High-Temperature Sensor Housing via Metal 3D Printing
Inhoudsopgave
Introduction: Defining High-Temperature Sensor Housings and Their Critical Role
In the demanding landscapes of modern industry – from the scorching heat within jet engines and automotive exhaust systems to the chemically aggressive environments of processing plants – the need for reliable data is paramount. Sensors are the vanguards of this data acquisition, monitoring critical parameters like temperature, pressure, flow, and vibration. However, these sensitive electronic components cannot withstand extreme conditions unprotected. This is where the high-temperature sensor housing comes into play. More than just a simple box, a high-temperature sensor housing is a meticulously engineered protective enclosure designed to shield delicate sensor elements from thermal extremes, corrosive agents, high pressures, and physical impacts, ensuring operational integrity and longevity in harsh environments.
These housings are mission-critical components. Failure is not an option when dealing with applications where sensor data informs safety protocols, controls complex processes, or optimizes performance in assets worth millions. Traditionally, manufacturing these specialized housings involved subtractive methods like CNC machining, often starting from expensive billet materials or complex casting processes. While effective, these methods can face limitations in terms of geometric complexity, material waste, lead times for custom designs, and the ability to integrate advanced features like internal cooling channels or intricate mounting points seamlessly.
Enter metal additive manufacturing (AM), more commonly known as metal 3d printen. This transformative technology offers a fundamentally different approach, building parts layer by layer directly from digital designs using high-performance metal powders. For high-temperature sensor housings, metal AM unlocks unprecedented possibilities. It allows engineers to design and produce highly complex, optimized, and robust enclosures that were previously difficult or impossible to manufacture. This technology enables the creation of lightweight yet strong structures, integrated functional features, and rapid iteration cycles, making it an increasingly vital tool for industries demanding peak performance under extreme conditions. As we delve deeper, we will explore the specific applications, the compelling advantages of using metal AM, the crucial role of material selection (focusing on robust alloys like IN625 and 316L), and the key considerations for successfully leveraging this technology for your high-temperature sensor housing needs. Partnering with an experienced provider like Met3dp, equipped with cutting-edge technology and material expertise, becomes crucial in realizing the full potential of additive manufacturing for these demanding components.
The significance of a well-designed and manufactured high-temperature sensor housing cannot be overstated. It serves multiple crucial functions:
- Thermal Protection: Shielding sensitive electronics (piezoelectric crystals, thermistors, semiconductors) from ambient temperatures that can exceed hundreds or even thousands of degrees Celsius. The housing material and design must minimize heat transfer to the internal components.
- Environmental Sealing: Preventing ingress of moisture, dust, corrosive gases, chemicals, and other contaminants that could damage the sensor or interfere with its readings. Hermetic sealing is often a requirement.
- Pressure Containment: In applications involving pressurized gases or liquids, the housing must withstand significant internal or external pressures without deformation or leakage.
- Mechanical Robustness: Protecting the sensor from vibration, shock, abrasion, and physical impacts inherent in industrial, automotive, or aerospace environments.
- Electromagnetic Shielding (EMI/RFI): In some cases, the housing must shield the sensor from electromagnetic or radio frequency interference that could corrupt the signal.
- Mounting and Integration: Providing secure and reliable mounting points for attaching the sensor to the larger system or structure, often requiring specific thread types, flange designs, or bracket configurations.
Metal 3D printing provides a powerful pathway to address these multifaceted requirements with greater design freedom and efficiency than ever before. The ability to work with advanced, high-temperature alloys and create optimized geometries makes it an ideal solution for pushing the boundaries of sensor performance and reliability in the world’s most challenging operating conditions.
Core Applications: Where are High-Temp Sensor Housings Deployed?
The resilience and protective capabilities of high-temperature sensor housings make them indispensable across a wide spectrum of demanding B2B applications and industries. Procurement managers and engineers in these sectors constantly seek robust solutions capable of withstanding extreme environments while ensuring accurate data acquisition. Metal 3D printing, particularly with high-performance alloys, offers tailored solutions for these critical needs.
Here’s a breakdown of key sectors and specific use cases where these specialized housings are vital:
- Ruimtevaart en defensie:
- Gas Turbine Engines: Monitoring turbine inlet temperature (TIT), exhaust gas temperature (EGT), blade temperature, bearing temperature, and pressure within the hot sections of jet engines and auxiliary power units (APUs). Housings must withstand extreme temperatures (often >1000°C), high pressures, and intense vibrations. Materials like IN625 are standard choices. Metal AM allows for complex cooling channels within the housing walls and lightweight designs crucial for aerospace.
- Rocket Propulsion Systems: Measuring combustion chamber temperatures and pressures, nozzle temperatures, and fuel line conditions. Environments involve cryogenic temperatures, rapid thermal cycling, and extreme vibrations.
- Air Data Systems: Protecting sensors that measure airspeed, altitude, and angle of attack, particularly on high-speed aircraft where aerodynamic heating is significant.
- Environmental Control Systems (ECS): Monitoring temperatures within high-temperature bleed air ducts.
- Automobiel:
- Exhaust Gas Systems: Housing sensors (Lambda/O2 sensors, EGT sensors, particulate matter sensors) located directly in the exhaust stream post-combustion or within catalytic converters and diesel particulate filters (DPFs). These environments involve high temperatures (up to 900°C+), corrosive gases, and significant vibration. 316L and specialized stainless steels are common, with IN625 used in high-performance or racing applications. AM enables complex shapes to fit tight engine compartments and optimized flow characteristics around the sensor tip.
- Turbochargers: Monitoring temperatures and pressures within the turbocharger unit itself, where temperatures can soar under boost conditions.
- Motorcomponenten: Protecting sensors monitoring oil temperature, coolant temperature, and cylinder head temperature in high-performance or heavy-duty engines.
- Electric Vehicle (EV) Battery Systems: While not always “high temperature” in the traditional sense, housings for sensors monitoring battery cell temperatures require excellent thermal conductivity, electrical insulation (often via coatings), and robustness, areas where AM can offer design advantages.
- Stroomopwekking:
- Industriële gasturbines: Similar to aerospace, monitoring critical temperatures and pressures in the combustion and exhaust sections for performance optimization and safety. Reliability and long service life are paramount.
- Coal-Fired and Biomass Power Plants: Housing sensors in boilers, furnaces, and flue gas desulfurization (FGD) systems, exposed to high temperatures, abrasive fly ash, and corrosive gases.
- Nuclear Power: Protecting sensors in reactor cooling systems and other critical areas, requiring materials with specific radiation resistance and stringent quality control, often necessitating specialized alloys or meticulous manufacturing processes achievable with AM.
- Industrial Manufacturing and Processing:
- Furnaces and Kilns: Monitoring internal temperatures in heat treating furnaces, glass manufacturing tanks, cement kilns, and ceramic firing processes where temperatures can reach well over 1500°C. Materials like ceramics or platinum are sometimes used for the sensor elements themselves, but the housing still requires high-temperature metal alloys for structural integrity and mounting.
- Chemical and Petrochemical Processing: Housing sensors measuring temperature, pressure, and flow in reactors, distillation columns, and pipelines containing high-temperature, high-pressure, and often highly corrosive fluids. Material compatibility (e.g., resistance to specific chemicals) is critical, making alloys like Hastelloy (similar characteristics to IN625) or specific stainless grades essential. AM allows for custom flange designs and integrated thermowells.
- Metal Smelting and Foundries: Protecting sensors used to monitor molten metal temperatures or atmospheric conditions within smelting operations.
- Plastics Injection Molding and Extrusion: Monitoring melt temperatures within barrels and dies requires robust sensor housings resistant to thermal cycling and pressure.
- Medisch:
- Sterilization Equipment: Housings for temperature and pressure sensors used inside autoclaves and other high-temperature sterilization systems (e.g., steam, ethylene oxide). Housings must withstand repeated cycles of high temperature, pressure, and moisture, often requiring medical-grade materials like 316L stainless steel, validated through AM processes.
- Surgical Tools: While less common for housings per se, AM is used for intricate parts of sensorized surgical instruments that might experience localized heating during use (e.g., from cauterization).
Why This Matters for B2B:
Understanding these diverse applications highlights the need for versatile manufacturing solutions. Procurement managers require suppliers who can:
- Handle a range of high-performance materials (like IN625, 316L, and potentially others).
- Produce complex geometries tailored to specific integration needs.
- Offer rapid prototyping for new sensor designs or applications.
- Scale production from single prototypes to small or medium batches.
- Provide robust quality assurance and material certifications (e.g., aerospace or medical compliance).
Metal 3D printing service providers, such as Met3dp, equipped with advanced powder bed fusion technologies (like Selective Electron Beam Melting – SEBM or Selective Laser Melting – SLM) and a portfolio of quality-controlled metal powders, are ideally positioned to meet these demanding B2B requirements for high-temperature sensor housings across industries.
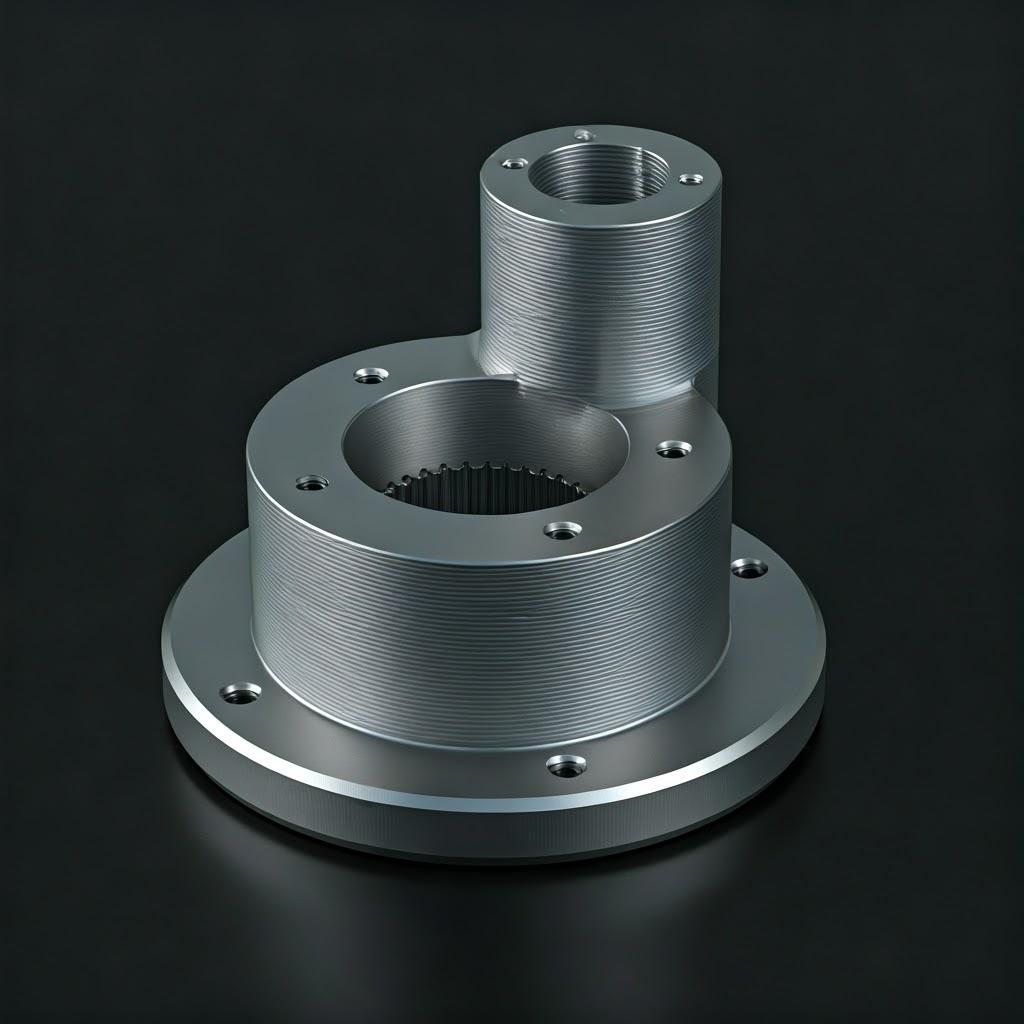
Additive Advantage: Why Choose Metal 3D Printing for Sensor Housings?
While traditional manufacturing methods like CNC machining and investment casting have long served the purpose of creating sensor housings, metal additive manufacturing (AM) presents a suite of compelling advantages, particularly for high-temperature applications demanding complex designs, high performance, and optimized production cycles. For engineers designing cutting-edge sensor systems and procurement managers seeking efficient, reliable sourcing solutions, understanding these benefits is key to leveraging the full potential of metal 3D printing.
1. Unmatched Design Freedom and Complexity:
- Intricate Geometries: Traditional methods struggle with complex internal features, undercuts, and non-linear shapes without costly multi-axis machining or complex casting molds. Metal AM builds parts layer by layer, enabling the creation of highly intricate internal channels for cooling or wiring, conformal designs that hug complex surfaces, and integrated mounting features, all within a single monolithic part.
- Deelconsolidatie: Multiple components of a traditional sensor housing assembly (e.g., housing body, mounting brackets, connectors, heat sinks) can often be consolidated into a single, 3D-printed part. This reduces assembly time, eliminates potential failure points at joints or welds, simplifies inventory management, and can lead to a lighter, more robust final product.
- Topology Optimization and Lightweighting: AM allows engineers to use sophisticated software tools to optimize the structure of the sensor housing. Material is placed only where it’s structurally necessary to withstand thermal and mechanical loads, resulting in significantly lighter components without sacrificing strength. This is particularly critical in weight-sensitive applications like aerospace and automotive. Lattice structures can be incorporated for further weight reduction or enhanced heat dissipation.
2. Accelerated Prototyping and Development Cycles:
- Snelle iteratie: Creating prototypes for new sensor housing designs using traditional methods can take weeks or months due to tooling requirements (molds, fixtures). With metal AM, a new design iteration can often be printed and tested within days. This rapid feedback loop drastically accelerates the product development cycle, allowing engineers to refine designs, test functionality, and reach optimal solutions much faster.
- Eliminatie van gereedschap: Metal AM is a “tool-less” manufacturing process. This eliminates the significant upfront cost and lead time associated with designing and fabricating molds, dies, or complex fixtures, making it highly cost-effective for low-to-medium volume production runs and custom designs.
3. Enhanced Performance and Functionality:
- Optimized Thermal Management: The design freedom of AM enables the integration of sophisticated thermal management features directly into the housing. This can include internal cooling channels precisely following heat-sensitive areas, thin walls for controlled heat transfer, or integrated heat sinks with complex fin geometries optimized via simulation – features often impossible to machine or cast.
- Materiaaleigenschappen: AM processes, when properly controlled, can produce parts with densities exceeding 99.9%, resulting in mechanical properties comparable or even superior to wrought or cast materials, especially when combined with appropriate post-processing like Hot Isostatic Pressing (HIP). This ensures the housing meets the demanding strength and durability requirements of high-temperature environments. Companies like Met3dp utilize advanced powder production techniques (gas atomization, PREP) to ensure high sphericity and flowability, leading to denser, higher-quality printed parts.
- Maatwerk: Each sensor application might have unique space constraints, mounting requirements, or environmental challenges. AM allows for the cost-effective production of highly customized housing designs tailored to specific needs without the economic penalties associated with traditional custom manufacturing.
4. Supply Chain and Production Efficiency:
- Productie op aanvraag: Metal AM enables distributed manufacturing and production closer to the point of need. Parts can be printed on demand, reducing the need for large inventories of diverse housing types and minimizing warehousing costs.
- Minder materiaalverspilling: Subtractive manufacturing, like CNC machining, starts with a larger block of material and removes excess, generating significant waste (swarf). Additive manufacturing uses only the material needed to build the part (plus support structures), leading to much higher material utilization efficiency, especially important when working with expensive high-temperature alloys like IN625.
- Digital Inventory: Designs are stored digitally (CAD files), allowing for easy retrieval and printing of legacy parts or updated designs without maintaining physical tooling or large stocks.
5. Access to Advanced Materials:
- While traditional methods can work with high-temperature alloys, AM platforms are increasingly adept at processing materials like Nickel-based superalloys (IN625, IN718, Hastelloy X), Cobalt-Chrome alloys, Titanium alloys, and specialized stainless steels (like 316L). The layer-wise nature of AM can offer unique microstructural control possibilities during the build process.
Table: Metal AM vs. Traditional Methods for High-Temp Sensor Housings
Functie | Metal 3D Printing (AM) | CNC-bewerking | Investeringscasting |
---|---|---|---|
Complex ontwerp | Very High (Internal channels, lattices) | Moderate (Limited by tool access) | High (Requires complex molds) |
Deel Consolidatie | Uitstekend | Beperkt | Gematigd |
Lichtgewicht | Excellent (Topology optimization) | Limited (Material removal constraints) | Moderate (Design constraints) |
Prototyping Speed | Zeer snel (dagen) | Moderate (Days to weeks) | Slow (Weeks to months – tooling) |
Kosten gereedschap | Geen | Low (Fixtures) | High (Mold design & fabrication) |
Materiaal Afval | Laag | Hoog | Gematigd |
Maatwerk | High & Cost-Effective | Moderate (Setup time per design) | Low (Requires mold changes) |
Lead Time (Low Vol) | Snel | Gematigd | Langzaam |
Lead Time (High Vol) | Moderate (Scalability dependent) | Snel | Moderate to Fast |
Typische materialen | IN625, 316L, Ti6Al4V, CoCr, etc. | All machinable metals | Most castable metals |
Exporteren naar Sheets
Choosing metal AM for high-temperature sensor housings isn’t just about adopting a new manufacturing technique; it’s about unlocking superior performance, accelerating innovation, and optimizing the entire product lifecycle, from design conception to final deployment in the field. Partnering with a knowledgeable metaal 3D printen service provider ensures access to the right technology, materials, and expertise to realize these advantages fully.
Material Selection Matters: IN625 and 316L for Demanding Environments
The performance and reliability of a high-temperature sensor housing are fundamentally dictated by the material from which it is made. Choosing the right metal powder for additive manufacturing is crucial, balancing thermal resistance, mechanical strength, corrosion resistance, manufacturability, and cost. For the majority of demanding high-temperature sensor applications, two materials stand out in the realm of metal AM: Inconel 625 (IN625), a nickel-based superalloy, and 316L Stainless Steel, a widely used austenitic stainless steel. Understanding their distinct properties and suitability for different operating conditions is vital for engineers and procurement specialists.
Inconel 625 (IN625): The High-Performance Choice
IN625 is a nickel-chromium-molybdenum-niobium superalloy renowned for its exceptional combination of high strength, outstanding corrosion resistance, and excellent fabricability, particularly at elevated temperatures.
- Key Properties & Advantages for Sensor Housings:
- High-Temperature Strength & Creep Resistance: IN625 maintains significant tensile and yield strength at temperatures up to 815°C (1500°F) and exhibits excellent resistance to creep (deformation under sustained load) at even higher temperatures. This is critical for housings operating in gas turbines, exhaust manifolds, and industrial furnaces.
- Uitstekende corrosiebestendigheid: It offers superb resistance to a wide range of corrosive environments, including oxidizing and reducing conditions, pitting, crevice corrosion, and intergranular attack. It performs exceptionally well in environments containing acids (sulfuric, phosphoric, nitric), seawater, chloride ions, and alkaline media. This makes it ideal for chemical processing, marine applications, and harsh exhaust streams.
- Excellent Fatigue Strength: Resists failure under cyclic loading and thermal cycling conditions, common in aerospace and automotive applications.
- Good Fabricability & Weldability (in AM): While traditionally known for good weldability, IN625 is also well-suited for powder bed fusion AM processes (SLM and SEBM). It generally exhibits good processability, allowing for the creation of dense, high-integrity parts. Post-processing like heat treatment is often required to optimize properties.
- Oxidatiebestendigheid: Forms a protective oxide layer, resisting degradation in high-temperature oxidizing atmospheres.
- Overwegingen:
- Kosten: IN625 is significantly more expensive than stainless steels due to its high nickel and alloying element content.
- Gewicht: It is denser than stainless steel and titanium alloys.
- Bewerkbaarheid: Can be more challenging to machine in post-processing compared to 316L.
- Typical High-Temperature Sensor Applications: Aerospace engine components, high-performance automotive exhaust systems, industrial furnace fixtures, chemical reactor vessels, flare tips, nuclear applications.
316L Stainless Steel: The Versatile Workhorse
316L is an austenitic chromium-nickel stainless steel containing molybdenum, which enhances its corrosion resistance, particularly against chlorides and non-oxidizing acids. The ‘L’ denotes low carbon content (≤0.03%), improving resistance to sensitization (intergranular corrosion after welding or high-temperature exposure).
- Key Properties & Advantages for Sensor Housings:
- Goede corrosiebestendigheid: Offers excellent resistance to atmospheric corrosion, general corrosion in moderately aggressive chemical environments, and pitting corrosion in chloride-containing media (better than 304 stainless steel). Suitable for many industrial, food processing, and medical applications.
- Good High-Temperature Properties (Moderate): While not a superalloy like IN625, 316L retains useful strength and oxidation resistance at temperatures up to about 870°C (1600°F) for intermittent service, though continuous service temperatures are typically lower (around 500-600°C or 932-1112°F) to avoid sensitization and ensure long-term structural integrity.
- Excellent Formability & Weldability (in AM): 316L is one of the easiest and most common materials to process using metal AM technologies. It generally prints well, achieving high density and good surface finish.
- Kosteneffectiviteit: Significantly less expensive than nickel-based superalloys like IN625, making it a preferred choice when the absolute extreme performance of IN625 is not required.
- Biocompatibiliteit: Medical grades of 316L are widely used for implants and instruments, making it suitable for sensor housings in medical sterilization or certain implantable device applications.
- Overwegingen:
- Lower Temperature Limit: Not suitable for the extreme temperatures (>800°C continuous) where IN625 excels. Strength decreases significantly at very high temperatures.
- Susceptibility to Certain Corrosives: Can be susceptible to stress corrosion cracking in hot chloride environments and is less resistant than IN625 to certain strong acids.
- Typical High-Temperature Sensor Applications: Automotive exhaust components (non-performance critical), industrial processing (moderate temperatures), food and beverage processing, medical sterilization equipment, general industrial sensor protection.
Table: IN625 vs. 316L for Metal AM Sensor Housings
Eigendom | Inconel 625 (IN625) | 316L roestvrij staal | Key Consideration for Sensor Housings |
---|---|---|---|
Primaire legeringselementen | Ni, Cr, Mo, Nb | Fe, Cr, Ni, Mo | Determines core material characteristics |
Max. Service Temp. | ~815°C+ (1500°F+) Continuous | ~500-600°C (932-1112°F) Continuous | Defines operational limits; IN625 superior for extreme heat |
Strength at High Temp. | Uitstekend | Gematigd | Critical for maintaining structural integrity under thermal load |
General Corrosion Resist. | Uitstekend | Erg goed | Resistance to chemical attack, oxidation |
Chloride Corrosion Resist. | Uitstekend | Goed | Important for marine, chemical, and some exhaust environments |
AM Verwerkbaarheid | Goed | Uitstekend | Ease of printing, achieving density, surface finish |
Relatieve kosten | Hoog | Laag | Significant factor in material selection & procurement |
Dikte | ~8.44 g/cm³ | ~8.00 g/cm³ | Impacts overall component weight |
Biocompatibiliteit | Generally good (specific testing req.) | Excellent (Medical grades available) | Relevant for medical device applications |
Exporteren naar Sheets
The Role of Powder Quality:
Regardless of the alloy chosen, the quality of the metal powder used in the AM process is paramount. Characteristics like:
- Sfericiteit: Smooth, spherical powder particles flow easily and pack densely, leading to more uniform layers and higher final part density.
- Deeltjesgrootteverdeling (PSD): A controlled PSD ensures consistent melting behavior and good surface finish.
- Puurheid: Low levels of impurities (like oxygen, nitrogen) are crucial for achieving optimal mechanical properties and corrosion resistance.
- Vloeibaarheid: Essential for uniform powder bed spreading in AM machines.
Companies like Met3dp invest heavily in advanced powder manufacturing techniques such as Vacuum Induction Melting Gas Atomization (VIGA) and Plasma Rotating Electrode Process (PREP). These methods produce hoogwaardige metaalpoeders with the high sphericity, controlled PSD, low satellite content, and excellent flowability required for demanding applications like high-temperature sensor housings. Utilizing premium powders directly translates to superior component integrity, better performance, and increased reliability – critical factors for engineers and procurement managers specifying these parts. Choosing the right material, backed by high-quality powder and expert processing, is the foundation for successful high-temperature sensor housing manufacturing via metal AM.
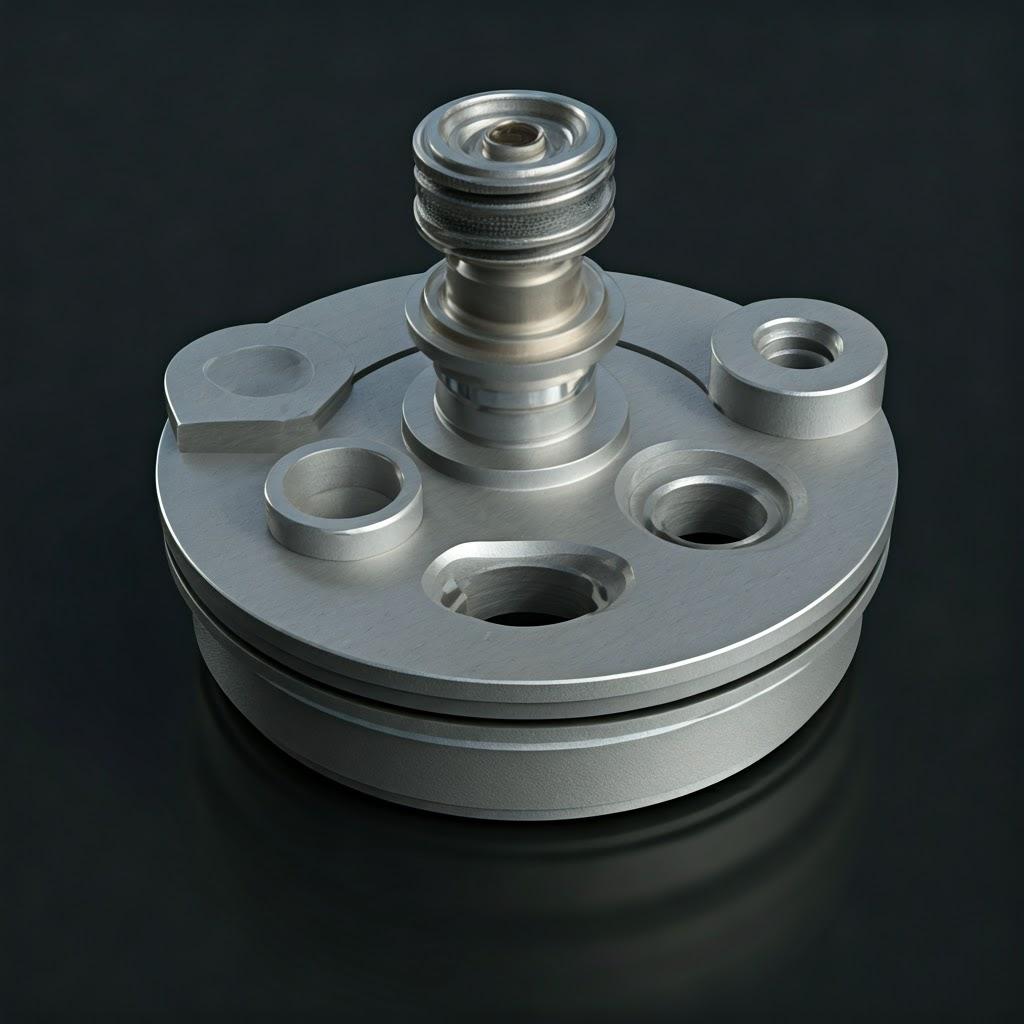
Design for Additive Manufacturing (DfAM): Optimizing Sensor Housings for Printing
Successfully leveraging metal additive manufacturing (AM) for high-temperature sensor housings requires more than simply converting an existing CAD file designed for machining or casting. It demands a fundamental shift in design thinking, embracing principles known as Design for Additive Manufacturing (DfAM). DfAM isn’t just about making a part printable; it’s about strategically using the unique capabilities of AM to enhance performance, reduce weight, consolidate parts, and optimize the entire manufacturing process, resulting in superior components that meet the stringent demands of aerospace, automotive, and industrial applications. Failing to consider DfAM early can lead to printing failures, excessive post-processing, compromised performance, and higher costs.
Why DfAM is Non-Negotiable for Sensor Housings:
High-temperature sensor housings often involve a delicate balance: protecting sensitive internal components from extreme heat and harsh environments while potentially needing to manage heat transfer, accommodate wiring, provide secure mounting, and fit within tight space constraints. DfAM empowers engineers to address these competing requirements with unprecedented geometric freedom.
Key DfAM Considerations for High-Temperature Sensor Housings:
- Optimalisatie van de wanddikte:
- Minimale dikte: AM processes have limitations on the minimum wall thickness they can reliably produce (often around 0.4-0.8 mm, depending on the machine, material, and feature height). Designing below this can lead to incomplete features or build failures.
- Structurele integriteit: Walls must be thick enough to withstand mechanical loads (pressure, vibration) and thermal stresses at operating temperature. Finite Element Analysis (FEA) is crucial here.
- Thermisch beheer: Wall thickness directly impacts heat transfer. Thinner walls might be desired for rapid heat dissipation weg from the sensor in some designs (using integrated fins), while thicker walls or insulating features (like internal voids or lattices) might be needed to shield the sensor. DfAM allows tailoring thickness precisely where needed.
- Bedrukbaarheid: Very thick sections can accumulate thermal stress, increasing distortion risk. Consider incorporating internal lattice structures or pockets to reduce bulk in thick sections without compromising strength significantly.
- Internal Channels and Cavities:
- Functionality: AM excels at creating complex internal channels for routing wires, delivering cooling fluids (if applicable), or precisely positioning the sensor element within the housing.
- Zelfdragende hoeken: Overhanging internal features generally require support structures. However, designing channels with angles typically greater than 45 degrees from the horizontal allows them to be “self-supporting,” eliminating the need for internal supports which can be impossible to remove. Teardrop or diamond shapes are often preferred for horizontal channels over simple circles or squares for better printability without supports.
- Powder Removal: Crucially, internal cavities and channels must have access points designed in to allow for the complete removal of unfused metal powder after printing. Trapped powder can add weight, potentially sinter during heat treatment (affecting performance), or contaminate the sensor environment. Consider multiple access ports or design channels that loop back to an exterior opening.
- Support Structure Strategy:
- Doel: Supports anchor the part to the build plate, prevent warping, and support overhanging features (typically below 45 degrees).
- Minimization: Supports add material cost, printing time, and require a post-processing removal step that can affect surface finish. The primary DfAM goal is to minimize or eliminate the need for supports through:
- Optimal Orientation: Orienting the part on the build plate to make steep overhangs self-supporting or to place supports on non-critical surfaces. Build simulation software can help determine the best orientation to balance support needs, print time, and thermal stress.
- Designing-Out Overhangs: Using chamfers or fillets instead of sharp 90-degree overhangs where possible.
- Ease of Removal: When supports are necessary, design them for easy removal. This includes using appropriate support types (e.g., block, lattice, cone), ensuring adequate spacing between the support and the part (the interface layer), providing clear access for tools, and designing specific “breakaway” points. Avoid supports on critical sealing surfaces, threads, or complex external features if possible.
- Mounting Features and Integration:
- Threads: While AM can print threads, they often lack the required precision and strength, especially for fine pitches. It’s generally recommended to design holes slightly undersized and tap the threads during post-processing (CNC machining). For larger, non-critical threads, printing might be feasible but requires careful design and testing.
- Flanges and Sealing Surfaces: These require high flatness and specific surface finishes. Design these features with extra material (“machining allowance”) so they can be precisely machined post-print to meet specifications. Ensure the design allows for proper fixturing during machining.
- Brackets and Attachments: Use topology optimization software to design lightweight yet strong mounting brackets integrated directly into the housing body. This eliminates fasteners, reduces weight, and simplifies assembly.
- Lattice Structures and Infill:
- Toepassingen: Incorporating internal lattice structures can significantly reduce weight while maintaining structural integrity, dampen vibrations, or increase surface area for heat exchange if designed as part of a thermal management system.
- Ontwerp: Choose appropriate lattice cell types (e.g., cubic, octet-truss) and sizes based on load requirements and printability. Ensure adequate openings for powder removal. Variable density lattices can further optimize material usage.
- Thermal Management Features:
- Conforme koelkanalen: Channels that precisely follow the contours of heat-sensitive areas, providing much more efficient cooling than traditionally drilled straight channels.
- Integrated Heat Sinks: Complex fin geometries optimized through simulation (CFD – Computational Fluid Dynamics) can be printed directly onto the housing exterior to maximize heat dissipation to the ambient environment.
- Surface Features and Text:
- Raised or recessed logos, part numbers, or instructions can be easily incorporated into the design. Consider minimum feature size limitations and orientation for best definition. Textured surfaces for grip or aesthetics are also possible.
Collaboration and Simulation:
Effective DfAM is often a collaborative process. Engaging with your additieve productie provider, like Met3dp, early in the design stage is highly recommended. Their experts understand the specific nuances and capabilities of their machines (e.g., SEBM vs. SLM) and materials (IN625, 316L) and can provide invaluable feedback on printability, orientation strategies, and potential challenges. Utilizing simulation tools (FEA for stress/thermal analysis, CFD for fluid flow/heat transfer, topology optimization, and build process simulation) is crucial for validating designs voor committing to costly metal prints, ensuring the final housing performs as intended in its demanding high-temperature environment. By embracing DfAM, companies can transform the high-temperature sensor housing from a simple enclosure into a highly optimized, performance-enhancing component.
Achieving Precision: Tolerances, Surface Finish, and Accuracy in Metal AM
While metal additive manufacturing offers remarkable design freedom, it’s crucial for engineers and procurement managers to have realistic expectations regarding the achievable levels of precision – encompassing dimensional tolerances, surface finish, and overall geometric accuracy. Unlike the sub-micron precision possible with some conventional machining processes, metal AM (specifically Powder Bed Fusion – PBF technologies like SLM and SEBM commonly used for sensor housings) operates within a different tolerance paradigm. Understanding these capabilities and limitations is essential for designing functional parts and specifying requirements correctly.
Dimensional Tolerances:
- Typische bereiken: As a general guideline, metal PBF processes can typically achieve tolerances in the range of ±0.1 mm to ±0.2 mm for smaller features (up to ~20-50mm), plus potentially a small percentage (e.g., ±0.05% to ±0.2%) of the overall dimension for larger parts. This often aligns with general tolerance standards like ISO 2768-m (medium) or sometimes -f (fine), but it’s highly dependent on various factors. Specific features might achieve tighter tolerances, while large, complex parts might exhibit greater deviation.
- Key Influencing Factors:
- Materiaaleigenschappen: Each metal alloy exhibits different shrinkage rates upon cooling and solidification, which must be compensated for in the build preparation. Variations in powder batches can also play a role.
- Thermische spanningen: The rapid heating and cooling inherent in PBF processes generate internal stresses that can cause warping and distortion, affecting final dimensions.
- Part Geometry and Size: Larger parts and complex geometries with varying cross-sections are more susceptible to thermal distortion. Tall, thin features can be prone to deviation.
- Bouwrichting: The orientation of the part on the build plate significantly impacts thermal behavior, support requirements, and achievable tolerances on different features.
- Ondersteunende structuren: Supports influence local thermal conditions and can leave witness marks affecting dimensions after removal.
- Machine Calibration & Condition: Accuracy depends heavily on the precise calibration of the laser/electron beam system, scanner accuracy, and overall machine health.
- Procesparameters: Layer thickness, beam power, scan speed, and scan strategy all influence the melt pool dynamics and resulting part accuracy.
- Designing for Tolerance: For critical dimensions (e.g., mating interfaces, diameters for bearings or seals) that require tolerances tighter than the standard AM process capability, the best practice is to design the feature with additional “stock” material (e.g., 0.5-1.0 mm) and specify post-process machining to achieve the final required tolerance. Clearly identify these critical dimensions on engineering drawings.
Oppervlakteafwerking (ruwheid):
- As-Built Condition: The surface finish of as-built metal AM parts is inherently rougher than machined surfaces. Typical Ra (average roughness) values range from 5 µm to 25 µm, but this varies significantly:
- Oriëntatie: Top-facing (up-skin) surfaces are generally smoother. Side walls show layer lines. Down-facing (down-skin) surfaces supported by structures tend to be the roughest due to the support interface.
- Material & Powder: Finer metal powders generally lead to smoother finishes but may process differently. Material type also influences melt pool behavior and surface texture. IN625 and 316L can yield relatively good finishes with optimized parameters.
- Procesparameters: Lower layer thickness usually results in a finer finish but increases build time. Beam parameters and scan strategy also impact surface melt characteristics.
- Process Type: SEBM (Electron Beam) typically produces slightly rougher surfaces than SLM (Laser Beam) due to higher energy input and powder sintering effects, but may have advantages in reduced residual stress.
- Verbetering van de oppervlakteafwerking: If the as-built roughness is insufficient (e.g., for sealing surfaces, fluid flow channels, or aesthetic requirements), extensive post-processing is necessary. Options include bead blasting, tumbling, chemical etching, electropolishing, grinding, and precision machining/polishing (discussed further in the next section).
Geometric Accuracy:
- Definitie: This refers to the overall fidelity of the printed part compared to the original CAD model, encompassing form features like flatness, roundness, and cylindricity, as well as positional accuracy of features.
- Uitdagingen: Warpage due to thermal stress is the primary challenge affecting overall geometric accuracy, especially for large or complex sensor housings. Residual stress can also cause distortion after the part is removed from the build plate.
- Mitigation: Careful DfAM (minimizing stress concentrations), optimized build orientation, robust support strategy, precise thermal management during the build (e.g., build plate heating), validated process parameters, and post-build stress relief heat treatments are all critical for achieving good geometric accuracy. Build simulation software can help predict and compensate for potential distortion.
Quality Control and Assurance:
Achieving and verifying the required precision demands a robust quality control process from the AM service provider.
- Process Monitoring: Real-time monitoring of melt pool characteristics, temperature, oxygen levels, and other parameters during the build can help ensure consistency.
- Metrology: Post-build inspection using Coordinate Measuring Machines (CMMs), 3D laser scanners, or traditional gauging methods is essential to verify dimensional tolerances and geometric accuracy against specifications.
- Materiaalcertificering: Ensuring the incoming metal powder meets specifications and providing material certifications with the final parts.
- QMS and Industry Standards: Partnering with a supplier like Met3dp, which operates under a rigorous Quality Management System (QMS) and holds relevant certifications (potentially including AS9100 for aerospace or ISO 13485 for medical, depending on their market focus), provides confidence in their ability to deliver industrial-grade components that meet demanding precision requirements. Procurement managers should verify a potential supplier’s quality credentials and inspection capabilities.
In summary, while metal AM may not match the inherent precision of multi-axis CNC machining in its as-built state, careful design (DfAM), process control, and planned post-processing allow for the production of high-precision, industrial-grade high-temperature sensor housings suitable for the most critical applications. Clear communication of requirements between the designer and the AM service provider is key to success.
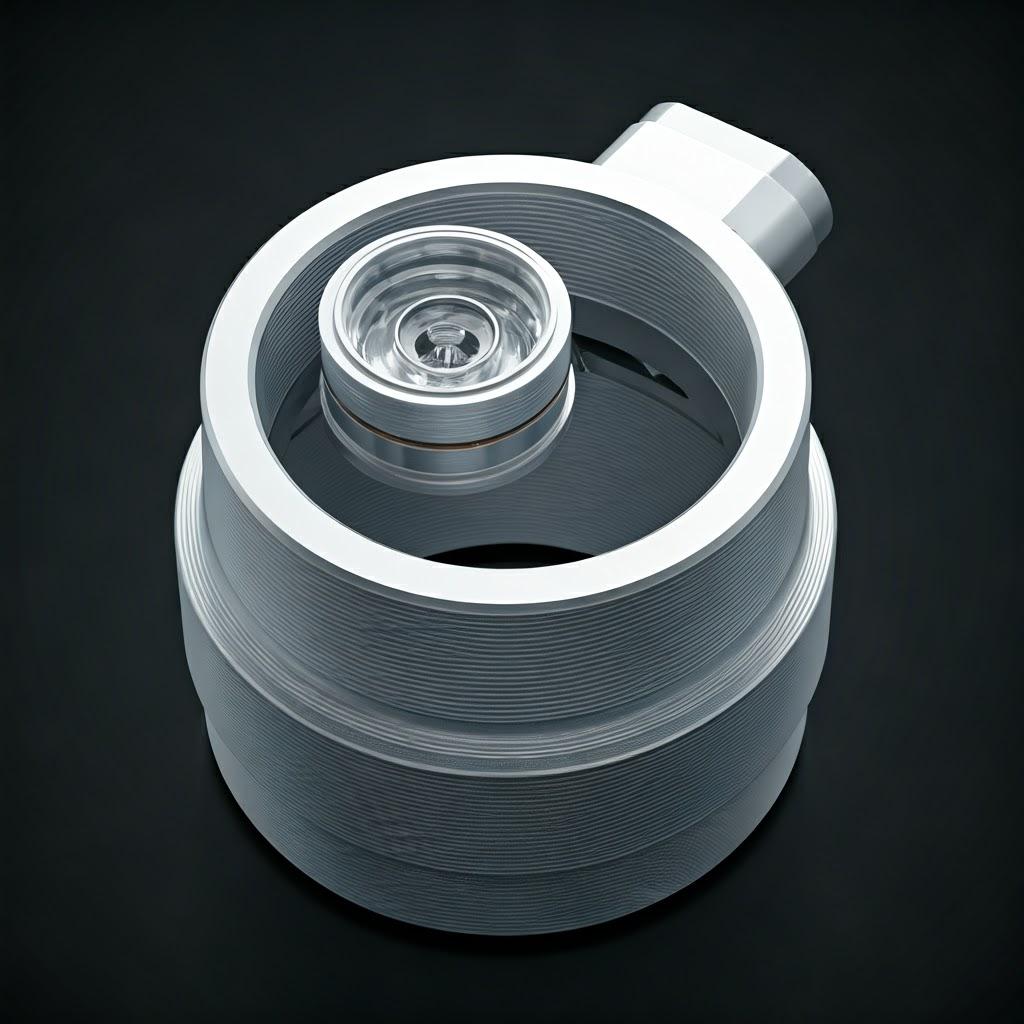
Beyond Printing: Essential Post-Processing Steps for Sensor Housings
A common misconception about metal additive manufacturing is that parts emerge from the printer ready for immediate use. In reality, particularly for demanding applications like high-temperature sensor housings made from alloys like IN625 or 316L, the printing stage is just one step in a comprehensive manufacturing workflow. Post-processing is not merely optional; it is an essential phase that transforms the raw, as-built part into a functional, reliable component meeting stringent engineering specifications. These steps are critical for relieving stress, achieving required tolerances and surface finishes, ensuring material properties, and guaranteeing cleanliness.
Critical Post-Processing Stages for Metal AM Sensor Housings:
- Stress Relief / Heat Treatment:
- Why it’s Crucial: The layer-by-layer fusion process involves intense, localized heating followed by rapid cooling. This creates significant internal stresses within the printed part (residual stress). If not relieved, these stresses can cause distortion (immediately or over time), reduce fatigue life, and compromise mechanical properties. For high-temperature alloys like IN625, designed to operate under thermal loads, stress relief is absolutely mandatory.
- Proces: Parts are typically heated in a controlled atmosphere (vacuum or inert gas like argon) furnace to a specific temperature, held for a duration (soaked), and then cooled at a controlled rate. The exact cycle (temperature, time, cooling rate) depends heavily on the material (IN625 requires different cycles than 316L) and the desired final properties.
- Further Heat Treatments: Beyond basic stress relief, other heat treatments might be necessary:
- Oplossing ontharden: Dissolves precipitates, homogenizes the microstructure, improves ductility. Often used for IN625.
- Aging (Precipitation Hardening): For specific alloys (though less common for standard IN625/316L builds unless tailored properties are needed), this step strengthens the material by forming fine precipitates.
- Provider Capability: Ensure your AM service provider has calibrated furnaces with the required atmosphere control and temperature capabilities or works with certified heat treatment partners.
- Onderdeel verwijderen van bouwplaat:
- Parts are typically printed on a thick metal build plate. Removal usually involves wire EDM (Electrical Discharge Machining) or sawing. This must be done carefully to avoid damaging the part, especially near the base.
- Draagstructuur verwijderen:
- As discussed under DfAM, supports must be removed. This can be done manually (breaking, cutting with hand tools) or via machining (milling, grinding).
- Uitdagingen: Can be labor-intensive, potentially damaging the part surface if not done carefully, and access can be difficult for complex internal supports. Witness marks or rougher surface patches are common where supports were attached and often require further finishing.
- Heet isostatisch persen (HIP):
- Doel: HIP combines high temperature (below melting point) and high pressure (using an inert gas like argon) in a specialized vessel. This process collapses internal micro-porosity that can sometimes remain after printing, even in high-quality builds.
- Voordelen: Achieves near 100% density, significantly improves fatigue strength, ductility, and overall mechanical property consistency.
- Toepassingen: Often mandatory for critical, fatigue-sensitive components in aerospace and medical applications. It adds cost and lead time but provides the highest material integrity. For many industrial sensor housings, it might be optional unless very high pressures or extreme fatigue life is required.
- CNC-bewerking:
- Noodzaak: As AM tolerances and surface finish may not meet all requirements, precision machining is often required for:
- Critical Tolerances: Achieving tight dimensional tolerances (e.g., ±0.01-0.05 mm) on features like mating surfaces, diameters, or sensor mounting interfaces.
- Oppervlakken afdichten: Creating perfectly flat and smooth surfaces for O-rings or gasket seals.
- Threads: Tapping or milling precise threads.
- Verbetering van de oppervlakteafwerking: Achieving very smooth surfaces (low Ra) on specific functional areas.
- Overwegingen: Requires careful design and execution of workholding fixtures to hold the complex AM part securely without distortion. Machining allowances must be included in the DfAM phase. Machining IN625 can be challenging due to its work-hardening nature.
- Noodzaak: As AM tolerances and surface finish may not meet all requirements, precision machining is often required for:
- Afwerking oppervlak:
- Beyond machining, various techniques refine the overall surface:
- Bead Blasting / Sand Blasting: Uses abrasive media propelled by compressed air to create a uniform, clean, matte finish. Removes loose powder particles and slightly smooths the surface. Different media (glass beads, aluminum oxide) produce different finishes.
- Tumbling / Vibratory Finishing: Parts are placed in a tub with abrasive media, which vibrates or tumbles. Good for deburring edges and achieving a uniform finish on batches of smaller parts, but less suitable for delicate features or maintaining sharp edges.
- Polishing / Lapping: Manual or automated processes using progressively finer abrasives to achieve very smooth, often mirror-like finishes (Ra < 0.1 µm). Labor-intensive and usually applied only to specific critical areas.
- Elektrolytisch polijsten: An electrochemical process that removes a microscopic layer of material, resulting in a very smooth, clean, and often brighter surface. Particularly effective for 316L stainless steel. Can improve corrosion resistance.
- Beyond machining, various techniques refine the overall surface:
- Schoonmaken:
- Thorough cleaning is vital to remove any residual metal powder (especially from internal channels), machining fluids, blasting media, or other contaminants that could interfere with sensor operation or downstream processes. Ultrasonic cleaning baths with appropriate solvents are often used.
- Coating (optioneel):
- Depending on the specific application, specialized coatings might be applied:
- Thermal Barrier Coatings (TBCs): Ceramic coatings applied to reduce heat transfer into the housing, further protecting the sensor. Common in gas turbine applications.
- Corrosion/Wear Resistant Coatings: To enhance durability in extremely aggressive environments beyond the inherent capability of IN625 or 316L.
- Dielectric Coatings: For electrical insulation if required.
- Depending on the specific application, specialized coatings might be applied:
- Final Inspection and Testing:
- After all processing, parts undergo final inspection: dimensional checks (CMM, scanning), visual inspection, NDT (e.g., dye penetrant testing for surface cracks, CT scanning for internal integrity), pressure testing (if applicable), and verification of material certifications.
Planning for Post-Processing:
It’s essential to discuss post-processing requirements with your AM service provider during the initial quotation and design review phases. A capable partner like Met3dp, knowledgeable in various afdrukmethoden and materials like IN625 and 316L, can advise on the necessary steps, integrate them into the production plan, and either perform them in-house or manage them through qualified partners. Factoring in the time and cost associated with these essential post-processing steps is critical for accurate project planning and budgeting for high-temperature sensor housings.
Navigating Challenges: Overcoming Hurdles in Metal AM Production
While metal additive manufacturing unlocks significant potential for creating advanced high-temperature sensor housings, it’s important to acknowledge that it is a sophisticated process with inherent complexities and potential challenges. Understanding these common hurdles and the strategies employed by experienced AM service providers to mitigate them is crucial for both engineers designing parts and procurement managers selecting manufacturing partners. Proactive planning and process control are key to ensuring consistent quality and reliable production.
Common Challenges in Metal AM for Sensor Housings & Mitigation Strategies:
- Vervorming en vervorming:
- Cause: Uneven heating and cooling cycles during the layer-by-layer build process create thermal gradients and internal stresses. As these stresses accumulate, they can cause the part to warp or distort, pulling away from the build plate or deviating from the intended geometry. This is particularly pronounced in large parts or designs with abrupt changes in cross-section.
- Mitigation:
- Thermal Simulation: Using build simulation software to predict areas of high stress and potential distortion voor afdrukken.
- Geoptimaliseerde oriëntatie: Selecting a build orientation that minimizes large flat surfaces parallel to the build plate and reduces overhangs.
- Robust Support Structures: Designing effective supports to anchor the part securely and act as heat sinks.
- Optimalisatie van procesparameters: Fine-tuning laser/electron beam power, scan speed, and scan strategy (e.g., checkerboard patterns) to manage heat input.
- Build Plate Heating: Maintaining an elevated temperature on the build plate reduces thermal gradients.
- Post-Build Stress Relief: Essential heat treatment immediately after printing to relax internal stresses before removing supports or the part from the plate.
- Restspanning:
- Cause: Even if visible warping is controlled, significant internal stresses can remain locked within the as-built part. These can compromise the part’s strength, lead to delayed cracking, or cause distortion when material is removed during post-machining.
- Mitigation:
- Mandatory Stress Relief: As mentioned, appropriate heat treatment cycles tailored to the alloy (IN625, 316L) are non-negotiable for relieving residual stress.
- Ontwerpoverwegingen: Avoiding sharp internal corners and large variations in mass can help reduce stress concentrations.
- Procesbeheersing: Stable and optimized printing parameters minimize stress build-up.
- Moeilijkheden bij het verwijderen van de steunstructuur:
- Cause: Supports, while necessary, can be difficult and time-consuming to remove, especially complex internal supports or those attached to delicate features. Removal can damage the part surface or leave undesirable witness marks.
- Mitigation:
- DfAM: Prioritizing designs that minimize or eliminate the need for supports through self-supporting angles and optimal orientation.
- Smart Support Design: Using support types (e.g., lattice, conical) that are easier to remove, optimizing the interface layer between the support and part for easier separation, and ensuring tool access.
- Skilled Technicians: Employing experienced technicians with the right tools (hand tools, cutting tools, potentially EDM or machining) for careful removal.
- Post-Removal Finishing: Planning for subsequent finishing steps (blasting, grinding, machining) to clean up support contact points.
- Poreusheid:
- Cause: Small voids or gas bubbles trapped within the solidified metal. Can originate from gas trapped within the powder, insufficient melting, or instability in the melt pool. Porosity reduces density and can significantly degrade mechanical properties, especially fatigue strength.
- Mitigation:
- Hoogwaardig poeder: Using powders with high sphericity, controlled particle size distribution, low internal gas content, and good flowability (like those produced by Met3dp using advanced atomization). Proper powder handling and storage are also key.
- Geoptimaliseerde procesparameters: Ensuring sufficient energy input (beam power/speed) to fully melt the powder and allow gas to escape, while avoiding overheating which can cause keyhole porosity.
- Controlled Atmosphere: Maintaining a high-purity inert gas atmosphere (Argon or Nitrogen for SLM) or high vacuum (SEBM) to minimize oxidation and gas pickup.
- Heet isostatisch persen (HIP): The most effective method to eliminate remaining micro-porosity for critical applications.
- Surface Roughness and Feature Definition:
- Cause: Layer-wise building, partially melted powder particles adhering to surfaces (especially down-skins), and support contact points contribute to surface roughness. Very fine features may lose definition due to melt pool size and heat spread.
- Mitigation:
- Parameter Tuning: Adjusting layer thickness, beam parameters, and contour scans.
- Oriëntatie: Prioritizing critical surfaces for upward-facing orientation.
- Nabewerking: Utilizing appropriate finishing techniques (blasting, tumbling, machining, polishing) to achieve the required Ra value.
- Design Compensation: Slightly exaggerating very fine features in the CAD model if necessary, accounting for process limitations.
- Cracking:
- Cause: Can occur during solidification (hot cracking) or upon cooling (cold cracking) due to high thermal stresses, particularly in crack-sensitive alloys or complex geometries with high restraint.
- Mitigation:
- Materiaalkeuze: Some alloys are inherently more prone to cracking.
- Parameter Optimization: Adjusting scan strategies, pre-heating the build plate (common in SEBM), or using specific laser modulation can reduce cracking susceptibility.
- Verlichting van stress: Prompt heat treatment after the build is crucial.
- Powder Handling and Safety:
- Issue: Fine metal powders (especially reactive materials like Titanium, Aluminum, or potentially Nickel alloys under certain conditions) can be flammable or explosive. Inhalation also poses health risks.
- Mitigation: Experienced providers operate under strict safety protocols: using inert gas handling systems (glove boxes), proper grounding to prevent static discharge, mandatory Personal Protective Equipment (PPE) for operators, specialized vacuum systems, and waste disposal procedures.
- Consistency and Repeatability:
- Uitdaging: Ensuring that parts produced in different builds, on different machines, or at different times exhibit the same dimensions, material properties, and performance.
- Mitigation: Rigorous process control, regular machine calibration and maintenance, stringent powder quality management (testing incoming batches, controlled recycling), standardized operating procedures, comprehensive data logging, and a robust Quality Management System (QMS).
Partnering for Success:
Navigating these challenges successfully requires deep expertise in materials science, process physics, DfAM, and quality control. Established metal AM service providers like Met3dp invest heavily in advanced equipment, process development, skilled personnel, and quality systems to overcome these hurdles consistently. When procuring high-temperature sensor housings via AM, selecting a partner with demonstrated experience in handling relevant materials (IN625, 316L) and a proven track record in delivering high-quality, industrial-grade components is paramount to mitigating risks and achieving project success.
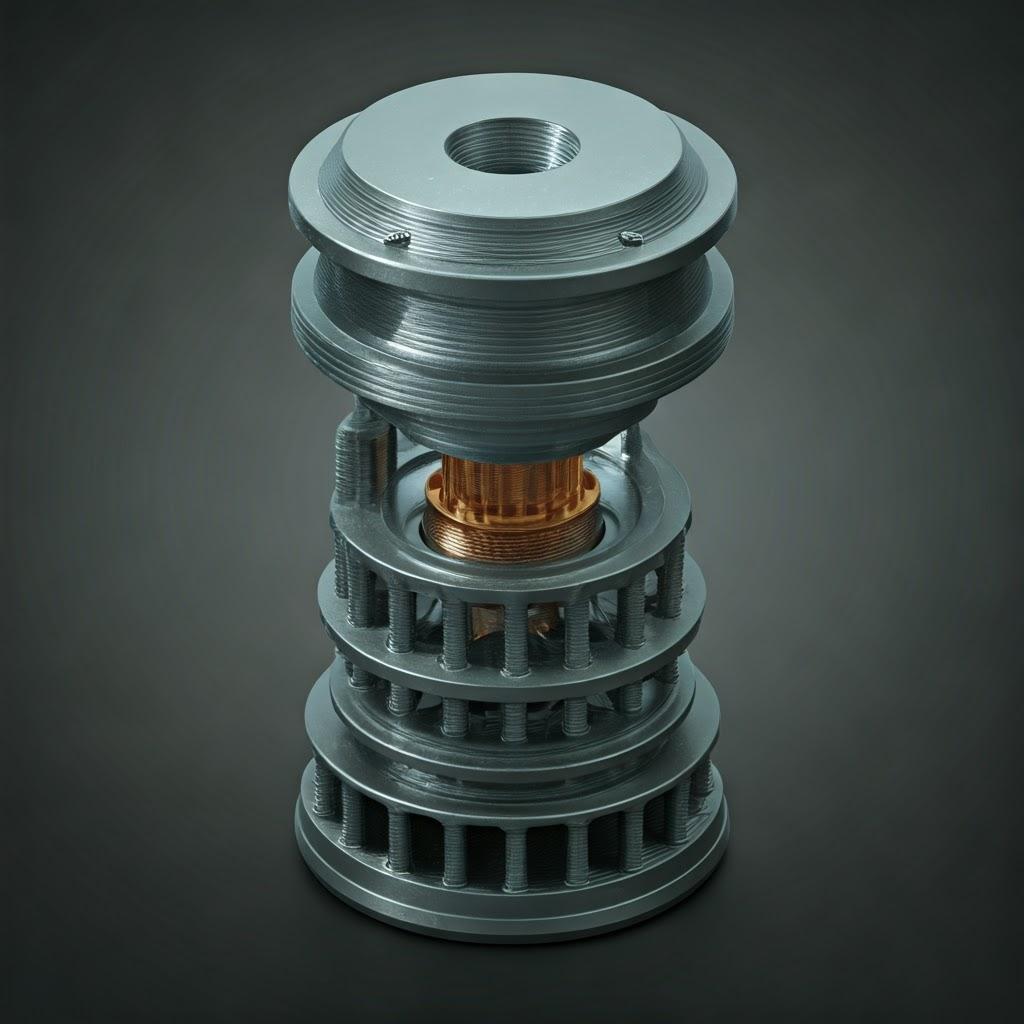
Supplier Selection: Choosing the Right Metal 3D Printing Service Partner
Embarking on the journey of producing high-temperature sensor housings using metal additive manufacturing requires more than just an innovative design and the right material choice; it necessitates selecting the right manufacturing partner. The capabilities, expertise, and quality standards among metal AM service providers can vary significantly. Choosing an unsuitable supplier can lead to project delays, cost overruns, suboptimal part quality, and potentially component failure in critical applications. For engineers and procurement managers in demanding sectors like aerospace, automotive, medical, and industrial manufacturing, conducting thorough due diligence is paramount to establishing a successful and reliable B2B manufacturing partnership.
Key Criteria for Evaluating Metal AM Service Providers:
- Demonstrated Technical Expertise & Relevant Experience:
- Material Specialization: Does the provider have proven, hands-on experience printing, processing, and heat-treating the specific alloy required (e.g., IN625, 316L)? Ask for evidence, such as parameter development documentation or case studies.
- Application Experience: Have they successfully produced parts with similar complexity, size, and functional requirements, particularly for high-temperature or harsh environments? Experience with sensor housings or related components is a significant plus.
- Industry Track Record: Do they understand the specific quality and documentation requirements of your industry (e.g., traceability for aerospace, biocompatibility considerations for medical)?
- Equipment, Technology, and Capacity:
- Machine Portfolio: What specific types of metal AM machines do they operate (e.g., Selective Laser Melting – SLM/LPBF, Selective Electron Beam Melting – SEBM)? Do these align with your material choice (SEBM is often preferred for highly reactive or crack-prone materials, potentially offering benefits in reduced residual stress)? What is the build volume capacity – can it accommodate your part size?
- Technology Relevance: Are their machines current models with robust process monitoring capabilities? How well are they maintained and calibrated? Providers like Met3dp invest in industry-leading systems known for accuracy and reliability.
- Capacity & Scalability: Assess their current workload and machine availability. Can they accommodate your prototype needs quickly? More importantly, do they have the capacity and redundancy to scale up to low or medium-volume series production if required later?
- Material Capabilities & Powder Quality Management:
- Materiaal Portfolio: Beyond IN625 and 316L, what other relevant alloys do they offer?
- Powder Sourcing & Control: This is critical. Where do they source their powders? What are their procedures for testing incoming powder batches (e.g., chemistry, Particle Size Distribution – PSD, morphology, flowability)? How do they handle, store, and recycle powder to prevent contamination and ensure consistent quality? Companies like Met3dp, which manufacture their own hoogwaardige metaalpoeders using advanced gas atomization and PREP technologies, often have superior control over this crucial input material.
- Materiaalcertificering: Can they provide full material traceability and Certificates of Conformance (CoCs) linking the powder batch to the final part?
- Comprehensive Post-Processing Capabilities:
- In-House vs. Outsourced: Identify which essential post-processing steps (stress relief/heat treatment, support removal, basic finishing, CNC machining, inspection) they perform in-house versus manage through external partners. In-house capabilities often allow for better control and potentially faster turnaround.
- Partner Network: If outsourcing, ensure they use qualified and certified partners (e.g., Nadcap certified heat treaters for aerospace).
- Integrated Workflow: The ideal partner manages the entire process seamlessly, from printing through all required post-processing and final inspection, delivering a finished component.
- Quality Management System (QMS) & Certifications:
- ISO 9001: This is the baseline certification for a reputable manufacturing supplier, indicating a structured approach to quality management.
- Industry-Specific Certifications: Depending on your application, look for:
- AS9100: Essential for aerospace suppliers.
- ISO 13485: Required for medical device components.
- IATF 16949: Relevant for automotive suppliers (though less common for pure AM service providers unless integrated).
- Request Documentation: Ask to see current certification documents and inquire about their quality control procedures, including process monitoring, part inspection methods (CMM, scanning), and non-destructive testing (NDT) capabilities if needed.
- Design Support & DfAM Expertise:
- A valuable partner doesn’t just print files; they act as a consultant. Do they offer Design for Additive Manufacturing (DfAM) reviews? Can they provide expert feedback on optimizing your sensor housing design for better printability, reduced support needs, improved performance, and lower cost? A collaborative approach early on is highly beneficial.
- Communication, Responsiveness & Project Management:
- Evaluate their communication style. Are they responsive to inquiries? Do they provide clear and detailed quotes? Will you have a dedicated point of contact or project manager? Effective communication is vital for managing complex AM projects.
- Location and Logistics:
- While global shipping is common, proximity can sometimes be advantageous for very rapid iterations or close collaboration. Assess their shipping experience and partnerships to ensure reliable delivery.
Partnering with Met3dp:
Selecting a metal AM partner is a strategic decision. Companies like Met3dp stand out as a leading provider of additive manufacturing solutions. Headquartered in Qingdao, China, Met3dp specializes in both advanced 3D printing equipment, including SEBM systems known for reliability and accuracy, and the research and manufacture of high-performance metal powders using industry-leading gas atomization and PREP technologies. Their decades of collective expertise span materials science, process optimization, and application development across aerospace, medical, automotive, and other demanding fields. By offering comprehensive solutions and a consultative approach, Met3dp positions itself as a reliable partner capable of guiding clients from design optimization through to the delivery of high-quality, mission-critical high-temperature sensor housings. Thoroughly evaluating potential suppliers against these criteria will help ensure you select a partner who can meet your technical requirements, quality standards, and business objectives.
Understanding Costs and Timelines: Factors Influencing Sensor Housing Production
One of the critical aspects for procurement managers and engineers considering metal additive manufacturing for high-temperature sensor housings is understanding the associated costs and production timelines. While AM offers compelling advantages like design freedom and tooling elimination, its cost structure and lead time drivers differ significantly from traditional manufacturing methods. Having a clear picture of these factors is essential for accurate budgeting, project planning, and realistic expectation setting.
Key Factors Influencing Metal AM Costs:
- Material Type and Consumption:
- Alloy Choice: The base cost of the metal powder is a primary driver. Nickel-based superalloys like IN625 are substantially more expensive (often 5-10x or more) than stainless steels like 316L due to the cost of nickel, molybdenum, niobium, etc.
- Volume: The cost is directly related to the volume of the final part plus the volume of any required support structures. Larger, denser parts consume more expensive powder. Efficient DfAM focusing on lightweighting (where appropriate) can yield significant cost savings.
- Behandeling van poeder: The supplier’s efficiency in handling, recycling, and refreshing powder influences the effective material cost passed on to the customer.
- Part Design Complexity:
- Geometric Intricacy: Highly complex designs with intricate internal channels, very thin walls, or features requiring extensive, difficult-to-remove supports increase the build complexity and post-processing effort, driving up costs.
- Topology Optimization/Lattices: While these techniques reduce material volume (saving material cost), they can sometimes increase build time slightly due to complex scan paths and may require more intensive build preparation and simulation, potentially impacting overall cost.
- Part Size and Build Plate Utilization:
- Footprint & Height: Larger parts occupy more space on the build plate and generally require taller builds, leading to longer print times and higher machine time costs.
- Nesting: The ability to “nest” multiple parts efficiently onto a single build plate significantly impacts cost per part, especially for smaller components. Suppliers aim to maximize build plate utilization to amortize setup and operational costs over more parts.
- Machine Time (Build Time):
- Calculation: This is often a major cost component, calculated based on the estimated time the AM machine is occupied. It depends on the number of layers (determined by part height and layer thickness settings) and the time required to scan the cross-sectional area of the part(s) and supports for each layer.
- Beïnvloedende factoren: Chosen layer thickness (thinner layers = better finish but longer time), scan speed, hatching parameters, and machine overhead rates all contribute.
- Ondersteunende structuren:
- Materiaalkosten: The volume of powder used for supports adds directly to material costs.
- Removal Labor/Time: Removing supports requires manual labor or machining time, adding to the post-processing costs. Designs minimizing support needs are therefore more cost-effective.
- Vereisten voor nabewerking: This is arguably the most significant variable cost factor beyond the basic print.
- Hittebehandeling: Required for stress relief and optimizing properties; adds furnace time and labor costs. Vacuum/inert atmosphere furnaces are expensive to operate.
- HIP (Hot Isostatic Pressing): Adds substantial cost and lead time due to specialized equipment and long cycle times, but necessary for ultimate material integrity in critical applications.
- CNC-bewerking: Required for tight tolerances, threads, and sealing surfaces. Cost depends on the complexity, number of features, material (IN625 is harder to machine), and setup time.
- Afwerking oppervlak: Costs vary widely from simple bead blasting (low cost) to extensive manual polishing (high cost).
- Inspectie: Basic dimensional checks are standard, but detailed CMM reports, NDT (CT, dye penetrant), or pressure testing add cost based on the level required.
- Bestelvolume:
- Schaalvoordelen: While AM avoids tooling costs (making it competitive for prototypes and low volumes), some economies of scale exist. Setup costs (build preparation) are amortized over more parts in larger batches. Optimized nesting on full build plates reduces machine time cost per part. Price breaks are typically offered for higher quantities, but the curve may flatten compared to traditional high-volume methods like casting.
Factors Influencing Production Lead Times:
Lead time is the total duration from order placement to part delivery. It often takes longer than newcomers expect due to the multiple stages involved.
- Pre-Processing (1-3+ days):
- Order review, DfAM consultation (if needed), CAD file preparation, build layout planning (orientation, supports), slicing, and machine programming.
- Machine Queue & Setup (Variable: hours to days):
- Waiting time for an available machine with the correct material loaded. Setup involves loading the file, preparing the build plate, and initiating the print.
- Printing Time (Hours to Days):
- Highly variable based on part size, height, complexity, and density on the build plate. Can range from <12 hours for small parts to 3-7+ days for very large/complex builds or fully packed plates.
- Cooling Time (Hours to 1 day):
- Parts must cool down within the machine or in a controlled manner before removal to minimize thermal shock and stress.
- Post-Processing (Days to Weeks): This stage often dictates the overall lead time.
- Standard: Stress relief, part removal, support removal, and basic bead blast might take 2-5 days.
- Extensive: Adding HIP (requires scheduling with specialized facilities, cycle times are long), multi-axis CNC machining (programming, setup, machining time), advanced polishing, coating, and comprehensive inspection can easily extend this stage by 1-4+ weeks depending on complexity and scheduling.
- Quality Control & Shipping (1-3+ days):
- Final inspection, documentation preparation, packaging, and transit time.
Typical Lead Time Ranges (Estimates):
- Simple Prototype (e.g., 316L, basic finish, minimal machining): 1 – 2 weeks
- Complex Part (e.g., IN625, heat treat, moderate machining, inspection): 3 – 5 weeks
- Highly Critical Part (e.g., IN625, HIP, extensive machining, NDT, coating): 5 – 8+ weeks
Optimizing Cost & Lead Time:
- Engage Early: Discuss design and requirements with your AM provider early (DfAM).
- Clear RFQ: Provide comprehensive information (CAD, drawings, specs, quantities, required dates) in your Request for Quote (RFQ) to enable accurate pricing and lead time estimation.
- Specify Only Necessary Tolerances/Finishes: Avoid over-specifying requirements, as tighter tolerances and finer finishes significantly increase post-processing cost and time.
- Consider Material Choice Carefully: Use IN625 only when its extreme properties are truly necessary; 316L is significantly more cost-effective if its performance envelope is sufficient.
Understanding these cost and time dynamics allows for better planning and decision-making when incorporating metal AM into the supply chain for high-temperature sensor housings.
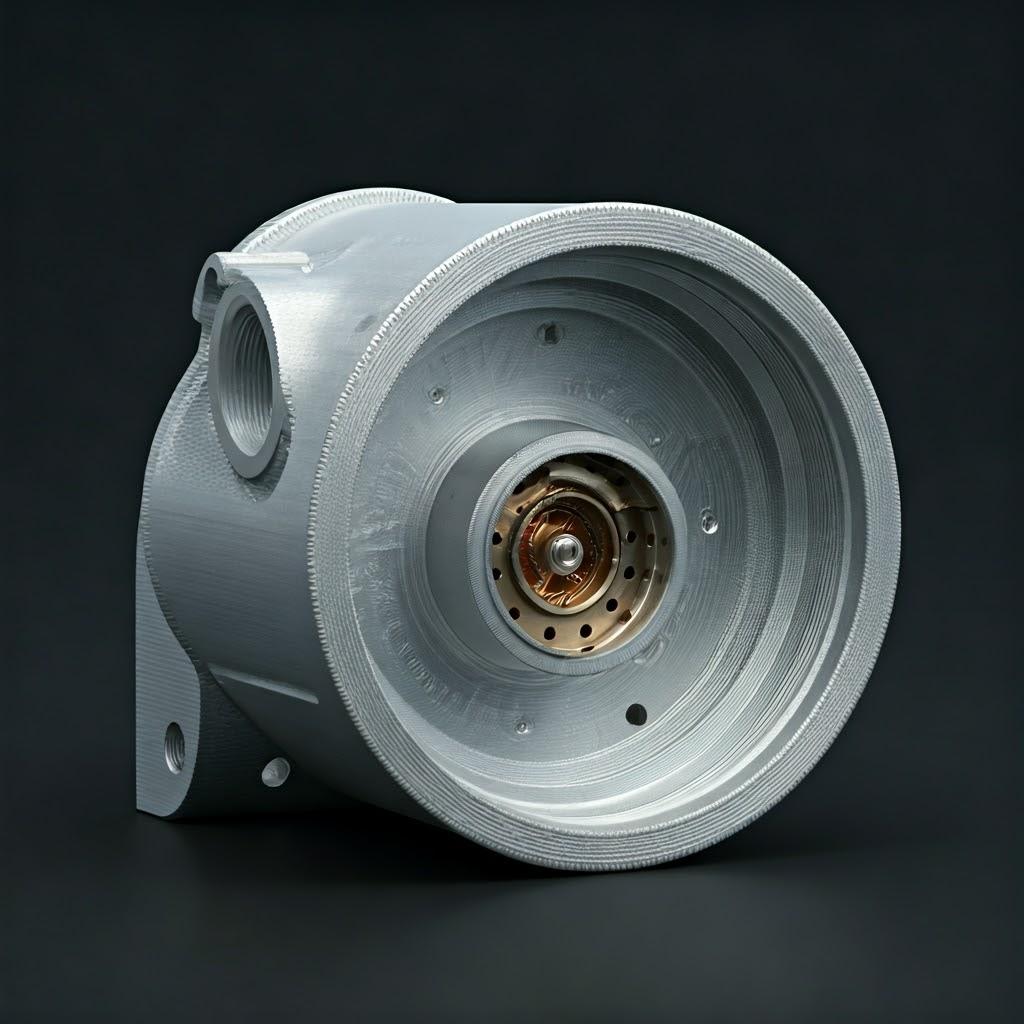
Frequently Asked Questions (FAQ) for High-Temp Sensor Housings
Here are answers to some common questions engineers and procurement specialists have when considering metal additive manufacturing for high-temperature sensor housings:
Q1: How does the temperature resistance and overall performance of 3D printed IN625 or 316L compare to the same alloys produced by traditional methods (wrought, cast)?
A: When produced using optimized parameters on well-maintained machines and subjected to appropriate post-processing (especially stress relief/heat treatment and potentially HIP), metal AM parts made from IN625 and 316L can achieve mechanical properties (tensile strength, yield strength, elongation) that are comparable, and sometimes even superior (particularly fatigue strength after HIP), to conventionally manufactured counterparts. The key is achieving full density (typically >99.9% with PBF processes) and a homogenous, fine-grained microstructure. The temperature resistance is inherent to the alloy composition; therefore, correctly processed AM IN625 will offer similar high-temperature strength and corrosion resistance to wrought IN625, suitable for extreme environments. Likewise, AM 316L will match the performance profile of wrought 316L. However, properties are highly dependent on the entire process chain – from powder quality to print parameters and post-processing execution. Always request material property data or certifications from your supplier.
Q2: Can metal 3D printing reliably produce hermetically sealed sensor housings?
A: Yes, the underlying metal AM processes (SLM, SEBM) are capable of producing fully dense parts (relative density >99.9%) that are inherently leak-tight and suitable for forming the basis of a hermetic seal. The challenge often lies not in the bulk material density but in the design and execution of sealing features. Achieving reliable hermeticity typically involves:
- Ontwerp: Incorporating features suitable for sealing mechanisms (e.g., precisely machined surfaces for O-rings/gaskets, features designed for laser/electron beam welding of feedthroughs or lids).
- Nabewerking: Precision machining of sealing surfaces to achieve required flatness and surface finish is often necessary. Welding operations for feedthroughs or closures must be performed correctly.
- Testen: Implementing rigorous leak testing (e.g., helium leak detection) as part of the quality control process. So, while the AM process provides a dense structure, achieving certified hermetic sealing usually requires careful design integration and post-processing steps.
Q3: What are the main limitations or challenges when using metal AM for high-temperature sensor housings?
A: While powerful, metal AM has limitations to consider:
- As-Built Tolerances & Surface Finish: Generally not as precise as CNC machining, requiring post-processing for critical features.
- Kosten: Can be more expensive than traditional methods for very simple parts or extremely high volumes. Material costs, especially for superalloys like IN625, are high. Extensive post-processing adds significantly to the cost.
- Groottebeperkingen: Build chamber dimensions limit the maximum size of a single-piece part (though large housings can sometimes be printed in sections and joined).
- Residual Stress & Distortion: Requires careful management through DfAM, process control, and mandatory heat treatment.
- Ondersteunende structuren: Need for supports can impact design freedom slightly and requires removal effort.
- Thorough DfAM Required: Simply printing a design made for machining often leads to suboptimal results or failures; designing specifically for AM is crucial.
Q4: Is metal 3D printing a viable option for volume production (e.g., thousands) of sensor housings?
A: Metal AM is increasingly viable for low-to-medium volume production (from tens to thousands of parts annually) for several reasons:
- No Tooling Costs: Eliminates the high upfront investment and lead time for molds or complex fixtures required for casting or stamping, making it cost-effective for moderate volumes.
- Complexe geometrieën: Enables production of complex designs that are difficult or impossible with traditional methods, offering performance advantages that justify the piece price.
- Maatwerk: Allows for cost-effective production of multiple design variants or customized housings within the same production run. However, for very high volumes (tens or hundreds of thousands) of relatively simple sensor housing designs, traditional methods like die casting or high-speed machining may still offer a lower piece price once tooling costs are amortized. The crossover point depends heavily on part complexity, size, material, and required post-processing. As AM technology continues to improve in speed and cost-efficiency, its viability for higher volumes is constantly expanding.
Q5: What specific information should I provide to a metal AM service provider to get an accurate quote (RFQ) for my sensor housing design?
A: To receive the most accurate and timely quote, provide the following:
- 3D CAD-model: In a standard format like STEP or IGES. This is essential for analyzing geometry, volume, and planning the build.
- 2D Engineering Drawing: Clearly defining:
- Material specification (e.g., IN625, 316L, including any specific grade or standard).
- Critical dimensions and required tolerances (using GD&T – Geometric Dimensioning and Tolerancing).
- Surface finish requirements (Ra values) for specific surfaces or overall.
- Identification of any critical features (e.g., sealing surfaces, threads).
- Required Post-Processing: Specify all necessary steps (e.g., stress relief cycle, HIP requirement, specific machining operations, polishing, coating type).
- Hoeveelheid: Number of parts required (for prototypes and potential future volumes).
- Testing & Inspection: Detail any specific testing (leak test, pressure test) or inspection reports (CMM, NDT) needed.
- Required Delivery Date: Your target timeline.
- Application Context (Optional but helpful): Briefly describing the operating environment can help the provider offer better DfAM advice or confirm material suitability.
Providing comprehensive information upfront minimizes delays and ensures the quote accurately reflects the full scope of work.
Conclusion: The Future of High-Performance Sensor Housings with Metal AM
The landscape of manufacturing components for extreme environments is undergoing a significant transformation, and metal additive manufacturing is at the forefront of this evolution. For high-temperature sensor housings – critical protectors of sensitive instruments in aerospace, automotive, power generation, and industrial processing – metal AM is not just an alternative; it is increasingly becoming the optimal solution for achieving unprecedented levels of performance, design integration, and manufacturing agility.
By leveraging the layer-by-layer PBF processes, engineers can finally break free from the constraints of traditional subtractive or forming methods. Metal AM enables the creation of sensor housings with highly complex internal geometries for optimized thermal management or wiring, topology-optimized structures for minimal weight with maximum strength, and consolidated designs that reduce part count and potential failure points. The ability to rapidly prototype and iterate designs accelerates innovation cycles, allowing companies to bring superior sensing solutions to market faster. Furthermore, the capacity to effectively process high-performance alloys like the exceptionally heat-and-corrosion-resistant IN625, alongside versatile workhorses like 316L stainless steel, ensures that housings can be precisely tailored to withstand the specific chemical, thermal, and mechanical challenges of their intended application.
However, unlocking the full potential of metal AM requires a holistic approach. Success hinges on embracing Design for Additive Manufacturing (DfAM) principles from the outset, understanding the nuances of process parameters, meticulously managing post-processing steps like heat treatment and precision machining, and implementing rigorous quality control. Most importantly, it requires partnership with an expert AM service provider equipped with the right technology, materials expertise, and process knowledge.
The future points towards even greater integration of metal AM into the digital manufacturing thread. We anticipate continued advancements in machine speed and accuracy, an expanding portfolio of printable high-temperature materials, enhanced simulation tools for predictable outcomes, and increasingly sophisticated in-process monitoring for quality assurance. As these trends converge, metal AM will become even more accessible and cost-effective, further solidifying its role in producing next-generation, high-performance sensor housings that enable safer, more efficient, and more reliable operations across critical industries.
For organizations looking to harness the power of additive manufacturing for their demanding sensor applications, the journey begins with exploring the possibilities. We invite you to consider how metal AM could elevate your next high-temperature sensor housing project. As a leader in the field, Met3dp provides comprehensive solutions, combining decades of expertise with cutting-edge metal AM equipment and materials. Contact Met3dp today to discuss your specific requirements and discover how our capabilities can power your organization’s additive manufacturing goals, transforming challenges into high-performance realities.
Delen op
MET3DP Technology Co, LTD is een toonaangevende leverancier van additieve productieoplossingen met hoofdkantoor in Qingdao, China. Ons bedrijf is gespecialiseerd in 3D printapparatuur en hoogwaardige metaalpoeders voor industriële toepassingen.
Onderzoek om de beste prijs en een op maat gemaakte oplossing voor uw bedrijf te krijgen!
gerelateerde artikelen
Over Met3DP
Recente update
Ons product
NEEM CONTACT MET ONS OP
Nog vragen? Stuur ons nu een bericht! Na ontvangst van uw bericht behandelen wij uw verzoek met een heel team.
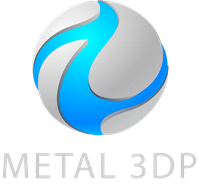
Metaalpoeders voor 3D printen en additieve productie
BEDRIJF
PRODUCT
contact informatie
- Qingdao-stad, Shandong, China
- [email protected]
- [email protected]
- +86 19116340731