3D 프린팅 파우더
목차
적층 제조(AM)라고도 하는 3D 프린팅은 특수 파우더를 사용하여 연속적인 레이어링 방식으로 3차원 구성 요소를 제작합니다. 이 가이드는 3D 프린팅용 파우더의 유형, 특성, 사양, 제조 방법, 주요 공급업체 및 가격, 산업 전반의 응용 분야, 대체품과의 비교, 자주 묻는 질문 등을 살펴보는 심층적인 3D 프린팅용 파우더에 대한 참고 자료입니다.
개요 3D 프린팅 파우더
3D 프린팅 파우더는 플라스틱, 금속 및 세라믹 플랫폼에서 적층 부품 제작을 가능하게 하는 원료 공급원입니다. 주요 특징
- 상태: 초미립자 분말
- 크기 범위: 일반적으로 10-150 미크론
- 형태: 대부분 구형 입자 모양
- 구성: 구성: 폴리머, 금속 합금, 세라믹, 사암 혼합물
- 주요 속성: 엔지니어링된 입자 크기 분포, 유동성, 팩 밀도 및 미세 구조
3D 프린팅 파우더는 파우더의 물리적 특성과 열/운동 프린팅 프로세스와의 상호 작용을 엄격하게 제어함으로써 다른 방법으로는 달성할 수 없는 복잡한 부품 형상과 재료 구성 그라데이션을 쉽게 구현할 수 있습니다.
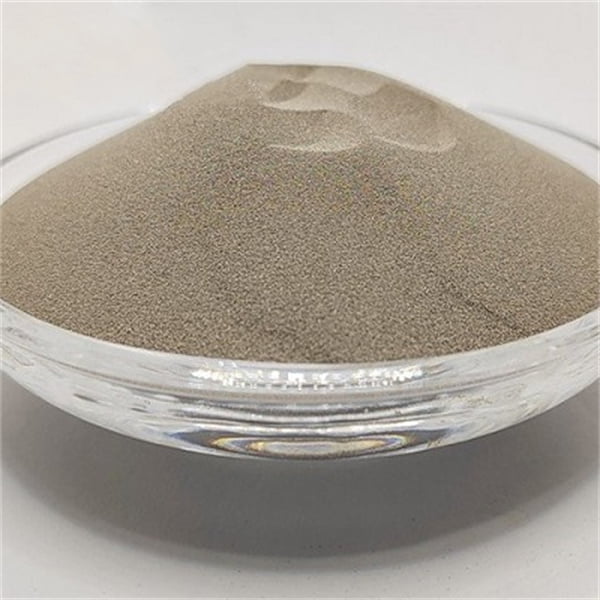
3D 프린팅 파우더의 종류
범주 | 재료 | 인쇄 방법 |
---|---|---|
플라스틱 | 나일론, ABS, TPU, PEKK, PEEK... | 선택적 레이저 소결(SLS) |
금속 | 스테인리스, 공구강, 티타늄 및 합금, 초합금... | 직접 금속 레이저 소결(DMLS) |
도자기 | 알루미나, 지르코니아, 실리콘 카바이드 | 바인더 분사, 융합 증착 모델링 |
합성물 | 금속/플라스틱 혼합물, 사암 혼합물 | 멀티 제트 퓨전(MJF), 결합 금속 증착 |
생체 적합성 | PEEK, PLGA, TCP... | 선택적 레이저 용융(SLM) |
표 1: 상업용 3D 프린팅 파우더의 주요 카테고리, 재료 및 관련 프린팅 플랫폼
폴리머, 금속, 세라믹 및 복합 분말은 항공우주, 자동차, 의료, 치과 및 산업 시장 전반의 최종 사용 부품 생산을 지원합니다.
제조방법
방법 | 설명 | 재료 적합성 | 장점 | 단점 |
---|---|---|---|---|
원자화 | 이 포괄적인 용어는 용융 금속을 미세한 입자로 분해하는 다양한 기술을 포괄합니다. 용융된 금속은 노즐을 통해 고압 가스나 물 흐름으로 강제 유입되어 물방울을 구형 입자로 빠르게 응고시킵니다. | 금속(철, 알루미늄, 티타늄 합금) | – 높은 생산율 – 일관된 입자 크기 및 모양 – 우수한 분말 흐름성 | – 높은 에너지 투입 필요 – 입자에 산화물 형성 가능성 – 특정 재료로 제한 |
가스 분무 | 가장 일반적인 원자화 방법으로, 불활성 가스(일반적으로 질소)를 사용하여 용융 금속을 분해합니다. | 원자화와 유사하지만 일반적으로 표면 품질이 더 좋고 입자 크기에 대한 제어가 더 엄격합니다. | – 타 미립화 방식에 비해 우수한 분말 품질 – 반응성 금속에 적합 | Atomization과 유사하지만 장비 비용이 더 높습니다. |
물 분무 | 고압 워터제트를 사용하여 용융 금속을 조각화합니다. 가스 원자화보다 비용 효율적이지만 구형 입자가 덜 생성됩니다. | 일부 금속(철, 구리) 및 일부 폴리머 | – 가스 분무화보다 비용이 저렴합니다. – 수분에 민감한 재료에 적합합니다. | – 낮은 분말 품질(불규칙한 모양) – 고성능 응용 분야에는 적합하지 않을 수 있습니다. |
플라즈마 원자화 | 전기 아크는 공급 원료(금속 와이어 또는 분말)를 용융 상태로 가열합니다. 그런 다음 용융된 금속은 노즐을 통해 배출되고 플라즈마 토치를 사용하여 원자화됩니다. | 광범위한 재료(금속, 합금, 세라믹) | – 고융점 재료 취급 가능 – 복합분말 제조에 적합 | – 복잡하고 비용이 많이 드는 프로세스 – 엄격한 안전 조치 필요 |
기계적 분쇄 | 벌크 재료를 미세한 분말로 분쇄하거나 분쇄하는 물리적 공정입니다. | 부서지기 쉬운 재료(세라믹, 일부 폴리머) | – 다른 방법에 비해 설치가 간단하고 비용이 저렴합니다. | – 입자 크기 및 형태에 대한 제한된 제어 – 분쇄 중 불순물이 유입될 수 있음 |
화학 기상 증착(CVD) | 기체 전구체가 반응하여 시드 입자에 고체 침전물을 형성하는 화학 공정입니다. | 금속, 세라믹 및 일부 고급 재료 | – 입자 구성에 대한 고순도 및 정밀한 제어 – 복잡한 형상 생성 가능 | – 제한된 생산 속도로 느린 공정 – 높은 자본 투자 |
전해 원자화 | 전해조는 금속 양극을 이온으로 분해하는 데 사용됩니다. 그런 다음 이온은 음극에서 전자와 결합하여 금속 입자를 형성합니다. | 금속 | – 환경 친화적인 공정(고온 방지) – 습기에 민감한 재료에 적합 | – 원자화 방식에 비해 생산 속도가 낮음 – 특정 전해질 및 음극 소재에 제한됨 |
구상화 | 다른 방법으로 생산된 불규칙한 형태의 분말의 형태를 개선하기 위해 사용되는 추가 공정입니다. 입자 응집을 구형으로 촉진하기 위해 열처리 또는 화학 공정이 포함됩니다. | 대부분의 분말 유형(금속, 폴리머, 세라믹) | – 분말 흐름성 및 패킹 밀도 향상 – 인쇄성 향상 | – 추가 처리 단계를 추가합니다. – 모든 애플리케이션에 필요하지 않을 수도 있습니다. |
속성 3D 프린팅 파우더
속성 | 설명 | 3D 프린팅의 중요성 | 예시 및 고려사항 |
---|---|---|---|
입자 크기 및 분포 | 개별 분말 입자의 크기 변화와 다양한 크기 범위에 걸친 전체 확산을 나타냅니다. 마이크로미터(μm) 단위로 측정됩니다. | 인쇄 적성, 해상도 및 최종 부품 밀도에서 중요한 역할을 합니다. – 너무 큰: 유동성 방해, 고르지 못한 퍼짐, 긁어 모으기 결함 가능성. – 너무 작은: 표면적이 증가하면 굳어지고 패킹이 불량해 강도에 영향을 줄 수 있습니다. | – SLS(선택적 레이저 소결): 일반적으로 세부적인 특징을 위해 더 미세한 분말(20-80 µm)을 선호합니다. – MJF(멀티 제트 퓨전): 흐름 제한을 극복할 수 있는 잉크젯 기술의 능력으로 인해 약간 더 큰 입자(50-100 µm)를 사용할 수 있습니다. – 금속 분말: 긴밀한 분포(좁은 범위)는 최종 부품의 우수한 패킹 밀도와 최소 다공성을 위해 이상적입니다. |
입자 형태학 | 개별 파우더 입자의 모양입니다. | 입자가 얼마나 잘 결합되는지, 유동성 및 최종 부품의 표면 마감에 영향을 미칩니다. – 구의: 최고의 패킹 밀도와 유동성을 제공하여 강력하고 균일한 부품을 생산합니다. – 불규칙한 모양: 틈과 불일치가 생겨 잠재적으로 강도와 표면 품질에 영향을 미칠 수 있습니다. | – 플라스틱 분말: 일반적으로 최적의 인쇄 가능성을 위해 구형 또는 거의 구형입니다. – 금속 분말: 금속재질 및 제작방식에 따라 달라질 수 있습니다. 구형 형태가 선호되지만 원자화와 같은 후처리 기술을 통해 달성될 수도 있습니다. |
유동성 | 자체 중량 또는 최소한의 전단력으로 분말이 쉽게 흐를 수 있습니다. | 인쇄 중 일관된 재료 증착과 균일한 레이어 형성에 중요합니다. – 흐름성이 좋습니다: 원활한 퍼짐을 보장하고 레이어 결함 위험을 최소화합니다. – 낮은 유동성: 고르지 않은 증착, 불일치 및 잠재적인 인쇄 문제가 발생할 수 있습니다. | – 입자 크기 분포가 좁은 분말 입자 크기 간섭이 적어 흐름이 더 좋아지는 경향이 있습니다. – 첨가제 및 표면 처리 입자 사이의 마찰을 줄여 유동성을 향상시키는 데 사용할 수 있습니다. |
포장 밀도 | 분말 입자가 얼마나 촘촘하게 쌓일 수 있는지를 나타내는 척도입니다. 분말이 차지하는 전체 부피에 대한 백분율로 표시됩니다. | 인쇄된 부품의 최종 밀도, 강도 및 치수 정확도에 영향을 미칩니다. – 높은 포장 밀도: 향상된 기계적 특성과 치수 정밀도로 밀도가 높은 부품을 만들 수 있습니다. – 낮은 패킹 밀도: 다공성이 높고 잠재적으로 약하며 치수 정확도가 낮은 부품이 생성됩니다. | – 파티클 모양 중요한 역할을 합니다. 구형 입자는 불규칙한 모양보다 더 효율적으로 포장됩니다. – 바인더 제팅과 같은 프로세스 적절한 바인더 침투를 허용하기 위해 약간 낮은 포장 밀도로 이점을 얻을 수 있습니다. |
소결성 | 3D 프린팅 프로세스 중에 일반적으로 열이나 레이저 에너지를 통해 분말 입자가 융합되거나 결합되는 능력입니다. | 강력하고 기능적인 인쇄 부품을 만드는 데 필수적입니다. – 좋은 소결성: 강력한 입자 간 결합을 가능하게 하여 견고하고 기능적인 부품을 만듭니다. – 불량한 소결성: 응력이 가해지면 접착력이 약해지고 부품 고장이 발생할 수 있습니다. | – 재료 구성: 금속은 일반적으로 고온에서 강한 결합을 형성하는 고유한 능력으로 인해 우수한 소결성을 갖습니다. – 폴리머 파우더 접착력을 강화하기 위해 특정 첨가제나 후처리 단계(예: 소결 오븐)가 필요한 경우가 많습니다. |
화학 성분 | 분말 재료의 원소 구성. | 강도, 내열성, 생체 적합성과 같은 인쇄된 부품의 최종 특성을 결정합니다. – 재료 선택 원하는 응용 프로그램 및 기능 요구 사항에 따라 중요합니다. – 가루를 섞어서 사용 가능 특정 특성을 달성하기 위해(예: 강도 대 중량 비율을 개선하기 위해 금속을 결합함) | – 금속 분말 티타늄과 같은 순수 금속부터 맞춤형 특성을 지닌 복잡한 합금까지 다양합니다. – 폴리머 파우더 의료용 나일론, 폴리아미드 및 생체 적합성 재료가 포함될 수 있습니다. |
열 속성 | 융점, 열전도율, 열팽창 계수를 포함한 다양한 온도에서 분말 재료의 거동입니다. | 인쇄 및 후처리 중 치수 안정성, 뒤틀림, 열 변형과 같은 영향 요인. – 난방 제어 재료의 열 한계를 초과하여 부품 결함을 유발하는 것을 방지하는 데 필수적입니다. – 파우더와 빌드 플랫폼의 열적 특성 일치 뒤틀림을 최소화하고 치수 정확도를 보장합니다. | – 금속 분말 융점이 높은 경우가 많으며 SLM(Selective Laser Melting)과 같은 레이저 기반 공정 중에 정밀한 온도 제어가 필요합니다. – 폴리머 파우더 낮은 온도에서는 부드러워지거나 녹을 수 있습니다. |
3D 프린팅 파우더 사양
속성 | 설명 | 인쇄성 및 부품 품질에 미치는 영향 | 머티리얼 예제 |
---|---|---|---|
입자 크기 및 분포 | 개별 입자 직경과 분말 내 변화를 나타냅니다. 미크론(μm) 단위로 측정됩니다. | 미세 분말(< 50 µm)은 높은 분리능과 표면 마감을 제공하지만 흐름이 어렵고 특별한 취급이 필요할 수 있습니다. 더 거친 분말(> 100 µm)은 유동성을 향상시키지만 세부 묘사가 제한되고 표면 거칠기가 증가할 수 있습니다. 좁은 크기 분포는 일관된 포장 및 인쇄 동작을 보장합니다. | 폴리머: 나일론(15~75μm), 폴리프로필렌(40~100μm) |
입자 형태학 | 개별 파우더 입자의 모양입니다. | 구형 입자는 자유롭게 흐르고 효율적으로 포장되어 인쇄성이 우수합니다. 불규칙한 모양은 입자 간 결합을 향상시킬 수 있지만 흐름 문제를 일으킬 수 있으며 특정 인쇄 기술이 필요할 수 있습니다. | 폴리머: 제조 공정으로 인해 일반적으로 구형입니다. |
겉보기 밀도 및 포장 밀도 | 겉보기 밀도는 느슨한 부어진 상태의 단위 부피당 분말의 중량입니다. 패킹 밀도는 태핑이나 진동 후에 달성할 수 있는 최대 밀도입니다. | 겉보기 밀도는 분말 흐름과 취급에 영향을 미칩니다. 패킹 밀도는 인쇄된 부품의 최종 밀도와 기계적 특성에 영향을 미칩니다. 일반적으로 패킹 밀도가 높을수록 부품이 더 강해집니다. | 폴리머: 겉보기 밀도(0.3~0.8g/cm3), 충전 밀도(0.5~0.9g/cm3) |
유동성 | 중력 또는 최소한의 교반으로 분말이 쉽게 흐를 수 있습니다. | 우수한 유동성은 인쇄 중 분말을 균일하게 퍼뜨리는 데 중요합니다. 유동성이 좋지 않으면 레이어 불일치 및 인쇄 결함이 발생할 수 있습니다. | 폴리머: 일반적으로 구형 형태로 인해 자유롭게 흐릅니다. 유동성을 향상시키기 위해 첨가제를 사용할 수 있습니다. |
수분 함량 | 분말 입자 내에 갇혀 있는 수증기의 양입니다. | 과도한 수분은 인쇄 중에 증기 폭발이나 일관되지 않은 용융 동작과 같은 문제를 일으킬 수 있습니다. 대부분의 분말에는 엄격한 수분 관리가 필요합니다. | 폴리머: 일반적으로 가수분해를 방지하고 일관된 인쇄 동작을 보장하기 위해 수분 함량이 매우 낮습니다(< 0.1wt%). |
화학 성분 및 순도 | 분말의 원소 구성 및 불순물의 존재 여부. | 화학 성분은 인쇄된 부품의 최종 특성을 결정합니다. 불순물은 인쇄성, 기계적 성능 및 표면 품질에 영향을 미칠 수 있습니다. | 폴리머: 일관된 특성과 인쇄성을 보장하기 위해 고순도 등급의 재료가 사용됩니다. |
열 속성 | 고분자의 녹는점, 유리전이온도(Tg) 및 열전도율. | 열적 특성은 인쇄 공정 매개변수와 인쇄된 부품의 최종 미세 구조에 영향을 미칩니다. | 폴리머: 녹는점과 Tg는 레이저 출력이나 베드 온도와 같은 인쇄 매개변수를 설정하는 데 중요합니다. |
3D 프린팅 파우더 공급업체
재질 | 주요 애플리케이션 | 대표 공급업체 | 고려 사항 |
---|---|---|---|
폴리머 파우더 | – 프로토타이핑 – 기능성 부품 – 의료 기기 – 소비재 | * 폴리아미드(나일론): BASF, 에보닉, 아르케마 * 폴리락트산(PLA): 네이처웍스(NatureWorks), 엑슨모빌 케미컬(ExxonMobil Chemical), 듀폰(DuPont) * 폴리프로필렌(PP): 로얄 DSM, SABIC, 렙솔 | * 입자 크기 및 분포는 인쇄 가능성 및 최종 부품 특성에 영향을 미칩니다. * 내열성, 유연성, 생체 적합성과 같은 재료 특성은 다양합니다. * 후처리 기술과 화학적 호환성을 고려하십시오. |
금속 분말 | – 항공우주 부품 – 자동차 부품 – 의료용 임플란트 – 도구 및 다이 | * 티타늄 합금: AP Powder Company, Höganäs, GE Additive * 스테인리스 스틸: 목수 적층 제조, SLM 솔루션, EOS GmbH * 알루미늄 합금: Rio Tinto Alcan, DLP 제조, Exone | * 분말의 형태(형상)는 유동성과 충전밀도에 영향을 미칩니다. * 입자 크기는 최종 부품의 기계적 특성에 영향을 미칩니다. * 반응성 금속 분말을 취급할 때는 안전 프로토콜이 중요합니다. |
복합 분말 | – 고강도 경량 구조 – 전도성 부품 – 향상된 특성을 지닌 생체 적합성 임플란트 | * 고분자-금속 복합재: LPW 기술, Markforged, 데스크탑 금속 * 세라믹-금속 복합재: Sandvik Hyperion, Extrude Hone, 플라즈마 기술 * 고분자-탄소 섬유 복합재: Stratasys, 데스크탑 메탈, 헨켈 | * 선택은 원하는 특성(강도, 전도성, 생체적합성)의 조합에 따라 달라집니다. * 서로 다른 재료 간의 인터페이스는 최적의 성능을 위해 세심한 고려가 필요합니다. * 단일 재료 파우더에 비해 프린팅 매개변수는 조정이 필요할 수 있습니다. |
응용 3D 프린팅 파우더
프린팅 파우더는 산업 전반에 걸쳐 복잡한 맞춤형 부품 형상을 제작할 수 있는 독보적인 제품입니다:
산업 | 컴포넌트 예시 | 혜택 |
---|---|---|
항공우주 | 터빈 블레이드, 로켓 노즐, 무인 항공기 섀시 | 무게 감소, 성능 향상 |
의료 | 환자 맞춤형 임플란트, 보철물 | 맞춤형 사이징, 생체 적합성 |
자동차 | 열교환기, 경량 섀시 요소 | 부품 통합, 효율성 |
산업 | 맞춤형 생산 툴링, 지그 | 개발 일정 단축 |
표 5: 3D 프린팅 파우더 기능을 활용하는 주요 사용 사례 분야
설계를 빠르게 반복하고 단납기를 경제적으로 인쇄할 수 있어 최종 사용 부품의 혁신을 실현할 수 있습니다.
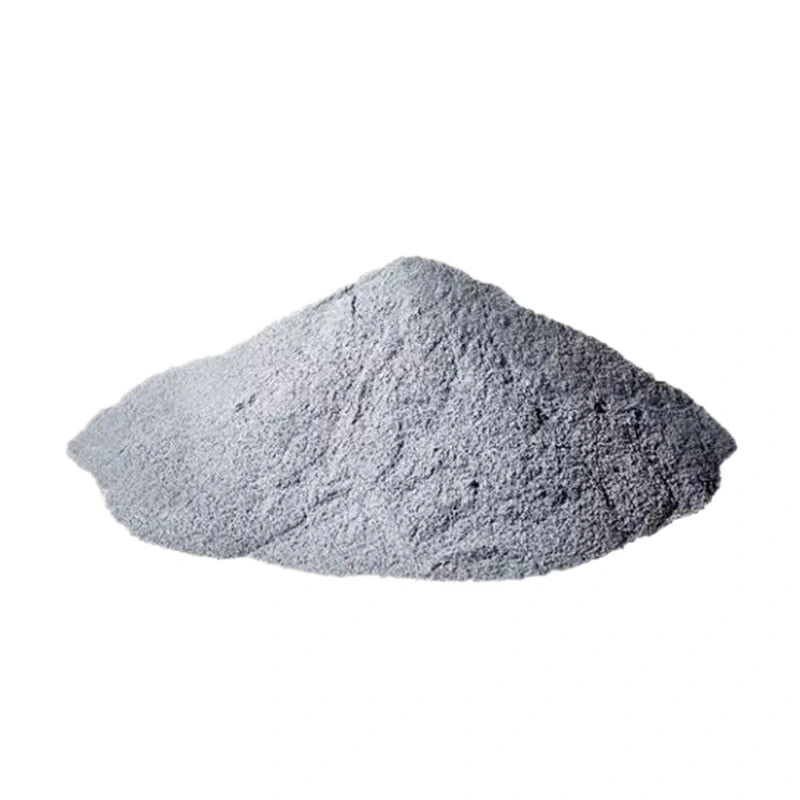
분말 기반 3D 프린팅의 장단점
장점 | 단점 |
---|---|
높은 정확도와 분해능 | 분말 취급 및 안전 |
다양한 재료 | 제한된 빌드 크기 |
최소한의 지원 구조 | 후처리 요구 사항 |
빠른 생산 속도 | 높은 초기 투자 비용 |
자주 묻는 질문
Q: 금속 3D 프린팅 파우더에 가장 적합한 입자 크기 범위는 무엇인가요?
A: 10~45미크론은 분말 취급 시 초미세 분말의 문제를 피하면서 포장과 확산이 용이합니다. 대부분의 합금은 30±15μm 분포에서 우수한 성능을 발휘합니다.
Q: 어떤 폴리머 파우더 3D 프린팅 공정이 최고의 기계적 성능을 제공하나요?
A: 선택적 레이저 소결(SLS)을 사용하면 탁월한 융착 및 미세 피처 생산이 가능하므로 사출 성형 공정에 필적하거나 그 이상의 고성능 플라스틱 부품을 제작할 수 있습니다.
Q: 사용하지 않은 3D 프린팅 파우더는 얼마나 오래 보관할 수 있나요?
A: 서늘하고 건조한 환경에서 습기로부터 건조제로 밀봉하여 보관하면 파우더는 최소 12개월 동안 흐름 특성을 유지합니다. 개봉한 분말도 눈에 띄는 성능 저하가 나타나기 전까지 6개월 이상 지속됩니다.
Q: 스타팅 파우더의 품질이 프린트된 부품의 특성에 큰 영향을 미치나요?
A: 예, 파우더 화학 순도와 파우더 특성의 적절한 제어는 최종 부품의 기계적 특성, 미관, 치수 정확도 및 성능 신뢰성을 크게 결정합니다.
공유
중국 칭다오에 본사를 둔 선도적인 적층 제조 솔루션 제공업체인 MET3DP Technology Co. 당사는 산업용 3D 프린팅 장비와 고성능 금속 분말을 전문으로 합니다.
관련 기사
Met3DP 소개
최근 업데이트
제품
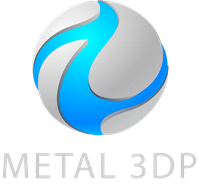
3D 프린팅 및 적층 제조용 금속 분말
문의 정보
- 칭다오시, 산둥성, 중국
- [email protected]
- [email protected]
- +86 19116340731