Aerospace Fixtures with Stable Properties 3D Printed in Invar
目次
Introduction: The Critical Role of Dimensional Stability in Aerospace Fixturing
In the demanding world of aerospace manufacturing, precision isn’t just a goal; it’s a fundamental requirement. From commercial airliners carrying hundreds of passengers to sophisticated satellites exploring distant planets, every component must be manufactured and assembled with exacting tolerances. Failure is not an option. Central to achieving this unparalleled level of accuracy are aerospace fixtures – the unsung heroes of the production line. These custom tools are essential for holding components securely, positioning them accurately during assembly, guiding machining processes, and verifying final dimensions.
However, the aerospace environment itself presents significant challenges. Components and the tooling used to create them are often subjected to considerable temperature fluctuations, whether during manufacturing processes involving heat, transit between climate-controlled facilities, or the operational environment of the final aircraft or spacecraft. Even minor thermal expansion or contraction in a fixture can lead to deviations that compromise the integrity and fit of critical aerospace parts. This makes 寸法安定性, particularly a low coefficient of thermal expansion (CTE), a paramount concern for many aerospace tooling applications.
Traditionally, manufacturing these complex and precise fixtures involved subtractive methods like CNC machining, often from large billets of material, leading to significant material waste and long lead times, especially for intricate designs. Enter 金属積層造形(AM), commonly known as metal 3D printing. This transformative technology offers a powerful alternative, enabling the creation of highly complex, lightweight, and functionally optimized fixtures with unprecedented speed and design freedom.
For applications demanding the utmost dimensional stability, materials like FeNi36 (commonly known as Invar) are indispensable. This unique nickel-iron alloy exhibits an extraordinarily low CTE near room temperature, making it ideal for fixtures used in sensitive inspection, metrology, and assembly operations where temperature variations cannot be allowed to affect accuracy. Combining the material properties of Invar with the manufacturing advantages of metal AM creates a potent solution for modern aerospace tooling challenges.
As a leading provider of additive manufacturing solutions, メット3dp specializes in leveraging advanced metal 3Dプリンティング technologies and high-performance metal powders to meet the stringent requirements of industries like aerospace. Headquartered in Qingdao, China, Met3dp provides comprehensive solutions, from industry-leading 3D printing equipment to specialized metal powders like FeNi36, enabling manufacturers to produce mission-critical parts and tooling with exceptional accuracy and reliability.
What Are Aerospace Fixtures Used For? Key Applications and Functions
Aerospace fixtures are indispensable tools used across the entire lifecycle of aircraft and spacecraft production, from initial component fabrication to final assembly and ongoing maintenance. Their primary role is to ensure consistency, accuracy, and efficiency in manufacturing processes. Procurement managers and engineers sourcing these tools need to understand their diverse applications to specify the right requirements for their aerospace tooling suppliers.
Key types and applications include:
- Assembly Jigs and Fixtures: These are perhaps the most common type. They securely hold multiple components in the correct orientation relative to each other while they are joined (e.g., riveting, bonding, welding). Complex assemblies like wings, fuselages, and engine pylons rely heavily on large, precise assembly jigs to maintain overall geometry.
- Function: Ensure accurate alignment, prevent movement during joining, improve repeatability, reduce assembly time.
- Inspection Fixtures: Used in conjunction with CMMs (Coordinate Measuring Machines), vision systems, or manual gauges to check the dimensional accuracy of manufactured parts. These fixtures must hold the part securely and repeatably in a known position without distorting it. For high-precision measurements, the fixture’s dimensional stability is paramount, making Invar a common material choice.
- Function: Provide stable and repeatable part location for measurement, guarantee inspection accuracy, facilitate quality control processes.
- Machining Fixtures: Hold raw materials or partially finished components securely during CNC machining operations (milling, drilling, turning). They must withstand significant cutting forces while maintaining precise positioning of the workpiece relative to the cutting tool.
- Function: Ensure accurate material removal, resist tool forces, guarantee dimensional accuracy of machined features, improve safety.
- CMM Fixtures (Coordinate Measuring Machine Fixtures): A subset of inspection fixtures specifically designed for use with CMMs. They often feature modular designs, kinematic mounting points, and low-contact-area supports to maximize probe access and minimize part distortion. Stability and rigidity are critical.
- Function: Optimize CMM measurement routines, ensure measurement repeatability, minimize setup time.
- Welding Fixtures: Hold parts in alignment during welding processes. They must withstand the heat generated during welding without significant distortion that could misalign the parts. They also need to provide adequate access for the welding torch and often incorporate grounding points.
- Function: Maintain part alignment during thermal cycles, ensure weld joint quality, manage heat dissipation, ensure operator safety.
- Trim and Drill Fixtures: Guide cutting tools (routers, drills) to ensure holes, cutouts, and edge trims are performed in the correct locations on components, often composite panels or sheet metal parts.
- Function: Ensure accurate hole patterns and trim lines, improve process repeatability, reduce manual layout time.
Industries and Procurement Considerations:
While intrinsically linked to aerospace manufacturers, the need for these fixtures extends to:
- Space and Satellite Manufacturing: Requiring extreme precision and often utilizing materials designed for vacuum and thermal cycling.
- Defense Contractors: Building military aircraft, missiles, and ground systems with rigorous specifications.
- Maintenance, Repair, and Overhaul (MRO) Facilities: Utilizing fixtures for component repair, inspection, and re-assembly, often requiring custom or legacy tooling solutions.
について procurement managers そして supply chain specialists, sourcing aerospace fixtures involves ensuring suppliers can meet stringent quality standards (e.g., AS9100 compliance), provide necessary documentation (material certifications, inspection reports), guarantee repeatability for 一括注文, and offer competitive lead times. Choosing an aerospace fixture manufacturer or supplier with proven expertise and robust quality systems is crucial.
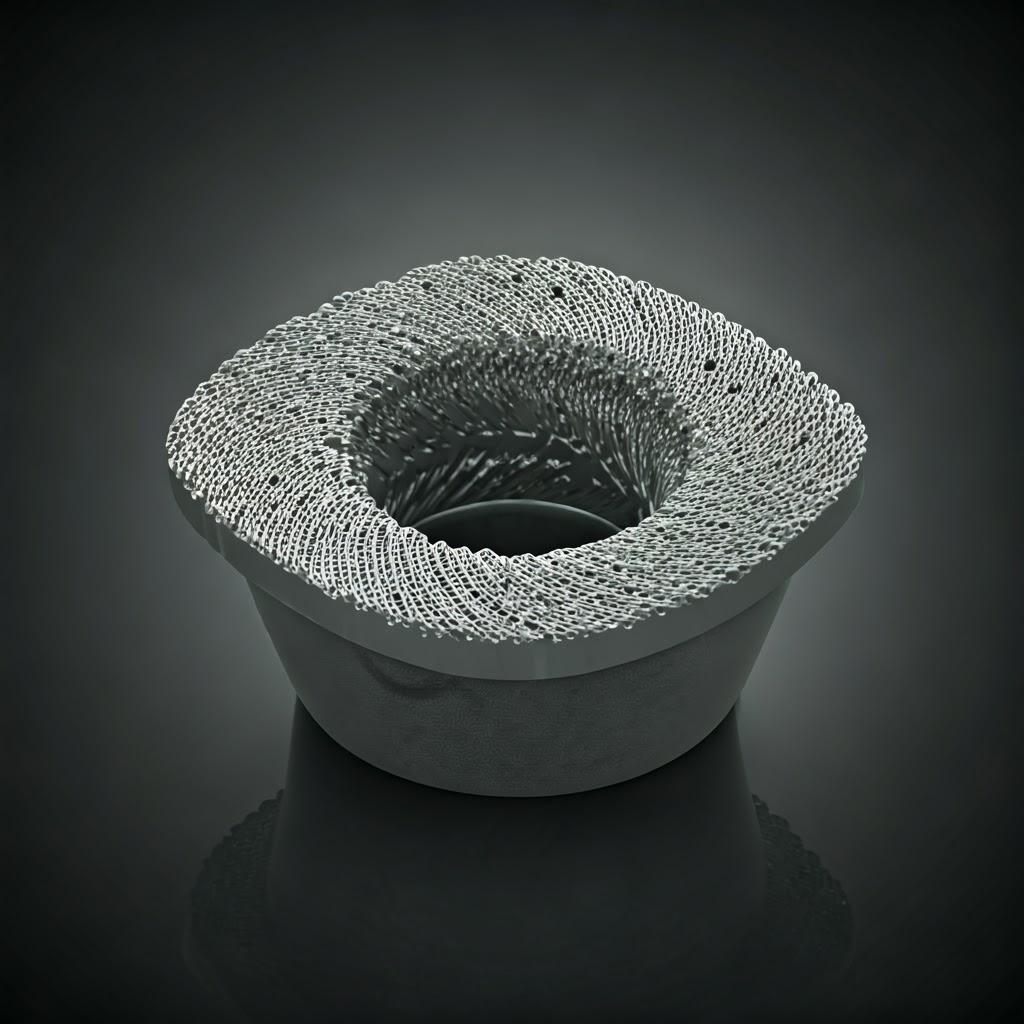
Why Use Metal 3D Printing for Aerospace Fixtures? Advantages Over Traditional Manufacturing
For decades, aerospace fixtures were predominantly manufactured using traditional subtractive methods, primarily CNC machining large blocks or plates of metal (like aluminum, steel, or Invar) or through casting and subsequent machining. While effective, these methods present limitations, particularly when dealing with complex geometries, urgent timelines, or the need for lightweight tooling. Metal additive manufacturing offers compelling advantages that directly address these limitations, making it an increasingly preferred method for industrial fixture production.
Let’s compare metal AM (specifically powder bed fusion techniques like Selective Laser Melting – SLM/Laser Powder Bed Fusion – LPBF, and Selective Electron Beam Melting – SEBM) with traditional approaches:
Metal AM vs. Traditional Manufacturing for Fixtures:
特徴 | 金属積層造形(AM) | Traditional (CNC Machining / Casting) | Advantage of AM for Fixtures |
---|---|---|---|
デザインの自由 | High; enables complex internal channels, organic shapes, lattices. | Moderate to Low; limited by tool access, draft angles (casting). | Creation of conformal cooling/vacuum channels, topology optimization, part consolidation. |
リードタイム | Fast, especially for complex or low-volume parts. Digital setup. | Can be long, especially for complex parts requiring multiple setups. | Rapid prototyping, faster iteration, quick response for urgent tooling needs (AOG situations). |
廃棄物 | Low; uses only necessary material (powder). | High; significant waste from subtractive machining (“buy-to-fly ratio”). | More sustainable, lower raw material cost impact for expensive alloys like Invar. |
Complexity Cost | Less sensitive to complexity; cost driven by volume/height. | High; complex geometries significantly increase machining time/cost. | Economical production of highly customized or intricate fixtures. |
軽量化 | Excellent; topology optimization easily integrated. | Possible but often requires complex machining strategies. | Easier handling of large fixtures, reduced inertia, potential for robotic integration. |
部品の統合 | High potential; multiple components can be printed as one unit. | Low; assembly of multiple machined/cast parts is common. | Reduced assembly time, fewer potential failure points, simplified supply chain. |
Export to Sheets
Key Benefits of AM for Aerospace Fixtures:
- Complex Geometries for Enhanced Functionality: AM allows engineers to design fixtures with features impossible to machine traditionally. Examples include:
- Conformal Cooling/Vacuum Channels: Channels precisely following the contour of the part being held can improve cooling efficiency during machining or provide uniform vacuum clamping.
- Internal Lattice Structures: Reducing weight significantly while maintaining necessary stiffness, crucial for large assembly or inspection jigs that need to be moved manually or robotically.
- Lightweighting through Topology Optimization: Software tools can analyze load paths and remove material from non-critical areas, resulting in fixtures that are significantly lighter than their traditionally manufactured counterparts. This improves ergonomics, reduces strain on supporting structures (like CMM beds), and can lower shipping costs for wholesale fixture distribution.
- パーツの統合: A fixture that might traditionally require assembling ten machined components can potentially be redesigned and printed as a single, monolithic part. This reduces part count, eliminates assembly labor and tolerances stack-up issues, and simplifies procurement and inventory management.
- ラピッドプロトタイピングと反復: Need a slight modification to a fixture design? With AM, a new iteration can often be printed and ready for testing in days, compared to weeks for traditional methods. This accelerates the development cycle for new aircraft programs or manufacturing processes.
- On-Demand Production and Digital Inventory: Fixture designs exist as digital files (CAD data). Instead of stocking bulky physical fixtures, companies can maintain a digital inventory and print fixtures only when needed. This reduces warehousing costs and allows for easy replacement of damaged or worn tooling. Met3dp’s robust printing capabilities support this model, providing reliable on-demand manufacturing.
Met3dp utilizes industry-leading 金属3Dプリンティング technologies, including high-power laser and electron beam systems, capable of producing dense, high-resolution metal parts. Our printers offer substantial build volumes and exceptional accuracy, making them suitable for a wide range of aerospace fixture sizes and complexities. By partnering with Met3dp, aerospace manufacturers and their tier suppliers gain access to these advantages, enabling them to optimize their tooling strategies.
Recommended Materials: FeNi36 (Invar) and 316L for Aerospace Tooling Stability and Durability
Choosing the right material is critical for the performance and longevity of any aerospace fixture. The selection depends heavily on the specific application requirements, particularly dimensional stability, strength, durability, and cost. For metal 3D printed fixtures, two materials stand out for aerospace applications, albeit for different reasons: FeNi36 (Invar) そして 316Lステンレス鋼. Both are available as high-quality, spherical powders optimized for additive manufacturing from specialist 金属粉サプライヤー like Met3dp.
FeNi36 (Invar 36): The Champion of Thermal Stability
Invar is a unique nickel-iron alloy containing approximately 36% nickel. Its defining characteristic, and the primary reason for its use in aerospace tooling, is its incredibly low Coefficient of Thermal Expansion (CTE) at temperatures around and below room temperature.
- Why Low CTE Matters: In aerospace, precision is often measured in microns. If an inspection fixture holding a critical wing spar expands or contracts even slightly due to a change in shop floor temperature between morning and afternoon, the measurements taken could be inaccurate, potentially leading to out-of-tolerance parts passing inspection. Invar’s stability minimizes this variable. Its CTE is roughly one-tenth that of steel and one-twentieth that of aluminum near room temperature.
- 代表的な用途 CMM fixtures, optical benches, laser positioning tools, composite layup molds (especially master molds or tooling where thermal cycling needs to be minimized), alignment jigs for sensitive components.
- 機械的特性: While prized for its low CTE, Invar is not a high-strength material compared to aerospace steels or titanium alloys. It offers moderate strength and hardness, sufficient for many fixture applications where it primarily serves a positioning and holding function rather than bearing extreme mechanical loads. Its properties are generally isotropic when printed and properly heat-treated.
- AM Considerations: Printing Invar requires careful control over process parameters and thermal management during the build to minimize internal stresses, which can otherwise lead to distortion. Post-print heat treatment (annealing) is typically mandatory to relieve stress and achieve the desired low CTE state and dimensional stability. Met3dp leverages its deep expertise in materials science and process optimization, supported by advanced equipment like our SEBM printers, to successfully process challenging materials like Invar. Our advanced powder making system, utilizing gas atomization, produces FeNi36 powder with high sphericity and flowability, crucial for achieving dense and reliable printed parts.
- Procurement: Invar is a relatively expensive alloy due to its high nickel content and specialized production. Using AM can mitigate some costs by reducing material waste compared to machining from solid billets, making it more viable for aerospace procurement budgets focused on performance.
316L Stainless Steel: The Versatile Workhorse
316L is an austenitic stainless steel alloy containing chromium, nickel, and molybdenum. It is one of the most widely used materials in metal AM due to its excellent combination of properties, printability, and cost-effectiveness.
- プロパティ
- 耐食性: Excellent resistance to atmospheric corrosion and various chemicals, making it suitable for fixtures used in different shop environments.
- Strength and Ductility: Offers good mechanical strength and toughness, sufficient for many general-purpose fixtures, including some machining and assembly applications.
- 溶接性: Easily weldable if modifications or repairs are needed (though less common for AM parts).
- 費用対効果: Significantly less expensive than Invar or titanium alloys.
- When to Choose 316L: It’s the ideal choice for aerospace fixtures where the extreme thermal stability of Invar is not the primary requirement, but good mechanical properties, durability, corrosion resistance, and reasonable cost are important.
- 代表的な用途 General assembly jigs, handling fixtures, non-critical machining fixtures, support structures, brackets, MRO tooling where cost is a major factor.
- AM Considerations: 316L is known for its excellent printability across various powder bed fusion platforms (LPBF and SEBM). It generally requires less stringent process control than Invar regarding thermal management, although stress relief heat treatments are still recommended for optimal performance and dimensional accuracy.
- 空室状況 As a widely used industrial material, high-quality 316L powder is readily available from reputable metal AM powder manufacturers like Met3dp, ensuring a stable supply chain for wholesale or bulk fixture production.
Material Comparison for Aerospace Fixtures:
プロパティ | FeNi36 (Invar) | 316Lステンレス鋼 | Key Consideration for Fixtures |
---|---|---|---|
熱膨張係数(CTE) (Approx. near RT) | Very Low (~1.2 ppm/°C) | Moderate (~16 ppm/°C) | インバー for critical dimensional stability (inspection, CMM). |
Tensile Strength (Typical) | Moderate (~480-550 MPa) | Good (~500-600 MPa) | 316L is slightly stronger, suitable for higher load fixtures. |
耐食性 | Fair (can rust in humid conditions) | 素晴らしい | 316L for durability in various shop environments. |
相対コスト | 高い | 中程度 | Cost/benefit analysis based on stability needs. |
Printability / Post-Processing | Challenging (stress control) | Good (well-understood) | Requires expert process control for Invar. |
Primary Application Driver | 寸法安定性 | Durability & Cost-Effectiveness | Match material to the fixture’s most critical function. |
Export to Sheets
Met3dp’s commitment extends to providing not just the printing service but also the high-quality materials necessary for success. Our portfolio includes a wide range of 高品質の金属粉, optimized for additive manufacturing through techniques like gas atomization and Plasma Rotating Electrode Process (PREP), ensuring high sphericity, good flowability, and low oxygen content for dense, high-performance parts. Whether your aerospace fixture demands the unparalleled stability of Invar or the robust versatility of 316L, Met3dp has the materials and expertise to deliver.
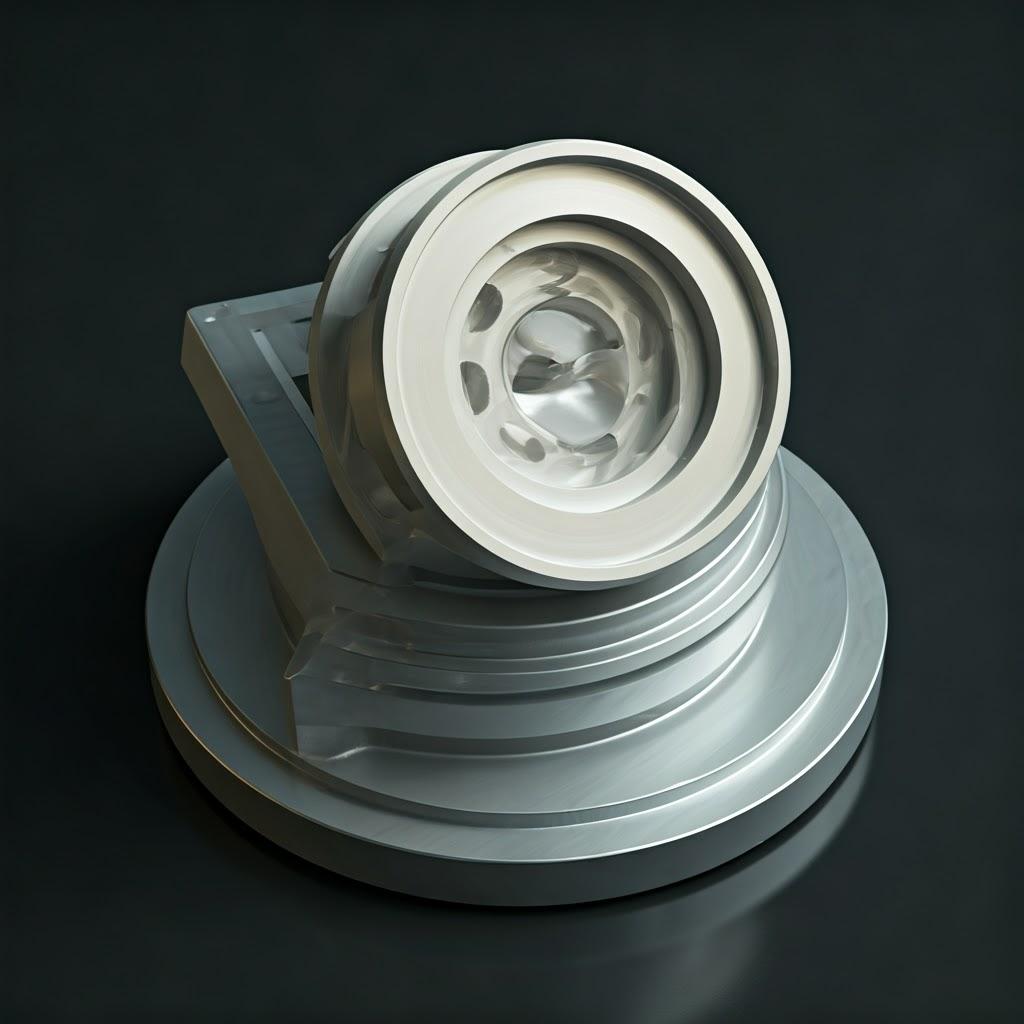
Design Considerations for Additively Manufactured Aerospace Fixtures (DfAM)
Simply replicating a traditionally designed fixture using additive manufacturing often fails to capture the full potential of the technology. To truly leverage the benefits of metal 3D printing – lightweighting, improved functionality, part consolidation, and faster production – engineers must embrace 積層造形設計 (DfAM) principles. Applying DfAM specifically to aerospace fixtures can result in tools that are not only effective but also more ergonomic, cost-efficient, and tailored to their specific function.
Key DfAM considerations for aerospace fixtures include:
- Topology Optimization and Lightweighting:
- Concept: Use software algorithms to analyze the load paths within a fixture design and remove material from areas that do not contribute significantly to stiffness or strength.
- Benefit: Can achieve substantial weight reductions (often 30-60% or more) compared to solid designs, while maintaining or even increasing rigidity. This is critical for large assembly jigs or CMM fixtures that need to be handled manually or mounted on equipment with weight limits.
- Implementation: Define load cases, keep-out zones (e.g., clamping points, datum surfaces), and manufacturing constraints (minimum thickness). The software generates an organic, optimized shape.
- 格子構造:
- Concept: Incorporate internal geometric patterns (strut-based, triply periodic minimal surfaces – TPMS) to fill volumes instead of using solid material.
- Benefit: Provides excellent stiffness-to-weight ratios, allows for integration of fluid channels, and can aid in thermal management during printing.
- アプリケーション Ideal for bulky fixture bodies where overall stiffness is required but solid material is unnecessary weight.
- Minimum Feature Size and Wall Thickness:
- Understanding Limits: Metal AM processes have limitations on the smallest features (pins, holes) and thinnest walls they can reliably produce. This varies by machine and material but is often in the range of 0.4-1.0 mm.
- Design Rule: Ensure critical features exceed these minimums. Avoid overly thin walls that may warp or fail during printing or use. Met3dp’s technical team can provide guidance based on our specific equipment capabilities, including our advanced SEBM プリンター.
- Support Structure Strategy:
- Necessity: Most metal AM processes require support structures for overhanging features (typically below 45 degrees from the horizontal) to prevent collapse and anchor the part to the build plate.
- DfAM Approach:
- Orientation: Orient the part on the build plate to minimize the amount of support needed (self-supporting angles).
- Design Integration: Modify geometries slightly (e.g., use chamfers instead of sharp overhangs) to make them self-supporting.
- アクセシビリティ: Design fixtures so that support structures are easy to access and remove during post-processing without damaging the part.
- Contact Points: Minimize the contact area between supports and the final part surface to reduce witness marks.
- Designing for Post-Processing:
- Machining Allowances: If ultra-high precision is required on specific surfaces (e.g., datum planes, mating interfaces), design these areas with extra material (“machining stock” or “offset”) that can be accurately CNC machined after printing. Typically, 0.5-1.0 mm of stock is sufficient.
- Tool Access: Ensure that areas requiring machining or specific surface finishing are accessible to the necessary tools (milling cutters, grinders, polishing tools).
- Integrating Functional Features:
- パーツの統合: Combine multiple components (brackets, clamps, locators) into a single printed part.
- Embedded Functionality: Design integrated clamping mechanisms, standardized mounting points (e.g., ball lock receivers), vacuum ports/channels, air cooling channels, or even channels for sensors.
- Identification: Include embossed or engraved part numbers, logos, or instructions directly into the design.
Leveraging DfAM requires a shift in thinking from subtractive constraints to additive possibilities. Partnering with an experienced metal 3D printing service provider like Met3dp early in the design phase is highly recommended. Our application development team can assist aerospace engineers and fixture designers in optimizing their concepts for additive manufacturing, ensuring functionality, printability, and cost-effectiveness.
Achievable Tolerance, Surface Finish, and Dimensional Accuracy in Metal AM Fixtures
Understanding the levels of precision achievable with metal additive manufacturing is crucial for setting realistic expectations and determining the necessary post-processing steps for aerospace fixtures. While AM technology is advancing rapidly, it’s important to differentiate between as-built accuracy and the final accuracy achievable after post-processing.
Tolerances:
- As-Built Tolerances: Parts produced using powder bed fusion (LPBF/SEBM) typically achieve dimensional tolerances in the range of ±0.1 mm to ±0.2 mm for smaller features, or ±0.1% to ±0.2% of the nominal dimension for larger features.
- Factors Influencing Tolerance:
- Printer Calibration & Condition: Regular calibration and maintenance of the AM system are critical. Met3dp prides itself on operating industry-leading equipment maintained for optimal performance and accuracy.
- 素材: Different materials behave differently during melting and solidification. The inherent stability of Invar, once properly heat-treated, can contribute to holding tighter tolerances post-build compared to materials with higher residual stress.
- Part Size and Geometry: Larger parts and complex geometries are more susceptible to thermal distortion during the build, potentially widening tolerances.
- Thermal Stresses: Residual stresses built up during printing can cause minor warping or deviation after the part is removed from the build plate. Careful process parameter control and optimized build strategies help mitigate this.
- サポート体制: The location and removal of supports can slightly affect the dimensions of adjacent surfaces.
- Achieving Tighter Tolerances: For critical features requiring tolerances tighter than the as-built capability (e.g., < ±0.05 mm), post-machining is necessary. This involves CNC machining specific surfaces or features after the printing and heat treatment steps.
表面仕上げ:
- As-Built Surface Finish: The surface roughness (typically measured as Ra) of as-built metal AM parts depends heavily on the process (LPBF generally yields smoother surfaces than SEBM), material, particle size distribution of the powder, layer thickness, and the orientation of the surface relative to the build direction.
- Typical Values: As-built Ra values often range from 5 µm to 20 µm (micrometers). Upward-facing horizontal surfaces tend to be smoother, while downward-facing surfaces impacted by support structures and angled surfaces are typically rougher.
- 表面仕上げの改善: If a smoother finish is required for functional reasons (e.g., reducing friction, sealing surfaces) or aesthetics, various post-processing methods can be employed:
- Bead Blasting / Sanding: Creates a uniform matte finish, removing loose powder particles (Ra might improve slightly or stay similar but appear more uniform).
- Tumbling / Vibratory Finishing: Can smooth edges and surfaces for batches of smaller parts.
- Polishing / Lapping: Can achieve very smooth, mirror-like finishes (Ra < 0.8 µm or even lower) but is typically localized to specific areas due to labor intensity.
- 機械加工: Produces finishes comparable to traditional machining (Ra 0.8 µm – 3.2 µm or better).
寸法精度:
Dimensional accuracy refers to how closely the final part conforms to the intended CAD model dimensions. It encompasses both tolerance and the absence of geometric distortions like warping. Achieving high dimensional accuracy in AM aerospace fixtures relies on:
- High-Quality Input: Accurate CAD model, appropriate DfAM application.
- Optimized Process Parameters: Correct energy input, scan strategy, layer thickness, thermal management.
- Robust Equipment: Well-maintained and calibrated printers, like Met3dp’s fleet, designed for industrial accuracy and reliability.
- Effective Post-Processing: Proper stress relief and machining of critical features.
- 厳格な品質管理: In-process monitoring and final inspection (e.g., CMM) to verify dimensions.
Met3dp combines advanced printing technology with meticulous process control and quality assurance protocols to maximize the as-built accuracy of aerospace fixtures and provides comprehensive post-processing solutions to meet the most demanding tolerance and finish requirements.
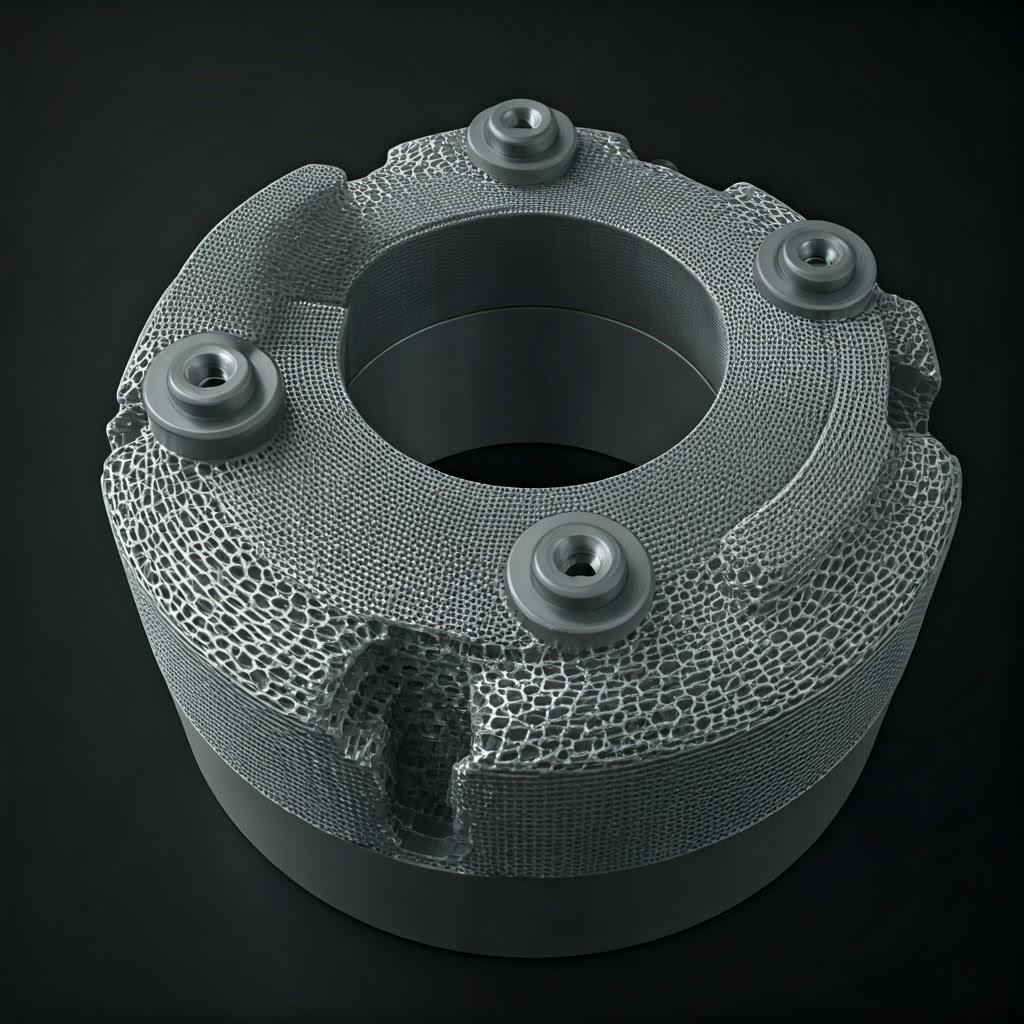
Post-Processing Requirements for 3D Printed Aerospace Fixtures
Additive manufacturing is rarely the final step in producing a functional aerospace fixture. Post-processing encompasses a series of essential stages required to transform the as-built part from the printer into a finished tool ready for use on the production floor. The specific steps depend on the material, design complexity, and application requirements. For aerospace fixtures, especially those made from Invar, post-processing is critical for achieving the desired properties and accuracy.
一般的な後処理には次のようなものがある:
- Stress Relief / Heat Treatment:
- 目的 To relieve internal stresses built up during the layer-by-layer printing process and to achieve the desired material microstructure and properties.
- Importance for Invar: Absolutely critical. A specific annealing cycle is required not only to minimize stress (preventing distortion over time) but also to stabilize the material’s microstructure, ensuring it achieves its characteristic ultra-low Coefficient of Thermal Expansion (CTE). Skipping or improperly performing this step negates the primary reason for choosing Invar.
- Importance for 316L: Highly recommended for stress relief, improving dimensional stability and mechanical properties, especially for fixtures subjected to cyclic loading or tight tolerances.
- プロセス Involves heating the part in a controlled atmosphere furnace to specific temperatures for defined durations, followed by controlled cooling. Parameters vary significantly by material.
- Part Removal from Build Plate:
- プロセス Typically done using wire EDM (Electrical Discharge Machining) or a bandsaw to carefully cut the part(s) away from the base plate they were printed on.
- 支持構造の撤去:
- 目的 To remove the temporary structures used during printing.
- 方法: Can range from manual breaking/clipping for accessible supports to more involved methods like CNC machining or grinding for supports in intricate areas. DfAM plays a key role in making this step easier.
- Consideration: Care must be taken not to damage the part surface during support removal. Minor witness marks where supports were attached are common.
- CNC Machining (If Required):
- 目的 To achieve tighter tolerances (typically < ±0.1 mm), specific surface finishes (e.g., Ra < 1.6 µm), or create features that are difficult to print accurately (e.g., sharp edges, threaded holes).
- アプリケーション Machining datum surfaces, locating pins/bores, mating interfaces, critical dimensions identified on the engineering drawing.
- Consideration: Requires careful setup to accurately locate the AM part in the CNC machine. Designing reference features into the AM part can facilitate this.
- 表面仕上げ:
- 目的 To improve surface smoothness, aesthetics, or prepare the surface for coating.
- 方法:
- Bead Blasting: Provides a clean, uniform matte finish.
- Sanding/Grinding: Manual or automated methods to remove layer lines or smooth specific areas.
- 研磨: Achieves a smooth, often reflective surface for low-friction or sealing applications.
- Tumbling/Vibratory Finishing: Batch process suitable for smaller, durable parts.
- Inspection and Validation:
- 目的 To verify that the final fixture meets all dimensional and tolerance specifications defined in the design.
- 方法: Primarily using Coordinate Measuring Machines (CMMs), laser scanners, or traditional metrology tools (calipers, micrometers). Non-Destructive Testing (NDT) methods like CT scanning might be used for highly critical parts to check for internal defects, though less common for typical fixtures.
- Documentation: Generating inspection reports is often a requirement for aerospace components and tooling.
Partnering with a full-service AM provider like Met3dp simplifies this multi-stage process. We offer or manage the necessary post-processing steps, including specialized heat treatments for alloys like Invar, precision machining, various finishing options, and rigorous quality inspection, ensuring that the final aerospace fixture delivered meets all specifications.
Common Challenges in 3D Printing Aerospace Fixtures and Mitigation Strategies
While metal additive manufacturing offers significant advantages for producing aerospace fixtures, it’s not without its challenges. Understanding these potential hurdles and the strategies to overcome them is crucial for successful implementation. Aerospace engineers and procurement managers should discuss these points with their chosen AM supplier.
- Distortion and Warping:
- チャレンジ: The rapid heating and cooling cycles inherent in powder bed fusion can create significant internal stresses within the part. These stresses can cause the part to warp during the build, upon removal from the build plate, or even later during heat treatment if not managed correctly. This is particularly pronounced in larger parts or materials like Invar.
- Mitigation Strategies:
- Thermal Simulation: Software simulation before printing can predict areas prone to high stress and distortion, allowing for adjustments to orientation or support strategy.
- Optimized Orientation & Supports: Carefully selecting the build orientation and designing robust support structures to anchor the part effectively.
- Process Parameter Control: Fine-tuning laser/electron beam power, scan speed, and layer thickness. Met3dp utilizes optimized parameter sets developed through extensive experience.
- Stress Relief Heat Treatment: Essential step performed immediately after printing, often while the part is still on the build plate, to relax internal stresses before significant distortion occurs.
- Support Removal Difficulties:
- チャレンジ: Supports in complex internal channels or hard-to-reach areas can be extremely difficult and time-consuming to remove, potentially damaging the part in the process.
- Mitigation Strategies:
- DfAM: Designing parts to be self-supporting where possible, maximizing accessibility to supported areas.
- Specialized Support Structures: Using support types designed for easier removal (e.g., thinner contact points, specific geometries).
- Advanced Removal Techniques: Utilizing methods like electrochemical machining or abrasive flow machining for internal channels, although these add cost and complexity. Careful planning during the design phase is the best approach.
- Porosity and Density:
- チャレンジ: Insufficient melting or trapped gas can lead to small voids (porosity) within the printed part. While fixtures may not always require the 100% density needed for flight-critical components, significant porosity can compromise strength, stiffness, and dimensional stability.
- Mitigation Strategies:
- High-Quality Powder: Using spherical, highly flowable metal powders with low oxygen content and controlled particle size distribution, such as those produced by Met3dp’s advanced gas atomization process.
- Optimized Print Parameters: Ensuring sufficient energy density to fully melt the powder layers. Met3dp develops robust parameters for each material/machine combination.
- Controlled Atmosphere: Maintaining a high-purity inert gas environment (Argon or Nitrogen) in the build chamber to minimize oxidation.
- 熱間静水圧プレス(HIP): For applications demanding the absolute highest density, HIP (applying high temperature and pressure) can be used post-print to close internal pores (adds cost and lead time).
- Achieving and Verifying Tight Tolerances:
- チャレンジ: Consistently achieving tolerances below ±0.1 mm directly from the printer is difficult. Verifying these tolerances across complex geometries also requires sophisticated metrology.
- Mitigation Strategies:
- Process Control & Calibration: Maintaining printers in optimal condition.
- Designing for Machining: Explicitly planning for post-machining of critical features (as discussed in DfAM and Post-Processing sections).
- Robust Quality Management System (QMS): Implementing rigorous inspection protocols using calibrated CMMs or scanners at various stages. Met3dp operates under a stringent QMS to ensure parts meet specifications.
Successfully navigating these challenges requires a combination of design expertise, material science knowledge, precise process control, and comprehensive post-processing capabilities. Met3dp’s decades of collective expertise in metal additive manufacturing positions us as a reliable partner capable of tackling complex aerospace fixture projects and delivering high-quality, dependable tooling solutions.
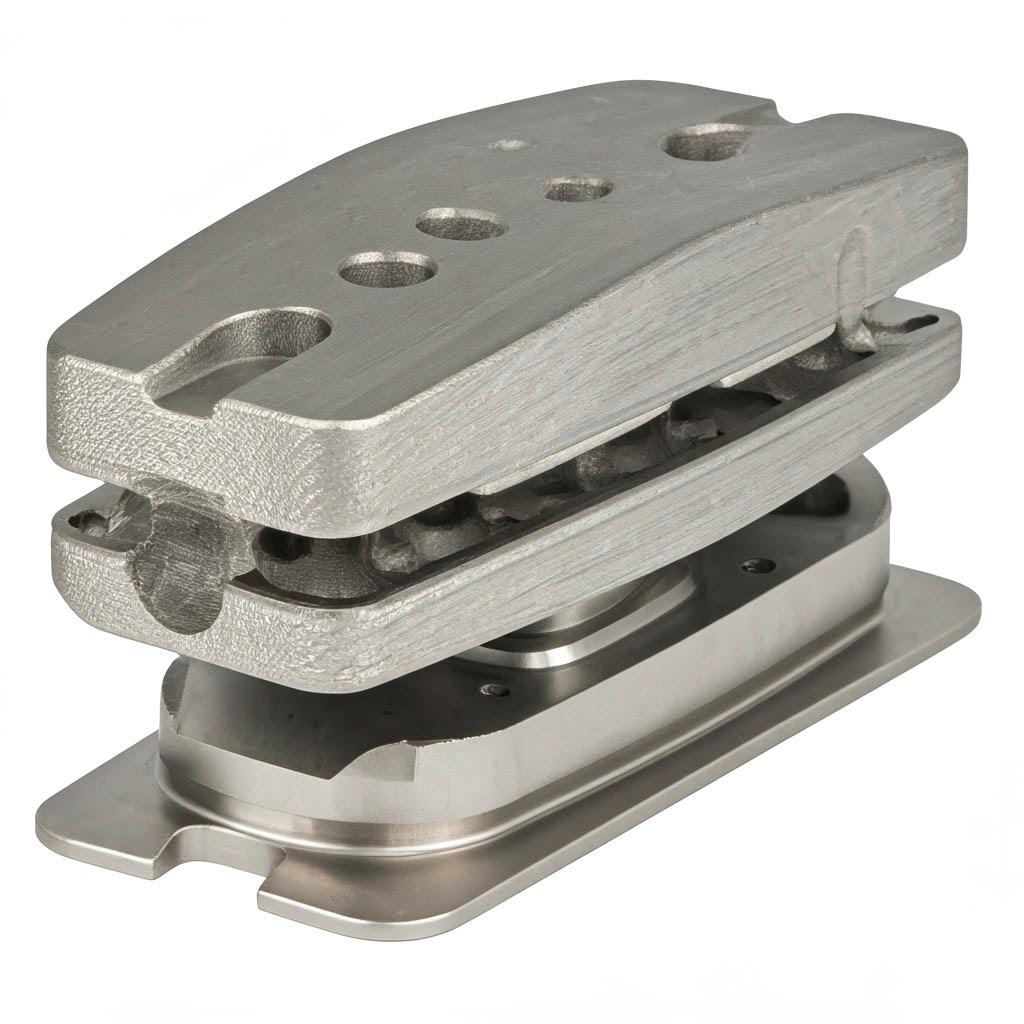
How to Choose the Right Metal 3D Printing Service Provider for Aerospace Fixtures
Selecting the right additive manufacturing partner is as critical as choosing the right material or optimizing the design, especially for demanding aerospace applications. The quality, reliability, and dimensional accuracy of your 3D printed fixtures heavily depend on the capabilities and expertise of your chosen AM supplier. For engineers and procurement managers evaluating potential service providers, here are key criteria to consider:
- Aerospace Industry Experience & Certifications:
- Requirement: Proven track record working with aerospace clients and understanding their specific needs (traceability, documentation, quality expectations).
- Look For: Ideally, AS9100 certification (the quality management standard for Aviation, Space, and Defense organizations) or at minimum a robust ISO 9001 certified Quality Management System (QMS) with demonstrated aerospace project experience. Ask for case studies or references.
- Material Expertise & Availability:
- Requirement: Specific, demonstrated experience in processing the required materials, particularly challenging alloys like FeNi36 (Invar). Understanding the nuances of printing parameters and heat treatment is crucial.
- Look For: A provider that not only lists the material but can discuss successful projects, share material datasheets based on their processes, and potentially offer material certifications. Access to high-quality, aerospace-grade metal powders is essential. Met3dp manufactures a wide range of 高性能金属粉末, including Invar and 316L, ensuring material quality and consistency.
- Technological Capabilities:
- Requirement: Access to appropriate industrial-grade metal AM systems (e.g., Laser Powder Bed Fusion – LPBF, Selective Electron Beam Melting – SEBM) with sufficient build volume for your fixture sizes and the necessary precision.
- Look For: Information on their specific printer fleet, documented accuracy and resolution capabilities, build envelope dimensions, and suitability for the chosen material (e.g., SEBM can be advantageous for certain materials prone to stress). Met3dp utilizes industry-leading printers known for their reliability and accuracy.
- Integrated Post-Processing Capabilities:
- Requirement: The ability to manage or perform all necessary post-processing steps in-house or through vetted partners. This includes critical heat treatments (especially for Invar), support removal, precision CNC machining, surface finishing, and inspection.
- Look For: A provider offering a seamless, end-to-end solution from print to finished part. This simplifies the supply chain and ensures accountability. Ask about their heat treatment furnace capabilities (atmosphere control, calibration) and CNC machining tolerances.
- Robust Quality Management System (QMS):
- Requirement: A comprehensive QMS covering process control, material traceability (from powder batch to final part), equipment calibration, operator training, and non-conformance management.
- Look For: Documented procedures, evidence of process monitoring, and rigorous final inspection protocols, often including CMM reports as standard deliverables for aerospace tooling.
- Lead Time, Capacity, and Scalability:
- Requirement: Ability to meet project deadlines and potentially scale production for larger orders or wholesale fixture supply agreements.
- Look For: Transparency about current lead times, available capacity, and experience handling projects of similar scope or volume.
- Technical Support and Collaboration:
- Requirement: Access to knowledgeable engineers who can provide DfAM guidance, discuss technical trade-offs, and collaborate on finding the optimal manufacturing solution.
- Look For: A provider who acts as a partner rather than just a print bureau. Responsiveness, clear communication, and a willingness to engage technically are key indicators.
Met3dp embodies these qualities, offering comprehensive metal AM solutions built on decades of collective expertise. We provide not only state-of-the-art SEBM printers and advanced metal powders but also crucial application development services and a commitment to quality, making us an ideal industrial partner for demanding aerospace fixture applications.
Cost Factors and Lead Time for 3D Printed Aerospace Fixtures
Understanding the variables that influence the cost and production timeline is essential for budgeting and project planning when utilizing metal AM for aerospace fixtures. Both cost and lead time can vary significantly based on several factors:
コスト要因:
- Material Choice & Volume: This is often a primary cost driver.
- 素材の種類 High-performance alloys like FeNi36 (Invar) are significantly more expensive per kilogram than materials like 316Lステンレス鋼 due to raw material costs (high nickel content) and specialized powder production.
- Part Volume/Mass: The amount of metal powder consumed directly impacts cost. Larger, denser parts are more expensive. AM’s ability to create lightweight structures via topology optimization or lattices can offer cost savings here compared to solid machined parts, especially with expensive materials.
- Part Complexity & Size (Build Time):
- Build Height: Longer print times directly correlate with increased machine operational cost. Taller parts take longer to print than shorter parts of similar volume.
- 複雑さ: While AM handles complexity well, highly intricate designs may require more support structures or slower printing parameters, increasing time and cost.
- サポート体制: The volume of support material needed adds to both print time and post-processing effort (removal).
- Print Orientation & Nesting:
- Optimization: How a part is oriented on the build plate affects its height (build time) and the amount of support needed. Experienced AM providers optimize orientation and nest multiple parts together in a single build (一括注文) to maximize machine efficiency and reduce per-part cost.
- Post-Processing Intensity:
- Mandatory Steps: Stress relief/heat treatment and support removal are standard costs.
- Optional/Required Steps: The extent of CNC machining required for tight tolerances is a major potential cost adder. Similarly, extensive surface finishing (polishing) increases labor costs significantly. Inspection requirements (e.g., CMM programming and execution time) also contribute.
- 注文量:
- 規模の経済: While AM is cost-effective for low volumes, some economies of scale can be achieved with larger batches (e.g., 10+ units) through optimized nesting and dedicated machine runs, potentially offering advantages for wholesale fixture procurement.
Lead Time Components:
Lead time refers to the total time from order placement to part delivery. It comprises several stages:
- Pre-Processing: Design review, DfAM checks, build preparation (orientation, support generation, slicing), and job scheduling (queue time): 1-5 business days.
- 印刷: Actual machine time required to build the part(s): Can range from 1 day to several days, depending on part height, volume, and nesting.
- Cooldown: Allowing the build chamber and parts to cool safely before removal: Several hours to overnight.
- 後処理: This can be the most variable and often longest part of the lead time.
- 熱処理: 1-3 days (including furnace time and cooling).
- Support Removal & Basic Finishing: 1-2 days.
- Precision Machining: Highly variable, from 1 day to 1-2 weeks depending on complexity and machine availability.
- Inspection: 1-2 days (including CMM programming and reporting).
- 配送: Dependent on location and selected service level.
Typical Lead Times:
- Simple 316L fixtures (minimal post-processing): 5-10 business days.
- Complex Invar fixtures (requiring heat treatment and moderate machining): 10-20 business days.
- Highly complex fixtures with extensive machining: 3-6 weeks or more.
It is always recommended to request a formal quote from your chosen AM service provider, like Met3dp, providing your CAD files and detailed requirements (material, tolerances, finishes, quantity). This will yield the most accurate cost estimate and projected lead time for your specific aerospace fixture.
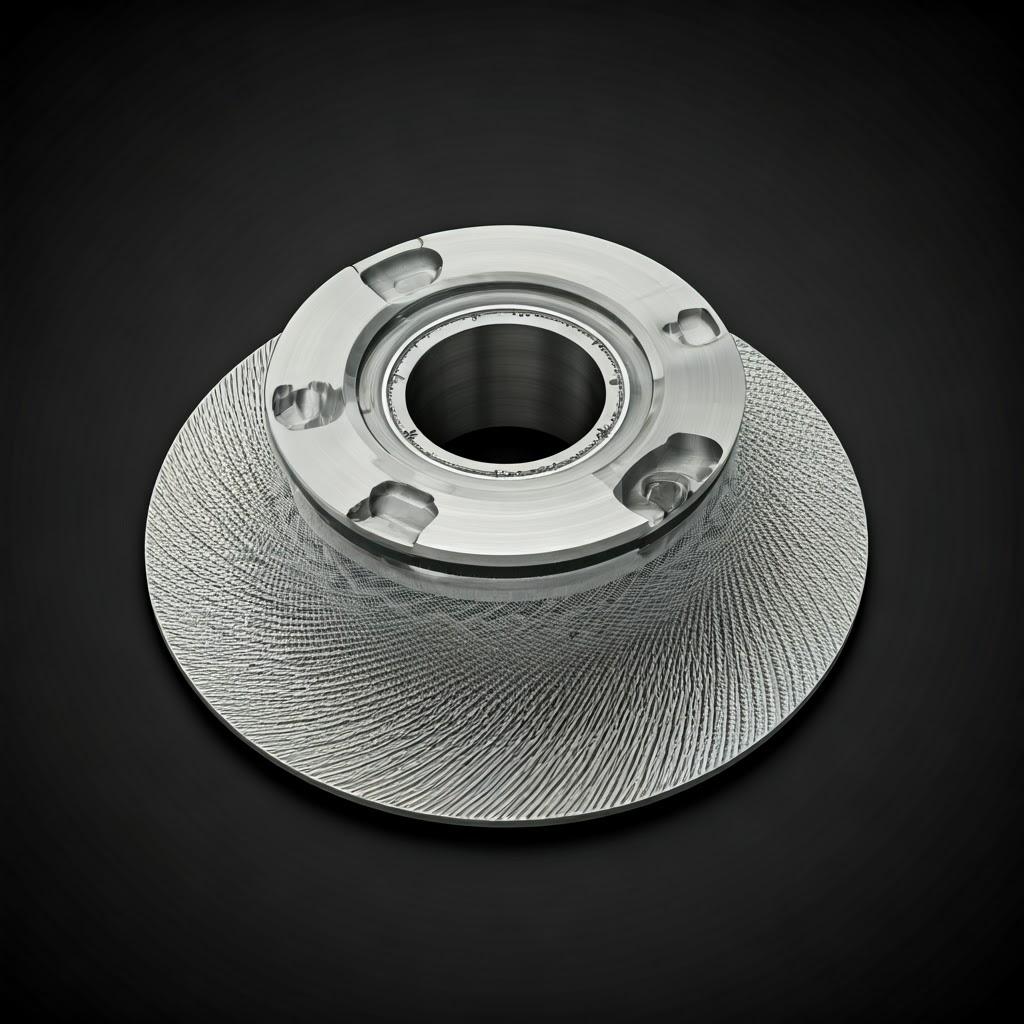
Frequently Asked Questions (FAQ) about 3D Printing Aerospace Fixtures
Here are answers to some common questions engineers and procurement specialists have about using metal AM for aerospace fixtures:
- Q1: How does the cost of a 3D printed Invar fixture compare to a traditionally machined one?
- A: It depends heavily on complexity and volume. For highly complex, one-off, or low-volume Invar fixtures, metal 3D printing is often more cost-effective due to reduced material waste (Invar is expensive) and avoiding complex multi-axis CNC setups. For simpler geometries produced in higher volumes, traditional machining might still be cheaper. AM offers significant savings by minimizing the ‘buy-to-fly’ ratio inherent in machining expensive materials like Invar from large billets.
- Q2: What is the maximum size of an aerospace fixture that can be 3D printed?
- A: This depends entirely on the build volume of the specific metal 3D printer used. Industrial systems vary, but many leading platforms, including those utilized by Met3dp, offer substantial build envelopes. Common maximum dimensions are often in the range of 250x250x300 mm to 400x400x400 mm, with some larger format machines exceeding these dimensions. Very large fixtures can sometimes be printed in sections and then assembled.
- Q3: Can 3D printed fixtures meet the stringent tolerance requirements for aerospace applications?
- A: Yes, but typically through a combination of AM and post-processing. While as-built tolerances are often around ±0.1-0.2 mm, critical features requiring tighter tolerances (e.g., ±0.025 mm or ±0.05 mm) are achieved by designing the part with machining stock and using post-print CNC machining on those specific surfaces. Careful DfAM planning and process control are essential.
- Q4: What quality certifications should I look for in an AM supplier for aerospace fixtures?
- A: The most relevant certification is AS9100, the standard for Quality Management Systems for Aviation, Space, and Defense Organizations. At a minimum, look for ISO 9001 certification coupled with demonstrated experience and traceability processes suitable for the aerospace industry. Evidence of robust internal quality control and material certification handling is crucial.
Conclusion: Enhancing Aerospace Operations with Additively Manufactured Fixtures
In the relentless pursuit of precision, efficiency, and innovation within the aerospace industry, tooling plays a pivotal role. Aerospace fixtures, essential for ensuring accuracy from component fabrication through final assembly and inspection, are evolving thanks to the capabilities of metal additive manufacturing. By leveraging AM, manufacturers can create fixtures with optimized designs, enhanced functionality through complex geometries, and significantly reduced weight – benefits that are difficult or impossible to achieve with traditional methods alone.
The ability to print using specialized materials like FeNi36 (Invar) unlocks new levels of performance for applications demanding extreme 寸法安定性 in the face of temperature fluctuations, critical for inspection and metrology tooling. Simultaneously, versatile materials like 316Lステンレス鋼 offer durable and cost-effective solutions for a wide range of general-purpose fixtures.
Successfully implementing metal AM for aerospace fixtures requires careful consideration of design (DfAM), material properties, achievable tolerances, post-processing needs, and potential challenges. Most importantly, it necessitates partnering with an experienced and capable additive manufacturing service provider. A knowledgeable supplier brings not just printing capacity, but also expertise in materials science, process optimization, quality management, and collaborative technical support.
Met3dp stands ready to be that partner. With our industry-leading metal AM systems, advanced powder manufacturing capabilities, comprehensive post-processing solutions, and deep expertise in aerospace applications, we help organizations harness the power of additive manufacturing to create next-generation tooling.
Ready to explore how metal 3D printing can revolutionize your aerospace fixture strategy? Contact the experts at メット3dp today to discuss your project requirements and discover how our cutting-edge systems and high-performance materials can elevate your manufacturing operations.
シェアする
MET3DP Technology Co., LTDは、中国青島に本社を置く積層造形ソリューションのリーディングプロバイダーです。弊社は3Dプリンティング装置と工業用途の高性能金属粉末を専門としています。
関連記事
Met3DPについて
最新情報
製品
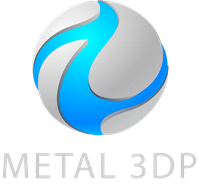
3Dプリンティングと積層造形用金属粉末