molybdeenlegering voor metaaladditieve productie
Inhoudsopgave
Overzicht van kracht van molybdeenlegering
Molybdeenlegeringspoeder is een belangrijk materiaal voor industriële metaal 3D printtoepassingen zoals tooling, lucht- en ruimtevaart, olie en gas en optiek.
Belangrijkste kenmerken van molybdeen-legeringspoeder:
Attribuut | Beschrijving |
---|---|
Sterkte bij hoge temperaturen | Behoudt sterkte tot 1300°C |
Warmtegeleiding | Op hetzelfde niveau als staal, 2-3X dat van titanium |
Corrosieweerstand | Uitstekende weerstand tegen zuren en chloriden |
Algemene legeringen | Mo-Ti, Mo-TiB2, Mo-La2O3, Mo-ZrO2 |
Toepassingen | Gereedschappen, lucht- en ruimtevaart, optica, nucleair |
Het hoge smeltpunt, de sterkte en thermische eigenschappen van molybdeen maken het zeer waardevol voor geprinte onderdelen die onder extreme temperaturen werken. Het biedt nieuwe ontwerpmogelijkheden ten opzichte van traditionele molybdeenverwerking.
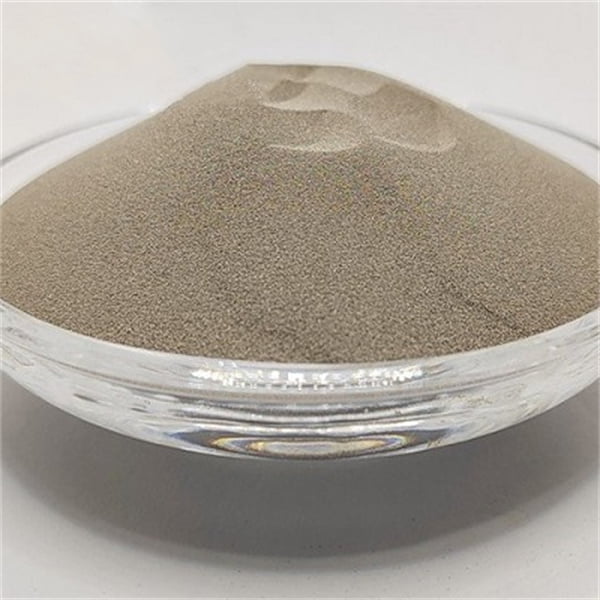
Toepassingen van kracht van molybdeenlegering
De unieke eigenschappen van molybdeenlegeringen maken ze geschikt voor:
Industrie | Toepassingen |
---|---|
Gereedschap | Plastic spuitgietmatrijzen, extrusiematrijzen, vormgereedschap |
Lucht- en ruimtevaart | Voorranden, straalbuizen, motoronderdelen |
Optiek | Spiegels, precisieoptiek, substraten |
Nucleair | Plasma gerichte componenten, hitteschilden |
Olie en gas | Downhole-gereedschap, kleppen, boorkoponderdelen |
3D-printen maakt complexe componenten op basis van molybdeen mogelijk met conforme koelkanalen en lichtgewicht roosters die niet mogelijk zijn met conventionele methoden.
Enkele specifieke toepassingen die gebruik maken van molybdeenlegeringen zijn onder andere:
- Spuitgietmatrijzen met conforme koeling voor kortere cyclustijden
- Voorranden van hypersonische voertuigen die bestand zijn tegen intense verhitting
- Spiegelsubstraten die bestand zijn tegen thermische vervorming
- Straalpijpen voor lucht- en ruimtevaart met geïntegreerde koelkanalen
- Onderdelen voor downhole boren die sterk en corrosiebestendig moeten zijn
Molybdeenlegeringen maken lichtere, beter presterende metalen onderdelen mogelijk in verschillende industrieën.
Populaire molybdeen legering macht voor Metal AM
Veel gebruikte molybdeenlegeringen voor 3D printen met metaalpoederbedfusie zijn onder andere:
Legering | Kenmerken | Toepassingen |
---|---|---|
Mo-Ti | Hoge sterkte, 1200°C gebruik | Ruimtevaart, nucleair |
Mo-La2O3 | Uitstekende kruipweerstand | Ruimtevaart, optica |
Mo-ZrO2 | Breuktaaiheid, vervormbaarheid | Industrieel, gereedschap |
Mo-TiB2 | Hardheid, slijtvastheid | Gereedschap, optiek |
Mo-Re | Sterkte bij hoge temperaturen | Nucleair, lucht- en ruimtevaart |
Het hoge smeltpunt van molybdeen maakt een breed scala aan legeringsadditieven mogelijk om eigenschappen als hardheid, sterkte, vervormbaarheid en corrosiebestendigheid naar wens aan te passen.
molybdeenlegering macht Kenmerken
Molybdeen legeringspoeder voor metaal AM heeft de volgende eigenschappen:
Parameter | Details |
---|---|
Deeltjesvorm | Bolvormig, sommige satellieten toegestaan |
Deeltjesgrootte | 15-45 micron typisch |
Grootteverdeling | D10, D50, D90 binnen nauwe marges |
Vloeibaarheid | Uitstekende vloei, niet geagglomereerd |
Schijnbare dichtheid | Meer dan 4 g/cc |
Puurheid | Hoge zuiverheid, bij voorkeur zuurstofarm |
Gasatomisatie wordt vaak gebruikt om het bolvormige poeder van de molybdeenlegering te produceren dat ideaal is voor poederbedfusieprinten.
Het controleren van de samenstelling en het minimaliseren van onzuiverheden zoals zuurstof zijn van cruciaal belang om de beoogde materiaaleigenschappen in de geprinte onderdelen te bereiken.
Vereisten voor metalen 3D printers
Voor het printen van onderdelen van molybdeenlegeringen zijn robuuste industriële metaalprinters met:
Systeem | Typische specificatie |
---|---|
Laserkracht | 300-500W |
Bouw volume | Minimaal 250 x 250 x 300 mm |
Inert gas | Argon heeft de voorkeur boven stikstof |
Precisie-optiek | Minimale spotgrootte 50 micron |
Behandeling van poeder | Gesloten-lus metaalpoedersysteem |
Operationele software | Vergemakkelijkt productie in plaats van prototyping |
Het hoge smeltpunt van molybdeenlegeringen vereist voldoende laservermogen en gasbescherming. Geautomatiseerde poederbehandelingssystemen verbeteren de productiviteit en recyclebaarheid van het poeder.
Procesparameters voor metaal 3D printen
Typische laserprocesparameters voor poederbedfusie van molybdeenlegeringen:
Parameter | Bereik |
---|---|
Laserkracht | 250-500 W |
Scansnelheid | 400-1200 mm/s |
Hatch-afstand | 80-180 μm |
Laagdikte | 20-100 µm |
Diameter straal | 50-100 µm |
Afschermingsgas | Argon, 0-5% waterstofmengsels |
Lagere porositeit en hogere dichtheden worden bereikt met een hoger laservermogen en een fijnere afstand tussen de arceringen.
Procesoptimalisatie is nodig om voor elke molybdeenlegering een balans te vinden tussen dichtheid en restspanningen en scheurneiging.
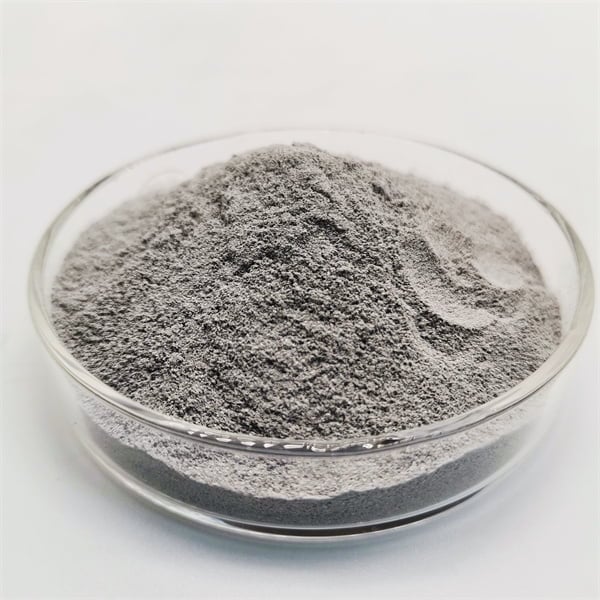
Ontwerprichtlijnen voor metaal 3D printen
Belangrijkste ontwerpprincipes voor onderdelen van molybdeenlegeringen:
Ontwerpaspect | Richtlijnen |
---|---|
Wanddikte | Minimale dikte 1-2 mm |
Overstekken | 45-60° minimaal zonder steunen |
Oppervlakteafwerking | As-print is ruw, nabewerken indien nodig |
Resterende spanning | Zorgvuldige scanstrategieën en gloeien |
Ondersteunt | Zorgvuldig ontwerp om het gebruik van steunen te minimaliseren |
De hoge stijfheid van molybdeenlegeringen maakt restspanningsbeheer kritisch. Er is simulatiesoftware nodig om scanpatronen en ondersteuningsstructuren te optimaliseren.
Mechanische eigenschappen van gedrukte kracht van molybdeenlegering
Typische mechanische eigenschappen van gedrukte molybdeenlegeringen:
Legering | Dichtheid (g/cc) | Sterkte (MPa) | Hardheid (HV) |
---|---|---|---|
Mo-Ti | 9.9 | 700-900 | 350-450 |
Mo-La2O3 | 10.1 | 850-1050 | 400-500 |
Mo-ZrO2 | 9.8 | 600-800 | 300-400 |
Mo-TiB2 | 9.5 | 650-850 | 400-600 |
Mo-Re | 10.5 | 900-1100 | 350-450 |
De eigenschappen zijn afhankelijk van de samenstelling, procesparameters en warmtebehandeling. Molybdeenlegeringen leveren uitzonderlijke prestaties bij hoge temperaturen.
Ondersteunende structuren voor het afdrukken van energie uit molybdeenlegeringen
Bij het printen van onderdelen van molybdeenlegeringen zijn vaak ondersteunende structuren nodig:
- Overstekken groter dan 45° vereisen meestal steunen
- Dichte ondersteuningsblokken of sparse ondersteuningsrasters kunnen worden gebruikt
- Ondersteuning met laag contactoppervlak aanbevolen om oppervlaktedefecten te minimaliseren
- Zorgvuldige oriëntatie minimaliseert behoefte aan ondersteuning
- Oplosbare PVA of breekbare plastic steunen beschikbaar
Het minimaliseren van het gebruik van dragers vermindert oppervlaktedefecten en nabewerkingstijd. De hoge stijfheid van molybdeen leidt ertoe dat ondersteuningsstructuren gemakkelijker loslaten.
Veel voorkomende defecten in gedrukte molybdeenlegering vermogen
Mogelijke defecten bij het afdrukken van molybdeenlegeringen:
Defect | Oorzaak | Preventie |
---|---|---|
Porositeit | Lage poederdichtheid, gebrek aan fusie | Procesparameters optimaliseren |
Kraken | Restspanningen | Geometrie wijzigen, scannen, steunen |
Kromtrekken | Thermische spanningen | Substraat voorverwarmen, spanning verlichten |
Oppervlakteruwheid | Ongesmolten deeltjes, balling | Vermogen, snelheid, focus aanpassen |
Anisotropie | Richting microstructuur | Bouworiëntatie optimaliseren |
Defecten kunnen geminimaliseerd worden door zorgvuldige parameterkeuze, poederspreiding, scanstrategie en het optimaal oriënteren van werkstukken op de bouwplaat.
Methoden voor nabewerking
Typische nabewerkingsstappen voor geprinte onderdelen van een molybdeenlegering:
Methode | Doel |
---|---|
Ondersteuning verwijderen | Ondersteunende structuren van onderdeel verwijderen |
Oppervlakteafwerking | Oppervlakteafwerking verbeteren |
Heet isostatisch persen | Interne holtes verwijderen, dichtheid verbeteren |
Hittebehandeling | Restspanningen verlichten |
Deelnemen | Meerdere geprinte onderdelen lassen |
De as-geprinte microstructuur en mechanische eigenschappen van molybdeenlegeringen kunnen ook worden aangepast door warmtebehandeling. Dit verbetert eigenschappen zoals ductiliteit en breuktaaiheid.
Kwalificatietesten
Grondige tests nodig om geprinte molybdeencomponenten te kwalificeren:
Test methode | Typische vereisten |
---|---|
Dichtheidsanalyse | > 99% van bewerkt materiaal |
Trekproeven | Voldoen aan minimale specificaties voor sterkte en vervormbaarheid |
Microstructuur | Consistente, defecte korrelstructuur |
Hardheid testen | Zoals vereist voor toepassing |
Impact testen | Minimale impactenergie voor breuken |
Niet-destructieve evaluatie zoals CT-scans helpen bij het identificeren van eventuele interne holtes of defecten.
Het selecteren van een kracht van molybdeenlegering Leverancier
Belangrijke factoren bij het kiezen van een energieleverancier voor molybdeenlegeringen:
Factor | Criteria |
---|---|
Kwaliteitssystemen | ISO 9001 of AS9100 gecertificeerd |
Poeder karakterisatie | Gegevens over de deeltjesgrootteverdeling en morfologie |
Procesbeheersing | Strakke controle van het gasvernevelingsproces |
Specialisatie | Focus op gasgeatomiseerde legeringen op maat voor AM |
Technische hulp | Applicatie-ingenieurs om productontwikkeling te ondersteunen |
Klantreferenties | Praktijkvoorbeelden van AM-toepassingen |
Als je een leverancier kiest met poeder dat speciaal is geoptimaliseerd voor AM, krijg je de beste printresultaten.
Kostenanalyse van gedrukte onderdelen van molybdeenlegering
Kostenfactoren voor gedrukte onderdelen van molybdeenlegeringen:
- Hoge kosten van molybdeenpoeder - $350-700/kg
- Printerproductiviteit beïnvloedt kosten per onderdeel
- Materiaalgebruik van 30-50%
- Arbeid voor nabewerkingsstappen
- Bijkomende kosten voor HIP, machinale bewerking, warmtebehandeling
Kostenmodel factoren:
- Investering in aanschaf printer - $500,000+
- Lage-gematigde opbouwsnelheid - 5-15 cm3/uur
- Matig-hoog materiaal
Kostenvoordelen ten opzichte van traditionele verwerking
Voordelen van het printen van molybdeenlegeringen ten opzichte van traditionele methoden:
Additieve productie | Traditionele verwerking | |
---|---|---|
Doorlooptijd | Dagen | Weken |
Ontwerpvrijheid | Complexe geometrieën, roosters | Ontwerpbeperkingen |
Maatwerk | Gemakkelijk aan te passen ontwerpen | Moeilijke procesveranderingen |
Consolidatie | Geïntegreerde, geprinte assemblages | Meerdere productiestappen |
Materiaal afval | Bijna netto vorm, weinig afval | Hoge materiaalverwijdering |
Voor kleine tot middelgrote volumes is AM kosteneffectiever. Traditionele methoden hebben voordelen voor hoge volumes.
Duurzaamheidsvoordelen van metaal 3D printen
Voordelen van duurzaamheid bij het printen van molybdeenlegeringen:
- Verminder materiaalverspilling door alleen het benodigde poeder te gebruiken
- Lichtgewicht, geoptimaliseerde ontwerpen mogelijk maken door topologieoptimalisatie
- Lokale productie vermindert transportemissies
- Poederrecycling verbetert de duurzaamheid nog verder
- Productie op aanvraag voorkomt overproductie
- Geconsolideerde onderdelen verminderen de verwerking stroomafwaarts
De technologie bevordert duurzamere benaderingen van technisch ontwerp en productie.
Toepassingen die voordeel halen uit molybdeenlegeringen
Belangrijke toepassingen die profiteren van de kracht van molybdeenlegeringen:
Sollicitatie | Voordelen |
---|---|
Spuitgietmatrijzen | Hoge temperatuurbestendigheid, conforme koeling |
Stuwraketten voor de ruimtevaart | Bestand tegen uitlaattemperaturen van 2300°C |
Voorranden van vliegtuigen | Geschikt voor hoge temperaturen tijdens hypersonische vluchten |
Kernfusiereactoren | Verdraagt extreme neutronenstraling |
Optische spiegels | Bestand tegen thermische vervorming |
3D-printen maakt complexe geometrieën mogelijk die niet mogelijk zijn met gesmede molybdeen onderdelen.
Trends en ontwikkelingen op het gebied van energie uit molybdeenlegeringen
Opkomende trends in poeders van molybdeenlegeringen:
- Nieuwe legeringssamenstellingen op maat voor AM-eigenschappen
- Grotere batchgroottes geproduceerd voor schaalvoordeel
- Strengere controle op poedereigenschappen en kwaliteit
- Verbeterde recyclebaarheid van poeders
- Dalende kosten door grotere productievolumes
- Breder scala aan beschikbare deeltjesgrootteverdelingen
- Meer concurrentie tussen leveranciers
- Meer lokalisatie van de toeleveringsketen buiten China
De poeders worden steeds optimaler en zuiniger naarmate de AM-markt groeit.
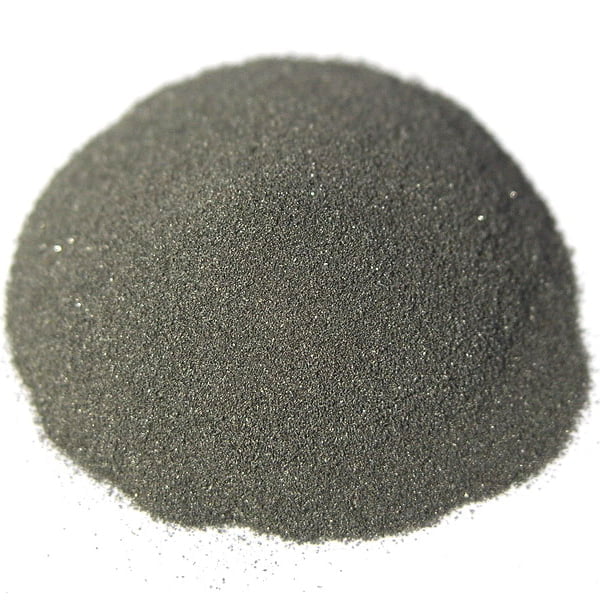
Samenvatting van het vermogen van molybdeenlegeringen voor Metal AM
- Essentieel voor hoge temperatuur, corrosiebestendige geprinte onderdelen
- Vereist printers met hoge vermogensdichtheid en inerte atmosfeer
- Zorgvuldige procesbeheersing nodig om defecten te minimaliseren
- Biedt prestatieverbeteringen ten opzichte van conventioneel molybdeen
- Toepassingen in gereedschapmakerij, lucht- en ruimtevaart, energie, optica
- Hoge materiaalkosten maar lagere totale onderdeelkosten
- Verbeterde poeders en beschikbaarheid in de toeleveringsketen in opkomst
Molybdeenlegeringen zullen lichtere additief vervaardigde metalen componenten met hogere prestaties mogelijk maken voor veeleisende industriële toepassingen.
FAQ
Vraag | Antwoord |
---|---|
Welke deeltjesgrootte wordt aanbevolen voor molybdeenlegeringen? | 15-45 micron, afhankelijk van legering en toepassing. |
Welke printers kunnen molybdeenlegeringen verwerken? | Krachtige systemen van EOS, Concept Laser, Trumpf, GE Additive. |
Welke afwerking kan worden verkregen op bedrukte oppervlakken? | De as-print is ruw met 10-15 μm Ra. Bij machinale bewerking is dit minder dan 1 μm. |
Welke nabewerking is meestal vereist? | Verwijderen van steunen, spanningsverlaging, heet isostatisch persen, machinale bewerking. |
Hoe recyclebaar zijn de poeders? | Poeders kunnen over het algemeen 5-10 keer worden hergebruikt voordat ze worden ververst. |
Delen op
MET3DP Technology Co, LTD is een toonaangevende leverancier van additieve productieoplossingen met hoofdkantoor in Qingdao, China. Ons bedrijf is gespecialiseerd in 3D printapparatuur en hoogwaardige metaalpoeders voor industriële toepassingen.
Onderzoek om de beste prijs en een op maat gemaakte oplossing voor uw bedrijf te krijgen!
gerelateerde artikelen
Over Met3DP
Recente update
Ons product
NEEM CONTACT MET ONS OP
Nog vragen? Stuur ons nu een bericht! Na ontvangst van uw bericht behandelen wij uw verzoek met een heel team.
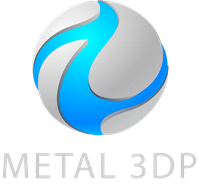
Metaalpoeders voor 3D printen en additieve productie