販売のための金属粉末
目次
概要 販売用金属粉末
金属粉末は、金属射出成形、積層造形、粉末冶金などの製造プロセスで使用される、細かく噴霧された金属材料です。重要な詳細情報 販売のための金属粉末:
- ステンレス鋼、チタン、ニッケル、アルミニウムなどの多くの合金が利用可能です。
- 最適な流動性と充填性を実現するには、粒子サイズは通常 5 ~ 45 ミクロンです。
- ガスアトマイズ、水アトマイズ、カルボニル分解、電気分解、粉砕により製造されます。
- 固体形状と比較して、単位重量あたりの表面積が大きくなります。
- 形態、サイズ分布、純度などの粉末の特性は厳密に管理されています。
- 小規模な研究開発バッチから大量の商業用量まで販売されます。
- バージングレードとリサイクルグレードの両方で提供されます。
- 航空宇宙、自動車、医療、産業市場にわたる最終用途コンポーネントの製造に使用されます。
一般的な金属粉末の種類
素材 | 主要物件 | 一般的な用途 |
---|---|---|
ステンレス | 耐食性、耐久性 | ポンプ、バルブ、工具 |
チタン合金 | 重量比強度が高い | 航空宇宙、医療用インプラント |
コバルトクロム | 耐摩耗性/耐腐食性 | 歯科、医療機器 |
ニッケル合金 | 耐熱性、靭性 | タービンブレード、ロケットノズル |
アルミニウム合金 | 軽量、導電性 | 自動車、エレクトロニクス |
さまざまな用途やプロセスの適合性に合わせて、多くのグレードや合金が用意されています。
金属粉末処理装置
設備 | 説明 |
---|---|
アトマイザー | 溶融合金を微細な液滴に変換し、凝固して粉末粒子にします。 |
ふるい | 粉末を特定の粒径範囲に分類します。 AMにとって重要です。 |
ミキサー | 混合した粉末を均質化し、均一な組成にします。 |
コンパクター | 圧力と熱を使用して粉末を緻密なコンパクトに圧縮します。 |
焼結炉 | 粉末を溶融直前まで加熱して圧縮し、強度を高めます。 |
純度や特性を維持しながら反応性微粉末を安全に取り扱うために必要な特殊な装置。
金属粉末 仕様
パラメータ | 代表値 | 役割 |
---|---|---|
粒子径 | 1~100ミクロン | 充填、拡散、溶融に影響を与える |
サイズ分布 | 狭い範囲 | 密度、流動性の向上 |
形態学 | 球状が好ましい | AMでの粉体流動を可能にします |
見かけ密度 | ソリッドの40-60% | 最終部品の密度に影響を与える |
タップ密度 | ソリッドの60-80% | 高いほど圧縮に優れています |
流量 | 25~35秒/50g | 高速粉体流動により AM の生産性が向上 |
酸化物含有量 | 重量で <0.5% | 酸化は材料特性に影響を与えます |
製造プロセスの要件と仕様に基づいて最適化された粉末特性。
金属粉末を販売するサプライヤー
サプライヤー | 材料 | 生産規模 |
---|---|---|
サプライヤー 1 | カスタム合金、高融点金属 | 小規模な研究開発バッチ |
サプライヤー 2 | ステンレス、工具鋼、ニッケル | 中~大容量 |
サプライヤー 3 | チタン、アルミニウム合金 | 大量生産 |
サプライヤー 4 | 難削材合金、貴金属 | 小ロット |
価格は、素材、品質、ロットサイズ、流通、リサイクルなどの要因によって異なります。
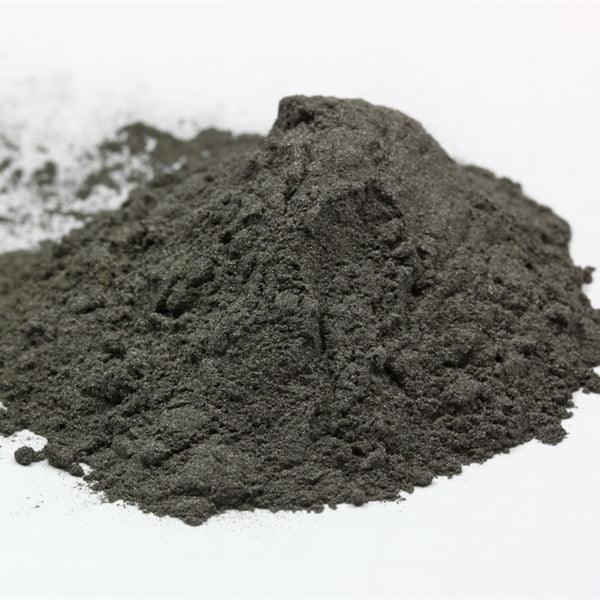
金属粉末サプライヤーの選び方
金属粉末のサプライヤーを選択する際に考慮すべき主な要素は次のとおりです。
- 素材オプション – サプライヤーは、貴社のプロセスと互換性のあるさまざまな合金を提供する必要があります。
- 品質システム – ISO 9001 または AS9100 認証は信頼できる品質管理を示します。
- 技術的専門知識 – 粉末製造と冶金に関する知識を求めます。
- ロットトレーサビリティ – サプライヤーは各粉末ロットに対して完全な認証を提供する必要があります。
- サンプリング – 独自の粉末分析と試験を行うためにサンプルを依頼します。
- 一貫性 – 粉末の組成と特性がロット間で異なってはなりません。
- 試験能力 – サプライヤーは、サイズ、形状、化学的性質などの粉末の特性を十分にテストする必要があります。
- 価格 – 希望する材料、数量、純度などについてサプライヤー間の価格を比較します。
お客様の用途のニーズと品質要件に重点を置いた金属粉末サプライヤーと提携してください。
AM処理用に金属粉末を最適化する方法
金属粉末を使用して高密度で欠陥のない 3D プリント部品を実現するには、次の AM プロセス最適化ガイドラインに従ってください。
- 粒度分布が厳密な、高純度の球状のガスアトマイズ粉末から始めます。
- 酸化や汚染を防ぐため、粉末は不活性ガス下の密閉容器に適切に保管してください。
- サイズ分布、形態、流量、密度、化学組成など、新しい粉末ロットを完全に特徴付けます。
- 予混合合金を均一にブレンドして、最終部品の組成勾配を防ぎます。
- 使用済みの粉末をふるいにかけてリフレッシュし、欠陥の原因となるサテライトや大きな凝集物を除去します。
- 粉末の粒子サイズに応じて層の厚さを調整します。比率は 10:1 から始めるのが良いでしょう。
- 酸化を避けるため、加工中は酸素/水分との接触を最小限に抑えてください。
- テストビルドで出力や速度などを変更することで、理想的なレーザー/電子ビームパラメータを調整します。
粉末サプライヤーと緊密に連携して、AM プロセスに最適な粉末特性を特定します。
粉末ベースの AM 部品の設計原則
金属粉末を利用するバインダージェッティング、DMLS、SLS などの積層造形プロセス向けの部品を設計する場合は、次の設計原則を考慮してください。
- 表面がサポートされていないことを防ぐため、45 度を超えるオーバーハングを避けてください。
- 破損を防ぐために、壁の厚さを 0.8 ~ 1 mm より大きく設計してください。
- 応力を軽減するために、コーナーに小さなフィレットと半径を含めます。鋭利な角は割れやすい。
- サポート要件を最小限に抑えるために、パーツをビルド チャンバー内に配置します。
- 最高の解像度を得るために、テキストなどの方向に依存するフィーチャを構築方向に沿って配置します。
- 可能であれば、サブアセンブリを 1 つの印刷パーツに統合します。
- 後処理ステップを考慮して、ストック材料にさらに 0.5 ~ 1 mm の余裕を持たせてください。
- 従来の製造可能性の制約ではなく、機能を考慮して形状を最適化します。
AM プロセス エンジニアと協力して、特定の金属粉末製造方法に合わせた部品を設計します。
金属AM部品の後処理
積層造形金属部品の一般的な後処理技術には、次のようなものがあります。
- サポート解除 – 部品から支持構造を慎重に取り外します。
- ストレス解消 – 部品を 600 ~ 800°C に加熱して、層状の蓄積による残留応力を軽減します。
- 機械加工 – CNC フライス加工、旋削、穴あけにより、寸法精度と表面仕上げが向上します。
- 研削 – 自動または手動の研削プロセスにより、より厳しい公差が得られます。
- 研磨 – 残留粒子/酸化物層を除去し、滑らかな表面仕上げを実現します。
- コーティング – 耐食性や耐久性を高めるために、陽極酸化などの機能性コーティングを適用します。
- 熱間静水圧プレス(HIP) – 高温と静水圧を加えることにより、内部構造をさらに高密度化します。
印刷された金属コンポーネントの取り扱いに精通した資格のあるオペレーターを使用して後処理を行います。部品を最終アセンブリに統合するために必要な手順を組み込みます。
インストールする方法 金属粉末-ベースのコンポーネント
設置および最終使用のために金属 AM 部品を準備する場合:
- 表面を徹底的に洗浄します。最適な接着のために、浮遊粉、酸化、油、フィルムなどを取り除きます。
- 必要に応じて保護コーティングと機能コーティングを適用します – 腐食、摩耗、摩擦などを改善します。
- 接合作業中は慎重に温度を制御してください。予熱速度と冷却速度が重要です。
- 応力を最小限に抑えるために、他の金属コンポーネントと嵌合するときの熱膨張の違いを考慮してください。
- 適切な接合技術を選択します。接着剤、機械的ファスナー、ろう付け、溶接はすべて効果的に使用できます。
- 鍛造材料と比較して、金属 AM 部品の延性と耐衝撃性が低いことを考慮します。ストレスが集中するものを避けてください。
- X線、超音波、浸透探傷試験などの技術を使用して定期的に検査を実行し、欠陥がないか確認します。
統合プロセス全体を通じて設計および製造エンジニアと協力して、パフォーマンス、信頼性、安全性を確保します。
粉末ベースの AM 部品の操作とメンテナンス
金属 AM コンポーネントから最適な稼働パフォーマンスを実現するには、次の手順を実行します。
- 合金の仕様に従って長期間使用する場合は、推奨温度範囲内で動作させてください。
- 疲労破壊につながる可能性のある過度の周期的応力を避け、追加の安全係数を計画してください。
- 過酷な環境での腐食損傷を防ぐために、保護コーティングと処理を使用してください。
- 使用中に部品の摩耗、亀裂、寸法の歪み、その他の劣化がないか定期的に確認してください。
- ベアリングやヒンジなどの可動印刷部品を分解して洗浄し、潤滑剤を再塗布します。
- AM を利用して、必要に応じて交換部品やスペアをオンデマンドで生産します。
- 元の CAD と寸法を定期的に比較してください。降伏強度に近い場合、材料は時間の経過とともにクリープする可能性があります。
合金と用途に精通したエンジニアと協力して、適切なメンテナンスのスケジュールと手順を作成します。
使用の長所と短所 金属粉末 従来の方法との比較
金属粉末ベースの AM の使用には、従来の製造アプローチと比較して利点と制限の両方があります。
メリット
- 複雑で有機的な形状を自由にデザインできます。
- 機能に合わせて最適化することで軽量化を実現。
- カスタマイズとラピッドプロトタイピング機能。
- 廃棄物の削減 - 必要な材料のみを使用します。
- サブアセンブリを単一の印刷パーツに統合します。
- 新しいコンポーネントの開発時間の短縮。
デメリット
- 少量生産では部品あたりのコストが高くなります。
- 層ベースの構造による異方性特性。
- 最終的な材料仕様を達成するには、後処理が必要になることがよくあります。
- パーツの最大サイズの制限。
- 展伸金属よりも延性と破壊靱性が低い。
- 粉末の品質と汚染に対するプロセスの敏感性。
生産量、コスト目標、品質ニーズ、アプリケーション要件と比較して、メリットとデメリットを比較検討します。
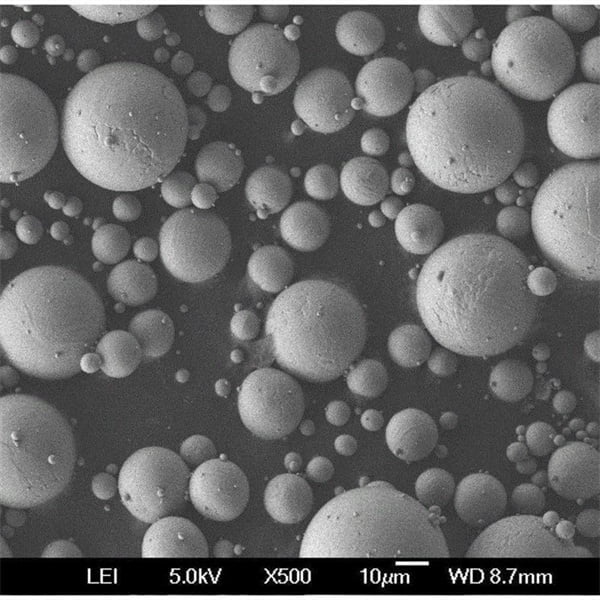
よくあるご質問
Q: 金属粉末を使用する主な利点は何ですか?
A: 従来の製造と比較して、設計の自由度、軽量化、部品の統合、迅速なプロトタイピング、無駄の削減、開発時間の短縮が可能です。
Q: 金属 AM 部品には通常どのような後処理方法が使用されますか?
A: 応力除去、機械加工、研削、研磨、コーティング、熱間静水圧プレスが一般的です。統合と組み立てに必要な手順を適用します。
Q: ほとんどの金属粉末はどのようにして製造されますか?
A: ガスアトマイズは、不活性ガス流によって溶融合金を急速に冷却して微細な粉末粒子にする一般的な製造方法です。
Q:金属粉末を取り扱う際の注意点は何ですか?
A: 微粉末の吸入を避けるために保護具を使用してください。火災の危険を制御するために、粉末は換気の良い場所で取り扱い、発火源を避けてください。
Q: 金属 AM 粉末の最適な粒径範囲はどれですか?
A: 通常は 10 ~ 45 ミクロンです。大きすぎると粉がうまく伸びません。細かすぎると固まったり吹き飛んだりする可能性があります。
Q: リサイクルパウダーはバージンパウダーとどう違うのですか?
A: リサイクルされた粉末は、適切にリフレッシュされていれば同等の性能を発揮できますが、サイズ分布が広くなったり、密度に影響を与える粒子が球状ではなくなったりする可能性があります。
Q: 入荷した金属粉末に対してどのような QC テストを行う必要がありますか?
A: 化学組成分析、粒度分布、形態チェック、流量試験、その他の特性評価を実施して、粉末の品質を検証します。
Q: どの合金が金属 AM プロセスと互換性がありますか?
A: チタン、ステンレス鋼、インコネル、アルミニウムなどのほとんどの標準合金を加工できます。一部の高炭素工具鋼は依然として課題が残っています。
シェアする
MET3DP Technology Co., LTDは、中国青島に本社を置く積層造形ソリューションのリーディングプロバイダーです。弊社は3Dプリンティング装置と工業用途の高性能金属粉末を専門としています。
関連記事
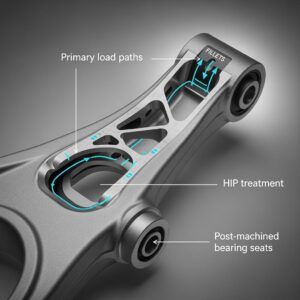