パウダーベッド・フュージョン
目次
概要
粉末床溶融は、熱エネルギーを使用して粉末床の領域を層ごとに選択的に溶融し、部品を造形する積層造形プロセスである。現在、生産用途で最も一般的に使用されている金属3Dプリンティング技術の1つです。
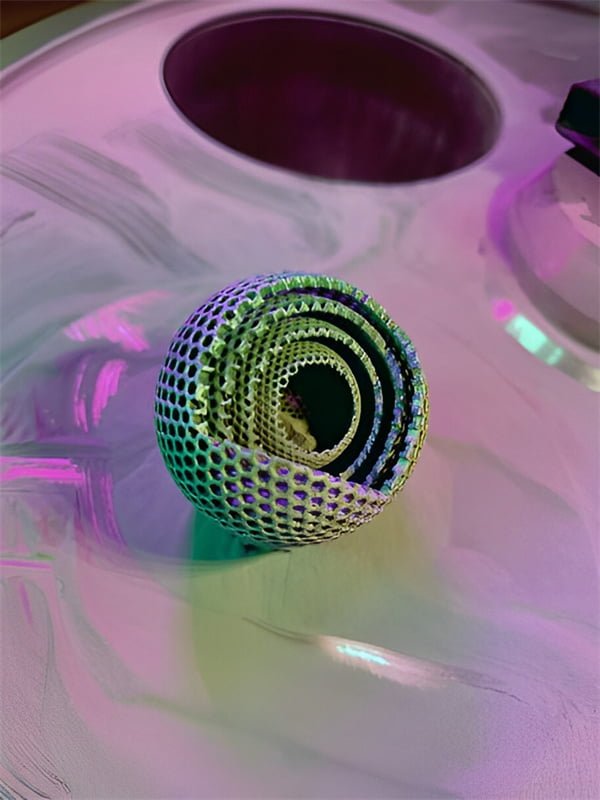
パウダーベッド融解に関するいくつかの重要な詳細:
- アディティブ・マニュファクチャリングのバット光重合に属する。
- レーザーや電子ビームのような熱エネルギー源を使用して、材料の粉末を溶かして融合させる。
- 使用される粉末は通常、ステンレス鋼、チタン、アルミニウム、ニッケル合金、コバルトクロムなどの金属である。ポリマーやセラミックもプロセスによっては使用できる。
- 粉末床溶融は、従来の製造に匹敵する機械的特性を持つ、完全に緻密な金属部品を作ることができる。
- 従来のサブトラクティブ技術では不可能だった複雑な形状が可能になる。
- 用途は、航空宇宙、医療、歯科、自動車、一般産業など多岐にわたる。
- 一般的なパウダーベッド技術には、選択的レーザー溶融(SLM)、直接金属レーザー焼結(DMLS)、電子ビーム溶融(EBM)、バインダージェッティングなどがある。
粉末床溶融プロセス
開発された粉末床溶融技術にはいくつかの種類がある。主なものは以下の通り:
プロセス | 説明 |
---|---|
選択的レーザー溶融 (SLM) | 高出力レーザーを使用して、ベッド内の金属粉末を完全に溶融・融合させる。 |
ダイレクトメタルレーザー焼結(DMLS) | SLMに似ているが、完全溶融ではなく粉末の焼結を目的としている。 |
電子ビーム溶解(EBM) | 電子ビームをエネルギー源として粉末を溶かす。真空中で行う。 |
マルチ・ジェット・フュージョン(MJF) | エネルギー源で焼結する前のポリマー粉末床に定着剤をインクジェット印刷する。 |
バインダー・ジェット | 液体結合剤を選択的に堆積させて粉末材料を結合させ、その後焼結する。 |
選択的レーザー溶融(SLM) は、今日使用されている最も一般的な粉末溶融技術である。高出力レーザー(ファイバー、CO2、YAGなど)をパウダーベッドに集光し、メルトプールを形成して材料を溶融する。各レイヤーが終わるとパウダーベッドは下がり、新しいパウダーがその上に散布される。SLMは完全溶融を使用するため、完全に高密度な部品を作ることができる。ステンレス鋼、チタン、アルミニウム、インコネルなどの材料が一般的に使用される。
ダイレクトメタルレーザー焼結(DMLS) も同様の操作を行うが、粉末を部分的に溶融して粒子間にネックを形成し、固体部品を製造することを目的としている。DMLSは、SLMに比べてレーザー出力に対する要求が低い。
電子ビーム溶解(EBM) は、真空下で集束した電子ビームをエネルギー源として使用し、金属粉末を層ごとに溶融する。EBMは、ビームがより速くスキャンできるため、レーザーベースのプロセスよりも高い造形速度を可能にする。EBMは、主に航空宇宙用途のチタン合金で使用されています。
マルチジェット核融合(MJF) MJFは、インクジェット印刷ヘッドを使用して、ポリマー粉末床に定着剤を選択的に付着させ、その後エネルギー源によって焼結させる。MJFは熱可塑性プラスチックの高速焼結を可能にする。
バインダー噴射 まず、粉末材料を結合させるために、選択された領域に液体結合剤を沈殿させ、次に焼結して部品を緻密化する。金属、セラミック、ポリマーに使用できる。
パウダーベッド融合材料
粉末床溶融積層造形では、さまざまな材料を使用することができる。最も一般的なものは以下の通りです:
素材 | プロセス | アプリケーション |
---|---|---|
ステンレス | SLM、DMLS、バインダージェッティング | 医療用インプラント、工具、一般エンジニアリング |
チタン合金 | SLM、EBM | 航空宇宙および医療用インプラント |
アルミニウム合金 | SLM、EBM | 自動車および航空宇宙の軽量化 |
ニッケル超合金 | SLM、EBM | タービンブレード、極限環境用ロケットノズル |
コバルトクロム | SLM、DMLS | 歯科インプラントと補綴 |
ポリマー | MJF、バインダージェッティング | プロトタイピングと最終使用プラスチック部品 |
セラミックス | バインダー噴射 | 医療用インプラント、航空宇宙 |
最も広く使われているのは ステンレス鋼耐食性と機械的特性に優れている。 チタン合金 Ti6Al4Vのような材料は、鋼やニッケル合金よりも軽量化できるため、航空宇宙分野で人気がある。 アルミニウム合金 自動車や航空宇宙用の軽量部品を可能にする。
ニッケル超合金 インコネルは高温タービンブレードやロケットノズルに使用される。 コバルトクロム合金 は生体適合性があり、歯科修復に広く使用されている。 ポリマー ナイロン、PEEK、ポリアミドなどのプラスチック部品を焼結することができる。 セラミックス ジルコニアやアルミナのようなものは、医療用インプラントに応用されている。
粒度分布、流動性、充填密度、融点は、加工性と最終部品の特性を決定する重要な粉末材料の特性である。
パウダーベッド融合の応用
粉末床溶融積層造形は、航空宇宙、医療、歯科、自動車、および一般的なエンジニアリング業界全体で使用されています。代表的な用途は以下の通り:
産業 | アプリケーション |
---|---|
航空宇宙 | タービンブレード、ロケットノズル、翼、人工衛星、ドローン |
メディカル | 整形外科用および歯科用インプラント、補綴物、手術器具 |
自動車 | 軽量化プロトタイプ、カスタム金型 |
インダストリアル | 金属工具、鉱山機械、液体処理 |
建築 | 装飾、ファサード、照明、家具 |
で 航空宇宙粉末床溶融法は、人工衛星やUAVのような一品生産の部品に最適です。タービン、ノズル、機体などの軽量チタンやニッケル合金部品に使用されます。
について メディカルカスタマイズされたチタンやコバルトクロムのインプラントや補綴物は、主要な応用分野である。また、個人化された手術器具も可能にする。
で 自動車パウダーベッドは、軽量プロトタイプや治具のようなカスタム金型や治具に使用されます。用途 インダストリアル また、特殊な工具、治具、最終用途の金属部品も製造できる。
で 建築パウダーベッドフュージョンは、建築物や家具の装飾的・機能的要素のためのユニークな形状を容易にします。
パウダーベッド融合の利点
粉末溶融技術の主な利点には、以下のようなものがある:
- 複雑な形状 - 複雑な内部構造や格子も可能だ。
- カスタマイズ - 部品は個々の用途に合わせて調整することができる。
- 軽量化 - 設計を最適化することで部品の重量を減らす。
- 統合 - アセンブリを単一部品にまとめる。
- 高強度 - 錬成材に匹敵する強度を持つ、完全に緻密な金属。
- リードタイムの短縮 - デジタルファイルから部品への迅速なターンアラウンド。
- マス・カスタマイゼーション - 規模の経済と部品のカスタマイズを組み合わせた。
- 持続可能性 - 減算法に比べて廃棄物が少ない。
カスタムメイドの複雑な形状を持つ高密度の金属部品を製造する能力により、粉末溶融炉はあらゆる産業分野の軽量で高性能な部品に理想的なものとなっている。この技術は、アセンブリを単一部品に統合することを可能にし、製造コストと在庫コストを削減します。また、積層造形の使用により、CNC機械加工のような従来の減法的手法よりも材料の無駄が大幅に削減されます。
パウダーベッド融合の限界
現在の制限事項には以下のようなものがある:
- サイズの制約 - 建設量は通常1立方メートル未満。
- 表面仕上げ - 後処理を必要とする階段状の効果。
- ビルド速度 - 大量生産方式よりも遅い。
- 異方性 - 材料特性の方向性の変化。
- 規格 - 規格や仕様の欠如。
- ソフトウェア - デザインルールとファイル作成の複雑さ。
- 費用 - 設備や資材のコストはまだ比較的高い。
最大部品サイズは、機械の造形容積によって制限され、改善されつつあるが、それでも通常は1立方メートル未満である。レイヤー・バイ・レイヤー・プロセスのため、表面仕上げが悪くなり、平滑化や研磨が必要になることがある。
全体的な造形速度は、射出成形のような大量生産技術に比べて遅い。部品はまた、造形方向によって異方性を示すこともある。航空宇宙や医療といった規制の厳しい業界では、プリント部品の品質に関する規格や仕様がないことも制約となっている。最適な部品を設計し、ファイルを前処理するには、高度なソフトウェアの専門知識が必要です。
システムコストと材料コストは、従来の製造に比べればまだ比較的高い。しかし、採用が進むにつれてコストは低下しており、部品の性能、カスタマイズ、設計の柔軟性により、コストを正当化できる用途も多い。
後処理
後工程とは、完成部品を得るために、造形工程の後に必要な工程を指す:
- 粉の除去 - 部品はブラシを使って未溶融粉末から分離される。
- 除去をサポート - 支持構造を切断し、表面を洗浄する。
- 表面仕上げ - サンディング、研磨、ビーズブラストによる改善
プロセス・パラメーター
粉末床溶融には、特性、性能、生産性を最適化するために調整可能ないくつかの重要なプロセスパラメーターがある:
パラメータ | 典型的な範囲 | 効果 |
---|---|---|
レーザー出力 | 50-500W | 溶融速度、メルトプールサイズ、深さへの浸透性 |
スキャン速度 | 100-10,000 mm/s | 凝固速度、冷却速度、微細構造 |
ハッチの間隔 | 50-200 μm | オーバーラッピングトラック、密度、接着強度 |
層厚 | 20-100 μm | 解像度、表面粗さ、ビルドタイム |
スキャン戦略 | 島、ストライプ、チェス盤 | 残留応力、歪み、異方性 |
プロセス雰囲気 | 真空、不活性ガス | 酸化、汚染、多孔性 |
レーザー出力 は、投入エネルギー、溶融速度、メルトプールの寸法、浸透深さに影響する。 スキャン速度 は、凝固速度と冷却速度を制御し、結晶粒の形態と欠陥形成に影響を与える。
ハッチの間隔 はスキャントラック間の間隔を設定し、レイヤー間のオーバーラップ、高密度化、結合に影響する。 層厚 は、解像度、表面粗さ、および総加工時間を決定する。
スキャン戦略 (スキャンパターン)は、印刷方向に基づく残留応力、歪み、異方性特性に影響を与える。 プロセス雰囲気 は酸化と汚染のレベルを決定する。
粉体リサイクル
- 未溶融パウダーを採取し、ふるいにかけて大きな粒子を取り除くことができる。
- 通常20サイクルまで再利用可能
- 粉体コストを大幅に削減
- 新鮮なパウダーを補充し、相性を維持する。
- 再利用のしきい値を監視する物件
粉末床溶融プロセスでは、未溶融の粉末を再利用し、さらに製造する。脱パウダーの後、ルースパウダーを採取し、ふるいにかけて大きな粒子を取り除き、新しいパウダーとブレンドしてから再利用する。
一般的な再利用率は、材料、粒子径の変化、汚染レベルにもよりますが、最大20サイクルです。この再利用により、材料効率が大幅に改善され、部品全体のコストが削減されます。再利用される粉末の比率と特性は、リフレッシュ率を決定するためにモニターされます。
品質管理
粉末溶融炉で使用される主な品質管理手段には、以下のようなものがある:
- 粉体の化学分析
- 粒度分布分析
- パウダー再利用トラッキング
- メルトプール監視
- 部品形状検査
- 機械的特性試験
- 非破壊検査(X線など)
- CTスキャンによる内部欠陥の検査
- 表面粗さ測定
投入された粉体の化学的性質と粒度分布が分析され、高品質が保証される。パウダーのリフレッシュ率が追跡されます。メルトプール監視のような工程内監視システムは、造型中の欠陥を検出します。
プリント部品の幾何公差を測定します。機械試験では、プロセス・パラメータと造形方向に基づいて特性を評価します。非破壊検査とCTスキャンで内部の欠陥を特定します。表面仕上げを評価します。すべてのデータは、工程の校正と最適化のために分析されます。
コスト分析
一般的な粉末溶融炉の部品コストは以下の通りである:
- 機械減価償却
- 材料費
- 前処理と後処理の労力
- 建設時間とエネルギー消費
- 再利用可能な粉の量
- 購入比率
機械設備費は、使用状況に応じて予想耐用年数で償却する。材料費は、部品の数量と購入比率に基づいて計算される。人件費には、ファイルの準備、セットアップ、デパウダリング、仕上げの各工程が含まれます。
エネルギー使用量は、造型時間と出力レベルに依存する。再利用可能なパウダーは、全体的な材料費を削減します。3:1から20:1の購入対飛行比は、高価値部品では一般的です。
サプライヤー
主な粉末床溶融システム・サプライヤーには次のようなものがある:
サプライヤー | キーテクノロジー |
---|---|
イーオーエス | DMLS (直接金属レーザー焼結) |
3Dシステムズ | DMP(ダイレクトメタルプリンティング) |
GEアディティブ | DMLM (ダイレクトメタルレーザー溶融) |
トルンフ | TruPrint 金属3Dプリンター |
シスマ | レーザー金属溶融システム |
追加 | フォームアップ金属3Dプリンター |
イーオーエス そして 3Dシステムズ は、粉末溶融炉の初期のパイオニアであり、今日もリーダーであり続けている。 GEアディティブ はConcept Laser社とArcam EBM社を買収し、レーザーと電子ビームの両技術を提供する。 トルンフ そして シスマ また、産業用SLMシステムも提供している。 追加 はミシュランとファイブスの合弁会社で、金属積層造形に焦点を当てている。
また、カーペンター、サンドビック、プラクセア、LPWテクノロジー、AP&Cなど、粉末床溶融用材料のサプライヤーも多い。
コスト比較
プロセス | 設備費 | 材料費 | スピード |
---|---|---|---|
パウダーベッド融合 | $100K - $1M+ | $100-500/kg | 5~100cm3/時 |
CNC加工 | $50K - $500K | $5-50/キロ | 50~500cm3/時 |
射出成形 | $100K - $1M+ | $2-5/kg | 100~1000cm3/時 |
パウダーベッドシステムは、産業用プリンターで$10万円から、大規模生産システムで$100万円以上と、設備コストが高い。材料は$100-500/kgの範囲である。生産速度は技術によって5-100cm3/hrと異なります。
CNC加工は$50,000前後から設備費が安い。金属材料費は$5-50/kgと安い。加工速度は毎時50~500cm3です。
射出成形システムも$100,000以上する。しかし、プラスチック材料は$2-5/kgと非常に安い。速度は100-1000cm3/時です。
従って、粉末溶融炉が費用対効果に優れるのは、性能が高いコストに見合う、少量で高価値の金属部品に限られる。
パウダーベッド・フュージョンとバインダージェッティングの比較
パウダーベッド・フュージョン | バインダー・ジェット | |
---|---|---|
材料 | 金属、ポリマー、セラミック | 金属、ポリマー、セラミック |
密度 | 完全高密度部品 | 多孔質部分、浸透が必要 |
精度 | 中、±0.1%(後処理あり | 中、±0.2% |
表面仕上げ | 中程度、仕上げが必要 | フェアで層状の質感が残る |
スピード | 遅い、エネルギー源に依存 | エネルギー源に依存しない高速性 |
アプリケーション | 最終用途金属部品 | 金型、鋳造パターン、プロトタイプ |
- 粉末床溶融は完全に緻密な部品を作ることができるが、バインダージェッティング部品は多孔質であり、浸透を必要とする。
- バインダージェッティングの精度は中程度だが、パウダーベッドフュージョンは後処理によってより高い精度を達成できる。
- パウダー・ベッド・フュージョンの表面仕上げには仕上げが必要だが、バインダー・ジェットは層状のテクスチャー仕上げとなる。
- バインダージェットの造粒速度は、エネルギー源によって制限されるパウダーベッドプロセスよりもはるかに速い。
- パウダーベッドは最終用途の部品に多く使用され、バインダージェッティングは金型、鋳造、コンセプトモデルに適している。
粉末床融合と直接エネルギー蒸着の比較
パウダーベッド・フュージョン | 体外式除細動器 | |
---|---|---|
材料 | 主に金属 | 金属、ポリマー |
幾何学 | 複雑さを可能にする | 中程度の複雑性 |
精度 | 中~高 | ミディアム |
表面仕上げ | 中程度、仕上げが必要 | ラフ、さらに仕上げ |
スケーラビリティ | 中小部品 | 中型から大型部品 |
蒸着率 | 低、スキャン速度による | 高いが、ノズルを大きくすると増加する |
- 粉末溶融炉は主に金属で使用されるが、DEDは金属とポリマーを使用できる。
- 粉末溶融炉は、幾何学的な制約があるDEDよりも複雑な溶融が可能である。
- 精度はパウダーベッド融合の方が高い。DEDの精度は中程度。
- DEDは、添加物ビーズにより、より多くの仕上げを必要とする粗い表面を作り出す。
- 粉末溶融炉はより小さな部品を製造し、DEDは中型から大型のニアネットシェイプを製造する。
- DEDはブローパウダー方式を採用しているため、蒸着速度がはるかに速い。
そのため、一般的に粉末溶融炉は、小さくて複雑な形状を中程度の速度で製造する。DEDは、より大きな単純な形状をより速く作るが、仕上げ作業が多くなる。
パウダーベッド融合の未来
粉末溶融炉の今後の開発分野には、以下のようなものがある:
- 最大数立方メートルまでの大容量製造
- 製造速度を向上させるスキャン方法の高速化
- 高温合金、MMC、ポリマーなどの拡張材料
- 粉末冶金とCNCを統合したハイブリッド製造
- 自動化されたデパウダリングと後処理
- 高度なリアルタイム・モニタリングと制御
- より厳格な資格認定手続き
より大きな造形プラットフォームは、より大きな部品や、より高い生産スループットを可能にする。新しい高速スキャン技術により、造形速度が飛躍的に向上する。材料の選択肢は、特に高性能合金へと拡大し続けるだろう。
シェアする
MET3DP Technology Co., LTDは、中国青島に本社を置く積層造形ソリューションのリーディングプロバイダーです。弊社は3Dプリンティング装置と工業用途の高性能金属粉末を専門としています。
関連記事
Met3DPについて
最新情報
製品
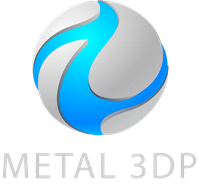
3Dプリンティングと積層造形用金属粉末