釜山で付加製造による廃棄物の削減
目次
1.はじめに釜山で高まる持続可能な製造業の必要性
韓国第2の都市であり、海運、自動車、重工業の重要な拠点である釜山は、今まさに重要な局面を迎えている。世界的な規制が強化され、ESG(環境・社会・ガバナンス)基準が譲れないものとなる中、釜山の製造業者は従来の生産方法を見直さなければならない。
韓国は、2050年までに炭素排出量を正味ゼロにすることを公約している。この目標に沿って、釜山の産業部門は、エネルギー消費を削減し、廃棄物を抑制し、材料効率を向上させる方法で事業を近代化する必要に迫られている。
釜山で廃棄物削減が優先される理由
- 産業密度:釜山には主要な造船所、自動車部品メーカー、電子部品メーカーがあり、これらすべてが産業廃棄物を大量に排出している。
- 環境規制:韓国環境省は検査を強化し、炭素を多く含むプロセスに課税し、グリーン技術にインセンティブを与えている。
- グローバル・サプライチェーンの需要:国際的なパートナーやバイヤーは、持続可能性が高いサプライヤーに好意を寄せている。
ゲームチェンジャーとしての積層造形(AM)
積層造形は、しばしばこう呼ばれる。 3DプリンティングAMは、製造工程の無駄を省く強力なツールとして台頭してきている。従来のサブトラクティブ・マニュファクチャリング(ブロックから材料を削り出す)とは異なり、AMは必要な材料だけを使い、層ごとに部品を作ります。
釜山では、AMを採用するということは
- 材料の無駄が少ない
- サプライチェーンの短縮
- 現地生産
- カーボンフットプリントの削減
このような持続可能性のメリットは、単なる机上の空論ではない。釜山の航空宇宙、医療、自動車の各分野の企業、特に高性能金属AMシステムを使用している企業によって、すでに実現されている。
2.産業廃棄物削減における積層造形の役割
従来型製造と積層造形
特徴 | トラディショナル(減算法) | アディティブ・マニュファクチャリング(AM) |
---|---|---|
材料の使用 | 高廃棄物(例:60~80%の材料除去) | 無駄を省いたニアネットシェイプ |
工具 | 高価な金型・工具が必要 | ツールは不要 |
インベントリー | 大量在庫と倉庫保管が必要 | オンデマンド生産で過剰在庫を最小化 |
エネルギー使用 | 高い(特に金属加工用) | 多くのAM工程でより低い |
スクラップ率 | 人為的ミスや欠陥による高 | 最適化されたデジタル設計で低コストを実現 |
AMはいかに無駄を省くか
- ニア・ネットシェイプ・プロダクション:AMは最終形状に近いパーツを作るため、トリミングや機械加工、後加工の必要性を減らすことができる。
- デジタル・ファーストの製造:部品はCADファイルから直接作成されるため、精度が向上し、当てずっぽうの作業がなくなります。
- ローカライズされた生産:AMは、使用場所の近くで生産することを可能にし、包装や輸送の無駄を削減する。
- オンデマンド製作:過剰生産や大量の在庫を保管する必要がないため、陳腐化した在庫や廃棄を減らすことができる。
持続可能性を支える積層造形技術
AMテクノロジー | 廃棄物削減のメリット |
---|---|
パウダーベッドフュージョン(PBF) | 未使用のパウダーを再利用し、余分な材料を最小限に抑える |
指向性エネルギー蒸着(DED) | 補修やビルドアップに必要な部分のみ材料を加える |
バインダー・ジェット | 低いエネルギー使用量、最小限のサポート構造 |
これらの方法の詳細については、Metal3DPのウェブサイトをご覧ください。 印刷方法ページ.
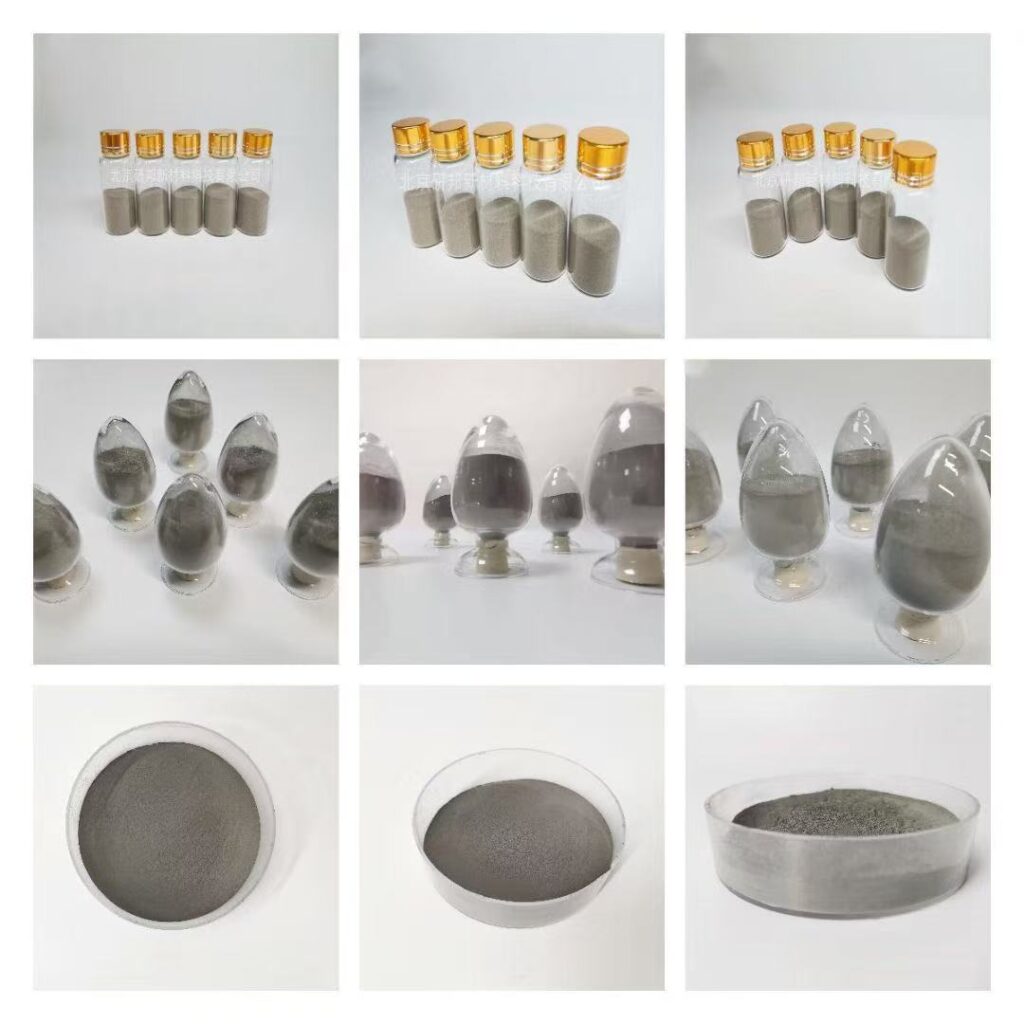
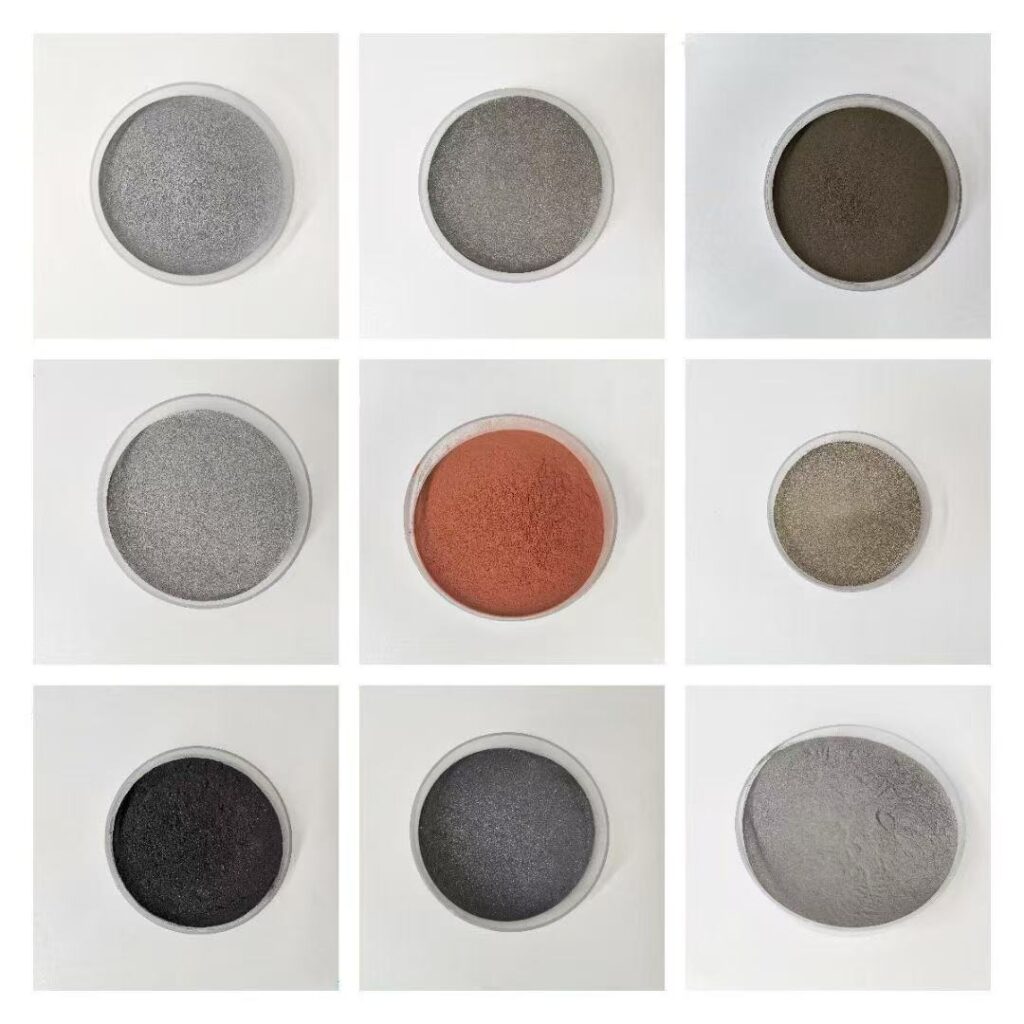
3.釜山における企業の主な環境的・経済的便益
アディティブ・マニュファクチャリングへの移行は、地球にとって良いだけでなく、賢明なビジネス上の決断でもある。AMを業務に組み込んだ釜山の企業は、さまざまな面でコスト削減を報告している。
環境面でのメリット
- 🌍 廃棄物削減:減算法に比べ、材料廃棄量が最大90%減少。
- 💨 炭素排出量の削減:輸送の必要性が少なく、エネルギー集約的な工程が少ない。
- ♻️ 素材のリサイクル性:多くのAMシステムでは、劣化を最小限に抑えて粉末を再利用できる。
- 🌱 グリーン規制への対応:韓国および国際的な持続可能性基準を満たすのに役立つ。
経済効果
ベネフィット | 説明 |
---|---|
材料の節約 | 原材料コストを最大80%削減 |
工具の排除 | 金型製作を回避して数万ドルを節約 |
市場投入までの時間を短縮 | AMはプロトタイピングと生産サイクルを短縮する |
在庫コストの削減 | オンデマンド生産と保管費用の削減 |
部品性能の向上 | 軽量で最適化された部品が総所有コストを削減 |
ケーススタディ釜山を拠点とする航空宇宙サプライヤー
釜山を拠点とする航空宇宙Tier-2サプライヤーは、金属積層造形に切り替えた後、チタン廃棄物を75%削減しました。同社は、Metal3DPの球状チタン合金パウダーを使用して、航空機キャビンで使用される複雑なブラケットとハウジングをプリントしました。
「以前は無垢のチタンビレットから部品を加工していましたが、材料の半分以上を無駄にしていました。今は必要な分だけを使うようになり、部品はさらに強くなりました"
- 釜山航空宇宙部品株式会社 CTO
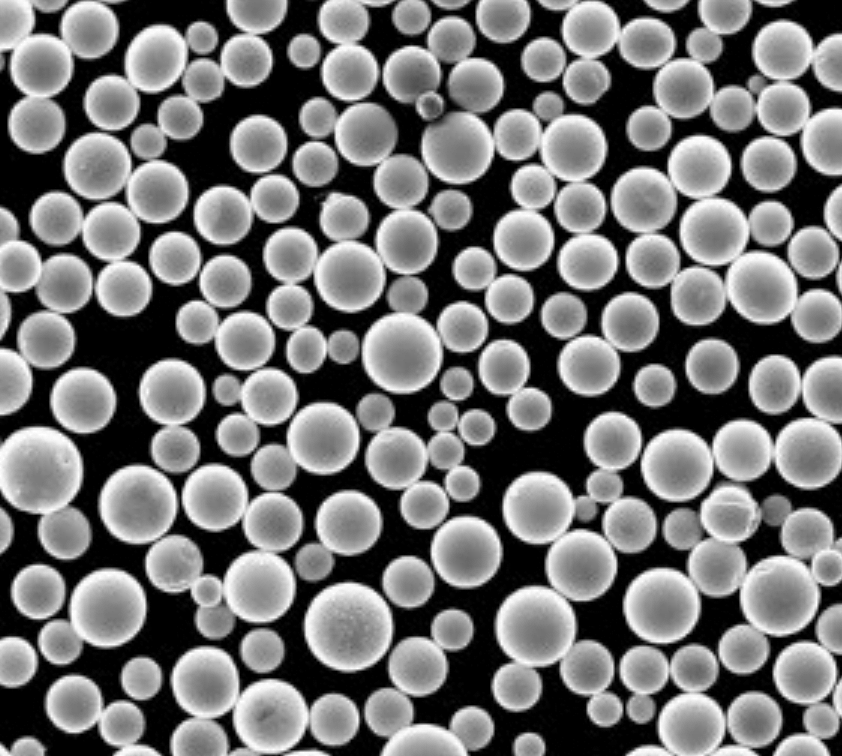
4.積層造形の恩恵を受ける釜山のトップ産業
釜山は産業活動の中心地であり、港へのアクセス、熟練した製造労働力、韓国および世界の主要市場への近接性から戦略的重要性を有している。釜山のいくつかの産業は、廃棄物を減らし生産効率を向上させるため、積層造形技術を急速に導入している。
釜山で積層造形を導入する主要産業
産業 | AMアプリケーション | 廃棄物削減のメリット |
---|---|---|
航空宇宙 | 軽量ブラケット、タービンブレード、構造部品 | チタンとアルミニウムの廃棄物を最大80%削減 |
医療機器 | カスタムインプラント、手術器具、補綴物 | 工具の無駄をなくし、患者に特化したソリューションを可能にする |
自動車 | エンジン部品、熱交換器、治具・備品 | スクラップを減らし、プロトタイピングを合理化 |
海洋工学 | プロペラ部品、ポンプハウジング、耐食性部品 | 最適化された形状により、原材料の使用量を削減 |
金型 | コンフォーマル冷却チャンネル、ダイインサート | 工具寿命を延ばし、余分な加工を減らす |
釜山における航空宇宙産業
釜山には、ボーイングやエアバスなどのグローバルOEMに供給する航空宇宙部品メーカーが数社ある。これらの企業は、部品の形状を最適化し、重量を減らし、チタンやインコネルなどの高価値材料の無駄を大幅に削減するために、金属積層造形に注目している。
- 適用例:Metal3DPの高性能Ti-6Al-4V粉末を使用して、釜山の航空宇宙企業がブラケット生産用のチタンビレットの廃棄量を70%削減しました。
医療分野無駄を省いた精密さ
この地域で成長している医療機器部門は、材料ロスを最小限に抑えながら患者固有のインプラントやツールを製造できるAMの能力から恩恵を受けている。電子ビーム溶解(EBM)のようなAM技術は、CoCrMoやTiNbZr合金の生体適合性金属インプラントの印刷に最適です。
- 例:Metal3DPの生体適合性粉末を使用したカスタム頭蓋インプラントは、病院の在庫廃棄物を削減し、手術結果を改善します。
医療および航空宇宙分野での積層造形についてご興味がおありですか?Metal3DPの 金属 3D プリント ソリューション ページ 実世界での応用を探求する。
5.積層造形は従来の方法と比べてどのように材料の無駄を削減するか
積層造形の最も強力な論拠の1つは、原材料の無駄を大幅に削減できることである。CNC機械加工、鍛造、鋳造などの従来の減法的手法と比較して、AMがどのようにこれを達成しているかを説明しよう。
減法製造:廃棄物問題
サブトラクティブ工法は、材料の塊から始まり、切断、穴あけ、研磨によって一部を取り除く。特に、チタン、コバルトクロム、ニッケル基合金などの高価な金属を扱う場合、大量のスクラップが発生する。
- 材料歩留まり:複雑な部品では30%を下回ることが多い。
- 二次廃棄物:切粉、クーラント、磨耗した工具
- 後処理:さらなる材料除去とエネルギー使用を追加
積層造形:効率的なレイヤー・バイ・レイヤー
積層造形は、部品の形状に必要な材料のみを使用して部品を一から作り上げる。粉末床溶融システムで未使用の粉末はリサイクルして再利用できるため、材料効率がさらに向上する。
基準 | 減法製造 | アディティブ・マニュファクチャリング |
---|---|---|
材料歩留まり | 20-50% | 90-98% |
必要な工具 | はい | いいえ |
スクラップ | 高い | 最小限 |
再利用性 | 低い | 高い(特に粉体) |
エネルギー消費 | 高い(機械加工、鍛造) | 下部(局所融合) |
廃棄物削減の定量化
プロセス | 初期素材 | 最終部品重量 | 廃棄物発生量 |
---|---|---|---|
CNC加工(チタン) | 10kgビレット | 2kg部分 | 廃棄物8kg |
パウダーベッド・フュージョン(AM) | 2.2 kg パウダー | 2kg部分 | 0.2 kg 未使用(リサイクル可能) |
このコントラストは、材料コストと持続可能性が重要な関心事である産業において、なぜAMが好まれる手法になりつつあるのかを示している。
6.Metal3DPが釜山で信頼できる積層造形パートナーである理由
産業グレードの積層造形に関しては、適切なサプライヤーを選択することが生産効率を左右します。中国の青島に本社を置くMetal3DPは、金属AMによる廃棄物の削減と部品性能の向上を目指す釜山およびアジア全域の製造業者にとって信頼できるパートナーです。
Metal3DP の特徴は何ですか?
業界をリードする金属3Dプリンター
- 高精度と大量生産
- 航空宇宙、自動車、医療用途に最適化
- 基幹部品の安定した印刷性能
✅ 高度な粉末製造能力
Metal3DPは、最先端のガスアトマイズとPREP(プラズマ回転電極プロセス)システムにより、高品質の球状金属粉末を製造します。
- 球形度が高く酸素含有量が低い
- 優れた流動性と充填密度
- レーザーシステムとEBMシステムの両方に対応
✅ 豊富なパウダー・ポートフォリオ
合金 | 申し込み | メリット |
---|---|---|
Ti-6Al-4V | 航空宇宙、医療 | 軽量、生体適合性、耐腐食性 |
CoCrMo | 整形外科、歯科 | 高強度、耐摩耗性、生体適合性 |
インコネル718 | ターボ機械 | 耐高温性、疲労性能 |
ステンレススチール316L | 一般工学 | 手頃な価格、耐腐食性 |
当社の全製品をご覧ください。 Metal3DP製品ページ.
✅ ターンキー積層造形ソリューション
- 機器 + パウダー + アプリケーション・サポート
- AMの設計と導入に関する技術コンサルティング
- 後処理および材料試験サービス
✅ アジア全域のB2Bクライアントからの信頼
釜山からバンコクまで、Metal3DPは信頼できるサプライチェーン、専門家によるコンサルティング、高性能材料でアジア太平洋地域の製造業者をサポートしています。
私たちの使命とグローバルな展開については、こちらをご覧ください。 会社概要ページ.
7.韓国でAM用高品質金属粉末を調達する方法
アディティブ・マニュファクチャリングのアウトプットの品質は、金属粉末の品質と直結しています。釜山および韓国全土の企業にとって、信頼性が高く、安定した高性能の粉末を調達することは、単なる材料の決定ではなく、戦略的な決定なのです。
パウダーの品質が重要な理由
- 流動性:粉末床溶融システムにおける層の均一性に影響
- 粒度分布:梱包密度と印刷解像度に影響
- 球形度:パウダーの固まりを抑え、のびを良くします。
- 純度:低い酸素と窒素レベルは、機械的完全性のために不可欠である。
B2Bバイヤーにとって重要な考慮事項
ファクター | 重要性 | 何を探すべきか |
---|---|---|
認証 | 材料のトレーサビリティと規格遵守の確保 | ISO13485、ASTM、AMS、GB規格 |
バッチの一貫性 | 再現性のある部品品質には欠かせない | 均一なPSD、化学組成 |
テクニカルサポート | 実装とトラブルシューティングの迅速化 | 冶金学者やAMエンジニアへのアクセス |
配送物流 | 生産のダウンタイムを最小限に抑えるために重要 | 現地倉庫保管または迅速な出荷オプション |
Metal3DPの粉末製造の優位性
Metal3DPは、レーザーおよび電子ビーム粉末床融合技術用に最適化された幅広い高性能金属粉末を製造しています。ガスアトマイズとPREPシステムにより、私たちのパウダーは以下を提供します:
- 高い真球度 (>95%)
- 優れた流動性
- 酸素と窒素の含有量が低い
- バッチ間の一貫性
釜山を拠点とするメーカーを含め、韓国全土の航空宇宙、医療、自動車分野の大手AMユーザーに供給しています。
当社の粉体技術と全合金ポートフォリオをご覧ください。 Metal3DP製品ページ.
釜山を拠点とする産業で人気のパウダー
合金 | 産業 | 特徴 |
---|---|---|
Ti-6Al-4V | 航空宇宙、医療 | 軽量、耐腐食性 |
CoCrMo | 整形外科 | 生体適合性、耐摩耗性 |
インコネル 625/718 | エネルギー, 海洋 | 高温、耐酸化性 |
316Lステンレス鋼 | 一般産業 | コスト効率に優れ、耐腐食性 |
私たちは、お客様のアプリケーションのニーズに合わせた標準的なパウダーとカスタマイズされたパウダーの両方を提供しています。
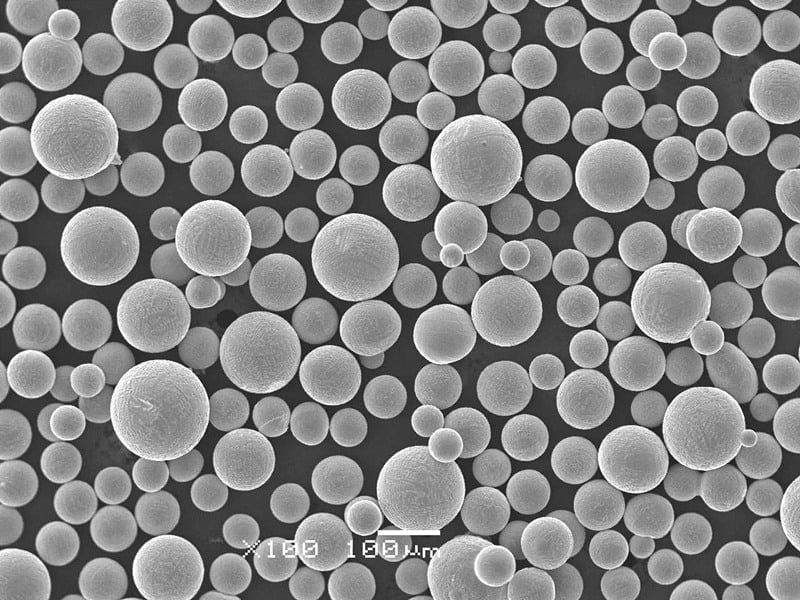
8.工場における積層造形のステップバイステップガイド
従来の工場環境で積層造形の導入を成功させるには、戦略的で段階的なアプローチが必要です。釜山の中規模部品サプライヤーであれ、大規模OEMであれ、構造化されたロードマップに従うことで、スムーズな統合とROIが実現します。
ステップ1:アプリケーションの適合性を評価する
✅ 高コスト、高廃棄部品の特定
デザインの複雑さやカスタマイズの必要性を探す。
現在のスクラップ率と工具費を評価する。
ヒント:航空宇宙用ブラケットや手術器具など、少量で高価値の部品から始める。
ステップ2:AMエキスパートとの提携
✅ 材料と機器の両方を提供するサプライヤーを選ぶ
技術サポートとトレーニングが利用可能であることを確認する。
✅ 実績とアプリケーションの専門知識を評価する。
Metal3DPは、SEBMプリンターから球状金属粉末、後処理コンサルティングに至るまで、完全なAMソリューションを提供しています。
当社の統合ソリューションがお客様のAMジャーニーをどのように加速させるかについては、当社のウェブサイトをご覧ください。 金属3Dプリンティングソリューションのページ.
ステップ3:適切なAM技術の選択
テクノロジー | 最適 | メリット |
---|---|---|
レーザー粉末床融合(LPBF) | 高解像度、小型部品 | 優れた表面仕上げ、精密 |
電子ビーム溶解(EBM) | 大きく密集した部分 | 製造速度が速く、残留応力が低い |
指向性エネルギー蒸着(DED) | 部品の修理や大規模な建設 | ハイブリッド製造に適用 |
ステップ4: インフラのセットアップ
✅ 電源、換気、不活性ガスシステムが整っていることを確認する。
粉体の取り扱いおよび保管プロトコルの確立 ✅ 粉体の取り扱いおよび保管プロトコルの確立
エンジニアリングおよび品質管理チームのトレーニング
ステップ5:パイロット、モニター、スケールアップ
いくつかの部品でパイロット生産を行う。
✅ 品質指標と材料利用率を監視する
✅ 徐々に規模を拡大し、無駄の多い減算的オペレーションを置き換える。
9.よくある質問釜山における廃棄物削減のためのアディティブ・マニュファクチャリング
アディティブ・マニュファクチャリングへの移行を検討している釜山のメーカー、サプライヤー、エンジニアからよく寄せられる質問をまとめた。
AMに切り替えた場合の典型的な廃棄物削減量は?
ほとんどのメーカーは、特にチタンやインコネルのような高価値の金属を使用する場合、サブトラクティブ加工と比較して70-90%の材料廃棄量の削減を経験しています。
アディティブ・マニュファクチャリングは小ロット生産に費用対効果があるか?
もちろんです。AMは金型が不要になり、セットアップ時間が短縮され、オンデマンド生産が可能になるため、少量多品種の生産環境に理想的です。
AMは韓国の環境規制をクリアするのに役立つか?
そうです。アディティブ・マニュファクチャリングは、エネルギー消費を削減し、材料の無駄を減らし、現地生産を可能にすることで、グリーン・マニュファクチャリングの目標をサポートする。
粉体のリサイクル性を確保するには?
高純度でPSDが制御された球状粉末を使用してください。Metal3DPのパウダーは、レーザーおよび電子ビームシステムの両方で高いリサイクル性を発揮するように設計されています。
Metal3DPを始めるには?
ご相談は、直接お問い合わせいただくか、以下のウェブサイトをご覧ください。 会社ホームページ をご覧ください。
結論:釜山における積層造形で廃棄物のない未来を築く
釜山がスマート産業ハブへと進化を続ける中、製造業者は持続可能性、効率性、革新性に沿った技術を取り入れる必要がある。積層造形、特に金属AMは、廃棄物を削減し、サプライチェーンを簡素化し、新しい設計の可能性を解き放つ比類のない機会を提供します。
航空宇宙、ヘルスケア、自動車、海洋工学のいずれに携わる方でも、今こそ3Dプリンティングがどのようにビジネスを変革できるかを探求する時です。
Metal3DPは、高品質のパウダー、信頼性の高いプリンティングシステム、アディティブマニュファクチャリングのためのエキスパートサポートを提供します。
今日から、あなたの変革を始めましょう。 会社概要ページ またはお問い合わせください。
🔗 使用した内部リンクのまとめ(合計5本)
アンカーテキスト | リンクページ |
---|---|
印刷方法ページ | https://met3dp.com/printing-methods/ |
金属 3D プリント ソリューション ページ | https://met3dp.com/metal-3d-printing/ |
Metal3DP製品ページ | https://met3dp.com/product/ |
会社概要ページ | https://met3dp.com/about-us/ |
会社ホームページ | https://met3dp.com/ |
シェアする
MET3DP Technology Co., LTDは、中国青島に本社を置く積層造形ソリューションのリーディングプロバイダーです。弊社は3Dプリンティング装置と工業用途の高性能金属粉末を専門としています。
関連記事
Met3DPについて
最新情報
製品
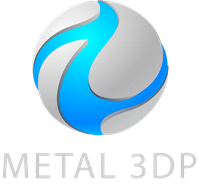
3Dプリンティングと積層造形用金属粉末