粉体製造:用途、メンテナンス、利点
目次
パウダー製造 粉体製造とは、様々な産業で様々な用途に使用される粉体を製造するために使用される工業プロセスを指します。このガイドでは、主要な装置、プロセス、アプリケーション、サプライヤーやシステムを選択する際の考慮事項など、粉体製造の詳細な概要を説明しています。
パウダー製造の概要
粉体製造は、サブミクロンから数千ミクロンの固体材料の微粒子を製造する。粉末は、金属、セラミック、プラスチック、顔料、医薬品、食品などの製品に広く使用されている。
世界の粉末製造市場は2022年に325億米ドルとなり、2023年から2030年までのCAGRは7.2%で成長すると予測されている。製薬セクターが世界粉末市場の30%以上で最大のシェアを占めている。しかし、金属粉末分野は自動車と航空宇宙用途に牽引されて最も高い成長を示している。
粒度分布、形態、密度、流動性などの粉体特性は、アプリケーションの要件を満たすために、製造プロセスを通じて厳密に制御する必要があります。粉末製造の主な4つのステップは以下の通りである:
- 製造 機械的粉砕または化学的処理による粉末の製造
- 分類 ふるい、分級機、またはエアセパレーターを使用した粒子径に基づく
- 修正 粉砕、造粒、乾燥、混合、その他の処理による粉体特性の変化
- 配合 他の粉末や添加物とのブレンドによる
粉末製造技術の選択は、材料、最終的な粒子径と分布、粉末の形態、純度、使用目的によって決まる。
パウダー製造の主な利点
- 高い表面積/体積比が反応性、溶解性、性能を高める
- 所望の特性に合わせた粒子径と粒子分布の調整能力
- パウダーベースのプロセスが複雑な形状の製造を可能にする
- バルク材に比べ低い処理温度でエネルギーを節約
- 多孔質粉末成形品は、強度と低密度のユニークな組み合わせを持っている。
粉体製造の課題
- 粉塵の発生と取り扱いによる安全衛生上の危険性
- 粉末は、可燃性粒子が空気中に浮遊すると爆発する可能性がある。
- 粉体の搬送、混合、圧縮に特化した装置が必要
- 粒子の凝集は、製品の流動性と均一性に影響を与える可能性がある。
- 商業規模での一貫した粉体特性の制御と維持
粉体製造に使用される装置
さまざまな専用装置や機械が、目的の特性を持つ粉体を製造し、最終製品に加工するために使用される。ここではその概要を紹介する:
設備 | 説明 |
---|---|
ボールミル | セラミックボールや金属ボールなどの粉砕メディアを部分的に充填した円筒を回転させ、衝撃と摩擦によって材料を粉砕し、微粉末にする。 |
ハンマーミル | スイングハンマーを使用し、高速でスクリーンに原料を当てて粉砕する。粗粉砕に有効。 |
コロイドミル | 高いせん断力を持つローター・ステーター機構を採用し、懸濁物質をサブミクロンサイズに粉砕する。 |
ジェットミル | 高圧エアジェットを利用し、粒子間の衝突により粒径を縮小。ミクロン、サブミクロンの粉砕が可能。 |
萎縮工場 | インペラでスラリーを攪拌し、粒子同士をせん断・衝突させて粉砕する。 |
スプレードライヤー | 液体混合物を熱風で噴霧し、水分を蒸発させることにより、急速に微粉末に乾燥させる。 |
空気分級機 | 抗力による粒子の沈降速度の差に基づき、制御された気流を使用して粒径別に粒子を分離する。 |
振動ふるい | 振動スクリーンとメッシュを使用して、粉体微粒子を粒度別に選別する。 |
粉砕機 | 圧縮、圧縮、接着によって粉体の粗い凝集体を形成し、流動性とハンドリングを改善する。 |
ミキサー | タンブリング、攪拌、流動化により、複数の粉体の均質化と混合を実現。 |
ブリケットプレス | 高圧をかけて粉体を圧縮し、さまざまなサイズや形状の緻密なブリケットにする。 |
粉体製造の主要工程
主な粉体製造工程と、それらが使用される代表的な素材や産業について:
プロセス | 原材料/産業 |
---|---|
機械的粉砕 | 金属、合金、セラミックス、鉱物、顔料、農薬 |
降水量 | セラミックス、顔料、触媒材料、特殊化学品 |
電解 | 金属、合金、化合物 |
プラズマ合成 | セラミックス、サーメット、超合金 |
固体反応 | セラミックス、触媒、蛍光体、電池材料 |
スプレー乾燥 | 食品、医薬品、洗剤、顔料、セラミックス |
ゾル-ゲル合成 | セラミックス、触媒、コーティング、光学 |
極低温粉砕 | ポリマー、エラストマー、医薬品、食品 |
粉砕や摩砕のような機械的なサイズダウン法は、最も広く使われている粉末製造技術である。しかし、特定の化学組成や結晶構造を持つ材料は、電解、噴霧乾燥、沈殿、ゾル-ゲル合成などの高度な技術によって製造される。
粉体製造の応用と用途
特殊な製造工程を経て生産される粉末は、幅広い産業や製品に利用されている。主な用途には以下のようなものがある:
業界/製品 | 申し込み |
---|---|
冶金学と金属部品 | 粉末冶金による焼結部品、積層造形用合金粉末の製造 |
セラミックスと耐火物 | エレクトロニクス用アドバンストセラミックパウダー、遮熱コーティング |
ポリマーとプラスチック | 粉体塗料、粉体成形材料 |
塗料とコーティング | 顔料、エクステンダー、分散剤 |
医薬品と栄養補助食品 | 医薬品有効成分、賦形剤、栄養補助食品 |
飲食 | 香料、増粘剤、乳化剤、粉ミルク、ドリンクミックス |
化学薬品と触媒 | 特殊化学合成、触媒材料 |
農業 | 微量栄養素および放出肥料、粉末農薬 |
化粧品とパーソナルケア | 顔料、タルク、改質剤、有効成分 |
エネルギー貯蔵 | 電池正極・電解質、燃料電池材料 |
粉末材料の市場は、バルク材料と比較して、製造部門全体で高い性能と柔軟性を提供するため、急速に拡大している。
設計上の考慮事項と基準
粉体製造システムの設計には、容量、材料特性、爆発リスク、ハンドリング効率、安定した製品品質などのパラメータを慎重に考慮する必要がある。
安全で効果的な粉体処理装置を設計するための主な基準は以下の通りである:
- NFPA 654 - 火災および粉塵爆発の防止に関する規格
- ISO 12100 - 機械の安全性
- ASTM B215 - 試験用ふるいの規格
- ASTM B822 - 空気透過性を用いた粒子径の標準試験方法
- ISO 4497 - 流動化システムの安全要求事項
装置の設計には、粉砕媒体、インペラーの回転数、スクリーンの寸法、ノズルの大きさなどの機械的側面と、バッチ運転か連続運転か、温度、圧力、流量、複数の操作の統合などのプロセス要因が含まれる。
粉体の品質と処理能力を維持するためには、自動化された監視・制御システムが不可欠である。不活性ガスブランケット、爆発防止ベント、電気接地による爆発防止は非常に重要です。
粉体処理装置のサプライヤーを選ぶ
粉体ラインの性能と効率を最適化するために信頼できる粉体機器メーカーを選ぶには、さまざまなパラメーターを評価する必要がある:
パラメータ | 説明 |
---|---|
実績のある経験 | 粉体産業への供給年数と事業規模 |
ターンキー機能 | 原料から最終製品までの一貫システムを提供 |
カスタム・エンジニアリング | 特定の粉体特性と生産能力に合わせて装置をカスタマイズする能力 |
機器の範囲 | 粉砕機、空気分級機、混合・供給システム、封じ込めソリューション、自動化システムを提供します。 |
設置および試運転サービス | 現場でのインストール、テスト、最適化サポートに対応する能力 |
継続的なサポート | ダウンタイムを最小限に抑えるためのメンテナンス契約とスペアパーツの供給 |
基準の遵守 | 関連する安全および品質規格の認証を受けた製品 |
エネルギー効率 | 運転コストを最小限に抑える低エネルギー設計 |
プロセスの最適化 | 粉体システムの性能向上のためのモデリングとシミュレーションの活用 |
粉体処理装置の大規模な資本購入を決定する前に、様々なベンダーを評価し、リファレンスを得ることが重要である。
粉体製造装置コスト
粉体製造における設備コストは、以下のような要因によって大きく異なる:
- 粉砕機の種類 - ボールミル、空気分級機、ジェットミルなど
- 容量 - トン/時の処理能力
- 材質 - ステンレススチール、カーボンスチール、アルミニウム
- 自動化と計装のレベル
- その他のハンドリングアクセサリー - コンベヤー、ホッパー、バッグ、サイクロン
- カスタマイズの要件
- アフターサービス契約
一般的な粉体処理装置の価格帯の目安は以下の通りである:
設備 | 出力容量 | 価格帯 |
---|---|---|
ボールミル | 1 - 200 kg/時 | $10,000 – $500,000 |
ジェットミル | 毎時10~2000kg | $50,000 – $1,000,000 |
空気分級機 | 500 - 10000 kg/時 | $40,000 – $700,000 |
ミキサー | 5~500kg/バッチ | $5,000 – $250,000 |
流動層乾燥機 | 毎時10~5000kg | $30,000 – $1,000,000 |
大量生産および完全自動化プラント用の大型システムは、$1百万円以上となる。正確な価格については、資格のある粉体機器サプライヤーに相談することをお勧めします。
粉体製造装置の設置と操作
粉体処理装置が最適な効率で安全に機能するためには、適切な設置および操作手順が必要です。以下にガイドラインを示します:
- 入念な現場準備と、振動のない平坦な基礎への機器の固定
- 製造元の指示に従った機器モジュールの組み立て
- テスト走行前のアライメント、漏れ、クリアランスのチェック
- 設計性能を確認するための乾湿試験試運転
- 高温試運転前の防爆システムの検証
- 供給量とパラメーターを徐々に定格容量まで引き上げる
- すべてのプロセス変数(流量、圧力、負荷、電力、温度、振動)の連続モニタリング
- 物質の蓄積や詰まりがないか定期的に点検
- 粉塵を封じ込めるための負圧差の維持
- 定期的なメディア交換と予防メンテナンス
- 電気機器の修理は、有資格の電気技師のみが行う
- 標準作業手順に関する適切なオペレーター・トレーニング
- 取扱説明書、メンテナンス記録、安全手順の文書化
機器ベンダーと提携し、その専門知識を活用することで、設置を合理化し、機器の寿命を最大限に延ばすための運用を最適化することができます。
粉体処理装置のメンテナンス
定期的なメンテナンスは、粉体ハンドリングシステムの安定した機能と安全のために不可欠です。主な内容は以下の通りです:
検査
- 材料の蓄積、漏れ、腐食、詰まりをチェックする
- 安全機能(接地、換気、バルブ、非常停止)の点検
- 統合制御システムと計測器の検証
予防メンテナンス
- フィルター、スクリーン、シール、ガスケット、ベルトの適時交換
- 粉砕機の媒体交換 - ボール、ライナー
- 爆発ベント、アラーム、不活性化のテスト
- 計量ベッド、温度センサー、圧力センサーの校正
- ベアリング、ギア、モーターの潤滑
故障メンテナンス
- 振動分析、サーモグラフィなどによる問題診断
- 不良部品(インペラ、ドライブ、ベルト)の修理/交換
- 重要部品のスペアパーツ在庫の管理
衛生と清掃
- 水の浸入を防ぐため、洗浄前に機器を隔離する。
- 定期的な掃除機清掃と送風機による埃の堆積防止
- 粉体洗浄用の可燃性溶剤は避けること
ドキュメンテーション
- すべての点検、メンテナンス活動に関する設備記録の更新
- スケジュールを最適化するために、摩耗率、交換頻度を追跡
- 主な修理や故障を報告し、解決策を文書化する
OEMと密接に協力し、サービス契約を結ぶことで、問題のトラブルシューティングやダウンタイムを最小限に抑えることができる。
粉体製造における主な考慮事項
粉体製造プロセスを選択する際に考慮すべき重要な要素には、以下のようなものがある:
製品の品質
- 粒度分布は、流動性、成形性、分散性などの粉体特性に影響を与えます。
- 粉末の形態と内部構造が性能を左右する
- 凝集とコンタミネーションを最小限に抑えることが重要
- 一貫したかさ密度、含水率、純度
安全性
- エンジニアリングと封じ込めソリューションによるダストコントロール
- 火災・爆発防止対策
- 騒音レベルが高い場合、防音カバーが必要になることがある
- 必要に応じて本質安全防爆仕様の電気機器を使用する
材料特性
- 研磨性は装置の摩耗とメディアの選択に影響する
- 熱安定性と化学的安定性がプロセス・パラメーターに影響する
- 破砕性、圧縮性、静電帯電を考慮する。
定員
- 生産規模が設備サイズと自動化レベルを左右する
- バッチ運転と連続運転は柔軟性と生産高に影響する
エネルギー消費
- 過粉砕や必要以上の大型装置を最小限に抑える
- さまざまな粉砕技術のエネルギー効率を検討する
- 熱回収、可変周波数ドライブ、自動化によりエネルギー使用量を削減
資本コストと営業コスト
- 設備コスト、メンテナンス、消耗品、エネルギー使用量
- 労働力、監視/制御システム、ダウンタイムによる影響
- テストおよび検証要件
これらのパラメータを考慮した慎重なプロセス設計と機器選定が、粉体製造プラントを成功させる鍵である。
粉体製造の利点と限界
メリット
- 希望する粒径と粒度分布を持つ粉体を精密に設計する能力
- 管理されたプロセスにおける優れた再現性と製品の一貫性
- 部品は、バルク材料と比較して、より複雑な形状に加工することができる。
- 低い処理温度でエネルギーを節約
- 高い表面積が反応性と性能を高める
- 金属、セラミック、ポリマー、化学薬品、食品素材など、幅広い素材に対応。
制限事項
- 粉体の取り扱いは面倒で、こぼれやすい。
- 粉塵暴露、火災、爆発などの安全衛生上の危険性
- 搬送、混合、加工に必要な特殊機器
- 粉体は、凝集性、研磨性、反応性があり、緩和が必要な場合がある。
- 大規模で均一性を維持するのは難しいことである。
- 大量生産に不向きなバッチプロセス
適切なエンジニアリングと安全対策を行えば、多くの用途において、粉末をベースとする先端材料の利点は制限を上回る。
粉体製造 - FAQ
Q: 粉体製造に使用される最も一般的な粉砕機の種類は何ですか?
A: ボールミル、ハンマーミル、ジェットミルは、粉体製造において最も一般的に使用される粉砕機です。用途によって、供給原料、必要な最終粒子径、処理能力、コンタミネーションリスクなどの要因に基づいて、最適な粉砕機を選択する必要があります。
Q: 粉末の取り扱いにおける粉塵爆発を防ぐために、どのような予防措置がとられていますか?
A: 一次的な爆発防止方法には、着火源の回避、静電気の蓄積の抑制、爆発範囲の空気-粉体混合物の回避、窒素/二酸化炭素による不活性化、爆発ベント、本質安全防爆の電気機器などがある。適切な粉塵管理と封じ込めも重要である。
Q:作業員が微粉末にさらされるリスクはどのように軽減されますか?
A: 戦略には、完全密閉型搬送システム、局所排気装置、集塵機、オペレーターエリアの隔離、グローブボックス/バッグイン/バッグアウトの封じ込め、人工呼吸器などのPPE、曝露時間の手順管理、危険認識トレーニングなどが含まれる。
Q: 粉体製造時に行われる重要な品質管理試験とは何ですか?
A: 重要な粉末特性試験には、粒度分析、モルフォロジー、流動性、嵩/真密度分析、水分分析、圧縮性、分散性、ブレンド均一性、化学組成、安定性などがあります。これらのパラメータは加工性と製品性能を決定します。
Q:粉体処理装置を選択する際の専門的なヒントを教えてください。
A: 資格のあるサプライヤーを早期に獲得すること、信頼できる情報源からリファレンスを得ること、デモとサンプルを要求すること、テストを通じて主張を検証すること、複数のベンダーから見積もりを取ること、OEMの能力と経験を評価すること、安全性とサポートサービスを優先すること、将来の拡張ニーズを計画すること、ライフサイクル全体のコストを考慮すること。
シェアする
MET3DP Technology Co., LTDは、中国青島に本社を置く積層造形ソリューションのリーディングプロバイダーです。弊社は3Dプリンティング装置と工業用途の高性能金属粉末を専門としています。
関連記事
Met3DPについて
最新情報
製品
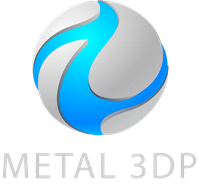
3Dプリンティングと積層造形用金属粉末