Electric Motor Jackets via Metal 3D Printing for Thermal Efficiency
目次
The relentless pursuit of higher performance, longer range, and faster charging in the electric vehicle (EV) market places immense pressure on component design, particularly thermal management systems. The electric motor, the heart of the EV powertrain, generates significant heat during operation. Efficiently dissipating this heat is paramount not only for performance and reliability but also for the longevity of the motor and associated components. Traditional cooling solutions often face limitations in complexity, weight, and thermal efficiency. This is where metal additive manufacturing (AM), or 3Dプリンティング, emerges as a game-changing technology, enabling the production of highly optimized EV motor cooling jackets with unprecedented design freedom and thermal performance. Companies specializing in advanced metal powders and 金属3Dプリンティング solutions, like Met3dp, are at the forefront of this revolution, empowering automotive engineers and procurement managers to rethink thermal management design.
Introduction: Revolutionizing EV Thermal Management with 3D Printed Motor Cooling Jackets
An Electric Vehicle (EV) motor cooling jacket, also known as a motor housing or stator housing with integrated cooling channels, is a critical component responsible for regulating the operating temperature of the electric motor. As electrical energy is converted into mechanical motion, resistive losses in the windings and core generate substantial heat. If not managed effectively, this heat can lead to:
- Reduced Motor Efficiency: Higher temperatures increase electrical resistance, leading to greater energy loss.
- Component Degradation: Prolonged exposure to excessive heat can degrade insulation materials, bearings, and magnets, significantly shortening motor lifespan.
- Performance Throttling: To prevent overheating, the vehicle’s control system may limit motor power output, negatively impacting driving performance, especially during demanding conditions like high-speed driving or towing.
- 安全性への懸念: In extreme cases, overheating can pose safety risks.
The fundamental purpose of the cooling jacket is to provide pathways for a coolant (typically a water-glycol mixture) to circulate around the heat-generating parts of the motor, primarily the stator, absorbing heat and transferring it away to a radiator. The effectiveness of this heat transfer is directly linked to the design of the cooling channels within the jacket – their path, shape, surface area, and proximity to heat sources.
Why Thermal Management Matters More Than Ever in EVs:
The demands on EV thermal management systems are intensifying due to several industry trends:
- Increased Power Density: Motors are becoming smaller and more powerful to meet performance expectations and packaging constraints, concentrating heat generation in a smaller volume.
- Faster Charging: High-speed charging generates significant heat not only in the battery but also influences the thermal load on the entire powertrain system during subsequent operation.
- Extended Range Goals: Optimizing every aspect of vehicle efficiency, including minimizing energy losses due to heat, is crucial for maximizing driving range.
- Performance Demands: Consumers expect EVs to offer acceleration and sustained power output comparable or superior to internal combustion engine vehicles, requiring robust thermal management.
Traditional Manufacturing Limitations:
Conventional manufacturing methods for motor cooling jackets, such as casting (sand casting, die casting) and machining from billet, face inherent limitations:
- Geometric Constraints: Casting processes struggle to create highly complex internal channel geometries with thin walls or intricate pathways needed for optimal coolant flow and heat exchange. Draft angles, core placement limitations, and minimum wall thicknesses restrict design freedom.
- 体重だ: Cast components often require thicker walls than structurally necessary simply due to manufacturing process constraints, adding unnecessary weight – a critical penalty in EVs where range is paramount.
- Tooling Costs & Lead Times: Creating molds and dies for casting is expensive and time-consuming, making it less suitable for low-to-medium volume production runs or rapid prototyping iterations.
- Assembly Complexity: Sometimes, complex cooling circuits require multiple cast or machined parts to be assembled and sealed, introducing potential leak paths and additional manufacturing steps.
The Additive Manufacturing Transformation:
Metal 3D printing fundamentally overcomes these limitations. By building the cooling jacket layer by layer directly from metal powder (such as specialized alloys like CuCrZr or AlSi10Mg), AM enables:
- 圧倒的な設計自由度: Engineers can design highly complex, topology-optimized internal cooling channels that precisely follow the contours of heat sources, maximizing surface area and turbulent flow for superior heat transfer. Features like thin walls, intricate lattice structures, and conformal channels, impossible or prohibitively expensive with traditional methods, become feasible.
- パーツの統合: Multiple components of a traditional cooling assembly can potentially be integrated into a single 3D printed part, reducing assembly time, weight, and potential points of failure.
- 軽量化: Material can be placed precisely where needed for structural integrity and thermal function, allowing for significant weight reduction compared to cast counterparts.
- ラピッドプロトタイピングと反復: Designs can be modified and reprinted quickly without the need for expensive tooling changes, accelerating development cycles and enabling performance optimization.
- 素材のカスタマイズ: AM allows for the use of advanced metal alloys specifically chosen for their thermal conductivity, strength-to-weight ratio, and corrosion resistance properties, tailored to the demanding EV environment.
Leading providers like Met3dp, leveraging advanced powder manufacturing techniques like gas atomization and Plasma Rotating Electrode Process (PREP) alongside state-of-the-art Selective Electron Beam Melting (SEBM) and Laser Powder Bed Fusion (L-PBF) printers, offer the high-quality materials and manufacturing precision required for these critical components. Their expertise spans the entire process chain, from powder production to finished part, ensuring reliability and performance for demanding automotive applications. As the EV industry continues its rapid expansion, metal AM is poised to become an indispensable tool for designing and manufacturing the next generation of high-performance motor cooling jackets.
Core Applications: Where are 3D Printed EV Motor Cooling Jackets Making an Impact?
While the potential for 3D printed cooling jackets spans various electric motor applications, their adoption is currently most prominent and impactful in sectors where performance, weight, and design optimization are critical differentiators. Automotive Original Equipment Manufacturers (OEMs) and their Tier 1 suppliers are primary explorers and adopters, driven by the unique demands of the EV market. Procurement managers and engineering teams within these organizations are increasingly evaluating metal AM providers for both prototyping and series production solutions.
Key Application Areas:
- High-Performance Electric Vehicles (Hypercars & Sports EVs):
- チャレンジ: These vehicles push the boundaries of power density and sustained performance. Motors operate under extreme loads, generating immense heat that conventional cooling systems struggle to manage effectively within tight packaging constraints. Weight reduction is also paramount for handling and acceleration.
- AM Solution: Metal 3D printing allows for topology-optimized cooling jackets with highly intricate internal channels designed using computational fluid dynamics (CFD) simulations. These jackets maximize heat extraction from critical areas like stator windings and end turns, enabling higher continuous power output without overheating. Materials like Copper alloys (e.g., CuCrZr), offering superior thermal conductivity, are often favored, despite manufacturing challenges, which AM helps overcome. Lightweighting achieved through optimized design further enhances vehicle dynamics. Specialist manufacturers and performance divisions are key wholesale buyers in this niche.
- Premium & Mainstream Electric Vehicles:
- チャレンジ: While perhaps less extreme than hypercars, mainstream EVs still require efficient thermal management for range, reliability, and fast charging capability. OEMs seek cost-effective solutions that offer improvements over traditional casting, especially as motor power densities increase across segments. Reducing NVH (Noise, Vibration, Harshness) through optimized housing design is also a factor.
- AM Solution: Additive manufacturing, particularly using cost-effective and well-understood Aluminum alloys like AlSi10Mg, provides a pathway to improved thermal performance compared to basic cast designs. AM enables conformal cooling channels that hug the stator more closely, reducing thermal resistance. Part consolidation can simplify assembly lines. While cost-competitiveness with high-volume die casting remains a consideration, AM offers significant value in the development phase for rapid iteration and performance validation. As AM technology matures and costs decrease, its adoption in series production for premium segments is growing, with distributors playing a role in managing the supply chain for these components.
- Electric Motorsport (Formula E, Electric GT, etc.):
- チャレンジ: Motorsport represents the pinnacle of performance optimization under strict regulations. Teams require maximum power output, minimal weight, and extreme reliability under race conditions. Development cycles are short, demanding rapid prototyping and manufacturing of bespoke components.
- AM Solution: Metal 3D printing is extensively used in motorsport for its ability to deliver highly customized, lightweight components with optimized performance characteristics quickly. Cooling jackets are prime candidates, allowing teams to tailor thermal management precisely to their unique motor designs and race strategies. The ability to iterate designs between races based on performance data is invaluable. Material choice (often high-strength Aluminum or specialized alloys) and intricate internal geometries are key benefits leveraged by race teams, who often partner directly with AM service providers.
- Commercial Electric Vehicles (Buses, Trucks):
- チャレンジ: Heavy-duty electric vehicles involve large, powerful motors operating under constant load cycles. Reliability, durability, and efficiency are critical for minimizing operating costs. Thermal management must be robust to handle sustained high torque demands and varying environmental conditions.
- AM Solution: While cost sensitivity is high, the potential for improved efficiency and reliability through optimized cooling can offer long-term value. AM can be used to create cooling jackets with enhanced coolant flow distribution, preventing hot spots and extending motor life. For specialized commercial vehicles or during the development of new powertrain platforms, AM provides a flexible manufacturing solution. Procurement departments in commercial vehicle manufacturing look for reliable industrial metal printing suppliers capable of meeting durability standards.
- Aerospace Electric Propulsion (Urban Air Mobility, Drones):
- チャレンジ: Although nascent, electric propulsion in aerospace demands extreme lightweighting and exceptionally high reliability. Thermal management is critical due to air density changes and the severe consequences of component failure.
- AM Solution: Metal 3D printing is already a staple in aerospace for its ability to produce lightweight, complex parts. For electric motor cooling in drones or future UAM vehicles, AM allows for highly integrated and optimized thermal management systems, often combining structural elements with cooling channels in a single component using materials like high-strength Aluminum or Titanium alloys. Rigorous quality control and certification, offered by experienced providers like Met3dp, are essential.
Functions Enhanced by 3D Printing:
Across these applications, metal 3D printing specifically enhances the 機能 of the cooling jacket:
- Enhanced Heat Transfer: Optimized channel geometry (complex paths, turbulators, increased surface area) improves the heat transfer coefficient between the motor components and the coolant.
- Targeted Cooling: Coolant flow can be directed precisely to identified hotspots within the motor.
- Reduced Thermal Gradients: More uniform cooling minimizes temperature variations across the motor, reducing stress and improving longevity.
- Improved Coolant Flow: Optimized channel design minimizes pressure drop, potentially allowing for smaller, more efficient coolant pumps.
- Integration Potential: Cooling channels can be integrated directly into motor structural components, reducing part count and assembly complexity.
The ability to leverage these functional improvements makes 3D printed cooling jackets a compelling proposition for engineers seeking performance gains and procurement managers looking for innovative solutions from advanced manufacturing suppliers.
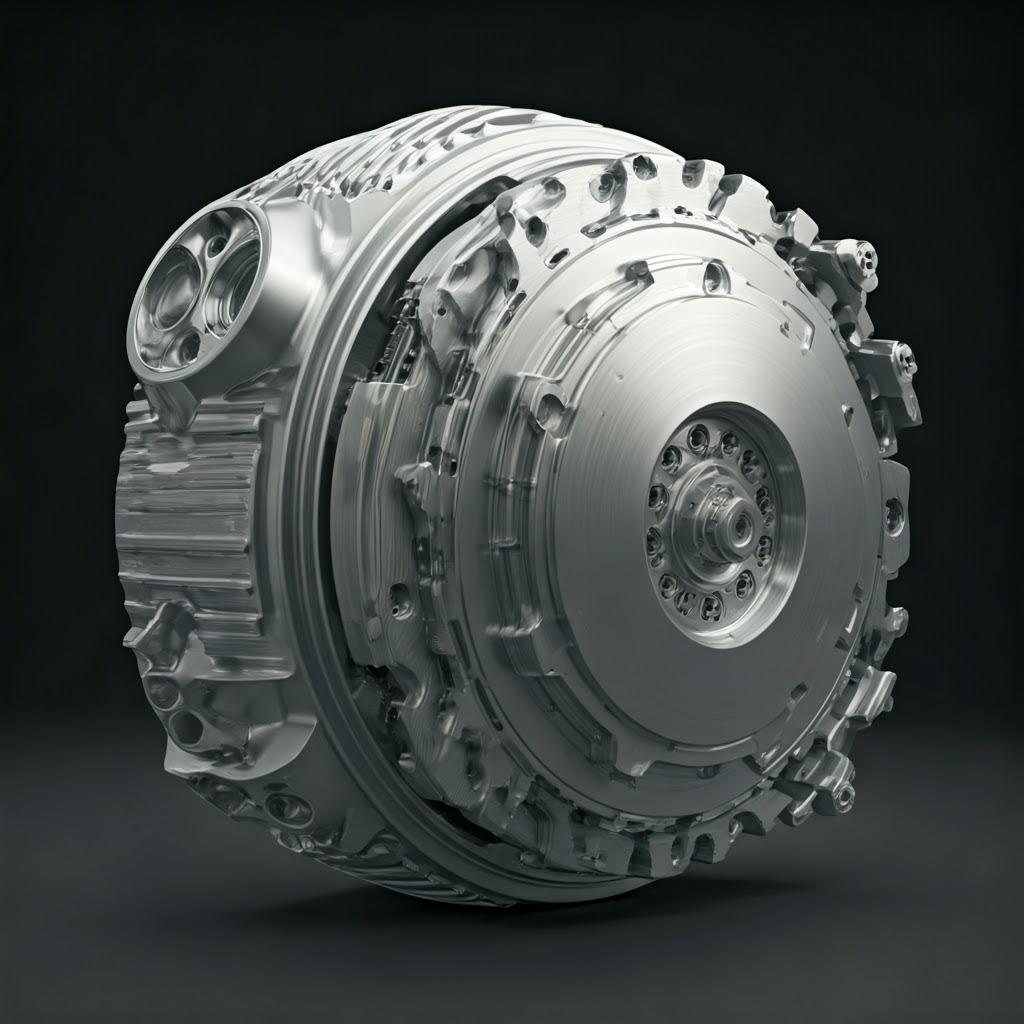
The Additive Advantage: Why Choose Metal 3D Printing for EV Cooling Jackets Over Traditional Methods?
The decision for automotive OEMs, Tier 1 suppliers, and performance vehicle manufacturers to adopt metal additive manufacturing for EV motor cooling jackets stems from a compelling set of advantages that directly address the shortcomings of conventional methods like casting and machining. While traditional processes remain suitable for certain applications, metal AM offers transformative potential, particularly when pushing the boundaries of performance, efficiency, and design integration. Evaluating these benefits is crucial for engineering leads and procurement specialists sourcing advanced automotive components.
1. Unmatched Geometric Complexity & Design Freedom:
- Traditional Limitation: Casting processes are constrained by the need for molds and cores. Designing intricate internal passages with undercuts, sharp turns, or variable cross-sections is difficult, costly, or impossible. Draft angles are required, and minimum wall thicknesses often exceed structural necessities. Machining internal channels into a solid block is also highly restrictive.
- AM Advantage: Layer-by-layer construction removes most geometric constraints. Metal AM enables:
- Topology Optimized Channels: Algorithms determine the most efficient load paths and material distribution. For cooling jackets, this translates to channels that precisely follow heat sources, maximizing contact area and minimizing material usage and weight.
- Conformal Cooling: Channels can conform precisely to the shape of the stator or rotor, maintaining a consistent, minimal distance for highly efficient heat transfer, unlike the often-compromised paths in cast designs.
- Internal Lattice Structures: Lightweight, intricate lattice structures can be incorporated within channel walls or the jacket body to enhance structural rigidity while minimizing mass, or even within the channels themselves to promote turbulent flow and increase heat transfer surface area.
- Thin, Uniform Walls: Walls can be designed to be much thinner (down to sub-millimeter levels, process permitting) and more uniform than possible with casting, reducing weight and thermal resistance.
- Integrated Features: Functional features like mounting points, sensor housings, or fluid connectors can be seamlessly integrated into the single printed part.
2. Superior Thermal Performance:
- Traditional Limitation: The geometric restrictions of casting often lead to suboptimal coolant flow paths, potential dead zones where coolant stagnates, and larger distances between the coolant and the heat source, resulting in higher thermal resistance and less efficient heat dissipation.
- AM Advantage: The design freedom enabled by AM directly translates to superior thermal performance:
- Maximized Surface Area: Complex internal geometries, including fins or lattice structures within channels, dramatically increase the surface area available for heat exchange.
- Optimized Flow Paths: CFD simulations can be used to design channels that ensure uniform coolant velocity, minimize pressure drop, and induce turbulence where needed to maximize the heat transfer coefficient.
- Reduced Thermal Bottlenecks: Conformal channels minimize the distance heat must travel from the source (stator windings) to the coolant, significantly reducing thermal resistance.
- Targeted Cooling: Coolant can be preferentially directed to known hotspots within the motor design.
3. Significant Lightweighting Potential:
- Traditional Limitation: Casting often necessitates thicker sections for mold filling and structural integrity assumptions, leading to heavier components. Machining from billet starts with excess material.
- AM Advantage: Material is added only where needed. Topology optimization and lattice structures allow for drastic reductions in material usage while maintaining or even increasing structural performance and stiffness-to-weight ratio. Weight reduction is critical in EVs for improving range, handling, and overall efficiency. Even a few kilograms saved contribute meaningfully.
4. Part Consolidation:
- Traditional Limitation: Complex cooling systems might require multiple cast or machined components (e.g., separate jacket halves, manifolds, connectors) that need to be assembled, bolted, welded, or brazed, introducing potential leak points, assembly labor, and tolerance stack-up issues.
- AM Advantage: Metal AM allows for the consolidation of multiple functional elements into a single, monolithic printed part. This simplifies the supply chain, reduces assembly time and cost, improves reliability by eliminating joints and seals, and often contributes to further weight reduction. This is a significant benefit for wholesale buyers and procurement teams managing complex assemblies.
5. Accelerated Development & Prototyping:
- Traditional Limitation: Creating tooling (molds, dies) for casting is a major investment in time (weeks or months) and cost. Design iterations require expensive tooling modifications or complete remakes. Machining prototypes can be faster but may not replicate the final cast part’s properties or geometry accurately.
- AM Advantage: AM is a tool-less process. Designs can be sent directly from CAD to the printer. Prototypes can be produced in days, allowing engineers to rapidly test and iterate designs based on thermal and structural simulations or physical testing. This drastically shortens the development cycle, reduces risk, and allows for more optimized final designs before committing to mass production. Companies like Met3dp, offering both advanced printers and materials, can facilitate this rapid iteration process.
6. Material Flexibility & Advanced Alloys:
- Traditional Limitation: Casting is often limited to specific, well-established alloys (primarily Aluminum alloys for cooling jackets). Introducing new or difficult-to-cast alloys can be challenging.
- AM Advantage: Metal AM processes like L-PBF and SEBM are compatible with a wider range of advanced metal powders, including:
- High Thermal Conductivity Copper Alloys (e.g., CuCrZr): Offer significantly better heat transfer than Aluminum but are notoriously difficult to cast complex shapes without defects. AM makes intricate copper alloy jackets feasible.
- High-Strength Aluminum Alloys: Specific Al alloys optimized for AM offer excellent strength-to-weight ratios.
- チタン合金: For applications demanding extreme lightweighting and corrosion resistance (though less common for primary cooling jackets due to lower thermal conductivity and higher cost).
- カスタム合金: AM providers like Met3dp, with in-house powder production using techniques like gas atomization, can even support the development and use of custom alloys tailored to specific thermal and mechanical requirements.
B2B Supply Chain & Manufacturing Advantages:
- Reduced Tooling Investment: Eliminates high upfront costs associated with casting molds.
- オンデマンド制作: Enables manufacturing closer to the point of need, potentially simplifying logistics.
- Flexible Batch Sizes: Economically viable for low-to-medium volume production runs, ideal for niche vehicles, motorsport, or initial production ramps before high-volume tooling is justified.
- Digital Inventory: Designs exist as digital files, allowing parts to be printed as needed, reducing physical inventory requirements.
Comparison Table: AM vs. Traditional Methods for EV Cooling Jackets
特徴 | 金属積層造形(AM) | 伝統的な鋳造 | 伝統的な機械加工 |
---|---|---|---|
幾何学的複雑性 | Very High (Internal channels, lattices, conformal) | Moderate to Low (Draft angles, core limits) | Low (Limited internal features) |
熱性能 | Potentially Very High (Optimized flow, max SA) | Moderate (Compromised flow paths) | Moderate to High (If design allows) |
軽量化 | Excellent (Topology optimization, lattices) | Fair (Minimum wall thickness limits) | Fair (Material removal limits) |
部品の統合 | High Potential | Low Potential | Very Low Potential |
Prototyping Speed | Very Fast (Days) | Slow (Weeks/Months for tooling) | Moderate (Days/Weeks) |
金型費用 | None / Very Low | 高い | Low (Fixturing) |
素材オプション | Wide (Al, Cu, Ti, Steel, custom alloys) | Limited (Mainly Al, some Fe alloys) | Wide (Depends on billet availability) |
Ideal Volume | Low to Medium, Prototyping | 高い | Low, Prototyping |
Cost per Part (Low Vol) | 中~高 | Very High (Due to tooling amortization) | 高い |
Cost per Part (High Vol) | High (Process time) | 低い | 中~高 |
サプライチェーン | Potentially Simpler (On-demand, digital) | Complex (Tooling suppliers, foundries) | Simpler (Material suppliers, machine shops) |
Export to Sheets
While cost per part in very high volumes can still favor traditional casting, the compelling technical advantages, particularly in performance, weight, and development speed, make metal 3D printing an increasingly attractive and strategically important manufacturing method for EV motor cooling jackets, especially for performance-driven applications and companies seeking a competitive edge. Choosing an experienced additive manufacturing partner is key to realizing these benefits.
Material Matters: Selecting High-Performance Powders like CuCrZr and AlSi10Mg
The choice of material is fundamental to the performance and reliability of any engineered component, and 3D printed EV motor cooling jackets are no exception. The metal powder selected dictates the jacket’s thermal conductivity, mechanical strength, weight, corrosion resistance, and ultimately, its ability to meet the demanding requirements of electric vehicle powertrains. Additive manufacturing opens the door to using materials that might be difficult or impossible to shape using traditional methods, offering engineers greater flexibility but also requiring careful consideration. For EV cooling jackets, two material families stand out: Aluminum alloys and Copper alloys.
Why Material Selection is Critical:
- 熱伝導率: This is arguably the most crucial property. Higher thermal conductivity allows heat to transfer more readily from the motor’s heat sources (stator) through the jacket material to the coolant, minimizing thermal resistance and keeping the motor cooler.
- Mechanical Strength & Durability: The cooling jacket is often a structural part of the motor assembly. It must withstand vibrations, mechanical loads, and internal coolant pressure throughout the vehicle’s lifetime. Temperature variations also induce thermal stresses.
- 体重だ: Minimizing component weight is critical for maximizing EV range and performance. Lighter materials contribute directly to this goal.
- 耐食性: The material must be compatible with standard automotive coolants (e.g., water-glycol mixtures) and resist corrosion over many years of service and exposure to varying environmental conditions.
- Manufacturability (Printability): Not all alloys are equally easy to process using metal AM technologies like L-PBF or SEBM. Factors like laser/electron beam absorption, flowability of the powder, weldability, and susceptibility to cracking or residual stress during printing must be considered.
- コストだ: Material cost is a significant factor in the overall component price, especially for higher-volume production. Procurement teams must balance performance requirements with budget constraints.
Recommended Powders for EV Cooling Jackets:
1. Aluminum Alloys (Specifically AlSi10Mg):
- 概要 AlSi10Mg is one of the most common and well-characterized aluminum alloys used in metal additive manufacturing. It’s essentially an aluminum-silicon-magnesium casting alloy adapted into powder form.
- キー・プロパティ
- Good Thermal Conductivity: While not as high as copper, AlSi10Mg offers good thermal conductivity (around 150-180 W/m·K after heat treatment), significantly better than steels or titanium alloys.
- 優れた強度対重量比: Aluminum alloys are inherently lightweight (density ~2.68 g/cm³). AlSi10Mg offers good mechanical strength and stiffness, especially after appropriate heat treatment (T6), making it suitable for structural components.
- 良好な印刷性: It generally processes well with L-PBF systems, exhibiting good weldability and relatively lower residual stress compared to some other alloys. This makes it a reliable choice for complex geometries.
- 耐食性: Exhibits good resistance to corrosion, suitable for typical automotive coolant environments.
- 費用対効果: Aluminum powders are generally more affordable than copper or titanium alloys, making AlSi10Mg a strong candidate for cost-sensitive applications and scaling towards series production.
- Why it Matters for Cooling Jackets: AlSi10Mg provides a well-balanced combination of thermal performance, low weight, adequate strength, good manufacturability, and reasonable cost. It’s often the default starting point for many automotive AM applications, including thermal management components. Its widespread use means processing parameters are well-understood by experienced AM service providers.
2. Copper Alloys (Specifically CuCrZr – Copper Chromium Zirconium):
- 概要 Copper alloys are highly attractive for thermal management due to their exceptional thermal conductivity. CuCrZr is a precipitation-strengthened copper alloy designed to offer a good balance between conductivity and mechanical strength at elevated temperatures.
- キー・プロパティ
- 優れた熱伝導性: This is the primary advantage. CuCrZr boasts very high thermal conductivity (typically >300 W/m·K), roughly double that of AlSi10Mg. This allows for significantly more efficient heat extraction from the motor.
- Good Mechanical Strength (at temperature): While pure copper is soft, the Chromium and Zirconium additions allow for age hardening, significantly increasing its strength and allowing it to retain good mechanical properties even at the elevated operating temperatures seen in electric motors.
- 良好な耐食性: Generally compatible with automotive coolants.
- Higher Density: Copper alloys are significantly denser (~8.9 g/cm³) than aluminum alloys, meaning a copper jacket will be heavier than an aluminum one of identical geometry. However, the improved thermal performance might allow for smaller or thinner designs, potentially offsetting some of the weight penalty.
- 課題だ:
- 印刷可能: Copper alloys are notoriously challenging to print using L-PBF, primarily due to copper’s high reflectivity and thermal conductivity. It reflects much of the laser energy (requiring higher power lasers, often green lasers) and rapidly dissipates heat, making it difficult to create a stable melt pool. This can lead to defects like porosity or lack of fusion if not managed carefully. Processing requires specialized equipment and finely tuned parameters. SEBM can be advantageous due to better energy absorption.
- コストだ: Copper alloy powders are significantly more expensive than aluminum powders.
- Why it Matters for Cooling Jackets: For applications demanding the absolute highest level of thermal performance (e.g., high-performance racing motors, extremely power-dense applications), the superior thermal conductivity of CuCrZr can be enabling. It allows engineers to push thermal limits further than possible with aluminum, potentially leading to higher continuous power output or more compact motor designs. The manufacturing challenges mean partnering with a highly experienced AM provider with proven copper printing capabilities is essential. Wholesale buyers in performance markets specifically seek suppliers capable of handling these advanced materials.
Met3dp’s Role in Material Excellence:
Choosing the right powder is only part of the equation; the 品質 of that powder is equally critical for achieving reliable, high-performance parts. This is where a vertically integrated partner like Met3dp provides significant value:
- 高度なパウダー製造: Met3dp utilizes industry-leading powder manufacturing technologies:
- Gas Atomization (GA): This process uses high-pressure inert gas jets to break up a stream of molten metal into fine droplets, which solidify into spherical powder particles. Met3dp’s equipment employs unique nozzle and gas flow designs to achieve high sphericity and good flowability – crucial for consistent powder bed layering in AM machines.
- プラズマ回転電極プロセス(PREP): In PREP, a rapidly rotating electrode made of the target metal is melted by a plasma torch. Centrifugal force flings off molten droplets, which solidify in an inert atmosphere into highly spherical powders with very few satellites (smaller attached particles) and low internal porosity. This often results in superior powder quality, ideal for demanding applications.
- 品質管理: Rigorous control over particle size distribution (PSD), morphology (sphericity), flowability, chemical composition, and purity is essential. Consistent powder quality ensures predictable printing behavior and final part properties.
- Wide Material Portfolio: While AlSi10Mg and CuCrZr are key for cooling jackets, Met3dp manufactures a broad range of high-quality metal powders, including various Titanium alloys (TiNi, TiTa, TiAl, TiNbZr), Cobalt-Chrome (CoCrMo), Stainless Steels, and Superalloys. This breadth of expertise ensures a deep understanding of metal powder characteristics and processing. You can explore their offerings further on their 製品ページ.
- Material & Process Expertise: Met3dp combines its powder expertise with deep knowledge of AM printing processes (including SEBM and L-PBF), ensuring that the chosen powder is optimally processed to achieve the desired material properties in the final cooling jacket.
Comparison Table: Key Material Properties
プロパティ | AlSi10Mg (Typical, Heat Treated) | CuCrZr (Typical, Heat Treated) | 単位 | Importance for Cooling Jacket |
---|---|---|---|---|
熱伝導率 | ~150 – 180 | >300 | W/m·K | 非常に高い |
密度 | ~2.68 | ~8.9 | g/cm³ | High (Lower is better) |
降伏強度 | ~250 – 300 | ~400 – 500 | MPa | 高い |
極限引張強さ | ~400 – 450 | ~500 – 600 | MPa | 高い |
Printability (L-PBF) | グッド | チャレンジング | – | 高い |
相対コスト | より低い | より高い | – | 高い |
耐食性 | グッド | グッド | – | 高い |
Export to Sheets
Conclusion on Materials:
The selection between AlSi10Mg and CuCrZr (or other potential alloys) depends heavily on the specific application’s performance requirements versus cost and weight constraints. AlSi10Mg offers a robust, cost-effective solution with good all-around properties suitable for many EV applications. CuCrZr provides superior thermal performance for the most demanding scenarios, albeit with higher costs and manufacturing complexity. Partnering with a knowledgeable material supplier and AM service provider like Met3dp, who controls powder quality from atomization to final print, ensures access to high-quality materials and the expertise needed to leverage them effectively for optimal EV motor cooling jacket performance.
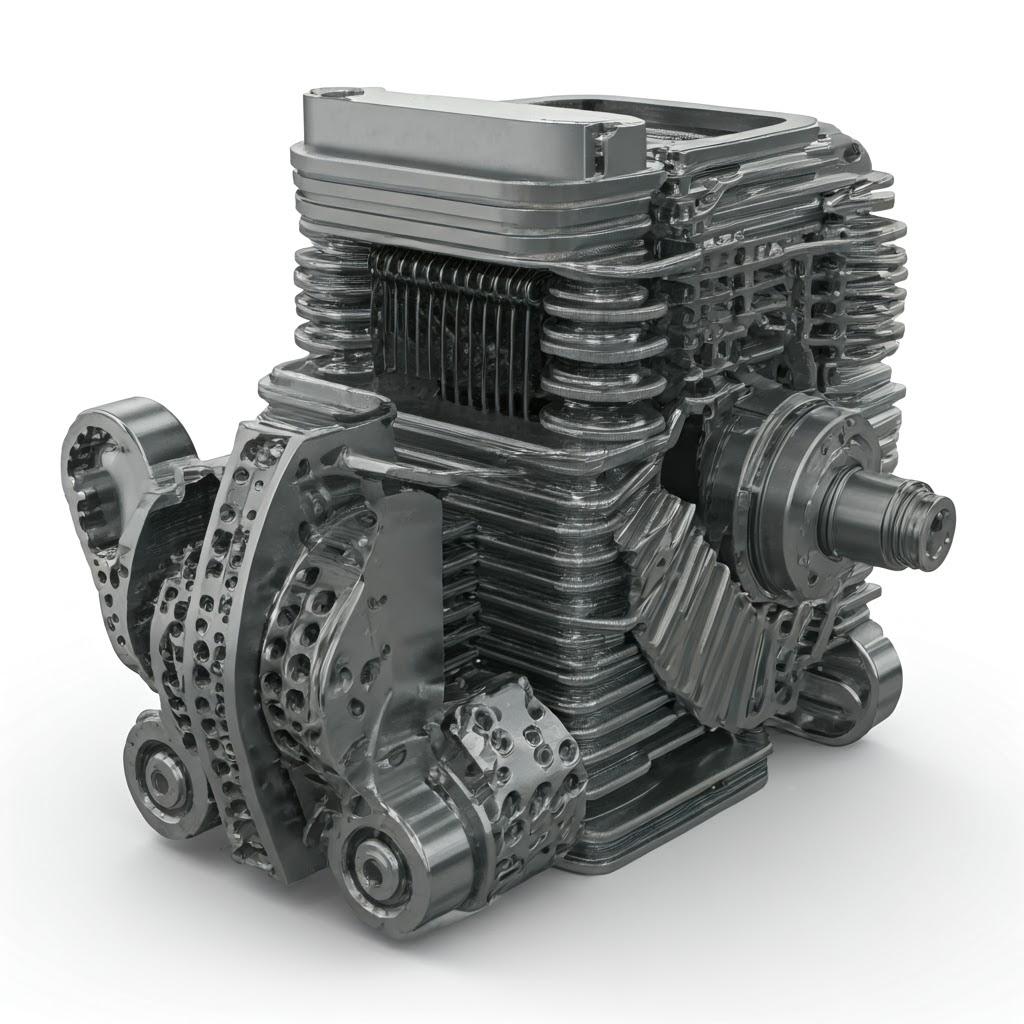
Design for Additive Manufacturing (DfAM): Optimizing Cooling Jacket Geometry for Peak Performance
Simply replicating a design intended for casting or machining using metal additive manufacturing rarely unlocks the technology’s full potential. To truly leverage the advantages of 3D printing for EV motor cooling jackets – enhanced thermal performance, reduced weight, and part consolidation – engineers must embrace Design for Additive Manufacturing (DfAM). DfAM is not just a set of rules but a mindset shift, encouraging designers to think in terms of layers, optimize for the specific AM process being used (like Laser Powder Bed Fusion – L-PBF or Selective Electron Beam Melting – SEBM), and exploit the geometric freedom offered. For procurement managers engaging with AM suppliers, understanding DfAM principles helps in evaluating the feasibility and optimization level of proposed designs.
Core DfAM Principles for EV Cooling Jackets:
- Embrace Complexity for Function:
- Challenge Conventional Thinking: Forget the limitations of draft angles, core pulls, and line-of-sight machining access. AM thrives on complexity if it serves a purpose.
- Optimize Internal Channels: This is where AM shines for cooling jackets. Instead of simple round or rectangular channels, design:
- Conformal Channels: Paths that precisely follow the contours of the stator or other heat sources, maintaining a minimal, consistent distance for optimal heat transfer.
- Variable Cross-Sections: Channels that narrow or widen to control coolant velocity, promote turbulence in specific areas, or accommodate packaging constraints.
- Complex Paths: Split, merge, and route channels in intricate ways to ensure coolant reaches all critical areas and hotspots identified through thermal simulation (CFD).
- Internal Features: Incorporate turbulators (fins, dimples, gyroid structures) directly into channel walls to trip the boundary layer, enhance turbulent flow, and significantly increase the heat transfer coefficient without substantial pressure drop penalties if designed correctly.
- Integrate Functionality: Combine mounting bosses, sensor ports, fluid inlets/outlets, and even structural elements directly into the single printed jacket, eliminating assembly steps and potential leak points.
- Topology Optimization and Lightweighting:
- Let Software Guide: Utilize topology optimization software early in the design process. Define load cases (mechanical, thermal), keep-out zones, and performance targets (e.g., maximize stiffness, minimize mass, optimize thermal flux). The software will generate organic, often non-intuitive shapes that efficiently distribute material only where needed.
- 格子構造: Incorporate internal lattice structures (e.g., honeycomb, gyroid, stochastic foam) within the jacket’s solid walls. These can significantly reduce weight while maintaining high stiffness and strength. Different lattice types offer varying properties (isotropic vs. anisotropic) suitable for different load conditions. Ensure the chosen lattice unit cell size is printable with the selected AM process and resolution.
- Thin, Ribbed Walls: Replace thick, solid sections with thinner walls reinforced by optimized rib patterns, achieving similar structural performance with less material and weight.
- Minimize and Optimize Support Structures:
- Self-Supporting Angles: Design features with overhang angles greater than the critical self-supporting angle for the chosen material and process (typically around 45° for L-PBF, potentially higher for SEBM). This minimizes the need for sacrificial support structures.
- Internal Channel Design: Design internal horizontal or low-angle channels with non-circular cross-sections (e.g., teardrop, diamond) that are inherently self-supporting, reducing or eliminating the need for internal supports that are difficult or impossible to remove. Avoid long, flat internal ceilings.
- Accessible Supports: Where supports are unavoidable (e.g., at inlets/outlets, complex external features), design them for easy removal during post-processing without damaging the functional surfaces. Consider break-away points or structures that allow tool access. Powder-based supports (common in SEBM) are easier to remove than melt-pool supports (L-PBF) but may affect surface finish.
- Support Strategy Matters: Discuss support strategy early with your chosen AM service provider, like Met3dp. Their experience with specific machines and materials can guide design choices to minimize support requirements and associated costs/risks.
- Consider Wall Thickness and Feature Resolution:
- Minimum Wall Thickness: Understand the minimum printable wall thickness for the process and material (often 0.3-0.5 mm for L-PBF, slightly thicker for SEBM). Design walls thick enough for structural and thermal requirements but avoid unnecessary bulk. Very thin walls can be prone to warping or damage.
- Feature Resolution: Small features, sharp corners, and intricate details have limits based on beam spot size, powder particle size, and layer thickness. Ensure critical features like sealing surfaces or small channel details are within the achievable resolution. Avoid knife edges; use small radii or chamfers.
- Plan for Post-Processing:
- Machining Allowances: Identify critical interfaces, sealing surfaces, or features requiring tight tolerances that will need CNC machining after printing. Add sufficient sacrificial stock material (e.g., 0.5-2 mm) in these areas during the design phase.
- Powder Removal: Design internal channels with sufficient diameter and smooth transitions to facilitate the removal of unfused powder after the build. Incorporate access ports if necessary for complex internal networks, which can be plugged or welded shut later. Trapped powder is a significant quality risk.
- Heat Treatment Considerations: Understand how heat treatment (required for optimal properties in alloys like AlSi10Mg and CuCrZr) might cause minor distortion. Design features robustly or plan for final machining after heat treatment.
- Leverage Simulation (CFD & FEA):
- Iterative Design Loop: DfAM is most effective when tightly integrated with simulation. Use Computational Fluid Dynamics (CFD) to model coolant flow and heat transfer within the proposed channel designs. Use Finite Element Analysis (FEA) to assess structural integrity under mechanical and thermal loads.
- Validate Optimization: Use simulation results to refine channel paths, optimize wall thicknesses, validate topology optimization results, and predict potential problem areas (e.g., hotspots, high stress concentrations) before committing to a print. This iterative loop of design-simulate-refine is key to maximizing performance.
DfAM Guidelines Summary Table:
DfAM Principle | Key Considerations for EV Cooling Jackets | ベネフィット |
---|---|---|
Embrace Complexity | Conformal channels, variable cross-sections, internal turbulators, integration | Superior thermal performance, reduced thermal resistance, part count reduction |
Topology Optimization | Apply early, define loads/constraints, utilize software effectively | Maximum lightweighting, optimal material usage, high stiffness-to-weight |
格子構造 | Incorporate internally for weight/stiffness, check printability | Significant weight reduction, tailored mechanical properties |
Support Minimization | Design self-supporting angles (>45°), optimize internal channel shapes | Reduced post-processing time/cost, lower risk of surface damage |
Accessible Supports | Plan for removal access, consider break-away points | Easier and cleaner support removal, preserved functional surfaces |
壁厚 | Adhere to min/max limits, use thin walls + ribs | Reduced weight, faster print times, material savings |
フィーチャー・レゾリューション | Respect process limits for small features, holes, sharp edges | Ensures manufacturability, prevents feature failure or inaccuracy |
Plan for Post-Processing | Add machining stock, design for powder removal, consider heat treat effects | Achieves final tolerances, ensures cleanliness, prevents distortion issues |
Leverage Simulation | Use CFD for thermal/flow, FEA for structural, iterate design | Performance prediction & optimization, reduced physical prototypes |
Export to Sheets
By adopting these DfAM principles, engineering teams can move beyond simply using 3D printing as a replacement manufacturing method and start truly harnessing its power to create next-generation EV motor cooling jackets that significantly outperform their traditional counterparts. Collaboration with experienced AM providers, who understand the nuances of different 印刷方法 and materials, is crucial for successful DfAM implementation.
Precision Unleashed: Achieving Tight Tolerances and Superior Surface Finish in 3D Printed Cooling Jackets
While metal additive manufacturing excels at creating complex geometries, a common question from engineers and procurement managers, especially those accustomed to precision machining, revolves around the achievable dimensional accuracy, tolerances, and surface finish of 3D printed parts. For functional components like EV motor cooling jackets, these aspects are critical for proper assembly, sealing, fluid dynamics, and overall performance. Understanding the capabilities and limitations of metal AM in this regard is essential for setting realistic expectations and planning necessary post-processing steps.
Understanding Tolerances in Metal AM:
- General Tolerances: As a starting point, metal AM processes like L-PBF and SEBM can typically achieve general dimensional tolerances comparable to investment casting. A common standard referenced is ISO 2768, with parts often falling into the medium (m) or coarse (c) tolerance classes as-built.
- ISO 2768-m (Medium): Often achievable for many features directly off the printer. For example, for a feature size of 100 mm, the tolerance might be ±0.3 mm.
- ISO 2768-c (Coarse): A safer assumption for less critical dimensions or more complex geometries. For 100 mm, this might be ±0.5 mm.
- Tighter Tolerances: Achieving tolerances tighter than ISO 2768-m usually requires post-machining of specific features. Tolerances typical of CNC machining (e.g., ±0.05 mm or better) are not generally achievable directly from the AM process across the entire part.
- Factors Influencing Tolerance:
- Machine Calibration & Quality: High-end industrial printers, like those utilized by Met3dp, with precise motion control, beam calibration, and thermal management systems, inherently produce more accurate parts. Regular maintenance and calibration are crucial.
- 素材の特性: Different metal powders exhibit varying shrinkage rates, thermal expansion coefficients, and stress behaviors during printing, impacting final dimensions. Experienced providers develop specific parameter sets to compensate for material behavior.
- Part Geometry & Size: Large, complex parts or those with significant variations in cross-section are more prone to thermal distortion and deviation from the intended geometry. Internal stresses built up during the layer-by-layer process can cause warping.
- Build Orientation & Supports: How a part is oriented on the build platform affects dimensional accuracy due to factors like layer stepping on curved surfaces and the influence of support structures. Supports can slightly mar surfaces upon removal and locally affect geometry.
- 熱管理: The heating and cooling cycles during the build process significantly impact residual stress and potential distortion. Processes like SEBM, which operate at elevated build chamber temperatures, often result in lower residual stress compared to L-PBF, potentially improving dimensional stability for certain geometries and materials.
- 後処理: Stress relief heat treatments can cause minor dimensional changes. Support removal can affect local accuracy. Machining is used to achieve the final, precise tolerances on critical features.
Surface Finish (Roughness):
- As-Built Surface Roughness (Ra): The surface finish of as-built metal AM parts is inherently rougher than machined surfaces. It’s influenced by powder particle size, layer thickness, beam parameters, and surface orientation.
- Typical Ra Values (L-PBF): Often range from 6 µm to 20 µm (micrometers) Ra, depending on the factors above. Upward-facing surfaces tend to be smoother than downward-facing surfaces (which require support) or vertical walls (which show layer lines).
- Typical Ra Values (SEBM): Generally rougher than L-PBF due to larger powder particles and partial sintering, often in the 20 µm to 35 µm Ra range or higher.
- Impact of Surface Finish:
- Sealing: As-built surfaces are usually too rough for effective O-ring or gasket sealing. These surfaces typically require machining or polishing.
- Fluid Dynamics: Rough internal channel surfaces can increase pressure drop and potentially alter heat transfer characteristics compared to smooth channels. While sometimes beneficial for inducing turbulence, excessive roughness is usually undesirable.
- Fatigue Life: Surface roughness can act as initiation points for fatigue cracks, although for cooling jackets, this is often less critical than for highly stressed structural components.
- 表面仕上げの改善: Various post-processing techniques can significantly improve surface finish:
- CNC Machining: Provides the smoothest, most precise finish but is typically limited to accessible surfaces.
- Abrasive Flow Machining (AFM): Flows abrasive media through internal channels to smooth them.
- Electrochemical Polishing: Removes material electrochemically for a bright, smooth finish.
- Mass Finishing (Tumbling, Vibratory Finishing): Uses media to smooth external surfaces.
- Micro-machining / Polishing: Manual or automated polishing for specific areas.
Met3dp’s Commitment to Precision:
Achieving consistent tolerances and desired surface finishes requires not just advanced equipment but deep process understanding. Met3dp emphasizes:
- Industry-Leading Equipment: Utilizing printers known for their accuracy and reliability is the foundation.
- Optimized Parameters: Extensive experience in developing and refining build parameters for specific alloys like AlSi10Mg and CuCrZr to minimize deviations and achieve consistent results.
- 厳格な品質管理: Implementing metrology checks (e.g., CMM scanning, 3D scanning) during and after production to verify dimensional accuracy against specifications.
- Integrated Post-Processing: Offering or managing necessary post-processing steps, including precision machining and surface finishing, to meet final drawing requirements.
Tolerance & Surface Finish Expectations Summary:
パラメータ | As-Built (Typical Range) | Achievable with Post-Processing | Importance for Cooling Jacket |
---|---|---|---|
General Tolerance | ISO 2768-m / -c (±0.3 to ±0.5mm @100mm) | Machining Tolerances (±0.05mm+) | Moderate (Overall fit), High (Interfaces) |
表面粗さ(Ra) | 6-35 µm (L-PBF/SEBM) | <1 µm possible (Machined/Polished) | High (Sealing surfaces), Moderate (Internal channels) |
再現性 | Good (with process control) | Excellent (Machining) | High (For series production) |
Export to Sheets
Conclusion on Precision:
While metal AM parts do not emerge from the printer with the mirror finish and micron-level accuracy of CNC machining across all surfaces, they offer remarkable complexity combined with respectable as-built precision. For EV cooling jackets, critical interfaces requiring tight tolerances or smooth sealing surfaces will typically necessitate post-machining. However, the bulk of the complex geometry, including internal channels, can often be used with its as-built tolerances and finish, or with specialized internal finishing processes if required. Setting clear specifications on drawings, understanding the process capabilities, and working with a capable AM partner like Met3dp are key to successfully leveraging metal 3D printing for precision-sensitive applications.
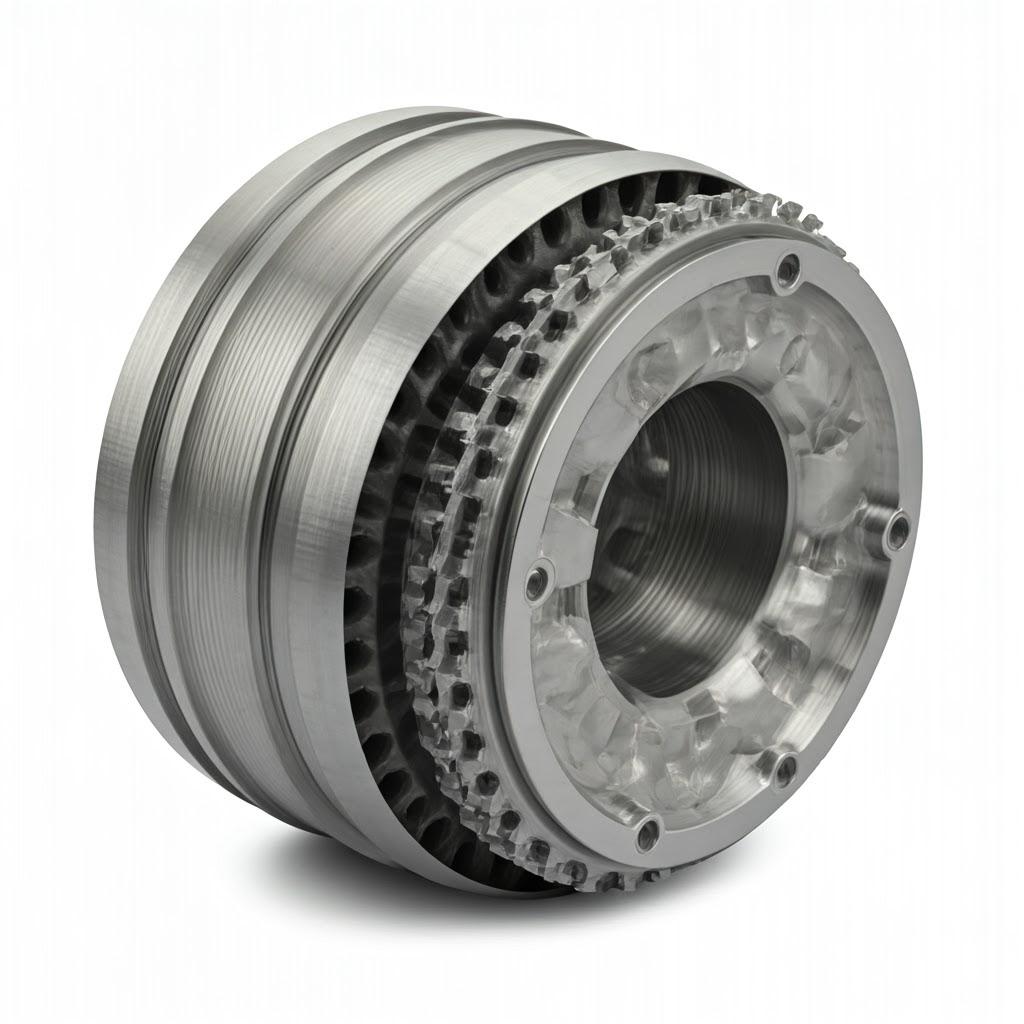
Beyond the Build: Essential Post-Processing Steps for Functional EV Cooling Jackets
The journey of a metal 3D printed component doesn’t end when the printer stops. For an EV motor cooling jacket to transition from a raw printed part to a functional, reliable component ready for vehicle integration, it must undergo a series of crucial post-processing steps. These steps are not optional extras; they are integral to achieving the required mechanical properties, dimensional accuracy, surface characteristics, and overall quality demanded by the automotive industry. Understanding this workflow is vital for engineers designing the parts and for procurement teams selecting an AM supplier, as integrated post-processing capabilities significantly impact lead time, cost, and final part quality.
Common Post-Processing Workflow for AM Cooling Jackets:
- De-powdering / Cleaning:
- 目的 To remove all residual, unfused metal powder trapped within the component, especially from intricate internal cooling channels.
- 方法: Typically involves manual brushing, compressed air blow-off, bead blasting, or specialized powder handling stations, sometimes combined with vibration. For complex internal networks, specialized flushing or flow-through systems might be necessary. Careful design (DfAM) incorporating access ports and avoiding powder traps is crucial here.
- Importance: Trapped powder can impede coolant flow, detach later causing system contamination, add weight, and interfere with subsequent steps like heat treatment or welding. Thorough cleaning is paramount.
- ストレス解消:
- 目的 The rapid heating and cooling cycles inherent in L-PBF and, to a lesser extent, SEBM, create significant internal stresses within the printed part. Stress relief is a heat treatment performed before removing the part from the build plate (or immediately after) to reduce these internal stresses.
- Method: Heating the entire build plate with the parts attached in an inert atmosphere furnace to a specific temperature (below the aging or solutionizing temperature), holding it, and then slowly cooling. Temperatures and times are material-specific (e.g., ~300-350°C for AlSi10Mg).
- Importance: Reduces the risk of distortion or cracking when the part is cut from the build plate and during subsequent machining or thermal cycles in operation.
- Part Removal from Build Plate:
- 目的 To separate the printed cooling jacket(s) from the metal build plate they were fused to during the printing process.
- 方法: Typically done using wire Electrical Discharge Machining (EDM) or a bandsaw. Wire EDM generally provides a cleaner cut with less mechanical stress but is slower.
- Importance: Needs to be done carefully to avoid damaging the part.
- 支持構造の撤去:
- 目的 To remove the sacrificial support structures generated during the print to anchor overhangs and complex features.
- 方法: Can involve manual breaking and grinding (for accessible supports), CNC machining, or EDM. Support removal from internal channels is particularly challenging and highlights the importance of DfAM to minimize internal supports or design them for removal (e.g., using chemical etching for some materials/support types, though less common for Al/Cu).
- Importance: Supports are non-functional and add weight. Their removal can leave witness marks or slightly rougher surfaces (“scars”) that may require further finishing depending on the location. Incomplete removal is unacceptable.
- Heat Treatment (Solutionizing, Aging, Annealing):
- 目的 To achieve the desired final mechanical properties (strength, hardness, ductility) and ensure microstructural stability. Most AM metals require heat treatment to optimize performance, as the as-built microstructure is often non-equilibrium and anisotropic.
- AlSi10Mg: Typically undergoes a T6 temper (solution heat treatment followed by artificial aging) to significantly increase strength and hardness.
- CuCrZr: Requires solution treatment followed by aging to achieve precipitation hardening, boosting strength while retaining good conductivity.
- Method: Controlled heating and cooling cycles in calibrated furnaces, often under vacuum or inert atmosphere to prevent oxidation. Specific temperature profiles and durations are critical and alloy-dependent.
- Importance: Essential for meeting the mechanical performance requirements specified in the design. Affects final dimensions slightly, so it’s often done before final machining.
- 目的 To achieve the desired final mechanical properties (strength, hardness, ductility) and ensure microstructural stability. Most AM metals require heat treatment to optimize performance, as the as-built microstructure is often non-equilibrium and anisotropic.
- CNC Machining:
- 目的 To achieve tight tolerances, specific surface finishes, and precise geometric features on critical interfaces that cannot be achieved directly by the AM process.
- Common Areas: Sealing surfaces (O-ring grooves, flat gasket faces), mounting holes/bores, connector interfaces, any surface requiring high perpendicularity, flatness, or parallelism.
- Method: Using standard CNC milling machines, lathes, or grinders. Requires careful fixture design to hold the complex AM part securely without distortion. Requires the DfAM step of adding machining stock.
- Importance: Guarantees correct assembly, sealing integrity, and interfacing with mating components in the motor assembly.
- 表面仕上げ:
- 目的 To improve surface smoothness (reduce Ra), enhance appearance, or prepare surfaces for coating.
- Methods (as needed):
- External Surfaces: Bead blasting (for a uniform matte finish), tumbling/vibratory finishing (for general smoothing/deburring), manual or robotic polishing (for specific smooth areas).
- Internal Channels: Abrasive Flow Machining (AFM), chemical polishing/etching (material dependent), or potentially left as-built if CFD analysis shows the roughness is acceptable or beneficial.
- Importance: Critical for sealing surfaces, can improve fluid dynamics in channels, and affects aesthetic appearance.
- Cleaning and Inspection:
- 目的 Final cleaning to remove any machining fluids, debris, or contaminants. Comprehensive inspection to verify conformance to all specifications.
- 方法: Aqueous or solvent cleaning, ultrasonic cleaning. Inspection includes:
- Dimensional: Coordinate Measuring Machine (CMM), 3D scanning.
- Integrity: Leak testing (pressure decay or immersion testing) is essential for a cooling jacket to ensure no porosity or cracks allow coolant leakage. Non-Destructive Testing (NDT) like X-ray or CT scanning might be used to detect internal defects or verify powder removal in highly critical applications.
- 素材: Hardness testing, potentially microstructural analysis on witness coupons.
- Visual: Thorough visual inspection for surface defects.
- Importance: Final quality gate ensures the part is fit for purpose and meets all drawing requirements before shipment to the customer or assembly line.
The Importance of Integrated Services:
Managing this multi-step post-processing chain can be complex. Partnering with an AM service provider like Met3dp, which offers or manages these processes in an integrated workflow, provides several advantages for procurement teams and engineers:
- Streamlined Logistics: Single point of contact reduces complexity.
- プロセス制御: Ensures consistency and quality control across all stages.
- Optimized Workflow: Reduces overall lead time compared to shipping parts between multiple specialist vendors.
- Accountability: Clear responsibility for the final part quality.
Post-Processing Summary Table:
ステップ | 目的 | 一般的な方法 | 主な検討事項 |
---|---|---|---|
De-powdering | Remove residual powder | Brushing, Air Jet, Blasting, Flushing | Internal channels, powder traps, completeness |
応力緩和 | Reduce internal stress before part removal | Furnace heat treatment (on build plate) | Prevents warping/cracking, material-specific cycle |
Part Removal | Separate part from build plate | Wire EDM, Bandsaw | Avoid part damage, cut quality |
サポートの取り外し | Remove sacrificial supports | Manual breaking, Machining, Grinding, EDM | Accessibility (internal), surface marks, completeness |
熱処理 | Achieve final mechanical properties (strength, hardness) | Furnace cycles (Solutionizing, Aging), Vacuum/Inert Gas | Material-specific (T6 for Al, Aging for CuCrZr), affects dimensions |
CNC加工 | Achieve tight tolerances & fine finish on critical features | Milling, Turning, Grinding | Machining stock (DfAM), fixture design, tolerances |
表面仕上げ | Improve Ra, aesthetics, prepare for coating | Blasting, Polishing, AFM (internal), Tumbling | Sealing surfaces, internal channels, specific needs |
Cleaning & Inspection | Final cleanliness, verify conformance to specifications | Cleaning methods, CMM, 3D Scan, Leak Test, NDT, Visual | LEAK TESTING IS CRITICAL, dimensional checks |
Export to Sheets
Successfully navigating the post-processing maze is critical for producing high-quality, functional EV motor cooling jackets via metal AM. It requires careful planning during the design phase and close collaboration with an experienced manufacturing partner who understands the intricacies of each step.
Navigating Challenges: Common Pitfalls in 3D Printing Cooling Jackets and Mitigation Strategies
While metal additive manufacturing offers significant advantages for producing complex components like EV motor cooling jackets, the technology is not without its challenges. Understanding potential pitfalls and how experienced manufacturers mitigate them is crucial for engineers designing these parts and for procurement managers selecting reliable suppliers. Proactively addressing these challenges ensures higher quality, better consistency, and reduced risk in adopting AM for critical automotive applications.
Common Challenges & Mitigation Strategies:
- Residual Stress, Warping, and Distortion:
- チャレンジ: The rapid, localized heating and cooling inherent in layer-by-layer fusion processes (especially L-PBF) generate significant thermal gradients, leading to internal stresses. These stresses can cause parts to warp during the build, distort when removed from the build plate, or even crack. Large, flat sections or asymmetric designs are particularly susceptible.
- Mitigation Strategies:
- Optimized Build Orientation: Orienting the part to minimize large flat surfaces parallel to the build plate and reduce thermal gradients across layers.
- Thermal Engineering: Using optimized scan strategies (e.g., island scanning, chessboard patterns) to distribute heat more evenly and reduce localized stress peaks.
- Appropriate Support Structures: Well-designed supports anchor the part securely to the build plate, resisting warping forces during the build.
- Process Selection: SEBM, with its high-temperature build environment, generally results in lower residual stress compared to L-PBF, making it potentially advantageous for large or complex parts prone to warping.
- Stress Relief Heat Treatment: Performing a stress relief cycle before removing the part from the build plate is crucial to relax internal stresses.
- Simulation: Using build simulation software to predict stress accumulation and distortion, allowing for design modifications or optimized support strategies before printing.
- DfAM: Designing parts with features that inherently reduce stress concentration (e.g., avoiding sharp internal corners, using fillets).
- 多孔性:
- チャレンジ: Small voids or pores can form within the printed material due to incomplete fusion between layers, gas entrapment from the powder or atmosphere, or keyholing defects (vapor depressions) caused by excessive energy input. Porosity can degrade mechanical properties (especially fatigue life) and, critically for a cooling jacket, create potential leak paths.
- Mitigation Strategies:
- High-Quality Powder: Using powder with high sphericity, good flowability, low internal gas porosity, and controlled particle size distribution is fundamental. Met3dp’s use of GA and PREP technologies targets these characteristics.
- Optimized Process Parameters: Carefully tuning laser/beam power, scan speed, layer thickness, hatch spacing, and gas flow (in L-PBF) for the specific material to ensure complete melting and fusion without overheating. Extensive parameter development is key.
- Inert Atmosphere Control: Maintaining a high-purity inert gas atmosphere (Argon or Nitrogen for L-PBF, Vacuum for SEBM) to minimize oxidation and gas pickup during melting.
- Quality Control (NDT): Implementing Non-Destructive Testing methods like X-ray radiography or Computed Tomography (CT) scanning to detect internal porosity, especially in critical regions or as part of process qualification. Density measurements (e.g., Archimedes method) can provide an overall indication of porosity.
- Leak Testing: Mandatory pressure testing of every cooling jacket to confirm its integrity and absence of through-porosity.
- Support Removal Difficulties (Especially Internal):
- チャレンジ: While supports are necessary, removing them cleanly without damaging the part can be difficult, time-consuming, and costly. Supports inside complex internal cooling channels are particularly challenging, as access is limited. Incomplete removal can impede flow or detach later.
- Mitigation Strategies:
- DfAM Focus: The primary strategy is to design for minimal support use, especially internally (self-supporting angles, optimized channel shapes).
- Accessible Support Design: Designing external supports for easy access with removal tools and incorporating break-away features.
- Process Choice: SEBM often uses powder-based supports which are generally easier to remove via blasting than the fully melted supports common in L-PBF.
- Specialized Removal Techniques: Utilizing methods like Abrasive Flow Machining (AFM) or chemical etching (if material compatibility allows) for internal channel support remnants or surface smoothing.
- Inspection: Using borescopes or CT scanning to verify complete support and powder removal from internal passages.
- Powder Removal & Cross-Contamination:
- チャレンジ: Ensuring all unfused powder is removed from internal channels can be difficult. Additionally, if a manufacturer processes multiple material types, preventing cross-contamination between powders (e.g., steel powder mixing with aluminum) is critical, as even trace amounts can drastically affect material properties.
- Mitigation Strategies:
- DfAM for Powder Removal: Designing channels with adequate diameters, smooth bends, and access ports.
- Rigorous Cleaning Protocols: Implementing multi-stage cleaning processes (blowing, vibration, flushing) and verifying cleanliness.
- Dedicated Equipment: Ideally, using dedicated printers, build modules, and powder handling equipment for different material families (e.g., reactive vs. non-reactive, steel vs. aluminum vs. copper) to prevent cross-contamination.
- Strict Powder Handling Procedures: Implementing meticulous procedures for powder loading, unloading, sieving, and storage. Batch traceability is essential.
- Surface Finish & Roughness Control:
- チャレンジ: The as-built surface finish of AM parts is relatively rough compared to machining. While acceptable for some surfaces, critical areas like sealing faces require improvement, and internal channel roughness can impact flow and heat transfer in unpredictable ways if not managed.
- Mitigation Strategies:
- Parameter Optimization: Fine-tuning parameters (e.g., contour scans, smaller layer heights) can improve finish on certain surfaces, but often at the cost of build time.
- Build Orientation: Orienting critical surfaces optimally relative to the build direction (e.g., upward-facing surfaces are often smoother).
- 後処理: Utilizing appropriate surface finishing techniques (machining, polishing, AFM, etc.) targeted at the surfaces where smoothness is required.
- CFD Analysis: Using CFD to understand the impact of expected internal channel roughness on pressure drop and heat transfer, informing design decisions or finishing requirements.
- Achieving Leak-Proof Integrity:
- チャレンジ: For a cooling jacket, being leak-proof is non-negotiable. Porosity, micro-cracks (from residual stress), or defects at interfaces can all lead to coolant leaks.
- Mitigation Strategies:
- Robust Process Control: All the strategies aimed at reducing porosity and residual stress contribute here.
- Careful Post-Processing: Ensuring machining or support removal doesn’t introduce defects.
- 100% Leak Testing: Implementing mandatory, rigorous leak testing (e.g., pressure decay testing) on every single part according to defined automotive standards. This is a critical final quality check.
- Potential Impregnation: In some cases (though less desirable), micro-porosity can be sealed using specialized impregnation resins, but this is typically a recovery action rather than a primary strategy.
Addressing Challenges Requires Expertise:
Overcoming these potential pitfalls requires significant expertise in materials science, AM process physics, DfAM, and rigorous quality control. This is why selecting an experienced manufacturing partner like Met3dp is crucial. Their deep understanding of powder characteristics (from their own advanced production), printer capabilities, process parameter optimization, and integrated post-processing, backed by robust quality management systems, provides assurance that these challenges will be proactively managed to deliver reliable, high-performance EV cooling jackets. Engaging with suppliers early in the design phase allows engineers to leverage this expertise and mitigate potential issues before they arise.
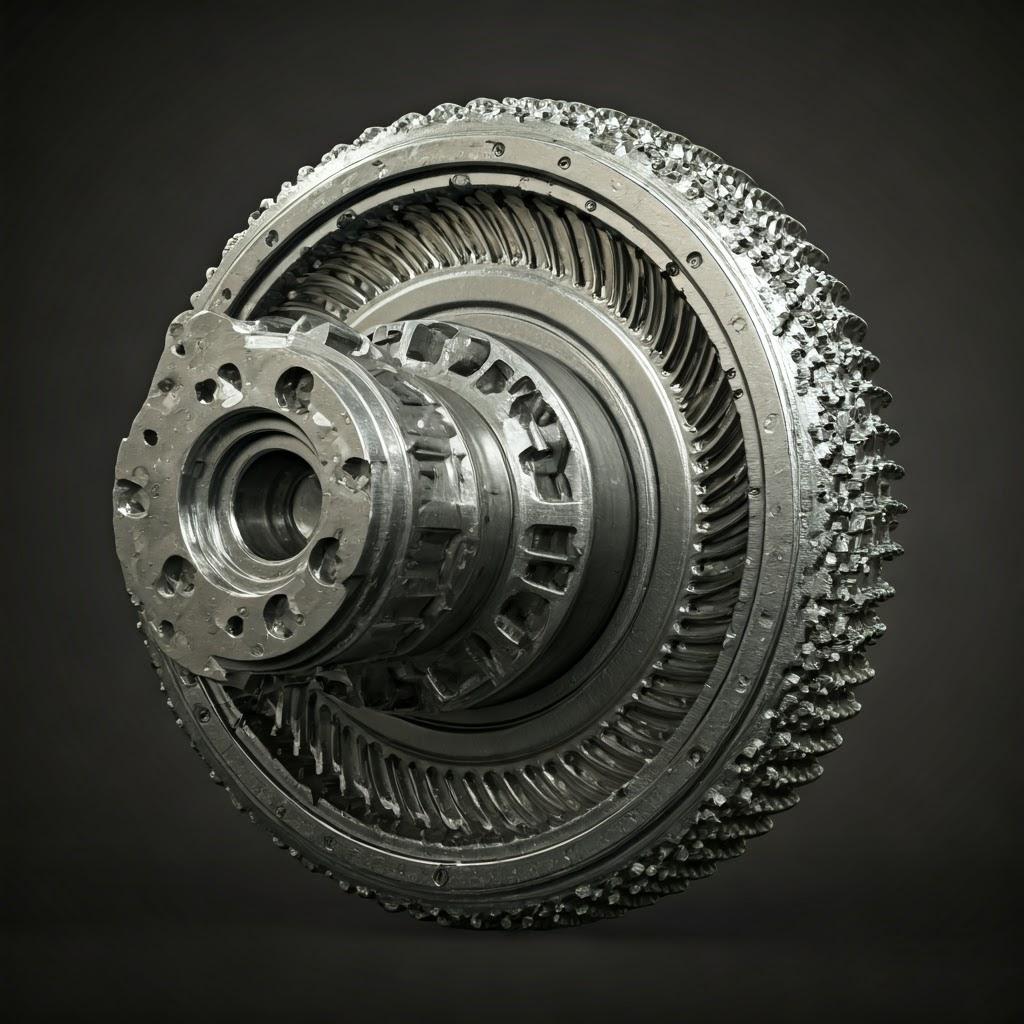
Partner Selection: Choosing the Right Metal 3D Printing Service Provider for Automotive Components
The success of implementing metal additive manufacturing for critical components like EV motor cooling jackets hinges not only on robust design and material selection but critically on the capabilities and reliability of the chosen manufacturing partner. Selecting the right AM service provider is a strategic decision for engineering teams and procurement managers, impacting quality, cost, lead time, and the overall success of the project. Given the demanding nature of the automotive industry, the evaluation criteria extend beyond mere printing capabilities.
Key Criteria for Evaluating Metal AM Suppliers for Automotive Applications:
- Quality Management Systems & Certifications:
- Requirement: The automotive industry demands rigorous quality control. Look for suppliers with a robust Quality Management System (QMS) certified to ISO 9001 as a baseline. While IATF 16949 certification (the global automotive standard) might be rare for pure AM service providers currently, demonstrating awareness, alignment with its principles (e.g., process control, traceability, risk management), and a clear roadmap towards it is a significant advantage.
- Why it Matters: Certifications indicate a commitment to documented processes, continuous improvement, traceability, and consistent quality – essential for reliable automotive component supply.
- Evaluation: Ask for current certifications, audit reports (if possible), details on their QMS, traceability procedures (from powder batch to final part), and calibration records.
- Material Expertise & Powder Quality Control:
- Requirement: Deep understanding of the materials being processed (e.g., AlSi10Mg, CuCrZr) is crucial. This includes knowledge of their metallurgical behavior during printing and heat treatment. Crucially, the supplier must have stringent controls over incoming powder quality and handling procedures to prevent contamination and ensure consistency.
- Why it Matters: Material properties directly dictate part performance. Inconsistent powder quality or poor handling leads to unpredictable print results and potential component failures. Expertise ensures correct parameter settings and heat treatments are applied.
- Evaluation: Inquire about their powder sourcing strategy (in-house production like Met3dp vs. external suppliers), powder testing procedures (PSD, morphology, chemistry, flowability), batch tracking, storage conditions, and handling protocols (especially for reactive metals or preventing cross-contamination). Discuss their experience with the specific alloys required. A provider like Met3dp, manufacturing its own high-quality powders using advanced methods like PREP and Gas Atomization, offers a distinct advantage in controlling this critical input. You can learn more 私たちについて and our integrated approach.
- Technological Capabilities & Capacity:
- Requirement: The supplier should possess state-of-the-art AM equipment (L-PBF, SEBM, or others relevant to the application) suitable for the chosen materials and required precision. Equally important are comprehensive in-house or tightly managed external capabilities for all necessary post-processing steps (stress relief, heat treatment, machining, finishing, inspection). Sufficient capacity to handle prototyping volumes and scale to low-to-medium series production is also key.
- Why it Matters: Technology dictates capability (accuracy, speed, material compatibility). Integrated post-processing streamlines the workflow, reduces lead times, and ensures accountability. Adequate capacity prevents bottlenecks and ensures on-time delivery, critical for automotive timelines.
- Evaluation: Assess their machine park (type, age, number of machines, build volume), available post-processing equipment, metrology capabilities (CMM, scanners), software tools (build preparation, simulation), and stated capacity. Inquire about their ability to scale production if needed. Met3dp’s focus on industry-leading print volume, accuracy, and reliability addresses these needs directly.
- Technical Expertise & Engineering Support:
- Requirement: The ideal partner acts as more than just a print bureau; they should offer DfAM guidance, feasibility assessments, build simulation insights, and collaborative problem-solving. Their team should include experienced engineers and metallurgists who understand both AM and the target application’s demands.
- Why it Matters: Collaboration ensures designs are optimized for manufacturability, performance, and cost-effectiveness. Expert support can help overcome design challenges and accelerate development.
- Evaluation: Review case studies or examples of similar projects. Assess the technical depth of their team during initial discussions. Inquire about their DfAM support process and simulation capabilities. Look for partners willing to invest time in understanding your specific requirements.
- Track Record & Industry Experience:
- Requirement: Proven experience in producing parts for demanding industries, ideally automotive or aerospace, is highly valuable. References or case studies demonstrating successful project execution, particularly with similar materials or component types, build confidence.
- Why it Matters: Experience implies familiarity with industry expectations, common challenges, and quality requirements. A proven track record reduces the risk associated with adopting a relatively new manufacturing technology.
- Evaluation: Ask for relevant case studies, customer testimonials, or references (respecting confidentiality). Inquire about their experience with parts requiring leak testing, tight tolerances, or specific material certifications.
- Project Management & Communication:
- Requirement: Clear communication channels, defined project timelines, regular updates, and responsive customer service are essential, especially during prototyping and production ramp-up. Professional project management ensures smooth execution.
- Why it Matters: Keeps projects on track, facilitates quick resolution of issues, and builds a strong working relationship. Critical for meeting tight automotive development schedules.
- Evaluation: Assess responsiveness during the quoting and initial discussion phases. Inquire about their project management process and designated points of contact.
- Cost & Lead Time Competitiveness:
- Requirement: While cost shouldn’t be the のみ factor, the supplier’s pricing structure must be transparent and competitive relative to the value and quality offered. Lead times must align with project deadlines.
- Why it Matters: Budget adherence and on-time delivery are fundamental business requirements.
- Evaluation: Obtain detailed quotes breaking down costs (material, machine time, post-processing, NRE). Compare quotes from multiple qualified suppliers. Discuss lead time estimates realistically, considering complexity and post-processing needs.
Supplier Evaluation Checklist Summary:
基準 | Key Questions to Ask | Why It’s Crucial for Automotive AM |
---|---|---|
Quality System/Certs | ISO 9001? IATF awareness/plans? Traceability process? Audit results? | Ensures consistent quality, reliability, process control |
材料に関する専門知識 | Experience with required alloys? Powder sourcing/QC? Handling protocols? | Guarantees correct material properties, prevents defects & contamination |
Technology & Capacity | Machine park (type/qty/volume)? Post-processing capabilities (in-house)? Metrology? Scalability? | Determines technical feasibility, workflow efficiency, on-time delivery |
テクニカルサポート | DfAM guidance offered? Simulation capabilities? Engineering team expertise? Collaborative approach? | Optimizes design for AM, accelerates development, solves problems |
実績 | Automotive/relevant industry experience? Case studies/references? Similar parts produced? | Reduces risk, demonstrates understanding of industry requirements |
Project Management | Communication process? Project updates? Responsiveness? Dedicated contacts? | Ensures smooth execution, meets deadlines, builds trust |
コストとリードタイム | Transparent pricing? Competitive quote? Realistic lead times? Alignment with project needs? | Meets budget and schedule constraints |
Export to Sheets
Selecting the right metal AM partner is a critical step for any company looking to leverage this technology for demanding applications like EV motor cooling jackets. A thorough evaluation based on these criteria will help identify suppliers like Met3dp, who possess the necessary combination of quality systems, material control, technological prowess, expertise, and customer focus required to deliver reliable, high-performance components for the future of electric mobility.
Understanding the Investment: Cost Factors and Typical Lead Times for 3D Printed Cooling Jackets
While the technical advantages of metal 3D printing for EV cooling jackets are compelling, understanding the associated costs and lead times is essential for project planning, budgeting, and making informed decisions, especially for procurement departments comparing AM against traditional manufacturing routes. The cost structure of AM differs significantly from casting or machining, particularly concerning volume dependency and tooling.
Key Cost Drivers in Metal Additive Manufacturing:
- Material Cost & Consumption:
- Powder Price: The base cost per kilogram of the metal powder is a primary factor. Advanced alloys like CuCrZr are significantly more expensive than common AlSi10Mg. High-quality powder with specific characteristics (sphericity, PSD) also commands a premium.
- Part Volume & Density: The actual volume of the final part dictates the amount of powder fused. DfAM techniques like topology optimization and lattice structures directly reduce material consumption and cost.
- サポート体制: Material used for support structures also contributes to overall consumption, although this powder is often recyclable (with careful quality control). Minimizing supports through DfAM reduces this cost.
- Waste/Recycling: Some powder is inevitably lost or degraded during handling and printing. Efficient powder recycling processes employed by the supplier can help mitigate this cost, but require rigorous testing to ensure recycled powder quality.
- Machine Time (Build Time):
- Primary Driver: This is often the largest cost component, representing the time the expensive AM machine is occupied printing the part.
- Influencing Factors:
- Part Height (Z-axis): Build time is directly proportional to the number of layers, hence the part’s height in the build orientation is critical.
- Part Volume/Area per Layer: The amount of material to be fused in each layer affects the time required for scanning.
- 複雑さ: Highly complex geometries may require slower scan speeds or more intricate scan strategies.
- 層の厚さ: Thinner layers improve resolution and surface finish but significantly increase the number of layers and thus build time.
- Machine Type & Power: Faster machines with higher power lasers/beams or multiple beams can reduce build times but have higher hourly operating rates.
- Nesting/Packing Density: Printing multiple parts simultaneously in one build significantly improves machine utilization and reduces the cost per part. Experienced suppliers optimize build layouts.
- 人件費:
- Pre-Processing: Build preparation (CAD file processing, orientation, support generation, slicing) requires skilled technicians/engineers.
- Machine Operation: Monitoring the build process.
- 後処理: This can be highly labor-intensive, involving de-powdering, part removal, support removal, heat treatment setup, machining setup/operation, finishing, cleaning, and inspection. The complexity of the part and the level of finishing required heavily influence post-processing labor.
- 後処理費用:
- Consumables & Energy: Heat treatment (furnace time, inert gas/vacuum), machining (tool wear, coolant), finishing media (blasting, polishing).
- Specialized Processes: Costs associated with specific steps like wire EDM, AFM, CT scanning, or specialized coating applications.
- Quality Control & Inspection:
- Labor & Equipment: Time spent on dimensional inspection (CMM, scanning), leak testing, NDT, material testing (if required), and documentation. The level of QC required impacts cost.
- Non-Recurring Engineering (NRE):
- Initial Setup: Costs associated with initial design consultation, DfAM optimization, specific fixture design (for machining/inspection), or process parameter development for unique applications. Usually amortized over the first batch of parts.
- Quantity (Batch Size):
- Amortization: NRE costs and setup labor are spread over the number of parts produced.
- Machine Utilization: Larger batches allow for better build plate nesting, significantly improving machine time efficiency and reducing the cost per part.
- Learning Curve: Efficiencies in post-processing can often be gained with larger batches.
- Volume Breaks: Suppliers often offer tiered pricing based on quantity.
Cost Comparison Caveats:
Directly comparing AM costs to traditional methods requires careful consideration of volume.
- Prototyping & Low Volume (<100s): AM is often highly cost-competitive or even cheaper due to the absence of tooling costs (molds/dies for casting).
- Medium Volume (100s – low 1000s): The comparison becomes complex. Optimized AM parts (lightweight, consolidated) might offer functional advantages justifying a potential cost premium, or costs might be comparable depending on complexity and post-processing.
- High Volume (10,000s+): Traditional methods like die casting typically offer a lower cost per part due to economies of scale, assuming the design is suitable for casting. However, the total cost of ownership (considering performance gains, weight savings, simplified assembly from AM) should be evaluated.
Typical Lead Times:
Lead time is the duration from order placement (and final design confirmation) to part delivery. It’s highly variable but follows a general pattern:
- Prototyping (1-10 units):
- Typical Range: 1 to 4 weeks.
- Influencing Factors: Current machine availability, build time (often 1-3 days for a cooling jacket depending on size/complexity), required post-processing complexity (basic stress relief and support removal vs. full heat treatment, extensive machining, and finishing). Expedited options are often available at a premium.
- Low Volume Production (10s – low 100s):
- Typical Range: 4 to 8 weeks.
- Influencing Factors: Need for optimized build layouts, scheduling machine time for multiple builds, potentially developing specific fixtures for machining or inspection, managing the flow through various post-processing steps efficiently. Material availability for larger quantities can also play a role.
- Medium Volume Production (high 100s – 1000s):
- Typical Range: 8 to 16+ weeks (often involving phased deliveries).
- Influencing Factors: Requires significant machine capacity planning, potentially dedicated machine time, robust supply chain for powder, potentially scaling up post-processing capabilities, and extensive quality control planning. Process optimization and establishing a stable production rhythm are key.
Factors Accelerating/Decelerating Lead Times:
- Accelerating: Clear design specifications, DfAM optimized parts (fewer supports, less post-processing), readily available powder, good supplier relationship/communication, choosing a supplier with integrated capabilities.
- Decelerating: Design changes mid-process, complex geometries requiring extensive supports or intricate post-processing, non-standard material requests, supplier capacity constraints, shipping/logistics delays.
Lead Time & Cost Summary Table:
ファクター | コストへの影響 | Impact on Lead Time | Mitigation / Optimization |
---|---|---|---|
デザインの複雑さ | Increases (Build time, supports, post-proc.) | Increases (Build, post-proc.) | DfAM for simplification where possible, optimize supports |
Part Size/Volume | Increases (Material, build time) | Increases (Build time) | DfAM for lightweighting, nesting parts in build |
素材の選択 | Significant (CuCrZr >> AlSi10Mg) | Minor (Different parameters), Major (If sourcing delays) | Select based on true need, ensure supplier has material expertise |
数量 | Decreases per part (Amortization, efficiency) | Increases overall, Decreases per part potentially (efficiency) | Optimize batch sizes, plan production schedule |
後処理 | Significant Driver (Labor, equipment time) | Significant Driver | DfAM to minimize machining/finishing needs, integrated supplier |
Quality Req.s | Increases (Inspection time, NDT costs) | Increases (Inspection time) | Define requirements clearly upfront |
Export to Sheets
Understanding the interplay of these factors allows for more accurate budgeting and project scheduling when considering metal AM for EV motor cooling jackets. Open discussions with potential suppliers like Met3dp about specific design requirements and volume expectations are crucial for obtaining realistic cost estimates and lead time projections.
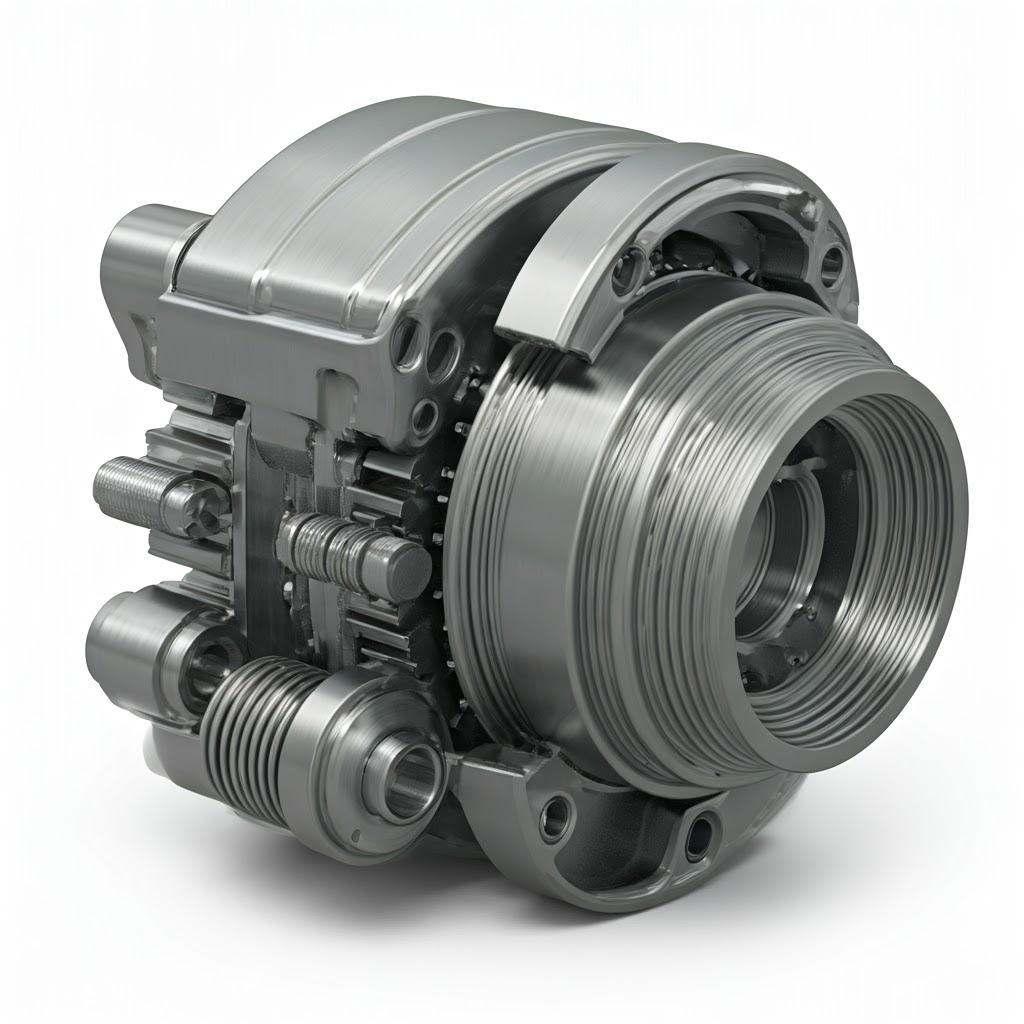
Frequently Asked Questions (FAQ) for Procurement and Engineering Teams
Here are answers to some common questions engineers and procurement managers have when considering metal 3D printing for EV motor cooling jackets:
1. How does the cost of a 3D printed cooling jacket compare to traditional casting, especially as production volume increases?
- 答え: The cost comparison depends heavily on volume and complexity.
- Prototypes & Low Volume (< ~100 units): Metal 3D printing is often より費用対効果が高い than casting because it avoids the extremely high upfront cost and long lead time associated with creating casting molds or dies.
- Medium Volume (~100 – 2,000 units): This is a transition zone. The cost-competitiveness of AM depends on factors like design complexity (AM handles complexity better), potential for part consolidation (reducing assembly costs), lightweighting benefits (value of weight saved), and the specific AM process/material versus the casting method (e.g., sand vs. die casting). Optimized AM parts might command a premium justified by performance gains.
- High Volume (10,000+ units): For relatively simple designs manufacturable via die casting, traditional methods typically achieve a lower piece price due to established economies of scale. However, if AM enables significant performance improvements (better cooling, higher motor efficiency) or weight reduction (improved vehicle range), a total cost of ownership analysis might still favor AM even at higher volumes for certain applications. It’s crucial to evaluate not just piece price but the overall value proposition.
2. What are the typical testing and validation procedures required to qualify a 3D printed metal cooling jacket for automotive use?
- 答え: Qualification involves rigorous testing beyond standard dimensional checks, mirroring requirements for traditionally manufactured parts but with added focus on AM-specific aspects. Key procedures include:
- Material Property Verification: Tensile testing, hardness testing, and microstructural analysis (often using witness coupons printed alongside the parts) to confirm the material meets specifications after printing and heat treatment. Consistency across builds is monitored.
- Leak Testing: Mandatory 100% pressure decay or helium leak testing to ensure fluid containment integrity under operational pressures. Acceptance criteria are typically stringent.
- Dimensional Validation: Full layout inspection using CMM or 3D scanning to verify conformance to drawings, including critical interface dimensions and GD&T callouts.
- 非破壊検査(NDT): Depending on criticality, CT scanning or X-ray inspection might be employed (especially during process qualification) to detect internal defects like porosity or lack of fusion. Dye penetrant or magnetic particle testing might be used on surfaces after machining.
- Burst Pressure Testing: Testing samples to failure under hydrostatic pressure to determine the safety margin above maximum operating pressure.
- Thermal Cycling & Vibration Testing: Simulating operational conditions to assess durability and resistance to fatigue under combined thermal and mechanical loads.
- Coolant Compatibility Testing: Ensuring long-term resistance to corrosion and degradation when exposed to specified automotive coolants.
- Process Validation (PPAP Elements): Aligning with elements of the Production Part Approval Process (PPAP) framework, including process flow diagrams, FMEAs (Failure Modes and Effects Analysis), control plans, and capability studies, demonstrates manufacturing readiness for series production.
3. Can the complex internal cooling channels designed with DfAM be reliably and consistently produced, and how is their internal quality verified?
- 答え: Yes, producing complex internal channels reliably is a key strength of metal AM, but it requires careful design and rigorous process control.
- Reliability & Consistency: Achieved through:
- DfAM: Designing channels with self-supporting shapes (e.g., teardrop, diamond) and smooth transitions to minimize the need for internal supports and facilitate powder removal.
- Optimized Parameters: Using validated print parameters specific to the material and channel geometry to ensure complete fusion and minimize defects.
- パウダーの質: Using high-quality, flowable powder.
- Robust Cleaning: Implementing thorough, validated de-powdering procedures.
- Verification: Internal quality is verified through:
- Visual Inspection (where possible): Using borescopes to visually inspect accessible portions of the channels for obstructions, support remnants, or gross defects.
- Flow Testing: Measuring pressure drop across the channels at defined flow rates to ensure they are clear and match CFD predictions. Blockages or significant deviations indicate problems.
- CT Scanning: Computed Tomography provides a detailed 3D view of the internal structure, allowing verification of channel geometry, detection of internal porosity or powder remnants, and assessment of wall thickness. This is often used during process development and qualification, and potentially on a sampling basis during production for highly critical parts.
- Leak Testing: This serves as a final functional check confirming the overall integrity of the channel walls.
- Reliability & Consistency: Achieved through:
Partnering with an experienced AM provider like Met3dp, who has robust processes for DfAM, parameter optimization, cleaning, and inspection (including potential NDT), is essential for achieving reliable and verifiable complex internal geometries. Explore our range of metal powders and solutions suitable for these demanding applications.
Conclusion: Driving the Future of EV Performance with Additive Manufactured Cooling Jackets
The transition to electric mobility demands continuous innovation across every vehicle system, and thermal management stands out as a critical enabler for performance, range, and reliability. As we’ve explored, EV motor cooling jackets represent a prime opportunity where the limitations of traditional manufacturing can be overcome by the transformative capabilities of metal additive manufacturing.
By embracing metal 3D printing, engineers gain unprecedented design freedom. They can craft cooling jackets with intricate, conformal internal channels optimized through advanced simulation, maximizing heat transfer exactly where needed. Topology optimization and lattice structures allow for significant lightweighting, contributing directly to vehicle efficiency and range. Furthermore, the ability to consolidate multiple components into a single printed part simplifies assembly, reduces potential failure points, and streamlines the supply chain.
The journey involves careful material selection, choosing between the balanced performance of alloys like AlSi10Mg or the superior thermal conductivity of CuCrZr, powered by high-quality powders. Success requires meticulous adherence to Design for Additive Manufacturing (DfAM) principles, navigating potential challenges like residual stress and porosity through expert process control, and implementing comprehensive post-processing and validation steps, including crucial leak testing.
Choosing the right manufacturing partner – one with proven expertise, robust quality systems, advanced technological capabilities, and a deep understanding of materials – is paramount. Companies like Met3dp, with vertically integrated capabilities spanning from advanced powder production to precision printing and application development support, are ideally positioned to help automotive manufacturers harness the full potential of AM.
Metal 3D printing is no longer just a prototyping tool; it is a viable, strategic manufacturing solution offering tangible performance benefits for demanding EV components. As the electric vehicle market continues to accelerate, the adoption of additively manufactured motor cooling jackets will undoubtedly play an increasingly important role in pushing the boundaries of thermal efficiency, power density, and overall vehicle performance. By partnering with leading experts and embracing this advanced technology, OEMs and suppliers can help drive the future of electric mobility.
Explore how Met3dp’s cutting-edge systems and powders can power your organization’s additive manufacturing goals by visiting our website: https://met3dp.com/.
シェアする
MET3DP Technology Co., LTDは、中国青島に本社を置く積層造形ソリューションのリーディングプロバイダーです。弊社は3Dプリンティング装置と工業用途の高性能金属粉末を専門としています。
関連記事
Met3DPについて
最新情報
製品
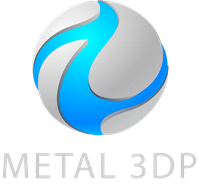
3Dプリンティングと積層造形用金属粉末