Proszki do druku 3D
Spis treści
Druk 3D, znany również jako produkcja addytywna (AM), wykorzystuje specjalistyczne proszki do konstruowania trójwymiarowych komponentów w kolejnych metodach warstwowych. Niniejszy przewodnik stanowi dogłębne źródło informacji na temat proszków do druku 3D - badając rodzaje, cechy, specyfikacje, metody produkcji, kluczowych dostawców i ceny, zastosowania w różnych branżach, porównania z alternatywami, często zadawane pytania i nie tylko.
Przegląd Proszki do druku 3D
Proszki do druku 3D są surowcami umożliwiającymi wytwarzanie części z tworzyw sztucznych, metalu i ceramiki. Kluczowe cechy:
- Stan: Proszki o ultradrobnych cząstkach
- Zakres rozmiarów: Zazwyczaj 10-150 mikronów
- Morfologia: Najczęściej kulisty kształt cząstek
- Skład: Polimer, stop metali, ceramika, mieszanki piaskowca
- Kluczowe właściwości: Zaprojektowany rozkład wielkości cząstek, płynność, gęstość upakowania i mikrostruktura
Wykorzystując ścisłą kontrolę nad właściwościami fizycznymi proszku i interakcjami z termicznymi/kinetycznymi procesami drukowania, proszki do druku 3D ułatwiają skomplikowane geometrie części i gradienty składu materiału, których nie można osiągnąć w inny sposób.
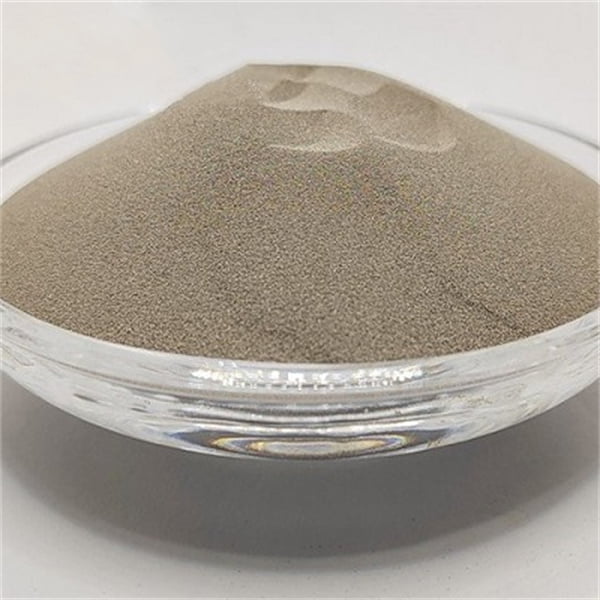
Rodzaje proszków do druku 3D
Kategoria | Materiały | Metoda drukowania |
---|---|---|
Tworzywa sztuczne | Nylony, ABS, TPU, PEKK, PEEK... | Selektywne spiekanie laserowe (SLS) |
Metale | Stale nierdzewne, narzędziowe, tytan i stopy, nadstopy... | Bezpośrednie spiekanie laserowe metali (DMLS) |
Ceramika | Tlenek glinu, tlenek cyrkonu, węglik krzemu | Strumieniowanie spoiwa, modelowanie osadzania topionego |
Kompozyty | Mieszanki metal/plastik, mieszanki piaskowca | Fuzja wielostrumieniowa (MJF), osadzanie związanego metalu |
Biokompatybilność | PEEK, PLGA, TCP... | Selektywne topienie laserowe (SLM) |
Tabela 1: Główne kategorie, materiały i powiązane platformy drukowania dla komercyjnych proszków do druku 3D
Proszki polimerowe, metalowe, ceramiczne i kompozytowe wspierają produkcję części do zastosowań końcowych w przemyśle lotniczym, motoryzacyjnym, medycznym, dentystycznym i przemysłowym.
Metody produkcji
Metoda | Opis | Przydatność materiału | Zalety | Wady |
---|---|---|---|---|
Atomizacja | Ten ogólny termin obejmuje różne techniki rozbijania stopionego metalu na drobne cząstki. Stopiony metal jest wtłaczany przez dyszę do strumienia gazu lub wody pod wysokim ciśnieniem, szybko zestalając kropelki w kuliste cząstki. | Metale (żelazo, aluminium, stopy tytanu) | - Wysoka wydajność produkcji - Stały rozmiar i kształt cząstek - Dobra sypkość proszku | - Wymaga dużego nakładu energii - Potencjalne tworzenie się tlenków na cząstkach - Ograniczone do niektórych materiałów |
Atomizacja gazu | Najpopularniejsza metoda atomizacji, wykorzystująca gaz obojętny (zazwyczaj azot) do rozbijania stopionego metalu. | Podobne do atomizacji, ale generalnie lepsza jakość powierzchni i ściślejsza kontrola nad rozmiarem cząstek. | - Najwyższa jakość proszku w porównaniu z innymi metodami atomizacji - Odpowiedni do metali reaktywnych | Podobny do atomizacji, ale wyższy koszt sprzętu |
Atomizacja wody | Wykorzystuje strumień wody pod wysokim ciśnieniem do rozdrobnienia stopionego metalu. Bardziej opłacalna niż atomizacja gazowa, ale wytwarza mniej kulistych cząstek. | Niektóre metale (żelazo, miedź) i niektóre polimery | - Niższy koszt niż w przypadku atomizacji gazowej - Dobrze nadaje się do materiałów niewrażliwych na wilgoć | - Niższa jakość proszku (nieregularne kształty) - Może nie być idealny do zastosowań wymagających wysokiej wydajności |
Atomizacja plazmowa | Łuk elektryczny podgrzewa materiał wsadowy (drut metalowy lub proszek) do stanu stopionego. Stopiony metal jest następnie wyrzucany przez dyszę i rozpylany za pomocą palnika plazmowego. | Szeroki zakres materiałów (metale, stopy, ceramika) | - Może obsługiwać materiały o wysokiej temperaturze topnienia - Nadaje się do tworzenia proszków kompozytowych | - Złożony i kosztowny proces - Wymaga rygorystycznych środków bezpieczeństwa |
Rozdrabnianie mechaniczne | Proces fizyczny polegający na rozdrabnianiu lub mieleniu materiału sypkiego na drobny proszek. | Kruche materiały (ceramika, niektóre polimery) | - Prostsza i tańsza konfiguracja w porównaniu z innymi metodami | - Ograniczona kontrola nad rozmiarem i morfologią cząstek - Może wprowadzać zanieczyszczenia podczas mielenia |
Chemiczne osadzanie z fazy gazowej (CVD) | Proces chemiczny, w którym gazowe prekursory reagują, tworząc stały osad na cząsteczce zalążkowej. | Metale, ceramika i niektóre zaawansowane materiały | - Wysoka czystość i precyzyjna kontrola nad składem cząstek - Możliwość tworzenia złożonych geometrii | - Powolny proces z ograniczonym tempem produkcji - Wysokie inwestycje kapitałowe |
Atomizacja elektrolityczna | Ogniwo elektrolityczne służy do rozkładu metalowej anody na jony. Jony łączą się następnie z elektronami na katodzie, tworząc cząsteczki metalu. | Metale | - Proces przyjazny dla środowiska (unika wysokich temperatur) - Odpowiedni dla materiałów wrażliwych na wilgoć | - Niższy wskaźnik produkcji niż w przypadku metod atomizacji - Ograniczony do niektórych elektrolitów i materiałów anodowych |
Sferoidyzacja | Dodatkowy proces stosowany w celu poprawy kształtu proszków o nieregularnych kształtach wytwarzanych innymi metodami. Obejmuje obróbkę cieplną lub procesy chemiczne sprzyjające aglomeracji cząstek w kule. | Większość rodzajów proszków (metale, polimery, ceramika) | - Zwiększa płynność proszku i gęstość upakowania - Poprawia drukowalność | - Dodaje dodatkowy etap przetwarzania - może nie być konieczny w przypadku wszystkich aplikacji. |
Właściwości Proszki do druku 3D
Nieruchomość | Opis | Znaczenie dla druku 3D | Przykłady i rozważania |
---|---|---|---|
Rozmiar i rozkład cząstek | Odnosi się do zmienności wielkości poszczególnych cząstek proszku i ogólnego rozrzutu w różnych zakresach wielkości. Mierzone w mikrometrach (µm). | Odgrywa kluczową rolę w możliwości drukowania, rozdzielczości i końcowej gęstości części. – Zbyt duży: utrudniona płynność, nierównomierne rozprowadzanie i potencjalne wady zgrabiania. – Za mały: Zwiększona powierzchnia może prowadzić do zbrylania i słabego upakowania, wpływając na wytrzymałość. | – SLS (selektywne spiekanie laserowe): Generalnie preferuje drobniejsze proszki (20-80 µm) w celu uzyskania szczegółowych cech. – MJF (Multi Jet Fusion): Nieco większe cząstki (50-100 µm) mogą być stosowane ze względu na zdolność technologii atramentowej do pokonywania ograniczeń przepływu. – Proszki metali: Ścisła dystrybucja (wąski zakres) jest idealna dla dobrej gęstości upakowania i minimalnej porowatości w części końcowej. |
Morfologia cząsteczek | Kształt poszczególnych cząstek proszku. | Wpływa na stopień upakowania cząstek, płynność i wykończenie powierzchni końcowej części. - Sferyczny: Oferują najlepszą gęstość upakowania i płynność, prowadząc do mocnych i jednolitych części. - Nieregularne kształty: Może tworzyć luki i niespójności, potencjalnie wpływając na wytrzymałość i jakość powierzchni. | – Proszki z tworzyw sztucznych: Ogólnie sferyczny lub prawie sferyczny dla optymalnej drukowności. - Proszki metali: Może się różnić w zależności od metalu i metody produkcji. Preferowane są morfologie sferyczne, ale można je osiągnąć za pomocą technik przetwarzania końcowego, takich jak atomizacja. |
Płynność | Łatwość, z jaką proszek przepływa pod własnym ciężarem lub przy minimalnej sile ścinającej. | Krytyczne dla spójnego osadzania materiału i równomiernego tworzenia warstw podczas drukowania. - Dobra płynność: Zapewnia płynne rozprowadzanie i minimalizuje ryzyko wad warstwy. - Słaba płynność: Może prowadzić do nierównomiernego osadzania, niespójności i potencjalnych problemów z drukowaniem. | – Proszki o wąskim rozkładzie wielkości cząstek mają tendencję do lepszego przepływu ze względu na mniejsze zakłócenia wielkości cząstek. - Dodatki i obróbka powierzchni może być stosowany w celu poprawy płynności poprzez zmniejszenie tarcia między cząstkami. |
Gęstość upakowania | Miara tego, jak ciasno można upakować cząstki proszku. Wyrażona jako procent całkowitej objętości zajmowanej przez proszek. | Wpływa na ostateczną gęstość, wytrzymałość i dokładność wymiarową drukowanej części. - Wysoka gęstość upakowania: Prowadzi do gęstszych części o lepszych właściwościach mechanicznych i precyzji wymiarowej. - Niska gęstość upakowania: Skutkuje to częściami o większej porowatości, potencjalnie słabszymi i mniej dokładnymi wymiarowo. | – Kształt cząsteczki odgrywa znaczącą rolę. Cząsteczki sferyczne pakują się bardziej efektywnie niż cząsteczki o nieregularnych kształtach. - Procesy takie jak Binder Jetting mogą korzystać z nieco niższych gęstości upakowania, aby umożliwić właściwą infiltrację spoiwa. |
Spiekalność | Zdolność cząstek proszku do łączenia się ze sobą podczas procesu drukowania 3D, zazwyczaj za pomocą ciepła lub energii laserowej. | Niezbędne do uzyskania wytrzymałych i funkcjonalnych części drukowanych. - Dobra spiekalność: Umożliwia silne wiązanie międzycząsteczkowe, prowadząc do uzyskania wytrzymałych i funkcjonalnych części. - Słaba spiekalność: Może powodować słabe wiązania i potencjalne uszkodzenie części pod wpływem naprężeń. | – Skład materiału: Metale generalnie mają dobrą spiekalność ze względu na ich naturalną zdolność do tworzenia silnych wiązań w wysokich temperaturach. - Proszki polimerowe często wymagają określonych dodatków lub etapów przetwarzania końcowego (np. pieców do spiekania) w celu zwiększenia wiązania. |
Skład chemiczny | Skład pierwiastkowy materiału proszkowego. | Określa ostateczne właściwości wydrukowanej części, takie jak wytrzymałość, odporność na ciepło i biokompatybilność. - Wybór materiału ma kluczowe znaczenie w oparciu o pożądaną aplikację i wymagania funkcjonalne. - Proszki mogą być mieszane w celu osiągnięcia określonych właściwości (np. łączenie metali w celu poprawy stosunku wytrzymałości do masy). | – Proszki metali Mogą to być zarówno czyste metale, takie jak tytan, jak i złożone stopy o dostosowanych właściwościach. - Proszki polimerowe mogą obejmować nylony, poliamidy i biokompatybilne materiały do zastosowań medycznych. |
Właściwości termiczne | Zachowanie materiału proszkowego w zmiennych temperaturach, w tym temperatura topnienia, przewodność cieplna i współczynnik rozszerzalności cieplnej. | Czynniki wpływające na stabilność wymiarową, wypaczenia i odkształcenia cieplne podczas drukowania i obróbki końcowej. - Kontrolowane ogrzewanie jest niezbędne, aby uniknąć przekroczenia limitów termicznych materiału i spowodowania wad części. - Dopasowanie właściwości termicznych proszku i platformy roboczej minimalizuje wypaczenia i zapewnia dokładność wymiarową. | – Proszki metali często mają wysoką temperaturę topnienia i wymagają precyzyjnej kontroli temperatury podczas procesów laserowych, takich jak SLM (selektywne topienie laserowe). - Proszki polimerowe może mięknąć lub topić się w niższych temperaturach, |
Specyfikacje proszku do druku 3D
Nieruchomość | Opis | Wpływ na drukowność i jakość części | Przykłady materiałów |
---|---|---|---|
Rozmiar i rozkład cząstek | Odnosi się do poszczególnych średnic cząstek i zmienności w obrębie proszku. Mierzone w mikronach (µm). | Drobne proszki ( 100 µm) poprawiają płynność, ale mogą ograniczać szczegóły i zwiększać chropowatość powierzchni. Wąski rozkład wielkości zapewnia spójne upakowanie i zachowanie podczas drukowania. | Polimery: Nylon (15-75 µm), polipropylen (40-100 µm) |
Morfologia cząsteczek | Kształt poszczególnych cząstek proszku. | Sferyczne cząstki przepływają swobodnie i pakują się wydajnie, co prowadzi do dobrej drukowalności. Nieregularne kształty mogą poprawić wiązanie międzycząsteczkowe, ale mogą powodować problemy z przepływem i wymagać specjalnych technik drukowania. | Polimery: Zazwyczaj kuliste ze względu na procesy produkcyjne. |
Gęstość pozorna i gęstość upakowania | Gęstość pozorna to masa proszku na jednostkę objętości w stanie sypkim. Gęstość upakowania to maksymalna gęstość osiągana po stuknięciu lub wibracji. | Gęstość pozorna wpływa na przepływ proszku i obsługę. Gęstość upakowania wpływa na końcową gęstość drukowanej części i jej właściwości mechaniczne. Wyższa gęstość upakowania generalnie prowadzi do mocniejszych części. | Polimery: Gęstość pozorna (0,3-0,8 g/cm³), gęstość upakowania (0,5-0,9 g/cm³) |
Płynność | Łatwość, z jaką proszek przepływa pod wpływem grawitacji lub przy minimalnym mieszaniu. | Dobra płynność ma kluczowe znaczenie dla równomiernego rozprowadzania proszku podczas drukowania. Słaba płynność może prowadzić do niespójności warstw i defektów druku. | Polimery: Ze względu na swoją kulistą morfologię są zazwyczaj sypkie. Dodatki mogą być stosowane w celu poprawy płynności. |
Zawartość wilgoci | Ilość pary wodnej uwięzionej w cząsteczkach proszku. | Nadmiar wilgoci może powodować problemy podczas drukowania, takie jak eksplozje pary lub niespójne zachowanie podczas topienia. Większość proszków wymaga ścisłej kontroli wilgotności. | Polimery: Zazwyczaj bardzo niska zawartość wilgoci (< 0,1 wt%), aby zapobiec hydrolizie i zapewnić spójne zachowanie druku. |
Skład chemiczny i czystość | Skład pierwiastkowy proszku i obecność wszelkich zanieczyszczeń. | Skład chemiczny określa ostateczne właściwości drukowanej części. Zanieczyszczenia mogą wpływać na drukowalność, wydajność mechaniczną i jakość powierzchni. | Polimery: Materiał o wysokiej czystości jest stosowany w celu zapewnienia stałych właściwości i możliwości drukowania. |
Właściwości termiczne | Temperatura topnienia, temperatura zeszklenia (Tg) dla polimerów i przewodność cieplna. | Właściwości termiczne wpływają na parametry procesu drukowania i ostateczną mikrostrukturę drukowanej części. | Polimery: Temperatura topnienia i Tg są kluczowe dla ustawienia parametrów drukowania, takich jak moc lasera lub temperatura stołu. |
Dostawcy proszków do druku 3D
Materiał | Kluczowe aplikacje | Reprezentatywni dostawcy | Rozważania |
---|---|---|---|
Proszki polimerowe | - Prototypowanie - Części funkcjonalne - Urządzenia medyczne - Towary konsumpcyjne | * Poliamid (nylon): BASF, Evonik, Arkema * Kwas polimlekowy (PLA): NatureWorks, ExxonMobil Chemical, DuPont * Polipropylen (PP): Royal DSM, SABIC, Repsol | * Rozmiar i rozkład cząstek wpływa na drukowalność i końcowe właściwości części. * Właściwości materiału, takie jak odporność na ciepło, elastyczność i biokompatybilność są różne. * Rozważ zgodność chemiczną z technikami przetwarzania końcowego. |
Proszki metali | - Komponenty lotnicze i kosmiczne - Części samochodowe - Implanty medyczne - Narzędzia i matryce | * Stopy tytanu: AP Powder Company, Höganäs, GE Additive * Stal nierdzewna: Carpenter Additive Manufacturing, SLM Solutions, EOS GmbH * Stopy aluminium: Rio Tinto Alcan, DLP Manufacturing, Exone | * Morfologia (kształt) proszku wpływa na płynność i gęstość upakowania. * Wielkość ziarna wpływa na właściwości mechaniczne końcowej części. * Protokoły bezpieczeństwa mają kluczowe znaczenie podczas pracy z reaktywnymi proszkami metali. |
Proszki kompozytowe | - Lekkie konstrukcje o wysokiej wytrzymałości - Komponenty przewodzące - Biokompatybilne implanty o ulepszonych właściwościach | * Kompozyty polimerowo-metalowe: LPW Technology, Markforged, Desktop Metal * Kompozyty ceramiczno-metalowe: Sandvik Hyperion, Extrude Hone, Plasma Technik * Kompozyty polimerowo-włókniste: Stratasys, Desktop Metal, Henkel | * Wybór zależy od pożądanej kombinacji właściwości (wytrzymałość, przewodność, biokompatybilność). * Interfejs między różnymi materiałami wymaga starannego rozważenia w celu uzyskania optymalnej wydajności. * Parametry drukowania mogą wymagać dostosowania w porównaniu do proszków jednomateriałowych. |
Zastosowania Proszki do druku 3D
Proszki do drukowania w wyjątkowy sposób ułatwiają tworzenie złożonych, niestandardowych geometrii części w różnych branżach:
Przemysł | Przykładowe komponenty | Korzyści |
---|---|---|
Lotnictwo i kosmonautyka | Łopatki turbin, dysze rakiet, podwozia UAV | Redukcja wagi, wzrost wydajności |
Medyczny | Implanty i protezy dopasowane do pacjenta | Spersonalizowany rozmiar, biokompatybilność |
Motoryzacja | Wymienniki ciepła, lekkie elementy podwozia | Konsolidacja części, wydajność |
Przemysłowy | Niestandardowe oprzyrządowanie produkcyjne, przyrządy | Skrócone ramy czasowe rozwoju |
Tabela 5: Główne sektory wykorzystujące możliwości druku 3D w proszku
Zdolność do szybkiej iteracji projektów i ekonomicznego drukowania krótkich serii umożliwia innowacje w zakresie części końcowych.
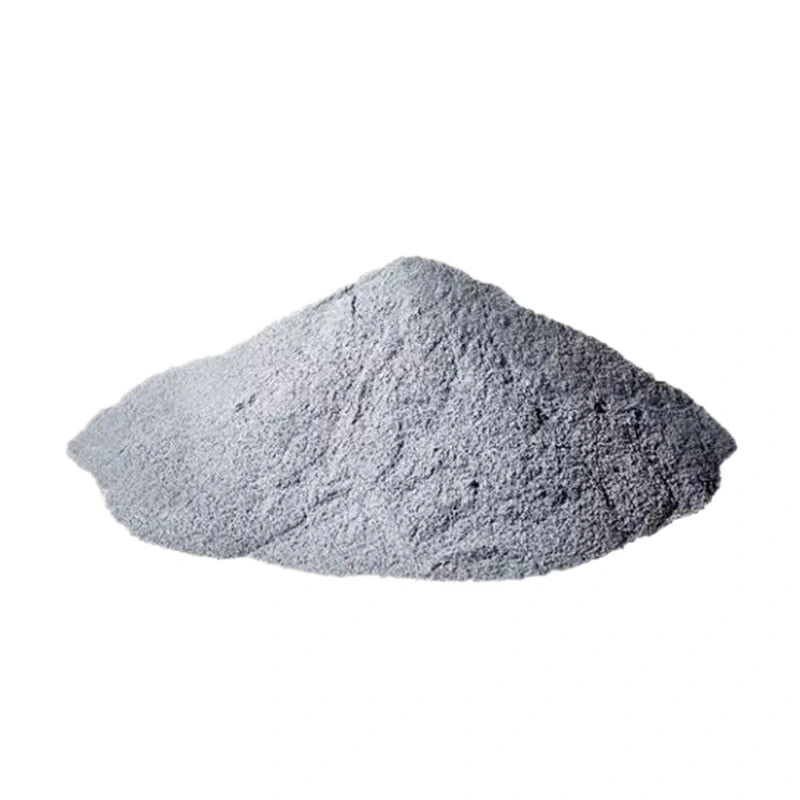
Plusy i minusy druku 3D w proszku
Plusy | Wady |
---|---|
Wysoka dokładność i rozdzielczość | Obsługa i bezpieczeństwo proszków |
Szeroki zakres materiałów | Ograniczony rozmiar kompilacji |
Minimalne struktury wsparcia | Wymagania dotyczące przetwarzania końcowego |
Szybkie tempo produkcji | Wysoka inwestycja początkowa |
Najczęściej zadawane pytania
P: Jaki zakres wielkości cząstek sprawdza się najlepiej w przypadku proszków do druku 3D z metalu?
O: 10-45 mikronów ułatwia dobre upakowanie i rozprowadzanie, jednocześnie unikając wyzwań związanych z ultradrobnymi proszkami wokół obsługi proszku. Większość stopów dobrze radzi sobie z dystrybucją 30±15 μm.
P: Który proces druku 3D z proszku polimerowego zapewnia najlepszą wydajność mechaniczną?
O: Selektywne spiekanie laserowe (SLS) umożliwia doskonałe stapianie i produkcję drobnych elementów - tworząc wysokowydajne części z tworzyw sztucznych rywalizujące lub przewyższające procesy formowania wtryskowego.
P: Jak długo można przechowywać niewykorzystany proszek do drukarek 3D?
O: Przechowywane w chłodnym i suchym miejscu, zabezpieczone przed wilgocią środkiem osuszającym - proszki zachowują właściwości przepływowe przez co najmniej 12 miesięcy. Nawet otwarte proszki wytrzymują ponad 6 miesięcy przed zauważalną degradacją.
P: Czy jakość proszku wyjściowego ma znaczący wpływ na właściwości drukowanych części?
O: Tak, czystość chemiczna proszku oraz odpowiednia kontrola właściwości proszku silnie determinują końcowe właściwości mechaniczne części, estetykę, dokładność wymiarową i niezawodność działania.
Udostępnij
MET3DP Technology Co., LTD jest wiodącym dostawcą rozwiązań w zakresie produkcji addytywnej z siedzibą w Qingdao w Chinach. Nasza firma specjalizuje się w sprzęcie do druku 3D i wysokowydajnych proszkach metali do zastosowań przemysłowych.
Zapytaj o najlepszą cenę i spersonalizowane rozwiązanie dla Twojej firmy!
Powiązane artykuły
Informacje o Met3DP
Ostatnia aktualizacja
Nasz produkt
KONTAKT
Masz pytania? Wyślij nam wiadomość teraz! Po otrzymaniu wiadomości obsłużymy Twoją prośbę całym zespołem.
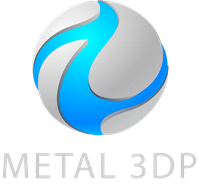
Proszki metali do druku 3D i produkcji addytywnej
PRODUKT
cONTACT INFO
- Miasto Qingdao, Shandong, Chiny
- [email protected]
- [email protected]
- +86 19116340731