金属積層造形用の SLM
目次
選択的レーザー溶融の概要
選択的レーザー溶融(SLM)は、レーザーを使用して金属粉末粒子を層ごとに選択的に溶融・融合させ、完全に高密度なパーツを造形する粉末床溶融金属3Dプリンティングプロセスである。
SLM テクノロジーの主な特性:
特徴 | 説明 |
---|---|
材料 | ステンレス鋼、チタン、アルミニウム、ニッケル合金などの金属 |
レーザー式 | ファイバー、CO2、またはダイレクト・ダイオード・レーザー |
雰囲気 | 不活性アルゴンまたは窒素雰囲気 |
決議 | 150μmまでの微細形状が可能 |
精度 | 寸法±0.2%以内の部品 |
SLMは、航空宇宙、医療、自動車、産業用途向けの複雑でカスタマイズ可能な金属部品を可能にする。
選択的レーザー溶融の仕組み
SLM印刷プロセスは次のように機能する:
- 3Dモデルを2D断面レイヤーにスライス
- パウダーをビルドプレートに薄く塗る
- レーザーが層を選択的にスキャンし、粉末を溶かす
- 溶けた粉が固まり、融合する
- ビルドプレートが下がり、新しいレイヤーが上に広がる
- フルパートが出来上がるまで、この工程を繰り返す
未溶融パウダーは、コンポーネントを作り上げる際にサポートを提供する。これにより、専用の支持構造なしで複雑な形状が可能になります。
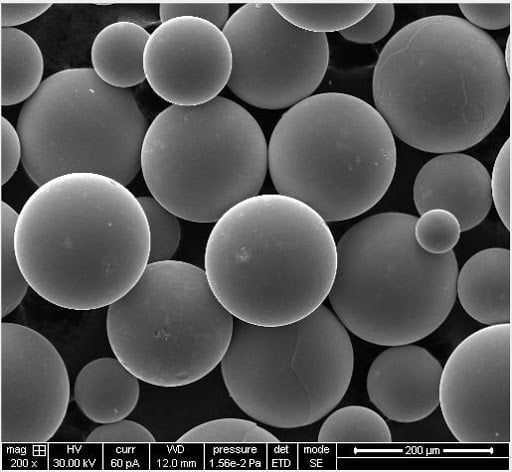
選択的レーザー溶融システムの種類
いくつかある。 SLM システム構成:
システム | 詳細 |
---|---|
シングルレーザー | 溶融用高出力レーザー1台 |
マルチレーザー | 複数のレーザーでビルド速度を向上 |
スキャンシステム | ガルボミラーまたは固定光学系 |
金属粉の取り扱い | オープンシステムまたはクローズドパウダーリサイクル |
大気制御 | アルゴンまたは窒素で満たされた密閉ビルド・チャンバー |
マルチレーザーシステムは造形時間を短縮し、クローズドループパウダーハンドリングは効率性とリサイクル性を向上させる。
選択的レーザー溶融用材料
SLMに使用される一般的な金属材料には次のようなものがある:
素材 | メリット |
---|---|
アルミニウム合金 | 軽量で強度が高い |
チタン合金 | 高い強度対重量比 |
ステンレス鋼 | 耐食性、高靭性 |
工具鋼 | 高い硬度と耐摩耗性 |
ニッケル合金 | 高温耐性 |
コバルトクロム | 生体適合性に優れ、摩耗性が良い |
さまざまな合金粉末は、用途に応じて必要とされる強度、硬度、耐熱性、生体適合性などの特性を可能にする。
選択的レーザー溶融の応用
SLM金属印刷の代表的な用途には、以下のようなものがある:
産業 | アプリケーション |
---|---|
航空宇宙 | エンジン部品、軽量構造 |
メディカル | カスタムインプラント、補綴物、器具 |
自動車 | 軽量部品、カスタム金型 |
インダストリアル | 軽量化部品、最終用途生産 |
石油・ガス | 耐食バルブ、坑口部品 |
SLMは、複雑なカスタム金属部品を一体化し、重量と性能を最適化することができる。
選択的レーザー溶融の利点
SLM技術の主な利点:
ベネフィット | 説明 |
---|---|
複雑な形状 | 有機的な形状のための無制限の設計自由度 |
パート統合 | 単一部品として印刷されたアセンブリ |
カスタマイズ | カスタム部品の生産に容易に対応 |
軽量化 | 格子構造とトポロジーの最適化 |
材料の節約 | 減算法に比べて廃棄物を削減 |
後処理 | サポート除去と表面仕上げが必要な場合がある |
これらの利点により、より高性能な最終用途の金属部品を、競争力のあるリードタイムとコストで、より少ない生産量で製造することが可能になる。
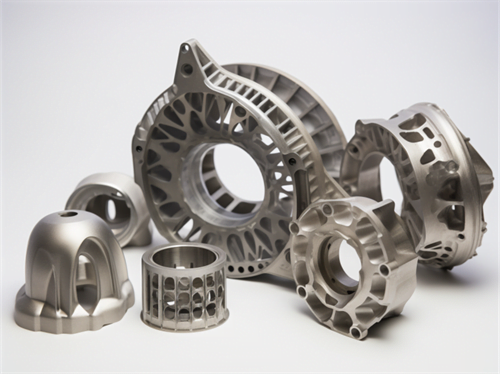
選択的レーザー溶融の限界
SLMの限界には次のようなものがある:
制限 | 説明 |
---|---|
パーツサイズ | 通常1m3以下のプリンター造形量に制限される |
生産性 | 生産速度が比較的遅いため、大量生産には限界がある |
後処理 | サポート除去、機械加工、仕上げが必要な場合がある |
異方性 | 機械的特性は製造方向によって異なる |
表面仕上げ | 印刷面は比較的粗い |
オペレーターの専門知識 | プリンターに関する豊富な経験が必要 |
この技術は、複雑な金属部品の少量から中量の生産に最適である。
SLMプリンターサプライヤー
大手SLMシステムメーカー
会社概要 | 注目のシステム |
---|---|
イーオーエス | EOS Mシリーズ |
3Dシステムズ | DMPシリーズ |
GEアディティブ | Xライン2000R |
トルンフ | TruPrint 1000、3000 |
SLMソリューション | SLM500、SLM800 |
レニショー | AM500、AM400 |
250mm×250mm×300mm程度の小型のものから、生産性の高い800mm×400mm×500mmの大型のものまで、さまざまなマシンが用意されている。
SLM 3Dプリンタの選択
SLMシステムを選択する際の主な考慮事項:
ファクター | 優先順位 |
---|---|
ビルドボリューム | 必要な部品サイズに合わせる |
対応素材 | Ti、Al、ステンレス、工具鋼のような必要な合金 |
不活性ガスシステム | 密閉された自動アルゴンまたは窒素ハンドリング |
レーザー技術 | ファイバー、CO2、またはダイレクト・ダイオード・レーザー |
スキャン方法 | ガルボまたは固定ミラースキャン |
パウダーハンドリング | クローズド・ループ・リサイクルが望ましい |
最適なSLMシステムは、用途に必要な材料、造形量、速度、粉体ハンドリング機能を提供する。
SLM施設要件
SLMプリンターを稼動させるためには、施設は以下を満たさなければならない:
- 電力レベル 20~60 kW(代表値
- 20~25℃前後の安定した温度
- 70% RH以下の低湿度
- 微粒子制御と金属粉の取り扱い
- 不活性ガスの供給と排気
- 排出される微粒子に対する排気フィルター
- 大気監視システム
- 強力な人的安全手順
SLMシステムは、電力、冷却、粉体処理、不活性ガス供給など、かなりのインフラを必要とする。
SLM印刷プロセス・パラメーター
典型的なSLM印刷パラメータ:
パラメータ | 典型的な範囲 |
---|---|
レーザー出力 | 100-400 W |
スキャン速度 | 100-2000 mm/s |
層厚 | 20-100 μm |
ハッチの間隔 | 50-200 μm |
スポットサイズ | 50~100μm |
スキャンパターン | レイヤーごとに交互に回転 |
各合金粉末の完全な高密度部品を達成するためには、これらのパラメーターを正確に調整する必要がある。
SLM 設計ガイドラインと制限
主なSLM設計ガイドラインは以下の通り:
ガイドライン | 理由 |
---|---|
最小肉厚 | 熱の蓄積と反りを避ける |
オーバーハング | 支えがなくても倒壊を防ぐ |
薄いフィーチャーは避ける | 溶融や気化を防ぐ |
強さのためのオリエント | 荷重方向に最適化する |
サポート利用の最小化 | 後処理の簡素化 |
SLMプロセスでは、オーバーハング角や最小フィーチャサイズなど、幾何学的な要件を考慮する必要があります。
SLM後処理の要件
SLM部品の一般的な後処理工程:
プロセス | 目的 |
---|---|
サポート解除 | ソフトウェアから自動生成サポートを削除する |
粉の除去 | 内部通路に残ったパウダーを取り除く |
表面仕上げ | 機械加工による仕上げ面と粗さの改善 |
ストレス解消 | 熱処理による残留応力の低減 |
熱間静水圧プレス | 密度を高め、内部空隙を減らす |
後加工のレベルは、公差、表面仕上げ、材料特性などの用途要件によって異なる。
SLM部品の認定試験
SLMコンポーネントの代表的な認定試験:
テスト・タイプ | 説明 |
---|---|
密度分析 | 鍛造素材と比較して密度を測定 |
機械試験 | 引張、疲労、破壊靭性試験 |
メタログラフィー | 微細構造イメージングと欠陥解析 |
化学分析 | 組成が仕様に適合していることを確認する |
非破壊 | CTスキャンまたはX線による空洞検査 |
徹底的なテストにより、SLM部品が生産用途に投入される前に要件を満たしていることが確認される。
のメリット SLM テクノロジー
選択的レーザー溶融には重要な利点がある:
- 鋳造やCNCでは不可能な複雑で有機的な形状
- トポロジー最適化による軽量構造
- 単一プリント部品への部品統合
- 減算法に比べて廃棄物を削減
- カスタマイズと迅速なデザインの反復
- 金属部品のジャスト・イン・タイム生産
- 鍛造素材に迫る高い強度と硬度
このような利点から、SLMはあらゆる産業において、高価値で少量の部品をオンデマンドで生産するのに適している。
SLM印刷導入の課題
SLM導入の障壁には以下のようなものがある:
チャレンジ | 緩和戦略 |
---|---|
高いプリンターコスト | サービスビューローの活用、ROIの検証 |
素材オプション | 開発中の新合金、特殊サプライヤー |
プロセス知識 | トレーニングプログラム、学習曲線 |
規格 | 開発中の部品認定プロトコル |
後処理 | 開発中の自動化プロセス |
技術が成熟するにつれて、こうした障壁は、材料、設備、トレーニングの改善、業界全体の標準化努力によって軽減されつつある。
選択的レーザー溶融の未来
SLM技術の新たなトレンド:
- 500 x 500 x 500 mmを超える大きな造形量
- マルチレーザーシステムによる造形速度の高速化
- 高温超合金を含む発泡合金
- 粉体のリサイクル性とハンドリングの向上
- サポートの自動削除と後処理
- AMとCNCを組み合わせたハイブリッド製造
- 設計最適化のための専用ソフトウェア
- プロセスパラメータと部品認定の標準化
SLMシステムは、造形サイズ、速度、材料、信頼性の面で進歩し続け、より多くの産業用途で生産ニーズに応えられるようになるだろう。
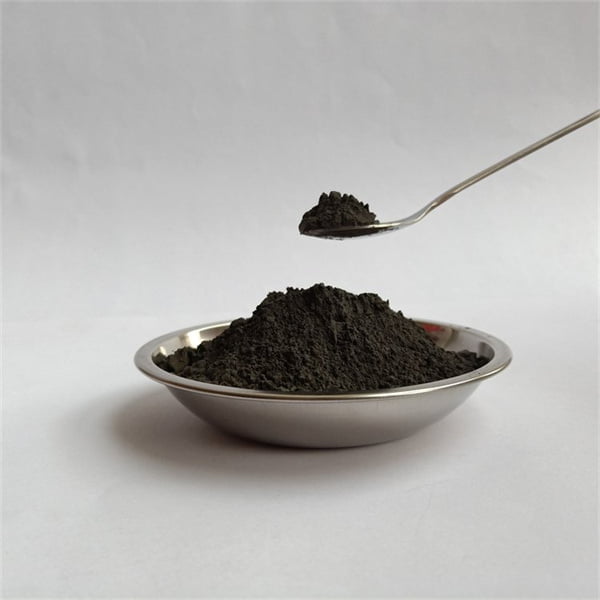
要点まとめ
- SLMは金属粉末をレーザーで選択的に融合し、フル密度の3Dプリントを実現する
- 微細で複雑な形状が可能な粉末床溶融プロセス
- 航空宇宙、医療、自動車、工業用途に最適
- ステンレス、チタン、アルミニウム、ニッケル合金などの金属を使用
- 部品の統合、カスタマイズ、軽量化のメリットを提供
- 制御された雰囲気と堅牢なパウダーハンドリングシステムが必要
- 印刷された部品には、かなりの後処理が必要な場合がある。
- 少量生産から中量生産のアプリケーションをリードする技術
- 素材、製造サイズ、スピード、品質の継続的改善
- 高性能プリント金属部品の実現
選択的レーザー溶融は、カスタマイズされた金属部品をオンデマンドで製造する産業用製造ソリューションとして成長を続けるだろう。
よくあるご質問
質問 | 答え |
---|---|
SLMに適合する材料は? | ステンレス鋼、チタン、アルミニウム、工具鋼、ニッケル合金、コバルトクロムなど、溶接可能な合金のほとんど。 |
SLM部品の一般的な精度は? | ほとんどの形状で±0.2%程度の寸法精度が達成可能です。 |
どのような後処理が必要ですか? | サポート除去、粉体除去、表面仕上げ、応力除去、熱間静水圧プレスが一般的。 |
一般的なSLMの欠陥とは? | ポロシティ、クラック、層間剥離、反り、表面仕上げ不良、未溶融粒子。 |
SLMで使用されるレーザーの種類は? | ファイバーレーザー、CO2レーザー、高出力ダイオードが一般的に使用される。 |
シェアする
MET3DP Technology Co., LTDは、中国青島に本社を置く積層造形ソリューションのリーディングプロバイダーです。弊社は3Dプリンティング装置と工業用途の高性能金属粉末を専門としています。
関連記事
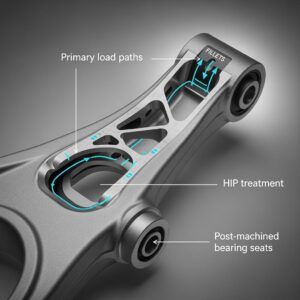