Reinforced Lever Arms via Maraging Steel Additive Manufacturing
目次
Introduction: The Critical Role of High-Strength Levers and the Maraging Steel AM Solution
Lever arms are fundamental mechanical components found across countless industrial applications, translating input force into amplified output force or motion. From the intricate actuation systems in aerospace landing gear to the robust linkages in heavy industrial machinery, the reliability and strength of these components are often paramount. Failure is rarely an option, particularly when levers operate under extreme loads, high fatigue cycles, or demanding environmental conditions. Traditionally, manufacturing high-strength lever arms involved subtractive methods like CNC machining from billet stock or forging, processes that, while established, come with limitations in geometric complexity, material waste, and potentially long lead times, especially for custom or low-volume requirements.
Enter the transformative power of 金属積層造形(AM), specifically utilizing high-performance materials like M300 (also known as 1.2709) maraging steel. This combination presents a paradigm shift for designing and producing reinforced lever arms that meet and often exceed the performance benchmarks of their conventionally manufactured counterparts. Maraging steels are a class of low-carbon, ultra-high-strength steels renowned for their exceptional strength, hardness, and toughness, achieved through a relatively simple low-temperature aging heat treatment after fabrication. When processed via AM techniques such as Powder Bed Fusion – Laser Beam (PBF-LB, often referred to as SLM or DMLS), M300 allows for the creation of lever arms with intricate internal structures, optimized topologies for superior strength-to-weight ratios, and consolidated designs that were previously impossible or prohibitively expensive to manufacture.
The synergy between M300’s inherent material properties and the design freedom afforded by AM unlocks significant advantages for engineers and procurement managers in sectors including:
- 航空宇宙 Creating lightweight yet robust actuation levers, control surface linkages, and structural brackets.
- 自動車: Producing high-performance suspension components, customized tooling levers, and engine parts for motorsport and specialized vehicles.
- メディカルだ: Manufacturing strong, durable levers for surgical instruments and medical devices (though biocompatibility considerations are separate).
- 産業製造: Fabricating heavy-duty levers for automation systems, robotics, specialized machinery, and high-pressure tooling applications.
For B2B clients, including 卸売業者, industrial parts suppliersそして 販売店, sourcing M300 AM lever arms offers access to cutting-edge component technology, enabling the supply of superior parts with potential benefits in performance, customization, and supply chain agility. As a leading provider of 付加製造ソリューション, Met3dp leverages its deep expertise in both advanced metal powders and industrial printing systems to deliver high-quality, reliable M300 maraging steel components, including mission-critical lever arms. Our commitment to industry-leading print volume, accuracy, and reliability ensures that parts meet the stringent requirements of demanding applications.
This blog series will delve into the specifics of utilizing M300 maraging steel via additive manufacturing for reinforced lever arms, covering everything from applications and material properties to design considerations, post-processing, quality control, and supplier selection.
Applications: Where Reinforced Maraging Steel Levers Excel
The unique combination of ultra-high strength, good toughness, and manufacturability via AM makes M300 maraging steel lever arms ideal candidates for applications where performance under extreme conditions is non-negotiable. Traditional materials or manufacturing methods might struggle to meet the complex demands of modern engineering challenges, paving the way for M300 AM levers to provide superior solutions. Key application areas include:
- 航空宇宙と防衛
- Actuation Systems: Levers within flight control surface actuators (ailerons, elevators, rudders), landing gear deployment and retraction mechanisms, and thrust reverser systems demand exceptional strength-to-weight ratios and fatigue resistance. M300 AM allows for topology-optimized designs that minimize weight while maximizing structural integrity under cyclic loading.
- Structural Brackets and Linkages: Connecting critical components within airframes or defense systems where high loads and vibration are present. AM enables complex geometries that integrate multiple functions, reducing part count and assembly complexity.
- Missile Components: Fins, control actuators, and internal structural elements requiring high strength in compact forms.
- Automotive (Performance and Specialized):
- Suspension Components: Control arms, pushrods, and bell cranks in racing or high-performance vehicles benefit from M300’s high strength and stiffness, allowing for lightweight designs that improve handling dynamics.
- Engine and Drivetrain: High-stress levers within valve trains, transmission systems, or customized engine modifications.
- Tooling and Fixturing: Durable, wear-resistant levers for assembly line fixtures, robotic end-effectors, and specialized manufacturing tools where longevity and precision are key. The ability to integrate conformal cooling channels via AM can significantly enhance the performance of tooling levers used in high-temperature processes like plastic injection molding.
- Industrial Machinery and Automation:
- Heavy-Duty Linkages: Levers in large presses, construction equipment, mining machinery, and agricultural implements where high impact loads and abrasive wear are common. M300’s strength and hardness provide durability.
- ロボット工学: Arms and linkages in industrial robots requiring high stiffness, precision, and payload capacity within a compact envelope. AM allows for customized designs tailored to specific robotic tasks.
- Specialized Equipment: Levers used in high-pressure systems (e.g., hydraulics), process automation, and bespoke manufacturing equipment where off-the-shelf components are inadequate.
- Tooling and Mold Making:
- Injection Mold Components: While often thought of for inserts, lever-like mechanisms within complex molds (e.g., lifters, slides) can benefit from M300’s high strength and wear resistance, especially when intricate cooling or ejection features are needed. AM facilitates the creation of these complex internal geometries.
- Die Casting Components: Levers and mechanisms within die-casting tools exposed to high thermal and mechanical stresses.
- Fixtures and Jigs: Creating robust and precise levers for workholding and assembly fixtures requiring long-term durability and dimensional stability.
Table: Example Applications and Benefits of M300 AM Levers
産業分野 | 適用例 | Key Benefit of M300 AM | Relevant B2B Interest |
---|---|---|---|
航空宇宙 | Flight Control Actuator Lever | High Strength-to-Weight Ratio, Fatigue Resistance | Aerospace Component Supplier, MRO |
Automotive (Performance) | Suspension Bell Crank | Lightweighting, High Stiffness, Custom Geometry | Performance Parts Distributor, OEM |
産業機械 | Heavy Press Linkage | Extreme Load Bearing Capacity, Wear Resistance | Industrial Equipment Manufacturer, Wholesaler |
Automation/Robotics | Robot Arm Lever | High Precision, Stiffness, Complex Integrated Features | Robotics Integrator, Automation Supplier |
工具 | Injection Mold Lifter Mechanism | Wear Resistance, Ability to Integrate Conformal Cooling | Mold Making Company, Tooling Supplier |
ディフェンス | Missile Fin Actuation Lever | High Strength, Compact Design, Reliability | Defense Contractor, Systems Integrator |
Export to Sheets
Procurement managers and engineers seeking a custom lever supplier capable of handling demanding requirements will find that M300 additive manufacturing offers unparalleled design flexibility coupled with exceptional material performance, enabling solutions previously unattainable.
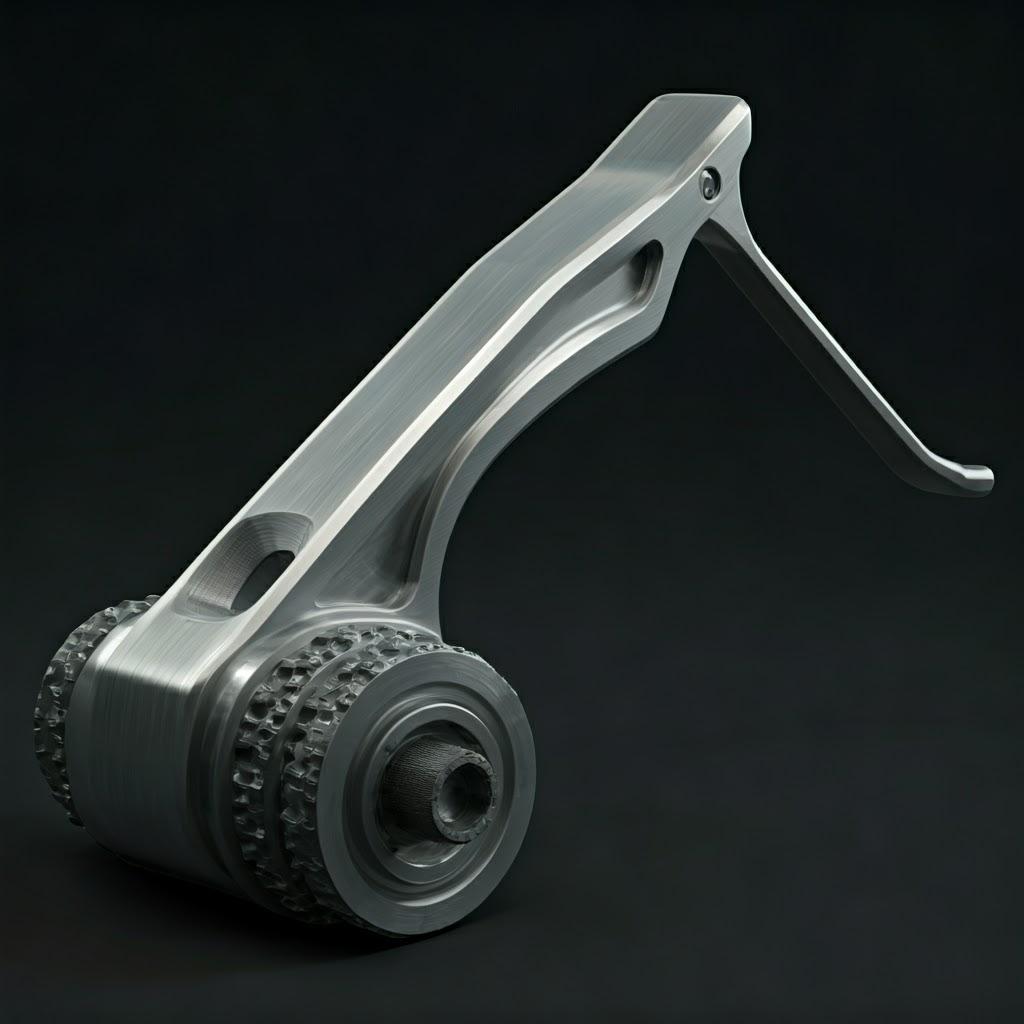
Why Choose Metal Additive Manufacturing for Lever Arm Production?
While traditional manufacturing methods like CNC machining, casting, and forging have long served the industry, metal additive manufacturing offers a compelling suite of advantages, particularly for high-strength, complex components like reinforced lever arms made from M300 maraging steel. Understanding these benefits is crucial for engineers optimizing designs and procurement managers evaluating production strategies.
1. Unparalleled Geometric Freedom:
- Complex Shapes: AM builds parts layer-by-layer, enabling the creation of intricate internal channels (e.g., for hydraulic fluid or cooling), complex external shapes, and organic forms derived from topology optimization algorithms. This allows levers to be designed purely for functional performance, often resulting in lighter and stronger parts compared to those constrained by traditional manufacturing limitations.
- Topology Optimization: Software can computationally determine the most efficient material distribution within a defined design space to withstand specific loads. AM is often the only viable way to manufacture these highly optimized, often organic-looking, lever designs, leading to significant weight savings without compromising strength – critical in aerospace and automotive applications.
- Internal Lattice Structures: Lightweight yet strong internal lattice structures can be incorporated into the lever’s design, further reducing mass while maintaining stiffness and strength where needed.
2. Part Consolidation:
- Multiple components that would traditionally be manufactured separately and then assembled (e.g., a lever arm, its pivot bosses, mounting brackets) can often be redesigned and printed as a single, monolithic part.
- メリット Reduces assembly time and labor, eliminates potential points of failure at joints (welds, fasteners), simplifies inventory management, and often leads to a lighter and stronger overall system. This is a significant advantage for wholesale additive manufacturing providers aiming to streamline customer supply chains.
3. Material Efficiency:
- AM is an “additive” process, meaning material is only added where it’s needed. This contrasts sharply with subtractive methods like CNC machining, where a significant portion of expensive billet material (like M300) can end up as waste chips.
- While some support structures are needed in AM and require removal, the overall material utilization is typically much higher, reducing raw material costs and environmental impact, especially for complex parts or expensive alloys.
4. Rapid Prototyping and Iteration:
- AM allows designers and engineers to quickly produce functional prototypes of lever arms directly from CAD models.
- This accelerates the design-test-iterate cycle significantly compared to waiting for traditional tooling or complex machining setups. Design flaws can be identified and corrected faster, leading to a better final product in less time.
5. Customization and Low-Volume Production:
- AM requires no part-specific tooling (like molds or dies). This makes it economically viable to produce highly customized lever arms or small batches tailored to specific applications or customer requirements.
- Ideal for specialized machinery, replacement parts for legacy systems, or performance upgrades where mass production isn’t feasible or necessary.
6. Enhanced Performance Potential:
- Beyond lightweighting, the design freedom allows for integrating features that enhance performance. For tooling levers used in processes like injection molding, integrated conformal cooling channels following the contours of the lever can dramatically improve cooling efficiency, reduce cycle times, and enhance the quality of the molded part.
Table: AM vs. Traditional Manufacturing for High-Strength Levers
特徴 | Metal Additive Manufacturing (PBF-LB) | CNC Machining (Subtractive) | Casting / Forging |
---|---|---|---|
幾何学的複雑性 | Very High (Internal channels, lattices) | Moderate to High (Limited internal) | Low to Moderate (Tooling dependent) |
部品の統合 | 素晴らしい | 限定 | 限定 |
廃棄物 | Low (Supports + some powder loss) | High (Chip generation) | Moderate (Gates, risers, flash) |
Lead Time (Prototype) | 速い | Moderate to Fast | Slow (Tooling required) |
Lead Time (Production) | Moderate (Machine time dependent) | Fast (For simpler parts) | Fast (Once tooling exists) |
金型費用 | なし | Low (Fixturing) | 非常に高い |
Ideal Volume | Low to Medium, High Customization | Low to High (Less complex parts) | High Volume (Standardized parts) |
トポロジー最適化 | Highly Suitable | Difficult / Impossible to Manufacture | Very Difficult / Impossible |
内部機能 | 素晴らしい | Very Limited / Impossible | Limited (Cores required) |
Strength (M300) | Excellent (Near wrought post-processing) | Excellent (Wrought properties) | Good (Can have porosity/defects) |
Export to Sheets
While CNC machining offers excellent precision and surface finish, and casting/forging excel at high-volume production of simpler shapes, 金属積層造形 provides a unique blend of design freedom, material efficiency, and performance enhancement capabilities that make it the superior choice for producing complex, high-strength M300 maraging steel lever arms, especially for demanding, customized, or weight-sensitive applications. Companies like Met3dp, specializing in both the printing process and 高品質の金属粉, are key enablers of this technological advantage.
Material Focus: M300 (1.2709) Maraging Steel Powder Properties and Advantages
The performance of any 3Dプリント component is intrinsically linked to the quality and properties of the raw material used. For high-strength lever arms demanding exceptional mechanical performance, M300 maraging steel (also identified by Werkstoff number 1.2709) is a standout choice within the additive manufacturing landscape. Understanding its characteristics is vital for appreciating why it’s selected for such critical applications.
M300 belongs to the maraging steel family, characterized by their very low carbon content (typically <0.03%) and high alloy composition, primarily Nickel (Ni), Cobalt (Co), Molybdenum (Mo), and Titanium (Ti). Unlike conventional steels that gain hardness through carbon and quenching, maraging steels achieve their remarkable strength through the precipitation of intermetallic compounds during a relatively low-temperature aging heat treatment (~480-500°C) after the initial printing process (which leaves the material in a softer, solution-annealed state).
Key Properties of M300 Maraging Steel for AM:
- 超高強度: After proper aging heat treatment, M300 typically achieves ultimate tensile strengths (UTS) exceeding 1900-2000 MPa (275-290 ksi) and yield strengths (YS) around 1800-1950 MPa (260-280 ksi). This exceptional strength allows lever arms to withstand enormous forces without permanent deformation.
- Good Toughness: Despite its high strength and hardness (typically 50-55 HRC after aging), M300 retains reasonable toughness and ductility (elongation at break often 5-10%). This is crucial for lever arms, as it provides resistance to fracture under impact or sudden load application, preventing brittle failure.
- 高い硬度と耐摩耗性: The high hardness achieved after aging translates directly to excellent wear resistance, essential for levers experiencing sliding or abrasive contact with other components.
- Good Machinability (After Aging): While very strong, aged M300 exhibits good machinability, comparable to other tool steels of similar hardness. This is important because critical features, mating surfaces, or bearing bores on 3D printed levers often require finish machining to achieve tight tolerances or specific surface finishes. Machinability in the softer, as-printed state is even better.
- Excellent Dimensional Stability During Aging: The precipitation hardening process occurs with minimal distortion and predictable, near-uniform volumetric shrinkage (typically around 0.05-0.1%). This allows designers to accurately compensate for size changes during heat treatment, ensuring dimensional accuracy in the final part.
- Good Weldability (Relevant for AM): The low carbon content gives maraging steels good weldability characteristics. This is fundamentally important for powder bed fusion processes, which essentially involve microscopic welding layer by layer. It results in dense, metallurgically sound parts with minimal risk of hot cracking during the build process.
Table: Typical Mechanical Properties of M300 (1.2709) After Additive Manufacturing and Aging
プロパティ | Typical Value Range (Metric) | Typical Value Range (Imperial) | Significance for Lever Arms |
---|---|---|---|
極限引張強さ(UTS) | 1900 – 2100 MPa | 275 – 305 ksi | Maximum stress the lever can withstand before fracture. |
Yield Strength (YS, 0.2%) | 1800 - 2000 MPa | 260 – 290 ksi | Stress level at which permanent deformation begins. |
硬度 | 50 – 55 HRC | – | Resistance to scratching, indentation, and wear. |
破断伸度 | 5 – 10 % | 5 – 10 % | Ductility; ability to deform before fracturing (toughness indicator). |
弾性係数 | ~180 – 190 GPa | ~26 – 27.5 Msi | Stiffness; resistance to elastic deformation under load. |
密度 | ~8.0 – 8.1 g/cm³ | ~0.29 lb/in³ | Affects weight and inertia. |
Export to Sheets
(Note: Exact properties depend on specific AM process parameters, build orientation, and heat treatment cycle. These are representative values.)
The Importance of Powder Quality:
The success of printing M300 parts hinges critically on the quality of the metal powder feedstock. An additive manufacturing materials supplier like Met3dp understands that factors such as:
- 真球度: Highly spherical powder particles ensure good flowability within the AM machine’s recoater system, leading to uniform powder layers and reducing the risk of voids or defects.
- 粒度分布(PSD): A controlled PSD is essential for achieving high packing density in the powder bed, contributing to fully dense final parts with optimal mechanical properties.
- Purity and Chemistry: Strict control over the alloy composition and minimization of impurities (like oxygen and nitrogen) are vital for consistent material properties and preventing defects during printing and heat treatment.
- 流動性: Ensures consistent powder deposition across the build plate, layer after layer.
Met3dp employs industry-leading powder production technologies, including advanced ガス噴霧 そして プラズマ回転電極プロセス(PREP) システムである。 Our gas atomization utilizes unique nozzle and gas flow designs to produce M300 powders with exceptional sphericity and flowability. Coupled with rigorous quality control, we ensure our Met3dp metal powders meet the stringent requirements for producing high-integrity, high-performance M300 maraging steel components, including critical lever arms demanded by wholesale buyers and industrial clients. The inherent advantages of M300, combined with high-quality powder and precise AM processing, make it the premier choice for reinforced levers in demanding applications. Sources and related content
Design for Additive Manufacturing (DfAM): Optimizing Lever Arms for Printing
Simply replicating a design intended for CNC machining or casting using additive manufacturing often fails to leverage the full potential of the technology and can even introduce new challenges. Designing にとって Additive Manufacturing (DfAM) is a critical philosophy that optimizes parts like high-strength lever arms specifically for the layer-by-layer PBF-LB process using M300 maraging steel. Applying DfAM principles not only enhances performance but can also significantly reduce costs associated with material usage, print time, and post-processing efforts – key considerations for industrial component suppliers そして volume purchasers.
Here are essential DfAM considerations for M300 lever arms:
- Leverage Geometric Freedom – Think Additively:
- Topology Optimization: Utilize specialized software to remove material from non-critical areas while maintaining structural integrity under defined load cases. This often results in organic, bone-like structures that are significantly lighter yet just as strong or stronger than bulky, traditionally designed levers. AM is uniquely capable of producing these complex forms.
- Internal Lattices: Incorporate internal lattice structures within thicker sections of the lever. These can drastically reduce weight and material consumption while providing tailored stiffness and strength characteristics. Different lattice types (e.g., cubic, gyroid, diamond) offer varying properties.
- パーツの統合: Analyze adjacent components or features (brackets, mounts, bosses) and explore redesigning them into a single, integrated lever arm print. This eliminates assembly steps, fasteners, and potential failure points.
- Integrated Functionality: Design internal channels for hydraulics, lubrication, sensor wiring, or conformal cooling (especially relevant if the lever functions as part of a tool).
- Minimize and Optimize Support Structures:
- Orientation Strategy: The orientation of the lever arm on the build plate profoundly impacts support requirements, surface finish, print time, and potentially residual stress. Analyze different orientations to minimize downward-facing surfaces and overhangs that require support.
- Self-Supporting Angles: Design features with angles typically greater than 45 degrees relative to the build plate, as these often do not require support structures. Avoid large, flat downward-facing surfaces.
- Sacrificial Features: Instead of complex, hard-to-remove supports, sometimes small features can be added to the design specifically to support a critical area, which are then easily machined away later.
- Design for Support Removal: Ensure adequate access for tools to remove support structures, especially in internal cavities or complex areas. Design supports that break away cleanly where possible.
- Wall Thickness and Feature Size:
- Minimum Wall Thickness: PBF-LB processes have limitations on the minimum achievable wall thickness (often around 0.4-0.8 mm, depending on geometry and height). Ensure designs respect these limits to prevent features from failing during the build.
- 均一性: While AM allows varying thickness, drastic changes can sometimes lead to differential cooling and stress. Aim for smooth transitions where possible. Avoid overly thick, bulky sections which can act as heat sinks and increase residual stress.
- Manage Stress Concentrations:
- Filleting: Use generous fillets and radii at sharp internal corners and transitions where stress naturally concentrates. This improves fatigue life, a critical factor for cyclically loaded lever arms.
- Smooth Transitions: Ensure smooth geometric transitions between thin and thick sections.
- Thermal Management Considerations:
- Large, solid cross-sections can accumulate heat during the printing process, potentially leading to higher residual stresses. Using topology optimization or internal lattices helps mitigate this by reducing the thermal mass.
- Consider how heat will dissipate during the build; strategic orientation can sometimes help.
- Design for Post-Processing:
- Machining Allowances: If specific surfaces require tight tolerances or a superior finish achievable only through machining, add extra ‘stock’ material (e.g., 0.5-1.0 mm) to those areas in the design file.
- Workholding Features: Consider adding temporary features (lugs, flat surfaces) that can aid in securely holding the part during post-processing steps like machining or inspection, which can be removed afterwards.
- 表面仕上げの期待: Understand that different orientations produce different as-built surface finishes (down-skins supported areas are typically rougher). Design critical surfaces to be side walls or up-skins where possible, or designate them for machining.
Table: DfAM Strategies for M300 Lever Arms
DfAM Principle | 戦略 | Benefit(s) |
---|---|---|
幾何学的自由 | Topology Optimization, Lattices, Channels | Weight Reduction, Performance Enhancement, Material Savings |
部品の統合 | Integrate adjacent parts into one design | Reduced Assembly, Fewer Failure Points, Simpler Logistics |
Support Optimization | Smart Orientation, Self-Supporting Angles | Reduced Print Time, Less Material Waste, Easier Post-Processing |
Feature Constraints | Respect Min. Wall Thickness, Smooth Transitions | Improved Print Success Rate, Reduced Stress |
ストレスマネジメント | Generous Filleting, Avoid Sharp Corners | Increased Fatigue Life, Improved Durability |
Thermal Considerations | Avoid Large Solid Masses, Use Lattices | Lower Residual Stress, Improved Dimensional Stability |
後処理 | Machining Allowance, Workholding Features | Achieves Final Tolerances/Finish, Easier Handling during Manufacturing |
Export to Sheets
Applying these AM design guidelines for steel parts is crucial for success. Engaging with experienced AM service providers like Met3dp early in the design process can provide valuable insights. Our engineering teams can assist clients in optimizing their lever arm designs, ensuring manufacturability, cost-effectiveness, and maximum performance leveraging our deep understanding of the PBF-LB process and M300 material behavior.
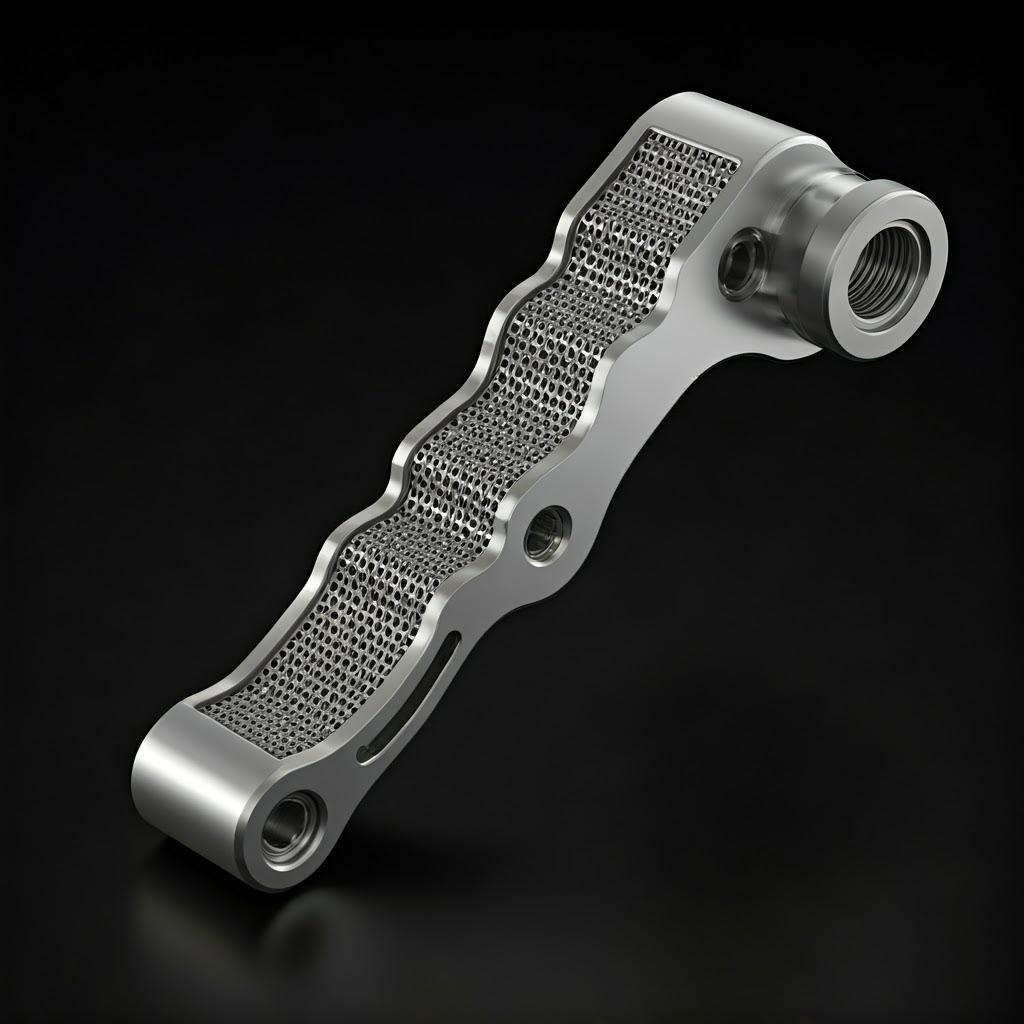
Achievable Tolerances, Surface Finish, and Dimensional Accuracy in M300 AM
Engineers and procurement managers must have realistic expectations regarding the precision achievable with metal additive manufacturing. While PBF-LB technology, particularly with high-quality machines and materials like M300 maraging steel, offers remarkable capabilities, it differs from the precision typically associated with multi-axis CNC machining as a primary process. Understanding the typical tolerances, surface finish, and accuracy helps in designing parts appropriately and planning necessary post-processing steps.
1. Tolerances:
- General Tolerances: As a rule of thumb, for well-calibrated industrial PBF-LB systems printing M300, achievable general tolerances are often in the range of ±0.1 mm to ±0.2 mm for smaller features (e.g., up to 50-100 mm), or ±0.1% to ±0.2% of the nominal dimension for larger parts. Some providers may quote standards like ISO 2768-m (medium) or -f (fine) for as-printed parts, but this can be geometry-dependent.
- Factors Influencing Tolerance:
- Machine Calibration: Regular calibration and maintenance are critical.
- Part Size and Geometry: Larger parts and complex geometries may exhibit greater deviation.
- Orientation: The direction of build significantly impacts dimensional accuracy on specific features.
- Thermal Effects: Residual stress and minor warping can affect tolerances, especially if not properly managed during the build and initial stress relief.
- サポート体制: Areas where supports attach and are removed may show slight deviations or witness marks.
- Critical Tolerances: For features requiring tighter tolerances than achievable as-printed (e.g., bearing bores, precision mating surfaces), finish machining after heat treatment is standard practice.
2. Surface Finish (Roughness):
- As-Built Roughness (Ra): The surface roughness of as-printed M300 parts typically ranges from Ra 8 µm to 20 µm (approx. 315 to 790 µin).
- Factors Influencing Roughness:
- 層の厚さ: Thicker layers (e.g., 50 µm) generally result in rougher surfaces than thinner layers (e.g., 20-30 µm), but print faster.
- Laser Parameters: Scan speed, power, and strategy affect melt pool dynamics and surface texture.
- Orientation: This is a major factor:
- Up-skin surfaces (facing upwards) tend to be smoother.
- Side walls show layer lines and depend on the angle relative to the build direction. Vertical walls are generally smoother than angled ones.
- Down-skin surfaces (overhanging or supported) are typically the roughest due to contact with support structures or the melt dynamics on overhangs.
- パウダーの特徴 Particle size distribution influences the texture.
- Achievable Finish After Post-Processing: Standard finishing techniques can significantly improve the surface:
- Bead Blasting/Shot Peening: Provides a uniform matte finish, often Ra 3-6 µm.
- Tumbling/Vibratory Finishing: Can smooth surfaces and edges, achieving Ra 1-5 µm depending on media and time.
- 研磨: Manual or automated polishing can achieve mirror-like finishes (Ra < 0.5 µm or better).
- 機械加工: Can achieve very smooth and precise surfaces (Ra < 1 µm).
3. Dimensional Accuracy and Stability:
- As-Printed Accuracy: Relates to the tolerances mentioned above. A well-controlled process minimizes deviation from the intended CAD geometry.
- Heat Treatment Effects: The critical aging heat treatment for M300 causes a small, generally uniform, and predictable volumetric 縮み一般的には 0.05% to 0.1%.
- Compensation: Experienced AM providers account for this shrinkage during the build preparation phase by slightly scaling the part model upwards. This ensures that after the aging process, the lever arm achieves the target dimensions with high accuracy.
- ストレス解消: Performing a stress relief heat treatment before removing the part from the build plate is crucial for minimizing distortion and maintaining dimensional stability throughout the post-processing chain.
Table: Summary of M300 AM Precision Characteristics
パラメータ | As-Printed Typical Range | Post-Processed Potential | Key Influencing Factors |
---|---|---|---|
General Tolerance | ±0.1-0.2 mm or ±0.1-0.2% | < ±0.02 mm (via Machining) | Machine Calibration, Part Size/Geometry, Orientation |
表面粗さ(Ra) | 8 – 20 µm | < 0.5 µm (via Polishing/Machining) | Orientation, Layer Thickness, Laser Parameters, Supports |
寸法安定性 | Good (with stress relief) | Excellent (predictable HT shrinkage) | Stress Relief Protocol, Aging HT Uniformity |
Export to Sheets
Met3dp utilizes state-of-the-art PBF-LB equipment with precise calibration and process control to maximize the achievable accuracy and surface quality of M300 lever arms directly from the 金属3Dプリンティング process. We work closely with clients to understand critical features and tolerances, planning necessary post-processing steps, including high-precision machining when required, to deliver parts that meet exact specifications. Our rigorous quality control ensures that dimensional accuracy, including compensation for heat treatment shrinkage, is verified before shipment.
Essential Post-Processing Steps for Maraging Steel Lever Arms
Printing the M300 lever arm is only the first major step; a series of crucial post-processing operations are required to transform the as-built part into a functional, high-performance component meeting stringent engineering requirements. These steps are not optional – particularly the aging heat treatment – and significantly influence the final mechanical properties, dimensional accuracy, and surface characteristics. Understanding this workflow is vital for accurate cost estimation and lead time planning by procurement managers and engineers.
The typical post-processing sequence for M300 AM lever arms includes:
- Stress Relief Heat Treatment (Recommended):
- 目的 To reduce internal stresses built up during the rapid heating and cooling cycles of the PBF-LB process. This minimizes the risk of distortion or cracking when the part is cut from the build plate and during subsequent handling or heat treatment.
- Method: Typically performed while the part is still attached to the build plate in a vacuum or inert atmosphere furnace. Temperatures are generally higher than aging but below the transformation temperature (e.g., 650-820°C, held for 1-2 hours, followed by slow cooling). Exact parameters depend on part geometry and established best practices. Note: Some providers may integrate stress relief implicitly or skip it for certain geometries, but it’s generally good practice for complex or large M300 parts.
- Part Removal from Build Plate:
- 目的 To separate the printed lever arm(s) from the metal build plate they were fused to during printing.
- Method: Commonly done using Wire Electrical Discharge Machining (Wire EDM) for a clean cut, or sometimes band sawing for less critical applications. Care must be taken not to damage the part.
- 支持構造の撤去:
- 目的 To remove the temporary structures generated during the printing process to support overhangs and downward-facing surfaces.
- Method: This can be a labor-intensive step depending on the complexity and accessibility of the supports. Methods include:
- Manual breaking or cutting using hand tools (pliers, chisels).
- Machining (milling, grinding) for more stubborn or integrated supports.
- Sometimes specialized electrochemical or abrasive flow processes for internal supports.
- 課題だ: Incomplete removal can affect performance; aggressive removal can damage the part surface. This highlights the importance of DfAM to minimize support needs.
- Aging Heat Treatment (Mandatory for Properties):
- 目的 This is the critical step that develops the ultra-high strength and hardness of M300 maraging steel. In the as-printed (and stress-relieved) state, the material is relatively soft and ductile (around 30-35 HRC). Aging causes the precipitation of fine intermetallic particles within the metal matrix.
- Method: Performed in a precisely controlled vacuum or inert atmosphere furnace to prevent oxidation.
- Typical Cycle: Heat to ~480°C – 500°C (900°F – 932°F), hold for 3 to 6 hours, then cool (air cooling or furnace cooling is acceptable).
- Result: Transforms the material to its high-strength state (UTS > 1900 MPa, Hardness > 50 HRC). As mentioned, this step causes a small, predictable shrinkage that must be accounted for in the initial design scaling.
- Machining (As Required):
- 目的 To achieve critical dimensions, tight tolerances (beyond as-printed capability), specific surface finishes, or features like threads, bearing seats, or precision mating surfaces.
- Method: Standard CNC machining operations (milling, turning, drilling, grinding). Aged M300 is readily machinable, though appropriate cutting tools and parameters for high-hardness materials should be used.
- Surface Finishing (As Required):
- 目的 To improve surface roughness, provide a uniform aesthetic appearance, enhance wear resistance, or prepare for coatings.
- Method: Various techniques can be employed after heat treatment and machining (if applicable):
- Bead Blasting: Creates a clean, matte finish.
- Tumbling/Vibratory Finishing: Smooths surfaces and edges.
- 研磨: Achieves very smooth, often reflective surfaces.
- コーティング: Applying specialized coatings like PVD (Physical Vapor Deposition), DLC (Diamond-Like Carbon), or others for enhanced wear resistance, corrosion protection, or lubricity.
- Inspection and Quality Control:
- 目的 To verify that the finished lever arm meets all specified requirements.
- Method: Includes dimensional checks (CMM, calipers, gauges), material property verification (hardness testing), surface finish measurement, and potentially Non-Destructive Testing (NDT) like CT scanning or dye penetrant testing to check for internal defects or surface cracks, especially for critical applications.
Workflow Summary:
Build Plate -> 応力緩和 -> Part Removal -> サポートの取り外し -> Aging Heat Treatment -> (Machining if needed) -> (Surface Finishing if needed) -> 検査 -> Final Part
Partnering with an AM parts finishing service provider or a manufacturer like Met3dp that offers comprehensive, end-to-end solutions including these critical post-processing steps ensures that the M300 lever arms achieve their full performance potential and meet all specifications reliably.
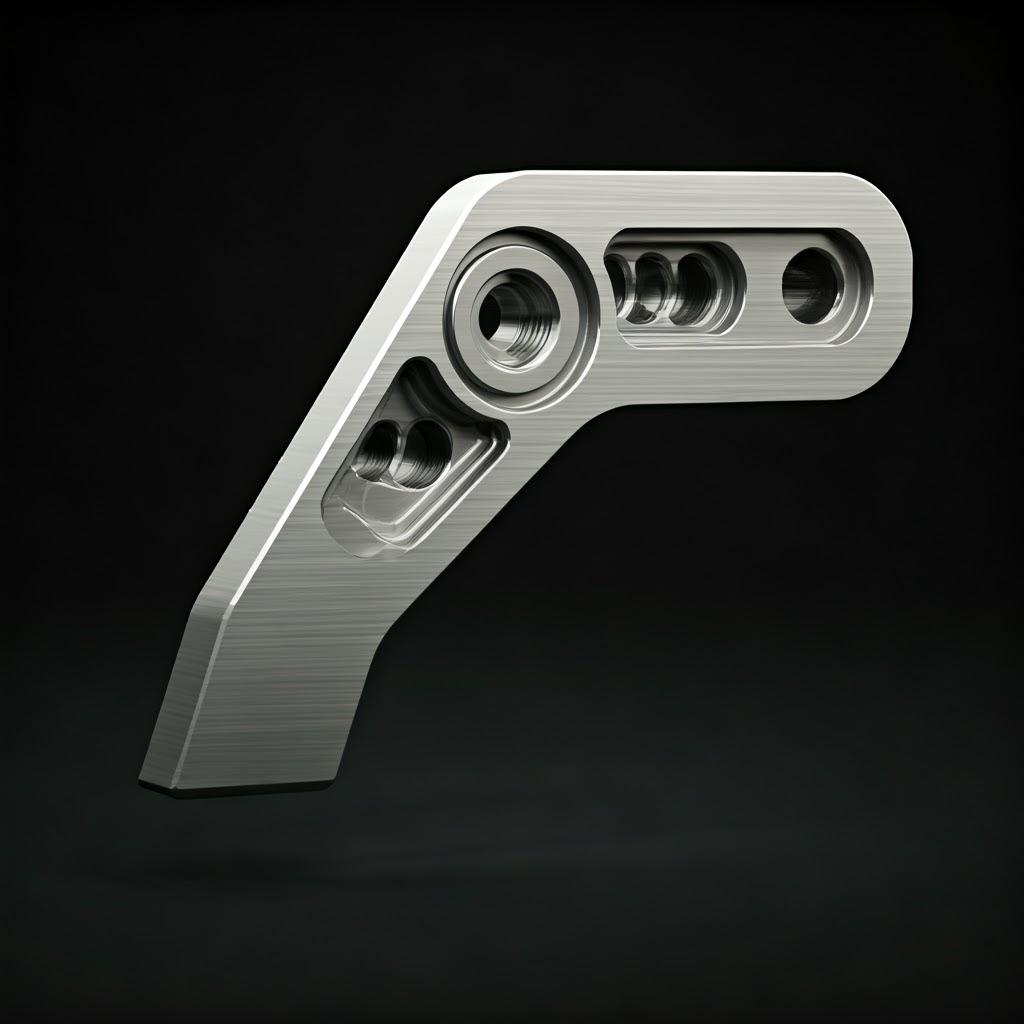
Navigating Common Challenges in Maraging Steel AM and Mitigation Strategies
While M300 maraging steel additive manufacturing offers immense benefits, like any advanced manufacturing process, it presents potential challenges. Awareness of these issues and implementing robust mitigation strategies are key to consistently producing high-quality, reliable lever arms. Experienced service providers proactively manage these factors through process control, material expertise, and DfAM.
1. Residual Stress and Warping:
- チャレンジ: The rapid, localized heating and cooling inherent in PBF-LB can generate significant internal stresses within the printed part. If unmanaged, these stresses can cause warping (distortion) during the build, after removal from the plate, or even cracking.
- Causes: High thermal gradients, large solid cross-sections, inadequate support.
- Mitigation Strategies:
- Build Plate Heating: Pre-heating the build plate reduces thermal gradients.
- Optimized Scan Strategies: Using specific laser scanning patterns (e.g., island scanning, sectoring) helps distribute heat more evenly.
- Effective Support Structures: Properly designed supports anchor the part and help dissipate heat.
- Stress Relief Heat Treatment: Performing this step (often before plate removal) significantly reduces internal stresses.
- DfAM: Designing parts with reduced thermal mass (e.g., using lattices instead of solid sections) and avoiding abrupt geometry changes.
2. Cracking (During Build or Heat Treatment):
- チャレンジ: Cracks can sometimes form either during the printing process (hot cracking) or, more commonly for M300, during post-build heat treatments if stresses are too high or procedures are incorrect.
- Causes: Excessive residual stress, impurities in the powder, incorrect heat treatment parameters (heating/cooling rates too fast), poor part design leading to stress concentrations.
- Mitigation Strategies:
- Residual Stress Management: Implementing the strategies listed above.
- High-Quality Powder: Using powder with controlled chemistry and low impurities (Oxygen, Nitrogen) minimizes material-related cracking susceptibility. Met3dp’s focus on powder quality is critical here.
- プロセスパラメータの最適化 Fine-tuning laser power, scan speed, and other parameters for the specific M300 powder batch.
- Proper Heat Treatment Protocols: Adhering to validated stress relief and aging cycles with controlled ramp rates and atmospheres.
- DfAM: Designing parts with generous fillets and avoiding sharp internal corners where cracks might initiate.
3. Support Removal Difficulty and Surface Quality:
- チャレンジ: Supports, while necessary, can be difficult and time-consuming to remove, especially from complex internal geometries. Removal processes can also leave witness marks or damage the part surface.
- Causes: Overly dense or poorly designed supports, difficult-to-access locations, strong bonding between support and part.
- Mitigation Strategies:
- DfAM for Supports: Designing parts to be self-supporting where possible, optimizing orientation, using easily removable support types (e.g., conical, thin-walled).
- Optimized Support Parameters: Adjusting laser parameters where supports touch the part to ensure adequate adhesion but easier separation.
- Specialized Removal Techniques: Utilizing appropriate tools and methods (manual, machining, potentially EDM or chemical etching for specific cases).
- 後処理: Planning for finishing steps (blasting, polishing) to remove witness marks if required.
4. Porosity:
- チャレンジ: Small voids or pores within the printed material can compromise mechanical properties, particularly fatigue life.
- Causes: Incorrect laser parameters (power too low/high, speed too fast), gas entrapment from the powder or shield gas, poor powder quality or flowability leading to incomplete melting or uneven layers.
- Mitigation Strategies:
- Parameter Optimization: Developing robust process parameters that ensure full melting and fusion between layers (achieving >99.5% density is typical).
- High-Quality Powder: Using powder with good sphericity, controlled PSD, and low trapped gas content. Met3dp’s advanced atomization techniques (Gas Atomization, PREP) are key here.
- Proper Machine Operation: Ensuring correct shield gas flow and oxygen levels within the build chamber.
- 熱間静水圧プレス(HIP): While ideally avoided through process optimization, HIP (applying high pressure and temperature) can be used as a post-processing step to close internal pores. However, it adds cost and lead time.
5. Inconsistent Material Properties:
- チャレンジ: Variations in hardness, strength, or ductility across a part or between different builds.
- Causes: Uneven heat treatment (furnace temperature variations), inconsistent process parameters during the build, variations in powder quality between batches.
- Mitigation Strategies:
- Calibrated Furnaces: Using precisely controlled and calibrated vacuum/inert atmosphere furnaces for heat treatment.
- Process Monitoring & Control: Implementing in-situ monitoring (e.g., melt pool monitoring) and rigorous quality control throughout the AM process.
- Powder Batch Control: Strict quality control and testing of incoming powder batches to ensure consistency.
- Standardized Procedures: Adhering to validated and documented procedures for printing and all post-processing steps.
Table: Common M300 AM Challenges and Solutions
チャレンジ | Primary Cause(s) | Key Mitigation Strategy(ies) |
---|---|---|
Residual Stress / Warping | Thermal Gradients, Bulky Geometry | Optimized Scan Strategy, Supports, Stress Relief HT, DfAM (Lattices) |
クラッキング | High Stress, Impurities, Incorrect HT | Stress Management, Quality Powder, Parameter Tuning, Correct HT Protocols, DfAM (Fillets) |
Support Removal Difficulty | Complex Geometry, Poor Support Design | DfAM (Minimize Supports, Optimize Orientation), Optimized Support Parameters, Access Planning |
多孔性 | Incorrect Parameters, Gas, Poor Powder Flow | Parameter Optimization, High-Quality Powder, Process Control, HIP (Secondary) |
Inconsistent Properties | Uneven HT, Process Variation, Powder Inconsistency | Calibrated Furnaces, Process Monitoring, Powder QC, Standardized Procedures |
Export to Sheets
By understanding these potential issues and partnering with an experienced additive manufacturing service provider like Met3dp, companies can confidently leverage the power of M300 maraging steel AM. Our expertise in materials science, process optimization using our industry-leading equipment, and rigorous quality control systems are designed to proactively mitigate these challenges, ensuring the delivery of robust, reliable, high-performance lever arms that meet the demanding requirements of industries like aerospace, automotive, and industrial manufacturing.
Selecting the Right Metal Additive Manufacturing Service Provider for Lever Arms
Choosing the right manufacturing partner is as critical as the design and material selection, especially when dealing with high-performance components like M300 maraging steel lever arms. The capabilities, expertise, and quality systems of your chosen provider directly impact the success of your project, final part quality, cost-effectiveness, and supply chain reliability. For procurement managers and engineers sourcing these advanced components, particularly for B2B manufacturing contracts または industrial component supply, evaluating potential providers requires looking beyond just the quoted price.
Here are key criteria to consider when selecting a metal AM supplier for your M300 lever arm project:
- Proven Expertise with Maraging Steel (M300):
- Does the provider have documented experience specifically with M300 (1.2709)? This material requires nuanced understanding, particularly regarding optimized print parameters and, crucially, precise heat treatment protocols (stress relief and aging).
- Ask for case studies, sample parts, or data demonstrating their success with M300 in similar applications or complexities.
- Appropriate Technology and Equipment:
- Do they operate well-maintained, industrial-grade Powder Bed Fusion – Laser Beam (PBF-LB) machines suitable for M300?
- What is their machine capacity and redundancy? Can they handle your required volume and meet lead times, even if one machine is down for maintenance?
- Inquire about machine calibration frequency and process monitoring capabilities. Met3dp prides itself on printers delivering industry-leading print volume, accuracy, and reliability.
- Material Quality, Handling, and Traceability:
- How do they source their M300 powder? Do they manufacture it themselves (like Met3dp) or source it from qualified suppliers?
- What procedures are in place for powder quality control (chemistry, PSD, morphology), storage (preventing moisture/contamination), and handling/recycling to ensure batch-to-batch consistency?
- Can they provide full material traceability from powder batch to finished part?
- Comprehensive Post-Processing Capabilities:
- Does the provider offer the necessary post-processing steps in-house or through tightly controlled, qualified partners? This includes stress relief, precision part removal (e.g., wire EDM), support removal, critical aging heat treatment in calibrated vacuum/inert furnaces, CNC machining for tight tolerances, and various surface finishing options.
- An integrated service offering simplifies the supply chain and ensures accountability for the final part quality.
- Robust Quality Management System (QMS):
- Is the provider certified to relevant quality standards? ISO 9001 is a baseline requirement for industrial suppliers. For aerospace or medical applications, certifications like AS9100 or ISO 13485 may be necessary.
- What are their inspection capabilities (CMM, NDT, material testing)? How do they ensure dimensional accuracy and material properties meet specifications?
- Engineering and DfAM Support:
- Can their engineering team provide Design for Additive Manufacturing (DfAM) consultation? Assisting with topology optimization, support strategy, and designing for post-processing can significantly improve the part and reduce costs. Met3dp offers comprehensive 医療、航空宇宙、自動車などの業界向けアプリケーション開発サービス as part of its solutions.
- Communication, Responsiveness, and Lead Time Reliability:
- How effectively do they communicate throughout the quoting, production, and delivery process? Are they responsive to inquiries and transparent about project status?
- Do they provide realistic lead time estimates and have a track record of on-time delivery?
- Cost vs. Overall Value:
- While cost is always a factor, evaluate the total value proposition. A slightly cheaper quote might be negated by poor quality, delays, or lack of necessary expertise, leading to higher costs downstream. Consider the provider’s reliability, quality, expertise, and support as part of the overall value.
Met3dp stands as a leading provider of additive manufacturing solutions, uniquely positioned due to our integrated expertise spanning high-performance 金属粉 (produced using advanced Gas Atomization and PREP technologies) and cutting-edge SEBM/PBF-LB printers. Our decades of collective expertise ensure a deep understanding of materials like M300 and the entire AM workflow. By partnering with メット3dp, you gain access to a reliable manufacturer committed to quality, innovation, and helping you leverage the full potential of additive manufacturing for your critical lever arm applications and beyond.
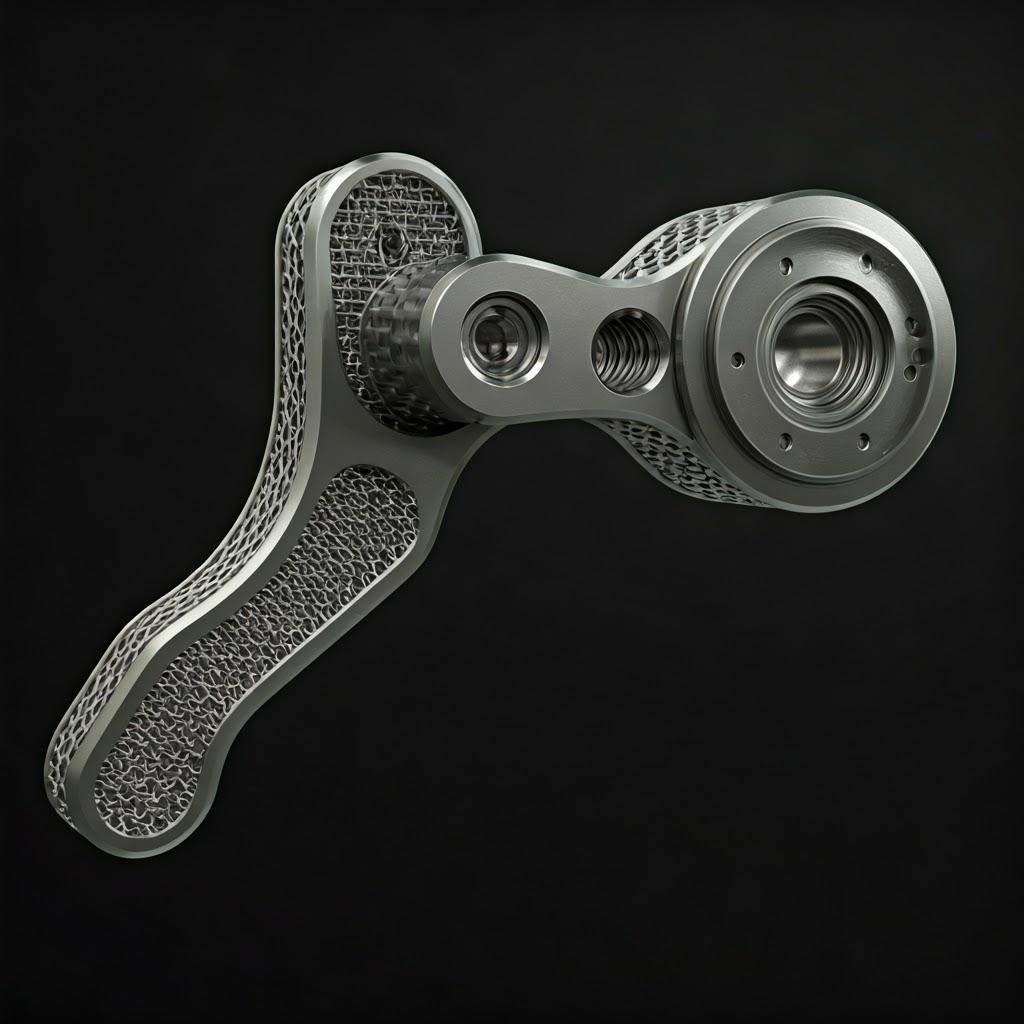
Understanding Cost Factors and Lead Times for AM Maraging Steel Levers
Budgeting and project scheduling require a clear understanding of what drives the cost and production timeline for additively manufactured M300 maraging steel lever arms. Unlike traditional mass production methods, AM costs are calculated differently, and lead times involve multiple distinct stages.
Key Cost Factors:
- Material Consumption:
- Part Volume: The actual volume of the final lever arm. M300 powder is a high-performance (and relatively expensive) alloy.
- Support Structure Volume: Material used for supports adds to consumption and must be accounted for. Effective DfAM minimizes this.
- Powder Waste/Recycling: While powder can be recycled, there are handling losses and lifecycle limits that factor into overall cost.
- マシン・タイム
- Build Height: PBF-LB builds layer by layer, so taller parts take longer.
- Part Volume & Density: Larger/denser parts require more laser scanning time per layer.
- パート・コンプレックス: Intricate features might require slower scanning parameters.
- Nesting Efficiency: How many parts can be efficiently packed onto a single build plate affects the amortized machine cost per part. This is crucial for B2B manufacturing quotes involving volume.
- 労働だ:
- Setup & Teardown: Preparing the machine, loading powder, unloading the build, and cleaning.
- 後処理: Manual labor for support removal, part handling, finishing, and inspection can be significant, especially for complex parts.
- Engineering/QA: Design review, build preparation, quality assurance checks.
- Post-Processing Intensity:
- 熱処理: Costs associated with furnace time for stress relief and the critical aging cycle. Vacuum/inert atmosphere furnaces are required.
- 機械加工: Extent and complexity of required CNC machining operations add cost based on machine time and programming.
- 表面仕上げ: The level of finish required (blasting vs. tumbling vs. high polishing) impacts labor and process costs.
- Quality Requirements:
- Inspection Level: Basic dimensional checks vs. comprehensive CMM reports, NDT (CT, dye penetrant), material testing – higher assurance levels increase cost.
- Certifications & Documentation: Costs associated with providing material certs, certificates of conformity, and adhering to specific industry standards (e.g., AS9100).
- 注文数量:
- 規模の経済: While AM avoids tooling costs, some economies of scale exist. Larger batches allow for better nesting, potentially dedicated machine runs, and amortization of setup/programming costs over more parts, often enabling better volume pricing.
Typical Lead Time Components:
Lead time for an M300 AM lever arm is the sum of several stages:
- Quoting and Design Review: (1-5 days) Initial assessment, DfAM feedback, quote generation.
- Scheduling/Queue Time: (Variable: 1 day – 2+ weeks) Depends on the service provider’s current machine backlog.
- 印刷: (1-3+ days) Highly dependent on part height, volume, and nesting.
- Cooling & Stress Relief: (0.5-1 day) Allowing the build plate to cool, performing stress relief HT.
- Part & Support Removal: (0.5-2+ days) Depending on complexity and method (Wire EDM, manual).
- Aging Heat Treatment: (1-2 days) Includes furnace cycle time and cooling.
- Machining & Finishing (if required): (1-5+ days) Depends heavily on the extent of work needed.
- Inspection & Shipping Prep: (1-2 days) Final QA checks, documentation, packaging.
Total Estimated Lead Time: 通常、以下の範囲である。 1.5 to 4 weeks for standard projects. Highly complex parts, those requiring extensive post-processing, or very large orders may take longer. Expedited options are sometimes available at a premium cost.
Understanding these cost drivers and lead time components allows for better planning and communication between engineering, procurement, and the AM service provider. Transparent discussions about requirements and expectations are crucial for a successful partnership.
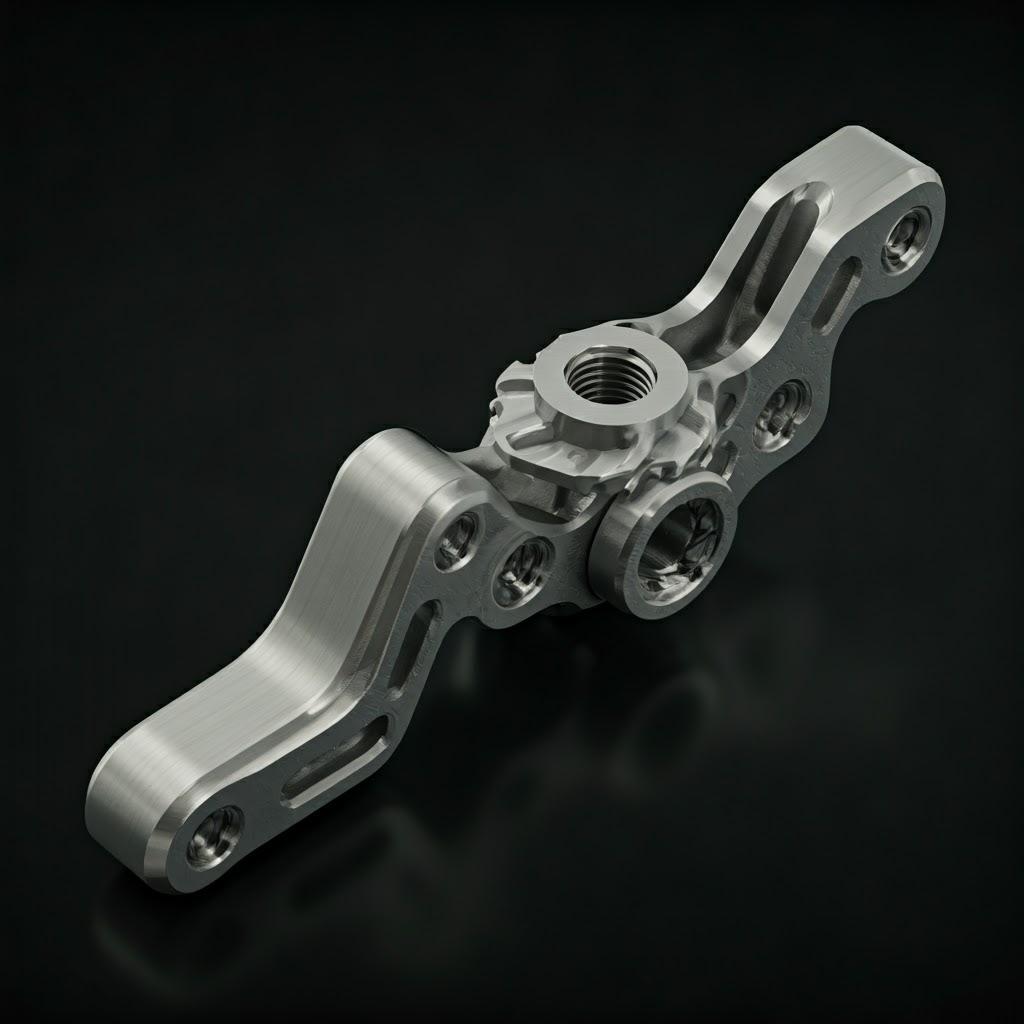
Frequently Asked Questions (FAQ) about 3D Printed Maraging Steel Levers
Here are answers to some common questions regarding reinforced lever arms produced using M300 maraging steel additive manufacturing:
Q1: How does the strength of a 3D printed M300 lever arm compare to one machined from wrought M300 bar stock?
A: When processed correctly using optimized PBF-LB parameters and appropriate post-processing (including stress relief and aging heat treatment), the mechanical properties (tensile strength, yield strength, hardness) of 3D printed M300 components are highly comparable to wrought M300 specifications. They often achieve near-wrought properties (typically >95-98% of wrought values) and significantly exceed the properties of cast M300. In some cases, the fine microstructure achieved through AM can even offer benefits in specific properties like fatigue resistance, although this is geometry and application-dependent. Consistent process control and quality powder are key to achieving these results.
Q2: What is the typical aging heat treatment cycle required for 3D printed M300 parts? Is it always necessary?
A: Yes, the aging heat treatment is absolutely necessary to achieve the characteristic ultra-high strength and hardness of M300 maraging steel. In the as-printed state, the material is relatively soft (~30-35 HRC). The typical aging cycle involves heating the part in a vacuum or inert atmosphere furnace to approximately 480°C to 500°C (900°F to 932°F), holding it at that temperature for 3 to 6 hours, and then allowing it to cool. This precipitates hardening phases within the metal matrix. Without this step, the lever arm would not possess the required mechanical properties for high-strength applications.
Q3: Can complex internal features, like hydraulic channels or conformal cooling passages, be effectively integrated into M300 lever arms using additive manufacturing?
A: Yes, absolutely. This is one of the primary advantages of using additive manufacturing for components like lever arms. The layer-by-layer building process allows for the creation of intricate internal channels and complex hollow structures that would be impossible or prohibitively expensive to produce using traditional methods like machining. For lever arms used in hydraulic systems, integrated fluid pathways can be designed. For levers that are part of tooling (e.g., in molding), conformal cooling channels that follow the shape of the lever can be integrated to provide highly efficient thermal management, improving performance and cycle times. DfAM principles are essential to ensure these channels are designed for effective printing and later powder removal/cleaning.
Conclusion: The Future of High-Performance Levers with Maraging Steel AM and Met3dp
The convergence of advanced materials like M300 (1.2709) maraging steel and the transformative capabilities of metal additive manufacturing represents a significant leap forward in the production of high-strength, high-performance industrial lever arms. As we’ve explored throughout this series, this combination allows engineers and manufacturers to break free from the constraints of traditional methods, enabling:
- これまでにないデザインの自由度: Creating topology-optimized, lightweight structures with complex internal features.
- パフォーマンスの向上: Achieving superior strength-to-weight ratios, integrating functionality like cooling channels, and consolidating assemblies.
- 材料効率: Reducing waste compared to subtractive manufacturing.
- Agile Production: Enabling rapid prototyping, customization, and efficient low-to-medium volume production without dedicated tooling.
From demanding aerospace actuators and performance automotive components to robust industrial machinery linkages and specialized tooling, M300 AM levers offer tangible benefits in strength, durability, weight reduction, and overall system efficiency. While challenges exist, understanding DfAM principles, meticulous post-processing (especially the critical aging heat treatment), and robust quality control allows these challenges to be effectively managed.
The future of advanced manufacturing increasingly relies on leveraging such innovative combinations of materials and processes. As a leader in both high-performance 金属粉製造 そして industrial additive manufacturing systems, Met3dp is at the forefront of this evolution. Our comprehensive expertise ensures that we can partner with organizations across aerospace, automotive, medical, and industrial sectors to realize the full potential of M300 maraging steel and other advanced alloys for their most critical components.
Whether you are designing a next-generation lever arm, seeking a reliable supplier for complex metal AM parts, or exploring how additive manufacturing can transform your production capabilities, Met3dp has the technology, materials, and expertise to support your goals.
Contact Met3dp today to discuss your specific requirements and discover how our cutting-edge 付加製造ソリューション can power your organization’s innovation and accelerate your journey towards next-generation manufacturing.
シェアする
MET3DP Technology Co., LTDは、中国青島に本社を置く積層造形ソリューションのリーディングプロバイダーです。弊社は3Dプリンティング装置と工業用途の高性能金属粉末を専門としています。
関連記事
Met3DPについて
最新情報
製品
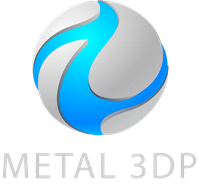
3Dプリンティングと積層造形用金属粉末