Custom Heat Transfer Plates
目次
Introduction – The Power of Customization in Heat Transfer with Metal 3D Printing
In the realm of thermal management, efficiency and adaptability are paramount. Industries ranging from aerospace and automotive to electronics and medical devices constantly seek innovative solutions to optimize heat exchange processes. Traditional manufacturing methods for heat transfer plates often impose limitations on design complexity and material choices, hindering the ability to achieve peak performance and tailor solutions to specific application needs. Enter metal 3D printing, a transformative technology that unlocks unprecedented possibilities for creating custom heat transfer plates. This advanced manufacturing approach, also known as metal additive manufacturing, empowers engineers and procurement managers to design and produce intricate geometries with optimized thermal properties, using high-performance materials like CuCrZr and pure copper. By eliminating the constraints of conventional manufacturing, metal 3Dプリンティング facilitates the creation of bespoke heat exchanger components that can significantly enhance the efficiency, lifespan, and overall performance of critical systems. At メタル3DPテクノロジー株式会社, we are at the forefront of this revolution, providing cutting-edge metal 3D printing equipment and a comprehensive portfolio of high-quality metal powders, including those ideal for heat transfer applications. Our commitment to industry-leading print volume, accuracy, and reliability ensures that our customers can realize the full potential of additive manufacturing for thermal management solutions.
What are Custom Heat Transfer Plates Used For? – Diverse Applications Across Industries
Custom heat transfer plates, manufactured through the versatility of metal 3D printing, serve a multitude of critical functions across a wide spectrum of industries. Their ability to be precisely tailored to specific requirements makes them indispensable components in various thermal management systems. Here are some key application areas:
- 航空宇宙 In aerospace, efficient heat dissipation is crucial for the performance and safety of aircraft and spacecraft. Custom heat transfer plates are used in:
- Electronics cooling: Managing the thermal loads of sensitive avionics and control systems.
- Engine cooling: Optimizing heat transfer in engine components to improve efficiency and longevity.
- Actuator thermal management: Ensuring reliable operation of hydraulic and electromechanical actuators under varying thermal conditions.
- 自動車: The automotive industry relies heavily on effective heat management for engine cooling, battery thermal management in electric vehicles, and power electronics cooling. Metal 3D printed heat transfer plates enable:
- High-performance cooling solutions: Creating complex internal cooling channels within engine blocks and cylinder heads for optimized heat extraction.
- Battery thermal management systems: Designing intricate cooling plates for electric vehicle battery packs to maintain optimal operating temperatures and extend battery life.
- Cooling of power electronics: Managing the heat generated by inverters, converters, and other power electronic components.
- 医療機器 Precise temperature control is vital in many medical applications. Custom heat transfer plates are utilized in:
- 医療用画像機器: Cooling components in MRI, CT, and X-ray machines to ensure accurate and reliable operation.
- Laboratory equipment: Maintaining stable temperatures in thermal cyclers, PCR machines, and other analytical instruments.
- Patient cooling/warming systems: Designing custom heat exchangers for therapeutic temperature management.
- 産業製造: Numerous industrial processes generate significant amounts of heat that need to be efficiently managed. Metal 3D printed heat transfer plates find applications in:
- Cooling of molds and dies: Optimizing cycle times and improving part quality in injection molding and die-casting processes through conformal cooling channels.
- Heat exchangers for chemical processing: Creating corrosion-resistant and efficient heat exchangers tailored to specific chemical environments.
- Cooling of electronic components in industrial automation: Ensuring the reliable operation of PLCs, servo drives, and other industrial control systems.
- Electronics Cooling: With the increasing power density of electronic devices, effective cooling solutions are paramount. Custom heat transfer plates are used for:
- Cooling of CPUs and GPUs: Designing high-performance heat sinks and cold plates with optimized fin structures and flow paths.
- Thermal management of power supplies: Dissipating heat generated by high-power electronic components.
- LED cooling: Ensuring the longevity and performance of high-brightness LEDs through efficient heat extraction.
作成する能力 complex internal geometries そして conformally cooled surfaces through metal 3D printing allows for significant improvements in heat transfer efficiency and opens up new possibilities for designing innovative thermal management solutions across these diverse industries.
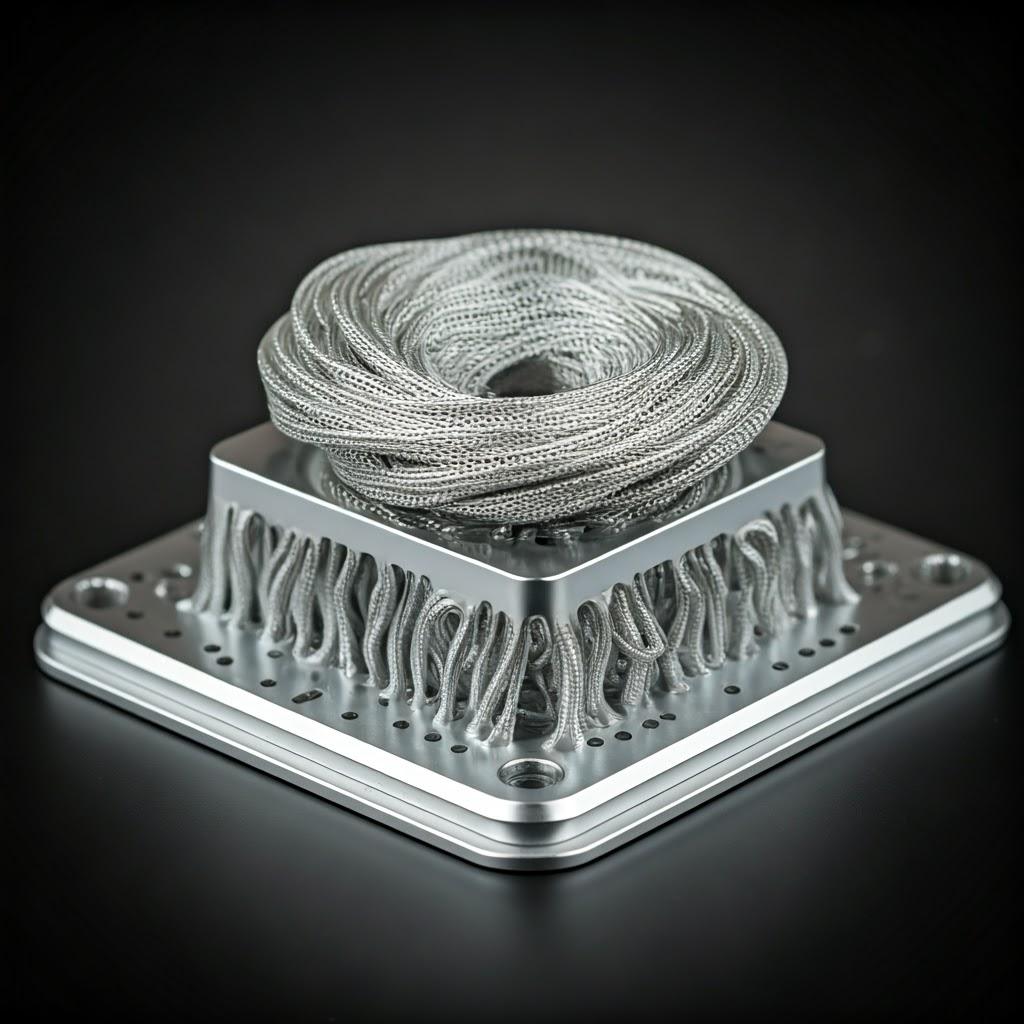
Why Choose Metal 3D Printing for Custom Heat Transfer Plates? – Advantages Over Traditional Methods
Opting for metal 3D printing to manufacture custom heat transfer plates offers a compelling array of advantages over traditional manufacturing techniques such as machining, casting, and brazing. These benefits translate to improved performance, enhanced design freedom, reduced costs in certain applications, and faster development cycles. Here’s a detailed look at the key advantages:
- デザインの自由と複雑さ: Metal 3D printing liberates engineers from the design constraints imposed by traditional methods. It enables the creation of:
- Intricate internal channels: Complex cooling pathways can be designed within the heat transfer plate to maximize surface area and optimize fluid flow for enhanced heat exchange efficiency. This includes features like lattice structures, gyroid infills, and conformal cooling channels that closely follow the contours of the heat-generating component.
- Customized geometries: Heat transfer plates can be tailored to fit specific spaces and integrate seamlessly with existing systems, regardless of their complexity. This is particularly beneficial in applications with limited space or unconventional shapes.
- Integrated features: Features like mounting points, flow distributors, and sensor housings can be directly incorporated into the design, reducing the need for secondary assembly processes and potential leak points.
- 素材の最適化: Metal 3D printing allows for the precise use of materials, placing them only where needed for functional performance. This can lead to:
- 軽量化: By optimizing the internal structure and eliminating unnecessary material, the weight of the heat transfer plate can be significantly reduced, which is crucial in aerospace and automotive applications.
- マルチマテリアル対応: While not always straightforward, some metal 3D printing technologies can potentially combine different metals within a single part, allowing for tailored thermal and mechanical properties in different regions of the heat transfer plate. Our range of high-quality metal powders supports diverse material requirements.
- パフォーマンスの向上: The design freedom and material optimization enabled by metal 3D printing directly translate to improved thermal performance:
- Increased heat transfer efficiency: Complex internal channels and optimized surface areas maximize the contact between the heat-generating component and the coolant, leading to more efficient heat dissipation.
- Improved temperature uniformity: Conformal cooling channels can provide more even temperature distribution across the surface of the heat transfer plate, preventing hot spots and improving the reliability of the cooled component.
- Reduced Assembly and Integration Costs: Integrating features and complex geometries into a single 3D printed part can eliminate the need for multiple components and assembly steps, leading to:
- Lower manufacturing costs: Reduced material waste, fewer manufacturing processes, and decreased labor can make metal 3D printing cost-competitive for complex or low-volume production runs.
- Simplified supply chain: Fewer parts to manage and procure streamline the supply chain.
- Improved reliability: Eliminating joints and fasteners reduces the risk of leaks and failures.
- Faster Prototyping and Development Cycles: Metal 3D printing enables rapid iteration and prototyping of heat transfer plate designs:
- Quick turnaround times: Prototypes can be produced in a fraction of the time compared to traditional methods, allowing for faster design validation and optimization.
- Easy design modifications: Changes to the design can be implemented quickly and printed without the need for new tooling or molds.
- Accelerated time-to-market: Faster prototyping and design cycles lead to quicker product development and market entry.
- Customization and Low-Volume Production: Metal 3D printing is particularly advantageous for producing highly customized heat transfer plates or for low-volume production runs where the cost of traditional tooling would be prohibitive. This allows for tailored solutions for niche applications or specialized equipment.
By leveraging the capabilities of metal 3D printing, companies can achieve significant advancements in the design, performance, and efficiency of their heat transfer systems. Contact Met3dp to explore how our metal AM solutions can benefit your specific application.
Recommended Materials and Why They Matter – Unleashing the Potential of CuCrZr and Cu Powders
The choice of material is paramount in determining the performance and reliability of a heat transfer plate. For custom applications leveraging metal 3D printing, CuCrZr (Copper-Chromium-Zirconium) そして pure Copper (Cu) stand out as excellent candidates due to their exceptional thermal properties. At Metal3DP, we offer high-quality powders of both these materials, specifically optimized for additive manufacturing processes. Let’s delve into why these materials are highly recommended:
1. Copper (Cu): The Gold Standard for Thermal Conductivity
- Exceptional Thermal Conductivity: Pure copper boasts one of the highest thermal conductivities among engineering metals (around 390-400 W/m·K). This means it can efficiently transfer heat away from the source, making it ideal for applications where rapid and effective heat dissipation is critical.
- 高い導電性: Copper also exhibits excellent electrical conductivity, which can be beneficial in applications where the heat transfer plate also serves an electrical function.
- Good Ductility and Malleability: While these properties are less directly related to heat transfer, they can be advantageous during post-processing or integration of the component.
- アプリケーション Pure copper is widely used in applications such as:
- High-performance heat sinks for electronics: Cooling CPUs, GPUs, and power electronics.
- Thermal management in electric vehicles: Battery cooling plates and motor coolers.
- Induction heating coils: Utilizing both its thermal and electrical conductivity.
- Certain heat exchanger components: Where the primary requirement is maximum heat transfer.
2. CuCrZr (Copper-Chromium-Zirconium): High Strength at Elevated Temperatures
- 優れた熱伝導性: CuCrZr offers a high thermal conductivity (around 330-350 W/m·K), slightly lower than pure copper but still significantly better than many other metals.
- 高い強度と硬度: The addition of chromium and zirconium significantly enhances the strength and hardness of copper, especially at elevated temperatures. This makes it suitable for applications where the heat transfer plate is subjected to mechanical stress and high operating temperatures.
- 優れたクリープ耐性: CuCrZr exhibits excellent resistance to creep (deformation under sustained stress at high temperatures), which is crucial for long-term reliability in demanding thermal environments.
- 良好な耐食性: Compared to pure copper, CuCrZr often shows improved resistance to certain corrosive environments.
- アプリケーション CuCrZr is particularly well-suited for:
- Welding electrodes: Requiring high thermal and electrical conductivity along with high strength at elevated temperatures.
- High-temperature heat exchangers: Operating in environments with both high thermal loads and mechanical stress.
- Components in aerospace and automotive engines: Where strength and thermal management are critical.
- Molds and dies with conformal cooling channels: Benefiting from both efficient heat transfer and the material’s ability to withstand injection pressures.
Why These Materials are Ideal for Metal 3D Printing:
- Powder Availability and Quality: Metal3DP offers high-quality, spherical powders of both Cu and CuCrZr, specifically engineered for optimal flowability and packing density in powder bed fusion processes like Selective Laser Melting (SLM) and Electron Beam Melting (EBM). Our advanced powder making system ensures consistent quality and performance.
- 加工性: Both copper and CuCrZr can be effectively processed using various metal 3D printing techniques, allowing for the creation of complex geometries and intricate internal features.
- Achievable Density and Mechanical Properties: When processed correctly, 3D printed parts made from these powders can achieve high densities and mechanical properties that meet or exceed those of conventionally manufactured parts.
By selecting the appropriate material – pure copper for maximum thermal conductivity or CuCrZr for a balance of high thermal conductivity and high-temperature strength – engineers can tailor the performance of their custom heat transfer plates to meet the specific demands of their applications. Metal3DP’s expertise in metal 3D printing and our range of high-performance powders empower our customers to achieve optimal thermal management solutions. Sources and related content
Design Considerations for Additive Manufacturing of Heat Transfer Plates – Optimizing for Performance and Efficiency
Designing heat transfer plates for additive manufacturing requires a different mindset compared to traditional methods. The unique capabilities and limitations of metal 3D printing processes like Selective Laser Melting (SLM) and Electron Beam Melting (EBM) open up new avenues for optimization but also necessitate careful consideration of several design factors. Here are key aspects to consider when designing custom heat transfer plates for metal 3D printing:
- Thermal Performance Optimization: The primary goal of a heat transfer plate is efficient heat exchange. Consider these design elements:
- Internal Channel Design: Metal 3D printing allows for the creation of complex internal cooling channels that maximize the surface area in contact with the coolant and optimize fluid flow. This includes:
- コンフォーマル冷却チャンネル: Designing channels that closely follow the contours of the heat-generating component ensures uniform cooling and eliminates hot spots.
- Lattice Structures and Fin Designs: Incorporating intricate internal lattices or fin structures within the flow channels can significantly increase the heat transfer surface area and promote turbulent flow, enhancing heat exchange efficiency.
- Variable Channel Cross-Sections: Optimizing the shape and size of the channels along the flow path can minimize pressure drop and ensure uniform flow distribution.
- Surface Area Maximization: External features like fins, microchannels, and textured surfaces can be incorporated to increase the surface area exposed to the surrounding environment, enhancing heat dissipation.
- Material Distribution: Consider using variable density or wall thickness to optimize heat flow paths and minimize weight without compromising structural integrity.
- Internal Channel Design: Metal 3D printing allows for the creation of complex internal cooling channels that maximize the surface area in contact with the coolant and optimize fluid flow. This includes:
- 製造性のための設計(DFM): While metal 3D printing offers design freedom, certain guidelines should be followed to ensure successful printing:
- サポート体制: Overhanging features and complex geometries may require support structures to prevent collapse or distortion during printing. Design the part with minimal overhangs and consider self-supporting angles where possible. Plan for easy removal of support structures post-printing.
- Orientation: The orientation of the part on the build platform can significantly impact surface finish, support requirements, and mechanical properties. Optimize the orientation to minimize support volume and achieve the desired surface quality on critical heat transfer surfaces.
- 壁の厚さ: Ensure sufficient wall thickness to provide structural integrity and facilitate heat conduction. Consider the minimum feature size and wall thickness limitations of the chosen printing process.
- Internal Features: Design internal channels and features with consideration for powder removal. Ensure there are escape holes for unmolten powder to be effectively removed after printing.
- Tolerances and Clearances: Account for the achievable tolerances of the metal 3D printing process when designing mating surfaces or interfaces with other components.
- Material Selection and Integration:
- 素材の互換性: Choose materials like CuCrZr or pure copper based on the specific thermal and mechanical requirements of the application, as discussed earlier.
- Multi-Material Design (Advanced): Explore the potential of multi-material printing (if available with the chosen technology) to optimize different aspects of the heat transfer plate, such as using a highly conductive material for heat transfer paths and a stronger material for structural support.
- Integration with System Design:
- Mounting Features: Design integrated mounting features, such as bolt holes or flanges, to ensure secure and efficient integration of the heat transfer plate into the overall system.
- Fluid Connections: Carefully design inlet and outlet ports for the coolant to ensure proper flow and prevent leaks. Consider the type of fittings that will be used.
- Sensor Integration: If temperature or flow sensors are required, design appropriate housings or mounting points for seamless integration.
By carefully considering these design aspects, engineers can leverage the unique capabilities of metal 3D printing to create custom heat transfer plates with significantly enhanced thermal performance, reduced weight, and optimized integration into their specific applications. Consulting with experienced metal 3D printing service providers like メタル3DP early in the design process can help identify potential challenges and optimize the design for successful manufacturing and performance.
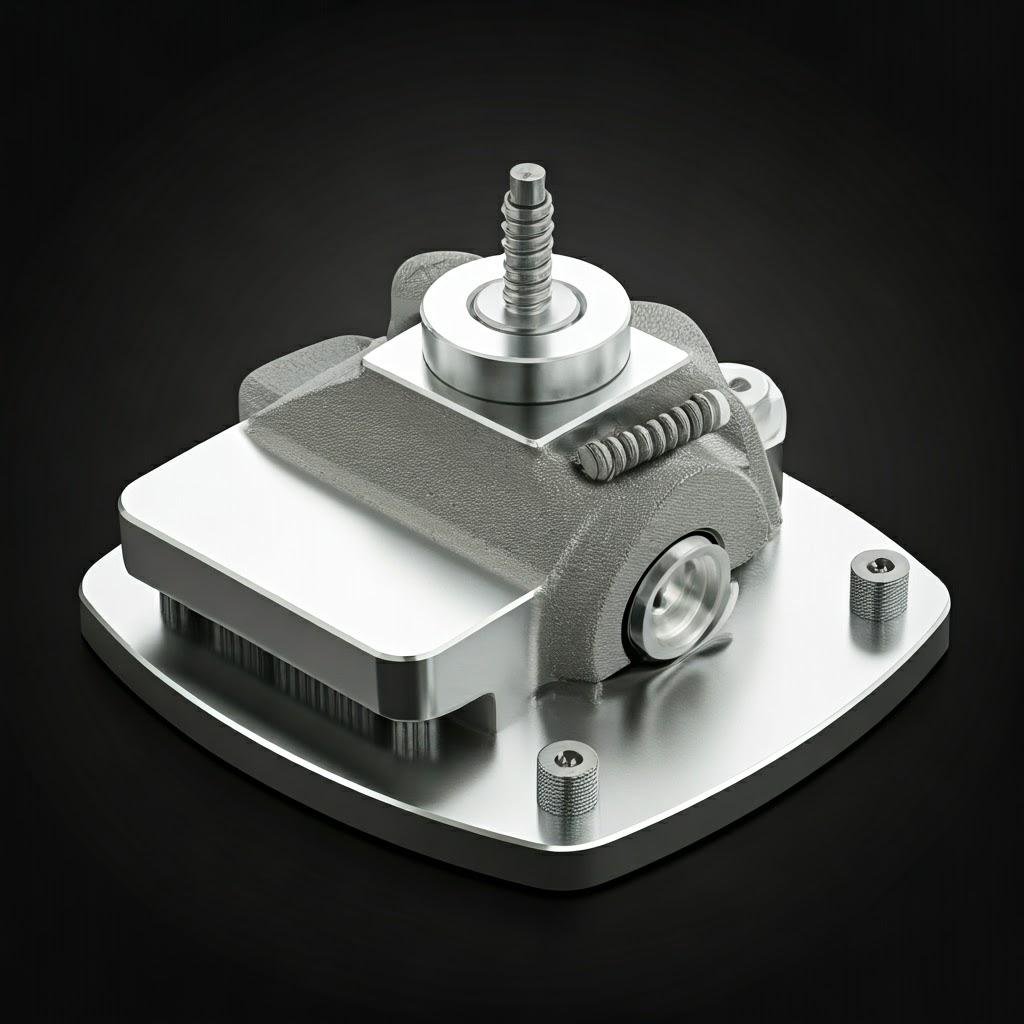
Tolerance, Surface Finish, and Dimensional Accuracy in 3D Printed Heat Transfer Plates
Achieving the required tolerance, surface finish, and dimensional accuracy is crucial for the functional performance and integration of custom heat transfer plates. Metal 3D printing processes offer varying levels of precision, and understanding these capabilities is essential for effective design and application.
- 寸法精度: The dimensional accuracy achievable in metal 3D printing depends on several factors, including the printing technology (SLM, EBM, etc.), the material used, the part geometry, and the process parameters. Generally:
- SLM (Selective Laser Melting): Typically offers good dimensional accuracy, with achievable tolerances often in the range of ±0.05 to ±0.1 mm for smaller features. Larger parts may exhibit slightly wider tolerances.
- EBM (Electron Beam Melting): Can also achieve good accuracy, although surface finish might be slightly rougher compared to SLM. Tolerances are generally comparable to SLM.
- 精度に影響する要因:
- Material Shrinkage: Metals shrink as they solidify after melting. The amount of shrinkage depends on the material and needs to be accounted for in the design and process parameters.
- Thermal Distortion: Residual stresses built up during the printing process can lead to warping or distortion, especially in complex geometries. Optimized build orientation and support structures can mitigate this.
- Calibration and Maintenance: Properly calibrated and maintained 3D printing equipment is essential for achieving consistent dimensional accuracy.
- 表面仕上げ: The surface finish of metal 3D printed parts is typically rougher compared to machined surfaces.
- SLMだ: Generally produces parts with a surface roughness (Ra) in the range of 5-20 µm as-built.
- EBMである: Often results in a slightly rougher surface finish, typically in the range of 10-30 µm Ra. The coarser finish is due to the larger powder particle size and higher build temperatures.
- Impact on Heat Transfer: For heat transfer plates, the surface finish can affect the fluid flow and heat transfer efficiency. Rougher surfaces can increase turbulence, which might enhance heat transfer in some applications but also increase pressure drop.
- Tolerance: Tolerance refers to the allowable variation in a dimension. Specifying appropriate tolerances is crucial for ensuring proper fit and function.
- 設計上の考慮事項: Design tolerances should be based on the functional requirements of the heat transfer plate and the capabilities of the chosen metal 3D printing process. Avoid specifying unnecessarily tight tolerances, as this can increase manufacturing costs and lead times.
- 後処理: If tighter tolerances or smoother surface finishes are required, post-processing techniques such as CNC machining, grinding, polishing, or surface coatings can be employed. These processes can significantly improve the dimensional accuracy and surface finish of 3D printed parts.
- Achieving Desired Precision: To achieve the desired tolerance, surface finish, and dimensional accuracy for custom heat transfer plates:
- 素材の選択: Choose a material and printing process that inherently offers the best possible precision for the application.
- デザインの最適化: Design the part with consideration for the limitations and capabilities of the chosen printing process. Minimize large flat surfaces and incorporate features that enhance stiffness and reduce distortion.
- プロセスパラメータの最適化 Work with experienced metal 3D printing providers like Metal3DP who can optimize the printing parameters (laser power, scan speed, layer thickness, build orientation, etc.) to achieve the best possible accuracy and surface finish.
- Post-Processing Planning: If the as-printed quality is insufficient, plan for appropriate post-processing steps to meet the required specifications. We offer comprehensive post-processing services to enhance the functionality and aesthetics of your 3D printed parts.
- 品質管理: Implement rigorous quality control measures, including dimensional inspection and surface roughness measurements, to ensure that the manufactured parts meet the specified requirements.
By understanding the achievable tolerances and surface finishes in metal 3D printing and planning accordingly in the design and post-processing stages, engineers can successfully produce high-precision custom heat transfer plates that meet the demanding requirements of their applications.
Post-Processing Requirements for Metal 3D Printed Heat Transfer Plates
While metal 3D printing offers significant advantages in creating complex geometries for custom heat transfer plates, post-processing steps are often necessary to achieve the final desired properties, surface finish, and dimensional accuracy. The specific post-processing requirements depend on the application, the chosen printing process, and the material. Here are common post-processing steps for metal 3D printed heat transfer plates:
- 支持構造の撤去: Support structures are often required during the printing process to support overhanging features and prevent distortion. These structures need to be carefully removed after the build is complete. Methods include:
- 手動による除去: Using hand tools like pliers, cutters, and scrapers.
- 機械加工: Employing CNC machining to precisely remove supports, especially in areas with tight tolerances.
- ワイヤー放電加工(EDM): Suitable for removing complex or difficult-to-access support structures.
- Powder Removal: In powder bed fusion processes like SLM and EBM, un-sintered powder remains trapped within internal channels and cavities. Effective powder removal is crucial for the functionality of heat transfer plates with intricate internal cooling channels. Techniques include:
- Brushing and Blowing: Using compressed air and brushes to dislodge loose powder.
- Vibration and Ultrasonic Cleaning: Applying vibrations or ultrasonic waves to help dislodge trapped powder.
- Chemical растворение (Dissolution): In some cases, specific solvents can be used to dissolve trapped powder (material compatibility is critical).
- Dedicated Powder Removal Systems: Specialized equipment designed for efficient powder extraction from complex geometries.
- Stress Relief Heat Treatment: Residual stresses build up during the rapid heating and cooling cycles of metal 3D printing. Stress relief heat treatment is often necessary to:
- Improve Mechanical Properties: Reduce brittleness and enhance ductility.
- Enhance Dimensional Stability: Prevent warping or cracking over time.
- Prepare for Subsequent Machining: Reduce the risk of distortion during machining operations. The specific heat treatment cycle (temperature and duration) depends on the material. For example, CuCrZr may require solution annealing followed by aging to achieve optimal strength and conductivity.
- 表面仕上げ: The as-printed surface finish of metal 3D printed parts is typically rough. Depending on the application requirements, various surface finishing techniques can be employed:
- Media Blasting: Using abrasive media to remove partially sintered powder and improve surface uniformity.
- 研磨: Mechanical or chemical polishing to achieve smoother surfaces, which can be important for reducing fluid friction and improving sealing in heat transfer applications.
- Grinding and Lapping: For achieving tighter tolerances and very smooth surfaces on critical mating areas.
- CNC Machining: In cases where very tight tolerances or specific surface finishes are required on certain features, CNC machining can be used as a secondary process. This is often applied to interfaces, mounting surfaces, or critical flow channels.
- Leak Testing: For heat transfer plates designed with internal cooling channels, leak testing is essential to ensure the integrity of the fluid pathways and prevent coolant leaks during operation. This can involve pressure testing with air or liquids.
- Cleaning and Inspection: Final cleaning to remove any residual contaminants and thorough inspection to ensure dimensional accuracy, surface quality, and overall integrity are crucial before the heat transfer plate is integrated into the final system.
で メタル3DP, we understand the importance of comprehensive post-processing to ensure the optimal performance of your custom metal 3D printed parts. We offer a range of post-processing services to meet your specific requirements, ensuring that your heat transfer plates are delivered with the desired properties, finish, and accuracy. Our expertise in both metal 3D printing and post-processing techniques allows us to provide end-to-end solutions for your thermal management needs.
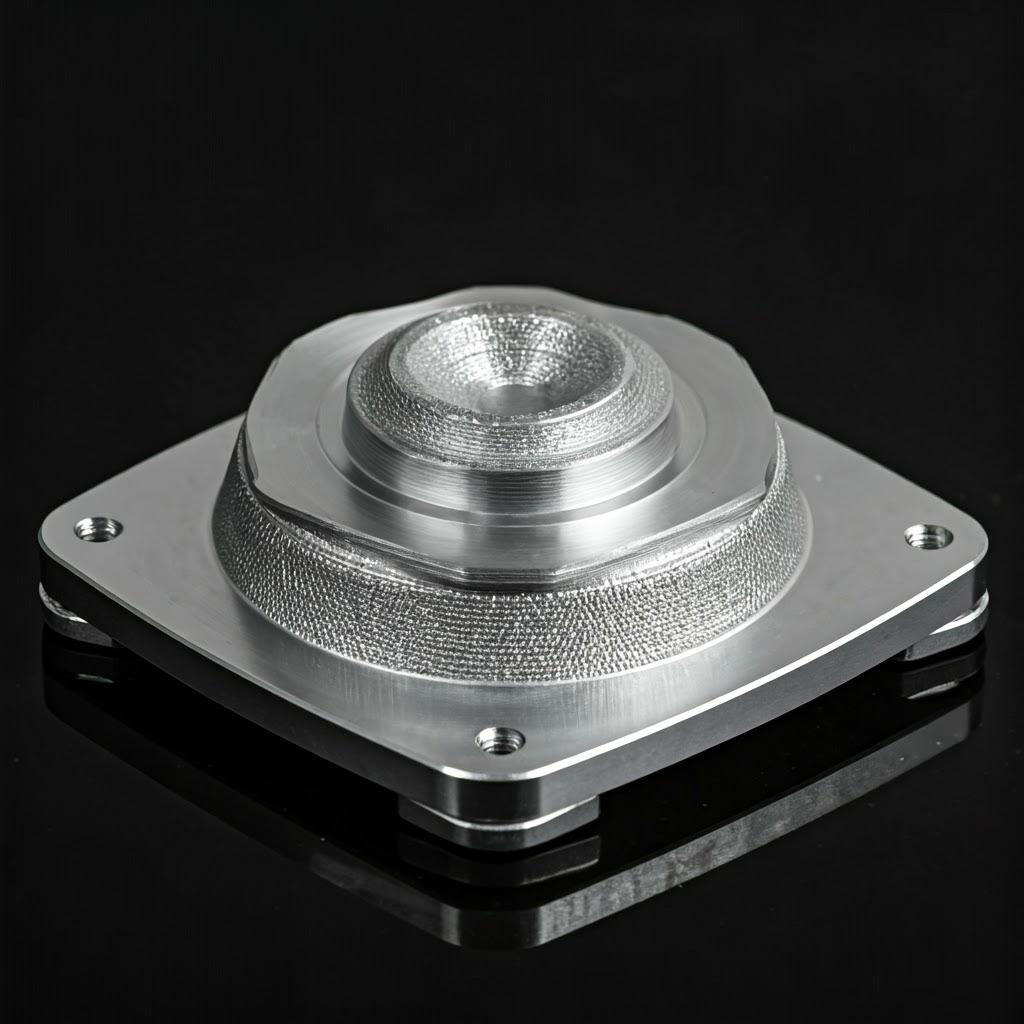
Common Challenges and How to Avoid Them in Metal 3D Printing of Heat Exchangers
While metal 3D printing offers numerous advantages for creating custom heat transfer plates, several challenges can arise during the design and manufacturing process. Understanding these potential issues and implementing appropriate strategies to avoid them is crucial for successful outcomes. Here are some common challenges and how to mitigate them:
- Warping and Distortion: Thermal stresses induced during the rapid heating and cooling cycles of metal 3D printing can lead to warping or distortion, especially in large or thin-walled parts.
- How to Avoid:
- Optimize Build Orientation: Orient the part to minimize unsupported areas and reduce the build height.
- Strategic Support Placement: Use sufficient and strategically placed support structures to anchor the part to the build platform and prevent movement during printing.
- プロセスパラメータの最適化 Adjust laser power, scan speed, and layer thickness to minimize thermal gradients.
- Stress Relief Heat Treatment: Perform post-print stress relief to alleviate internal stresses.
- Design for Additive Manufacturing (DFAM): Incorporate features like ribs or gussets to increase stiffness and reduce the likelihood of distortion.
- How to Avoid:
- Support Removal Difficulties: Removing support structures from intricate internal channels or delicate features can be challenging and may damage the part’s surface.
- How to Avoid:
- Self-Supporting Angles: Design features with angles greater than 45 degrees to minimize the need for supports.
- Smart Support Design: Use dissolvable support materials (if available for the chosen material and process) or design supports with breakaway points for easier removal.
- Consider Part Orientation: Orient the part to minimize the number of internal supports required.
- Plan for Access: Ensure there are adequate access points for support removal tools or powder evacuation.
- How to Avoid:
- Porosity and Density Issues: Achieving fully dense parts with minimal porosity is crucial for optimal thermal conductivity and mechanical strength.
- How to Avoid:
- Optimize Process Parameters: Carefully control laser power, scan speed, hatch spacing, and layer thickness to ensure complete melting and fusion of the metal powder.
- High-Quality Powder: Use high-quality, spherical metal powders with good flowability and packing density, such as those offered by メタル3DP.
- Inert Atmosphere: Ensure a clean and controlled inert gas atmosphere during printing to prevent oxidation and contamination.
- パウダーベッドの準備: Maintain a uniform and dense powder bed.
- How to Avoid:
- 表面粗さ: As-printed metal 3D parts typically have a higher surface roughness compared to machined parts, which can affect fluid flow and heat transfer.
- How to Avoid:
- Optimize Process Parameters: Smaller powder particle sizes and thinner layers can result in smoother surfaces.
- 後処理: Plan for surface finishing techniques like media blasting, polishing, or machining if smoother surfaces are required.
- Consider Build Orientation: Surfaces oriented upwards tend to be rougher than downward-facing surfaces.
- How to Avoid:
- Dimensional Accuracy Challenges: Achieving tight tolerances can be difficult due to material shrinkage and thermal distortion.
- How to Avoid:
- Design with Realistic Tolerances: Understand the achievable tolerances of the chosen printing process and design accordingly.
- Process Calibration: Ensure the 3D printer is properly calibrated and maintained.
- Material Shrinkage Compensation: Account for material shrinkage in the design phase and process parameters.
- Post-Processing Machining: For critical dimensions, plan for secondary CNC machining to achieve the required accuracy.
- How to Avoid:
- Material Property Variations: The microstructure and mechanical properties of 3D printed metals can sometimes vary depending on the build direction and process parameters.
- How to Avoid:
- Optimize Process Parameters: Develop and adhere to optimized printing parameters to ensure consistent material properties throughout the part.
- 熱処理: Implement appropriate heat treatment cycles to homogenize the microstructure and improve mechanical properties.
- Material Characterization: Conduct thorough material testing to understand the anisotropic behavior (if any) and account for it in the design.
- How to Avoid:
- コストを考慮する: Metal 3D printing can be expensive, especially for large volumes or complex parts requiring significant post-processing.
- How to Avoid:
- デザインの最適化: Design for material efficiency and minimize the need for extensive support structures.
- Strategic Material Selection: Choose the most cost-effective material that meets the performance requirements.
- Consider Hybrid Manufacturing: For certain features, consider combining 3D printing with traditional manufacturing methods.
- How to Avoid:
By proactively addressing these potential challenges through careful design, optimized process parameters, and appropriate post-processing, engineers can successfully leverage the benefits of metal 3D printing to create high-performance custom heat transfer plates for a wide range of applications. Partnering with experienced metal 3D printing service providers like Metal3DP can provide valuable insights and support in navigating these challenges.
How to Choose the Right Metal 3D Printing Service Provider for Custom Heat Transfer Plates
Selecting the right metal 3D printing service provider is a critical decision that can significantly impact the success of your project for custom heat transfer plates. With a growing number of companies offering metal AM services, it’s essential to evaluate potential partners based on several key criteria to ensure you receive high-quality parts that meet your specific requirements. Here’s a guide on how to choose the right provider:
- Material Capabilities: Ensure the provider has experience working with the specific metal powders required for your heat transfer plate, such as CuCrZr and pure copper.
- Powder Portfolio: Check if they offer a range of high-quality metal powders, ideally from reputable manufacturers. Metal3DP boasts an advanced powder making system and a wide selection of high-performance metal powders optimized for additive manufacturing.
- 材料に関する専門知識: Inquire about their experience and expertise in processing the desired materials, including optimized printing parameters and post-processing techniques specific to those alloys.
- Printing Technology and Equipment: Understand the types of metal 3D printing technologies they utilize (e.g., SLM, EBM, DMLS).
- Technology Suitability: Determine if their technology is well-suited for the complexity, size, and tolerance requirements of your heat transfer plate design. Metal3DP offers industry-leading SEBM printers known for their accuracy and reliability.
- Equipment Maintenance and Calibration: A provider with well-maintained and regularly calibrated equipment is more likely to produce consistent and accurate parts.
- Design and Engineering Support: A good service provider should offer design consultation and engineering support to optimize your heat transfer plate for additive manufacturing.
- DFAM Expertise: Do they have expertise in Design for Additive Manufacturing (DFAM) principles to help you leverage the unique capabilities of metal 3D printing?
- Simulation and Analysis: Can they offer simulation services (e.g., thermal analysis, CFD) to validate the performance of your design before production?
- Post-Processing Services: As discussed earlier, post-processing is often crucial for metal 3D printed parts.
- In-House Capabilities: Check if they offer the necessary post-processing services in-house, such as support removal, powder removal, heat treatment, surface finishing, and CNC machining. Metal3DP provides comprehensive post-processing services.
- 品質管理: Inquire about their quality control procedures and inspection methods to ensure the final parts meet your specifications.
- Quality Assurance and Certifications: A reputable provider should have robust quality management systems in place.
- 認定: Look for certifications such as ISO 9001 or AS9100 (for aerospace applications), which demonstrate a commitment to quality.
- Material Traceability: Ensure they can provide material traceability for the metal powders used in your parts.
- Experience and Portfolio: Review their past work and case studies to assess their experience in producing similar parts or serving your industry.
- 業界経験: Do they have experience working with companies in aerospace, automotive, medical, or industrial manufacturing?
- 部品の複雑さ: Evaluate the complexity and quality of the parts they have produced.
- Communication and Customer Service: Effective communication and responsive customer service are essential for a smooth and successful project.
- Responsiveness: Are they prompt in responding to inquiries and providing updates?
- テクニカルサポート: Do they have knowledgeable technical staff who can address your questions and concerns?
- Cost and Lead Time: While not the only factors, cost and lead time are important considerations.
- Pricing Structure: Understand their pricing model and get a clear breakdown of costs.
- リードタイム Inquire about their typical lead times for similar projects.
- Location and Logistics: Consider the provider’s location and their ability to handle shipping and logistics efficiently.
By carefully evaluating potential metal 3D printing service providers based on these criteria, you can select a partner that aligns with your project requirements and ensures the successful manufacturing of your custom heat transfer plates. Metal3DPへのお問い合わせ today to discuss your specific needs and learn how our comprehensive solutions can empower your additive manufacturing goals.
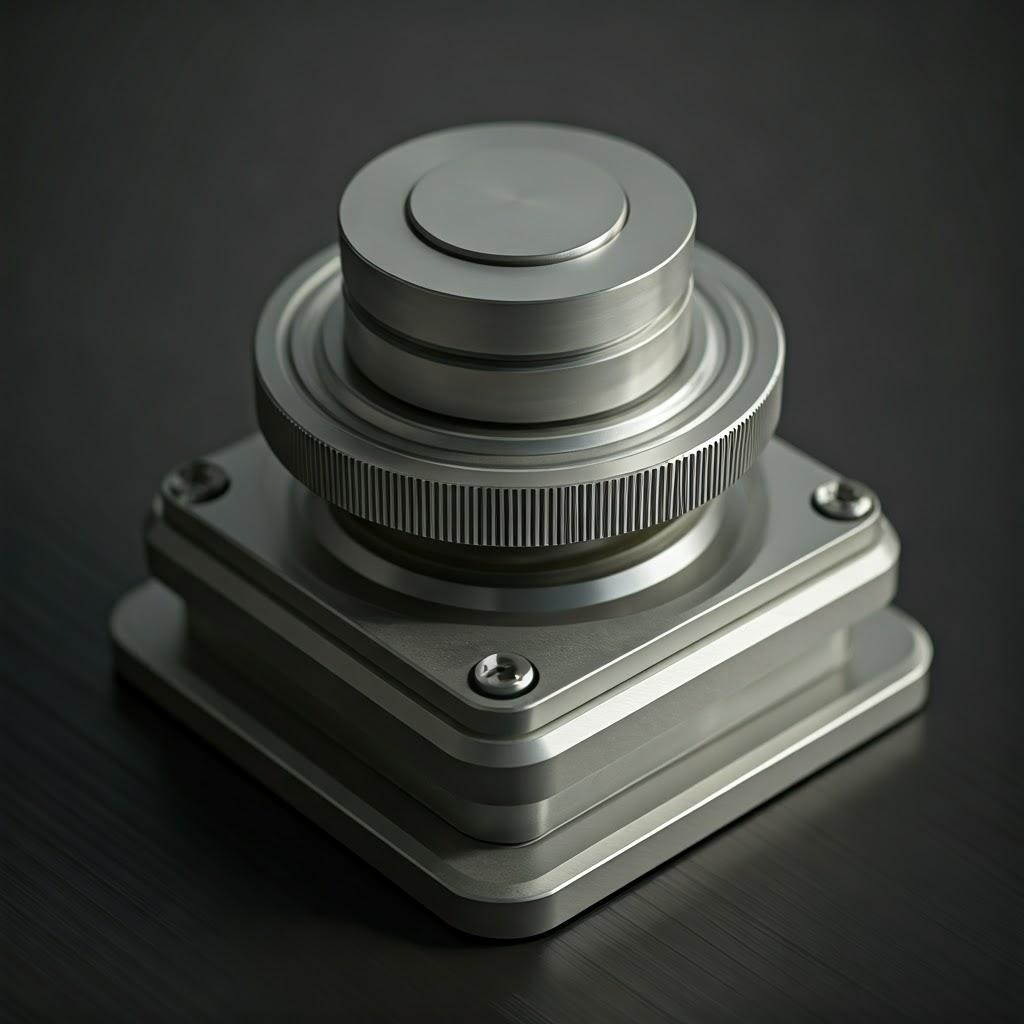
Cost Factors and Lead Time for Custom Metal 3D Printed Heat Transfer Plates
Understanding the factors that influence the cost and lead time for custom metal 3D printed heat transfer plates is crucial for budgeting and project planning. Unlike traditional manufacturing, the economics of metal 3D printing are driven by a different set of variables. Here’s a breakdown of the key cost and lead time considerations:
コスト要因:
- 材料費: The cost of the metal powder (e.g., CuCrZr, pure copper) is a significant factor. Specialty alloys and higher purity grades typically have higher costs. The quantity of material used for the part and support structures also contributes to the overall material cost.
- ビルドタイム: The time it takes to print the part is a major cost driver. Longer build times consume more machine time and energy. Factors affecting build time include:
- Part Volume and Complexity: Larger and more complex parts generally take longer to print.
- Layer Height: Thinner layers result in finer details but increase build time.
- Number of Parts per Build: Optimizing the build platform to include multiple parts can improve efficiency and reduce the cost per part.
- Machine Operation and Maintenance: The cost of operating and maintaining the metal 3D printing equipment is factored into the overall cost. This includes energy consumption, consumables (e.g., recoater blades, filters), and machine maintenance.
- Pre-Processing Costs: This includes the time and effort involved in design optimization for additive manufacturing, build preparation, and generating support structures.
- 後処理費用: As discussed earlier, post-processing steps like support removal, powder removal, heat treatment, surface finishing, and machining add to the overall cost. The complexity and extent of post-processing required will significantly impact the final price.
- 人件費: The cost of skilled technicians and engineers involved in the entire process, from design to post-processing and quality control, is a factor.
- Tooling Costs (Minimal): Unlike traditional manufacturing methods that require expensive molds or dies, metal 3D printing typically has minimal tooling costs, which can be a significant advantage for low-volume production or custom parts.
- Quality Assurance and Inspection: Costs associated with quality control procedures, material testing, and dimensional inspection are included.
Lead Time Factors:
- Design and Optimization: The time required to design or optimize the heat transfer plate for additive manufacturing, including any simulations or iterations.
- Build Preparation: Setting up the print job, including build platform preparation, material loading, and parameter selection.
- 印刷時間: The actual duration of the 3D printing process.
- Cooling Time: The time required for the printed part to cool down before it can be removed from the build platform.
- Post-Processing Time: The time needed for all the required post-processing steps, which can vary significantly depending on the complexity and desired finish.
- Quality Control and Inspection: The time taken for dimensional inspection, material testing, and other quality checks.
- Shipping and Handling: The time required for packaging and shipping the final parts.
Strategies to Potentially Reduce Costs and Lead Times:
- Design Optimization for AM: Designing parts specifically for additive manufacturing can minimize material usage, build time, and the need for extensive support structures.
- Build Platform Optimization: Nesting multiple parts on a single build platform can improve efficiency.
- 素材の選択: Choosing the most cost-effective material that meets the performance requirements.
- Minimizing Post-Processing: Designing parts that require minimal post-processing can reduce both cost and lead time.
- Strategic Partner Selection: Choosing a metal 3D printing service provider like メタル3DP with efficient processes and in-house capabilities can help optimize both cost and lead time.
It’s important to discuss your specific requirements and project details with your chosen metal 3D printing service provider to get an accurate estimate of the cost and lead time for your custom heat transfer plates.
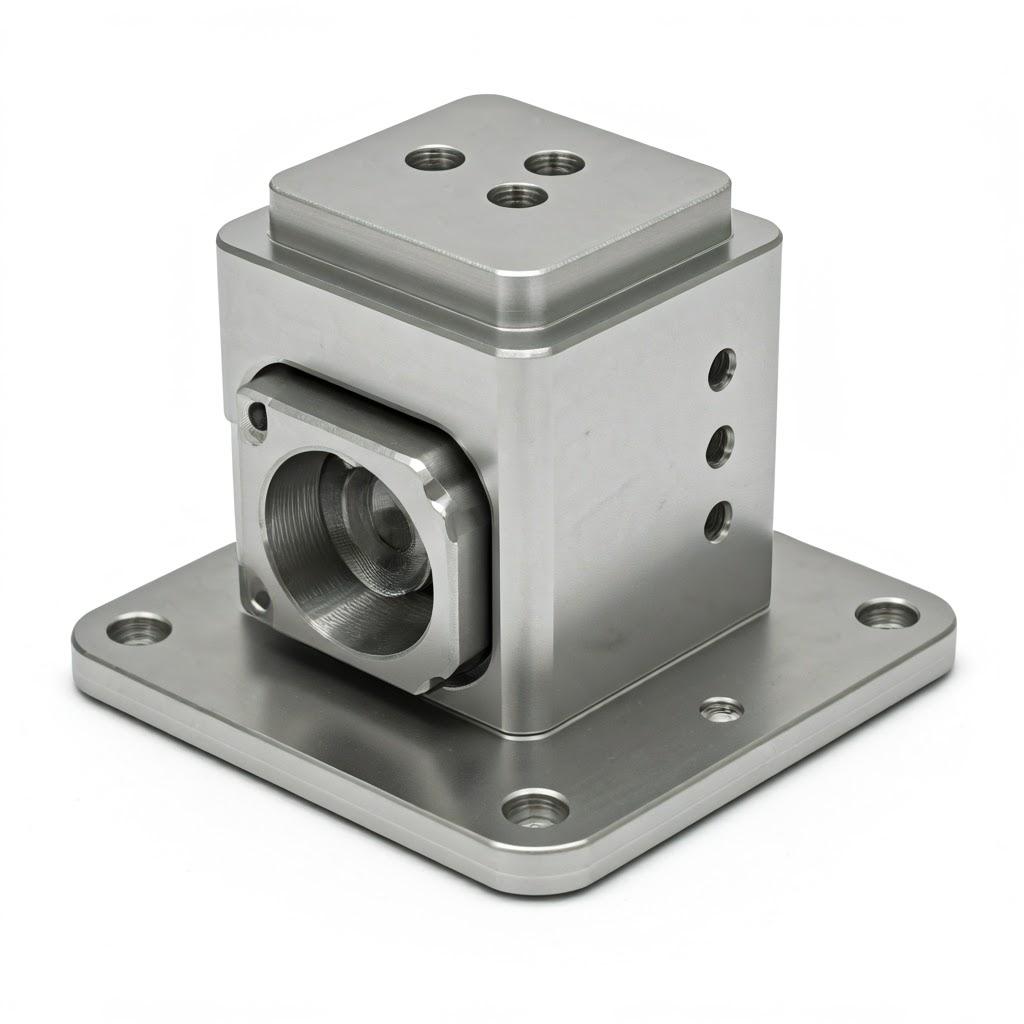
よくある質問(FAQ)
- Q: What are the typical tolerances achievable with metal 3D printing for heat transfer plates?
- A: Achievable tolerances depend on the printing technology and part geometry. Generally, Selective Laser Melting (SLM) can achieve tolerances in the range of ±0.05 to ±0.1 mm for smaller features. Larger parts may have slightly wider tolerances. Post-processing like CNC machining can be used for tighter tolerances if required.
- Q: Can metal 3D printed heat transfer plates be used in high-temperature applications?
- A: Yes, materials like CuCrZr are specifically chosen for their high strength and good thermal conductivity at elevated temperatures, making them suitable for demanding thermal environments. The specific temperature limits will depend on the material and the application requirements.
- Q: What kind of surface finish can I expect from a metal 3D printed heat transfer plate?
- A: The as-printed surface finish is typically rougher than machined surfaces, with Ra values ranging from 5-30 µm depending on the printing process. Post-processing techniques like polishing or machining can be employed to achieve smoother surfaces if needed for your application.
- Q: Is metal 3D printing cost-effective for producing custom heat transfer plates?
- A: Metal 3D printing can be cost-effective, especially for complex geometries, low to medium volume production, and highly customized parts where traditional tooling costs would be prohibitive. Factors like material cost, build time, and post-processing requirements will influence the overall cost.
- Q: How long does it typically take to get a custom metal 3D printed heat transfer plate?
- A: Lead times vary depending on the complexity of the part, the chosen material and printing process, the required post-processing, and the service provider’s workload. It can range from a few days for simple prototypes to several weeks for complex parts requiring extensive post-processing. Metal3DPへのお問い合わせ for a specific lead time estimate for your project.
Conclusion – Embracing the Future of Heat Transfer with Metal 3D Printing and Met3dp
作成する能力 custom heat transfer plates with intricate geometries and optimized material properties through metal 3D printing represents a significant leap forward in thermal management technology. By overcoming the design limitations of traditional manufacturing, metal AM empowers engineers and procurement managers to develop innovative solutions that enhance efficiency, reduce weight, and improve the overall performance of critical systems across diverse industries, from aerospace and automotive to medical and industrial applications.
Materials like high-conductivity pure copper and high-strength CuCrZr, processed with the precision of metal 3D printing, unlock new possibilities for designing heat exchangers tailored to specific needs. The design freedom allows for complex internal cooling channels, conformal geometries, and integrated features, leading to more efficient heat transfer and improved system integration.
While challenges such as achieving tight tolerances and managing surface finish exist, advancements in metal 3D printing technology and sophisticated post-processing techniques are continuously expanding the possibilities. Choosing the right metal 3D printing service provider is paramount to navigating these challenges and ensuring the successful realization of your custom heat transfer plate designs.
で メタル3DPテクノロジー株式会社, we are committed to providing cutting-edge metal additive manufacturing solutions. Our industry-leading SEBM printers, coupled with our extensive portfolio of high-quality metal powders, including those ideal for thermal management applications, and our comprehensive post-processing services, make us a trusted partner for your custom heat transfer plate needs. We are dedicated to helping you harness the full potential of metal 3D printing to drive innovation and achieve your engineering goals. Explore our metal 3D printing services そして contact us today to discuss how we can collaborate on your next project and help you embrace the future of heat transfer.
シェアする
MET3DP Technology Co., LTDは、中国青島に本社を置く積層造形ソリューションのリーディングプロバイダーです。弊社は3Dプリンティング装置と工業用途の高性能金属粉末を専門としています。
関連記事
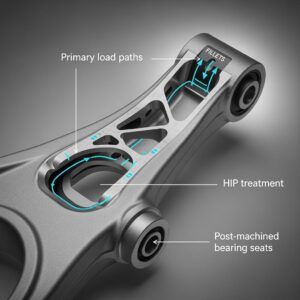