3D Printing Powders
Table of Contents
3D printing, also known as additive manufacturing (AM), utilizes specialized powders to construct three-dimensional components in successive layering methods. This guide serves an in-depth reference on powders for 3D printing – exploring types, traits, specifications, manufacturing methods, key suppliers & pricing, applications across industries, comparisons to alternatives, FAQs and more.
Overview of 3D Printing Powders
3D printing powders are raw material feedstocks enabling additive part fabrication across plastic, metal and ceramic platforms. Key traits:
- State: Ultrafine particulate powders
- Size range: Typically 10-150 microns
- Morphology: Most often spherical particle shape
- Composition: Polymer, metal alloy, ceramic, sandstone blends
- Key properties: Engineered particle size distribution, flowability, pack density and microstructure
By leveraging tight control of powder physical properties and interactions with thermal/kinetic printing processes, 3D printing powders facilitate intricate part geometries and material compositional gradients not achievable otherwise.
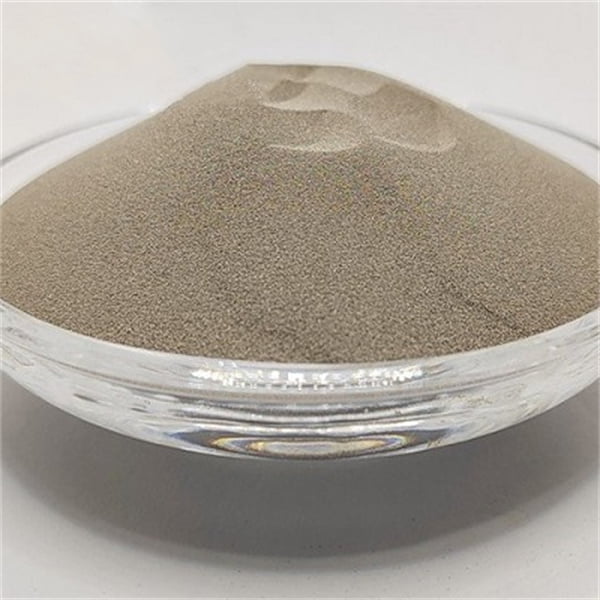
Types of 3D Printing Powders
Category | Materials | Printing Method |
---|---|---|
Plastics | Nylons, ABS, TPU, PEKK, PEEK… | Selective laser sintering (SLS) |
Metals | Stainless, tool steels, titanium & alloys, superalloys… | Direct metal laser sintering (DMLS) |
Ceramics | Alumina, zirconia, silicon carbide | Binder jetting, fused deposition modeling |
Composites | Metal/plastic blends, sandstone mixes | Multi jet fusion (MJF), bound metal deposition |
Bio-compatible | PEEK, PLGA, TCP… | Selective laser melting (SLM) |
Table 1: Major categories, materials and associated printing platforms for commercial 3D printing powders
Polymer, metal, ceramic and composite powders support production of end-use parts across aerospace, automotive, medical, dental and industrial markets.
Manufacturing Methods
Method | Description | Material Suitability | Advantages | Disadvantages |
---|---|---|---|---|
Atomization | This umbrella term encompasses various techniques that break down molten metal into fine particles. The molten metal is forced through a nozzle into a high-pressure gas or water stream, rapidly solidifying the droplets into spherical particles. | Metals (Iron, Aluminum, Titanium Alloys) | – High production rate – Consistent particle size and shape – Good powder flowability | – Requires high energy input – Potential for oxide formation on particles – Limited to certain materials |
Gas Atomization | The most common atomization method, using an inert gas (typically nitrogen) to break up the molten metal. | Similar to Atomization, but generally better surface quality and tighter control over particle size. | – Superior powder quality compared to other atomization methods – Suitable for reactive metals | Similar to Atomization, but higher equipment cost |
Water Atomization | Utilizes a high-pressure water jet to fragment the molten metal. More cost-effective than gas atomization but produces less spherical particles. | Some metals (Iron, Copper) and some polymers | – Lower cost than gas atomization – Well-suited for moisture-insensitive materials | – Lower powder quality (irregular shapes) – May not be ideal for high-performance applications |
Plasma Atomization | An electric arc heats the feedstock material (metal wire or powder) to a molten state. The molten metal is then ejected through a nozzle and atomized using a plasma torch. | Wide range of materials (metals, alloys, ceramics) | – Can handle high melting point materials – Suitable for creating composite powders | – Complex and high-cost process – Requires stringent safety measures |
Mechanical Pulverization | A physical process that grinds or mills bulk material into fine powder. | Brittle materials (ceramics, some polymers) | – Simpler and lower-cost setup compared to other methods | – Limited control over particle size and morphology – May introduce impurities during grinding |
Chemical Vapor Deposition (CVD) | A chemical process where gaseous precursors react to form a solid deposit on a seed particle. | Metals, ceramics, and some advanced materials | – High purity and precise control over particle composition – Can create complex geometries | – Slow process with limited production rate – High capital investment |
Electrolytic Atomization | An electrolytic cell is used to decompose a metal anode into ions. The ions then combine with electrons at the cathode to form metal particles. | Metals | – Environmentally friendly process (avoids high temperatures) – Suitable for moisture-sensitive materials | – Lower production rate than atomization methods – Limited to certain electrolytes and anode materials |
Spheroidization | An additional process used to improve the shape of irregularly shaped powders produced by other methods. Involves heat treatment or chemical processes to encourage particle agglomeration into spheres. | Most powder types (metals, polymers, ceramics) | – Enhances powder flowability and packing density – Improves printability | – Adds an extra processing step – May not be necessary for all applications |
Properties of 3D Printing Powders
Property | Description | Importance for 3D Printing | Examples & Considerations |
---|---|---|---|
Particle Size & Distribution | Refers to the variation in size of individual powder particles and the overall spread across different size ranges. Measured in micrometers (µm). | Plays a crucial role in printability, resolution, and final part density. – Too large: hindered flowability, uneven spreading, and potential for raking defects. – Too small: increased surface area can lead to caking and poor packing, affecting strength. | – SLS (Selective Laser Sintering): Generally prefers finer powders (20-80 µm) for detailed features. – MJF (Multi Jet Fusion): Slightly larger particles (50-100 µm) can be used due to inkjet technology’s ability to overcome flow limitations. – Metal powders: Tight distribution (narrow range) is ideal for good packing density and minimal porosity in the final part. |
Particle Morphology | The shape of individual powder particles. | Impacts how well particles pack together, flowability, and surface finish of the final part. – Spherical: Offer the best packing density and flowability, leading to strong and uniform parts. – Irregular shapes: Can create gaps and inconsistencies, potentially affecting strength and surface quality. | – Plastic powders: Generally spherical or near-spherical for optimal printability. – Metal powders: Can vary depending on the metal and production method. Spherical morphologies are preferred but may be achieved through post-processing techniques like atomization. |
Flowability | The ease with which powder flows under its own weight or with minimal shear force. | Critical for consistent material deposition and even layer formation during printing. – Good flowability: Ensures smooth spreading and minimizes the risk of layer defects. – Poor flowability: Can lead to uneven deposition, inconsistencies, and potential printing issues. | – Powders with a narrow particle size distribution tend to flow better due to less particle size interference. – Additives and surface treatments can be used to improve flowability by reducing friction between particles. |
Packing Density | The measure of how tightly powder particles can be packed together. Expressed as a percentage of the total volume occupied by the powder. | Affects the final density, strength, and dimensional accuracy of the printed part. – High packing density: Leads to denser parts with improved mechanical properties and dimensional precision. – Low packing density: Results in parts with higher porosity, potentially weaker and less dimensionally accurate. | – Particle shape plays a significant role. Spherical particles pack more efficiently than irregular shapes. – Processes like Binder Jetting can benefit from slightly lower packing densities to allow for proper binder infiltration. |
Sinterability | The ability of powder particles to fuse or bond together during the 3D printing process, typically through heat or laser energy. | Essential for achieving strong and functional printed parts. – Good sinterability: Enables strong inter-particle bonding, leading to robust and functional parts. – Poor sinterability: May result in weak bonds and potential part failure under stress. | – Material composition: Metals generally have good sinterability due to their inherent ability to form strong bonds at high temperatures. – Polymer powders often require specific additives or post-processing steps (e.g., sintering ovens) to enhance bonding. |
Chemical Composition | The elemental makeup of the powder material. | Determines the final properties of the printed part, such as strength, heat resistance, and biocompatibility. – Material selection is crucial based on the desired application and functional requirements. – Powders can be blended to achieve specific properties (e.g., combining metals for improved strength-to-weight ratio). | – Metal powders can range from pure metals like titanium to complex alloys with tailored properties. – Polymer powders can include nylons, polyamides, and biocompatible materials for medical applications. |
Thermal Properties | The behavior of the powder material under varying temperatures, including melting point, thermal conductivity, and coefficient of thermal expansion. | Impact factors like dimensional stability, warping, and heat distortion during printing and post-processing. – Controlled heating is essential to avoid exceeding the material’s thermal limits and causing part defects. – Matching thermal properties of powder and build platform minimizes warping and ensures dimensional accuracy. | – Metal powders often have high melting points and require precise temperature control during laser-based processes like SLM (Selective Laser Melting). – Polymer powders may soften or melt at lower temperatures, |
3D Printing Powder Specifications
Property | Description | Impact on Printability & Part Quality | Material Examples |
---|---|---|---|
Particle Size & Distribution | Refers to the individual particle diameters and the variation within the powder. Measured in microns (µm). | Fine powders (< 50 µm) offer high resolution and surface finish but can be challenging to flow and may require special handling. Coarser powders (> 100 µm) improve flowability but can limit detail and increase surface roughness. A narrow size distribution ensures consistent packing and printing behavior. | Polymers: Nylon (15-75 µm), Polypropylene (40-100 µm) |
Particle Morphology | The shape of individual powder particles. | Spherical particles flow freely and pack efficiently, leading to good printability. Irregular shapes can improve inter-particle bonding but may cause flow issues and require specific printing techniques. | Polymers: Typically spherical due to manufacturing processes. |
Apparent Density & Packing Density | Apparent density is the weight of powder per unit volume in its loose, poured state. Packing density is the maximum density achievable after tapping or vibration. | Apparent density affects powder flow and handling. Packing density influences the final density of the printed part and its mechanical properties. Higher packing density generally leads to stronger parts. | Polymers: Apparent density (0.3-0.8 g/cm³), Packing density (0.5-0.9 g/cm³) |
Flowability | The ease with which powder flows under gravity or with minimal agitation. | Good flowability is crucial for uniform powder spreading during printing. Poor flowability can lead to layer inconsistencies and printing defects. | Polymers: Typically free-flowing due to their spherical morphology. Additives can be used to improve flowability. |
Moisture Content | The amount of water vapor trapped within the powder particles. | Excess moisture can cause issues during printing, such as steam explosions or inconsistent melting behavior. Most powders require strict moisture control. | Polymers: Typically very low moisture content (< 0.1 wt%) to prevent hydrolysis and ensure consistent printing behavior. |
Chemical Composition & Purity | The elemental makeup of the powder and the presence of any impurities. | The chemical composition determines the final properties of the printed part. Impurities can affect printability, mechanical performance, and surface quality. | Polymers: High purity grade material is used to ensure consistent properties and printability. |
Thermal Properties | Melting point, glass transition temperature (Tg) for polymers, and thermal conductivity. | Thermal properties influence the printing process parameters and the final microstructure of the printed part. | Polymers: Melting point and Tg are crucial for setting printing parameters like laser power or bed temperature. |
3D Printing Powder Suppliers
Material | Key Applications | Representative Suppliers | Considerations |
---|---|---|---|
Polymer Powders | – Prototyping – Functional parts – Medical devices – Consumer goods | * Polyamide (Nylon): BASF, Evonik, Arkema * Polylactic Acid (PLA): NatureWorks, ExxonMobil Chemical, DuPont * Polypropylene (PP): Royal DSM, SABIC, Repsol | * Particle size and distribution impact printability and final part properties. * Material properties like heat resistance, flexibility, and biocompatibility vary. * Consider chemical compatibility with post-processing techniques. |
Metal Powders | – Aerospace components – Automotive parts – Medical implants – Tools and dies | * Titanium Alloys: AP Powder Company, Höganäs, GE Additive * Stainless Steel: Carpenter Additive Manufacturing, SLM Solutions, EOS GmbH * Aluminum Alloys: Rio Tinto Alcan, DLP Manufacturing, Exone | * Powder morphology (shape) affects flowability and packing density. * Grain size influences mechanical properties of the final part. * Safety protocols are crucial when handling reactive metal powders. |
Composite Powders | – Lightweight structures with high strength – Conductive components – Biocompatible implants with enhanced properties | * Polymer-Metal Composites: LPW Technology, Markforged, Desktop Metal * Ceramic-Metal Composites: Sandvik Hyperion, Extrude Hone, Plasma Technik * Polymer-Carbon Fiber Composites: Stratasys, Desktop Metal, Henkel | * Selection depends on the desired combination of properties (strength, conductivity, biocompatibility). * Interface between different materials requires careful consideration for optimal performance. * Printing parameters may need adjustment compared to single-material powders. |
Applications of 3D Printing Powders
Printing powders uniquely facilitate complex, customized part geometries across industries:
Industry | Example Components | Benefits |
---|---|---|
Aerospace | Turbine blades, rocket nozzles, UAV chassis | Weight reduction, performance gains |
Medical | Patient-matched implants, prosthetics | Personalized sizing, bio-compatibility |
Automotive | Heat exchangers, lightweight chassis elements | Parts consolidation, efficiency |
Industrial | Custom production tooling, jigs | Shortened development timelines |
Table 5: Major use case sectors taking advantage of 3D printing powder capabilities
The ability to rapidly iterate designs and print short runs economically enables end-use part innovation.
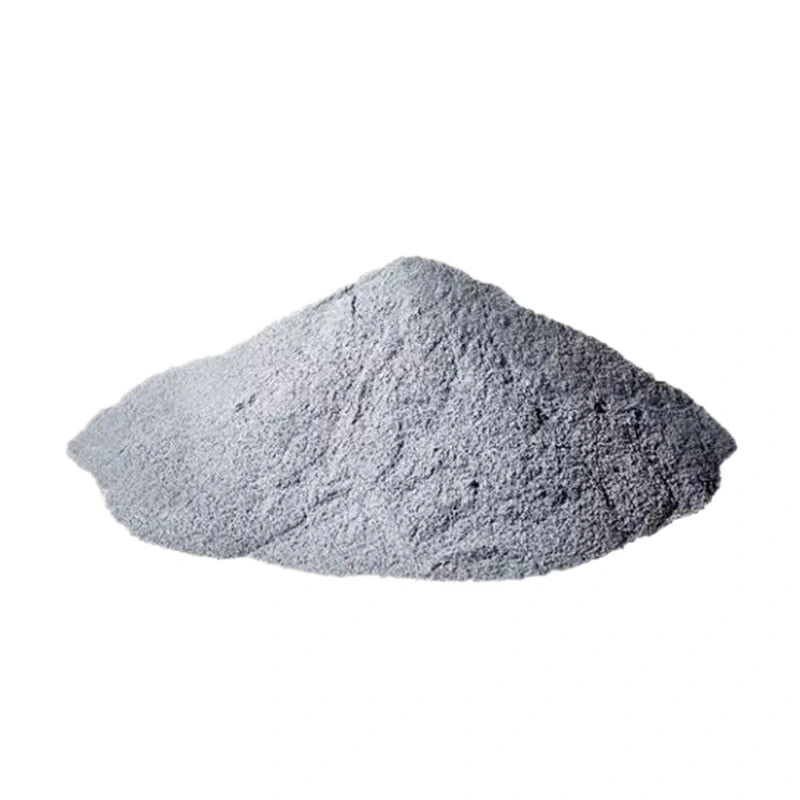
Pros and Cons of Powder-Based 3D Printing
Pros | Cons |
---|---|
High Accuracy and Resolution | Powder Handling and Safety |
Wide Range of Materials | Limited Build Size |
Minimal Support Structures | Post-Processing Requirements |
Fast Production Rates | High Initial Investment |
FAQs
Q: What particle size range works best for metal 3D printing powders?
A: 10-45 microns facilitates good packing and spreading while avoiding challenges with ultrafine powders around powder handling. Most alloys perform well 30±15μm distribution.
Q: Which polymer powder 3D printing process offers the best mechanical performance?
A: Selective laser sintering (SLS) allows excellent fusion and fine feature production – creating high performing plastic parts rivaling or exceeding injection molding processes.
Q: How long can unused 3D printing powder last in storage?
A: Kept sealed with desiccant from moisture in a cool, dry environment – powders maintain flow characteristics at least 12 months. Even opened powders last 6+ months before notable degradation.
Q: Does the quality of starting powder significantly influence printed part properties?
A: Yes, powder chemistry purity plus adequate control of powder characteristics strongly determine final part mechanical properties, aesthetics, dimensional accuracy and performance reliability.
Share On
MET3DP Technology Co., LTD is a leading provider of additive manufacturing solutions headquartered in Qingdao, China. Our company specializes in 3D printing equipment and high-performance metal powders for industrial applications.
Inquiry to get best price and customized Solution for your business!
Related Articles
About Met3DP
Recent Update
Our Product
CONTACT US
Any questions? Send us message now! We’ll serve your request with a whole team after receiving your message.
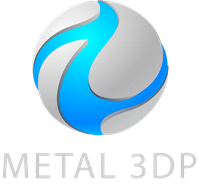
Metal Powders for 3D Printing and Additive Manufacturing
COMPANY
PRODUCT
cONTACT INFO
- Qingdao City, Shandong, China
- [email protected]
- [email protected]
- +86 19116340731