3D Printed Exhaust Outlets
目次
Introduction to 3D Printed Exhaust Outlets for Automotive Applications
The automotive industry is constantly pushing the boundaries of innovation, seeking lighter, more efficient, and higher-performing components. Among these critical parts, the exhaust outlet plays a vital role in managing engine emissions and overall vehicle performance. Traditionally manufactured through processes like casting and forging, exhaust outlets are now undergoing a transformative shift with the advent of metal 3Dプリンティング, also known as metal additive manufacturing. This cutting-edge technology offers unprecedented design freedom, material flexibility, and the potential for enhanced functionality, making it an increasingly attractive solution for automotive engineers and procurement managers.
Metal 3D printing enables the creation of complex geometries that were previously impossible or cost-prohibitive with conventional manufacturing methods. This opens doors to optimizing exhaust flow, reducing weight, and integrating additional features directly into the component. For businesses looking for advanced manufacturing solutions, understanding the capabilities and benefits of 3D printed exhaust outlets is crucial. Companies like Metal3DP Technology Co., LTD, a leading provider of additive manufacturing solutions headquartered in Qingdao, China, are at the forefront of this revolution, offering industry-leading print volume, accuracy, and reliability for mission-critical automotive parts. Their expertise in both 3D printing equipment and high-performance metal powders positions them as a trusted partner for automotive manufacturers exploring the advantages of additive manufacturing.
Key Applications of 3D Printed Exhaust Outlets in the Automotive Sector
The versatility of metal 3D printing allows for the application of 3D printed exhaust outlets across a wide spectrum of the automotive industry. Here are some key areas where these components are making a significant impact:
- Performance Vehicles: In high-performance cars and racing applications, every gram of weight saved and every improvement in exhaust flow can translate to enhanced speed and efficiency. 3D printing allows for the creation of lightweight, aerodynamically optimized exhaust outlet designs that maximize performance.
- Luxury and Custom Vehicles: The ability to create complex and customized designs makes metal 3D printing ideal for luxury and bespoke vehicles. Manufacturers can offer unique exhaust outlet designs that differentiate their products and cater to individual customer preferences.
- Electric Vehicles (EVs): While EVs don’t have traditional combustion engines, thermal management remains critical. 3D printing can be used to create intricate cooling channels within exhaust outlets (for auxiliary systems or thermal management of other components), optimizing heat dissipation and improving overall system efficiency.
- Aftermarket and Replacement Parts: Metal 3D printing offers a cost-effective solution for producing low volumes of aftermarket or replacement exhaust outlets, especially for older or niche vehicle models where traditional tooling may no longer be available or economically viable.
- Prototyping and Testing: Before committing to mass production, automotive engineers can leverage metal 3D printing to rapidly prototype and test various exhaust outlet designs. This allows for quick iterations and performance evaluations, accelerating the development cycle.
Exploring the range of applications highlights the transformative potential of metal 3D printing in the automotive sector. To learn more about the capabilities of metal 3D printing, you can visit 金属3Dプリンティング.
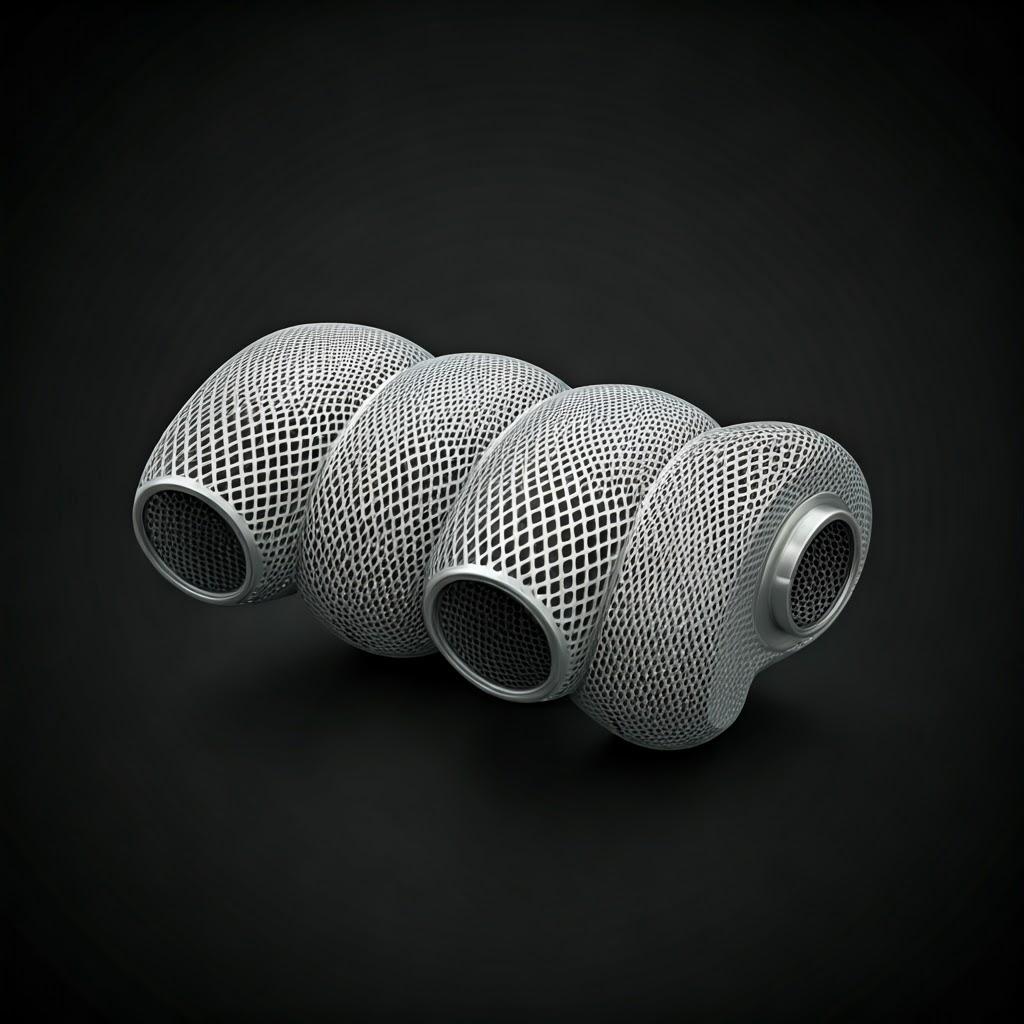
Advantages of Metal 3D Printing for Exhaust Outlet Manufacturing Over Traditional Methods
Adopting metal 3D printing for the manufacturing of exhaust outlets offers several compelling advantages compared to traditional methods like casting, forging, and machining:
- デザインの自由と複雑さ: Metal 3D printing allows for the creation of intricate internal channels, complex geometries, and optimized flow paths that are difficult or impossible to achieve with traditional manufacturing. This design freedom can lead to improved exhaust gas flow, reduced backpressure, and enhanced engine performance.
- 軽量化: By optimizing designs and utilizing lightweight metal powders, 3D printed exhaust outlets can be significantly lighter than their traditionally manufactured counterparts. This weight reduction contributes to improved fuel efficiency and overall vehicle performance.
- 材料効率: Additive manufacturing processes build parts layer by layer, using only the necessary material. This significantly reduces material waste compared to subtractive methods like machining, leading to cost savings and a more sustainable manufacturing process.
- ラピッドプロトタイピングとカスタマイズ: Metal 3D printing enables rapid iteration of designs and the production of customized exhaust outlets without the need for expensive tooling changes. This agility is crucial for accelerating product development and catering to specific performance requirements or niche markets.
- Integration of Features: 3D printing allows for the integration of multiple components into a single part, reducing the need for assembly and potentially improving the reliability and durability of the exhaust system. For instance, features like mounting brackets or sensors can be directly incorporated into the exhaust outlet design.
- オンデマンド製造: Metal 3D printing facilitates on-demand production, eliminating the need for large production runs and warehousing of parts. This is particularly beneficial for low-volume production, aftermarket components, or customized applications.
Considering these advantages, it’s clear why metal 3D printing is gaining traction as a preferred manufacturing method for automotive exhaust outlets. Metal3DP’s commitment to providing advanced metal powders ensures that these benefits can be fully realized in the final product. 彼らの 高度な粉体製造システム plays a crucial role in delivering high-quality materials for demanding automotive applications.
Material Selection: Why IN625 and 17-4PH are Ideal for 3D Printed Exhaust Outlets
The choice of material is paramount in determining the performance and durability of an exhaust outlet. For metal 3D printing of automotive exhaust outlets, IN625 and 17-4PH stainless steel are often recommended due to their exceptional properties:
IN625 (Nickel-Chromium-Molybdenum Alloy):
| Property | Value | Benefit for Exhaust Outlets| High-Temperature Strength | Maintains strength up to elevated temperatures (around 815°C / 1500°F) | Ensures structural integrity in the hot exhaust environment. | | Corrosion Resistance | Excellent resistance to oxidation, pitting, and crevice corrosion | Withstands the corrosive nature of exhaust gases and environmental factors, leading to a longer lifespan. | | Fatigue Strength | High fatigue strength | Resists cracking and failure under the cyclic thermal and mechanical stresses experienced by exhaust systems. | | Weldability | Good weldability | Facilitates any necessary post-processing or integration with other exhaust system components. | | Creep Resistance | Excellent creep resistance at high temperatures | Prevents deformation under sustained high temperatures and loads. |
17-4PH Stainless Steel (Precipitation Hardening Stainless Steel):
| Property | Value | Benefit for Exhaust Outlets | | Strength | High strength and hardness after heat treatment | Provides excellent durability and resistance to mechanical damage. | | Corrosion Resistance | Good corrosion resistance | Offers adequate protection against exhaust gases and environmental exposure. | | Ductility and Toughness | Good ductility and toughness | Allows for some flexibility and impact resistance, reducing the risk of brittle failure. | | Cost-Effectiveness | Generally more cost-effective than IN625 | Can be a more economical option for certain applications where extreme high-temperature performance isn’t the primary concern. | | Machinability | Good machinability in the annealed state | Facilitates any necessary post-processing or integration. |
The selection between IN625 and 17-4PH depends on the specific requirements of the automotive application. For extreme high-temperature environments and demanding performance needs, IN625 offers superior resistance. For applications where high strength and good corrosion resistance are crucial, and cost is a significant factor, 17-4PH presents a viable alternative. Metal3DP offers a range of 高品質の金属粉 including these alloys, ensuring customers can choose the optimal material for their 3D printed exhaust outlets. Their expertise in material science and additive manufacturing processes guarantees the production of high-performance components tailored to the rigorous demands of the automotive industry.
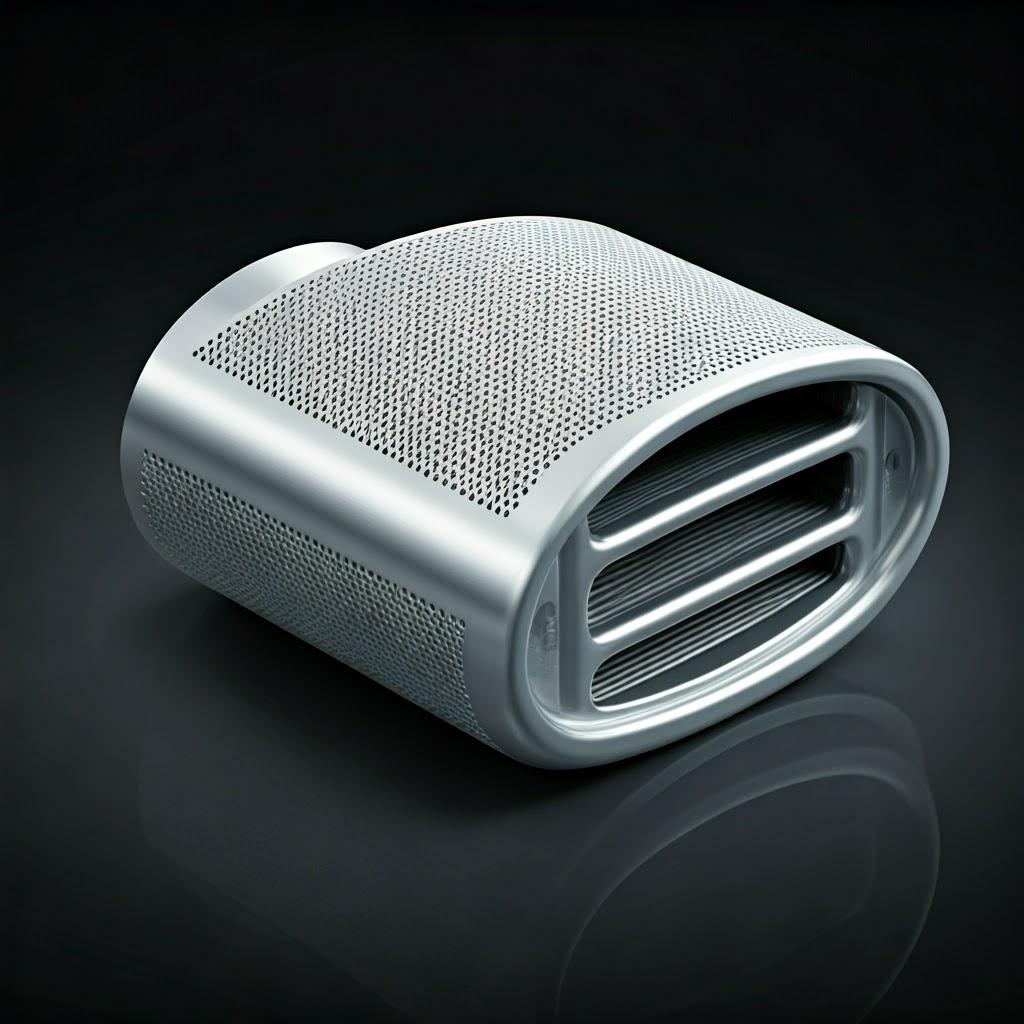
Design Optimization for Additively Manufactured Exhaust Outlets
The transition to metal 3D printing opens up a realm of possibilities for optimizing the design of automotive exhaust outlets. Unlike traditional manufacturing constraints, additive manufacturing allows for intricate geometries that can significantly enhance performance and efficiency. Here are key design considerations for additively manufactured exhaust outlets:
- Topology Optimization: This computational technique can be employed to identify and remove material in non-critical areas while maintaining structural integrity. For exhaust outlets, this can lead to significant weight reduction without compromising strength or durability. The organic, lattice-like structures often resulting from topology optimization are only achievable through additive manufacturing.
- Computational Fluid Dynamics (CFD) Analysis: Integrating CFD simulations into the design process allows engineers to analyze and optimize exhaust gas flow. By simulating different internal channel designs, restrictions and turbulence can be minimized, leading to improved engine efficiency and reduced backpressure. 3D printing enables the realization of these complex internal geometries.
- Thermal Management Integration: Additive manufacturing facilitates the incorporation of intricate cooling channels directly into the exhaust outlet structure. This can be crucial for managing high temperatures, protecting surrounding components, and even recovering waste heat in advanced automotive systems.
- パーツの統合: Instead of assembling multiple components, 3D printing allows for the consolidation of several parts into a single, integrated exhaust outlet. This reduces the number of joints and fasteners, potentially improving reliability, reducing assembly time, and lowering overall system weight. Features like mounting brackets, sensor housings, or even catalytic converter elements can be directly incorporated.
- Customization and Performance Tuning: For high-performance vehicles or specific engine configurations, 3D printing allows for the creation of highly customized exhaust outlet designs tailored to achieve optimal performance characteristics. This level of customization is difficult and expensive with traditional methods.
- Surface Texture Optimization: Additive manufacturing offers control over surface textures, which can influence heat transfer and fluid flow. Tailoring the internal surface finish of the exhaust outlet can potentially enhance heat dissipation or reduce flow resistance.
By embracing these design considerations unique to additive manufacturing, automotive engineers can create exhaust outlets that offer superior performance, reduced weight, and enhanced functionality compared to traditionally manufactured parts. Metal3DP’s expertise in additive manufacturing processes and material selection supports the realization of these complex and optimized designs. Their understanding of design for additive manufacturing (DfAM) principles ensures that customers can leverage the full potential of metal 3D printing.
Achieving Precision: Tolerance, Surface Finish, and Dimensional Accuracy in 3D Printed Exhaust Outlets
In the demanding automotive industry, precision is paramount. Metal 3D printing has evolved significantly in its ability to produce parts with tight tolerances, controlled surface finishes, and high dimensional accuracy. Here’s what automotive engineers and procurement managers can expect:
- Tolerance Capabilities: Modern metal 3D printing technologies, such as Selective Laser Melting (SLM) and Electron Beam Melting (EBM), can achieve dimensional tolerances ranging from ±0.05 mm to ±0.1 mm, depending on the part geometry, size, and material. For critical interfaces and mounting points on exhaust outlets, these tolerances ensure proper fit and functionality within the overall exhaust system. Metal3DP’s printers are engineered to deliver industry-leading accuracy, ensuring that 3D printed exhaust outlets meet stringent automotive standards.
- 表面仕上げ: The as-built surface finish in metal 3D printing typically ranges from 5 to 20 Ra (Roughness average) micrometers. While this may be suitable for some internal features, post-processing techniques like polishing, machining, or abrasive blasting can be employed to achieve smoother surface finishes, which may be required for optimal flow characteristics or aesthetic reasons on external surfaces of the exhaust outlet.
- 寸法精度: Dimensional accuracy refers to the ability of the 3D printing process to reproduce the intended design dimensions. Factors influencing dimensional accuracy include material shrinkage during solidification, thermal gradients, and the calibration of the 3D printer. Experienced service providers like Metal3DP implement rigorous process control and calibration procedures to maximize dimensional accuracy and minimize deviations from the CAD model.
- Design for Manufacturing (DFM) Considerations: To achieve the desired levels of tolerance, surface finish, and dimensional accuracy, it’s crucial to consider the limitations and capabilities of the chosen 3D printing process during the design phase. Features like thin walls, overhangs, and intricate internal structures can impact the achievable precision. Collaboration with experienced additive manufacturing specialists is essential to optimize designs for manufacturability and ensure the required precision is met.
By understanding the achievable precision levels and employing appropriate design and post-processing strategies, automotive manufacturers can confidently utilize metal 3D printing to produce exhaust outlets that meet the stringent requirements of the industry.
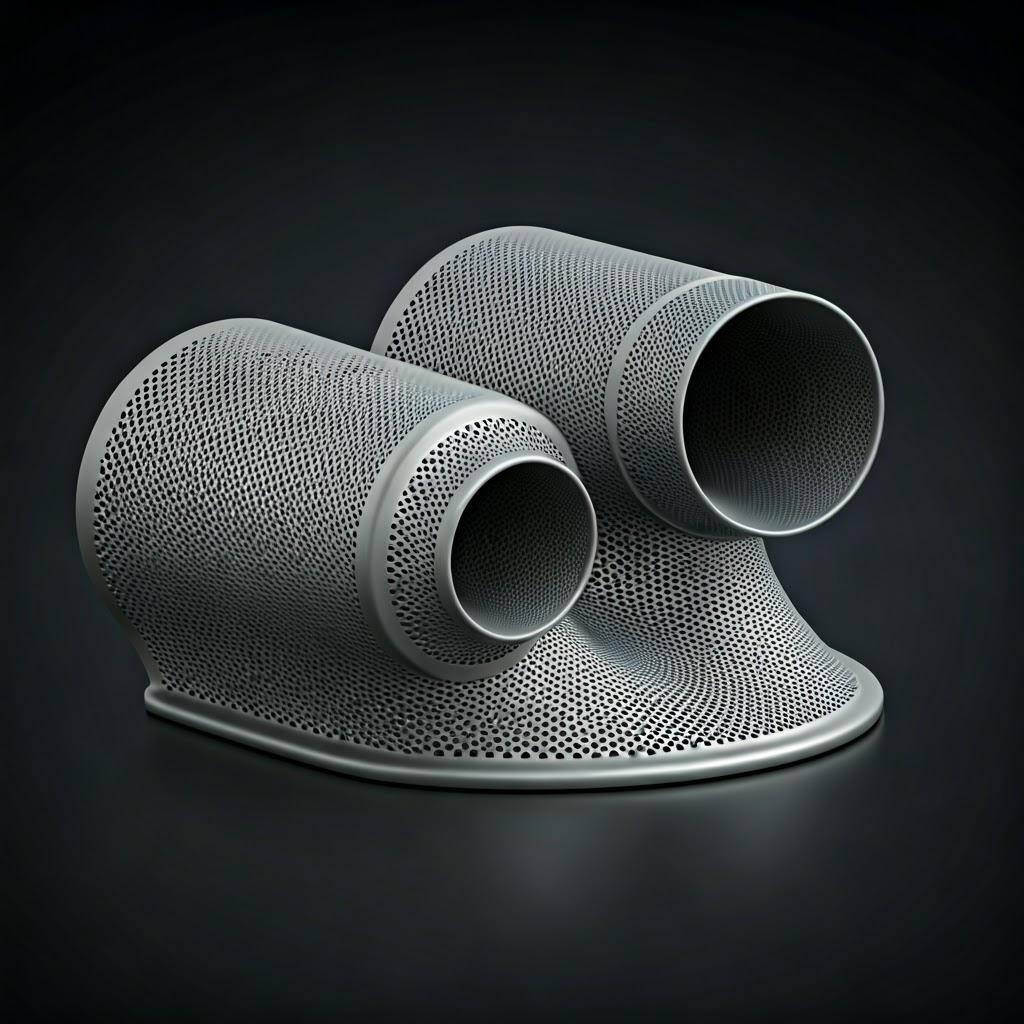
Post-Processing Techniques for 3D Printed Automotive Exhaust Outlets
While metal 3D printing offers significant advantages in creating complex geometries, post-processing steps are often necessary to achieve the final desired properties, surface finish, and dimensional accuracy of automotive exhaust outlets. Common post-processing techniques include:
- サポートの取り外し: Metal 3D printing often requires the use of support structures to prevent warping and ensure proper formation of overhanging features. These supports need to be carefully removed after the printing process, typically through manual cutting, machining, or chemical dissolution, depending on the material and support type.
- 熱処理: To relieve internal stresses induced during the printing process and to achieve the desired mechanical properties (e.g., hardness, strength, ductility), heat treatment is often performed. This may involve processes like stress relieving, annealing, or precipitation hardening, depending on the material and application requirements.
- CNC Machining: For critical surfaces requiring very tight tolerances or specific surface finishes that cannot be directly achieved through 3D printing, CNC machining can be employed as a secondary operation. This is often used for mating surfaces, threaded holes, or other high-precision features.
- 表面仕上げ: To improve the surface finish for aesthetic or functional reasons (e.g., reducing flow resistance), various surface finishing techniques can be applied, including:
- 研磨: Mechanical or electrochemical polishing can create smooth, lustrous surfaces.
- Abrasive Blasting: Using media like glass beads or ceramic particles to create a uniform matte finish and remove minor surface imperfections.
- 振動仕上げ: Placing parts in a vibrating chamber with abrasive media to smooth edges and surfaces.
- コーティング: Coatings can be applied to enhance the corrosion resistance, wear resistance, or thermal barrier properties of the exhaust outlet. Common coatings include ceramic coatings, electroplating, or painting.
- Inspection and Quality Control: After post-processing, thorough inspection using techniques like coordinate measuring machines (CMM), non-destructive testing (NDT), and surface roughness measurement is crucial to ensure that the 3D printed exhaust outlets meet the required specifications and quality standards.
The specific post-processing steps required will depend on the material, the intended application, and the desired final properties of the exhaust outlet. Collaborating with a full-service metal 3D printing provider like Metal3DP, which offers comprehensive post-processing capabilities, can streamline the manufacturing process and ensure high-quality finished parts.
Overcoming Common Challenges in Metal 3D Printing of Exhaust Outlets
While metal 3D printing offers numerous advantages, there are also potential challenges that need to be addressed to ensure successful production of high-quality exhaust outlets:
- Warping and Distortion: Thermal stresses during the printing process can lead to warping or distortion of the part, especially for large or complex geometries. Proper design for additive manufacturing (DfAM) principles, optimized build parameters, and the use of support structures can help mitigate these issues.
- Residual Stresses: The layer-by-layer build process can induce residual stresses within the printed part, which can affect its mechanical properties and dimensional stability. Post-processing heat treatment is often necessary to relieve these stresses.
- 多孔性: Internal voids or porosity can occur in 3D printed metal parts, which can reduce their strength and fatigue resistance. Optimizing printing parameters, material selection, and powder quality are crucial for minimizing porosity. Metal3DP’s 高度な粉体製造システム ensures high-quality powders with excellent flowability, which helps in producing dense, low-porosity parts.
- 表面粗さ: As-built surface roughness can be higher compared to traditional manufacturing methods, which may not be suitable for all applications. Post-processing techniques are often required to achieve smoother surfaces.
- Support Removal Challenges: Removing support structures from intricate internal channels or delicate features can be challenging and may require specialized techniques to avoid damaging the part. Design modifications to minimize the need for supports can be beneficial.
- コストを考慮する: While metal 3D printing can be cost-effective for low-volume production and complex geometries, the initial investment in equipment and materials can be significant. Understanding the cost drivers and optimizing designs for efficient printing are important for cost management.
- Scalability for Mass Production: While metal 3D printing is ideal for prototyping and low-to-medium volume production, scaling up for mass production of automotive components can present challenges in terms of production speed and cost-effectiveness compared to established high-volume manufacturing processes. Hybrid manufacturing approaches combining 3D printing for complex features with traditional methods for bulk production may be a solution in some cases.
By understanding these potential challenges and working with experienced metal 3D printing providers like Metal3DP, automotive manufacturers can develop effective strategies to mitigate risks and leverage the benefits of additive manufacturing for their exhaust outlet applications.
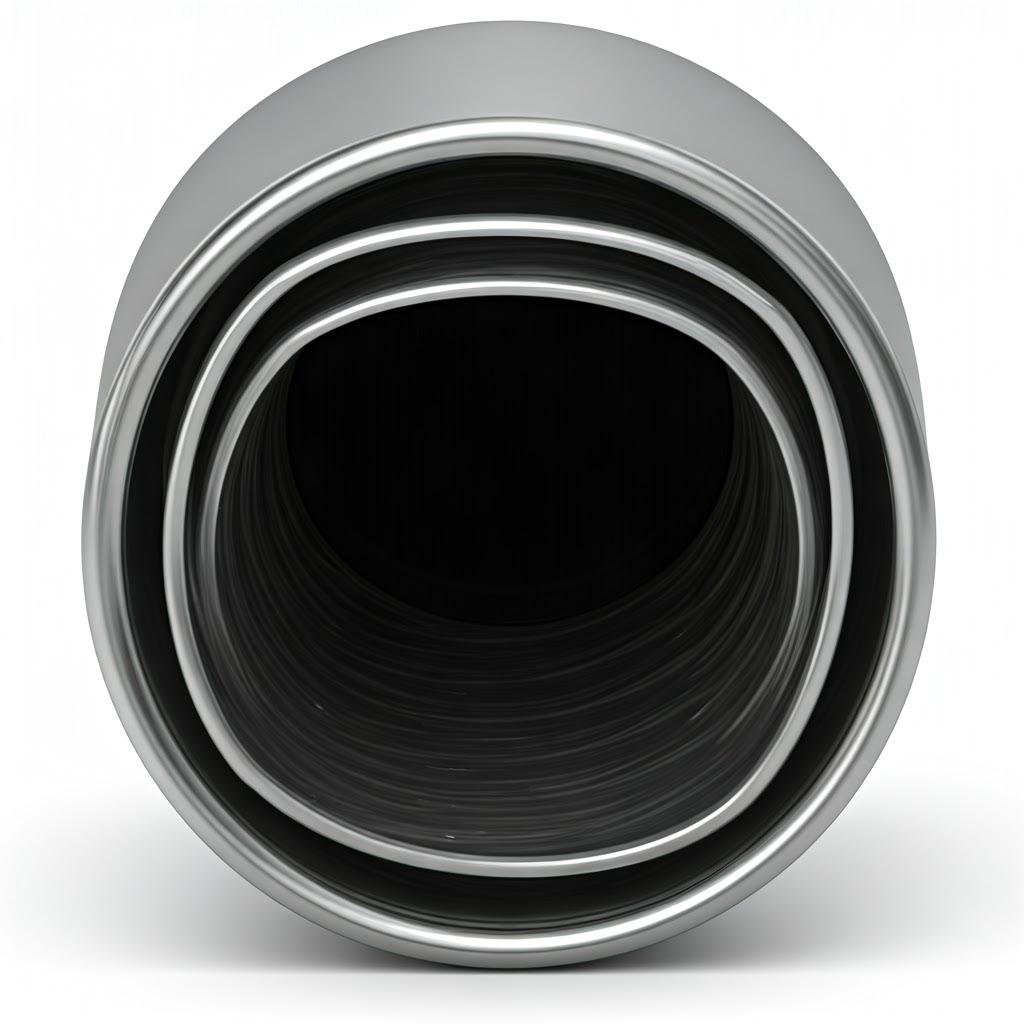
Selecting the Right Metal 3D Printing Service Provider for Automotive Components
Choosing the right metal 3D printing service provider is a critical decision that can significantly impact the quality, cost, and lead time of your automotive exhaust outlets. Here are key factors to consider when evaluating potential suppliers:
- Material Capabilities: Ensure the provider has experience working with the recommended materials for exhaust outlets, such as IN625 and 17-4PH, and possesses the necessary expertise in processing these materials to achieve the desired mechanical properties and corrosion resistance. Metal3DP manufactures a wide range of 高品質の金属粉, demonstrating their commitment to material excellence.
- Technology and Equipment: Inquire about the types of metal 3D printing technologies they utilize (e.g., SLM, DMLS, EBM) and the specifications of their equipment, including build volume, accuracy, and repeatability. Providers with industry-leading equipment, like Metal3DP’s printers that offer industry-leading print volume, accuracy and reliability, are better positioned to handle demanding automotive applications.
- Quality Assurance and Certifications: Verify if the provider has robust quality management systems in place and holds relevant certifications (e.g., ISO 9001, AS9100 for aerospace). This ensures that their processes are controlled and that the manufactured parts meet stringent quality standards.
- Design and Engineering Support: A valuable service provider will offer design for additive manufacturing (DfAM) expertise to help optimize your exhaust outlet design for the 3D printing process, potentially improving performance, reducing weight, and minimizing manufacturing costs.
- Post-Processing Capabilities: Determine if the provider offers the necessary post-processing services, such as support removal, heat treatment, CNC machining, and surface finishing, to deliver готовые to-use components. A comprehensive service offering can streamline the supply chain and ensure consistent quality.
- Experience in the Automotive Industry: Prior experience working with automotive clients and an understanding of the industry’s specific requirements and standards are significant advantages. Look for providers with a proven track record of delivering high-quality parts for automotive applications.
- Lead Times and Production Capacity: Discuss lead times for prototyping and production, as well as their capacity to handle your anticipated volumes. Ensure their timelines align with your project schedules.
- Cost Structure and Transparency: Obtain a clear understanding of their pricing model, including material costs, printing costs, and post-processing charges. A transparent and competitive pricing structure is essential.
- Communication and Customer Support: Evaluate the provider’s responsiveness, communication effectiveness, and overall customer support. A collaborative partner who is readily available to address your questions and concerns is crucial for a successful project.
By carefully considering these factors, you can select a metal 3D printing service provider that is well-equipped to meet the specific needs of your automotive exhaust outlet project.
Cost Analysis and Lead Time for 3D Printed Exhaust Outlet Production
Understanding the cost factors and lead times associated with metal 3D printing is essential for automotive engineers and procurement managers. Here’s a breakdown of the key considerations:
コスト要因:
- 材料費: The cost of metal powders varies significantly depending on the alloy and supplier. High-performance alloys like IN625 tend to be more expensive than standard stainless steels like 17-4PH. The quantity of material used per part also directly impacts the cost.
- Printing Costs: Printing costs are influenced by factors such as build time, machine utilization, and energy consumption. Complex geometries or large build volumes will typically result in higher printing costs.
- 後処理費用: The extent of post-processing required (e.g., support removal, heat treatment, machining, surface finishing, coating) will add to the overall cost. Complex post-processing steps will increase the final price.
- Design and Engineering Costs: If you require design optimization or engineering support from the service provider, these services will also factor into the total cost.
- Tooling Costs (vs. Traditional Methods): While metal 3D printing generally eliminates the need for expensive hard tooling, there may be costs associated with design for additive manufacturing and build preparation. For low to medium volumes, the absence of tooling costs often makes 3D printing more economical than traditional methods.
- 規模の経済: The cost per part in metal 3D printing can decrease with increasing production volumes, but the cost savings may not be as significant as in high-volume traditional manufacturing processes like injection molding or die casting.
リードタイム:
- プロトタイピング: Metal 3D printing offers significantly shorter lead times for prototyping compared to traditional methods that require tooling. Prototypes can often be produced within days or weeks, allowing for rapid design iteration.
- 少量生産: For low to medium production volumes, lead times for 3D printed exhaust outlets are typically shorter than those for traditional manufacturing, as there is no need to wait for tooling fabrication.
- 大量生産: Lead times for high-volume production using metal 3D printing can be longer than traditional methods due to the layer-by-layer build process. However, advancements in printing speed and automation are continuously improving production throughput.
- Post-Processing Time: The time required for post-processing steps can also impact the overall lead time. Complex post-processing requirements will extend the delivery schedule.
- 材料の入手可能性: Lead times for specific metal powders can vary depending on the supplier and alloy. Ensuring the chosen material is readily available is important for minimizing delays.
Understanding these cost and lead time factors will enable automotive manufacturers to make informed decisions about whether metal 3D printing is the right solution for their exhaust outlet needs and to effectively plan their production schedules and budgets.
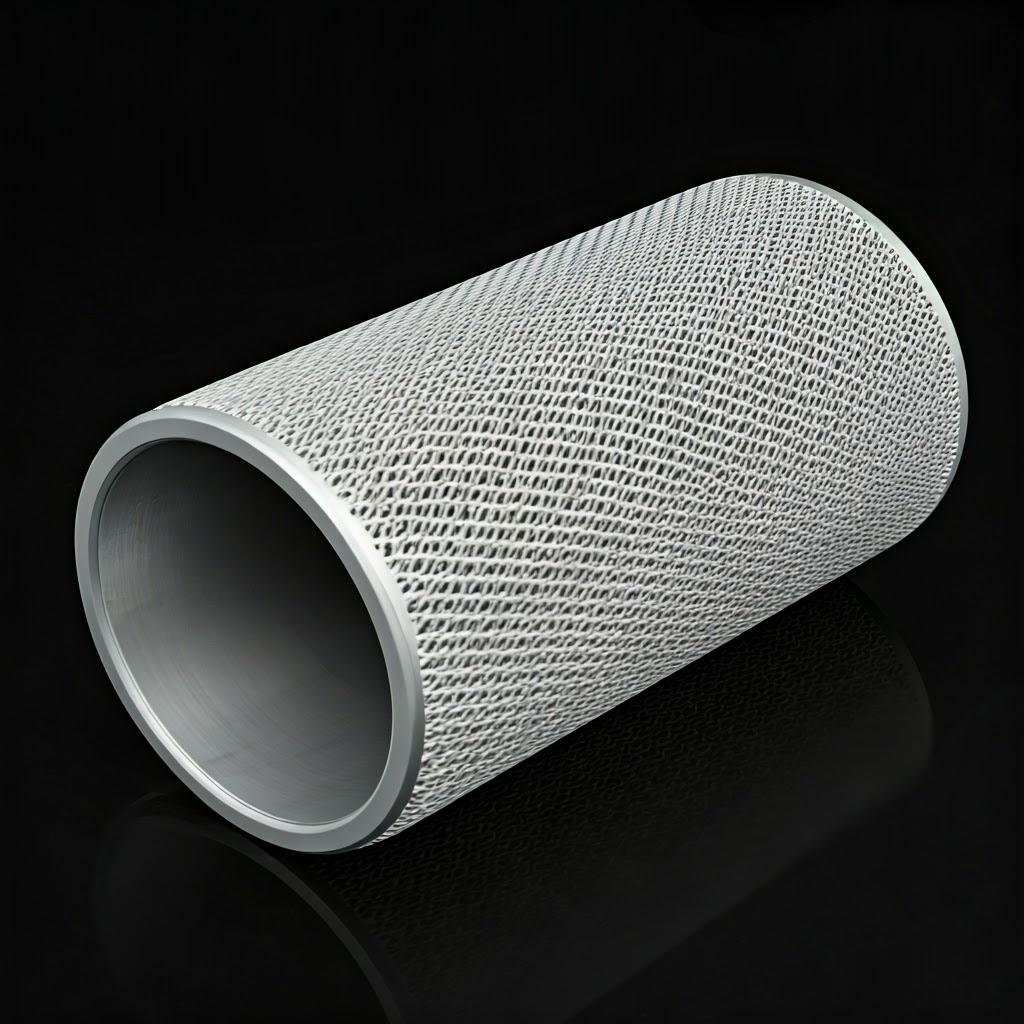
よくある質問(FAQ)
- Q: Can metal 3D printed exhaust outlets withstand high temperatures?
- A: Yes, with the appropriate material selection, such as IN625, metal 3D printed exhaust outlets can withstand the high temperatures encountered in automotive exhaust systems. The material’s high-temperature strength and creep resistance are crucial factors.
- Q: Are metal 3D printed exhaust outlets as durable as traditionally manufactured ones?
- A: When produced using high-quality metal powders and optimized printing parameters, metal 3D printed exhaust outlets can achieve comparable or even superior durability to traditionally manufactured parts. Factors like material density, mechanical properties achieved through post-processing (e.g., heat treatment), and proper design for the application are essential.
- Q: What is the typical size limitation for 3D printed exhaust outlets?
- A: The maximum size of a 3D printed exhaust outlet is primarily limited by the build volume of the metal 3D printer. Metal3DP offers printers with industry-leading print volume, allowing for the production of relatively large automotive components. However, very large parts may need to be printed in sections and then joined.
- Q: Can complex internal geometries be achieved in 3D printed exhaust outlets?
- A: Absolutely. One of the key advantages of metal 3D printing is the ability to create intricate internal channels and geometries that are difficult or impossible to achieve with traditional manufacturing methods. This allows for optimized exhaust flow and integrated features.
- Q: Is metal 3D printing cost-effective for mass production of exhaust outlets?
- A: While metal 3D printing is highly cost-effective for prototyping and low to medium volume production, traditional high-volume manufacturing methods like stamping and welding may still be more economical for very large production runs of simpler designs. However, for complex, customized, or low-volume applications, metal 3D printing offers significant cost advantages.
Conclusion: The Future of Automotive Exhaust Outlets with Metal 3D Printing
Metal 3D printing is rapidly transforming the landscape of automotive component manufacturing, and exhaust outlets are no exception. The technology offers a compelling combination of design freedom, material flexibility, and the potential for enhanced performance that traditional manufacturing methods often cannot match. From optimizing exhaust flow and reducing weight to enabling part consolidation and customization, the benefits of metal 3D printing are increasingly evident for automotive engineers and procurement managers.
Companies like Metal3DP Technology Co., LTD are at the forefront of this revolution, providing advanced 3D printing equipment and high-quality metal powders that empower automotive manufacturers to innovate and create next-generation exhaust systems. As the technology continues to mature and costs become more competitive, we can expect to see even wider adoption of metal 3D printed exhaust outlets across various automotive applications, driving improvements in performance, efficiency, and design innovation. Embracing metal additive manufacturing is no longer just an option; it’s becoming a strategic imperative for automotive companies looking to stay ahead in a rapidly evolving industry. Contact メタル3DP today to explore how their capabilities can power your organization’s additive manufacturing goals.
シェアする
MET3DP Technology Co., LTDは、中国青島に本社を置く積層造形ソリューションのリーディングプロバイダーです。弊社は3Dプリンティング装置と工業用途の高性能金属粉末を専門としています。
関連記事
Met3DPについて
最新情報
製品
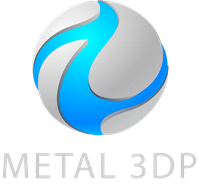
3Dプリンティングと積層造形用金属粉末