超合金AMによるロケットエンジン用イグナイターハウジング
目次
Revolutionizing Rocketry: Metal 3D Printed Igniter Housings in IN718 & Haynes 282
The quest for more efficient, powerful, and reliable access to space demands constant innovation in rocket propulsion technology. At the very heart of initiating the immense power of a rocket engine lies a critical, often underappreciated component: the igniter housing. This component operates under some of the most extreme conditions imaginable – facing searing temperatures, colossal pressures, and intense vibrations within fractions of a second. Its function is simple, yet failure is catastrophic: it must reliably house and protect the ignition source, ensuring controlled and consistent engine start-up, mission after mission. For decades, manufacturing these intricate components from high-performance superalloys has been a significant challenge, pushing the boundaries of traditional machining, casting, and fabrication techniques.
Enter the era of Superalloy Additive Manufacturing (AM), more commonly known as metal 3Dプリンティング. This transformative technology is fundamentally reshaping how complex, high-value components like rocket igniter housings are designed and produced. By building parts layer by layer directly from fine metal powder, AM unlocks unprecedented design freedom, enables the creation of previously impossible geometries, and offers pathways to enhanced performance and reduced lead times. Specifically, the ability to work effectively with advanced nickel-based superalloys such as インコネル718 (IN718) そして ヘインズ 282, materials chosen for their exceptional high-temperature strength and resistance to harsh environments, positions metal AM as a pivotal technology for next-generation rocket engine development.
This deep dive is tailored for aerospace engineers, propulsion system designers, manufacturing specialists, and procurement managers within the aerospace and defense sectors. Whether you are involved in designing launch vehicles, satellite propulsion systems, or hypersonic applications, understanding the capabilities, nuances, and advantages of utilizing metal AM for critical components like igniter housings is essential. We will explore the functional requirements, contrast AM with conventional methods, delve into the crucial material properties of IN718 and Haynes 282, and discuss why partnering with an experienced additive manufacturing solutions provider is key to success. The focus is on leveraging AM not just as a manufacturing method, but as an enabler of superior performance and reliability in demanding aerospace applications. Companies seeking reliable aerospace manufacturing partners そして wholesale suppliers of mission-critical 3D printed metal parts will find actionable insights into qualifying processes and materials for flight hardware. The inherent challenges of rocketry – extreme temperatures, volatile chemical reactions, immense structural loads, and zero tolerance for failure – necessitate manufacturing processes that are equally robust and advanced. Superalloy AM, particularly when utilizing high-quality powders and optimized process parameters offered by specialists like Met3dp, provides a compelling solution to these challenges, paving the way for lighter, more intricate, and higher-performing propulsion systems.
The Crucial Function: What Are Rocket Igniter Housings Used For?
The igniter housing is the linchpin of the rocket engine ignition sequence. While the engine itself generates thrust through the controlled, high-energy combustion of propellants, this process cannot begin without a reliable and precisely timed initiation event. The igniter housing serves as the protective enclosure and mounting structure for the device responsible for creating the initial flame or spark – the igniter itself (which could be pyrotechnic, hypergolic, torch, or spark-based).
Core Functions:
- Containment: It must safely contain the high pressures and temperatures generated by the igniter element during its brief but intense operation. This prevents damage to surrounding engine components and ensures the ignition energy is directed effectively towards the main propellant flow.
- Structural Support: The housing provides a rigid mounting point for the igniter, ensuring it remains correctly positioned relative to the combustion chamber or propellant injectors, even under severe launch vibrations and g-forces.
- Environmental Protection: It shields the sensitive igniter components from the harsh environment within the engine’s thrust chamber assembly before and during ignition, including reactive propellant vapors or extreme ambient temperatures.
- Interface: The housing often incorporates critical interface features, such as mounting flanges, sealing surfaces, and sometimes ports for wiring or small propellant feed lines (in the case of torch igniters), enabling secure integration into the larger engine assembly.
Applications Span the Breadth of Rocketry:
The fundamental need for reliable ignition means igniter housings are ubiquitous across various propulsion systems:
- Launch Vehicle Main Engines: From large liquid-propellant engines (like RP-1/LOX or LH2/LOX) powering first and second stages to solid rocket boosters (SRBs), robust ignition is paramount for mission success. Igniter housings here must withstand particularly high pressures and thermal shocks.
- Upper Stage Engines: Often requiring multiple restarts in space, the igniters and their housings for upper stage engines must be exceptionally reliable and capable of functioning after prolonged exposure to the vacuum and temperature extremes of space.
- Satellite Propulsion Systems: Used for orbit insertion, station-keeping, and attitude control, satellite thrusters (monopropellant, bipropellant, or electric) rely on miniature, highly precise igniter systems. Housings here prioritize low mass and high reliability over extended mission durations.
- Missile and Defense Systems: Tactical and strategic missile systems require instantaneous and reliable ignition under demanding operational conditions. Igniter housings must meet stringent military specifications (Mil-Spec) for shock, vibration, and environmental resistance.
- Research and Experimental Rockets: Providing a testbed for new technologies, these often push the boundaries of performance, requiring adaptable and often custom-designed igniter housings.
Supply Chain Considerations for B2B Buyers:
Procurement managers and 航空宇宙サプライヤー looking to source or manufacture igniter housings face unique challenges. The criticality of the part means:
- Stringent Quality Requirements: Traceability of materials, adherence to aerospace standards (e.g., AS9100), and rigorous inspection protocols are non-negotiable.
- 材料に関する専門知識: Sourcing and processing superalloys requires specialized knowledge and equipment.
- Reliability Data: Manufacturers must often provide extensive testing and qualification data to prove component reliability.
- カスタマイズの必要性: While some standardization exists, many applications require custom designs, demanding flexible manufacturing partners.
- Wholesale & Production Scaling: For established launch providers or satellite constellations, securing a reliable wholesale supply of qualified igniter housings manufactured consistently is crucial. This requires B2B aerospace manufacturing partners with proven production capabilities and robust quality management systems.
Understanding the precise operational demands – peak temperature, pressure cycle, vibration profile, required lifespan, propellant compatibility – is the first step in designing and manufacturing an effective igniter housing, informing material selection, design geometry, and the choice of manufacturing process.
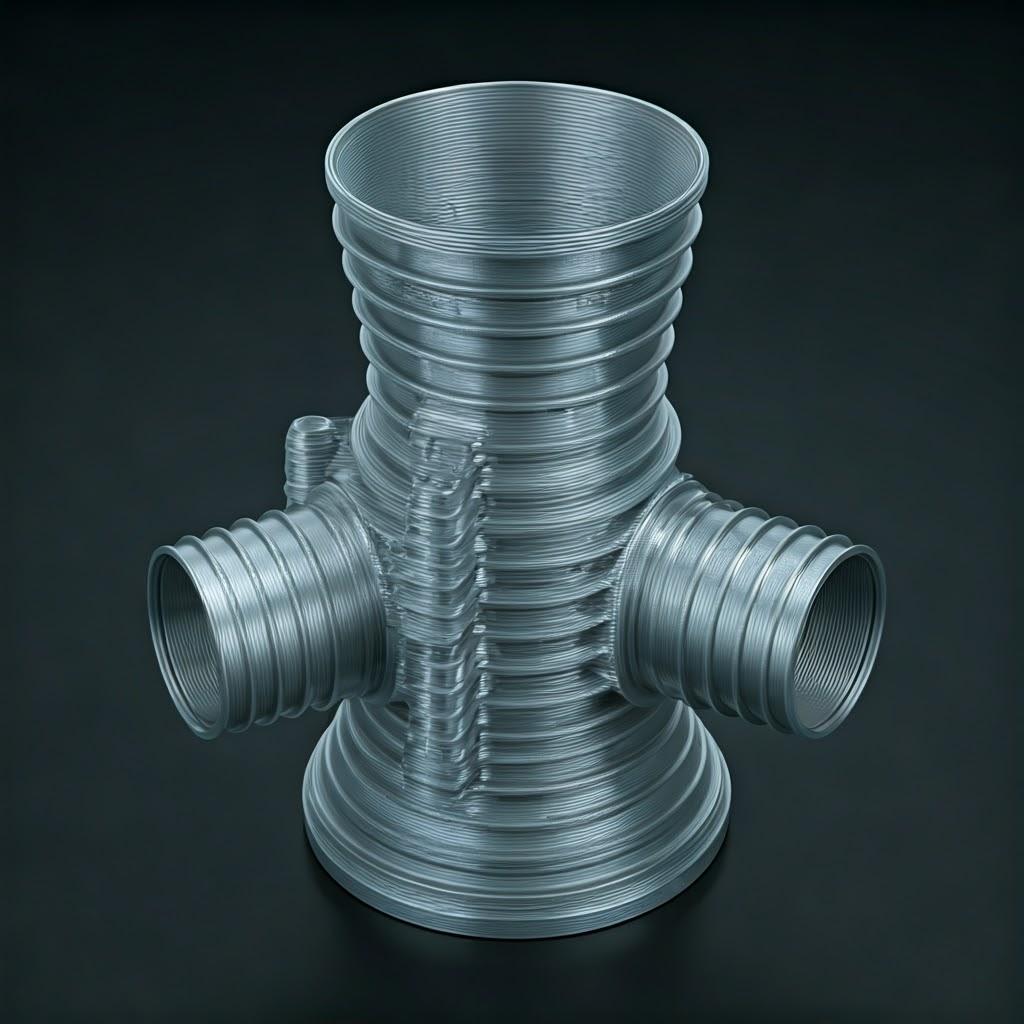
Why Metal Additive Manufacturing for Igniter Housings?
For decades, producing rocket igniter housings involved subtractive manufacturing (machining complex shapes from solid blocks or forgings of superalloys), casting, or intricate fabrication involving welding multiple pieces. While proven, these traditional methods face significant limitations when applied to the demanding requirements of modern igniter housings, especially those made from difficult-to-machine superalloys like IN718 and Haynes 282:
- Geometric Constraints: Machining internal, complex passages for cooling or propellant flow is extremely difficult, time-consuming, or impossible. Casting can struggle with thin walls, intricate details, and potential porosity issues in superalloys. Welding introduces potential weak points and residual stresses.
- 廃棄物: Subtractive manufacturing inherently wastes significant amounts of expensive superalloy material, turning it into machining chips.
- Long Lead Times: Complex machining setups, tooling creation, multi-step fabrication processes, and the inherent difficulty of working with superalloys contribute to lengthy development and production cycles.
- Part Count & Assembly: Traditional approaches often necessitate multiple components being assembled (e.g., bolted or welded together), increasing weight, complexity, potential leak paths, and failure points.
- Design Iteration Cost: Each design change requires significant reprogramming, new tooling, or fixture adjustments, making rapid prototyping and design optimization expensive and slow.
金属積層造形(AM), particularly powder bed fusion techniques like Selective Laser Melting (SLM) / Laser Powder Bed Fusion (LPBF) and Electron Beam Melting (EBM), offers compelling advantages that directly address these limitations:
特徴 | Traditional Manufacturing (Machining/Casting/Fab) | 金属積層造形(AM) | Benefit for Igniter Housings |
---|---|---|---|
幾何学的自由 | Highly constrained, especially internal features | Nearly limitless, enables complex internal channels, organic shapes | Optimized flow paths, integrated cooling, conformal channels, complex mounting features. |
部品の統合 | Often requires multiple parts & assembly | Enables single-piece, complex monolithic structures | Reduced part count, weight, assembly time, potential leak paths, and failure points. |
軽量化 | Limited by machining/casting constraints | Facilitates topology optimization, lattice structures, thin walls | Reduced overall engine mass, improved thrust-to-weight ratio, lower launch costs. |
材料の使用 | High waste (subtractive) / Tooling costs (casting) | Additive, uses only necessary material (+ supports), less waste | Significant cost savings on expensive superalloys like IN718 and Haynes 282. |
リードタイム | Long (tooling, setup, complex machining) | Short for prototypes & complex parts; digital workflow speeds iteration | Faster design validation, quicker development cycles, on-demand production potential. |
パフォーマンス | Limited by manufacturable geometries | Enables performance-driven designs (e.g., conformal cooling) | Improved thermal management, potentially higher efficiency, longer component life. |
Superalloy Handling | Difficult & slow to machine, casting challenges | AM processes are well-suited for layer-wise fusion of superalloys | Efficient processing of high-performance materials essential for extreme environments. |
Export to Sheets
活用することで 金属3Dプリンティング, engineers can design igniter housings that are not merely manufacturable, but truly optimized for function. Imagine internal cooling channels that precisely follow the contours of high-heat zones, or integrated mounting brackets and fluid ports created in a single build process. This level of design integration, facilitated by AM, allows aerospace component suppliers to offer parts that were previously inconceivable. For procurement managers seeking B2B metal printing services, AM provides a pathway to acquiring highly complex, performance-enhancing components, often with competitive lead times compared to traditional routes, especially for low-to-mid volume production runs characteristic of the aerospace industry. The ability to rapidly prototype and test multiple design iterations accelerates innovation cycles, allowing for faster optimization of engine performance and reliability. Furthermore, the layer-by-layer nature of AM allows for fine control over the microstructure of superalloys, potentially leading to tailored material properties within the component itself, although this requires deep process expertise.
Material Focus: IN718 and Haynes 282 Powders for Extreme Environments
The selection of materials for rocket igniter housings is dictated by the extreme conditions they endure: rapid temperature fluctuations often exceeding hundreds of degrees Celsius, high internal pressures during ignition, exposure to corrosive propellant byproducts, and significant mechanical loads from vibration and acceleration. Only a select few materials can reliably withstand this onslaught. Nickel-based superalloys stand out due to their exceptional combination of high-temperature strength, creep resistance, fatigue life, and corrosion resistance. Among these, Inconel 718 (IN718) and Haynes 282 have emerged as leading candidates for additively manufactured aerospace components.
Inconel 718 (IN718 / Alloy 718): The Workhorse Superalloy
IN718 is a precipitation-hardenable nickel-chromium alloy renowned for its excellent mechanical properties at elevated temperatures up to approximately 700°C (1300°F).
- キー・プロパティ
- High tensile, yield, and creep-rupture strength.
- Good fatigue resistance.
- Excellent resistance to oxidation and corrosion in harsh environments.
- Good weldability (important for potential post-processing or integration).
- Relatively good processability via metal AM techniques like LPBF.
- Why it Matters for Igniter Housings: Its high strength ensures structural integrity under pressure and vibration, while its temperature resistance handles the thermal loads during ignition. Its wide acceptance and extensive characterization data in aerospace provide confidence for critical applications. It often represents a good balance between performance and cost (relative to other superalloys).
- AM Considerations: IN718 is one of the most commonly used superalloys in metal AM. Optimized parameters exist, but careful control over the printing and subsequent heat treatment (solution annealing and aging) is crucial to achieve the desired precipitation hardening (gamma prime and gamma double-prime phases) that gives IN718 its strength.
Haynes 282: Superior High-Temperature Capability
Haynes 282 is a newer generation, precipitation-hardenable nickel-based superalloy specifically developed for improved high-temperature performance compared to alloys like IN718 or Waspaloy.
- キー・プロパティ
- Excellent creep strength at temperatures significantly higher than IN718 (up to 930°C / 1700°F).
- Good thermal stability and fatigue resistance.
- Good oxidation resistance.
- Improved fabricability and weldability compared to similar strength alloys like Waspaloy or R-41.
- Good processability via AM, though potentially requiring more specialized parameter sets than IN718.
- Why it Matters for Igniter Housings: For applications involving extremely high temperatures, longer duration burns, or where maximum creep resistance is needed (e.g., advanced engine designs, hypersonic applications), Haynes 282 offers a distinct advantage over IN718. It pushes the operational envelope further.
- AM Considerations: Requires precise thermal management during printing and carefully controlled heat treatment cycles to develop its optimal microstructure (gamma prime precipitates). Its higher cost means it’s typically selected only when IN718’s capabilities are insufficient.
Comparative Properties (Typical Values – Can Vary with Processing & Heat Treatment):
プロパティ | IN718 (Aged) | Haynes 282 (Aged) | Significance for Igniter Housings |
---|---|---|---|
Max Operating Temp (approx.) | ~700°C (~1300°F) | ~930°C (~1700°F) | Determines suitability for thermal load |
Yield Strength (RT) | ~1030 – 1170 MPa | ~800 – 900 MPa | Resistance to deformation under pressure |
Yield Strength (650°C) | ~890 – 1030 MPa | ~700 – 800 MPa | Strength retention at high temperature |
Creep Strength (Stress for 0.2% creep in 1000h @ 760°C) | より低い | ~200 MPa (Significantly Higher) | Resistance to slow deformation under load |
密度 | ~8.19 g/cm³ | ~8.41 g/cm³ | Impacts overall component weight |
耐酸化性 | グッド | 素晴らしい | Resistance to propellant byproducts/heat |
Export to Sheets
The Critical Role of Powder Quality:
Regardless of the alloy chosen, the success of manufacturing igniter housings via AM heavily depends on the quality of the metal powder feedstock. Key powder characteristics directly influence the final part’s density, microstructure, and mechanical properties:
- 真球度: Highly spherical powders flow evenly in the printer, leading to consistent layer deposition and reduced porosity.
- 粒度分布(PSD): An optimized PSD ensures good powder bed density and efficient melting. Fines can cause issues, while overly large particles may not melt completely.
- 流動性: Consistent flow ensures uniform layers, preventing defects. Measured by Hall flow rate or similar methods.
- Purity/Chemistry: Must strictly adhere to aerospace material specifications (e.g., AMS standards). Contaminants can severely degrade mechanical properties. Low oxygen and nitrogen content is crucial.
This is where specialized powder manufacturers like メット3dp play a vital role. Employing advanced production techniques like Vacuum Induction Melting Gas Atomization (VIGA) そして プラズマ回転電極プロセス(PREP), Met3dp produces high-purity, highly spherical superalloy powders (including IN718, Haynes 282, and other advanced alloys like CoCrMo, TiAl, etc.) specifically optimized for AM processes. Their rigorous quality control ensures the powder meets the stringent requirements for demanding applications like rocket igniter housings. Procurement managers seeking wholesale superalloy powder suppliers または B2B partners for end-to-end AM solutions should prioritize suppliers with demonstrated expertise in powder production and characterization, as this forms the foundation of any high-quality additively manufactured component. Explore Met3dp’s extensive 製品範囲 for materials suited to your demanding applications. Sources and related content
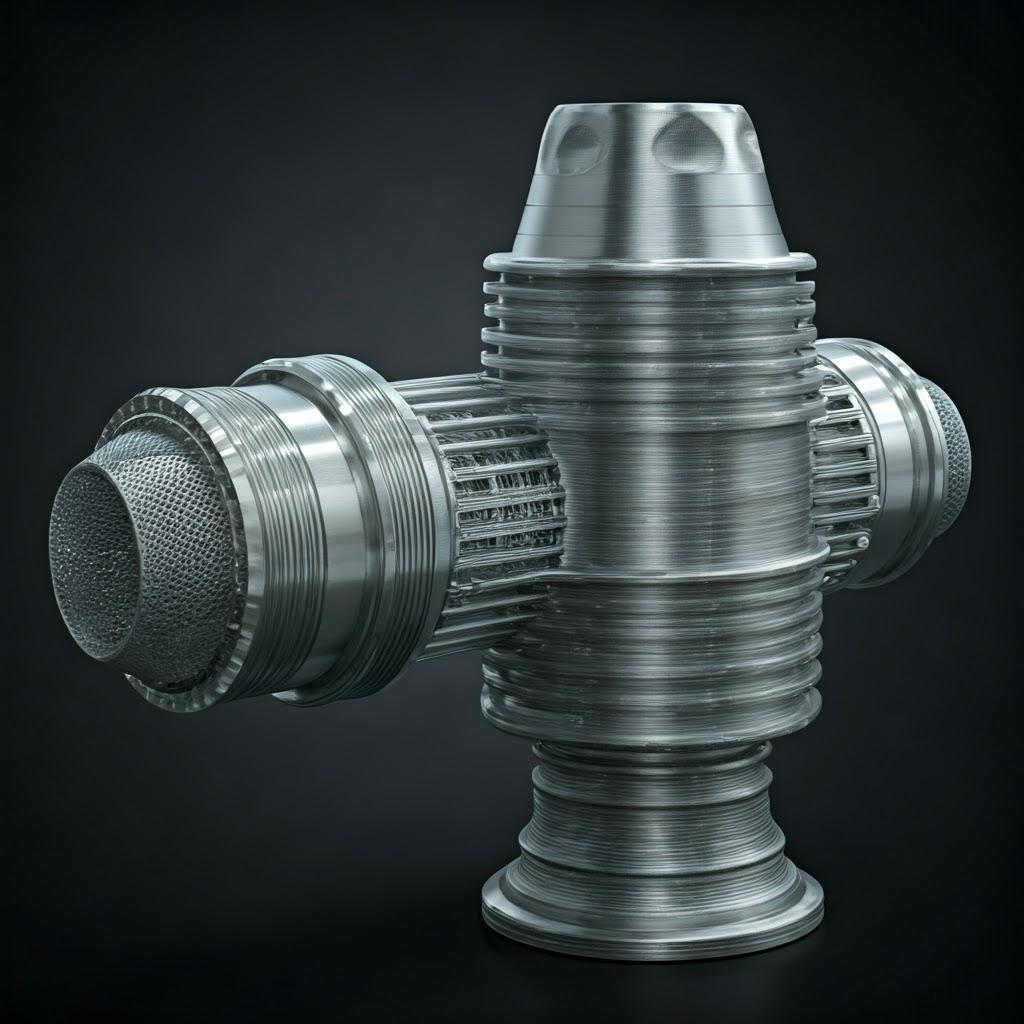
Design for Additive Manufacturing (DfAM): Optimizing Igniter Housings
One of the most profound shifts enabled by metal additive manufacturing is the liberation from the constraints imposed by traditional manufacturing methods. Instead of designing にとって manufacturability (i.e., simplifying designs to make them machinable or castable), AM allows engineers to design for function, prioritizing performance and letting the manufacturing process adapt. This philosophy is encapsulated in 積層造形設計 (DfAM). Applying DfAM principles to rocket igniter housings is not just beneficial; it’s essential for unlocking the full potential of superalloy AM in terms of performance, weight reduction, and reliability.
Shifting the Design Paradigm:
For engineers accustomed to subtractive or casting limitations, DfAM requires a different mindset. It involves leveraging the layer-by-layer construction to create features and complexities that were previously impossible or prohibitively expensive. For igniter housings, this translates into several key strategies:
- Embracing Geometric Complexity:
- Integrated Features: AM allows features like mounting brackets, sensor ports, fluid connectors, and even intricate sealing surfaces to be built directly into the housing structure. This eliminates the need for separate components, fasteners, or welding/brazing, reducing part count, assembly time, weight, and potential failure points (like leaks or stress concentrations at joints).
- Optimized Flow Paths: Internal passages for pyrotechnic gases, torch igniter propellants, or cooling fluids can be designed with smooth, aerodynamic curves and complex cross-sections optimized for flow efficiency and pressure drop minimization, rather than being restricted to straight, drilled holes.
- Strategic Support Structure Management:
- Minimizing Overhangs: While AM allows complex shapes, steeply angled overhangs (typically > 45-60 degrees from vertical, depending on the process and material) require support structures during the build. DfAM involves orienting the part on the build plate and tweaking geometries (e.g., using chamfers instead of sharp horizontal undersides) to minimize the need for supports.
- Self-Supporting Angles: Designing features with angles below the critical threshold allows them to be built without supports, saving material, build time, and post-processing effort.
- Designing for Removal: When supports are unavoidable, they must be designed for easy and clean removal without damaging the part surface. Access for tools must be considered, and contact points should be minimized and placed on non-critical surfaces where possible. Support “witness marks” (small surface artifacts left after removal) should be anticipated.
- Leveraging Internal Channels:
- Conformal Cooling: Perhaps one of AM’s killer applications. Cooling channels can be designed to follow the exact contours of high-heat areas within the igniter housing, providing far more efficient and targeted thermal management than traditionally drilled channels. This can improve component life, allow for higher performance operation, or enable weight savings by reducing the bulk material needed for heat sinking.
- Powder Removal Access: A critical DfAM consideration for internal channels is ensuring that all unfused powder can be removed after printing. This means designing channels with sufficient diameter, smooth bends, and strategically placed entry/exit ports. Dead-end voids must be avoided. Simulation tools can help visualize powder removal.
- Intelligent Lightweighting:
- Topology Optimization: Using specialized software, engineers can define loads, constraints, and design spaces, and the software algorithmically removes material from low-stress areas, resulting in an optimized, often organic-looking structure that meets performance requirements with minimum mass. This is ideal for aerospace components where weight savings are paramount.
- 格子構造: Internal lattice or gyroid structures can replace solid material, providing excellent stiffness-to-weight ratios and potentially aiding in vibration damping or thermal management. These complex internal structures are only feasible via AM.
- Considering AM Process Specifics:
- Wall Thickness & Feature Size: AM processes have minimum printable wall thicknesses and feature resolutions (dependent on laser/electron beam spot size, layer thickness, powder size). Designs must respect these limits.
- 異方性: Material properties in AM parts can sometimes vary slightly depending on the build direction (X, Y vs. Z). While this is becoming less pronounced with modern machines and optimized parameters, it should be considered for highly stressed components. Build orientation should align critical stresses with the strongest build direction if significant anisotropy exists.
- Stress Concentrations: Using fillets and smooth transitions instead of sharp internal corners is even more critical in AM, as sharp corners can be points of stress concentration and potential crack initiation, especially in fatigue-prone applications.
- Designing for Post-Processing:
- Machining Allowances: If critical surfaces require tight tolerances or specific finishes achievable only by machining, extra material (“machining stock” or “oversize”) must be added to those features in the AM design file.
- Inspection Access: Ensure that critical features, especially internal ones, are accessible for NDT methods like CT scanning or potentially borescopic visual inspection.
- 熱処理に関する考慮事項: Design should account for potential (though usually minor) distortion during heat treatment cycles.
Partnering with an experienced AM provider like Met3dp, who offers comprehensive engineering support, is invaluable. Their experts can guide designers through the DfAM process, leveraging deep knowledge of their specific 印刷方法, material behaviors (IN718, Haynes 282), and simulation capabilities to optimize igniter housing designs for printability, performance, and cost-effectiveness. This collaborative approach ensures that the final design truly harnesses the unique advantages offered by additive manufacturing, moving beyond simply replicating traditionally manufactured designs and creating genuinely superior components. Engaging B2B design engineering services specializing in AM can significantly shorten the learning curve and accelerate the adoption of optimized designs.
Achieving Precision: Tolerance, Surface Finish, and Dimensional Accuracy in AM Igniter Housings
While metal AM offers incredible geometric freedom, it’s crucial for engineers and procurement managers to have realistic expectations regarding the precision achievable directly from the printer (the “as-built” state). Achieving the tight tolerances and specific surface finishes often required for aerospace components like igniter housings typically involves a combination of controlled AM processing and targeted post-processing steps.
Understanding Tolerances in Metal AM:
- General Achievability: For robust metal AM processes like Laser Powder Bed Fusion (LPBF) using superalloys, typical achievable dimensional tolerances are often in the range of ±0.1 mm to ±0.2 mm (±0.004″ to ±0.008″) for smaller features, or ±0.1% to ±0.2% of the dimension for larger features. Electron Beam Melting (EBM) might have slightly looser general tolerances due to its higher processing temperatures but excels in reducing residual stress.
- Influencing Factors: Actual tolerances depend heavily on:
- Part size and geometry (larger parts, complex shapes can see more variation).
- Build orientation (thermal expansion/contraction effects can vary).
- Material properties (superalloys’ thermal characteristics).
- Machine calibration and process parameter stability.
- Support strategy (supports can influence local accuracy).
- GD&T for AM: Geometric Dimensioning and Tolerancing (GD&T) is essential for clearly defining critical tolerances on AM part drawings. It allows specifying allowable variations in form, orientation, location, and profile for key features (e.g., mounting flanges, sealing surfaces, port locations) independent of just linear dimensions. Applying GD&T effectively requires understanding the specific capabilities and potential variations inherent in the AM process.
Surface Finish (Roughness): As-Built vs. Finished:
- As-Built Surface Roughness (Ra): The surface finish of as-built metal AM parts is inherently rougher than machined surfaces due to the layer-wise fusion of powder particles. Typical Ra values for LPBF superalloy parts range from 5 µm to 20 µm (approx. 200 µin to 800 µin). EBM parts are generally rougher.
- Factors Affecting Ra:
- 層の厚さ: Thinner layers generally produce smoother surfaces but increase build time.
- Powder Particle Size Distribution (PSD): Finer powders can lead to smoother finishes.
- Beam Parameters: Laser/electron beam power, speed, and focus influence melt pool stability and surface outcome.
- Orientation: “Up-skin” surfaces (facing upwards during build) are typically smoother than “down-skin” surfaces (undersides relying on supports or self-support). Vertical walls often have the best finish. Support contact points also leave witness marks.
- When Finishing is Required: While the as-built finish might be acceptable for non-critical external surfaces or some internal structures, critical interfaces usually require secondary finishing:
- Sealing Surfaces: Require very smooth finishes (often <1 µm Ra) to ensure proper sealing.
- Mating Flanges: Need controlled flatness and smoothness for proper assembly.
- High-Performance Flow Paths: Smoother surfaces reduce friction and turbulence.
- Fatigue-Critical Areas: Surface roughness can act as initiation sites for fatigue cracks; smoother finishes improve fatigue life.
Achieving Dimensional Accuracy and Verification:
- Accuracy vs. Tolerance: Accuracy refers to how close the average measured dimension is to the nominal design value, while tolerance is the allowed range of variation. High accuracy requires well-calibrated machines and tightly controlled processes.
- プロセス制御: Reputable AM service providers like Met3dp utilize printers known for their industry-leading accuracy and reliability. This is underpinned by rigorous machine calibration routines, environmental controls (temperature, humidity, oxygen levels), real-time process monitoring (e.g., melt pool monitoring), and validated parameter sets for specific materials like IN718 and Haynes 282.
- Metrology and Inspection: Verifying the dimensional accuracy of complex AM parts, especially those with internal features like igniter housings, is critical. Common techniques include:
- Coordinate Measuring Machines (CMM): Provide high-accuracy point measurements on accessible features.
- Structured Light / Laser 3D Scanning: Capture detailed geometric data of the entire external surface, allowing comparison to the original CAD model (Color mapping deviations). Essential for complex shapes.
- Industrial Computed Tomography (CT) Scanning: The gold standard for non-destructively measuring internal features and verifying wall thicknesses, channel dimensions, and detecting internal defects/porosity. Crucial for qualifying critical aerospace parts.
Meeting Aerospace Standards:
Achieving the necessary precision requires a holistic approach: DfAM principles to minimize inherent process variations, tightly controlled AM processing on high-quality equipment, appropriate post-processing, and rigorous metrology. Precision manufacturing suppliers serving the aerospace sector must demonstrate robust quality management systems (QMS) to ensure consistency and traceability throughout this entire workflow. Procurement managers seeking B2B metal printing services should inquire specifically about the provider’s tolerance capabilities, available surface finishing options, metrology equipment, and quality control procedures for ensuring dimensional conformance to drawing specifications.
Table: Common Surface Finishing Techniques for AM Superalloys
テクニック | 説明 | Typical Achievable Ra (µm) | 長所 | 短所 |
---|---|---|---|---|
Bead Blasting | Propelling abrasive media (glass beads, ceramic) onto the surface | 3 – 10 | Uniform matte finish, removes loose powder, relatively fast/cheap | Line-of-sight limited, minimal material removal, can embed media |
Tumbling / Vibratory Finishing | Parts agitated with media in a drum/bowl | 1 – 5 | Smooths edges, good for batches, can reach some recessed areas | Slow, can damage delicate features, media selection critical |
CNC加工 | Cutting tools remove material to achieve precise dimensions & finish | < 0.8 (or better) | High precision, tight tolerances, excellent finish, versatile | Line-of-sight, requires fixtures, material removal, cost/time intensive |
研磨 | Manual or automated abrasive polishing | < 0.4 (mirror possible) | Very smooth finish, good for specific areas | Labor-intensive (manual), geometry constraints (automated) |
Abrasive Flow Machining (AFM) | Abrasive putty forced through internal channels/external features | 0.5 – 3 | Excellent for internal channels & complex shapes, automated | Specialized equipment, media cost, can alter dimensions slightly |
Electrochemical Polishing (ECP) | Electrochemical dissolution removes material peaks | 0.2 – 2 | Very smooth, stress-free finish, good for complex shapes, deburrs | Requires conductive material, electrolyte handling, material removal |
Export to Sheets
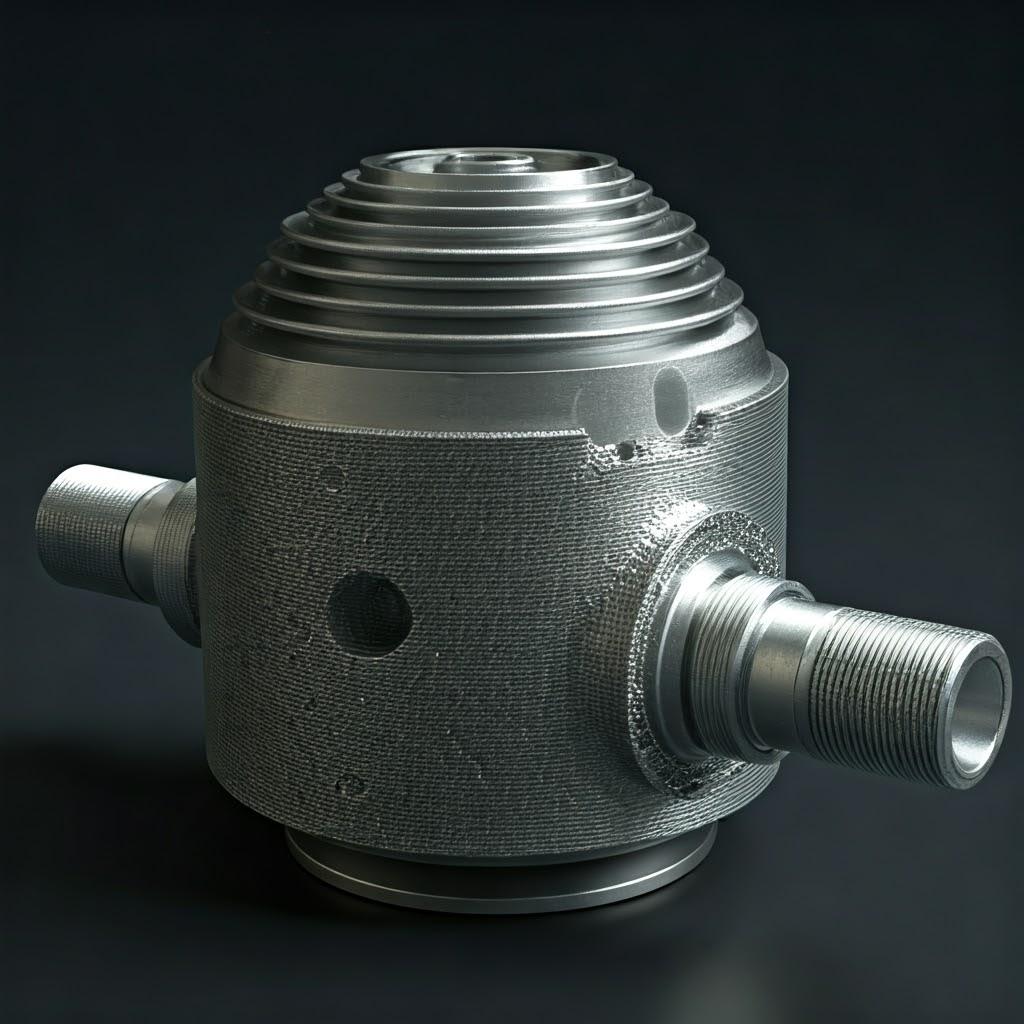
Beyond the Print: Essential Post-Processing for AM Igniter Housings
Creating a dimensionally accurate rocket igniter housing using IN718 or Haynes 282 via metal AM is a significant achievement, but the journey from raw print to flight-ready component is far from over. A series of critical post-processing steps are nearly always required to relieve internal stresses, achieve the desired material properties, meet final tolerance and surface finish requirements, and ensure the part is free from defects. Omitting or improperly executing these steps can severely compromise the performance and reliability of the final component.
The Necessary Sequence for Superalloy AM Parts:
- Stress Relief (SR):
- Why: The rapid heating and cooling cycles inherent in LPBF/EBM create significant residual stresses within the printed part and between the part and the build plate. These stresses can cause distortion or even cracking when the part is removed from the plate.
- How: Typically performed while the part is still attached to the build plate in a controlled atmosphere furnace (vacuum or inert gas like Argon). The cycle involves heating to a specific temperature below the aging temperature (e.g., for IN718, might be around 950-1050°C, but consult specific procedures), holding for a defined time, and cooling slowly. This allows stresses to relax without significantly altering the microstructure yet.
- ビルドプレートからの取り外し:
- How: Once stress-relieved, the part (or multiple parts on the plate) is separated from the build plate. Common methods include Wire Electrical Discharge Machining (Wire EDM) for a clean cut, or using a band saw. Care must be taken not to damage the parts.
- 支持構造の撤去:
- Why: Supports are necessary evils during the build but must be removed completely.
- How: This can be a labor-intensive process. Supports may be manually broken off (if designed with small contact points), machined away, ground off, or removed using EDM. Access to internal supports can be particularly challenging and requires careful DfAM planning.
- Heat Treatment (Solution Annealing & Aging):
- Why: This is arguably the most critical step for developing the required mechanical properties (strength, hardness, creep resistance) in precipitation-hardenable superalloys like IN718 and Haynes 282. The as-built microstructure is generally not optimal.
- How: This involves specific, multi-step thermal cycles performed in a highly controlled vacuum or inert atmosphere furnace to prevent oxidation.
- ソリューション・アニーリング: Heating to a high temperature (e.g., ~980°C for IN718, higher for Haynes 282) dissolves certain elements into the matrix and homogenizes the structure.
- Aging (Precipitation Hardening): Subsequent lower temperature holds (e.g., a two-step process around 720°C and 620°C for IN718) cause the formation of strengthening precipitates (Gamma Prime γ’ and Gamma Double Prime γ” in IN718; primarily γ’ in Haynes 282).
- Control is Key: Precise temperature control, ramp rates, hold times, and cooling rates defined in aerospace specifications (e.g., AMS standards for heat treatment IN718) are crucial. Incorrect heat treatment leads to suboptimal properties. Potential for minor distortion must be managed.
- 熱間静水圧プレス(HIP):
- Why: Although AM processes aim for full density (>99.5%), microscopic internal pores (gas porosity or lack-of-fusion voids) can sometimes remain. These act as stress concentrators, degrading fatigue life and fracture toughness. HIP uses high temperature (below solution annealing temp) and high isostatic pressure (typically 100-200 MPa using Argon gas) to diffusionally bond and close these internal voids.
- メリット Significantly improves fatigue properties, increases ductility and fracture toughness, enhances inspectability (eliminates spurious NDT indications from pores), and ensures maximum density. Often mandated for critical 航空宇宙部品.
- Timing: HIP is typically performed after stress relief but before final heat treatment (solution & age), although different sequences exist.
- 機械加工:
- Why: To achieve final tolerances on critical interfaces (e.g., flanges, sealing grooves, threaded holes) that are tighter than as-built AM capabilities, and to obtain very smooth surface finishes where required.
- How: Standard CNC machining techniques (milling, turning, drilling, grinding) are used. However, machining heat-treated superalloys is challenging due to their high strength and work-hardening tendencies. Requires appropriate cutting tools, speeds, feeds, and robust part fixturing. Machining stock must have been included in the DfAM phase.
- 表面仕上げ:
- Why: To achieve specific Ra values, improve flow characteristics in channels, remove support witness marks, or prepare for coatings.
- How: As detailed previously (blasting, polishing, AFM, ECP, etc.), selected based on requirements for specific surfaces (external vs. internal). Finishing internal channels of complex igniter housings remains a significant challenge often requiring specialized techniques like AFM or ECP.
- Cleaning and Non-Destructive Testing (NDT):
- Why: Ensure all residual powder (especially from internal channels), machining fluids, and contaminants are removed. Verify the part’s integrity and confirm it meets all specifications before delivery.
- How:
- クリーニング: Ultrasonic cleaning, solvent flushing, specialized procedures for internal channels.
- NDT: A multi-pronged approach is common for critical parts:
- Visual Inspection (VT): Surface defects, completeness.
- Dimensional Inspection: CMM, 3D Scanning (as discussed).
- CT Scanning: Essential for verifying internal geometry, wall thickness, and detecting internal voids or inclusions non-destructively.
- Fluorescent Penetrant Inspection (FPI): Detects surface-breaking cracks or defects.
- (Sometimes) Ultrasonic Testing (UT) or Eddy Current Testing (ECT): Depending on geometry and specific requirements.
Successfully navigating this complex post-processing workflow requires significant expertise and specialized equipment. Companies like Met3dp, offering comprehensive metal AM solutions, often manage this entire chain, either through in-house capabilities or qualified partners, providing customers with a single point of contact and ensuring seamless integration from design to finished, qualified part. Engaging B2B finishing services specializing in metal AM parts is crucial for companies without these extensive in-house capabilities.
Overcoming Hurdles: Common Challenges in Superalloy AM for Igniter Housings & Solutions
Additive manufacturing of superalloys like IN718 and Haynes 282 for demanding applications such as rocket igniter housings is a powerful capability, but it’s not without its challenges. Achieving consistent, high-quality results requires a deep understanding of the materials, the AM process physics, and potential pitfalls. Proactively addressing these challenges is key to successfully implementing AM for critical aerospace components.
Key Challenges and Mitigation Strategies:
- Residual Stress & Distortion:
- チャレンジ: The rapid, localized heating and cooling during layer-wise fusion induce significant thermal gradients, leading to internal stresses. These stresses can cause part warpage during the build, distortion after removal from the build plate, or even cracking.
- Solutions:
- Process Simulation: Using software to predict thermal gradients and stress accumulation allows for optimization of build orientation and support structures before 印刷
- Optimized Build Strategy: Careful selection of build orientation, potentially angling the part, can mitigate stress. Using appropriate scan strategies (e.g., island scanning, layer rotation) helps distribute heat more evenly.
- Intelligent Support Structures: Supports act not only to hold overhangs but also as heat sinks and anchors against warping. Simulation helps optimize their placement and type.
- 熱管理: Maintaining a consistently elevated temperature in the build chamber (especially crucial in EBM, but also beneficial in LPBF) reduces thermal gradients.
- Mandatory Stress Relief: Performing the on-plate stress relief heat treatment immediately after printing is non-negotiable for superalloys.
- Cracking (Solidification & Liquation):
- チャレンジ: Superalloys, particularly complex chemistries, can be susceptible to cracking during solidification (hot tearing) or due to the liquation (melting) of lower-melting-point phases in the heat-affected zone of previously solidified layers.
- Solutions:
- Alloy Selection & Powder Quality: IN718 generally exhibits good AM processability. Haynes 282 is also manageable but may require more dialed-in parameters. Using high-purity powder with controlled chemistry minimizes detrimental phases.
- Parameter Optimization: Fine-tuning laser/electron beam power, scan speed, and layer thickness (energy density) is critical to control the melt pool size and cooling rate, minimizing cracking susceptibility.
- Pre-heating: Elevated build chamber temperatures reduce thermal shock.
- Post-Build Heat Treatment: Appropriate stress relief and HIP cycles can help heal or mitigate micro-cracking.
- Porosity (Lack of Fusion, Keyhole, Gas):
- チャレンジ: Internal voids can compromise mechanical properties, especially fatigue life. Porosity can arise from:
- Lack of Fusion (LoF): Insufficient energy density fails to completely melt powder particles or fuse adjacent tracks/layers.
- Keyhole Porosity: Excessive energy density creates an unstable, deep melt pool that can collapse, trapping vapor/gas.
- Gas Porosity: Gas trapped within powder particles or introduced via contaminated shield gas gets entrapped during solidification.
- Solutions:
- Rigorous Parameter Development: Extensive testing (coupon level) to define robust process windows with optimal energy density.
- High-Quality Powder: Using powder with high sphericity, controlled PSD, good flowability, and low internal gas content (a strength of Met3dp’s VIGA/PREP powders) is paramount. Proper powder handling and storage are essential to prevent moisture/contamination.
- Process Monitoring & Control: Ensuring proper shield gas flow and purity, maintaining vacuum levels (EBM), and potentially using real-time melt pool monitoring systems.
- 熱間静水圧プレス(HIP): Highly effective at closing LoF and gas porosity, significantly improving density and mechanical integrity. Often considered mandatory for critical parts.
- チャレンジ: Internal voids can compromise mechanical properties, especially fatigue life. Porosity can arise from:
- Powder Removal from Internal Channels:
- チャレンジ: Complex internal geometries, like cooling channels or propellant passages in igniter housings, can make removing all unfused powder extremely difficult. Trapped powder can sinter during heat treatment, blocking channels or becoming loose contamination later.
- Solutions:
- DfAM for Depowdering: Designing channels with sufficient diameter, smooth bends, no dead ends, and strategically placed access/drain holes.
- ビルド方向: Orienting the part to facilitate powder drainage via gravity during the build and depowdering process.
- Specialized Equipment: Using vibration tables, controlled gas blow-outs, or ultrasonic cleaning systems designed for powder removal.
- Inspection: CT scanning is often the only way to definitively verify complete powder removal from intricate internal networks.
- Microstructure and Mechanical Property Control:
- チャレンジ: Achieving the specific, homogenous microstructure (grain size, phase distribution, precipitate morphology) required by aerospace specifications, and ensuring consistent mechanical properties across the part and from build-to-build. The thermal history of AM parts is complex and location-dependent.
- Solutions:
- Validated Processes: Using thoroughly developed and validated process parameters and heat treatment cycles specific to the alloy and machine.
- Homogenization Treatments: Solution annealing steps in heat treatment help homogenize the microstructure.
- 厳格な品質管理: Extensive mechanical testing (tensile, fatigue, creep) on build witness coupons processed alongside the parts, coupled with microstructural analysis, to verify properties meet requirements. Statistical process control (SPC) helps ensure repeatability.
- Scalability and Consistency:
- チャレンジ: Transitioning from prototypes to serial production while maintaining consistent quality across multiple builds, potentially on different machines.
- Solutions:
- Robust Quality Management System (QMS): Implementing AS9100 or equivalent QMS covering all aspects from powder handling to final inspection.
- Machine Qualification & Calibration: Ensuring all machines used for production are properly qualified and regularly calibrated.
- Standardized Procedures: Using identical, validated process parameters and procedures across all builds.
- Traceability: Meticulous tracking of powder batches, build parameters, post-processing steps, and inspection results for each part.
Successfully tackling these challenges requires a combination of advanced technology, material science expertise, process control discipline, and rigorous quality assurance. Partnering with a knowledgeable AM process optimization supplier like Met3dp, who possesses not only state-of-the-art equipment (accurate printers, advanced powder production) but also the deep engineering know-how to navigate these complexities, significantly de-risks the adoption of AM for critical components like rocket igniter housings. Their experience helps aerospace AM projects move from concept to qualified hardware more efficiently and reliably.
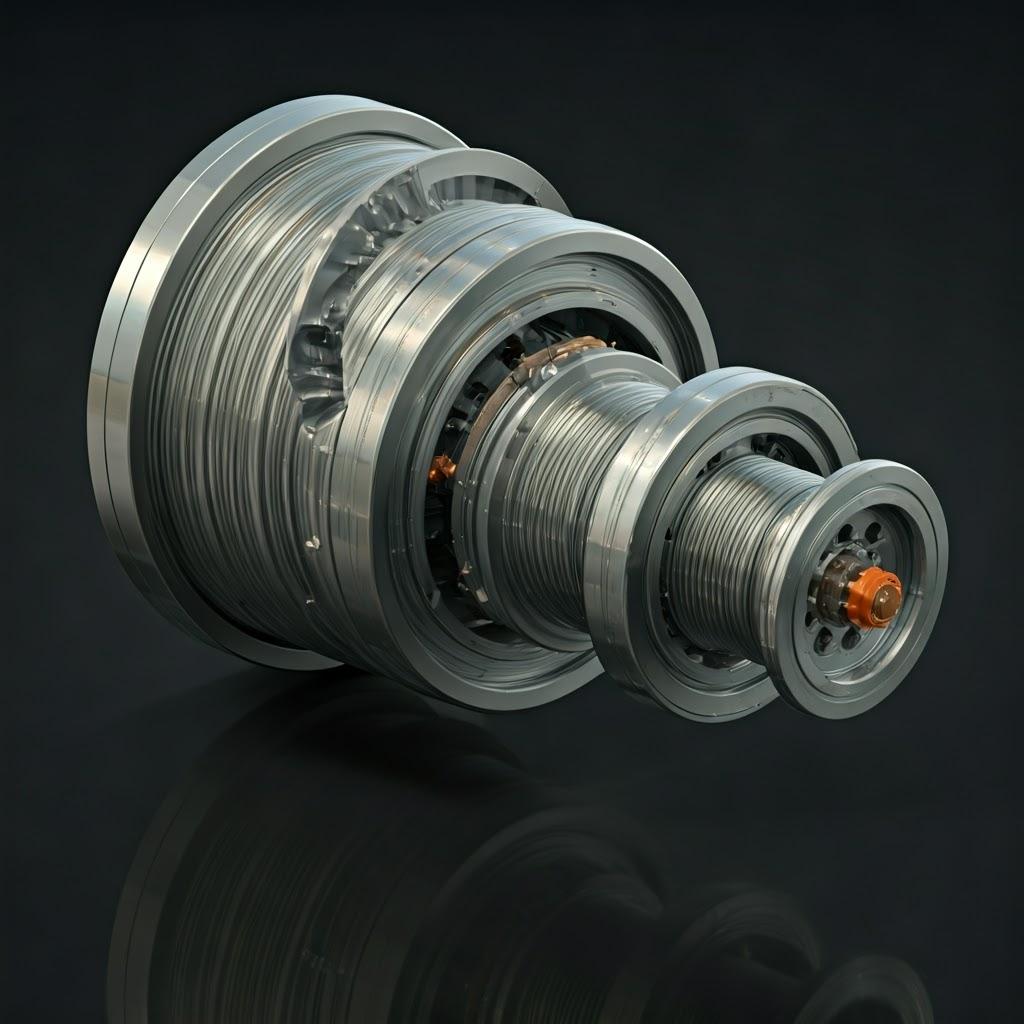
Selecting Your Partner: How to Choose the Right Metal AM Service Provider
The decision to incorporate additively manufactured superalloy components like rocket igniter housings into critical flight hardware is significant. Equally significant is the choice of your additive manufacturing partner. This is not merely a transactional purchase; it’s the formation of a technical partnership where trust, expertise, and proven quality systems are paramount. Selecting the right metal 3D printing service provider goes far beyond comparing quotes; it involves a rigorous evaluation of capabilities, certifications, experience, and quality commitment, especially when dealing with the demanding standards of the aerospace industry. An unsuitable supplier can lead to project delays, budget overruns, subpar components, and potentially catastrophic failures.
Key Criteria for Evaluating Aerospace AM Suppliers:
When sourcing safety-critical parts like igniter housings made from IN718 or Haynes 282, your evaluation process should be thorough. Consider these essential factors:
- Aerospace Certifications & Quality Management System (QMS):
- AS9100: This is the gold standard QMS for the Aviation, Space, and Defense industries. Certification to AS9100 demonstrates a provider’s commitment to rigorous quality processes, traceability, risk management, and continuous improvement tailored to aerospace needs. Non-negotiable for most flight hardware.
- ISO 9001: A foundational QMS certification, indicating documented processes and quality control. Necessary, but AS9100 provides aerospace-specific rigor.
- Nadcap Accreditation: While AS9100 covers the overall system, Nadcap provides specific accreditation for special processes like heat treatment, non-destructive testing (NDT), materials testing, and welding. Suppliers holding relevant Nadcap accreditations demonstrate exceptional proficiency in these critical areas.
- Action: Always request copies of current certifications and audit their scope to ensure they cover the relevant processes (AM, heat treat, NDT).
- Demonstrated Expertise with Superalloys & Aerospace:
- Material Specificity: Look for deep experience specifically with the required superalloys (IN718, Haynes 282). Ask about their parameter development process, material characterization data, and typical mechanical properties achieved.
- Application Experience: Have they produced similar aerospace components before? Can they share (non-proprietary) case studies or examples demonstrating their understanding of aerospace requirements (e.g., tolerance, finish, NDT needs)?
- Years in Operation & Team Expertise: A long track record and experienced engineering team often correlate with process maturity and problem-solving capabilities. Met3dp, for instance, leverages decades of collective expertise in metal additive manufacturing. Learn more about their background on their 会社概要 ページ。
- Equipment, Technology & Capacity:
- Machine Fleet: Do they operate state-of-the-art LPBF or EBM machines suitable for reactive superalloys? Are the machines well-maintained and calibrated? Met3dp utilizes printers delivering industry-leading print volume, accuracy, and reliability.
- ビルド・ボリューム: Ensure their machines can accommodate the size of your igniter housing.
- Capacity & Redundancy: Do they have sufficient machine capacity to meet your prototype and potential production needs without excessive queue times? Do they have multiple machines for redundancy?
- Material Capabilities, Control & Traceability:
- Powder Sourcing & Quality: Do they produce their own powder (like Met3dp’s advanced gas atomization and PREP systems) or source it from qualified suppliers? How do they verify incoming powder quality (chemistry, PSD, morphology, flowability)?
- Powder Handling & Management: Strict procedures are needed for handling expensive and sensitive superalloy powders to prevent contamination and ensure traceability (batch tracking, recycling protocols).
- Full Traceability: Demand end-to-end traceability from the specific powder batch used, through build parameters, machine logs, post-processing records, and final inspection data, all linked to the unique serial number of your part.
- Integrated Post-Processing Capabilities:
- Workflow Management: Does the provider offer a complete, managed solution including stress relief, heat treatment, HIP, support removal, CNC machining, surface finishing, and NDT? Managing this complex chain through a single point of contact simplifies logistics and accountability.
- Subcontractor Management: If post-processing steps are outsourced, how does the primary AM provider qualify, audit, and manage these subcontractors to ensure compliance with aerospace standards?
- Engineering & DfAM Support:
- Collaborative Partnership: Can their engineers work with your team to optimize the design for additive manufacturing (DfAM), advise on material selection, simulate the build process, and develop optimal support strategies? Access to skilled AM application engineers is crucial for leveraging the technology effectively.
- Robust Metrology & NDT Capabilities:
- Inspection Equipment: Do they possess the necessary equipment (CMM, 3D scanners, CT scanners, FPI lines, etc.) and trained personnel to perform the required levels of inspection for critical aerospace parts?
- Reporting: Ensure they can provide comprehensive inspection reports documenting compliance with all drawing specifications and NDT requirements.
- Communication, Project Management & Scalability:
- Responsiveness: Evaluate their responsiveness during the quoting process and technical discussions.
- Project Management: Do they assign a dedicated point of contact? How do they communicate progress and handle potential issues?
- スケーラビリティ: Discuss their ability and processes for scaling from prototype quantities to potential low-rate initial production or series production if required by your program.
正しい選択 B2B additive manufacturing service provider is an investment in quality and reliability. Conducting thorough due diligence using these criteria will help ensure you partner with a supplier capable of meeting the stringent demands of manufacturing flight-qualified rocket igniter housings. Look for aerospace AM supplier evaluation checklists and conduct site audits if possible to verify capabilities firsthand. Qualifying wholesale 3D printing partners for aerospace requires this level of scrutiny to mitigate risks effectively.
Understanding the Investment: Cost Factors and Lead Times for AM Igniter Housings
Additive manufacturing offers tremendous technical advantages for components like rocket igniter housings, but understanding the associated costs and lead times is crucial for project planning and budgeting. Unlike mass-produced items, the metal 3D printing cost for complex, high-performance parts is influenced by a multitude of interacting factors. Similarly, additive manufacturing lead times involve more than just the print duration itself.
Breaking Down the Cost Drivers:
The final price of an AM superalloy igniter housing is typically composed of several key elements:
- 材料費:
- Powder Price: Nickel-based superalloys like IN718 and Haynes 282 are inherently expensive raw materials compared to common steels or aluminum alloys. Haynes 282 generally carries a premium over IN718 due to its composition and performance.
- Volume & Supports: Cost is driven by the volume of the final part plus the volume of material used for support structures (which becomes scrap or requires recycling). Efficient DfAM to minimize volume and supports directly impacts cost.
- Powder Quality & Sourcing: High-quality, aerospace-grade powder with tight specifications commands a higher price but is essential for performance. Providers producing powder in-house (like Met3dp) may have better cost control and quality assurance.
- Recycling Strategy: The provider’s strategy for recycling unfused powder impacts overall material efficiency and cost.
- Machine Time (Amortization & Operation):
- Build Duration: This is often the largest cost component. It depends on:
- Part Volume: Larger parts take longer.
- Part Height: Taller parts require more layers, increasing time.
- 複雑さ: Intricate features require more complex scanning paths by the laser/electron beam.
- Nesting Density: Printing multiple parts in a single build (nesting) improves machine utilization and reduces per-part cost, but requires careful planning.
- Machine Hourly Rate: Reflects the capital investment in expensive AM equipment, maintenance, facilities, energy consumption, and specialized operational software. Rates vary based on machine type and provider.
- Build Duration: This is often the largest cost component. It depends on:
- 人件費:
- Skilled Operators: Significant human effort is involved in build preparation (file setup, powder loading), machine monitoring, part removal, powder handling/sieving, extensive support removal (often manual), detailed post-processing steps, and rigorous inspection. Highly skilled technicians and engineers command higher labor rates.
- Post-Processing Complexity:
- Essential Steps: Stress relief, heat treatment (long furnace cycles in controlled atmospheres), and potentially HIP are standard for superalloys and add significant cost due to equipment time, energy, and specialized environments (vacuum, inert gas).
- Finishing Requirements: CNC machining for tight tolerances, surface polishing, or specialized internal channel finishing (AFM, ECP) add costs based on time and complexity.
- NDT Requirements: Extensive NDT (especially CT scanning) requires expensive equipment and expert interpretation, adding to the overall cost.
- 影響: Post-processing can easily account for 30% to 60% or even more of the total cost for a complex, highly specified aerospace part.
- Non-Recurring Engineering (NRE):
- Initial Setup: For new designs, NRE costs cover DfAM consultation, build simulation and optimization, development of custom support strategies, potential process parameter adjustments, and initial qualification/testing activities. This is typically amortized over the first batch of parts.
- Quality Assurance & Certification:
- Overhead: Maintaining certifications like AS9100, performing regular calibrations, developing and maintaining documentation, conducting witness coupon testing, and performing final inspections all contribute to overhead costs factored into the part price.
Estimating Lead Times:
Lead time is the total duration from order placement to part delivery and is similarly multi-faceted:
- Pre-Processing (Days): Final DfAM checks, build file preparation, simulation, scheduling, and machine queuing time (can vary significantly based on demand).
- Build Time (Days to Weeks): The actual printing process, highly dependent on part size, complexity, and nesting. Large or complex igniter housings can take several days to print.
- Post-Processing (Weeks): This often dominates the lead time. Multiple furnace cycles (SR, Heat Treat, HIP) each take hours to days including heating/cooling. Machining setup and run times add days. NDT and inspection add further time. Logistics between different processing steps (especially if outsourced) add buffer time.
- Total Lead Time: For prototype AM superalloy igniter housings, expect lead times ranging from several weeks to a couple of months. For qualified production batches, similar or slightly optimized lead times are typical, heavily influenced by the extent of post-processing and testing required.
Cost Optimization & Value Proposition:
While the per-part cost of AM superalloys might seem high compared to traditional methods for simple parts, the value proposition often lies in:
- Reduced Assembly Costs: Part consolidation eliminates downstream assembly labor and complexity.
- Reduced Weight: Lower mass translates to launch cost savings or increased payload capacity.
- パフォーマンスの向上: Enhanced designs (e.g., conformal cooling) can lead to better efficiency or longer component life.
- Shorter Development Cycles: Rapid prototyping accelerates design validation.
- Reduced Tooling Costs: AM avoids the high NRE of casting molds or forging dies, making it economical for low-to-mid volumes.
Obtaining accurate wholesale 3D printing quotes requires providing detailed drawings (including GD&T), specifications (material, tolerances, finish, NDT), and expected quantities. Experienced providers like Met3dp can offer detailed B2B manufacturing cost estimations and work collaboratively to optimize designs for both performance and manufacturability, balancing cost, lead time, and mission requirements.
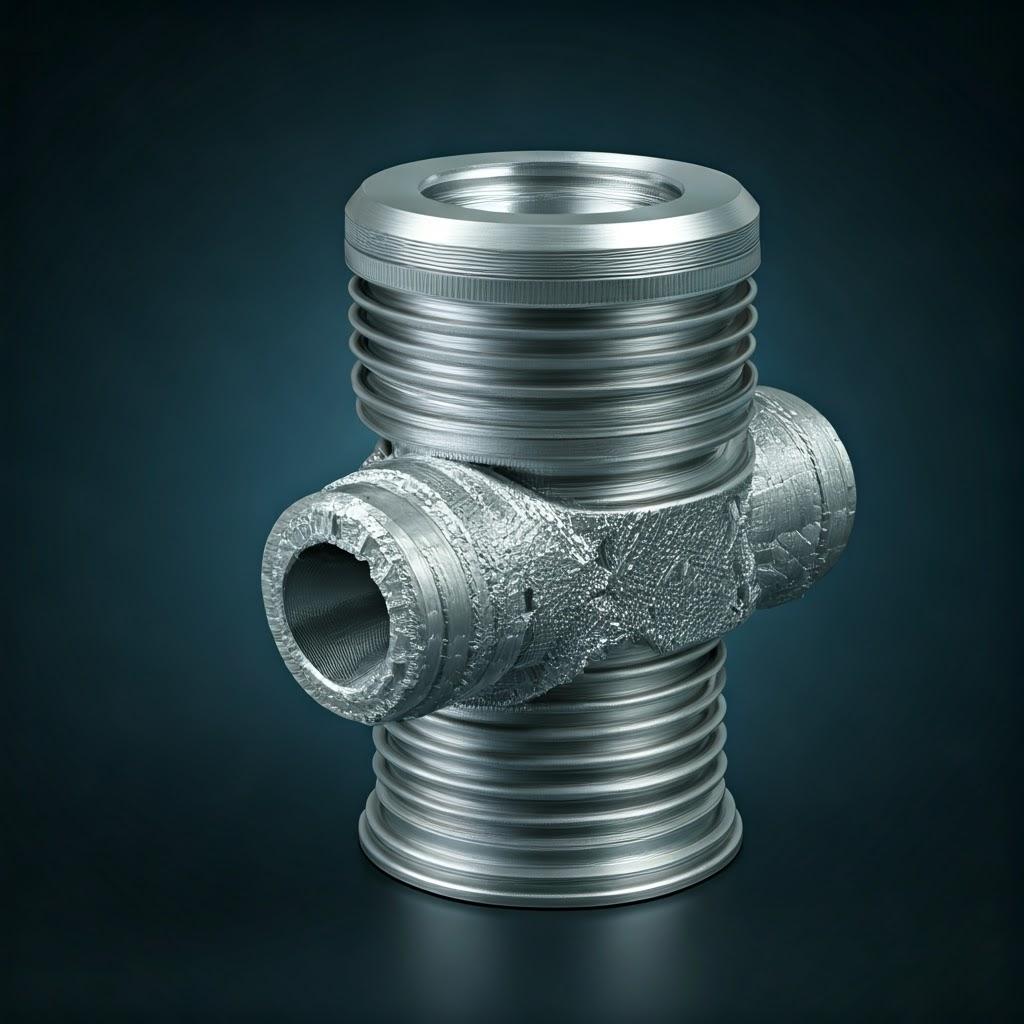
Frequently Asked Questions (FAQ) about AM Rocket Igniter Housings
Here are answers to some common questions regarding the use of additive manufacturing for rocket igniter housings using IN718 and Haynes 282:
Q1: How does the mechanical performance (strength, fatigue, creep) of AM IN718/Haynes 282 compare to wrought or cast versions after proper post-processing?
- A: When produced using optimized and validated process parameters, followed by appropriate post-processing including stress relief, Hot Isostatic Pressing (HIP), and specific solution & aging heat treatments, the mechanical properties of AM IN718 and Haynes 282 can be highly competitive with, and sometimes even exceed, those of their wrought or cast counterparts. AM often results in a finer grain structure, which can enhance tensile strength. HIP significantly improves fatigue life by closing internal porosity. Creep properties are heavily dependent on correct heat treatment to achieve the desired precipitate structure. Rigorous process control and testing against established material specifications (e.g., AMS standards) are essential to guarantee performance equivalence or superiority for critical applications.
Q2: Can AM igniter housings meet the stringent cleanliness and contamination control requirements for rocket propulsion systems?
- A: Yes, but it requires meticulous attention throughout the process. Key considerations include:
- Design (DfAM): Designing internal channels to allow for complete powder removal (no dead ends, sufficient diameter, smooth paths, access ports).
- Powder Removal: Utilizing specialized techniques (vibration, controlled gas flow, potentially solvents if compatible) post-print.
- Cleaning Protocols: Implementing multi-stage cleaning processes validated for effectiveness.
- Verification: Often using methods like CT scanning or borescope inspection to confirm internal cleanliness.
- ハンドリング Maintaining cleanliness throughout all subsequent post-processing and handling steps. With careful planning and execution by an experienced provider, AM parts can meet typical aerospace cleanliness levels (e.g., defined by oxygen compatibility requirements).
Q3: What is the typical production lead time for a batch of qualified AM igniter housings (e.g., 10-20 units)?
- A: Lead times are highly variable based on several factors: part complexity, size, material choice, specific post-processing requirements (especially HIP, heat treat cycles, machining complexity, NDT extent), current machine queue times at the provider, and qualification/documentation needs. However, a rough estimate for a batch of 10-20 qualified superalloy igniter housings would likely range from 8 to 16 weeks, potentially longer if extensive qualification testing or unforeseen challenges arise. Prototyping a single unit might be faster (e.g., 4-8 weeks), but qualification adds significant time. It’s crucial to discuss lead time expectations early with the chosen supplier.
Q4: Are 3D printed superalloy parts weldable for integration into larger engine assemblies?
- A: Generally, yes. Both IN718 and Haynes 282 possess good weldability characteristics, and parts produced via AM using these alloys can typically be welded using standard processes (e.g., TIG, Electron Beam Welding) compatible with superalloys. As with wrought or cast forms, proper procedures (cleanliness, joint design, filler material selection if needed, potential pre/post-weld heat treatments) must be followed. The weldability should be confirmed through process qualification testing, as the fine-grained microstructure of AM parts might behave slightly differently during welding compared to coarser-grained traditional materials. It’s essential to perform welding trials and qualification specific to the AM component and the joining process.
Q5: How does Met3dp ensure the quality and traceability of its AM powders and printed components for aerospace clients?
- A: Met3dp ensures quality and traceability through a multi-layered approach rooted in their expertise as both a powder producer and an AM solutions provider:
- 高度なパウダー製造: Utilizing industry-leading Vacuum Induction Melting Gas Atomization (VIGA) and Plasma Rotating Electrode Process (PREP) technologies ensures high purity, excellent sphericity, and controlled Particle Size Distribution (PSD) in their metal powders.
- Strict Powder QC: Each powder batch undergoes rigorous testing for chemical composition, PSD, morphology, flowability, and gas content, with certificates of analysis provided. Strict batch control and segregation are maintained.
- Robust QMS: Implementing comprehensive quality management systems (potentially aligned with ISO 9001 / AS9100 principles) covering all operational stages.
- Process Control & Monitoring: Utilizing validated build parameters on well-maintained, calibrated machines with potential for in-situ monitoring. Detailed build logs are recorded.
- Witness Coupon Strategy: Processing material test coupons alongside actual parts in each build allows for destructive testing (tensile, hardness, microstructural analysis) to verify that the build achieved the required material properties.
- Integrated Post-Processing: Managing or closely controlling all necessary post-processing steps to ensure they meet specifications.
- Rigorous NDT & Metrology: Employing advanced inspection techniques (CMM, 3D scanning, CT scanning, FPI) to verify dimensional accuracy and internal integrity.
- Full Documentation: Providing comprehensive documentation packages that offer complete traceability from the raw powder batch through all manufacturing, processing, and inspection steps to the final certified component.
Conclusion: Igniting the Future of Propulsion with Superalloy Additive Manufacturing
The journey through the complexities and capabilities of producing rocket igniter housings via superalloy additive manufacturing reveals a technology that is not just viable, but truly transformative for the aerospace industry. Metal AM, leveraging high-performance materials like IN718 and Haynes 282, offers engineers unprecedented freedom to design components optimized for the extreme environments of rocket propulsion systems. The ability to create intricate internal geometries for enhanced cooling or flow, consolidate multiple parts into a single monolithic structure for reduced weight and complexity, and rapidly iterate designs marks a significant leap beyond the constraints of traditional manufacturing.
We’ve explored the critical function of igniter housings, delved into the compelling reasons for adopting AM – from lightweighting and part consolidation to enabling 複雑な幾何学 impossible through other means. Understanding the nuances of materials like IN718 and Haynes 282, mastering the principles of Design for Additive Manufacturing (DfAM), and meticulously managing essential post-processing steps like heat treatment, Hot Isostatic Pressing (HIP), and precision machining are all crucial pieces of the puzzle. Furthermore, navigating challenges related to residual stress, porosity, and quality assurance requires deep expertise and robust process control.
Achieving success in implementing AM for such critical applications hinges on selecting the right partner. A provider must possess not only cutting-edge technology but also proven expertise in superalloys, stringent aerospace quality certifications (like AS9100), comprehensive post-processing capabilities, and a collaborative engineering approach.
メット3dp stands at the forefront of this technological revolution, uniquely positioned as both a manufacturer of high-quality, specialized metal powders – utilizing advanced VIGA and PREP techniques – and a provider of comprehensive additive manufacturing solutions. Our industry-leading printers ensure accuracy and reliability, while our decades of collective expertise in metal AM guarantee that we understand the intricacies of processing demanding materials like IN718 and Haynes 282 for critical applications. We offer an integrated approach, supporting clients from initial design consultation and DfAM optimization through printing, post-processing, and final quality assurance, ensuring components meet the rigorous standards of the aerospace sector.
The future of rocket propulsion lies in leveraging innovative manufacturing methods to achieve higher performance, greater reliability, and faster development cycles. Superalloy additive manufacturing is a cornerstone of this future.
Ready to revolutionize your propulsion components and explore the possibilities of metal AM for your most challenging applications?
Contact the experts at Met3dp today to discuss your specific igniter housing requirements or other demanding aerospace projects. Visit our website at https://met3dp.com/ to learn more about our capabilities and discover how our additive manufacturing solutions can propel your innovations forward.
シェアする
MET3DP Technology Co., LTDは、中国青島に本社を置く積層造形ソリューションのリーディングプロバイダーです。弊社は3Dプリンティング装置と工業用途の高性能金属粉末を専門としています。
関連記事
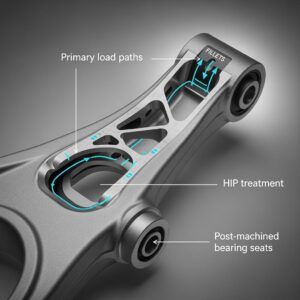