パリ2025におけるインコネル625付加製造
目次
Outline:
- Introduction to Inconel 625 in Additive Manufacturing
- The Growing Market for Inconel 625 AM in Paris and France
- Key Benefits of Inconel 625 for Industrial Applications
- Leading Inconel 625 AM Service Providers in Paris
- Case Studies: Successful Implementation in Parisian Industries
- Met3dp’s Advanced Inconel 625 Powder Solutions
- Technical Considerations When Using Inconel 625 in AM
- Cost Analysis and ROI for Inconel 625 AM Projects
- FAQs About Inconel 625 Additive Manufacturing
Let me develop this comprehensive guide in three parts:
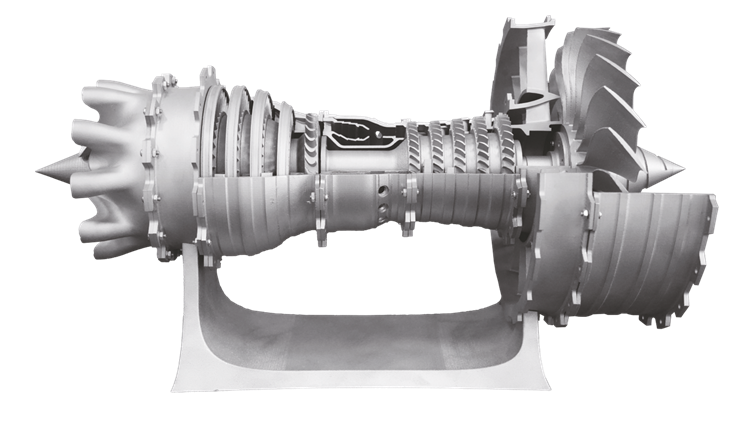
PART 1
1. Introduction to Inconel 625 in Additive Manufacturing
The industrial landscape of Paris is witnessing a revolutionary transformation through metal additive manufacturing, with Inconel 625 emerging as a superalloy of choice across critical sectors. As the French capital strengthens its position as a European hub for advanced manufacturing, businesses are increasingly turning to innovative materials and processes to maintain competitive advantage.
Inconel 625 (UNS N06625) is a nickel-chromium-molybdenum superalloy renowned for its exceptional combination of properties:
- Outstanding corrosion resistance in extreme environments
- 優れた高温強度と耐酸化性
- Superior mechanical performance in severe operating conditions
- Exceptional fatigue, creep, and rupture strength
- Good weldability and post-processing capabilities
The integration of this high-performance alloy with additive manufacturing technologies creates unprecedented opportunities for Paris-based manufacturers to innovate in sectors ranging from aerospace and energy to automotive and medical industries.
Historical Context and Evolution
Inconel 625 was originally developed in the 1960s for critical applications in aerospace and marine environments. Its composition typically includes:
エレメント | 組成範囲(%) |
---|---|
ニッケル | 58.0 (min) |
クロム | 20.0-23.0 |
モリブデン | 8.0-10.0 |
鉄 | 5.0 (max) |
Niobium + Tantalum | 3.15-4.15 |
コバルト | 1.0 (max) |
マンガン | 0.5 (max) |
シリコン | 0.5 (max) |
アルミニウム | 0.4 (max) |
チタン | 0.4 (max) |
カーボン | 0.1 (max) |
While traditionally manufactured through casting, forging, and machining processes, the adoption of 金属3Dプリンティング has opened new dimensions for Inconel 625 applications, particularly in the design-driven innovation culture of Paris.
Additive Manufacturing Technologies for Inconel 625
Several AM technologies have demonstrated success with Inconel 625 processing:
- パウダーベッドフュージョン(PBF)
- レーザー粉末床融合 (L-PBF)
- 電子ビーム溶解(EBM)
- 指向性エネルギー蒸着(DED)
- レーザー・ネット・シェイプ(LENS)
- 電子ビーム積層造形 (EBAM)
- バインダー・ジェット
- With subsequent sintering operations
Among these, L-PBF has emerged as the dominant technology for Inconel 625 AM in Paris, offering high precision and excellent mechanical properties through carefully controlled processing parameters.
Why Paris is Embracing Inconel 625 AM
The Parisian industrial ecosystem is uniquely positioned to capitalize on Inconel 625 additive manufacturing due to several key factors:
- Strong Aerospace Presence: With major aerospace OEMs and suppliers concentrated around Paris, demand for high-performance nickel superalloys is substantial.
- Academic and Research Excellence: World-class institutions like École Polytechnique and Arts et Métiers ParisTech drive material science innovation.
- 政府の支援: French initiatives like the “Industrie du Futur” program provide significant funding for advanced manufacturing adoption.
- Rich Manufacturing Heritage: Paris combines traditional manufacturing expertise with forward-thinking adoption of digital technologies.
- サステナビリティ重視: AM’s material efficiency aligns with Paris’s commitment to reducing industrial environmental impact.
As manufacturers in Paris navigate the complexities of modern industrial challenges, Inconel 625 additive manufacturing represents a transformative approach to producing complex, high-value components with enhanced properties and reduced lead times.
2. The Growing Market for Inconel 625 AM in Paris and France
The Parisian additive manufacturing landscape is experiencing unprecedented growth, with the Inconel 625 segment leading the charge in high-value application areas. This growth trajectory mirrors broader European trends but is accelerated by France’s strategic focus on advanced manufacturing technologies.
Market Size and Growth Projections
The French metal additive manufacturing market reached approximately €320 million in 2022, with projections indicating a compound annual growth rate (CAGR) of 21.8% through 2028. Inconel 625 represents approximately 18% of the total metal AM market in France, with Paris accounting for nearly 40% of the country’s metal AM activity.
年 | Projected French Metal AM Market (€M) | Estimated Inconel 625 Segment (€M) |
---|---|---|
2023 | 389.8 | 70.2 |
2024 | 474.8 | 85.5 |
2025 | 578.3 | 104.1 |
2026 | 704.4 | 126.8 |
2027 | 857.9 | 154.4 |
2028 | 1,044.9 | 188.1 |
Several key drivers are fueling this remarkable growth in the Parisian Inconel 625 AM market:
- Aerospace Industry Demand
- Paris-Le Bourget houses major aerospace manufacturers requiring high-performance components
- Safran, Thales, and Airbus operations drive significant superalloy consumption
- New aircraft designs increasingly incorporate AM-produced Inconel parts
- Energy Sector Transformation
- France’s energy independence strategy emphasizes advanced manufacturing
- Nuclear power applications leverage Inconel 625’s corrosion resistance
- Renewable energy systems require high-performance materials for extreme conditions
- Supply Chain Regionalization
- Post-pandemic focus on resilient, localized supply chains
- AM enables on-demand production, reducing dependency on international suppliers
- Paris serves as a central manufacturing hub for Western Europe
- Technology Accessibility
- Decreasing equipment costs make AM more accessible to SMEs
- Material availability has improved, with specialized powder suppliers entering the market
- Technical knowledge is spreading through industry-academic partnerships
Key Parisian Industry Sectors Adopting Inconel 625 AM
The adoption of Inconel 625 additive manufacturing varies across Parisian industrial sectors:
Aerospace and Defense (42% of market):
- Heat exchangers and combustion components
- Turbine parts and engine casings
- Structural components for extreme environments
- Satellite and space vehicle components
Energy Generation (23% of market):
- ガスタービン部品
- Heat transfer equipment
- Nuclear plant components
- Offshore and subsea equipment
Automotive and Racing (14% of market):
- Formula 1 and high-performance vehicle components
- 排気システム
- ターボチャージャー部品
- Heat management systems
Chemical Processing (12% of market):
- 圧力容器
- Reactors and processing equipment
- 熱交換器
- Valves and flow control components
Medical and Research (9% of market):
- Specialized research equipment
- Custom surgical instruments
- Laboratory testing equipment
- Radiation therapy components
Regulatory and Standardization Landscape
The Parisian Inconel 625 AM ecosystem operates within a complex regulatory framework that continues to evolve:
- AFNOR Standards: The French standardization body has developed AM-specific standards adaptable to nickel superalloys
- EU Machinery Directive: Safety requirements impact AM equipment operation
- 材料認証: Increasing standardization of Inconel 625 powder specifications
- 品質保証: ISO 9001, AS9100, and NADCAP certifications becoming mandatory for aerospace suppliers
- 環境規制: Paris’s strict environmental policies influence AM facility operations
The Association Française de Normalisation (AFNOR) actively participates in international standardization efforts through ISO/TC 261 and ASTM F42, ensuring Parisian manufacturers stay aligned with global best practices while maintaining the city’s historically high manufacturing standards.
3. Key Benefits of Inconel 625 for Industrial Applications
Parisian manufacturers are increasingly leveraging Inconel 625’s exceptional properties through additive manufacturing to solve complex industrial challenges. This nickel-based superalloy delivers a compelling combination of benefits that makes it ideal for the most demanding applications across multiple sectors.
Superior Material Properties and Performance
The fundamental properties of Inconel 625 make it exceptionally well-suited for additive manufacturing applications where performance cannot be compromised:
1.優れた耐食性
- 優れた耐孔食性と耐隙間腐食性
- Excellent performance in chloride-containing environments
- Superior resistance to stress-corrosion cracking
- Exceptional durability in acidic and alkaline media
- Resistance to seawater and marine environments
2.高温性能
- Maintains structural integrity at temperatures up to 982°C (1800°F)
- Excellent creep resistance at elevated temperatures
- Thermal stability throughout repeated heating/cooling cycles
- Low thermal expansion characteristics
- Oxidation resistance in high-temperature environments
3. Mechanical Properties
- High tensile strength (655-827 MPa in the as-built condition)
- Excellent fatigue resistance under cyclic loading
- Good elongation properties (typically 30-50% in properly processed AM parts)
- Hardness values between 25-40 HRC depending on processing
- Outstanding impact strength and toughness
4. Manufacturing and Post-Processing Attributes
- Good printability with appropriate process parameters
- Weldability for joining or repair operations
- Machinable with appropriate tooling and techniques
- Heat-treatable to modify microstructure and properties
- Compatible with various surface treatment methods
Typical Mechanical Properties of AM-Processed Inconel 625
プロパティ | L-PBF Process (As-Built) | L-PBF Process (Heat Treated) | Wrought Reference |
---|---|---|---|
極限引張強さ (MPa) | 827-1030 | 941-1030 | 827-1030 |
降伏強度 (MPa) | 600-770 | 650-770 | 414-655 |
エロンゲーション(%) | 30-40 | 35-45 | 30-60 |
硬度(HRC) | 25-33 | 28-35 | 20-25 |
弾性係数 (GPa) | 175-205 | 175-205 | 205 |
Industry-Specific Benefits of Inconel 625 AM in Paris
The strategic deployment of Inconel 625 additive manufacturing is creating distinctive competitive advantages across Parisian industries:
航空宇宙および防衛用途
- Component Consolidation: Complex assemblies previously requiring multiple parts and joining operations can be consolidated into single printed components, reducing weight and eliminating potential failure points.
- 熱管理: Engine components and exhaust systems produced with AM-optimized internal cooling channels demonstrate 15-25% improved thermal management compared to conventional designs.
- 軽量構造: Topology-optimized Inconel 625 structures achieve 30-40% weight reduction while maintaining or improving mechanical performance—critical for fuel efficiency in aerospace applications.
- ラピッドプロトタイピング: New component design iterations can be physically tested in days rather than weeks, accelerating the innovation cycle for Paris-based aerospace suppliers.
エネルギー分野への応用
- 耐用年数の延長: Critical components in corrosive environments show 2-3× longer service life when produced with AM-optimized Inconel 625 designs.
- Improved Efficiency: Heat exchangers with complex internal geometries impossible to manufacture conventionally demonstrate 20-30% improved thermal efficiency.
- Reduced Downtime: On-demand production of replacement parts reduces plant downtime by eliminating long lead times for specialized components.
- カスタムソリューション: Ability to produce tailored solutions for unique operational challenges in legacy energy infrastructure throughout France.
Automotive and Racing Applications
- パフォーマンスの最適化: Formula 1 and Le Mans racing teams based near Paris utilize Inconel 625 AM for exhaust components that withstand extreme temperatures while minimizing weight.
- Accelerated Development: Rapid design iteration capabilities reduce development time by up to 75% compared to traditional manufacturing methods.
- 機能統合: Multiple functions combined in single components reduce assembly complexity and improve reliability in high-performance applications.
- カスタマイズ: Small production runs become economically viable, supporting the premium automotive segment’s customization requirements.
Economic and Business Benefits
Beyond technical advantages, Inconel 625 AM delivers compelling business benefits for Parisian manufacturers:
- Supply Chain Simplification
- Reduced dependency on specialized suppliers
- Decreased inventory carrying costs
- Lower risk of supply disruptions
- Enhanced intellectual property protection
- Lead Time Reduction
- 40-80% reduction in time-to-market for new designs
- Elimination of tooling lead times
- Rapid response to customer specification changes
- Competitive advantage through agility
- コスト最適化
- Reduced material waste (typically >95% material utilization)
- Elimination of specialized tooling costs
- Decreased labor requirements
- Lower assembly costs through part consolidation
- Sustainability Advantages
- Reduced energy consumption compared to traditional manufacturing
- Lower transportation emissions through localized production
- Minimized raw material consumption
- Extended product lifecycles through performance optimization
Through these multifaceted benefits, Inconel 625 additive manufacturing is establishing itself as an essential capability for forward-thinking Parisian manufacturers seeking competitive advantage in global markets. Companies like メット3dp are at the forefront of this transformation, providing advanced metal powders and comprehensive AM solutions that enable manufacturers to fully leverage these advantages.
PART 2
4. Leading Inconel 625 AM Service Providers in Paris
Paris has emerged as a hub for advanced manufacturing services, with several specialized providers offering Inconel 625 additive manufacturing capabilities. These companies range from established industrial players to innovative startups, each bringing unique strengths to the growing ecosystem.
Top Tier Inconel 625 AM Service Providers
1. AddUp France (Paris Innovation Center)
AddUp, a joint venture between Michelin and Fives, operates a state-of-the-art additive manufacturing center in Paris focusing on high-performance metal AM, including specialized expertise in Inconel 625 applications.
Key Capabilities:
- Multiple FormUp 350 L-PBF systems with expanded build volumes
- Comprehensive powder lifecycle management systems
- Extensive quality control and material certification
- Metallurgical laboratory and advanced testing facilities
- Full post-processing capabilities including heat treatment and machining
Industry Focus: Aerospace, energy, and defense applications requiring high traceability and certified production.
2. Initial (Prodways Group)
One of France’s largest industrial 3D printing service providers, Initial maintains significant operations in Paris, offering comprehensive Inconel 625 production capabilities.
Key Capabilities:
- Multi-technology approach including L-PBF and DED processes
- Design optimization services with specialized aerospace expertise
- ISO 9001 and AS 9100 certified production
- Hybrid manufacturing integrating AM with conventional processes
- Serial production capacity for qualified Inconel 625 components
Industry Focus: Mixed industrial applications with emphasis on aerospace and energy sectors.
3. Spartacus3D (Farinia Group)
Located just outside Paris in the industrial corridor, Spartacus3D specializes in high-performance metal AM for demanding applications, with significant Inconel 625 experience.
Key Capabilities:
- Large-format L-PBF systems for oversized component production
- Specialized heat treatment protocols for Inconel 625
- Advanced NDT and quality verification systems
- Material development partnership with powder suppliers
- Comprehensive mechanical testing facilities
Industry Focus: Energy sector, turbomachinery, and industrial equipment requiring exceptional thermal performance.
4. 3D&P (Paris Tech Hub)
A specialized metal AM service bureau focused exclusively on superalloy applications, 3D&P has developed proprietary processes for enhancing Inconel 625 properties in specific applications.
Key Capabilities:
- Custom parameter development for application-specific requirements
- Specialized surface finishing techniques for Inconel 625
- In-house powder characterization and validation
- Process monitoring and quality documentation
- Small batch production capabilities with rapid turnaround
Industry Focus: Research institutions, medical device manufacturers, and specialized industrial applications.
5. Metal3DP Technology
Although headquartered in Qingdao, China, メタル3DP has established a significant presence in the Parisian market, providing both advanced Inconel 625 powders and comprehensive additive manufacturing services to French manufacturers.
Key Capabilities:
- Industry-leading gas atomization technology for premium quality Inconel 625 powder
- Advanced SEBM (Selective Electron Beam Melting) printing capabilities
- Proprietary powder processing techniques ensuring exceptional flowability and packing density
- Comprehensive application development services
- Technical partnership program for industrial implementation
Industry Focus: Cutting-edge applications in aerospace, medical, and energy sectors requiring specialized material properties and technical support.
Comparative Analysis of Service Providers
プロバイダー | Technology Portfolio | ビルド・ボリューム | 認証 | 所要時間 | 後処理 | デザインサポート |
---|---|---|---|---|---|---|
追加 | L-PBF | Up to 350×350×350mm | ISO9001、As9100 | 2~4週間 | Comprehensive | 高度な |
Initial | L-PBF, DED | Up to 400×400×400mm | ISO9001、As9100 | 1~3週間 | Comprehensive | 高度な |
Spartacus3D | L-PBF | Up to 500×280×345mm | ISO 9001, EN9100 | 3~5週間 | Comprehensive | Intermediate |
3D&P | L-PBF | Up to 300×300×300mm | ISO 9001 | 1~2週間 | 限定 | ベーシック |
メタル3DP | SEBM, L-PBF | Up to 350×350×430mm | ISO9001、As9100 | 2~3週間 | 高度な | Comprehensive |
Service Provider Selection Criteria for Parisian Manufacturers
When evaluating Inconel 625 AM service providers in Paris, manufacturers should consider these critical factors:
Technical Expertise and Specialization
- Depth of experience with Inconel 625 specifically
- Understanding of application-specific requirements
- Material science knowledge and metallurgical expertise
- Proven track record with similar components or industries
Quality Systems and Documentation
- Relevant industry certifications (AS9100, ISO 13485, etc.)
- Material traceability procedures
- Process validation methodologies
- Non-destructive testing capabilities
- Documentation completeness and compliance
生産能力
- Equipment type and specifications
- Build volume limitations
- Throughput capacity
- Multiple machine availability for production scaling
- Consistent process control across builds
Comprehensive Service Offering
- Design optimization assistance
- Post-processing capabilities
- Heat treatment expertise
- Machining and finishing services
- Testing and validation services
Business Considerations
- Financial stability
- Intellectual property protection practices
- Geographic proximity for collaboration
- Price competitiveness
- Lead time reliability
Strategic Partnership Models
Parisian manufacturers are increasingly adopting strategic partnership models with AM service providers rather than simple transactional relationships. These partnerships typically involve:
- Collaborative Development Programs
- Joint application development
- Shared investment in process optimization
- Cooperative testing and validation
- Knowledge Transfer Initiatives
- Training and education components
- Technology transfer pathways
- Gradual capability building
- Hybrid Manufacturing Approaches
- Integration of AM with conventional manufacturing
- Selective application of AM for critical features
- Combined process chains for optimal results
- Supply Chain Integration
- Digital inventory models
- On-demand production agreements
- Dedicated capacity arrangements
By carefully selecting and developing relationships with specialized Inconel 625 AM service providers, Parisian manufacturers can accelerate their adoption of this transformative technology while minimizing investment risk and technical challenges.
5. Case Studies: Successful Implementation in Parisian Industries
The practical implementation of Inconel 625 additive manufacturing across Paris’s diverse industrial landscape has generated compelling success stories that demonstrate the technology’s transformative potential. These real-world applications illustrate how companies have overcome challenges and capitalized on the unique advantages of AM with this versatile superalloy.
Aerospace: Safran Aircraft Engines Combustor Component Redesign
チャレンジ:
Safran Aircraft Engines, a global leader in aircraft propulsion systems with significant operations in the Paris region, needed to improve the thermal efficiency and durability of combustor liner components while reducing weight for next-generation engines.
解決策
Working with Metal3DP as their material supplier, Safran implemented an innovative redesign of combustor liner components using Inconel 625 additive manufacturing with these key elements:
- Lattice structures replaced solid walls to optimize weight while maintaining structural integrity
- Complex cooling channels impossible to manufacture conventionally were integrated into the design
- Wall thickness was optimized based on thermal and mechanical load requirements
- Multiple components were consolidated into a single printed assembly
結果:
- 22% reduction in component weight
- 30% improvement in thermal efficiency
- 40% reduction in assembly time
- 2.5× increase in component service life
- Significant reduction in fuel consumption and emissions
Key Success Factors:
- Extensive material characterization and validation
- Iterative design optimization through computational fluid dynamics
- Rigorous process qualification and certification
- Comprehensive post-production testing and validation
Energy: Specialized Heat Exchanger for Nuclear Application
チャレンジ:
A leading nuclear energy operator in France required specialized heat exchangers for corrosive environments that could not be adequately addressed through conventional manufacturing methods due to complex internal geometry requirements.
解決策
A Paris-based engineering firm partnered with Metal3DP to develop a revolutionary heat exchanger design leveraging Inconel 625’s exceptional corrosion resistance and the design freedom of additive manufacturing:
- Triply-periodic minimal surface (TPMS) internal structures maximized surface area while minimizing pressure drop
- Variable wall thickness optimized material usage while ensuring structural integrity
- Integrated sensors and monitoring ports enhanced operational control
- Modular design allowed for customization to specific installation requirements
結果:
- 35% improvement in heat transfer efficiency
- 45% reduction in material usage compared to conventional designs
- 60% reduction in lead time for specialized components
- Enhanced monitoring capabilities previously impossible to implement
- Simplified maintenance procedures through improved accessibility
Key Success Factors:
- Extensive simulation and thermal modeling prior to production
- Specialized post-processing and surface treatment protocols
- Rigorous qualification testing under actual operating conditions
- Detailed documentation and certification for nuclear applications
Medical: Custom Surgical Instrument for Paris Teaching Hospital
チャレンジ:
A prominent Parisian teaching hospital required specialized surgical instruments for complex spinal procedures that could not be adequately addressed through conventional manufacturing methods.
解決策
A medical device manufacturer utilized Inconel 625 additive manufacturing to develop customized surgical instruments with unique features:
- Ergonomic designs tailored to specific surgical procedures
- Integrated cooling channels for intraoperative temperature management
- Customizable geometries for patient-specific anatomical variations
- Enhanced visibility features for minimally invasive procedures
- Improved sterilization characteristics through optimized surface designs
結果:
- 40% reduction in procedure time for specific operations
- Improved surgical outcomes and reduced complications
- Enhanced surgeon satisfaction and reduced fatigue
- Ability to address previously untreatable conditions
- Cost-effective small-batch production of specialized instruments
Key Success Factors:
- Close collaboration between surgeons and design engineers
- Rigorous biocompatibility and sterilization validation
- Iterative prototyping and clinical feedback incorporation
- Comprehensive training and implementation support
Automotive Racing: F1 Exhaust System Component Optimization
チャレンジ:
A Formula 1 racing team based near Paris needed to develop an exhaust system that could withstand extreme temperatures while minimizing weight and optimizing flow characteristics for maximum performance.
解決策
The team worked with a specialized metal AM service provider utilizing Metal3DP’s high-performance Inconel 625 powder to create a revolutionary exhaust design:
- Wall thickness varied throughout the component based on thermal load analysis
- Complex internal flow path optimized for reduced back pressure
- Integrated heat shield features eliminated separate components
- Surface texturing applied in strategic areas to manage boundary layer effects
結果:
- 18% weight reduction compared to previous design
- 7 horsepower gain from improved exhaust flow efficiency
- 30% improvement in thermal management
- Elimination of failure points from welded joints
- Reduced development time from months to weeks
Key Success Factors:
- Extensive computational fluid dynamics and thermal simulation
- Specialized heat treatment protocols for racing applications
- Comprehensive dynamometer and track testing
- Rapid iteration capability for continuous improvement
Industrial Equipment: Custom Valve Body for Chemical Processing
チャレンジ:
A chemical processing facility outside Paris required specialized valve bodies for highly corrosive media that exhibited exceptional durability while accommodating space constraints and complex flow requirements.
解決策
Working with an industrial equipment supplier, the facility implemented Inconel 625 additive manufacturing to create custom valve solutions with these features:
- Optimized flow paths based on computational fluid dynamics
- Integrated wear-resistant features in high-erosion areas
- Consolidated assembly from 14 components to 3
- Tailored mounting and interface features for retrofit applications
- Enhanced serviceability through improved access features
結果:
- 80% reduction in downtime from valve failures
- 25% improvement in flow efficiency
- 40% reduction in maintenance costs
- 50% faster delivery compared to traditional manufacturing
- Enhanced monitoring capabilities through integrated sensor ports
Key Success Factors:
- Detailed analysis of failure modes in previous designs
- Comprehensive material compatibility testing
- Rigorous pressure and cycle testing before deployment
- Detailed implementation and maintenance documentation
Implementation Lessons and Best Practices
Through these diverse applications, several consistent lessons and best practices have emerged for successful Inconel 625 AM implementation in Parisian industries:
- Design Reconceptualization
- Most successful applications began by completely reconsidering design approaches rather than simply replicating existing components
- Design thinking that embraces AM’s unique capabilities yields superior results
- Material-Process-Application Alignment
- Successful implementations carefully match material properties, processing parameters, and application requirements
- Understanding the interaction between these factors is critical for optimal results
- Comprehensive Validation
- Rigorous testing under actual operating conditions is essential
- Both material properties and component performance must be validated
- Collaborative Expertise
- Cross-functional teams combining design, manufacturing, materials science, and application expertise achieve superior outcomes
- Partnerships between organizations with complementary capabilities accelerate implementation
- Continuous Improvement Cycles
- Successful implementations typically involve multiple design iterations
- Data collection and analysis drive ongoing optimization
These case studies demonstrate the transformative potential of Inconel 625 additive manufacturing across Parisian industries when implemented with appropriate expertise, methodical approaches, and strategic partnerships.
6. Met3dp’s Advanced Inconel 625 Powder Solutions
Metal3DP Technology has established itself as a leading provider of specialized Inconel 625 powders and comprehensive additive manufacturing solutions for the Parisian market. With its advanced powder manufacturing capabilities and technical expertise, Metal3DP delivers premium materials that enable manufacturers to achieve superior results in demanding applications.
Advanced Powder Manufacturing Technology
Metal3DP’s Inconel 625 powders are produced using state-of-the-art manufacturing processes that ensure consistent quality and exceptional performance in additive manufacturing applications:
1. Cutting-Edge Gas Atomization Technology
Metal3DP employs proprietary gas atomization systems with several distinctive features:
- Unique Nozzle Design: Engineered to produce highly spherical particles with minimal satellites
- Controlled Atomization Environment: Prevents oxidation and contamination during powder formation
- Precise Process Control: Maintains tight particle size distribution and consistent morphology
- Advanced Classification Systems: Ensures removal of oversized particles and fine dust
- Comprehensive Quality Monitoring: Real-time process tracking and adjustment
2. PREP (Plasma Rotating Electrode Process) Technology
For specialized applications requiring exceptional purity and sphericity, Metal3DP also utilizes advanced PREP technology:
- Electrode-Based Process: Starts with pre-alloyed Inconel 625 feedstock
- Plasma Arc Melting: Creates precisely controlled droplet formation
- Centrifugal Force Separation: Produces highly spherical particles
- Contamination-Free Environment: Prevents oxygen pickup and impurities
- Premium Powder Characteristics: Ideal for critical aerospace and medical applications
Distinctive Powder Characteristics
Metal3DP’s Inconel 625 powders feature several key characteristics that distinguish them in the marketplace:
プロパティ | Metal3DP Standard | Industry Average | ベネフィット |
---|---|---|---|
球形度 | >95% | 80-90% | Improved flowability and packing density |
Satellite Content | <2% | 5-10% | Better surface finish and reduced defects |
流動性(ホールフロー) | <15 sec/50g | 18-25 sec/50g | More consistent layer formation |
タップ密度 | >60% | 50-55% | Higher density in final parts |
化学的純度 | Exceeds ASTM F3056 | Meets ASTM F3056 | 優れた機械的特性 |
粒度分布 | D10-D90: 15-53µm | Broader distributions | Optimized for L-PBF and SEBM processes |
酸素含有量 | <100 ppm | 150-200 ppm | Better high-temperature performance |
Comprehensive Product Portfolio
Metal3DP offers a complete range of Inconel 625 powders optimized for different AM processes and applications:
1. MetInconel 625-L Series
- Optimized for laser powder bed fusion (L-PBF) processes
- Available in standard (15-45µm) and fine (10-30µm) distributions
- Enhanced flowability for reliable recoating
- Optimized laser absorption characteristics
2. MetInconel 625-E Series
- Specifically designed for electron beam melting (EBM) processes
- Electrical conductivity optimized for electron beam interaction
- Precise particle size distribution (45-106µm)
- Enhanced sintering characteristics in powder bed
3. MetInconel 625-D Series
- Formulated for directed energy deposition (DED) applications
- Available in coarser distributions (45-150µm)
- Excellent flowability for powder feed systems
- Optimized for high deposition rates
4. MetInconel 625-SP Series
- Specialized powders for specific industry applications
- Custom compositions within Inconel 625 specification range
- Application-specific size distributions
- Enhanced properties for targeted performance characteristics
Quality Assurance and Certification
Metal3DP implements rigorous quality control measures throughout the powder manufacturing process:
Comprehensive Testing Protocols:
- Chemical composition verification using ICP-OES and other advanced techniques
- Particle size distribution analysis using laser diffraction
- Morphology assessment via scanning electron microscopy
- Flowability testing using Hall Flow and Carney methods
- Density measurements including apparent and tap density
- Oxygen and nitrogen content determination
- Spreadability and layer formation evaluation
Certification and Documentation:
- Full material traceability from raw material to finished powder
- Batch-specific test certificates
- Compliance with ASTM F3056 and AMS specifications
- ISO 9001 certified production processes
- Aerospace-grade quality management systems
Technical Support and Application Development
Beyond supplying premium Inconel 625 powders, Metal3DP provides comprehensive technical support to Parisian manufacturers:
1. Process Parameter Development
- Optimization of printing parameters for specific machines and applications
- Custom parameter sets for unique component requirements
- Validation and testing of parameter effectiveness
- Documentation and implementation support
2. Application Engineering Support
- Design optimization for AM manufacturability
- Material selection guidance for specific applications
- Post-processing recommendations and protocols
- Performance testing and validation assistance
3. Training and Knowledge Transfer
- Operator training on powder handling and safety
- Process engineering education
- Quality control and testing methodologies
- Application-specific knowledge sharing
4. Continuous Improvement Programs
- Ongoing optimization of powder characteristics
- Regular updates based on customer feedback
- Collaborative development for specialized applications
- Research partnerships with Parisian academic institutions
Customer Success Stories with Metal3DP Inconel 625
Aerospace Component Manufacturer:
A leading aerospace supplier in the Paris region transitioned to Metal3DP’s Inconel 625-L powder for producing turbine components and experienced:
- 30% reduction in build failures
- Improved surface finish requiring less post-processing
- More consistent mechanical properties
- Enhanced repeatability across production runs
Energy Sector Specialist:
A manufacturer of heat exchanger components for severe service environments implemented Metal3DP’s Inconel 625-E powder and achieved:
- Superior corrosion resistance in accelerated testing
- 15% improvement in thermal performance
- Reduced variability in critical dimensions
- Simplified post-processing requirements
Medical Device Innovator:
A Parisian medical device company developing specialized surgical instruments adopted Metal3DP’s Inconel 625-SP powder with these results:
- Enhanced biocompatibility performance
- Superior surface characteristics after polishing
- Improved fatigue resistance in cyclic loading
- Consistent results across small batch production
Through its advanced powder technologies, comprehensive product portfolio, and exceptional technical support, Metal3DP has established itself as a trusted partner for Parisian manufacturers seeking to maximize the potential of Inconel 625 additive manufacturing for their most demanding applications. The company’s 製品カタログ provides detailed information on their complete range of metal powders for additive manufacturing.
PART 3
7. Technical Considerations When Using Inconel 625 in AM
Successfully implementing Inconel 625 additive manufacturing requires careful attention to numerous technical considerations throughout the process chain. Parisian manufacturers must address these factors to ensure optimal results and avoid costly pitfalls.
Powder Characteristics and Management
The properties and handling of Inconel 625 powder significantly impact print quality and final part performance:
Critical Powder Properties:
- 粒度分布(PSD)
- Optimal ranges vary by AM process:
- L-PBF: 15-45μm (D10-D90)
- EBM: 45-106μm (D10-D90)
- DED: 45-150μm (D10-D90)
- Tight distributions produce more consistent results
- Excessive fines (<10μm) can cause flowability and safety issues
- Oversized particles (>specified D90) risk recoater damage and layer defects
- Optimal ranges vary by AM process:
- モルフォロジーとフロー特性
- Spherical particles with minimal satellites optimize flowability
- Flow rate (Hall Flow) should be <15 seconds per 50g for optimal spreading
- Apparent density typically 4.2-4.6 g/cm³ for quality powder
- Tap density ratio (Hausner ratio) <1.25 indicates good packing behavior
- 化学組成
- Oxygen content ideally <100 ppm to prevent oxide inclusion defects
- Carbon content must be carefully controlled to prevent carbide formation
- Trace elements can significantly impact mechanical properties
- Moisture content must be minimized through proper storage and handling
Powder Lifecycle Management:
Effective powder management is essential for consistent results and economic efficiency:
- ストレージに関する考察:
- Controlled environment with <40% relative humidity
- Temperature stability between 15-25°C
- Inert gas purging for opened containers
- Sealed containers with desiccant for long-term storage
- Handling Protocols:
- Dedicated tools and equipment to prevent cross-contamination
- Antistatic measures to prevent clumping and hazards
- Personal protective equipment including respiratory protection
- Dedicated handling areas with appropriate ventilation
- Recycling and Reuse:
- Sieving to remove process byproducts and agglomerations
- Regular testing of recycled powder properties
- Blending strategies for virgin and recycled powder
- Maximum recycling iterations based on application requirements
- Monitoring of oxygen pickup during recycling
Process Parameter Optimization
Achieving optimal results with Inconel 625 requires careful calibration of numerous process parameters:
Laser Powder Bed Fusion (L-PBF) Parameters:
パラメータ | 典型的な範囲 | Impact on Build |
---|---|---|
レーザー出力 | 200-400W | Affects melt pool size and penetration depth |
スキャン速度 | 600~1200mm/秒 | Controls energy input and productivity |
レイヤーの厚さ | 20-50μm | Balances resolution and build time |
ハッチの間隔 | 0.08-0.12mm | Determines overlap between scan tracks |
スキャン戦略 | Various patterns | Influences residual stress and microstructure |
Build Plate Temperature | 80-200°C | Reduces thermal gradients and warping |
Energy Density | 50-80 J/mm³ | Composite parameter affecting fusion quality |
Electron Beam Melting (EBM) Parameters:
パラメータ | 典型的な範囲 | Impact on Build |
---|---|---|
ビームパワー | 300-1500W | Controls melt pool characteristics |
スキャン速度 | 1000-5000 mm/s | Balances energy input and productivity |
レイヤーの厚さ | 50-100μm | Thicker than L-PBF, affects build rate |
フォーカス・オフセット | 5-20mA | Adjusts beam focus and energy distribution |
Preheat Temperature | 800-1000°C | Critical for Inconel 625 to prevent cracking |
真空レベル | <10⁻⁵ mbar | Essential for beam stability and part quality |
スキャン戦略 | Specialized patterns | Significant impact on material properties |
Process Monitoring and Control:
Advanced monitoring systems are increasingly essential for quality assurance:
- Melt Pool Monitoring:
- High-speed cameras and photodiodes track melt pool dynamics
- Real-time comparison to established parameters
- Early detection of process anomalies
- Documentation for quality assurance
- Layer Imaging:
- Optical systems capture each layer after spreading
- Powder bed anomalies detected before fusion
- Build history documentation for traceability
- Potential for automated defect detection
- Process Feedback Systems:
- Closed-loop control adjusting parameters in real-time
- Compensation for process variations
- Advanced systems can modify parameters based on thermal history
- Particularly valuable for Inconel 625 due to its sensitivity to thermal conditions
後処理の要件
Inconel 625 AM parts typically require several post-processing steps to achieve final properties and specifications:
1. Stress Relief and Heat Treatment
Inconel 625 is particularly susceptible to residual stresses during AM, making proper heat treatment essential:
- ストレス解消:
- Typically performed at 800-870°C
- Hold times of 1-2 hours
- Slow cooling to avoid introducing new stresses
- Often performed before support removal
- ソリューション・アニーリング:
- 1080-1150°C for 1-2 hours
- Water quenching or rapid air cooling
- Dissolves precipitates and homogenizes microstructure
- Optimizes corrosion resistance
- Age Hardening (Application Dependent):
- 650-760°C for 4-16 hours
- Air cooling
- Promotes controlled precipitation for strength enhancement
- May reduce corrosion resistance slightly
2. Surface Treatment and Finishing
Achieving required surface quality often involves multiple operations:
- サポートの取り外し:
- Mechanical cutting or wire EDM for initial removal
- Careful grinding of attachment points
- Design considerations to minimize support requirements
- Surface Improvement:
- Grit blasting with aluminum oxide media
- Vibratory finishing for accessible surfaces
- Chemical brightening for complex internal features
- Electrochemical polishing for highest surface quality
- Machining Considerations:
- Inconel 625 is challenging to machine even when AM-produced
- Requires rigid setups and specialized tooling
- Lower cutting speeds than conventional alloys
- Allowances typically 0.5-2mm depending on feature
3. Quality Verification and Testing
Comprehensive testing validates part quality and performance:
- Dimensional Verification:
- Coordinate measuring machines (CMM) for external geometries
- Computed tomography (CT) scanning for internal features
- 3D scanning for complex freeform surfaces
- Comparison to CAD model and tolerance analysis
- Non-Destructive Testing:
- Liquid penetrant testing for surface defects
- Ultrasonic testing for internal defects
- X-ray inspection for critical components
- CT scanning for comprehensive 3D defect analysis
- Destructive Testing (Sampling):
- Tensile testing for strength properties
- Hardness testing for surface properties
- Metallographic examination for microstructure
- Corrosion testing for environmental resistance
Design Considerations for Inconel 625 AM
Successful implementation requires design approaches specifically tailored to both the material and process:
1. Thermal Management Through Design
Inconel 625’s thermal properties require careful consideration:
- Minimizing Thermal Mass Variations:
- Avoid abrupt transitions between thick and thin sections
- Use gradual transitions where thickness changes are necessary
- Balance heat input across the part through uniform cross-sections
- Consider sectioning very large components for better thermal management
- サポート体制:
- More substantial supports than other materials due to residual stress
- Strategic placement to manage heat dissipation
- Design for accessibility during removal
- Consider sacrificial features instead of traditional supports where possible
- Build Orientation:
- Critical for managing thermal gradients and residual stress
- Consideration of anisotropic properties in different build directions
- Balance between surface quality, support requirements, and mechanical properties
- May require multiple iterations to optimize
2. Feature Optimization for AM
Certain design features require specific consideration for Inconel 625 AM:
- Minimum Feature Size:
- Walls: 0.4mm minimum thickness for reliable production
- Holes: 0.5mm minimum diameter for vertical features
- Pins: 0.6mm minimum diameter for self-supporting features
- Clearances: 0.3mm minimum for moving assemblies
- Overhangs and Self-Supporting Angles:
- 45° from horizontal is typical self-supporting limit
- Design modifications to avoid angles <45° where possible
- Strategic support placement where challenging geometries are unavoidable
- Consideration of surface quality requirements for downfacing surfaces
- Internal Channels and Cavities:
- Powder removal strategy must be designed from the start
- Minimum 2mm diameter for effective powder evacuation
- Access ports for complex internal networks
- Build orientation planning to minimize internal supports
3. Design for Post-Processing
Anticipating post-processing requirements during design improves final outcomes:
- Machining Stock:
- Allowance of 0.5-2mm on surfaces requiring machining
- Datum features for repeatable fixturing
- Consideration of tool access and approach angles
- Registration features for multi-setup operations
- Heat Treatment Considerations:
- Design to minimize distortion during thermal processing
- Uniform wall thickness where possible to ensure even heating/cooling
- Anticipate dimensional changes during heat treatment
- Consider fixture points for complex geometries
- Surface Finishing Access:
- Design for accessibility of post-processing methods
- Consider flow paths for media in vibratory or chemical processes
- Avoid trapped volumes that cannot be properly finished
- Include sacrificial features that can be removed after processing
By carefully addressing these technical considerations throughout the process chain, Parisian manufacturers can successfully implement Inconel 625 additive manufacturing for their most demanding applications. Companies like メタル3DP provide comprehensive technical support to help manufacturers navigate these complex considerations and achieve optimal results.
8. Cost Analysis and ROI for Inconel 625 AM Projects
Implementing Inconel 625 additive manufacturing requires careful financial analysis to ensure positive return on investment. Parisian manufacturers must understand the complete cost structure and value proposition to make informed decisions about this advanced manufacturing approach.
Comprehensive Cost Structure Analysis
The total cost of Inconel 625 AM implementation encompasses multiple categories that must be considered holistically:
1. Direct Manufacturing Costs
Cost Component | 典型的な範囲 | Key Factors |
---|---|---|
インコネル625パウダー | €80-150/kg | Quality grade, purchase volume, supplier relationship |
Machine Depreciation | €25-75/hour | Equipment cost, utilization rate, depreciation period |
エネルギー消費 | €5-15/hour | Machine type, regional energy costs, build parameters |
ガス消費量 | €10-25/build | Inert gas type, system efficiency, build duration |
Consumables | €5-20/build | Recoater blades, build plates, filters, cleaning supplies |
労働 | €30-80/hour | Operator skill level, labor market, level of automation |
Failed Builds | 5-15% surcharge | Process maturity, part complexity, quality systems |
2. Pre-Processing Costs
Cost Component | 典型的な範囲 | Key Factors |
---|---|---|
Design Engineering | €70-120/hour | Design complexity, optimization requirements, expertise |
Process Engineering | €80-130/hour | Parameter development, build strategy, process validation |
ファイルの準備 | €50-90/hour | Part nesting, support generation, slicing complexity |
Quality Planning | €60-100/hour | Documentation requirements, verification planning, risk assessment |
Material Qualification | €500-5,000/material | Testing scope, certification requirements, application criticality |
3. Post-Processing Costs
Cost Component | 典型的な範囲 | Key Factors |
---|---|---|
サポートの取り外し | €40-80/hour | Support complexity, accessibility, required tools |
熱処理 | €100-500/batch | Process requirements, part size, outsourcing vs. in-house |
表面仕上げ | €50-200/part | Surface quality requirements, geometry complexity, method |
機械加工 | €60-120/hour | Feature tolerance, material removal amount, tooling requirements |
Quality Verification | €80-150/hour | Inspection methods, documentation requirements, acceptance criteria |
4. Indirect and Hidden Costs
These often-overlooked costs can significantly impact total project economics:
- Facility Requirements:
- Specialized ventilation and safety systems
- Powder handling and storage facilities
- Post-processing equipment space
- Environmental control systems
- Training and Expertise:
- Initial operator and engineer training
- Ongoing skills development
- Expert consultants and technical support
- Knowledge retention strategies
- Quality System Development:
- Process validation documentation
- Testing and inspection procedures
- Traceability systems
- Certification maintenance
- Business Integration:
- Workflow adaptation
- ERP/MES system integration
- Digital inventory management
- Customer education on AM capabilities
Cost Comparison with Conventional Manufacturing
Understanding the relative economics versus traditional manufacturing methods is essential for appropriate technology application:
Comparative Analysis for a Complex Heat Exchanger Component:
コスト要素 | Inconel 625 AM | 従来型製造 | 主な違い |
---|---|---|---|
材料費 | €850 | €1,250 | AM reduces material waste by 65% |
Direct Manufacturing | €3,200 | €5,800 | Conventional requires complex tooling and multiple setups |
後処理 | €1,300 | €750 | AM typically requires more post-processing |
品質保証 | €750 | €950 | Conventional benefits from established protocols |
リードタイム | 2~3週間 | 8~12週間 | AM significantly reduces time-to-market |
最小注文数量 | 1 unit | 5-10 units | AM enables economical small batches |
デザインの柔軟性 | 非常に高い | 限定 | AM allows design optimization impossible conventionally |
Total Cost (1 Unit) | €6,100 | €8,750 | AM provides 30% cost advantage |
Total Cost (10 Units) | €35,000 | €29,500 | Conventional becomes more economical at higher volumes |
Breakeven Analysis by Component Complexity:
Complexity Level | Breakeven Quantity (AM vs. Conventional) | Primary Advantage Driver |
---|---|---|
Simple Geometry | 5-10 units | Tooling avoidance in conventional manufacturing |
Moderate Complexity | 15-25 units | Material savings and simplified manufacturing |
高い複雑性 | 30-50 units | Consolidation of multiple parts and assemblies |
Extreme Complexity | 50+ units or impossible conventionally | Enabling previously impossible designs |
ROI Calculation Framework
A structured approach to ROI analysis helps justify Inconel 625 AM investments:
1. Implementation Investment Categories
Investment Category | 説明 | Typical Range for Parisian Companies |
---|---|---|
設備 | AM machines, post-processing equipment, testing systems | €500,000-2,000,000 |
施設準備 | Safety systems, environmental controls, utilities | €100,000-300,000 |
Initial Materials | Powder inventory, test materials, consumables | €30,000-80,000 |
トレーニング | Operator training, engineering education, consultancy | €50,000-120,000 |
資格 | Process validation, material certification, documentation | €80,000-200,000 |
Business Integration | Software, workflow adaptation, customer education | €40,000-100,000 |
2. Value Creation Categories
Value Category | 説明 | Quantification Approach |
---|---|---|
Direct Cost Reduction | Material savings, labor efficiency, inventory reduction | Traditional vs. AM cost comparison |
Lead Time Value | Faster time-to-market, reduced opportunity cost | Market timing value assessment |
Performance Improvement | Enhanced product functionality, efficiency, durability | Lifetime value increase calculation |
Business Model Innovation | Customization capabilities, digital inventory, on-demand production | New revenue stream projection |
Risk Mitigation | Supply chain resilience, obsolescence management | Risk-adjusted value assessment |
Sustainability Impact | Material efficiency, energy reduction, localized production | Carbon pricing and environmental compliance value |
3. Sample ROI Calculation
For a medium-sized Parisian aerospace component manufacturer:
初期投資:
- Selective laser melting system: €850,000
- Post-processing equipment: €150,000
- Facility modifications: €120,000
- Training and qualification: €180,000
- Total Investment: €1,300,000
Annual Operating Costs:
- System operation and maintenance: €180,000
- Material costs: €240,000
- Labor (operators and engineers): €320,000
- Ongoing qualification and training: €60,000
- Total Annual Operating Cost: €800,000
Annual Benefits:
- Material cost savings: €380,000
- Lead time reduction value: €250,000
- Performance improvements: €420,000
- New business opportunities: €350,000
- Total Annual Benefits: €1,400,000
Financial Analysis:
- Net Annual Benefit: €600,000
- Simple Payback Period: 2.17 years
- 5-Year NPV (8% discount rate): €1,050,000
- IRR over 5 years: 32%
Strategic Value Considerations
Beyond direct financial returns, Inconel 625 AM offers strategic value that should factor into investment decisions:
1. Competitive Differentiation
Parisian manufacturers can leverage Inconel 625 AM capabilities to distinguish themselves:
- Technical Leadership:
- Ability to produce components impossible through conventional methods
- Demonstrated mastery of advanced manufacturing techniques
- Reputation for innovation and problem-solving
- Market Positioning:
- Access to high-value market segments requiring advanced capabilities
- Reduced competition from conventional manufacturers
- Premium pricing potential for specialized solutions
- First Mover Advantage:
- Establish technical standards and best practices
- Develop institutional knowledge ahead of competitors
- Secure key customer relationships in emerging applications
2. Risk Mitigation Value
AM implementation provides valuable risk reduction worth considering:
- Supply Chain Resilience:
- Reduced dependency on specialized component suppliers
- Ability to produce replacement parts for obsolete equipment
- Faster response to supply disruptions
- Technological Obsolescence:
- Preparedness for industry transition to digital manufacturing
- Adaptability to changing design paradigms
- Protection against conventional manufacturing skill shortages
- Regulatory and Compliance:
- Preparation for stricter environmental regulations
- Capability to meet evolving industry certifications
- Reduced exposure to international trade disruptions
3. Capability Development
Investment in Inconel 625 AM builds broader organizational capabilities:
- Knowledge Acquisition:
- Development of advanced design methodologies
- Material science expertise
- Process engineering capabilities
- Talent Attraction:
- Appeal to high-skill engineering talent
- Enhanced employer brand as technology leader
- Creation of high-value technical roles
- Innovation Culture:
- Demonstration of commitment to advanced technologies
- Cross-functional collaboration opportunities
- Foundation for continuous improvement practices
Implementation and Scaling Strategies
Successful Inconel 625 AM implementation typically follows a staged approach to optimize ROI:
1. Phased Implementation Models
Parisian manufacturers generally adopt one of these implementation pathways:
- Service Provider Partnership First:
- Initial projects outsourced to specialized service providers
- Knowledge transfer component in service agreements
- Gradual capability building before equipment investment
- Lower initial investment but slower capability development
- Focused Application Development:
- Identification of specific high-value applications
- Investment targeted to these limited use cases
- Expanded application scope as expertise develops
- Balanced approach to risk and capability building
- Full Capability Investment:
- Comprehensive initial investment in equipment and expertise
- Rapid capability development
- Higher initial risk but faster potential returns
- Appropriate for organizations with existing AM expertise
2. Scaling Considerations
As implementation matures, scaling strategies should consider:
- Application Expansion:
- Systematic identification of additional suitable components
- Value analysis for each potential application
- Prioritization based on financial and strategic factors
- Continuous business case development
- Capacity Management:
- Build volume optimization for maximum utilization
- Multi-shift operation consideration
- Balanced make/buy decisions for peak loading
- Strategic equipment selection for production flexibility
- Organizational Integration:
- Development of AM-specific design capabilities
- Integration with conventional manufacturing workflows
- Training program expansion
- Knowledge management systems implementation
Through comprehensive cost analysis, detailed ROI calculation, and consideration of strategic value, Parisian manufacturers can make informed decisions about implementing Inconel 625 additive manufacturing. This methodical approach ensures investments align with business objectives and deliver optimal returns.
9. FAQs About Inconel 625 Additive Manufacturing
General Information About Inconel 625 AM
Q: What makes Inconel 625 particularly suitable for additive manufacturing?
A: Inconel 625 is exceptionally well-suited for additive manufacturing due to several key characteristics:
- Excellent weldability, which translates to good processability in powder fusion AM processes
- High resistance to thermal cracking, reducing build failures
- Outstanding mechanical properties in the as-built condition
- Exceptional corrosion resistance maintained through the AM process
- Good powder recycling characteristics, improving economic viability
These properties make it one of the most widely adopted superalloys in metal additive manufacturing, particularly for applications requiring exceptional performance in harsh environments.
Q: How do the properties of AM-produced Inconel 625 compare to conventionally manufactured versions?
A: AM-produced Inconel 625 typically exhibits:
- 引張強さ: Often 5-15% higher than wrought material due to finer microstructure
- 降伏強度: Typically 10-20% higher in as-built condition
- 伸び: Usually comparable or slightly lower (30-40% vs. 40-50% for wrought)
- 耐疲労性: Potentially lower without proper post-processing due to surface roughness
- 微細構造: Finer dendritic structure with directional solidification patterns
- 異方性: Mechanical properties may vary by 5-15% depending on build orientation
- 耐食性: Generally equivalent after proper heat treatment
With appropriate post-processing, AM-produced Inconel 625 can match or exceed conventional material in most applications, while offering design freedoms impossible with traditional manufacturing.
Q: What are the typical applications for Inconel 625 AM in Paris?
A: In the Paris region, Inconel 625 AM is frequently utilized in:
- 航空宇宙
- Combustion components for aircraft engines
- Heat exchangers and thermal management systems
- Structural components for high-temperature zones
- Repair and replacement parts for legacy systems
- エネルギーだ:
- ガスタービン部品
- Heat exchanger applications
- Nuclear industry components
- Oil and gas extraction equipment
- Automotive/Racing:
- Formula 1 and motorsport exhaust systems
- ターボチャージャー部品
- Specialized high-temperature sensors
- Test equipment for extreme conditions
- 化学処理:
- Reactor components for corrosive environments
- Specialized valve bodies and flow control equipment
- Heat exchangers for aggressive media
- 触媒サポート構造
- メディカルだ:
- Specialized surgical instruments
- Custom medical devices
- Research equipment for extreme conditions
- Sterilization equipment components
Technical Questions About Implementation
Q: What are the key parameters for successful Inconel 625 printing?
A: Successful Inconel 625 printing typically relies on these critical parameters:
For Laser Powder Bed Fusion (L-PBF):
- レーザー出力: 285-350W optimal for most systems
- スキャン速度: 900-1000 mm/s for balance of quality and productivity
- 層の厚さ: 30-40μm standard for most applications
- Hatch Spacing: 0.10-0.12mm for optimal overlap
- Build Plate Temperature: 150-200°C to reduce residual stress
- Energy Density: 60-75 J/mm³ optimal range for full density
- Scan Strategy: Checkerboard or rotating pattern to reduce residual stress
For Electron Beam Melting (EBM):
- Beam Power: 600-1200W depending on feature requirements
- スキャン速度: 2000-4500 mm/s adjusted for feature type
- 層の厚さ: 50-75μm standard
- Preheat Temperature: 900-950°C critical for crack prevention
- Focus Offset: 10-15mA for optimal beam characteristics
- Scan Strategy: Specialized multibeam approaches for efficiency
These parameters may require adjustments based on specific equipment, powder characteristics, and component geometry.
Q: What are the most common challenges when implementing Inconel 625 AM, and how can they be addressed?
A: Common challenges and their solutions include:
- Residual Stress and Distortion
- 解決策 Optimize build orientation, implement proper support structures, use heated build platforms, perform in-process stress relief, and develop appropriate heat treatment cycles.
- 表面粗さ
- 解決策 Optimize process parameters for downskin surfaces, implement appropriate post-processing methods (electropolishing, vibratory finishing), and design for accessibility of finishing operations.
- Porosity and Defects
- 解決策 Use high-quality powder from reputable suppliers like メタル3DP, implement rigorous powder management protocols, optimize process parameters through test builds, and utilize in-process monitoring systems.
- Material Property Variation
- 解決策 Standardize process parameters, implement comprehensive quality systems, conduct regular material testing, and account for anisotropy in design.
- Post-Processing Complexity
- 解決策 Design parts with post-processing in mind, develop standardized post-processing workflows, invest in specialized equipment, and partner with post-processing specialists.
- Cost Management
- 解決策 Implement powder recycling protocols, optimize nesting for build efficiency, identify high-value applications, and consider hybrid manufacturing approaches.
Q: What heat treatment and post-processing steps are recommended for Inconel 625 AM parts?
A: The recommended post-processing workflow typically includes:
- 応力緩和 (mandatory)
- 870°C for 1 hour
- Furnace or argon cooling
- Performed before support removal to prevent distortion
- 熱間静水圧プレス(HIP) (for critical applications)
- 1120°C at 100-150 MPa for 3-4 hours
- Eliminates internal porosity
- Improves fatigue performance by 30-40%
- 溶体化焼鈍
- 1080°C for 1 hour
- Water quenching
- Homogenizes microstructure and dissolves undesired phases
- 表面処理
- Mechanical: Grit blasting (aluminum oxide, 100-150 μm)
- Chemical: Electropolishing in specialized solutions
- Mechanical + Chemical: Vibratory finishing followed by chemical brightening
- Machining: Critical surfaces with dimensional requirements
- Quality Verification
- Dimensional inspection: CMM or 3D scanning
- NDT: Dye penetrant, ultrasonic, or X-ray inspection
- Metallurgical: Sample evaluation for microstructure and properties
- Performance Testing: Application-specific validation
The specific protocol should be tailored to the application requirements and relevant industry standards.
Economic and Business Questions
Q: What is the typical cost structure for Inconel 625 AM parts in Paris?
A: The cost structure for Inconel 625 AM parts in Paris typically breaks down as follows:
Cost Component | Percentage of Total | 備考 |
---|---|---|
Material (Powder) | 15-25% | Depends on part density and powder recycling efficiency |
Machine Operating Costs | 25-35% | Includes depreciation, energy, gas, and consumables |
労働 | 15-20% | Includes machine operation, setup, and monitoring |
後処理 | 15-25% | Highly variable based on finishing requirements |
品質保証 | 5-15% | Depends on certification requirements and industry |
Design & Engineering | 5-10% | Higher for complex optimized designs |
Overhead & Administration | 10-15% | Includes facility costs and business operations |
For a typical aerospace component weighing 2kg, total costs in Paris range from €1,800-3,500 depending on complexity, quantity, and certification requirements.
Q: How does the ROI timeline typically look for implementing Inconel 625 AM?
A: ROI timelines vary significantly based on implementation approach and application, but typically follow these patterns:
- Service Bureau Approach (No Equipment Investment)
- Immediate ROI possible for high-value, low-volume applications
- Typical breakeven on first 5-10 projects for complex components
- Limited to applications with clear cost or performance advantages
- Focused In-House Implementation (Single Machine)
- 18-30 months to breakeven on capital investment
- Positive cash flow typically achieved within 12 months
- Full ROI accelerated by identifying high-value applications
- Comprehensive AM Implementation (Multiple Technologies)
- 24-48 months to complete ROI on full investment
- Phased positive returns as capabilities mature
- Strategic benefits often exceed direct financial returns
Key factors accelerating ROI include:
- Focusing initially on applications impossible to manufacture conventionally
- Identifying high-value use cases with significant performance advantages
- Leveraging design optimization to reduce material and weight
- Developing repeatable processes that minimize operator intervention
- Building a portfolio of applications across multiple product lines
Q: What are the intellectual property considerations for Inconel 625 AM in France?
A: Key IP considerations in the French context include:
- Patent Protection
- Process parameters may be patentable if novel and non-obvious
- Optimized designs for AM can receive patent protection
- Custom material compositions may qualify for patent protection
- French patent system follows European Patent Convention standards
- Trade Secrets
- Process parameter sets often better protected as trade secrets
- Material handling procedures and recycling protocols
- Custom post-processing techniques
- French law provides strong trade secret protection under EU Directive 2016/943
- Design Rights
- Unregistered design rights automatic but limited to 3 years
- Registered Community Designs provide 25 years of protection
- 3D scan data of AM parts may create copyright implications
- Contractual Protections
- Customer vs. manufacturer ownership of parameter sets
- Clear delineation of design ownership in service agreements
- Confidentiality provisions for powder specifications and processing details
- Data security requirements for digital design files
- 規制遵守
- CE marking requirements for end-use parts
- Documentation requirements for regulated industries
- Material traceability and process validation records
- GDPR compliance for digital manufacturing data
Working with experienced legal counsel familiar with both AM and French IP law is essential for proper protection of valuable intellectual assets.
Industry-Specific Questions
Q: How is certification handled for Inconel 625 AM parts in aerospace applications?
A: Aerospace certification for Inconel 625 AM parts in France typically follows this framework:
- Regulatory Environment
- EASA (European Union Aviation Safety Agency) regulations apply
- Specific requirements defined in EASA Part 21
- Additional requirements from prime contractors (Airbus, Safran, etc.)
- Process certification often through Nadcap (National Aerospace and Defense Contractors Accreditation Program)
- Material Qualification
- Powder must meet aerospace material specifications
- Extensive testing of mechanical and chemical properties
- Statistical process control documentation
- Batch testing and certification
- Process Qualification
- Detailed process parameter validation
- Production of test specimens and demonstration parts
- Documentation of process controls and monitoring
- Establishment of acceptable variance limits
- パート資格
- Design validation through testing and analysis
- First article inspection and approval
- Detailed documentation of post-processing
- Non-destructive testing validation
- Quality System Requirements
- AS9100D certification typically required
- Material traceability from powder to finished part
- Build monitoring and documentation
- Validated inspection methodologies
The certification process typically takes 12-18 months for a new application, with costs ranging from €100,000-300,000 depending on complexity.
Q: How are Parisian manufacturers integrating Inconel 625 AM with traditional manufacturing processes?
A: Parisian manufacturers are implementing several hybrid manufacturing approaches:
- Selective Application Strategy
- Using AM only for the most complex features
- Combining with conventional manufacturing for simpler geometries
- Example: AM complex internals joined to traditionally manufactured housings
- Additive-Subtractive Combinations
- AM to create near-net shapes
- Precision machining for critical interfaces and features
- Integrated within single manufacturing cells in advanced facilities
- Reduced setup time through specialized fixturing for AM parts
- Repair and Enhancement Applications
- Conventional components enhanced with additively manufactured features
- Repair of conventional components using directed energy deposition
- Customization of standard components with AM-added features
- Particularly valuable for legacy equipment support
- Digital Manufacturing Integration
- Digital thread connecting design, simulation, AM, and traditional processes
- Unified quality systems incorporating multiple manufacturing methods
- Shared metrology and inspection approaches
- Common material specification and testing frameworks
- Workflow Optimization
- Parallel processing of AM and conventional components
- Synchronized production planning
- Unified inventory and logistics systems
- Integrated training programs covering multiple manufacturing technologies
Leading Parisian manufacturers typically start with focused applications while developing comprehensive integration strategies for longer-term implementation.
Q: What future developments are expected in Inconel 625 AM in Paris?
A: The Parisian Inconel 625 AM ecosystem is expected to evolve in several exciting directions:
- Advanced Material Developments
- Modified Inconel 625 compositions optimized specifically for AM
- Nano-reinforced variants for enhanced properties
- Process-specific powder formulations with improved flowability and reduced oxygen content
- Multi-material capabilities combining Inconel 625 with compatible alloys
- Process Innovations
- Higher-temperature build chambers for reduced residual stress
- Multi-laser systems for increased productivity
- Integrated in-situ monitoring with closed-loop control
- Hybrid processes combining powder bed and directed energy approaches
- Application Expansion
- Greater adoption in nuclear and hydrogen energy applications
- Increased use in specialized medical devices
- Expansion into civil infrastructure for extreme environments
- Growth in custom tooling for challenging manufacturing processes
- Industry Structure Evolution
- Closer integration between powder suppliers and machine manufacturers
- Specialized post-processing service providers
- Industry-specific AM centers of excellence
- Collaborative networks sharing specialized equipment and expertise
- Educational and Workforce Developments
- Specialized AM engineering programs at Parisian universities
- Industry-academic research partnerships focused on Inconel 625
- Technical certification programs for AM operators
- Cross-training programs for conventional manufacturing experts
- Regulatory and Standards Progress
- Harmonized certification protocols across industries
- Standardized powder specifications for AM applications
- Unified testing methodologies for AM-produced superalloys
- Digital certification frameworks leveraging process monitoring data
次のような企業 メタル3DP are at the forefront of these developments, with their advanced powder technology and comprehensive 印刷方法 providing the foundation for continued innovation in Inconel 625 additive manufacturing.
Conclusion: Embracing the Future of Manufacturing with Inconel 625 AM
The adoption of Inconel 625 additive manufacturing represents a significant competitive opportunity for Parisian manufacturers across aerospace, energy, medical, and industrial sectors. By combining the exceptional material properties of this versatile superalloy with the design freedom of advanced AM processes, forward-thinking companies can achieve unprecedented performance, efficiency, and innovation.
As the technology continues to mature, successful implementation will require careful attention to material selection, process optimization, design methodology, and business strategy. Companies that develop comprehensive capabilities in Inconel 625 AM will be well-positioned to lead in high-value manufacturing sectors and address the most demanding engineering challenges of the 21st century.
For manufacturers seeking to explore the possibilities of Inconel 625 additive manufacturing, partnering with experienced material providers like Metal3DP offers a proven pathway to success. With their advanced powder technology, technical expertise, and comprehensive support capabilities, Metal3DP enables Parisian manufacturers to fully capitalize on this transformative manufacturing approach.
To learn more about implementing Inconel 625 additive manufacturing in your operations, visit Metal3DPのウェブサイト for detailed information on their powder products, technical services, and application development support.
シェアする
MET3DP Technology Co., LTDは、中国青島に本社を置く積層造形ソリューションのリーディングプロバイダーです。弊社は3Dプリンティング装置と工業用途の高性能金属粉末を専門としています。
関連記事
Met3DPについて
最新情報
製品
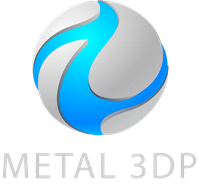
3Dプリンティングと積層造形用金属粉末