Additive Manufacturing of Jet Engine Vane Segments
目次
Introduction: The Critical Role of Vane Segments in Modern Jet Engines
The relentless pursuit of efficiency, power, and reliability in aerospace propulsion systems places immense demands on every component within a jet engine. Among the most critical are the vane segments, stationary airfoils strategically positioned within the engine’s compressor and turbine sections. These components are not merely passive structures; they are precision-engineered elements vital for directing the flow of high-pressure, high-temperature gases, optimizing engine performance, and ensuring operational safety under extreme conditions. Understanding the function and challenges associated with vane segments is fundamental to appreciating the transformative potential of advanced manufacturing techniques like metal additive manufacturing (AM).
Vane segments, often grouped into nozzle guide vanes (NGVs) in the turbine section or stator vanes in the compressor, perform the crucial task of guiding the airflow or hot gas stream onto the subsequent rotating blades (rotors) at the optimal angle and velocity. This precise directional control is paramount for maximizing energy extraction (in the turbine) or pressure increase (in the compressor). Any deviation from the intended flow path due to vane imprecision, wear, or damage can lead to significant drops in thrust, increased fuel consumption, and potentially catastrophic engine failure. The aerodynamic design of these airfoils is incredibly complex, often featuring sophisticated curves, twists, and thicknesses meticulously calculated using computational fluid dynamics (CFD) to manage shockwaves, minimize pressure losses, and ensure smooth, efficient flow transition between stages.
The environment within which these components operate, particularly in the hot sections (combustor exit and high-pressure turbine), is arguably one of the most challenging engineering arenas. Vane segments here are subjected to:
- 極端な気温: Gas temperatures exiting the combustor can exceed 1500∘C (2732∘F), pushing even advanced superalloys close to their material limits. This necessitates sophisticated internal cooling schemes and thermal barrier coatings (TBCs).
- 高圧: The compressed air and expanding combustion gases exert enormous pressure on the vane surfaces.
- Oxidative and Corrosive Attack: The high-temperature, high-velocity gas stream is chemically aggressive, leading to oxidation and hot corrosion that degrade material integrity over time.
- Thermal Cycling: Engines undergo repeated heating and cooling cycles during startup, operation, and shutdown, inducing thermal stresses that can lead to fatigue cracking.
- Vibrational Loads: High-frequency vibrations inherent in engine operation contribute to fatigue and potential fretting wear at contact points.
Traditionally, manufacturing these complex, high-performance components, especially those made from difficult-to-machine nickel-based superalloys, has relied heavily on investment casting followed by extensive secondary machining and finishing operations. While proven, casting faces limitations in producing the increasingly intricate internal cooling geometries required for next-generation engine efficiency. Furthermore, casting tooling is expensive, lead times can be long, and achieving consistent, defect-free components requires stringent process control. The need for lighter, more efficient engines with lower emissions drives innovation towards manufacturing methods that can overcome these limitations. This is where metal additive manufacturing, with its ability to build complex parts layer-by-layer directly from digital models, offers a compelling alternative, enabling designs and performance levels previously unattainable. Companies seeking reliable aerospace component suppliers そして turbine parts manufacturers are increasingly exploring AM solutions to meet these demanding OEM requirements and stringent aerospace performance standards.
Applications and Demands: Where are Vane Segments Used?
Jet engine vane segments are integral components found throughout the gas path, from the initial compression stages to the final exhaust nozzle, though their design, material, and operating conditions vary significantly depending on their location. Their primary function remains consistent: to manage airflow or gas flow direction and velocity, conditioning it for optimal interaction with the rotating blades. Understanding their specific roles in different engine sections highlights the diverse engineering challenges and the broad applicability of advanced manufacturing solutions.
Key Application Areas:
- Compressor Section (Stator Vanes):
- Function: Located between rotating compressor stages (rotors), stator vanes diffuse the airflow, converting kinetic energy (velocity) into potential energy (pressure). They redirect the swirling air exiting the rotors, preparing it for smooth entry into the next rotor stage at the correct angle.
- Operating Conditions: Temperatures and pressures progressively increase through the compressor stages, but are significantly lower than in the turbine section. Materials typically include titanium alloys, steels, or nickel alloys in the final stages.
- Design Focus: Aerodynamic efficiency, minimizing flow separation and losses, structural integrity to withstand pressure loads and vibration. Complexity can arise from variable stator vane (VSV) systems, which adjust vane angles for optimal performance across different engine speeds.
- Manufacturing Challenges: Achieving precise airfoil profiles, maintaining tight tolerances, ensuring durability against fatigue and potential foreign object damage (FOD).
- Turbine Section (Nozzle Guide Vanes – NGVs):
- Function: Positioned immediately downstream of the combustor and before each turbine rotor stage (High-Pressure Turbine – HPT, Intermediate-Pressure Turbine – IPT, Low-Pressure Turbine – LPT). NGVs accelerate the extremely hot, high-pressure gas exiting the combustor and direct it onto the turbine blades at the optimal angle to drive rotation efficiently.
- Operating Conditions: This is the harshest environment in the engine. NGVs face the highest temperatures (often exceeding the alloy’s melting point without cooling), extreme thermal gradients, high pressures, and a highly oxidative/corrosive gas stream.
- Design Focus: Maximizing aerodynamic efficiency, withstanding extreme temperatures and thermal shock, incorporating complex internal cooling passages (conformal cooling, impingement cooling, film cooling) to maintain material integrity, resisting creep deformation and oxidation/corrosion.
- Manufacturing Challenges: Producing intricate internal cooling networks, casting or fabricating from high-performance nickel or cobalt-based superalloys, applying thermal barrier coatings (TBCs), achieving high dimensional accuracy, ensuring extremely high reliability and durability. The complexity of hot gas path components makes them prime candidates for AM.
- Exhaust Section:
- Function: Vanes may be present in the exhaust nozzle, particularly in military aircraft with variable geometry or thrust-vectoring nozzles, to help shape and direct the exhaust flow for optimal thrust and maneuverability.
- Operating Conditions: Temperatures are lower than in the HPT but still significant. Focus is on aerodynamic control and durability.
- Manufacturing Challenges: Balancing weight, aerodynamic performance, and mechanical actuation systems if variable geometry is involved.
Industry Demands & B2B Considerations:
The demands placed on vane segments directly influence the requirements for manufacturers and suppliers within the aerospace supply chain. Key considerations for procurement managers and engineers include:
- 素材の性能: Sourcing materials (like the nickel superalloys discussed later) that meet stringent aerospace specifications for high-temperature strength, creep resistance, fatigue life, and environmental resistance. This involves qualifying 金属粉サプライヤー and ensuring material traceability.
- Manufacturing Precision: Achieving tight dimensional tolerances and precise airfoil contours is critical for performance. Suppliers must demonstrate robust quality control and metrology capabilities.
- Cooling Technology: For HPT NGVs, the ability to manufacture complex internal cooling passages is a key differentiator. This is a major driver towards additive manufacturing.
- 耐久性と信頼性: Vane segments are flight-critical components. Ensuring long service life and resistance to failure modes like cracking, creep, and burn-through is paramount. This impacts both メーカー production and the MRO (Maintenance, Repair, Overhaul) market, where reliable replacement parts are essential.
- 費用対効果: Balancing performance and reliability with manufacturing cost is crucial. While initial component cost matters, total lifecycle cost, including maintenance and fuel efficiency impacts, is increasingly important.
- リードタイム: Reducing manufacturing lead times, especially for complex cast components or new designs, is a significant advantage offered by AM, enabling faster development cycles and quicker MRO turnaround.
The challenges associated with conventional manufacturing of these intricate, high-temperature components, especially NGVs, have opened the door for metal AM to provide innovative solutions, meeting the ever-increasing performance demands of modern aviation.
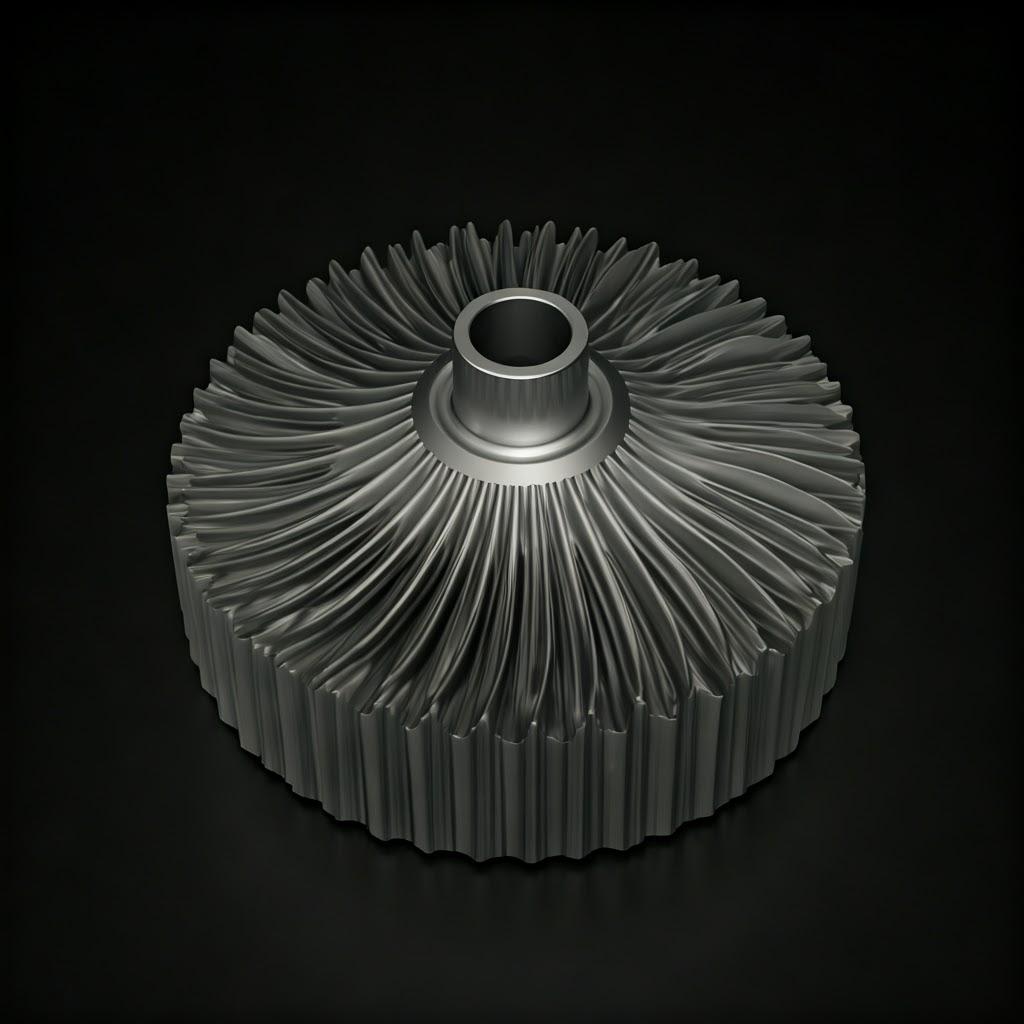
Why Metal Additive Manufacturing for Vane Segments? Advantages Over Traditional Methods
The decision to adopt metal additive manufacturing (AM), also known as metal 3Dプリンティング, for critical components like jet engine vane segments is driven by a compelling set of advantages that address the inherent limitations of traditional methods like investment casting and CNC machining, particularly when dealing with complex geometries and high-performance superalloys. While casting has been the workhorse for decades, AM offers transformative potential in design freedom, lead time reduction, material efficiency, and performance enhancement.
Comparison: AM vs. Traditional Methods for Vane Segments
特徴 | インベストメント鋳造 | CNC Machining (Subtractive) | 金属積層造形(AM) |
---|---|---|---|
幾何学的複雑性 | Moderate to High; Limited by tooling & core removal | Limited by tool access; Internal features difficult | Very High; Enables complex internal cooling, lattices, topology optimization |
内部機能 | Possible with ceramic cores (complex, fragile) | Very limited or impossible | Ideal for intricate conformal cooling channels |
素材適合性 | Well-established for superalloys | Difficult & slow for superalloys (tool wear, cost) | Excellent for superalloys (e.g., IN738LC, Rene 41); Near-net shape reduces machining |
Lead Time (Tooling) | High (Weeks to Months for mold creation) | N/A (No specific tooling) | None (Directly from CAD) |
Lead Time (Production) | Moderate (casting, cooling, finishing cycles) | Slow for complex parts / hard materials | Potentially faster for complex, low-volume parts & prototypes |
廃棄物 | Moderate (runners, gates) | High (material removed as chips) | Low (Uses only necessary material + supports) |
部品の統合 | 限定 | 限定 | High potential (combining multiple parts into one AM build) |
Design Iteration Speed | Slow (requires tooling modification) | Moderate (requires CAM reprogramming) | Fast (modify CAD file, reprint) |
Initial Setup Cost | High (Tooling) | Moderate (Fixturing, CAM) | Moderate to High (Machine cost, process development) |
Ideal Volume | Medium to High Volume | Low to Medium Volume | Low to Medium Volume, High Complexity, Customization |
Export to Sheets
Key Benefits of AM for Vane Segments:
- これまでにないデザインの自由度: This is arguably the most significant advantage. AM allows engineers to break free from the constraints imposed by casting molds and machining tool access.
- コンフォーマル冷却チャンネル: AM enables the creation of highly intricate cooling channels that follow the contour of the airfoil shape, placing cooling air precisely where it’s needed most. This leads to more effective and efficient cooling compared to the typically straight, drilled passages possible with casting, allowing for higher turbine entry temperatures (improving efficiency) or longer component life at existing temperatures.
- Topology Optimization & Lightweighting: Algorithms can optimize material placement, removing non-load-bearing material while maintaining structural integrity. This can lead to lighter vane segments, contributing to overall engine weight reduction and improved fuel economy. Lattice structures can be incorporated for stiffness and weight reduction.
- パーツの統合: Assemblies previously made of multiple cast or machined pieces can potentially be redesigned and printed as a single, monolithic component. This reduces part count, eliminates joining processes (like brazing or welding) which can be failure points, simplifies assembly, and potentially lowers overall cost.
- Reduced Lead Times for Development and Production:
- No Tooling: Eliminating the need for expensive and time-consuming casting molds drastically shortens the time from final design to first part. This accelerates rapid prototyping for aerospace applications and allows for much faster design iteration cycles.
- Faster MRO: For the MRO market, AM offers the potential for on-demand printing of replacement parts, reducing reliance on large inventories and long lead times associated with casting suppliers. This is particularly valuable for older engines where original tooling may no longer exist.
- Improved Material Efficiency:
- Near-Net Shape: AM builds parts layer by layer, using only the material required for the part and its support structures. This contrasts sharply with subtractive CNC machining, where a significant portion of expensive superalloy starting stock can end up as chips. While powder feedstock is expensive, the buy-to-fly ratio is often much better with AM.
- Reduced Machining: AM produces near-net shape parts that require significantly less final machining compared to castings, further saving time and cost, especially with difficult-to-machine superalloys.
- Enhanced Performance Potential:
- Optimized Cooling: As mentioned, superior cooling designs enabled by AM can directly translate to higher engine efficiency (due to higher allowable gas temperatures) or increased component durability (better thermal management).
- 新合金開発: AM processes, particularly powder bed fusion techniques, can sometimes process alloys that are difficult or impossible to cast or forge, opening doors for new materials with superior properties.
- Digital Manufacturing Workflow: AM is inherently digital, integrating seamlessly with CAD, simulation (CFD, FEA), and quality control systems. This enables a highly controlled, data-rich manufacturing process, crucial for flight-critical 航空宇宙部品.
While AM offers substantial benefits, it’s important to acknowledge that challenges remain (discussed in a later section). However, for complex, high-value components like jet engine vane segments operating in extreme environments, the advantages offered by metal 3D printing for aerospace—particularly the design freedom for thermal management and reduced lead times—present a compelling value proposition for OEM, MRO providers, and the entire aerospace supply chain. 次のような企業 メット3dp, with expertise in both advanced metal powders and printing systems, are pivotal in realizing this potential.
Material Focus: IN738LC and Rene 41 for High-Temperature Performance
The selection of materials for jet engine vane segments, especially those operating in the high-pressure turbine section, is dictated by the extreme conditions they endure. Only a select group of materials, primarily nickel-based superalloys, possess the necessary combination of high-temperature strength, creep resistance, fatigue life, and resistance to oxidation and hot corrosion. Among the leading candidates frequently considered for additive manufacturing of these demanding components are IN738LC (Inconel 738 Low Carbon) and Rene 41. Understanding their properties is crucial for engineers and procurement managers sourcing 金属粉サプライヤー or AM services.
Nickel-Based Superalloys: The Foundation
Nickel-based superalloys derive their exceptional high-temperature capabilities from their specific microstructure. They typically consist of:
- Austenitic FCC Matrix (Gamma – γ): The primary nickel-rich phase provides good baseline ductility and corrosion resistance.
- Precipitates (Gamma Prime – γ′): Coherent, ordered precipitates, primarily Ni3(Al,Ti), are finely dispersed within the matrix. These γ′ precipitates are the key strengthening mechanism at high temperatures, impeding dislocation movement. The volume fraction, size, and stability of γ′ are critical design parameters.
- Carbides: Carbides (e.g., MC, M23C6, M6C) form at grain boundaries and within grains. They contribute to grain boundary strength and inhibit grain boundary sliding, but excessive or unfavorable carbide morphologies can reduce ductility and fatigue life.
- Solid Solution Strengtheners: Elements like Cobalt (Co), Molybdenum (Mo), Tungsten (W), and Chromium (Cr) dissolve into the gamma matrix, providing additional strength. Cr is also vital for oxidation and corrosion resistance by forming a protective chromium oxide layer (Cr2O3).
IN738LC (Inconel 738 Low Carbon)
IN738LC is a precipitation-hardenable nickel-based superalloy widely used in the hot sections of gas turbines, particularly for blades and vanes, primarily manufactured via investment casting. Its adaptation to additive manufacturing processes like Selective Laser Melting (SLM) / Laser Powder Bed Fusion (LPBF) and Electron Beam Melting (EBM) / Selective Electron Beam Melting (SEBM) is an area of active development and application.
- 主な特徴
- Excellent High-Temperature Strength: Maintains significant strength up to temperatures around 980∘C (1800∘F).
- 優れたクリープ耐性: Resists deformation under sustained load at high temperatures, critical for components under centrifugal (blades) or gas pressure (vanes) loads.
- Superior Hot Corrosion Resistance: High chromium content (around 16%) provides excellent resistance to sulfidation and oxidation encountered in turbine environments, often outperforming alloys like IN718 in this regard.
- Microstructural Stability: Designed for stability during long-term exposure to high temperatures.
- Low Carbon Variant: The “LC” denotes Low Carbon content compared to the original IN738. This is specifically aimed at improving weldability and reducing susceptibility to strain-age cracking, which is highly relevant for the layer-by-layer fusion process inherent in AM.
- Composition (Typical Weight %):
- Ni: Balance (~61%)
- Cr: 15.7-16.3%
- Co: 8.0-9.0%
- Mo: 1.5-2.0%
- W: 2.4-2.8%
- Ta: 1.5-2.0%
- Nb: 0.6-1.1%
- Al: 3.2-3.7%
- Ti: 3.2-3.7%
- C: 0.09-0.13% (Low Carbon target)
- B: 0.007-0.012%
- Zr: 0.03-0.08%
- Relevance for AM: IN738LC’s susceptibility to cracking during welding/solidification makes it challenging for AM processes, particularly LPBF. Careful control over process parameters (laser power, scan speed, layer thickness, preheating) and optimized heat treatments (including HIP) are essential to achieve dense, crack-free parts with the desired microstructure and mechanical properties. SEBM, with its high vacuum environment and elevated build chamber temperatures, can offer advantages in processing crack-sensitive alloys like IN738LC. Sourcing high-quality, spherical IN738LCパウダー with controlled particle size distribution and low oxygen content is critical for successful printing. Companies like Met3dp, utilizing advanced gas atomization, focus on producing powders optimized for AM processes, ensuring good flowability and consistent melting behavior crucial for high-temperature alloy AM.
ルネ41
Rene 41 is another well-established precipitation-strengthened nickel-based superalloy known for its exceptional strength at elevated temperatures, making it suitable for demanding aerospace applications including turbine components, afterburner parts, and high-performance fasteners.
- 主な特徴
- Very High Strength: Exhibits excellent tensile and yield strength up to approximately 870∘C (1600∘F). It offers higher strength than many other superalloys in the 650−980∘C (1200−1800∘F) range.
- Good Oxidation Resistance: Suitable for use in oxidizing atmospheres encountered in jet engines.
- Age-Hardenable: Strength is developed through heat treatment processes that precipitate the strengthening γ′ phase.
- Fabricability Challenges: Known to be difficult to machine and weld in the aged condition due to its high strength. AM offers near-net shape benefits, reducing post-machining needs.
- Composition (Typical Weight %):
- Ni: Balance (~55%)
- Cr: 18.0-20.0%
- Co: 10.0-12.0%
- Mo: 9.0-10.5%
- Ti: 3.0-3.3%
- Al: 1.4-1.8%
- Fe: 5.0% Max
- C: 0.06-0.12%
- B: 0.003-0.01%
- Relevance for AM: Similar to IN738LC, Rene 41 presents challenges for AM due to its high γ′ content and susceptibility to solidification cracking and strain-age cracking during post-weld heat treatment (analogous to AM thermal cycles). Achieving optimal AM parameters requires careful development to control the thermal history of the material. Preheating the build plate/chamber, optimizing scan strategies to manage thermal gradients, and developing specific post-build heat treatment cycles (including solution annealing, aging, and potentially HIP) are crucial for obtaining the required microstructure and mechanical properties. High-quality Rene 41 powder with controlled chemistry and morphology is essential. Met3dp’s commitment to producing high-sphericity, good flowability powders through techniques like gas atomization and PREP technology directly addresses the need for reliable feedstock for demanding alloys like Rene 41, positioning them as a key nickel superalloy powder distributor and AM solutions provider.
材料選択の考慮事項:
The choice between IN738LC and Rene 41 (or other superalloys like Hastelloy X, Haynes 282, CM247LC) for a specific vane segment depends on:
- Maximum Operating Temperature: Rene 41 generally offers higher strength at intermediate high temperatures, while IN738LC might be preferred for its hot corrosion resistance at slightly higher temperatures or specific creep requirements.
- Corrosion/Oxidation Environment: IN738LC’s higher Cr content typically provides better resistance to hot corrosion.
- 製造工程: The specific AM process used (LPBF vs. SEBM) can influence material processability and final properties. SEBM’s higher processing temperatures can be beneficial for crack-prone alloys.
- 後処理の要件: The complexity and cost associated with necessary heat treatments (HIP, aging) and finishing.
- Certification Requirements: Ensuring the chosen material and process combination can meet stringent aerospace material specifications and certification standards (e.g., AMS specifications).
Partnering with a knowledgeable metal AM service provider または material supplier like Met3dp, which has experience processing these challenging high-temperature superalloys and understands the nuances of powder quality and process optimization, is critical for successfully implementing AM for jet engine vane segments. Exploring Met3dp’s extensive product portfolio can provide insight into the range of high-performance metal powders available for such demanding applications.
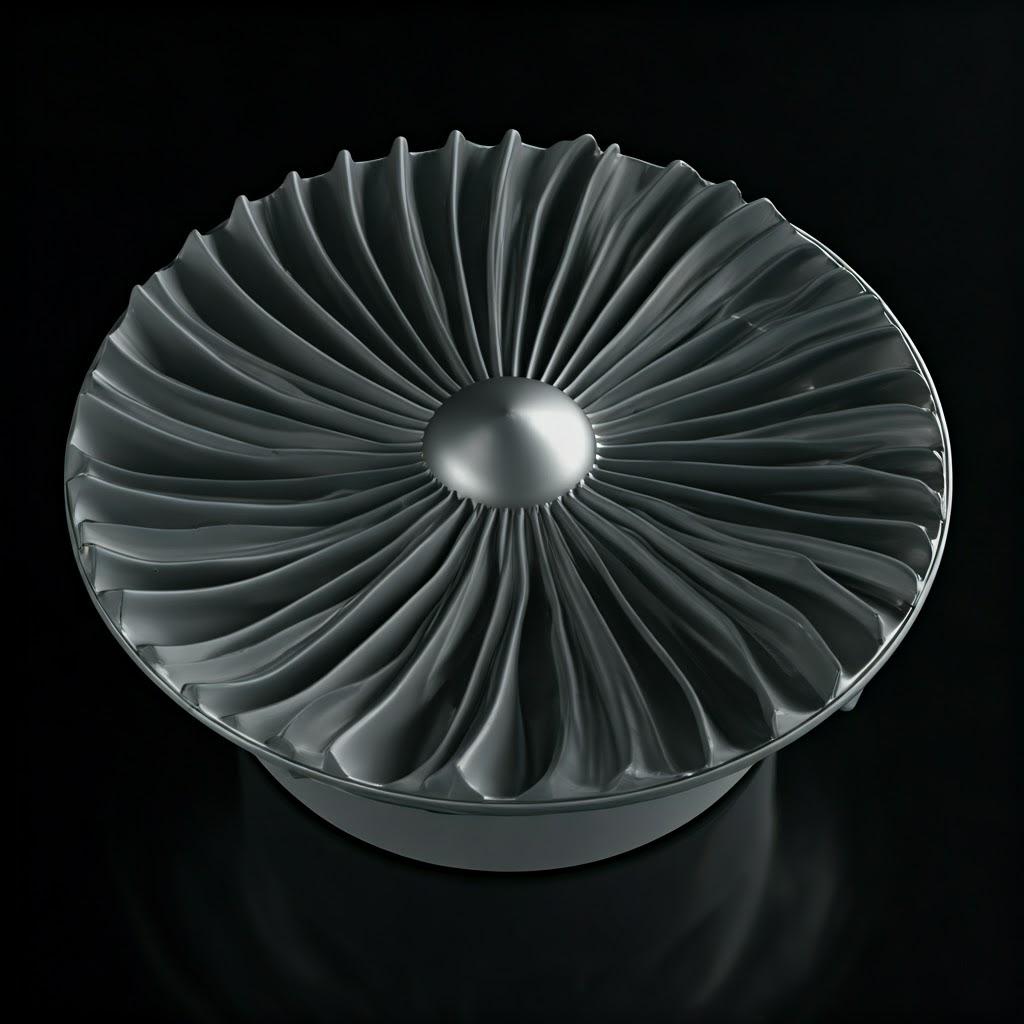
Design for Additive Manufacturing (DfAM): Optimizing Vane Segments
Simply replicating a design intended for casting or machining using additive manufacturing often fails to capture the true potential of the technology and can even introduce new manufacturing challenges. To fully leverage the benefits of AM for complex components like jet engine vane segments, engineers must embrace 積層造形設計 (DfAM) principles. DfAM is not just about ensuring a part できる be printed; it’s about optimizing the design to enhance performance, reduce weight, minimize production costs, and improve manufacturability using AM processes like Laser Powder Bed Fusion (LPBF) or Selective Electron Beam Melting (SEBM). For demanding aerospace component design, DfAM is becoming an indispensable skill.
Key DfAM Principles for AM Vane Segments:
- Leveraging Geometric Freedom for Performance:
- Conformal Cooling: This is a primary driver for using AM in hot section vanes (NGVs). DfAM encourages designing cooling channels that precisely follow the 3D contours of the airfoil, including leading and trailing edges. This allows for:
- More uniform temperature distribution across the vane surface.
- Reduced peak metal temperatures.
- Minimized thermal gradients, reducing stress and improving fatigue life.
- More efficient use of cooling air, potentially reducing bleed air requirements and improving overall engine efficiency.
- Integration of advanced cooling features like turbulators, trip strips, or optimized impingement holes directly into the AM build.
- Complex Aerodynamic Shapes: AM removes many constraints on airfoil geometry, allowing for more aggressive twists, curves, and optimized profiles derived from advanced CFD simulation for AM, potentially improving aerodynamic efficiency beyond what’s easily achievable with casting.
- Conformal Cooling: This is a primary driver for using AM in hot section vanes (NGVs). DfAM encourages designing cooling channels that precisely follow the 3D contours of the airfoil, including leading and trailing edges. This allows for:
- Topology Optimization and Lightweighting:
- Material Reduction: Software tools can analyze the stress distribution within a vane segment under operational loads and intelligently remove material from low-stress regions, while reinforcing critical areas. This can lead to significant weight savings compared to traditionally manufactured parts, contributing to better fuel efficiency and thrust-to-weight ratios.
- 格子構造: Internal lattice or gyroid structures can be incorporated to provide structural support with minimal mass. However, considerations for thermal conductivity, cleanability (powder removal), and inspectability are crucial when using lattices in vane applications.
- 部品の統合:
- Identify opportunities to combine multiple components (e.g., separate airfoil, platform segments, mounting features) into a single, monolithic printed part. This reduces assembly time and cost, eliminates potential failure points at joints (brazing, welding), and simplifies the supply chain. Careful consideration must be given to printing orientation, support structures, and potential residual stress in consolidated designs.
- Support Structure Strategy:
- Support structures are often necessary in PBF processes to anchor the part to the build plate, support overhanging features (typically angles below 45 degrees from the horizontal), and manage thermal stresses during the build.
- Minimization: Design features to be self-supporting wherever possible (e.g., using chamfers or fillets instead of sharp overhangs).
- アクセシビリティ: Ensure supports are placed in locations where they can be effectively removed during post-processing without damaging the part. Internal supports within complex cooling channels are extremely difficult or impossible to remove and must be avoided through careful design or orientation choices.
- 熱管理: Supports also act as heat sinks. Their placement and density can influence local cooling rates and resulting residual stress and microstructure.
- Feature Size and Wall Thickness:
- AM processes have limitations on minimum printable feature size (e.g., diameter of cooling holes) and minimum wall thickness. These depend on the specific machine, process parameters (beam spot size, layer thickness), and material (powder characteristics). Designs must respect these limits to ensure features are accurately reproduced and structurally sound. Trailing edges, often very thin, require careful consideration.
- Orientation Optimization:
- The orientation of the vane segment on the build plate significantly impacts:
- 表面仕上げ: Up-facing and down-facing surfaces have different roughness characteristics. Vertical walls generally achieve better finishes. Critical aerodynamic surfaces should be oriented optimally.
- Support Requirements: Affects the amount and location of support structures needed.
- ビルドタイム: Z-height is a primary driver of build time.
- 機械的特性: Anisotropy (direction-dependent properties) can occur in AM parts; orientation affects stress direction relative to build layers.
- 残留応力: Orientation influences thermal gradients and stress accumulation.
- The orientation of the vane segment on the build plate significantly impacts:
- Powder Removal:
- Internal channels and complex features must be designed to allow for the complete removal of unfused powder after the build. Trapped powder can add weight, potentially sinter during heat treatment (causing blockages or defects), and interfere with inspections or coatings. Escape holes might need to be incorporated.
- Designing for Post-Processing:
- Consider subsequent steps like heat treatment (HIP accessibility), machining (adding sacrificial material or locating features), inspection (NDT accessibility), and coating. For example, ensure surfaces requiring tight tolerances have sufficient stock material for finish machining.
Implementing DfAM effectively often requires close collaboration between design engineers, materials scientists, and AM process specialists. Utilizing simulation tools for thermal, structural, and fluid dynamics analysis tailored for AM processes is highly recommended. Engaging with experienced aerospace engineering design partners or DfAM services can significantly accelerate the adoption curve and maximize the benefits of additive manufacturing for jet engine vane segments.
Achievable Precision: Tolerance, Surface Finish, and Dimensional Accuracy in AM Vanes
While additive manufacturing offers remarkable geometric freedom, achieving the tight tolerances, specific surface finishes, and high dimensional accuracy required for flight-critical components like jet engine vane segments necessitates a clear understanding of AM process capabilities and often involves secondary finishing operations. Engineers and procurement managers must have realistic expectations about the “as-built” state of AM parts versus the final component requirements defined by aerospace tolerances and performance standards.
Factors Influencing Precision in Metal AM (LPBF/SEBM):
- Machine Calibration & Accuracy: The precision of the laser/electron beam positioning system, scanner calibration, and overall machine stability are fundamental. Reputable providers like Met3dp invest heavily in printers delivering industry-leading print volume, accuracy, and reliability, which forms the baseline for achievable precision.
- Process Parameters: Laser/electron beam power, scan speed, layer thickness, beam spot size, hatch spacing, and contour parameters significantly impact melt pool stability, solidification behavior, and thus dimensional accuracy and surface finish.
- パウダーの特徴 Particle size distribution (PSD), morphology (sphericity), and flowability of the metal powder (e.g., IN738LC, Rene 41) affect powder bed density, melting consistency, and final part quality. High-quality powders, such as those produced using Met3dp’s advanced gas atomization, contribute to better precision.
- Thermal Effects: Residual stresses built up during the rapid heating and cooling cycles can cause warping and distortion, impacting overall dimensional accuracy. Preheating (especially in SEBM), optimized scan strategies, and post-build stress relief are crucial for mitigation.
- Part Geometry & Orientation: Complex shapes, large overhangs requiring extensive supports, and tall, thin features are inherently more challenging to produce with high accuracy. Orientation affects surface finish and potential for distortion.
- サポート体制: Supports influence thermal behavior and can leave witness marks upon removal, affecting surface finish and sometimes local accuracy.
Typical As-Built Capabilities:
It’s crucial to consult specific provider capabilities, but general expectations for nickel superalloys via PBF are:
- 寸法精度:
- Typically in the range of ±0.1 mm to ±0.3 mm (±0.004” to ±0.012”) for smaller dimensions, or ±0.1% to ±0.2% of the nominal dimension for larger features.
- SEBM often has slightly looser tolerances than LPBF due to higher processing temperatures causing some sintering and potential part growth, but offers advantages in reduced residual stress.
- Accuracy can vary significantly depending on the feature’s size, location, and orientation within the build.
- Surface Finish (Roughness – Ra):
- As-Built: Highly dependent on orientation and whether it’s an up-facing, down-facing (supported), or vertical surface.
- Vertical Walls: Often achieve the best finish, potentially Ra 6 – 12μm (240 – 470μin).
- Up-facing Surfaces: Generally smoother than down-facing, Ra 10 – 20μm (390 – 790μin).
- Down-facing Surfaces (Supported): Typically the roughest due to contact with support structures, potentially Ra 15 – 30μm (590 – 1180μin) or higher.
- Internal Channels: Roughness can be higher and harder to improve via post-processing.
- Aerodynamic Requirements: Critical airfoil surfaces often require much smoother finishes (e.g., Ra 1.6μm or better) than achievable in the as-built state, necessitating polishing or machining.
- As-Built: Highly dependent on orientation and whether it’s an up-facing, down-facing (supported), or vertical surface.
Bridging the Gap: Post-Machining and Quality Control:
For most jet engine vane applications, the as-built precision of AM parts is insufficient for critical features.
- Targeted Machining: CNC machining is typically required for:
- Mating surfaces (e.g., platform interfaces, shroud connections).
- Airfoil leading and trailing edges (if extremely tight profiles are needed).
- Seal slots or grooves.
- Drilling/reaming of critical location holes.
- Achieving very smooth aerodynamic surfaces if required beyond what polishing can achieve.
- 表面仕上げ: Techniques like abrasive flow machining (AFM), electrochemical polishing, or manual polishing may be used to improve surface finish, especially on external airfoil surfaces, reducing friction and improving aerodynamic performance.
- 品質保証: Rigorous inspection is mandatory.
- Coordinate Measuring Machines (CMM): Used for verifying critical dimensions against the CAD model and engineering drawings.
- 3D Scanning: Provides a full-field comparison of the manufactured part geometry against the nominal design.
- 表面粗さ測定: Using profilometers to verify surface finish requirements.
- NDT (Non-Destructive Testing): Crucial for internal integrity checks (discussed later).
Engaging with an AM service provider who understands these requirements and has integrated 精密積層造形 with robust post-machining capabilities and stringent quality assurance supplier protocols (like AS9100 certification) is essential. Met3dp’s focus on high-accuracy 金属3Dプリンティング systems provides a strong foundation, but achieving final part requirements is a holistic process involving DfAM, controlled printing, and meticulous post-processing and inspection.
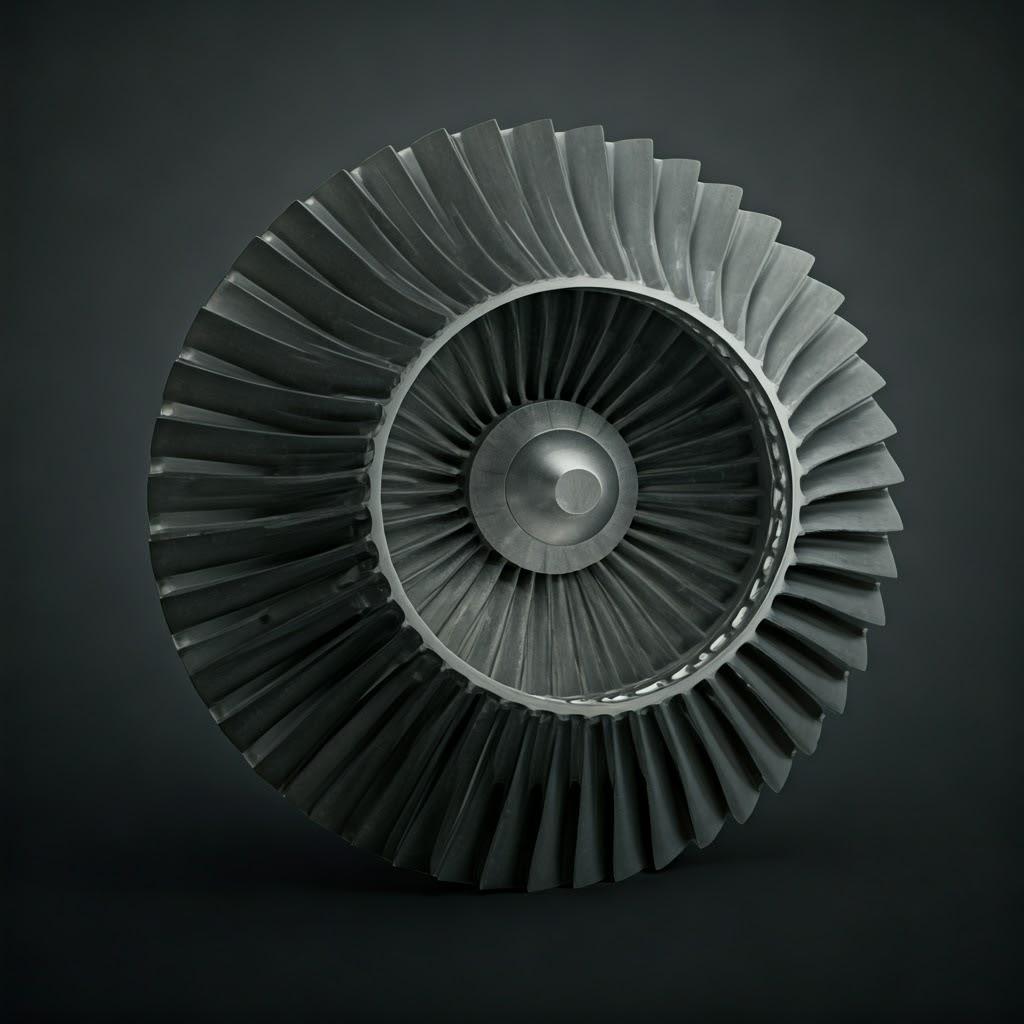
Essential Post-Processing Steps for AM Vane Segments
The journey of an additively manufactured jet engine vane segment doesn’t end when the printer stops. The “green” part, fresh off the build plate, requires a sequence of critical post-processing steps to transform it into a functional, reliable aerospace component. These steps are essential for relieving stress, removing temporary structures, achieving required material properties, ensuring dimensional accuracy, applying protective coatings, and verifying integrity. Neglecting or improperly executing any of these stages can compromise the part’s performance and safety. Companies offering aerospace post-processing services play a vital role in the AM ecosystem.
Common Post-Processing Workflow for AM Superalloy Vanes:
- Powder Removal:
- Immediately after the build finishes and the chamber cools sufficiently, the build job is removed.
- The bulk of the unfused powder surrounding the parts is recovered (often sieved and reused).
- Parts require careful cleaning using compressed air, vibration, or specialized depowdering stations to remove trapped powder, especially from internal channels and complex features. This step is critical to prevent issues in subsequent heat treatment or operation.
- ストレス解消:
- Due to the rapid heating/cooling cycles inherent in PBF, significant residual stresses build up within the part while it’s still attached to the build plate.
- A thermal stress relief cycle is typically performed before removing the part from the build plate. This involves heating the entire assembly (part + plate) in a furnace to a specific temperature (below the aging temperature for the alloy), holding it, and then slowly cooling.
- This reduces the risk of cracking or distortion when the part is subsequently cut from the plate.
- Part Removal from Build Plate:
- Once stress-relieved, the vane segment(s) are separated from the build plate.
- Common methods include wire Electrical Discharge Machining (EDM) or band sawing. Care must be taken not to damage the parts during this process.
- 支持構造の撤去:
- The temporary support structures need to be removed. This can be challenging, especially for dense supports or those in difficult-to-reach areas.
- Methods include:
- Manual removal (breaking, pliers – suitable for easily accessible, lighter supports).
- Machining (milling away support interfaces).
- EDM (for precise removal near critical surfaces).
- Witness marks left by supports often need to be blended or machined smooth.
- 熱処理:
- This is arguably the most critical post-processing stage for achieving the desired mechanical properties in precipitation-hardenable superalloys like IN738LC and Rene 41. The as-built microstructure is often non-ideal (fine grains, chemical segregation, non-optimized precipitates).
- 熱間静水圧プレス(HIP): This is frequently mandatory for critical aerospace parts. Parts are subjected to high temperature (below solutioning temp) and high inert gas pressure (e.g., Argon) simultaneously in a specialized vessel. HIP effectively closes internal porosity (gas and lack-of-fusion pores) leading to full densification, improved fatigue life, ductility, and reduced property scatter. HIP services are specialized but essential for AM aerospace components.
- ソリューション・アニーリング: Heating the part to a high temperature to dissolve precipitates and create a homogeneous solid solution, followed by rapid cooling (quenching).
- Aging Treatment(s): Heating to one or more intermediate temperatures for specific durations to precipitate the strengthening γ′ phase with the desired size, morphology, and distribution. Specific superalloy heat treatment cycles are tailored to the alloy and desired properties (e.g., optimizing for creep vs. fatigue).
- Machining / Finishing:
- As discussed previously, CNC machining is used to achieve final tolerances on critical dimensions, mating surfaces, seal slots, and potentially airfoil profiles.
- Grinding, polishing, or other surface finishing techniques may be applied to meet surface finish standards, particularly for aerodynamic surfaces. Reliable CNC machining aerospace parts suppliers often work closely with AM providers.
- コーティング:
- For vanes operating in the hottest turbine sections (NGVs), application of a Thermal Barrier Coating (TBC) is standard practice.
- TBCs are multi-layered ceramic coatings (typically Yttria-Stabilized Zirconia – YSZ) applied over a metallic bond coat (often MCrAlY type).
- They provide thermal insulation, significantly reducing the metal surface temperature and protecting against oxidation and hot corrosion, thereby extending component life. Surface preparation before coating is critical.
- 非破壊検査(NDT):
- Essential for verifying the internal and external integrity of the final part without damaging it.
- Computed Tomography (CT Scanning): Increasingly used for AM parts, providing a full 3D view to detect internal voids, inclusions, cracks, and trapped powder, as well as verify complex internal channel geometry.
- Fluorescent Penetrant Inspection (FPI): Detects surface-breaking cracks and defects.
- Radiography (X-ray): Can detect internal voids and inclusions.
- Ultrasonic Testing: Can detect subsurface defects.
- 厳格な NDT for additive manufacturing protocols are required for part certification.
The specific sequence and parameters of these post-processing steps must be carefully developed and validated for each specific vane design, material, and application to ensure the final part meets all performance and safety requirements.
Navigating Challenges in Additive Manufacturing of Vane Segments
While metal AM offers significant advantages for producing jet engine vane segments, the technology is not without its challenges, especially when working with high-performance superalloys and aiming for flight-critical applications. Successfully navigating these hurdles requires deep process understanding, meticulous control, robust quality management, and often, advanced simulation and monitoring techniques. Awareness of these potential issues is crucial for both AM providers and their customers.
Key Challenges and Mitigation Strategies:
- Residual Stress and Distortion/Cracking:
- チャレンジ: The rapid, localized heating and cooling cycles inherent in PBF processes create steep thermal gradients, leading to the build-up of internal stresses. These stresses can cause part distortion (warping), detachment from the build plate, or even cracking, particularly in complex geometries or crack-sensitive materials like IN738LC or Rene 41.
- Mitigation:
- Preheating: Maintaining the build chamber and/or build plate at elevated temperatures (common in SEBM, increasingly used in LPBF for superalloys) reduces thermal gradients.
- Optimized Scan Strategies: Using techniques like island scanning, checkerboard patterns, or optimized scan vector lengths and rotations helps distribute heat more evenly and reduce stress accumulation.
- サポート体制: Properly designed supports help anchor the part and conduct heat away.
- Process Simulation: 使用 AM process simulation software to predict temperature fields and stress accumulation allows for optimization of orientation and support strategy before printing.
- Post-Build Stress Relief: Performing a thermal stress relief cycle before removing the part from the build plate is critical.
- Porosity Defects:
- チャレンジ: Internal voids or pores can act as stress concentrators, significantly reducing fatigue life and mechanical properties. Porosity can arise from:
- Gas Porosity: Trapped gas (e.g., Argon shielding gas, dissolved gas in powder) forming spherical pores.
- Lack-of-Fusion Porosity: Insufficient energy input or improper melting leading to voids between layers or scan tracks (often irregular in shape).
- Mitigation:
- Parameter Optimization: Careful development and control of process parameters (power, speed, hatch spacing, layer thickness) to ensure complete melting and fusion.
- Powder Quality Control: Using high-quality powder with low internal porosity and controlled gas content. Maintaining powder dryness and proper handling to avoid moisture pickup. Met3dp’s advanced powder making system focuses on achieving low porosity feedstock.
- Shielding Gas Control: Ensuring proper inert gas flow and chamber atmosphere control during printing (especially in LPBF).
- 熱間静水圧プレス(HIP): Highly effective at closing both gas and lack-of-fusion pores, achieving near-full density. Often mandatory for critical parts.
- チャレンジ: Internal voids or pores can act as stress concentrators, significantly reducing fatigue life and mechanical properties. Porosity can arise from:
- 支持構造の撤去:
- チャレンジ: While essential during the build, supports must be removed afterward. Removal can be time-consuming, costly, and risks damaging the part, especially with intricate internal cooling channels where supports are generally unacceptable and must be designed out.
- Mitigation:
- DfAM: Designing for self-supporting angles (typically >45 degrees) and minimizing overhangs. Orienting the part to reduce support needs.
- Optimized Support Design: Using support structures (e.g., lattice supports, conical supports) that are strong enough during the build but easier to remove. Designing breakaway points.
- Advanced Removal Techniques: Employing careful manual removal, CNC machining, or EDM where necessary.
- Microstructure Control:
- チャレンジ: The rapid solidification inherent in AM leads to fine-grained microstructures, which can differ significantly from coarser-grained cast components. Achieving the desired grain structure (columnar vs. equiaxed), phase distribution (e.g., γ′ size and morphology), and minimizing detrimental phases (like certain carbides) requires careful control over thermal history.
- Mitigation:
- Process Parameter Control: Beam parameters and scan strategies influence solidification conditions.
- Tailored Heat Treatments: Developing specific post-build heat treatment cycles (solutioning, aging, potentially HIP) to homogenize the microstructure and precipitate strengthening phases correctly is critical for superalloy heat treatment. This often requires significant development effort compared to established casting protocols.
- Powder Management and Contamination:
- チャレンジ: Superalloys can be sensitive to contamination (e.g., oxygen pickup, cross-contamination from other materials). Maintaining powder quality throughout handling, storage, printing, and recycling is crucial. Powder degradation over multiple reuse cycles can affect part quality.
- Mitigation:
- Strict Handling Protocols: Using dedicated equipment, controlled atmosphere glove boxes, proper sieving procedures, and tracking powder history/reuse cycles.
- Powder Quality Monitoring: Regularly testing powder chemistry, PSD, and flowability.
- High-Quality Virgin Powder: Starting with high-purity, low-oxygen powder from reputable 金属粉サプライヤー.
- Process Monitoring and Quality Control:
- チャレンジ: Ensuring consistency and quality layer-by-layer throughout a potentially long build process requires robust monitoring and control. Detecting defects early is crucial.
- Mitigation:
- In-situ Monitoring: Implementing systems like melt pool monitoring (using cameras or photodiodes), thermal imaging, or layer imaging to detect anomalies during the build.
- Machine Calibration & Maintenance: Regular checks and calibration of laser/electron beam systems, gas flow, temperature sensors, etc.
- Rigorous NDT: Comprehensive post-build inspection using CT scanning and other methods as part of the AM quality control framework.
- Certification and Qualification:
- チャレンジ: Establishing the process repeatability and reliability required to meet stringent aerospace performance standards and achieve certification for flight-critical components is a complex and lengthy process. This involves demonstrating statistically consistent material properties and part performance.
- Mitigation:
- 標準化: Adhering to developing industry standards (ASTM, ISO, SAE) for AM processes, materials, and testing.
- Process Validation: Extensive testing and documentation to establish a stable, repeatable manufacturing process (Process Specification).
- Material Allowables: Generating statistically significant material property data for AM materials comparable to existing databases for cast/wrought alloys.
- Partnership: Working closely with certification authorities (FAA, EASA) and experienced certified AM production partners.
Successfully overcoming these aerospace manufacturing challenges requires a combination of advanced technology, materials science expertise, rigorous process control, and a commitment to quality. Partnering with an experienced AM provider like Met3dp, which understands the nuances of different 印刷方法 and has experience with demanding superalloys, is essential for mitigating risks and realizing the benefits of AM for jet engine vane segments.
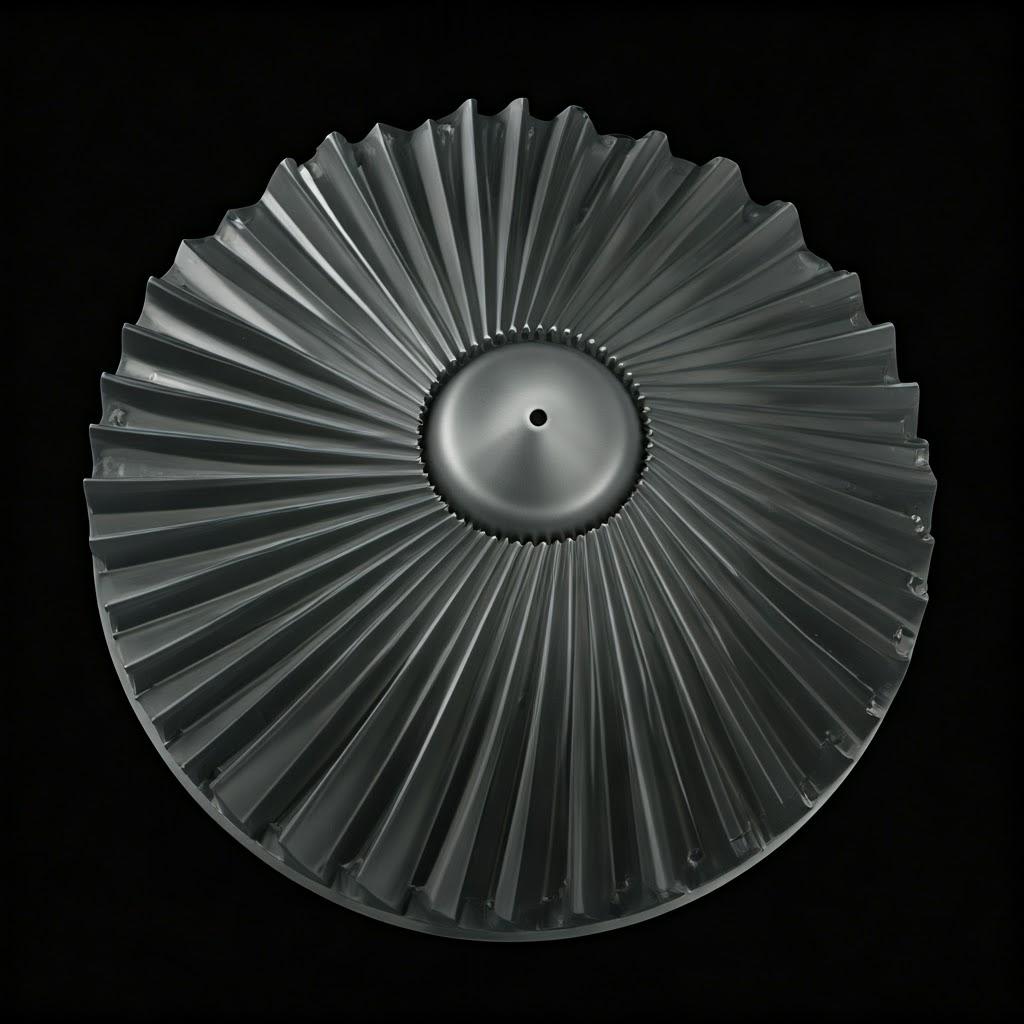
Selecting Your Partner: How to Choose the Right Metal AM Service Provider
The successful adoption of additive manufacturing for demanding applications like jet engine vane segments hinges not only on the technology itself but significantly on the expertise, capabilities, and quality commitment of your chosen AM service provider or manufacturing partner. Selecting the right B2B additive manufacturing partner is a critical decision for engineers and procurement managers navigating the aerospace supply chain. The provider must demonstrate proficiency not just in printing, but across the entire value chain, from design consultation to final part qualification.
Key Criteria for Evaluating Metal AM Service Providers:
- Aerospace Certifications and Quality Management System (QMS):
- AS9100 Certification: This is non-negotiable for suppliers involved in manufacturing flight-critical aerospace components. AS9100 builds upon ISO 9001, adding specific requirements for quality, safety, and reliability demanded by the aerospace industry. Verify the provider’s certification status and scope.
- Robust QMS: Look for evidence of a mature QMS covering all aspects: process control, material traceability, document management, calibration, non-conformance handling, corrective actions, and continuous improvement.
- Proven Experience with Relevant Materials and Processes:
- Superalloy Expertise: The provider must have demonstrable experience successfully printing the specific nickel-based superalloys required (e.g., IN738LC, Rene 41). Ask for case studies, material property data from their processes, and evidence of parameter development for these challenging materials.
- Process Mastery (LPBF/SEBM): Deep understanding of the chosen AM process (Laser Powder Bed Fusion or Selective Electron Beam Melting) is crucial. This includes knowledge of how process parameters affect microstructure, defects, and mechanical properties in the specific alloys. Companies like Met3dp, offering solutions like advanced SEBM プリンター, bring specific process advantages for certain alloys.
- Equipment Capabilities and Capacity:
- Machine Quality & Maintenance: Are they using industrial-grade, well-maintained AM systems from reputable manufacturers? Enquire about their machine calibration and preventative maintenance schedules. Met3dp prides itself on printers delivering industry-leading print volume, accuracy, and reliability.
- ビルド・ボリューム: Ensure their machines can accommodate the size of your vane segments.
- Process Monitoring: Do their machines incorporate in-situ monitoring capabilities (melt pool monitoring, thermal imaging) to enhance quality control?
- Capacity: Can they meet your required production volumes and lead times?
- Powder Handling and Management:
- Stringent Protocols: Given the sensitivity of superalloys to contamination, evaluate their procedures for powder receiving inspection, storage (controlled environment), handling (use of glove boxes), sieving, traceability (batch tracking), and recycling/reuse protocols. Cross-contamination control is paramount.
- Powder Sourcing: Do they source high-quality powder from reputable 金属粉サプライヤー, or like Met3dp, possess advanced powder making systems (e.g., gas atomization, PREP) ensuring optimal powder characteristics (sphericity, flowability, low oxygen)?
- Integrated Post-Processing Capabilities:
- Comprehensive Services: Ideally, the provider should offer or manage a seamless workflow including stress relief, part removal, support removal, heat treatment (including HIP services), CNC machining, surface finishing, NDT, and coating preparation.
- Qualified Partners: If certain processes (like HIP, specialized NDT, or TBC coating) are outsourced, ensure they use qualified and approved vendors who also meet aerospace standards. Managing these external processes efficiently is key to reliable end-to-end AM solutions.
- Engineering and Technical Support:
- DfAM Expertise: Can they provide expert guidance on Design for Additive Manufacturing to optimize your vane segment design for performance and manufacturability?
- Metallurgical Support: Access to materials scientists or metallurgists knowledgeable about superalloys and AM process-property relationships is invaluable.
- Simulation Capabilities: Experience with AM process simulation can help predict and mitigate risks like distortion.
- Project Management and Communication:
- Clear communication channels, defined project milestones, regular updates, and responsive customer service are essential for complex projects.
- Track Record and Financial Stability:
- Look for a provider with a proven history of delivering high-quality aerospace components. Customer references and case studies are valuable.
- Assess the provider’s financial stability, especially for long-term production programs.
Choosing a partner like メット3dp, which combines expertise in advanced SEBM printers, high-quality metal powder production, and a deep understanding of additive manufacturing applications, can significantly de-risk the process of implementing AM for critical components. Their focus on providing comprehensive solutions makes them a strong contender for organizations seeking a reliable aerospace AM supplier.
Understanding Cost Drivers and Lead Times for AM Vane Segments
While additive manufacturing offers compelling technical benefits, understanding the economic factors – cost and lead time – is crucial for making informed decisions about its adoption for jet engine vane segments. Both metal 3D printing price structures and delivery timelines differ from traditional manufacturing methods like casting.
Key Cost Drivers in Metal AM:
- 金属粉のコスト:
- Nickel-based superalloys like IN738LC and Rene 41 are inherently expensive raw materials due to their elemental composition (high Ni, Co, Nb, Ta content) and the sophisticated atomization processes required to produce high-quality, spherical powders suitable for AM. Powder cost is often a significant portion of the final part cost, typically priced per kilogram.
- Powder reuse (recycling unfused powder) helps mitigate costs, but requires careful management and testing to ensure quality is maintained over multiple cycles. The efficiency of powder usage (buy-to-fly ratio) is generally better in AM than subtractive machining but needs careful tracking.
- AM Machine Time:
- Industrial metal AM systems represent a significant capital investment, and their operational costs (energy, inert gas, maintenance) contribute to hourly machine rates.
- Print time is primarily driven by the total volume of the part(s) being printed and the Z-height of the build. Factors influencing build time include:
- Part Complexity & Volume: Larger, denser parts take longer.
- 層の厚さ: Thinner layers improve resolution but increase build time.
- Scan Strategy & Parameters: Optimized parameters balance speed and quality.
- Nesting & Build Density: Printing multiple parts simultaneously can improve machine utilization but may extend overall build time.
- 人件費:
- Skilled labor is required for various stages:
- Build Preparation: CAD file processing, support generation, build setup.
- Machine Operation & Monitoring.
- 後処理: Depowdering, part removal, support removal, finishing (often manual effort involved).
- Skilled labor is required for various stages:
- 後処理費用:
- These can be substantial and must be fully accounted for:
- Stress Relief & Heat Treatment: Furnace time and energy consumption.
- HIP (Hot Isostatic Pressing): Specialized equipment and processing cycles add significant cost but are often necessary for critical parts.
- サポートの取り外し: Can be labor-intensive or require machining/EDM time.
- CNC Machining: Cost depends on the extent of machining required, material hardness, and tolerance requirements.
- Surface Finishing & Coating: Costs associated with polishing, TBC application, etc.
- NDT & Inspection: Equipment and specialized technician time (e.g., CT scanning analysis).
- These can be substantial and must be fully accounted for:
- Non-Recurring Engineering (NRE) Costs:
- For new part designs or materials, significant upfront effort may be needed for DfAM, process parameter development, material characterization, and process qualification/certification. These NRE costs are typically amortized over the production volume.
- Quality Assurance & Certification Costs:
- Maintaining AS9100 certification, performing rigorous inspections, material testing, and documentation all contribute to overhead costs reflected in part pricing.
Lead Time Considerations:
AM offers distinct advantages in lead time, particularly for prototypes and complex, low-volume parts, contributing to supply chain optimization in aerospace.
- Tooling Elimination: The most significant lead time saving compared to investment casting is the elimination of mold design and fabrication time (weeks to months).
- ラピッドプロトタイピング: New designs or iterations can be printed directly from CAD files within days or weeks, enabling much faster development cycles.
- Production Lead Time Components:
- Design & Prep: Finalizing DfAM, simulation, build file preparation (hours to days).
- Print Time: Can range from hours for small parts to many days for large, complex builds or full build plates.
- Cooling & Depowdering: Hours.
- 後処理: This often dictates the overall lead time. Stress relief, HIP cycles, heat treatment, machining queues, NDT, and coating can collectively take days to weeks, depending on complexity and supplier scheduling/capacity. HIP, in particular, can be a bottleneck as it’s often done in batches.
- Inspection & Shipping: Days.
- Comparison to Casting: While casting production cycles might be relatively fast once tooling exists, the initial tooling lead time is long. For established parts, casting might be faster for very high volumes. However, for new designs, replacements (MRO), or complex parts requiring intricate cores, AM often provides a significantly shorter overall time-to-part. Bulk order additive manufacturing requires careful planning around machine capacity and post-processing workflows.
Calculating the true additive manufacturing ROI requires considering not just the per-part cost but also the value of reduced lead times, design flexibility, potential performance improvements, and simplified supply chains (e.g., part consolidation, reduced inventory).
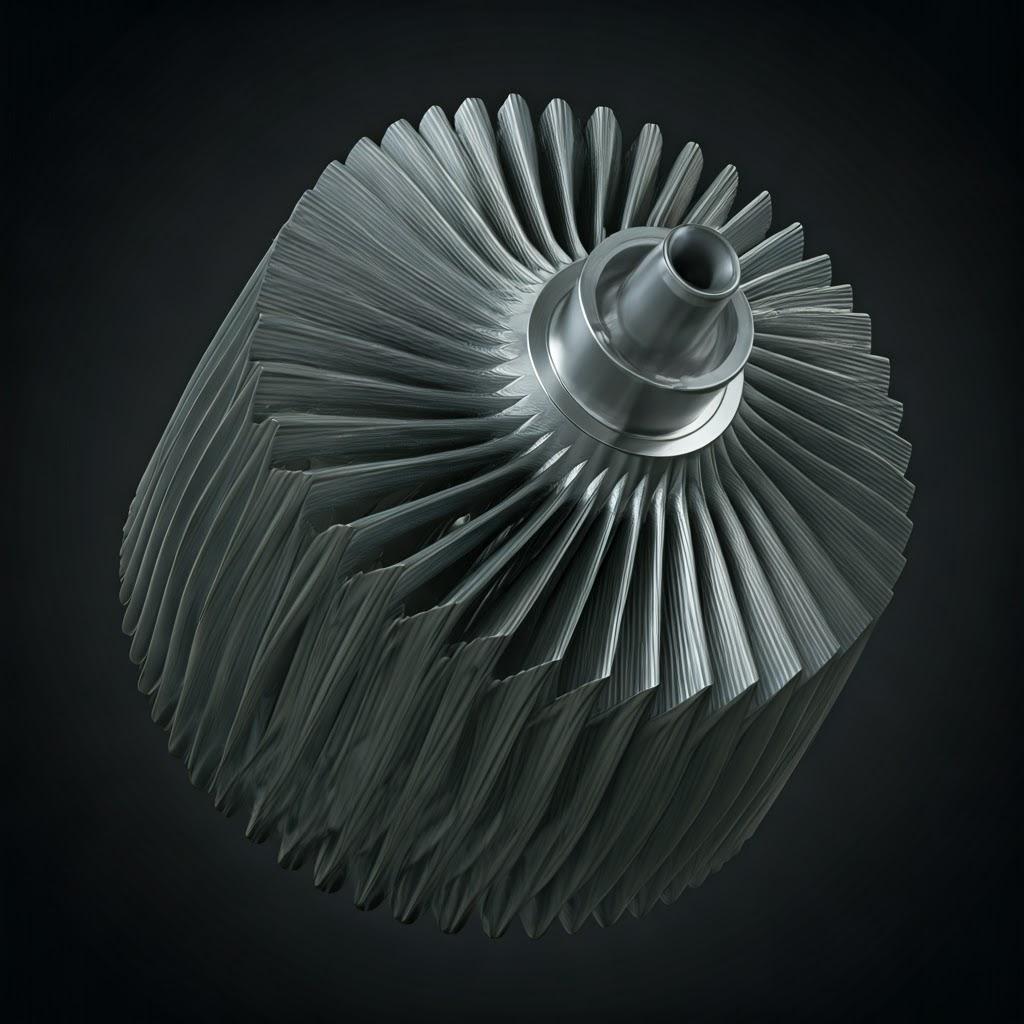
Frequently Asked Questions (FAQ) about AM for Jet Engine Vanes
Here are answers to some common questions regarding the use of additive manufacturing for producing jet engine vane segments:
- How do the mechanical properties of additively manufactured superalloys (like IN738LC or Rene 41) compare to their traditionally cast counterparts?
- With optimized AM process parameters, appropriate post-processing including Hot Isostatic Pressing (HIP) and tailored heat treatments, the mechanical properties of AM superalloys can be comparable to, and sometimes even exceed, those of cast materials. AM typically results in a finer grain structure, which can enhance fatigue strength. However, properties like creep resistance might behave differently and require specific validation for the AM microstructure. Tensile strength, yield strength, and ductility can meet or exceed cast specifications after proper HIP and heat treatment cycles designed specifically for the AM material’s characteristics. Rigorous testing and qualification are essential to confirm properties for any specific application, ensuring they meet demanding aerospace material specifications.
- Is metal AM significantly more expensive than investment casting for vane segments?
- The cost comparison is highly dependent on several factors:
- パート・コンプレックス: For highly complex designs with intricate internal cooling channels that are difficult or impossible to cast, AM can be cost-competitive or even cheaper due to the elimination of complex cores and associated yield losses.
- 生産量: For very high volumes of relatively simple designs where casting tooling is already established, casting is often more cost-effective per part. AM excels in low-to-medium volume production, prototyping, and situations where design flexibility or rapid iteration is needed.
- 金型費用: AM avoids the high upfront cost and long lead time associated with casting tooling. This makes it advantageous for new product introductions or MRO replacements.
- Material & Post-Processing: The cost of superalloy powders and extensive post-processing (HIP, machining, NDT) significantly impacts the final AM part cost.
- A total cost of ownership analysis, considering lead time, design benefits (e.g., efficiency gains from better cooling), and supply chain simplification, is necessary for a true comparison beyond the initial aerospace component pricing.
- The cost comparison is highly dependent on several factors:
- Is additive manufacturing mature enough for serial production of flight-critical vane segments in commercial or military engines?
- Yes, metal additive manufacturing is increasingly being adopted for the serial production of certain flight-critical components, including vane segments and other static parts, by major aerospace OEMs. The technology has matured significantly in terms of process stability, monitoring, and quality control. However, implementation requires:
- 厳格な process validation aerospace protocols.
- Establishment of stable, repeatable manufacturing processes.
- Comprehensive NDT and quality assurance procedures.
- Full certification by relevant airworthiness authorities (e.g., FAA, EASA).
- Development of robust material property databases and design allowables for AM materials.
- While adoption is growing, it’s still often applied strategically to components where AM offers the clearest benefits (e.g., complex cooling, part consolidation, specific alloys). Certified AM production is a reality but demands significant investment and expertise.
- Yes, metal additive manufacturing is increasingly being adopted for the serial production of certain flight-critical components, including vane segments and other static parts, by major aerospace OEMs. The technology has matured significantly in terms of process stability, monitoring, and quality control. However, implementation requires:
- What are the primary limitations on the complexity of internal cooling passages that can be created using AM?
- AM enables significantly more complex cooling geometries than casting, including conformal cooling channels, micro-features like turbulators, and optimized branching networks. However, limitations exist:
- Minimum Feature Size: Determined by the AM process resolution (beam spot size, layer thickness).
- Powder Removal: Channels must be designed to allow for complete removal of unfused powder after printing. Dead-end pockets or overly tortuous paths can be problematic.
- サポート体制: Internal supports are generally avoided as they cannot be removed. Designs must rely on self-supporting angles or optimized orientations.
- Inspection: Verifying the internal geometry and cleanliness of complex channels requires advanced NDT like high-resolution CT scanning.
- AM enables significantly more complex cooling geometries than casting, including conformal cooling channels, micro-features like turbulators, and optimized branching networks. However, limitations exist:
Conclusion: Elevating Aerospace Propulsion with Additive Manufacturing
The journey through the intricacies of additively manufacturing jet engine vane segments reveals a technology poised to redefine the boundaries of aerospace propulsion. Metal AM, particularly utilizing high-performance nickel-based superalloys like IN738LC and Rene 41, offers a paradigm shift away from the constraints of traditional casting and machining. The ability to create highly complex geometries, most notably optimized conformal cooling channels, directly translates into the potential for engines that run hotter, are more fuel-efficient, produce fewer emissions, and offer enhanced durability.
The advantages extend beyond pure performance; the リードタイムの短縮 enabled by tool-less manufacturing accelerate development cycles and offer unprecedented responsiveness for MRO operations. The principles of DfAM unlock lightweighting opportunities through topology optimization and lattice structures, while パート統合 simplifies designs and improves reliability. While challenges related to residual stress, microstructure control, post-processing complexity, and certification remain, they are being actively addressed through advancements in process simulation, in-situ monitoring, tailored heat treatments, and the development of robust industry standards.
Successfully harnessing the power of AM for these critical components requires more than just access to a printer. It demands a holistic approach encompassing deep materials science expertise, meticulous process control, rigorous quality assurance, and strategic partnerships. Choosing the right metal AM service provider—one with proven aerospace credentials (AS9100), demonstrated success with superalloys, comprehensive post-processing capabilities, and strong engineering support—is paramount.
Met3dp stands at the forefront of this digital manufacturing transformation.と。 our deep expertise spanning advanced metal powder production using industry-leading techniques, state-of-the-art SEBM printing solutions known for accuracy and reliability, and a commitment to comprehensive application support, Met3dp empowers aerospace innovators. We partner with organizations to navigate the complexities of AM adoption, from design optimization to final part qualification, enabling the realization of next-generation propulsion systems.
について future of aerospace manufacturing is undeniably intertwined with additive manufacturing. For components like jet engine vane segments operating at the heart of the turbine, AM is not just an alternative manufacturing method; it is an enabling technology, paving the way for levels of performance, efficiency, and design innovation previously thought impossible. Contact Met3dp to explore how our capabilities can power your organization’s additive manufacturing goals and help shape the future of flight.
シェアする
MET3DP Technology Co., LTDは、中国青島に本社を置く積層造形ソリューションのリーディングプロバイダーです。弊社は3Dプリンティング装置と工業用途の高性能金属粉末を専門としています。
関連記事
Met3DPについて
最新情報
製品
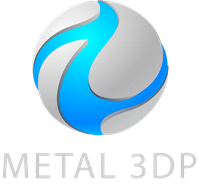
3Dプリンティングと積層造形用金属粉末