal AM make it suitable for producing actuator housings used in a wide array of demanding industries and critical applications. The ability to create complex shapes, utilize high-performance alloys, and produce parts on-demand caters to sectors where reliability, performance, and specific material properties are non-negotiable.
Key Industries & Applications:
- 航空宇宙・防衛
- Function: Housings for actuators controlling fuel systems, hydraulic flight controls, landing gear mechanisms, and environmental control systems.
- Why Metal AM? Extreme weight sensitivity necessitates topology optimization and complex, lightweight designs. High-performance alloys are required for extreme temperature variations and demanding operational stresses. Rapid prototyping and low-volume production capabilities are essential for development and specialized aircraft. B2B suppliers specializing in aerospace-grade AM are critical partners.
- Oil & Gas (Upstream, Midstream, Downstream):
- Function: Housings for actuators on pipeline valves, wellhead control systems (e.g., safety valves, choke valves), refinery process control valves, and subsea equipment.
- Why Metal AM? Need for high corrosion resistance (sour gas, saltwater), high-pressure containment, and reliability in remote or hazardous locations. Ability to print complex internal channels for hydraulic or pneumatic routing within the housing itself. Material options like IN625 offer superior performance in corrosive environments. Sourcing from a qualified actuator housing manufacturer using AM ensures component integrity.
- 化学処理:
- Function: Actuator housings for valves handling aggressive chemicals, high temperatures, and high pressures in reactors, distillation columns, and transfer lines.
- Why Metal AM? Superior chemical resistance offered by specific alloys (e.g., Stainless Steels, Nickel Alloys) is paramount. Complex geometries might be needed for specialized mixing or flow control applications integrated within the actuator space. Reduced lead times for replacement parts minimize costly plant downtime.
- Power Generation (Nuclear, Fossil Fuels, Renewables):
- Function: Housings for actuators controlling steam turbines (throttle, governor valves), feedwater systems, cooling circuits, and safety relief valves.
- Why Metal AM? Requirements for high-temperature strength, creep resistance, and long-term durability. In nuclear applications, specific material certifications and traceability are essential, which AM processes can meticulously document. Ability to consolidate parts within the housing reduces potential leak paths and assembly complexity.
- Automotive & Transportation:
- Function: Housings for specialized actuators in performance vehicles, heavy-duty trucks (e.g., exhaust gas recirculation (EGR) valves, turbocharger wastegates), and potentially future electric vehicle thermal management systems.
- Why Metal AM? Weight reduction, performance optimization through complex design, and rapid prototyping for development cycles. Potential for conformal cooling channels integrated into housings for electric motors or power electronics within the actuator.
- Medical & Pharmaceutical:
- Function: Housings for actuators in bioreactors, process control systems for drug manufacturing, and potentially for specialized medical devices requiring precise fluid control.
- Why Metal AM? Requirement for hygienic designs, high purity materials (like specific grades of stainless steel), and excellent cleanability. Ability to produce complex, crevice-free internal surfaces. Biocompatible materials may be needed for certain applications.
- Industrial Manufacturing & Automation:
- Function: Housings for actuators used in factory automation, robotics, process control skids, and specialized machinery requiring precise flow or motion control.
- Why Metal AM? Customization for specific machine integration, potential for part consolidation, and on-demand production for spares or unique configurations. Finding a flexible metal AM service provider is key for varied industrial needs.
Functional Advantages Enabled by Metal AM:
- パーツの統合: Integrating features like mounting brackets, sensor ports, or fluid channels directly into the housing design, reducing assembly steps, potential leak points, and overall weight.
- Topology Optimization: Using software tools to remove unnecessary material while maintaining structural integrity, resulting in significantly lighter housings without compromising strength – crucial for aerospace and automotive applications.
- Conformal Cooling/Heating Channels: Integrating complex internal channels that follow the contours of the housing or internal components, allowing for more efficient thermal management of motors or electronics within the actuator.
- Complex Internal Geometries: Creating intricate internal pathways for hydraulics or pneumatics that would be impossible or prohibitively expensive to machine traditionally.
- Customization & On-Demand Production: Enabling cost-effective production of low-volume, highly customized actuator housings tailored to specific valve interfaces or operating environments without the need for dedicated tooling.
The breadth of these applications highlights the growing role of metal AM in pushing the boundaries of what’s possible in valve actuation technology, offering tangible benefits across performance-critical sectors. Procurement teams looking for wholesale pricing on advanced components should investigate AM suppliers capable of handling diverse industrial requirements.
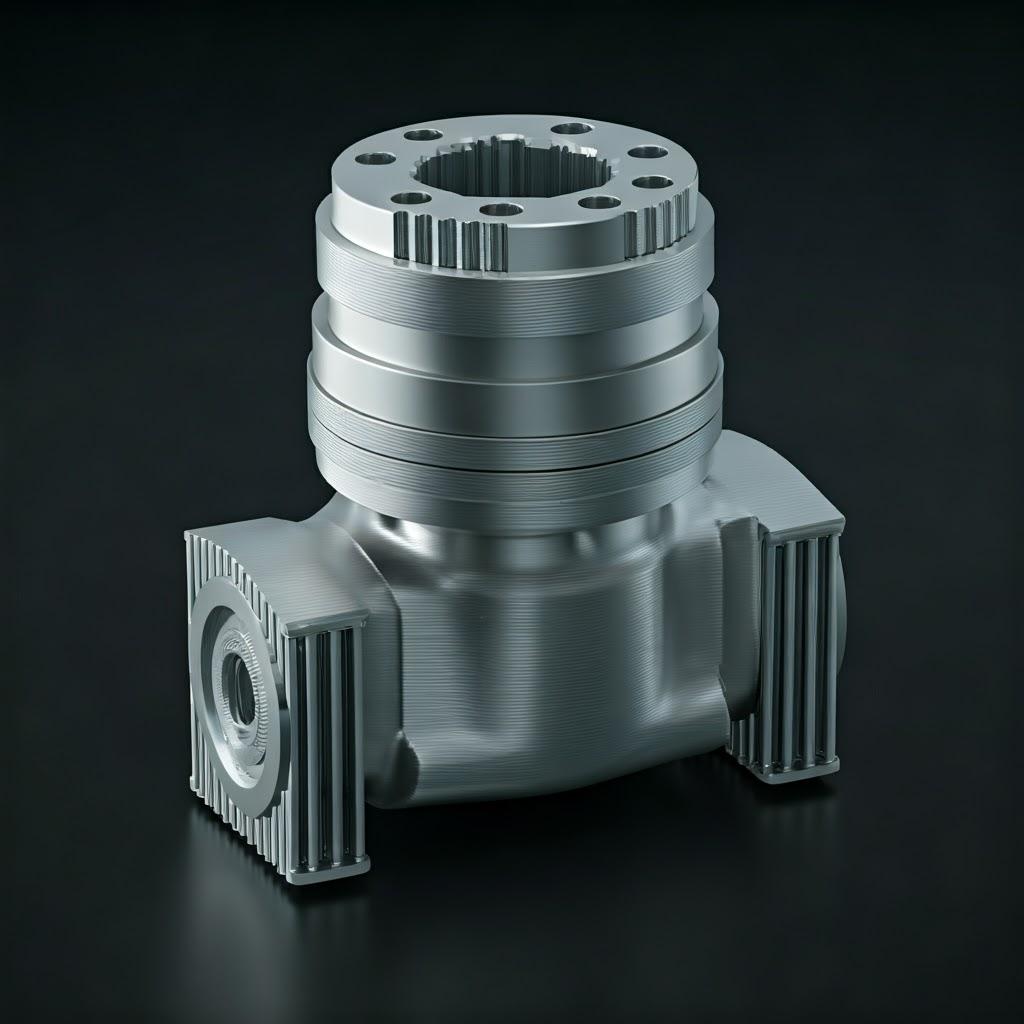
Why Metal 3D Printing? Advantages Over Traditional Manufacturing for Actuator Housings
While traditional methods like casting and machining have served the industry well, 金属3Dプリンティング offers a compelling suite of advantages, particularly for complex, high-performance, or customized valve actuator housings. These benefits address many of the inherent limitations of older techniques, providing engineers and manufacturers with powerful new capabilities.
Comparison: Metal AM vs. Traditional Methods for Actuator Housings
特徴 | Metal Additive Manufacturing (e.g., PBF-LB/M, PBF-EB/M) | Traditional Casting (Sand, Investment) | Traditional Machining (from Billet) |
---|---|---|---|
デザインの自由 | Very High (Complex geometries, internal channels) | Moderate (Limited by mold capabilities) | Moderate to High (Limited by tool access) |
Complexity Cost | Relatively insensitive to complexity | Increases significantly with complexity | Increases significantly with complexity |
廃棄物 | Low (Powder reused) | Moderate (Gates, risers, sprues) | High (Significant chip generation) |
Tooling Requirement | None (Digital file) | High (Molds, patterns required) | Low (Fixtures, standard tools) |
Tooling Lead Time | 該当なし | 数週間から数か月 | N/A (Fixture setup time) |
Prototyping Speed | Fast (Days) | Slow (Requires tooling) | Moderate to Fast (Depends on complexity) |
Ideal Volume | Low to Medium, Complex Parts, Customization | High Volume, Standardized Parts | Low to Medium Volume, Simpler Parts |
部品の統合 | Excellent capability | Limited capability | Limited capability |
Weight Optimization | Excellent (Topology optimization feasible) | 限定 | Moderate (Material removal possible) |
素材オプション | Growing range of weldable alloys | Wide range of castable alloys | Wide range of machinable alloys |
Initial Setup Cost | High (Machine cost) / Moderate (Service Bureau) | High (Tooling cost) | Low to Moderate (Machine/Tooling) |
Per-Part Cost (Low Vol) | Competitive to High | Very High (Due to tooling amortization) | 高い |
Per-Part Cost (High Vol) | High (Can be less competitive) | 低い | 中~高 |
Export to Sheets
Key Advantages of Metal AM for Actuator Housings:
- 比類なき設計の自由度:
- 複雑な幾何学: AM excels at producing intricate shapes, internal lattice structures for weight reduction, and integrated features (like fluid channels or mounting points) that are impossible or prohibitively expensive with casting or machining. This allows designers to optimize housings for flow, thermal management, or structural efficiency in ways previously unattainable.
- パーツの統合: Multiple components that would traditionally be manufactured separately and then assembled (e.g., housing body, brackets, covers, connectors) can potentially be printed as a single, monolithic part. This reduces assembly time, BOM complexity, potential leak paths, and overall weight.
- ラピッドプロトタイピングと反復:
- スピードだ: Producing functional metal prototypes in days rather than weeks or months allows for faster design validation, testing, and refinement cycles. Changes can be made digitally and reprinted quickly without the need for costly tooling modifications.
- イノベーションだ: This accelerates the pace of innovation, enabling engineers to experiment with novel designs and performance enhancements more readily.
- Weight Reduction through Optimization:
- Topology Optimization: Software can be used to computationally determine the most efficient material distribution within the housing to meet specific load requirements. AM can then produce these highly organic, optimized shapes, significantly reducing weight while maintaining or even increasing stiffness – a critical advantage in aerospace, automotive, and mobile applications.
- 格子構造: Internal lattices can replace solid material sections, drastically cutting weight while providing tailored structural support or vibration damping properties.
- 廃棄物の削減:
- Additive vs. Subtractive: AM builds parts layer by layer, using only the material needed for the part and its supports. Unused powder can typically be recycled and reused in subsequent builds. This contrasts sharply with subtractive machining, which starts with a solid block and cuts away material, generating significant waste (chips), especially for complex parts or expensive alloys like Inconel.
- コスト削減: Reduced waste translates directly to lower material costs, particularly important when dealing with high-value metal powders.
- On-Demand & Customized Production:
- Tooling-Free Manufacturing: Eliminating the need for molds or dies makes low-volume production runs and one-off custom parts economically viable. This is ideal for producing spare parts for legacy systems, customized housings for specific applications, or adapting designs quickly to changing requirements.
- Distributed Manufacturing: Digital design files can be sent electronically to AM service providers globally, enabling localized production closer to the point of need, potentially simplifying logistics for international B2B suppliers and distributors.
- Access to High-Performance Materials:
- AM processes can work with a range of advanced metal alloys, including stainless steels (like 316L), nickel superalloys (like IN625), titanium alloys, and others, chosen specifically for their properties like corrosion resistance, high-temperature strength, or strength-to-weight ratio, matching the demands of the target application. Companies like Met3dp specialize in producing high-quality powders optimized for these demanding applications.
While metal AM may not replace traditional methods for all actuator housings (especially simple, very high-volume ones), its advantages provide compelling value propositions for complex, critical, customized, or weight-sensitive components, driving its adoption across performance-driven industries.
Material Selection: Recommended Powders (316L, IN625) for Optimal Performance
Choosing the right material is fundamental to the success of any engineering component, and valve actuator housings are no exception. The operating environment, required mechanical properties, regulatory requirements, and cost considerations all influence material selection. Metal additive manufacturing offers a growing portfolio of alloys, but for a broad range of industrial valve actuator applications, Austenitic Stainless Steel 316L and Nickel-Chromium Superalloy IN625 (Inconel 625) are frequently excellent choices.
Selecting high-quality, consistent metal powder is paramount for achieving reliable results in metal AM. Leading providers like メット3dp utilize advanced powder manufacturing techniques, such as gas atomization and Plasma Rotating Electrode Process (PREP), to produce powders with high sphericity, good flowability, controlled particle size distribution, and low levels of impurities. These characteristics are crucial for achieving dense, defect-free printed parts with predictable mechanical properties. Met3dp’s expertise ensures that the powders meet the stringent requirements for mission-critical applications.
Austenitic Stainless Steel 316L:
- 説明 316L is a low-carbon version of 316 stainless steel, an austenitic chromium-nickel stainless steel containing molybdenum. The “L” signifies lower carbon content (typically <0.03%), which minimizes harmful carbide precipitation during welding or thermal processing, thereby enhancing corrosion resistance, particularly in welded sections.
- キー・プロパティ
- 優れた耐食性: Exhibits superior resistance to general corrosion, pitting, and crevice corrosion compared to 304 stainless steel, especially in chloride-containing environments, sulfuric acid, and various industrial chemicals.
- Good Weldability & Formability: Easily weldable and processable using AM techniques.
- Good Strength & Ductility: Offers a good combination of tensile strength, yield strength, and elongation, suitable for many structural applications.
- Hygienic Properties: Often used in food processing, pharmaceutical, and medical applications due to its cleanability and resistance to bacterial growth.
- 費用対効果: Generally more affordable than nickel-based superalloys.
- Why Choose 316L for Actuator Housings?
- Ideal for general industrial applications, chemical processing, food and beverage, pharmaceutical, water treatment, and marine environments where good corrosion resistance and moderate strength are required.
- Provides a reliable and cost-effective solution when the extreme temperature or corrosion challenges necessitating IN625 are not present.
- Well-understood material with extensive data available, simplifying design and qualification.
- 検討する:
- Limited strength at elevated temperatures (typically suitable up to ~500-600°C, depending on load).
- Susceptible to stress corrosion cracking in certain hot chloride environments.
Nickel-Chromium Superalloy IN625 (Inconel® 625):
- 説明 IN625 is a non-magnetic, corrosion- and oxidation-resistant nickel-based superalloy. Its high strength is derived from the solid solution strengthening effect of refractory metals like molybdenum and niobium in the nickel-chromium matrix.
- キー・プロパティ
- Outstanding Corrosion Resistance: Exceptional resistance to a wide range of corrosive media, including high-purity water, saltwater, acids (sulfuric, phosphoric, nitric, hydrochloric), alkalis, and organic acids. Highly resistant to pitting, crevice corrosion, and intergranular attack. Excellent in sour gas environments.
- High Strength at Elevated Temperatures: Maintains significant strength and toughness from cryogenic temperatures up to ~980°C (1800°F). Excellent fatigue and creep-rupture strength.
- Excellent Fabricability: Readily processed using various metal AM techniques.
- 耐酸化性: Forms a protective oxide layer, providing excellent resistance in high-temperature oxidizing atmospheres.
- Why Choose IN625 for Actuator Housings?
- Essential for demanding applications in aerospace (engine components, exhaust systems), oil and gas (subsea, downhole, sour gas service), chemical processing (handling aggressive media), power generation (high-temperature steam, gas turbines), and marine engineering (seawater exposure).
- Chosen when service conditions involve extreme temperatures, high pressures, and severely corrosive environments where stainless steels would fail.
- Its high strength allows for potentially thinner walls or more compact designs compared to 316L under similar loads.
- 検討する:
- Significantly higher material cost compared to 316L.
- Density is higher than stainless steel (~8.44 g/cm³ vs. ~8.0 g/cm³ for 316L).
- Requires careful control of AM process parameters to manage residual stresses due to its high thermal expansion and strength.
Material Selection Summary Table:
特徴 | ステンレススチール316L | Nickel Superalloy IN625 |
---|---|---|
Primary Elements | Fe、Cr、Ni、Mo | Ni、Cr、Mo、Nb |
耐食性 | Excellent (General, Pitting, Crevice) | Outstanding (Wide range, Severe conditions) |
High Temp. Strength | Moderate (Up to ~500-600°C) | Excellent (Up to ~980°C) |
Cryogenic Toughness | グッド | 素晴らしい |
密度 | ~8.0 g/cm³ | ~8.44 g/cm³ |
相対コスト | より低い | より高い |
代表的なアプリケーション | General Industrial, Chemical, Food/Bev, Marine | Aerospace, Oil & Gas, Severe Chemical, Power |
AM Processability | グッド | Good (Requires careful parameter control) |
Export to Sheets
Ultimately, the choice between 316L and IN625 (or potentially other alloys available through metal AM) depends on a thorough analysis of the specific application’s requirements. Consulting with material experts and experienced AM service providers like Met3dp, who possess deep knowledge of various 印刷方法 and material performance, is crucial for making the optimal selection for your valve actuator housing project. This ensures the final component delivers the necessary performance, reliability, and lifespan demanded by its operating environment. Sources and related content
Design for Additive Manufacturing (DfAM): Optimizing Actuator Housing Geometry for Metal AM
Simply taking a design intended for casting or machining and sending it to a metal 3D printer rarely yields optimal results. To fully leverage the capabilities of additive manufacturing and produce high-quality, cost-effective valve actuator housings, engineers must embrace 積層造形設計 (DfAM) principles. DfAM involves rethinking component design to suit the layer-by-layer building process, minimizing potential issues, reducing post-processing needs, and maximizing the unique benefits AM offers.
Applying DfAM specifically to actuator housings requires considering factors like orientation, support structures, wall thickness, internal channels, feature resolution, and potential for part consolidation. Partnering with an experienced AM service provider like Met3dp, which offers comprehensive application development services, can be invaluable during the design phase. Their expertise ensures designs are optimized for specific AM processes (like Powder Bed Fusion – Laser Beam (PBF-LB/M) or Electron Beam (PBF-EB/M)) and materials (like 316L or IN625).
Key DfAM Considerations for Actuator Housings:
- Build Orientation:
- 影響: The orientation of the housing on the build plate significantly affects surface finish on different faces, the amount and location of required support structures, build time, and potentially anisotropic mechanical properties (properties varying with direction).
- Strategy: Orient the part to minimize downward-facing surfaces (overhangs) that require supports. Prioritize critical surfaces or features for upward-facing or vertical orientations to achieve better surface finish. Consider how orientation affects residual stress accumulation. Complex simulations may be needed for optimal orientation.
- サポート体制:
- Necessity: Metal AM processes require support structures for overhangs (typically beyond 45 degrees from vertical) and bridges to prevent collapse, anchor the part to the build plate, and conduct heat away during the build.
- Design Implications: Supports consume material, add build time, and require removal during post-processing, which can leave witness marks or be difficult in hard-to-reach areas.
- Strategy: Design with self-supporting angles (chamfers, fillets) where possible. Minimize steep overhangs. If supports are unavoidable, design features that allow for easier access and removal (e.g., strategically placed openings). Consider sacrificial features that incorporate necessary support but are easily machined off later.
- Wall Thickness & Feature Size:
- Minimums: AM processes have limitations on the minimum wall thickness and feature size they can reliably produce (dependent on machine, laser/electron beam spot size, and powder characteristics). Typical minimums might range from 0.4mm to 1.0mm.
- Maximums & Thermal Management: Very thick sections can accumulate excessive heat and residual stress, potentially leading to distortion or cracking.
- Strategy: Maintain wall thicknesses above the process minimum. Avoid large, solid volumes where possible; consider internal lattice structures or hollow sections. Use gradual transitions between thick and thin sections to manage thermal gradients.
- Holes and Internal Channels:
- オーバーハング Horizontally oriented holes create internal overhangs. Small holes might be self-supporting up to a certain diameter, while larger ones may require internal supports (difficult to remove) or be designed as diamond or teardrop shapes to become self-supporting.
- Complex Channels: AM excels at creating complex internal channels for cooling, hydraulics, or pneumatics. Design these channels with smooth bends and self-supporting geometries. Ensure channels are designed for effective powder removal after printing.
- Strategy: Orient parts to print holes vertically whenever feasible. Use self-supporting shapes for horizontal holes. For intricate channels, carefully consider powder removal access and potentially design in clean-out ports.
- Topology Optimization & Lightweighting:
- Concept: Use software to remove material from non-critical areas while ensuring the housing meets all structural and functional requirements. This often results in organic-looking, highly efficient structures.
- アプリケーション Ideal for actuator housings where weight is a primary concern (aerospace, automotive). Can significantly reduce material consumption and build time.
- Strategy: Define load cases, constraints, and design space accurately in the optimization software. Ensure the resulting geometry is manufacturable via AM (considering overhangs, minimum feature sizes).
- パーツの統合:
- Opportunity: Identify opportunities to combine multiple components (e.g., housing body, mounting flanges, heat sinks, sensor mounts) into a single printed part.
- メリット Reduces assembly labor, part count (BOM simplification), potential leak paths, and often overall weight.
- Strategy: Analyze the actuator assembly for consolidation candidates. Ensure the consolidated design remains manufacturable and allows access for any internal components that still need assembly.
- Designing for Post-Processing:
- Machining Allowances: If critical features require very tight tolerances or specific surface finishes achievable only through machining, add extra material (machining stock) to those surfaces in the AM design.
- Support Removal Access: Ensure areas requiring support removal are accessible with tools.
- Heat Treatment Considerations: Design to minimize distortion during stress relief or other heat treatment cycles (e.g., symmetry, gradual thickness changes).
DfAM Checklist for Actuator Housings:
- [ ] Optimized build orientation chosen?
- [ ] Support structures minimized and designed for removal?
- [ ] Wall thicknesses and feature sizes within process limits?
- [ ] Holes and internal channels designed for printability and powder removal?
- [ ] Topology optimization or lightweighting explored?
- [ ] Part consolidation opportunities utilized?
- [ ] Allowances for machining and post-processing included?
- [ ] Design reviewed with AM experts/service provider?
By integrating DfAM principles early in the design cycle, manufacturers can unlock the full potential of metal AM, producing valve actuator housings that are lighter, stronger, more functional, and potentially more cost-effective than their traditionally manufactured counterparts. This proactive approach is key for wholesale buyers and B2B procurement teams seeking innovative and efficient component solutions.
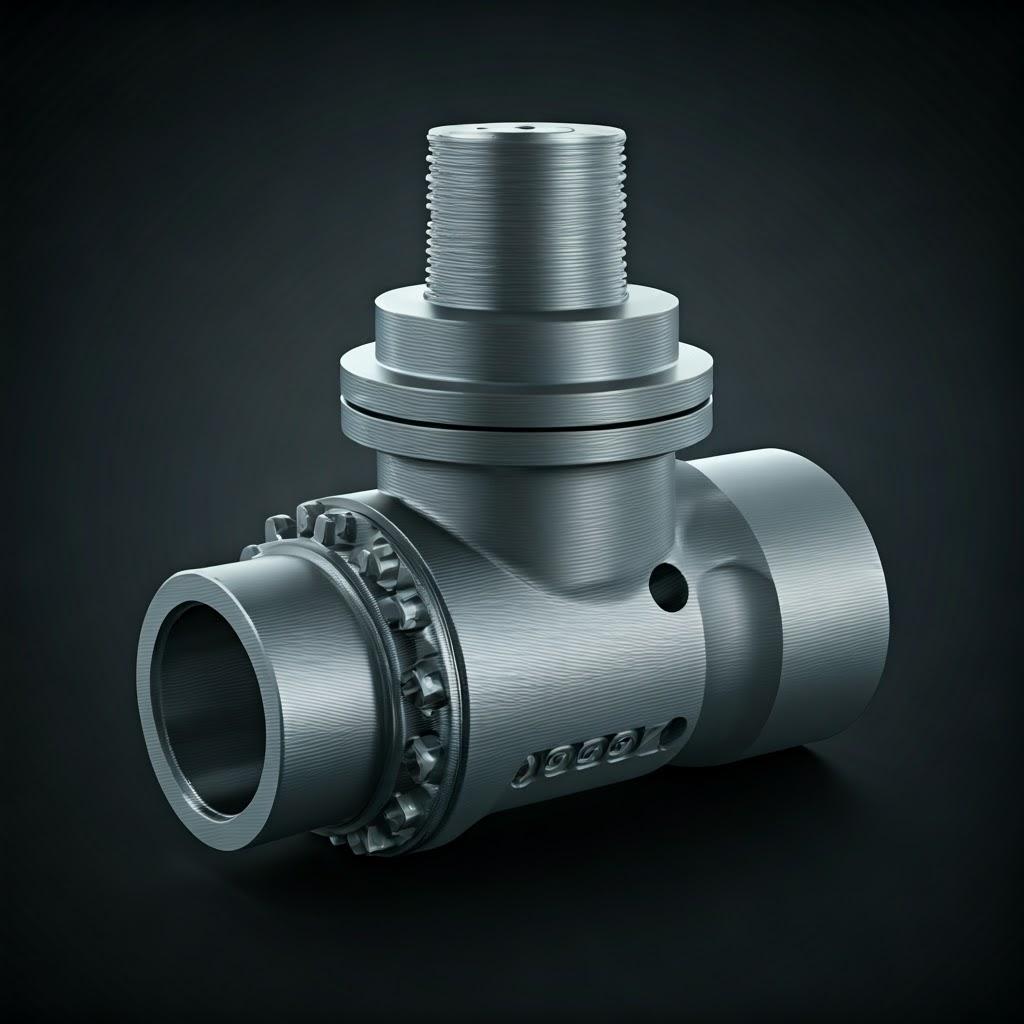
Precision Matters: Achieving Tight Tolerances and Surface Finish in 3D Printed Housings
While metal additive manufacturing offers incredible design freedom, understanding and managing achievable tolerances and surface finishes is critical for functional components like valve actuator housings. These housings often have critical interface dimensions, sealing surfaces, and bearing bores that require a specific level of precision to function correctly. Procurement managers and engineers must have realistic expectations and understand how AM interacts with traditional precision requirements.
The “as-built” state of a metal AM part differs significantly from a machined component. The layer-wise fusion process inherently creates a rougher surface texture, and thermal stresses during printing can lead to minor shrinkage or distortion. However, metal AM can serve as a near-net-shape process, often combined with secondary machining operations to achieve final tolerances on critical features.
Factors Influencing Tolerance and Surface Finish in Metal AM:
- AMプロセス: Different metal AM technologies yield varying results. Powder Bed Fusion (PBF-LB/M and PBF-EB/M) generally offers higher accuracy and finer finishes compared to Directed Energy Deposition (DED). PBF-EB/M (Electron Beam) often produces parts with lower internal stress but potentially rougher surfaces than PBF-LB/M (Laser Beam). Met3dp’s focus on advanced PBF systems ensures high levels of achievable precision.
- 素材: The type of metal powder used (e.g., 316L, IN625) influences melt pool behavior, shrinkage, and achievable surface finish.
- Machine Calibration & Parameters: Laser/electron beam power, scan speed, layer thickness, and powder characteristics directly impact melt pool stability, density, surface roughness, and dimensional accuracy. Consistent machine calibration is crucial.
- Part Geometry & Size: Large or complex parts are more prone to thermal distortion. Feature size and location within the build chamber can also affect accuracy.
- Build Orientation: As mentioned in DfAM, orientation significantly impacts surface finish. Upward-facing and vertical surfaces are typically smoother than downward-facing surfaces (supported) or “stair-stepped” curved surfaces.
- サポート体制: Removal of supports inevitably leaves witness marks, affecting the local surface finish and requiring subsequent finishing operations.
- 後処理: Steps like heat treatment (stress relief) can cause slight dimensional changes. Machining, grinding, polishing, or electro-polishing are often used to achieve the final required tolerances and surface finishes on specific features.
Typical As-Built Capabilities (Powder Bed Fusion):
- 寸法精度: General tolerances for as-built PBF parts are often cited in the range of ±0.1mm to ±0.2mm or ±0.1% to ±0.2% of the dimension, whichever is greater. However, this can vary significantly based on the factors above. Achieving tighter tolerances usually requires post-machining.
- Surface Roughness (Ra): As-built surface roughness depends heavily on orientation and process parameters.
- Vertical Walls: Typically smoother, potentially Ra 6-15 µm.
- Upward-Facing Surfaces: Can achieve relatively good finishes.
- Downward-Facing (Supported) Surfaces: Rougher due to support contact, potentially Ra 15-30 µm or more.
- Stair-Stepping Effect: Visible on gently sloping or curved surfaces due to the layer-wise build.
Achieving Precision in Actuator Housings:
- Hybrid Approach (AM + Machining): This is the most common strategy for high-precision housings.
- Print the housing using metal AM, leveraging its ability to create complex overall shapes, internal features, and optimized structures (near-net shape).
- Design the AM part with added machining stock (e.g., 0.5mm – 2mm) on critical surfaces.
- Post-print, perform CNC machining on critical features like:
- Mounting flanges (flatness, hole positions)
- Sealing surfaces (O-ring grooves, gasket faces)
- Bearing bores (diameter, concentricity, cylindricity)
- Threaded holes (tapping after printing/machining)
- This approach combines the design freedom of AM with the precision of machining where it matters most.
- Designing for As-Built Tolerances: For non-critical features or housings where standard AM tolerances suffice, designing with these capabilities in mind can reduce or eliminate the need for post-machining, lowering costs.
- Surface Finishing Techniques: Beyond machining, various techniques can improve the as-built surface finish:
- Abrasive Blasting (Sandblasting, Bead Blasting): Provides a uniform matte finish, removes loose powder, but doesn’t significantly improve dimensional accuracy.
- Tumbling/Vibratory Finishing: Uses media to smooth surfaces and edges, effective for overall finish improvement but less controlled for specific dimensions.
- 研磨: Mechanical or electrochemical polishing can achieve very smooth, mirror-like finishes (low Ra) required for some sealing or hygienic applications.
- Micro-Machining: Techniques like laser polishing or micro-milling can target specific small features.
Tolerance & Surface Finish Summary Table:
Feature/Process | Typical As-Built (PBF) Range | Achievable with Post-Machining | Common Application in Actuator Housings |
---|---|---|---|
General Tolerance | ±0.1 to ±0.2 mm / ±0.1-0.2% | Down to ±0.01 mm or better | Overall shape (As-Built OK), Interface dimensions (Machining needed) |
表面粗さ(Ra) | 6 – 30+ µm | Down to <0.1 µm (Polishing) | General surfaces (As-Built OK), Sealing faces (Machining/Polishing) |
Flatness/Parallelism | 中程度 | 高い | Mounting flanges, Gasket surfaces (Machining needed) |
Hole Diameter/Position | 中程度 | 高い | Bearing bores, Mounting holes, Threaded holes (Machining/Tapping) |
Export to Sheets
Engineers designing actuator housings for metal AM must clearly define the critical tolerances and surface finish requirements for each feature. Working closely with the AM service provider is essential to determine the best manufacturing strategy – whether relying on as-built accuracy or planning for specific post-processing steps like machining – to ensure the final housing meets all functional requirements reliably and cost-effectively. B2B buyers should specify these critical dimensions clearly in RFQs (Request for Quotations).
Post-Processing Pathways: Essential Finishing Steps for Functional Actuator Housings
Producing a valve actuator housing using metal additive manufacturing doesn’t end when the part comes out of the printer. A series of crucial post-processing steps are typically required to transform the raw, as-built component into a functional, finished product ready for assembly and deployment. Understanding these steps is vital for estimating realistic lead times, costs, and ensuring the final part meets all performance specifications.
The specific post-processing pathway depends heavily on the chosen AM process, the material (e.g., 316L, IN625), the complexity of the design, and the final application requirements regarding tolerances, surface finish, and mechanical properties. Engaging with a full-service provider who understands these nuances is beneficial for procurement managers coordinating B2B orders.
Common Post-Processing Steps for Metal AM Actuator Housings:
- Powder Removal / Depowdering:
- 目的 To remove any unfused metal powder trapped within internal channels, cavities, or adhered to the surface of the printed part.
- 方法: Manual brushing, compressed air blow-off, ultrasonic cleaning baths, specialized powder handling stations. For complex internal geometries, careful design (DfAM) for powder drainability is crucial. Incomplete powder removal can compromise functionality or lead to contamination.
- Importance: Essential for all AM parts, especially those with internal features common in actuator housings.
- Stress Relief / Heat Treatment:
- 目的 The rapid heating and cooling cycles inherent in PBF processes create internal residual stresses within the part. These stresses can cause distortion (especially after removal from the build plate) or negatively impact mechanical properties (like fatigue life). Stress relief heat treatment minimizes these stresses. Other heat treatments (like solution annealing, aging, or Hot Isostatic Pressing – HIP) may be required to achieve desired final microstructure and mechanical properties (e.g., increased strength, ductility, creep resistance).
- 方法: Performed in controlled atmosphere furnaces or vacuum furnaces at specific temperatures and durations tailored to the alloy (e.g., different cycles for 316L vs. IN625). HIP involves applying high pressure and temperature simultaneously to close internal porosity and improve density/fatigue life.
- Importance: Critical for dimensional stability and achieving optimal material performance, especially for demanding applications. Often the first step after depowdering and before support removal/machining.
- Part Removal from Build Plate:
- 目的 To separate the printed housing(s) from the metal build plate they were fused to during the printing process.
- 方法: Typically done using wire EDM (Electrical Discharge Machining), sawing, or machining. Care must be taken not to damage the parts.
- Importance: Necessary step before further processing can occur.
- 支持構造の撤去:
- 目的 To remove the temporary support structures required during the build process.
- 方法: Manual removal (breaking off, cutting), CNC machining, wire EDM, grinding. Access can be challenging for internal supports.
- Importance: Required for fit, form, and function. Can be labor-intensive and impact surface finish at contact points (“witness marks”).
- Machining (Secondary Machining):
- 目的 To achieve tight tolerances, critical geometric features (GD&T), and specific surface finishes on designated part features that cannot be met by the as-built AM process.
- 方法: CNC milling, turning, drilling, tapping, grinding. As discussed previously, requires designing the AM part with appropriate machining allowances.
- Importance: Often essential for actuator housings requiring precise interfaces, sealing surfaces, bearing fits, or threaded connections.
- Surface Finishing & Cleaning:
- 目的 To achieve the desired surface texture, improve aesthetics, enhance cleanability, or prepare the surface for coatings.
- 方法: Abrasive blasting (bead/sand), tumbling, polishing (mechanical, electrochemical), passivation (especially for stainless steels to enhance corrosion resistance). Final cleaning to remove any machining fluids or debris.
- Importance: Dependent on application requirements – critical for sealing surfaces, hygienic applications, or cosmetic appearance.
- Inspection and Quality Control (QC):
- 目的 To verify that the finished housing meets all dimensional, material, and functional specifications.
- 方法: Dimensional inspection (CMM, laser scanning, gauges), surface roughness testing, material verification (chemical analysis, mechanical testing on witness coupons), NDT (Non-Destructive Testing like CT scanning for internal defects/porosity, dye penetrant testing for surface flaws), pressure testing.
- Importance: Ensures part quality, reliability, and traceability, especially crucial for critical applications in aerospace, oil & gas, and medical sectors. Met3dp emphasizes industry-leading accuracy and reliability, backed by robust QC processes.
Typical Post-Processing Workflow Example:
- Build Completion -> Depowdering -> Stress Relief (Furnace) -> Part Removal (Wire EDM) -> Support Removal (Manual/Machining) -> CNC Machining (Critical Features) -> Surface Finishing (e.g., Blasting/Passivation) -> Final Cleaning -> Inspection (CMM, NDT) -> Packaging & Shipping.
Understanding this multi-step process is crucial for project planning. The time and cost associated with post-processing can be significant and should be factored into any comparison between AM and traditional manufacturing methods. Partnering with a metal AM supplier who offers integrated post-processing capabilities can streamline the workflow and ensure consistency.
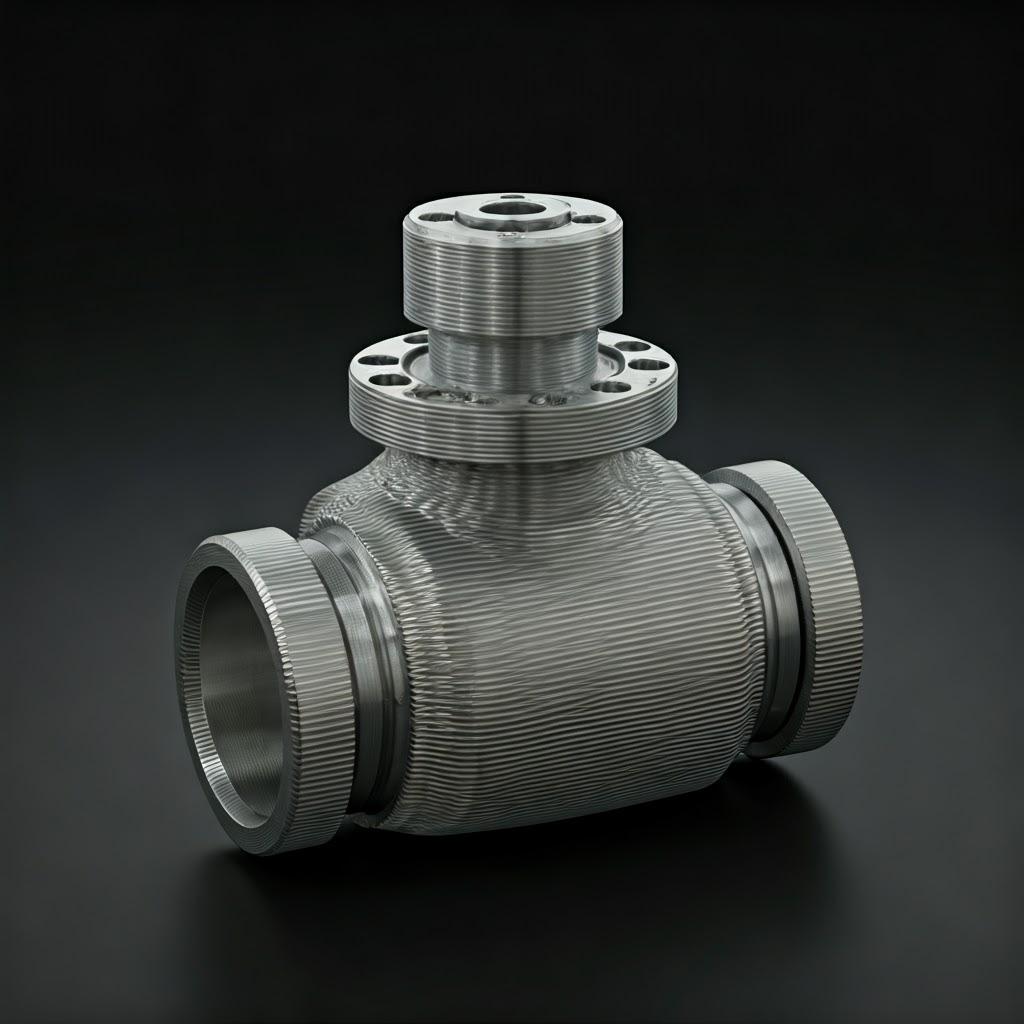
Overcoming Challenges: Mitigating Risks in Metal AM for Actuator Housings
While metal additive manufacturing offers significant advantages, it’s not without its challenges. Successfully implementing metal AM for critical components like valve actuator housings requires awareness of potential pitfalls and proactive strategies to mitigate risks throughout the design, printing, and post-processing stages. Addressing these challenges ensures the production of reliable, high-quality parts that meet stringent performance requirements. Industrial distributors and B2B buyers need assurance that their suppliers have robust processes to manage these potential issues.
Common Challenges and Mitigation Strategies:
- Residual Stress and Distortion:
- チャレンジ: Rapid heating/cooling cycles cause stress buildup, potentially leading to part warpage, cracking, or dimensional inaccuracies, especially after removal from the build plate or during heat treatment. Alloys like IN625 can be particularly susceptible.
- Mitigation:
- DfAM: Design features to minimize large thermal gradients (e.g., avoid abrupt thickness changes, use fillets).
- Build Strategy: Optimize build orientation and support structures to counteract stress and anchor the part effectively. Use simulation tools to predict stress patterns.
- Process Parameters: Fine-tune laser/beam parameters (power, speed, scan strategy) to reduce thermal input and stress. Utilize heated build chambers where available.
- 後処理: Implement appropriate stress relief heat treatment cycles promptly after printing and before support removal. Consider HIP for stress reduction and defect closure.
- Porosity and Internal Defects:
- チャレンジ: Small voids or pores can form within the printed material due to incomplete fusion between layers, gas entrapment, or powder inconsistencies. Porosity can negatively impact mechanical properties, particularly fatigue life and pressure tightness.
- Mitigation:
- High-Quality Powder: Use consistent, high-purity metal powders with good flowability and controlled particle size distribution, such as those produced by Met3dp using advanced atomization techniques. Ensure proper powder handling and storage to avoid contamination or moisture absorption.
- Optimized Process Parameters: Develop and rigorously qualify printing parameters (power, speed, layer thickness, hatch spacing) to ensure full melting and fusion, achieving high part density (>99.5% is common).
- Process Monitoring: Utilize in-situ monitoring systems (if available) to detect potential anomalies during the build.
- 後処理: Hot Isostatic Pressing (HIP) is highly effective at closing internal gas porosity, significantly improving density and mechanical integrity.
- NDT: Employ CT scanning or other NDT methods to inspect critical parts for internal defects.
- Support Structure Removal Difficulties:
- チャレンジ: Supports in complex internal channels or hard-to-reach areas can be very difficult or impossible to remove completely, potentially trapping powder or obstructing fluid flow. Removal processes can also damage the part surface.
- Mitigation:
- DfAM: Design parts to be self-supporting where possible (using angles <45°, chamfers). Optimize orientation to minimize supports. Design internal channels for accessibility or use sacrificial features.
- Support Strategy: Use support types designed for easier removal (e.g., thin contact points, specific geometries).
- Advanced Removal Techniques: Consider electrochemical machining or chemical etching for support removal in specific cases (requires material compatibility).
- Surface Finish Limitations:
- チャレンジ: As-built surface roughness may not meet requirements for sealing surfaces, fluid flow efficiency, or aesthetics. Stair-stepping on curved surfaces can be an issue.
- Mitigation:
- Build Orientation: Optimize orientation to place critical surfaces vertically or upwards.
- Fine Parameters: Use smaller layer thicknesses and optimized beam parameters (can increase build time).
- 後処理: Plan for necessary secondary machining, polishing, or other surface finishing operations on critical areas. Acknowledge that achieving machined finishes often requires the hybrid AM + Machining approach.
- Material Property Variability & Qualification:
- チャレンジ: Ensuring consistent mechanical properties (strength, ductility, fatigue life) batch-to-batch and part-to-part requires rigorous process control and validation, especially for critical applications. Properties can be anisotropic (direction-dependent).
- Mitigation:
- Robust Process Control: Maintain strict control over powder quality, machine calibration, process parameters, and post-processing steps.
- Material Testing: Regularly perform tensile tests, hardness tests, and microstructure analysis on witness coupons printed alongside actual parts.
- Qualification Standards: Follow established industry standards (e.g., ASTM, ISO, AMS) for AM process and material qualification.
- Supplier Expertise: Partner with experienced AM service providers like Met3dp, who have deep materials science knowledge and established quality management systems (e.g., ISO 9001, AS9100 potentially).
- Cost and Lead Time:
- チャレンジ: Metal AM can have higher per-part costs than traditional methods for simple, high-volume parts due to machine time, powder cost, and necessary post-processing. Lead times include printing and extensive post-processing.
- Mitigation:
- DfAM for Cost: Utilize topology optimization and part consolidation to reduce material usage and potentially build time. Design for efficient post-processing.
- Application Selection: Focus AM on applications where its benefits (complexity, speed for low vol, customization) outweigh the costs – complex actuator housings are often prime candidates.
- Efficient Workflow: Work with suppliers who offer integrated printing and post-processing capabilities to streamline the workflow and potentially reduce overall lead time. Request detailed quotes covering all steps for accurate B2B cost comparison.
By understanding these challenges and implementing appropriate mitigation strategies, manufacturers can confidently leverage metal AM to produce complex, high-performance valve actuator housings that meet the demanding requirements of modern industrial applications. A proactive approach focusing on DfAM, process control, and collaboration with knowledgeable suppliers is key to success.
Supplier Selection: Choosing the Right Metal AM Service Provider for Actuator Housings
Selecting the right additive manufacturing partner is as critical as the design and material choices when producing functional components like valve actuator housings. The quality, reliability, and cost-effectiveness of your final product heavily depend on the capabilities, expertise, and quality systems of your chosen metal AM service provider. For procurement managers, engineers, and B2B buyers, evaluating potential suppliers requires a thorough assessment beyond just quoting price.
A reliable supplier acts as a partner, offering technical guidance, ensuring process consistency, and delivering parts that meet stringent specifications. Companies like メット3dp, headquartered in Qingdao, China, exemplify the qualities of a leading provider, specializing in both advanced metal AM equipment and high-performance powders, backed by decades of collective expertise.
Key Criteria for Evaluating Metal AM Service Providers:
- Technical Expertise & Experience:
- Application Knowledge: Does the supplier understand the specific challenges and requirements of industrial components like valve actuator housings? Do they have experience with similar parts or industries (aerospace, oil & gas, medical)?
- Materials Science: Do they possess deep knowledge of the materials you require (e.g., 316L, IN625), including their behavior during printing and post-processing? Can they advise on material selection?
- DfAM Support: Do they offer design consultation or DfAM services to help optimize your housing design for printability, performance, and cost-effectiveness?
- Problem Solving: Can they demonstrate a track record of overcoming AM challenges (warpage, porosity, etc.)?
- Technology & Equipment:
- AM Process Capability: Do they operate the appropriate metal AM technology (e.g., PBF-LB/M, PBF-EB/M) best suited for your housing’s complexity, material, and tolerance requirements?
- Machine Fleet & Capacity: Do they have sufficient, well-maintained machines to handle your volume requirements and provide reasonable lead times? What is the build volume of their machines? Met3dp highlights industry-leading print volume, accuracy, and reliability.
- パウダーハンドリング: Do they have robust procedures for powder handling, storage, traceability, and recycling to ensure material quality and consistency? Met3dp’s use of advanced gas atomization and PREP technologies for powder production is a significant advantage here.
- Material Portfolio & Quality:
- Available Materials: Do they offer the specific alloys (316L, IN625, etc.) you need? Can they source or process other specialized alloys if required?
- パウダーの質: Can they provide documentation or certification regarding the quality, composition, and characteristics (particle size distribution, morphology) of the powders they use? Do they manufacture their own powders or source from reputable suppliers?
- Material Traceability: Do they maintain full traceability of powder batches throughout the manufacturing process?
- Post-Processing Capabilities:
- Integrated Services: Does the supplier offer in-house capabilities for essential post-processing steps like heat treatment, support removal, CNC machining, surface finishing, and cleaning? An integrated workflow often improves lead times, quality control, and accountability.
- Subcontractor Management: If they subcontract certain processes (like HIP or specialized NDT), do they have a robust system for managing and qualifying these vendors?
- Quality Management System (QMS) & Certifications:
- 認定: Do they hold relevant certifications, such as ISO 9001 (General Quality Management), AS9100 (Aerospace), ISO 13485 (Medical Devices), or specific customer/industry approvals? Certifications indicate a commitment to standardized processes and quality control.
- Inspection & Testing: What are their capabilities for dimensional inspection (CMM, scanning), material testing, and NDT (CT scanning, dye penetrant, ultrasonic)? Can they provide detailed inspection reports?
- プロセス制御: Do they have documented procedures for machine calibration, parameter control, environmental monitoring, and process validation?
- Cost, Lead Time & Communication:
- Quoting Clarity: Do they provide detailed quotes that break down costs for printing, materials, supports, post-processing, and inspection?
- Lead Time Estimates: Are their lead time estimates realistic and based on current capacity and the full scope of work (including post-processing)?
- Responsiveness & Support: Are they responsive to inquiries? Is there a dedicated point of contact for technical and commercial questions? How do they handle project updates and communication?
- Location & Logistics:
- 配送: Consider the logistics and costs associated with shipping parts from the supplier’s location, especially for international B2B transactions.
- Facility Audits: Is it possible to audit their facility (in person or virtually) to verify their capabilities and processes?
Supplier Evaluation Checklist:
基準 | 質問 | Ideal Response Indicator |
---|---|---|
専門知識 | Experience with actuator housings/similar parts? DfAM support offered? | Yes, Case studies available, Design services offered |
テクノロジー | Appropriate AM process? Sufficient capacity? Modern equipment? | Yes, Specific machines listed, Capacity stated |
材料 | Required alloys available? Powder quality certified? Traceability maintained? | Yes, Material datasheets, Certs of Conformance, Trace logs |
後処理 | In-house machining, heat treat, finishing? Qualified subcontractors? | Yes, List of in-house capabilities, Vendor quals |
品質 | Relevant certifications (ISO 9001, AS9100)? Advanced inspection capabilities? | Yes, Certs provided, CMM/CT/NDT available |
コマーシャル | Clear quotes? Realistic lead times? Good communication? | Yes, Detailed quotes, Transparent communication |
物流 | Favorable location/shipping? Audit possible? | Yes, Reasonable shipping, Open to audits |
Export to Sheets
Choosing a supplier is a strategic decision. Look for a partner like Met3dp that demonstrates not only the technical capabilities but also a commitment to quality, collaboration, and understanding your specific application needs. Thorough vetting ensures a successful outcome for your complex actuator housing project.
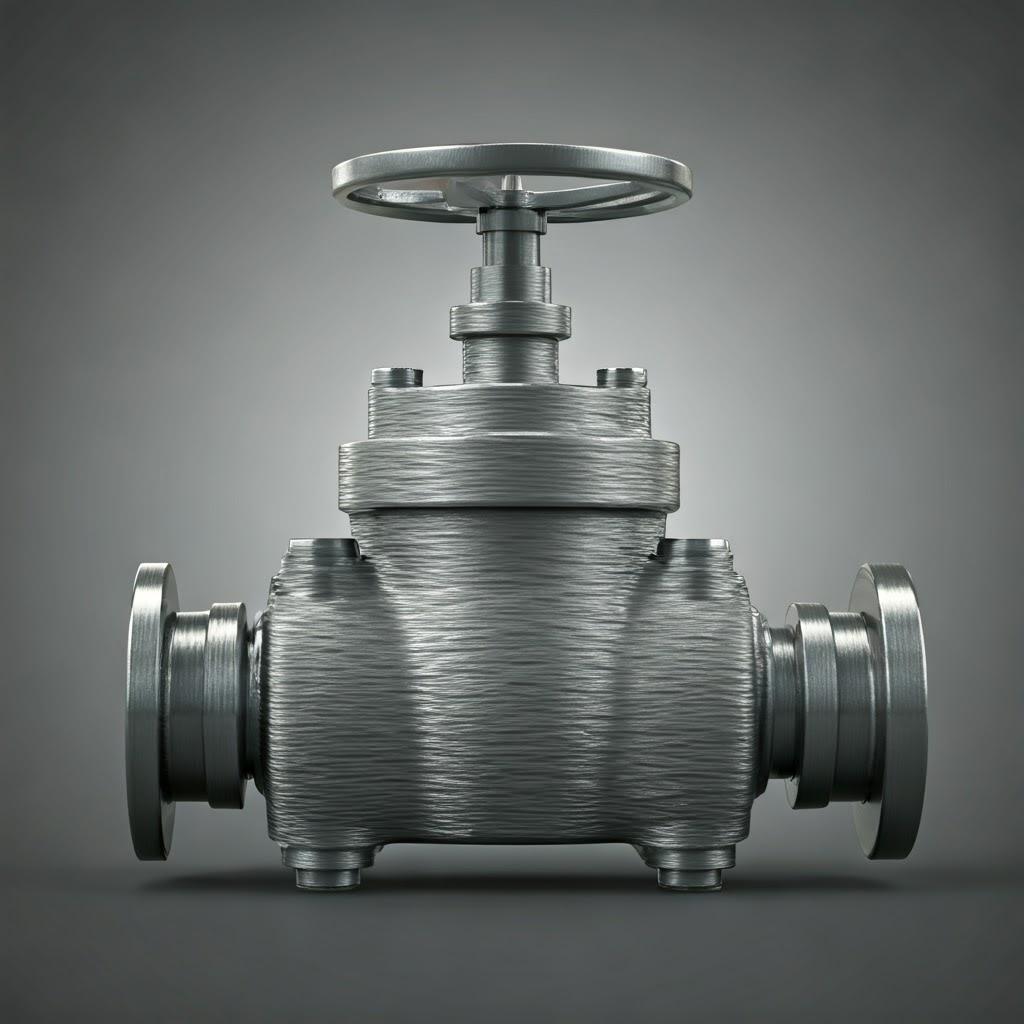
Cost & Timeline: Understanding Pricing Factors and Lead Times for B2B Orders
One of the most critical considerations for procurement managers and engineers evaluating metal additive manufacturing for valve actuator housings is understanding the associated costs and expected timelines. While AM offers unique advantages, its cost structure and lead time components differ from traditional methods. Clear communication with potential suppliers and a comprehensive understanding of the factors involved are essential for accurate budgeting and project planning in a B2B context.
Factors Influencing the Cost of Metal AM Actuator Housings:
- Part Volume & Material Consumption:
- Direct Material Cost: The amount of metal powder consumed is a primary cost driver. Larger or denser parts require more material. High-performance alloys like IN625 are significantly more expensive per kilogram than 316L.
- サポート材: Material used for support structures also adds to the cost. Optimized designs (DfAM) minimize support needs.
- Machine Time (Build Time):
- Complexity & Height: Build time is largely determined by the height of the part(s) in the build chamber and the number of layers required. Complex internal features don’t necessarily increase print time significantly (unlike machining), but taller parts do.
- Nesting & Build Density: Suppliers aim to maximize the number of parts printed in a single build (“nesting”) to distribute the machine setup and operation costs. Unit cost decreases as more parts are printed simultaneously.
- Machine Rate: AM machines have high capital costs and operational expenses (power, gas, maintenance), factored into an hourly machine rate.
- Labor & Engineering:
- File Preparation: Setting up the build file, optimizing orientation, and generating support structures requires skilled technician/engineer time.
- DfAM Services: If design assistance or optimization is required, this engineering time adds to the cost.
- Post-Processing Labor: Manual tasks like depowdering, support removal, surface finishing, and inspection contribute significantly to the overall labor cost.
- 後処理の要件:
- 熱処理: Costs associated with furnace time, energy, and controlled atmospheres/vacuum. HIP is a relatively expensive but often necessary step for critical parts.
- 機械加工: CNC machining time, tooling, and programming costs for achieving tight tolerances and specific finishes. The more features requiring machining, the higher the cost.
- 表面仕上げ: Costs depend on the method (blasting, tumbling, polishing) and the required level of finish.
- Inspection: Time and equipment costs for CMM, NDT (e.g., CT scanning), and other quality checks.
- Powder Quality & Management:
- Premium Powders: Using high-quality, certified powders (essential for reliable performance) costs more than lower-grade powders. Providers like Met3dp invest heavily in powder production technology.
- Recycling & Handling: Costs associated with powder sieving, testing, and management to ensure quality when reusing powder.
- Order Volume & Urgency:
- ボリュームディスカウント: Per-part costs typically decrease with larger batch sizes due to amortization of setup costs and optimized build nesting. Wholesale pricing structures may apply for significant quantities.
- Expedited Service: Faster lead times usually incur premium charges.
Factors Influencing Lead Times:
- ビルドタイム: The actual printing time, which can range from hours to several days depending on part height and build density.
- Machine Availability & Queue: Supplier backlog and scheduling significantly impact when a build can start.
- Post-Processing Duration: This is often the longest part of the timeline.
- Heat Treatment Cycles: Can take 1-3 days (including furnace heating/cooling).
- Machining: Varies greatly with complexity (days to weeks).
- Support Removal/Finishing: Labor-intensive steps that add time.
- HIP: Requires scheduling with specialized facilities and can add a week or more.
- Inspection: Can add several days depending on the extent required.
- Shipping & Logistics: Time required for packaging and transport.
Typical Lead Time Breakdown (Example – May Vary Significantly):
- File Prep & Scheduling: 1-5 days
- 印刷: 1-7 days
- 熱処理: 1~3日
- Support Removal / Basic Finishing: 1~3日
- CNC Machining (if required): 3-10 days
- Advanced Finishing / HIP (if required): 3-7 days
- Inspection: 1~3日
- 配送: 1-5 days (domestic)
Total Estimated Lead Time: Could range from 2週間 (simple part, no machining) to 6+ weeks (complex part, extensive post-processing).
Getting Accurate Quotes & Timelines:
- Provide a complete 3D CAD model and 2D drawing specifying critical dimensions, tolerances (GD&T), surface finishes, and material.
- Clearly define all post-processing requirements (heat treatment specs, finishing, inspection needs).
- Specify the required quantity and desired delivery date.
- Discuss expectations and potential trade-offs (e.g., cost vs. speed) with the supplier.
Understanding these cost drivers and timeline components allows B2B buyers and engineers to have informed discussions with suppliers like those found on the main Met3dp homepage, budget effectively, and set realistic project schedules for acquiring complex metal AM actuator housings.
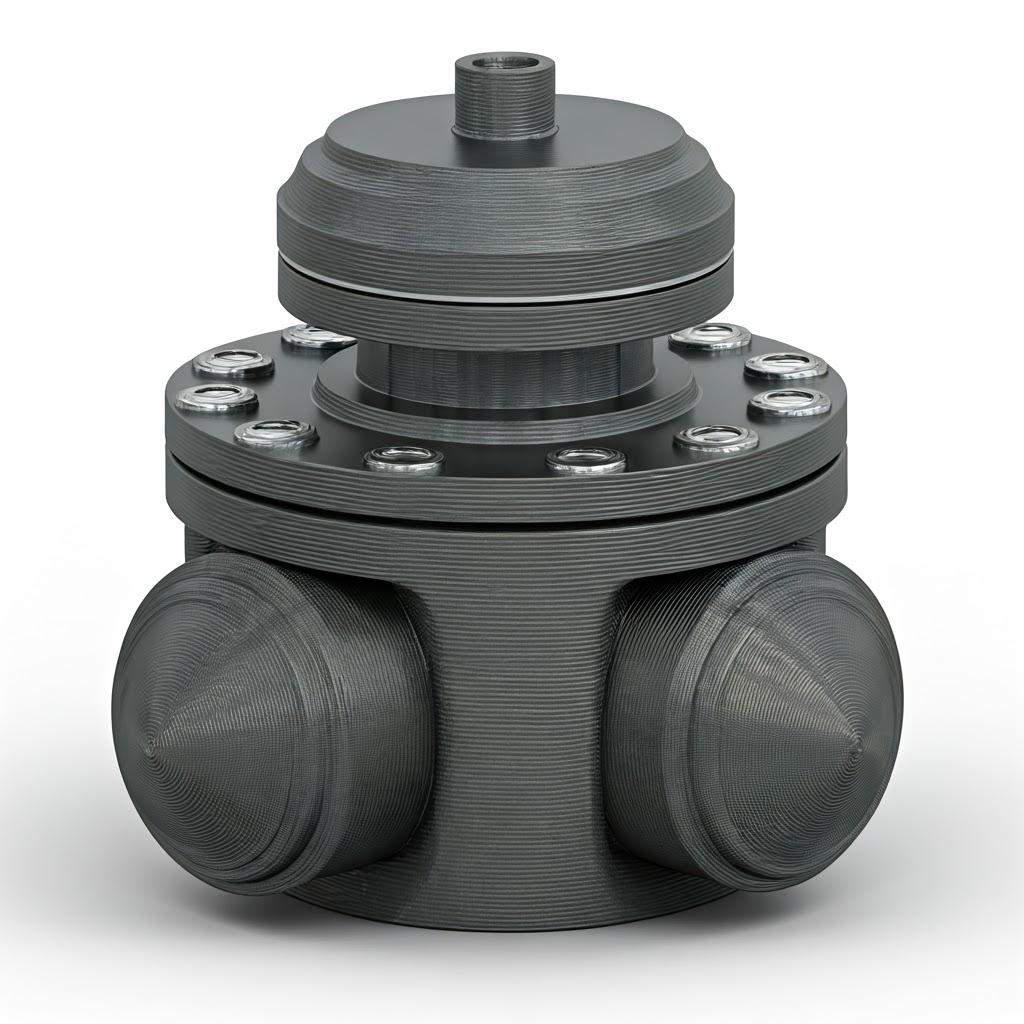
Frequently Asked Questions (FAQ): Addressing Common Questions about Metal 3D Printed Actuator Housings
Here are answers to some common questions engineers and procurement managers have when considering metal additive manufacturing for valve actuator housings:
1. Is metal 3D printing strong enough for industrial actuator housings?
Absolutely. Metal AM processes like Powder Bed Fusion (using lasers or electron beams) can produce parts with densities exceeding 99.5%, often matching or even surpassing the mechanical properties (tensile strength, yield strength, hardness) of equivalent wrought or cast materials, especially after appropriate post-processing like heat treatment or Hot Isostatic Pressing (HIP). When using high-performance alloys like 316L Stainless Steel or IN625 Nickel Superalloy, and partnering with experienced providers who optimize process parameters and perform rigorous quality control (like Met3dp), the resulting housings exhibit excellent strength, durability, and pressure integrity suitable for demanding industrial environments. The key is proper design (DfAM), material selection, process control, and post-processing tailored to the application’s load requirements.
2. How does the cost of a metal 3D printed actuator housing compare to casting or machining?
The cost comparison depends heavily on part complexity, volume, and material:
- 複雑さ: For highly complex geometries, internal features, or topology-optimized designs, metal AM can be より費用対効果が高い than machining (due to reduced setup and toolpath complexity) or casting (due to avoiding intricate tooling costs).
- ボリューム:
- Low Volume (Prototypes, 1-100 parts): Metal AM is often competitive or cheaper than casting (avoids high tooling costs) and potentially competitive with machining (depending on complexity).
- Medium Volume (100s of parts): Costs become more comparable, requiring careful analysis. Part consolidation via AM can sometimes offset higher per-part print costs.
- High Volume (1000s+ parts): Traditional casting or high-volume machining is typically more economical for simpler, standardized designs.
- 素材: AM significantly reduces waste for expensive alloys like IN625 compared to subtractive machining, which can lead to cost savings despite higher powder costs.
Rule of Thumb: AM is most cost-effective for complex, low-to-medium volume parts, especially when leveraging design freedom for part consolidation or performance enhancement. Always get detailed quotes for your specific housing design from both AM providers and traditional manufacturers for a direct comparison.
3. What level of detail and minimum feature size can be achieved with metal AM for features like sensor ports or internal channels?
The achievable level of detail depends on the specific AM process (PBF-LB/M generally offers finer features than PBF-EB/M), the machine’s laser/electron beam spot size, the powder particle size, and the chosen layer thickness. Typically:
- Minimum Wall Thickness: Around 0.4mm to 1.0mm.
- Minimum Feature Size (e.g., pins, bosses): Diameters around 0.5mm to 1.0mm.
- Small Holes: Diameters down to 0.5mm may be possible, but printability (especially horizontally) and powder removal become challenging. Designing slightly larger holes or using self-supporting shapes (teardrops) is often recommended.
- Internal Channels: Complex channels are a strength of AM, but minimum diameters are often kept above 1-2mm to ensure effective powder removal. Design considerations (smooth bends, access points) are crucial.
For extremely fine details or critical tolerances on small features, it’s common practice to print the main housing structure via AM and then use secondary micro-machining or standard CNC machining to create those precise features during post-processing. Discussing specific feature requirements with your AM provider during the DfAM stage is essential.
Conclusion: The Future of Valve Actuation with Metal Additive Manufacturing
Metal additive manufacturing is rapidly transitioning from a prototyping tool to a viable, value-driven production method for complex industrial components, and valve actuator housings stand as a prime example of its potential. By overcoming the geometric constraints of traditional casting and machining, metal AM empowers engineers to design housings that are lighter, more efficient, highly customized, and capable of integrating advanced features like internal channels or optimized mounting points.
The ability to utilize high-performance alloys like corrosion-resistant 316L stainless steel and high-temperature IN625 superalloy ensures that 3D printed housings can meet the rigorous demands of critical applications in aerospace, oil & gas, chemical processing, power generation, and beyond. While challenges related to process control, post-processing, and cost exist, they are continuously being addressed through advancements in technology, materials science, and DfAM methodologies.
Partnering with knowledgeable and capable suppliers is paramount to successfully leveraging metal AM. Companies like Met3dp, with their integrated expertise in advanced printing systems (offering industry-leading volume and accuracy), high-quality powder production using cutting-edge atomization techniques, and comprehensive application support, are enabling this manufacturing transformation.
For engineers seeking enhanced performance and design freedom, and for procurement managers looking for resilient supply chains, reduced lead times for complex parts, and potential for total cost reduction through part consolidation and optimization, metal AM presents a compelling pathway forward. As the technology matures and adoption grows, metal 3D printed valve actuator housings will undoubtedly play an increasingly significant role in the future of precise, reliable, and efficient industrial flow control systems. Exploring the possibilities offered by providers on platforms like Met3dp is the first step towards unlocking this potential for your applications.
シェアする
MET3DP Technology Co., LTDは、中国青島に本社を置く積層造形ソリューションのリーディングプロバイダーです。弊社は3Dプリンティング装置と工業用途の高性能金属粉末を専門としています。
関連記事
Met3DPについて
最新情報
製品
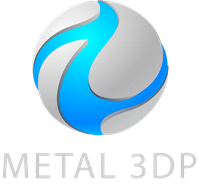
3Dプリンティングと積層造形用金属粉末