3D Printed Frame Connectors for EV Chassis Structures
目次
Introduction: The Critical Role of Frame Connectors in EV Chassis and the Additive Advantage
The automotive industry is undergoing a seismic shift, driven by the relentless push towards electrification. Electric Vehicles (EVs) are no longer a niche concept but a rapidly expanding segment demanding innovative engineering solutions. Central to EV design is the chassis structure – the vehicle’s skeleton – which must balance strength, stiffness, crashworthiness, and, critically, weight. Within this complex assembly, frame connectors, often referred to as nodes or joints, play a pivotal yet often underestimated role. These components are the crucial intersections where various structural members of the chassis frame meet, tasked with transferring loads, maintaining geometric integrity, and contributing significantly to the overall torsional rigidity and crash performance of the vehicle.
Traditionally, frame connectors have been manufactured using methods like casting (investment, sand, or die casting) or fabrication involving multiple stamped and welded pieces. While proven, these methods often come with limitations, particularly concerning design flexibility, weight optimization potential, tooling costs, and lead times, especially during prototyping and low-to-mid volume production runs. The unique demands of EV architecture, including accommodating large battery packs, optimizing weight distribution for range and handling, and meeting stringent safety standards, exacerbate these limitations. Engineers constantly seek ways to create lighter, stronger, and more geometrically complex components to maximize efficiency and performance.
This is where メタル 3Dプリンティングとしても知られている。 アディティブ・マニュファクチャリング(AM), emerges as a transformative technology. By building components layer by layer directly from digital designs using high-performance metal powders, AM shatters the constraints of traditional manufacturing. For EV frame connectors, this translates into several compelling advantages:
- これまでにないデザインの自由度: AM allows for the creation of highly complex, topology-optimized geometries that would be impossible or prohibitively expensive to produce using conventional methods. This enables engineers to design connectors that are intrinsically stronger and lighter, placing material only where it’s structurally necessary.
- Significant Lightweighting: Weight reduction is paramount in EVs to maximize battery range and improve vehicle dynamics. AM enables the production of hollow internal structures, complex lattice designs, and optimized forms that significantly reduce the mass of frame connectors without compromising structural integrity.
- パーツの統合: Complex connector assemblies previously made from multiple welded or bolted parts can often be redesigned and printed as a single, monolithic component. This reduces part count, eliminates potential failure points at joints, simplifies assembly, and lowers overall system complexity and weight.
- ラピッドプロトタイピングと反復: AM allows for the swift production of functional prototypes directly from CAD data. This accelerates design validation cycles, enabling engineers to test and refine connector designs much faster than traditional methods involving costly tooling modifications.
- 素材の多様性: AM processes can utilize a wide range of high-performance metal alloys, including advanced aluminum alloys like A7075 and AlSi10Mg, which offer excellent strength-to-weight ratios ideal for automotive structural applications.
- On-Demand & Distributed Manufacturing: AM facilitates localized, on-demand production, potentially reducing supply chain dependencies and enabling faster delivery, particularly for specialized or low-volume requirements sought by automotive component suppliers and distributors.
In essence, metal additive manufacturing provides automotive engineers and procurement managers with a powerful tool to reimagine how critical structural components like frame connectors are designed and produced. It offers a pathway to enhanced vehicle performance, improved efficiency, and accelerated development cycles, addressing the core challenges of modern EV chassis engineering. Companies like Met3dp, with deep expertise in both advanced metal powder production and industrial 3D printing systems, are at forefront of enabling this transition, providing the materials and technology necessary to realize the full potential of AM in automotive applications. As the EV market continues its exponential growth, the adoption of 3D printed frame connectors is poised to become increasingly integral to building the next generation of lighter, safer, and more efficient electric vehicles. This article delves into the specifics of using metal AM for EV frame connectors, exploring applications, materials, design considerations, and the factors involved in successfully implementing this cutting-edge manufacturing approach.
Applications & Use Cases: Where are 3D Printed EV Frame Connectors Deployed?
The versatility of metal additive manufacturing allows 3D printed frame connectors to be strategically deployed in various locations within an EV chassis structure, addressing specific engineering challenges and unlocking performance benefits. These components are not limited to a single type or location but find application wherever complex load paths, tight packaging constraints, lightweighting imperatives, or the need for rapid design iteration converge. Procurement managers sourcing wholesale EV connectors or seeking specialized automotive component suppliers should be aware of the diverse potential applications.
Here’s a breakdown of key application areas and use cases:
1. Primary Chassis Nodes (Space Frame / Skateboard Architectures):
- Function: Connecting main longitudinal rails, cross members, and suspension mounting points. These are often high-stress areas critical for overall chassis stiffness and crash energy management.
- Why AM? Allows for highly optimized shapes to efficiently transfer complex multi-axial loads. Enables integration of mounting features for suspension components, battery enclosures, or powertrain elements directly into the connector, reducing part count. Lightweighting through topology optimization is crucial here.
- 例を挙げよう: A-pillar to sill connection, B-pillar base node, suspension tower connections, main rail intersections in skateboard platforms.
2. Subframe Connectors:
- Function: Joining components within front or rear subframes, which typically house the powertrain, steering, and suspension systems.
- Why AM? Subframes often require intricate designs to package components tightly. AM allows for complex internal geometries and mounting features within the connectors. Part consolidation can simplify subframe assembly. High-strength aluminum alloys like A7075 are beneficial for stiffness and durability.
- 例を挙げよう: Connectors linking subframe rails, suspension arm mounting points integrated into nodes, steering rack mounts incorporated into connector geometry.
3. Battery Enclosure Integration Points:
- Function: Connecting the protective battery enclosure structure to the main vehicle body or chassis rails. These points must be strong enough to support the battery’s significant weight and protect it during impact events.
- Why AM? Allows for bespoke connector designs tailored to specific battery pack shapes and mounting strategies. Can incorporate features for thermal management (e.g., cooling channel integration points) or sealing. Design flexibility facilitates optimal load path management around the battery module.
- 例を挙げよう: Nodes connecting the battery tray perimeter frame to the vehicle sills or floor structure.
4. Suspension Mounting Points:
- Function: Providing robust and precise locations for attaching suspension links, control arms, dampers, and anti-roll bars to the chassis or subframes. Accuracy and stiffness are paramount for vehicle dynamics.
- Why AM? Enables the creation of highly stiff yet lightweight mounting structures. Allows for fine-tuning of suspension geometry pickup points during the development phase through rapid prototyping. Complex shapes can accommodate challenging packaging requirements around wheels and brakes.
- 例を挙げよう: Control arm mounting brackets integrated into chassis nodes, shock absorber top mount connectors, anti-roll bar connection points.
5. Roll Cage / Safety Structure Connectors (Performance/Motorsport EVs):
- Function: Joining tubes or structural members in specialized roll cages or safety structures required for high-performance or motorsport EVs. These demand exceptional strength and predictable deformation under extreme loads.
- Why AM? Enables complex multi-tube intersections with optimized geometry for maximum strength and energy absorption. Can be tailored precisely to specific tube profiles and angles, ensuring perfect fit-up for welding or bonding. Lightweighting is critical in motorsport.
- 例を挙げよう: Nodes connecting roll hoop, A-pillar bars, roof bars, and chassis mounting points.
6. Prototyping and Low-Volume Production:
- Function: Creating functional connectors for early-stage vehicle prototypes, concept cars, or niche/specialty EVs where tooling costs for traditional methods are prohibitive.
- Why AM? Eliminates the need for expensive casting molds or stamping dies. Allows for rapid design changes and iterations based on testing feedback. Ideal for validating chassis designs before committing to mass production tooling. Enables manufacturers to bring specialized EVs to market faster.
- 例を挙げよう: Any of the above applications, but specifically for vehicles produced in limited quantities or during the initial development phases.
Industry Applicability:
The use of 3D printed frame connectors spans various segments within the EV market:
- Passenger Vehicles: Increasingly used in premium EVs and performance models where lightweighting and advanced structures are key differentiators. Also valuable during platform development.
- Commercial Vehicles (Light Duty): Potential for optimizing chassis nodes in electric vans and light trucks where payload capacity and range are critical.
- Electric Motorcycles & Powersports: Ideal for complex frame junctions in electric motorcycles, ATVs, and UTVs where weight and space are highly constrained.
- Autonomous Shuttles & Pods: Often feature unique space frame designs where custom, complex connectors are essential.
- Motorsport & High-Performance EVs: Early adopters leveraging AM for maximum performance, lightweighting, and rapid development.
Table: Use Case Summary for 3D Printed EV Frame Connectors
アプリケーションエリア | Key Function(s) | Primary Benefits of Using AM | Target EV Segments | Relevant B2B Keywords |
---|---|---|---|---|
Primary Chassis Nodes | Load transfer, Stiffness, Crash management | Topology optimization, Lightweighting, Part consolidation | Passenger, Commercial, Motorsport | Wholesale chassis nodes, EV space frame connectors supplier |
Subframe Connectors | Component mounting, Stiffness, Packaging | Complex geometry, Part consolidation, High-strength materials | Passenger, Commercial | Automotive subframe parts distributor, 3D printed brackets |
Battery Integration | Battery support, Protection, Sealing integration | Custom design, Optimal load paths, Feature integration | All EV segments | EV battery enclosure components, Custom metal parts B2B |
Suspension Mounts | Precise geometry, Stiffness, Durability | High stiffness-to-weight, Rapid iteration, Complex shapes | Passenger, Motorsport, Powersports | Suspension component supplier, AM automotive brackets |
Roll Cage / Safety | High strength, Energy absorption, Precise fit-up | Optimized intersections, Lightweighting, Customization | Motorsport, High-Performance | Roll cage connectors manufacturer, Safety structure parts |
Prototyping / Low Volume | Design validation, Fast iteration, Tooling avoidance | Speed, Cost-effectiveness (low vol), Design flexibility | All EV segments, Specialty Vehicles | Rapid prototyping services, Low-volume automotive parts |
Export to Sheets
By understanding these diverse applications, engineers can identify opportunities to leverage metal AM, while procurement managers can better specify requirements when engaging with metal AM service providers or seeking wholesale suppliers of these advanced components. The ability to tailor connector design precisely to its function and location within the EV chassis is a core strength of additive manufacturing in this domain.
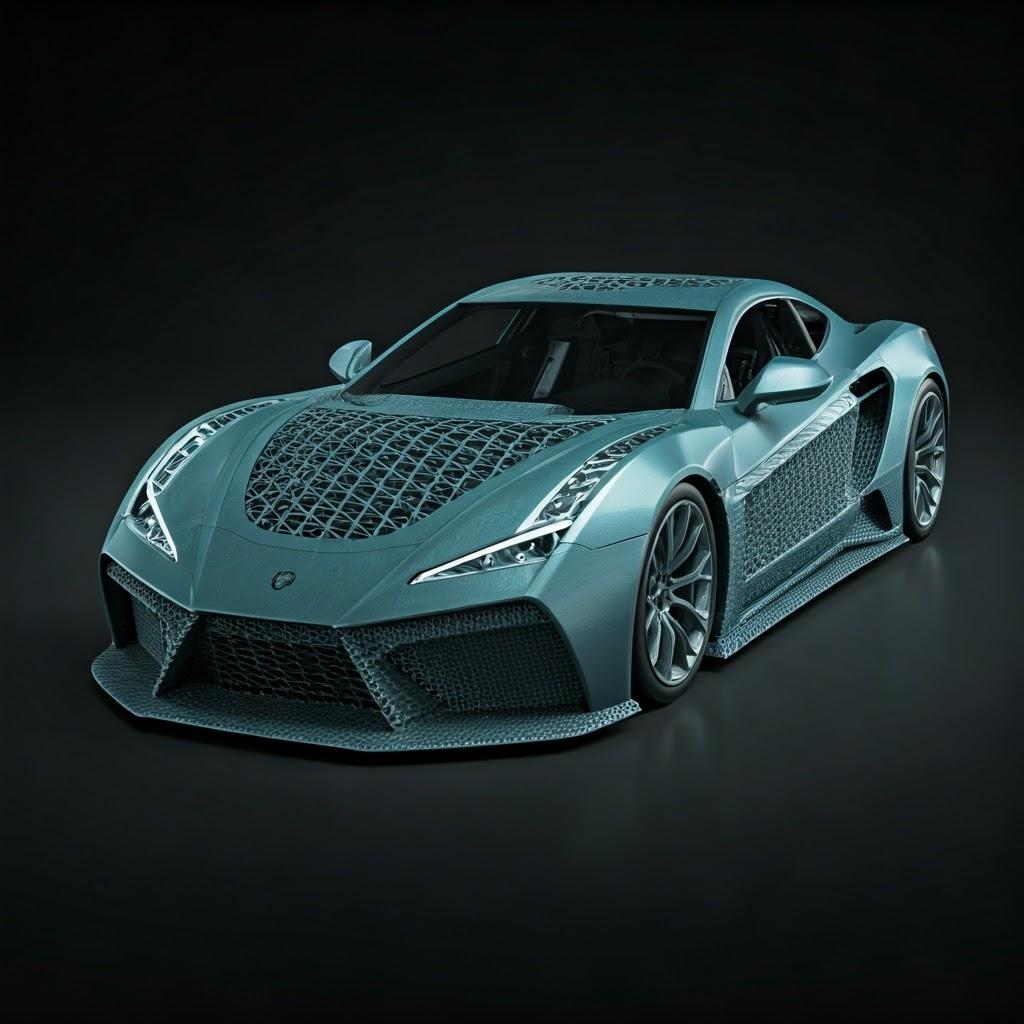
Why Choose Metal 3D Printing for EV Frame Connectors? Unlocking Performance & Efficiency
The decision to adopt metal additive manufacturing (AM) for producing electric vehicle (EV) frame connectors over established methods like casting or fabrication isn’t merely about embracing novelty; it’s a strategic choice driven by tangible engineering and business advantages. For automotive manufacturers, tier-1 suppliers, and procurement specialists evaluating production methods, understanding why AM offers a compelling alternative is crucial. The benefits directly address key challenges in EV development: maximizing range (lightweighting), ensuring safety (strength and reliability), managing complexity (part consolidation), and accelerating time-to-market (speed).
Let’s dissect the primary advantages of utilizing metal 3D printing for these critical structural components:
1. Radical Lightweighting Potential:
- 課題: Weight is the enemy of EV range and performance. Every kilogram saved translates to longer driving distances, better acceleration, and improved handling. Traditional connectors, often designed with uniform wall thicknesses or bulky sections due to manufacturing constraints (e.g., casting draft angles, machining access), carry excess mass.
- The AM Solution: Metal AM enables トポロジー最適化 and the creation of complex internal structures (like lattices or hollow cavities) that are impossible or impractical with other methods. Algorithms determine the most efficient load paths, allowing designers to place material precisely where needed for strength and remove it elsewhere. This results in connectors that are significantly lighter (often 20-50% or more) while maintaining or even increasing stiffness and strength compared to their conventional counterparts. This is a paramount benefit for EV chassis design.
- Example: A cast aluminum connector might weigh 1.5 kg, while a topology-optimized, 3D printed version using AlSi10Mg could achieve the same performance at 0.8 kg.
2. Unmatched Design Freedom and Complexity:
- 課題: Traditional methods impose significant geometric constraints. Casting requires careful consideration of draft angles, wall thickness variations, and mold complexity. Machining is limited by tool access and the subtractive nature of the process. Fabricated assemblies are constrained by stamping limitations and welding access.
- The AM Solution: AM builds parts layer by layer, freeing designers from many traditional constraints. This allows for:
- Organic Shapes: Creating smooth, flowing forms that follow optimal stress paths.
- Internal Channels: Incorporating cooling channels, wiring conduits, or fluid passages directly within the connector.
- Negative Draft: Designing features that would be impossible to remove from a mold.
- Undercuts & Complex Passages: Facilitating intricate designs for packaging and function. This design freedom enables engineers to create highly integrated and efficient connector designs tailored perfectly to their specific location and function within the complex EV architecture.
3. Part Consolidation:
- 課題: Complex chassis junctions often require multiple individual parts (e.g., stamped brackets, machined blocks, cast elements) to be assembled via welding, bolting, or bonding. Each joint represents a potential failure point, adds assembly time and cost, introduces tolerance stack-up issues, and increases overall weight.
- The AM Solution: Metal AM excels at producing complex, monolithic components. An assembly of several parts can often be redesigned as a single, integrated 3D printed connector.
- メリット
- Reduced Part Count: Simplifies inventory, logistics, and assembly processes.
- Lower Assembly Labor & Time: Reduces manufacturing bottlenecks.
- Improved Structural Integrity: Eliminates weak points associated with joints.
- Reduced Weight: Eliminates fasteners and overlapping material.
- Tighter Tolerances: Reduces tolerance stack-up across multiple assembled parts.
- B2B Implication: Suppliers offering consolidated AM parts provide significant value in simplifying the supply chain for automotive manufacturers.
- メリット
4. Accelerated Prototyping and Development Cycles:
- 課題: Developing new vehicle platforms or iterating on existing designs requires physical prototypes for testing and validation. Creating tooling (molds, dies) for traditional methods is time-consuming (weeks or months) and expensive. Design changes necessitate costly and slow tooling modifications.
- The AM Solution: Metal AM allows functional prototypes of frame connectors to be produced directly from CAD data in a matter of days, without any tooling.
- メリット
- スピードだ: Drastically reduces the time between design conception and physical part testing.
- 反復: Enables rapid design-build-test cycles, allowing engineers to quickly refine connector geometry, test different materials, and validate performance.
- Cost-Effectiveness (for Prototypes): Avoids huge upfront tooling investments during the development phase.
- Risk Reduction: Allows for thorough validation before committing to expensive mass-production tooling.
- メリット
5. Material Performance and Selection:
- 課題: EV connectors require materials offering high strength, stiffness, durability, fatigue resistance, and corrosion resistance, often combined with low density. Selecting the optimal material and ensuring its properties are realized through the manufacturing process is critical.
- The AM Solution: Metal AM processes, particularly powder bed fusion (like SLM/DMLS), work with specialized metal powders engineered for high performance. Alloys like AlSi10Mg and high-strength aluminum series (like A7075 – although printability requires expertise) offer excellent strength-to-weight ratios suitable for demanding structural applications. Companies like Met3dp specialize in developing and producing high-quality, spherical metal powders using advanced gas atomization techniques, ensuring the consistency and purity needed for reliable, high-performance printed parts. The rapid solidification inherent in AM can sometimes even yield finer microstructures and improved mechanical properties compared to cast equivalents.
6. Suitability for Low-to-Mid Volume Production & Customization:
- 課題: Tooling costs for casting or stamping are only amortized effectively over very high production volumes. For niche vehicles, performance variants, or early production ramps, these costs can be prohibitive. Customization is also difficult and expensive with traditional tooling.
- The AM Solution: As a tool-less process, AM is economically viable for lower production volumes where tooling costs would dominate. It also allows for easy customization – unique connector designs for different vehicle variants can be produced without tooling changes. This provides flexibility for manufacturers and opens opportunities for B2B suppliers specializing in custom metal parts.
Table: AM vs. Traditional Methods for EV Frame Connectors
特徴 | 金属積層造形(AM) | Traditional Casting (e.g., Die, Investment) | Traditional Fabrication (Stamping/Welding) |
---|---|---|---|
軽量化 | Excellent (Topology optimization, lattices, hollow structures) | Moderate (Limited by draft, uniform thickness) | Limited (Based on sheet thickness, assembly method) |
デザインの自由 | Very High (Complex geometries, internal channels, undercuts) | Moderate (Requires draft angles, avoids undercuts) | Low (Constrained by stamping forms, weld access) |
部品の統合 | Excellent (Complex single-piece parts possible) | Limited (Complex molds increase cost significantly) | Poor (Requires multiple parts and joining) |
Prototyping Speed | Very Fast (Days) | Slow (Weeks/Months for tooling) | Slow (Weeks/Months for tooling) |
金型費用 | なし | 高い | 高い |
Cost (Low Volume) | 競争的 | Very High (Due to tooling amortization) | Very High (Due to tooling amortization) |
Cost (High Volume) | Can be higher per part (process time) | Lower per part | Lowest per part |
廃棄物 | Low (Powder recyclability) | Moderate (Runners, gates) | Moderate (Sheet offcuts) |
代表的な素材 | AlSi10Mg, A7075*, Ti6Al4V, Steels, Superalloys | Aluminum Alloys, Magnesium Alloys, Zinc Alloys | Steels, Aluminum Alloys |
Ideal Use Case | Prototyping, Low-Mid Volume, High Complexity, Max Lightweighting | High Volume, Moderate Complexity | Very High Volume, Simpler Geometries |
Export to Sheets
Note: Printing A7075 requires specialized process control due to its susceptibility to hot tearing.
In conclusion, the decision to use metal 3D printing for EV frame connectors is underpinned by its ability to deliver lighter, stronger, more integrated components faster and with greater design flexibility than traditional methods, particularly during development and for low-to-mid volume production. It empowers engineers to push the boundaries of EV chassis design and efficiency, aligning perfectly with the core demands of electric mobility.
Material Deep Dive: A7075 and AlSi10Mg Aluminum Alloys for High-Performance Connectors
Selecting the right material is fundamental to the success of any engineering component, and 3D printed EV frame connectors are no exception. These parts operate under demanding conditions, requiring a balance of strength, stiffness, low density, durability, and often corrosion resistance. Among the various metal powders available for additive manufacturing, aluminum alloys are frequently favored for automotive structural applications due to their excellent strength-to-weight ratios. Two prominent candidates often considered for EV connectors are AlSi10Mg そして A7075. Understanding their distinct properties, benefits, and considerations within the context of metal AM is crucial for engineers and procurement managers aiming to source high-performance components.
AlSi10Mg: The Workhorse AM Aluminum Alloy
AlSi10Mg is arguably the most widely used aluminum alloy in metal powder bed fusion (PBF) processes like Selective Laser Melting (SLM) or Direct Metal Laser Sintering (DMLS). It’s essentially a casting alloy adapted for AM, known for its excellent printability and good balance of properties.
- 構成: Primarily Aluminum (Al), with Silicon (Si, ~9-11%) and Magnesium (Mg, ~0.2-0.45%) as the main alloying elements. Silicon improves fluidity and reduces solidification shrinkage (enhancing printability), while Magnesium allows for strengthening through heat treatment (precipitation hardening).
- Key Properties & Benefits for EV Connectors:
- 優れた印刷適性: Its relatively wide solidification range and good flowability make it easier to process reliably in PBF systems, resulting in dense parts with fewer defects compared to some other high-strength aluminum alloys. This translates to more consistent quality for suppliers and buyers.
- 優れた強度対重量比: While not as strong as high-zinc alloys like A7075, AlSi10Mg offers a very respectable balance of strength and low density, making it suitable for many structural EV applications where lightweighting is key.
- Good Thermal Properties: Possesses good thermal conductivity, which can be beneficial if the connector is near heat sources or if integrated cooling features are desired.
- 耐食性: Exhibits good resistance to corrosion, suitable for the typical operating environments of a vehicle chassis.
- 熱処理可能: As-printed parts can be further strengthened through T6 heat treatment (solutionizing and artificial aging), significantly improving yield strength and ultimate tensile strength.
- 溶接性: Can be welded, although specific procedures are required.
- 費用対効果: Generally more established and readily available as an AM powder compared to more specialized alloys, potentially impacting cost.
- 検討する:
- Lower Strength than A7075: Its peak strength, even after heat treatment, falls short of alloys like A7075.
- Lower Ductility/Fracture Toughness: Can be less ductile than wrought alloys, requiring careful design to manage stress concentrations.
- Typical Applications in EV Connectors: Ideal for moderately loaded connectors, complex geometries where printability is paramount, prototypes, and applications where its balance of properties is sufficient and cost-effectiveness is a factor. Suitable for primary chassis nodes, subframe connectors, and battery integration points.
A7075 (Aluminum 7075): The High-Strength Challenger
A7075 is a well-known high-strength aluminum alloy from the 7xxx series, primarily alloyed with Zinc (Zn), Magnesium (Mg), and Copper (Cu). It’s traditionally used in aerospace and high-performance applications in its wrought form due to its exceptional strength-to-weight ratio, rivaling that of some steels. Adapting it for AM presents challenges but offers significant performance potential.
- 構成: Primarily Aluminum (Al), with Zinc (~5.1-6.1%), Magnesium (~2.1-2.9%), and Copper (~1.2-2.0%) as key alloying elements.
- Key Properties & Benefits for EV Connectors:
- 卓越した強度対重量比: This is the primary driver for considering A7075. After appropriate heat treatment (e.g., T6 condition), it achieves significantly higher tensile and yield strengths than AlSi10Mg, allowing for even greater lightweighting potential or performance in highly stressed connectors.
- 高い硬度: Offers good wear resistance.
- Excellent Fatigue Strength: Crucial for components subjected to cyclic loading, common in vehicle chassis.
- Challenges & Considerations in AM:
- Printability Issues: A7075 has a wide solidification range and is highly susceptible to hot tearing or solidification cracking during the rapid heating and cooling cycles of PBF processes. This makes it challenging to print dense, crack-free parts consistently. Successfully printing A7075 requires specialized powders with modified compositions or grain refiners, tightly controlled process parameters (laser power, scan speed, layer thickness), and specific platform heating strategies.
- 残留応力: High residual stresses can build up during printing, potentially leading to distortion or cracking, necessitating careful thermal management and post-processing stress relief.
- Heat Treatment Complexity: Achieving the desired T6 properties requires precise multi-step heat treatment cycles.
- Corrosion Susceptibility: Generally less corrosion resistant than AlSi10Mg, especially to stress corrosion cracking (SCC), potentially requiring protective coatings depending on the application environment.
- Powder Availability & Cost: A7075 powder suitable for reliable AM is less common and typically more expensive than AlSi10Mg powder.
- Typical Applications in EV Connectors: Best suited for highly loaded structural connectors where maximum strength and stiffness are critical, and the higher performance justifies the increased processing complexity and cost. Examples include critical suspension mounting points, nodes in performance vehicle space frames, or connectors where minimizing deflection under load is paramount. Requires a service provider with proven expertise in processing this challenging alloy.
Met3dp’s Role in Material Excellence:
Successfully leveraging alloys like AlSi10Mg and A7075 in additive manufacturing hinges on the quality of the metal powder feedstock. This is where a company like Met3dp plays a critical role.
- 高度なパウダー製造: Met3dp utilizes industry-leading ガス霧化 and potentially プラズマ回転電極プロセス(PREP) technologies. Their gas atomization systems employ unique nozzle and gas flow designs optimized to produce metallic powders with:
- 高い真球度: Ensures excellent powder flowability within the AM machine, leading to uniform powder bed density and consistent melting.
- Low Porosity: Minimizes internal pores within the powder particles, contributing to higher density in the final printed part.
- Controlled Particle Size Distribution (PSD): Tailored PSD for optimal packing density and melting behavior in PBF systems.
- 高純度: Minimizing impurities that can negatively affect material properties and printability.
- マテリアル・ポートフォリオ While specializing in materials like TiNi, TiTa, TiAl, TiNbZr, CoCrMo, stainless steels, and superalloys, Met3dp’s expertise in powder metallurgy extends to producing high-quality aluminum alloy powders optimized for AM processes. Their commitment ensures customers receive powders tailored for demanding applications like EV connectors. Explore their 高品質の金属粉 詳細についてはこちらをご覧ください。
- プロセスの専門知識: Beyond powders, Met3dp’s understanding of AM processes, including their own SEBM (Selective Electron Beam Melting) printers, provides valuable insight into the powder-process interaction crucial for achieving desired material properties in the final component.
Table: Comparison of AlSi10Mg and A7075 for 3D Printed EV Connectors
特徴 | AlSi10Mg | A7075 (AM Processed) | Key Consideration for EV Connectors |
---|---|---|---|
Primary Advantage | Excellent Printability, Balanced Properties | 卓越した強度対重量比 | Match material to the specific load case and performance requirement. |
Tensile Strength (T6) | Good (e.g., 300-350 MPa Yield) | Very High (e.g., 450-500+ MPa Yield) | Higher strength allows for more aggressive lightweighting. |
密度 | Low (~2.67 g/cm³) | Low (~2.81 g/cm³) | Both offer significant weight savings over steel. |
印刷適性 | 素晴らしい | Challenging (Hot Tearing Risk) | Requires expert process control for A7075. |
熱処理 | Standard T6 | Precise, Multi-Step T6 | Impacts final properties and cost. |
耐食性 | グッド | Moderate (SCC risk) | May require coating for A7075 in harsh environments. |
延性 | 中程度 | Moderate-to-Low | Design must account for potential brittleness. |
コストと空室状況 | More Common, Lower Cost | Less Common, Higher Cost | Impacts overall component budget. |
Ideal Use Case | General purpose, Complex shapes, Prototypes | High-stress components, Max performance | Choose based on performance needs vs. manufacturing complexity. |
Export to Sheets
Choosing the Right Alloy:
The choice between AlSi10Mg and A7075 for an EV frame connector depends on a careful analysis of the specific application’s requirements:
- For maximum performance in critical, high-stress areas: A7075 is the target, provided you partner with a supplier possessing the specialized expertise (like potentially Met3dp or their partners) to print it reliably.
- For general structural applications, complex geometries, or faster prototyping: AlSi10Mg offers a robust and more easily manufacturable solution with good all-around properties.
Ultimately, leveraging the unique benefits of these advanced aluminum alloys through metal AM, supported by high-quality powders and expert processing, empowers the design and production of next-generation EV frame connectors that are lighter, stronger, and more optimized than ever before.
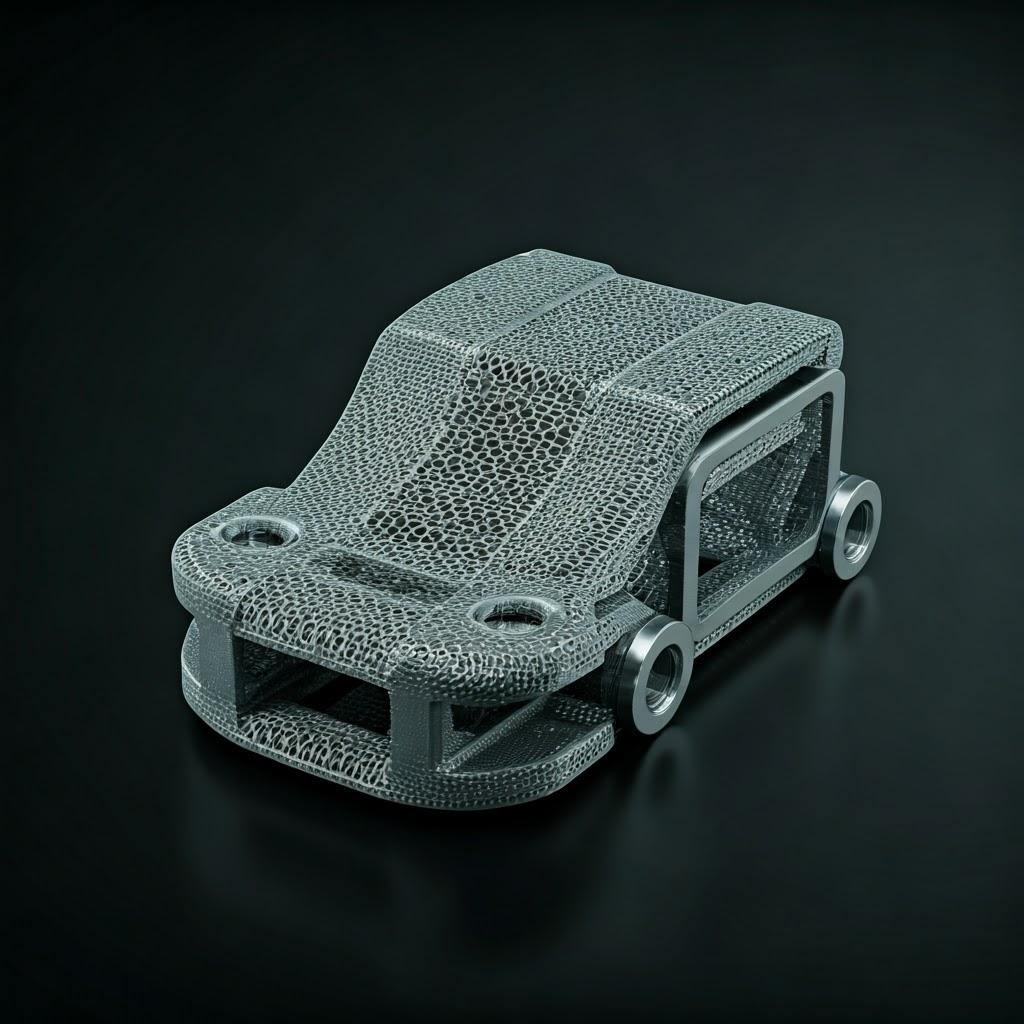
Design for Additive Manufacturing (DfAM): Optimizing EV Connectors for 3D Printing Success
Simply replicating a design intended for casting or machining and sending it to a metal 3D printer rarely unlocks the full potential of additive manufacturing. To truly harness the benefits of lightweighting, part consolidation, and enhanced performance for EV frame connectors, engineers must embrace 積層造形設計 (DfAM) principles. DfAM is not just a suggestion; it’s a fundamental shift in design thinking that considers the unique capabilities and constraints of the layer-by-layer building process right from the concept stage. Applying DfAM is crucial for achieving optimal results, reducing printing time and cost, minimizing post-processing efforts, and ensuring the structural integrity of the final component. Procurement managers should look for suppliers who demonstrate strong DfAM capabilities, as this directly impacts the quality and cost-effectiveness of the delivered parts.
Here are key DfAM considerations for optimizing EV frame connectors for metal AM processes like Powder Bed Fusion (PBF):
1. Topology Optimization:
- Concept: This is often the starting point for lightweighting structural components. Topology optimization software uses Finite Element Analysis (FEA) to determine the most efficient load paths within a defined design space, given specific load cases, constraints, and performance targets (e.g., stiffness, stress limits). The software iteratively removes material from areas experiencing low stress, leaving behind an optimized, often organic-looking structure that meets performance requirements with minimum mass.
- Application for EV Connectors: Ideal for complex nodes connecting multiple chassis members. It allows engineers to sculpt connectors that efficiently transfer loads from suspension points, cross members, and rails, resulting in significant weight savings (often 20-50%+) compared to conventionally designed parts. The output often requires some smoothing or refinement for manufacturability.
- Benefit: Maximizes strength-to-weight ratio, directly contributing to increased EV range and improved dynamics.
2. Lattice Structures and Internal Voids:
- Concept: AM allows for the creation of internal lattice structures (e.g., honeycomb, gyroid, stochastic foams) or hollow sections within the connector body. These structures can significantly reduce weight while maintaining good stiffness and potentially offering benefits like vibration damping or enhanced energy absorption during crash events.
- Application for EV Connectors: Can be applied selectively within less-stressed regions of the connector identified through analysis or used to create specific mechanical responses. Hollow sections are simpler but effective for mass reduction. Careful design is needed to ensure powder removal from internal cavities after printing.
- Benefit: Further weight reduction beyond topology optimization alone, potential for tailored mechanical properties. Requires careful simulation and understanding of lattice performance.
3. Part Consolidation Strategy:
- Concept: Actively look for opportunities to redesign assemblies of multiple parts (brackets, fasteners, connectors) into a single, monolithic 3D printed component.
- Application for EV Connectors: A complex junction involving a main connector body, several mounting brackets, and fasteners can potentially be redesigned as one integrated piece. This requires careful consideration of assembly sequences, access for maintenance (if needed), and the functionality of the original components.
- Benefit: Reduced part count, simplified supply chain and assembly, elimination of joints (potential failure points), reduced weight, potentially lower overall system cost. A key value proposition for B2B suppliers using AM.
4. Support Structure Minimization and Optimization:
- Concept: In PBF processes, downward-facing surfaces and overhangs beyond a certain angle (typically <45 degrees from the horizontal) require support structures built from the same material. These supports anchor the part to the build plate, prevent warping, and support overhanging features during melting. However, supports consume extra material, increase print time, and require removal in post-processing (adding cost and potentially damaging surfaces). DfAM aims to minimize the need for supports or design them for easy removal.
- Strategies:
- Part Orientation: Carefully selecting the build orientation can drastically reduce the amount of supported area. Orienting critical surfaces upwards or vertically can improve their finish and accuracy. Simulation tools can help find the optimal orientation balancing support volume, print time, distortion risk, and surface quality.
- Self-Supporting Angles: Designing overhangs to be at angles greater than ~45 degrees whenever possible.
- Chamfers and Fillets: Replacing sharp horizontal overhangs with chamfered or filleted edges that can be self-supporting.
- Integrated Supports: Designing features that act as supports but become part of the final component or are easily machined away.
- Accessible Supports: Designing support structures that are easily accessible for manual or tool-based removal, avoiding complex internal supports where possible.
- Benefit: Reduced material consumption, faster print times, lower post-processing costs, reduced risk of surface damage during support removal.
5. Feature Resolution and Wall Thickness:
- Concept: AM processes have limitations on the minimum size of features (holes, slots, pins) and the minimum wall thickness they can reliably produce. These limitations depend on the machine, laser spot size, powder particle size, and process parameters.
- Guidelines (Typical for Aluminum in PBF):
- Minimum Wall Thickness: ~0.4 – 1.0 mm (thicker often recommended for structural integrity and handling).
- Minimum Hole Diameter: ~0.5 – 1.0 mm (smaller holes may require post-drilling).
- Minimum Feature Size: ~0.2 – 0.5 mm.
- Application for EV Connectors: Ensure critical features like bolt holes, mounting surfaces, and thin walls are designed within the process capabilities. Avoid overly thin sections that could warp or be fragile. Thick sections can increase print time and residual stress, so uniform thickness or gradual transitions are preferred where possible.
- Benefit: Ensures manufacturability, prevents print failures, achieves desired part functionality.
6. Designing for Post-Processing:
- Concept: Consider how the part will be handled and finished after printing.
- 検討する:
- Machining Allowances: If critical surfaces (e.g., mating faces, bearing bores) require high precision or specific finishes achievable only through machining, add extra material (stock) to these areas in the CAD model.
- 熱処理: Understand how heat treatment (e.g., T6 for AlSi10Mg/A7075) might cause minor distortion and account for it if necessary.
- Inspection Access: Ensure critical features are accessible for measurement and Non-Destructive Testing (NDT).
- Powder Removal: Design internal channels or cavities with adequate drainage holes for easy removal of unfused powder, especially for complex lattice structures.
- Benefit: Streamlines the post-processing workflow, ensures final dimensional accuracy and surface finish requirements are met, facilitates quality control.
7. Leveraging AM Process Characteristics:
- Concept: Understand the nuances of the specific AM process being used (e.g., SLM, DMLS, EBM). Different 印刷方法 have subtle differences in surface finish, achievable tolerances, and material properties.
- アプリケーション Design choices might be slightly adjusted based on the chosen technology. For example, Electron Beam Melting (EBM), like the SEBM systems Met3dp offers expertise in for certain materials, operates at higher temperatures, reducing residual stress but potentially resulting in rougher surfaces compared to laser-based systems. This knowledge influences decisions on orientation and post-processing needs.
- Benefit: Optimizes the design for the specific manufacturing process, leading to better quality and potentially lower costs.
Table: Key DfAM Principles for EV Connectors
DfAM Principle | 目的 | Key Techniques | Benefit for EV Connector |
---|---|---|---|
Topology Optimization | Maximize Stiffness-to-Weight Ratio | FEA-driven material removal, Organic shapes | Significant lightweighting, Optimal load transfer |
Lattice/Hollow Structures | Reduce Mass, Tailor Properties | Internal lattices (gyroids, etc.), Hollow sections | Additional weight savings, Vibration damping, Energy absorption |
部品の統合 | Simplify Assembly, Reduce Part Count | Redesigning multi-part assemblies into single monolithic prints | Reduced complexity, Fewer failure points, Lower assembly cost |
Support Minimization | Reduce Cost, Time, Post-Processing Effort | Optimal orientation, Self-supporting angles, Chamfers/fillets, Accessible supports | Lower material use, Faster prints, Easier finishing |
フィーチャー・レゾリューション | Ensure Manufacturability & Functionality | Adhering to min. wall thickness, hole size, feature size guidelines | Prevents print failures, Ensures features form correctly |
Design for Post-Processing | Facilitate Finishing & Quality Control | Machining allowances, Heat treatment consideration, Inspection access, Powder removal | Ensures final specs are met, Streamlines workflow, Improves QC |
Leverage Process Char. | Optimize for Specific AM Technology | Understanding process nuances (SLM vs. EBM), Tailoring design accordingly | Better quality, Potentially lower cost, Optimized properties |
Export to Sheets
By integrating these DfAM principles, engineering teams working with expert AM providers like Met3dp can design and produce EV frame connectors that are not just replacements for traditional parts but are superior components optimized for the demanding environment of electric vehicle chassis. This proactive design approach is fundamental to realizing the transformative potential of additive manufacturing in the automotive sector.
Achieving Precision: Tolerance, Surface Finish, and Dimensional Accuracy in 3D Printed Connectors
While metal additive manufacturing offers unparalleled design freedom, a critical question for engineers and procurement managers considering it for functional components like EV frame connectors revolves around precision: What level of tolerance, surface finish, and dimensional accuracy can realistically be achieved? Understanding these aspects is vital for ensuring proper fit, assembly, and performance within the tightly controlled environment of an automotive chassis. The required precision often dictates the necessary post-processing steps and influences the overall cost and lead time.
Dimensional Accuracy and Tolerances:
Dimensional accuracy refers to how closely the final printed part conforms to the dimensions specified in the original CAD model. Tolerance defines the permissible range of variation for a given dimension.
- Typical As-Printed Tolerances: For metal Powder Bed Fusion (PBF) processes like SLM/DMLS using aluminum alloys, typical achievable dimensional tolerances are often in the range of:
- ± 0.1 mm to ± 0.2 mm for smaller features (e.g., up to 50-100 mm)
- ± 0.1% to ± 0.2% of the nominal dimension for larger features.
- Factors Influencing Accuracy:
- Machine Calibration: The accuracy and calibration of the 3D printer itself (laser positioning, scanner accuracy, Z-axis movement) are fundamental. High-quality industrial systems, like those Met3dp focuses on, offer better inherent accuracy.
- Process Parameters: Laser power, scan speed, layer thickness, and hatching patterns significantly impact melt pool stability and solidification, affecting dimensional accuracy. Optimized parameters are crucial.
- 素材の特性: Different alloys exhibit varying shrinkage rates and thermal behavior during processing.
- Thermal Stress and Distortion: Residual stresses built up during the layer-by-layer heating and cooling can cause warping or distortion, especially in large or complex parts. Build plate heating, optimized scan strategies, and proper support structures help mitigate this.
- Part Size and Geometry: Larger parts and complex geometries with thin walls or large overhangs are generally more prone to distortion.
- Part Orientation: The orientation of the part on the build plate affects thermal gradients, support requirements, and ultimately, dimensional accuracy across different axes.
- パウダーの質: Consistent powder characteristics (particle size distribution, morphology) contribute to predictable melting and solidification. Met3dp’s focus on high-quality spherical powders aids in achieving better consistency.
- Comparison to Other Methods:
- Casting (Die/Investment): Can achieve good tolerances, sometimes comparable to or slightly better than as-printed AM for certain features, but often requires draft angles. Tool wear can affect long-term consistency.
- 機械加工: Offers the highest level of precision, capable of achieving tolerances of ±0.01 mm or better for critical features.
- Implications for EV Connectors: For general connector geometry, as-printed tolerances may be sufficient. However, critical interfaces like mounting holes, bearing surfaces, or mating faces often require tighter tolerances than AM can achieve directly. This necessitates secondary machining operations on those specific features.
Surface Finish (Roughness):
Surface finish, typically quantified by the average roughness (Ra), describes the texture of the part’s surfaces.
- As-Printed Surface Finish: Metal PBF processes inherently produce surfaces with a noticeable roughness due to the partially melted powder particles adhering to the surface and the layered nature of the build.
- Typical Ra Values (Aluminum PBF): 6 µm to 20 µm (micrometers), depending heavily on orientation and parameters.
- Orientation Impact:
- Top Surfaces: Generally smoother as they are the last layer melted by the laser.
- Vertical Walls: Show distinct layer lines, contributing to roughness.
- Upward-Facing Sloped Surfaces: Tend to be smoother than downward-facing ones.
- Downward-Facing (Supported) Surfaces: Typically the roughest, as they interface with support structures which leave witness marks upon removal.
- Factors Influencing Surface Finish:
- 層の厚さ: Thinner layers generally result in slightly smoother vertical walls but increase print time.
- Powder Particle Size: Finer powders can lead to smoother finishes but may pose challenges in flowability.
- Laser Parameters: Scan speed and energy density influence melt pool dynamics and surface texture.
- Support Strategy: The type, density, and location of supports significantly impact the finish of supported surfaces after removal.
- Comparison to Other Methods:
- Casting (Sand): Very rough surfaces (Ra > 12.5 µm).
- Casting (Investment/Die): Much smoother than sand casting, potentially smoother than as-printed AM in some cases (Ra 1-6 µm).
- 機械加工: Can achieve very smooth finishes (Ra < 1 µm), depending on the specific process (milling, grinding, polishing).
- Implications for EV Connectors: As-printed surface finish is often acceptable for non-critical surfaces. However, surfaces involved in sealing, bearing interfaces, or those requiring specific fatigue performance may need improvement through post-processing (e.g., bead blasting, tumbling, machining, polishing). The aesthetic roughness might also be a factor for visible components.
Achieving Higher Precision:
When the as-printed tolerances or surface finish are insufficient for the functional requirements of the EV connector, post-processing becomes essential.
- CNC Machining: The most common method to achieve tight tolerances and fine surface finishes on specific features. Critical bores, mounting faces, and interfacing surfaces are typically machined after printing and heat treatment. DfAM principles dictate adding machining stock to these areas.
- 表面処理: Techniques like bead blasting, shot peening (can improve fatigue life), tumbling, or polishing can improve the overall surface finish and remove loosely adhering particles.
- Quality Control & Inspection: Verifying dimensional accuracy and tolerances is critical. Common methods include:
- Coordinate Measuring Machines (CMM): Provide high-accuracy point measurements for verifying critical dimensions.
- 3D Scanning (Laser or Structured Light): Capture the full geometry of the part for comparison against the original CAD model, ideal for complex shapes and verifying overall form.
- Traditional Metrology: Calipers, micrometers, gauges for specific feature checks.
Table: Precision Aspects of 3D Printed EV Connectors (Aluminum PBF)
パラメータ | Typical As-Printed Range | Key Influencing Factors | Post-Processing for Improvement | Relevance for EV Connectors |
---|---|---|---|---|
Tolerance (General) | ±0.1 to ±0.2 mm / ±0.1% to ±0.2% | Machine calibration, Thermal stress, Orientation, Material, Parameters | CNC Machining (for critical features) | Fit, Assembly, Functionality |
Surface Finish (Ra) | 6 µm to 20 µm | Orientation (supports!), Layer thickness, Parameters, Powder size | Bead Blasting, Tumbling, Polishing, Machining | Sealing, Wear, Fatigue Life, Aesthetics |
寸法精度 | High, but subject to variation | Thermal management, Support strategy, Part complexity, Size | CNC Machining, Stress Relief | Ensures part matches design intent, Critical for performance |
Inspection Methods | 該当なし | 該当なし | CMM, 3D Scanning, Traditional Metrology | Verification of tolerances and accuracy against specifications (QA) |
Export to Sheets
In summary, while metal AM provides geometric freedom, achieving the high precision often required for automotive components like EV frame connectors typically involves a combination of optimized printing processes and targeted post-processing, particularly CNC machining for critical features. Procurement managers should clearly define tolerance and surface finish requirements in RFQs and work with AM service providers who have robust quality control systems and post-processing capabilities to ensure the final parts meet all engineering specifications.
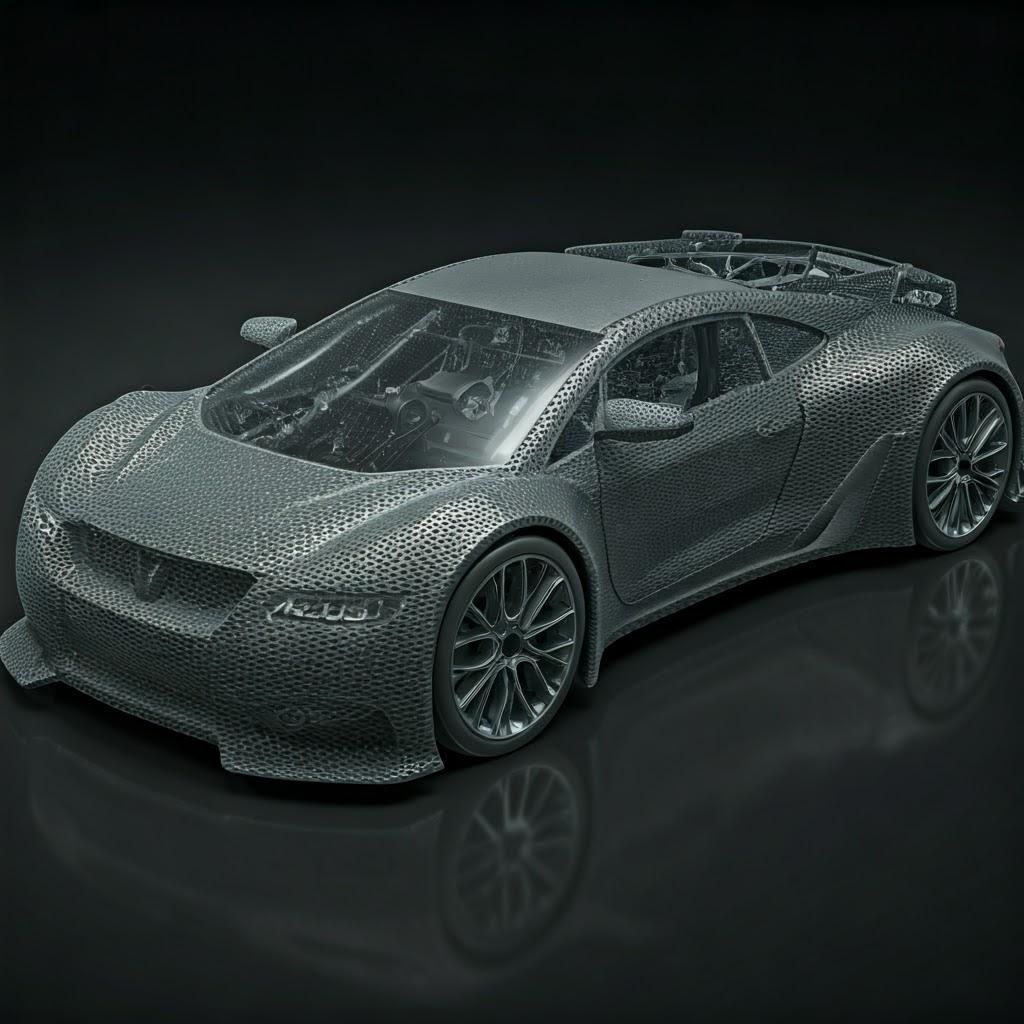
Beyond the Print: Essential Post-Processing Steps for EV Frame Connectors
The journey of a 3D printed metal EV frame connector doesn’t end when the printer stops. The “green” part, fresh off the build plate, requires several crucial post-processing steps to transform it into a functional, reliable automotive component meeting stringent performance and quality standards. These steps are not optional; they are integral to achieving the desired mechanical properties, dimensional accuracy, surface finish, and overall integrity of the connector. Understanding this workflow is vital for engineers specifying parts and for procurement managers factoring in total cost and lead time when sourcing from metal AM suppliers.
Here’s a breakdown of the typical post-processing workflow for metal PBF (SLM/DMLS) printed aluminum alloy (like AlSi10Mg or A7075) EV connectors:
1. Powder Removal:
- プロセス Once the build chamber cools, the build platform containing the printed connectors is removed. The surrounding unfused powder must be carefully extracted. This usually involves brushing, vacuuming, or using compressed air within a controlled environment (depowdering station) to reclaim the loose powder for potential recycling. Complex internal channels or lattice structures designed using DfAM require particular attention to ensure all powder is removed, often involving shaking, vibration, or targeted air jets.
- Importance: Residual powder can sinter during subsequent heat treatment, interfere with mating surfaces, add weight, or become loose during operation. Thorough removal is critical.
2. Stress Relief (Optional but Recommended):
- プロセス Due to the rapid heating and cooling cycles during printing, significant internal residual stresses can build up within the part, especially for complex geometries or materials like A7075. A stress relief heat treatment cycle (at a temperature lower than full solution treatment) can be performed while the part is still attached to the build plate (or immediately after removal) to relax these stresses.
- Importance: Reduces the risk of distortion or cracking during subsequent steps (like removal from the build plate or machining) and improves dimensional stability.
3. Removal from Build Plate:
- プロセス Connectors are typically printed on a thick metal build plate, anchored by the support structures. Separation usually involves cutting the supports close to the plate using a bandsaw, wire Electrical Discharge Machining (EDM), or sometimes a grinder. Wire EDM offers high precision and minimal mechanical stress but is slower.
- Importance: Frees the individual parts for further processing. Requires careful handling to avoid damaging the connectors.
4. Heat Treatment (Crucial for Properties):
- プロセス For alloys like AlSi10Mg and A7075, heat treatment is essential to achieve the required final mechanical properties (strength, hardness). The most common cycle for these aluminum alloys is T6 Temper:
- 溶液処理: Heating the parts to a specific high temperature (e.g., ~500-540°C for AlSi10Mg, ~460-480°C for A7075) for a set duration to dissolve alloying elements into the aluminum matrix.
- 焼き入れ: Rapidly cooling the parts (usually in water or polymer) to trap the elements in a supersaturated solid solution. Quenching needs to be fast to prevent premature precipitation.
- Artificial Aging (Precipitation Hardening): Reheating the parts to a lower temperature (e.g., ~150-180°C) for an extended period (hours). This allows the dissolved alloying elements to precipitate out as fine, dispersed particles within the metal matrix, which impede dislocation movement and significantly increase strength and hardness.
- Importance: Develops the final mechanical properties specified in the design. As-printed parts have significantly lower strength than T6 heat-treated parts. Precise control of temperature, time, and quench rate is critical. Improper heat treatment can lead to suboptimal properties or distortion.
5. Support Structure Removal:
- プロセス The support structures, now fully heat-treated along with the part, must be removed. This is often a manual or semi-automated process involving:
- Breaking/Clipping: Easily accessible supports might be broken off using pliers or clippers.
- 機械加工: Milling or grinding is often required to remove support interfaces more precisely and cleanly, especially from critical surfaces.
- Hand Finishing: Filing or grinding using hand tools might be needed for intricate areas.
- Importance: Supports are sacrificial and not part of the final geometry. Removal can be labor-intensive and constitutes a significant portion of post-processing cost. Poor removal can damage the part surface. DfAM strategies that minimize supports pay dividends here.
6. Surface Finishing:
- プロセス Depending on requirements, various surface finishing techniques can be applied:
- Bead Blasting / Shot Blasting: Propels media (glass beads, ceramic shot) against the surface to create a uniform, matte finish, remove loosely adhered particles, and potentially clean up support witness marks. Shot peening (using spherical metallic shot) can also induce compressive residual stresses, improving fatigue life.
- Tumbling / Vibratory Finishing: Parts are placed in a tumbler with media, causing them to rub against each other and the media to deburr edges and achieve a smoother, more uniform finish over time.
- 研磨: For specific requirements like aesthetics or very low friction, manual or automated polishing can achieve mirror-like finishes.
- 機械加工: As discussed, critical surfaces are often machined to achieve the required smoothness and dimensional tolerance.
- Importance: Improves aesthetics, removes surface imperfections, prepares surfaces for coating, and can enhance mechanical properties like fatigue resistance.
7. Machining of Critical Features:
- プロセス As highlighted under Tolerances, critical interfaces (mounting holes, mating faces, bearing seats) are often CNC machined to achieve tolerances and surface finishes beyond the capability of the as-printed process. This requires proper fixturing of the potentially complex AM part.
- Importance: Ensures precise fit and function within the EV chassis assembly. Requires careful planning during the DfAM phase (adding machining stock).
8. Inspection and Quality Assurance (QA):
- プロセス Throughout the post-processing stages, and especially at the end, rigorous inspection is required.
- 寸法検査: Using CMM, 3D scanning, or traditional metrology to verify tolerances.
- 非破壊検査(NDT): Techniques like X-ray or Computed Tomography (CT) scanning can be used to detect internal defects like porosity or cracks, especially for critical components. Dye penetrant or magnetic particle inspection might be used for surface crack detection.
- Material Property Verification: Hardness testing or tensile testing of sample coupons printed alongside the parts can verify successful heat treatment.
- Importance: Guarantees that the final connector meets all engineering specifications and quality standards before being shipped to the customer or integrated into the vehicle. Essential for safety-critical automotive parts.
9. Optional Coating / Painting:
- プロセス Depending on the operating environment and material (e.g., A7075’s lower corrosion resistance), a protective coating (e.g., anodizing, chemical conversion coating, painting) may be applied.
- Importance: Enhances corrosion resistance, wear resistance, or provides desired aesthetics.
Table: Overview of Post-Processing Steps for AM EV Connectors
ステップ | プロセス説明 | 目的 | 主な検討事項 |
---|---|---|---|
1. Powder Removal | Brushing, Vacuuming, Air jets | Remove unfused powder, Enable recycling | Thoroughness (esp. internal channels), Safety (powder handling) |
2. Stress Relief | Controlled heating/cooling cycle (sub-solution temp) | Reduce residual stress, Prevent distortion/cracking | Timing (often on build plate), Necessity depends on part/material |
3. Plate Removal | Sawing, Wire EDM, Grinding | Separate parts from build plate | Minimize part damage, Method affects speed/cost |
4. Heat Treatment (T6) | Solutionizing, Quenching, Aging | Develop final mechanical properties (Strength, Hardness) | CRITICAL for performance, Requires precise control, Potential distortion |
5. Support Removal | Breaking, Clipping, Machining, Hand finishing | Remove sacrificial supports | Labor-intensive, Risk of surface damage, DfAM impact |
6. Surface Finishing | Blasting, Tumbling, Polishing, Machining | Improve finish, Deburr, Enhance fatigue life, Prepare for coating | Required finish level, Cost, Method choice |
7. Machining (Critical) | CNC Milling, Turning, Drilling | Achieve tight tolerances/fine finishes on specific features | Requires machining stock (DfAM), Fixturing complex shapes |
8. Inspection / QA | Dimensional (CMM, Scan), NDT (CT, X-Ray), Material Testing | Verify conformance to specifications, Ensure integrity | CRITICAL for safety, Methods depend on criticality |
9. Coating (Optional) | Anodizing, Painting, Conversion Coating | Enhance corrosion/wear resistance, Aesthetics | Necessity based on material/environment |
Export to Sheets
Successfully navigating these post-processing steps requires expertise, specialized equipment, and robust quality control systems. When selecting a metal AM service provider for EV frame connectors, it’s crucial to evaluate their capabilities not just in printing, but across this entire workflow, ensuring they can deliver finished components that meet the rigorous demands of the automotive industry. Providers offering end-to-end solutions, from DfAM support through printing and qualified post-processing, offer significant advantages to OEMs and suppliers.
Navigating Challenges: Common Issues in Printing EV Connectors and Mitigation Strategies
While metal additive manufacturing offers significant advantages for producing EV frame connectors, it’s not without its challenges. Like any advanced manufacturing process, achieving consistent, high-quality results requires a deep understanding of potential pitfalls and the implementation of effective mitigation strategies. Awareness of these challenges is crucial for both the AM service provider and the customer (engineers, procurement managers) to set realistic expectations and ensure project success. Partnering with an experienced provider like Met3dp, who leverages high-quality materials and advanced 印刷方法, can significantly reduce the risk associated with these issues.
Here are some common challenges encountered when 3D printing metal EV frame connectors and how to address them:
1. Residual Stress, Warping, and Distortion:
- Issue: The rapid, localized heating by the laser or electron beam and subsequent cooling creates significant temperature gradients within the part and between the part and the build plate. This leads to internal residual stresses. If these stresses exceed the material’s yield strength at elevated temperatures, they can cause the part to warp, distort its shape, or even detach from the build plate during printing. This is particularly relevant for large parts or those with significant changes in cross-section.
- Mitigation Strategies:
- Thermal Simulation: Using simulation software during the DfAM phase to predict areas of high stress concentration and potential distortion based on part geometry and orientation.
- Optimized Part Orientation: Selecting a build orientation that minimizes large, flat surfaces parallel to the build plate and reduces thermal gradients.
- Robust Support Structures: Designing effective supports that not only anchor the part but also help conduct heat away and resist warping forces.
- Build Plate Heating: Maintaining an elevated temperature for the build plate (common in many PBF systems) reduces the temperature differential and lowers residual stress.
- Optimized Scan Strategies: Using specific laser scan patterns (e.g., island scanning, alternating hatches) to distribute heat input more evenly and reduce localized stress buildup.
- Stress Relief Heat Treatment: Performing an intermediate or post-build stress relief cycle, as discussed previously.
2. Porosity (Gas and Lack-of-Fusion):
- Issue: Porosity refers to small voids within the printed material, which can significantly degrade mechanical properties, particularly fatigue strength and fracture toughness. It typically occurs in two forms:
- Gas Porosity: Caused by dissolved gases (often hydrogen in aluminum alloys) trapped within the melt pool during solidification, forming spherical pores. Can originate from contaminated powder or inadequate shielding gas.
- Lack-of-Fusion (LoF) Porosity: Irregularly shaped voids caused by incomplete melting and fusion between adjacent melt tracks or subsequent layers. Often results from insufficient energy input (laser power too low, scan speed too high) or poor powder layer recoating.
- Mitigation Strategies:
- High-Quality Powder: Using high-purity, dry, spherical powders with controlled particle size distribution, like those produced using Met3dp’s advanced atomization techniques. Proper powder handling and storage are crucial to prevent moisture absorption and contamination.
- Optimized Process Parameters: Rigorously developed and validated parameters (laser power, scan speed, layer thickness, hatch spacing) ensure complete melting and fusion. Parameter sets often need optimization for specific alloys and machines.
- Inert Atmosphere Control: Maintaining a high-purity inert gas atmosphere (Argon or Nitrogen) within the build chamber minimizes oxidation and gas pickup.
- Recoating System Check: Ensuring the powder recoater mechanism spreads uniform, dense layers across the build area.
- 非破壊検査(NDT): Using CT scanning or X-ray inspection on final parts (especially critical ones) to detect and quantify internal porosity.
3. Cracking (Solidification/Liquation):
- Issue: Some alloys, particularly high-strength aluminum alloys with wide solidification ranges like A7075, are susceptible to cracking during the rapid solidification of the PBF process.
- Solidification Cracking (Hot Tearing): Occurs in the last stages of solidification when tensile stresses across dendrite arms tear apart the remaining liquid film.
- Liquation Cracking: Occurs in the heat-affected zone (HAZ) of previously solidified layers when low-melting-point phases re-melt and are pulled apart by thermal stresses.
- Mitigation Strategies:
- Alloy Modification/Selection: Using AM-specific grades of alloys where possible (e.g., specific A7075 powder formulations with grain refiners) or selecting less susceptible alloys like AlSi10Mg if performance requirements allow.
- Specialized Process Parameters: Employing carefully tuned parameters (e.g., specific laser power modulation, pre-heating) known to reduce cracking susceptibility for the given alloy. Requires significant process development expertise.
- Build Plate Heating: Higher pre-heating can reduce thermal gradients and cracking risk.
- Optimized Scan Strategies: Specific patterns can help manage thermal stresses.
- NDT: Inspection (e.g., dye penetrant, CT) to detect cracks post-build.
4. Support Structure Removal Difficulties & Damage:
- Issue: Removing supports, especially dense or intricately placed ones, can be time-consuming and risks damaging the part surface (scratches, gouges) or even breaking delicate features. Supports in internal channels can be particularly challenging to remove completely.
- Mitigation Strategies:
- DfAM for Support Reduction: Designing parts with self-supporting angles and optimizing orientation to minimize the need for supports is the primary strategy.
- Optimized Support Design: Using support structures with lower density where possible, employing easily breakable interface layers between the support and the part, and ensuring accessibility for removal tools. Software tools often offer various support types and customization options.
- Appropriate Removal Techniques: Using the right tools (wire EDM for clean cuts, careful manual breaking, targeted machining) based on the support type and location.
- Skilled Technicians: Experienced technicians are better able to remove supports without damaging the part.
5. Achieving Consistent Material Properties:
- Issue: Ensuring that the mechanical properties (strength, ductility, fatigue life) are consistent throughout the part and from build to build can be challenging due to the sensitivity of the PBF process to parameter variations, powder quality fluctuations, and machine calibration drifts.
- Mitigation Strategies:
- Robust Process Control: Implementing strict process monitoring and control (laser power monitoring, melt pool monitoring where available, inert atmosphere control). Using high-quality, well-maintained AM systems.
- Powder Quality Management: Consistent feedstock is crucial. Utilizing powder from reputable suppliers like Met3dp with strong quality control, implementing powder batch tracking, and managing powder recycling procedures carefully (testing recycled powder properties).
- Standardized Procedures: Adhering to qualified printing procedures, post-processing steps (especially heat treatment), and machine maintenance schedules.
- Coupon Testing: Printing and testing witness coupons alongside actual parts within each build to verify that the desired material properties are being achieved consistently.
- Calibration and Maintenance: Regular calibration and preventative maintenance of the AM equipment.
6. Cost and Lead Time Management:
- Issue: While offering advantages, metal AM can sometimes have higher per-part costs and longer lead times compared to traditional methods, especially for simpler parts at high volumes. Factors include machine hour rates, powder cost, build times (influenced by part volume and height), and extensive post-processing.
- Mitigation Strategies:
- DfAM for Efficiency: Optimizing designs not just for performance but also for printability (reducing supports, minimizing build height through orientation, nesting multiple parts on a build plate).
- プロセスの最適化: Fine-tuning parameters for faster build speeds where acceptable quality can be maintained.
- Streamlined Post-Processing: Efficient workflows and automation where possible for support removal and finishing.
- Strategic Application: Focusing AM on applications where its benefits (complexity, lightweighting, consolidation, speed for low volumes) provide the most value, justifying the cost (e.g., high-performance connectors, prototypes, complex nodes).
- Clear Communication with Supplier: Working closely with the AM service provider to understand cost drivers and lead time estimates early in the project. Requesting detailed quotes (RFQ responses) that break down costs.
Table: Common AM Challenges for EV Connectors & Mitigation
チャレンジ | 潜在的な影響 | Key Mitigation Strategies | B2B Relevance |
---|---|---|---|
Residual Stress / Warping | Dimensional inaccuracy, Build failure | Thermal simulation, Optimized orientation, Supports, Build plate heating, Scan strategies, Stress relief | Supplier’s simulation and process control capability affects part quality. |
Porosity (Gas / LoF) | Reduced strength, Fatigue life, Leak paths | High-quality powder, Optimized parameters, Atmosphere control, NDT | Powder quality (e.g., Met3dp) and process control are key supplier differentiators. |
Cracking (Solidification) | Catastrophic failure, Reduced strength | Alloy selection/modification, Specialized parameters, Pre-heating, NDT | Supplier expertise with challenging alloys (like A7075) is critical. |
Support Removal Difficulty | Surface damage, High labor cost, Longer lead time | DfAM (minimize supports), Optimized support design, Proper removal tools, Skilled labor | Efficient post-processing impacts final cost and delivery time. |
Inconsistent Properties | Unreliable performance, Safety concerns | Process control, Powder management, Standardized procedures, Coupon testing, Calibration | Supplier’s Quality Management System (QMS) and process consistency are vital. |
Cost / Lead Time | Budget overruns, Project delays | DfAM for efficiency, Process optimization, Streamlined post-processing, Strategic application, Clear supplier communication | Transparent quoting (RFQ) and realistic lead times build trust. |
Export to Sheets
By acknowledging these potential challenges and proactively implementing mitigation strategies through careful design, material selection, process control, and post-processing, manufacturers can successfully leverage metal additive manufacturing to produce high-performance, reliable EV frame connectors, pushing the boundaries of electric vehicle design and efficiency. Choosing a knowledgeable and well-equipped AM partner is paramount in navigating these complexities effectively.
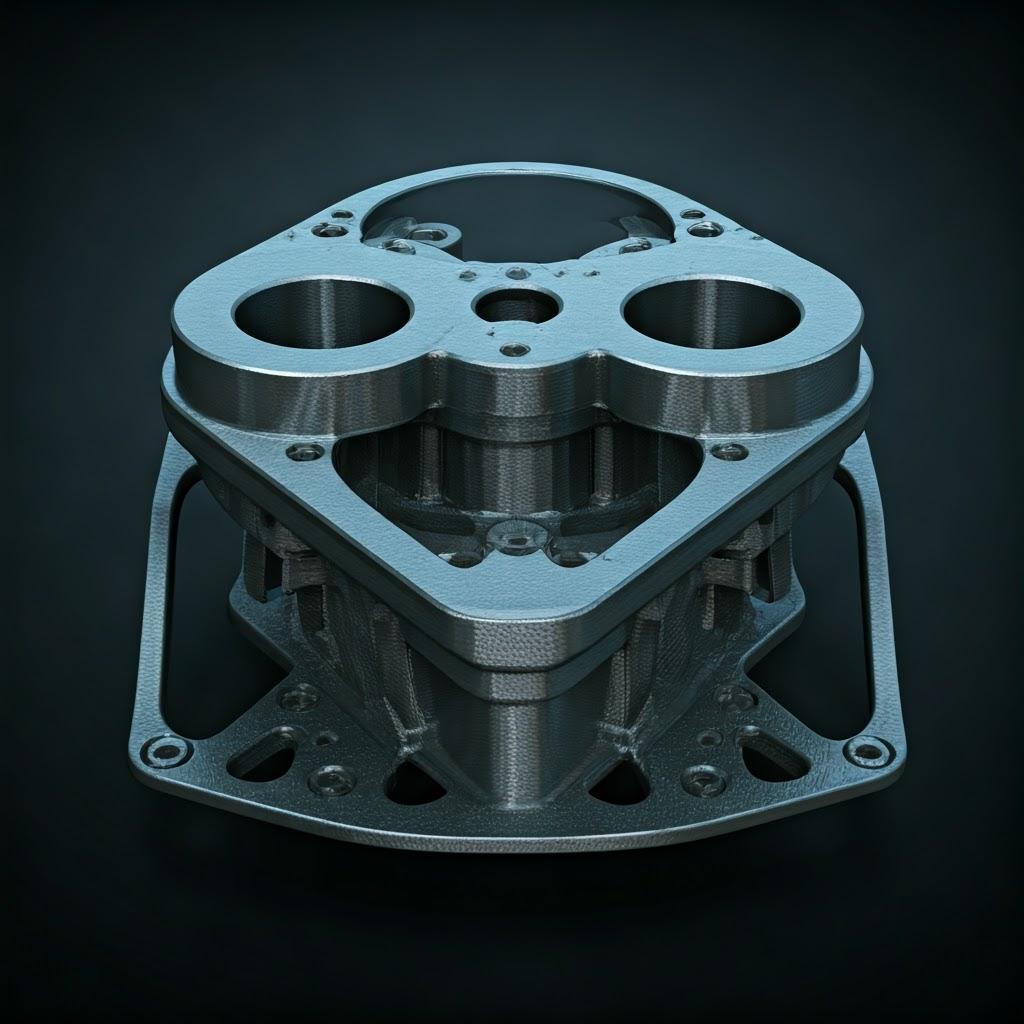
Selecting Your Partner: How to Choose the Right Metal AM Service Provider for EV Components
The success of implementing 3D printed metal EV frame connectors hinges significantly on the capabilities and expertise of your chosen additive manufacturing (AM) service provider. This is more than just a transactional purchase; it’s often a technical partnership, especially when dealing with complex structural components requiring high levels of quality control and engineering support. For procurement managers and engineers tasked with sourcing these parts, whether for prototyping, low-volume production, or evaluating suppliers for potential serial production, a thorough vetting process is essential. Selecting the right partner ensures access to the necessary technology, materials expertise, quality assurance, and support to achieve your project goals effectively and efficiently.
Here are key criteria to evaluate when choosing a metal AM service provider for critical EV components like frame connectors:
1. Technical Expertise and Engineering Support:
- DfAM Capabilities: Does the provider offer Design for Additive Manufacturing (DfAM) support? Can they assist your engineering team in optimizing connector designs for lightweighting (topology optimization, lattices), part consolidation, support minimization, and overall printability? True partners offer collaborative design consultation, not just printing services.
- Materials Science Knowledge: Do they possess deep expertise in the specific metal alloys required (e.g., AlSi10Mg, A7075)? Can they advise on material selection based on performance requirements and manufacturability? Do they understand the nuances of achieving desired properties through process control and heat treatment for these materials? Expertise in challenging alloys like A7075 is a significant differentiator.
- プロセスの最適化: Do they have robust, well-documented procedures for process parameter optimization for different materials and geometries? Can they demonstrate control over factors influencing porosity, residual stress, and dimensional accuracy?
- Problem-Solving: How do they approach potential challenges like build failures, distortion, or quality issues? Look for a proactive and transparent approach to troubleshooting.
2. Equipment, Technology, and Capacity:
- Printer Technology: What type of metal AM systems do they operate (e.g., Laser Powder Bed Fusion – L-PBF/SLM/DMLS, Electron Beam Melting – EBM)? Do they have machines suitable for the required materials and part sizes? Different technologies have varying strengths (e.g., EBM often results in lower residual stress but rougher surfaces).
- Machine Fleet and Redundancy: How many machines do they have? Is there redundancy to handle potential downtime or large orders? Assess their capacity relative to your volume requirements (prototypes, series production).
- Maintenance and Calibration: Do they adhere to rigorous maintenance and calibration schedules for their equipment to ensure consistent performance?
- ソフトウェアだ: What software do they use for build preparation, simulation (thermal, stress), and potentially topology optimization?
3. Material Portfolio and Quality:
- Relevant Alloys: Do they offer the specific aluminum alloys (AlSi10Mg, A7075) needed for your EV connectors? What is their experience level with these specific materials?
- Powder Sourcing and Management: Where do they source their metal powders? Do they have stringent quality controls for incoming powder and robust procedures for powder handling, storage, and recycling to maintain traceability and prevent contamination? Companies like メット3dp, which manufacture their own 高品質の金属粉 using advanced atomization techniques, often have an advantage in ensuring feedstock consistency.
- New Material Development: Are they actively involved in qualifying new materials or developing parameters for challenging alloys? This indicates a commitment to innovation.
4. Post-Processing Capabilities:
- In-House vs. Outsourced: What post-processing steps (powder removal, stress relief, heat treatment, support removal, machining, surface finishing, inspection) do they perform in-house? Which are outsourced? In-house capabilities generally allow for better control over quality, lead time, and cost.
- Heat Treatment Expertise: Do they have properly calibrated furnaces and documented procedures for critical heat treatments like T6 for aluminum alloys? Can they provide certification?
- Machining Capabilities: Do they have CNC machining capabilities suitable for achieving tight tolerances on complex AM parts? Or do they have established relationships with qualified machining partners?
- Finishing Options: Can they provide the required surface finishes (blasting, tumbling, polishing)?
5. Quality Management System (QMS) and Certifications:
- ISO 9001: This is the baseline certification indicating a documented QMS for consistent quality. It’s essential for any reputable manufacturing partner.
- IATF 16949: This is the critical certification for suppliers to the automotive industry. It builds upon ISO 9001 with specific, stringent requirements for automotive quality management, including process control, traceability, risk management (FMEA), and continuous improvement. A provider with IATF 16949 certification demonstrates a commitment and capability to meet the rigorous demands of automotive production. While not all AM providers have it yet, those serving the automotive sector seriously should be working towards it or possess it.
- Aerospace Certifications (e.g., AS9100): While specific to aerospace, this certification also indicates a very high level of process control and quality management, which can be beneficial.
- Traceability: Can they provide full traceability from raw powder batch to the final shipped part, including process data and inspection records? This is non-negotiable for automotive components.
6. Project Management and Communication:
- Clear Quotations (RFQ Response): Do they provide detailed and transparent quotes that break down costs and lead times?
- Communication: Are they responsive, proactive, and easy to communicate with? Is there a dedicated point of contact for your projects?
- Project Tracking: How do they manage project timelines and provide updates?
7. Experience and Case Studies:
- Track Record: Do they have demonstrable experience producing similar components (structural parts, automotive components)? Can they provide relevant case studies or references (respecting confidentiality)?
- Industry Focus: Do they specialize or have significant experience in the automotive sector? Understanding industry-specific requirements is crucial.
8. Cost, Value, and Lead Time:
- 競争力のある価格設定: Is their pricing competitive for the level of service, quality, and expertise offered? Beware of providers offering significantly lower prices, as this may indicate compromises in quality, materials, or process control. Focus on overall value, not just the lowest price.
- Realistic Lead Times: Do they provide achievable lead time estimates based on current capacity and the complexity of the project?
Why Consider Met3dp?
Based on these criteria, a company like メット3dp presents a compelling profile. As a provider specializing in both 3Dプリンティング装置 そして 高性能金属粉末, they possess a unique end-to-end understanding of the metal AM process.
- 材料に関する専門知識: Their focus on producing high-quality spherical metal powders using advanced gas atomization ensures a reliable foundation for printing dense, high-performance parts. Their portfolio includes innovative alloys, showcasing materials science depth.
- Technological Know-How: Offering comprehensive solutions spanning printers (including SEBM), powders, and application development services suggests deep technical expertise across the AM value chain.
- Industry Focus: Targeting mission-critical parts in aerospace, medical, automotive, and other fields indicates experience with demanding applications.
- Comprehensive Solutions: Their ability to partner with organizations for application development and digital manufacturing transformations positions them as more than just a parts supplier, but a potential strategic partner.
Table: Key Evaluation Criteria for AM Service Providers
基準 | Key Questions to Ask | Why It Matters for EV Connectors | Look For |
---|---|---|---|
技術的専門知識 | DfAM support? Materials knowledge (AlSi10Mg, A7075)? Process optimization? Problem-solving approach? | Optimizes design, ensures properties, guarantees quality, reduces risk | Collaborative DfAM, Deep materials science, Documented processes, Proven troubleshooting |
Equipment & Capacity | Technology type (L-PBF/EBM)? Fleet size/redundancy? Maintenance/calibration protocols? Software used? | Ensures capability, handles volume, maintains consistency, enables advanced design/simulation | Suitable machines, Adequate capacity, Rigorous maintenance, Modern software |
Material Portfolio/Quality | Offers required alloys? Powder sourcing/QC? Powder management procedures? | Ensures performance, guarantees consistency, prevents defects | Specific alloys available, Reputable powder source (e.g., Met3dp), Strict powder handling protocols |
後処理 | In-house vs. outsourced capabilities? Heat treatment control? Machining precision? Finishing options? | Ensures final properties/tolerances, Controls lead time/cost | Comprehensive in-house capabilities (esp. Heat Treat, Machining, NDT), Qualified partners if outsourced |
QMS & Certifications | ISO 9001? IATF 16949 (critical for automotive)? AS9100? Full traceability? | Guarantees consistent quality, Meets automotive standards, Ensures accountability | ISO 9001 (minimum), IATF 16949 (highly desired/required), Full material & process traceability |
Project Mgmt & Comm. | Clear quotes (RFQ)? Responsiveness? Dedicated contact? Project tracking? | Ensures smooth workflow, transparency, and timely delivery | Detailed RFQs, Proactive communication, Clear reporting |
Experience & Case Studies | Track record with similar parts/industry? References available? | Demonstrates capability and understanding of specific challenges | Relevant automotive/structural part examples, Positive client feedback |
Cost, Value, Lead Time | Competitive pricing (value-based)? Realistic lead times? | Balances budget with quality and speed | Transparent pricing, Focus on total value, Achievable delivery dates |
Export to Sheets
Choosing the right metal AM service provider is a strategic decision. By carefully evaluating potential partners against these criteria, focusing on technical expertise, quality systems (especially IATF 16949 for automotive), and a collaborative approach, automotive manufacturers and suppliers can confidently leverage additive manufacturing to produce innovative, high-performance EV frame connectors.
Understanding the Investment: Cost Factors and Lead Times for 3D Printed EV Connectors
While the technical benefits of using metal additive manufacturing for EV frame connectors – lightweighting, design freedom, part consolidation – are compelling, understanding the associated costs and typical lead times is crucial for project planning, budgeting, and making informed decisions, especially for procurement managers comparing AM to traditional manufacturing methods. The cost structure of AM differs significantly from casting or machining, particularly concerning tooling and volume sensitivity.
Key Cost Factors:
The final price of a 3D printed metal EV connector is influenced by a complex interplay of factors. When requesting quotes (RFQs) from service providers, understanding these drivers helps in evaluating proposals and identifying potential cost optimization opportunities through DfAM.
- 材料費:
- Powder Type: Different metal powders have vastly different costs per kilogram. Standard alloys like AlSi10Mg are generally less expensive than specialized or high-strength alloys like AM-grade A7075 or titanium alloys.
- Powder Consumption: This includes not only the powder that forms the final part but also the powder used for support structures and potentially some waste or non-recyclable powder. The part’s overall volume (bounding box within the printer) also influences how much surrounding powder is involved, although much of this is recyclable.
- Machine Time (Printer Usage):
- Part Volume: The actual volume of material being sintered directly impacts print time. Larger, denser parts take longer.
- Part Height (Z-Height): Print time is often heavily influenced by the number of layers required. Taller parts generally take longer to print, regardless of volume, due to the recoating time for each layer. Orientation choices during DfAM significantly impact this.
- パート・コンプレックス: Highly complex geometries with intricate features might require slower scan speeds or specific strategies, potentially increasing print time.
- Support Structure Volume: The volume of material needed for supports adds directly to print time. Minimizing supports via DfAM reduces this cost.
- Nesting/Build Density: Service providers aim to maximize the number of parts printed in a single build (nesting). Builds packed with many parts distribute the machine setup and run time costs, lowering the per-part cost compared to printing a single part alone. Your required quantity influences nesting efficiency.
- Machine Hour Rate: Service providers have an hourly rate for their expensive AM equipment, covering depreciation, maintenance, energy, facility costs, and labor.
- 人件費:
- Setup & Teardown: Preparing the machine for a build (loading powder, setting up parameters) and removing the parts and cleaning the machine afterward.
- デパウダリング: Manual or semi-automated work to remove unfused powder.
- サポートの取り外し: Often a significant manual labor component, especially for complex parts or hard-to-reach supports.
- Finishing & Machining: Labor involved in bead blasting, tumbling, CNC machining setup and operation, polishing, etc.
- Inspection & QA: Labor for dimensional checks, NDT analysis, documentation.
- 後処理費用:
- Stress Relief / Heat Treatment: Costs associated with furnace time, energy consumption, and potentially specialized atmospheres.
- 機械加工: Costs for CNC machine time, tooling, and fixture creation (if needed). This can be a substantial cost if extensive machining is required.
- 表面仕上げ: Costs for equipment usage (blasters, tumblers) and consumables (media).
- Testing & Inspection: Costs for NDT equipment usage (e.g., CT scanning time), CMM inspection time, or destructive testing of coupons.
- Engineering and Data Preparation:
- DfAM Support: If the service provider assists significantly with design optimization, this engineering time may be factored into the cost.
- Build Preparation: Time spent orienting parts, generating support structures, slicing the model, and creating the build file.
- Quantity and Batch Size:
- 規模の経済: AM exhibits some economies of scale, but differently than traditional methods. Setup costs are distributed over more parts in larger batches. Efficient nesting significantly lowers per-part machine time costs. However, the fundamental relationship between part volume/height and print time remains. Volume discounts are common but may plateau sooner than with casting/stamping due to the direct link between material/time and cost per part.
- Prototyping vs. Production: One-off prototypes will have a higher per-part cost than parts produced in a batch of 10, 50, or 100.
Typical Lead Times:
Lead time refers to the total time from order placement (or design finalization) to receiving the finished parts. It’s influenced by several sequential steps:
- Order Processing & Planning (1-3 days): Final quote approval, scheduling the job into the production queue.
- Build Preparation (0.5-2 days): Finalizing orientation, support generation, slicing, build file creation. Can occur partly in parallel with queue time.
- Printer Queue Time (Variable: 1 day – 2+ weeks): How busy the service provider’s relevant machines are. High demand or dedicated machine use for large projects can significantly impact this.
- Printing Time (Variable: 12 hours – 1+ week): Highly dependent on part size (especially height), complexity, and the number of parts nested in the build. A single large connector or a full plate of smaller connectors can take several days to print.
- Cooling & Depowdering (0.5-1 day): Allowing the build chamber and parts to cool sufficiently before careful powder removal.
- Post-Processing (Variable: 2 days – 2+ weeks): This is often the most variable part of the lead time.
- Stress Relief/Heat Treatment: Typically 1-2 days (including furnace time and cooling).
- Build Plate Removal/Support Removal: 0.5 – 3+ days, depending on complexity and labor intensity.
- Machining: Highly variable depending on the extent of machining required and machine shop scheduling (0.5 – 5+ days).
- Surface Finishing: 0.5 – 2 days.
- Inspection/QA: 0.5 – 2+ days depending on requirements (e.g., external lab NDT).
- Shipping (1-5 days): Depending on location and shipping method chosen.
Overall Estimated Lead Time:
- Simple Prototypes (minimal post-processing): ~1 – 2 weeks
- Complex Prototypes / Small Batches (with heat treat, basic finishing): ~2 – 4 weeks
- Production Parts (with heat treat, machining, rigorous QA): ~4 – 8+ weeks
Important Note: These are general estimates. Complex parts, challenging materials (A7075), extensive machining, stringent QA, or high machine utilization at the supplier can significantly extend these timelines. Always request specific lead time estimates in your RFQ.
Table: Summary of Cost Drivers and Lead Time Factors
Factor Category | 主な推進要因 | コストへの影響 | Impact on Lead Time |
---|---|---|---|
素材 | Powder type (alloy), Part volume, Support volume | High (Direct material consumption) | Minimal (Covered by Print Time) |
Machine Time | Part height, Part volume, Nesting efficiency, Support volume | Very High (Machine hour rate) | Very High (Actual time printing) |
労働 | Setup, Depowdering, Support removal, Finishing, Machining, QA | High (Manual effort involved) | Moderate (Contributes to post-processing time) |
後処理 | Heat treat, Machining extent, Finishing level, NDT requirements | Moderate to Very High (Depending on complexity) | High (Often the most variable & longest stage) |
エンジニアリング | DfAM support needed, Build preparation complexity | 低~中程度 | Low (Mostly upfront planning) |
数量 | Number of identical parts per order/build | Moderate (Economies of scale via nesting/setup) | Low (Affects scheduling more than per-part time) |
Scheduling | Service provider’s machine queue | Minimal (Indirect) | Moderate to High (Waiting time for machine) |
Export to Sheets
Understanding these cost and lead time dynamics allows for better budgeting, project planning, and realistic comparisons between AM and traditional manufacturing routes when sourcing EV frame connectors. Open communication with potential suppliers during the RFQ process is key to obtaining accurate estimates for specific projects.
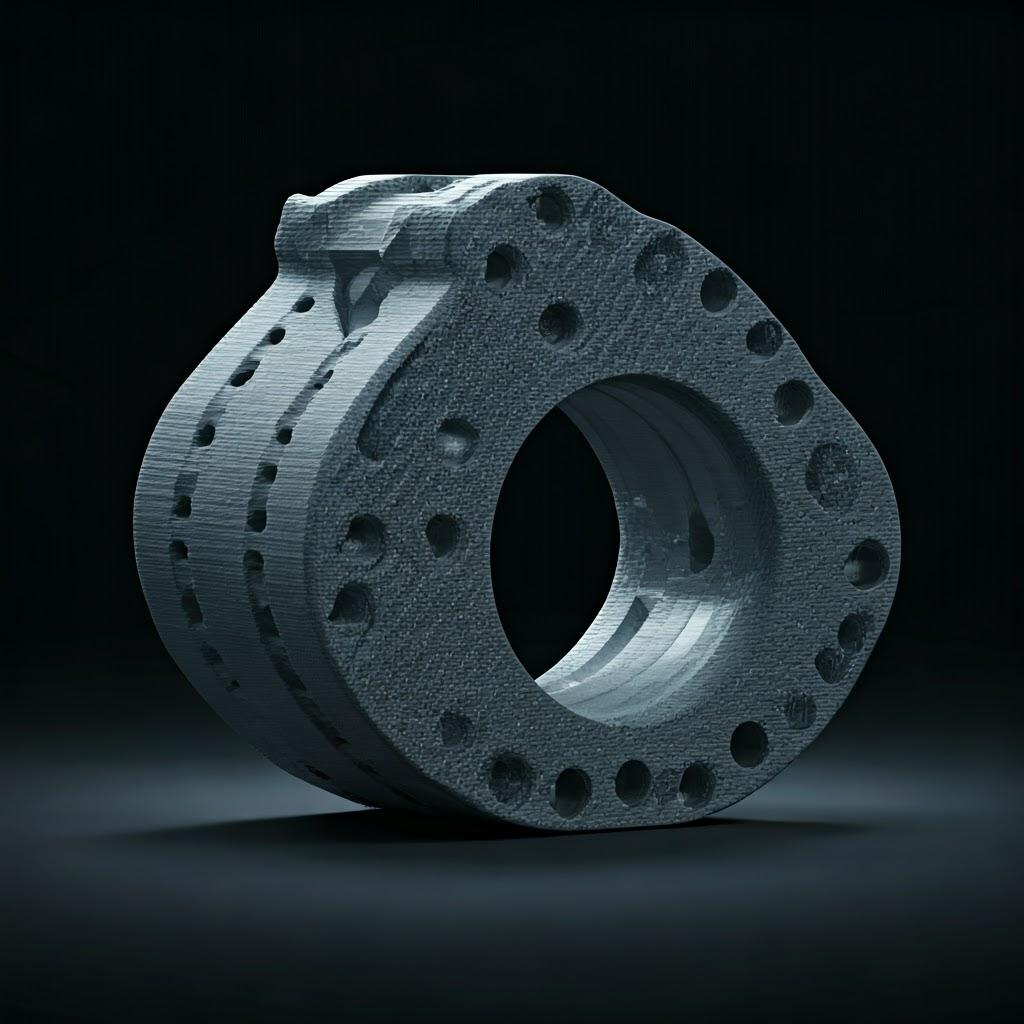
Frequently Asked Questions (FAQ) about 3D Printed EV Frame Connectors
Here are answers to some common questions engineers and procurement managers have about using metal additive manufacturing for electric vehicle frame connectors:
1. Are 3D printed metal connectors as strong or reliable as connectors made by casting or machining?
- 答え: Yes, absolutely, provided they are designed, printed, and post-processed correctly. Metal AM processes like L-PBF can produce fully dense parts (typically >99.5% density) with mechanical properties that can meet or even exceed those of equivalent cast materials.
- 素材の特性: Using high-quality powders (like AlSi10Mg or A7075) and applying appropriate heat treatments (like T6) results in high strength, stiffness, and durability. For instance, heat-treated AlSi10Mg printed parts can achieve properties comparable to A356 casting alloys, while properly processed A7075 can offer strengths significantly higher, approaching wrought levels.
- デザインの最適化: DfAM techniques like topology optimization allow engineers to create designs that are inherently stronger for their weight compared to traditional designs constrained by casting or machining limitations.
- Reliability: Reliability comes from robust process control, high-quality materials, thorough post-processing (especially heat treatment and stress relief), and rigorous quality assurance (including NDT for critical parts). Partnering with an experienced provider with strong quality systems (ideally IATF 16949 certified or compliant) is crucial for ensuring reliability in demanding automotive applications. The layer-by-layer process requires careful control to avoid defects like porosity or lack-of-fusion, but when controlled, the resulting parts are highly reliable.
2. Is metal 3D printing cost-effective for mass production of EV frame connectors?
- 答え: It depends on the definition of “mass production” and the specific part. Currently, metal AM is generally most cost-effective のために:
- プロトタイピング: Rapid production of functional prototypes without tooling costs.
- Low-to-Mid Volume Production: Typically runs from single units up to hundreds or potentially low thousands of parts per year, where the high cost of traditional tooling (casting molds, stamping dies) cannot be amortized effectively.
- Highly Complex or Consolidated Parts: Where AM enables designs that are impossible or prohibitively expensive to make otherwise, or where consolidating multiple parts into one AM component saves significant assembly cost and improves performance.
- Bridge Production: Producing initial batches of parts while waiting for mass production tooling to be completed.
- 比較する: について very high volumes (tens or hundreds of thousands per year) of relatively simple connector designs, traditional methods like die casting or stamping/welding usually offer a lower per-part cost due to faster cycle times and lower material costs, despite the high initial tooling investment.
- Future Trend: Technology advancements, faster machines, lower powder costs, and increased automation in post-processing are continuously improving the economics of AM, pushing the break-even point towards higher volumes. However, for true mass production automotive scales today, traditional methods often remain more economical for simpler components. The value proposition for AM in higher volumes lies strongly in parts where complexity, consolidation, and lightweighting offer significant performance or system-level cost benefits.
3. What key information should I provide to a service provider when requesting a quote (RFQ) for 3D printed EV connectors?
- 答え: To receive an accurate and timely quote, provide as much detailed information as possible:
- CAD Model: A 3D model in a standard format (e.g., STEP, IGES). Ensure the model is “watertight” and suitable for AM.
- Material Specification: Clearly state the desired alloy (e.g., AlSi10Mg, A7075) and any required temper condition (e.g., T6 heat treatment).
- Technical Drawing (Optional but Recommended): A 2D drawing specifying critical dimensions, tolerances (using Geometric Dimensioning and Tolerancing – GD&T), surface finish requirements (Ra values) for specific features, and any other critical technical requirements.
- 数量: Specify the number of parts required for this order and, if applicable, estimated annual volume for production intent.
- 後処理の要件: Detail all necessary steps: heat treatment specs, specific surfaces requiring machining (highlighting them and specifying tolerances/finish), required surface treatments (e.g., bead blasting, anodizing), inspection requirements (e.g., CMM report, NDT needs like CT scanning).
- Testing/Certification Needs: Any requirements for material certifications, certificates of conformance, coupon testing results, specific automotive standards compliance (e.g., IATF 16949 traceability).
- Application Context (Optional but helpful): Briefly describing the connector’s function and location in the EV can help the provider understand criticality and offer better DfAM advice.
- Desired Lead Time: Indicate your required delivery timeframe.
4. What quality certifications are most important when choosing a supplier for automotive components like EV connectors?
- 答え: Quality certifications demonstrate a supplier’s commitment to consistent processes and product quality. For automotive applications:
- ISO 9001: This is the foundational standard for Quality Management Systems (QMS). It’s a minimum requirement for any credible manufacturing supplier.
- IATF 16949: This is the most important standard for the automotive industry supply chain. It integrates ISO 9001 with specific, more rigorous requirements tailored to automotive needs, focusing heavily on defect prevention, risk management (FMEA), process control, traceability, and continuous improvement. Choosing an IATF 16949 certified supplier provides the highest level of confidence for automotive components. If a provider isn’t fully certified yet, inquire about their compliance status and roadmap towards certification.
- AS9100: While specific to aerospace, this standard also signifies a very mature and robust QMS, often exceeding ISO 9001 requirements, particularly regarding traceability and process control.
Conclusion: Accelerating EV Innovation with Additive Manufactured Frame Connectors
The relentless drive towards lighter, safer, and more efficient electric vehicles demands innovation across every aspect of vehicle design, particularly within the critical chassis structure. As we’ve explored, metal additive manufacturing offers a powerful and transformative approach to producing EV frame connectors, moving beyond the limitations of traditional casting and fabrication methods.
By leveraging the capabilities of metal AM, specifically processes like Laser Powder Bed Fusion, engineers can unlock unprecedented benefits:
- Significant Lightweighting: Through topology optimization and advanced geometries like internal lattices, AM enables the creation of connectors that drastically reduce vehicle mass, directly contributing to extended battery range and enhanced performance.
- 比類なき設計の自由度: The layer-by-layer process liberates designers to create highly complex, organic shapes that follow optimal load paths and integrate multiple functions, leading to more efficient and elegant structural solutions.
- パーツの統合: AM allows for the integration of multiple components into a single, monolithic printed part, simplifying assembly, reducing weight, eliminating potential failure points, and streamlining the supply chain.
- Accelerated Development: Rapid prototyping without tooling dramatically shortens design iteration cycles, allowing for faster validation and quicker time-to-market for new EV platforms and models.
- 高性能素材: AM enables the use of advanced aluminum alloys like AlSi10Mg and high-strength A7075, tailored to the specific demands of structural automotive applications.
However, realizing these benefits requires a holistic approach. Embracing Design for Additive Manufacturing (DfAM) principles is not optional but essential for optimizing parts for the process. Careful consideration must be given to achievable tolerances, surface finishes, and the necessary post-processing steps – including critical heat treatments and potentially precision machining – to meet final engineering requirements. Navigating potential challenges like residual stress, porosity, and support removal demands expertise and robust process control.
Crucially, the success of adopting 3D printed connectors relies heavily on selecting the right manufacturing partner. Evaluating potential suppliers based on their technical expertise, material quality, process control, post-processing capabilities, capacity, and, critically for automotive, their Quality Management System (ideally IATF 16949 certified or compliant), is paramount.
次のような企業 メット3dp, with their foundation in producing high-quality metal powders and providing comprehensive solutions that span AM equipment and application development, represent the type of knowledgeable partner needed to navigate the complexities and unlock the full potential of additive manufacturing. Their expertise ensures that the materials and processes employed meet the high standards required for mission-critical automotive components.
Metal 3D printing is no longer just a prototyping technology; it is a viable and increasingly compelling manufacturing solution for demanding applications like EV frame connectors. By strategically implementing AM, automotive companies can accelerate innovation, push the boundaries of vehicle performance and efficiency, and build the next generation of electric vehicles.
Ready to explore how metal additive manufacturing can revolutionize your EV chassis components? 連絡先 メット3dp today to discuss your project requirements and discover how our cutting-edge systems, advanced metal powders, and application expertise can power your organization’s additive manufacturing goals.
シェアする
MET3DP Technology Co., LTDは、中国青島に本社を置く積層造形ソリューションのリーディングプロバイダーです。弊社は3Dプリンティング装置と工業用途の高性能金属粉末を専門としています。
関連記事
Met3DPについて
最新情報
製品
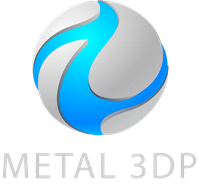
3Dプリンティングと積層造形用金属粉末