Spring Retainers for Aerospace Mechanisms via AM
目次
Introduction: The Critical Role of Spring Retainers in Aerospace and the AM Advantage
In the demanding realm of aerospace engineering, every component, no matter how seemingly small, plays a critical role in ensuring safety, reliability, and performance. Spring retainers are exemplary of such components. Tasked with securing and correctly positioning springs within complex mechanical assemblies like engine valve trains, landing gear retraction systems, and flight control actuators, these parts operate under extreme conditions, including high cyclical loads, significant temperature variations, and intense vibrations. Failure is simply not an option. Traditionally manufactured through methods like machining from bar stock or forging, the production of aerospace-grade spring retainers demands precision, high-strength materials, and rigorous quality control. However, the constant drive for enhanced performance, reduced weight, and optimized designs is pushing the aerospace industry towards innovative manufacturing solutions.
Enter Metal Additive Manufacturing (AM), often referred to as metal 3Dプリンティング. This transformative technology is rapidly changing how high-performance components, including spring retainers, are designed and produced. Unlike subtractive methods that remove material, AM builds parts layer-by-layer directly from digital models using high-performance metal powders. This approach unlocks unprecedented design freedom, enabling the creation of complex geometries, internal features, and topology-optimized structures that are impossible or prohibitively expensive to achieve through conventional means. For aerospace spring retainers, this translates to opportunities for significant weight reduction without compromising strength, improved fatigue life through optimized stress distribution, and potential consolidation of multi-part assemblies into single, more reliable components. Furthermore, AM facilitates rapid prototyping and on-demand production, offering agility in development cycles and resilience in the supply chain – critical factors for aerospace manufacturers and B2B suppliers seeking reliable component sourcing. As a leader in 金属積層造形ソリューション, Met3dp leverages cutting-edge powder bed fusion technologies and advanced material science to produce aerospace components that meet the industry’s stringent requirements.
The adoption of AM for critical parts like spring retainers signifies a shift towards smarter, more efficient, and higher-performing aerospace systems. It addresses key industry challenges: the relentless pursuit of lighter aircraft for fuel efficiency and payload capacity, the need for components capable of withstanding increasingly harsh operating environments, and the demand for shorter development timelines and more flexible manufacturing processes. Procurement managers and engineers involved in sourcing or designing aerospace components must understand the capabilities and advantages AM offers for parts like spring retainers to maintain a competitive edge and contribute to the next generation of aviation and space exploration technology. This article delves into the specifics of using metal AM for aerospace spring retainers, covering applications, material selection, design principles, quality considerations, and how to partner with the right AM service provider.
What Are Aerospace Spring Retainers Used For? Key Applications and Functions
Aerospace spring retainers are fundamental components found in a multitude of critical systems across aircraft, spacecraft, and related ground support equipment. Their primary function is to provide a secure seat or interface for a compression spring, ensuring it remains correctly aligned and transmits force effectively within a mechanism. The specific design and material of a retainer are dictated by its precise application and the operational demands it must endure. Sourcing these precision components often involves navigating a complex B2B aerospace supply chain, where reliability and adherence to specifications are paramount.
Here’s a breakdown of key application areas and the functions spring retainers perform:
1. Aircraft Engine Valve Trains:
- Function: In piston and even some turbine engine components, spring retainers are crucial parts of the valve train. They work in conjunction with valve springs and keepers (or collets) to ensure intake and exhaust valves open and close at precisely the right moments during the engine cycle.
- Demands: This application involves extremely high cyclical loads (millions of cycles over the engine’s life), high temperatures, and the need for low mass to prevent valve float at high RPMs. Material fatigue resistance and strength-to-weight ratio are critical. AM allows for optimized designs that minimize mass while maintaining structural integrity.
2. Landing Gear Systems:
- Function: Spring retainers are used within shock struts (oleo struts) and retraction/extension mechanisms. They help manage the large compression springs that absorb landing impacts and facilitate the smooth operation of the gear deployment and stowage sequences.
- Demands: Landing gear systems experience massive impact loads, significant static loads, and exposure to environmental factors (moisture, de-icing fluids, runway debris). Retainers here must possess exceptional strength, toughness, and corrosion resistance. The ability of AM to produce complex internal features can be advantageous for integrating retainers into intricate strut designs.
3. Flight Control Actuation Systems:
- Function: Hydraulic, pneumatic, or electromechanical actuators that move control surfaces (ailerons, elevators, rudders) often incorporate springs for centering, return-to-neutral functions, or preload application. Spring retainers ensure these springs are properly located and function reliably under varying aerodynamic loads.
- Demands: These systems require high reliability and precision. Retainers must withstand constant, albeit often lower-magnitude, cyclical loading and maintain dimensional stability across a wide temperature range. Design optimization through AM can help reduce the overall weight of the actuation system, contributing to aircraft efficiency.
4. Fuel System Components:
- Function: Pressure relief valves, regulators, and check valves within fuel systems utilize springs to control flow and pressure. Spring retainers are essential for the correct assembly and function of these valves.
- Demands: Compatibility with aviation fuels, resistance to vibration, and consistent performance over time are key requirements. Depending on the specific valve, high strength or specific corrosion resistance might be needed.
5. Escape Systems and Cargo Bay Mechanisms:
- Function: Ejection seat mechanisms, canopy jettison systems, and cargo door latches often rely on powerful springs for rapid actuation. Retainers ensure these springs deliver their stored energy effectively when commanded.
- Demands: High impact strength, reliability after long periods of dormancy, and often stringent space and weight constraints are typical. AM’s design flexibility can be crucial for fitting retainers into tightly packaged systems.
6. Rotorcraft Systems:
- Function: Helicopter rotor heads and flight control systems utilize numerous springs for damping, control feedback, and mechanism biasing. Spring retainers are integral to these assemblies.
- Demands: Very high fatigue life requirements due to the constant vibration and dynamic loads in rotorcraft. Lightweighting is also a major driver.
Summary Table: Aerospace Spring Retainer Applications
アプリケーションエリア | Key Function | Critical Demands | Potential AM Benefit |
---|---|---|---|
Engine Valve Train | Secure valve springs, ensure proper valve timing | High cycles, high temp, fatigue resistance, low mass | Lightweighting, performance |
ランディングギア | Seat springs in shock struts & retraction mechanisms | High impact loads, static strength, corrosion resistance, toughness | Complex integration |
Flight Control Actuator | Position springs for centering, preload, return | High reliability, precision, fatigue life, wide temp range | 軽量化 |
Fuel System Valves | Ensure correct spring function in valves/regulators | Fuel compatibility, vibration resistance, consistent performance | Customized design |
Escape/Cargo Systems | Enable spring function in latches, jettison systems | High impact strength, reliability, space/weight constraints | 設計の柔軟性 |
Rotorcraft Systems | Support springs in rotor heads, flight controls | Very high fatigue life, vibration resistance, lightweighting | Performance optimization |
Export to Sheets
Understanding these diverse and demanding applications highlights why aerospace spring retainers are not commodity items but highly engineered components. For procurement managers and wholesale buyers, partnering with a capable aerospace parts supplier familiar with these requirements and advanced manufacturing methods like AM is crucial for ensuring system integrity and performance.
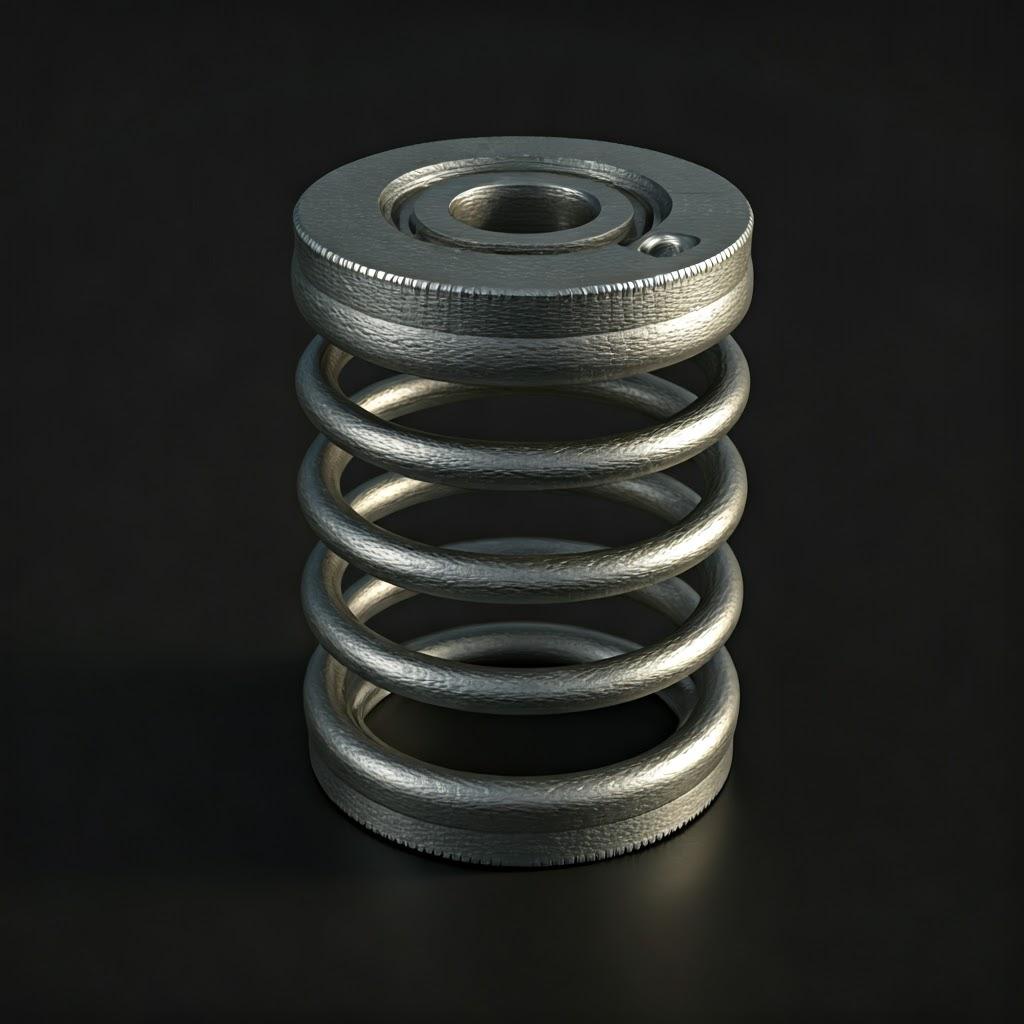
Why Use Metal 3D Printing for Aerospace Spring Retainers? Unlocking Performance and Efficiency
While traditional manufacturing methods like CNC machining and forging have long served the aerospace industry well, metal additive manufacturing (AM) presents compelling advantages, particularly for components like spring retainers operating under demanding conditions. The decision to adopt AM is driven by the potential to significantly enhance performance, improve design efficiency, optimize the supply chain, and ultimately create superior aerospace systems. For businesses involved in the B2B supply of aerospace components, understanding and leveraging these benefits is becoming increasingly vital.
Here’s a breakdown of the key reasons why metal AM is an attractive option for producing aerospace spring retainers:
1. Unprecedented Design Freedom & Complexity:
- Challenge with Traditional Methods: Machining complex internal features, undercuts, or organically optimized shapes in retainers can be difficult, time-consuming, or impossible. Forging requires expensive tooling and is limited in geometric complexity.
- AM Advantage: AM builds parts layer by layer, allowing for highly intricate geometries. This enables:
- Topology Optimization: Algorithms can redesign the retainer to place material only where structurally needed, drastically reducing weight while maintaining or increasing strength and stiffness. This is paramount in aerospace for fuel savings and increased payload.
- Internal Features: Cooling channels, integrated sensors pathways, or complex seating surfaces can be designed directly into the retainer.
- パーツの統合: Multi-component retainer assemblies (e.g., a retainer with integrated keepers or locators) can potentially be redesigned and printed as a single, monolithic part, reducing part count, assembly time, and potential failure points.
2. Lightweighting Opportunities:
- Aerospace Imperative: Reducing weight is a constant goal in aerospace design. Lighter components lead to lower fuel consumption, increased range or payload, and improved maneuverability.
- AM Advantage: As mentioned, topology optimization is a primary driver. Additionally, AM allows for the use of lattice structures or complex internal voids within the retainer’s less stressed areas, further cutting mass without sacrificing critical performance characteristics like spring seating or load transfer. Even small weight savings per retainer can add up significantly across an entire aircraft or engine.
3. Material Performance Optimization:
- チャレンジ: Machining certain high-performance alloys (like titanium alloys or specific superalloys) can be difficult and generate significant waste (buy-to-fly ratio). Casting may not achieve the required microstructural properties or dimensional accuracy.
- AM Advantage: AM processes, particularly Powder Bed Fusion (PBF) methods like Selective Laser Melting (SLM) and Electron Beam Melting (EBM), work effectively with challenging aerospace-grade materials like Ti-6Al-4V and precipitation-hardening steels like 17-4PH.
- Near-Net Shape: AM produces parts very close to their final dimensions, significantly reducing material waste compared to machining from billet.
- Controlled Microstructure: AM process parameters can be tuned to influence the resulting microstructure, potentially enhancing properties like fatigue strength relevant for retainers. Met3dp’s expertise in powder metallurgy and process control ensures optimal material properties.
4. Rapid Prototyping and Accelerated Development:
- チャレンジ: Creating prototypes using traditional methods involves tooling lead times (forging) or extensive machining setup and time. Design iterations can be slow and costly.
- AM Advantage: AM allows engineers to go directly from a CAD model to a physical metal prototype, often within days. This dramatically speeds up design validation, functional testing, and iteration cycles for new or improved retainer designs. Multiple design variations can be printed simultaneously in a single build for comparative testing.
5. Supply Chain Optimization and On-Demand Production:
- チャレンジ: Traditional aerospace supply chains can involve long lead times, high inventory costs for spares, and vulnerability to disruptions. Minimum order quantities for forged or cast parts can be large.
- AM Advantage:
- リードタイムの短縮: For low-to-medium volume production or spare parts, AM can often deliver components faster than traditional methods reliant on tooling or extensive setup.
- オンデマンド製造: Digital inventory allows parts like retainers to be printed as needed, reducing physical warehousing requirements and the risk of part obsolescence. This is highly valuable for MRO (Maintenance, Repair, Overhaul) operations and for suppliers managing diverse aerospace part portfolios.
- Distributed Manufacturing: Parts can potentially be printed closer to the point of need, further streamlining logistics.
6. Suitability for Customization and Low Volumes:
- チャレンジ: Producing small batches or customized variations of retainers via traditional methods is often cost-prohibitive due to setup and tooling costs.
- AM Advantage: AM is economically viable for low production volumes and even one-off custom parts, as it does not require part-specific tooling. This benefits specialized aerospace applications or rapid development programs.
Comparison Table: AM vs. Traditional Manufacturing for Spring Retainers
特徴 | 金属積層造形(AM) | Traditional Machining (CNC) | 伝統的な鍛造 |
---|---|---|---|
デザインの複雑さ | Very High (Internal features, topology opt.) | Moderate to High (Limited by tool access) | Low to Moderate (Requires draft angles) |
軽量化 | Excellent potential via optimization/lattices | Limited (Material removal constraints) | Limited (Geometry constraints) |
廃棄物 | Low (Near-net shape) | High (Especially for complex parts) | Moderate (Flash removal) |
Lead Time (Proto) | Short (Days) | Moderate (Days/Weeks) | Long (Weeks/Months – tooling) |
Lead Time (Prod) | Moderate (Scalable) | Moderate to Long | Moderate (Post-tooling) |
金型費用 | なし | Low (Fixturing) | Very High (Dies) |
Cost (Low Volume) | 競争的 | High (Setup intensive) | Very High (Tooling amortization) |
Cost (High Volume) | Can be higher per part | 競争的 | Most Competitive |
部品の統合 | High potential | Low potential | Low potential |
素材オプション | Growing range, good for Ti, Ni alloys, Steels | Very Wide | Wide range of forgeable alloys |
Export to Sheets
In summary, while traditional methods remain crucial, metal AM offers a powerful alternative for producing aerospace spring retainers with enhanced performance, reduced weight, and greater design and supply chain flexibility. For aerospace engineers and procurement managers seeking competitive advantages and reliable aerospace parts suppliers, exploring the potential of AM is essential.
Recommended Materials for AM Spring Retainers: 17-4PH and Ti-6Al-4V Deep Dive
Selecting the right material is paramount for aerospace spring retainers, given their critical function and the harsh operating conditions they face. Additive manufacturing processes work with specialized metal powders, and two materials stand out as excellent candidates for 3D printing high-performance retainers: 17-4PHステンレス鋼 そして Ti-6Al-4Vチタン合金. Both offer a compelling blend of strength, fatigue resistance, and environmental resilience, making them suitable for various aerospace applications. Choosing between them depends on the specific requirements of the application, such as maximum operating temperature, weight sensitivity, and corrosion environment.
Met3dp, leveraging its advanced powder manufacturing capabilities including gas atomization and Plasma Rotating Electrode Process (PREP) technologies, produces high-sphericity, excellent-flowability 金属粉 optimized for demanding AM applications, including these critical aerospace alloys. Our rigorous quality control ensures material consistency vital for repeatable, high-quality component production.
1. 17-4PH Stainless Steel (UNS S17400 / AISI 630)
- 概要 17-4PH is a chromium-nickel-copper precipitation-hardening martensitic stainless steel. It’s widely used in aerospace due to its excellent combination of high strength, good corrosion resistance, good toughness, and its ability to be hardened to various strength levels through simple heat treatment.
- Why it Matters for Spring Retainers:
- High Strength & Hardness: After appropriate heat treatment (e.g., Condition H900, H1025), 17-4PH achieves high tensile and yield strength, enabling retainers to withstand significant spring forces and dynamic loads without yielding or failure.
- Good Fatigue Resistance: Crucial for applications like engine valve trains involving millions of load cycles.
- 良好な耐食性: Generally superior to standard martensitic stainless steels and adequate for many aerospace environments, though not as resistant as austenitic grades or titanium in highly corrosive conditions.
- Moderate Temperature Capability: Suitable for applications typically up to around 315∘C (600∘F), although strength decreases at elevated temperatures.
- Weldability & Machinability (Post-AM): Can be machined after printing if very tight tolerances or specific surface finishes are required beyond what AM and standard post-processing achieve.
- 費用対効果: Generally more cost-effective than titanium alloys.
- AM Considerations: 17-4PH is readily processable using Laser Powder Bed Fusion (L-PBF / SLM). Post-print heat treatment is essential to achieve the desired final properties (solution annealing followed by aging). Careful parameter control during printing is needed to minimize residual stress and ensure dense parts. Hot Isostatic Pressing (HIP) may be employed for critical applications to eliminate any potential internal porosity and further enhance fatigue properties.
2. Ti-6Al-4V (Grade 5 Titanium / UNS R56400)
- 概要 Ti-6Al-4V (often called Ti64) is the workhorse alpha-beta titanium alloy, accounting for a large percentage of all titanium usage. It’s renowned in aerospace for its high strength-to-weight ratio, excellent corrosion resistance, and good performance at moderately elevated temperatures.
- Why it Matters for Spring Retainers:
- 卓越した強度対重量比: Significantly lighter than steel (around 40-45% less dense) while offering comparable or even superior strength, depending on heat treatment. This is a major advantage for lightweighting initiatives in engines, landing gear, and airframes.
- Excellent Fatigue Strength: Titanium alloys generally exhibit excellent fatigue performance, critical for long-life dynamic components.
- 優れた耐食性: Highly resistant to corrosion from jet fuel, hydraulic fluids, atmospheric conditions, and saltwater environments.
- Good Elevated Temperature Performance: Retains useful strength up to approximately 315−400∘C (600−750∘F), offering a higher operating ceiling than 17-4PH in some conditions.
- 生体適合性: While less relevant for typical retainers, it’s a key feature of Ti64 for medical applications.
- AM Considerations: Ti-6Al-4V is well-suited for both L-PBF and Electron Beam Melting (EBM) processes. EBM, like the Selective Electron Beam Melting (SEBM) systems offered by Met3dp, often produces parts with lower residual stress due to the higher processing temperatures but may have a rougher initial surface finish. L-PBF can achieve finer features and better surface finish as-built. Post-processing typically involves stress relief annealing, and HIP is commonly used for critical aerospace parts to ensure maximum density and fatigue performance. Machining may be required for critical tolerance features. Careful atmosphere control (inert gas or vacuum) is essential during printing due to titanium’s reactivity.
Material Properties Comparison (Typical Values – Heat Treated Conditions)
プロパティ | 単位 | 17-4PH (e.g., H900) | Ti-6Al-4V (Annealed) | 備考 |
---|---|---|---|---|
密度 | g/cm3 (lb/in3) | ~7.8 (0.282) | ~4.43 (0.160) | Ti64 is significantly lighter. |
極限引張強さ | MPa (ksi) | ~1310 (190) | ~950 (138) | 17-4PH can achieve higher peak strength. |
降伏強度 (0.2%) | MPa (ksi) | ~1170 (170) | ~880 (128) | 17-4PH (H900) has higher yield strength. |
弾性係数 | GPa (Msi) | ~197 (28.5) | ~114 (16.5) | 17-4PH is stiffer. |
破断伸度 | % | ~10% | ~14% | Ti64 generally shows higher ductility. |
硬度 | HRC | ~40-45 | ~36 | 17-4PH (H900) is harder. |
最高使用温度 | ∘C (∘F) | ~315 (600) | ~350-400 (660-750) | Application dependent; Ti64 has edge. |
耐食性 | 一般 | グッド | 素晴らしい | Ti64 superior, especially in chlorides. |
相対コスト | Index | より低い | より高い | Titanium alloys are more expensive. |
Export to Sheets
Note: Properties achievable via AM depend significantly on the specific printing process (L-PBF/EBM), parameters used, build orientation, and post-processing steps (heat treatment, HIP). The values above are indicative.
Choosing the Right Material:
- Choose 17-4PH if:
- The absolute highest strength and hardness are primary requirements.
- Weight is less critical than cost.
- Operating temperatures remain below approx. 315∘C.
- Good, but not exceptional, corrosion resistance is sufficient.
- Choose Ti-6Al-4V if:
- Weight reduction is a critical design driver (high strength-to-weight ratio needed).
- Excellent fatigue life is paramount.
- Superior corrosion resistance is required.
- Operating temperatures may exceed those suitable for 17-4PH.
- Higher material cost is acceptable for performance gains.
Partnering with an experienced AM provider like Met3dp, which not only supplies high-quality powders but also possesses deep knowledge of material processing and aerospace requirements, is crucial. We can assist engineers and procurement teams in selecting the optimal material and defining the necessary manufacturing and post-processing steps to produce reliable, high-performance aerospace spring retainers tailored to their specific application needs. Our comprehensive solutions span printers, 先進的な金属粉末, and application development support.
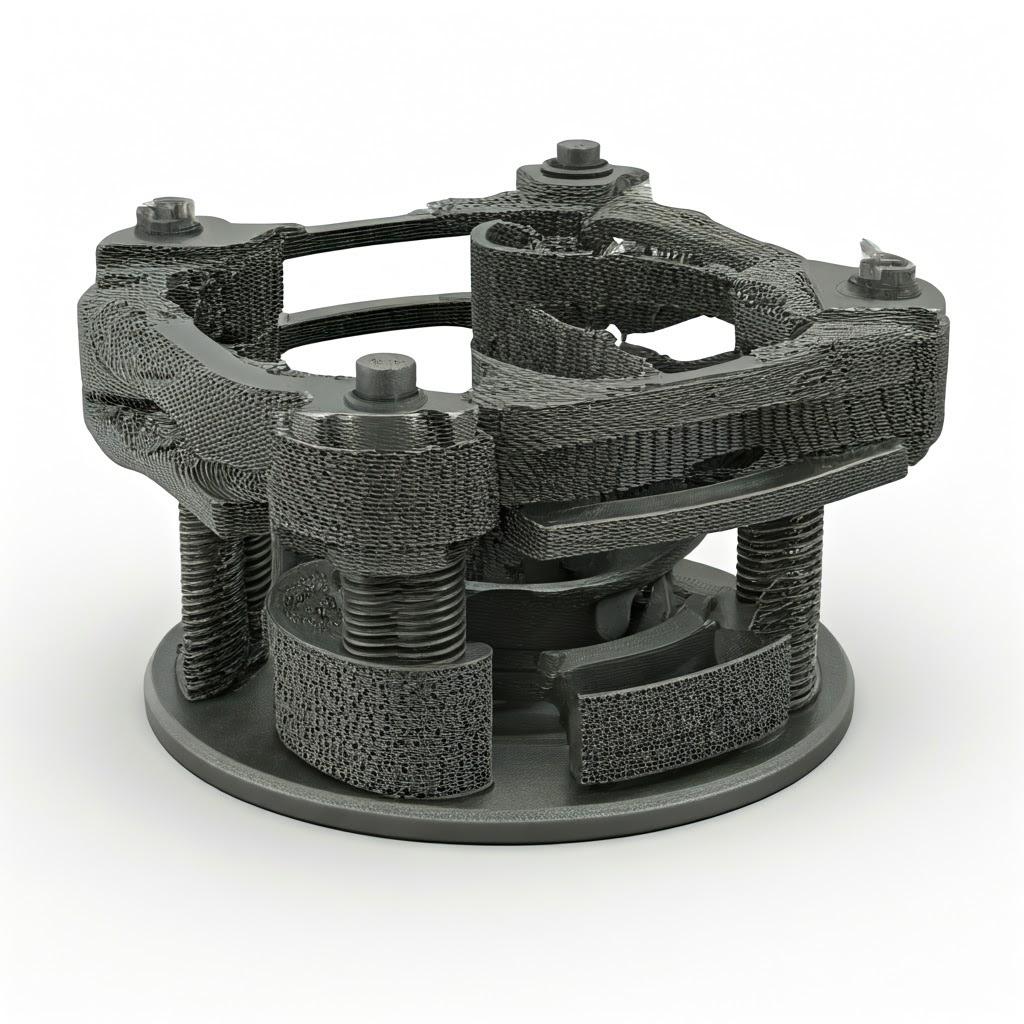
Design Considerations for Additively Manufactured Spring Retainers: Optimizing for Performance
Transitioning the design of an aerospace spring retainer from traditional manufacturing methods to additive manufacturing isn’t just about converting a file format; it requires embracing a different design philosophy known as Design for Additive Manufacturing (DfAM). Applying DfAM principles from the outset is crucial for maximizing the benefits of AM – lightweighting, performance enhancement, and cost-effectiveness – while minimizing potential manufacturing challenges. Engineers and designers accustomed to the constraints of machining or forging must learn to leverage the freedoms offered by layer-by-layer construction. Collaborating early with an experienced AM service provider, who understands the nuances of specific processes like Selective Laser Melting (SLM/L-PBF) or Selective Electron Beam Melting (SEBM), is highly recommended to ensure a successful outcome.
Here are key DfAM considerations for aerospace spring retainers:
1. Build Orientation and Support Strategy:
- 影響: How the retainer is oriented on the build plate significantly affects surface finish, dimensional accuracy, the amount and location of required support structures, residual stress accumulation, and potentially even anisotropic mechanical properties.
- 検討する:
- Critical Surfaces: Orient the part so that critical surfaces (like the spring seating face or valve stem interface) have the best possible as-built finish or are easily accessible for post-machining. Upward-facing surfaces generally have better finish than downward-facing or steeply angled ones.
- Support Minimization: Inclined surfaces below a certain angle (typically < 45 degrees relative to the build plate, but process-dependent) require support structures to prevent collapse during printing. Orienting the part to maximize self-supporting angles drastically reduces support material usage, printing time, and post-processing effort (support removal).
- 熱管理: Orientation influences heat distribution during the build, affecting residual stress and potential warping. Simulation tools can help predict optimal orientation.
- Feature Resolution: Fine features may resolve better in certain orientations relative to the layer deposition direction.
2. Minimum Feature Sizes and Wall Thickness:
- 制限: AM processes have limits on the smallest features they can accurately produce. This includes minimum wall thickness, hole diameters, and pin sizes. These limits depend on the specific machine, material (powder particle size), and process parameters (laser/electron beam spot size, layer thickness).
- 検討する:
- Typical Values: For L-PBF, minimum wall thicknesses are often around 0.4−0.5 mm, while EBM might be slightly higher. Small holes (< 0.5−1.0 mm) can be challenging to produce accurately without distortion or closure.
- Design Rules: Adhere to the specific design rules provided by the AM service provider (like Met3dp) for their chosen machine and material combination (e.g., 17-4PH on L-PBF vs. Ti-6Al-4V on SEBM). Avoid knife-edges or extremely thin sections that may warp or fail to resolve properly.
3. Designing for Support Removal:
- チャレンジ: Support structures, while necessary, must be removed after printing. This can be labor-intensive and potentially damage the part if access is poor or supports are attached to delicate features.
- 検討する:
- アクセシビリティ: Design the retainer so that areas requiring support are easily accessible for manual or automated removal tools (e.g., pliers, cutters, potentially CNC machining or wire EDM for tough-to-reach internal supports).
- Sacrificial Layers: Sometimes, adding a small amount of extra material (offset) where supports touch the part can allow for cleaner removal without marring the final surface, with the extra material machined away later.
- Break-Away Points: Design supports with perforation points or structures that facilitate easier breaking away from the main component.
- Internal Supports: Avoid complex internal supports where possible, as they can be extremely difficult or impossible to remove and may trap powder. If internal channels are needed, design them to be self-supporting or ensure clear access for powder removal and inspection.
4. Topology Optimization and Lightweighting:
- Opportunity: This is a major strength of AM. Software tools can analyze the load paths within the retainer and remove material from non-critical areas, creating organic, efficient structures.
- 検討する:
- Load Cases: Accurately define all relevant static, dynamic, and fatigue load cases the retainer will experience in service.
- Manufacturing Constraints: Ensure the optimization software considers AM constraints like minimum feature size, self-supporting angles, and avoiding enclosed voids that trap powder.
- Stress Concentrations: While topology optimization aims to reduce stress, ensure the resulting complex geometry doesn’t inadvertently create new stress concentration points. Smooth transitions and fillets are essential.
- Validation: Optimized designs must be thoroughly validated through Finite Element Analysis (FEA) and rigorous physical testing to ensure they meet all performance and safety requirements.
5. Part Consolidation:
- Opportunity: If the original design involved multiple components assembled together (e.g., a retainer and separate locking keepers), evaluate if AM allows them to be redesigned and printed as a single, integrated part.
- メリット Reduced part count, simplified assembly, potentially lower weight, elimination of joints that could be failure points.
- 検討する: Ensure the consolidated design still allows for assembly within the larger mechanism (e.g., can the valve stem still be inserted?) and that all functional requirements are met.
6. Designing for Powder Removal:
- チャレンジ: Unfused powder must be removed from the completed part, especially from internal channels or complex features.
- 検討する:
- Escape Holes: If designing internal channels or hollow sections (for lightweighting), ensure there are adequate escape holes for powder removal during post-processing. Consider line-of-sight access if possible.
- Channel Geometry: Avoid sharp internal corners or complex pathways where powder can easily get trapped. Smooth, flowing internal geometries are preferred.
7. CAD Modeling for AM:
- File Formats: While STL is common, newer formats like 3MF are often preferred as they contain more information (e.g., materials, colors, exact geometry definition).
- Model Quality: Ensure CAD models are “watertight” (no holes or errors in the surfaces) and have appropriate resolution for the intended feature sizes.
- Collaboration: Share native CAD files (e.g., STEP) with the AM provider if possible, as this allows for easier analysis, orientation optimization, and potential design feedback.
By carefully considering these DfAM principles, engineers can design aerospace spring retainers that fully leverage the capabilities of metal AM, resulting in components that are lighter, stronger, potentially more reliable, and optimized for their specific function within critical aerospace mechanisms. Engaging with AM experts, such as the team at Met3dp, early in the design process can significantly streamline development and ensure manufacturability. Met3dp offers comprehensive solutions, including deep insights into various AM printing methods and their associated design rules.
Achievable Tolerance, Surface Finish, and Dimensional Accuracy in AM Spring Retainers
A common question from engineers and procurement managers new to metal additive manufacturing concerns the precision achievable with the technology. While AM offers incredible geometric freedom, it’s important to have realistic expectations regarding as-built tolerances, surface finish, and overall dimensional accuracy, especially when compared to precision machining. For critical components like aerospace spring retainers, understanding these aspects is vital for determining necessary post-processing steps and ensuring the final part meets stringent drawing specifications.
Dimensional Accuracy and Tolerances:
- General Range: As a rule of thumb, typical dimensional accuracy for as-built metal AM parts (both L-PBF and EBM) falls within the range of ±0.1 mm to ±0.2 mm (±0.004 in to ±0.008 in) for smaller features, or around ±0.1% to ±0.2% of the overall dimension for larger parts. However, this is highly dependent on several factors:
- Machine Calibration: Well-maintained and accurately calibrated machines yield better results.
- Process Parameters: Laser/electron beam power, scan speed, layer thickness, and thermal management strategies all influence accuracy.
- Part Geometry and Size: Larger parts and complex geometries are more susceptible to thermal distortion, potentially affecting overall accuracy. Thin walls or unsupported features may warp.
- 素材: Different materials exhibit varying degrees of shrinkage and stress build-up during processing.
- ビルド方向: The orientation on the build plate affects how thermal stresses accumulate and can lead to anisotropic shrinkage or distortion.
- Achieving Tighter Tolerances: For critical dimensions on a spring retainer – such as the diameter interfacing with the valve stem, the flatness of the spring seating surface, or overall height – the as-built AM tolerances may not be sufficient. In these cases, post-process machining is typically required. Features requiring tolerances tighter than ±0.1 mm usually need to be finished via CNC milling, turning, or grinding. It’s crucial to account for this in the design phase by adding sufficient stock material (e.g., 0.5 – 1.0 mm) to surfaces that will be machined.
Surface Finish (Roughness):
- As-Built Condition: The surface finish of AM parts is inherently rougher than machined surfaces due to the layer-by-layer process and partially melted powder particles adhering to the surface.
- L-PBF (SLM): Generally produces a better as-built surface finish compared to EBM, typically ranging from Ra=6 to 15 μm (240 to 600 μin). The finish varies depending on the surface orientation: upward-facing surfaces are usually smoothest, followed by vertical walls, while downward-facing surfaces relying on supports tend to be roughest.
- EBM (SEBM): Operates at higher temperatures, often leading to more powder sintering and a rougher surface finish, typically Ra=20 to 35 μm (800 to 1400 μin) or higher. However, EBM parts generally have lower internal stress.
- Impact on Performance: Surface roughness can impact fatigue life (rough surfaces can act as crack initiation sites) and sealing capabilities. For a spring retainer, the finish on the spring contact surface and any dynamic sealing surfaces is critical.
- 表面仕上げの改善: Various post-processing techniques are used:
- 機械加工: Provides the best control for achieving smooth, specific Ra values on critical faces.
- Bead Blasting / Shot Peening: Can provide a uniform matte finish and, in the case of shot peening, induce beneficial compressive stresses to improve fatigue life.
- Tumbling / Vibratory Finishing: Uses abrasive media to smooth surfaces and round edges, suitable for overall finish improvement but less precise than machining.
- 研磨: Manual or automated polishing can achieve very smooth, mirror-like finishes where required, but is often labor-intensive.
- Electropolishing: An electrochemical process that can smooth surfaces, particularly effective on stainless steels like 17-4PH.
Summary Table: Typical AM Precision (As-Built)
パラメータ | プロセス | 典型的な範囲 | Key Influencing Factors | Post-Processing for Improvement |
---|---|---|---|---|
寸法公差 | L-PBF / EBM | ±0.1−0.2 mm or ±0.1−0.2% | Machine, Parameters, Geometry, Material, Orientation | CNC Machining, Grinding |
表面粗さ(Ra) | L-PBF | 6−15 μm | Orientation, Parameters, Powder Size | Machining, Polishing, Blasting |
表面粗さ(Ra) | EBM | 20−35+ μm | Orientation, Parameters, Powder Size | Machining, Polishing, Blasting |
Export to Sheets
Note: These are general guidelines. Specific capabilities should be confirmed with the AM service provider.
Implications for Procurement and Quality:
Procurement managers and quality engineers sourcing AM spring retainers must clearly define the required tolerances and surface finishes on engineering drawings, specifically indicating which features require post-machining. Relying solely on as-built AM dimensions and finishes is often insufficient for critical aerospace applications. Collaboration with the AM provider is key to understanding the achievable precision of their specific process and planning the necessary finishing operations to meet all functional requirements. This ensures that the final component delivered aligns perfectly with the demanding specifications of the aerospace industry.
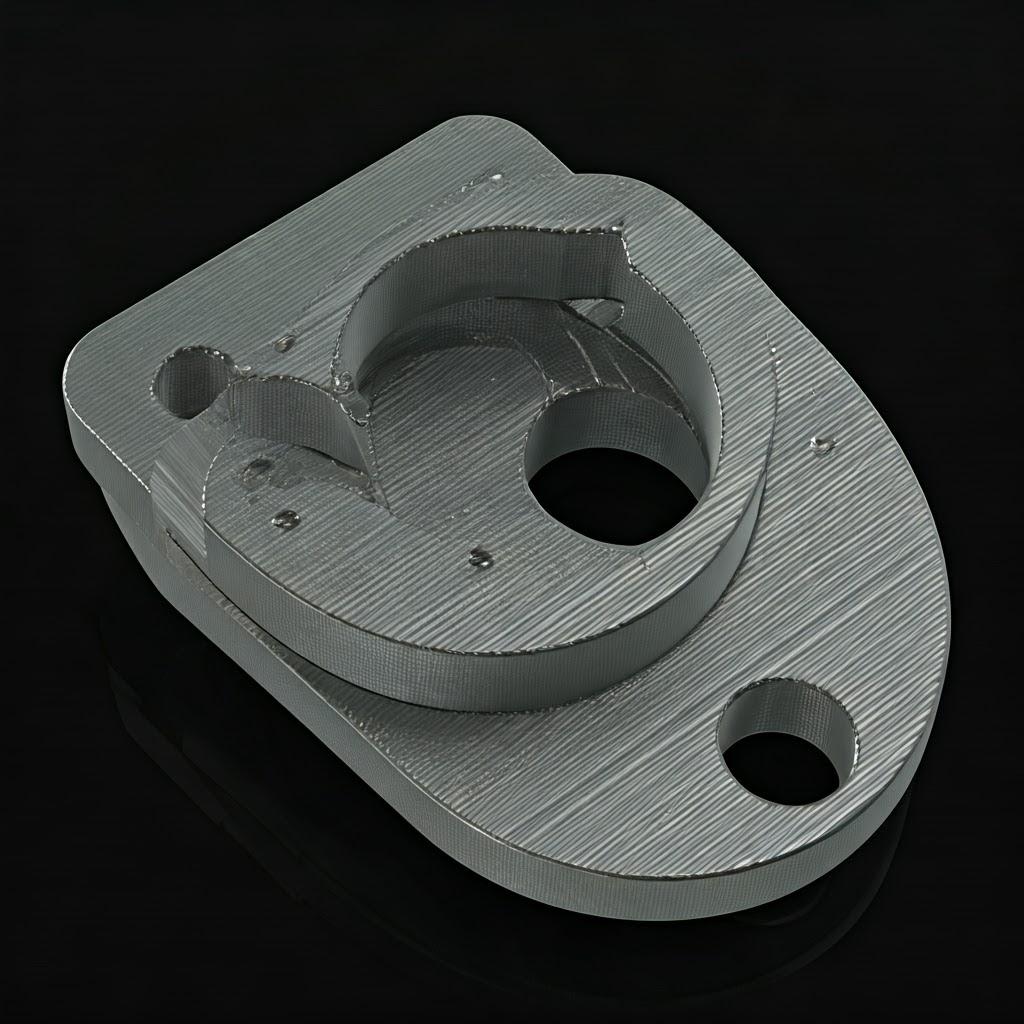
Essential Post-Processing Requirements for 3D Printed Aerospace Spring Retainers
Producing an aerospace spring retainer using metal additive manufacturing doesn’t end when the part comes off the build plate. A series of crucial post-processing steps are almost always required to transform the as-built component into a flight-ready part that meets stringent aerospace standards for mechanical properties, dimensional accuracy, surface integrity, and overall quality. Understanding these steps is essential for engineers designing the parts and for procurement managers sourcing AM services, as post-processing significantly impacts final part cost and lead time.
The typical post-processing workflow for AM aerospace components like spring retainers involves several key stages:
1. Stress Relief:
- Why it’s Needed: The rapid heating and cooling cycles inherent in Powder Bed Fusion processes (especially L-PBF) induce significant residual stresses within the printed part and at the interface with the build plate. These stresses can cause distortion or cracking during or after the build, particularly when the part is removed from the plate or during subsequent machining.
- プロセス Parts are typically heat-treated while still attached to the build plate in a controlled atmosphere furnace (inert gas like argon, or vacuum, especially for reactive materials like Ti-6Al-4V). The specific temperature and duration depend on the material (e.g., for Ti-6Al-4V, typically 650−800∘C; for 17-4PH, it might be combined with solution annealing). This allows internal stresses to relax without causing significant distortion. EBM processes, running at higher temperatures, generally result in lower as-built stress, but a stress relief cycle is still often recommended.
- Importance: A critical first step to ensure dimensional stability and prevent part failure during subsequent handling or processing.
2. Part Removal from Build Plate:
- プロセス Once stress-relieved (if applicable), the part(s) need to be separated from the build plate. This is commonly done using:
- Wire Electrical Discharge Machining (Wire EDM): Precise method, good for complex or tightly nested parts, minimal force applied to the part.
- Bandsaw: Faster and lower cost for simpler separations, but less precise and induces more mechanical stress.
- Consideration: The chosen method depends on part geometry, material, required precision, and cost considerations.
3. Support Structure Removal:
- チャレンジ: Removing the support structures generated during the build process.
- 方法:
- 手動による除去: Using pliers, cutters, and hand tools. Labor-intensive, requires skill to avoid damaging the part surface. Best suited for easily accessible supports.
- Machining (CNC): Used for more integrated supports or where a clean surface finish is required at the support interface.
- Wire EDM: Can be used for intricate or hard-to-reach internal supports.
- Importance: Supports must be fully removed, and the contact points often need further finishing to meet surface requirements. DfAM plays a huge role here – designing for easier support removal saves significant time and cost.
4. Heat Treatment (Property Optimization):
- Why it’s Needed: As-built AM parts often do not possess the optimal microstructure or mechanical properties required for demanding aerospace applications. Heat treatment refines the microstructure and achieves the desired strength, hardness, ductility, and fatigue resistance specified for the chosen alloy.
- プロセス
- 17-4PH: Typically involves 溶体化焼鈍 followed by Precipitation Hardening (Aging) at a specific temperature (e.g., H900, H1025, H1150 condition) to achieve the target strength/toughness balance.
- Ti-6Al-4V: Usually involves アニーリング (standard or duplex) to improve ductility and fracture toughness, or potentially solution treating and aging (STA) for higher strength applications, though this can reduce toughness.
- Importance: Absolutely critical for meeting the material specifications required for aerospace certification. Heat treatment cycles must be carefully controlled and documented.
5. Hot Isostatic Pressing (HIP):
- Why it’s Needed: While AM processes aim for full density, microscopic internal pores (due to gas entrapment or lack-of-fusion defects) can sometimes remain. These pores can act as crack initiation sites, significantly reducing fatigue life – a major concern for cyclically loaded parts like spring retainers.
- プロセス Parts are subjected to high temperature (below melting point) and high-pressure inert gas (typically Argon) in a specialized HIP vessel. The combination of heat and pressure causes internal voids to collapse and metallurgically bond, effectively eliminating porosity and achieving near 100% theoretical density.
- Importance: Often mandated for critical Class 1 or Class 2 aerospace components, especially those subject to high fatigue loads. It significantly improves fatigue strength, ductility, and fracture toughness, enhancing overall part reliability. Met3dp understands the criticality of processes like HIP for aerospace-grade components.
6. Surface Finishing and Machining:
- Why it’s Needed: To achieve the final required dimensional tolerances, surface finishes (Ra values), and specific geometric features (e.g., chamfers, precise radii) indicated on the engineering drawing.
- Processes:
- CNC Machining (Milling, Turning, Grinding): To precisely finish critical dimensions, flatness, parallelism, and concentricity on features like spring seats, pilot diameters, and interfacing surfaces.
- Blasting (Bead, Sand): For a uniform cosmetic finish or cleaning.
- ショットピーニング: To induce compressive surface stresses for enhanced fatigue life.
- Tumbling/Vibratory Finishing: For deburring and general surface smoothing.
- 研磨: For very low Ra requirements on specific surfaces.
- Importance: Ensures the retainer fits correctly within its assembly and performs its function reliably. Requires careful fixture design to hold the often complex AM part geometry during machining.
7. Cleaning and Inspection:
- Why it’s Needed: To ensure the part is free from contaminants (loose powder, machining fluids) and meets all dimensional and quality specifications.
- Processes:
- クリーニング: Ultrasonic cleaning, solvent wiping, or specialized cleaning procedures.
- 寸法検査: Using Coordinate Measuring Machines (CMM), laser scanners, or traditional metrology tools.
- 非破壊検査(NDT): Critical for aerospace validation. Common methods include:
- Visual Inspection: Magnified inspection for surface defects.
- Dye Penetrant Inspection (DPI/FPI): To detect surface-breaking cracks.
- Computed Tomography (CT) Scanning: X-ray based method to detect internal defects (porosity, inclusions) and verify complex internal geometries.
- Ultrasonic Testing (UT): Can detect subsurface flaws.
- Importance: Final verification that the part is free from defects and conforms to all drawing and specification requirements before delivery.
This comprehensive post-processing chain highlights that metal AM for aerospace is not just about printing; it’s an integrated manufacturing process where each step is vital for achieving the final quality and performance demanded by the industry. Partnering with a service provider like Met3dp, who has expertise across the entire workflow from powder to finished, inspected part, is crucial for success.
Common Challenges in AM Spring Retainer Production and Mitigation Strategies
While metal additive manufacturing offers significant advantages for producing complex aerospace components like spring retainers, the technology is not without its challenges. Awareness of these potential issues and implementing effective mitigation strategies are key to achieving consistent, high-quality results and ensuring the reliability expected in aerospace applications. Businesses seeking wholesale AM services or looking for a reliable manufacturing partner need to ensure their chosen provider has robust processes to address these challenges.
Here are some common challenges encountered in the AM production of spring retainers and how they can be managed:
1. Warping and Distortion:
- チャレンジ: Significant temperature gradients during the layer-wise melting and solidification process generate internal stresses. If these stresses exceed the material’s yield strength at elevated temperature, the part can warp or distort, especially thin sections or large flat areas.
- Mitigation Strategies:
- Optimized Build Orientation: Orienting the part to minimize large flat surfaces parallel to the build plate and reduce overhangs can help.
- Robust Support Structures: Well-designed supports anchor the part securely to the build plate, resisting deformation forces.
- プロセスパラメータの最適化 Fine-tuning laser/electron beam power, scan speed, and scan strategy can minimize stress build-up. Met3dp utilizes optimized parameter sets for its materials.
- Build Plate Heating: Maintaining an elevated temperature in the build chamber (inherent in EBM, possible in some L-PBF systems) reduces thermal gradients and lowers stress.
- Immediate Stress Relief: Performing a stress relief heat treatment cycle immediately after the build, often before removal from the plate, is crucial.
2. Difficulty in Support Structure Removal:
- チャレンジ: Supports in hard-to-reach areas, internal channels, or attached to delicate features can be time-consuming and difficult to remove without damaging the part.
- Mitigation Strategies:
- DfAM: Design the part for minimal support reliance (using self-supporting angles) and ensure good access to supported areas. Avoid complex internal supports where possible.
- Optimized Support Design: Use support structures with appropriate density and break-off points designed for easier removal (often software-generated with tunable parameters).
- Appropriate Removal Techniques: Employing the right tools (manual, CNC, wire EDM) based on support location and geometry.
- Skilled Technicians: Experienced personnel are essential for careful and efficient support removal.
3. Residual Stress Management:
- チャレンジ: Even if warping is controlled, significant residual stress can remain within the part, potentially compromising fatigue life or causing distortion during post-machining.
- Mitigation Strategies:
- Process Selection: EBM generally produces parts with lower residual stress than L-PBF due to higher process temperatures.
- プロセスパラメータの最適化 As with warping, optimized parameters help manage stress accumulation.
- Effective Stress Relief Cycles: Implementing appropriate post-build heat treatment is the primary method for reducing residual stress to acceptable levels. HIP also helps relieve stress.
4. Porosity (Gas and Lack-of-Fusion):
- チャレンジ: Microscopic voids can form within the material due to trapped gas during powder atomization or printing, or incomplete melting/fusion between layers or scan tracks (lack-of-fusion). Porosity severely degrades mechanical properties, particularly fatigue strength.
- Mitigation Strategies:
- High-Quality Powder: Using powder with low internal gas porosity, controlled particle size distribution, and high sphericity/flowability is critical. Met3dp’s advanced gas atomization and PREP technologies ensure high-purity, dense powders suitable for critical applications.
- Optimized Print Parameters: Ensuring sufficient energy density and proper overlap between scan tracks to achieve full melting and fusion.
- Inert Atmosphere Control: Maintaining a high-purity inert gas atmosphere (Argon or Nitrogen for L-PBF) or vacuum (EBM) prevents oxidation and contamination that can lead to porosity.
- 熱間静水圧プレス(HIP): The most effective way to eliminate any remaining internal porosity after printing. Often mandatory for critical aerospace parts.
5. Surface Roughness and Feature Definition:
- チャレンジ: Achieving the required smooth surface finish (low Ra) and sharp definition on small features directly from the AM process can be difficult.
- Mitigation Strategies:
- Process Selection & Orientation: L-PBF generally offers finer finish and feature resolution than EBM. Orienting critical surfaces optimally helps.
- Parameter Tuning: Adjusting layer thickness, beam spot size, and scan parameters can influence finish.
- 後処理: Planning for necessary surface finishing steps like machining, blasting, or polishing where required by the drawing specifications.
6. Powder Management and Quality Control:
- チャレンジ: Ensuring the consistency, purity, and traceability of metal powders is vital for repeatable results. Handling reactive powders like titanium requires special precautions to prevent contamination (oxygen/nitrogen pickup) or safety hazards (static discharge).
- Mitigation Strategies:
- Supplier Qualification: Sourcing powder from reputable suppliers with robust quality control like Met3dp.
- Powder Traceability: Implementing systems to track powder batches throughout their lifecycle (storage, use, recycling).
- Powder Handling Procedures: Using closed-loop handling systems, inert atmosphere glove boxes, and strict protocols for sieving and recycling powder to maintain quality and ensure operator safety.
- Regular Powder Testing: Characterizing powder properties (chemistry, particle size distribution, flowability, morphology) before use and after recycling.
7. Consistency and Repeatability:
- チャレンジ: Ensuring that parts produced in different builds or on different machines meet the same specifications consistently.
- Mitigation Strategies:
- Standardized Procedures: Implementing rigorous process control for all stages (build setup, printing, post-processing, inspection).
- Machine Calibration & Maintenance: Regular calibration and preventative maintenance of AM equipment.
- Quality Management Systems (QMS): Adhering to industry standards like AS9100 provides a framework for ensuring consistency and quality in aerospace manufacturing.
- Process Monitoring: Utilizing in-situ monitoring tools (melt pool monitoring, thermal imaging) where available to detect potential build anomalies in real-time.
By proactively addressing these challenges through careful design, process optimization, rigorous quality control, and appropriate post-processing, reliable and high-performance aerospace spring retainers can be successfully manufactured using metal AM. Choosing a knowledgeable and experienced B2B manufacturing partner equipped to handle these complexities is paramount for aerospace companies seeking to leverage the benefits of additive manufacturing.
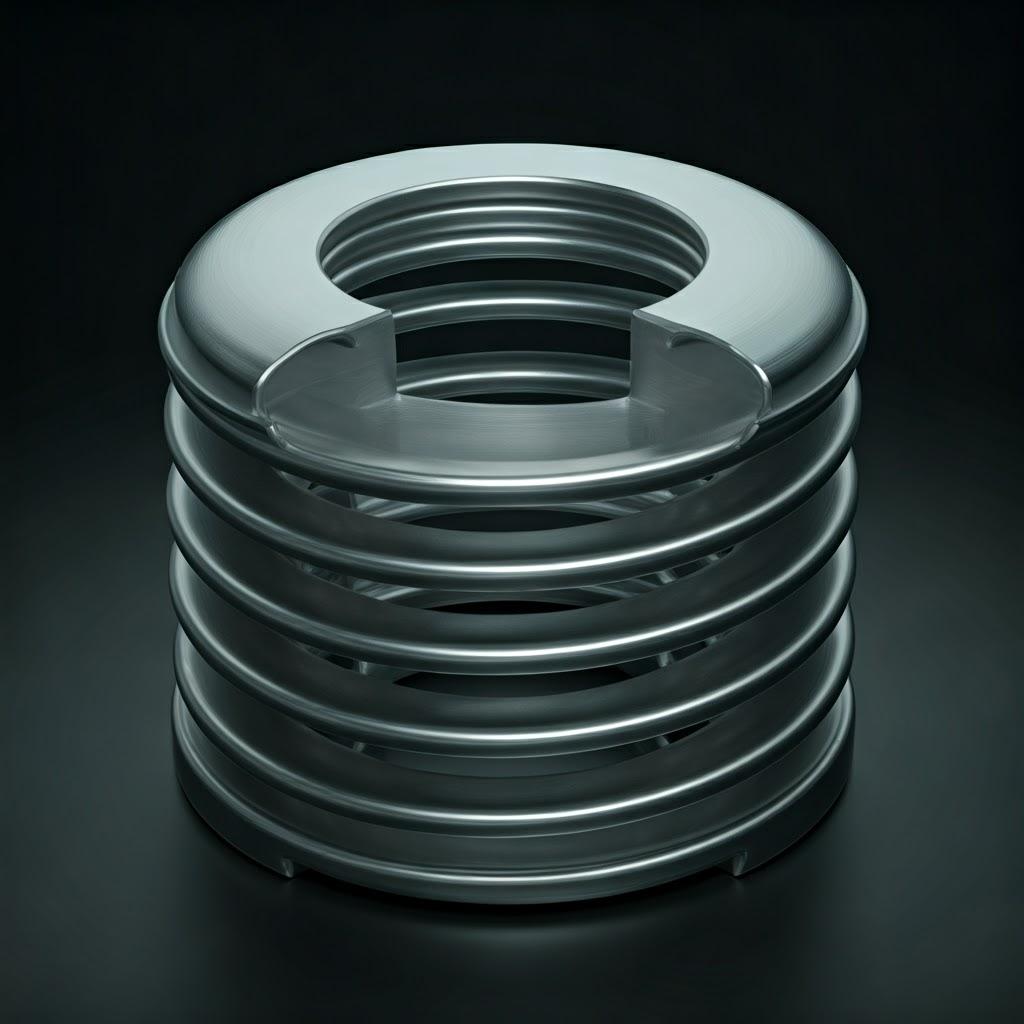
How to Choose the Right Metal 3D Printing Service Provider for Aerospace Components
Selecting the right additive manufacturing partner is as critical as perfecting the component design, especially within the aerospace sector where quality, reliability, and traceability are non-negotiable. Not all AM service providers possess the necessary expertise, equipment, and quality systems to produce flight-worthy components like spring retainers. For engineers and procurement managers tasked with sourcing these parts, evaluating potential B2B manufacturing partners requires careful consideration of several key factors. Choosing wisely ensures access to technical proficiency, robust processes, and components that meet stringent aerospace requirements.
Here’s a guide to evaluating and selecting a metal AM service provider for aerospace components:
1. Aerospace Certifications and Quality Management System (QMS):
- AS9100 Certification: This is the gold standard for aerospace manufacturing. Certification to AS9100 indicates the provider has implemented a rigorous QMS tailored to the demands of the aviation, space, and defense industries. It covers aspects like risk management, configuration management, traceability, and process control. Lack of AS9100 should be a significant red flag for critical component sourcing.
- Other Certifications: Depending on the scope of services, certifications like NADCAP (National Aerospace and Defense Contractors Accreditation Program) for special processes (heat treatment, NDT, welding/joining if applicable post-AM) demonstrate specific process proficiency. ISO 9001 is a foundational QMS but generally insufficient on its own for aerospace work.
2. Technical Expertise and Engineering Support:
- Deep Material Knowledge: The provider must have proven experience working with the specified aerospace alloys (e.g., 17-4PH, Ti-6Al-4V) and understand their behavior during AM processing and post-treatment.
- Process Mastery: Expertise in the relevant AM technologies (L-PBF, EBM/SEBM) is crucial. They should understand the advantages and limitations of each and guide you towards the optimal process for your retainer design and requirements.
- DfAM Capabilities: Look for providers who offer DfAM consultation. Can they review your design and suggest modifications to improve manufacturability, reduce weight, minimize supports, or enhance performance? Providers like Met3dp, with decades of collective expertise, offer comprehensive 医療、航空宇宙、自動車などの業界向けアプリケーション開発サービス.
- Post-Processing Know-How: They need a thorough understanding of required post-processing steps (stress relief, heat treatment, HIP, machining, NDT) and either possess these capabilities in-house or manage them through certified partners.
3. Equipment, Capacity, and Technology:
- Industrial-Grade Machines: Ensure the provider uses robust, well-maintained industrial AM systems suitable for producing high-quality metal parts, not just prototyping machines. Met3dp utilizes industry-leading SEBM printers known for accuracy and reliability in demanding applications.
- Relevant Technology: Do they operate the specific AM technology (L-PBF or EBM/SEBM) best suited for your material and application?
- ビルド・ボリューム: Can their machines accommodate the size of your spring retainer and allow for efficient nesting if producing multiple parts?
- Capacity & Scalability: Assess their current workload and capacity to meet your required volumes (from prototypes to potential low-volume production) and lead times. Can they scale production if needed?
4. Material Quality, Handling, and Traceability:
- Powder Sourcing & Quality: Where do they source their metal powders? Do they use powders specifically optimized for AM from reputable manufacturers? Met3dp stands out by manufacturing its own high-performance metal powders using advanced Gas Atomization and PREP technologies, ensuring quality control from the very beginning.
- マテリアルハンドリング Especially for reactive materials like titanium, ensure they have strict procedures for powder handling, storage, sieving, and recycling within controlled (e.g., inert) environments to prevent contamination.
- Traceability: Robust systems must be in place to track powder batches from sourcing through processing to the final part, ensuring full material traceability – a fundamental aerospace requirement.
5. Quality Control and Inspection Capabilities:
- Metrology: Access to calibrated inspection equipment like CMMs, laser scanners, or structured light scanners for verifying dimensional accuracy.
- 非破壊検査(NDT): In-house or certified partner capabilities for required NDT methods (e.g., FPI for surface cracks, CT scanning for internal defects) are essential for critical part validation.
- Documentation: Ability to provide comprehensive documentation packages, including material certifications, build logs, heat treatment records, inspection reports, and certificates of conformity.
6. Experience and Track Record:
- Aerospace Focus: Prioritize providers with demonstrable experience in manufacturing parts for the aerospace industry. Ask for case studies, references, or examples of similar components they have produced.
- Proven Reliability: Look for long-term players with a stable history and positive reputation within the industry. Explore the provider’s background; learning more about Met3dp reveals a strong foundation in metal AM equipment and materials.
7. Communication and Partnership Approach:
- Responsiveness: Are they communicative and responsive to inquiries and technical questions?
- Collaboration: Do they approach the relationship as a partnership, offering proactive advice and working collaboratively to solve challenges? This is vital for optimizing designs and ensuring project success.
Choosing a supplier based solely on the lowest quoted price can be detrimental in aerospace. A thorough evaluation across these technical, quality, and service criteria will help identify a capable and reliable metal AM partner like Met3dp, ensuring your critical aerospace spring retainers are produced to the highest standards.
Understanding Cost Factors and Lead Times for AM Aerospace Spring Retainers
Additive manufacturing offers unique advantages, but understanding the cost structure and typical timelines is crucial for project planning, budgeting, and managing expectations, especially for procurement professionals comparing AM to traditional methods. The cost and lead time for producing aerospace spring retainers via AM are influenced by a complex interplay of factors spanning design, materials, processing, and quality assurance.
Key Cost Drivers:
- 材料費:
- Powder Price: The base cost of the aerospace-grade metal powder. Titanium alloys (like Ti-6Al-4V) are significantly more expensive than stainless steels (like 17-4PH).
- Material Consumption: Includes the material in the final part, the material used for support structures (which becomes scrap or needs extensive recycling), and any test coupons printed alongside the parts. Efficient nesting of parts in the build chamber helps reduce relative material consumption per part.
- Machine Time / Build Time:
- Part Volume & Height: Larger or taller parts naturally take longer to print. Build time is primarily driven by the total volume of material to be melted and the total number of layers (height).
- 複雑さ: Highly complex geometries might require slower scan speeds or specific strategies, potentially increasing build time.
- Nesting Density: How many parts can be efficiently packed into a single build? Higher density reduces the machine time cost allocated per part.
- Machine Operating Cost: Different AM machines have varying hourly operating rates based on their purchase price, maintenance, energy consumption, and consumables (e.g., inert gas).
- 人件費:
- Pre-Processing: Engineering time for DfAM review, build file preparation, support generation, and simulation.
- Machine Setup & Operation: Skilled technicians required for loading powder, setting up the build, monitoring the process, and unloading.
- Post-Processing Labor: Often the most significant labor component. Includes part removal, extensive manual support removal, surface finishing (blasting, tumbling, manual polishing), and inspection. Machining labor adds further cost if required.
- Post-Processing Operations:
- Thermal Treatments: Costs associated with furnace time and controlled atmospheres for stress relief and heat treatment (annealing, aging).
- 熱間静水圧プレス(HIP): A specialized and relatively expensive process due to the high pressures, temperatures, and equipment involved. Cost is often based on the volume occupied within the HIP unit.
- 機械加工: CNC programming, setup, fixture design, and machine time for finishing critical features.
- 表面処理: Costs for shot peening, polishing, coating, etc.
- Quality Assurance & Inspection:
- NDT: Costs associated with performing and interpreting non-destructive tests like CT scanning or FPI.
- 寸法検査: CMM programming and operation time.
- Documentation: Time spent generating required reports and certifications.
- Overhead and Profit: Standard business costs and profit margins of the AM service provider.
Typical Lead Time Factors:
Lead time is the total duration from order placement to part delivery. For AM aerospace parts, it often involves more than just the printing time:
- Order Processing & Engineering Review: (1-5 days) Initial review, potential DfAM feedback, quote finalization.
- Build Preparation & Scheduling: (1-7 days) File preparation, build layout optimization (nesting), scheduling the job on an available machine (queue times can vary significantly).
- 印刷時間: (1-5+ days) Dependent on part size, height, complexity, and number of parts per build. Running 24/7 is common.
- Cooldown & Part Removal: (0.5-1 day) Allowing the build chamber and parts to cool safely before excavation and removal from the build plate.
- 後処理: (1-4+ weeks) This is often the longest and most variable part of the lead time.
- Stress Relief / Heat Treatment / HIP: Furnace cycles can take several days each, including ramp-up, soak times, and controlled cooling. Scheduling access to furnaces/HIP units (especially if outsourced) adds time.
- Support Removal: Can range from hours to days depending on complexity.
- Machining: Setup, programming, and machining time, potentially requiring multiple setups.
- Surface Finishing: Time required varies greatly with the chosen method.
- Inspection & NDT: Can take several days depending on the extent of inspection required and lab turnaround times.
- Final QA & Shipping: (1-3 days) Final checks, documentation packaging, and transit time.
Summary Table: Cost & Lead Time Influences
Factor Category | Key Influences | コストへの影響 | Impact on Lead Time |
---|---|---|---|
部品設計 | Volume, Height, Complexity, Support Requirements | 高い | 高い |
素材 | Powder Type (Ti vs. Steel), Amount Used | 高い | 低い |
AMプロセス | Machine Time, Build Rate, Nesting Efficiency | 高い | 高い |
労働 | Setup, Operation, Support Removal, Finishing, Inspection | 高い | 高い |
後処理 | Heat Treat, HIP, Machining Extent, NDT Requirements | 非常に高い | 非常に高い |
品質 | Certification Requirements, Documentation Level | 中程度 | 中程度 |
注文 | Quantity (Batch Size), Expedite Requests | 中程度 | 中程度 |
プロバイダー | Queue Time, Efficiency, Location | 低い | 中程度 |
Export to Sheets
Given these variables, providing a generic cost or lead time is difficult. The best approach is always to submit a specific Request for Quote (RFQ) with detailed drawings and specifications to qualified providers like Met3dp. This allows them to assess the requirements accurately and provide a tailored estimate for your aerospace spring retainer project. Understanding these factors helps procurement managers and engineers engage in more informed discussions with suppliers and plan projects realistically.
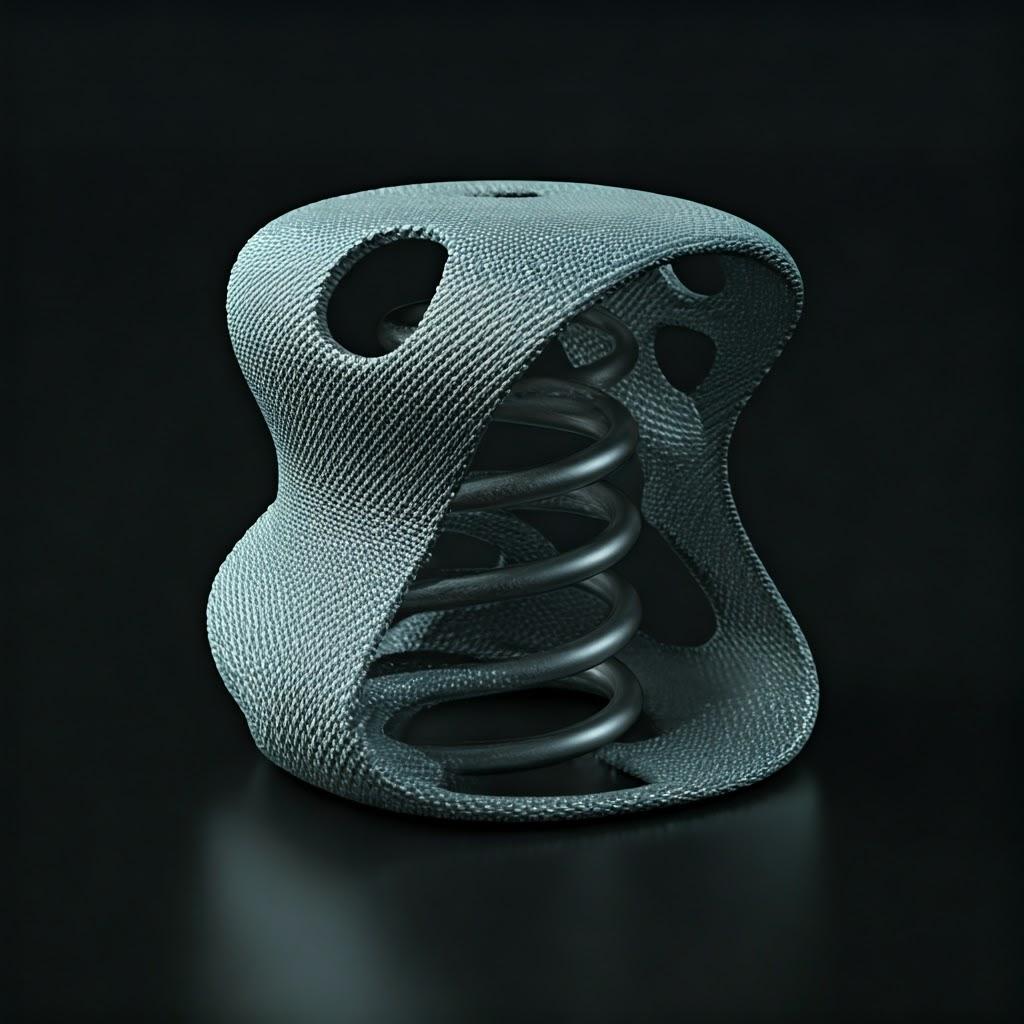
Frequently Asked Questions (FAQ) about AM Aerospace Spring Retainers
Here are answers to some common questions regarding the use of additive manufacturing for aerospace spring retainers:
1. How does the fatigue life of AM spring retainers compare to those made by traditional machining?
The fatigue life of AM spring retainers can be comparable, and in some cases potentially superior, to traditionally machined counterparts, but it is highly dependent on several factors. Key considerations include:
- Material Integrity: Achieving near-full density (>99.9%) through optimized print parameters and, critically, 熱間静水圧プレス(HIP) is essential to eliminate internal porosity which acts as fatigue crack initiation sites.
- 微細構造: Appropriate post-print heat treatments are crucial to develop the desired microstructure for fatigue resistance in alloys like 17-4PH and Ti-6Al-4V.
- 表面仕上げ: As-built AM surfaces are relatively rough and can negatively impact fatigue life. Post-processing steps like 加工 critical surfaces and/or applying surface treatments like shot peening (which induces beneficial compressive stresses) are often necessary to meet or exceed the fatigue performance of machined parts.
- Design (DfAM): AM allows for optimized designs that can potentially reduce stress concentrations compared to traditional designs constrained by machining limitations. When manufactured with rigorous process control, appropriate post-processing (including HIP), and thorough quality assurance, AM spring retainers can absolutely meet the demanding fatigue life requirements of aerospace applications.
2. Are 3D printed metal spring retainers certified for flight? Can they be used in critical aerospace applications?
Yes, additively manufactured metal components, including spring retainers, can be certified for flight and are increasingly being used in critical aerospace applications. However, certification is not automatic; it requires a structured and rigorous approach:
- プロセス・クオリフィケーション: The entire manufacturing process – from powder handling, specific AM machine and parameters, through all post-processing steps (heat treat, HIP, machining, NDT) – must be meticulously documented, controlled, and validated to ensure repeatability and consistency.
- Material Allowables: Extensive material testing (tensile, fatigue, fracture toughness, etc.) is performed on AM-produced specimens to establish statistically reliable material property data (design allowables) specific to the qualified process. This data must meet aerospace standards (e.g., MMPDS).
- Quality Management System: The manufacturer must operate under a certified aerospace QMS, typically AS9100, ensuring traceability, process control, and rigorous quality checks.
- Part-Specific Qualification: Depending on the criticality (e.g., flight-critical Class 1 parts), individual part designs may require specific qualification testing and analysis, potentially involving regulatory bodies like the FAA or EASA. Met3dp operates with the understanding of these stringent requirements, providing the necessary process control and material quality suitable for components intended for demanding industries like aerospace.
3. What is the typical minimum order quantity (MOQ) for AM spring retainers? Is it suitable for prototyping and low-volume production?
One of the significant advantages of additive manufacturing is its economic viability for low volumes, including prototypes and small production runs. Unlike traditional methods like forging or casting that require expensive tooling amortization, AM has minimal setup costs tied to specific part geometry.
- プロトタイピング: AM is ideal for producing single pieces or very small batches (e.g., 1-10 units) of spring retainers for design validation, fit checks, and initial functional testing, often with significantly shorter lead times than traditional prototyping methods.
- 少量生産: AM remains competitive for small batch production (e.g., tens to potentially hundreds of units), especially for complex designs or where on-demand availability is needed for spares or specialized applications.
- MOQ: While technically an MOQ of one part is possible, the per-part cost is generally higher for single pieces due to the fixed costs of setup and machine time allocation. Costs become more economical as batch sizes increase, allowing for better nesting within the build chamber and amortization of setup/post-processing efforts. Many AM service providers cater specifically to B2B clients needing prototype and low-volume industrial parts and do not impose high MOQs. Always discuss your volume requirements with the provider when requesting a quote.
Conclusion: Elevating Aerospace Mechanisms with Met3dp’s Additive Manufacturing Solutions
Aerospace spring retainers, though often small, are indispensable components operating under extreme conditions where failure is unacceptable. The journey through their application, material demands, design intricacies, and manufacturing challenges underscores the need for precision and reliability. As we’ve explored, metal additive manufacturing offers a powerful suite of tools to meet and exceed these demands, moving beyond the constraints of traditional methods. The ability to create lightweight, topology-optimized designs from high-performance alloys like 17-4PH and Ti-6Al-4V, coupled with the potential for part consolidation and accelerated development cycles, marks AM as a key enabler for the next generation of aerospace innovation.
Successfully leveraging AM for these critical components requires more than just access to a 3D printer; it demands a deep understanding of materials science, process physics, design for additive manufacturing (DfAM), and the rigorous post-processing and quality assurance protocols mandated by the aerospace industry. From managing residual stress and ensuring full density through HIP to achieving micron-level tolerances via post-machining and validating integrity through NDT, the path to a flight-ready AM part is complex and requires expert navigation.
This is where choosing the right partner becomes paramount. メット3dp stands at the forefront of metal additive manufacturing, offering a comprehensive ecosystem of solutions tailored for demanding industrial applications, including aerospace. Our capabilities extend from the development and production of high-quality, spherical metal powders using industry-leading Gas Atomization and PREP technologies, to providing cutting-edge Selective Electron Beam Melting (SEBM) systems renowned for their print volume, accuracy, and reliability.
Our decades of collective expertise in metal AM empower us to partner with aerospace engineers and procurement managers, providing not just printing services but holistic support encompassing material selection guidance, DfAM consultation, process optimization, and insights into achieving certified, flight-ready components. We understand the critical nature of parts like spring retainers and are committed to delivering solutions that enhance performance, reduce weight, and contribute to the safety and efficiency of aerospace mechanisms.
Whether you are exploring AM for rapid prototyping, seeking a reliable supplier for low-volume production of complex retainers, or aiming to implement AM technology within your own facilities, Met3dp has the technology, materials, and expertise to support your goals.
Elevate your aerospace components with the power of additive manufacturing. Contact Met3dp today to discuss your spring retainer project or explore how our advanced metal powders and SEBM systems can accelerate your organization’s journey into next-generation manufacturing.
シェアする
MET3DP Technology Co., LTDは、中国青島に本社を置く積層造形ソリューションのリーディングプロバイダーです。弊社は3Dプリンティング装置と工業用途の高性能金属粉末を専門としています。
関連記事
Met3DPについて
最新情報
製品
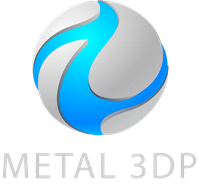
3Dプリンティングと積層造形用金属粉末