3D Printed Electronics Bays for UAVs
目次
Introduction: Revolutionizing UAV Design with 3D Printed Electronics Bays
Unmanned Aerial Vehicles (UAVs), commonly known as drones, have rapidly transitioned from niche applications to indispensable tools across a multitude of sectors, including aerospace, defense, surveillance, agriculture, logistics, and infrastructure inspection. At the heart of every advanced UAV lies the electronics bay – a critical enclosure housing the flight controller, sensors, communication systems, power distribution units, and other vital avionics. The design and manufacture of this bay significantly impact the drone’s overall performance, reliability, payload capacity, and flight endurance. Traditionally, manufacturing these enclosures involved methods like CNC machining from billet material or complex sheet metal fabrication, often leading to compromises in weight, design flexibility, and production lead times.
Enter the era of 金属積層造形(AM), more commonly known as metal 3Dプリンティング. This transformative technology is rewriting the rules for designing and producing complex, high-performance components like UAV electronics bays. Instead of subtracting material, AM builds parts layer by layer directly from digital models using specialized metal powders. This approach unlocks unprecedented design freedom, enabling engineers to create highly optimized, lightweight structures with integrated functionalities that were previously impossible or prohibitively expensive to manufacture.
For procurement managers and engineers focused on sourcing custom UAV electronics bays, understanding the potential of metal 3D printing is crucial. It offers a pathway to:
- パフォーマンスの向上: Creating lighter bays increases payload capacity and flight time. Integrated cooling channels improve thermal management for sensitive electronics.
- Rapid Innovation: Faster prototyping and iteration cycles accelerate development timelines.
- Supply Chain Resilience: On-demand production reduces reliance on complex traditional supply chains and tooling.
- パーツの統合: Multiple components can be integrated into a single printed part, reducing assembly time, weight, and potential failure points.
次のような企業 メット3dp, a leading provider of additive manufacturing solutions, are at the forefront of this revolution. Specializing in advanced 金属3Dプリンティング technologies and high-performance metal powders, Met3dp empowers industries to leverage AM for mission-critical components. Our expertise spans Selective Electron Beam Melting (SEBM) and other powder bed fusion processes, coupled with the in-house production of superior quality metal powders using state-of-the-art gas atomization and Plasma Rotating Electrode Process (PREP) technologies. This vertical integration ensures materials optimized for demanding applications like UAV electronics bays, delivering parts with exceptional density, mechanical properties, and reliability.
This blog post serves as a comprehensive guide for engineers and procurement specialists considering metal 3D printing for custom UAV electronics bays. We will delve into the applications, advantages, material selection (focusing on AlSi10Mg and A6061), design considerations, quality standards, post-processing, challenges, supplier selection, and cost factors. Whether you are looking for a wholesale supplier of 3D printed drone components or seeking a reliable manufacturing partner for bespoke designs, this guide will provide the insights needed to make informed decisions and harness the power of additive manufacturing for next-generation UAV systems.
Key Applications: Where Custom UAV Electronics Bays Make a Difference
The versatility and performance enhancements offered by 3D printed metal electronics bays make them suitable for a wide array of UAV applications, particularly where weight, thermal performance, and environmental resilience are critical design drivers. As UAVs push the boundaries of endurance, payload capacity, and operational environments, the demands on their core components intensify. Custom-designed, additively manufactured electronics bays provide tailored solutions meeting these stringent requirements.
1. Aerospace and Defense: This sector represents a primary market for high-performance UAVs used in surveillance, reconnaissance, target acquisition, and communication relays.
- Requirement: Extreme lightweighting, high structural integrity, resistance to vibration and shock, reliable thermal management for densely packed electronics operating in varying altitudes and temperatures. MIL-STD compliance is often necessary.
- AM Advantage: Metal 3D printing allows for topology optimization to remove unnecessary material while maintaining strength, integration of conformal cooling channels, and the use of high-strength, aerospace-grade aluminum alloys like AlSi10Mg and A6061. Custom mounts and fixtures for specific sensors or communication gear can be directly integrated into the bay design, reducing part count and assembly complexity. Procurement managers in defense contracting benefit from the potential for rapid deployment and replacement parts produced on-demand.
2. Commercial Surveillance and Security: UAVs are increasingly used for border patrol, critical infrastructure monitoring (pipelines, power lines), event security, and large-area surveillance.
- Requirement: Long endurance, reliable operation in diverse weather conditions, secure housing for sensitive cameras and sensors, potentially EMI shielding.
- AM Advantage: Lightweight bays extend flight times crucial for persistent surveillance. Metal enclosures offer inherent durability and environmental protection compared to polymers. Design flexibility allows for integrated features like Faraday cages or specific mounting points for advanced electro-optical/infrared (EO/IR) payloads. UAV component suppliers utilizing AM can offer customized enclosure solutions tailored to specific sensor suites.
3. Logistics and Delivery Drones: The emerging field of drone delivery requires UAVs capable of carrying significant payloads reliably and efficiently, often in urban or semi-urban environments.
- Requirement: Maximized payload-to-weight ratio, robust construction for frequent takeoff/landing cycles, efficient thermal dissipation for electronics managing power delivery and navigation.
- AM Advantage: Every gram saved in the airframe, including the electronics bay, translates directly to increased payload capacity or range. Metal AM enables the creation of durable yet lightweight bays capable of withstanding the rigors of delivery operations. Complex geometries achievable with AM can facilitate better airflow and heat dissipation.
4. Industrial Inspection and Mapping: Drones equipped with specialized sensors are used for inspecting wind turbines, bridges, solar farms, and for creating detailed topographical maps or 3D models.
- Requirement: Stable platform for high-resolution sensors, resistance to industrial environments (dust, moisture), precise mounting for sensor alignment, efficient heat management for processing units.
- AM Advantage: 3D printing allows for the creation of highly rigid and stable mounting structures integrated within the electronics bay, minimizing vibration effects on sensitive Lidar or photogrammetry equipment. Custom seals and ingress protection features can be designed into the bay. Optimized thermal pathways ensure electronics operate within safe limits during long inspection flights.
5. Scientific Research and Environmental Monitoring: UAVs deploy sensors into challenging environments – from volcanic plumes to arctic conditions – to gather crucial data.
- Requirement: Environmental resilience (temperature extremes, corrosive atmospheres), customized sensor integration, lightweight design for maximizing flight time in remote areas.
- AM Advantage: Metal AM allows the use of alloys resistant to specific environmental challenges. Bespoke bay designs can accommodate unique research payloads and ensure their protection and optimal function. The ability to rapidly prototype and modify designs is invaluable for research missions with evolving requirements.
Table: UAV Application vs. Electronics Bay Requirements & AM Benefits
Application Sector | Key Electronics Bay Requirements | How Metal 3D Printing Adds Value | Relevant B2B Keywords |
---|---|---|---|
航空宇宙・防衛 | Lightweight, High Strength, Vibration Resistance, Thermal Mgmt. | Topology Optimization, Integrated Cooling, High-Performance Alloys (AlSi10Mg, A6061), Part Consolidation, Rapid Prototyping | Defense UAV components, Military drone parts supplier, AS9100 |
Commercial Security | Long Endurance, Weather Resistance, Sensor Protection, EMI Shielding | Lightweighting, Durable Metal Enclosure, Custom Mounts, Integrated Shielding Features | Surveillance drone parts, UAV sensor housing manufacturer |
物流と配送 | Max Payload Capacity, Robustness, Thermal Efficiency | Extreme Lightweighting, Durable Construction, Optimized Airflow/Heat Sink Design | Delivery drone components wholesale, UAV logistics solutions |
Industrial Inspection | Sensor Stability, Environmental Sealing, Precise Mounting | High Rigidity Structures, Integrated Seals (IP rating), Custom Sensor Mounts, Thermal Management | Industrial drone parts supplier, UAV inspection systems |
Research & Monitoring | Environmental Resilience, Custom Payload Integration, Lightweight | Specialized Alloys, Bespoke Design Freedom, Rapid Iteration, Weight Reduction | Research UAV components, Custom drone parts manufacturing |
Export to Sheets
By understanding these specific application needs, engineers can leverage the design freedom of metal AM, and procurement managers can identify UAV parts distributors and manufacturers like Met3dp capable of delivering tailored, high-performance solutions. The ability to customize electronics bays precisely for the mission enhances the overall value and capability of the UAV system.
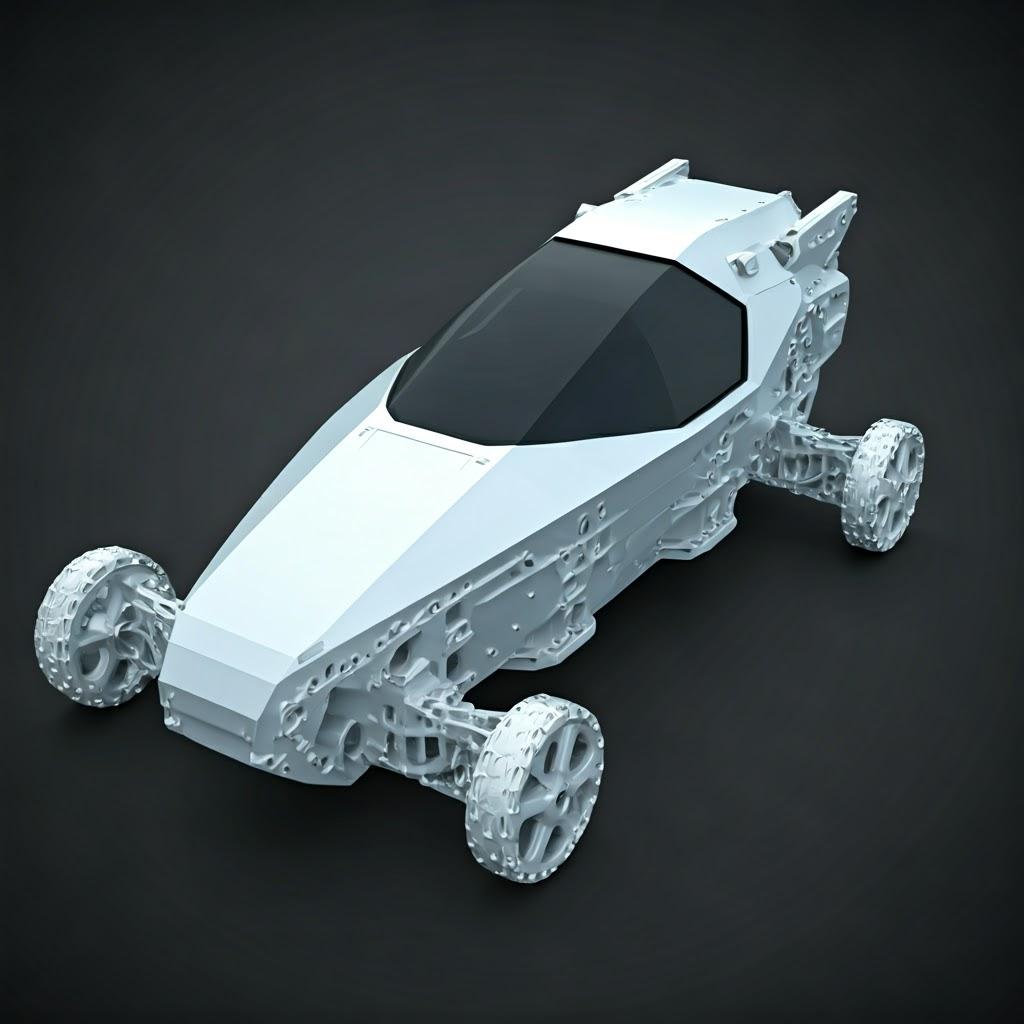
Why Metal 3D Printing? Unlocking Performance Advantages for UAV Electronics Bays
Choosing the right manufacturing process is as critical as selecting the right materials or design. For custom UAV electronics bays, metal additive manufacturing offers a compelling suite of advantages over traditional methods like CNC machining, casting, or sheet metal fabrication. These benefits directly address the core challenges faced by UAV designers and manufacturers: weight reduction, thermal management, design complexity, lead time, and cost-effectiveness for custom or low-volume production.
1. Unmatched Lightweighting Potential:
- チャレンジ: Every gram saved on a UAV component contributes to longer flight times, increased payload capacity, or enhanced maneuverability. Traditional methods often leave excess material or require bulky designs to achieve necessary strength.
- AM Solution: Metal 3D printing excels at creating complex, topology-optimized geometries. Algorithms can analyze stress distributions and remove material from non-critical areas, resulting in highly efficient, lattice-like structures or organically shaped parts that maintain structural integrity with significantly reduced mass. This is particularly effective for aluminum alloys like AlSi10Mg and A6061, which already possess favorable strength-to-weight ratios. For UAV manufacturing solutions providers, offering topology-optimized components is a key differentiator.
2. Design Freedom and Part Consolidation:
- チャレンジ: Traditional manufacturing methods impose constraints. Machining is limited by tool access, sheet metal by bending radii, and casting by draft angles and mold complexity. Assembling multiple simple parts increases weight, potential failure points, and labor costs.
- AM Solution: Additive manufacturing builds parts layer by layer, freeing designers from many traditional constraints. This enables:
- Complex Internal Channels: Integrate conformal cooling channels that follow the contours of heat-generating components for superior thermal management.
- Integrated Features: Combine brackets, mounts, connectors, and housings into a single printed part. This drastically reduces assembly time, fastener count, and overall weight.
- Organic Shapes: Create complex curves and variable wall thicknesses optimized for airflow or structural load paths.
- カスタマイズ: Easily tailor designs for specific sensor payloads or mission requirements without the need for expensive tooling changes.
3. Enhanced Thermal Management:
- チャレンジ: UAV electronics bays often house densely packed, heat-generating components. Efficiently dissipating this heat is critical for reliability and performance, especially in varying ambient temperatures and altitudes. Traditional heat sinks can be bulky and add significant weight.
- AM Solution: Metal 3D printing allows for the integration of highly efficient thermal management features directly into the bay’s structure:
- コンフォーマル冷却チャンネル: As mentioned, channels can precisely follow heat sources, using air or liquid cooling.
- Optimized Heat Sink Structures: Print complex fin geometries or lattice structures with significantly higher surface area-to-volume ratios than traditional heat sinks, improving convective cooling.
- High Thermal Conductivity Materials: Utilize aluminum alloys like AlSi10Mg and A6061, known for their excellent thermal conductivity.
4. Rapid Prototyping and Accelerated Development:
- チャレンジ: Developing new UAV platforms involves iterative design cycles. Traditional prototyping methods, especially those requiring tooling (like casting), can be slow and expensive, hindering innovation.
- AM Solution: Metal 3D printing allows engineers to move directly from a CAD model to a physical metal prototype often within days. This facilitates:
- Faster Design Verification: Quickly test form, fit, and function.
- Reduced Iteration Costs: Make design modifications digitally and reprint without tooling changes.
- Quicker Time-to-Market: Accelerate the overall product development lifecycle, a critical advantage in the fast-paced UAV industry. This speed is attractive to procurement managers needing rapid solutions.
5. Cost-Effectiveness for Complex and Low-Volume Production:
- チャレンジ: Tooling costs for traditional methods like injection molding or die casting can be substantial, making them uneconomical for custom designs or low-to-medium volume production runs typical for specialized UAVs. CNC machining complex geometries can result in high material waste and long machining times.
- AM Solution: Metal 3D printing is a toolless process. The primary cost drivers are material consumption, machine time, and post-processing. This makes it highly competitive for:
- Bespoke Designs: Producing unique, customized electronics bays.
- 少量生産: Manufacturing specialized UAV components without high upfront tooling investment.
- 複雑な幾何学: Creating parts that would be difficult or impossible to machine or cast. While per-part cost might be higher than mass-produced simple parts, the total cost of ownership (including tooling, assembly, and improved performance) is often lower for complex, specialized components like UAV electronics bays.
Table: Metal AM vs. Traditional Manufacturing for UAV Electronics Bays
特徴 | 金属積層造形(AM) | CNC加工 | 板金加工 | キャスティング |
---|---|---|---|---|
軽量化 | Excellent (Topology Optimization, Lattices) | Good (Material Removal, but limited complexity) | Fair (Limited by forming) | Fair (Requires draft angles, thicker walls) |
デザインの複雑さ | Very High (Internal channels, integrated features, organic shapes) | Moderate (Limited by tool access) | Low (Limited by bending/joining) | Moderate (Requires molds, draft angles) |
部品の統合 | 素晴らしい | 限定 | 限定 | 限定 |
熱管理 | Excellent (Conformal cooling, optimized heat sinks) | Fair (Machined heat sinks) | 貧しい | Fair (Can cast fins, limited complexity) |
Prototyping Speed | Very Fast | Fast (Depending on complexity) | 中程度 | Slow (Requires pattern/mold) |
金型費用 | なし | Low (Fixturing) | Moderate (Dies, Bending tools) | High (Molds/Patterns) |
Low Volume Cost | 競争的 | Can be High (Material waste, machine time) | Competitive (If design is simple) | Very High (Due to tooling amortization) |
素材オプション | Growing Range (Incl. AlSi10Mg, A6061) | Wide Range | Moderate Range | Wide Range |
Ideal Use Case | Complex, Lightweight, Custom, Low-Medium Vol., Integrated Features | High Precision, Simpler Geometries, Wide Material Choice | Simple Enclosures, Brackets, High Volume | High Volume, Near-Net Shape (less complex) |
Export to Sheets
By leveraging these advantages, companies specializing in 金属3Dプリントサービス, such as Met3dp, provide a powerful alternative for manufacturing next-generation UAV electronics bays that meet and exceed the demanding performance requirements of modern aerial systems.
Material Matters: Selecting AlSi10Mg and A6061 for Optimal UAV Performance
The choice of material is fundamental to the success of any engineering component, and UAV electronics bays are no exception. The material dictates the bay’s weight, strength, thermal conductivity, corrosion resistance, and ultimately, its suitability for the demanding operational environment of a drone. For metal 3D printing, aluminum alloys are often the preferred choice for UAV applications due to their excellent balance of low density and good mechanical properties. Among these, AlSi10Mg そして A6061 stand out as particularly well-suited and are commonly recommended powders.
Understanding the specific characteristics of these alloys and why they excel in additive manufacturing is crucial for engineers designing UAV systems and procurement managers sourcing these components.
AlSi10Mg: AlSi10Mg is a widely used aluminum alloy in additive manufacturing, belonging to the Al-Si-Mg family. It’s essentially a casting alloy adapted for powder bed fusion processes (like Laser Powder Bed Fusion – LPBF/SLM and Electron Beam Melting – EBM).
- キー・プロパティ
- 優れた印刷適性: The silicon content improves fluidity in the melt pool, leading to good processing characteristics and density during printing.
- 優れた強度対重量比: Offers respectable mechanical strength, especially after appropriate heat treatment, combined with low density ($ \approx 2.67 , g/cm^3 ).∗∗∗<16>HighThermalConductivity:∗∗Facilitatesefficientheatdissipationfromenclosedelectronics( \approx 120-140 , W/m \cdot K $ depending on heat treatment).
- 良好な耐食性: Suitable for operation in various atmospheric conditions.
- 溶接性: Can be welded if necessary during post-processing or assembly.
- Benefits for UAV Electronics Bays:
- Lightweight Structures: Its low density is ideal for minimizing overall UAV weight.
- 複雑な幾何学: Its excellent printability allows for the creation of intricate designs, including thin walls, internal channels, and lattice structures often required for optimized bays.
- Thermal Performance: Its high thermal conductivity aids in passively or actively cooling sensitive avionics.
- Availability and Cost: It is one of the most common and relatively cost-effective metal AM powders.
- 検討する:
- Mechanical properties (yield strength, ultimate tensile strength, elongation) are good but generally lower than wrought alloys like A6061 unless specifically heat treated (e.g., T6).
- Achieving peak properties often requires stress relief and subsequent heat treatment (solutionizing and aging).
A6061 (Often Modified for AM, e.g., Scalmalloy® or similar): A6061 is a precipitation-hardenable aluminum alloy containing magnesium and silicon as its major alloying elements. It’s traditionally known as a wrought alloy, valued for its good mechanical properties, weldability, and corrosion resistance. Adapting it effectively for AM has required development, often resulting in specialized variants or parameter optimization.
- Key Properties (of AM-processed A6061 or variants):
- Higher Strength Potential: Compared to AlSi10Mg, A6061 (especially specialized AM variants) can achieve significantly higher tensile and yield strengths after proper heat treatment, approaching or exceeding traditional wrought A6061-T6 properties.
- Good Toughness and Fatigue Resistance: Offers better resistance to fracture and cyclic loading compared to typical AlSi alloys.
- 良好な耐食性: Similar or better than AlSi10Mg.
- Good Thermal Conductivity: Also provides effective heat dissipation ($ \approx 150-170 , W/m \cdot K $ after T6).
- Lower Printability (Historically): Traditional A6061 can be more challenging to print without defects (like cracking) compared to AlSi10Mg due to its wider solidification range. However, specialized powder compositions and optimized process parameters developed by companies like Met3dp have significantly improved its processability.
- Benefits for UAV Electronics Bays:
- High-Strength Applications: Ideal for bays requiring maximum structural integrity, perhaps those subject to high G-loads, significant vibration, or acting as semi-structural airframe components.
- 耐久性がある: Enhanced toughness and fatigue resistance contribute to a longer service life, especially in demanding operational cycles.
- Performance Critical Designs: When maximizing strength-to-weight ratio is paramount, AM A6061 variants can offer superior performance.
- 検討する:
- May require more stringent process control during printing compared to AlSi10Mg to avoid defects.
- Often requires specific, multi-step heat treatments (solutionizing, quenching, aging) to achieve optimal mechanical properties.
- Powder cost and processing might be higher than standard AlSi10Mg.
Met3dp’s Role in Material Excellence: Choosing the right powder is only part of the equation; the quality of that powder is paramount. Met3dp stands out as a premier 金属粉サプライヤー by controlling the entire production process.
- 高度なパウダー製造: Utilizing industry-leading Gas Atomization and Plasma Rotating Electrode Process (PREP) technologies, Met3dp produces metal powders with:
- 高い真球度: Ensures excellent powder flowability and uniform spreading in the printer bed, crucial for consistent layer deposition.
- Low Porosity: Minimizes internal voids within powder particles, leading to denser, stronger final parts.
- Controlled Particle Size Distribution (PSD): Optimized PSD tailored for specific AM processes (LPBF, SEBM) ensures predictable melting behavior and high resolution.
- 高純度: Reduced oxygen and other contaminants prevent defects and ensure optimal material properties.
- Optimized Materials Portfolio: Beyond standard alloys, Met3dp develops and optimizes powders like AlSi10Mg and A6061 specifically for additive manufacturing, ensuring reliable performance and enabling customers to print high-quality, dense metal parts with superior mechanical properties. Our portfolio extends to innovative alloys like TiNi, TiTa, TiAl, TiNbZr, CoCrMo, stainless steels, and superalloys, catering to diverse 金属3Dプリンティング アプリケーションを使用する。
Table: Comparison of AlSi10Mg and A6061 for 3D Printed UAV Electronics Bays
プロパティ | AlSi10Mg (Typical AM, As-Built/Stress Relieved) | AlSi10Mg (Typical AM, T6 Heat Treated) | A6061 / Variants (Typical AM, T6 Heat Treated) | Importance for UAV Bay |
---|---|---|---|---|
密度 | $ \approx 2.67 , g/cm^3 $ | $ \approx 2.67 , g/cm^3 $ | $ \approx 2.70 , g/cm^3 $ | Very High (Lightweighting) |
Yield Strength (YS) | $ \approx 140-180 , MPa $ | $ \approx 230-280 , MPa $ | $ \approx 250-350+ , MPa $ | High (Structural Integrity) |
Ultimate Tensile (UTS) | $ \approx 250-350 , MPa $ | $ \approx 300-380 , MPa $ | $ \approx 300-400+ , MPa $ | High (Structural Integrity) |
Elongation @ Break | $ \approx 3-8 % $ | $ \approx 2-6 % $ | $ \approx 6-15 % $ | Moderate (Toughness/Ductility) |
熱伝導率 | $ \approx 120-140 , W/m \cdot K $ | $ \approx 130-150 , W/m \cdot K $ | $ \approx 150-170 , W/m \cdot K $ | Very High (Heat Dissipation) |
印刷適性 | 素晴らしい | 素晴らしい | Good to Very Good (Process Dependent) | High (Manufacturability, Defect Reduction) |
熱処理 | Recommended (Stress Relief minimum, T6 optional) | Required for peak properties | Required for peak properties | Moderate to High (Process Step, Cost) |
相対コスト | より低い | より低い | より高い可能性 | Moderate (Component Cost) |
こんな方に最適 | General purpose, complex designs, good thermal performance | Strength-enhanced general purpose | High-strength, high-durability requirements | Application Specific |
Export to Sheets
Note: Specific properties can vary significantly based on the AM machine, process parameters, powder quality, build orientation, and exact heat treatment cycle.
Ultimately, the choice between AlSi10Mg and A6061 depends on the specific performance requirements of the UAV electronics bay. For many applications demanding good all-around performance, excellent printability, and effective thermal management, AlSi10Mg is a robust and cost-effective choice. When maximum strength, toughness, and fatigue life are paramount, heat-treated A6061 (or specialized AM variants) becomes the preferred option, provided the manufacturing process is well-controlled. Consulting with an experienced metal additive manufacturing provider like Met3dp, with deep material science expertise and high-quality powder production capabilities, is essential to selecting and successfully utilizing the optimal material for your custom UAV electronics bay.
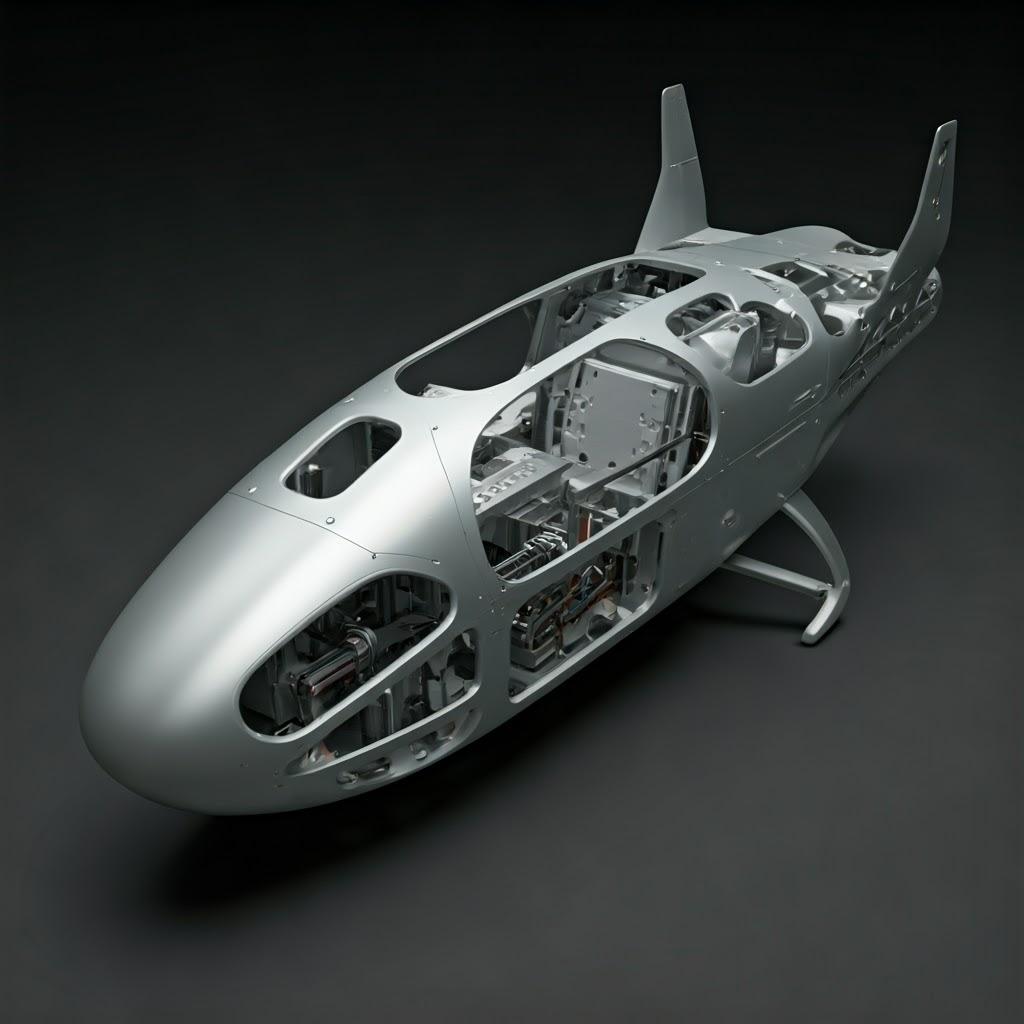
Design for Additive Manufacturing (DfAM): Optimizing UAV Electronics Bays
Simply replicating a design intended for CNC machining or sheet metal using additive manufacturing rarely unlocks the full potential of the technology. To truly harness the benefits of metal 3D printing – lightweighting, part consolidation, enhanced thermal management – engineers must embrace 積層造形設計 (DfAM) principles. DfAM involves rethinking the design process from the ground up, considering the unique capabilities and constraints of layer-by-layer fabrication. Optimizing a UAV electronics bay using DfAM requires careful attention to geometry, topology, feature integration, support structures, and material characteristics.
1. Topology Optimization: This is perhaps the most powerful DfAM tool for lightweighting. Topology optimization software uses Finite Element Analysis (FEA) to determine where material is essential to carry loads and maintain stiffness, removing it from areas where it isn’t needed.
- プロセス Define load cases (vibration, shock, static loads from components), design space (maximum allowable volume), and optimization goals (e.g., minimize mass while meeting stiffness requirements).
- 出力: Often results in organic, lattice-like, or bone-like structures that are highly efficient but difficult or impossible to create with traditional methods.
- UAV Bay Application: Significantly reduces the weight of the bay’s main structure and mounting features, directly improving flight endurance or payload capacity. It ensures strength is placed precisely where needed to withstand operational stresses.
2. Lattice Structures: Incorporating internal or external lattice structures can further reduce weight while maintaining structural integrity and potentially enhancing other properties.
- 種類だ: Various lattice cell types exist (cubic, octet, gyroid, etc.), each offering different mechanical properties (stiffness, energy absorption) and manufacturability characteristics.
- メリット
- 軽量化: High porosity significantly cuts down mass.
- エネルギー吸収: Can improve vibration damping and shock resistance for sensitive electronics.
- 熱管理: High surface area can aid in passive cooling if designed for airflow.
- Manufacturability: Self-supporting lattice designs can minimize the need for internal support structures during printing.
- UAV Bay Application: Used selectively within walls or internal features to reduce mass without compromising overall rigidity. Can be integrated into mounting points for vibration isolation.
3. Part Consolidation: DfAM encourages integrating multiple functions or components into a single printed part.
- Traditional Approach: An electronics bay might consist of a machined housing, separate brackets for PCBs, individual mounts for connectors, covers, and potentially a separate heat sink, all assembled with fasteners.
- AM Approach: Design the bay as a single piece incorporating:
- Integrated PCB standoffs, card guides, and mounting bosses.
- Built-in connector housings.
- Conformal cooling channels or integrated heat sink features.
- Snap-fit features or integrated closures (though metal snap-fits require careful design).
- Cable routing channels or tie-down points.
- メリット Reduces part count, assembly time, weight (eliminates fasteners), potential points of failure, and simplifies inventory management for procurement managers.
4. Feature Design Considerations:
- 壁の厚さ: AM processes can create very thin walls, but there are practical limits depending on the machine, material, and part geometry (typically >0.4-0.5 mm). Ensure walls are thick enough for structural integrity and handling. Variable wall thickness, easily achieved with AM, can optimize material usage.
- Holes and Channels: Horizontal holes often print slightly elliptical and may require support. Vertical holes generally print more accurately. Small internal channels (<0.5 mm) can be difficult to clear of powder. Design channels with self-supporting shapes (diamond, teardrop) where possible. Consider access points for powder removal.
- Overhangs and Supports: Surfaces angled less than ~45 degrees from the horizontal typically require support structures during printing to prevent collapse or warping. Supports add material cost, print time, and post-processing effort (removal and surface finishing).
- DfAM Strategy: Orient the part on the build plate to minimize steep overhangs. Design features to be self-supporting (e.g., use chamfers instead of sharp overhangs, design channels with teardrop shapes). If supports are unavoidable, design them for easy removal and minimize their contact points on critical surfaces.
- Minimum Feature Size: Small pins, bosses, or thin fins have minimum printable sizes related to the laser/electron beam spot size and powder particle size.
- Filleting: Add fillets to sharp internal corners to reduce stress concentrations, which is good practice generally but particularly important in AM where layer lines can act as potential initiation sites.
5. Designing for Thermal Management: DfAM allows sophisticated thermal solutions to be built directly into the bay.
- Conformal Cooling: Channels that precisely follow the contours of heat-generating components (processors, power regulators).
- Integrated Heat Sinks: Print complex fin structures (pin fins, wavy fins, lattices) with high surface areas directly onto the bay walls where needed.
- Heat Pipes Integration: Design channels or cavities specifically shaped to accommodate the insertion and bonding of heat pipes during assembly.
- Material Choice: Leverage the thermal conductivity of AlSi10Mg or A6061.
6. Considering the AM Process: 具体的には 印刷方法 used impact design choices. For example:
- Laser Powder Bed Fusion (LPBF/SLM): Generally offers finer resolution and better surface finish but may require more support structures and can generate higher residual stresses.
- Electron Beam Melting (EBM/SEBM): Operates at higher temperatures, reducing residual stress and often requiring fewer supports, but typically has a rougher surface finish and slightly lower resolution. Met3dp’s expertise in SEBM allows for efficient production of components with complex geometries and reduced post-processing needs.
Table: DfAM Strategies for UAV Electronics Bays
DfAM Principle | テクニック | Benefit for UAV Bay | Implementation Notes |
---|---|---|---|
軽量化 | Topology Optimization, Lattice Structures | Reduced mass, increased flight time/payload | Requires specialized software, careful load case definition |
部品の統合 | Integrating brackets, mounts, connectors, thermal features | Reduced part count, assembly time, weight, failure points | Rethink assembly; consider accessibility for electronics installation/maintenance |
熱管理 | Conformal cooling channels, integrated optimized heat sinks | Improved electronic reliability, performance | Requires thermal simulation (CFD), consider fluid flow if liquid cooled |
Support Reduction | Optimal part orientation, self-supporting angles (>45°), teardrop shapes | Reduced print time, material waste, post-processing effort, improved surface finish | Analyze overhangs; use AM-specific design features |
Feature Optimization | Minimum wall thickness/feature size, hole orientation, filleting corners | Improved manufacturability, structural integrity, reduced stress concentrations | Adhere to process-specific design rules provided by the AM service provider |
Process Awareness | Designing for specific AM technology (LPBF vs. EBM) | Optimized print success, reduced stress/distortion, tailored surface finish | Consult with AM provider (like Met3dp) on machine capabilities |
Export to Sheets
By integrating these DfAM principles, engineers can design UAV electronics bays that are not just manufactured additively but are truly optimized for the process, unlocking significant performance gains and competitive advantages. Collaborating with an experienced AM partner like Met3dp early in the design phase is highly recommended to leverage their expertise in DfAM and ensure manufacturability.
Precision and Quality: Tolerance, Surface Finish, and Dimensional Accuracy Standards
While metal 3D printing offers incredible design freedom, it’s crucial for engineers and procurement managers to have realistic expectations regarding the achievable precision, tolerances, and surface finish of printed parts. These factors directly impact the fit, form, and function of the UAV electronics bay, influencing how well PCBs mount, connectors align, and the bay integrates with the overall airframe. Quality control throughout the AM workflow is essential to meet the demanding requirements of aerospace and high-performance applications.
1. Dimensional Accuracy and Tolerances: Metal AM processes build parts layer by layer, and various factors influence the final dimensions.
- Typical Tolerances: As a general guideline, for well-controlled processes like LPBF or SEBM using alloys like AlSi10Mg or A6061, achievable tolerances are often in the range of:
- $ \pm 0.1 $ to $ \pm 0.2 $ mm for smaller dimensions (e.g., up to 20-50 mm).
- $ \pm 0.1% $ to $ \pm 0.2% $ of the nominal dimension for larger features.
- These are general figures; tighter tolerances can often be achieved on specific features with process optimization or secondary machining, while very large or complex parts might exhibit slightly larger deviations.
- Factors Influencing Accuracy:
- Machine Calibration: Precision of the machine’s axes, laser/electron beam spot size, and energy delivery.
- Process Parameters: Layer thickness, scan speed, power, hatch spacing, etc.
- 素材の特性: Shrinkage during solidification and cooling, thermal expansion.
- Thermal Stresses: Residual stresses built up during printing can cause warping or distortion, especially in large or asymmetric parts. EBM/SEBM, operating at higher temperatures, generally results in lower residual stress.
- Part Geometry & Orientation: How the part is oriented on the build platform affects support needs, thermal gradients, and potential distortion.
- サポート体制: Supports influence thermal behavior and can affect accuracy, especially at contact points after removal.
- 後処理: Stress relief heat treatments can cause minor dimensional changes. Machining achieves much tighter tolerances on specific features.
- Achieving Tight Tolerances: For critical interfaces (e.g., mounting points, connector cutouts, mating surfaces), it’s common practice to design the AM part slightly oversized (“plus stock”) and then use post-process CNC machining to achieve the required tight tolerances (e.g., $ \pm 0.025 $ to $ \pm 0.05 $ mm).
2. Surface Finish (Roughness): The layer-wise nature of AM results in a characteristic surface texture. Surface roughness (typically measured as Ra – arithmetic average roughness) varies depending on the process, material, orientation, and whether the surface was supported.
- Typical Ra Values (As-Built):
- LPBF/SLM: Generally smoother, often in the range of $ 6 – 15 , \mu m $ Ra, depending on orientation (upward-facing surfaces are smoother than downward-facing or side walls).
- EBM/SEBM: Typically rougher due to larger powder particles and higher processing temperatures, often $ 20 – 40 , \mu m $ Ra or higher.
- Supported Surfaces: Surfaces where supports were attached will be significantly rougher after removal and require further finishing.
- 表面仕上げの改善: If a smoother finish is required for sealing, aesthetics, fatigue performance, or precise mating:
- Bead Blasting/Tumbling: Common methods to achieve a uniform matte finish and slightly improve Ra (e.g., down to $ 5-10 , \mu m ).∗∗∗Polishing/Lapping:∗∗Canachieveverysmooth,mirror−likefinishes( < 1 , \mu m $ Ra) but is typically localized to specific functional surfaces due to cost and effort.
- 機械加工: Provides excellent surface finish on specific features.
- Chemical Polishing/Electropolishing: Can smooth complex geometries but requires specialized handling.
3. Quality Control and Assurance: Ensuring consistent quality is paramount, especially for aerospace components. Reputable 金属3Dプリントサービスプロバイダー like Met3dp implement rigorous quality control measures throughout the workflow:
- Powder Quality Control: Incoming powder inspection (chemistry, PSD, morphology, flowability), proper storage, and handling to prevent contamination and moisture absorption. Met3dp’s in-house powder production ensures tight control over material quality from the start.
- Process Monitoring: In-situ monitoring systems (melt pool monitoring, thermal imaging) can track build consistency in real-time, potentially detecting anomalies layer by layer.
- Build Validation: Printing test coupons alongside actual parts to verify material properties (tensile strength, density) for each build.
- Post-Build Inspection:
- Dimensional Metrology: Using CMMs (Coordinate Measuring Machines), 3D scanners, or traditional gauges to verify dimensions and tolerances against the CAD model and drawing specifications.
- 非破壊検査(NDT): Techniques like X-ray computed tomography (CT scanning) can detect internal defects like porosity or lack of fusion without damaging the part. Dye penetrant or magnetic particle inspection can identify surface-breaking defects.
- 密度の測定: Using methods like the Archimedes principle to verify part density, indicating the absence of significant internal porosity.
- Documentation and Traceability: Maintaining records of powder batches, machine parameters, build logs, inspection results, and post-processing steps for full traceability, often required for aerospace (AS9100) and medical certifications.
Table: Precision & Quality Considerations for 3D Printed UAV Bays
パラメータ | Typical AM Capability (Al Alloys) | 影響要因 | Improvement Methods | Importance for UAV Bay |
---|---|---|---|---|
寛容 | $ \pm 0.1-0.2 $ mm or $ \pm 0.1-0.2 % $ | Machine, Parameters, Material, Thermal Stress, Geometry, Supports, Post-Proc. | Optimized Parameters, Stress Relief, Post-Machining | High (Fit of PCBs, connectors, mating parts) |
Surface Finish (Ra) | $ 6-15 , \mu m $ (LPBF), $ 20-40+ , \mu m $ (EBM) | Process, Orientation, Supports, Parameters | Bead Blasting, Tumbling, Polishing, Machining, Electropolishing | Moderate to High (Sealing, fatigue, aesthetics) |
Internal Defects | Can occur (Porosity, Lack of Fusion) | Parameters, Powder Quality, Gas Flow, Support Strategy | Optimized Parameters, Hot Isostatic Pressing (HIP), NDT (CT) | Very High (Structural integrity, reliability) |
品質保証 | Essential for critical parts | Supplier’s QMS, Process Control, Inspection Methods | Rigorous QMS (e.g., AS9100), In-Process Monitoring, NDT | Very High (Safety, reliability, compliance) |
Export to Sheets
Engineers designing UAV electronics bays should specify critical tolerances and surface finish requirements directly on their drawings. Procurement managers should partner with AM suppliers like Met3dp who demonstrate robust quality management systems, advanced inspection capabilities, and a commitment to delivering parts that meet stringent aerospace or industrial standards. Understanding the inherent capabilities and limitations of the AM process allows for realistic specifications and efficient integration of post-processing steps where necessary.
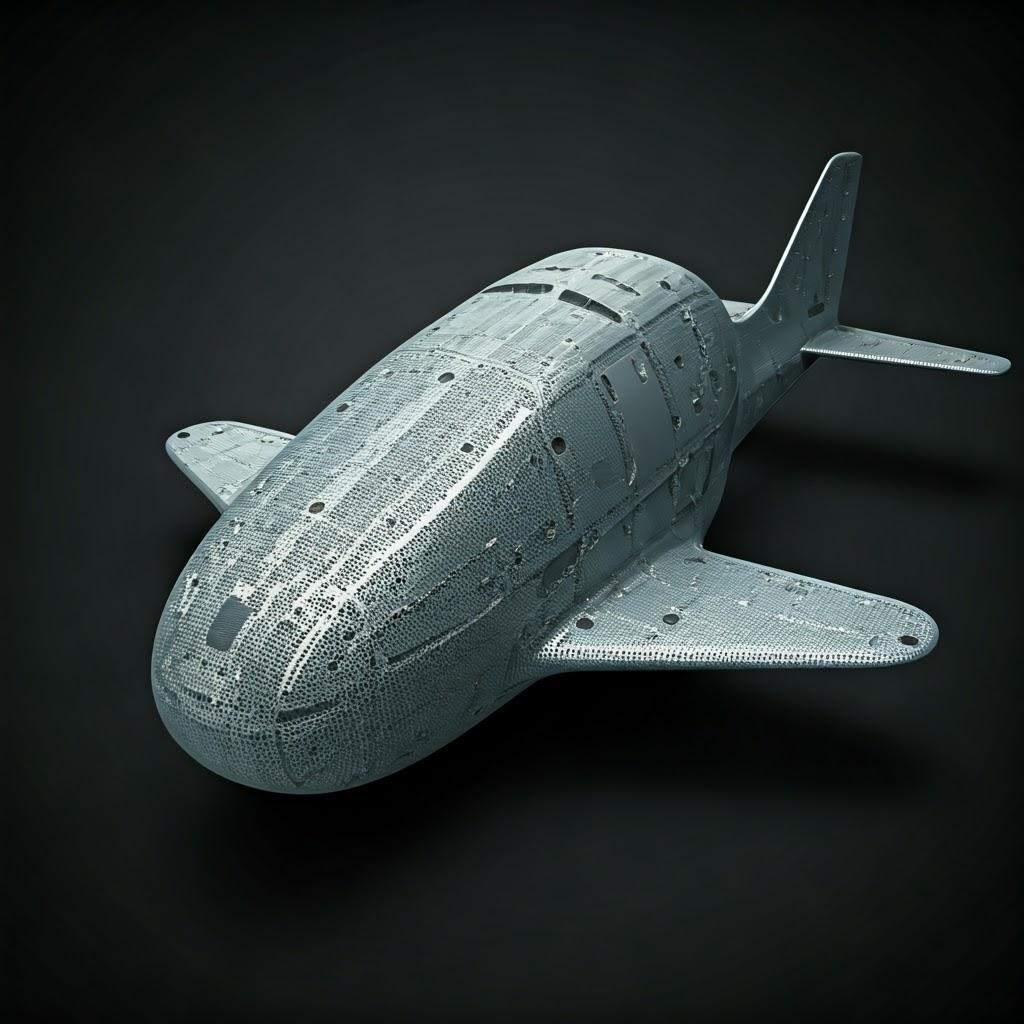
Beyond the Print: Essential Post-Processing Steps for UAV Electronics Bays
The journey of a metal 3D printed part doesn’t end when it comes out of the printer. For components like UAV electronics bays, several crucial post-processing steps are typically required to achieve the desired material properties, dimensional accuracy, surface finish, and overall functionality. These steps add time and cost to the manufacturing process, so understanding them is vital for project planning and budgeting.
1. Powder Removal:
- プロセス The first step after the build finishes and the build chamber cools is to remove the part from the build plate and carefully excavate it from the surrounding unmelted metal powder. This powder is often recycled for future builds after sieving and quality checks.
- チャレンジ: Removing powder completely, especially from complex internal channels, small cavities, or intricate lattice structures designed into the UAV bay, can be challenging.
- Techniques: Compressed air blowing, vibration, manual brushing, ultrasonic cleaning baths. Access holes might need to be designed into the part specifically for powder removal from internal cavities.
2. Support Structure Removal:
- プロセス As discussed in DfAM, overhangs and certain features require support structures during the build. These metallic supports are physically attached to the part and must be removed.
- Techniques: Supports are typically removed manually using wire EDMs, saws, grinders, or hand tools. This process requires care to avoid damaging the part itself. Where supports contact the part, small marks or witness lines will remain, requiring further finishing.
- Consideration: Designing supports for easy removal (e.g., with smaller contact points or specific break-off geometries) can significantly reduce post-processing time and effort. EBM/SEBM often requires fewer, less dense supports compared to LPBF.
3. Stress Relief / Heat Treatment:
- プロセス Due to the rapid heating and cooling cycles during powder bed fusion, significant residual stresses can build up within the printed part. These stresses can cause distortion (especially after removal from the build plate) and negatively impact mechanical properties, particularly fatigue life. A stress relief heat treatment (conducted at a specific temperature below the aging temperature) is almost always necessary for aluminum alloy parts like AlSi10Mg and A6061.
- Further Heat Treatment (e.g., T6 Temper): To achieve the full mechanical property potential (higher strength and hardness) of alloys like AlSi10Mg and A6061, a more comprehensive heat treatment cycle is required. This typically involves:
- ソリューション化: Heating the part to a high temperature to dissolve alloying elements into the aluminum matrix.
- 焼き入れ: Rapidly cooling the part (in water, air, or polymer) to trap the elements in a supersaturated solid solution.
- Aging (Precipitation Hardening): Reheating the part to a lower temperature for a specific time to allow the alloying elements to precipitate out as fine particles, strengthening the material.
- 設備 Controlled atmosphere furnaces are required to prevent oxidation during heat treatment.
- Consideration: Heat treatment can cause minor dimensional changes (warping or shrinkage), which must be accounted for, especially if tight tolerances are required. Fixturing during heat treatment may be necessary for complex geometries.
4. Machining (CNC):
- 目的 To achieve tighter tolerances, specific surface finishes, or features that are difficult to print accurately (e.g., threaded holes, perfectly flat mating surfaces, precise bearing bores).
- プロセス The 3D printed bay is mounted onto a CNC milling machine or lathe. Critical features identified on the engineering drawing are machined to their final specifications. This often involves removing a small amount of “stock” material intentionally left on during the AM process.
- Consideration: Requires careful setup and potentially custom fixturing to hold the often complex geometry of the AM part. Adds significant time and cost but is often essential for functional requirements.
5. Surface Finishing:
- 目的 To improve the as-built surface roughness for aesthetics, sealing, wear resistance, fatigue performance, or preparation for coatings.
- Common Techniques for UAV Bays:
- Bead Blasting: Provides a uniform, non-directional matte finish by propelling fine glass beads or ceramic media. Good for general cleanup and improving Ra slightly.
- Tumbling (Vibratory Finishing): Parts are placed in a tub with abrasive media and vibrated. Smooths edges and surfaces over time, suitable for batches of parts.
- Sanding/Grinding/Polishing: Manual or automated processes to achieve smoother finishes on specific areas. Polishing can achieve mirror-like finishes but is labor-intensive.
- Consideration: The chosen method depends on the required finish level, part geometry, and cost constraints.
6. Cleaning and Inspection:
- プロセス After all mechanical and thermal processing, the part must be thoroughly cleaned to remove any machining fluids, blasting media, or residues. Final inspection (dimensional check, visual inspection, NDT if required) is performed to ensure the part meets all specifications before delivery or assembly.
7. Coating or Anodizing (Optional):
- 目的 To enhance corrosion resistance, improve wear resistance, provide electrical insulation, or alter the aesthetic appearance.
- Anodizing (for Aluminum): An electrochemical process that creates a hard, durable aluminum oxide layer on the surface. Can be dyed various colors. Improves corrosion and wear resistance.
- Other Coatings: Chromate conversion coatings (for corrosion protection and paint adhesion), paints, powder coatings, or specialized functional coatings.
- Consideration: Coating processes may add thickness, which needs to be accounted for in the design tolerances.
Table: Post-Processing Steps for 3D Printed UAV Electronics Bays
Post-Processing Step | 目的 | Common Techniques | 主な検討事項 | Impact on UAV Bay |
---|---|---|---|---|
パウダー除去 | Remove unmelted powder | Compressed Air, Brushing, Vibration, Ultrasonic Clean | Access to internal channels, powder recyclability | Enables handling, prevents contamination |
サポートの取り外し | Remove temporary build supports | Manual (Wire EDM, Saw, Hand Tools) | Risk of part damage, surface marks, labor cost | Achieves final geometry |
応力緩和 | Reduce internal stresses, prevent distortion | Furnace Heat Treatment (Sub-Aging Temp) | Required for stability, minor dimensional change | Improves stability, prevents cracking |
Heat Treatment (e.g., T6) | Achieve optimal mechanical properties (Strength, Hardness) | Solutionizing, Quenching, Aging | Furnace required, potential distortion, time/cost | Enhances strength, durability |
Machining (CNC) | Achieve tight tolerances, specific features, smooth surfaces | Milling, Turning, Drilling, Tapping | Fixturing, setup time, cost, removes material | Ensures precise fit of components, mating parts |
表面仕上げ | Improve roughness, aesthetics, prepare for coating | Bead Blasting, Tumbling, Polishing, Sanding | Desired Ra, geometry limitations, cost | Improves sealing, fatigue life, appearance |
Cleaning & Inspection | Remove residues, verify specifications | Washing, Visual, Dimensional Metrology, NDT | Thoroughness, equipment needs (CMM, CT scanner) | Ensures quality, readiness for assembly |
Coating/Anodizing | Enhance corrosion/wear resistance, insulation, aesthetics | Anodizing, Conversion Coating, Painting | Added thickness, masking requirements, environmental considerations | Increases environmental resilience, durability |
Export to Sheets
Understanding this comprehensive post-processing workflow is crucial for accurately estimating lead times and costs when sourcing custom UAV electronics bays via metal AM. Engaging with a full-service provider like Met3dp, offering not just printing but also in-house post-processing capabilities (heat treatment, machining, finishing), can streamline the entire production process and ensure a high-quality final product.
Navigating Manufacturing: Common Challenges and Solutions in 3D Printing UAV Bays
While metal additive manufacturing offers tremendous advantages for producing custom UAV electronics bays, like any advanced manufacturing process, it comes with its own set of potential challenges. Awareness of these issues and proactive strategies to mitigate them are key to successful production outcomes, ensuring parts meet quality standards and performance requirements. Engineers, designers, and procurement teams should work closely with their AM service provider to navigate these potential hurdles.
1. Warping and Distortion:
- チャレンジ: The intense, localized heating and rapid cooling inherent in powder bed fusion processes create thermal gradients, leading to residual stress accumulation within the part. When the part is removed from the build plate, these stresses can relax, causing it to warp or distort, deviating from the intended geometry. This is particularly problematic for large, flat surfaces or asymmetric designs common in electronics bays.
- Solutions:
- Optimized Part Orientation: Orienting the part to minimize large flat areas parallel to the build plate and reduce thermal gradients across layers.
- Robust Support Structures: Well-designed supports anchor the part firmly to the build plate, resisting deformation during the build. EBM/SEBM’s higher build temperature inherently reduces stress compared to LPBF.
- プロセスパラメータの最適化 Fine-tuning laser/beam power, scan speed, and scan strategies (e.g., island scanning) to manage heat input and reduce stress buildup.
- Stress Relief Heat Treatment: Performing a stress relief cycle immediately after printing, often while the part is still attached to the build plate, is crucial for stabilizing the component before support removal or machining.
- Simulation: Using process simulation software to predict stress accumulation and potential distortion, allowing for design modifications or compensation strategies (e.g., pre-deforming the CAD model) before printing.
2. Support Removal Difficulties and Surface Quality Issues:
- チャレンジ: Supports are necessary but add complexity. Removing them can be labor-intensive, especially from intricate internal features or delicate structures. The surfaces where supports were attached inevitably have a rougher finish and may show witness marks that require significant finishing work. Improper removal can damage the part.
- Solutions:
- DfAM for Support Minimization: Designing self-supporting angles (>45°), using chamfers, and optimizing orientation significantly reduces the need for supports.
- Smart Support Design: Using support types (e.g., tree supports, block supports with easily breakable interfaces) designed for easier removal and minimal surface contact. Software tools can optimize support placement.
- Process Selection: EBM/SEBM generally requires fewer supports than LPBF due to the self-sintering nature of the powder cake at high temperatures.
- 後処理のテクニック: Employing appropriate tools (wire EDM for precise cuts, careful grinding/polishing) and planning for necessary surface finishing on supported areas.
3. Porosity:
- チャレンジ: Small voids or pores can form within the printed material due to trapped gas (gas porosity) or incomplete melting/fusion between layers or scan tracks (lack of fusion porosity). Porosity reduces part density, degrades mechanical properties (especially fatigue strength), and can compromise the integrity of the electronics bay.
- Solutions:
- High-Quality Powder: Using powder with low internal gas content, high sphericity, and controlled PSD, like those produced by Met3dp’s advanced atomization processes, is fundamental. Proper powder handling and storage are also critical.
- Optimized Process Parameters: Developing robust parameter sets (power, speed, hatch distance, focus) validated to achieve >99.5% density for the specific alloy and machine. Gas flow control within the build chamber is also important.
- 熱間静水圧プレス(HIP): A post-processing step where the part is subjected to high temperature and high Argon gas pressure. This can effectively close internal pores (but not surface-connected defects), significantly improving density and mechanical properties. Often used for critical aerospace or medical components.
- NDT Inspection: Using CT scanning to detect and quantify internal porosity, ensuring it remains within acceptable limits defined by the application standard.
4. Cracking:
- チャレンジ: Some aluminum alloys, particularly those with wide solidification ranges like traditional A6061 if not processed carefully, can be susceptible to solidification cracking or hot tearing during the rapid cooling phase of AM. Thermal stresses can also contribute to cracking.
- Solutions:
- Alloy Selection: Choosing alloys with good printability (like AlSi10Mg) or using specialized AM-grade alloys (like modified A6061 variants) designed to resist cracking.
- Parameter Optimization: Careful control over energy input and thermal gradients. Preheating the build plate (standard in EBM/SEBM, optional in LPBF) can help reduce thermal shock.
- Scan Strategy: Using specific scan patterns that distribute heat more evenly.
- ストレス解消: Prompt stress relief can prevent stress-induced cracking after the build.
5. Dimensional Accuracy and Repeatability:
- チャレンジ: Consistently achieving the required tolerances build after build can be challenging due to the multitude of factors influencing accuracy (machine calibration drift, minor variations in powder, slight differences in thermal history).
- Solutions:
- Robust Quality Management System (QMS): Implementing a certified QMS (like ISO 9001 or AS9100 for aerospace) ensures procedures are followed consistently.
- Regular Machine Calibration and Maintenance: Ensuring the AM system performs within specification.
- Process Monitoring and Control: Utilizing in-situ monitoring tools and statistical process control (SPC) to track build consistency.
- Standardized Procedures: Consistent powder handling, build setup, and post-processing protocols.
- Feedback Loop: Using dimensional inspection data to refine process parameters or compensation strategies over time.
Table: Common AM Challenges & Mitigation Strategies for UAV Bays
チャレンジ | Primary Cause(s) | 緩和戦略 | Key Focus Area |
---|---|---|---|
Warping/Distortion | Residual Thermal Stress | Optimized Orientation, Robust Supports, Optimized Parameters, Stress Relief HT, Simulation | Thermal Management, Design |
Support Removal/Surface | Need for Supports, Support Design | DfAM (Minimize Supports), Smart Support Design, Process Selection (EBM vs LPBF), Careful Removal, Post-Finishing | DfAM, Post-Processing |
多孔性 | Trapped Gas, Lack of Fusion | High-Quality Powder, Optimized Parameters, HIP, NDT (CT Scanning) | Material, Process Control |
クラッキング | Alloy Susceptibility, High Thermal Stress | Alloy Selection (Printable Grades), Optimized Parameters, Preheating, Scan Strategy, Stress Relief | Material, Process Control |
Accuracy/Repeatability | Process Variability, Calibration Drift | Robust QMS, Machine Calibration, Process Monitoring, Standardized Procedures, Dimensional Inspection Feedback Loop | Quality System, Process |
Export to Sheets
Successfully manufacturing high-quality, reliable 3D printed UAV electronics bays requires a deep understanding of the AM process and proactive management of these potential challenges. Partnering with an experienced metal AM manufacturing expert like Met3dp, which combines high-quality materials, advanced equipment (including SEBM printers known for reduced stress), optimized processes, and rigorous quality control, provides the best foundation for overcoming these hurdles and achieving successful production outcomes.
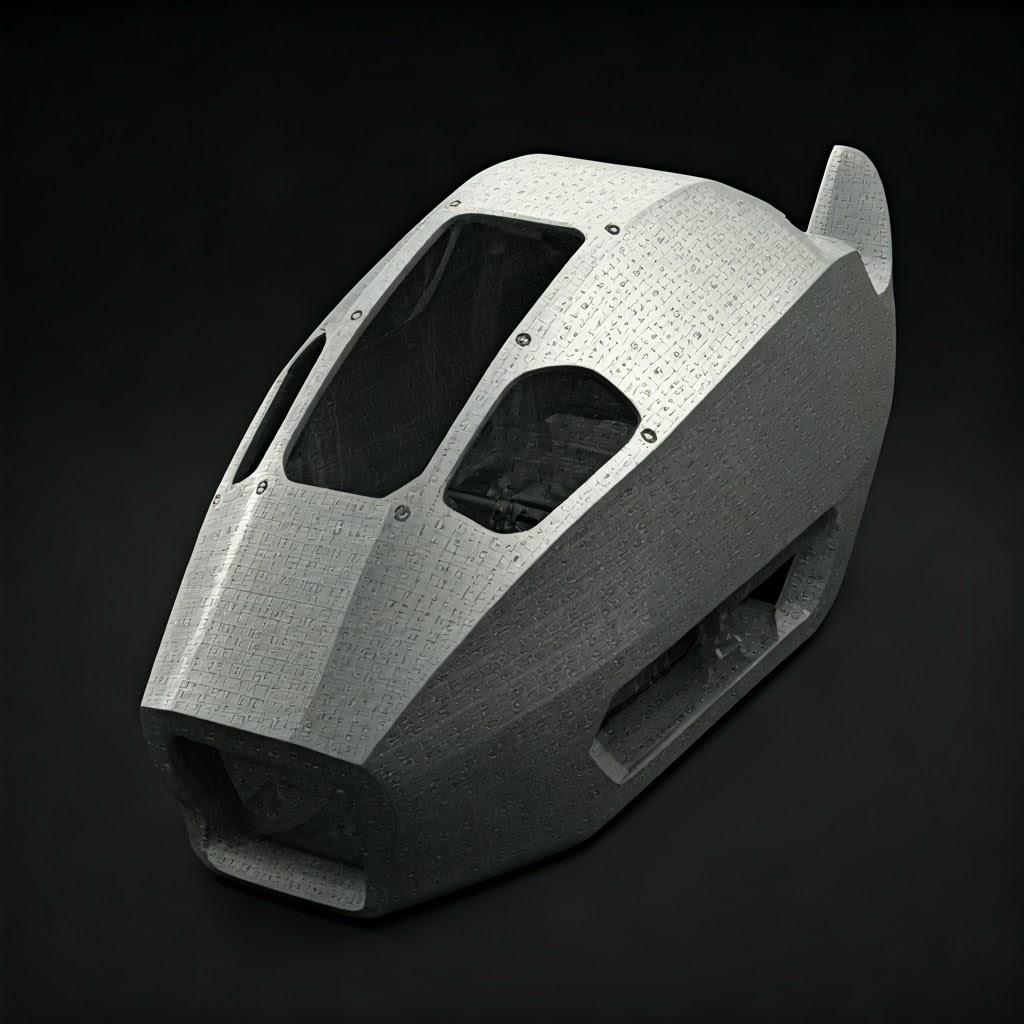
Choosing Your Partner: Selecting a High-Capability Metal 3D Printing Service Provider
Selecting the right manufacturing partner is arguably one of the most critical decisions when adopting metal additive manufacturing for components like UAV electronics bays. The quality, reliability, and performance of the final part are directly linked to the capabilities, expertise, and quality systems of your chosen supplier. For engineers and procurement managers, evaluating potential 金属3Dプリントサービスプロバイダー requires looking beyond just price and considering a range of technical and operational factors. Partnering with a high-capability supplier ensures access to the right technology, materials expertise, and quality assurance needed for demanding applications.
Here are key criteria to consider when evaluating potential partners:
1. Technological Capabilities and Equipment:
- Range of AM Processes: Does the provider offer the most suitable AM technology for your needs (e.g., LPBF/SLM for fine features, EBM/SEBM for lower stress and potentially fewer supports)? Do they have machines suited for the required part size and material (Aluminum alloys like AlSi10Mg, A6061)?
- Machine Fleet and Capacity: Do they have sufficient machine capacity to handle your prototyping and potential production volumes within acceptable lead times? Redundancy in equipment can mitigate risks associated with machine downtime.
- Up-to-Date Technology: Is their equipment modern and well-maintained? Are they investing in new technologies and process improvements? Met3dp, for instance, utilizes industry-leading SEBM printers known for reliability and accuracy in demanding applications.
2. Materials Expertise and Portfolio:
- 材料の入手可能性: Do they offer the specific alloys you require (AlSi10Mg, A6061)? Do they have experience processing these materials?
- Powder Quality Control: How do they manage and qualify their metal powders? Do they source from reputable suppliers, or better yet, produce their own high-quality powders? Companies like Met3dp, with in-house powder production using advanced Gas Atomization and PREP technologies, offer superior control over material quality, ensuring high sphericity, low porosity, and optimal PSD for consistent results.
- 素材開発: Do they have materials engineers or scientists on staff? Can they offer guidance on material selection or potentially work with custom alloys if needed?
3. Design for Additive Manufacturing (DfAM) Support:
- 専門知識: Does the provider have engineers experienced in DfAM? Can they review your designs and provide constructive feedback for optimization (lightweighting, support reduction, feature integration)?
- Collaboration: Are they willing to work collaboratively during the design phase to ensure manufacturability and leverage the full potential of AM? Early engagement can save significant time and cost later.
4. Post-Processing Capabilities:
- In-House Services: Does the provider offer a comprehensive range of in-house post-processing services, including stress relief, heat treatment (to specific tempers like T6), CNC machining, support removal, and surface finishing? A vertically integrated supplier can streamline the workflow, reduce lead times, and maintain quality control throughout the entire process.
- Managed Services: If they don’t perform all steps in-house, do they have a network of qualified and reliable partners for services like HIP, NDT, or specialized coatings? How do they manage quality across their supply chain?
5. Quality Management System (QMS) and Certifications:
- 認定: Does the provider hold relevant quality certifications? For aerospace components, AS9100 is the critical standard. ISO 9001 demonstrates a fundamental commitment to quality management. Other industry-specific certifications (e.g., medical ISO 13485) can indicate a high level of process control.
- Traceability: Can they provide full material and process traceability, documenting powder batches, machine parameters, build logs, post-processing steps, and inspection results? This is essential for critical components.
- Inspection Capabilities: What dimensional metrology (CMM, 3D scanning) and NDT (CT scanning, dye penetrant) capabilities do they possess to verify part quality against specifications?
6. Experience and Track Record:
- 業界経験: Have they successfully produced parts for similar applications, particularly in the aerospace or UAV industry? Can they provide case studies or references?
- テクニカルサポート: Do they offer responsive technical support throughout the project lifecycle?
- Reliability and Reputation: What is their reputation in the industry for quality, on-time delivery, and customer service? Checking reviews, testimonials, and industry standing can be insightful. Learning more 私たちについて can provide confidence in our established expertise and commitment.
7. Cost and Lead Time:
- Transparent Quoting: Is their quoting process clear and detailed, outlining costs for printing, materials, supports, and post-processing?
- 競争力のある価格設定: While cost is a factor, it shouldn’t be the sole driver. Ensure you are comparing quotes for equivalent levels of quality, inspection, and service. Cheapest is rarely best for critical components.
- Realistic Lead Times: Do they provide realistic lead time estimates based on current capacity and the complexity of your part? Can they accommodate expedited requests if needed?
Table: Evaluating Metal AM Service Providers for UAV Bays
Evaluation Criterion | Key Questions to Ask | Why It Matters for UAV Bays | Look For |
---|---|---|---|
テクノロジーと設備 | What AM processes? Machine models/size? Capacity? Age/Maintenance? | Suitability for Al alloys, part size, lead time reliability | Appropriate tech (LPBF/EBM), sufficient capacity, modern well-maintained machines |
材料に関する専門知識 | Offer AlSi10Mg/A6061? Powder QC process? In-house powder production? Material development support? | Ensures correct material properties, consistency, reliability; access to optimized/custom materials | Proven experience with Al alloys, strong powder QC (in-house production ideal), materials engineering support |
DfAM Support | Offer DfAM review? Experienced AM engineers? Collaborative approach? | Optimizes design for performance (weight, thermal) & manufacturability | Dedicated AM application engineers, proactive design feedback |
後処理 | In-house capabilities (Heat Treat, CNC, Finishing)? Qualified external network? | Streamlined workflow, quality control, reduced lead time | Comprehensive in-house services preferred, especially heat treatment & CNC |
Quality & Certs | QMS (ISO 9001)? AS9100 certified? Traceability procedures? Inspection capabilities (CMM, NDT)? | Ensures part reliability, safety, compliance for aerospace applications | AS9100 (if required), robust QMS, full traceability, advanced inspection equipment |
Experience & Reputation | UAV/Aerospace experience? Case studies/references? Technical support responsiveness? Industry standing? | Confidence in their ability to handle complex/critical parts, reliable partnership | Proven track record in relevant industries, positive customer feedback, responsive support |
コストとリードタイム | Transparent quoting? Competitive pricing (value vs. lowest cost)? Realistic lead times? Expediting options? | Budget adherence, project scheduling, supply chain planning | Clear quotes, fair pricing reflecting quality, reliable delivery estimates |
Export to Sheets
正しい選択 metal AM supplier is a strategic decision. Look for a partner, not just a vendor – one that acts as an extension of your engineering team, offering expertise, reliability, and a commitment to quality. Companies like Met3dp, with decades of collective expertise, comprehensive solutions spanning printers, advanced powders, and application development, position themselves as ideal partners for organizations seeking to leverage AM for demanding applications like UAV electronics bays.
Understanding Investment: Cost Factors and Lead Time for Additively Manufactured Bays
While metal additive manufacturing offers significant performance benefits for UAV electronics bays, it’s essential for engineers and procurement teams to understand the factors influencing the cost and lead time associated with this technology. Unlike traditional mass production methods, AM cost structures are different, driven primarily by material volume, machine time, and post-processing complexity rather than tooling amortization.
コスト要因:
- Material Consumption:
- Part Volume: The direct amount of metal powder melted to create the part. Larger or denser parts consume more material.
- サポート体制: Powder used to build necessary supports also adds to material cost. Efficient DfAM to minimize supports helps reduce this.
- パウダー代: The price per kilogram of the chosen metal powder (e.g., specialized AM-grade A6061 might be more expensive than standard AlSi10Mg). High-quality powders from reputable suppliers like Met3dp ensure better results but factor into the cost.
- Waste/Recycling: While powder can be recycled, there are efficiency losses and quality control costs associated with powder management.
- マシン・タイム
- ビルドタイム: The total time the AM machine is occupied printing the part(s). This is influenced by:
- Part Height: The primary driver, as printing is layer by layer. Taller parts take longer.
- Part Volume/Density: More material to melt per layer increases scan time.
- 層の厚さ: Thinner layers offer higher resolution but significantly increase build time.
- Machine Utilization: How many parts can be nested onto a single build plate? Maximizing build plate density reduces per-part machine time cost.
- Machine Hourly Rate: Varies depending on the AM technology (EBM vs. LPBF), machine model, and provider’s overheads.
- ビルドタイム: The total time the AM machine is occupied printing the part(s). This is influenced by:
- Labor and Setup:
- Build Preparation: Time taken by technicians to load powder, prepare the build file, set up the machine, and level the build plate.
- Post-Processing Labor: Significant labor costs are associated with powder removal, support removal, heat treatment setup, machining setup/operation, surface finishing, cleaning, and inspection. Complex parts requiring extensive manual finishing will incur higher labor costs.
- 後処理の要件:
- 熱処理: Costs associated with furnace time, energy consumption, and potentially protective atmospheres.
- 機械加工: CNC machine time, tooling costs, and programming/setup labor. The number and complexity of machined features directly impact cost.
- 表面仕上げ: Costs vary greatly depending on the method (e.g., simple bead blast vs. multi-stage polishing).
- Inspection: Costs for dimensional inspection (CMM time) and NDT (CT scanning time/analysis) if required.
- デザインの複雑さ:
- Intricacy: While AM handles complexity well, highly intricate designs might require more complex support strategies, longer print times (due to extensive scanning), and more challenging powder/support removal, increasing labor costs.
- Tolerance Requirements: Tighter tolerances usually necessitate post-machining, adding cost.
- 注文数量:
- Setup Cost Amortization: Fixed setup costs (build file prep, machine setup) are amortized over the number of parts in a build. Producing multiple units in a single build generally lowers the per-part cost compared to a one-off prototype.
- ボリュームディスカウント: Suppliers may offer discounts for larger batch orders or recurring production runs, reflecting efficiencies in planning and production. This is relevant for 卸売業者 or those establishing regular production.
Lead Time Factors:
Lead time is the total time from order placement to part delivery. For metal AM, it typically comprises:
- Quoting and Order Processing: Reviewing the design, generating a quote, confirming the order (can range from hours to days).
- Build File Preparation and Scheduling: Preparing the print job (orientation, supports) and scheduling it on an available machine (can range from hours to weeks depending on backlog).
- 印刷時間: The actual duration the part spends printing in the machine (can range from hours for small parts to several days or even weeks for very large/tall parts or full build plates).
- Cooling and Depowdering: Allowing the build chamber and part to cool sufficiently before careful powder removal (hours to a day).
- 後処理: This is often the most significant and variable part of the lead time:
- Stress Relief/Heat Treatment: Typically 1-3 days (including furnace cycles and cooling).
- Support Removal & Initial Finishing: Can range from hours to days depending on complexity.
- Machining: Highly variable based on complexity and shop scheduling (days to weeks).
- Surface Finishing: Variable (hours to days).
- Inspection: Variable (hours to days).
- 配送: Transit time to the customer’s location.
Typical Lead Times:
- Simple Prototypes (minimal post-processing): 5-10 business days might be achievable.
- Parts Requiring Heat Treatment & Basic Finishing: 2-4 weeks is common.
- Complex Parts with Extensive Machining & Inspection: 4-8 weeks or longer is possible.
Table: Cost & Lead Time Drivers for 3D Printed UAV Bays
ドライバー | コストへの影響 | Impact on Lead Time | Mitigation / Optimization Strategies |
---|---|---|---|
Part Size/Volume | High (Material, Machine Time) | High (Print Time) | DfAM (Topology Optimization, Lattices), Nesting multiple parts |
素材の選択 | Moderate (Powder Price) | 最小限 | Select appropriate material for requirements (e.g., AlSi10Mg often cheaper than specialized alloys) |
デザインの複雑さ | Moderate-High (Supports, Post-Proc Labor) | Moderate-High (Print Time, Post-Proc Time) | DfAM (Minimize Supports, Design for Finishing), Simplify non-critical features |
Tolerance Needs | High (If Machining Required) | High (Machining Schedule) | Specify tolerances only where needed, Leverage AM accuracy where possible |
表面仕上げ | Moderate-High (Labor, Specialized Processes) | Moderate (Finishing Time) | Specify finish only where needed, Choose cost-effective methods (e.g., bead blast vs. polish) |
熱処理 | Moderate (Furnace Time, Labor) | Moderate (Process Duration) | Often necessary for Al alloys; ensure requirement is justified by performance needs |
Inspection Needs | Moderate-High (Equipment Time, Labor, NDT) | Moderate (Inspection Time/Schedule) | Specify NDT/CMM only for critical features/parts based on risk assessment |
注文数量 | Lower Per-Part Cost for Batches | Initial lead time similar, faster subsequent runs | Order in batches where possible, establish long-term agreements for recurring needs (attractive for 卸売) |
Supplier Capacity | Minimal (Indirectly via efficiency) | High (Queue Time, Scheduling) | Choose supplier with adequate capacity, communicate timelines clearly |
Export to Sheets
Understanding these factors allows for better budgeting, project planning, and communication with your AM service provider. Getting detailed quotes early in the design process and discussing lead time expectations upfront is crucial for successful project execution.
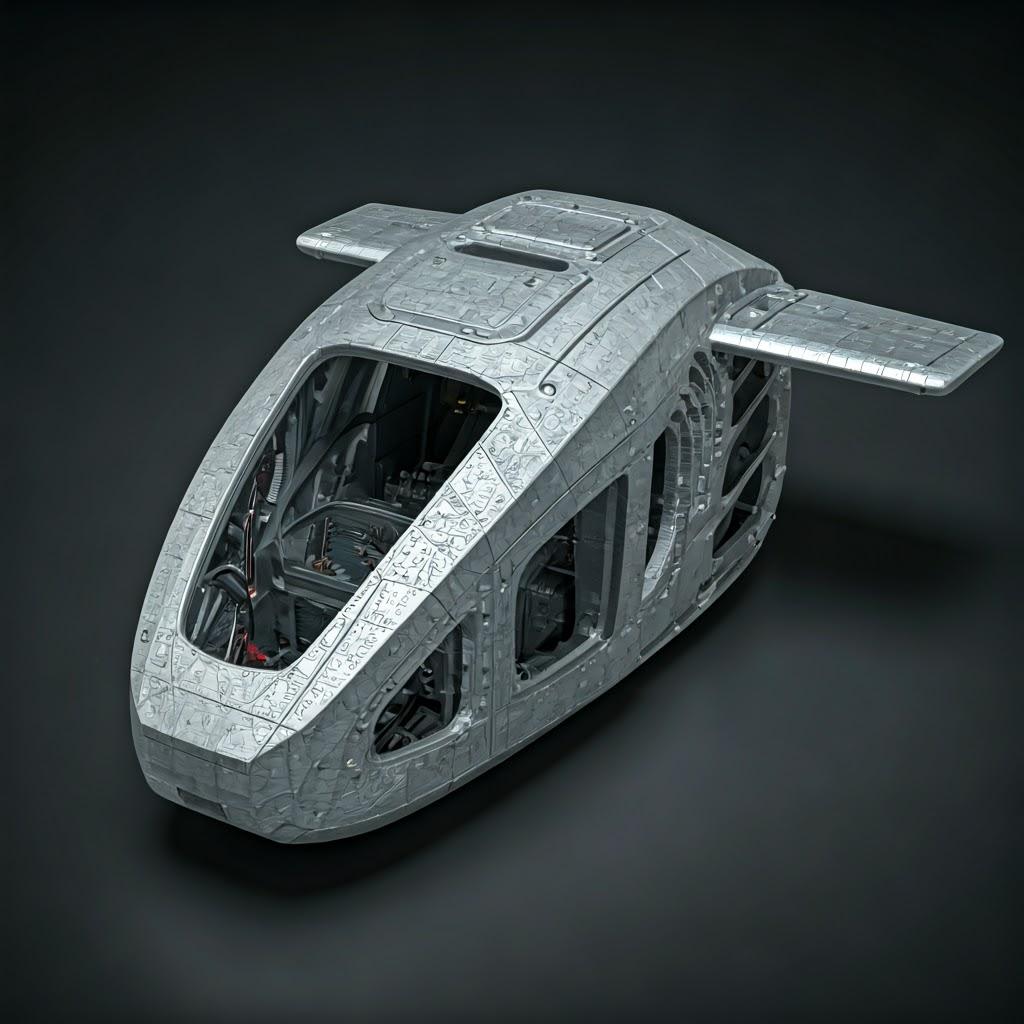
The Met3dp Advantage: Partnering for Advanced UAV Component Manufacturing
Choosing Met3dp as your additive manufacturing partner for custom UAV electronics bays offers distinct advantages rooted in our comprehensive capabilities, commitment to quality, and deep expertise in metal AM. We understand the critical nature of aerospace components and provide integrated solutions designed to meet the stringent demands of the industry.
- Integrated Solutions Provider: Met3dp isn’t just a printing service; we are a complete solutions provider. From our 業界をリードするSEBMプリンター delivering exceptional accuracy and reliability, to our advanced in-house metal powder production, we control key aspects of the value chain. This integration ensures consistency, quality, and optimized performance for your components.
- Superior Metal Powders: Our use of cutting-edge Gas Atomization and PREP technologies allows us to manufacture high-sphericity, high-purity metal powders like AlSi10Mg and A6061, specifically optimized for additive manufacturing. This translates directly to denser, stronger, and more reliable printed parts – crucial for mission-critical UAV electronics bays.
- Deep Materials and Process Expertise: With decades of collective expertise in metal additive manufacturing, our team provides invaluable support. We assist with material selection, offer DfAM guidance to optimize your designs for lightweighting and performance, and ensure the chosen manufacturing process aligns perfectly with your component requirements.
- Focus on Critical Applications: We specialize in producing parts for demanding industries like aerospace, medical, and automotive. Our processes and quality systems are geared towards meeting the high standards these sectors require, ensuring reliability and performance under challenging operating conditions.
- Comprehensive Capabilities: Beyond printing, we offer essential post-processing services, including heat treatment and potentially coordinating machining and finishing, providing a streamlined path from design to finished component.
- Partnership Approach: We believe in collaborating closely with our clients. We work to understand your specific challenges and goals, acting as an extension of your team to accelerate innovation and achieve optimal manufacturing outcomes.
By partnering with Met3dp, you gain access to cutting-edge technology, superior materials, and extensive expertise, ensuring your custom UAV electronics bays are manufactured to the highest standards of quality and performance.
Frequently Asked Questions (FAQ) about 3D Printed UAV Electronics Bays
Here are answers to some common questions engineers and procurement managers have about using metal 3D printing for UAV electronics bays:
1. How does the strength of 3D printed AlSi10Mg or A6061 compare to traditionally manufactured aluminum?
- When printed using optimized parameters and subjected to appropriate post-process heat treatments (like T6), the mechanical properties (yield strength, ultimate tensile strength) of AM AlSi10Mg and specialized AM A6061 can meet or even exceed those of their cast or wrought counterparts. For instance, heat-treated AM AlSi10Mg properties are often comparable to A356-T6 castings, while optimized AM A6061 can approach wrought 6061-T6 properties. However, properties like elongation (ductility) and fatigue strength can differ and are highly dependent on print quality (density, defects) and post-processing (HIP can improve fatigue). It’s crucial to work with a supplier like Met3dp who can provide material data sheets based on their specific process and ensure proper heat treatment protocols are followed.
2. Is metal 3D printing cost-effective for producing UAV electronics bays, especially compared to CNC machining?
- Cost-effectiveness depends heavily on part complexity, quantity, and design optimization.
- For highly complex geometries, topology-optimized designs, parts with internal channels, or consolidated assemblies, AM is often more cost-effective than machining the same design (which might be impossible or require extensive multi-axis setups and high material waste).
- For low-to-medium volume production (prototypes to hundreds of units), AM avoids high tooling costs associated with casting, making it very competitive.
- For very simple, block-like geometries produced in high volumes, traditional CNC machining might remain cheaper on a per-part basis.
- The true value often lies in the performance benefits (lightweighting, improved thermal management) enabled by AM, which can reduce overall system operating costs or increase mission capability, justifying a potentially higher component price.
3. What kind of environmental protection do 3D printed aluminum bays offer, and can they be further enhanced?
- Aluminum alloys like AlSi10Mg and A6061 naturally form a passive oxide layer that provides good corrosion resistance in typical atmospheric conditions. This is often sufficient for many UAV applications.
- However, for operation in harsh environments (e.g., marine/coastal areas with salt spray, highly corrosive industrial atmospheres), additional protection is recommended.
- Anodizing is a common and effective treatment for 3D printed aluminum. It creates a much thicker, harder, and more durable oxide layer, significantly enhancing corrosion and wear resistance. It can also provide electrical insulation and be dyed various colors.
- Other options include chromate conversion coatings (excellent corrosion resistance and paint adhesion) or specialized paints/powder coatings. These treatments ensure the longevity and reliability of the electronics bay even in challenging operational settings.
シェアする
MET3DP Technology Co., LTDは、中国青島に本社を置く積層造形ソリューションのリーディングプロバイダーです。弊社は3Dプリンティング装置と工業用途の高性能金属粉末を専門としています。
関連記事
Met3DPについて
最新情報
製品
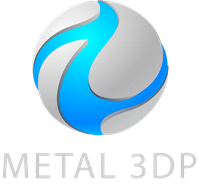
3Dプリンティングと積層造形用金属粉末