金属粉末製造
目次
概要
金属粉末 は、積層造形、金属射出成形、粉末冶金プレス・焼結などの製造技術の原料として使用される微細金属粒子である。化学組成、粒度分布、形態、微細構造を精密に制御して高度な特殊金属粉末を製造することは、完成部品の特性にとって極めて重要である。
さまざまな合金系から金属粉末を大量生産するためには、以下のようなさまざまな方法がある:
- ガス噴霧
- 水の霧化
- プラズマ霧化
- 電極誘導溶解ガス噴霧
- 回転電極プロセス
- カルボニルプロセス
- 電解プロセス
- 金属還元プロセス
それぞれの工程は、特定の用途に適した異なる特性を持つパウダーを生み出す。
金属粉末の製造方法
方法 | 使用金属 | 主な特徴 | 主な用途 |
---|---|---|---|
ガス噴霧 | チタン, アルミニウム, ステンレス鋼, 工具鋼, 超合金 | 球状パウダー、中程度の生産速度 | 金属射出成形、熱間静水圧プレス |
水の霧化 | 低合金鋼、鉄、銅 | 不規則な粉末形状、高い酸素含有量 | プレス・焼結工程 |
プラズマ霧化 | チタン合金、超合金 | 非常に微細な球状粉末 | 積層造形 |
回転電極 | タングステン、モリブデン、タンタル | 制御された結晶粒構造 | フィラメント、切削工具 |
カルボニルプロセス | 鉄、ニッケル、コバルト | 超微粒子高純度パウダー | 電子部品、磁石 |
電解 | 銅、ニッケル | 樹枝状薄片の形態 | 表面コーティング |
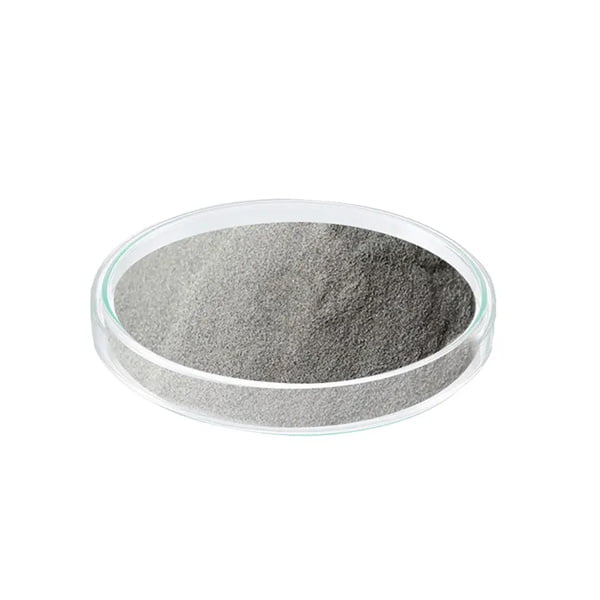
金属粉末 生産方法
異なる合金系から金属粉末を製造するために使用される様々な商業的方法がある。製造方法の選択は、以下のような要因に依存する:
- 合金材料の種類
- 純度要件
- 粒子径、形状、粒子構造など、ご希望の粉末特性
- 生産規模(トン/年
- パウダー最終用途
ここでは、金属粉末製造の最も一般的な工業プロセスを紹介する:
ガス噴霧プロセス
ガスアトマイズプロセスでは、溶融金属合金の流れは、通常窒素またはアルゴンの高圧ガスジェットによって分解される。金属流は微細な液滴に分解され、固化して粉末粒子になります。
ガスアトマイズ粉末は、球形で滑らかな表面形態を持つ。粒度分布は、プロセスパラメーターを調整することによって制御することができる。これは、チタン、アルミニウム、マグネシウム合金、ステンレス鋼、工具鋼、ニッケル超合金のような反応性材料に広く使用されている技術です。
パラメータ | 説明 |
---|---|
使用金属 | チタン合金、アルミニウム、マグネシウム、ステンレス鋼、工具鋼、超合金 |
粒子形状 | 球状の形態 |
粒子径 | 50 - 150 μm(代表値 |
純度 | 高濃度の不活性ガスで汚染を防止 |
酸素ピックアップ | 液体金属アトマイズと比較して最小 |
生産規模 | 年間最大1万トン |
水の霧化
水噴霧化では、溶融金属の流れに高速の水ジェットが当たる。急激な冷却により爆発が起こり、金属が微細な粒子に分解される。粉末は不規則な形状をしており、水との接触により酸素を多く含んでいる。
水アトマイズは、ステンレス鋼、合金鋼、鉄、銅の粉末をプレスや焼結タイプの用途に大量に製造するために使用される、より低コストのプロセスです。
パラメータ | 説明 |
---|---|
使用金属 | 炭素鋼、低合金鋼、ステンレス鋼、銅、鉄粉 |
粒子形状 | 爆発的な破水による不規則なモルフォロジー |
粒子径 | 10 - 300 μm(代表値 |
純度 | 低い位置で水と接触すると、酸素濃度が200~500ppm上昇する |
生産規模 | 非常に高く、年間5万トン以上 |
プラズマ霧化プロセス
プラズマアトマイズプロセスでは、プラズマトーチを使用して金属合金を溶解した後、ガスジェットによって微細な液滴に分解する。超高温のため、チタンアルミナイドのような反応性の高い元素をうまく霧化することができる。
粉末は球形に近い形状と狭い粒度分布をしており、レーザー溶融や電子ビーム溶融などの付加製造方法に適しています。
パラメータ | 説明 |
---|---|
使用金属 | チタン合金、ニッケル超合金、チタンアルミナイド |
粒子形状 | 球形度が高い |
粒子径 | 典型的には15~45μm |
純度 | 不活性雰囲気下で溶解するため、非常に高い純度 |
生産規模 | 低い、年間約100~1000トン |
回転電極プロセス(REP)
回転電極法では、円筒形の金属電極が真空チャンバー内で高速回転します。電気アークを使用して電極が溶解され、遠心力によって飛び散った溶融金属の液滴が冷却されて粉末になります。
REP 粉末は、タングステン、モリブデン、タンタルなどの航空宇宙用合金の細いワイヤやロッドへの熱間押し出しに最適な粒子構造と形態を備えています。
パラメータ | 説明 |
---|---|
使用金属 | タングステン、モリブデン、タンタル |
粒子形状 | 不規則で制御された微細構造 |
粒子径 | 45 – 150 μm(通常) |
純度 | 真空下での処理により非常に高い |
生産規模 | 少量の高価値粉末 |
電極誘導ガスアトマイズ(EIGA)
EIGA プロセスでは、誘導加熱を使用して、不活性ガス雰囲気内で消耗電極の先端を溶かします。液滴はアルゴン ジェットによって二次ガス噴霧され、微細な球状粉末になります。
EIGA は、制御された溶融と汚染の最小化を通じて、重要な航空宇宙部品用の反応性ニッケル超合金の非常に高い純度を実現します。
パラメータ | 説明 |
---|---|
使用金属 | ニッケル超合金、チタンアルミナイド |
粒子形状 | 球形 |
粒子径 | 15 – 53 μm(通常) |
純度 | 極めて高い、重要な合金向けにカスタマイズ |
生産規模 | 研究開発/試作から中量生産まで |
カルボニルプロセス
カルボニル法では、金属が揮発性カルボニルに変換され、制御された条件下で分解して均一な超微細金属粒子が生成されます。この方法は、高純度の鉄、ニッケル、コバルトの粉末を製造するのに適しています。
パラメータ | 説明 |
---|---|
使用金属 | 鉄、ニッケル、コバルト |
粒子形状 | 球形から多面体へ |
粒子径 | 典型的には1~10μm |
純度 | 極めて高い99.9%+純度 |
生産規模 | 年間最大3万トン |
その他の粉末製造方法
特殊金属粉末の製造に使用されるその他の技術には以下のものがあります。
- 電解プロセス: 電着法によって樹枝状形態の不規則な形状の銅およびニッケル粉末を製造するために使用される。
- 金属還元プロセス: 水素または炭素を使用して金属酸化物を還元し、チタン、ジルコニウム、タングステン、モリブデンの粉末を製造する
- 機械的合金化: 複合材料およびナノ構造合金を合成するための高エネルギーボールミル処理
金属粉末 仕様
金属粉末に対してテストされる重要な品質特性と仕様は、製造方法と最終用途によって異なりますが、通常は次のものが含まれます。
粉末化学
- 発光分光法または蛍光X線分光法による合金組成
- 微量合金元素
- 酸素、窒素、水素などの不純物元素
- 高温での強熱減量試験
粒度分布
- 体積平均粒子サイズ
- D10、D50、D90などの分布幅
粒子形状特性評価
- 形態学のための走査型電子顕微鏡
- アスペクト比やフォームファクタなどの形状要因
微細構造
- X線回折法で観察される相
- 画像から粒子特性を分析
粉末の特性
- 見かけ密度/タップ密度
- ホール流量計ファンネルテストによる流量
- 圧縮レベル
粉末の仕様要件は、さまざまな用途での最終用途に応じて大きく異なります。
パラメータ | 金属射出成形(MIM) | アディティブ・マニュファクチャリング | プレス・焼結 |
---|---|---|---|
粒子径範囲 | 3 – 25μm | 15 - 45 μm | 150 – 300 μm |
アスペクト比 | 1 – 1.25が望ましい | <1.5 球面 | 重要ではない |
酸素レベル | <1000 ppm | <500ppm | 2000~4000ppm |
見かけ密度 | >2.5 g/cm3 | >2.8 g/cm3 | 2~3g/cm3 |
ホール流量 | 15~35秒/50g | 25~35秒/50g | >12秒/50g |
特性評価方法
製品の性能に不可欠な金属粉末の特性を評価するために使用される分析方法はいくつかあります。
粒子サイズ分析
レーザー回折法は、粒子サイズ分布の特性評価に最も広く使用されています。この技術では、レーザー光線を分散粉末サンプルに通し、粒子サイズに応じた角度で光を散乱させます。回折パターンをコンピューターで分析すると、数秒以内に統計的に関連のある詳細なサイズ分布データが得られます。
形態学と表面イメージング
走査型電子顕微鏡 (SEM) は、光学顕微鏡に比べてはるかに高い倍率と焦点深度で、粉末粒子の形状、表面トポグラフィー、特徴の高解像度画像を提供します。
SEM イメージングは、粒子の丸み、サテライトの形成、表面の滑らかさ、多孔性などの欠陥を研究するために使用されます。
密度と流動特性の測定
バルク挙動を定量化するための標準試験方法は、以下を使用して確立されています。
- オリフィスを通る粉末の流量を測定するホール流量計漏斗
- 安息角で流動性を評価するカーニー漏斗
- タップ密度と圧縮率を測定するためのスコット容積計
これらの方法は、部品製造時の取り扱い、ブレンド、ダイ充填、広がりの容易さを予測するのに役立ちます。
組成と結晶構造を調べるためのX線法
- X線蛍光分光法は金属の元素組成を正確に識別し定量化する。
- X線回折は、回折ピークパターンによって存在する原子配列と位相を分析します。
金属粉末の用途
エンジニアリング金属粉末の主な最終用途は次のとおりです。
アディティブ・マニュファクチャリング
選択的レーザー溶融法 (SLM)、直接金属レーザー焼結法 (DMLS)、電子ビーム溶融法 (EBM) などの 3D 印刷技術としても知られ、チタン、アルミニウム、ステンレス鋼、超合金、コバルトクロム粉末から複雑な形状を構築します。
金属射出成形(MIM)
ステンレス鋼、チタン合金、工具鋼などの粉末をバインダーと混合し、射出成形してから焼結することで、小型で複雑な部品を低コストで大量に製造します。
粉末冶金プレスと焼結
鉄、銅、合金鋼の粉末を圧縮・焼結して、ギア、ブッシング、磁石などの大容量部品を製造します。
申し込み | 使用金属 | 主な不動産ニーズ |
---|---|---|
積層造形 | チタン合金、ニッケル超合金、アルミニウム、工具鋼、ステンレス鋼、コバルトクロム | 球状形態 良好な流動性 高純度 |
金属射出成形 | ステンレス鋼、チタン、工具鋼、タングステン重合金 | 25μm未満の微細粉末 良好な充填密度 |
プレスと焼結 | 鉄、鋼、ステンレス鋼、銅 | コスト効率の高い粉末潤滑コーティング |
溶接、ダイヤモンド工具、電子機器、表面コーティングなど、特殊金属粉末を使用する分野でのニッチな用途もあります。
サプライヤーと価格
さまざまな金属粉末の世界的な大手サプライヤーは次のとおりです。
会社概要 | 生産方法 | 材料 |
---|---|---|
サンドビック・オスプレイ | ガス噴霧 | チタン、アルミニウム、ニッケル合金 |
エーピーアンドシー | プラズマ霧化 | チタンアルミナイド、超合金 |
カーペンター・テクノロジー | ガス、水噴霧 | 工具鋼、ステンレス鋼、合金 |
ヘガネス | 水の霧化 | 鉄、ステンレス鋼 |
JFEスチール | 水の霧化 | ステンレス鋼粉末 |
リオ・ティント | アルミニウム粉末 | カルボニルニッケルと鉄 |
金属粉末の価格は、以下の要因によって大きく異なります。
- 合金の材質と組成
- 使用される製造方法
- 粒子特性を実現するための処理
- 純度レベルと汚染度
- 購入量 – 非常に大量の契約では価格が下がる
1 キログラムあたりの一般的な基本価格は次のとおりです。
素材 | 価格見積もり |
---|---|
ステンレス 316L | $12 – $30 / kg |
アルミニウム AlSi10Mg | $15 – $45 / kg |
チタン Ti-6Al-4V | $80 – $220 / kg |
ニッケル超合金インコネル718 | 1kgあたり$90~$250 |
AM用特殊合金 | 1kgあたり$250~$1000 |
高度にカスタマイズされた粒度分布、100 ppm 未満の酸素および窒素レベルの制御、および小ロット購入の場合、価格が大幅に上昇します。
粉末冶金の利点と限界
粉末冶金の利点
- 鋳造や機械加工では不可能な複雑な形状を製造できる能力
- ニアネットシェイプ製造により材料の無駄を削減
- より高性能な金属や合金を使用できる
- インゴット冶金では一貫した多孔構造は不可能
- コンポーネントは大量カスタマイズ可能
粉末製造と処理の限界
- 生産設備や処理設備への資本投資は非常に高額である
- 表面積が大きくなると、自然発火性の反応性粉末の取り扱いが危険になる
- 高い圧縮密度を達成するには高圧が必要になる場合がある
- 鋳造と比較した追加のプロセスステップ
- 粉末がLO/NOであるためAMマシンの携帯性が高い
粉末冶金と従来の鋳造プロセスを簡単に比較すると次のようになります。
パラメータ | 粉末冶金 | キャスティング |
---|---|---|
複雑な形状 | ✅ レイヤードAMビルドに最適 | 一般的な鋳造品に限定 |
機械的特性 | 熱間等方圧プレス後の鋳造特性に近づくことができる | ✅ 予測可能な特性 |
サイクルタイム | AM方式ではプロセスが遅い | ✅ 大量生産が速い |
寸法精度 | 後処理によって異なる | 精密鋳造に最適 |
設備費 | 産業用AMマシンとしては非常に高い | ✅ 資本コストの削減 |
金属の種類 | 継続的に拡大するオプション | ✅ 最も幅広い選択肢 |
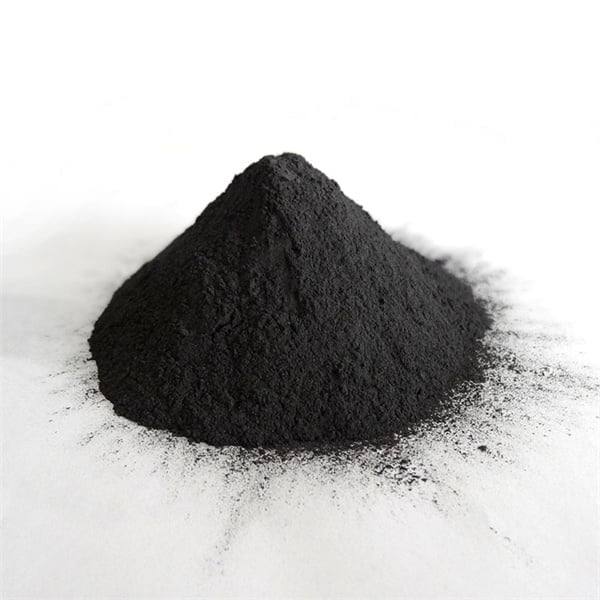
よくあるご質問
Q: 金属 3D プリント粉末に使用される一般的な粒子サイズの範囲はどれくらいですか?
A: 選択的レーザー溶融 (SLM) や電子ビーム溶融 (EBM) などの粉末床技術では、最適な粒子サイズの範囲は 15 ~ 45 ミクロンです。粉末が細かくなるほど解像度は向上しますが、取り扱いや処理が難しくなる場合があります。
Q: さまざまな方法による金属粉末の形態は何によって決まりますか?
A: ガスジェットや水衝撃による溶融ストリームの破壊力の強さやその後の冷却速度などの製造要因によって粒子の形状が決まります。冷却が速いと不規則な樹枝状粒子が生成され、凝固が遅いと(球状噴霧)滑らかな丸い構造になります。
Q: 積層造形における金属粉末の高純度が重要なのはなぜですか?
A: 不純物は欠陥や多孔性の問題を引き起こし、合金の微細構造を変え、密度を低下させ、負荷や温度下での性能に影響を及ぼし、機械的特性に悪影響を及ぼす可能性があります。目標酸素レベルは 500 ppm 未満、窒素レベルは 100 ppm 未満が一般的となっています。
Q: 輸送中および保管中に金属粉末はどのように安全に取り扱われますか?
A: 反応性金属粉末は不動態化処理され、酸化表面を形成して可燃性リスクを最小限に抑えます。粉末は、発火を防ぐために、輸送中は空気ではなくアルゴンなどの不活性ガス下でドラムに密封されます。保管容器は適切に接地する必要があります。作業員は取り扱い時に特殊な PPE を着用します。
Q: 一般的な粉末特性評価方法は何ですか?
A: ホール流量測定、タップ密度試験、比重測定法、LOI 試験、分光分析、金属組織学、レーザーまたはふるい技術を使用した粒度分布は、挙動の定量化、金属粉末製造の品質プロセス制御の構築、および特定の用途に対するバッチ適合性の評価に不可欠です。
シェアする
MET3DP Technology Co., LTDは、中国青島に本社を置く積層造形ソリューションのリーディングプロバイダーです。弊社は3Dプリンティング装置と工業用途の高性能金属粉末を専門としています。
関連記事
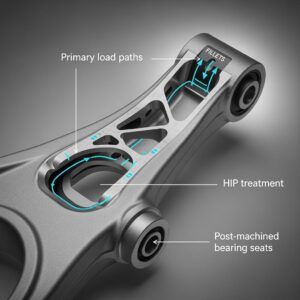