金属射出成形(MIM)を理解する
目次
金属射出成形 (MIM)は、公差の厳しい小型で複雑な金属部品を製造するために使用される製造プロセスです。MIMは、プラスチック射出成形の汎用性と機械加工金属の強度と完全性を兼ね備えています。この記事では、MIM技術、アプリケーション、装置、プロセス、設計上の考慮点などの詳細な概要を説明します。
金属射出成形の概要
金属射出成形は粉末冶金プロセスであり、射出成形技術を用いて小型の精密金属部品の大量生産を可能にする。
MIMの仕組み
MIMプロセスでは、微細な金属粉末をバインダー材料と混合し、金型に注入できる原料を作る。成形された部品はグリーン部品と呼ばれ、その後、バインダーを除去し、金属粉末を強固な構造に固めるために焼結される。基本的な手順は以下の通り:
- ミキシング - 金属微粉末をバインダーとブレンドし、均質な原料を作る。
- 射出成形 - 原料を溶かして金型に注入し、グリーン部品を形成する。
- 脱脂 - バインダーは、溶剤、熱、または触媒脱バインダーによって除去される。
- 焼結 - 脱バウンドした部品は焼結され、金属組織の緻密化と強化が行われる。
- 二次事業 - 機械加工、穴あけ、タッピングなどの追加仕上げ工程。
MIMの利点
MIMには、他の製造技術と比べていくつかの利点がある:
- 部品当たりのコストを抑えた大量生産
- 公差の厳しい複雑な形状
- ステンレス鋼、チタン、タングステン、コバルトクロムなど、さまざまな素材。
- スクラップ・ロスや材料の無駄を最小限に抑える
- ニアネットシェイプ加工による機械加工の低減
- 0.005ポンドから0.5ポンドの小さな部品サイズ
- アセンブリの組み合わせによる部品の統合
- 滑らかな表面と良好な仕上げ
MIMの限界
金属射出成形の限界には次のようなものがある:
- 高い立ち上げ費用と金型費用
- 部品のサイズ範囲が狭い
- 専用機材が必要
- 生産が遅い多段階プロセス
- 粉体特性に基づく寸法制限
- パウダーフローに基づく部品形状の制限
MIMの応用
MIMは、以下のような産業において、公差の厳しい小型で複雑な部品の製造に広く使用されている:
- 医療 - 整形外科用インプラント、歯科用インプラント、手術器具
- 自動車 - エンジン部品、バルブ、ギア
- 航空宇宙 - タービンブレード、インペラ、ノズル
- エレクトロニクス - コネクター、マイクロギア、シールド
- 銃器-トリガー、ハンマー、安全装置
- 時計 - ケース、ブレスレット、リューズ
- 工業用 - ノブ、ファスナー、切削工具
MIMは、インベストメント鋳造、機械加工、スタンピングといった他の金属部品製造プロセスと競合している。
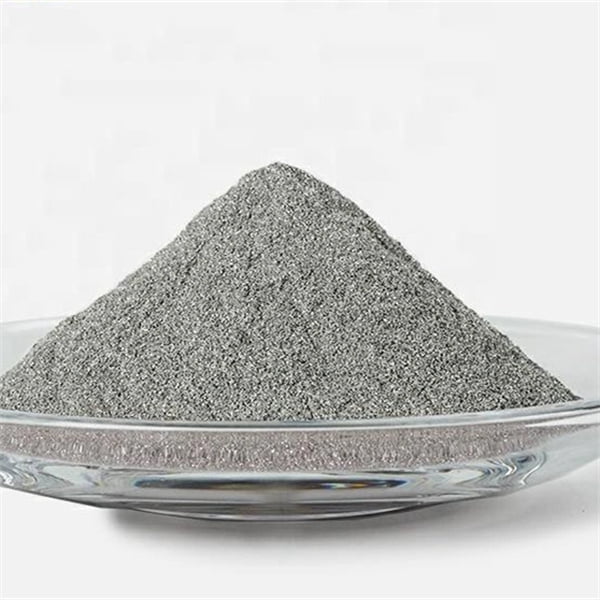
金属射出成形 設備ガイド
MIMプロセスの各段階には、専用の装置が必要です。ここでは、主なMIM装置の種類を紹介する:
設備 | 機能 |
---|---|
パウダーフィーダー | 微粉末を正確に測定 |
ミキサー | パウダーとバインダーを均一にブレンドする |
粉砕機 | 原料を成形用の顆粒にする |
射出成形機 | 原料を必要な形状に成形する |
脱バインダー炉 | 成形部品からバインダーを取り除く |
焼結炉 | 金属組織の緻密化と強化 |
研削盤 | ゲート、ランナー、平滑面を取り除く |
マシニングセンター | 焼結部品への穴あけ、旋盤加工、フライス加工 |
プロセスを統合し、生産性を最大化するために、高度な自動化、ハンドリングシステム、および制御が使用される。設備は、材料、部品サイズ、生産量、品質要件などの要因に基づいて慎重に選択されなければならない。
金属射出成形プロセス ステップバイステップ
MIM加工には、微細な金属粉末を完全に緻密な最終使用部品に変えるための複数の工程が含まれる。
ステップ1 - ミキシング
- 金属粉末とバインダーをミキサーで十分に混合し、均質な原料を製造する。
- 粉末の粒子径、形状、分布が成形性と焼結に影響する
- バインダーは射出成形時に流動性と接着性を与える
- ワックス、PP、PE、PVCなどの熱可塑性プラスチック、バインダーとして使用されるポリマー
- シグマブレード、Zブレード、ダブルプラネタリーミキサーを使用したミキシング
ステップ2 - 造粒
- 原料混合物は、射出成形用の小さなペレットに造粒される。
- 材料の流れを改善し、バレル内での偏析を防止します。
- 造粒機は、回転する刃で原料を均一な顆粒に切断します。
- 顆粒の形状とサイズは、充填密度と成形性に影響する。
ステップ3 - 射出成形
- 原料の顆粒は、必要な部品の形状とサイズに成形されます。
- 温度と圧力を制御した改良型射出成形機を使用
- 欠陥を最小化するための成形パラメータの最適化が重要
- グリーン部品と呼ばれるアズモールド部品は、形状は付与されているが強度はない
ステップ4 - 脱バインダー
- バインダーは、溶剤、熱、触媒のいずれかの方法でグリーン部分から抽出される。
- 溶剤脱バインダーは毛細管現象を利用してバインダーを溶解する。
- 熱脱バインダーは炉の中でバインダーを分解する。
- 触媒によるバインダー除去を促進する触媒脱バインダー
- 脱バインダーにより、金属粒子の多孔質構造を持つ茶色の部品ができる
ステップ5 - 焼結
- 茶色の部品は、制御された雰囲気炉で焼結される。
- 金属粒子間の結合は拡散と物質輸送によって形成される
- 焼結中に96-99%までのほぼ完全な密度を達成
- 雰囲気、温度、時間は欠陥を避けるために最適化される。
- 焼結収縮は成形時に考慮される
ステップ6 - セカンダリー・オペレーション
- 焼きなまし、機械加工、穴あけ、メッキなどの追加金属加工工程
- アニール処理により焼結による内部応力を緩和
- CNC加工でスプルーを除去し、表面を滑らかにし、機能を追加する。
- 強化または防錆のために施されるメッキおよび塗装
MIMプロセスは、プラスチック射出成形と粉末冶金の利点を組み合わせることで、複雑で高精度の金属部品を可能にする。
MIM部品の設計上の考慮点
MIMは、機械加工では不可能な幾何学的自由を可能にするが、ある種の設計上の配慮を必要とする:
- 肉厚 - 典型的な測定範囲は0.3~4.0mmで、一部のパウダーは6mmまで対応可能
- 表面仕上げ - 鋳造よりも滑らかな仕上がりだが、機械加工ほど精巧ではない。
- 寸法公差 - 部品形状に基づき±0.1%~±0.5%(ミクロンレベルの精度も可能
- 密度 - 最適化された焼結により、99%までのフル密度を達成可能
- 幾何学 - パウダーを閉じ込めず、バインダーを逃がすことが重要である。
- ドラフト角度 - 1~3°の抜き勾配を持つテーパー壁により、部品の排出を容易にします。
- ラディとフィレ - シャープなコーナーよりも緩やかなトランジションが好まれる
- 穴と空洞 - 貫通穴の最小直径は0.25~0.5mm
- スレッド - 成形も可能だが、精度を高めるために焼結後に機械加工することが多い。
- 表面の詳細 - 金型の磨耗を減らすために細かいディテールを制限する。
MIMの設計は、加工の容易さよりも、性能を最大化する形状に焦点を当てるべきである。このプロセスは、コストと重量を大幅に削減することで、複数部品のアセンブリを1つの部品に統合することを可能にします。
金属射出成形に使用される材料
MIMは、さまざまな産業において、幅広い金属、合金、セラミックから部品を製造することができる。
素材 | アプリケーション | プロパティ |
---|---|---|
ステンレス | 医療、銃器、海洋 | 耐食性、強度 |
低合金鋼 | 自動車、工業 | 磁気応答、機械加工性 |
軟磁性合金 | センサー、アクチュエーター | 高い透水性 |
硬質金属合金 | 切削工具 | 耐摩耗性、硬度 |
銅合金 | エレクトロニクス、サーマル | 電気伝導度 |
アルミニウム合金 | 電気、熱 | 軽量、導電性 |
チタン合金 | 航空宇宙、自動車 | 強度、生体適合性 |
タングステン合金 | 放射線遮蔽 | 高密度 |
サーメット | エレクトロニクス、光学 | 耐酸化性 |
部品の機能、コスト、後処理工程、合金適合性などの要素が、理想的なMIM材料の選択を決定する。
MIMサプライヤーと装置メーカー
多くの企業がMIM材料、サービス、生産、設備を世界的に提供している。ここでは、バリューチェーン全体にわたる主要なMIMサプライヤーを紹介する:
会社概要 | 製品/サービス |
---|---|
BASF | 原料、バインダー |
サンドビック・オスプレイ | 金属粉末 |
ヘガネス | 金属粉末 |
CNPCパウダー | 金属粉末 |
インドミム | MIM製品、サービス |
MPP | MIM製品、サービス |
ARCグループ | MIM製品、サービス |
アトラス・プレスド・メタルズ | MIM部品製造 |
エプソンアトミックス | MIM装置 |
ミラクロン | 射出成形機 |
エルニク | 焼結炉 |
かんせんけつごうき | 脱バインダー、焼結炉 |
また、MIMのサプライチェーン全体にわたって、多くの小規模な地域プレーヤーが関与している。MIMの採用を検討しているエンドユーザーは、必要とされる能力に応じて、材料サプライヤーや受託製造業者と提携することができる。
MIM部品と代替品のコスト分析
以下は、異なる製造工程で1000個の部品を製造した場合の推定コストの比較である:
プロセス | セットアップ費用 | 機械コスト | 金型費用 | 部品代 | 合計(1000部) |
---|---|---|---|---|---|
CNC加工 | 低い | $100,000 | $2,000 | $50 | $52,000 |
インベストメント鋳造 | 高い | $500,000 | $40,000 | $20 | $60,000 |
金属射出成形 | 高い | $750,000 | $100,000 | $15 | $115,000 |
スタンピング | 高い | $1,000,000 | $150,000 | $10 | $160,000 |
- CNC加工は生産量が少なく、部品コストが高く、複雑性に限界がある。
- インベストメント鋳造は10,000個までの生産に適している。
- MIMは複雑な形状の中・大量生産に有利
- プレス加工は金型費が非常に高いが、10万個以上の大量生産では部品価格が最も安くなる。
MIMが他のプロセスよりも経済的になるクロスオーバー・ポイントは、体積、複雑さ、サイズによって異なる。
MIMサプライヤーまたはパートナーの選択
費用対効果の高い部品製造には、有能なMIMサプライヤーや製造パートナーを選ぶことが重要です。以下に主な検討事項を示します:
- 技術的専門知識 - 類似のMIM部品、材料、業界に関する実務経験
- 品質システム - ISO9001認証取得、品質管理の実践
- 生産能力 - 現在および将来の数量要件を満たす能力
- 二次加工 - 機械加工、プレス、メッキ、塗装能力
- 部分最適化 - メリットを最大化するためのMIMサポート設計
- プロトタイピング - デザインを検証するためのラピッドプロトタイピングサービス
- 金型能力 - 社内での金型設計・製作が望ましい
- 原材料へのアクセス - 確立された原料供給ルート
- 研究開発能力 - 先端素材と製造技術の継続的な研究開発
- 顧客重視 - ニーズへの対応とコラボレーション・アプローチ
- コスト構造 - 価格モデルと予測数量に対する競争力
- 物流 - リードタイム要件を満たしながら、確実に部品を納入する能力
これらの要素に優先順位をつけることで、特定の用途に適した戦略的MIMパートナーを特定することができる。
MIM装置の設置
MIM機能を社内に導入する企業にとって、適切な機器の設置は極めて重要である。以下が主な検討事項である:
- MIMラインに必要な床面積は約2000~5000平方フィート
- 200~600kVAの安定した電源が必要
- 定格圧力100 psiの圧縮空気ライン
- 熱、排気、集塵のための排気
- 窒素、プロセス水、ガス供給などのユーティリティ
- 約20±3℃、50±20%の温湿度制御
- メザニン、付帯設備設置用プラットフォーム
- ホイスト、フォークリフト、大箱などのマテリアルハンドリングシステム
- コントロールルーム、監視用コンピューターシステム
- プロセスの安全性と機器操作に関するスタッフ・トレーニング
- プロセスシミュレーション、インストール検証のためのテスト実行
- 校正と予防メンテナンスのスケジュール
MIM装置を円滑に稼動させるには、十分なスペース、ユーティリティ、管理された条件が不可欠です。徹底したテストとトレーニングにより、実際の生産に備えます。
MIM機器メンテナンス
一貫したメンテナンスは、MIM製造装置の稼働時間と性能を向上させます。重要な側面
- 各機械の予防保全スケジュールを文書化
- 材料の流出、漏洩、埃、瓦礫の日常的な清掃
- フルードレベル、漏れ、異音、振動のチェック
- 圧力、温度、消費電力のモニタリング
- 暖房、冷房、制御システムのテスト
- スクリーン、スクリュー、バレルなどの磨耗部品の交換
- 部品の疲労、損傷、アライメントの検査
- 運転時間に基づく定期的なリビルドとオーバーホール
- 分析のためのメンテナンス・ログの追跡
- 重要部品のスペアパーツ在庫の保管
- 機器の適切な操作と安全性に関するトレーニング
- 機器ベンダーによるタイムリーなサービスとサポート
よく訓練されたスタッフと装置ベンダーとの協力により、ダウンタイムを最小限に抑えながら、MIM装置の生産性を最大限に高めることができる。
金属射出成形シミュレーションソフトウェア
シミュレーションソフトウェアは、実際の生産前にMIMプロセスをデジタルモデリングするために使用されます。以下のような利点があります:
- 金型充填パターンの予測とゲート位置の最適化
- 欠陥防止のための溶接ラインとエアトラップの特定
- 複雑な形状における熱勾配と凝固の研究
- 最終形状に及ぼす脱バインダーおよび焼結プロファイル効果のシミュレーション
- 製作前の金型設計の検証
- バーチャル・プロトタイピングによる試験コストの削減
- 視覚的表現による人材育成
市販のMIMシミュレーションパッケージには次のようなものがある:
- ミムシム - 焼結による成形の統合シミュレーション
- シグマ・ソフト - 金型充填と歪みの3次元FEM解析
- ネッチュ MIMPre - MIM原料のレオロジー特性のモデリング
- シマック添加剤 - AMプロセスのマルチフィジックスシミュレーション
- EOS PSW - 焼結と熱処理に焦点を当てたシミュレーション
MIMソフトウェアを使用することで、プロセスの一貫性が向上し、部品の品質が最適化され、物理的な試作コストが削減されます。シミュレーションから製造までの統合ワークフローが望ましい。
一般的なMIM不良のトラブルシューティング
MIM部品の典型的な欠陥と、その潜在的な根本原因には次のようなものがある:
欠陥 | 原因 |
---|---|
ショートショット | 射出圧力が低く、凝固が早い |
フラッシュ | カビの詰め過ぎ、カビの損傷 |
反り | 不均一な冷却、バインダーの問題 |
ひび割れ | 高速焼結、高バインダー含量 |
多孔性 | ホモジナイズ不良、トラップガス |
汚染 | 交差汚染、炉内雰囲気 |
寸法バリエーション | 原料問題、金型摩耗、収縮 |
表面の欠陥 | 気孔率、液体金属脆化 |
包含事項 | 汚染された原料、ノズルの詰まり |
欠陥の原因となっている工程パラメータを分離し、原料配合、成形パラメータ、脱バインダー、焼結プロファイルの調整などの是正措置を講じるためには、系統的な欠陥分析手法を用いるべきである。
MIM技術の利点
MIMは、他の金属部品製造アプローチに比べて大きな利点を提供する:
- 複雑さ - 複雑な3D形状が可能、アセンブリを統合
- 一貫性 - 部品のばらつきが少なく、再現性の高いプロセス
- 効率性 - 原材料の無駄を抑えたニアネットシェイプ加工
- オートメーション - 高度に自動化されたプロセスで労働力を削減
- 柔軟性 - 金属、セラミック、複合材など幅広い素材に対応
- 品質 - 良好な表面仕上げと機械的特性
- 生産性 - 部品単価を抑えながら大量生産
- 小型化 - 10μmまでの微細部品
- 持続可能性 - 機械加工と比較したエネルギー効率
- コスト - 中・大量生産で総コストを低減
MIMのユニークな機能は、自動車、航空宇宙、医療、エレクトロニクスなど多様な産業での採用を促進している。
金属射出成形の限界
多くの利点があるにもかかわらず、MIMには一定の限界がある:
- 高い初期金型投資
- 65グラム以下の限られたサイズ
- CNC加工より精度が低い
- 工程管理が必要な多孔性リスク
- 粉体特性に基づく材料選択の制限
- 微粉末の安全上の危険性
- 成形性に関連する部品形状の制約
- ロット間変動の可能性
- 溶製材より低い機械的特性
- 試作品の少量限定生産
- 多くの用途で二次加工が必要
- 特殊な設備と訓練を受けたオペレーターが必要
非常に高精度な部品や、少量生産の大型金属部品には、MIMよりも他のプロセスの方が適しているかもしれない。
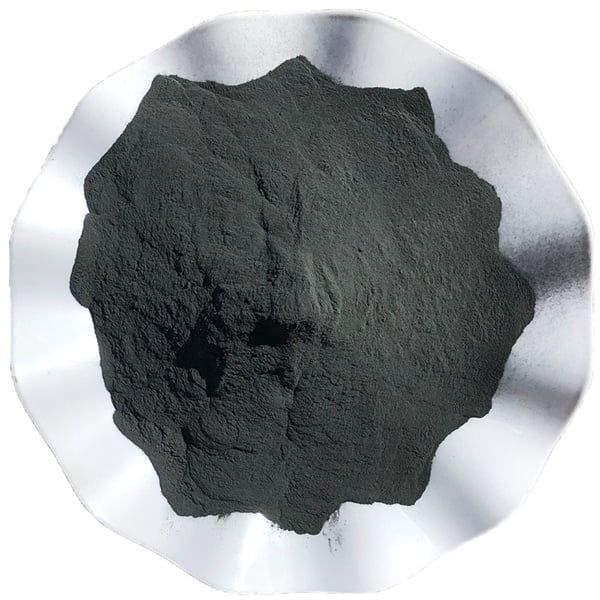
金属射出成形の未来
MIMは、技術と素材が改善され続けるにつれて、力強い継続的成長が見込まれる:
- 成形性とグリーン強度を向上させる新しいバインダーシステム
- ナノコンポジットを用いた新しい原料配合
- 電流制限を超える大型部品
- セラミックスとタングステン合金の採用増加
- 医療、エレクトロニクス分野の需要が好調
- アディティブ・マニュファクチャリングによるMIMツーリングの製造
- ロボット工学とインダストリー4.0の統合による自動化
- 過酷な環境下での用途拡大
- バウンドメタルデポジションによる金属3Dプリンティングとの融合
研究開発が進み、採用が容易になったことで、MIMの利用は今後数年間、多様な用途で急速に拡大するだろう。
シェアする
MET3DP Technology Co., LTDは、中国青島に本社を置く積層造形ソリューションのリーディングプロバイダーです。弊社は3Dプリンティング装置と工業用途の高性能金属粉末を専門としています。