Lightweight EV Battery Housing via Metal 3D Printing
目次
Introduction: The Critical Role of Lightweight EV Battery Housings
The electric vehicle (EV) revolution is transforming the automotive landscape, driven by the pursuit of sustainability, efficiency, and enhanced performance. Central to every EV is its battery pack – the powerhouse that dictates range, acceleration, and overall viability. Protecting this critical component is the EV battery housing, an enclosure performing multiple crucial roles beyond simple containment. It must provide robust structural integrity, shield sensitive cells from environmental hazards and potential impacts, manage significant thermal loads generated during charging and discharging, and contribute to the overall safety architecture of the vehicle. However, traditional manufacturing methods often result in battery housings that add considerable weight, directly impacting the vehicle’s range and efficiency – two key metrics for EV adoption.
Engineers and procurement managers in the automotive sector face persistent challenges in designing and sourcing battery housings that meet stringent requirements:
- 軽量化: Every kilogram saved translates to increased range or improved performance dynamics. Lightweighting is paramount in EV design.
- Structural Integrity & Safety: The housing must withstand vibrations, shocks, and, critically, protect the battery cells during crash events, preventing thermal runaway. Compliance with rigorous automotive safety standards (e.g., FMVSS, ECE regulations) is non-negotiable.
- 熱管理: Efficiently dissipating heat is vital for battery longevity, performance, and safety. Housings often require integrated cooling systems or features that facilitate heat exchange.
- Packaging & Space Optimization: Fitting large battery packs into vehicle platforms demands compact and efficiently designed enclosures.
- 費用対効果: While performance is key, solutions must be scalable and economically viable, especially as EV production volumes increase.
Addressing these interconnected challenges demands innovative approaches. This is where 金属積層造形(AM), commonly known as metal 3D printing, emerges as a transformative technology. By building components layer by layer directly from digital designs using high-performance metal powders, AM unlocks design possibilities and performance characteristics previously unattainable. For EV battery housings, metal AM offers a compelling pathway to creating lighter, stronger, and more thermally efficient enclosures, accelerating innovation in electric mobility. Companies are increasingly looking for reliable 付加製造ソリューション to gain a competitive edge in the rapidly evolving automotive lightweighting race.
What are EV Battery Housings Used For?
について electric vehicle battery enclosure is far more than just a box. It is a multi-functional, highly engineered system critical to the safe and efficient operation of the vehicle. Understanding its diverse functions highlights the complexity involved in its design and manufacture:
- Battery Cell Protection: The primary function is to physically shield the delicate battery cells (often lithium-ion) from external factors like moisture, dust, debris, and physical impacts. This ensures the longevity and reliable operation of the battery pack.
- Structural Support: The housing contributes significantly to the overall structural rigidity of the EV chassis, particularly in skateboard-style platforms where the battery pack forms part of the vehicle’s floor structure. It must withstand significant static and dynamic loads during driving.
- Thermal Regulation: Battery performance and lifespan are highly sensitive to temperature. The housing plays a crucial role in the EV thermal management system. This can involve passive cooling fins, interfaces for liquid cooling plates, or even integrated cooling channels directly within the housing walls, a feature uniquely enabled by additive manufacturing.
- Environmental Sealing: A robust seal is necessary to prevent ingress of water, salt, and other contaminants that could cause short circuits or corrosion, compromising safety and performance. IP ratings (Ingress Protection) like IP67 or higher are common requirements.
- Crash Safety: In the event of a collision, the battery housing must protect the cells from rupture or penetration, which could lead to dangerous thermal runaway events. It needs to absorb impact energy and maintain structural integrity under extreme conditions. This involves careful material selection and structural design.
- Electrical Insulation & EMI Shielding: The housing must help contain the high voltages within the pack and potentially provide electromagnetic interference (EMI) shielding to protect sensitive electronics within the vehicle.
Key Industries and Applications:
The primary consumers are EV manufacturers (OEMs) and their Tier 1 suppliers responsible for battery pack assembly. However, the technology is also relevant for:
- High-Performance and Luxury EVs: Where maximizing performance and minimizing weight are critical design goals.
- Electric Motorsport: Where bespoke, highly optimized, and lightweight components are essential.
- Specialty Electric Vehicles: Including buses, trucks, off-highway vehicles, and even electric aircraft (eVTOL), all requiring tailored battery protection solutions.
- Prototype Development: AM allows for rapid iteration and functional testing of new housing designs without the need for expensive tooling.
- Small-Series Production: For niche vehicles or initial production runs, AM can be more cost-effective than investing in traditional tooling.
As the demand for sophisticated EV component suppliers grows, understanding the multifaceted role of the battery housing is essential for delivering effective and safe solutions.
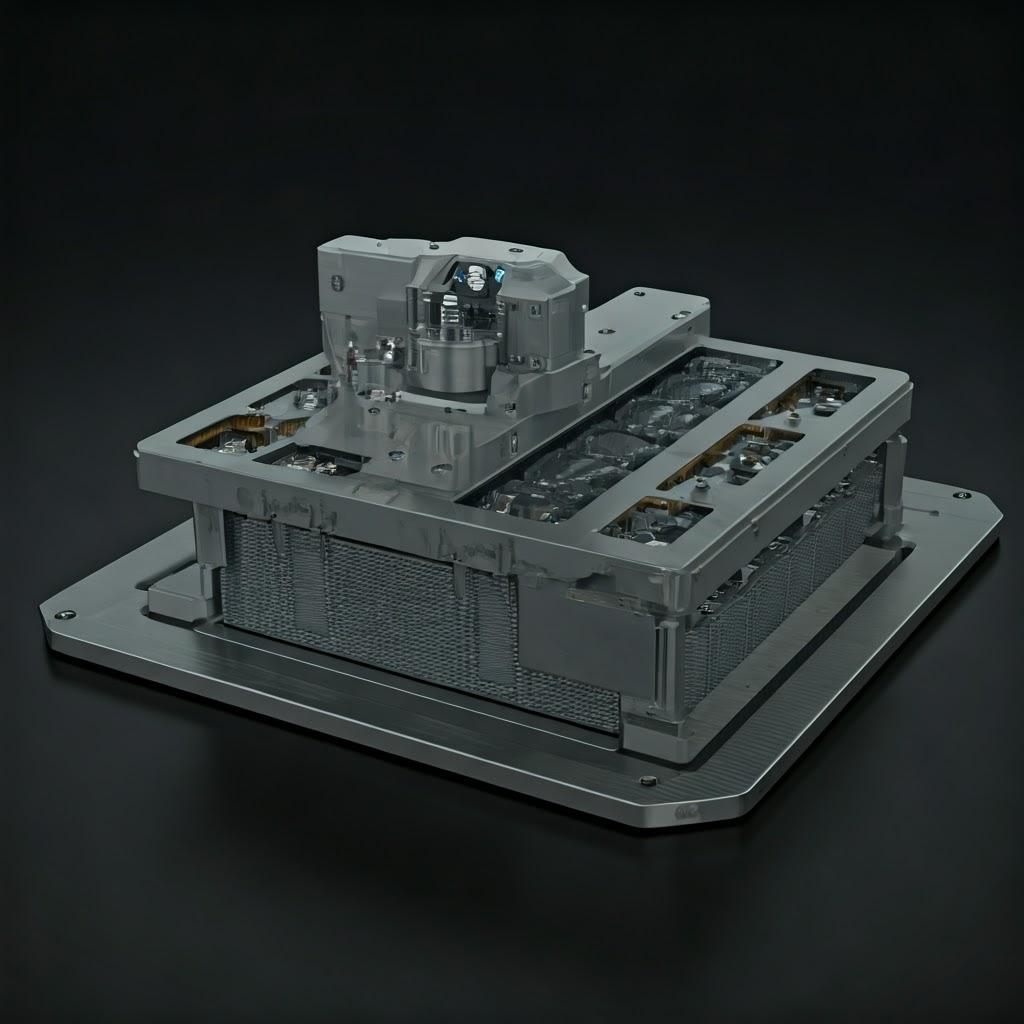
Why Use Metal 3D Printing for EV Battery Housings?
While traditional methods like high-pressure die casting (HPDC), sheet metal stamping, and CNC machining are established for producing automotive components, they present limitations when designing advanced EV battery housings, particularly regarding weight and thermal management complexity. Metal additive manufacturing offers significant advantages, making it an increasingly attractive option for automotive structural components like battery enclosures:
Advantages Over Traditional Methods:
- 比類なき設計の自由度: AM liberates designers from the constraints of traditional manufacturing. Complex internal features, such as intricate cooling channels following the exact contours of battery modules, can be directly integrated into the housing structure. This level of geometric complexity is often impossible or prohibitively expensive to achieve with casting or machining.
- Example: Designing conformal cooling channels that precisely match heat generation zones within the battery pack.
- Topology Optimization for Lightweighting: Using sophisticated software algorithms, designers can optimize the housing’s structure, placing material only where it’s needed to withstand specific loads. This results in organic-looking, highly efficient structures that significantly reduce weight compared to conventionally designed parts, directly addressing the lightweight design EV challenge.
- パーツの統合: Multiple components that would traditionally be manufactured separately and then assembled (e.g., housing base, cooling plates, brackets, interfaces) can potentially be redesigned and printed as a single, integrated unit. This reduces assembly time, eliminates potential leak paths, simplifies the supply chain, and often improves structural integrity.
- ラピッドプロトタイピングと反復: Creating prototypes using AM is significantly faster and less expensive than producing molds or dies for casting or setting up complex machining operations. This allows engineers to quickly test different designs, validate thermal performance, and iterate towards an optimal solution, drastically shortening development cycles for rapid prototyping EV parts.
- 材料効率: AM is an additive process, meaning material is added layer by layer, resulting in less material waste compared to subtractive processes like CNC machining, which starts with a solid block and removes material. While powder reuse is critical, the buy-to-fly ratio can be significantly better.
- オンデマンド製造: Digital designs can be sent to any capable metal AM system globally, enabling decentralized production and reducing reliance on complex supply chains and tooling inventory. This is particularly valuable for low-to-mid volume production or spare parts.
Benefits Summarized:
特徴 | Benefit for EV Battery Housing | Traditional Method Limitation |
---|---|---|
デザインの自由 | Integrated complex cooling, optimized shapes, conformal features | Mold/die constraints, machining access limitations |
Topology Optimization | Significant weight reduction (improved range/performance) | Difficult to achieve extreme lightweighting efficiently |
部品の統合 | Reduced assembly, fewer potential leak points, improved stiffness | Multiple parts require joining (welding, fasteners, seals) |
ラピッドプロトタイピング | Faster design validation, reduced development time & cost | High tooling costs & long lead times for prototypes |
Potential for Cost Savings | Lower cost for complex, low-volume parts (no tooling) | Tooling amortization requires high volumes |
Enhanced Thermal Mgmt. | More efficient cooling systems directly within the structure | Often relies on separate, less integrated cooling components |
Export to Sheets
探検 metal AM benefits automotive applications reveals a clear potential for overcoming the limitations of conventional processes, particularly when complexity, weight, and thermal performance are paramount, as they are with EV battery housings. Companies seeking cutting-edge solutions often compare additive manufacturing vs casting or machining to determine the best fit for their specific volume and complexity needs.
Recommended Aluminum Alloys & Why They Matter
Selecting the right material is crucial for the success of any engineering application, and 3D printed EV battery housings are no exception. Aluminum alloys are the front-runners due to their excellent balance of low density (lightweight), good thermal conductivity, adequate strength, and corrosion resistance. For metal additive manufacturing, specific aluminum alloys have proven particularly effective. Met3dp, leveraging its advanced powder production capabilities, including industry-leading gas atomization and Plasma Rotating Electrode Process (PREP) technologies, ensures the supply of high-quality, spherical aluminum 3D printing powders optimized for demanding applications like EV battery housings. Our focus on powder characteristics like high sphericity and good flowability translates directly into denser, more reliable printed parts.
Here are the top recommendations for this application:
1. AlSi10Mg:
- 説明 An aluminum alloy containing silicon and magnesium, traditionally used in casting. It translates well to powder bed fusion processes.
- キー・プロパティ
- Excellent printability and processability in Laser Powder Bed Fusion (LPBF).
- Good strength and hardness, suitable for structural components.
- Good thermal conductivity.
- Can be heat-treated (e.g., T6 condition) to significantly improve strength and hardness.
- Why it Matters for Battery Housings: Offers a robust combination of mechanical properties, good thermal performance, and reliable printing characteristics. Its cast-equivalent nature makes it familiar to engineers. The ability to heat treat allows tailoring properties post-printing. See our full range of 金属粉.
- 検討する: Strength is generally lower than high-strength 7xxx series alloys.
2. A6061 (Often requires specialized parameters or post-processing):
- 説明 A widely used wrought aluminum alloy known for its versatility, strength, weldability, and corrosion resistance. Printing 6061 can be more challenging than AlSi10Mg due to its solidification characteristics but is achievable with optimized parameters and potentially specialized machines.
- キー・プロパティ
- Good mechanical strength and toughness.
- 優れた耐食性。
- Good thermal conductivity.
- Can be heat treated (e.g., T6) for significantly enhanced strength.
- Good weldability (important if post-fabrication joining is needed).
- Why it Matters for Battery Housings: Its all-around performance, particularly corrosion resistance and post-processing weldability, makes it appealing. If T6 properties are required, it offers higher strength than AlSi10Mg T6 typically achieves in AM.
- 検討する: Can be prone to hot cracking during printing; requires careful parameter control and often specific heat treatments to achieve desired properties. Often requires collaboration with experienced AM providers like Met3dp.
3. A7075 (High Strength Applications):
- 説明 A high-strength aluminum-zinc alloy, typically used in aerospace and high-performance applications where strength-to-weight ratio is paramount. Printing 7075 poses challenges but offers top-tier mechanical properties.
- キー・プロパティ
- Very high strength-to-weight ratio, among the highest for aluminum alloys.
- Good fatigue strength.
- Can be heat treated to achieve peak strength (e.g., T6, T73).
- Why it Matters for Battery Housings: Ideal for applications demanding maximum lightweighting without compromising strength, such as performance EVs or motorsport battery enclosures. Allows for thinner walls and more aggressive topology optimization.
- 検討する: More challenging to print reliably than AlSi10Mg due to susceptibility to solidification cracking and residual stress. Corrosion resistance is generally lower than 6061, potentially requiring protective coatings. Requires significant expertise in process parameter development and post-process heat treatment.
Material Properties Comparison (Typical Values for AM – can vary significantly with parameters/post-processing):
プロパティ | AlSi10Mg (As-Built / T6) | A6061 (T6) | A7075 (T6 / T73) | 単位 | Importance for Battery Housing |
---|---|---|---|---|---|
密度 | ~2.67 | ~2.70 | ~2.81 | g/cm³ | Lower is better (Lightweighting) |
引張強度 | ~290 / ~330+ MPa | ~270 – 310+ MPa | ~500 – 570+ MPa | MPa | Structural Integrity, Crash Safety |
降伏強度 | ~180 / ~230+ MPa | ~240 – 275+ MPa | ~450 – 500+ MPa | MPa | Resistance to permanent deformation |
破断伸度 | ~6-10% / ~3-6% | ~8-12% | ~5-10% | % | Ductility, Impact Resistance |
熱伝導率 | ~130-150 | ~150-170 | ~130-150 | W/(m-K) | Heat Dissipation (Thermal Mgmt.) |
印刷適性 | 素晴らしい | Moderate (Needs Control) | チャレンジング | – | Manufacturability, Reliability |
耐食性 | グッド | 素晴らしい | Fair (Needs Protection) | – | Durability, Environmental Sealing |
Export to Sheets
Why Met3dp Powders Matter:
The theoretical properties of an alloy are only achievable if the starting material – the metal powder – is of exceptional quality. Met3dp utilizes advanced ガス噴霧 そして PREP(プラズマ回転電極プロセス) technologies. Our unique nozzle and gas flow designs in gas atomization produce powders with:
- 高い真球度: Ensures good powder flowability and dense packing on the powder bed, minimizing voids and porosity in the final part.
- Low Satellite Content: Reduces irregularities, leading to more uniform melting and solidification.
- Controlled Particle Size Distribution (PSD): Optimized for specific AM processes (LPBF, EBM) to ensure consistent layer deposition and melting behavior.
- 高純度: Minimizing contaminants that can compromise mechanical properties.
By controlling these powder characteristics, Met3dp provides high-performance aluminum alloys that enable our customers to reliably print dense, high-quality EV battery housings with superior mechanical properties and performance, directly leveraging the advantages of 金属3Dプリンティング. Choosing the right powder is the foundation for successful additive manufacturing.
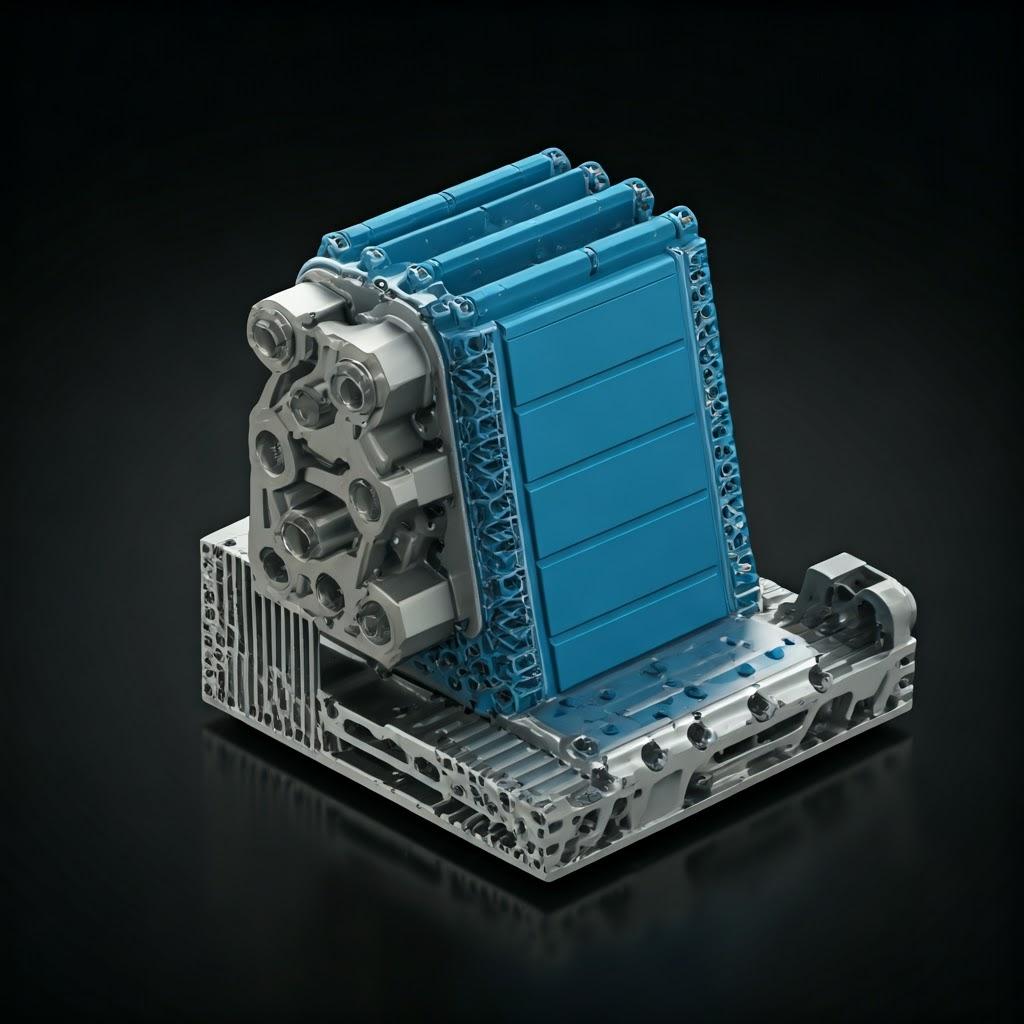
Design Considerations for Additive Manufacturing (DfAM) of Battery Housings
Simply replicating a design intended for casting or machining often fails to leverage the true potential of metal additive manufacturing. To unlock significant benefits in weight reduction, thermal performance, and functional integration for EV battery housings, designers must embrace 積層造形設計 (DfAM) principles. This involves rethinking the part’s geometry from the ground up, considering the layer-by-layer build process.
Key DfAM Principles for EV Battery Housings:
- Topology Optimization: This is arguably the most impactful DfAM technique for lightweighting.
- プロセス Using specialized software, engineers define the part’s functional requirements (load cases, mounting points, keep-out zones, performance targets like stiffness). The software then iteratively removes material from areas where it doesn’t contribute significantly to performance, leaving behind an optimized, often organic-looking structure.
- Benefit: Achieves maximum possible weight reduction while meeting or exceeding structural performance requirements. Ideal for DfAM automotive components where weight is critical.
- Example: Transforming a solid, blocky housing bracket into a skeletal structure that efficiently transfers loads.
- Lattice Structures & Infill: Instead of solid material, internal volumes can be filled with engineered lattice structures.
- 種類だ: Strut-based lattices, TPMS (Triply Periodic Minimal Surfaces) gyroids, etc.
- メリット Drastic weight reduction, tailored energy absorption characteristics (crucial for crash safety), increased surface area (beneficial for passive cooling or integration with active cooling systems), potential for vibration damping.
- アプリケーション Filling non-critical structural volumes or creating lightweight core structures within the housing walls. Exploring metal lattice structures offers new avenues for multi-functional design.
- Integrated & Conformal Cooling Channels: AM allows the creation of complex internal cooling channels that precisely follow the contours of heat-generating components (battery modules).
- Advantage: Far more effective heat transfer compared to traditional cooling plates or simple drilled channels. Improves battery performance, longevity, and safety.
- デザイン: Requires careful consideration of fluid flow (CFD analysis), channel diameter, surface roughness (as-printed vs. post-processed), and ensuring channels are self-supporting or designed for feasible support removal. Conformal cooling 3D printing is a major advantage for thermal management.
- Feature Integration & Part Consolidation: AM enables merging multiple parts into a single, complex component.
- 例を挙げよう: Integrating brackets, mounting bosses, fluid connectors, sealing grooves, or heat sinks directly into the main housing structure.
- メリット Reduces part count, eliminates assembly steps and associated tolerances/costs, removes potential leak paths (e.g., seals between assembled parts), simplifies supply chain, often increases overall stiffness and robustness.
- Designing for Self-Support & Support Minimization: Support structures are often necessary in metal PBF processes to anchor the part to the build plate and support overhanging features. However, they add material cost, print time, and require removal effort, potentially impacting surface finish.
- Strategy: Design features with self-supporting angles (typically >45 degrees from the horizontal plane for LPBF). Orient the part strategically on the build plate to minimize the need for supports, especially in hard-to-reach internal areas like cooling channels. Consider sacrificial features that support critical areas but are easily machined away later. Support minimization AM is key to cost-effective printing.
- Wall Thickness & Feature Size: AM processes have limitations on minimum printable wall thickness and feature resolution (dependent on machine, material, parameters).
- Consideration: Ensure designs respect these limits. Thin walls are key for lightweighting but must maintain structural integrity and print reliably. Incorporate fillets and smooth transitions to reduce stress concentrations.
DfAM Workflow Summary:
- Define Requirements: Loads, thermal targets, interfaces, constraints.
- Conceptual Design (AM-Focused): Explore topology optimization, lattices, feature integration.
- Detailed Design & Simulation: Refine geometry, run FEA (structural) and CFD (thermal/fluid) analyses. Simulate the build process to predict potential issues (stress, distortion).
- Optimize for Printing: Final adjustments for orientation, support strategy, minimum features.
By adopting a DfAM mindset, engineers can transform the EV battery housing from a simple container into a highly optimized, multi-functional system component, fully utilizing the capabilities offered by advanced 印刷方法 like those employed by Met3dp.
Achievable Tolerance, Surface Finish, and Dimensional Accuracy
While metal AM offers incredible design freedom, it’s essential to understand the achievable levels of precision. Engineers and procurement managers must have realistic expectations regarding tolerances, surface finish, and overall dimensional accuracy for 3D printed EV battery housings. These factors are critical for ensuring proper assembly, sealing, and functionality.
Tolerances:
- Typical Ranges: For metal Powder Bed Fusion (PBF) processes like Laser PBF (LPBF/SLM) and Electron Beam PBF (EB-PBF), typical as-built dimensional tolerances are often in the range of ±0.1mm to ±0.3mm or ±0.1% to ±0.2% of the dimension, whichever is larger. However, this can vary significantly.
- Factors Influencing Tolerances:
- Machine Calibration & Condition: Regular calibration and maintenance are crucial. Met3dp emphasizes the accuracy and reliability of its printing systems for mission-critical parts.
- Process Parameters: Layer thickness, laser/beam power, scan speed, hatching strategy all play a role.
- 素材の特性: Different alloys exhibit varying shrinkage and thermal behavior during melting and solidification.
- Part Geometry & Size: Larger parts and complex geometries are more prone to thermal distortion and deviation. Residual stress build-up can warp parts.
- Build Orientation & Supports: How the part is positioned and supported affects accuracy.
- 後処理: Stress relief heat treatments can cause minor dimensional changes. Machining achieves much tighter tolerances on specific features.
- Achieving Tighter Tolerances: For critical features (e.g., mating surfaces, bearing interfaces, sealing grooves), tolerances down to ±0.01mm to ±0.05mm can be achieved through post-process CNC machining. It’s often most cost-effective to print near-net shape and machine only the critical interfaces.
Surface Finish (Roughness):
- As-Built Surface Roughness (Ra): The surface finish of as-printed metal AM parts is inherently rougher than machined surfaces.
- Typical Values: Ra values often range from 6µm to 25µm, depending on the process (LPBF generally smoother than EB-PBF), material, orientation (upward-facing vs. downward-facing/supported surfaces), and parameters.
- 影響: Affects sealing effectiveness, fluid flow in channels, fatigue life, and aesthetics.
- 表面仕上げの改善: Post-processing is typically required to achieve smoother finishes.
- Abrasive Blasting (Sand, Bead): Provides a uniform matte finish, removing loose powder (Ra often 5-15µm).
- Tumbling/Vibratory Finishing: Smoothens surfaces and edges (Ra can reach 1-5µm).
- Machining/Grinding: Achieves very smooth finishes comparable to traditional manufacturing (Ra < 1µm possible).
- 研磨: For mirror-like finishes, often required for specific applications.
- Abrasive Flow Machining (AFM): Can be used to smooth internal channels.
- Design Consideration: Specify required surface finishes only where functionally necessary (e.g., sealing faces, interfaces) to control costs, as extensive surface finishing adds significant expense.
Dimensional Accuracy Management:
- Simulation: Build process simulation can predict distortion and allow for compensation in the initial design file.
- 品質管理: Post-print inspection using CMM (Coordinate Measuring Machines) or 3D scanning is essential to verify dimensional accuracy against the CAD model and specifications.
- Collaboration: Working closely with an experienced AM provider like Met3dp, who understands process capabilities and material behavior, is crucial for achieving the desired dimensional accuracy EV parts.
Summary Table: Precision Expectations
パラメータ | As-Built Typical Range | Achievable with Post-Processing | 主な検討事項 |
---|---|---|---|
寛容 | ±0.1 to ±0.3 mm / ±0.1-0.2% | Down to ±0.01 – 0.05 mm (Machining) | Part size, complexity, material, critical features |
Surface Finish (Ra) | 6µm – 25µm+ | < 1µm – 15µm (Various Methods) | Sealing, fatigue, flow, aesthetics, cost |
Export to Sheets
Understanding these parameters allows for realistic design specifications and informs decisions about necessary post-processing steps to ensure the final EV battery housing meets all functional requirements for 精密積層造形.
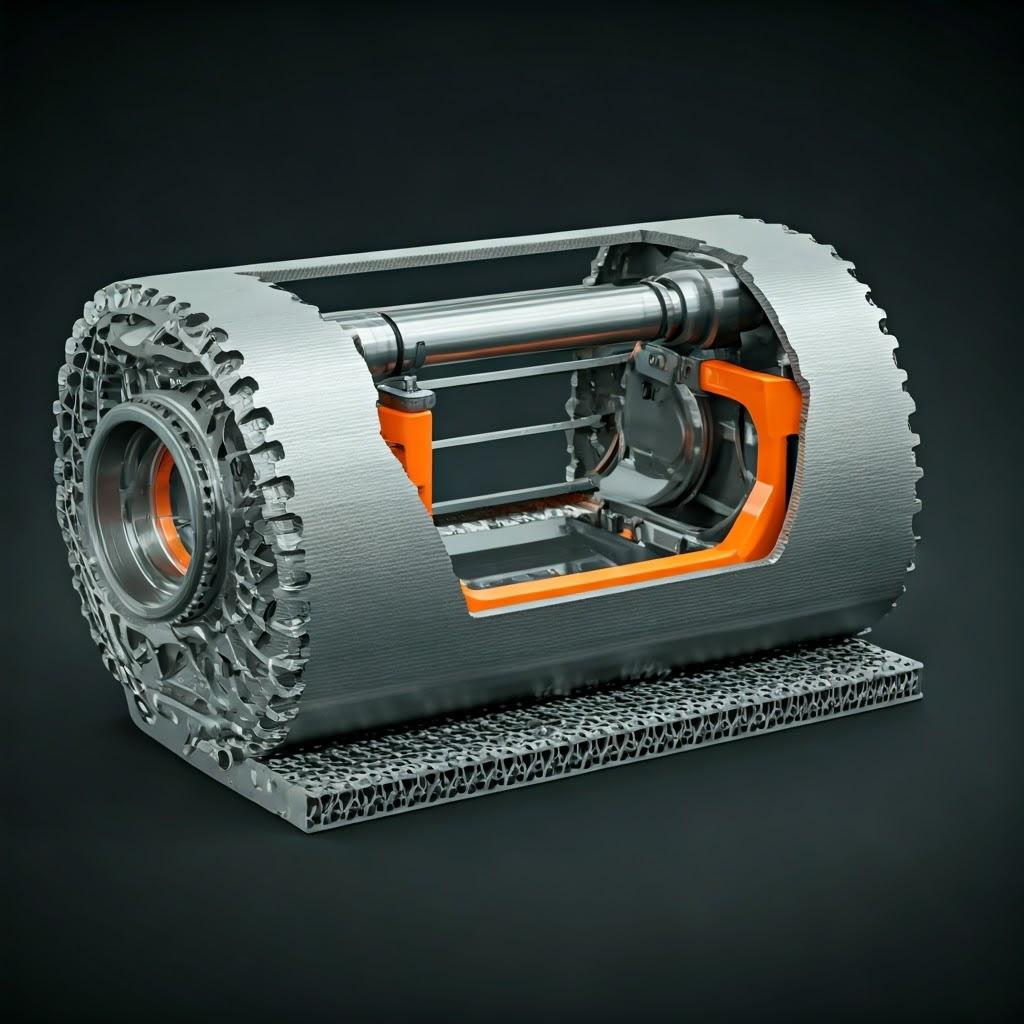
Post-Processing Requirements for Metal AM Battery Housings
A metal 3D printed part, upon removal from the build chamber, is rarely ready for its final application. This is especially true for demanding components like EV battery housings. A series of post-processing metal 3D printing steps are typically required to achieve the necessary material properties, dimensional accuracy, surface characteristics, and overall quality.
Common Post-Processing Steps:
- Stress Relief / Heat Treatment:
- 目的 To relieve internal stresses built up during the rapid heating and cooling cycles of the printing process, preventing distortion or cracking, and to achieve the desired final material microstructure and mechanical properties (e.g., strength, hardness, ductility).
- Method: Parts (often while still attached to the build plate) are heated in a controlled atmosphere furnace following specific temperature profiles (time, temperature, cooling rate) tailored to the alloy (e.g., T6 aging for aluminum heat treatment T6 AM). This is critical for alloys like AlSi10Mg, A6061, and A7075.
- Importance: Absolutely essential for structural integrity and predictable performance.
- Part Removal from Build Plate:
- Method: Typically done using wire EDM (Electrical Discharge Machining), sawing, or machining.
- Consideration: Careful removal is needed to avoid damaging the part.
- 支持構造の撤去:
- 目的 To remove the temporary structures used during the build process.
- 方法: Can involve manual breaking (for easily accessible supports), cutting tools, CNC machining, or sometimes wire EDM. Support removal metal 3D printing can be labor-intensive, especially for complex internal geometries.
- 課題だ: Accessing internal supports (e.g., within cooling channels) can be difficult and may require specialized techniques or DfAM considerations (designing for removal). Residual marks (support “witness marks”) may need further finishing.
- CNC Machining:
- 目的 To achieve tight tolerances on critical features, create flat sealing surfaces, drill/tap precise holes, and improve surface finish on specific areas.
- アプリケーション Essential for mating faces, mounting points, sealing grooves, bearing seats, and any dimension requiring higher precision than achievable in the as-built state. CNC machining AM parts is a standard practice for functional components.
- Surface Finishing & Cleaning:
- 目的 To remove loose powder, improve surface roughness, enhance aesthetics, or prepare the surface for coating.
- 方法:
- Abrasive Blasting (Sand/Bead): Creates a uniform matte finish.
- Tumbling/Vibratory Finishing: Smoothens surfaces and edges.
- 研磨: For very smooth or reflective surfaces.
- Abrasive Flow Machining (AFM) / Extrude Hone: Used to smooth internal channels by flowing abrasive media through them.
- クリーニング: Ultrasonic cleaning or chemical washing to remove trapped powder residues.
- Importance: Critical for sealing, fluid flow, fatigue life, and preventing powder contamination.
- Coating / Surface Treatment:
- 目的 To enhance corrosion resistance (especially for alloys like A7075), improve wear resistance, provide electrical insulation, or alter thermal properties.
- 方法: Anodizing (for aluminum), painting, powder coating, chemical conversion coatings (e.g., chromate conversion), plating. Surface treatment 3D printed metal adds protective layers.
- Inspection and Quality Control (QC):
- 目的 To verify that the final part meets all specifications.
- 方法:
- 寸法検査: CMM, 3D scanning.
- Material Property Testing: Tensile tests on representative samples.
- 非破壊検査(NDT): CT scanning (to inspect internal features and detect porosity), dye penetrant testing, ultrasonic testing.
- Leak Testing: Crucial for battery housings to ensure sealing integrity (pressure decay, helium leak testing).
- Importance: Ensures safety, reliability, and performance. Robust quality control additive manufacturing protocols are essential for automotive applications.
The extent and type of post-processing depend heavily on the specific application requirements, material choice, and design complexity. It’s crucial to factor these steps into the overall cost and lead time calculations when considering metal AM for EV battery housings. Partnering with a provider like Met3dp, who offers comprehensive solutions potentially including post-processing or manages a network of qualified partners, streamlines this workflow. Learn more 私たちについて and our capabilities.
Common Challenges in 3D Printing EV Battery Housings and Solutions
While metal AM offers tremendous advantages, printing large, complex components like EV battery housings is not without its challenges. Awareness of these potential issues and implementing appropriate mitigation strategies are key to successful outcomes.
1. Warping and Residual Stress:
- チャレンジ: The high thermal gradients inherent in PBF processes can cause significant internal stresses to build up within the part and at the interface with the build plate. This can lead to warping during the build, distortion after removal from the plate, or even cracking. Residual stress mitigation AM is a major focus.
- Solutions:
- Process Simulation: Predict stress accumulation and distortion, allowing for design compensation or optimized orientation/support strategies.
- Optimized Build Strategy: Careful selection of build orientation, robust support structures designed to anchor the part and manage heat.
- Parameter Optimization: Fine-tuning laser/beam power, scan speed, and layer thickness.
- Build Plate Heating: Maintaining an elevated temperature can reduce thermal gradients.
- Mandatory Stress Relief: Post-build heat treatment is crucial, often performed before removing the part from the build plate.
2. Support Removal from Complex Internal Geometries:
- チャレンジ: Integrated features like complex cooling channels, while a key benefit of AM, make support removal extremely difficult or impossible if not designed correctly. Trapped powder or support remnants compromise functionality (flow, heat transfer) and risk contamination. Internal support removal AM requires careful planning.
- Solutions:
- DfAM for Accessibility: Design channels with access points for tools or flushing media. Optimize channel paths and cross-sections to be self-supporting where possible.
- Specialized Removal Techniques: Abrasive flow machining (AFM), chemical etching (less common for aluminum supports), high-pressure fluid flushing.
- Post-Print Machining: Design parts so internal features can be accessed and finished via machining if necessary.
- Careful Inspection: Use methods like endoscopy or CT scanning to verify channel cleanliness.
3. Porosity:
- チャレンジ: Small voids or pores can form within the printed material due to trapped gas or incomplete fusion between layers. Porosity can significantly degrade mechanical properties (especially fatigue strength) and potentially create leak paths.
- Solutions:
- High-Quality Powder: Using powder with high sphericity, low internal gas porosity, and controlled particle size distribution, like the 高品質の金属粉 produced by Met3dp using advanced atomization, is fundamental. Low-quality powder is a primary cause of porosity.
- Optimized Process Parameters: Ensuring sufficient energy density for complete melting and appropriate shielding gas flow (in LPBF) to remove process byproducts.
- 熱間静水圧プレス(HIP): A post-processing step involving high temperature and pressure, which can effectively close internal pores, significantly improving density and mechanical properties. Often used for critical applications. Porosity reduction metal printing is key for structural parts.
4. Achieving Leak-Tightness:
- チャレンジ: Battery housings require excellent sealing (e.g., IP67 or higher) to protect cells from the environment. Achieving this with AM requires careful attention to design, surface finish, and potential porosity.
- Solutions:
- DfAM for Sealing: Incorporate well-defined sealing grooves designed for standard O-rings or gaskets. Ensure adequate wall thickness.
- Surface Finish Control: Machine sealing surfaces to achieve required smoothness and flatness.
- ポロシティ・コントロール: Minimize porosity through powder quality and parameter optimization, potentially using HIP.
- Impregnation/Sealing: In some cases, vacuum impregnation with sealant resins can close off remaining micro-porosity (use depends on application compatibility).
- Rigorous Leak Testing: Implement robust leak testing protocols (e.g., pressure decay, tracer gas) as part of the QC process. Ensuring leak proof 3D printing が重要だ。
5. Managing Large Build Sizes:
- チャレンジ: Battery housings can be large components, potentially exceeding the build volume of standard metal AM machines.
- Solutions:
- Large Format Printers: Utilize machines with larger build envelopes specifically designed for sizable components. Met3dp offers printers with industry-leading print volume.
- Segmentation: Design the housing in multiple sections that can be printed separately and then joined (e.g., via welding – necessitates using a weldable alloy like A6061 and careful joint design).
- ハイブリッド製造: Combine AM for complex sections with traditional manufacturing for simpler, larger elements.
6. Cost-Effectiveness vs. Traditional Methods:
- チャレンジ: While AM eliminates tooling costs, the cost per part (driven by material, machine time, post-processing) can be higher than traditional methods like casting, especially at high production volumes.
- Solutions:
- Leverage Complexity: Focus AM on designs where the added value (lightweighting, integrated features, performance) justifies the cost, particularly for complex parts where traditional tooling would be extremely expensive.
- Optimize Design (DfAM): Minimize material usage through topology optimization, reduce build time via orientation and support strategy, design for efficient post-processing.
- Target Applications: Ideal for prototypes, low-to-mid volume production, highly customized parts, or where rapid development cycles are critical. Analyze the Total Cost of Ownership (TCO), considering factors beyond just the part price (assembly simplification, improved vehicle performance). Evaluate large format metal AM cost dynamics.
By understanding these challenges and proactively implementing solutions, often in partnership with an experienced AM provider, manufacturers can successfully harness the power of metal 3D printing for producing advanced, lightweight EV battery housings.
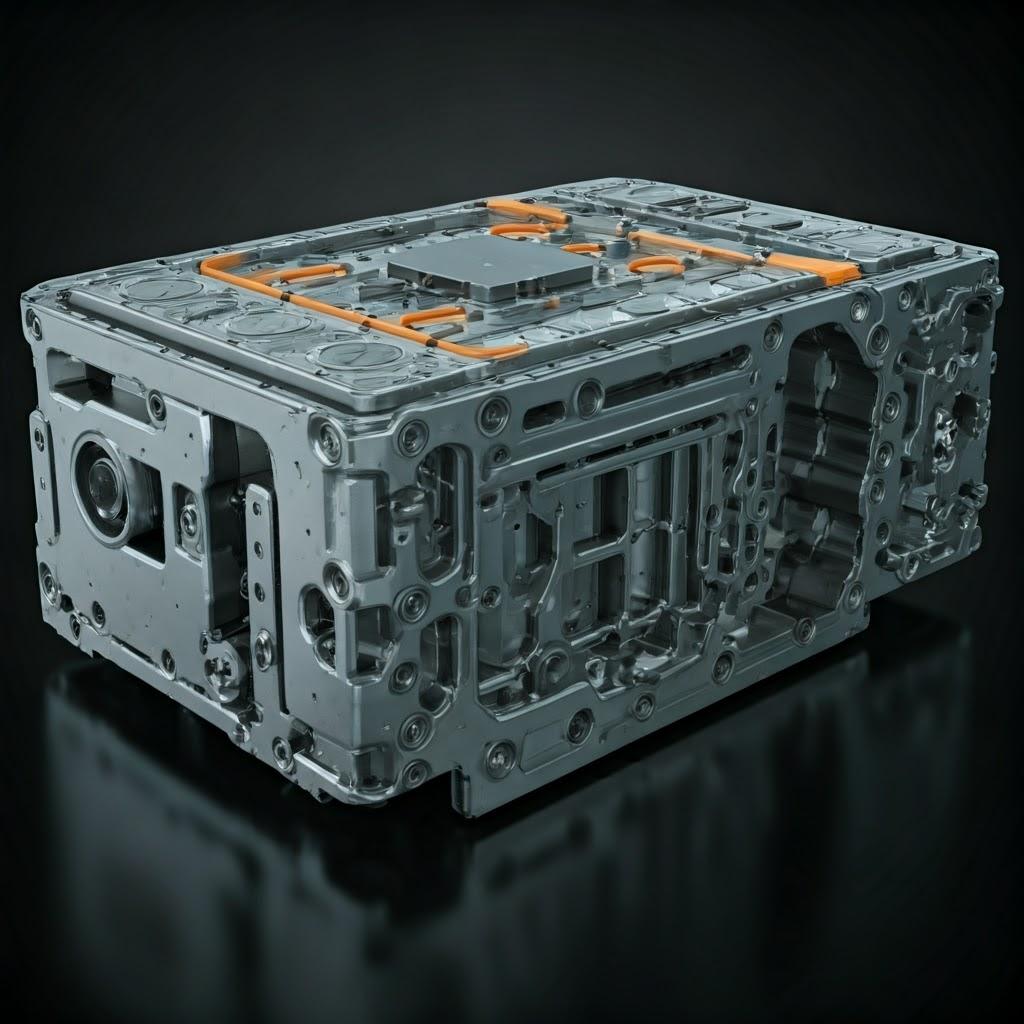
How to Choose the Right Metal 3D Printing Service Provider
Selecting the right manufacturing partner is as critical as the design and material choices when implementing metal additive manufacturing for demanding applications like EV battery housings. The capabilities, experience, and quality systems of your chosen provider will directly impact the success of your project. For engineers and procurement managers navigating the landscape of metal 3D printing service providers automotive, here are key criteria to evaluate:
- Automotive & Application Expertise:
- Does the provider have demonstrable experience with automotive components, particularly structural parts or thermal management systems?
- Do they understand the specific challenges and requirements of EV battery housings (lightweighting, thermal loads, safety standards, sealing)?
- Look for case studies or examples of similar projects.
- Material Expertise (Aluminum Alloys):
- Does the provider specialize in or have extensive experience printing the specific aluminum alloys you require (AlSi10Mg, A6061, A7075)?
- Do they possess validated process parameters and understand the necessary heat treatment protocols (e.g., T6 conditions) to achieve desired mechanical properties?
- Inquire about their material sourcing and quality control. A provider like Met3dp, which manufactures its own 高品質の金属粉 使用して advanced Powder Making Systems like Gas Atomization and PREP, offers greater control over material consistency and quality.
- Machine Capabilities & Technology:
- What types of metal AM technology do they offer (e.g., Laser Powder Bed Fusion – LPBF, Electron Beam Powder Bed Fusion – EB-PBF)?
- Do their machines offer sufficient build volume for your battery housing dimensions? Met3dp prides itself on printers with industry-leading print volume, accuracy and reliability.
- What is the age and condition of their equipment? Is it well-maintained and calibrated?
- Integrated Post-Processing Services:
- Can the provider handle the necessary post-processing steps in-house (heat treatment, CNC machining, surface finishing, inspection)? Or do they have a robust, managed network of qualified partners?
- An integrated service offering simplifies project management and ensures accountability throughout the manufacturing process.
- Quality Management Systems & Certifications:
- Is the provider certified to ISO 9001 (general quality management)?
- For automotive supply chains, IATF 16949 certification is highly desirable, indicating adherence to stringent automotive quality standards.
- Inquire about their quality control procedures, material traceability, and inspection capabilities (CMM, 3D scanning, NDT).
- Technical Support & Collaboration:
- Does the provider offer Design for Additive Manufacturing (DfAM) support or consultation?
- Can they assist with build process simulation or topology optimization?
- Effective communication and a collaborative approach are crucial, especially for complex projects. Met3dp leverages decades of collective expertise in metal additive manufacturing to provide comprehensive solutions and partner with clients.
- Lead Time & Capacity:
- Can they meet your required timelines for prototypes and potential low-volume production?
- Do they have sufficient capacity to handle your project without significant delays?
- Location & Logistics:
- Consider the provider’s location relative to your facilities for shipping time and cost, especially for larger components.
Evaluation Checklist:
基準 | Key Question | 重要性 |
---|---|---|
Automotive Experience | Proven track record with similar automotive parts? | 非常に高い |
Aluminum Alloy Expertise | Deep knowledge of processing & heat treating AlSi10Mg, A6061, A7075? | 非常に高い |
Machine Capability/Volume | Right technology (LPBF/EBPBF) & large enough build envelope? | 高い |
Material Quality Control | Robust procedures? In-house powder production (like Met3dp)? | 非常に高い |
Post-Processing Capability | Integrated services for heat treat, machining, finishing, inspection? | 高い |
品質認証 | ISO 9001 essential, IATF 16949 desirable for automotive? | 非常に高い |
Technical Support / DfAM | Can they assist with design optimization and process simulation? | 高い |
Lead Time / Capacity | Can they meet project deadlines? | 高い |
Communication & Project Mgmt | Clear communication channels & responsive project management? | 高い |
Export to Sheets
Choosing an additive manufacturing partner EV requires due diligence beyond just comparing quotes. Look for a provider like Met3dp that offers a holistic approach, combining advanced technology, material science expertise, and a commitment to quality, positioning themselves as a true partner in innovation.
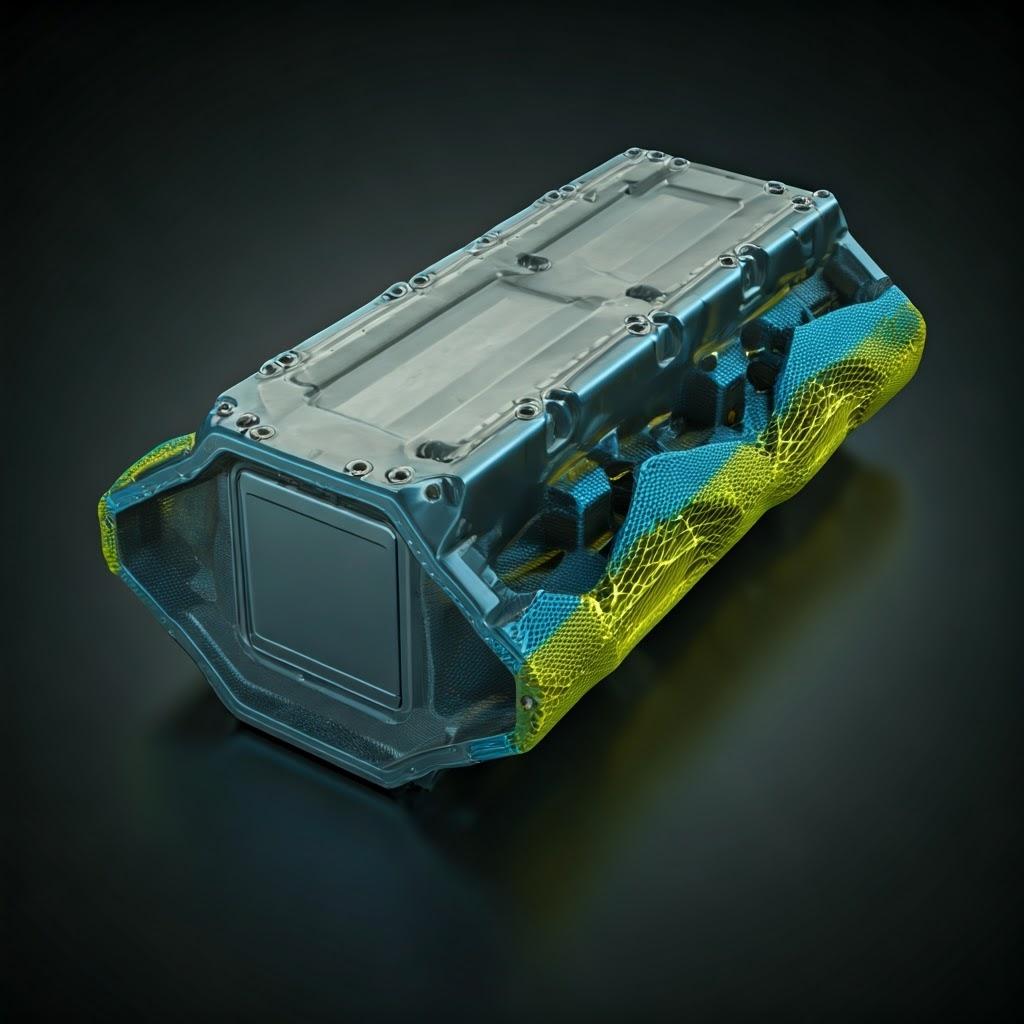
Cost Factors and Lead Time for AM Battery Housings
Understanding the economic and temporal aspects of producing EV battery housings via metal AM is crucial for project planning and budgeting. Both cost and lead time are influenced by several interrelated factors.
Factors Influencing Cost:
- Part Design & Complexity:
- Volume of Material: Directly impacts material cost and print time. Topology optimization significantly reduces this.
- Overall Size: Larger parts occupy the build chamber for longer.
- 複雑さ: Intricate features might require more complex support structures or longer print times per layer, but this is where AM often provides value over traditional methods facing complexity limits.
- 素材の種類
- The cost of specialized metal powders (e.g., high-strength aluminum alloys) varies. Powder quality and production method also influence price.
- マシン・タイム
- A primary cost driver. Calculated based on the total time the part occupies the AM machine. Influenced by part height (number of layers), exposure parameters, and nesting efficiency (printing multiple parts simultaneously).
- サポート体制:
- Volume of material used for supports.
- Labor and time required for support removal, especially for complex internal supports.
- 後処理の要件:
- Heat treatment (furnace time, energy).
- CNC machining (machine time, programming, setup).
- Surface finishing (labor, consumables, specialized equipment like AFM).
- Inspection (level of rigor, equipment used – CMM, CT scanning).
- 労働だ:
- Machine setup, powder handling, part removal, support removal, finishing, inspection.
- 注文量:
- Price per part generally decreases with higher volumes due to amortization of setup costs and potential for build nesting optimization, though the relationship is less steep than with traditional tooling amortization. AM is typically most competitive for EV component prototyping cost and low-to-mid volume series.
- Engineering/Development Support:
- Costs associated with DfAM consultation, simulation services, or process development if required.
Factors Influencing Lead Time:
- Design & File Preparation: Time required for design finalization, DfAM optimization, build simulation, and file preparation.
- Quoting & Order Processing: Administrative overhead.
- Machine Queue: Availability of suitable machines at the service provider.
- 印刷時間: Can range from hours to several days or even weeks depending on part height, volume, and nesting.
- Cooldown Time: Parts need to cool within the machine or build chamber before removal.
- 後処理: Can be a significant portion of the total lead time, involving multiple steps (heat treatment cycles, machining setup/runtime, finishing processes, inspection).
- 配送: Transit time to your facility.
Indicative Lead Times:
- プロトタイプ: Typically range from 1 to 4 weeks, depending heavily on complexity, size, post-processing needs, and provider capacity.
- 少量生産: Can range from several weeks to a few months, depending on the quantity, part complexity, and required process validation/qualification.
It’s essential to get detailed quotes that break down additive manufacturing pricing factors and provide realistic lead time metal AM parts estimates based on your specific design and requirements.
よくある質問(FAQ)
Q1: Is 3D printed aluminum strong enough for a structural EV battery housing?
A: Absolutely. Metal AM processes like LPBF, when combined with appropriate aluminum alloys (like AlSi10Mg, A6061, A7075) and correct post-process heat treatments (e.g., T6 condition), can produce parts with mechanical properties (tensile strength, yield strength) that are comparable or even superior to traditional aluminum castings. Through careful design (DfAM, topology optimization) and process control, 3D printed housings can meet the demanding structural and crash safety requirements for EVs. Partnering with experts ensures proper material selection and processing for optimal strength.
Q2: How does the cost of a 3D printed battery housing compare to a cast or fabricated one?
A: The cost comparison depends heavily on volume and complexity.
- Prototypes & Low Volume (e.g., < 100-500 units): Metal AM is often more cost-effective and significantly faster because it avoids the extremely high upfront cost and long lead time of creating molds or dies required for casting.
- High Volume (e.g., thousands of units): Traditional high-pressure die casting typically offers a lower cost per part once tooling is amortized.
- Complexity Factor: For highly complex designs with integrated features (like conformal cooling channels) that are difficult or impossible to cast or machine conventionally, AM can remain competitive even at moderate volumes or offer performance benefits that justify a potential cost premium. The value lies in design freedom and potential part consolidation, reducing assembly costs.
Q3: Can complex internal cooling channels be effectively cleaned and verified after printing?
A: Yes, but it requires careful planning. DfAM plays a crucial role – designing channels for accessibility, potentially with specific inlet/outlet ports for flushing, and minimizing the need for internal supports. Post-processing techniques like high-pressure fluid flushing, ultrasonic cleaning, and Abrasive Flow Machining (AFM) are used to remove trapped powder and smooth internal surfaces. Verification is key, often using methods like airflow testing, pressure testing, borescopic inspection (visual inspection with small cameras), or even CT scanning for critical applications to ensure channels are clear and free of obstructions or support remnants.
Q4: What is the typical lead time for a prototype EV battery housing using metal AM?
A: A typical lead time for a functional prototype EV battery housing produced via metal AM generally ranges from 1 to 4 weeks. This timeframe is highly dependent on factors such as the part’s size and complexity, the specific alloy chosen, the required post-processing steps (especially heat treatment and machining), the provider’s current machine queue, and the level of inspection needed. This is significantly faster than the months often required to get first parts from traditional casting tooling.
Conclusion: Accelerating EV Innovation with Metal AM Battery Housings
The relentless drive towards lighter, safer, and more efficient electric vehicles demands continuous innovation in component design and manufacturing. The EV battery housing, a critical component influencing range, performance, and safety, stands to benefit immensely from the capabilities of metal additive manufacturing. As we’ve explored, using 金属3Dプリンティング with advanced aluminum alloys like AlSi10Mg, A6061, and A7075 enables the creation of battery enclosures that are:
- Significantly Lighter: Through topology optimization and lattice structures, reducing overall vehicle weight and boosting range.
- Thermally Superior: Incorporating complex, conformal cooling channels directly into the structure for optimal battery temperature control.
- Highly Integrated: Consolidating multiple functions and parts into a single component, simplifying assembly and enhancing robustness.
- Rapidly Developed: Allowing for faster prototyping and design iteration cycles compared to traditional tooling-based methods.
While challenges exist, partnering with the right expert can overcome them. Met3dp stands at the forefront of this technological shift, offering a comprehensive ecosystem for automotive clients. Our strengths include:
- Advanced AM Systems: Delivering industry-leading print volume, accuracy, and reliability for mission-critical parts.
- Premium Metal Powders: Utilizing proprietary advanced Powder Making Systems (Gas Atomization & PREP) to produce 高品質の金属粉 optimized for density and performance.
- Integrated Expertise: Leveraging decades of collective expertise across equipment, materials science, and application development to support your project from concept to production.
Metal AM is no longer just a prototyping tool; it’s a viable manufacturing solution poised to reshape the future of EV manufacturing. By embracing additive manufacturing automotive industry leaders can unlock new levels of performance and accelerate their path to market.
Ready to explore how metal additive manufacturing can revolutionize your EV battery housing design?
Contact Met3dp today to discuss your project requirements and discover how our cutting-edge systems, advanced materials, and expert support can power your organization’s additive manufacturing goals and drive lightweight EV innovation. Visit our website at https://met3dp.com/ 詳細については、こちらをご覧ください。
シェアする
MET3DP Technology Co., LTDは、中国青島に本社を置く積層造形ソリューションのリーディングプロバイダーです。弊社は3Dプリンティング装置と工業用途の高性能金属粉末を専門としています。
関連記事
Met3DPについて
最新情報
製品
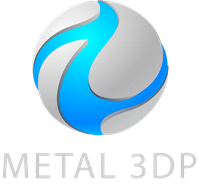
3Dプリンティングと積層造形用金属粉末