金属積層造形:包括的ガイド
目次
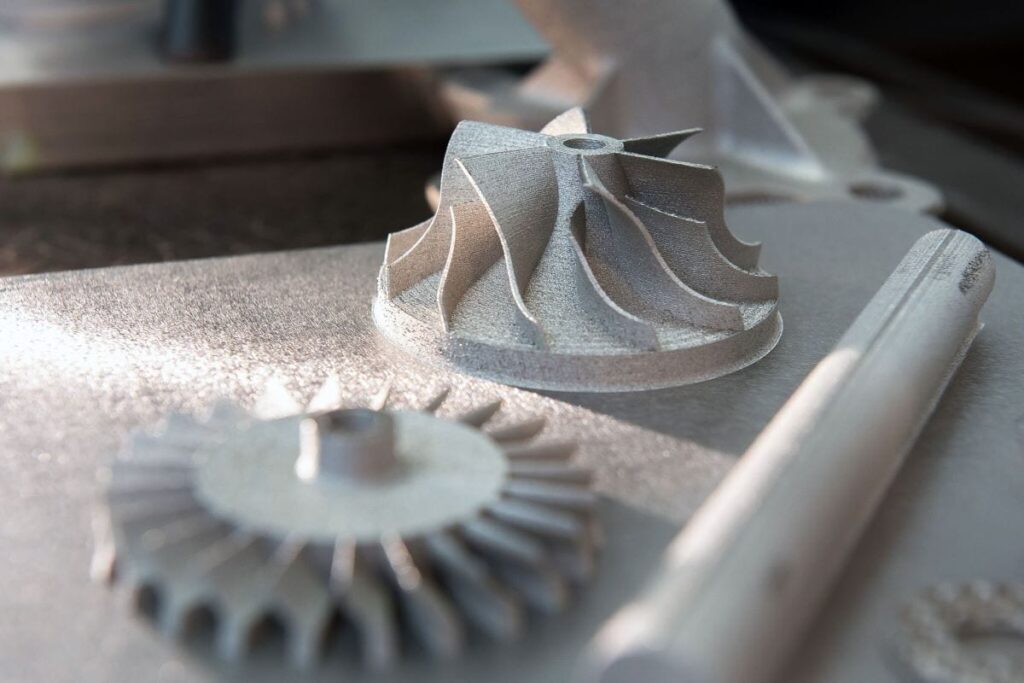
金属積層造形の概要
メタル アディティブ・マニュファクチャリング金属3Dプリンティングとしても知られる積層造形は、3Dモデルデータから直接金属部品を迅速に製造する革新的な技術です。材料を除去するCNC機械加工のような減法的製造方法とは対照的に、加法的製造は、ステンレス鋼、アルミニウム、チタン、ニッケル合金などの金属を使用して、コンポーネントを層ごとに構築します。
従来の製造に比べ、金属AMは設計の自由度、カスタマイズ、最適化を可能にし、重量、材料使用量、リードタイムを削減できる。部品を一体化したり、共形冷却チャネルを埋め込んだり、鋳造や機械加工では不可能な有機的形状で設計したりすることができます。金属3Dプリンティングは、航空宇宙、医療、自動車、エネルギーなどの業界全体にイノベーションの新たな可能性をもたらします。
この包括的なガイドでは、さまざまな金属AMプロセス、材料、アプリケーション、利点、および制限に関する技術的な詳細を提供します。重要な情報は比較しやすい表で示され、さまざまな金属3Dプリント技術の能力とトレードオフを強調しています。積層造形が金属加工にどのような革命をもたらしているか、詳しくご覧ください。
金属積層造形の主なハイライト:
- デジタル3D CADモデルから、高密度の最終金属部品を製造
- 機械加工のような減法的な方法とは異なり、材料を層ごとに加える。
- 鋳造や機械加工では不可能な複雑で最適化された形状が可能
- 従来の技術に比べ、廃棄物、エネルギー使用、リードタイムを削減
- ラピッドプロトタイピングだけでなく、部品の直接生産も容易にします。
- 航空宇宙、医療、自動車、その他の分野での用途拡大
金属積層造形プロセスの種類
金属部品を付加的に印刷するには、いくつかのアプローチがある。主な金属AMプロセスのカテゴリーには、粉末床溶融法、指向性エネルギー蒸着法、バインダージェッティング法、シートラミネーション法などがある。それぞれ、材料、精度、コストなどの面でユニークな能力を持っています。
表1:主な金属積層造形プロセスの概要
プロセス | 説明 | 材料 | 精度 | 後処理 |
---|---|---|---|---|
パウダーベッド・フュージョン | 熱エネルギーを使用して粉末層の領域を選択的に融合させる。選択的レーザー溶融(SLM)、直接金属レーザー焼結(DMLS)、電子ビーム溶融(EBM)などがある。 | アルミニウム、スチール、チタン、ニッケル合金 | 高、±0.1~0.2mm | 一部の機械加工と熱処理 |
直接エネルギー蒸着 | 熱エネルギーを集中させ、蒸着中の原料を溶かして材料を融合させる。レーザーエンジニアードネットシェーピング(LENS)やレーザー金属蒸着(LMD)が含まれる。 | アルミニウム、スチール、チタン、コバルトクロム | ミディアム、±0.5mm | さらなる加工と仕上げ |
バインダー・ジェット | 液状接合剤が粉末材料の層を選択的に接合する。部品は印刷後に焼結される。 | ステンレス鋼、一部の合金 | 低、± 2mm | 脱バインダー、焼結、浸透が必要 |
シートラミネート | シートメタルの層を接着して部品を形成し、レーザーやCNC機械加工でトリミングする。 | アルミニウム、スチール、チタン | ミディアム、±0.5mm | ラミネート加工後のレーザー切断またはCNC加工 |
パウダーベッド融合 選択的レーザー溶解(SLM)や電子ビーム溶解(EBM)のような技術は、現在最も広く使われている金属AMプロセスである。機械加工に匹敵する高分解能、優れた材料特性、ステンレス鋼からニッケル基合金までの幅広い金属を提供する。原料は微細な金属粉末で、層状に広げられ、制御された雰囲気のチャンバー内で、集中された熱源によって選択的に溶解される。
直接エネルギー蒸着 LENS(Laser Engineered Net Shaping)のような方法は、溶融プールを基材上に集束させ、材料を連続的に追加する。これにより、溶融した粉末やワイヤー原料を堆積させることで、より大きなサイズの部品を作り上げることができる。解像度は低いが、造形サイズはパウダーベッド法のように制限されない。後処理が少なくて済むが、表面仕上げは劣る。
バインダー噴射 は、液体結合剤を使って金属粉末の層を結合させる。出来上がった "グリーン "パーツは、その後焼結され、完全な密度を得るために銅やブロンズを浸透させなければならない。現在のところ材料の選択肢は限られていますが、バインダージェッティングを使えば、小さな複雑な金属部品をより手頃な価格で大量に生産することができます。
シートラミネート 薄いシートメタルの層を接着剤または溶接で貼り合わせる。その後、レーザーまたはCNC機械加工によって、積層体を3D形状に切断する。精度は高いが、シートの厚さによる形状の制限がある。
それぞれのプロセスには利点があり、最適な用途があります。適切な金属AM技術を選択するかどうかは、材料要件、精度、表面仕上げ、バッチサイズ、コストなどの要因によって決まる。
金属積層造形用材料
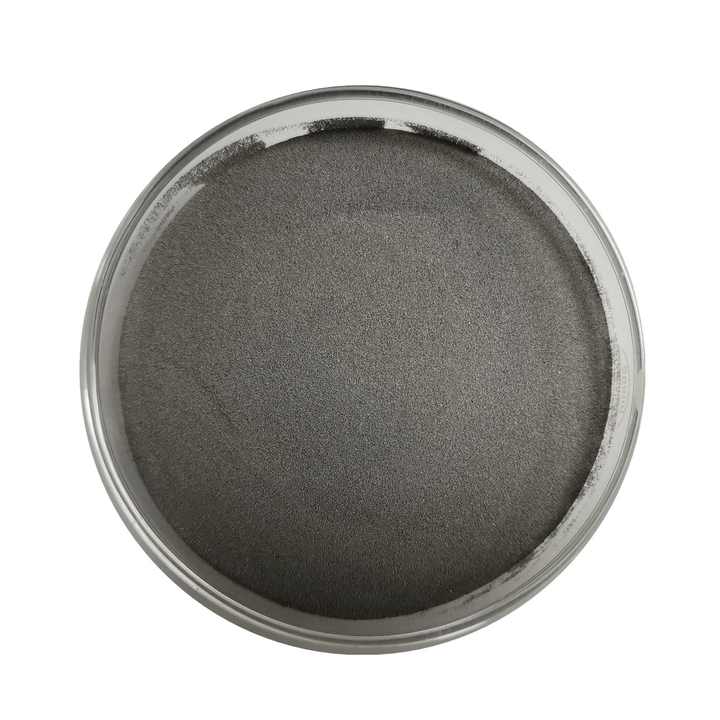
粉末床溶融法、指向性エネルギー蒸着法、バインダージェッティング法、シートラミネーション法などを用いて、ステンレス鋼から超合金まで幅広い金属をプリントすることができる。最も一般的に使用される金属AM材料は以下の通り:
表2:一般的な金属積層造形材料
素材 | プロセス | プロパティ | アプリケーション |
---|---|---|---|
ステンレス鋼 | PBF、BJ | 高強度、耐食性 | 航空宇宙、自動車、医療 |
アルミニウム合金 | PBF、DED | 軽量、良好な熱伝導性 | 自動車、航空宇宙 |
チタン合金 | PBF、DED | 高い強度対重量比 | 航空宇宙、医療用インプラント |
ニッケル合金 | PBF | 耐熱性と耐食性 | 航空宇宙、エネルギー |
コバルト・クローム | 体外式除細動器 | 生体適合性、耐摩耗性 | 医療用インプラント、工具 |
工具鋼 | PBF、BJ | 高硬度、熱安定性 | 金型 |
ステンレス鋼 316Lや17-4PHは、その強度、耐食性、印刷や後加工の比較的容易さにより、産業界で広く使用されている。
アルミニウム合金 ような AlSi10Mg 機械加工や鋳造が困難な航空宇宙部品や自動車部品の軽量化を可能にする。
チタン合金 Ti64のような高強度対重量比は、生体適合性と共に構造部品に理想的である。
ニッケル超合金 パウダー インコネル718やインコネル625は、高温での機械的特性に優れており、要求の厳しい用途に適している。
コバルトクロム合金粉 医療用インプラントや工具に適した高い剛性、生体適合性、耐摩耗性を誇る。
工具鋼 H13、D2、マルエージング鋼は、射出成形金型や鍛造金型などの金型用として、非常に高い硬度、強度、熱安定性を提供します。
研究開発の努力は、AMプロセスに適合する金属の種類を増やしている。貴金属やプラチナのようなエキゾチックな合金も、宝飾品や電子機器のような特殊な用途に採用されている。
金属積層造形仕様
金属AMマシンの能力を定義する主な要因は、造形量、層解像度、精度、対応材料である。精度、表面仕上げ、熱処理などの要件は、特定の用途によって異なります。
表3:金属AM装置の仕様と能力
パラメータ | 代表的な仕様 |
---|---|
ビルド・ボリューム | 50-500mm x 50-500mm x 50-500mm |
レイヤーの厚さ | 20~100ミクロン |
精密 | PBFは±0.1~0.2mm、DEDは±0.5mm |
表面仕上げ | Ra 10-25ミクロン、Rz 20-100ミクロン |
材料 | ステンレス鋼、アルミニウム合金、チタン合金、工具鋼、ニッケル合金 |
プロセス環境 | 真空または不活性アルゴン雰囲気 |
必要なサポート | 後処理で除去 |
熱処理 | 応力除去、溶体化処理、エージング |
ビルドボリューム ほとんどのパウダーベッドおよび指向性エネルギーシステムは、数立方インチから最大約1立方フィートの範囲です。バインダージェッティングやシートラミネーションプロセスには、より大きな装置が利用可能です。
層厚 ビルドプロセス中に20~100ミクロンまで変化させることができ、機械工の仕上げレベルの微細な解像度が得られます。より薄い層は表面仕上げを向上させるが、造形時間も長くなる。
精密 使用するAM機によって異なるが、粉末床溶融法では±0.1~0.2mm、指向性エネルギー蒸着法では±0.5mmである。
達成可能 表面仕上げ の範囲は10~25ミクロン(Ra)、20~100ミクロン(Rz)だが、改善するには研磨仕上げなどの後処理が必要になる。
のほぼすべての金属合金。 ステンレス鋼 への チタン そして ニッケル合金 近年、素材の選択肢は倍増している。
金属積層造形装置のサプライヤー
さまざまな企業が、工業用金属AMシステムと印刷サービスを提供している。粉末床溶融、指向性エネルギー蒸着、バインダージェッティング、シートラミネーション装置を提供する主要ベンダーには、以下のようなものがある:
表4:金属積層造形システムの主要サプライヤー
会社概要 | AMプロセス | 金属 | ビルド・ボリューム | コスト範囲 |
---|---|---|---|---|
イーオーエス | 粉末床溶融法(DMLS) | Al、Ti、Ni合金 | 250×250×325mm | $150,000-$1,000,000 |
SLMソリューション | 粉末溶融(SLM) | Al、Ti、工具鋼 | 250×250×300mm | $200,000-$1,000,000 |
HP | バインダー噴射 | ステンレス | 380 x 285 x 380 mm | $100,000-$500,000 |
デスクトップ・メタル | バインダー噴射 | ステンレス鋼、合金鋼 | 160 x 160 x 250 mm | $100,000-$500,000 |
シャキー | 直接エネルギー蒸着 | チタン、インコネル、ステンレス | 1500 x 750 x 750 mm | $500,000-$2,500,000 |
オプトメック | 直接エネルギー蒸着 | Al、Ti、CoCr | 610 x 610 x 610 mm | $250,000-$750,000 |
ファブリソニック | 超音波AM | Al、スチール、Ti | 600 x 900 x 600 mm | $250,000-$500,000 |
ドイツ企業 イーオーエス は直接金属レーザー焼結(DMLS)技術のパイオニアであり、チタン、アルミニウム、ニッケル合金などの金属用の幅広い産業用プリンターを提供している。
SLMソリューション また、最大500立方インチの造形量で鋼、チタン、アルミニウム、その他の金属を処理できる粉末床溶融装置も提供している。
HP、デスクトップメタル、 そして エクスワン 小型で複雑なステンレス鋼や合金鋼の部品の大量生産に重点を置いたバインダージェットを活用。
シャキー そして オプトメック チタン、アルミニウム、ニッケル超合金を使用した大規模金属印刷用の指向性エネルギー蒸着システムを提供する。
ファブリソニック は、金属部品の内部に配線やセンサーなどを埋め込むことができる特許取得済みの超音波積層造形法を採用している。
金属AM装置は通常、生産能力に応じて初期資本投資額が$10万から$100万以上と幅があるが、価格は急速に下落している。材料費は、使用する特定の合金によって大きく異なる。
金属積層造形アプリケーション
金属アディティブ・マニュファクチャリングは、航空宇宙、医療、自動車、一般産業などの用途に適した新たな設計の自由と能力をもたらす:
航空宇宙:軽量ブラケットと複雑な構造、コンフォーマル冷却を備えたエンジン部品、部品の統合による重量、材料使用量、リードタイムの削減
メディカル:カスタマイズされた整形外科用インプラント、骨とのオッセオインテグレーションを改善するための薄い壁や格子構造を持つ外科用器具、歯科用修復物
自動車:軽量格子構造、部品のマス・カスタマイゼーション、工場のワークフローを改善する治具や冶具のようなツーリング
産業用/民生用:有機的形状、マス・カスタマイゼーション、軽量格子構造を活用した照明、家具、スポーツ用品、楽器
工具:射出成形金型、金型、金型インサートにコンフォーマル冷却チャンネルを埋め込むことで、サイクルタイムを短縮できます。予備金型部品の迅速なターンアラウンド。
石油・ガス:カスタムパイプライン継手、高圧/腐食環境用のリグやバルブブロックなどの構造部品。
この技術は、多くの産業における製品開発で、迅速なツーリング、治具、プロトタイピングにも使用されている。以下は、金属AMの応用例と、従来の製造に対する利点です:
表5:金属積層造形の用途と利点
申し込み | メリットと従来のプロセス |
---|---|
航空機用ブラケット | 軽量化、部品統合 |
股関節インプラント | カスタマイズされた形状、加速された設計反復 |
熱交換器 | 複雑な内部チャンネルが熱伝達を改善 |
射出成形金型 | コンフォーマル冷却によるサイクル時間の短縮 |
自動車部品 | マス・カスタマイゼーション、軽量最適化 |
積層造形は、鋳造、機械加工、その他の従来の製造技術では不可能または経済的でなかった金属部品を製造する、これまでにない設計の自由をエンジニアに与える。
メタルAMの利点と欠点
サブトラクティブ・ファブリケーションや他の伝統的な金属製造方法と比較して、AMにはいくつかの重要な利点があるが、同時に考慮すべき限界もある:
表6:金属積層造形 - 長所と短所
メリット | デメリット |
---|---|
設計の自由度、複雑な形状 | 少量生産による部品サイズの制限 |
軽量化、材料の節約 | 鍛造金属よりも低い材料特性 |
リードタイムと金型コストの削減 | 寸法精度と表面仕上げの低下 |
統合アセンブリ、組み込み機能 | 設備費、材料費の上昇 |
マス・カスタマイゼーション、オンデマンド生産 | 後処理が必要な場合が多い |
材料の無駄を最小限に抑える | 限られたサイズと合金 |
ラピッドプロトタイピング、開発の加速 | 印刷材料の異方性 |
金属AMの主な利点は以下の通りである。 デザインの自由, パート統合, カスタマイズそして 製品開発の迅速化 サイクル。軽量化や材料の節約は、航空宇宙や自動車などの産業でも可能だ。
しかし、小さい 体積より高い 費用そして、その欠如である。 材料 商業規模での可用性は、従来の製造と比較して依然として障壁となっている。ほとんどの金属AMアプリケーションは、カスタマイズとリードタイム短縮の利点が今日のプリント部品コストの上昇を上回るような、少量から中量の生産に最適です。
金属AM装置と材料の価格が下落するにつれ、生産量と用途はより多くの産業で拡大し続けるだろう。品質の向上と造形サイズの拡大により、大量生産への採用が加速するだろう。
金属積層造形の未来
金属積層造形はまだ新興技術ではあるが、今後数年で大きく成長する見込みである。用途の拡大、新規参入企業、サプライチェーン全体での採用拡大が市場拡大の原動力となる。
- 世界の金属AM市場は、2028年までに$150億を突破し、2021年から2倍以上に拡大すると予測されている。航空宇宙と医療分野が需要の50%以上を占めると予想されている。
- システムメーカーは、連続生産アプリケーションに焦点を当てた、より大きな生産量のマシン、マルチレーザー、より高い生産性の装置を開発している。
- ニッケル超合金以外にも、より強度の高いアルミニウムや鋼、貴金属、マグネシウム、工具鋼など、利用可能な材料が広がっている。
- 高度な機械制御、ソフトウェア、試行錯誤を最小限に抑える合理化されたワークフローにより、品質と再現性は向上し続けている。
- AMによるサプライチェーンの最適化は、リードタイムが短縮され、プロトタイピングだけでなく、最終用途のコンポーネントの費用対効果が高まるにつれて、産業界全体で支持を集めている。
- カスタマイズされた分散型製造は、サプライチェーンのリスクと物流コストを削減する可能性がある。オンデマンドの現地生産が成長する。
- 各国政府は、産業用金属AMの研究、労働力開発プログラム、およびこの技術を中心とした地域の製造エコシステムの推進に多額の投資を行っている。
金属積層造形はまだ成熟途上にあるが、航空宇宙エンジンから患者に適合したインプラントまで、さまざまな用途で従来の製造と比較して明確な利点を示している。サプライチェーン全体でAMを採用する関係者が増えるにつれて、AMは製造業を変革し、設計革新の新時代を可能にするものと位置付けられている。
メタルAM よくある質問
Q: 金属3Dプリントに対応する素材は何ですか?
A: ステンレス鋼、アルミニウム合金、チタン、工具鋼、ニッケル超合金など、ほとんどの工業用金属を印刷できます。プロセスによっては、金、銀、プラチナなどの貴金属にも対応しています。
Q: 金属積層造形の精度はどのくらいですか?
A: ほとんどの粉末溶融炉の寸法精度は±0.1~0.2mm程度で、CNC機械加工と同様です。直接エネルギー蒸着は±0.5mm以上です。
Q: 金属AMは後処理が必要ですか?
A: 通常、表面仕上げや熱処理などの後処理が必要です。支持構造を除去し、表面を機械加工、サンディング、化学処理などで滑らかに仕上げます。
Q: 鋳造や機械加工と比較して、金属AMの利点は何ですか?
A: 設計の自由度、軽量構造、部品の統合、金型の削減、リードタイムの短縮、マスカスタマイゼーションなどの利点があります。AMは、サブトラクティブ技術では不可能な最適化された形状を可能にします。
Q: 金属3Dプリンティングの導入を促進している産業は何ですか?
A: 航空宇宙、医療・歯科、自動車、工業の各分野が、現在最も多く採用しています。この技術は、カスタマイズや軽量化がメリットの複雑な少量生産に最適です。
Q:金属AMは、従来の製造と比べてどのくらい高価ですか?
A: プリント金属部品は、大量生産にはまだ高価です。1000個以下の小ロットの場合、AMはコスト競争力があり、設計の柔軟性、市場投入までの時間の短縮、部品の統合、カスタマイズなどの利点によって相殺されます。
シェアする
MET3DP Technology Co., LTDは、中国青島に本社を置く積層造形ソリューションのリーディングプロバイダーです。弊社は3Dプリンティング装置と工業用途の高性能金属粉末を専門としています。
関連記事
Met3DPについて
最新情報
製品
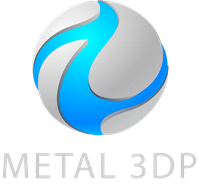
3Dプリンティングと積層造形用金属粉末