Drone Landing Gear 3D Printed for Strength and Lightness
目次
Introduction: The Critical Role of Advanced Drone Landing Gear
The Unmanned Aerial Vehicle (UAV), or drone, market is experiencing exponential growth, transforming industries from logistics and agriculture to surveillance and entertainment. Central to the safe and reliable operation of any drone, regardless of its size or application, is its landing gear. This seemingly simple component bears the brunt of repeated impacts, supports the entire weight of the aircraft (including sensitive payloads) upon landing, and often houses critical sensor equipment. Failures during landing can lead to catastrophic damage, mission failure, and significant financial loss. For procurement managers and engineers in the aerospace and drone manufacturing sectors, sourcing landing gear that offers exceptional strength, durability, and minimal weight is paramount.
Traditionally, drone landing gear has been manufactured using methods like CNC machining from billet materials or injection molding for smaller, less demanding applications. However, these methods often present limitations, particularly when dealing with complex geometries needed for shock absorption or integrating additional functionalities. Furthermore, achieving optimal strength-to-weight ratios – a critical factor for maximizing flight time and payload capacity – can be challenging and costly with conventional techniques.
This is where metal additive manufacturing (AM), commonly known as 金属3Dプリンティング, emerges as a revolutionary solution. By building components layer by layer directly from metal powder, AM enables the creation of highly optimized, lightweight, and robust drone landing gear structures that were previously impossible or prohibitively expensive to produce. This technology allows for intricate internal features, topology optimization for material reduction without compromising strength, and the use of advanced alloys tailored for demanding performance requirements. Companies like Met3dp, with deep expertise in both metal powder production and advanced printing systems, are at the forefront of leveraging AM to push the boundaries of drone performance and reliability. As drone technology continues to advance, metal AM is proving indispensable for developing next-generation landing gear systems that meet the increasing demands for lighter, stronger, and more functional UAV components. This shift impacts not only drone manufacturers but also the entire supply chain, demanding new considerations for wholesale suppliers and distributors focusing on advanced aerospace components.
Applications: Where is 3D Printed Drone Landing Gear Making an Impact?
The versatility of metal additive manufacturing allows for the production of landing gear tailored to a diverse range of UAV applications. The ability to customize designs, optimize for specific load cases, and utilize high-performance materials makes 3D printed landing gear increasingly attractive across various sectors. Procurement specialists sourcing components for drone fleets and engineers designing new UAV platforms are finding significant advantages with AM.
Here are some key areas where 3D printed metal landing gear is demonstrating its value:
- High-Payload Commercial Drones:
- Logistics & Delivery: Drones designed for package delivery require landing gear capable of handling varying payload weights and frequent landing cycles on diverse surfaces. Metal AM allows for topology-optimized designs that are strong enough to support heavy loads but light enough to maximize battery life and delivery range. Materials like AlSi10Mg provide a good balance of strength and weight.
- Agriculture & Surveying: Drones used for crop monitoring, spraying, or Lidar surveying often carry sensitive and expensive equipment. Robust landing gear, potentially incorporating vibration-damping lattice structures achievable through AM, is crucial for protecting these payloads during rough field landings. The corrosion resistance of materials like Ti-6Al-4V is also beneficial in agricultural environments.
- Demanding Military & Surveillance UAVs:
- Reconnaissance & Tactical Drones: These UAVs often operate in harsh conditions and require landing gear that can withstand hard landings on unprepared terrain. The superior strength and fatigue resistance of materials like Ti-6Al-4V, combined with designs optimized for impact absorption using AM, enhance mission reliability and aircraft longevity. Integration of stealth features or specific sensor housings directly into the landing gear structure is also possible.
- Long-Endurance Platforms: For large, long-endurance surveillance drones, minimizing every gram of weight is critical. Metal AM enables highly optimized, skeletal landing gear structures that provide the necessary strength with minimum material usage, directly contributing to extended flight times and operational range.
- Industrial Inspection & Maintenance Drones:
- Infrastructure Inspection (Bridges, Power Lines, Wind Turbines): Drones operating close to structures need precise handling and stable landing capabilities. Landing gear might need specific geometries for perching or landing on non-horizontal surfaces. AM allows for the creation of these custom, complex designs that would be difficult to machine traditionally.
- Confined Space Entry: Smaller inspection drones entering tanks or pipes may require unique landing gear configurations that also protect the drone body. AM enables rapid prototyping and production of these specialized designs.
- Specialized & Research Platforms:
- VTOL (Vertical Take-Off and Landing) Aircraft: Hybrid aircraft that transition between vertical and horizontal flight often have complex landing gear requirements integrating retraction mechanisms and varying load paths. AM facilitates the consolidation of parts and the creation of intricate kinematic mechanisms within the landing gear assembly.
- Experimental & Research Drones: Researchers developing novel drone concepts benefit from the rapid prototyping capabilities of metal AM. New landing gear designs can be quickly fabricated, tested, and iterated upon, accelerating the development cycle.
The common thread across these applications is the need for landing gear that pushes the boundaries of performance – lighter weight, higher strength, enhanced durability, and often, geometric complexity. Metal 3Dプリンティング provides the manufacturing pathway to meet these demands, enabling drone manufacturers and their suppliers to deliver more capable and reliable UAV systems. Met3dp supports these advanced applications not only through its printing services but also by supplying the high-quality, specialized metal powders required for peak performance.
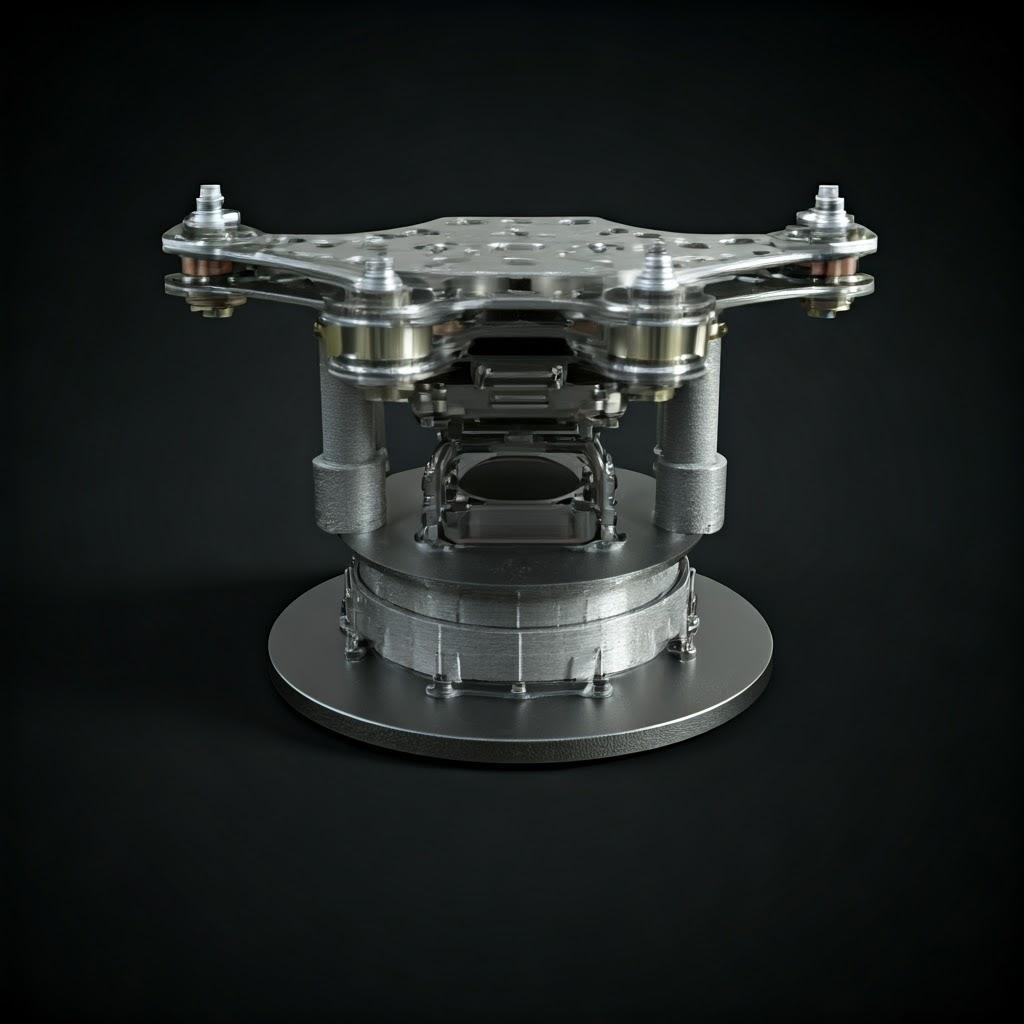
Why Metal 3D Printing for Drone Landing Gear Production?
Choosing the right manufacturing process is a critical decision for engineers and procurement managers aiming to optimize drone performance, cost, and time-to-market. While traditional methods have served the industry well, metal additive manufacturing offers a compelling suite of advantages specifically beneficial for producing drone landing gear. These benefits often translate directly into improved flight characteristics, enhanced durability, and streamlined supply chains for drone parts suppliers and manufacturers.
Key Advantages of Metal AM for Drone Landing Gear:
- Unmatched Lightweighting Potential:
- Topology Optimization: AM software allows engineers to input load conditions and design constraints, and the software generates a structure using material only where it’s structurally necessary. This results in organic-looking, highly efficient designs that can significantly reduce weight (often 20-50% or more) compared to traditionally manufactured parts, while maintaining or even increasing strength. This is crucial for drones, where reduced weight directly translates to longer flight times, increased payload capacity, or enhanced maneuverability.
- Internal Lattice Structures: Metal AM can create complex internal lattice or honeycomb structures within the landing gear struts. These structures provide excellent stiffness and energy absorption properties at a fraction of the weight of solid material. This is ideal for absorbing landing impacts and protecting the airframe and payload.
- Geometric Complexity & Design Freedom:
- Integrated Features: AM allows for the consolidation of multiple parts into a single, complex component. Brackets, sensor mounts, cable routing channels, or even parts of a retraction mechanism can be integrated directly into the landing gear structure during the printing process. This reduces part count, simplifies assembly, minimizes potential points of failure, and lowers overall system weight.
- Conformal Designs: Landing gear can be designed to conform perfectly to the drone’s fuselage or incorporate aerodynamic fairings, reducing drag. Complex curves and internal passages, difficult or impossible to achieve with CNC machining, are readily produced with AM.
- Rapid Prototyping & Iteration:
- スピードだ: Producing functional metal prototypes of landing gear designs can be done significantly faster with AM compared to setting up tooling for casting or extensive machining setups. Design modifications can be implemented and tested quickly, accelerating the development cycle for new drone platforms.
- Cost-Effective Iteration: The cost of printing a single prototype or a small batch is much lower with AM than with traditional methods that often involve high tooling or setup costs. This encourages design experimentation and optimization without prohibitive expense.
- Material Performance & Selection:
- 先進合金: AM processes, particularly powder bed fusion techniques like Selective Electron Beam Melting (SEBM) used by Met3dp, work effectively with high-performance aerospace alloys like Titanium (Ti-6Al-4V) and specialized Aluminum alloys (AlSi10Mg). These materials offer exceptional strength-to-weight ratios, fatigue resistance, and corrosion resistance perfectly suited for demanding landing gear applications.
- テーラード・プロパティ: The layer-by-layer building process and subsequent heat treatments allow for fine-tuning of the material’s microstructure and mechanical properties to meet specific performance targets.
- Supply Chain & Manufacturing Efficiency:
- オンデマンド制作: AM enables digital warehousing and on-demand production. Landing gear components can be printed as needed, reducing inventory holding costs and minimizing waste associated with overproduction. This is advantageous for distributors and wholesale suppliers managing component stock.
- Reduced Lead Times (for complex parts): While simple parts might be faster to machine, highly complex or consolidated landing gear designs can often be produced faster overall via AM by eliminating multiple machining steps, tooling creation, and assembly operations.
Comparison: Metal AM vs. Traditional Methods for Landing Gear
特徴 | 金属積層造形(AM) | CNC加工 | Casting / Injection Molding (Metals/Polymers) |
---|---|---|---|
デザインの複雑さ | High (complex internal features, lattices, topology optimization) | Moderate to High (limited by tool access) | Moderate (limited by mold complexity, draft angles) |
軽量化 | Excellent (topology optimization, lattices) | Good (material removal, pocketing) | Fair to Good (depends on design/material) |
部品の統合 | 素晴らしい | 限定 | 限定 |
素材オプション | Growing range of high-performance alloys (Ti, Al, Steel, etc.) | Wide range of machinable metals & plastics | Wide range of castable metals & moldable polymers |
強度対重量 | Excellent (optimized design + high-strength alloys) | Good (depends on alloy & design efficiency) | Variable (often lower for polymers/castings) |
Prototyping Speed | 速い | Moderate to Fast (depends on complexity) | Slow (requires tooling) |
金型費用 | なし | Low (fixtures may be needed) | High (mold/die costs) |
Cost per Part (Low Vol) | 中~高 | High (programming & setup time) | Very High (due to tooling amortization) |
Cost per Part (High Vol) | Moderate (improving with machine speed/efficiency) | 中~低 | 低い |
Lead Time (Prototype) | 短い | 中程度 | 長さ |
Lead Time (Production) | 中程度 | Moderate to Fast | Fast (once tooling is made) |
Export to Sheets
While traditional methods retain advantages in high-volume production of simpler designs, metal 3D printing offers transformative benefits for drone landing gear where weight, strength, complexity, and customization are critical drivers. Partnering with an experienced provider like Met3dp ensures access to state-of-the-art equipment and materials expertise to fully leverage these advantages.
Material Focus: AlSi10Mg vs. Ti-6Al-4V for Optimal Landing Gear Performance
Selecting the right material is fundamental to designing drone landing gear that meets stringent performance requirements. The choice directly impacts weight, strength, durability, fatigue life, corrosion resistance, and ultimately, the cost-effectiveness of the component. For metal 3D printing of drone landing gear, two materials stand out due to their excellent balance of properties: Aluminum alloy AlSi10Mg and Titanium alloy Ti-6Al-4V (Grade 5). Understanding their characteristics helps engineers and procurement specialists make informed decisions based on specific application needs.
Met3dp, leveraging its advanced gas atomization and PREP powder production technologies, manufactures high-quality spherical powders of both AlSi10Mg and Ti-6Al-4V, optimized for powder bed fusion processes like SEBM and SLM (Selective Laser Melting). This ensures consistent quality and optimal material properties in the final printed parts.
1. Aluminum Silicon Magnesium Alloy (AlSi10Mg): The Lightweight Workhorse
- 構成: Primarily Aluminum, with ~10% Silicon and small amounts of Magnesium.
- キー・プロパティ
- 密度が低い: (~2.67 g/cm³) Significantly lighter than steel and even titanium. This is its primary advantage for aerospace components where weight saving is critical.
- 優れた強度対重量比: Offers respectable strength, especially after appropriate heat treatment.
- 優れた熱伝導性: While less critical for landing gear, it’s a notable property.
- 良好な耐食性: Generally performs well in typical atmospheric conditions.
- 優れた印刷適性: It’s one of the most common and well-understood alloys for laser powder bed fusion (LPBF), allowing for fine features and good surface finish.
- Benefits for Drone Landing Gear:
- Significant Weight Reduction: Ideal for maximizing flight time and payload capacity on commercial, agricultural, and smaller surveillance drones.
- 費用対効果: Aluminum powder is generally less expensive than titanium powder, and printing speeds can often be higher, leading to lower overall part cost.
- Good Mechanical Properties: Sufficient strength and stiffness for many medium-duty drone applications.
- 検討する:
- Lower absolute strength and fatigue resistance compared to Ti-6Al-4V.
- Lower operating temperature limit compared to titanium.
- Requires post-print heat treatment (e.g., T6 condition) to achieve optimal mechanical properties.
- 代表的な用途 Landing gear for commercial delivery drones, agricultural UAVs, smaller inspection drones, and applications where minimizing weight is the absolute top priority and operating stresses are moderate.
2. Titanium Alloy Ti-6Al-4V (Grade 5): The High-Performance Champion
- 構成: Primarily Titanium, with ~6% Aluminum and ~4% Vanadium.
- キー・プロパティ
- 卓越した強度対重量比: Although denser than Aluminum (~4.43 g/cm³), its significantly higher strength results in an outstanding strength-to-weight ratio, often allowing for lighter parts than steel and sometimes even Aluminum for the same strength requirement.
- High Absolute Strength & Fatigue Life: Superior resistance to cyclic loading and impacts, crucial for durable landing gear enduring repeated landings.
- 優れた耐食性: Highly resistant to environmental degradation, including saltwater and various chemicals, making it suitable for marine or harsh environment operations.
- Good High-Temperature Performance: Retains strength at higher temperatures than aluminum alloys.
- 生体適合性: (Though not relevant for landing gear, it’s a key feature for medical applications).
- Benefits for Drone Landing Gear:
- Maximum Durability & Reliability: Ideal for military UAVs, high-impact scenarios, operations in corrosive environments, and landing gear subjected to extreme loads or fatigue cycles.
- Potential for Weight Savings (vs. Steel): Can replace steel components for significant weight reduction while maintaining or exceeding strength.
- デザインの最適化: Its high strength allows for highly optimized, thin-walled, and skeletal structures via topology optimization, potentially offsetting its higher density compared to aluminum in some strength-critical designs.
- 検討する:
- Higher material cost compared to AlSi10Mg.
- Can be more challenging to print and post-process than aluminum alloys, requiring careful parameter control and stress relief treatments. Met3dp’s expertise in SEBM and powder quality control is vital here.
- Higher density than AlSi10Mg.
- 代表的な用途 Landing gear for military and tactical UAVs, large high-payload drones, VTOL aircraft, drones operating in harsh or marine environments, and any application where maximum strength, fatigue life, and durability are paramount.
Material Selection Guide:
特徴 | AlSi10Mg | Ti-6Al-4V | Primary Consideration |
---|---|---|---|
密度 | Low (≈2.67g/cm3) | Medium (≈4.43g/cm3) | Weight Minimization (Absolute) |
強さ | グッド | 非常に高い | Durability, Impact Resistance, High Loads |
硬さ | 中程度 | 高い | Resistance to Deflection |
疲労寿命 | Fair to Good | 素晴らしい | Longevity, Repeated Landings |
Corrosion Res. | グッド | 素晴らしい | Operating Environment (Coastal, Chemical) |
最高温度 | 中程度 | 高い | High-Speed Flight, Proximity to Heat Sources |
印刷適性 | 素晴らしい | Good (Requires more control) | Manufacturing Ease, Feature Detail |
コスト | より低い | より高い | Budget Constraints, Wholesale Procurement |
Ideal Use Case | Weight-critical, moderate loads, cost-sensitive | Strength-critical, high impact, harsh environment | Balancing performance requirements and project constraints |
Export to Sheets
Met3dp’s Role: As a provider of both advanced SEBM 印刷方法 and high-quality AlSi10Mg and Ti-6Al-4V powders, Met3dp is uniquely positioned to support manufacturers. Our deep understanding of material science, powder characteristics derived from our specialized atomization processes, and printing parameter optimization ensures that customers achieve the desired mechanical properties and component quality for their drone landing gear, regardless of the chosen alloy. We work closely with clients, from engineers optimizing designs to procurement managers sourcing reliable components, to select and process the ideal material for their specific UAV application.
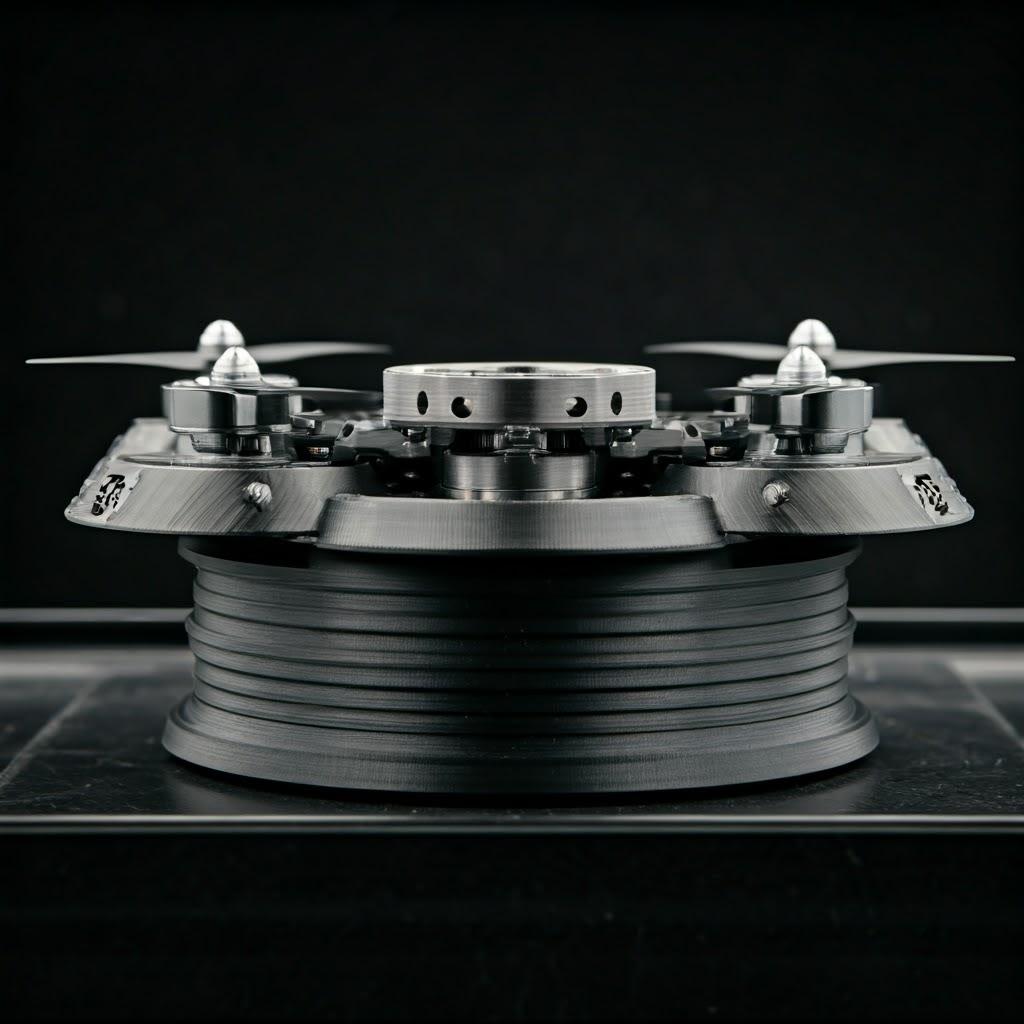
Design Optimization: Engineering Landing Gear for Additive Manufacturing Success
Simply replicating a traditionally designed landing gear using metal 3D printing often fails to unlock the technology’s full potential. To truly leverage the benefits of additive manufacturing – particularly lightweighting, part consolidation, and enhanced performance – engineers must embrace Design for Additive Manufacturing (DfAM) principles. This involves rethinking the design process from the ground up, considering the unique capabilities and constraints of layer-by-layer fabrication. For drone landing gear, DfAM is crucial for achieving significant weight savings and integrating functionalities that enhance overall UAV performance. Procurement managers should also be aware of these principles, as optimized designs often lead to more efficient production and potentially lower costs for wholesale orders.
Key DfAM Strategies for Drone Landing Gear:
- Topology Optimization:
- Concept: This is perhaps the most powerful DfAM tool for landing gear. Specialized software analyzes the load paths and stresses the component will experience during takeoff, landing, and ground handling. It then iteratively removes material from areas that don’t contribute significantly to structural integrity, leaving behind an organic, often bone-like structure that is highly optimized for strength-to-weight ratio.
- メリット Drastic weight reduction (often 20-50%+) without compromising strength or stiffness; identification of optimal load paths; creation of highly efficient structures impossible to manufacture conventionally.
- Tools: Software like Altair Inspire, nTopology, Autodesk Fusion 360 (Generative Design), ANSYS Discovery.
- 検討する: Optimized designs can be complex and require careful validation through simulation (FEA) and physical testing. Manufacturability checks within the AM process (e.g., minimum feature size, overhangs) are essential.
- 格子構造:
- Concept: Incorporating internal lattice or cellular structures within the landing gear struts or base. Various lattice types exist (e.g., cubic, octet-truss, gyroid) offering different mechanical properties.
- メリット Further significant weight reduction compared to solid material; tailored stiffness and compliance; excellent energy absorption properties for impact damping; vibration isolation for sensitive payloads; potential for integrating fluid channels if needed.
- アプリケーション Ideal for shock-absorbing elements within the landing gear, reducing the transmission of landing forces to the airframe. Can also fill larger volumes identified by topology optimization for stability.
- 検討する: Requires specialized software for generation; ensuring powder removal from complex internal lattices is crucial (designing in escape holes); requires careful analysis to predict mechanical behavior.
- パーツの統合:
- Concept: Redesigning assemblies consisting of multiple traditionally manufactured parts (brackets, fasteners, mounts, struts) into a single, integrated component printed as one piece.
- メリット Reduced part count simplifies assembly and lowers labor costs; eliminates fasteners (potential failure points); reduces overall weight by removing overlaps and redundant material; improves structural integrity; simplifies supply chain management for manufacturers and wholesale suppliers.
- Example: Integrating mounting points for wheels, brakes, sensors, or fairings directly into the main landing gear strut.
- 検討する: Increases the complexity of the single part; repair might require replacing the entire integrated component; requires careful design to manage stresses across the integrated features.
- Feature-Based Design Considerations:
- Self-Supporting Angles: Designing overhangs to be below the critical angle (typically around 45 degrees from the horizontal, depending on the material and machine) minimizes the need for support structures, saving material, print time, and post-processing effort.
- Minimum Wall Thickness: Understanding the minimum printable wall thickness for the chosen material (e.g., AlSi10Mg, Ti-6Al-4V) and AM process (SEBM, SLM) is crucial to avoid print failures or weak sections. Met3dp provides guidance based on its equipment capabilities.
- Hole Orientation: Printing holes horizontally often results in better circularity than printing them vertically due to the layer-wise construction. Consider orientation or design teardrop shapes for vertical holes to make them self-supporting.
- Designing for Post-Processing: If specific surfaces require high precision (e.g., mating interfaces, bearing bores), add sufficient stock material (machining allowance) in the design to allow for post-print CNC machining. Ensure accessibility for machining tools.
- Support Strategy Planning: While minimizing supports is ideal, some complex geometries will require them. Design features that allow for easier support removal (e.g., clear access paths, breakaway points). Consider the impact of support contact points on surface finish.
By applying these DfAM principles, engineers can design drone landing gear that is not just manufacturable via AM but is truly optimized for it. This results in components that are lighter, stronger, potentially more functional, and often more efficient to produce in the long run. Met3dp collaborates with clients, offering application development services to help optimize designs specifically for our advanced SEBM printing technology and high-performance metal powders, ensuring the final product meets demanding performance targets.
Achieving Precision: Tolerance, Surface Finish, and Accuracy in Metal AM
While metal additive manufacturing excels at producing complex geometries, a common question from engineers and procurement managers relates to the achievable precision: what level of dimensional accuracy, tolerances, and surface finish can be expected for components like drone landing gear? Understanding these aspects is crucial for ensuring proper fit, function, and assembly. The capabilities of the specific AM process (e.g., SEBM, SLM), the chosen material, part size and geometry, and post-processing steps all influence the final outcome.
1. Dimensional Accuracy and Tolerances:
- General Expectations: Metal AM processes like Selective Electron Beam Melting (SEBM) and Selective Laser Melting (SLM) typically achieve dimensional accuracy in the range of ±0.1 mm to ±0.2 mm (or ±0.1% to ±0.2% of the dimension, whichever is greater) for well-controlled processes and medium-sized parts. Smaller features can often hold tighter tolerances.
- Factors Influencing Accuracy:
- Machine Calibration: Regular and precise calibration of the AM system (laser/electron beam spot size, scanner accuracy, powder bed layering) is fundamental. Met3dp places high emphasis on machine maintenance and calibration for consistent results.
- Thermal Effects: The repeated heating and cooling cycles inherent in AM can cause internal stresses, leading to minor warping or distortion, especially in large or complex parts. Build strategy (scan pattern, orientation) and stress relief heat treatments are critical for mitigation.
- 素材の特性: Different materials exhibit varying shrinkage rates and thermal behavior during printing. Process parameters must be optimized for each specific alloy (e.g., AlSi10Mg vs. Ti-6Al-4V).
- Part Geometry & Size: Large, flat sections may be more prone to warping, while intricate, delicate features require careful parameter control to reproduce accurately. The industry-leading print volume of Met3dp’s printers allows for the production of large drone components, but managing thermal effects remains key.
- サポート体制: Supports help anchor the part and dissipate heat, influencing accuracy. Their placement and removal can also affect final dimensions.
- Achieving Tighter Tolerances: For critical features like bearing housings, mounting interfaces, or piston bores within a landing gear assembly, tolerances tighter than the standard AM process capability are often required. These are typically achieved through post-print CNC machining operations on specific surfaces.
2. Surface Finish (Roughness):
- As-Built Surface Finish: The surface finish of a part directly after printing depends heavily on the AM process, powder particle size, layer thickness, and surface orientation.
- Powder Bed Fusion (SLM/SEBM): Typically results in a surface roughness (Ra) ranging from 6 µm to 25 µm (micrometers). Downward-facing surfaces (supported) are generally rougher than upward-facing or vertical surfaces. SEBM, often using slightly larger powder and higher energy, might produce a slightly rougher finish than SLM initially, but offers advantages in reduced residual stress.
- Orientation: Vertical walls tend to be smoother than angled or horizontal surfaces due to the nature of layer stacking. Top surfaces are often smoother than side walls.
- 表面仕上げの改善: If a smoother surface is required for aesthetic reasons, fatigue performance, or mating interfaces, various post-processing techniques are employed:
- Bead Blasting / Shot Peening: Improves uniformity, removes loose powder, and can induce compressive stress (beneficial for fatigue life). Can achieve Ra values typically between 3 µm and 10 µm.
- Tumbling / Vibratory Finishing: Uses media to smooth surfaces, effective for batches of smaller parts. Ra values can be reduced significantly depending on media and time.
- CNC Machining: Provides the smoothest and most precise surfaces on targeted features (Ra < 1 µm possible).
- Polishing (Manual or Electrochemical): Can achieve very smooth, mirror-like finishes (Ra < 0.1 µm) but is often labor-intensive or requires specialized setups.
- Specification: Engineers should clearly specify required surface finishes on drawings, indicating which surfaces need improvement beyond the as-built state.
Met3dp’s Commitment to Precision:
At Met3dp, we understand that precision is critical for mission-critical components like drone landing gear. Our investment in industry-leading SEBM printers, combined with stringent process controls and high-quality metal powders manufactured in-house, allows us to deliver parts with excellent dimensional accuracy and reliable mechanical properties. We offer a range of Met3dp products and services, including post-processing options, to meet specific tolerance and surface finish requirements. Our team works with customers to understand their specific needs and develop manufacturing plans that ensure the final components meet or exceed expectations for fit, form, and function.
Tolerance and Surface Finish Summary Table:
パラメータ | As-Built (Typical PBF) | Post-Processed Options | 考察 |
---|---|---|---|
寸法公差 | ±0.1 to ±0.2 mm | CNC Machining (for specific features, < ±0.025 mm possible) | Geometry, material, thermal effects, machine calib. |
表面粗さ(Ra) | 6 µm – 25 µm | Bead Blasting (3-10 µm), Tumbling (Variable), Machining (<1 µm), Polishing (<0.1 µm) | Orientation, supports, functional requirements, cost |
Export to Sheets
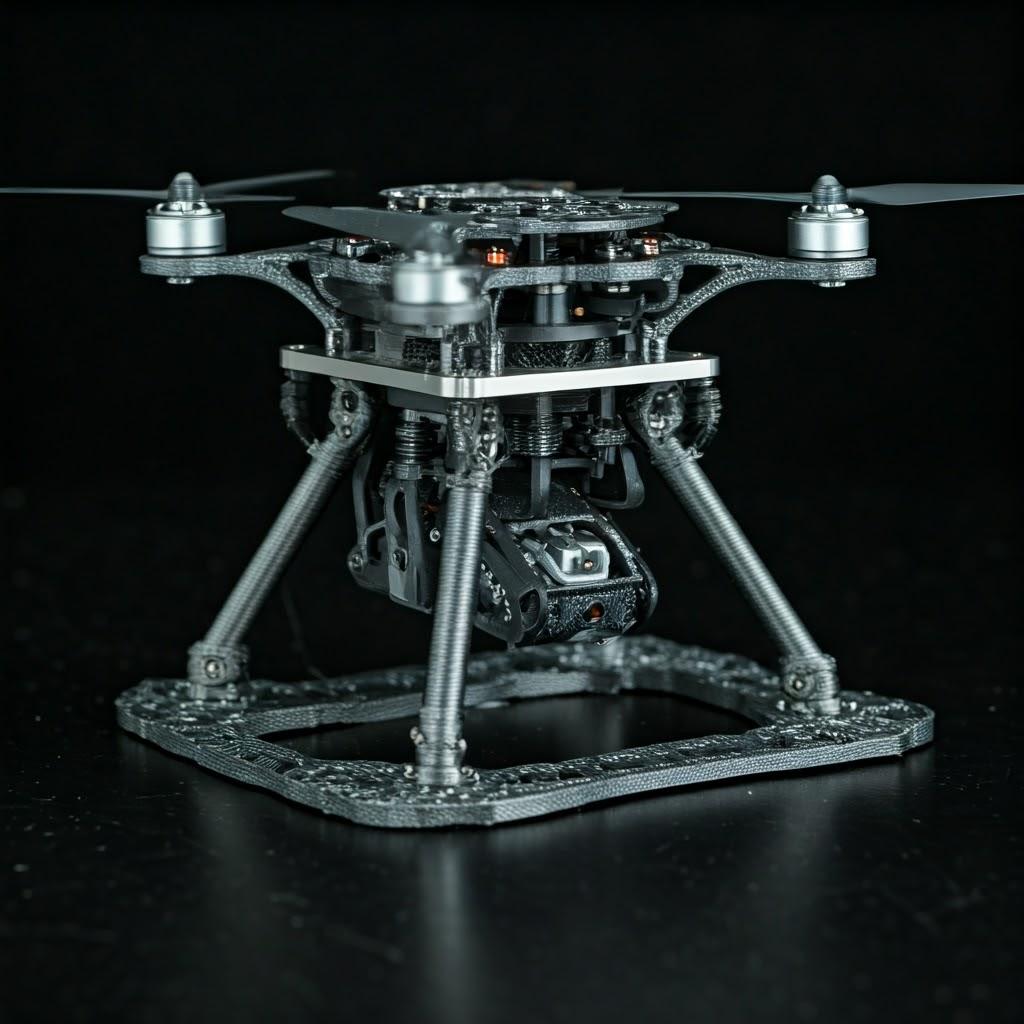
Beyond Printing: Essential Post-Processing for Drone Landing Gear
The additive manufacturing process creates the near-net shape of the drone landing gear, but it’s rarely the final step. To achieve the required mechanical properties, dimensional tolerances, surface finish, and overall functionality, a series of post-processing steps are typically essential. These steps transform the raw printed part into a finished, mission-ready component. Understanding these requirements is vital for both design engineers (who need to account for them) and procurement managers (who need to factor them into costs and lead times).
Common Post-Processing Steps for Metal AM Drone Landing Gear:
- Stress Relief / Heat Treatment:
- Why: The rapid heating and cooling cycles during printing induce internal stresses within the metal part. These stresses can lead to distortion over time or reduce the component’s fatigue life. Heat treatment relieves these stresses and homogenizes the material’s microstructure. Additionally, specific heat treatments (like Solution Annealing and Aging for AlSi10Mg, or Annealing for Ti-6Al-4V) are required to achieve the desired final mechanical properties (strength, hardness, ductility).
- プロセス Parts are heated in a controlled atmosphere furnace to specific temperatures for a set duration, followed by controlled cooling. Parameters vary significantly depending on the alloy (AlSi10Mg T6 treatment is very different from Ti-6Al-4V stress relief).
- HIP (Hot Isostatic Pressing): For critical applications demanding maximum density and fatigue life (common in aerospace), HIP may be employed. This process applies high temperature and high Argon gas pressure simultaneously to close any residual internal micro-porosity, further improving mechanical properties. Met3dp advises on appropriate heat treatment cycles based on material and application requirements.
- 支持構造の撤去:
- Why: Support structures are often necessary during printing to anchor the part to the build plate, prevent warping, and support overhanging features. These sacrificial structures must be removed.
- プロセス Depending on the design and material, supports can be removed manually (using pliers, cutters, grinders), via CNC machining, or sometimes through wire EDM (Electrical Discharge Machining) for delicate or hard-to-reach areas. DfAM principles aim to minimize supports or make them easily accessible for removal. The skill of the technician is crucial to avoid damaging the part surface during removal.
- CNC Machining:
- Why: As mentioned earlier, AM processes have inherent tolerance limits. For critical interfaces, mating surfaces, bearing bores, fastener holes, or any feature requiring high precision (tighter than standard AM tolerances), CNC machining is used. It ensures exact dimensions, parallelism, perpendicularity, and required surface finishes on specific areas.
- プロセス The 3D printed part is fixtured onto a CNC milling machine or lathe. Precision cutting tools remove small amounts of material from designated surfaces (requires designing parts with machining allowance).
- Importance for Landing Gear: Essential for ensuring accurate fitment of wheels, axles, retraction mechanisms, and attachment points to the drone airframe.
- Surface Finishing & Cleaning:
- Why: To improve the as-built surface roughness, enhance aesthetics, improve fatigue performance, prepare for coatings, or simply clean the part thoroughly.
- Processes:
- クリーニング: Removing any trapped or semi-sintered powder, especially from internal channels or complex lattice structures, often using compressed air, ultrasonic cleaning baths, or specialized chemical cleaning.
- Bead Blasting / Sand Blasting: Creates a uniform matte finish, removes minor imperfections, and can improve fatigue life through peening. Different media (glass beads, aluminum oxide) create different finishes.
- Tumbling / Vibratory Finishing: Smooths surfaces and edges using abrasive media in a tumbling barrel or vibratory bowl. Good for deburring and achieving a consistent finish on multiple parts simultaneously.
- 研磨: Manual or electro-polishing for very smooth, reflective surfaces where required (less common for landing gear unless for specific functional or aesthetic reasons).
- Anodizing (for Aluminum): An electrochemical process that creates a durable, corrosion-resistant, and often colored oxide layer on the surface of AlSi10Mg parts.
- コーティング: Application of specialized coatings for enhanced wear resistance, corrosion protection, or specific surface properties (e.g., paint, powder coating, specialized aerospace coatings).
Integrated Solutions:
The post-processing chain can be complex and requires expertise in various disciplines. Partnering with a service provider like Met3dp, which offers comprehensive solutions often including management of these necessary post-processing steps, can streamline the production workflow. We ensure that each step is performed correctly to guarantee the final drone landing gear meets all performance specifications and quality standards demanded by the aerospace industry.
Overcoming Hurdles: Common Challenges in 3D Printing Landing Gear and Solutions
While metal additive manufacturing offers significant advantages for producing drone landing gear, it’s not without its challenges. Engineers, manufacturers, and procurement teams should be aware of potential hurdles during the design, printing, and post-processing phases. Fortunately, with careful planning, process control, and expertise, these challenges can be effectively managed and overcome. Leveraging the experience of established providers like Met3dp is key to navigating these complexities successfully.
Common Challenges and Mitigation Strategies:
- Warping and Distortion:
- チャレンジ: Significant temperature gradients during the printing process can cause differential expansion and contraction, leading to internal stresses that warp or distort the part, especially large, flat, or asymmetric geometries.
- Solutions:
- Optimized Orientation: Carefully selecting the part’s orientation on the build plate to minimize thermal stress accumulation and reduce the need for supports on critical surfaces.
- Robust Support Structures: Using well-designed supports to anchor the part firmly to the build plate and act as heat sinks.
- Thermal Engineering: Utilizing build plate heating (common in SEBM and some SLM systems) to reduce temperature gradients.
- Optimized Scan Strategies: Employing specific laser/electron beam scan patterns (e.g., island scanning, checkerboard patterns) to distribute heat more evenly.
- Post-Print Stress Relief: Performing a stress relief heat treatment immediately after printing and before removing the part from the build plate is crucial, especially for high-stress materials like Ti-6Al-4V.
- Support Structure Removal Difficulty:
- チャレンジ: Supports, while necessary, can be difficult and time-consuming to remove, especially from internal channels, complex lattice structures, or delicate features. Removal can also damage the part surface if not done carefully.
- Solutions:
- DfAM for Support Reduction: Designing parts with self-supporting angles (typically <45°) and minimizing features that require extensive support.
- Optimized Support Design: Using support structures with lower density or specific geometries (e.g., cone, block, line supports) designed for easier breakaway or machining access. Software tools often allow customization of support contact points and density.
- Process Selection: Certain AM processes might inherently require fewer supports for specific geometries.
- Skilled Post-Processing: Employing experienced technicians with the right tools (manual, CNC, EDM) for careful support removal.
- 多孔性:
- チャレンジ: Small voids or pores can sometimes form within the printed material due to incomplete melting, gas entrapment, or powder inconsistencies. Porosity can negatively impact mechanical properties, particularly fatigue strength.
- Solutions:
- Optimized Print Parameters: Precise control over laser/electron beam power, scan speed, layer thickness, and atmosphere control (inert gas or vacuum) is critical to ensure full melting and consolidation. Met3dp meticulously develops and validates parameters for each material.
- High-Quality Powder: Using spherical metal powders with consistent particle size distribution, high purity, and good flowability, like those produced by Met3dp using advanced gas atomization and PREP technologies, minimizes porosity issues related to the raw material.
- 熱間静水圧プレス(HIP): As a post-processing step, HIP effectively closes internal voids, achieving near-full theoretical density, crucial for critical aerospace components.
- Residual Stress Management:
- チャレンジ: Beyond causing warping, residual stresses can remain locked within the part even after printing, potentially affecting its long-term performance and dimensional stability.
- Solutions:
- Optimized Build Strategy: Similar to warp mitigation, scan strategies and part orientation play a role.
- Appropriate Heat Treatment: Performing mandatory stress relief cycles tailored to the specific alloy (AlSi10Mg, Ti-6Al-4V) is the primary method for reducing residual stress to acceptable levels. The knowledge and experience of a provider like メット3dp is vital in defining and executing these critical thermal cycles.
- 表面粗さ:
- チャレンジ: The as-built surface finish of AM parts may not be suitable for all applications, particularly those requiring smooth surfaces for fatigue resistance, sealing, or low friction.
- Solutions:
- Parameter Optimization: Fine-tuning print parameters (e.g., smaller layer thickness, contour scanning) can improve finish on specific surfaces, sometimes at the cost of build speed.
- Orientation: Orienting critical surfaces vertically or upwards generally results in better finishes.
- 後処理: Utilizing the range of surface finishing techniques discussed previously (blasting, tumbling, machining, polishing) to achieve the specified Ra value.
Successfully producing high-quality, reliable 3D printed drone landing gear requires a deep understanding of the materials, the AM process, and potential challenges. By partnering with an experienced additive manufacturing provider like Met3dp, companies gain access to the necessary expertise, state-of-the-art equipment, high-quality materials, and process controls needed to navigate these hurdles and deliver superior components.
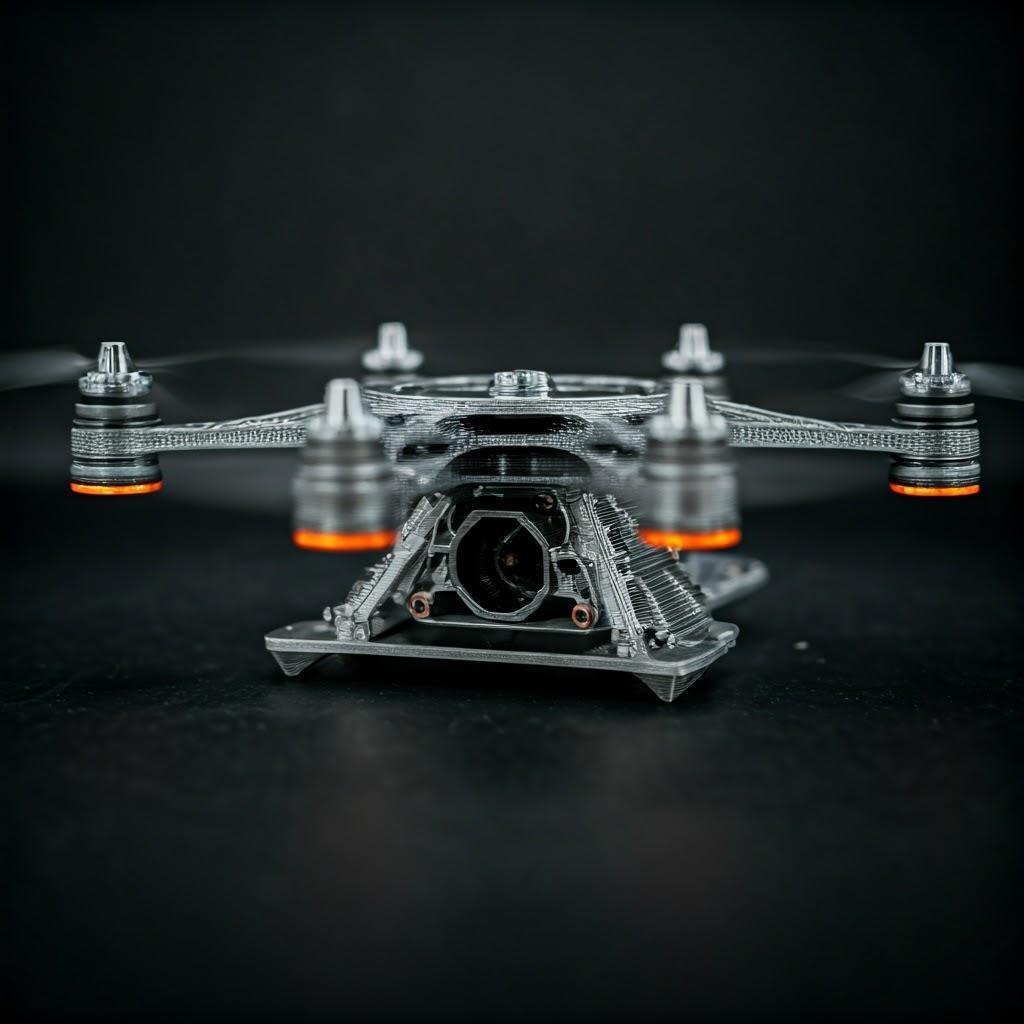
Supplier Selection: Choosing the Right Metal 3D Printing Partner for Drone Components
Selecting the right additive manufacturing partner is as critical as optimizing the design or choosing the correct material. The quality, reliability, and performance of your 3D printed drone landing gear depend heavily on the capabilities and expertise of your chosen service provider. For engineers seeking cutting-edge solutions and procurement managers aiming for reliable wholesale supply chains, evaluating potential partners based on a comprehensive set of criteria is essential.
Key Criteria for Evaluating Metal AM Suppliers:
- Quality Management & Certifications:
- Requirement: Look for suppliers with robust Quality Management Systems (QMS) and relevant certifications. ISO 9001 is a baseline, but for aerospace components like drone landing gear, AS9100 certification is highly desirable, indicating adherence to stringent aerospace industry quality standards.
- Why it Matters: Certifications demonstrate a commitment to process control, traceability, repeatability, and continuous improvement, ensuring consistent component quality.
- Material Expertise & Portfolio:
- Requirement: The supplier should have proven expertise in processing the specific materials you require (e.g., AlSi10Mg, Ti-6Al-4V). Assess their range of available materials. Do they manufacture their own powder or have stringent quality control for sourced powders? Met3dp’s in-house powder production using advanced gas atomization and PREP technology ensures high-quality, spherical powders optimized for AM.
- Why it Matters: Material quality directly impacts the final part’s mechanical properties and consistency. Expertise ensures correct parameter settings and handling procedures for optimal results.
- Technology & Equipment Capabilities:
- Requirement: Evaluate the supplier’s printing technology (e.g., SEBM, SLM/DMLS), machine models, build volume capacity, and maintenance procedures. Do they have the right equipment for your specific needs (e.g., SEBM for reduced stress in Ti-6Al-4V)?
- Why it Matters: State-of-the-art, well-maintained equipment, like Met3dp’s industry-leading SEBM printers, is crucial for achieving accuracy, good surface finish, and reliable mechanical properties. Adequate build volume is necessary for larger landing gear components.
- Technical Expertise & Support:
- Requirement: Does the supplier offer engineering support, including DfAM consultation, simulation capabilities, and application development assistance? Can they help optimize your design for additive manufacturing?
- Why it Matters: A partner with strong technical expertise can significantly enhance your component’s performance and manufacturability, potentially reducing weight and cost. Met3dp provides comprehensive solutions, including application development services.
- Post-Processing Capabilities:
- Requirement: Assess their in-house capabilities or established partnerships for necessary post-processing steps like heat treatment, HIP, CNC machining, support removal, and surface finishing.
- Why it Matters: A supplier offering a streamlined workflow, including managing post-processing, simplifies logistics, reduces lead times, and ensures accountability throughout the production process.
- Quality Control & Inspection:
- Requirement: Inquire about their quality control procedures, including material traceability, in-process monitoring, dimensional inspection methods (CMM, 3D scanning), material testing (tensile, density), and reporting.
- Why it Matters: Rigorous QC ensures that the final parts meet all specified requirements and performance standards before shipping.
- Track Record & Experience:
- Requirement: Look for experience in your industry (aerospace, drone manufacturing) and with similar components. Ask for case studies or references.
- Why it Matters: Proven experience indicates familiarity with industry expectations, standards, and common challenges.
- Lead Time, Capacity & Reliability:
- Requirement: Discuss realistic lead times for prototypes and production volumes. Assess their capacity to handle your potential order sizes, especially for wholesale procurement. Evaluate their on-time delivery track record.
- Why it Matters: Predictable lead times and reliable delivery are crucial for meeting project deadlines and maintaining smooth production schedules.
- Communication & Customer Service:
- Requirement: Evaluate their responsiveness, transparency, and willingness to collaborate throughout the project lifecycle.
- Why it Matters: Good communication fosters a strong partnership and ensures alignment on requirements and expectations.
Choosing a supplier isn’t just about finding the lowest quote; it’s about establishing a strategic partnership with a company that possesses the technology, expertise, and quality focus to deliver mission-critical components reliably. Met3dp aims to be that partner, offering a combination of advanced technology, materials science expertise, and a commitment to quality for demanding applications like drone landing gear.
Understanding Investment: Cost Factors and Lead Times for Wholesale & Prototyping Orders
Budget and timelines are critical considerations for any engineering project or procurement decision. When considering metal 3D printing for drone landing gear, understanding the factors that influence cost and lead time is essential for accurate planning and comparison with traditional manufacturing methods. These factors apply whether ordering single prototypes or larger wholesale batches.
Key Cost Drivers for Metal AM Drone Landing Gear:
- Material Type & Consumption:
- Factor: The cost per kilogram of metal powder varies significantly. High-performance alloys like Ti-6Al-4V are considerably more expensive than AlSi10Mg or stainless steels. The total volume of the part (including supports) directly impacts the amount of material consumed.
- 影響: Material cost is often a major component of the final price. Design optimization (topology optimization, lattices) helps reduce material usage and thus cost.
- Print Time (Machine Utilization):
- Factor: This is determined by the part’s volume, height (number of layers), complexity (scan time per layer), and the chosen layer thickness. Larger and more complex parts take longer to print. The AM machine’s hourly operating rate is a significant cost factor.
- 影響: Longer print times directly increase costs. Optimizing part orientation and minimizing support structures can sometimes reduce print height and time.
- Part Complexity & Design:
- Factor: While AM handles complexity well, extremely intricate designs or those requiring extensive, dense support structures can increase both print time and post-processing effort (support removal). Topology-optimized parts might print efficiently but require significant engineering time upfront.
- 影響: Highly complex geometries requiring significant support or very fine features may increase costs due to longer print/post-processing times.
- Labor & Setup:
- Factor: Costs associated with preparing the build file, setting up the AM machine, loading powder, unloading parts, and performing initial cleaning.
- 影響: Generally a smaller cost component, but relevant, especially for small batches or single prototypes.
- 後処理の要件:
- Factor: The extent and complexity of required post-processing steps significantly impact the final cost. Heat treatment, HIP, extensive CNC machining for tight tolerances, intricate support removal, and high-end surface finishing (polishing, coating) all add costs.
- 影響: Can be a substantial portion of the total cost, especially for high-precision or fatigue-critical parts. Clearly defining necessary post-processing is crucial for accurate quoting.
- Quality Assurance & Inspection:
- Factor: The level of required inspection (visual, dimensional CMM/scanning), material testing (tensile, density), and documentation (certificates of conformity, material traceability reports) adds labor and potentially destructive testing costs. AS9100 requirements typically involve more rigorous QA.
- 影響: Higher quality assurance levels increase costs but are often mandatory for aerospace applications.
- Order Volume (Prototyping vs. Wholesale):
- Factor: While AM avoids tooling costs, economies of scale are less pronounced than in traditional high-volume methods like casting. However, larger batch sizes allow for better machine utilization (nesting multiple parts in one build) and can slightly reduce the cost per part compared to single prototypes due to amortization of setup costs.
- 影響: Per-part cost decreases moderately with volume. AM remains highly cost-effective for low-to-mid volume production of complex parts and customized components.
Typical Lead Times:
Lead times depend heavily on the factors above, particularly part complexity, volume, machine availability, and post-processing requirements.
- プロトタイプ: Simple prototypes might be produced in a matter of days (e.g., 5-10 working days), while complex prototypes requiring significant post-processing could take 2-4 weeks.
- Production Batches (Wholesale): Lead times for production orders can range from several weeks to a few months, depending on the quantity, part complexity, required post-processing, and the supplier’s current capacity. Blanket orders with scheduled releases can help ensure consistent supply for ongoing needs.
Met3dp works closely with customers to provide transparent quotes that break down costs and offer realistic lead time estimates based on specific project requirements. Contact メット3dp today to discuss your drone landing gear project and receive a tailored quote.
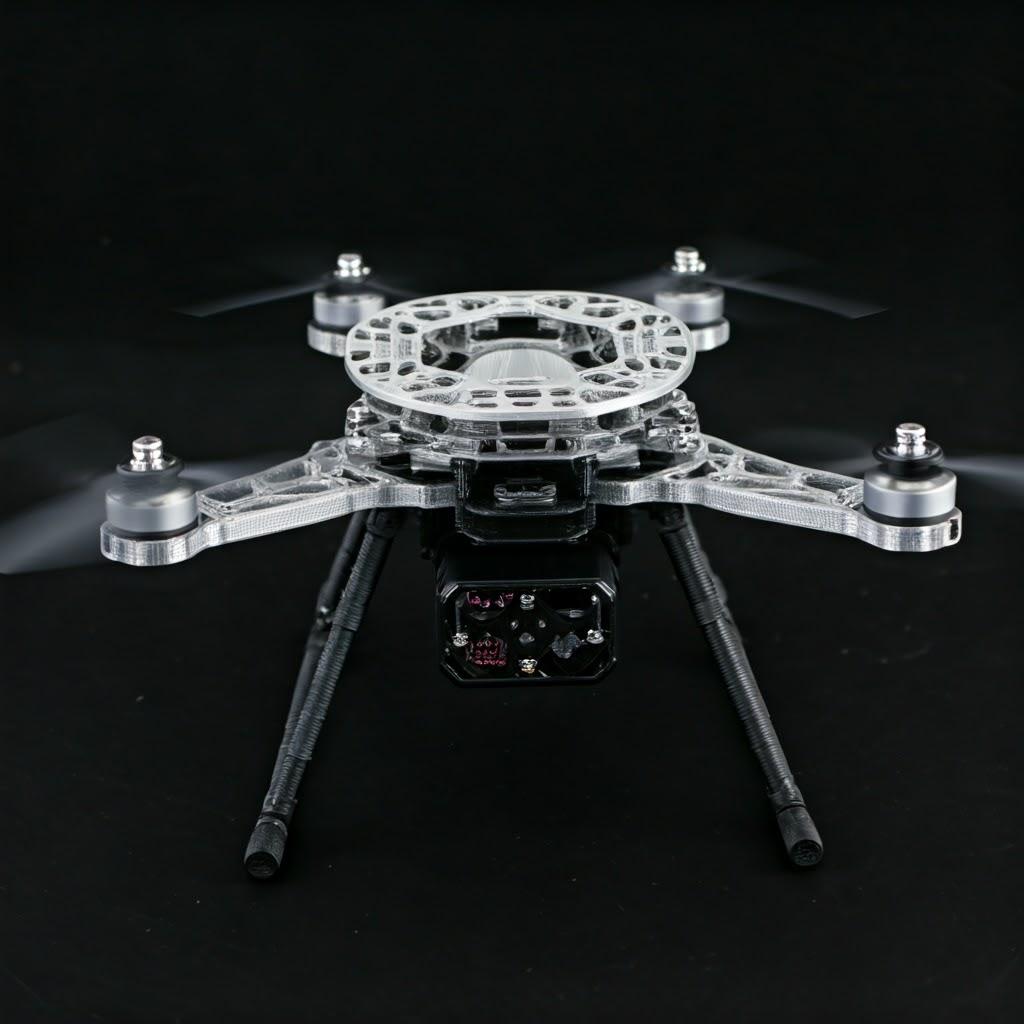
FAQ: Your Questions Answered on 3D Printed Drone Landing Gear
Here are answers to some frequently asked questions regarding the use of metal additive manufacturing for drone landing gear:
Q1: How does the strength of 3D printed metal landing gear compare to traditionally machined or cast components?
A: When using high-performance alloys like Ti-6Al-4V and appropriate process controls and post-processing (like heat treatment and HIP), 3D printed metal components can achieve mechanical properties (tensile strength, fatigue strength) that are comparable or even superior to those of wrought (machined from billet) or cast parts. Furthermore, AM enables topology optimization, allowing designs that achieve the required strength and stiffness at significantly lower weights than traditionally manufactured equivalents. For AlSi10Mg, proper T6 heat treatment is crucial to reach its full strength potential, which is suitable for many applications but generally lower than Ti-6Al-4V or high-strength steels.
Q2: Is metal 3D printing a cost-effective solution for producing drone landing gear, especially for larger quantities (wholesale)?
A: The cost-effectiveness depends on several factors. For highly complex designs, parts requiring significant lightweighting, or components benefiting from part consolidation, AM can be very cost-effective even at lower volumes due to avoided tooling costs and reduced material waste/assembly time. For simpler designs produced in very high volumes, traditional methods like casting or extensive machining might still be cheaper per part if tooling costs are amortized. However, AM is increasingly competitive for low-to-mid volume production runs (dozens to hundreds or even thousands of units, depending on the part) and offers unparalleled advantages in design freedom and speed for customization and iteration. Evaluating the total cost of ownership, including factors like improved drone performance due to lighter weight, is important.
Q3: What are the typical lead times involved in getting 3D printed drone landing gear prototypes and production orders?
A: Lead times vary significantly based on part complexity, size, material, required post-processing, order quantity, and the service provider’s capacity.
- プロトタイプ: Typically range from 5 working days to 4 weeks. Simpler parts in standard materials with minimal post-processing are faster.
- Production Orders: Can range from several weeks (e.g., 4-8 weeks) to a few months for larger quantities or parts requiring extensive post-processing and rigorous quality assurance steps. Establishing clear expectations and communication with your supplier is key.
Q4: Can complex features like internal shock absorption structures or integrated retraction mechanisms be 3D printed?
A: Yes, this is one of the major strengths of metal additive manufacturing. AM excels at creating complex internal geometries like lattice structures specifically designed for energy absorption or vibration damping. It also allows for the consolidation of multiple components, making it possible to print landing gear with integrated features of a retraction mechanism, brackets, or sensor housings as a single piece, reducing part count, weight, and assembly complexity. However, designing such complex, functional integrated systems requires significant DfAM expertise.
Conclusion: Elevating Drone Performance with Met3dp’s Additive Manufacturing Solutions
The demands on drone performance are constantly increasing – longer flight times, heavier payloads, greater reliability, and operation in tougher environments. Drone landing gear, a critical component subjected to repeated stresses, plays a vital role in meeting these demands. As we’ve explored, metal additive manufacturing offers a powerful suite of tools to revolutionize landing gear design and production.
By leveraging metal AM, engineers can:
- Achieve significant lightweighting through topology optimization and lattice structures, directly enhancing flight endurance and payload capacity.
- Create complex geometries integrating multiple functions, reducing part count and assembly complexity.
- Utilize high-performance materials like Ti-6Al-4V and AlSi10Mg, tailored for optimal strength, durability, and corrosion resistance.
- Accelerate prototyping and design iteration, bringing advanced drone concepts to market faster.
However, realizing these benefits requires more than just access to a 3D printer. It demands expertise in Design for Additive Manufacturing (DfAM), meticulous process control, deep materials science knowledge, and robust post-processing capabilities. Choosing the right manufacturing partner is paramount.
Met3dp stands at the forefront of industrial metal additive manufacturing. With our roots in both advanced powder manufacturing using proprietary gas atomization and PREP technologies, and our operation of industry-leading SEBM printing systems, we offer a vertically integrated approach. Our comprehensive solutions span from supplying high-quality, spherical metal powders (including AlSi10Mg, Ti-6Al-4V, and custom alloys) to providing expert DfAM support, precision printing services, and managing all necessary post-processing steps. Our commitment to quality, reflected in our process controls and focus on industry standards, ensures that the components we deliver meet the stringent requirements of the aerospace and UAV sectors. To learn more 私たちについて and our capabilities, visit our website.
For engineers and procurement managers seeking to push the boundaries of drone performance, partnering with Met3dp provides access to the technology, materials, and expertise needed to produce next-generation, high-performance drone landing gear. Let us help you elevate your UAV capabilities through the power of metal additive manufacturing.
シェアする
MET3DP Technology Co., LTDは、中国青島に本社を置く積層造形ソリューションのリーディングプロバイダーです。弊社は3Dプリンティング装置と工業用途の高性能金属粉末を専門としています。
関連記事
Met3DPについて
最新情報
製品
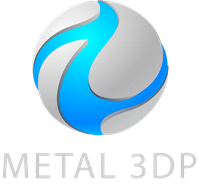
3Dプリンティングと積層造形用金属粉末