Motorbehuizing 3D printen met aluminium en titanium
Inhoudsopgave
Introductie: Revolutionaire productie van motorhuizen met 3D-printen van metaal
De motorbehuizing, ook wel motorblok, motorhuis of carter genoemd afhankelijk van de specifieke toepassing en de terminologie in de sector, vormt de hoeksteen van vrijwel alle verbrandingsmotoren en vele andere soorten machines voor het opwekken en omzetten van energie. Het dient als structurele fundering en omsluit kritieke bewegende delen zoals zuigers, krukassen en nokkenassen, terwijl het ook bevestigingspunten biedt voor hulpsystemen en vitale vloeistoffen zoals olie en koelvloeistof beheert. Traditioneel wordt voor de productie van deze complexe en robuuste onderdelen veel gebruik gemaakt van gevestigde methoden zoals gieten (zandgieten, spuitgieten) gevolgd door uitgebreide machinale bewerking. Hoewel deze conventionele processen effectief zijn, hebben ze vaak te maken met beperkingen op het gebied van ontwerpvrijheid, gewichtsoptimalisatie, doorlooptijden voor gereedschappen en de mogelijkheid om zeer aangepaste of kleine series kosteneffectief te produceren. De zoektocht naar betere prestaties, een efficiënter brandstofverbruik, minder uitstoot en gestroomlijnde toeleveringsketens in sectoren als de lucht- en ruimtevaart, de auto-industrie en industriële productie leidt tot een paradigmaverschuiving naar geavanceerdere productietechnieken. Maak kennis met metaal additive manufacturing (AM), beter bekend als metaal additive manufacturing. 3d printen. Deze transformatieve technologie ontwikkelt zich snel van prototyping naar serieproductie voor veeleisende toepassingen en biedt ongekende mogelijkheden om de manier waarop cruciale onderdelen zoals motorhuizen worden ontworpen, ontwikkeld en geproduceerd opnieuw uit te vinden.
Metalen 3D printtechnologieën, zoals Selective Laser Melting (SLM), Direct Metal Laser Sintering (DMLS) en Electron Beam Melting (EBM), laag voor laag onderdelen bouwen rechtstreeks vanuit digitale CAD-modellen met behulp van hoogenergetische bronnen (lasers of elektronenbundels) om fijne metaalpoeders samen te smelten. Deze additieve benadering verschilt fundamenteel van subtractieve (machinale bewerking) of formatieve (gieten, smeden) methoden en biedt een groot aantal voordelen die perfect geschikt zijn voor de uitdagingen van de moderne productie van motorhuizen. Stel je motorbehuizingen voor met ingewikkelde interne koelkanalen die precies de contouren volgen van warmteproducerende gebieden, wat onmogelijk is met gieten of boren. Stelt u zich eens significant lichtere structuren voor die bereikt worden door topologieoptimalisatie, waarbij alleen materiaal wordt verwijderd waar het structureel niet nodig is, wat leidt tot directe brandstofbesparingen in voertuigen en vliegtuigen. Denk aan de mogelijkheid om meerdere onderdelen te consolideren in een enkel, geïntegreerd 3D-geprint onderdeel, waardoor de assemblagetijd, potentiële lekken en de algehele complexiteit van het systeem afnemen. Bovendien maakt AM dure en tijdrovende tooling (mallen of matrijzen) overbodig, waardoor het economisch haalbaar is voor het produceren van aangepaste ontwerpen, oude onderdelen waarvoor geen tooling meer bestaat of kleine tot middelgrote productieseries. Dit vermogen is van onschatbare waarde voor het afstemmen van prestaties, nichemarkten voor voertuigen, snelle ontwikkelingscycli en het beheer van reserveonderdelen op aanvraag, waarbij direct wordt ingespeeld op de behoeften van inkoopmanagers die op zoek zijn naar flexibele en efficiënte productieoplossingen.
Bedrijven die voorop lopen in deze technologische golf, zoals Met3dpleveren de essentiële bouwstenen voor deze productierevolutie. Het hoofdkantoor is gevestigd in Qingdao, China. Met3dp is niet alleen gespecialiseerd in het ontwikkelen en leveren van toonaangevende metalen 3D printapparatuur, bekend om printvolume, nauwkeurigheid en betrouwbaarheid, maar ook in het produceren van hoogwaardige metaalpoeders die essentieel zijn voor het maken van dichte, hoogwaardige onderdelen. Door gebruik te maken van geavanceerde poederproductietechnieken zoals gasverstuiving en Plasma Rotating Electrode Process (PREP), zorgt Met3dp ervoor dat de sferische metaalpoeders een uitstekende vloeibaarheid en consistentie vertonen, wat leidt tot superieure mechanische eigenschappen in de uiteindelijke geprinte componenten. Hun expertise omvat een breed scala aan materialen die relevant zijn voor motorhuizen, waaronder aluminiumlegeringen, titaanlegeringen en op nikkel gebaseerde superlegeringen. Nu ingenieurs en inkoopspecialisten steeds meer het potentieel van AM verkennen, is het van cruciaal belang om de toepassing ervan op componenten zoals motorhuizen te begrijpen om een concurrentievoordeel te behouden en de voordelen van de volgende generatie productie ten volle te benutten. Dit artikel duikt diep in de wereld van 3D-geprinte motorhuizen, onderzoekt hun toepassingen, de overtuigende voordelen van het gebruik van metaal-AM, aanbevolen materialen zoals AlSi10Mg, Ti-6Al-4V en IN718, kritische ontwerpoverwegingen, haalbare precisie, behoeften voor nabewerking, potentiële uitdagingen, criteria voor leveranciersselectie, kostenfactoren en veelgestelde vragen, en biedt een uitgebreide gids voor bedrijven die deze innovatieve benadering overwegen.
Waar worden motorhuizen voor gebruikt? Belangrijkste industrieën en functies
De motorbehuizing is veel meer dan alleen een beschermend omhulsel; het is een multifunctioneel, zwaar belast onderdeel dat de ruggengraat vormt van een motor of gerelateerd aandrijflijn/vloeistofsysteem. Het ontwerp en het materiaal moeten voldoen aan strenge eisen die worden bepaald door de specifieke toepassing, bedrijfsomgeving en prestatieverwachtingen. Inzicht in de diverse rollen en industriële toepassingen van motorhuizen maakt duidelijk waarom het optimaliseren van het ontwerp- en fabricageproces door middel van technologieën zoals 3D-printen van metaal zo'n belangrijk potentieel biedt voor B2B-leveranciers, fabrikanten en eindgebruikers.
Kernfuncties van een motorbehuizing:
- Structurele ondersteuning: Biedt het hoofdframe voor de motor en ondersteunt de krukas, cilinders (of cilindervoeringen) en vaak de cilinderkop(pen). Het moet bestand zijn tegen aanzienlijke mechanische belastingen door verbrandingsdruk, roterende/reciprocerende massa's en externe trillingen.
- Insluiting: Omsluit de interne bewegende delen, beschermt ze tegen externe verontreinigingen (vuil, water) en bevat motorvloeistoffen (smeerolie, koelvloeistof). Het is van cruciaal belang dat de afdichting intact blijft.
- Uitlijning: Zorgt voor een nauwkeurige uitlijning van kritieke onderdelen zoals de hoofdlagers van de krukas en cilinderboringen, wat essentieel is voor een efficiënte werking, minimale slijtage en een lange levensduur. De toleranties zijn vaak erg krap.
- Warmteafvoer: Speelt een rol bij het beheersen van de motorwarmte, vaak met waterjacks of koelribben om de warmte van de verbrandingskamers en cilinders over te dragen aan het koelsysteem (vloeistof of lucht).
- Beheer van vloeistoffen: Bevat ingewikkelde doorgangen voor smeerolie (galerijen, toevoerleidingen naar lagers) en koelvloeistof (waterjacks). Het ontwerp moet een efficiënte doorstroming garanderen en lekken voorkomen.
- Bevestigingspunten: Biedt veilige locaties voor het bevestigen van de motor aan het chassis van het voertuig of het frame van de uitrusting, evenals montagepunten voor hulpcomponenten zoals de startmotor, dynamo, waterpomp, oliepomp, sensoren en transmissie/versnellingsbak.
- Geluids- en trillingsdemping: De massa en stijfheid van de behuizing dragen bij aan de demping van motorgeluiden en trillingen, verbeteren het comfort voor de machinist en verminderen de vermoeidheid van de omringende structuren.
Belangrijkste industrieën en specifieke toepassingen:
- Automobiel:
- Personenauto's: Motorblokken (carters) voor benzine- en dieselmotoren, transmissiebehuizingen, differentieelhuizen. Het streven naar lichtgewicht om het brandstofverbruik en de prestaties te verbeteren is van het grootste belang. Aluminiumlegeringen (zoals AlSi10Mg) zijn gebruikelijk, maar AM opent mogelijkheden voor geoptimaliseerde ontwerpen en mogelijk beter presterende materialen in nichetoepassingen. Groothandelsketens vertrouwen op consistente kwaliteit en kosteneffectieve productie.
- Motorsport: High-performance motorblokken, versnellingsbakbehuizingen, dry-sump pannen. Hier zijn maatwerk, snelle iteratie, lichtgewicht en maximale prestaties door complexe interne geometrieën (olie-/koelvloeistofdoorgangen) van cruciaal belang. Materialen zoals hoogwaardig aluminium, titanium (Ti-6Al-4V) en soms zelfs nikkelsuperlegeringen (IN718) voor onderdelen die grenzen aan de turbo worden overwogen. Met AM kunnen teams een concurrentievoordeel behalen door ontwerpen op maat te maken.
- Commerciële voertuigen (vrachtwagens, bussen): Grotere, robuuste carters voor dieselmotoren, transmissiebehuizingen. Duurzaamheid, betrouwbaarheid en kosteneffectiviteit over een lange levensduur zijn essentieel. Hoewel traditioneel gieten domineert, zou AM oplossingen kunnen bieden voor gespecialiseerde voertuigen of de vervanging van oude onderdelen.
- Lucht- en ruimtevaart:
- Vliegtuigmotoren (straalmotoren en turboprops): Versnellingsbakbehuizingen, behuizingen voor extra aandrijving, lagerbehuizingen, structurele behuizingen in de motorkern. Extreem lichtgewicht (met Ti-6Al-4V), hoge bedrijfstemperaturen (waarvoor IN718 of vergelijkbare superlegeringen nodig zijn) en absolute betrouwbaarheid zijn niet-onderhandelbaar. AM maakt complexe, sterk geoptimaliseerde geometrieën en onderdelenconsolidatie mogelijk, waardoor het gewicht afneemt en de buy-to-fly ratio verbetert. Strenge certificeringen (AS9100) zijn verplicht voor leveranciers.
- Ruimtevaart en lanceervoertuigen: Onderdelen van raketmotoren, behuizingen voor turbopompen, behuizingen voor stuwstofbeheersystemen. Vergelijkbare vereisten als vliegtuigmotoren, maar vaak met nog extremere temperatuurverschillen en drukvereisten. AM maakt snelle ontwikkeling en productie mogelijk van ingewikkelde componenten die nodig zijn voor complexe vloeistofdynamica en structurele integriteit.
- Industriële productie en energieopwekking:
- Stationaire motoren (generatoren, pompen): Carterbehuizingen voor industriële pompen, compressoren en turbines. Betrouwbaarheid, levensduur en vaak ook geluidsreductie zijn belangrijke factoren. AM kan worden gebruikt voor aangepaste configuraties, vervangingsonderdelen voor verouderde apparatuur waar de originele tooling niet meer voorhanden is, of onderdelen met verbeterde koeling of duurzaamheidskenmerken.
- Scheepsmotoren: Motorblokken, behuizingen van versnellingsbakken. Corrosiebestendigheid (vooral in zoutwateromgevingen) is een belangrijke overweging, naast duurzaamheid. Specifieke legeringen die geschikt zijn voor gebruik in de zeevaart kunnen worden verwerkt via AM.
- Zware machines (bouw, landbouw): Motorblokken, behuizingen voor hydraulische systemen, transmissiebehuizingen. Robuustheid en kosteneffectiviteit zijn de belangrijkste drijfveren. AM kan worden gebruikt voor gespecialiseerde apparatuur of geoptimaliseerde vervangingsonderdelen.
In deze diverse industrieën worden inkoopmanagers en ingenieurs geconfronteerd met gemeenschappelijke uitdagingen: betrouwbare leveranciers vinden, de voorraad voor talloze configuraties beheren, de doorlooptijd voor zowel ontwikkeling als productie verkorten, het gewicht minimaliseren met behoud van sterkte en de productiekosten onder controle houden. De mogelijkheid om complexe motorbehuizingen on-demand te produceren met behulp van metaal 3D printen biedt een overtuigende oplossing voor veel van deze uitdagingen, waardoor meer flexibele, efficiënte en potentieel beter presterende ontwerpen op maat van specifieke industriële behoeften mogelijk worden. Met3dp, met zijn robuuste printsystemen en hoogwaardige poederportfolio inclusief AlSi10Mg, Ti-6Al-4V en IN718, is goed gepositioneerd om samen te werken met bedrijven in deze sectoren om de voordelen van additive manufacturing voor kritieke motoronderdelen te realiseren.
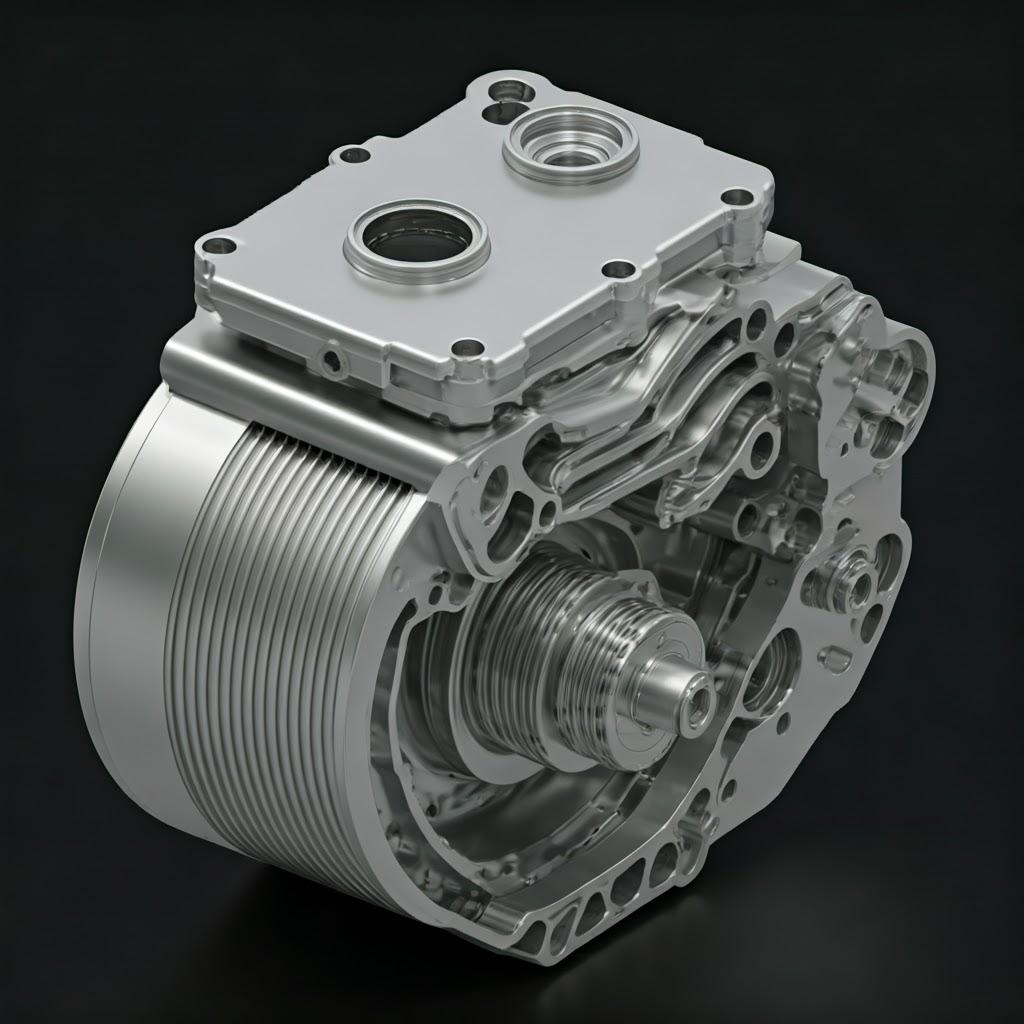
Waarom additieve metaalproductie gebruiken voor motorhuizen? Voordelen ten opzichte van traditionele methoden
Hoewel traditionele productiemethoden zoals gieten en machinaal bewerken de industrie al tientallen jaren goede diensten bewijzen bij het produceren van motorhuizen, hebben ze inherente beperkingen die effectief kunnen worden overwonnen door metaal additive manufacturing (AM). Voor ingenieurs die streven naar innovatie en inkoopmanagers die zich richten op efficiëntie en kosteneffectiviteit, is het begrijpen van de duidelijke voordelen van metaal AM essentieel om weloverwogen beslissingen te kunnen nemen over toekomstige productiestrategieën. De verschuiving naar AM gaat niet alleen over het toepassen van een nieuwe technologie; het gaat over het ontsluiten van nieuwe niveaus van prestaties, ontwerpvrijheid en flexibiliteit in de toeleveringsketen die steeds belangrijker worden in concurrerende wereldwijde markten.
Beperkingen van traditionele productie (gieten en machinaal bewerken):
- Ontwerpbeperkingen: Gieten is gebaseerd op mallen en kernen, waardoor de complexiteit van inwendige vormen beperkt is (zoals ondersnijdingen, ingewikkelde roosters). Om complexe interne geometrieën te bereiken, moeten vaak meerdere gegoten onderdelen worden geassembleerd of zijn uitgebreide, dure machinale bewerkingen nodig.
- Toolingkosten en doorlooptijden: Het maken van mallen (voor gieten) of speciale opspansystemen (voor machinale bewerking) is duur en tijdrovend. Dit maakt productie in kleine aantallen, prototyping en iteratie van ontwerpen langzaam en kostbaar. Bij elke ontwerpwijziging moet het gereedschap worden aangepast of vervangen.
- Materiaal afval: Subtractieve productie (machinale bewerking) begint met een groter blok materiaal en verwijdert overtollig materiaal, wat leidt tot aanzienlijk schroot (lage verhouding tussen aankoop en vlucht), vooral bij dure materialen zoals titanium of superlegeringen. Hoewel gieten aanvankelijk materiaalefficiënter is, levert machinale bewerking daarna nog steeds afval op.
- Uitdagingen voor gewichtsoptimalisatie: Het is moeilijk om een optimaal lichtgewicht te bereiken door alleen te gieten en machinaal te bewerken. Materiaal kan alleen worden verwijderd waar gereedschap bij kan en gieten vereist minimale wanddiktes en ontwerphoeken, waardoor vaak niet-dragend materiaal intact blijft.
- Deel Consolidatie Moeilijkheid: Complexe samenstellingen vereisen vaak dat meerdere afzonderlijke onderdelen worden gegoten, bewerkt en vervolgens samengevoegd (gelast, geschroefd), waardoor de assemblagetijd toeneemt, het gewicht toeneemt, er potentiële lekkage optreedt en er meer problemen zijn met toleranties.
- Complexiteit van de toeleveringsketen: Het beheren van gieterijen, machinefabrieken, assemblagelijnen en de bijbehorende logistiek voor traditioneel geproduceerde onderdelen kan complex zijn, vooral voor wereldwijde activiteiten of diverse productportfolio's. Lange doorlooptijden in verband met gereedschap en productieplanning kunnen de reactiesnelheid belemmeren. Lange doorlooptijden in verband met tooling en productieplanning kunnen het reactievermogen belemmeren.
Voordelen van additieve metaalproductie voor motorhuizen:
Metal AM pakt veel van deze beperkingen frontaal aan en biedt overtuigende voordelen voor de productie van motorhuizen:
- Ongekende ontwerpvrijheid:
- Complexe geometrieën: AM bouwt onderdelen laag voor laag op, waardoor zeer ingewikkelde interne en externe kenmerken kunnen worden gecreëerd zonder de beperkingen van mallen of toegang tot gereedschap. Dit maakt:
- Conforme koel-/smeerkanalen: Doorgangen kunnen precies complexe oppervlakken of warmte-beïnvloede zones volgen voor een enorm verbeterd thermisch beheer of gerichte smering, wat op conventionele wijze onmogelijk is.
- Interne roosters en geoptimaliseerde structuren: Topologie-optimalisatiesoftware kan organische, voor belasting geoptimaliseerde ontwerpen genereren, waarbij materiaal uit niet-kritieke gebieden wordt verwijderd en interne roosterstructuren worden ingebouwd voor stijfheid met een minimaal gewicht.
- Voordeel: Lichtere, efficiëntere ontwerpen, betere prestaties (betere koeling, smering), potentieel voor verbeterde geluids- en trillingsdemping door constructies.
- Complexe geometrieën: AM bouwt onderdelen laag voor laag op, waardoor zeer ingewikkelde interne en externe kenmerken kunnen worden gecreëerd zonder de beperkingen van mallen of toegang tot gereedschap. Dit maakt:
- Deelconsolidatie:
- Verminderde montage: Meerdere onderdelen die voorheen afzonderlijk werden gefabriceerd en geassembleerd, kunnen vaak opnieuw worden ontworpen en geprint als een enkel monolithisch onderdeel.
- Voordeel: Minder onderdelen, minder assemblagestappen en -kosten, minder potentiële lekroutes of storingspunten, verbeterde structurele integriteit, vereenvoudigde toeleveringsketen voor inkoopmanagers.
- Aanzienlijk lichter maken:
- Topologieoptimalisatie: Zoals gezegd maakt AM de praktische realisatie mogelijk van ontwerpen die zijn gegenereerd door topologieoptimalisatie, wat leidt tot een aanzienlijke gewichtsvermindering (vaak 20-50% of meer) terwijl de structurele prestaties behouden blijven of zelfs toenemen.
- Voordeel: Verbeterde brandstofefficiëntie (auto-industrie, luchtvaart), groter laadvermogen (luchtvaart), betere rijdynamiek (auto-industrie, motorsport), minder totale systeemmassa.
- Snelle prototyping en iteratie:
- Gereedschapsloze productie: Onderdelen worden rechtstreeks vanuit CAD-gegevens geprint, waardoor er geen mallen of matrijzen nodig zijn. Ontwerpwijzigingen kunnen snel worden doorgevoerd in het digitale model en binnen enkele dagen opnieuw worden geprint, in plaats van weken of maanden.
- Voordeel: Snellere ontwikkelingscycli, lagere R&D-kosten, de mogelijkheid om snel meerdere ontwerpvarianten te testen, snellere time-to-market voor nieuwe motorontwerpen.
- Aanpassing en productie in kleine oplages:
- Voordelige kleine hoeveelheden: De afwezigheid van gereedschapskosten maakt AM economisch haalbaar voor de productie van op maat gemaakte motorhuizen (bijv. voor motorsport, gespecialiseerde apparatuur) of kleine series die een investering in traditioneel gereedschap niet zouden rechtvaardigen.
- Voordeel: Mogelijkheid om nichemarkten te bedienen, oplossingen op maat aan te bieden, oudere onderdelen op aanvraag te produceren zonder dure voorraad gereedschappen aan te houden.
- Materiaalefficiëntie:
- Bijna-netvorm: Bij AM processen wordt meestal alleen het materiaal gebruikt dat nodig is om het onderdeel en de ondersteuningen te maken, wat resulteert in aanzienlijk minder afval in vergelijking met subtractieve bewerkingen, vooral belangrijk voor dure luchtvaartlegeringen zoals Ti-6Al-4V of IN718. Ongesmolten poeder kan vaak worden gerecycled.
- Voordeel: Lagere grondstofkosten, meer duurzaamheid, betere buy-to-fly ratio's zijn van cruciaal belang voor de economische aspecten van de luchtvaart.
- Vereenvoudiging van de toeleveringsketen en digitale inventarisatie:
- Productie op aanvraag: Onderdelen kunnen wanneer nodig dichter bij het punt van behoefte worden geproduceerd, waardoor de afhankelijkheid van complexe wereldwijde toeleveringsketens en grote fysieke voorraden afneemt. Ontwerpen kunnen digitaal worden opgeslagen.
- Voordeel: Lagere opslagkosten, minder risico op veroudering van voorraden, meer veerkracht in de toeleveringsketen, sneller reageren op aanvragen voor reserveonderdelen of aangepaste bestellingen.
De mogelijkheden van Met3dp benutten:
Kiezen voor een partner als Met3dp versterkt deze voordelen. Hun focus op zowel geavanceerde printsystemen (zoals SEBM, bekend om het verwerken van reactieve materialen en het verminderen van restspanningen) als hoogwaardige, sferische metaalpoeders zorgt ervoor dat de theoretische voordelen van AM zich vertalen in echte, high-performance motorhuizen. De toonaangevende gasverstuiving- en PREP-technologieën van Met3dp produceren poeders met de consistentie en zuiverheid die vereist is voor veeleisende toepassingen in de ruimtevaart, de automobielindustrie en de medische sector en zorgen ervoor dat de uiteindelijke onderdelen de benodigde dichtheid, mechanische eigenschappen en betrouwbaarheid bezitten. Hun uitgebreide oplossingen, die apparatuur, materialen en diensten voor applicatieontwikkeling omvatten, stellen bedrijven in staat om het potentieel van AM voor onderdelen zoals motorhuizen volledig te benutten. Terwijl traditionele methoden geschikt blijven voor grote volumes, gestandaardiseerde productie, biedt metal AM een krachtige, aanvullende en vaak superieure benadering voor componenten die hoge prestaties, complexe ontwerpen, lichtgewicht en productiecapaciteit vereisen.
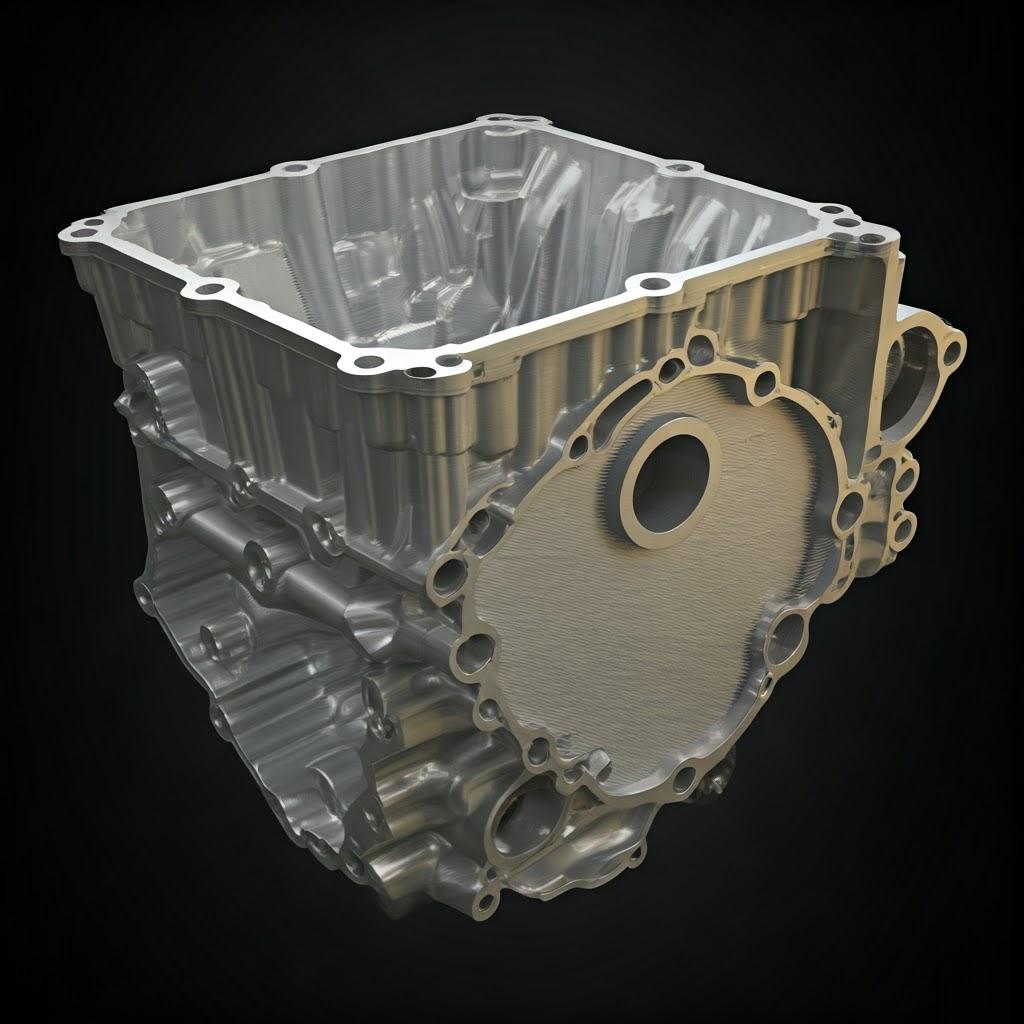
Aanbevolen materialen voor 3D-geprinte motorhuizen: AlSi10Mg, Ti-6Al-4V, IN718
De keuze van het juiste materiaal is van fundamenteel belang voor het succes van elk technisch onderdeel, en 3D-geprinte motorhuizen vormen hierop geen uitzondering. De keuze hangt sterk af van de specifieke toepassingsvereisten, zoals bedrijfstemperatuur, structurele belastingen, gewichtsdoelen, omgevingsomstandigheden (corrosie) en kostenbeperkingen. Metaal additive manufacturing biedt een groeiend aanbod van materialen, maar voor motorhuizen springen drie legeringen eruit vanwege hun bekende eigenschappen, verwerkbaarheid en relevantie voor belangrijke industrieën: Aluminium AlSi10Mg, Titanium Ti-6Al-4V en nikkellegering IN718. Elk biedt een unieke balans van eigenschappen waardoor ze geschikt zijn voor verschillende soorten toepassingen voor motorbehuizingen. Samenwerken met een deskundige metaalpoederleverancier en AM-serviceprovider, zoals Met3dp, die veel expertise heeft in het verwerken van deze specifieke materialen, is cruciaal voor het bereiken van optimale resultaten. Met3dp produceert deze hoogwaardige poeders niet alleen met behulp van geavanceerde atomisatietechnieken, maar heeft ook uitgebreide ervaring met het printen ervan op hun geavanceerde SEBM-systemen, zodat de onderdelen voldoen aan strenge kwaliteits- en prestatienormen.
1. Aluminiumlegering: AlSi10Mg
- Beschrijving: AlSi10Mg is een veelgebruikte aluminiumlegering bij het gieten en is een van de populairste keuzes geworden voor metaal AM via Laser Powder Bed Fusion (LPBF) processen zoals SLM/DMLS. Het bevat silicium (Si) voor verbeterde gietbaarheid (relevant voor smeltbadgedrag in AM) en vloeibaarheid, en magnesium (Mg) voor precipitatieharding door warmtebehandeling.
- Belangrijkste eigenschappen en voordelen voor motorhuizen:
- Lichtgewicht: Aluminiumlegeringen hebben een lage dichtheid (ongeveer 2,68 g/cm³) in vergelijking met staal of titanium, waardoor ze ideaal zijn voor auto- en luchtvaarttoepassingen waar gewichtsvermindering cruciaal is voor brandstofefficiëntie en prestaties.
- Goede verhouding sterkte/gewicht: Hoewel AlSi10Mg niet zo sterk is als staal of titanium, biedt het een goede balans tussen sterkte en een laag gewicht, voldoende voor veel toepassingen in motorhuizen en transmissiebehuizingen, vooral na de juiste warmtebehandeling (bijv. T6).
- Uitstekende thermische geleidbaarheid: Aluminiumlegeringen voeren warmte effectief af, wat voordelig is voor motoronderdelen die thermische belastingen moeten beheren.
- Goede corrosiebestendigheid: Biedt voldoende weerstand tegen corrosie in typische bedrijfsomgevingen.
- Uitstekende verwerkbaarheid: Het is een van de meest volwassen legeringen voor LPBF, met goed gedefinieerde printparameters en protocollen voor nabewerking (zoals spanningsontlasting en T6 warmtebehandeling).
- Kosteneffectief (relatief): Vergeleken met superlegeringen van titanium of nikkel is AlSi10Mg-poeder aanzienlijk goedkoper, waardoor het een haalbare keuze is voor bredere toepassingen in de auto-industrie en de industrie.
- Typische toepassingen: Automotorblokken (vooral voor prestatiegerichte/nichevoertuigen), transmissiebehuizingen, oliecarters, versnellingsbakbehuizingen, afdekkingen, beugels, prototypebehuizingen voor het testen van vorm/ pasvorm/functie.
- Overwegingen: Lagere sterkte bij hoge temperatuur in vergelijking met Ti of IN718 (over het algemeen geschikt tot ~150-200°C afhankelijk van de belasting). Vereist een zorgvuldige warmtebehandeling om optimale eigenschappen te verkrijgen. Kan een uitdaging zijn om te lassen of te repareren in vergelijking met andere legeringen.
Tabel: AlSi10Mg Eigenschappenoverzicht (Typische waarden na T6 Warmtebehandeling)
Eigendom | Typische waarde (LPBF, T6) | Eenheid | Betekenis voor motorhuizen |
---|---|---|---|
Dikte | ~2.68 | g/cm³ | Primaire drijfveer voor lichtgewicht |
Ultieme treksterkte | 430 – 480 | MPa | Geeft weerstand tegen breken onder spanning aan |
Opbrengststerkte | 280 – 350 | MPa | Spanning waarbij permanente vervorming begint |
Verlenging bij breuk | 6 – 10 | % | Meting van vervormbaarheid vóór breuk |
Elasticiteitsmodulus | ~70 | GPa | Stijfheid, weerstand tegen elastische vervorming |
Warmtegeleiding | 120 – 140 | W/(m-K) | Vermogen om warmte weg te leiden van hete plekken |
Max. diensttemperatuur | ~150 – 200 | °C | Geschatte limiet voor behoud van significante sterkte |
Exporteren naar Sheets
2. Titaniumlegering: Ti-6Al-4V (graad 5)
- Beschrijving: Ti-6Al-4V (vaak Ti64 genoemd) is het werkpaard van de titaniumindustrie, goed voor meer dan 50% van het totale titaniumgebruik. Het is een alfa-bèta legering met aluminium (Al) en vanadium (V), bekend om zijn uitstekende combinatie van hoge sterkte, lage dichtheid en uitstekende corrosiebestendigheid. Het wordt op grote schaal verwerkt met LPBF en Electron Beam Melting (EBM). Met3dp's expertise met EBM (SEBM - Selective Electron Beam Melting) is bijzonder relevant, omdat EBM vaak Ti-6Al-4V onderdelen produceert met lagere restspanningen in vergelijking met LPBF.
- Belangrijkste eigenschappen en voordelen voor motorhuizen:
- Uitzonderlijke verhouding sterkte/gewicht: Ti-6Al-4V heeft een sterkte die vergelijkbaar is met die van veel staalsoorten, maar met een ongeveer 40% lagere dichtheid (~4,43 g/cm³). Dit is een groot voordeel voor motoronderdelen in de lucht- en ruimtevaart en hoogwaardige automobieltoepassingen waar het minimaliseren van massa van het grootste belang is.
- Geschikt voor hoge temperaturen: Behoudt goede sterkte bij verhoogde temperaturen (tot ~350-400°C), aanzienlijk hoger dan aluminiumlegeringen.
- Uitstekende corrosiebestendigheid: Zeer goed bestand tegen corrosie door motorvloeistoffen, atmosferische omstandigheden en zelfs zout water, waardoor het geschikt is voor veeleisende omgevingen in de ruimtevaart en scheepvaart.
- Biocompatibiliteit: Hoewel het niet typisch relevant is voor motorbehuizingen, benadrukt de biocompatibiliteit de inerte aard ervan.
- Goede vermoeiingssterkte: Presteert goed onder cyclische belastingsomstandigheden die gebruikelijk zijn in motoren.
- Typische toepassingen: Behuizingen van versnellingsbakken voor de ruimtevaart, behuizingen voor extra aandrijvingen, lagersteunen, kritieke structurele motoronderdelen, onderdelen voor motorsportmotoren met hoge prestaties (waar kosten ondergeschikt zijn aan prestaties/gewicht), onderdelen die een hoge specifieke sterkte vereisen.
- Overwegingen: Aanzienlijk hogere materiaalkosten in vergelijking met aluminium of staal. Uitdagender en duurder om te bewerken tijdens de nabewerking. Reactieve aard vereist gecontroleerde atmosfeer (argon) of vacuüm (EBM) tijdens het printen. Lagere thermische geleidbaarheid dan aluminium.
Tabel: Ti-6Al-4V eigenschappenoverzicht (typische waarden, gegloeid)
Eigendom | Typische waarde (LPBF/EBM, gegloeid) | Eenheid | Betekenis voor motorhuizen |
---|---|---|---|
Dikte | ~4.43 | g/cm³ | Aanzienlijk lichter dan staal, zwaarder dan aluminium |
Ultieme treksterkte | 900 – 1100 | MPa | Hoge sterkte voor veeleisende structurele belastingen |
Opbrengststerkte | 830 – 1000 | MPa | Hoge weerstand tegen permanente vervorming |
Verlenging bij breuk | 10 – 18 | % | Goede vervormbaarheid |
Elasticiteitsmodulus | ~110 – 115 | GPa | Goede stijfheid |
Warmtegeleiding | ~6.7 – 7.5 | W/(m-K) | Relatief laag, kan leiden tot warmteontwikkeling als er niet mee wordt omgegaan |
Max. diensttemperatuur | ~350 – 400 | °C | Geschikt voor secties met gematigd hoge temperaturen |
Exporteren naar Sheets
3. Nikkel gebaseerde superlegering: IN718 (Inconel 718)
- Beschrijving: Inconel 718 is een zeer sterke, corrosiebestendige nikkel-chroom superlegering die precipitatiegehard is met niobium (Nb), molybdeen (Mo), aluminium (Al) en titanium (Ti). Het staat bekend om zijn vermogen om uitzonderlijke sterkte te behouden en bestand te zijn tegen kruipbreuk bij zeer hoge temperaturen. Het wordt vaak verwerkt via LPBF en EBM voor veeleisende toepassingen.
- Belangrijkste eigenschappen en voordelen voor motorhuizen:
- Uitstekende sterkte bij hoge temperaturen: Behoudt uitstekende mechanische eigenschappen (trek-, kruip- en breuksterkte) bij temperaturen tot 700°C en bruikbare sterkte tot ~980°C. Dit is essentieel voor onderdelen in de buurt van verbrandingszones of uitlaatgassen.
- Uitstekende weerstand tegen corrosie en oxidatie: Bestand tegen agressieve chemische omgevingen en oxidatie bij hoge temperaturen, cruciaal bij agressieve motoromstandigheden.
- Grote sterkte: Biedt een zeer hoge trek-, vloei- en vermoeiingssterkte, zelfs bij kamertemperatuur.
- Goede lasbaarheid (in vergelijking met andere superlegeringen): Hoewel er nog steeds expertise voor nodig is, wordt IN718 over het algemeen beschouwd als een van de beter lasbare nikkelsuperlegeringen, wat relevant kan zijn voor nabewerking of assemblage indien nodig.
- Typische toepassingen: Onderdelen van luchtvaartmotoren in hete delen (bijv. turbinebehuizingen, uitlaatcomponenten, hitteschilden, behuizingen bij turboladers), gasturbineonderdelen op land, industriële toepassingen bij hoge temperaturen. Minder gebruikelijk voor typische motorblokken voor auto's vanwege de kosten en dichtheid, maar relevant voor extreme prestaties of specifieke onderdelen met hoge hitte.
- Overwegingen: Hoogste materiaalkosten van de drie. Hoogste dichtheid (~8,19 g/cm³), waardoor het zwaar is, tenzij het strategisch wordt gebruikt waarbij de temperatuurbestendigheid essentieel is. Vereist zorgvuldige procesbeheersing tijdens het printen en specifieke, vaak complexe, warmtebehandelingen in meerdere fasen (oplossingsgloeien en veroudering) om optimale eigenschappen te verkrijgen. Bewerking is moeilijk en kostbaar vanwege de hoge sterkte en de neiging tot uitharden.
Tabel: IN718 Eigenschappen Overzicht (Typische waarden, Solution Annealed & Aged)
Eigendom | Typische waarde (LPBF/EBM, op leeftijd) | Eenheid | Betekenis voor motorhuizen |
---|---|---|---|
Dikte | ~8.19 | g/cm³ | Zwaarste van de drie; gebruik gerechtvaardigd door behoefte aan extreme temperaturen |
Ultieme treksterkte | 1250 – 1450 | MPa | Extreem hoge sterkte, houdt goed stand bij hoge temperaturen |
Opbrengststerkte | 1050 – 1250 | MPa | Zeer hoge weerstand tegen doorbuiging, cruciaal voor onderdelen onder hoge druk |
Verlenging bij breuk | 12 – 20 | % | Voldoende vervormbaarheid voor een superlegering met hoge sterkte |
Elasticiteitsmodulus | ~200 | GPa | Zeer stijf materiaal |
Warmtegeleiding | ~11.4 | W/(m-K) | Lage thermische geleidbaarheid |
Max. diensttemperatuur | ~700 (voor hoge belasting) | °C | Uitstekende prestaties in motoromgevingen met zeer hoge temperaturen |
Exporteren naar Sheets
Het juiste materiaal kiezen met Met3dp:
Het selectieproces bestaat uit het afwegen van prestatie-eisen tegen kosten en gewicht.
- Voor algemene auto- of industriële behuizingen waar gewichtsbesparing belangrijk is, maar de temperaturen gematigd zijn, AlSi10Mg is vaak de meest economische en praktische keuze.
- Voor ruimtevaarttoepassingen of toepassingen met hoge prestaties waarbij een aanzienlijke gewichtsbesparing en gematigde temperatuurbestendigheid vereist zijn, Ti-6Al-4V is de voorkeursoptie ondanks de hogere kosten.
- Voor onderdelen die worden blootgesteld aan extreme hitte, zoals onderdelen in de buurt van uitlaatsystemen of in de hete delen van straalmotoren of turbines, IN718 is onmisbaar, zelfs met zijn hoge dichtheid en kosten.
Een partner als Met3dp vroeg in het ontwerpproces inschakelen is zeer aan te bevelen. Hun grondige kennis van materiaalwetenschappen, poedereigenschappen afgeleid van hun geavanceerde productieprocessen (gasverstuiving, PREP) en uitgebreide ervaring met verschillende afdrukmethoden (inclusief SEBM geoptimaliseerd voor Ti-6Al-4V en mogelijk IN718) stelt hen in staat om begeleiding van onschatbare waarde te bieden. Ze kunnen ingenieurs en inkoopmanagers helpen om afwegingen te maken, het optimale poeder uit hun portfolio te kiezen en ervoor te zorgen dat het gekozen materiaal op de juiste manier wordt verwerkt om een motorbehuizing te leveren die voldoet aan alle prestatiespecificaties of deze zelfs overtreft.
Ontwerp voor Additive Manufacturing (DfAM): Motorhuizen optimaliseren voor 3D printen
Door een ontwerp dat bedoeld is om te gieten of machinaal te bewerken direct naar een metalen 3D-printer te sturen, wordt zelden het volledige potentieel van additive manufacturing ontsloten. Om echt gebruik te maken van de eerder beschreven voordelen - lichtgewicht, consolidatie van onderdelen, betere prestaties en kostenefficiëntie - moeten ingenieurs Design for Additive Manufacturing (DfAM) omarmen. DfAM is niet zomaar een set regels; het is een mentaliteitsverandering waarbij het ontwerp van componenten vanaf de basis opnieuw wordt bekeken, waarbij specifiek gebruik wordt gemaakt van de unieke mogelijkheden en rekening wordt gehouden met de inherente beperkingen van laag-voor-laag fabricage. Voor complexe onderdelen zoals motorhuizen is het toepassen van DfAM-principes cruciaal voor het maximaliseren van de ROI en het bereiken van superieure resultaten in vergelijking met traditionele methoden. Samenwerken met ervaren AM dienstverleners, zoals Met3dp, wiens applicatie-ingenieurs de nuances van DfAM begrijpen voor materialen als AlSi10Mg, Ti-6Al-4V en IN718, kan de leercurve aanzienlijk versnellen en leiden tot succesvollere, geoptimaliseerde ontwerpen die klaar zijn voor productie.
Belangrijkste DfAM-principes voor motorhuizen:
- Topologieoptimalisatie:
- Concept: Dit is misschien wel de meest invloedrijke DfAM-techniek voor motorhuizen. Met behulp van gespecialiseerde software (bijv. Altair Inspire, nTopology, Autodesk Generative Design) definiëren ingenieurs belastingsgevallen, randvoorwaarden, ontwerpruimte en prestatiedoelen (bijv. massa minimaliseren, stijfheid maximaliseren). De software verwijdert vervolgens iteratief materiaal uit niet-dragende gebieden en genereert zo een organische, zeer efficiënte structuur die de belangrijkste spanningspaden volgt.
- Toepassing: Verminder het gewicht van motorblokken, transmissiebehuizingen, montagebeugels en structurele steunen drastisch terwijl de stijfheid en sterkte behouden blijven of zelfs toenemen. Dit vertaalt zich rechtstreeks in een beter brandstofverbruik, een verbeterde voertuigdynamiek of een groter laadvermogen.
- Overwegingen: Geoptimaliseerde vormen kunnen zeer complex en niet-intuïtief zijn en lijken vaak op botstructuren. Ze zijn meestal onmogelijk of onbetaalbaar om op traditionele wijze te maken, maar zeer geschikt voor AM. Vereist zorgvuldige validatie door middel van FEA (Finite Element Analysis).
- Vakwerkconstructies en opvulling:
- Concept: Met AM kunnen interne rasterstructuren - complexe netwerken van onderling verbonden stokjes of zich herhalende cellen - worden gemaakt binnen vaste volumes. Deze kunnen op maat worden gemaakt voor specifieke eigenschappen zoals een hoge verhouding tussen stijfheid en gewicht, energieabsorptie (trillingsdemping) of het vergemakkelijken van de warmteoverdracht. Verschillende roostertypes (bijv. kubisch, octet-truss, gyroïde) bieden verschillende eigenschappen. Roosters met variabele dichtheid kunnen de materiaalverdeling verder optimaliseren.
- Toepassing: Massieve delen van de behuizing vervangen door lichtgewicht tralieliggers waar hoge sterkte niet de primaire drijfveer is, maar stijfheid of trillingsdemping gewenst is. Kan ook worden gebruikt om interne baffling te creëren of om de warmte-uitwisselingsoppervlakken in vloeistofdoorgangen te verbeteren.
- Overwegingen: Vereist gespecialiseerde software voor generatie en simulatie. Poeder verwijderen uit fijne roosters kan een uitdaging zijn (wordt later besproken). Structurele prestaties moeten grondig gevalideerd worden.
- Deelconsolidatie:
- Concept: Maak gebruik van de mogelijkheid van AM om complexe geometrieën te maken om meerdere, voorheen afzonderlijke componenten te combineren tot een enkel, monolithisch geprint onderdeel.
- Toepassing: Beugels, montagenokken, vloeistofaansluitingen of zelfs elementen van aangrenzende systemen rechtstreeks in de hoofdstructuur van de motorbehuizing integreren. Een oliepan, pomphuis en montagebeugel kunnen bijvoorbeeld worden samengevoegd.
- Voordeel: Vermindert het aantal onderdelen, elimineert bevestigingsmiddelen en afdichtingen (potentiële lekkagepunten), vereenvoudigt de assemblage, vermindert het gewicht, verbetert de structurele integriteit en stroomlijnt het voorraadbeheer voor inkoopteams.
- Overwegingen: Vereist een holistische kijk op het systeem. Kan de complexiteit van het geprinte onderdeel vergroten. Er moet worden nagedacht over toegang voor inspectie of mogelijke reparaties.
- Integratie van eigenschappen (bijv. Conformal Channels):
- Concept: Ontwerp interne kanalen en doorgangen die precies de contouren van oppervlakken of functionele vereisten volgen, in plaats van beperkt te zijn tot rechte lijnen die mogelijk zijn door boren of eenvoudige gietkernen.
- Toepassing: Creëer zeer efficiënte conforme koelkanalen die nauw aansluiten op cilindervoeringen of zones met hoge temperaturen voor superieur thermisch beheer. Optimaliseer interne oliegalerijen voor minder drukval en gerichte smering. Integreer sensorbehuizingen of bedradingsleidingen rechtstreeks in de behuizingswanden.
- Voordeel: Verbeterde motorprestaties, verbeterde duurzaamheid, minder thermische belasting, mogelijkheid tot verkleining van de motor door betere koelingsefficiëntie.
- Overwegingen: Bij het ontwerp van interne kanalen moet rekening worden gehouden met ondersteuningseisen en toegankelijkheid voor poederverwijdering. De minimale kanaaldiameter wordt beperkt door de resolutie van het AM-proces en de mogelijkheden om poeder te verwijderen.
- Ontwerpen voor minimale ondersteuningsstructuren:
- Concept: Poederbedfusieprocessen (LPBF, EBM) vereisen ondersteuningsstructuren voor overhangende elementen (meestal onder 45 graden van horizontaal) en om het onderdeel aan de bouwplaat te verankeren en de thermische spanning te beheersen. Deze ondersteuningen verbruiken extra materiaal, zorgen voor een langere printtijd en moeten verwijderd worden tijdens de nabewerking, wat arbeidsintensief kan zijn en het oppervlak van het onderdeel kan beschadigen. DfAM streeft ernaar om de noodzaak voor steunen waar mogelijk te minimaliseren.
- Toepassing: Richt het onderdeel strategisch op de bouwplaat. Ontwerp geleidelijke overgangen en afschuiningen/vijlen in plaats van scherpe overhangen. Gebruik zelfdragende hoeken (vaak >45 graden). Gebruik opofferingsribben of -elementen die gemakkelijk kunnen worden weggefreesd als steunen op kritieke plaatsen onvermijdelijk zijn. Ontwerp interne kanalen met ruit- of druppeldoorsneden in plaats van cirkelvormige om ze zelfdragend te maken.
- Voordeel: Kortere printtijd en -kosten, minder nabewerking, minimaal risico op oppervlakteschade tijdens het verwijderen van de drager, eenvoudigere poederverwijdering uit interne holtes.
- Overwegingen: Voor complexe behuizingen is het vaak moeilijk om volledig steunvrije ontwerpen te maken. Hiervoor is inzicht nodig in de specifieke procesbeperkingen (bijv. minimale vormgrootte, haalbare overhanghoeken voor het gekozen materiaal en de machine).
- Wanddikte en afmetingen:
- Concept: AM processen hebben beperkingen wat betreft de minimaal haalbare wanddikte en feature resolutie (bijvoorbeeld kleine gaten, dunne ribben). Ontwerpen onder deze limieten kan leiden tot printfouten of onderdelen zonder structurele integriteit. Omgekeerd kunnen te dikke doorsneden de thermische stress, de printtijd en het materiaalverbruik verhogen.
- Toepassing: Houd u aan de aanbevolen minimale wanddiktes (vaak 0,4-1,0 mm afhankelijk van proces en materiaal, maar het kan nodig zijn om dikker te zijn voor structurele integriteit). Vermijd waar mogelijk grote, massieve massa's; overweeg shelling en infill (rasters). Zorg ervoor dat kleine gaatjes of fijne details binnen de procesresolutie vallen.
- Overwegingen: Richtlijnen variëren per machine, materiaal en specifieke vormgeometrie. Raadpleeg de AM leverancier (zoals Met3dp) voor specifieke aanbevelingen op basis van hun apparatuur en ervaring.
- Nabewerking overwegen:
- Concept: Ontwerp met stroomafwaartse processen in gedachten. Als oppervlakken een hoge precisie of specifieke afwerking vereisen, zorg er dan voor dat ze toegankelijk zijn voor machinale bewerking of polijsten. Als interne kanalen grondig gereinigd moeten worden, zorg dan voor toegangspoorten voor poederverwijdering en spoelen.
- Toepassing: Voeg extra materiaal toe (bewerkingstoeslag) op oppervlakken die CNC worden bewerkt tot de uiteindelijke tolerantie. Ontwerp robuuste voorzieningen voor klemming tijdens bewerking. Zorg ervoor dat de interne kanalen voldoende inlaat- en uitlaatpoorten hebben voor ontpoedering. Vermijd te complexe interne geometrieën die poeder permanent vasthouden.
- Voordeel: Gestroomlijnde post-processing workflow, minder kans op schade, zorgt ervoor dat het uiteindelijke product aan alle specificaties voldoet.
Door deze DfAM-principes te integreren, kunnen ingenieurs verder gaan dan het simpelweg kopiëren van bestaande ontwerpen en beginnen met het creëren van echt geoptimaliseerde motorhuizen die gebruikmaken van de unieke voordelen van metaal-AM. Dit vereist een gezamenlijke aanpak tussen het ontwerpteam en de productiepartner om de haalbaarheid, efficiëntie en kwaliteit tijdens het hele proces te garanderen, van het eerste concept tot de uiteindelijke productie. product.
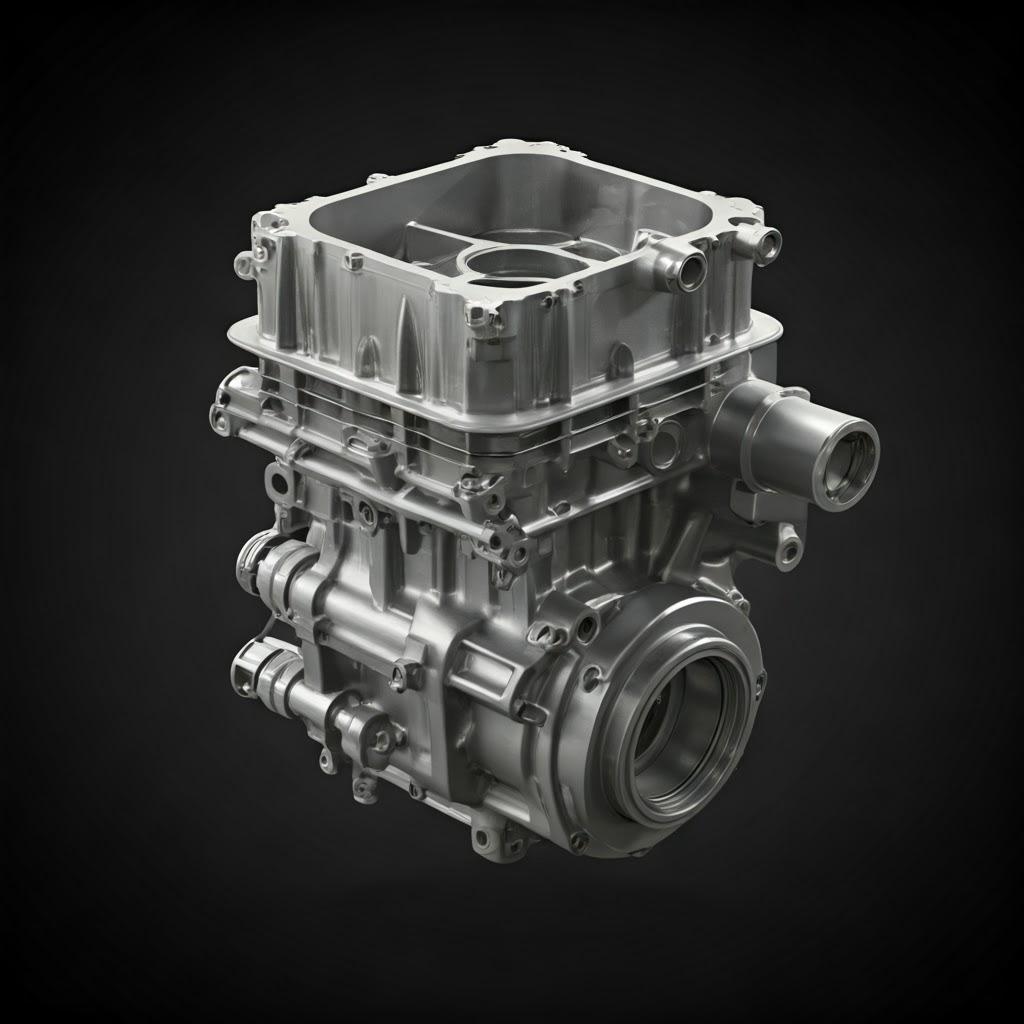
Bereikbare precisie: Tolerantie, oppervlakteafwerking en maatnauwkeurigheid in metaal-AM
Motorbehuizingen hebben vaak kritieke onderdelen die nauwe toleranties, specifieke oppervlakteafwerkingen en een hoge algehele maatnauwkeurigheid vereisen om een goede assemblage, afdichting en werking te garanderen. Inkoopmanagers en ingenieurs die additieve metaalproductie evalueren, moeten realistische verwachtingen hebben over de precisie die direct vanaf de printer haalbaar is ("as-built") en wat doorgaans nabewerkingsstappen zoals machinale bewerking vereist. Hoewel de metaal-AM-technologie aanzienlijk is verbeterd, is het over het algemeen geen directe vervanging voor machinale bewerking met hoge precisie in termen van haalbare toleranties en gladheid van het oppervlak direct vanaf de bouwplaat. Het biedt echter wel een uitstekend startpunt voor bijna-nettovormen, waardoor de daaropvolgende bewerkingsinspanningen aanzienlijk verminderen in vergelijking met het starten van een onbewerkt gietstuk of billet. De haalbare precisie hangt af van verschillende factoren, waaronder het specifieke AM proces (LPBF vs. EBM), de machinekwaliteit en -kalibratie, het gebruikte materiaal (AlSi10Mg, Ti-6Al-4V, IN718 gedragen zich verschillend), de onderdeelgrootte en -geometrie en de bouwrichting.
Dimensionale nauwkeurigheid en toleranties:
- Algemene verwachtingen: Als vuistregel kunnen goed gekalibreerde industriële AM-metaalsystemen (LPBF/EBM) vaak maatnauwkeurigheden bereiken in het bereik van ±0,1 mm tot ±0,3 mm of ±0,1% tot ±0,2% van de nominale maat, afhankelijk van welke groter is, voor onderdelen van gemiddelde grootte. Voor kleinere onderdelen kunnen plaatselijk nauwere toleranties gelden.
- LPBF (SLM/DMLS): Over het algemeen in staat tot een fijnere objectresolutie en mogelijk een iets betere nauwkeurigheid op kleinere details vergeleken met EBM vanwege de kleinere bundelspot en dunnere lagen.
- EBM (zoals SEBM van Met3dp): Werkt bij hogere temperaturen in een vacuüm, wat de opbouw van restspanningen tijdens het printen aanzienlijk vermindert. Dit kan leiden tot een betere algehele maatvastheid en minder vervorming, vooral voor grotere of complexe onderdelen gemaakt van scheurgevoelige of onder hoge druk staande materialen zoals Ti-6Al-4V of bepaalde nikkellegeringen. De minimale vormgrootte en de oppervlakteruwheid zijn echter meestal groter dan bij LPBF.
- Factoren die de nauwkeurigheid beïnvloeden:
- Machinekalibratie: Regelmatige kalibratie van het scannersysteem, de focus van de laser-/elektronenbundel en het bouwplatform is cruciaal. Hoogwaardige machineleveranciers garanderen robuuste kalibratieprocedures.
- Thermische effecten: De herhaalde verwarmings- en koelcycli die inherent zijn aan AM veroorzaken uitzetting en inkrimping, wat kan leiden tot spanningsopbouw en kromtrekken/vervorming, vooral bij grote of geometrisch complexe onderdelen. Het warme proces van EBM vermindert dit aanzienlijk. Een spanningsontlastende warmtebehandeling na de productie is essentieel voor LPBF onderdelen.
- Materiaaleigenschappen: Elk materiaal (AlSi10Mg, Ti-6Al-4V, IN718) heeft verschillende thermische geleidbaarheid, uitzettingscoëfficiënten en smeltbadgedrag, wat de uiteindelijke nauwkeurigheid beïnvloedt.
- Onderdeelgeometrie en -grootte: Grote, vlakke oppervlakken zijn vatbaarder voor kromtrekken. Hoge, dunne vormen kunnen minder stabiel zijn. Complexe interne structuren kunnen plaatselijke spanningen introduceren.
- Ondersteunende structuren: Goed ontworpen ondersteuningen helpen het onderdeel te verankeren en de thermische spanning te beheersen, waardoor de nauwkeurigheid verbetert. Een slechte ondersteuningsstrategie kan leiden tot vervorming.
- Bouwrichting: De oriëntatie van het werkstuk op de bouwplaat beïnvloedt de benodigde ondersteuning, thermische gradiënten en mogelijk de nauwkeurigheid van specifieke vormen vanwege de anisotrope aard van laaggewijs bouwen.
- Strenge toleranties bereiken: Voor kritieke onderdelen zoals lagerboringen, cilindervoeringvlakken, paringsoppervlakken of schroefgaten die toleranties vereisen die kleiner zijn dan de algemene AM-capaciteit (bijv. minder dan ± 0,05 mm), is altijd CNC-bewerking na het proces nodig. DfAM-principes moeten voorzien in het toevoegen van bewerkingsvoorraad (bijv. 0,5 - 1,5 mm) aan deze specifieke kenmerken in het CAD-model.
Oppervlakteafwerking (ruwheid):
- As-Built oppervlak: De oppervlakteafwerking van metalen AM-onderdelen is inherent ruwer dan machinaal bewerkte oppervlakken. Het wordt beïnvloed door de grootte van de poederdeeltjes, de laagdikte, de straalparameters en de oriëntatie van het oppervlak.
- LPBF: Produceert gewoonlijk oppervlakteruwheidswaarden (Ra) variërend van 6 µm tot 20 µm, afhankelijk van de hoek van het oppervlak ten opzichte van de bouwrichting (naar boven gerichte en verticale oppervlakken zijn over het algemeen gladder dan naar beneden gerichte oppervlakken die afhankelijk zijn van steunen).
- EBM: Door grotere poederdeeltjes en een hogere energie-input resulteert EBM over het algemeen in ruwere oppervlakken, vaak met Ra-waarden van 20 µm tot 40 µm of hoger.
- Betekenis voor motorhuizen:
- Stromingstrajecten: Ruwe interne oppervlakken in koelvloeistof- of oliedoorgangen kunnen de drukval verhogen en mogelijk de stromingsefficiëntie beïnvloeden.
- Oppervlakken afdichten: De oppervlakken in de fabriek zijn meestal ongeschikt voor kritische afdichtingen (bijv. pakkingvlakken); hiervoor zijn machinale bewerking of speciale coatings nodig.
- Vermoeidheidsduur: Oppervlakteruwheid kan dienen als initiatieplaats voor vermoeiingsscheuren. Voor dynamisch belaste behuizingen is het vaak nodig om de oppervlakteafwerking op kritieke plaatsen te verbeteren door polijsten of machinaal bewerken.
- Verbetering van de oppervlakteafwerking: Diverse nabewerkingstechnieken kunnen de as-built oppervlakteafwerking aanzienlijk verbeteren:
- Stralen (parelstralen, zandstralen): Zorgt voor een gelijkmatige matte afwerking, verwijdert los poeder en kan de Ra licht verbeteren (bijv. tot 5-10 µm Ra, afhankelijk van het startpunt en de media).
- Tuimelende/vibrerende afwerking: Gebruikt schurende media in een trommel of trilbak om oppervlakken glad te maken en randen te ontbramen, effectief voor batches van kleinere onderdelen of om algemene gladheid te bereiken.
- CNC-bewerking: Biedt de beste controle over de oppervlakteafwerking voor specifieke vormen, waarbij gemakkelijk Ra-waarden onder 1,6 µm of zelfs lager (spiegelglans) bereikt kunnen worden.
- Polijsten (handmatig of automatisch): Kan zeer gladde, spiegelachtige afwerkingen bereiken (Ra < 0,1 µm), maar is vaak arbeidsintensief en meestal voorbehouden aan specifieke functionele vereisten of esthetiek.
- Elektrochemisch polijsten: Kan complexe geometrieën gladmaken, maar vereist specifieke elektrolyten en instellingen.
De rol van Met3dp in precisie:
Het consistent bereiken van de vereiste precisie vereist een robuuste procesbeheersing. Met3dp, met zijn focus op hoogwaardige, sferische metaalpoeders geproduceerd via geavanceerde atomisatie, in combinatie met hun toonaangevende printapparatuur die bekend staat om nauwkeurigheid en betrouwbaarheid, biedt een sterke basis. Hun inzicht in materiaal-procesinteracties voor legeringen zoals AlSi10Mg, Ti-6Al-4V en IN718 stelt hen in staat om bouwparameters te optimaliseren en geschikte post-processingstrategieën aan te bevelen (inclusief het benutten van de unieke aspecten van verschillende afdrukmethoden zoals SEBM) om te voldoen aan de specifieke tolerantie- en oppervlakteafwerkingseisen die in technische blauwdrukken zijn vastgelegd voor veeleisende toepassingen van motorbehuizingen. Door in een vroeg stadium met hen samen te werken, kan realistisch worden ingeschat wat kan worden bereikt met de huidige constructie versus wat secundaire bewerkingen vereist, waardoor een efficiënte planning en kostenberekening voor de aanschaf kan worden gegarandeerd.
Essentiële nabewerkingsstappen voor 3D-geprinte motorhuizen
In tegenstelling tot onderdelen die worden geproduceerd door middel van netvormprocessen zoals spuitgieten of spuitgieten, vereisen metalen additief geproduceerde onderdelen bijna altijd een aantal nabewerkingsstappen om ze te transformeren van de ruwe, as-built staat in een functionele, afgewerkte motorbehuizing die klaar is voor assemblage. Deze stappen zijn cruciaal voor het bereiken van de vereiste mechanische eigenschappen, maatnauwkeurigheid, oppervlaktekenmerken en algehele kwaliteit en betrouwbaarheid. Inzicht in deze workflow is essentieel voor ingenieurs die de onderdelen ontwerpen en voor inkoopmanagers die tijd en kosten moeten budgetteren. De specifieke volgorde en noodzaak van elke stap hangen af van de gebruikte AM-technologie (LPBF vs. EBM), het materiaal (AlSi10Mg, Ti-6Al-4V, IN718 hebben verschillende behoeften), de complexiteit van het onderdeel en de uiteindelijke toepassingseisen. Vaak is het nodig om samen te werken met een fullserviceprovider of te coördineren met gespecialiseerde onderaannemers.
Typische nabewerkingsworkflow voor metalen AM motorhuizen:
- Ontpoederen:
- Doel: Verwijder zoveel mogelijk ongesmolten metaalpoeder van het onderdeel, vooral van interne kanalen en complexe geometrieën.
- Methoden: Handmatig borstelen, blazen met perslucht, stofzuigen, geautomatiseerde ontpoederingsstations die trillingen of rotatie met zich meebrengen. Voor complexe interne kanalen zijn een zorgvuldig ontwerp (toegangspoorten, gladde paden) en speciale procedures essentieel. Soms wordt ultrasone reiniging in een bad met oplosmiddel gebruikt.
- Belangrijk: Restpoeder kan de functionaliteit aantasten (doorgangen blokkeren), gewicht toevoegen en volgende stappen zoals warmtebehandeling of HIP verstoren. Onvolledige poederverwijdering is een belangrijk kwaliteitsprobleem.
- Stressverlichtende warmtebehandeling:
- Doel: Verminder de hoge restspanningen die ontstaan tijdens de snelle opwarm- en afkoelcycli van het printproces, vooral kritisch voor LPBF-onderdelen. Deze spanningen kunnen vervorming of scheuren veroorzaken tijdens het printen, na verwijdering van de bouwplaat of tijdens de daaropvolgende bewerking.
- Methoden: Het verhitten van het onderdeel (vaak terwijl het nog vastzit aan de bouwplaat) in een oven met gecontroleerde atmosfeer (bijv. argon, vacuüm) tot een specifieke temperatuur onder de verouderings- of gloeitemperatuur van het materiaal, het vasthouden gedurende een bepaalde tijd en dan langzaam afkoelen. Parameters variëren aanzienlijk per materiaal (bijv. AlSi10Mg ~300°C, Ti-6Al-4V ~650-800°C, IN718 ~980-1065°C voor homogenisatie/spanningsontlasting, hoewel specifieke cycli variëren).
- Belangrijk: Essentieel voor maatvastheid, het voorkomen van scheuren en het veilig verwijderen van de bouwplaat en de daaropvolgende bewerking. EBM-onderdelen hebben over het algemeen veel lagere restspanningen door het hete proces, maar een spanningsontlastingscyclus kan nog steeds nuttig zijn, afhankelijk van de legering en geometrie.
- Verwijdering van bouwplaat:
- Doel: Haal de geprinte motorbehuizing(en) los van de metalen bouwplaat waar ze op gesmolten zijn tijdens het printen.
- Methoden: Dit gebeurt meestal met behulp van draadvonken (Electrical Discharge Machining) of een lintzaag. De onderdelen mogen niet beschadigd raken.
- Belangrijk: Een noodzakelijke stap om de onderdelen vrij te maken voor verdere verwerking.
- Draagstructuur verwijderen:
- Doel: Verwijder de tijdelijke ondersteuningsstructuren die nodig zijn tijdens het bouwproces.
- Methoden: Dit kan variëren van eenvoudig handmatig breken (voor gemakkelijk bereikbare, lichte steunen) tot snijden met handgereedschap, CNC-bewerking of soms draadvonkmachines voor kwetsbare of moeilijk bereikbare steunen.
- Belangrijk: De steunen zijn niet functioneel en moeten verwijderd worden. Deze stap kan arbeidsintensief zijn en vereist vaardigheid om het oppervlak van het onderdeel niet te beschadigen, vooral bij complexe behuizingen met interne steunen. DfAM-strategieën zijn gericht op het minimaliseren van steunen.
- Heet isostatisch persen (HIP) - Optioneel maar vaak aanbevolen:
- Doel: Het elimineren van interne porositeit (kleine holtes) die soms achterblijven na het AM proces, waardoor mechanische eigenschappen zoals vermoeiingssterkte, breuktaaiheid en vervormbaarheid verbeteren.
- Methoden: Het onderdeel wordt gelijktijdig onderworpen aan een hoge temperatuur (onder het smeltpunt) en een hoge druk van inert gas (meestal argon, ~100-200 MPa) in een speciaal HIP-vat. De druk doet de interne holtes instorten, waardoor het materiaal diffuus wordt gebonden over de holle interfaces.
- Belangrijk: Cruciaal voor kritieke, vermoeiingsgevoelige onderdelen die vaak voorkomen in de ruimtevaart en hoogwaardige motortoepassingen in de auto-industrie. Verbetert de materiaalconsistentie en betrouwbaarheid aanzienlijk. Wordt vaak gespecificeerd voor Ti-6Al-4V en IN718 onderdelen in veeleisende toepassingen. Het kan ook de eigenschappen van AlSi10Mg verbeteren.
- Oplosgloeien en veroudering Warmtebehandeling (Ontwikkeling van eigenschappen):
- Doel: De uiteindelijke gewenste microstructuur en mechanische eigenschappen (sterkte, hardheid, vervormbaarheid) van de legering ontwikkelen. Dit is te onderscheiden van spanningsontlasting.
- Methoden: Omvat specifieke warmtebehandelingscycli in meerdere fasen, aangepast aan de legering.
- AlSi10Mg: Typisch een T6-cyclus (oplosbehandeling rond 500-540 °C, afschrikken, dan kunstmatige veroudering rond 150-170 °C) om precipitatieharding te bereiken.
- Ti-6Al-4V: Vaak gegloeid (bijv. ~700-850°C, koel) voor betere vervormbaarheid en stabiliteit, of mogelijk oplossingsbehandeld en verouderd (STA) voor hogere sterkte. Specifieke cycli hangen af van het gebruik van LPBF of EBM en de gewenste eigenschappenbalans.
- IN718: Vereist een complexe cyclus, meestal oplossingsbehandeling (~950-980°C) gevolgd door een verouderingsproces in twee stappen (~720°C en dan ~620°C) om versterkende fasen neer te slaan (gamma-prime en gamma-dubbel-prime).
- Belangrijk: Absoluut essentieel om de mechanische doelspecificaties te bereiken die in de materiaalinformatiebladen worden vermeld. Zonder de juiste warmtebehandeling zal het materiaal zoals het gebouwd of spanningsarm is niet optimaal sterk zijn of niet optimaal presteren.
- CNC-bewerking:
- Doel: Krappe toleranties, nauwkeurige geometrieën en gladde oppervlakafwerkingen bereiken op kritieke onderdelen waaraan niet kan worden voldaan met het AM proces zoals het is gebouwd.
- Methoden: Standaard CNC frezen, draaien, boren, tappen en slijpen. Vereist zorgvuldig ontwerp van de opspanning om het complexe AM-onderdeel stevig vast te houden zonder vervorming.
- Belangrijk: Nodig voor pasvlakken, lagerboringen, vlakheid van cilinderdeksels, afdichtingsgroeven, schroefgaten en alle voorzieningen die een hoge nauwkeurigheid vereisen voor assemblage en werking.
- Oppervlakteafwerking en -reiniging:
- Doel: Bereik de uiteindelijke gewenste oppervlaktestructuur, reinig het onderdeel grondig en breng eventueel beschermende of functionele coatings aan.
- Methoden: Zoals eerder besproken (stralen, tuimelen, polijsten). Gevolgd door grondige reiniging en inspectie om er zeker van te zijn dat er geen verontreinigingen, bewerkingsspanen of restpoeder achterblijft, vooral in interne doorgangen. Afhankelijk van de toepassing kunnen oppervlaktecoatings (bijvoorbeeld anodiseren voor aluminium, speciale slijtvaste of thermische barrièrecoatings) worden aangebracht.
- Belangrijk: Heeft invloed op esthetiek, corrosiebestendigheid, slijtvastheid, levensduur en vloeistofdynamica in de doorgangen. Eindschoonmaak is cruciaal voor de interne onderdelen van de motor.
Geïntegreerde aanpak:
Het beheren van deze multi-step workflow vereist expertise en coördinatie. Bedrijven zoals Met3dp, die gespecialiseerd zijn in printers en poeders, begrijpen deze hele waardeketen en kunnen vaak advies geven over of helpen bij het beheren van deze post-processing stappen door middel van partnerschappen, om ervoor te zorgen dat de uiteindelijke motorbehuizing aan alle specificaties voldoet. Inkoopmanagers moeten rekening houden met de kosten en doorlooptijd van deze essentiële stappen in hun algehele projectplanning wanneer ze metaal-AM overwegen.
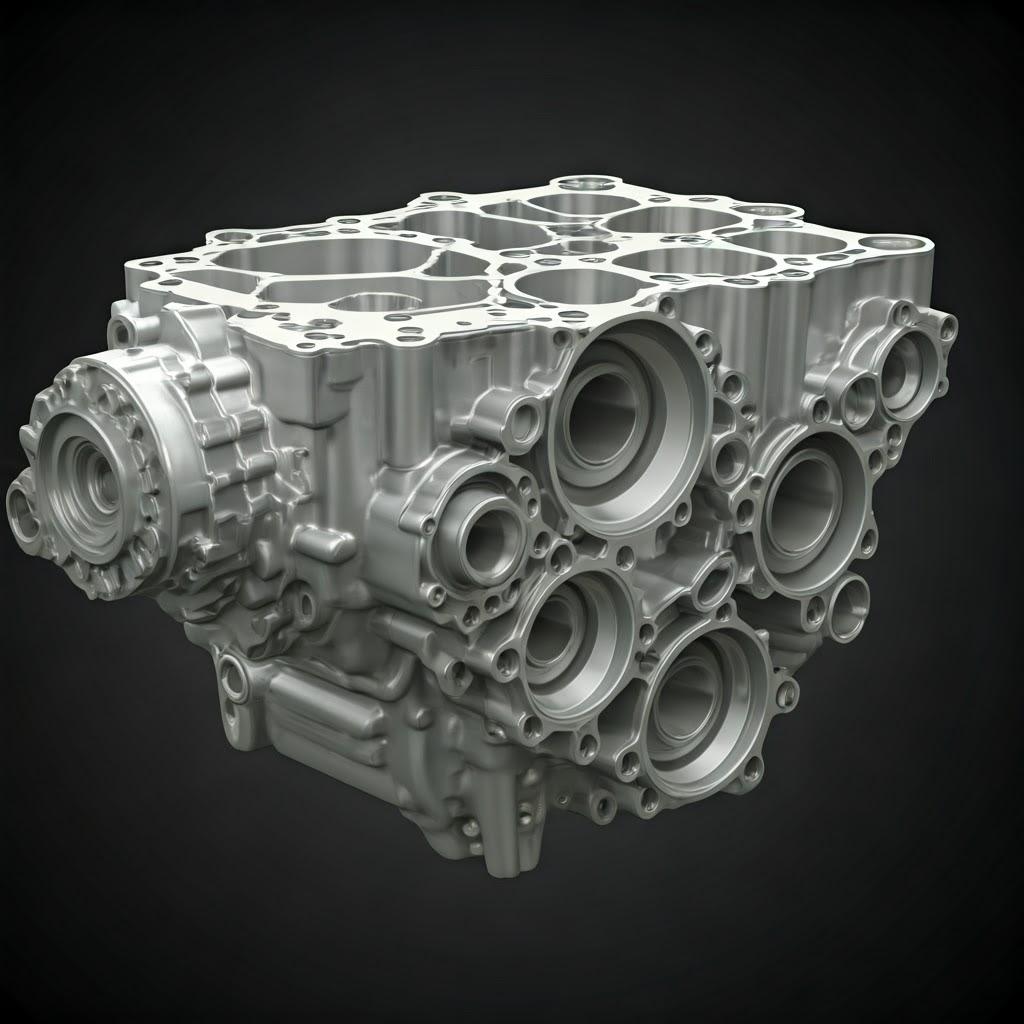
Veelvoorkomende uitdagingen bij het 3D printen van motorhuizen en strategieën om ze te beperken
Hoewel additive manufacturing van metaal een transformerend potentieel biedt voor motorhuizen, is het niet zonder uitdagingen. Ingenieurs, operators en inkoopmanagers moeten zich bewust zijn van mogelijke problemen die zich kunnen voordoen tijdens de print- en post-processingfasen. Inzicht in deze uitdagingen maakt proactieve beperking mogelijk door middel van zorgvuldig ontwerp (DfAM), strenge procescontrole, de juiste materiaalselectie en het benutten van de expertise van ervaren AM-leveranciers zoals Met3dp. Het succesvol omgaan met deze hindernissen is de sleutel tot het realiseren van de kwaliteit, prestaties en kostenvoordelen van AM-technologie.
Gemeenschappelijke uitdagingen en risicobeperkende strategieën:
- Restspanning, kromtrekken en scheuren:
- Uitdaging: De intense, plaatselijke verhitting en snelle afkoeling die inherent zijn aan poederbedfusieprocessen (vooral LPBF) genereren aanzienlijke thermische gradiënten, wat leidt tot interne spanningen in het onderdeel. Deze spanningen kunnen kromtrekken (vervorming ten opzichte van de bedoelde geometrie), loskomen van de bouwplaat of zelfs scheuren veroorzaken, vooral bij grote onderdelen, complexe geometrieën of materialen die gevoelig zijn voor warmscheuren (zoals sommige aluminiumlegeringen of nikkelsuperlegeringen als ze niet op de juiste manier worden verwerkt).
- Matigingsstrategieën:
- Proces selecteren: Elektronenstraalsmelten (EBM/SEBM), dat werkt bij verhoogde temperaturen in een vacuüm (bijv. >600°C voor Ti-6Al-4V), vermindert de thermische gradiënten en restspanning aanzienlijk in vergelijking met LPBF, waardoor het voordelig is voor grote titanium of spanningsgevoelige onderdelen. De focus van Met3dp op SEBM-technologie richt zich direct op deze uitdaging voor relevante materialen.
- Geoptimaliseerde bouwparameters: Het nauwkeurig afstellen van het vermogen van de laser/elektronenbundel, de scansnelheid, de scanstrategie (bijv. eiland scannen, laagrotatie) en de laagdikte kan spanningsopbouw minimaliseren.
- Bouwplaatverwarming (LPBF): Door de bouwplaat voor te verwarmen (tot 200°C of soms hoger voor specifieke materialen) wordt het temperatuurverschil tussen het gestolde materiaal en het omringende poederbed/-plaat verkleind, waardoor de spanning afneemt.
- Slimme ondersteuningsstrategie: Goed ontworpen ondersteuningsstructuren fungeren als koellichamen en ankers en helpen thermische spanningen te beheersen en kromtrekken te voorkomen. Softwaresimulatie kan helpen om de plaatsing van de ondersteuning te optimaliseren.
- DfAM: Onderdelen ontwerpen met geleidelijke overgangen, grote massieve blokken vermijden en spanningsverlagende functies inbouwen kan helpen.
- Onmiddellijke stressverlichting na de bouw: Uitvoeren van een warmtebehandelingscyclus met spanningsontlasting voor Het verwijderen van het onderdeel van de bouwplaat is cruciaal voor LPBF-onderdelen om vervorming of barsten bij het loslaten te voorkomen.
- Moeilijkheden bij het verwijderen van de steunstructuur:
- Uitdaging: Ondersteunende structuren zijn weliswaar noodzakelijk, maar brengen extra kosten met zich mee (materiaal, tijd) en moeten verwijderd worden. Het verwijderen van steunen uit interne kanalen, ingewikkelde geometrieën of kwetsbare onderdelen zonder het oppervlak van het onderdeel te beschadigen kan erg moeilijk, tijdrovend en duur zijn. Onbereikbare interne steunen kunnen onmogelijk volledig te verwijderen zijn.
- Matigingsstrategieën:
- DfAM voor zelfvoorziening: Geef voorrang aan het ontwerpen van onderdelen met zelfdragende hoeken (>45° in het algemeen, maar materiaal-/machinespecifiek), het gebruik van elementen zoals afschuiningen en vullingen en het kiezen van een optimale bouworiëntatie. Ontwerp interne kanalen met traan- of ruitvormen.
- Geoptimaliseerd steunontwerp: Gebruik software voor het maken van steunen om steunen te maken die sterk genoeg zijn tijdens het bouwen, maar gemakkelijker te verwijderen (bijv. kleinere contactpunten, geperforeerde structuren). Gespecialiseerde steunen (bijv. boomsteunen) kunnen de toegankelijkheid verbeteren.
- Toegankelijkheidsplanning: Zorg ervoor dat ontwerpen fysieke toegang of toegang met gereedschap mogelijk maken voor het verwijderen van steunen. Als interne steunen onvermijdelijk zijn, moet bij het ontwerp zorgvuldig worden nagedacht over hoe ze worden verwijderd (bijv. chemisch etsen - zeldzaam voor deze structurele metalen, toegang voor machinale bewerking).
- Proceskeuze: Voor sommige processen zijn minder steunen nodig voor bepaalde geometrieën (EBM heeft bijvoorbeeld soms minder steunen nodig dan LPBF vanwege het sinteren met poeder).
- Poederverwijdering uit interne kanalen:
- Uitdaging: Motorhuizen bevatten vaak complexe interne doorgangen voor koelvloeistof of smeermiddel. Ervoor zorgen dat al het ongesmolten metaalpoeder uit deze kanalen wordt verwijderd na het printen is essentieel voor de functionaliteit, maar kan een enorme uitdaging zijn, vooral voor lange, smalle of kronkelige doorgangen. Gevangen poeder kan de doorstroming blokkeren of tijdens het gebruik losraken, wat catastrofale motorstoringen kan veroorzaken.
- Matigingsstrategieën:
- DfAM voor De-Powdering: Ontwerp interne kanalen met soepele overgangen, vermijd scherpe hoeken of dode uiteinden waar poeder zich kan ophopen. Zorg voor voldoende inlaat- en uitlaatpoorten (mogelijk groter dan functioneel vereist en later afgedicht/bewerkt) om poederevacuatie en inspectietoegang mogelijk te maken. Overweeg minimale kanaaldiameters op basis van de grootte van de poederdeeltjes en de mogelijkheden om poeder te verwijderen (vaak >1-2 mm nodig).
- Geoptimaliseerde oriëntatie: Richt het onderdeel op de bouwplaat om de poederafvoer met behulp van de zwaartekracht te vergemakkelijken.
- Effectieve ontpoederingsprocedures: Gebruik meerassige rotatie-/vibratiestations, gerichte perslucht-/inertgasstralen en mogelijk ultrasone reiniging in geschikte vloeistoffen.
- Inspectie: Gebruik niet-destructieve methoden zoals CT-scannen (computertomografie) of boorscopische inspectie om te controleren of het poeder in kritieke doorgangen volledig is verwijderd.
- Poreusheid en materiaaldefecten:
- Uitdaging: Onvolledige versmelting tussen lagen of gasinsluiting tijdens het smelten kan leiden tot microscopische holtes (porositeit) in het geprinte materiaal. Een hoge porositeit tast de mechanische eigenschappen aan, vooral de vermoeiingssterkte en breuktaaiheid. Andere defecten zoals insluitsels (van vervuild poeder) of gebrekkige fusiezones kunnen ook voorkomen.
- Matigingsstrategieën:
- Hoogwaardig poeder: Het gebruik van hoogzuiver, sferisch poeder met een consistente deeltjesgrootteverdeling en goede vloeibaarheid is van het grootste belang. De geavanceerde gasatomisatie- en PREP-processen van Met3dp zijn ontworpen om dergelijke poeders te produceren, waarbij de gasporositeit die inherent is aan de grondstof wordt geminimaliseerd. Zorgvuldige poederbehandeling en recyclingprotocollen zijn ook cruciaal om verontreiniging te voorkomen.
- Geoptimaliseerde procesparameters: Het ontwikkelen en strikt controleren van geoptimaliseerde parameters (bundelvermogen, snelheid, focus, laagdikte, atmosfeerregeling) voor elke specifieke materiaal- en machinecombinatie is de sleutel tot het verkrijgen van dichte (>99,5%, vaak >99,9%) onderdelen.
- Heet isostatisch persen (HIP): Zoals vermeld bij nabewerking is HIP zeer effectief bij het sluiten van interne gasporositeit en het verbeteren van de dichtheid en mechanische eigenschappen. Het is vaak een standaardvereiste voor kritieke AM-onderdelen voor de ruimtevaart en de medische sector.
- Kwaliteitscontrole en NDO: Het implementeren van strenge kwaliteitscontroles, inclusief poederanalyse, smeltbadbewaking (waar beschikbaar) en niet-destructieve testen (NDT) zoals CT-scans of ultrasone testen op afgewerkte onderdelen, helpt bij het opsporen en voorkomen van defecten.
- Kosten en doorlooptijd:
- Uitdaging: Hoewel het op lange termijn voordelen biedt, kunnen de initiële kosten per onderdeel voor metaal-AM hoger zijn dan traditionele methoden, vooral voor grotere onderdelen of grotere volumes, vanwege de dure machines, materialen en uitgebreide nabewerking. Doorlooptijden kunnen ook langer zijn dan verwacht als de hele workflow niet efficiënt wordt beheerd.
- Matigingsstrategieën:
- Ontwerpoptimalisatie (DfAM): Het maximaliseren van het gewicht, het consolideren van onderdelen en het ontwerpen voor minimale ondersteuningen/nabewerking vermindert direct het materiaalverbruik, de printtijd en de arbeidskosten.
- Nesting en bouwoptimalisatie: Meerdere onderdelen tegelijk printen op een enkele bouwplaat (nesting) verbetert het machinegebruik en verlaagt de kosten per onderdeel.
- Gerichte toepassingsselectie: AM richten op toepassingen waar de unieke voordelen (complexiteit, lichtgewicht, maatwerk, consolidatie) de hoogste waarde bieden, in plaats van te proberen kosteneffectieve traditionele methoden te vervangen voor eenvoudige onderdelen in grote volumes.
- Samenwerken met ervaren aanbieders: Werken met efficiënte, ervaren serviceproviders zoals Met3dp, die hun workflows hebben geoptimaliseerd en inzicht hebben in kostenfactoren, kan helpen bij het beheren van uitgaven en zorgen voor realistische schattingen van doorlooptijden. Open communicatie met inkoopteams over kostenverdelingen is van vitaal belang.
Door deze uitdagingen te erkennen en robuuste strategieën te implementeren die gebaseerd zijn op gezonde DfAM-principes, nauwgezette procesbeheersing en sterke partnerschappen, kunnen fabrikanten vol vertrouwen gebruikmaken van additieve metaalproductie om hoogwaardige motorbehuizingen te produceren voor de veeleisende vereisten van de lucht- en ruimtevaart, de auto-industrie en de industrie.
Uw partner voor metaal 3D printen kiezen: Het evalueren van dienstverleners en leveranciers
Voor het succesvol implementeren van additive manufacturing van metaal voor kritieke onderdelen zoals motorhuizen is meer nodig dan alleen toegang tot een printer; het vereist een strategisch partnerschap met een bekwame en betrouwbare serviceprovider of leverancier. De juiste partner fungeert als een verlengstuk van uw engineering- en inkoopteams en biedt technische expertise, robuuste processen, consistente kwaliteit en betrouwbare levering. Voor B2B inkopers, groothandelaren en inkoopmanagers die door het groeiende landschap van AM leveranciers navigeren, is het evalueren van potentiële partners op basis van een gedefinieerde set criteria essentieel om risico's te beperken en projectsucces te garanderen. Een verstandige keuze betekent verder kijken dan alleen de opgegeven prijs om de algehele capaciteiten, kwaliteitssystemen en geschiktheid voor uw specifieke branche en toepassingsbehoeften te beoordelen.
Belangrijkste criteria voor het evalueren van Metal AM-partners:
- Technische expertise en toepassingsondersteuning:
- Beoordeling: Heeft de leverancier diepgaande kennis van het specifieke AM-proces (LPBF, EBM/SEBM), de materialen (AlSi10Mg, Ti-6Al-4V, IN718) en hun gedrag? Bieden ze Design for Additive Manufacturing (DfAM) ondersteuning om het ontwerp van uw motorbehuizing te optimaliseren voor printbaarheid, prestaties en kosteneffectiviteit? Kunnen ze advies geven over de afweging van materiaalselectie? Hebben ze ingenieurs met ervaring in uw bedrijfstak (lucht- en ruimtevaart, auto-industrie, industrie)?
- Waarom het belangrijk is: Motorbehuizingen zijn complexe onderdelen. Een partner met een sterke technische diepgang kan helpen om kostbare ontwerpfouten te voorkomen, de prestaties te optimaliseren, problemen op te lossen en ervoor te zorgen dat het onderdeel voldoet aan de functionele eisen. Aanbieders zoals Met3dp, met tientallen jaren collectieve expertise in metaal-AM op het gebied van materiaalkunde, procestechniek en applicatieontwikkeling, bieden hier aanzienlijke waarde.
- Machinepark & Technologie:
- Beoordeling: Met welke types en merken metaal AM-systemen werken ze? Hebben ze de juiste technologie (bijv. LPBF voor fijne vormen, EBM/SEBM voor titanium onderdelen met lage spanning) voor uw specifieke behuizingsbehoeften? Wat is hun machinecapaciteit (bouwvolume, aantal machines) om uw projectgrootte en potentiële productievolumes aan te kunnen? Zijn hun machines goed onderhouden en gekalibreerd?
- Waarom het belangrijk is: De specifieke technologie heeft invloed op haalbare eigenschappen, toleranties, oppervlakteafwerking en materiaaleigenschappen. Voldoende capaciteit zorgt voor redelijke doorlooptijden en schaalbaarheid. Aanbieders die investeren in toonaangevende apparatuur, zoals Met3dp's focus op systemen die een hoog printvolume, nauwkeurigheid en betrouwbaarheid leveren, laten zien dat ze zich inzetten voor kwaliteitsproductie.
- Materiaalportefeuille & Powder Quality Control:
- Beoordeling: Biedt de leverancier de specifieke legeringen die nodig zijn voor uw motorbehuizing (bijv. AlSi10Mg, Ti-6Al-4V, IN718)? Van cruciaal belang is: wat zijn hun processen voor het betrekken, verwerken, opslaan en recyclen van metaalpoeders? Hebben ze een robuuste kwaliteitscontrole voor binnenkomend poeder (bijv. chemische analyse, deeltjesgrootteverdeling, morfologie, vloeibaarheid)? Kunnen ze materiaalcertificeringen en traceerbaarheid leveren?
- Waarom het belangrijk is: De kwaliteit van het uiteindelijke geprinte onderdeel is fundamenteel afhankelijk van de kwaliteit van de poedergrondstof. Inconsistent of verontreinigd poeder leidt tot defecten en slechte mechanische eigenschappen. Bedrijven zoals Met3dp, die vervaardigen hun eigen hoogwaardige metaalpoeders met behulp van geavanceerde technieken zoals gasverstuiving en PREP, bieden superieure controle over de poederkwaliteit en -consistentie, wat meer zekerheid biedt voor kritieke toepassingen.
- Kwaliteitsbeheersysteem & certificeringen:
- Beoordeling: Werkt de aanbieder met een gecertificeerd kwaliteitsbeheersysteem (QMS)? Essentiële certificeringen zijn ISO 9001 (algemeen kwaliteitsmanagement). Voor luchtvaarttoepassingen is AS9100 meestal verplicht. Voor medische toepassingen kan ISO 13485 relevant zijn (hoewel dit minder geldt voor motorhuizen). Staan ze open voor audits? Wat zijn hun interne procedures voor kwaliteitscontrole tijdens en na de bouw?
- Waarom het belangrijk is: Certificeringen laten zien dat ze zich inzetten voor gestandaardiseerde processen, traceerbaarheid en voortdurende verbetering, waardoor ze vertrouwen geven in de betrouwbaarheid en herhaalbaarheid van hun productieprocessen. Dit is ononderhandelbaar voor onderdelen die cruciaal zijn voor de veiligheid en essentieel voor gereguleerde industrieën.
- Mogelijkheden voor nabewerking:
- Beoordeling: Biedt de leverancier de noodzakelijke nabewerkingsstappen in-house aan (bijv. warmtebehandeling, steunverwijdering, basisafwerking) of beheert hij deze via een gekwalificeerd netwerk van partners (bijv. HIP, CNC-verspaning, NDT, geavanceerde coating)? Hoe naadloos is deze integratie?
- Waarom het belangrijk is: Motorbehuizingen vereisen meerdere nabewerkingsstappen. Een partner die deze hele workflow kan beheren, vereenvoudigt de toeleveringsketen voor het inkoopteam en zorgt ervoor dat er tijdens het hele proces verantwoording wordt afgelegd. Inzicht in welke stappen intern worden uitgevoerd versus uitbesteed is belangrijk voor het beoordelen van de controle en mogelijke gevolgen voor de doorlooptijd.
- Track Record & Praktijkvoorbeelden:
- Beoordeling: Kan de leverancier succesvolle eerdere projecten aantonen, met name met componenten die qua complexiteit, materiaal of industrie vergelijkbaar zijn met uw motorbehuizing? Zijn ze bereid om casestudy's of referenties te delen (binnen de grenzen van vertrouwelijkheid)?
- Waarom het belangrijk is: Bewezen ervaring vermindert risico's. Bewijs van succesvolle uitvoering van soortgelijke projecten geeft vertrouwen in hun vermogen om aan uw eisen te voldoen.
- Communicatie, ondersteuning en transparantie:
- Beoordeling: Hoe ontvankelijk en communicatief is de leverancier tijdens de offerte- en projectbesprekingsfase? Zijn ze transparant over hun processen, mogelijkheden en mogelijke uitdagingen? Geven ze duidelijke projectupdates?
- Waarom het belangrijk is: Een sterke werkrelatie is gebaseerd op duidelijke, open communicatie. Dit is vooral belangrijk voor complexe AM projecten die iteratieve ontwerpaanpassingen of gezamenlijke probleemoplossing vereisen.
- Kosten en doorlooptijd:
- Beoordeling: Is hun prijsstelling concurrerend en transparant? Zijn de opgegeven doorlooptijden realistisch gezien de omvang van het werk (afdrukken en nabewerking)? Hoe verhouden ze zich tot andere gekwalificeerde leveranciers?
- Waarom het belangrijk is: Hoewel kosten altijd een factor zijn, moeten ze worden geëvalueerd in de context van kwaliteit, expertise en betrouwbaarheid. De goedkoopste offerte biedt misschien niet de beste waarde of het laagste risico. Zorg ervoor dat offertes duidelijk alle inbegrepen stappen beschrijven.
Tabel: Samenvatting checklist partnerevaluatie
Criteria | Sleutelvragen | Waarom het cruciaal is voor motorhuizen |
---|---|---|
Technische expertise | DfAM-ondersteuning? Materiaal-/proceskennis? Ervaring in de industrie? | Optimaliseert complexe ontwerpen, garandeert functionaliteit en voorkomt kostbare fouten. |
Machinepark/Techniek | Juiste proces (LPBF/EBM)? Volume opbouwen? Capaciteit? Machinekwaliteit? | Bepaalt haalbaarheid, kwaliteit, doorlooptijd, schaalbaarheid. |
Materiaal/poeder kwaliteit | Vereiste legeringen beschikbaar? Poeder QC? Traceerbaarheid? Leverancier vs. fabrikant (zoals Met3dp)? | Basis van onderdeelkwaliteit, mechanische eigenschappen, defectpreventie. |
Kwaliteitssysteem/certificaten | ISO 9001? AS9100 (indien luchtvaart)? Interne QC procedures? Auditeerbaar? | Zorgt voor procescontrole, herhaalbaarheid en naleving voor kritieke onderdelen. |
Nabewerking | Eigen capaciteiten? Beheerd netwerk? Workflow integratie? | Stroomlijnt complexe workflow, zorgt voor end-to-end kwaliteitsbeheer. |
Track record/casestudies | Relevante projectervaring? Referenties? | Vermindert risico's, geeft vertrouwen in uitvoeringsmogelijkheden. |
Communicatie/Ondersteuning | Verantwoordelijkheid? Transparantie? Potentieel tot samenwerking? | Zorgt voor een soepele projectuitvoering, lost problemen op. |
Kosten en doorlooptijd | Concurrerende & transparante prijzen? Realistische levertijden? Gedetailleerde offertes? | Balanceert budget met kwaliteit, betrouwbaarheid en time-to-market behoeften. |
Exporteren naar Sheets
Het selecteren van de juiste metaal-AM partner is een kritieke strategische beslissing. Door potentiële leveranciers grondig te evalueren aan de hand van deze criteria en zich te richten op leveranciers zoals Met3dp die end-to-end capaciteiten laten zien, van geavanceerde poederproductie tot betrouwbare printsystemen en toepassingsondersteuning, kunnen bedrijven de sterke partnerschappen opbouwen die nodig zijn om additive manufacturing met succes in te zetten voor hoogwaardige onderdelen zoals motorhuizen.
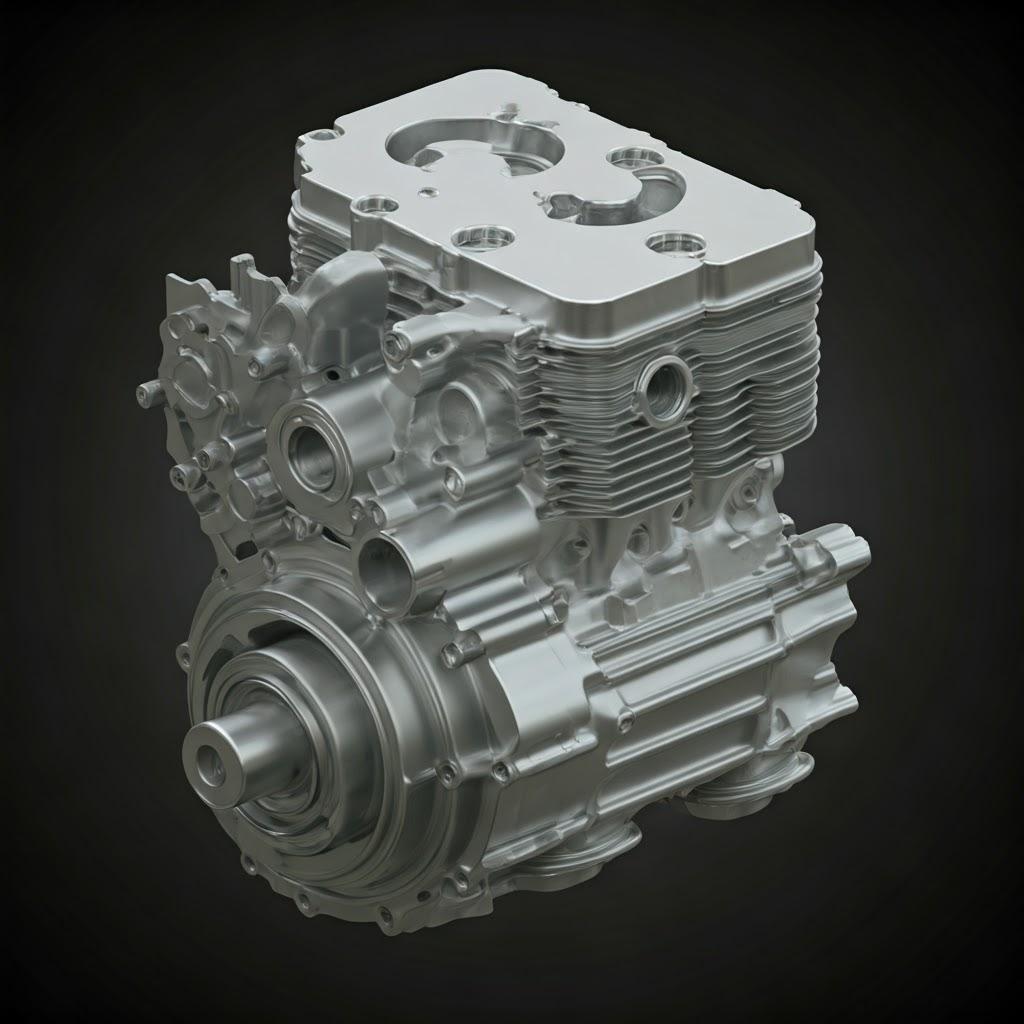
Inzicht in kostenfactoren en doorlooptijden voor 3D-geprinte motorhuizen
Een van de meest voorkomende vragen van ingenieurs en inkoopmanagers die additive manufacturing van metaal voor motorhuizen overwegen, draait om kosten en doorlooptijd. Hoewel AM aanzienlijke voordelen biedt in ontwerpvrijheid en potentiële waarde op lange termijn, is het cruciaal om de factoren te begrijpen die de prijsstructuur en productietijdlijnen bepalen in vergelijking met traditionele methoden. De kosten zijn niet simpelweg gebaseerd op gewicht; het is een complexe berekening die wordt beïnvloed door materiaalkeuze, machinegebruik, complexiteit van het onderdeel, arbeid en uitgebreide vereisten voor nabewerking. Ook doorlooptijden omvatten meer dan alleen de duur van het printen.
Primaire kostendrijvers voor metalen AM motorhuizen:
- Materiaalkosten:
- Prijs poeder: Metaalpoeders variëren aanzienlijk in prijs per kilogram. AlSi10Mg is relatief goedkoop, Ti-6Al-4V is aanzienlijk duurder en IN718 is meestal het duurste van de drie.
- Materiaalverbruik: Dit is inclusief het materiaal in het laatste deel plus het materiaal dat wordt gebruikt voor ondersteunende structuren. De inspanningen van DfAM om het aantal steunen te minimaliseren en het ontwerpvolume te optimaliseren, leiden direct tot een lager materiaalverbruik.
- Dikte: Dichtere materialen (zoals IN718) betekenen dat er meer kilo's nodig zijn voor hetzelfde volume in vergelijking met lichtere materialen (zoals AlSi10Mg).
- Poederrecycling: Efficiënte recycling van ongesmolten poeder helpt de totale materiaalkosten te verlagen, maar vereist een zorgvuldige kwaliteitscontrole om afbraak of verontreiniging te voorkomen. Ervaren leveranciers hebben geoptimaliseerde recyclingprotocollen.
- Machinetijd:
- Bouwvoorbereiding: Het instellen van de software, het voorbereiden van de bouwplaat en het laden/lossen van de machine dragen bij aan de totale tijd.
- Afdrukken tijd: Dit is vaak de grootste component van de machinetijd. Het hangt voornamelijk af van de deelhoogte (meer lagen = meer tijd), de volume van het materiaal dat per laag wordt gesmolten, de gekozen laagdikte en de scansnelheid/strategie. Complexe interne functies of uitgebreide ondersteuningsstructuren verlengen de printtijd.
- Koeltijd: Na het printen moet de bouwkamer afkoelen voordat de onderdelen veilig verwijderd kunnen worden, wat vooral belangrijk is bij het hoge-temperatuurproces van EBM.
- Machineafschrijvingen en overhead: De hoge kapitaalkosten van industriële metaal-AM-systemen zijn verdisconteerd in het uurtarief dat serviceproviders in rekening brengen.
- Arbeidskosten:
- Technicus Tijd: Er zijn bekwame technici nodig voor het instellen van de constructie, machinebediening, bewaking, ontpoederen, verwijderen van onderdelen, verwijderen van basisondersteuning en algemene bediening.
- Technische ondersteuning: DfAM-advies, procesplanning en engineering voor kwaliteitsborging dragen bij aan de arbeidscomponent.
- Arbeid na het verwerken: Handmatig steun verwijderen, oppervlakteafwerking (stralen, polijsten), inspectie en coördinatie van uitbestede stappen kunnen een aanzienlijke bijdrage leveren aan de arbeidskosten.
- Kosten voor nabewerking:
- Hittebehandeling: De oventijd, het energieverbruik en de gecontroleerde atmosfeer (vacuüm/inert gas) voor spanningsontlasting, HIP en de uiteindelijke behandeling van de eigenschappen brengen extra kosten met zich mee. HIP is een bijzonder gespecialiseerde en dure stap.
- Bewerking: De CNC bewerkingstijd voor kritische vormen hangt af van de hoeveelheid materiaal die verwijderd moet worden, de complexiteit van de vormen, de bewerkbaarheid van het materiaal (Ti-6Al-4V en IN718 zijn veel moeilijker te bewerken dan AlSi10Mg) en de opspanvereisten.
- Afwerking oppervlak: De kosten variëren afhankelijk van de methode (stralen is relatief goedkoop, uitgebreid polijsten is duur).
- Inspectie en kwaliteitsborging: Niet-destructief onderzoek (CT-scan, ultrasoon, penetrant), dimensionale inspectie (CMM) en materiaaltesten dragen bij aan de totale kosten, maar zijn essentieel voor kwaliteitsborging.
- Complexiteit en omvang van het onderdeel:
- Complexiteit: Hoewel AM uitblinkt in complexiteit, vereisen zeer ingewikkelde ontwerpen vaak meer ondersteunende structuren en een aanzienlijk uitdagender ontpopping en verwijdering van de ondersteuning, waardoor het werk en de risico's toenemen. Complexe interne kanalen kunnen geavanceerde inspectiemethoden vereisen.
- Grootte: Grotere onderdelen verbruiken meer materiaal en vereisen langere printtijden en mogelijk grotere, duurdere machines. Ze vormen ook een grotere uitdaging op het vlak van thermisch beheer en verwerking na het proces.
- Productievolume:
- Setup Afschrijving: Vaste setupkosten (bouwvoorbereiding) worden afgeschreven over het aantal onderdelen in een enkele bouw. Het printen van meerdere onderdelen (nesting) of grotere batches verlaagt over het algemeen de kosten per onderdeel.
- Kwantumkortingen: Voor doorlopende productie of grotere groothandelbestellingen kunnen leveranciers volumekortingen aanbieden op materialen en verwerking.
Tabel: Overzicht kostenfactoren
Kosten Categorie | Belangrijkste invloeden | Invloed op de kosten van motorhuisvesting |
---|---|---|
Materiaal | Poederprijs (Al < Ti < IN718), Deelvolume, Supportvolume, Dichtheid, Recycling | Belangrijke driver, vooral voor Ti & IN718. |
Machinetijd | Deelhoogte, Volume/complexiteit per laag, Machinesnelheid, Koeltijd | Belangrijke kostencomponent, direct gerelateerd aan de bouwtijd. |
Werk | Setup, Bediening, Ontpoederen, Verwijderen van ondersteuning, Afwerking, QA Engineering | Significant, vooral voor complexe onderdelen die veel handling vereisen. |
Nabewerking | Typen warmtebehandeling (HIP is duur), omvang en moeilijkheidsgraad machinale bewerking, afwerking | Kan 50% of meer van de totale kosten vertegenwoordigen. |
Complexiteit/Grootte | Intriciteit (steunen, reiniging), Totale afmetingen | Heeft invloed op materiaalgebruik, printtijd, arbeid en verwerkingskosten. |
Volume | Aantal onderdelen per build, Totale bestelhoeveelheid | Setup-afschrijving en potentiële kortingen verlagen de kosten per onderdeel. |
Exporteren naar Sheets
Overwegingen met betrekking tot doorlooptijd:
De totale doorlooptijd van een 3D-geprinte motorbehuizing is de som van verschillende stappen:
- Offerte en beoordeling ontwerp (1-5 dagen): Eerste dossierbeoordeling, DfAM-beoordeling/feedback, offerte maken.
- Orderbevestiging en planning (1-3 dagen): Afronden van ordergegevens en inplannen van de productie in de wachtrij voor machines.
- Bouwvoorbereiding en afdrukken (2 dagen - 2+ weken): Afhankelijk van de grootte van het onderdeel, de complexiteit, het aantal geneste onderdelen en de beschikbaarheid van de machine. Het printen zelf kan vele dagen duren voor grote/complexe behuizingen.
- Afkoelen en ontpoederen (1-2 dagen): Noodzakelijke afkoelingsperiode gevolgd door poederverwijdering.
- Nabewerking (1 - 4+ weken): Dit is vaak de meest variabele en mogelijk langste fase. Ze omvat:
- Ontspanning door stress (1-2 dagen)
- Bouwplaat verwijderen / steun verwijderen (1-3 dagen, afhankelijk van complexiteit)
- HIP (indien nodig, betekent vaak dat onderdelen moeten worden opgestuurd, waardoor de logistiek 1-2 weken langer duurt)
- Laatste warmtebehandeling (2-5 dagen, afhankelijk van de complexiteit van de cyclus)
- CNC-bewerking (2 dagen - 2+ weken, afhankelijk van complexiteit en planning machinewerkplaats)
- Afwerking en inspectie (1-5 dagen)
- Verzending (1-5 dagen): Afhankelijk van locatie en methode.
Totale geschatte levertijd: Voor een complexe metalen AM motorbehuizing die volledige nabewerking vereist, kunnen typische doorlooptijden variëren van 4 weken tot 10 weken of meer. Prototypes met minimale nabewerking kunnen sneller zijn (2-4 weken), terwijl voor luchtvaart gecertificeerde onderdelen die uitgebreide QA en gespecialiseerde nabewerking vereisen waarschijnlijk meer tijd nodig hebben.
Werken met Met3dp:
Ervaren leveranciers zoals Met3dp begrijpen deze kosten- en doorlooptijdfactoren. Ze kunnen gedetailleerde, transparante offertes leveren waarin alle stappen worden beschreven en ze werken samen met klanten om ontwerpen en processen te optimaliseren voor efficiëntie. Hun geïntegreerde aanpak, die poederproductie van hoge kwaliteit, betrouwbare printsystemen en applicatie-expertise combineert, is gericht op het stroomlijnen van de workflow en het leveren van hoogwaardige componenten binnen voorspelbare tijdsbestekken. Duidelijke communicatie met de gekozen AM-partner over specifieke vereisten en deadlines is cruciaal voor effectief projectmanagement.
Veelgestelde vragen (FAQ) over 3D-geprinte motorhuizen
Nu additive manufacturing van metaal steeds meer wordt toegepast voor functionele onderdelen, hebben ingenieurs en inkoopmanagers vaak specifieke vragen over de toepassing ervan op motorhuizen. Hier zijn antwoorden op een aantal veelgestelde vragen:
1. Is 3D-geprint metaal net zo sterk en betrouwbaar als metalen onderdelen die zijn gemaakt door gieten of smeden?
- Antwoord: Ja, absoluut. Wanneer geproduceerd met behulp van geoptimaliseerde procesparameters, hoogwaardige metaalpoeders (zoals die geproduceerd door Met3dp) en de juiste nabewerking (met name warmtebehandelingen zoals spanningsontlasting, HIP en oplossings-/verouderingscycli), kunnen metalen AM-onderdelen mechanische eigenschappen bereiken (treksterkte, vloeigrens, vermoeiingssterkte, hardheid) die vergelijkbaar zijn met, en soms zelfs superieur aan, die van gesmede of gegoten materialen. Ti-6Al-4V geproduceerd via AM kan bijvoorbeeld voldoen aan de ASTM-normen voor gegoten en gesmede equivalenten of deze zelfs overtreffen. De sleutel is strenge procescontrole, de juiste warmtebehandeling op maat van de legering (bijvoorbeeld T6 voor AlSi10Mg, specifieke cycli voor Ti-6Al-4V en IN718) en kwaliteitsborgingsmaatregelen zoals HIP om porositeit te minimaliseren voor kritieke toepassingen. Het is cruciaal om te werken met ervaren leveranciers die verstand hebben van materiaalwetenschappen en procesoptimalisatie om ervoor te zorgen dat het uiteindelijke onderdeel voldoet aan de vereiste specificaties voor betrouwbaarheid en duurzaamheid in veeleisende motoromgevingen of deze zelfs overtreft.
2. Kunnen grote motoronderdelen, zoals een volledig V8 motorblok, 3D-geprint worden?
- Antwoord: Technisch gezien, ja, het wordt steeds haalbaarder. Fabrikanten van metaal AM machines ontwikkelen voortdurend systemen met grotere bouwvolumes die in staat zijn om grote onderdelen te printen. Er zijn bijvoorbeeld bouwvolumes beschikbaar van meer dan 500mm x 500mm x 500mm en er bestaan zelfs nog grotere systemen op maat. Met3dp biedt printers met toonaangevende printvolumes die geschikt zijn voor grote onderdelen. Voor zeer grote behuizingen moeten echter verschillende factoren in overweging worden genomen:
- Kosten: Het printen van zeer grote volumes verbruikt aanzienlijke hoeveelheden duur poeder en vereist veel machinetijd, waardoor de kosten potentieel onbetaalbaar zijn in vergelijking met traditioneel gieten voor standaardproductie, tenzij de voordelen (bijv. extreem lichtgewicht, geïntegreerde complexe functies voor hoge prestaties) de kosten rechtvaardigen.
- Afdruktijd: De bouwtijden voor zeer grote, massieve of complexe onderdelen kunnen oplopen tot weken.
- Thermisch beheer: Het beheersen van restspanningen en potentiële vervorming wordt een grotere uitdaging bij grotere onderdelen, waardoor processen zoals EBM/SEBM (met de verwarmde kamer) mogelijk voordeliger zijn of een zeer zorgvuldig ontwerp van LPBF-parameters en ondersteuningsstrategieën vereisen.
- Nabewerking: Voor het hanteren, warmtebehandelen en bewerken van zeer grote AM onderdelen is gespecialiseerde apparatuur nodig.
- Alternatief: Voor sommige zeer grote constructies zou een alternatieve aanpak kunnen zijn om kleinere secties te printen die optimaal ontworpen zijn voor AM en deze vervolgens samen te voegen met conventionele methoden zoals lassen, hoewel dit assemblagestappen toevoegt. De haalbaarheid en kosteneffectiviteit moeten per geval zorgvuldig worden geëvalueerd.
3. Hoe verhouden de kosten van een 3D-geprint motorhuis zich tot die van een traditioneel gegoten motorhuis?
- Antwoord: Er is geen eenduidig antwoord, omdat dit sterk afhangt van verschillende factoren:
- Volume: Voor zeer hoge productievolumes (duizenden of tienduizenden) biedt traditioneel gieten (vooral spuitgieten) meestal lagere kosten per onderdeel door schaalvoordelen, ondanks de hoge initiële gereedschapskosten. Voor lage volumes (prototypes, aangepaste onderdelen, kleine serieproductie tot een paar honderd stuks) is metaal AM vaak aanzienlijk kosteneffectiever omdat er geen duur gereedschap (mallen/dieptrekvormen) nodig is.
- Complexiteit: AM blinkt uit in complexe geometrieën. Als het ontwerp ingewikkelde interne kanalen, topologie-optimalisatie of geconsolideerde kenmerken bevat die moeilijk of onmogelijk te gieten zijn, kan AM kosteneffectiever zijn, zelfs bij bescheiden volumes, omdat het complexe kernpakketten, meerdere bewerkingssets of assemblagestappen vermijdt die nodig zijn voor het gegoten equivalent.
- Materiaal: Voor dure materialen zoals Ti-6Al-4V of IN718 kan het bijna-netvorm proces van AM leiden tot een beter materiaalgebruik (minder afval) in vergelijking met het machinaal bewerken van billets, wat kostenbesparingen kan opleveren ondanks de hogere initiële poederkosten.
- Doorlooptijd en flexibiliteit: AM biedt veel kortere doorlooptijden voor initiële onderdelen (geen vertraging bij het bewerken) en maakt snelle iteratie van ontwerpen mogelijk, wat een aanzienlijke economische waarde heeft in R&D-fasen of tijdgevoelige projecten.
- Totale gebruikskosten: Bij het overwegen van lichtgewicht voordelen (brandstofbesparing gedurende de levensduur), prestatieverbeteringen (betere koeling) of vereenvoudiging van de toeleveringsketen (digitale voorraad, minder assemblage), is de totale eigendomskosten voor een AM-onderdeel lager kan zijn dan een traditioneel vervaardigd onderdeel, zelfs als de initiële aankoopprijs hoger is.
- Break-Even punt: Er is meestal een break-even volume waaronder AM goedkoper is en waarboven gieten goedkoper wordt (voor ontwerpen die geschikt zijn voor beide). Dit punt varieert sterk afhankelijk van complexiteit en materiaal. Een gedetailleerde kostenanalyse waarbij AM (inclusief alle nabewerkingen) wordt vergeleken met traditionele methoden (gereedschap + onderdeelkosten + machinale bewerking + assemblage) is nodig voor specifieke gevallen.
4. Welke kwaliteitscertificaten zijn het belangrijkst bij het kiezen van een leverancier voor 3D-geprinte motorbehuizingen van luchtvaartkwaliteit?
- Antwoord: Voor ruimtevaarttoepassingen zijn kwaliteit en traceerbaarheid van het grootste belang. De belangrijkste certificeringen voor een AM-metaalleverancier zijn onder andere:
- AS9100: Dit is de gestandaardiseerde Quality Management System-eis voor de luchtvaartindustrie. Het bevat ISO 9001 vereisten en voegt specifieke criteria toe met betrekking tot veiligheid, betrouwbaarheid, luchtwaardigheid en traceerbaarheid die cruciaal zijn voor luchtvaartonderdelen. Naleving is over het algemeen verplicht voor leveranciers die vluchtkritieke of primaire structurele onderdelen produceren.
- ISO 9001: Hoewel AS9100 de voorkeur heeft voor luchtvaart, toont ISO 9001-certificering een fundamentele toewijding aan principes voor kwaliteitsmanagement, procesbeheersing en documentatie, wat een essentiële basis is voor geloofwaardigheid.
- NADCAP (National Aerospace and Defense Contractors Accreditation Program): Terwijl AS9100 betrekking heeft op het algehele QMS, biedt NADCAP specifieke accreditatie voor speciale processen. Relevante NADCAP-accreditaties voor een AM-workflow zijn bijvoorbeeld warmtebehandeling, niet-destructief testen (NDT), materiaaltestlaboratoria en mogelijk lassen (als AM-onderdelen worden samengevoegd). Leveranciers hebben accreditatie nodig voor de specifieke processen die ze uitvoeren of beheren.
- Specifieke goedkeuringen van klanten: Grote luchtvaart-OEM's (Original Equipment Manufacturers) hebben vaak hun eigen aanvullende kwalificatievereisten voor leveranciers en lijsten van goedgekeurde leveranciers.
Ervoor zorgen dat de gekozen partner over de nodige certificeringen beschikt, geeft het vertrouwen dat hij voldoet aan de strenge normen voor kwaliteitscontrole, procesvalidatie en traceerbaarheid die de luchtvaartindustrie eist voor onderdelen zoals motorbehuizingen.
Conclusie: De toekomst van de productie van motorhuizen is additief
De reis door de fijne kneepjes van metaal additive manufacturing voor motorbehuizingen onthult een technologie die zich duidelijk voorbij rapid prototyping heeft bewogen naar het rijk van geavanceerde productie voor veeleisende eindgebruikerstoepassingen. Voor ingenieurs en inkoopmanagers in de auto-, lucht- en ruimtevaart- en industriële sectoren biedt AM-metaal met materialen als AlSi10Mg, Ti-6Al-4V en IN718 een aantrekkelijk pakket voordelen waar traditionele methoden simpelweg niet aan kunnen tippen. De mogelijkheid om ongekende ontwerpvrijheid te bereiken - waardoor topologieoptimalisatie voor radicale lichtgewicht, ingewikkelde conforme koelkanalen voor superieur thermisch beheer en de consolidatie van meerdere onderdelen in een enkele, robuuste component mogelijk worden - betekent een paradigmaverschuiving in de manier waarop motorprestaties, efficiëntie en betrouwbaarheid kunnen worden benaderd.
Hoewel er uitdagingen zijn met betrekking tot restspanning, ondersteuningsstructuren, poederverwijdering en de noodzaak van uitgebreide nabewerking, worden deze effectief aangepakt door middel van vooruitgang in DfAM-principes, geavanceerde procesbesturing (zoals te zien is in technologieën zoals de SEBM-systemen van Met3dp), materiaalproductie van hoge kwaliteit en geïntegreerd workflowbeheer. De sleutel ligt in het begrijpen van zowel het immense potentieel als de praktische overwegingen van de technologie. Succes vereist een holistische benadering: opnieuw nadenken over ontwerpmogelijkheden, zorgvuldig het juiste materiaal voor de toepassing selecteren, nauwkeurig de nabewerkingsstappen plannen en uitvoeren en, misschien wel het belangrijkst, de juiste productiepartner kiezen.
Een partner als Met3dp, met zijn diepe wortels in zowel de wetenschap van hoogwaardige metaalpoederproductie als de engineering van toonaangevende additive manufacturing-apparatuur, belichaamt de geïntegreerde expertise die nodig is. Hun toewijding aan kwaliteit, van de verneveling van sferische poeders tot de betrouwbare werking van hun printers, biedt de basis die nodig is om motorhuizen te produceren die voldoen aan de strenge eisen van de moderne industrie. Door gebruik te maken van dergelijke partnerschappen kunnen bedrijven de risico's van de toepassing van AM verminderen, ontwikkelingscycli versnellen en prestatievoordelen ontsluiten die voorheen onbereikbaar waren.
De beslissing om AM-metaal te gebruiken voor motorhuizen is strategisch. In sommige scenario's kan het gepaard gaan met hogere aanloopkosten per onderdeel in vergelijking met het gieten van grote volumes, maar de waardepropositie reikt vaak veel verder dan het initiële prijskaartje. Lagere assemblagekosten, een lager brandstofverbruik tijdens de levensduur door lichtgewicht onderdelen, een langere levensduur van onderdelen door beter thermisch beheer en een ongeëvenaarde flexibiliteit in de toeleveringsketen door productie op aanvraag en digitale voorraden dragen bij aan een aantrekkelijke total cost of ownership.
Naarmate industrieën de grenzen van prestaties en efficiëntie blijven verleggen, zal additive manufacturing van metaal ongetwijfeld een steeds grotere rol gaan spelen bij de productie van de volgende generatie motorhuizen en andere kritieke onderdelen. De toekomst van motorproductie gaat niet alleen over het maken van onderdelen; het gaat over het intelligent vervaardigen van geïntegreerde systemen - lichter, sterker, efficiënter en precies afgestemd op hun functie. Metal AM is een hoeksteentechnologie die deze toekomst mogelijk maakt.
Wilt u ontdekken hoe additive manufacturing van metaal een revolutie teweeg kan brengen in uw ontwerpen voor motorbehuizingen? Bezoek Met3dp voor meer informatie over onze geavanceerde SEBM-printers, hoogwaardige metaalpoeders en uitgebreide diensten voor applicatieontwikkeling. Neem vandaag nog contact op met ons team om uw projecteisen te bespreken en ontdek hoe onze expertise de additive manufacturing doelen van uw organisatie kan ondersteunen.
Delen op
MET3DP Technology Co, LTD is een toonaangevende leverancier van additieve productieoplossingen met hoofdkantoor in Qingdao, China. Ons bedrijf is gespecialiseerd in 3D printapparatuur en hoogwaardige metaalpoeders voor industriële toepassingen.
Onderzoek om de beste prijs en een op maat gemaakte oplossing voor uw bedrijf te krijgen!
gerelateerde artikelen
Over Met3DP
Recente update
Ons product
NEEM CONTACT MET ONS OP
Nog vragen? Stuur ons nu een bericht! Na ontvangst van uw bericht behandelen wij uw verzoek met een heel team.
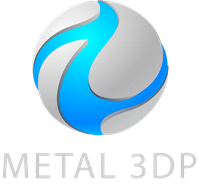
Metaalpoeders voor 3D printen en additieve productie