3D Printed Chassis Nodes for EVs: Revolutionizing Electric Vehicle Manufacturing
目次
はじめに
The electric vehicle (EV) industry is at the forefront of innovation, constantly seeking lighter, stronger, and more efficient components to enhance vehicle performance, range, and sustainability. Among these critical components, the chassis node plays a vital role in connecting various structural elements, influencing the vehicle’s overall integrity and safety. Traditional manufacturing methods for chassis nodes often involve complex multi-step processes, significant material waste, and design limitations. However, metal additive manufacturing, commonly known as metal 3Dプリンティング, offers a transformative alternative. By directly building complex geometries layer by layer from metal powders, metal 3D printing unlocks unprecedented design freedom, reduces weight, and streamlines production. This blog post explores the significant advantages of utilizing metal 3D printing for the production of EV chassis nodes, highlighting the benefits for engineers and procurement managers in the automotive sector. At メタル3DP, we are dedicated to providing cutting-edge metal additive manufacturing solutions, including advanced 3D printing equipment and high-performance metal powders, empowering the EV industry to push the boundaries of innovation.
What are EV Chassis Nodes Used For?
Chassis nodes in electric vehicles serve as critical junction points, connecting essential structural components such as suspension mounts, battery housings, motor mounts, and frame rails. These nodes bear substantial loads and stresses during vehicle operation, directly impacting the EV’s safety, handling, and overall performance. Their primary functions include:
- Load Distribution: Evenly distributing forces across the vehicle’s structure, ensuring stability and preventing stress concentration in specific areas.
- Component Integration: Providing robust and precise mounting points for various subsystems, ensuring their secure attachment and alignment.
- NVH (Noise, Vibration, and Harshness) Reduction: Optimizing the design to minimize the transmission of vibrations and noise into the cabin, enhancing passenger comfort.
- Crash Safety: Playing a crucial role in the vehicle’s crash structure, absorbing and dissipating impact energy to protect occupants.
- Weight Optimization: Efficiently connecting structural elements while minimizing overall weight, contributing to improved energy efficiency and range in EVs.
The complexity of these functions necessitates intricate designs that can be challenging and costly to produce using conventional manufacturing techniques. Metal 3D printing offers the flexibility to create highly optimized geometries tailored to specific load requirements and integration needs, paving the way for lighter and more efficient EV chassis designs. To learn more about the applications of metal 3D printing in various industries, visit our 金属 3D プリント ページ.
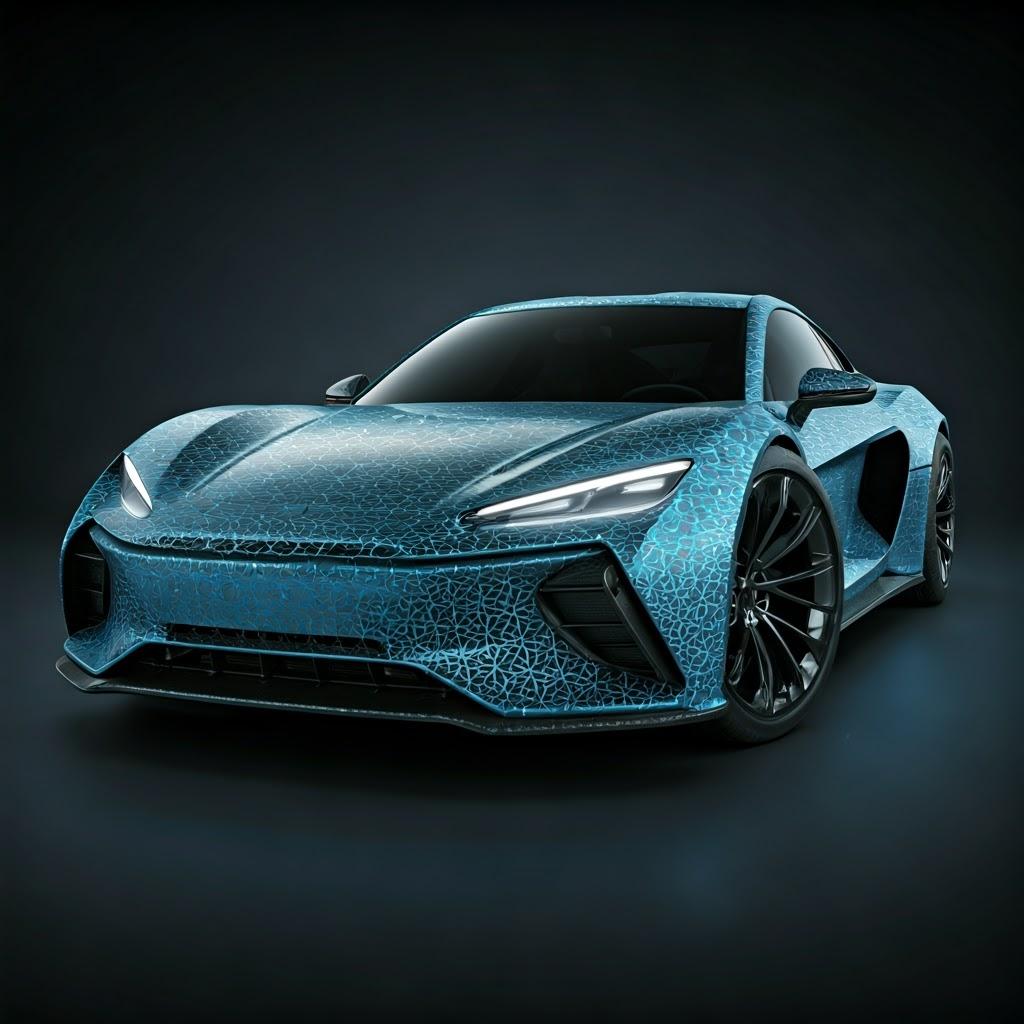
Why Use Metal 3D Printing for EV Chassis Nodes?
Adopting metal 3D printing for the manufacturing of EV chassis nodes presents a compelling array of advantages over traditional methods like casting, forging, or machining:
- Design Freedom and Topology Optimization: Metal 3D printing allows for the creation of complex internal lattices, intricate geometries, and optimized shapes that are simply not achievable with conventional manufacturing. This enables engineers to design chassis nodes with precisely the right amount of material where it’s needed, reducing weight without compromising structural integrity. Topology optimization algorithms, in conjunction with additive manufacturing, can lead to significant weight savings and improved performance.
- 軽量化: In the EV industry, every kilogram counts. Lighter vehicles translate directly to increased range and improved energy efficiency. Metal 3D printed chassis nodes, with their optimized designs and potential for hollow structures or lattice infills, can significantly reduce the weight of the chassis system compared to traditionally manufactured parts.
- パーツの統合: Metal 3D printing enables the consolidation of multiple components into a single, integrated part. This reduces the number of assembly steps, fasteners, and potential failure points, leading to lower manufacturing costs and improved reliability. A single 3D printed chassis node can incorporate features that would traditionally require several individual parts to be manufactured and joined.
- On-Demand Manufacturing and Reduced Lead Times: Traditional manufacturing processes often involve long lead times for tooling and setup. Metal 3D printing eliminates the need for complex tooling, allowing for rapid prototyping and on-demand production of chassis nodes. This agility is particularly valuable in the fast-paced EV industry, where design iterations and time-to-market are critical.
- Material Efficiency and Waste Reduction: Additive manufacturing processes build parts layer by layer, using only the material required for the final geometry. This significantly reduces material waste compared to subtractive methods like machining, where a substantial portion of the raw material is removed.
- Customization and Design Iteration: Metal 3D printing facilitates rapid design iterations and the creation of customized chassis nodes for specific vehicle platforms or performance requirements. Engineers can quickly modify designs based on testing and simulation results, accelerating the development cycle.
- パフォーマンスの向上: The ability to optimize the geometry and material distribution of chassis nodes through metal 3D printing can lead to improved stiffness, strength-to-weight ratio, and crash performance. Internal lattice structures, for example, can provide excellent energy absorption characteristics.
で メタル3DP, our advanced Selective Electron Beam Melting (SEBM) printers are ideally suited for producing complex, high-performance metal parts like EV chassis nodes, offering exceptional accuracy and material properties.
Recommended Materials and Why They Matter
The choice of metal powder is paramount in determining the final properties and performance of 3D printed EV chassis nodes. メタル3DP offers a range of high-quality metal powders specifically designed for demanding automotive applications. For EV chassis nodes, two particularly relevant materials are AlSi10Mg and A7075:
- AlSi10Mg (Aluminum Silicon Magnesium):
- プロパティ This aluminum alloy offers an excellent combination of high strength-to-weight ratio, good thermal conductivity, and corrosion resistance. It exhibits good ductility and is readily weldable.
- Benefits for Chassis Nodes: Its lightweight nature contributes to overall vehicle weight reduction, enhancing energy efficiency. The good thermal conductivity can aid in heat dissipation in certain areas of the chassis. Its high strength ensures structural integrity under load.
- アプリケーション Ideal for structural components requiring high strength and low weight, such as suspension mounts and frame connections.
- Metal3DP Advantage: Our AlSi10Mg powder is produced using advanced gas atomization technology, resulting in spherical particles with high flowability and packing density, ensuring optimal print quality and mechanical properties on our SEBM printers.
- A7075 (Aluminum Zinc Magnesium Copper):
- プロパティ This is a high-strength aluminum alloy known for its exceptional strength-to-weight ratio, often used in aerospace applications. It offers superior strength compared to AlSi10Mg but may have lower corrosion resistance and weldability.
- Benefits for Chassis Nodes: Its very high strength allows for the creation of lightweight components that can withstand significant loads, crucial for safety-critical areas of the chassis.
- アプリケーション Suitable for highly stressed nodes where maximum strength is paramount, such as critical suspension linkages or impact zones.
- Metal3DP Advantage: メタル3DP‘s A7075 powder is manufactured with precise control over particle size distribution and chemistry, ensuring consistent and reliable printing outcomes with our advanced powder bed fusion technology.
The selection between AlSi10Mg and A7075 will depend on the specific performance requirements of the chassis node, considering factors such as load-bearing capacity, weight targets, and environmental conditions. Our team at メタル3DP can provide expert guidance on material selection to optimize your EV chassis node design. We utilize industry-leading gas atomization and PREP technologies to ensure the highest quality of our 高品質の金属粉. Sources and related content
Design Considerations for Additive Manufacturing of EV Chassis Nodes
Designing EV chassis nodes for metal 3D printing requires a different mindset compared to traditional manufacturing. To fully leverage the capabilities of additive manufacturing, engineers must consider several key design principles:
- Topology Optimization: Employing sophisticated software tools to optimize the material distribution based on applied loads and constraints. This process identifies areas where material can be removed without compromising structural integrity, leading to significant weight reductions and improved performance. The organic, often counter-intuitive shapes resulting from topology optimization are readily achievable with metal 3D printing.
- 格子構造: Incorporating internal lattice structures within the chassis node can provide excellent strength-to-weight ratios and energy absorption capabilities. Different lattice patterns, such as gyroid, cubic, or diamond, offer varying mechanical properties and can be tailored to specific load requirements. These intricate internal geometries are a hallmark of additive manufacturing.
- パーツの統合: Designing multiple traditionally manufactured components as a single 3D printed part. This reduces assembly time, the number of fasteners required, and potential failure points. Features like integrated mounting brackets, channels for wiring or cooling, and complex internal flow paths can be incorporated seamlessly into a single design.
- Orientation and Support Structures: Carefully considering the build orientation during the 3D printing process is crucial for minimizing support structures, optimizing surface finish, and ensuring dimensional accuracy. Support structures are temporary elements needed to prevent overhangs and collapsing features during printing. Their removal requires post-processing and can impact surface quality. Intelligent design can minimize the need for extensive support.
- Wall Thickness and Feature Size: Adhering to the minimum feature sizes and wall thicknesses achievable with the chosen metal powder and printing process is essential for manufacturability. These parameters are influenced by the powder particle size, laser or electron beam spot size, and layer thickness. メタル3DP provides detailed design guidelines for each of our metal powders and printing systems.
- Surface Finish Considerations: Designing with the as-printed surface finish in mind. While post-processing techniques like machining or polishing can improve surface roughness, incorporating features that minimize the need for extensive finishing can reduce manufacturing costs and lead times.
- 熱管理: Integrating cooling channels or heat dissipation features directly into the chassis node design. The geometric freedom of metal 3D printing allows for the creation of complex internal channels that can efficiently manage heat generated by nearby components like batteries or motors.
By embracing these design considerations, engineers can unlock the full potential of metal 3D printing to create innovative, high-performance EV chassis nodes. Our team at メタル3DP offers comprehensive application development services to assist customers in optimizing their designs for additive manufacturing.
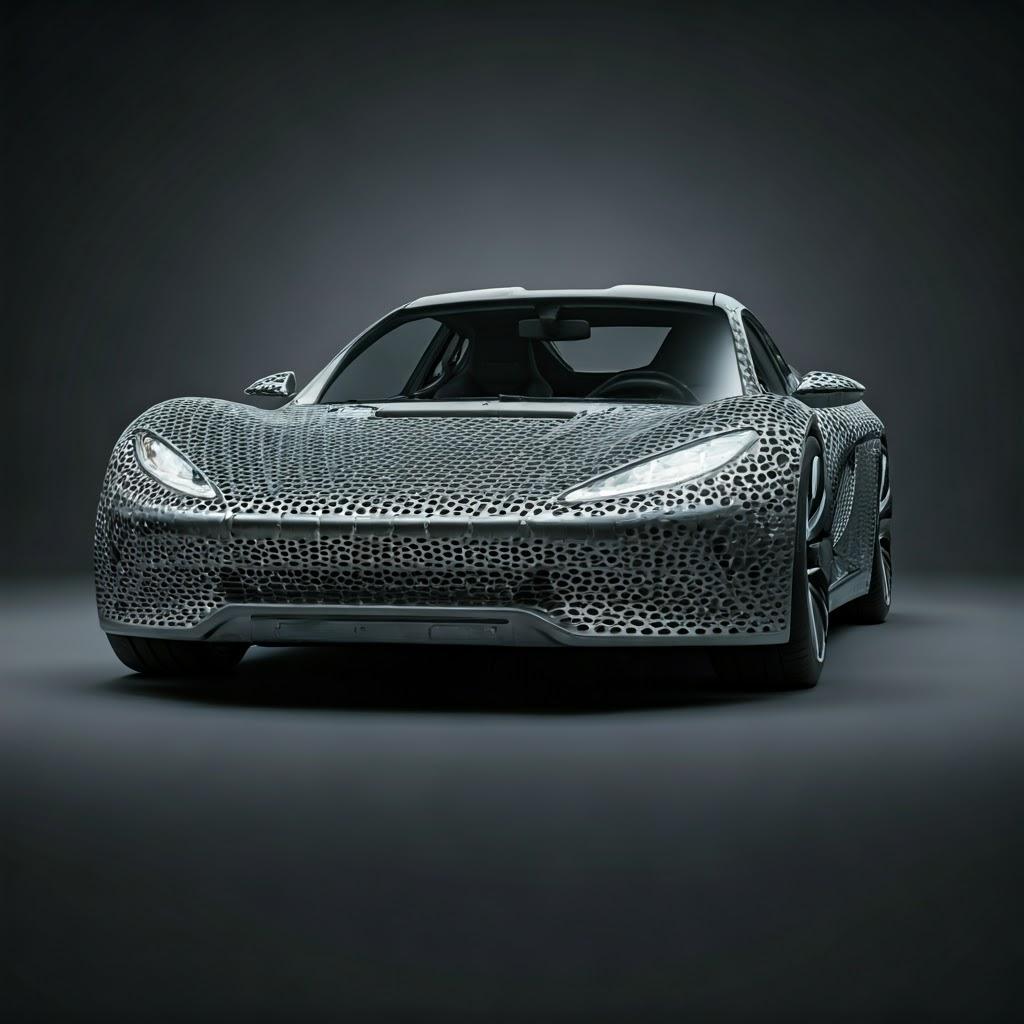
Tolerance, Surface Finish, and Dimensional Accuracy of 3D Printed Chassis Nodes
Achieving the required tolerance, surface finish, and dimensional accuracy is paramount for the functional integration and performance of EV chassis nodes. Metal 3D printing technologies have made significant advancements in these areas:
- Tolerance: The dimensional accuracy achievable with metal 3D printing depends on several factors, including the printing technology (e.g., SEBM, DMLS), the material used, the part geometry, and the build parameters. Generally, tolerances in the range of ±0.1 to ±0.2 mm can be achieved for critical dimensions. For higher precision requirements, post-processing steps like CNC machining can be employed to achieve tighter tolerances down to a few micrometers. メタル3DP‘s advanced printing systems are engineered for high accuracy and repeatability.
- 表面仕上げ: The as-printed surface finish in metal 3D printing is typically rougher than that achieved by machining or casting. The surface roughness (Ra) can range from 5 to 20 μm, depending on the printing process and material. For applications requiring smoother surfaces, various post-processing techniques such as abrasive blasting, polishing, or chemical etching can be applied. Careful part orientation during printing can also influence the surface finish of critical areas.
- 寸法精度: Dimensional accuracy refers to the ability of the 3D printed part to match the intended design dimensions. Factors affecting accuracy include thermal shrinkage during solidification, powder bed uniformity, and machine calibration. Advanced control systems and precise process parameters in メタル3DP‘s printers ensure high dimensional accuracy and consistency across multiple builds.
特徴 | Typical Achievable Range (As-Printed) | Potential with Post-Processing | Contributing Factors |
---|---|---|---|
寸法公差 | ±0.1−0.2 mm | ±0.01−0.05 mm | Printer accuracy, material shrinkage, build orientation, post-processing methods |
表面粗さ(Ra) | 5 – 20 μm | 0.1 - 1 μm | Printing process, layer thickness, powder size, post-processing techniques |
最小フィーチャーサイズ | 0.2 – 0.5 mm | 該当なし | Printing technology, material properties |
Export to Sheets
Understanding these capabilities and limitations is crucial for designing functional EV chassis nodes that meet the required specifications. Collaboration with an experienced metal 3D printing service provider like メタル3DP ensures that the chosen printing process and post-processing steps are optimized to achieve the desired tolerance, surface finish, and dimensional accuracy for your application.
Post-Processing Requirements for 3D Printed EV Chassis Nodes
While metal 3D printing offers significant advantages in creating complex geometries, post-processing is often necessary to achieve the final desired properties and finish for EV chassis nodes. Common post-processing steps include:
- 支持構造の撤去: Support structures, which are essential during the printing process to prevent collapse and ensure proper formation of overhangs, need to be carefully removed after printing. This can be done manually using tools or through automated processes like machining or dissolution, depending on the support material and part geometry.
- 熱処理: Heat treatment is often required to relieve internal stresses built up during the rapid solidification process of 3D printing and to achieve the desired mechanical properties of the material, such as hardness and tensile strength. The specific heat treatment cycle depends on the metal alloy used.
- 表面仕上げ: As mentioned earlier, various surface finishing techniques can be employed to improve the surface roughness of 3D printed parts. These include abrasive blasting, which uses fine media to remove surface imperfections; polishing, for achieving smoother surfaces; and chemical etching, which selectively removes material to improve surface finish.
- CNC Machining: For critical surfaces requiring very tight tolerances or specific geometric features that are difficult to achieve directly with 3D printing, CNC machining can be used as a secondary process. This hybrid manufacturing approach combines the design freedom of additive manufacturing with the precision of subtractive manufacturing.
- Coating and Surface Treatments: Depending on the application environment, coatings or surface treatments may be applied to enhance corrosion resistance, wear resistance, or other functional properties of the chassis node. Examples include anodizing for aluminum alloys or protective paints.
- Inspection and Quality Control: Thorough inspection using techniques like coordinate measuring machines (CMM), non-destructive testing (NDT), and material testing is crucial to ensure that the 3D printed chassis nodes meet the required dimensional accuracy, material integrity, and performance specifications.
The specific post-processing requirements for an EV chassis node will depend on the design, the chosen metal powder, and the intended application. Consulting with an experienced metal 3D printing service provider like メタル3DP is essential to determine the optimal post-processing workflow to achieve the desired results efficiently and cost-effectively. Our comprehensive solutions span from material selection to final part finishing, ensuring high-quality components for your EV applications.
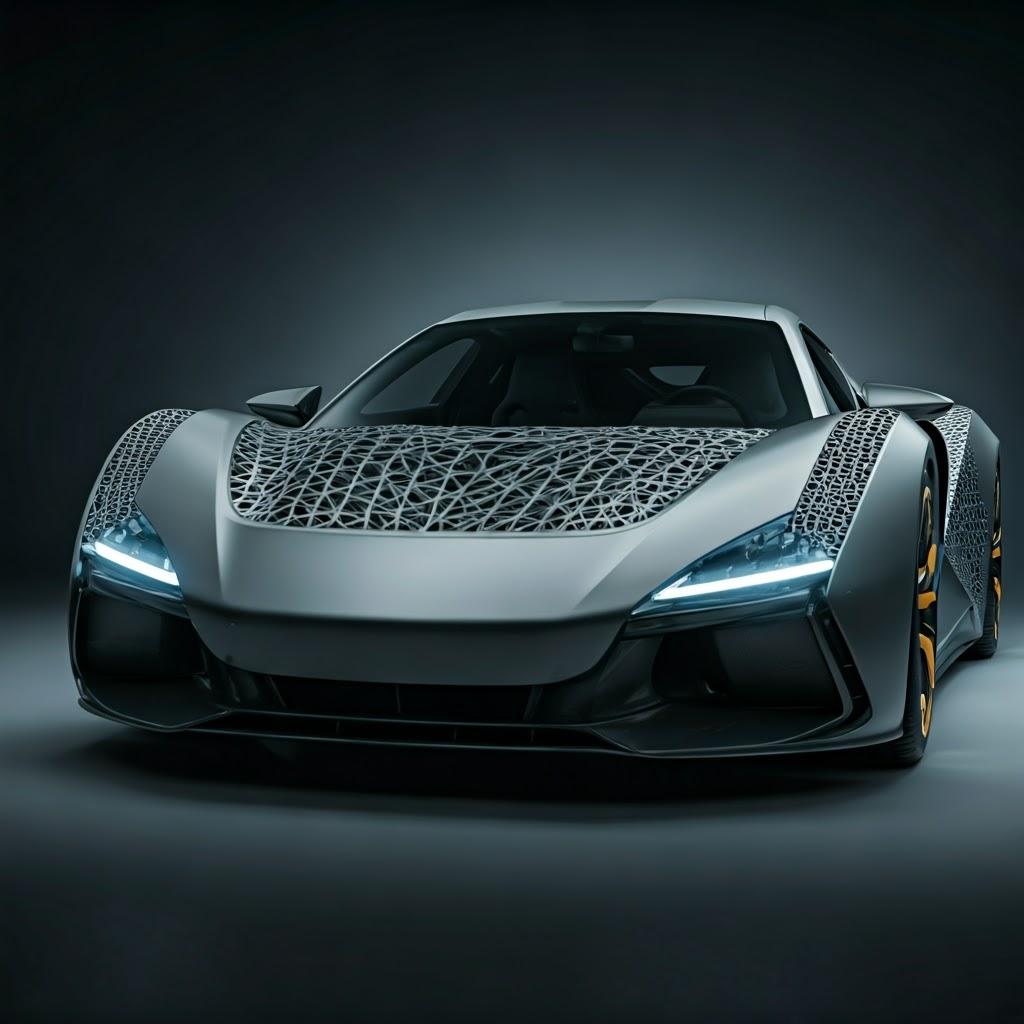
Common Challenges and How to Avoid Them in 3D Printing EV Chassis Nodes
While metal 3D printing offers numerous benefits, certain challenges can arise during the process. Understanding these potential issues and implementing preventative measures is crucial for successful production of EV chassis nodes:
- Warping and Distortion: Thermal stresses during the printing process can lead to warping or distortion of the part, especially for large or complex geometries.
- How to Avoid: Optimize part orientation, use appropriate support structures, control build chamber temperature, and consider stress-relieving heat treatments.
- 多孔性: Internal voids or pores within the printed part can compromise its mechanical strength and fatigue life.
- How to Avoid: Optimize printing parameters such as laser power, scan speed, and layer thickness. Ensure high-quality metal powder with good flowability and packing density. メタル3DP‘s advanced powder making system minimizes porosity in our materials.
- Support Removal Issues: Removing support structures can sometimes leave surface blemishes or even damage delicate features of the part.
- How to Avoid: Design parts with self-supporting angles where possible, optimize support structure design for easy removal, and utilize dissolvable support materials when appropriate.
- Surface Finish Limitations: Achieving a smooth surface finish directly from the 3D printing process can be challenging.
- How to Avoid: Consider the intended surface finish requirements during the design phase and plan for appropriate post-processing techniques like abrasive blasting or machining.
- Material Property Variability: Inconsistent material properties throughout the printed part can occur if the printing process is not well-controlled.
- How to Avoid: Work with a reputable metal 3D printing service provider like メタル3DP that has stringent quality control measures and optimized printing parameters for each material. Our industry-leading print volume, accuracy, and reliability ensure consistent material properties.
- コストを考慮する: While metal 3D printing can be cost-effective for certain applications, the initial investment and per-part costs can be higher than traditional methods for large production volumes or simple geometries.
- How to Avoid: Carefully evaluate the total cost of ownership, considering factors like design complexity, material usage, post-processing requirements, and production volume. Part consolidation and weight reduction can often offset higher per-part costs.
By proactively addressing these potential challenges through careful design, optimized printing parameters, and appropriate post-processing, manufacturers can successfully leverage metal 3D printing to produce high-quality EV chassis nodes.
How to Choose the Right Metal 3D Printing Service Provider for EV Chassis Nodes
Selecting the right metal 3D printing service provider is crucial for the successful production of high-performance EV chassis nodes. Consider the following factors when evaluating potential suppliers:
- Material Capabilities: Ensure the provider offers the specific metal powders required for your application, such as AlSi10Mg and A7075. Verify the quality and traceability of their materials. メタル3DP manufactures a wide range of high-quality metal powders optimized for various applications.
- 印刷技術: Understand the types of metal 3D printing technologies the provider utilizes (e.g., DMLS, SLM, EBM). Each technology has its own strengths and limitations in terms of build volume, accuracy, and material compatibility. Our company specializes in SEBM printers, offering industry-leading print volume, accuracy, and reliability. You can learn more about printing methods here.
- Equipment and Expertise: Assess the provider’s equipment capabilities, including build volume and precision. Evaluate their team’s expertise in design for additive manufacturing, material science, and post-processing. メタル3DP boasts decades of collective expertise in metal additive manufacturing.
- Quality Control and Certifications: Inquire about the provider’s quality control processes, inspection methods, and relevant industry certifications (e.g., ISO 9001, AS9100 for aerospace). Robust quality assurance is essential for critical automotive components.
- Post-Processing Services: Determine if the provider offers the necessary post-processing services, such as heat treatment, surface finishing, and CNC machining, to meet your requirements. A comprehensive service offering can streamline the production process.
- Lead Times and Production Capacity: Discuss lead times for prototyping and production, as well as the provider’s capacity to handle your anticipated volumes.
- Communication and Support: Evaluate the provider’s responsiveness, communication clarity, and technical support capabilities. A collaborative partner can significantly contribute to the success of your project.
- Cost Structure: Understand the provider’s pricing model, including material costs, printing fees, and post-processing charges. Obtain detailed quotes and compare them carefully.
By carefully evaluating these factors, you can select a metal 3D printing service provider that aligns with your specific needs and ensures the delivery of high-quality EV chassis nodes. Metal3DPへのお問い合わせ to explore how our capabilities can power your organization’s additive manufacturing goals.
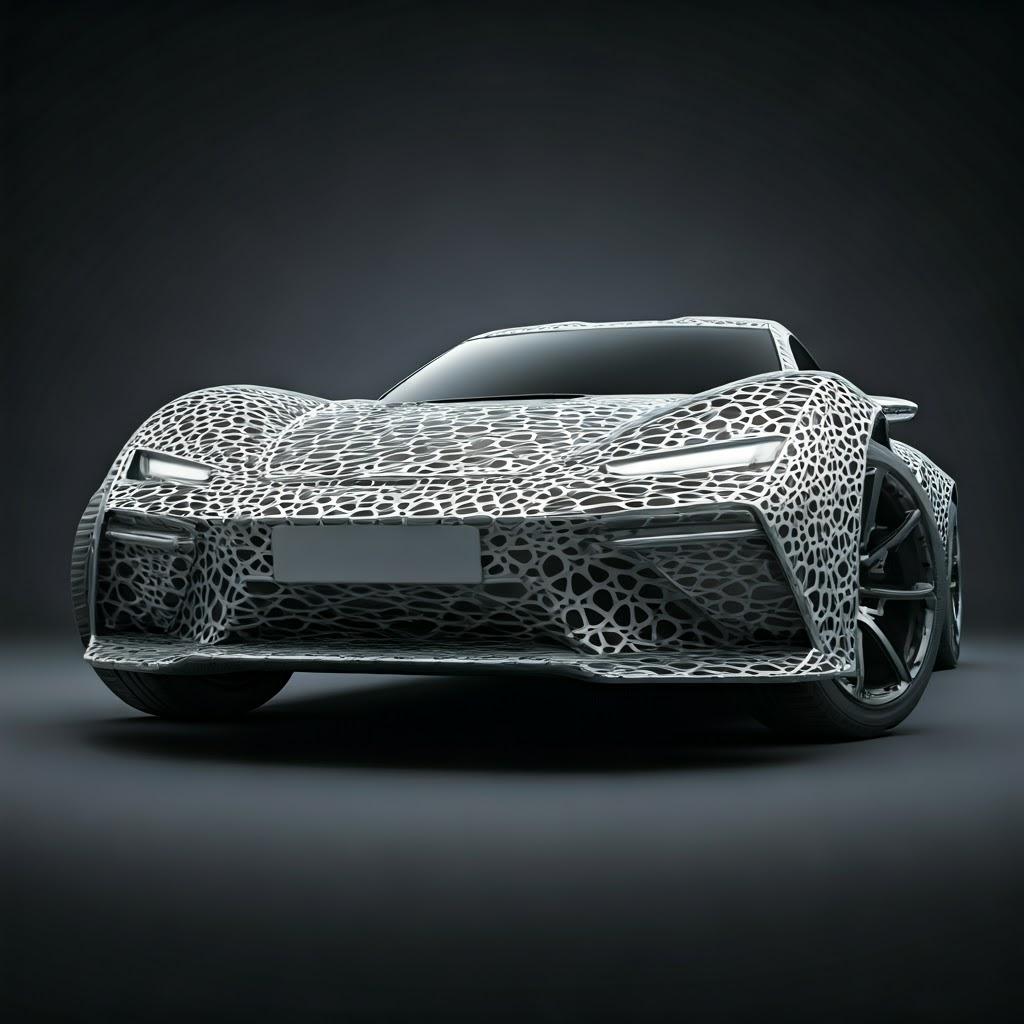
Cost Factors and Lead Time for 3D Printed EV Chassis Nodes
The cost and lead time for producing EV chassis nodes using metal 3D printing are influenced by several factors:
- Part Complexity and Volume: More complex designs and larger production volumes generally lead to higher overall costs. However, for low to medium volumes of complex parts, metal 3D printing can be more cost-effective than traditional methods due to the elimination of tooling costs.
- Material Selection and Usage: The cost of the metal powder varies depending on the alloy. The amount of material used, which is influenced by the part’s design and the need for support structures, also impacts the overall cost. Topology optimization and efficient design can minimize material usage.
- ビルドタイム: The time it takes to print a chassis node depends on its size, complexity, and the chosen printing technology. Longer build times translate to higher machine operating costs.
- 後処理の要件: The extent of post-processing required (e.g., support removal, heat treatment, surface finishing, machining) significantly affects both the cost and the lead time. Minimizing the need for extensive post-processing through design optimization can reduce both.
- Equipment and Labor Costs: The cost of operating and maintaining the metal 3D printing equipment, as well as the labor involved in design, printing, and post-processing, are factored into the overall price.
- Service Provider’s Pricing Structure: Different service providers have varying pricing models. It’s essential to obtain detailed quotes and understand all the associated costs.
リードタイム: The lead time for metal 3D printed EV chassis nodes can range from a few days for prototypes to several weeks for larger production runs, depending on the complexity of the part, the printing technology used, the availability of materials, and the post-processing requirements. One of the key advantages of metal 3D printing is the potential for significantly shorter lead times compared to traditional manufacturing processes that require tooling.
Cost/Lead Time Factor | インパクト | 緩和戦略 |
---|---|---|
部品の複雑さ | Higher cost and longer lead time for intricate designs | Design for additive manufacturing principles, part consolidation |
生産量 | Lower per-part cost for higher volumes (up to a certain point) | Evaluate break-even points compared to traditional manufacturing |
Material Type & Usage | Higher cost for specialized alloys; more material used increases cost | Topology optimization, lattice structures, efficient design |
Build Time | Longer print times increase machine costs | Optimize part orientation, consider using multiple printers for larger volumes |
後処理の必要性 | Adds cost and time | Design to minimize supports, select appropriate surface finish requirements |
Service Provider Factors | Pricing structure, equipment availability, expertise | Thoroughly vet potential providers, obtain detailed quotes |
Export to Sheets
Understanding these cost and lead time factors is crucial for making informed decisions about utilizing metal 3D printing for your EV chassis node applications. メタル3DP is committed to providing transparent cost structures and efficient lead times for our high-quality metal 3D printing services.
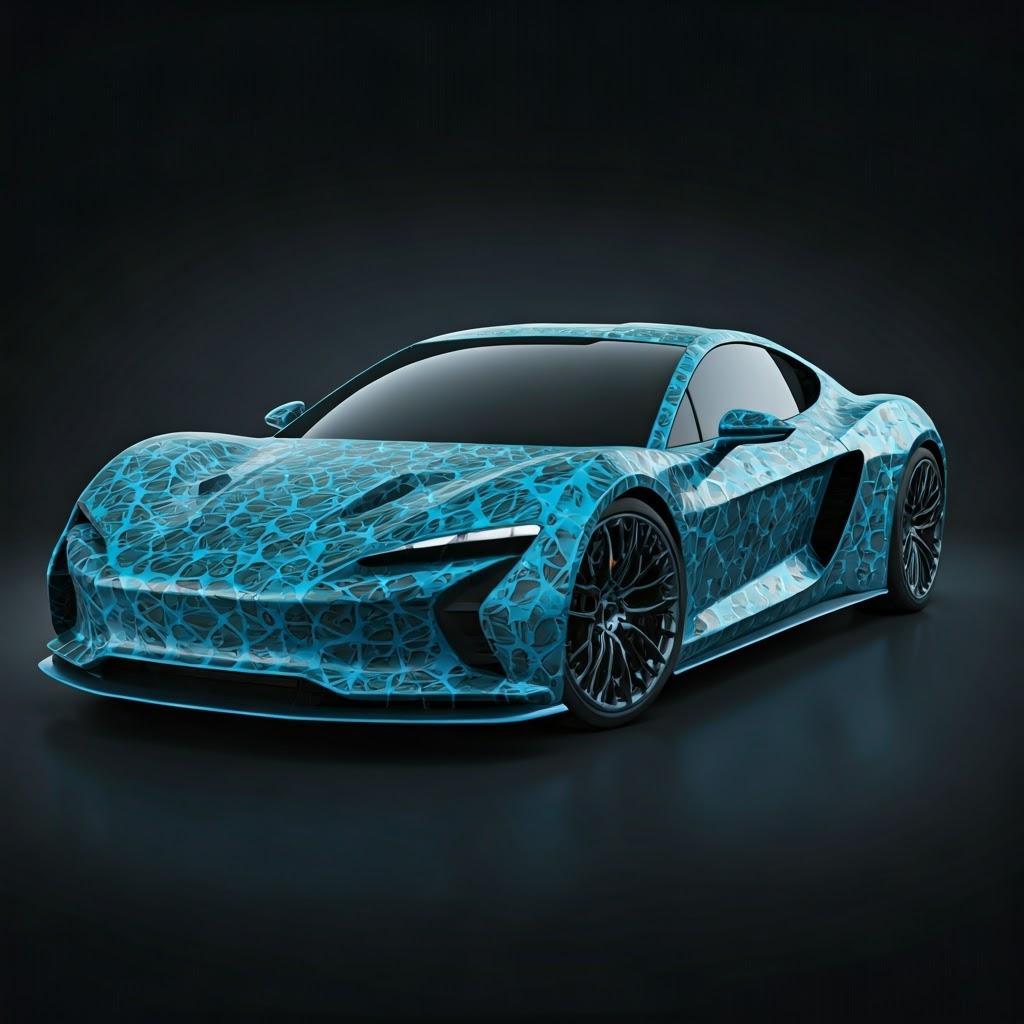
よくある質問(FAQ)
- What are the typical weight savings achievable by using 3D printed chassis nodes compared to traditionally manufactured ones? Weight savings can vary significantly depending on the specific design and the extent of topology optimization, but reductions of 20-50% are often achievable.
- Is metal 3D printing cost-effective for mass production of EV chassis nodes? For very high production volumes of simple geometries, traditional methods might still be more cost-effective. However, for complex designs, part consolidation, and low to medium volumes, metal 3D printing can offer cost advantages due to reduced tooling costs and assembly. The total cost of ownership, including potential weight savings and performance improvements, should be considered.
- What are the limitations of using metal 3D printing for EV chassis nodes? Current limitations include build volume constraints for very large parts, surface finish requirements for certain applications, and the need for specialized expertise in design and post-processing. However, the technology is rapidly evolving, with larger build volumes and improved surface finishes becoming increasingly common.
結論
Metal 3D printing presents a paradigm shift in the design and manufacturing of EV chassis nodes. Its ability to enable complex geometries, reduce weight, consolidate parts, and accelerate development cycles offers significant advantages for the electric vehicle industry. By leveraging advanced metal powders like AlSi10Mg and A7075 and partnering with experienced providers like メタル3DP, automotive engineers and procurement managers can unlock new levels of performance, efficiency, and innovation in their EV platforms. Embracing metal additive manufacturing is not just about replacing traditional methods; it’s about reimagining what’s possible in the pursuit of lighter, safer, and more sustainable electric vehicles. We at メタル3DP are proud to be at the forefront of this revolution, providing the cutting-edge systems and materials to drive the future of EV manufacturing.
シェアする
MET3DP Technology Co., LTDは、中国青島に本社を置く積層造形ソリューションのリーディングプロバイダーです。弊社は3Dプリンティング装置と工業用途の高性能金属粉末を専門としています。
関連記事
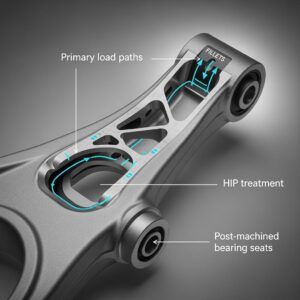