voor- en nadelen van verschillende 3D-geprinte metaalpoederproductieprocessen
Inhoudsopgave
Stel je voor dat je laag voor laag ingewikkelde metalen voorwerpen bouwt, met ongeëvenaarde ontwerpvrijheid en minimaal afval. Dat is de magie van 3D-geprinte metaalpoeders. Maar voordat deze minuscule metaalkorrels de bouwstenen worden van baanbrekende creaties, moeten ze met nauwgezette zorg worden geproduceerd.
Er bestaan verschillende metaalpoederproductieprocessen, elk met zijn eigen voor- en nadelen. De juiste keuze hangt af van de specifieke behoeften van uw 3D-geprinte project. Deze uitgebreide gids duikt in de fascinerende wereld van metaalpoederproductie en voorziet u van de kennis om weloverwogen beslissingen te nemen voor uw 3D geprinte inspanningen.
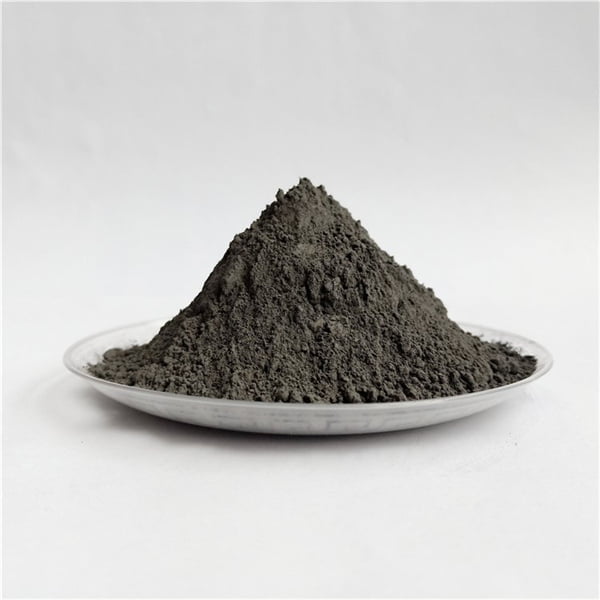
3D-geprinte metaalpoeders
Metaalpoeders zijn de onbezongen helden van 3D printen. Deze fijne, vrijstromende metaaldeeltjes, variërend in grootte van 10 tot 150 micrometer, dienen als grondstof voor verschillende metalen additive manufacturing (AM) technieken zoals Laser Powder Bed Fusion (LPBF) en Binder Jetting.
De kwaliteit en eigenschappen van het metaalpoeder zijn van grote invloed op de eigenschappen van het uiteindelijke geprinte onderdeel, zoals sterkte, oppervlakteafwerking en algemene prestaties. Daarom is het selecteren van het optimale metaalpoederproductieproces cruciaal voor het behalen van de gewenste resultaten bij 3D printen.
Onderzoek naar metaalpoederproductiemethoden
Metaalpoederproductie maakt gebruik van verschillende technieken om bulkmetaal te breken tot de gewenste deeltjesgrootte en morfologie. Laten we eens dieper ingaan op vier prominente methoden, elk met zijn eigen unieke verkoopargument en overwegingen:
1. Verstuivingstechnieken: Bulkmetaal afbreken met precisie
Verstuivingstechnieken zijn de werkpaarden in de metaalpoederproductie. Hierbij wordt gesmolten metaal via verschillende technieken omgezet in een fijne nevel van deeltjes:
- Voordelen en nadelen van de plasmaverstuivingsmethode: Plasmaatomisatie maakt gebruik van een plasmatoorts met hoge temperatuur om de metaalgrondstof te smelten. Het gesmolten metaal wordt vervolgens uitgeworpen in een gasstroom met hoge snelheid, waardoor het uiteenvalt in fijne deeltjes. Deze methode biedt uitstekende controle over de deeltjesgrootte en morfologie, waardoor het geschikt is voor het produceren van poeders van hoge kwaliteit voor veeleisende toepassingen zoals luchtvaart en medische implantaten. Door het hoge energieverbruik en de complexe apparatuur kan het echter een duurdere optie zijn.
- Voor- en nadelen van de roterende-elektrodeverstuivingsmethode (REA): REA maakt gebruik van een snel ronddraaiende elektrode die in een bad van gesmolten metaal wordt gedompeld. De centrifugale kracht die door de rotatie wordt gegenereerd, werpt minuscule metaaldruppeltjes af die stollen tot bolvormige deeltjes wanneer ze afkoelen in een gasstroom. Deze methode heeft hoge productiesnelheden en een goede controle over de deeltjesvorm, waardoor het ideaal is voor een breed scala aan metaalpoeders. Het proces kan echter interne spanningen in de deeltjes introduceren, wat de eigenschappen van het uiteindelijk geprinte onderdeel kan beïnvloeden.
- Voor- en nadelen van de waterverstuivingsmethode: Bij waterverstuiving is de aanpak eenvoudiger. Gesmolten metaal wordt in een waterstraal onder hoge druk gegoten, waardoor het uiteenvalt in fijne deeltjes. Deze methode is kosteneffectief en biedt hoge productiesnelheden, waardoor het zeer geschikt is voor bulktoepassingen. De resulterende deeltjes kunnen echter onregelmatig van vorm zijn en hogere oppervlakteoxides hebben, wat hun stroombaarheid en bedrukbaarheid kan beïnvloeden.
De juiste verstuivingsmethode kiezen:
De optimale verstuivingsmethode hangt af van factoren zoals de gewenste deeltjesgrootte en morfologie, het materiaaltype en de toepassingsvereisten.
Als u bijvoorbeeld zeer nauwkeurige, bolvormige deeltjes nodig hebt voor kritieke onderdelen in de ruimtevaart, dan kan plasmaverneveling de voorkeursoptie zijn. Voor kostengevoelige toepassingen waarbij de vorm van de deeltjes minder kritisch is, kan verneveling met water daarentegen een haalbare optie zijn.
2. Mechanisch frezen: Metaal vermalen tot poederperfectie
Mechanisch malen is een meer fysieke benadering. Bulkmetaal wordt gebroken en vermalen tot fijne deeltjes met behulp van krachtige molens zoals kogelmolens en attritormolens.
- Voordelen en nadelen van mechanisch frezen: Deze methode biedt goede controle over de deeltjesgrootteverdeling en kan een breed scala aan materialen aan, waaronder brosse metalen. Mechanisch malen kan echter interne spanningen en verontreiniging in het poeder introduceren als gevolg van het maalproces. Bovendien kan het bereiken van zeer fijne deeltjesgroottes een uitdaging zijn.
3. Methoden voor chemische reductie: Een transformatieve benadering
Chemische reductiemethoden vertrouwen op chemische reacties om metaaloxiden of andere verbindingen om te zetten in metaalpoeders.
- Voor- en nadelen van chemische reductiemethoden: Deze methoden bieden een hoge zuiverheid en kunnen poeders met unieke morfologieën produceren. Ze kunnen echter complex en tijdrovend zijn en gevaarlijke bijproducten genereren. Bovendien kan het een uitdaging zijn om de deeltjesgrootte en morfologie onder controle te houden.
4. Elektrolyse: Metaaldeeltjes opbouwen door middel van elektriciteit
Elektrolyse maakt gebruik van de kracht van elektriciteit om metaalpoeders te produceren. Er wordt een elektrische stroom door een metaalzoutoplossing geleid, waardoor de metaalionen zich als kleine deeltjes op een kathode afzetten.
- Voordelen en nadelen van elektrolyse: Elektrolyse biedt een hoge zuiverheid en een goede controle over de deeltjesgrootte en morfologie. Het proces kan echter langzaam en energie-intensief zijn, wat het gebruik voor grootschalige productie beperkt. Bovendien is het vaak beperkt tot specifieke metalen die gemakkelijk uit elektrolyten kunnen worden afgezet.
Een nichetoepassing voor 3D printen:
Elektrolyse wordt slechts beperkt toegepast bij 3D printen vanwege de lage productiesnelheid en de geschiktheid voor een kleiner aantal metalen in vergelijking met andere methoden.
Een metaalpoederproductieproces kiezen
Het selecteren van het ideale metaalpoederproductieproces gaat verder dan alleen de techniek zelf. Verschillende andere factoren spelen een cruciale rol:
- Materiaal compatibiliteit: Niet alle methoden zijn geschikt voor alle soorten metalen. Sommige methoden kunnen misschien niet overweg met het smeltpunt of de brosheid van een specifiek materiaal.
- Gewenste deeltjesgrootte en morfologie: De grootte en vorm van de metaaldeeltjes hebben een grote invloed op hun stroombaarheid, bedrukbaarheid en de eigenschappen van het uiteindelijke onderdeel. Technieken zoals plasmaatomisatie bieden meer controle over deze aspecten.
- Poeder Zuiverheid: De aanwezigheid van onzuiverheden zoals oxiden of andere verontreinigingen kan de bedrukbaarheid en mechanische eigenschappen van het uiteindelijke onderdeel beïnvloeden. Processen zoals chemische reductiemethoden kunnen poeders met een hoge zuiverheid leveren.
- Kosten: De productiekosten variëren afhankelijk van de complexiteit van de methode, het energieverbruik en de vereisten voor materiaalbehandeling. Waterverstuiving is over het algemeen een meer kosteneffectieve optie, terwijl plasmaverstuiving duurder kan zijn.
- Milieu-impact: Bepaalde methoden, zoals die waarbij gevaarlijke bijproducten betrokken zijn, kunnen een grotere ecologische voetafdruk hebben. Duurzame praktijken en verantwoord afvalbeheer zijn cruciale overwegingen.
De perfecte match vinden:
Door deze factoren zorgvuldig te evalueren en ze af te stemmen op uw specifieke projectvereisten, kunt u een weloverwogen beslissing nemen over het meest geschikte metaalpoederproductieproces voor uw 3D printbehoeften.
Extra overwegingen voor succes
Hoewel het productieproces van metaalpoeder een kritieke rol speelt, gaat het bereiken van optimale resultaten bij 3D printen verder dan alleen het poeder zelf. Hier volgen enkele aanvullende overwegingen:
- Behandeling en opslag van poeder: De juiste behandeling en opslag zijn essentieel om de kwaliteit van het poeder te behouden en vochtabsorptie of verontreiniging te voorkomen. Afhankelijk van het materiaal kan dit het gebruik van een omgeving met inert gas of opslag met gecontroleerde vochtigheid inhouden.
- Nabewerking van poeders: Bepaalde processen kunnen extra stappen vereisen zoals zeven of drogen om de gewenste deeltjesgrootteverdeling of vochtgehalte voor optimale bedrukbaarheid te bereiken.
- Machine compatibiliteit: Het gekozen metaalpoeder moet compatibel zijn met de technologie en bouwparameters van je specifieke 3D printer.
Door naast het metaalpoederproductieproces rekening te houden met deze aspecten, kunt u zorgen voor een soepele en succesvolle 3D-printervaring die de weg vrijmaakt voor de creatie van baanbrekende metalen voorwerpen.
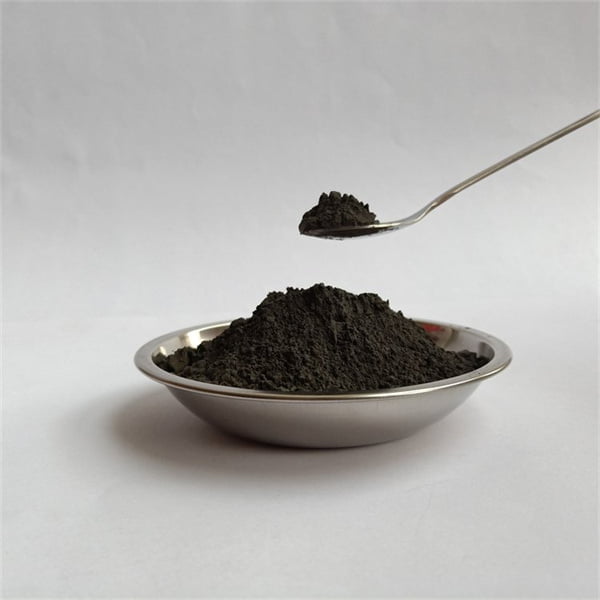
FAQ
V: Wat is de meest gebruikte methode voor het produceren van metaalpoeders voor 3D printen?
A: Verstuivingstechnieken, met name gasverstuivingstechnieken zoals plasmaverstuiving en verstuiving met roterende elektroden, zijn de meest gebruikte methoden voor het produceren van metaalpoeders voor 3D printen vanwege hun vermogen om goede controle te krijgen over de deeltjesgrootte en morfologie.
V: Met welke factoren moet ik rekening houden bij het kiezen van een metaalpoederproductieproces?
A: Verschillende factoren spelen een rol, waaronder het materiaaltype, de gewenste deeltjesgrootte en morfologie, de vereisten voor poederzuiverheid, kostenoverwegingen en de impact op het milieu.
V: Is er één "beste" methode voor metaalpoederproductie?
A: Er is niet één methode. De optimale keuze hangt af van uw specifieke projecteisen en de eigenschappen die u zoekt in het uiteindelijke geprinte onderdeel.
V: Wat zijn enkele van de uitdagingen bij de productie van metaalpoeder?
A: Het handhaven van een consistente deeltjesgrootte en morfologie, het bereiken van een hoge zuiverheidsgraad en het balanceren van kosteneffectiviteit met de gewenste poedereigenschappen zijn enkele van de voortdurende uitdagingen bij de productie van metaalpoeder.
V: Hoe zal de metaalpoederproductie evolueren in de toekomst?
A: In de toekomst zal de metaalpoederproductie waarschijnlijk worden gekenmerkt door technologische vooruitgang die leidt tot efficiëntere en duurzamere processen. Bovendien wordt er voortdurend onderzoek gedaan naar nieuwe poedervormige productietechnieken voor specifieke materialen en toepassingen.
Door de fijne kneepjes van metaalpoederproductieprocessen en hun invloed op 3D printresultaten te begrijpen, kunt u met meer vertrouwen en controle beginnen aan uw reis om innovatieve en functionele metalen voorwerpen te maken.
Delen op
MET3DP Technology Co, LTD is een toonaangevende leverancier van additieve productieoplossingen met hoofdkantoor in Qingdao, China. Ons bedrijf is gespecialiseerd in 3D printapparatuur en hoogwaardige metaalpoeders voor industriële toepassingen.
Onderzoek om de beste prijs en een op maat gemaakte oplossing voor uw bedrijf te krijgen!
gerelateerde artikelen
Over Met3DP
Recente update
Ons product
NEEM CONTACT MET ONS OP
Nog vragen? Stuur ons nu een bericht! Na ontvangst van uw bericht behandelen wij uw verzoek met een heel team.
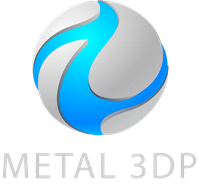
Metaalpoeders voor 3D printen en additieve productie