3D Printed Shock Mounts for Lightweight Automotive Applications
Inhoudsopgave
Revolutionizing Automotive Performance: An Introduction to 3D Printed Shock Tower Mounts
The relentless pursuit of performance, efficiency, and innovation defines the modern automotive industry. Engineers and designers constantly seek new materials, manufacturing processes, and design philosophies to push boundaries. From enhancing fuel economy and electric vehicle (EV) range to improving handling dynamics and passenger safety, every component is scrutinized for optimization potential. Within the intricate system of a vehicle’s chassis and suspension, the shock tower mount, also known as a strut mount or suspension top mount, plays a deceptively critical role. While often overlooked, this component is pivotal in connecting the suspension strut or shock absorber assembly to the vehicle’s chassis or body structure. It bears significant static and dynamic loads, isolates vibrations, and influences steering feel and overall vehicle stability. Traditionally manufactured through methods like stamping, casting, or machining, the design of shock tower mounts has often been constrained by the limitations of these processes, leading to compromises between strength, weight, and cost.
However, a transformative manufacturing technology is rapidly changing the landscape: Metaal Additive Manufacturing (AM), commonly known as metal 3d printen. This process builds parts layer by layer directly from digital models using high-performance metal powders. Metal AM unlocks unprecedented design freedom, enabling engineers to create highly optimized, lightweight, and complex structures that were previously impossible or prohibitively expensive to produce. For components like shock tower mounts, this technology offers a paradigm shift, moving away from bulky, over-engineered designs towards topologically optimized solutions that deliver superior performance at a fraction of the weight.
What is an Automotive Shock Tower Mount? (Function, Location, Importance)
To fully appreciate the impact of 3D printing, let’s delve deeper into the shock tower mount’s function. Its primary responsibilities include:
- Structural Connection: It serves as the robust upper anchor point for the MacPherson strut or shock absorber assembly, transferring suspension loads directly into the vehicle’s unibody or frame rails (specifically, the reinforced “shock towers” in the engine bay or rear chassis).
- Load Bearing: The mount constantly supports the vehicle’s weight distributed through the suspension spring. During operation, it endures significant dynamic forces generated by bumps, cornering, acceleration, and braking. These forces can be multi-axial and highly variable.
- Vibration Damping & Isolation (NVH Control): Often incorporating elastomeric (rubber or polyurethane) elements, the mount helps dampen high-frequency vibrations originating from the road surface and suspension components, preventing them from reaching the cabin and improving Noise, Vibration, and Harshness (NVH) characteristics.
- Steering Pivot (MacPherson Struts): In vehicles equipped with MacPherson strut front suspension (the most common type), the top mount usually incorporates a bearing that allows the entire strut assembly to rotate as the steering wheel is turned. This pivot function is critical for steering response and accuracy.
Located typically at the top of the front wheel wells (under the hood) and sometimes in the rear chassis structure, the integrity and performance of these mounts are paramount. A failing mount can lead to poor handling, clunking noises, uneven tire wear, compromised braking, and potentially catastrophic suspension failure. Therefore, designing and manufacturing these components requires meticulous attention to material strength, fatigue life, dimensional accuracy, and load path management.
The Evolution of Shock Mount Design and Manufacturing
Historically, shock tower mounts have evolved alongside vehicle construction techniques:
- Early Designs (Stamped Steel): Simple, cost-effective stamped steel components were common, often consisting of multiple pieces welded together. While functional, they were relatively heavy and offered limited design flexibility or NVH isolation.
- Cast Aluminum/Steel: Casting allowed for more integrated designs and better material distribution than stamping, offering improved strength-to-weight ratios. However, casting limitations include minimum wall thicknesses, draft angles, potential porosity issues, and significant tooling costs, making design changes expensive.
- Machined Components (Billet): For high-performance or aftermarket applications, mounts are sometimes machined from solid blocks (billet) of aluminum or steel. This offers high precision and strength but is material-intensive (high waste), time-consuming, and generally the most expensive option, unsuitable for mass production.
- Hybride ontwerpen: Many modern OEM mounts combine stamped steel or cast aluminum structural elements with integrated elastomeric bushings and bearings for NVH control and steering pivot functions.
While these traditional methods have served the industry well, they inherently struggle to achieve the complex, load-path-optimized, and ultra-lightweight geometries that modern vehicle architectures demand, especially with the rise of electrification and stringent efficiency targets.
The Emergence of Metal Additive Manufacturing in Automotive Components
Metal AM technologies, such as Powder Bed Fusion (PBF) – which includes Selective Laser Melting (SLM) and Electron Beam Melting (EBM) – are disrupting traditional automotive manufacturing paradigms. Initially adopted for rapid prototyping and tooling, the technology has matured significantly, now enabling the production of functional end-use parts, including critical structural components. The ability to:
- Create intricate internal channels and lattice structures.
- Consolidate multiple parts into a single, complex component.
- Utilize advanced alloys optimized for specific performance characteristics.
- Achieve near-net-shape production with reduced material waste.
- Facilitate rapid design iteration without costly tooling changes.
…makes metal AM exceptionally well-suited for components where weight reduction and performance optimization are critical – precisely the requirements for next-generation shock tower mounts.
Why Lightweighting Matters: Fuel Efficiency, Performance, and EV Range
Reducing vehicle mass, or “lightweighting,” is a primary objective across the automotive spectrum. The benefits are multi-faceted:
- Fuel Efficiency / Energy Consumption: Less weight requires less energy to accelerate and maintain speed, directly improving fuel economy in internal combustion engine (ICE) vehicles and increasing range in Electric Vehicles (EVs). This is crucial for meeting tightening global emissions regulations and consumer demands for longer EV ranges.
- Performance & Handling: Reducing unsprung mass (components like wheels, tires, brakes, and parts of the suspension) and overall vehicle weight improves acceleration, braking distances, and cornering agility. Lighter components respond faster to inputs, enhancing driver feedback and vehicle dynamics. Lightweighting the chassis, including shock towers, contributes to lowering the center of gravity.
- Payload Capacity: In commercial vehicles, reducing chassis weight can directly increase the allowable payload capacity.
- Secondary Weight Savings: Lighter components can sometimes allow for downsizing of related systems (e.g., brakes, powertrain components), leading to a cascading weight reduction effect.
Shock tower mounts, while seemingly small, are located high in the vehicle structure and contribute to overall mass. Lightweighting them using AM offers tangible benefits, particularly when multiplied across millions of vehicles produced annually. For procurement managers and B2B suppliers in the automotive sector, sourcing innovative lightweight solutions like 3D printed shock mounts represents a significant opportunity to add value and meet OEM demands.
Introducing Met3dp’s Role as a Premier Metal AM Solutions Provider for Automotive Procurement
Meeting the demanding requirements of the automotive industry for high-quality, reliable, and cost-effective 3D printed components requires a specialized partner. Met3dp, headquartered in Qingdao, China, is a leading provider of comprehensive metal additive manufacturing solutions. With decades of collective expertise, Met3dp specializes in both advanced metaal 3D printen equipment, including industry-leading Selective Electron Beam Melting (SEBM) systems known for accuracy and reliability, and the production of high-performance metal powders tailored for AM processes.
Our company employs cutting-edge gas atomization and Plasma Rotating Electrode Process (PREP) technologies to manufacture spherical metal powders (including advanced aluminum alloys like A7075 and AlSi10Mg) with exceptional sphericity, flowability, and purity – critical factors for printing dense, high-integrity automotive parts. We partner with automotive OEMs, Tier 1 suppliers, and engineering firms to develop and implement metal AM solutions, from initial design consultation and prototyping to series production support. For procurement professionals seeking a reliable B2B supplier capable of delivering mission-critical, lightweight automotive components like 3D printed shock mounts, Met3dp offers the technology, materials, and expertise required to accelerate innovation and achieve demanding performance targets.
Critical Applications: Where are 3D Printed Shock Mounts Used?
The unique advantages of metal additive manufacturing – particularly the ability to create lightweight, complex, and high-strength components – make 3D printed shock tower mounts an increasingly attractive solution across various segments of the automotive industry. While not yet ubiquitous in mass-market economy cars due to cost considerations, their adoption is rapidly growing in applications where performance, weight savings, customization, or rapid development are paramount. B2B suppliers and wholesale distributors focusing on advanced automotive components are seeing increased demand from these key sectors:
1. High-Performance and Racing Vehicles: Pushing the Limits
This is arguably the most prominent and earliest adoption area for 3D printed shock mounts. In motorsport (Formula 1, WEC, DTM, GT racing, rally, etc.) and high-performance road cars (supercars, hypercars), every gram saved translates directly into faster lap times and competitive advantage.
- Extreme Lightweighting: Topology optimization, enabled by AM, allows engineers to remove every non-essential gram of material while maintaining or even increasing stiffness and strength in critical load paths. This is vital for reducing unsprung mass and overall vehicle weight.
- Optimized Stiffness-to-Weight Ratio: AM allows for complex internal lattice structures and optimized external geometries that maximize stiffness exactly where needed, improving suspension accuracy, responsiveness, and handling precision under extreme cornering and braking loads.
- Rapid Iteration and Customization: Racing teams constantly refine suspension setups. AM allows for the rapid production of custom mount designs tailored to specific tracks, vehicle setups, or driver preferences, without the long lead times and high costs associated with traditional tooling. Design changes can be implemented and tested within days, not weeks or months.
- Integration of Features: Cooling ducts for brakes or sensors, or specific mounting points for aerodynamic elements, can potentially be integrated directly into the shock mount design, further consolidating parts and saving weight.
- Materiaalprestaties: Access to high-strength aluminum alloys (like A7075) or even titanium alloys (though less common for mounts due to cost) via AM allows for performance exceeding typical cast or stamped components.
Procurement managers for racing teams and performance vehicle manufacturers prioritize suppliers who can deliver cutting-edge technology, rapid turnaround, and guaranteed material properties – areas where specialized AM providers excel.
2. Electric Vehicles (EVs): Optimizing Weight and Battery Packaging
The transition to electric mobility presents unique engineering challenges, making lightweighting even more critical than in ICE vehicles. Batteries are heavy, significantly impacting overall vehicle mass and requiring compensatory weight savings elsewhere.
- Maximizing Range: Reducing the weight of components like shock mounts directly contributes to extending the vehicle’s driving range on a single charge – a key purchasing factor for consumers.
- Offsetting Battery Mass: Lightweighting the chassis and suspension components helps offset the substantial weight of the battery pack, maintaining desirable vehicle dynamics and potentially allowing for smaller, lighter suspension components elsewhere.
- Packaging Constraints: EV architectures often have unique packaging requirements due to the placement of batteries, electric motors, and control units. The design freedom of AM allows shock mounts to be shaped precisely to fit into tight spaces or around other components, something often difficult with traditional manufacturing constraints.
- NVH Challenges: EVs are inherently quieter than ICE vehicles, making suspension and road noise more perceptible. Optimized shock mount designs, potentially incorporating complex internal damping structures enabled by AM, could play a role in fine-tuning NVH characteristics specific to EV powertrains.
B2B suppliers focusing on the EV market need to offer solutions that address these specific challenges. Providing lightweight, topology-optimized 3D printed shock mounts manufactured from reliable materials like AlSi10Mg or A7075 aligns perfectly with the demands of EV OEMs seeking competitive advantages in range and performance.
3. Luxury and Premium Automotive Segments: Customization and Advanced Engineering
Manufacturers in the luxury and premium segments often compete based on technological prowess, advanced engineering, bespoke features, and exclusivity. Metal AM fits well within this philosophy.
- Low-Volume Production Viability: For limited-edition models or high-end vehicles with lower production volumes, the tooling costs associated with casting or stamping can be disproportionately high. AM offers a cost-effective way to produce complex, high-performance components without requiring dedicated tooling, making advanced designs feasible.
- Bespoke Engineering Solutions: AM enables the creation of unique shock mount designs tailored to specific model requirements or even customer personalization requests (in extreme cases), reinforcing brand exclusivity.
- Demonstrating Technological Leadership: Incorporating advanced manufacturing techniques like metal 3D printing into visible or critical components showcases a brand’s commitment to innovation and cutting-edge engineering, appealing to discerning customers.
- Prestatieverbetering: Similar to performance cars, luxury vehicles benefit from improved ride comfort and handling precision offered by optimized, lightweight suspension components.
Suppliers targeting the luxury automotive market must emphasize quality, precision, material excellence, and the ability to deliver unique design solutions. Metal 3D printing provides a powerful tool to meet these exacting standards.
4. Niche Vehicle Manufacturing and Prototyping: Speed and Flexibility
Beyond mainstream production, AM shines in niche applications and during the vehicle development process.
- Specialty Vehicles: Manufacturers of kit cars, armored vehicles, accessible vehicles, or other low-volume specialty vehicles can leverage AM for producing complex mounts without investing in expensive tooling.
- Aftermarket Performance Parts: Companies developing high-performance suspension upgrades for existing vehicle platforms can use AM to rapidly design, test, and produce optimized shock mounts offering superior performance compared to OEM parts.
- Snel prototypen: During the design and validation phase of any new vehicle program (including mass-market cars), engineers need to test multiple design iterations quickly. Metal AM allows for the production of functional prototypes of shock mounts with production-intent materials in a matter of days. This drastically accelerates the development cycle, allows for real-world testing earlier, and reduces overall R&D costs compared to traditional prototype tooling.
Automotive prototyping services and suppliers catering to niche manufacturers find metal AM indispensable for its speed, flexibility, and ability to produce functional parts directly from CAD data.
5. Potential in Commercial and Heavy-Duty Vehicle Sectors for Specialized Needs
While cost sensitivity is high in the commercial vehicle sector, specific applications could benefit from 3D printed mounts:
- Specialized Load Requirements: Trucks or buses with unique suspension configurations or extreme load demands might benefit from topology-optimized mounts designed for specific stress distributions.
- Weight Reduction in Specific Areas: Reducing weight in certain areas of large trucks can contribute to fuel savings or increased payload capacity over the vehicle’s lifetime.
- Replacement Parts / Legacy Vehicles: For older or specialized commercial vehicles where original tooling no longer exists, AM offers a potential solution for producing obsolete or hard-to-find replacement shock mounts on demand.
Meeting B2B Supply Chain Demands for Innovative Automotive Components
Across all these applications, a common thread emerges: the need for reliable, high-quality B2B suppliers capable of delivering these advanced components consistently. Procurement managers and engineering leads require partners who understand the nuances of metal AM, possess robust quality control systems, offer material expertise (especially with certified automotive-grade powders like A7075 and AlSi10Mg), and can scale production from prototypes to low or medium volumes. Companies like Met3dp, with integrated capabilities spanning powder production, advanced printing technologies (like SEBM), and application engineering support, are positioned to meet these evolving supply chain demands for innovative, lightweight automotive solutions like 3D printed shock tower mounts. The ability to procure these components wholesale or through structured supply agreements is becoming increasingly important as adoption grows.
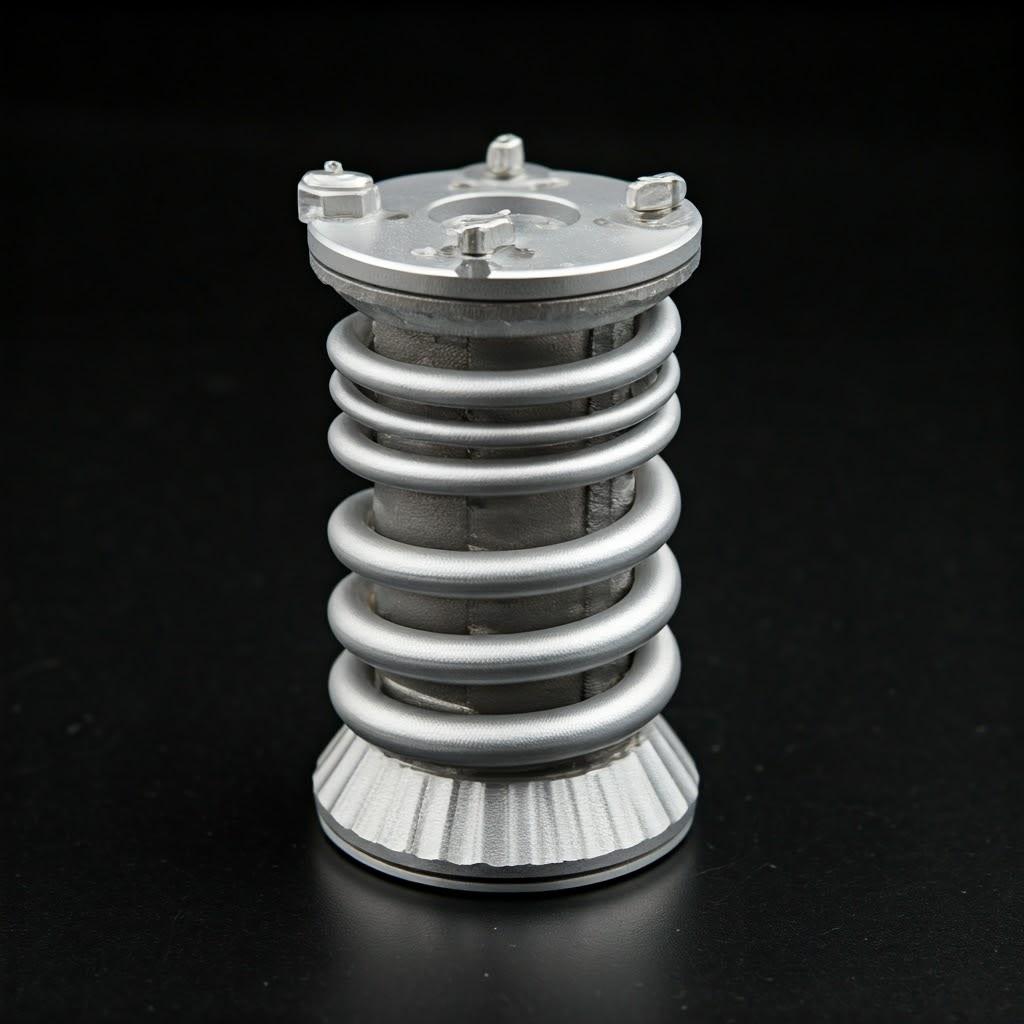
The Additive Advantage: Why Use Metal 3D Printing for Shock Tower Mounts?
The growing interest in metal 3D printing for automotive components like shock tower mounts isn’t just about adopting novel technology; it’s driven by tangible engineering and business advantages over traditional manufacturing methods like casting, stamping, and machining. These benefits address key industry pressures for improved performance, efficiency, and faster development cycles, making AM a compelling value proposition for automotive OEMs and suppliers engaged in B2B transactions for advanced components.
1. Unprecedented Design Freedom: Topology Optimization and Complex Geometries
This is perhaps the most significant advantage of AM. Unlike subtractive methods (machining) or forming methods (stamping, casting) that have inherent geometric constraints, additive manufacturing builds parts layer by layer, allowing for almost limitless complexity.
- Topologieoptimalisatie: This computational design technique allows engineers to define load cases, boundary conditions, and design space, and the software algorithm iteratively removes material from non-critical areas, leaving behind an organic, load-path-optimized structure. The result is a component that uses the minimum amount of material necessary to meet or exceed performance requirements. For a shock mount, this means achieving high stiffness and strength specifically where forces are concentrated, while drastically reducing weight elsewhere. Such complex, often bone-like structures are typically impossible or impractical to manufacture conventionally.
- Complexe interne kenmerken: AM can create intricate internal channels (e.g., for cooling or hydraulic damping, though less common in basic mounts) or complex lattice structures (gyroids, honeycombs) within the part. Lattices can further reduce weight while maintaining structural integrity or providing specific energy absorption characteristics, potentially enhancing crash performance or NVH properties.
- Conformal Design: Mounts can be designed to perfectly conform to surrounding components or fit within highly constrained packaging spaces in the vehicle chassis, maximizing space utilization – a key benefit in densely packed modern vehicles, especially EVs.
2. Significant Weight Reduction Compared to Traditional Manufacturing
Directly resulting from design freedom and topology optimization, metal AM enables substantial weight savings for shock tower mounts, often ranging from 30% to 60% or even more compared to equivalent cast or machined components designed for the same load cases.
- Reduced Material Usage: Topology optimization ensures material is placed only where functionally required.
- Elimination of “Over-Engineering”: Traditional methods often require bulkier designs to compensate for manufacturing limitations or uncertainties in load distribution. AM allows for more precise material placement.
- Impact on Vehicle Dynamics: As discussed earlier, reducing weight, especially unsprung mass or mass high in the vehicle structure, directly improves handling, acceleration, braking, and fuel/energy efficiency. These gains are highly sought after by automotive engineers and provide a competitive edge. For B2B suppliers, offering verifiable weight reduction through AM components is a strong selling point.
3. Part Consolidation: Reducing Assembly Complexity and Potential Failure Points
Traditional shock mount assemblies often consist of multiple components (e.g., main bracket, reinforcement plates, bearing housings) that need to be bolted, welded, or pressed together. AM allows designers to integrate these multiple functions into a single, monolithic printed part.
- Verminderd aantal onderdelen: Fewer individual parts simplify the supply chain, inventory management, and the final vehicle assembly process.
- Elimination of Joints/Fasteners: Joints (welds, bolts, rivets) are often potential points of stress concentration, corrosion initiation, or failure. A consolidated AM part eliminates these interfaces, potentially increasing overall durability and reliability.
- Reduced Assembly Time and Labor: Fewer parts to assemble directly translates to lower labor costs and faster throughput on the vehicle production line.
- Improved Dimensional Accuracy: Assembling multiple parts introduces tolerance stack-up issues. A single printed part can often hold tighter overall tolerances for critical interfaces.
This consolidation advantage is a significant factor for procurement departments looking to optimize overall manufacturing costs and improve product reliability.
4. Rapid Prototyping and Iterative Design Cycles for Faster Development
The automotive development process is lengthy and expensive. AM drastically accelerates the prototyping and validation stages for components like shock mounts.
- Snelheid: Functional metal prototypes can be produced directly from CAD data in days, compared to weeks or months required for traditional prototype tooling (e.g., soft tooling for casting, CNC programming and setup for machining).
- Cost-Effectiveness for Iteration: Engineers can design, print, and test multiple design variations quickly and relatively cheaply. This allows for more thorough optimization and validation before committing to final production design, reducing the risk of costly late-stage changes.
- Testing with Production Intent Materials: AM prototypes can be made using the same high-performance alloys (like A7075 or AlSi10Mg) intended for final production, providing much more accurate test results compared to prototypes made from different materials or processes. Companies like Met3dp can support this rapid prototyping phase, providing quick turnaround times for B2B clients.
5. Material Efficiency: Near-Net-Shape Production Minimizing Waste
Additive manufacturing is fundamentally different from subtractive manufacturing (machining from billet), where a significant portion of the raw material is cut away and becomes scrap (chips).
- Reduced Buy-to-Fly Ratio: AM processes, particularly powder bed fusion, use only the material needed to build the part and its supports. While some powder is non-recyclable or requires reprocessing, the overall material utilization is typically much higher than machining complex parts from billet. This “buy-to-fly” ratio (weight of raw material purchased vs. weight of the final part) is significantly lower.
- Duurzaamheid: Reduced material waste contributes to more sustainable manufacturing practices, an increasingly important factor for automotive brands and their supply chains.
- Cost Savings on Expensive Materials: For higher-cost alloys, minimizing material waste directly translates to lower component costs.
6. On-Demand Manufacturing and Distributed Production Potential for Automotive Suppliers
AM facilitates a more flexible and resilient supply chain model.
- Digital Inventory: Designs exist as digital files, allowing parts to be printed only when needed (on-demand manufacturing). This reduces the need for large physical inventories of spare parts or low-volume components.
- Distributed Manufacturing: Parts can potentially be printed at different locations closer to the point of assembly, provided certified machines, materials, and processes are used. This can reduce shipping costs and lead times, and improve supply chain resilience against disruptions. B2B suppliers can leverage this by establishing certified AM production hubs.
7. Enhanced Performance Characteristics: Stiffness-to-Weight Ratio Optimization
Ultimately, the combination of design freedom, lightweighting, and advanced materials allows 3D printed shock mounts to deliver superior performance.
- Geoptimaliseerde laadpaden: Ensuring forces are transmitted efficiently through the structure minimizes stress concentrations and maximizes stiffness.
- Improved NVH Tuning: Complex internal structures could potentially be designed to dampen specific frequencies more effectively than traditional elastomeric elements alone.
- Higher Fatigue Life: Optimized designs and high-quality AM processes can lead to components with excellent fatigue resistance, crucial for suspension components enduring millions of load cycles.
In summary, metal 3D printing offers a compelling suite of advantages for producing automotive shock tower mounts, moving beyond the constraints of traditional methods to deliver lighter, stronger, more optimized components faster and potentially more sustainably. These benefits align directly with the core objectives of the modern automotive industry, making AM an essential technology for forward-thinking manufacturers and their B2B procurement partners.
Material Matters: Recommended Metal Powders for 3D Printed Shock Mounts
Choosing the right material is fundamental to the success of any engineering component, and 3D printed shock tower mounts are no exception. The demanding automotive environment requires materials that offer a specific balance of properties: high strength-to-weight ratio, good fatigue resistance, adequate stiffness, corrosion resistance, and processability via additive manufacturing techniques. For structural automotive applications like shock mounts, high-performance aluminum alloys are often the primary candidates due to their low density combined with respectable mechanical properties. Two alloys stand out for metal AM in this context: A7075 en AlSi10Mg. The selection between them often depends on the specific performance requirements versus cost considerations. Equally crucial is the quality of the metal powder itself, as this directly impacts the final part’s integrity and performance – an area where specialized powder manufacturers like Met3dp play a vital role for B2B customers demanding consistency and reliability.
Introduction to High-Performance Aluminum Alloys in AM
Aluminum alloys are attractive for automotive lightweighting due to their density being approximately one-third that of steel. While traditional wrought aluminum alloys (like the 6000 and 7000 series) and cast alloys (like A356/A357, similar to AlSi7Mg, and AlSi10Mg) have been used for decades, adapting them or developing new variations for the layer-by-layer fusion process of AM presents unique challenges and opportunities. AM processes involve rapid melting and solidification, leading to microstructures often different from conventionally processed materials, which influences mechanical properties. Careful control over alloy composition and printing parameters is necessary to achieve desired performance.
Focus on A7075: Properties, Applications, and Why it Excels
- Samenstelling: A7075 is a 7000-series aluminum alloy, with zinc (typically 5-6%) as the primary alloying element, along with smaller amounts of magnesium and copper.
- Belangrijkste eigenschappen:
- Zeer hoge sterkte: When properly heat-treated (typically to a T6 temper condition – solution heat-treated and artificially aged), A7075 achieves tensile strengths comparable to many steels, making it one of the highest-strength aluminum alloys available. Its strength-to-weight ratio is exceptional.
- Goede vermoeiingssterkte: Critical for suspension components enduring cyclic loading.
- Fair Machinability: Can be machined to achieve tight tolerances on critical features after printing.
- Lower Corrosion Resistance (Compared to other Al alloys): More susceptible to corrosion, especially stress corrosion cracking (SCC), particularly in older temper conditions or if not properly treated/coated. Careful design and appropriate surface treatments (e.g., anodizing, painting) are often necessary. AM processing can influence SCC behavior.
- Hittebehandeling: Achieving the high-strength T6 temper typically requires a solution heat treatment followed by quenching and artificial aging. This post-processing step is crucial but adds complexity and cost, and requires careful control to minimize part distortion.
- AM Processability: Printing A7075 can be challenging due to its wide solidification range and susceptibility to hot cracking during the rapid heating/cooling cycles of AM. However, advancements in machine parameters, process control, and specifically adapted A7075 powder chemistries have made it increasingly feasible, though often requiring more expertise and finer tuning than alloys like AlSi10Mg.
- Toepassingen: Due to its high strength, it’s ideal for demanding structural applications where weight saving is critical and high loads are encountered. This includes aerospace structures, high-performance sporting goods, and critically loaded automotive components like suspension parts and potentially shock mounts in racing or premium vehicles.
- Why it Excels for Demanding Mounts: When maximum strength and minimum weight are the absolute priorities, and the associated costs (material, printing challenges, heat treatment) are acceptable, A7075 is a top contender for high-performance shock tower mounts.
Focus on AlSi10Mg: Properties, Applications, and Suitability
- Samenstelling: AlSi10Mg is an aluminum alloy containing approximately 9-11% silicon and small amounts of magnesium. It’s closely related to traditional casting alloys.
- Belangrijkste eigenschappen:
- Excellent AM Processability: This is arguably its biggest advantage. The silicon content provides good fluidity in the melt pool and a narrow solidification range, making it relatively easy to print dense, crack-free parts with a wide range of parameters on most laser powder bed fusion (LPBF/SLM) machines.
- Goede sterkte en hardheid: While not as strong as A7075-T6, AlSi10Mg offers a good combination of strength (often comparable to cast A356-T6) and hardness in the as-printed or stress-relieved state. Heat treatment can further enhance properties.
- Goed lasbaar: While less relevant for AM parts themselves, it indicates good fusion characteristics.
- Goede corrosiebestendigheid: Generally better than A7075.
- Good Thermal Properties: Offers good thermal conductivity.
- Hittebehandeling: Parts are often used in the as-printed state (after stress relief). Solution treatment and aging can be applied to increase strength and ductility, but the response is less dramatic than with A7075. Stress relief is commonly performed to reduce internal stresses built up during printing.
- Toepassingen: Due to its excellent printability and good all-around properties, AlSi10Mg is one of the most widely used aluminum alloys in metal AM. Applications include heat exchangers, engine parts, housings, brackets, and general-purpose structural components across automotive, aerospace, and industrial sectors.
- Suitability for General Automotive Mounts: For many mainstream or less extreme performance applications, AlSi10Mg offers a very attractive balance of good mechanical properties, excellent printability (leading to potentially lower printing costs and higher yields), and lower post-processing complexity compared to A7075. It’s often the default choice for lightweight aluminum AM components unless the extreme strength of A7075 is mandated.
Comparative Analysis: A7075 vs. AlSi10Mg for Shock Mounts
The choice between these two materials requires careful consideration of the specific application’s priorities.
Functie | A7075 (Typically T6 condition post-AM) | AlSi10Mg (As-printed or Stress Relieved/Aged) | Considerations for Shock Mounts |
---|---|---|---|
Dikte | ~2.81 g/cm³ | ~2.67 g/cm³ | Both offer significant weight savings over steel (~7.85 g/cm³). AlSi10Mg is slightly lighter. |
Opbrengststerkte | Very High (~450-500+ MPa) | Moderate (~230-280 MPa as-printed) | A7075 offers significantly higher strength, crucial for highly stressed, performance-critical mounts. |
Ultimate Tensile Str. | Very High (~520-570+ MPa) | Good (~350-450 MPa as-printed) | A7075 provides a greater safety margin for ultimate load cases. |
Elongation (Ductility) | Lower (~5-11%) | Moderate (~5-10% as-printed, can improve w/ HT) | Both can be relatively brittle compared to wrought alloys. Design must account for lower ductility. Heat treatment affects this. |
Vermoeidheid Sterkte | Goed | Fair to Good | A7075 generally superior, vital for suspension longevity. Requires careful design and process control for both. |
AM Verwerkbaarheid | More Challenging (Cracking risk) | Excellent (Robust, widely used) | AlSi10Mg generally leads to easier, more reliable printing with wider process windows, potentially lowering print cost/time. |
Hittebehandeling | Required (T6 for high strength) | Optional (Stress relief common, Aging possible) | A7075 requires complex, controlled heat treatment adding cost and distortion risk. AlSi10Mg often usable with just stress relief. |
Corrosieweerstand | Fair (Requires protection) | Goed | AlSi10Mg may require less stringent surface protection in some environments. |
Kosten | Higher (Powder, processing, HT) | Lower (Powder, easier processing) | A7075 is generally a more expensive solution overall due to material cost and processing complexity. |
Het meest geschikt voor | Extreme performance, high-stress, max weight saving applications (Racing, Supercars) | General lightweighting, good balance of properties & cost, complex geometries (EVs, Premium, Prototyping) | Match the material to the specific performance tier and cost target of the vehicle program. |
Exporteren naar Sheets
The Importance of Powder Quality: Sphericity, Flowability, Purity – Met3dp’s Expertise
Regardless of the alloy chosen, the quality of the metal powder feedstock is paramount for successful additive manufacturing, especially for demanding automotive applications requiring consistent, high-integrity parts in B2B supply chains. Key powder characteristics include:
- Sfericiteit: Ideally spherical powder particles ensure good flowability and high packing density in the powder bed. This leads to uniform layers and reduces the risk of voids or porosity in the final part. Irregular shapes or satellites (smaller particles stuck to larger ones) hinder flow and packing.
- Vloeibaarheid: Powders must flow consistently and smoothly through the printer’s recoating mechanism to create uniform layers across the build platform. Poor flowability can lead to uneven layers, defects, and build failures.
- Deeltjesgrootteverdeling (PSD): A controlled PSD, optimized for the specific AM machine and process (e.g., layer thickness), is crucial for achieving high part density and good surface finish. Too many fines can impair flowability and pose safety hazards, while too many large particles can lead to poor resolution and packing density.
- Purity / Low Oxygen Content: Contamination (e.g., oxygen, nitrogen, moisture) can lead to porosity, embrittlement, and compromised mechanical properties in the final part. High purity powders with low interstitial gas content are essential for critical applications.
Met3dp understands that premium parts start with premium powder. We employ toonaangevende poederproductietechnologieën to ensure our customers receive materials optimized for AM:
- Gasverstuiving (GA): This process uses high-velocity inert gas jets (like Argon or Nitrogen) to break up a stream of molten metal into fine, spherical droplets that solidify rapidly. Our advanced gas atomization equipment utilizes unique nozzle and gas flow designs to achieve exceptional sphericity and good flowability, crucial for consistent printing.
- Plasma roterende elektrode proces (PREP): Particularly suited for reactive or high-melting-point metals (though applicable to others), PREP involves rotating a consumable electrode rod while its tip is melted by a plasma torch. Centrifugal force ejects molten droplets that solidify in flight into highly spherical powders with very high purity and minimal satellites.
By controlling the entire process from alloy melting to atomization and powder classification, Met3dp ensures high consistency batch-to-batch, providing automotive manufacturers and their procurement teams with the reliable, high-quality aluminum powders (including A7075 and AlSi10Mg variants optimized for AM) needed to produce robust and reliable 3D printed components.
Sourcing High-Quality Aluminum Powders: Considerations for Wholesale Buyers and Procurement Managers
When sourcing metal powders for AM production, especially in bulk for automotive applications, procurement managers should consider:
- Supplier Manufacturing Process: Does the supplier use advanced atomization techniques (GA, PREP) known for producing high-quality spherical powder?
- Quality Control & Certification: Does the supplier have robust quality control procedures (e.g., chemical analysis, PSD analysis, morphology checks, flow testing)? Can they provide batch-specific certifications (Certificates of Conformity/Analysis)? Are they certified to relevant quality standards (e.g., ISO 9001)?
- Consistentie: Can the supplier guarantee consistent properties (PSD, chemistry, flowability) from batch to batch, crucial for repeatable manufacturing?
- Alloy Availability & Customization: Does the supplier offer the specific alloys needed (A7075, AlSi10Mg optimized for AM)? Can they potentially offer custom alloy development?
- Packaging & Handling: Are powders appropriately packaged under inert gas to prevent contamination and moisture uptake?
- Technische ondersteuning: Does the supplier offer technical support regarding powder handling, storage, and recommended printing parameters?
Met3dp’s Portfolio: Tailored Metal 3D Printing Powders for Optimal Performance
Met3dp manufactures a wide range of high-quality metal powders optimized specifically for laser and electron beam powder bed fusion processes. Our portfolio includes not only standard alloys like AlSi10Mg but also advanced and innovative materials such as high-strength A7075, Titanium alloys (Ti6Al4V, TiNi, TiTa, TiAl, TiNbZr), Cobalt-Chrome (CoCrMo), various Stainless Steels, Nickel-based Superalloys, and more. By leveraging our advanced powder making systems and deep expertise in materials science and additive manufacturing, we provide powders designed to deliver dense, high-quality metal parts with superior mechanical properties, meeting the stringent demands of the automotive industry. Explore our comprehensive range of Metal 3D Printing Powders or contact our team to discuss your specific material requirements for your 3D printed shock mount project or other automotive applications.
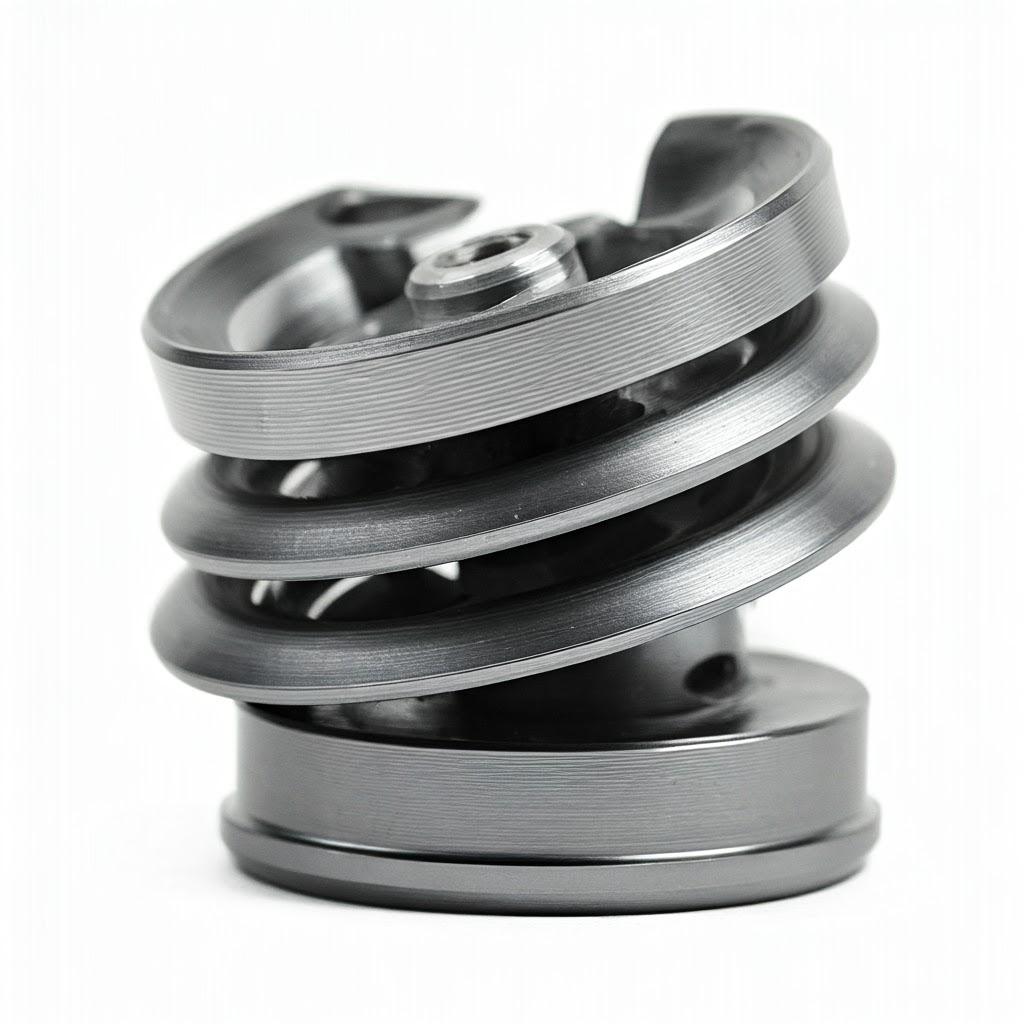
Design for Additive Manufacturing (DfAM): Optimizing Shock Mounts for 3D Printing
Transitioning from traditional manufacturing paradigms to metal additive manufacturing (AM) for components like automotive shock tower mounts requires more than simply converting an existing CAD file. To truly harness the power of AM and achieve the desired benefits of lightweighting, performance enhancement, and cost-effectiveness, engineers must embrace Ontwerp voor additieve productie (DfAM). DfAM is a methodology that integrates knowledge of the specific AM process capabilities and limitations directly into the design phase. It’s about thinking in terms of layers, supports, thermal behavior, and material properties unique to AM, rather than being constrained by the rules of casting, machining, or stamping. For B2B suppliers and procurement managers evaluating AM solutions, understanding DfAM principles is crucial for assessing a potential partner’s capability to deliver truly optimized and manufacturable components.
Fundamental DfAM Principles for Metal Powder Bed Fusion (PBF)
Metal Powder Bed Fusion (PBF) processes, including Selective Laser Melting (SLM) / Laser Powder Bed Fusion (LPBF) and Selective Electron Beam Melting (SEBM) – a technology where Met3dp possesses significant expertise – build parts by selectively melting layers of metal powder using a focused energy source (laser or electron beam). Key DfAM considerations stem from this layer-wise approach:
- Layer-Based Construction: Parts are built slice by slice. Features must be designed considering this build direction.
- Ondersteunende structuren: Overhanging features or sections angled below a certain threshold (typically < 45° from the horizontal plane) require support structures. These supports anchor the part to the build plate, prevent warping due to thermal stresses, support overhanging features during the build, and help conduct heat away from the melt zone. Designing to minimize the need for supports is a primary DfAM goal.
- Thermisch beheer: The rapid melting and solidification cycles create significant thermal gradients and internal stresses within the part. Design choices can influence heat distribution, residual stress accumulation, and the risk of warping or cracking.
- Minimum Feature Size: The laser/electron beam spot size, powder particle size, and layer thickness limit the minimum size of features (e.g., walls, holes, struts) that can be reliably printed.
- Anisotropie: Due to the layer-wise build process and directional solidification, mechanical properties can sometimes vary depending on the build direction (X, Y vs. Z axis). Design and orientation should consider load directions relative to potential anisotropy.
Topology Optimization Strategies for Maximum Weight Reduction and Stiffness
As introduced earlier, topology optimization is a cornerstone of DfAM for lightweighting. Applied to a shock tower mount:
- Define Design Space: A bounding box representing the maximum allowable volume for the mount is defined in CAD. Non-design spaces (e.g., keep-out zones for bolts, mating surfaces, spring seats) are also specified.
- Apply Loads and Constraints: Realistic load cases simulating various driving conditions (maximum braking, cornering forces, impact loads from potholes, static vehicle weight) are applied to the model. Boundary conditions representing where the mount attaches to the chassis and the strut are fixed.
- Set Objectives and Constraints: The primary objective is typically to minimize mass (or volume) while constraining stress levels below the material’s yield strength and limiting deflection (maximizing stiffness) under load. Minimum member sizes might also be constrained to ensure manufacturability.
- Run Optimization Algorithm: The software iteratively removes material from areas experiencing low stress, gradually converging towards an organic, efficient load-bearing structure.
- Interpret and Reconstruct: The raw output of topology optimization often consists of rough, faceted geometry. This needs interpretation by an engineer, followed by reconstruction into smooth, manufacturable CAD geometry (often using subdivision modeling or spline-based surfacing techniques), ensuring blend radii are added to reduce stress concentrations.
The result is a shock mount structure that is significantly lighter (30-60%+ reduction) than a conventional design yet meets or exceeds the required stiffness and strength targets. B2B clients benefit immensely when their AM supplier possesses strong capabilities in utilizing topology optimization software and translating results into practical designs.
Designing for Minimum Support Structures: Orientation and Feature Adjustments
Support structures are often a necessary evil in PBF. While essential for successful printing of certain geometries, they:
- Consume additional material.
- Increase print time.
- Require significant post-processing effort for removal.
- Can leave witness marks on the part surface after removal.
- Can be difficult or impossible to remove from complex internal cavities.
Therefore, minimizing supports is paramount:
- Deeloriëntatie: This is the first and most critical step. Rotating the part orientation on the build plate can drastically reduce the amount of overhanging area requiring support. Software tools can help analyze different orientations to find the optimal balance between support volume, build time, thermal stability, and potential impact on dimensional accuracy or surface finish on critical features.
- Zelfdragende hoeken: Most metal PBF processes can print overhangs up to a certain angle (often around 45°) without supports. Designing features like chamfers instead of sharp horizontal overhangs, or using angled transitions, can eliminate the need for supports in those areas.
- Feature Modification: Minor design changes can sometimes eliminate support needs. For example, changing a horizontal hole to a teardrop or diamond shape allows it to become self-supporting. Bridging short horizontal distances might be possible without supports depending on the process and material.
- Designing Sacrificial Features: In some cases, features can be designed to be part of the component during printing (acting as supports) but are machined away during post-processing.
Wall Thickness Considerations: Balancing Strength, Weight, and Printability
DfAM involves careful consideration of wall thicknesses:
- Minimum Printable Thickness: There’s a limit to how thin a wall can be reliably printed, typically around 0.3-0.5 mm, depending on the machine, material, and wall height. Very thin walls can be prone to warping or incomplete melting.
- Structural Requirements: Walls must be thick enough to withstand the applied loads without buckling or yielding. FEA simulation is crucial here.
- Lichtgewicht: Thinning non-critical walls is a key strategy for weight reduction, often guided by topology optimization results.
- Warmteafvoer: Wall thickness can influence heat flow during printing. Very thick sections can retain heat longer, potentially increasing residual stress.
Finding the optimal balance requires iterative design and analysis, often supported by AM process simulation.
Incorporating Lattice Structures for Lightweighting and Energy Absorption
Lattice structures or cellular materials are periodic arrangements of struts or surfaces that create lightweight yet strong infills. AM is uniquely capable of producing these complex structures.
- Soorten: Strut-based lattices (cubic, octet-truss), TPMS (Triply Periodic Minimal Surfaces like Gyroid, Schwarz Diamond), stochastic foams (less common in structural PBF).
- Voordelen:
- Very High Stiffness-to-Weight Ratio: Lattices can provide excellent structural support with minimal mass.
- Energy Absorption: Certain lattice types excel at absorbing impact energy through controlled deformation, potentially useful for crashworthiness or vibration damping.
- Warmteafvoer: High surface area can aid in thermal management if needed.
- Application in Shock Mounts: Instead of being fully solid, sections of the shock mount could be filled with an optimized lattice structure, further reducing weight while maintaining necessary stiffness or potentially adding damping properties. Designing and validating lattice performance requires specialized software tools and expertise.
Stress Concentration Management through Filleting and Smoothing
Sharp internal corners or abrupt changes in geometry are notorious stress concentrators, potentially leading to fatigue failure, especially in components subjected to cyclic loading like shock mounts.
- Generous Fillets/Radii: Applying smooth fillets or radii at all internal corners and junctions significantly reduces stress peaks by distributing the load over a larger area. Topology optimization outputs often require significant smoothing and filleting during the CAD reconstruction phase.
- Soepele overgangen: Gradual changes in cross-section are preferred over abrupt steps.
- FEA Verification: Finite Element Analysis should be used on the final DfAM design (including fillets) to verify that stress concentrations are within acceptable limits under all load cases.
Simulation-Driven Design: Predicting Performance Before Printing
Modern DfAM heavily relies on simulation tools:
- Structural Simulation (FEA): Predicts stress, strain, deformation, and fatigue life under operational loads, verifying the design’s integrity and guiding optimization.
- Topologieoptimalisatie: As discussed, computationally determines the most efficient material layout.
- AM Process Simulation (Thermal & Mechanical): Simulates the layer-by-layer build process itself. This can predict potential issues like deformation (warping), residual stress accumulation, areas prone to overheating, and the effectiveness of support structures. This allows engineers to modify the design, orientation, or support strategy voor committing to expensive and time-consuming physical prints, saving significant resources.
Collaborating with AM Service Providers like Met3dp for Design Optimization Support
Successfully implementing DfAM, especially for complex, critical components like shock mounts, often requires deep expertise in both component engineering and the nuances of specific AM processes. Partnering with an experienced AM service provider like Met3dp offers significant advantages for B2B clients. Met3dp’s team possesses extensive knowledge of various metaal 3D-printmethoden, materials, and DfAM best practices. We can collaborate closely with automotive engineering teams, providing:
- DfAM consultation and training.
- Support in topology optimization and CAD reconstruction.
- AM process simulation to de-risk production.
- Recommendations on optimal orientation and support strategies.
- Material selection guidance based on performance requirements.
This collaborative approach ensures that designs are not only innovative but also manufacturable, reliable, and cost-effective, accelerating the adoption of AM for lightweight automotive components.
Precision Engineering: Tolerance, Surface Finish, and Dimensional Accuracy in 3D Printed Mounts
While metal additive manufacturing offers unparalleled design freedom, achieving the tight tolerances and specific surface finishes required for many automotive components, including interfaces on a shock tower mount, necessitates a clear understanding of the technology’s capabilities and limitations. Precision engineering in AM involves managing expectations regarding as-printed accuracy and strategically incorporating post-processing steps where needed. For procurement managers sourcing 3D printed parts B2B, specifying realistic tolerances and understanding the factors influencing accuracy are key to ensuring components meet critical fit, form, and function requirements.
Understanding Achievable Tolerances with Metal PBF Technologies
Metal Powder Bed Fusion (PBF) processes, whether laser-based (PBF-LB/SLM) or electron beam-based (PBF-EB/SEBM), produce parts with a certain level of inherent dimensional variation.
- General Tolerances (As-Printed): As a rule of thumb, typical achievable tolerances for as-printed metal PBF parts might be in the range of ±0.1 mm to ±0.3 mm for smaller dimensions (e.g., up to 100 mm), potentially increasing to ±0.1% to ±0.3% for larger dimensions. These are general guidelines and can vary significantly.
- PBF-LB (Laser): Often capable of finer features and potentially slightly better accuracy on smaller parts due to smaller beam spot size and layer thicknesses.
- PBF-EB (Electron Beam – e.g., Met3dp’s SEBM): Operates in a vacuum with a pre-heated powder bed. This significantly reduces residual stress compared to PBF-LB, leading to less warping and potentially better dimensional stability, especially for larger or complex parts, although the surface finish might be rougher. The heated environment can sometimes make achieving very tight tolerances challenging due to thermal expansion during the build.
- ISO Standards: Normen zoals ISO/ASTM 52902 provide tolerance grades for AM parts, but specific achievable tolerances are highly dependent on the factors below. It’s crucial to discuss specific tolerance requirements with the AM service provider early in the design phase.
Factors Influencing Dimensional Accuracy
Achieving consistent dimensional accuracy in AM is complex and influenced by numerous interacting factors:
- Materiaaleigenschappen: The coefficient of thermal expansion, conductivity, and solidification behavior of the alloy (e.g., A7075 vs. AlSi10Mg) significantly impact shrinkage and distortion during printing and cooling.
- Machinekalibratie: Precise calibration of the energy source (laser/e-beam power, focus), scanning system (galvanometers), and recoating mechanism is critical. Reputable B2B suppliers like Met3dp invest heavily in rigorous calibration and maintenance protocols for their equipment (including their advanced SEBM printers) to ensure process repeatability.
- Afdrukparameters: Scan speed, power/current, layer thickness, hatch spacing, and scan strategy all influence the melt pool dynamics, heat input, cooling rates, and ultimately, dimensional accuracy and residual stress. Optimized parameter sets are crucial.
- Part Geometry and Size: Larger parts are generally more prone to distortion. Complex geometries with varying cross-sections can experience differential cooling and stress buildup. The location of the part on the build plate can also have minor effects.
- Ondersteunende strategie: The amount, type, and placement of support structures significantly influence heat dissipation and anchoring, directly impacting warping and final part accuracy. Effective support design is key.
- Thermisch beheer: The overall thermal environment (e.g., heated chamber in SEBM, localized heating in PBF-LB) plays a major role in controlling residual stresses and distortion.
- Nabewerking: Stress relief and heat treatment cycles can cause dimensional changes (shrinkage or growth) that must be anticipated and potentially compensated for in the initial design or accounted for via post-machining allowances. Support removal can also slightly affect dimensions if not done carefully.
Typical Surface Roughness (Ra) of As-Printed Metal Parts
Surface finish is another critical aspect, particularly for mating surfaces, sealing faces, or bearing seats. As-printed metal AM parts generally have a rougher surface compared to machined components.
- Meting: Surface roughness is often quantified using the arithmetic average roughness (Ra).
- Typische waarden:
- PBF-LB (Laser): Gewoonlijk varieert het van Ra 5 µm to 25 µm, depending on the material, parameters, layer thickness, and surface orientation (up-skin vs. down-skin surfaces, vertical walls). Inclined surfaces often exhibit more pronounced “stair-stepping.”
- PBF-EB (Electron Beam): Often results in a slightly rougher surface finish compared to PBF-LB, potentially Ra 15 µm to 35 µm or higher, due to larger powder particles sometimes used and the higher energy input causing more powder sintering to the surface. However, the finish can be very consistent.
- Factors Influencing Roughness: Layer thickness (thinner layers generally yield better finish), powder particle size and distribution, energy input (can cause partially sintered powder adherence), scan strategy (contour scans can improve sidewall finish), and overhang angles (down-facing surfaces supported by rough supports tend to be rougher).
For many functional surfaces on a shock mount (e.g., where bearings sit or precise interfaces are needed), the as-printed surface finish is often insufficient and requires improvement.
Strategies for Improving Surface Finish
Several methods can be employed, often during post-processing (discussed further in the next section), to achieve smoother surfaces:
- Parameter Optimization: Fine-tuning print parameters, such as using specific contour or skin scan strategies, can slightly improve the as-printed finish on certain surfaces.
- Abrasive Blasting: Processes like sandblasting, bead blasting, or shot peening provide a more uniform, matte finish by removing loosely adhered powder and smoothing minor irregularities. Shot peening also induces beneficial compressive stresses.
- Tuimelende/vibrerende afwerking: Using abrasive media in a tumbling barrel or vibratory bowl can effectively smooth external surfaces, especially for batches of smaller parts.
- Bewerking: CNC machining provides the highest level of surface finish control for specific features.
- Polijsten: Manual or automated polishing can achieve very smooth, mirror-like finishes where required for aesthetic or specific functional reasons (e.g., sealing surfaces).
- Electropolishing/Chemical Smoothing: Electrochemical or chemical processes can remove material preferentially from peaks, leading to a smoother surface, particularly effective on complex geometries.
- Abrasive Flow Machining (AFM): Forces an abrasive putty through the part, effective for smoothing internal channels and complex external features.
Achieving Critical Tolerances: The Role of Post-Machining
For features on a shock tower mount requiring high precision – such as the bore for a steering bearing, mounting holes for attaching to the chassis, or mating surfaces for strut assembly – the as-printed tolerances and surface finish are rarely sufficient. Post-print CNC machining is typically essential.
- Identify Critical Features: During the DfAM phase, engineers must identify all features requiring tolerances tighter than what AM can reliably achieve as-printed (e.g., tolerances tighter than ±0.1 mm, specific geometric dimensioning and tolerancing (GD&T) callouts, or Ra requirements smoother than ~5 µm).
- Design Machining Allowances: Sufficient extra material (machining stock, typically 0.5 mm to 2 mm or more, depending on potential distortion) must be added to these critical features in the CAD model voor afdrukken.
- Fixturing: The AM part design should also consider how it will be accurately located and clamped (fixtured) in a CNC machine for the subsequent machining operations. Datum features might need to be incorporated.
- Machining Process: Standard CNC milling, turning, drilling, boring, or grinding operations are used to bring the critical features into their final required dimensions and surface finish specifications.
Integrating machining into the workflow is standard practice for producing high-precision metal AM parts and is a capability that reliable B2B suppliers must offer, either in-house or through qualified partners.
Quality Control and Metrology for Verifying Part Accuracy in Production Runs
Ensuring that every 3D printed shock mount meets the stringent dimensional and tolerance requirements of the automotive industry is non-negotiable, especially for B2B suppliers delivering parts in volume. A robust quality control (QC) and metrology strategy is essential.
- Coordinate Measuring Machines (CMMs): Touch-probe CMMs provide highly accurate point measurements to verify critical dimensions, hole locations, flatness, parallelism, and other GD&T requirements against the nominal CAD data.
- 3D Laser Scanning / Structured Light Scanning: Non-contact scanning captures millions of points across the part’s surface, creating a detailed 3D model that can be compared to the original CAD file (scan-to-CAD comparison). This is excellent for verifying overall form, detecting warping, and inspecting complex surfaces, although typically less accurate than CMMs for individual feature measurements.
- Conventional Metrology Tools: Calipers, micrometers, height gauges, and specific functional gauges are also used for quick checks and specific feature measurements.
- Statistical Process Control (SPC): For production runs, SPC techniques monitor key dimensional outputs over time to ensure the process remains stable and capable of meeting specifications consistently.
- Reporting: Comprehensive inspection reports documenting compliance with all specified tolerances and GD&T callouts are crucial deliverables for B2B transactions, providing traceability and assurance of quality.
Met3dp integrates rigorous metrology and quality control throughout its manufacturing process, from powder verification to final part inspection, ensuring that components delivered to automotive clients meet the highest standards of precision and reliability.
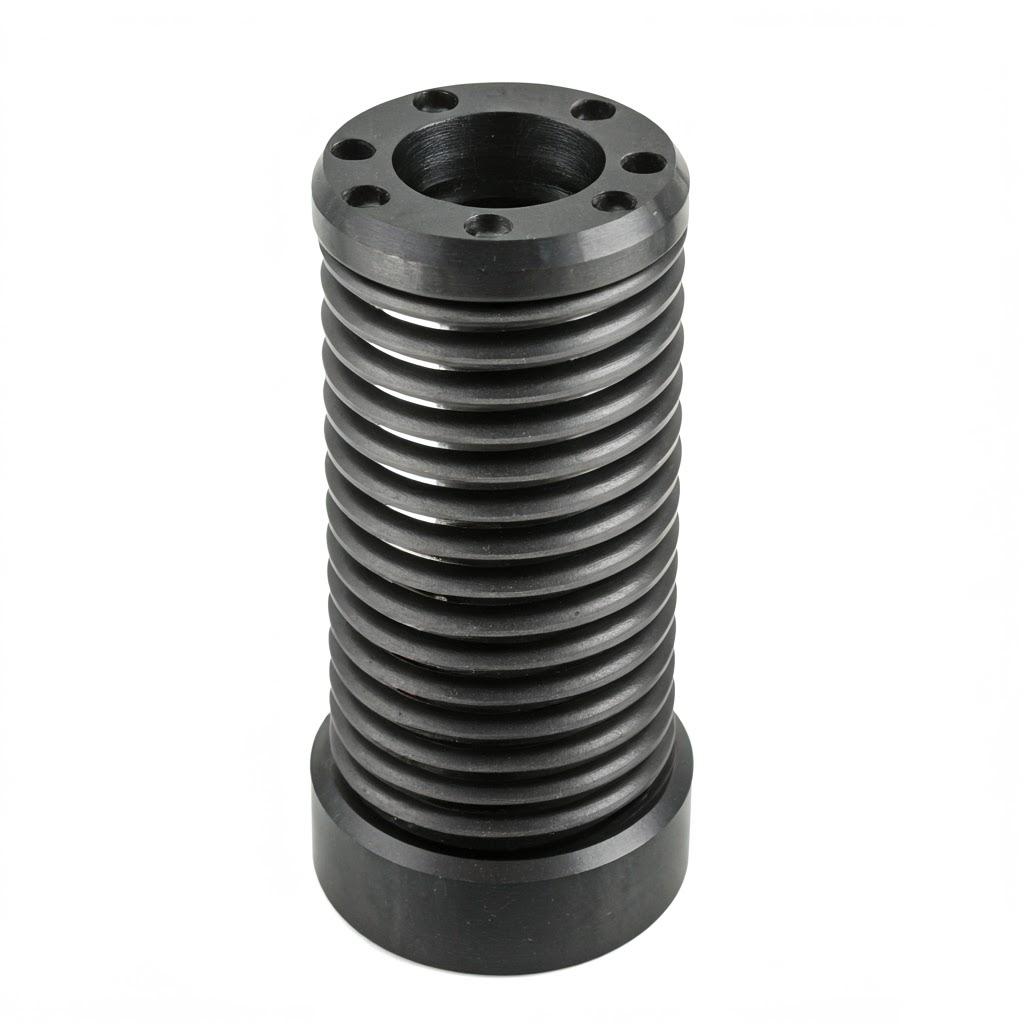
Beyond the Print Bed: Post-Processing Requirements for Automotive Shock Mounts
Creating a dimensionally accurate shock tower mount using metal additive manufacturing doesn’t end when the printer stops. The “as-printed” part, while geometrically complex, is rarely ready for final application. A series of crucial post-processing steps are typically required to transform the raw print into a functional, reliable, and durable automotive component. Understanding these steps, their purpose, and their impact on cost and lead time is vital for engineers designing AM parts and for procurement managers sourcing them from B2B suppliers. A capable AM partner like Met3dp often provides comprehensive post-processing services, offering an end-to-end solution.
1. Stress Relief and Heat Treatment: Why It’s Crucial
The rapid heating and cooling inherent in PBF processes generate significant internal stresses within the printed part. Additionally, for alloys like A7075, heat treatment is necessary to achieve the desired high-strength properties.
- Verlichting van stress:
- Doel: To reduce the residual stresses locked into the part during printing. High residual stresses can lead to distortion (especially after removal from the build plate or during subsequent machining) and can negatively impact fatigue life and stress corrosion cracking resistance.
- Proces: Typically involves heating the part (while still attached to the build plate, or sometimes after removal) to a specific temperature below the alloy’s critical transformation points, holding it for a period, and then slowly cooling it. This allows the material’s microstructure to relax, relieving stresses without significantly altering the core mechanical properties achieved during printing. For AlSi10Mg, stress relief is very common.
- Heat Treatment (Solutionizing & Aging):
- Doel: Primarily used for precipitation-hardening alloys like A7075 to achieve their target temper condition (e.g., T6) and significantly increase strength and hardness. AlSi10Mg can also undergo heat treatments for property modification, though it’s less common than for A7075.
- Process (Example for A7075 T6):
- Oplossing Behandeling: Heating the part to a high temperature (e.g., ~470-490°C) to dissolve the alloying elements (Zn, Mg, Cu) into a solid solution within the aluminum matrix.
- Afschrikken: Rapidly cooling the part (e.g., in water or polymer quenchant) to trap the dissolved elements in a supersaturated solution. This step is critical and must be fast enough to prevent unwanted precipitation. It can also induce distortion if not carefully controlled.
- Artificial Aging: Reheating the part to a lower temperature (e.g., ~120-150°C) for an extended period (hours). This allows controlled precipitation of fine hardening phases throughout the material, significantly increasing strength and hardness.
- Overwegingen: Heat treatment requires specialized furnaces with precise temperature control and potentially controlled atmospheres (e.g., vacuum or inert gas) to prevent oxidation. It adds significant time and cost to the workflow and carries a risk of part distortion, which must be managed through proper support during treatment or accounted for with larger machining allowances.
2. Support Structure Removal Techniques
Removing the support structures generated during the PBF process is often a labor-intensive step. The ease of removal depends heavily on the DfAM strategy employed.
- Handmatig verwijderen: For accessible supports, especially those designed with low-density interfaces or specific break points, simple hand tools (pliers, cutters, hammers, chisels) may be sufficient. This is often the first step.
- Machining (Milling/Grinding): Supports can be removed using standard CNC machining operations (e.g., milling flat support bases) or manual grinding tools. This provides more control than manual breaking and can achieve a smoother finish at the support interface but requires careful handling to avoid damaging the part.
- Wire EDM (elektrisch vonken): For supports in intricate or hard-to-reach internal areas, wire EDM can be used. An electrically charged wire precisely cuts through the metal supports. It’s slow and relatively expensive but highly effective for complex geometries where mechanical access is impossible.
- Bandzagen: Parts are often removed from the build plate using a band saw before detailed support removal begins.
Care must be taken during support removal to avoid damaging the part surface, especially on critical features. Witness marks left by supports may require further finishing steps.
3. Surface Finishing Operations
As discussed previously, the as-printed surface finish of metal AM parts is often too rough for final use. Various techniques are employed to achieve the desired texture, smoothness, or specific surface properties.
- Abrasive Blasting (Sand/Bead/Grit): Propels abrasive media (sand, glass beads, aluminum oxide) against the part surface. Cleans the surface, removes loosely adhered powder, provides a uniform matte finish, and can blend minor imperfections. Different media produce different finishes.
- Shot Peening: Similar to blasting but uses small spherical shots (metal or ceramic). Its primary purpose is not just finishing but inducing a layer of compressive residual stress on the part surface. This significantly improves fatigue life and resistance to stress corrosion cracking – highly beneficial for cyclically loaded suspension components like shock mounts.
- Tumbling / Vibratory Finishing: Parts are placed in a tub with abrasive media (ceramic, plastic, organic) which vibrates or tumbles. Provides effective deburring and surface smoothing, especially for batches of parts, but mainly affects external surfaces.
- Polijsten: Manual or automated processes using progressively finer abrasives to achieve a smooth, reflective surface (low Ra value). Typically applied only to specific areas requiring very low friction, sealing capability, or high aesthetic appeal.
- Abrasive Flow Machining (AFM) / Extrude Hone: Forces a viscoelastic polymer loaded with abrasive particles through or across the part. Effective for smoothing internal channels and complex external geometries that are difficult to reach otherwise.
- Electropolishing / Chemical Polishing: Electrochemical or chemical dissolution processes that preferentially remove microscopic peaks from the surface, resulting in a very smooth, clean, and often brighter finish. Effective for complex shapes but requires appropriate electrolytes/chemicals for the specific alloy.
The choice of finishing method depends on the required surface Ra, aesthetic requirements, fatigue life considerations, and cost targets.
4. CNC Machining for Critical Features
As highlighted in the previous section, post-print CNC machining is almost always necessary to achieve the tight tolerances (e.g., < ±0.1 mm), precise geometric features (bores, threads, planar faces), and smooth surface finishes (e.g., Ra < 1.6 µm) required for critical interfaces on the shock mount. This involves milling, turning, drilling, tapping, boring, or grinding operations performed on the stress-relieved or heat-treated AM part, using the pre-designed machining allowances. This ensures proper fitment with bearings, chassis mounting points, and the strut assembly.
5. Surface Treatments and Coatings
To enhance corrosion resistance, wear resistance, or provide a desired aesthetic appearance, further surface treatments are often applied to aluminum shock mounts:
- Anodiseren: An electrochemical process that creates a hard, durable layer of aluminum oxide on the surface. Improves corrosion resistance significantly, enhances wear resistance, provides electrical insulation, and can be dyed various colors. Different types (Type II – decorative/corrosion, Type III – hardcoat for wear) offer varying properties. Essential for A7075, beneficial for AlSi10Mg in harsh environments.
- Chromate Conversion Coating (Alodine / Iridite): A chemical treatment providing good corrosion resistance and an excellent base for paint adhesion. Less durable than anodizing. Environmental regulations are restricting some traditional chromate coatings (Hexavalent Chromium).
- Painting / Powder Coating: Applying liquid paint or electrostatically applied powder coating (which is then cured) provides excellent corrosion protection and a wide range of color options. Requires proper surface preparation (cleaning, potentially conversion coating) for good adhesion.
- Other Coatings: Specialized coatings (e.g., dry film lubricants, thermal barrier coatings) could be applied for specific performance enhancements, although less common for typical shock mounts.
6. Inspection and Quality Assurance Post-Processing
Quality control doesn’t stop after machining or coating. Final inspection ensures the finished part meets all specifications.
- Final Dimensional Inspection: Verifying critical dimensions after all processing steps using CMMs, scanners, or hand tools.
- Niet-destructief onderzoek (NDT):
- Visuele inspectie: Thorough check for surface defects, cracks, or inconsistencies.
- Dye Penetrant Testing (DPT): Detects surface-breaking cracks or porosity.
- Radiographic Testing (RT) / Computed Tomography (CT): X-ray methods used to inspect internal integrity, detecting voids, porosity, inclusions, or cracks within the part. CT scanning provides a full 3D view of internal structures. Crucial for validating critical components, especially during process qualification or for safety-critical applications.
- Ultrasoon testen (UT): Uses sound waves to detect internal flaws.
- Material Property Verification: Sometimes, sample coupons printed alongside the parts undergo destructive testing (e.g., tensile tests, hardness tests) to verify that the material properties meet requirements after all processing steps.
Streamlining Post-Processing for Scaled Production: Automation and Workflow Optimization for Distributors
For B2B suppliers aiming for higher volume production, efficiently managing this complex chain of post-processing steps is critical. This involves:
- Workflow Integration: Planning the sequence of operations logically to minimize handling and potential damage.
- Automatisering: Implementing robotics or automated systems for tasks like part handling, loading/unloading machines, blasting, or inspection where feasible.
- Specialized Partners: Developing relationships with qualified subcontractors for specialized processes (e.g., heat treatment, coating, NDT) if not performed in-house.
- Lean Manufacturing Principles: Optimizing layout, reducing batch sizes where practical, minimizing waiting times between steps.
Offering a streamlined, well-managed post-processing workflow is a key differentiator for AM service providers like Met3dp (https://met3dp.com/), enabling them to deliver finished, application-ready components reliably and efficiently to their automotive clients.
Navigating Challenges: Common Issues in 3D Printing Shock Mounts and Solutions
While metal additive manufacturing offers tremendous potential for creating lightweight and optimized shock tower mounts, it’s not without its challenges. Understanding potential issues and implementing robust solutions is crucial for ensuring part quality, reliability, and process repeatability – non-negotiable factors for automotive applications and B2B procurement. Experienced AM providers like Met3dp leverage their deep process knowledge and advanced equipment to proactively mitigate these common challenges.
Potential Issue: Warping and Distortion During Printing and Heat Treatment
- Cause: Significant temperature gradients between the molten material and surrounding powder/solidified layers induce internal stresses (residual stresses). As these stresses accumulate layer by layer, they can cause the part to warp, curl away from the build plate, or distort, especially in large or complex geometries. Subsequent heat treatment cycles (stress relief or aging) can also cause distortion as stresses redistribute or phase transformations occur.
- Solutions:
- Optimized Part Orientation: Orienting the part to minimize large flat surfaces parallel to the build plate, reduce unsupported overhangs, and minimize overall build height can lessen distortion risk.
- Robust Support Strategy: Well-designed supports are critical. They must securely anchor the part to the build plate, resist pulling forces, act as heat sinks to manage thermal gradients, and support the part’s geometry during subsequent heat treatment if necessary. Using simulation tools to optimize support placement and type is highly beneficial.
- AM Process Simulation: Simulating the build process beforehand can predict areas of high residual stress and potential distortion, allowing for adjustments to orientation, supports, or even the part design itself (e.g., adding stiffening ribs that are later removed).
- Controlled Thermal Management: Techniques like pre-heating the powder bed (inherent in SEBM processes like those used by Met3dp) significantly reduce thermal gradients, lowering residual stress and minimizing distortion compared to room-temperature PBF-LB processes. Careful control of build chamber temperature and gas flow is also important.
- Optimized Print Parameters: Tuning parameters like scan strategy (e.g., island scanning patterns) can help distribute heat more evenly and reduce stress buildup.
- Carefully Planned Heat Treatment: Designing stress relief and heat treatment cycles with controlled heating/cooling rates and potentially using specialized fixtures to support the part during treatment can minimize distortion during these critical post-processing steps. Adding sufficient machining stock compensates for unavoidable minor distortions.
Potential Issue: Difficulty in Support Removal, Especially Internal Channels
- Cause: Supports are needed but can be difficult to access and remove cleanly, especially dense supports, those attached to delicate features, or those located within complex internal geometries (though less common in typical shock mount designs). Poor DfAM planning is often a root cause.
- Solutions:
- DfAM for Accessibility: Designing the part with support removal in mind from the start is key. Maximize self-supporting angles, orient the part for access, and avoid internal cavities requiring supports where possible.
- Optimized Support Structures: Using support types that are easier to remove (e.g., lower density supports, supports with specific break-off points or perforation patterns, tree supports that minimize contact area) can significantly reduce removal effort. Software tools often offer various support generation strategies.
- Advanced Removal Techniques: Employing appropriate tools like specialized cutting pliers, grinders, ultrasonic cutters, or using processes like Wire EDM or Abrasive Flow Machining (AFM) for inaccessible areas.
- Material Choice (Less Common in PBF): While more common in other AM processes, research continues into dissolvable or chemically removable support materials compatible with metal PBF, but this is not standard practice currently.
- Sacrificial Features: Designing features intended to be machined away that also serve as supports during the build.
Potential Issue: Porosity and Internal Defects Affecting Structural Integrity
- Cause: Small voids or pores can form within the printed material due to several reasons: trapped gas within the powder particles or shield gas, incomplete fusion between layers or scan tracks (Lack of Fusion – LoF), or keyholing (vapor depression collapse) caused by excessive energy input. Porosity degrades mechanical properties (especially fatigue strength) and can act as crack initiation sites.
- Solutions:
- Optimized Print Parameters: This is the primary defense. Establishing a robust process window (correct laser/beam power, scan speed, hatch spacing, focus, layer thickness) for the specific material and machine is crucial to ensure complete melting and fusion without excessive energy input. Extensive parameter development is required.
- Hoogwaardig poeder: Using powder with high sphericity, controlled PSD, good flowability, and very low internal gas content/moisture is essential. Met3dp’s use of advanced Gas Atomization and PREP technologies ensures powder quality, minimizing porosity risk originating from the feedstock. Strict powder handling and storage protocols (e.g., drying, sieving, inert atmosphere storage) are also critical, especially for recycled powder.
- Stable Melt Pool Dynamics: Advanced process monitoring (e.g., using sensors to monitor melt pool size, temperature, or emissions) can potentially detect instabilities that might lead to porosity, allowing for real-time adjustments or flagging parts for further inspection.
- Appropriate Shielding Gas: Ensuring high-purity inert shielding gas (Argon or Nitrogen) with adequate flow rate in PBF-LB prevents oxidation and contamination of the melt pool, which can contribute to defects. SEBM’s vacuum environment inherently avoids this issue.
- Heet isostatisch persen (HIP): This post-processing step involves subjecting the part to high temperature (below melting point) and high isostatic pressure (using an inert gas like Argon) simultaneously. This effectively closes internal pores and voids through diffusion bonding and plastic deformation, resulting in a fully dense part (~100% density) with improved mechanical properties, particularly fatigue life. HIP adds significant cost and lead time but is often specified for critical aerospace and medical components, and increasingly for high-performance automotive parts where maximum reliability is demanded by B2B customers.
Potential Issue: Achieving Consistent Mechanical Properties Across Batches
- Cause: Variations in machine performance over time, inconsistencies in powder batches (new vs. recycled, different batches from supplier), deviations in process parameters, or inconsistencies in post-processing (especially heat treatment) can lead to variability in mechanical properties (strength, ductility, hardness, fatigue life) between different builds or batches of parts.
- Solutions:
- Strict Process Control: Implementing rigorous procedures for machine calibration, preventative maintenance, and process parameter validation. Using standardized build layouts and setup procedures.
- Robust Powder Management: Implementing strict protocols for powder handling, storage, traceability, sieving, blending, and rejuvenation/recycling. Regularly testing the quality (chemistry, PSD, flowability) of both virgin and recycled powder lots is crucial. B2B suppliers need transparent powder traceability.
- Comprehensive Quality Monitoring: Utilizing melt pool monitoring systems (if available), logging all process data for each build, and implementing statistical process control (SPC) to track key process indicators and outputs.
- Standardized Post-Processing: Ensuring all post-processing steps, especially critical heat treatments, are performed using calibrated equipment and precisely controlled, documented cycles.
- Rigorous QA/QC Testing: Regularly printing and testing standardized test coupons (e.g., tensile bars, density cubes) alongside production parts within each build or batch. Performing hardness tests, microstructural analysis, and NDT on parts or coupons to verify properties meet specifications consistently. Providing detailed quality documentation and certificates of conformity with each batch delivered to the B2B client.
Potential Issue: Surface Finish Imperfections
- Cause: Beyond the inherent roughness, issues like excessive “stair-stepping” on curved surfaces, partially sintered powder adhering strongly (especially in PBF-EB), dross formation, or witness marks from support structures can occur.
- Solutions:
- Parameter Tuning: Optimizing contour scan parameters, potentially using smaller layer thicknesses (increases build time/cost), adjusting energy input to minimize powder adherence.
- Appropriate Post-Processing Selection: Choosing the most effective surface finishing methods (blasting, peening, tumbling, polishing, AFM, electropolishing) based on the type of imperfection and the required final finish.
- DfAM for Surface Finish: Orienting the part so that critical surfaces are built as vertical walls or upward-facing surfaces, which generally have better finishes than down-facing or heavily supported surfaces. Minimizing support contact on critical areas.
- Effective Cleaning: Thorough powder removal immediately after the build (e.g., using compressed air, brushing, ultrasonic cleaning) is important before heat treatment, as trapped powder can become permanently sintered onto the surface.
By acknowledging these potential challenges and proactively implementing robust DfAM strategies, optimized process parameters, stringent quality control, and appropriate post-processing, experienced AM providers like Met3dp can consistently deliver high-quality, reliable 3D printed shock tower mounts that meet the demanding specifications of the automotive industry and the expectations of discerning B2B procurement partners.
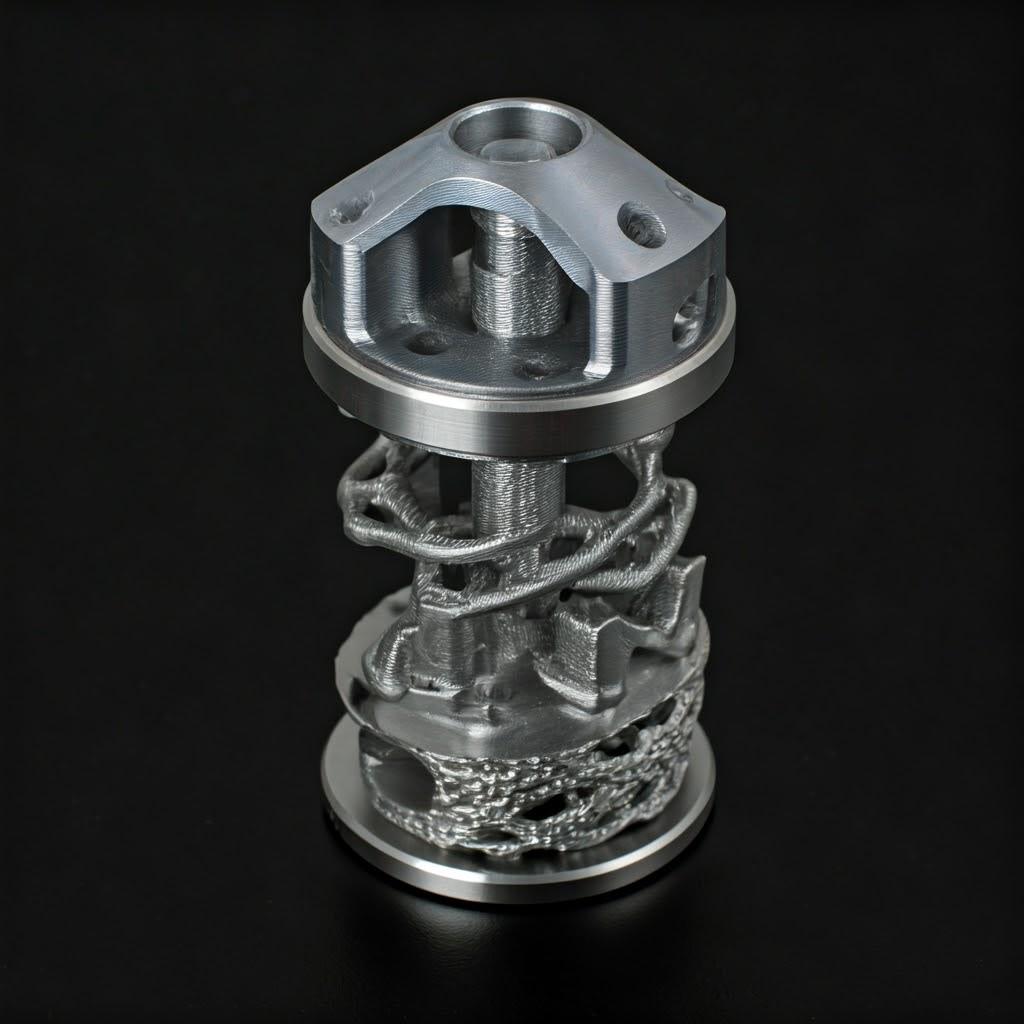
Partnering for Success: How to Choose the Right Metal 3D Printing Service Provider
Successfully implementing metal additive manufacturing for demanding applications like automotive shock tower mounts is not just about having the right design and material; it hinges critically on selecting the right manufacturing partner. The metal AM landscape includes a wide range of service providers, from small job shops to large, integrated manufacturers. For automotive OEMs, Tier 1 suppliers, and procurement managers seeking reliable, high-quality B2B partnerships for producing components like lightweight shock mounts, evaluating potential suppliers requires a rigorous assessment across several key areas. Choosing wisely ensures access to the necessary technology, expertise, quality assurance, and capacity to move from concept to validated production parts efficiently and reliably.
1. Evaluating Technical Capabilities: Machine Fleet, Materials, and Software
The foundation of any AM service provider is its technology infrastructure.
- Machine Fleet:
- Technologie: Do they operate the relevant PBF technology (PBF-LB/SLM or PBF-EB/SEBM) best suited for your material (e.g., AlSi10Mg prints well on both, A7075 can be challenging but feasible on optimized PBF-LB or potentially SEBM)? Does their specific machine model have a reputation for stability and accuracy? Met3dp utilizes industry-leading systems, including advanced SEBM printers known for reliability in producing low-stress parts.
- Bouwvolume: Do their machines offer build envelopes large enough for your shock mount design? Consider not just single part size but also the ability to nest multiple parts efficiently for production runs.
- Capacity & Redundancy: Do they have sufficient machine capacity to handle your prototyping and potential production volume needs without excessive queue times? Do they have multiple machines of the same type for redundancy in case of maintenance?
- Materiaalexpertise:
- Alloy Experience: Crucially, do they have proven experience and validated parameter sets specifically for the chosen alloy (A7075, AlSi10Mg)? Ask for material datasheets based on their actual machine outputs, not just generic powder specs.
- Materiaal Portfolio: Do they offer a range of relevant automotive materials? Can they advise on the optimal material choice for your specific load case, environment, and cost target?
- Behandeling van poeder: Do they have strict protocols for handling, storing, sieving, and recycling metal powders to maintain purity and ensure consistent part quality? This is paramount for B2B supply consistency.
- Software & Simulation:
- CAD/Build Prep: Do they use professional software for build preparation, orientation optimization, and support generation?
- Simulatiemogelijkheden: Do they offer AM process simulation (thermal/mechanical) to predict and mitigate potential issues like distortion before printing? Do they have topology optimization capabilities to support DfAM?
2. Industry Experience: Proven Track Record in Automotive or Related Fields
Experience in demanding industries translates to a better understanding of requirements and potential pitfalls.
- Automotive Focus: Have they successfully produced components for other automotive clients? Can they share (non-confidential) case studies or examples? Do they understand automotive standards and PPAP (Production Part Approval Process) requirements, even if full compliance isn’t always required for AM parts yet?
- Related Sectors: Experience in aerospace, defense, or medical industries often indicates a high level of process control, quality management, and experience with critical component manufacturing.
- Component Similarity: Have they produced parts with similar complexity, size, material, and tolerance requirements to your shock mount?
3. Quality Management Systems and Certifications
Robust quality systems are non-negotiable for automotive components.
- ISO 9001: This foundational QMS certification indicates documented processes, quality control procedures, and a commitment to continuous improvement. It’s a minimum requirement for a serious B2B supplier.
- AS9100: While an aerospace standard, its stringent requirements for process control, traceability, risk management, and quality assurance are highly relevant for high-performance automotive components. Suppliers holding AS9100 often demonstrate superior quality discipline.
- IATF 16949: The specific automotive quality standard. While full certification might be challenging for some aspects of current AM processes, a supplier demonstrating awareness and alignment with IATF principles (e.g., process control, risk analysis like FMEA, measurement system analysis) is advantageous.
- Audits: Are they open to customer audits of their facilities and processes? This transparency builds trust in B2B relationships.
4. Material Sourcing and Quality Control: Ensuring Powder Integrity
The quality of the final part is inseparable from the quality of the input powder.
- Source: Do they manufacture powder in-house or source it from qualified external suppliers? In-house production, like Met3dp’s use of advanced Gas Atomization and PREP technologies, offers greater control over quality and consistency.
- Incoming Inspection: What tests are performed on incoming powder batches (chemistry, PSD, morphology, flowability)?
- Traceerbaarheid: Can they provide full traceability for powder batches used in specific builds?
- Recycling Strategy: What is their process for handling and qualifying recycled powder to prevent degradation and ensure consistent properties? How much recycled powder is used?
5. Design Support and Engineering Expertise (DfAM Consultation)
A true partner offers more than just printing services.
- DfAM Knowledge: Do their engineers possess deep expertise in Design for Additive Manufacturing? Can they review your design and provide actionable recommendations for optimization (weight reduction, support minimization, feature modification for printability)?
- Collaborative Approach: Are they willing to work collaboratively with your engineering team throughout the design and iteration process?
- Problemen oplossen: Can they help troubleshoot design or manufacturing challenges based on their experience?
6. Post-Processing Capabilities: In-House vs. Outsourced
Post-processing is a critical and often time-consuming part of the workflow.
- Range of Services: What essential post-processing steps (stress relief/heat treatment, support removal, basic finishing like blasting) do they perform in-house?
- Advanced Capabilities: Do they have in-house capabilities for critical machining, advanced surface finishing (polishing, peening), coating (anodizing, painting), and NDT inspection (CT, DPT)?
- Supply Chain Management: If they outsource certain steps, do they have a network of qualified and reliable subcontractors? How do they manage quality and logistics for outsourced processes? Having key capabilities like heat treatment and CNC machining in-house generally offers better control over quality, lead time, and cost.
7. Lead Time and Production Capacity
The supplier must be able to meet your project timelines.
- Quoted Lead Times: Are their quoted lead times for prototypes and production runs realistic and competitive?
- On-Time Delivery Record: Can they provide data or references regarding their historical on-time delivery performance?
- Schaalbaarheid: Do they have the capacity (machines, personnel, post-processing bandwidth) to scale from initial prototypes to potential series production volumes required by your B2B needs?
- Transparantie: Are they transparent about their current workload and potential queue times?
8. Communication, Transparency, and Project Management
Effective B2B partnerships rely on clear and consistent communication.
- Responsiveness: Are they responsive to inquiries and requests for information?
- Dedicated Contact: Will you have a dedicated project manager or technical contact?
- Reporting: Do they provide regular updates on project status?
- Problem Resolution: How do they handle unexpected issues or delays? Is their communication proactive and solution-oriented?
- IP Protection: Do they have clear policies and procedures for protecting customer intellectual property (designs, data)?
Why Met3dp Stands Out: Comprehensive Solutions from Powder to Part
Met3dp, headquartered in Qingdao, China, is strategically positioned to be the ideal additive manufacturing partner for demanding automotive applications. We differentiate ourselves through:
- Integrated Capabilities: Spanning advanced metal powder production (Gas Atomization, PREP), state-of-the-art printing equipment (including high-performance SEBM systems), and comprehensive post-processing and quality assurance.
- Materiaalexpertise: Decades of collective experience in metallurgy and AM materials science, offering a wide portfolio including expertly processed A7075 and AlSi10Mg.
- Technological Edge: Utilizing industry-leading equipment to ensure powder quality, print accuracy, and part reliability.
- Collaborative Approach: Working closely with clients from DfAM consultation through to final part validation and production.
- Quality Focus: Implementing rigorous quality control measures throughout the entire process chain.
To learn more about our company philosophy, facilities, and commitment to advancing industrial additive manufacturing, please visit our About Met3dp page. We believe our comprehensive approach provides the reliability, quality, and expertise required for successful B2B partnerships in the automotive sector.
Understanding the Investment: Cost Factors and Lead Time for 3D Printed Shock Mounts
While the performance benefits of 3D printed shock mounts are compelling, understanding the associated costs and typical manufacturing timelines is crucial for project planning, budgeting, and making informed decisions within a B2B procurement context. Metal additive manufacturing involves different cost structures and lead time dynamics compared to traditional methods, requiring careful analysis.
Major Cost Drivers in Metal AM
The final price per part for a 3D printed shock mount is influenced by a combination of factors:
- Materiaalkosten:
- Powder Type: The base cost of the metal powder itself varies significantly. High-performance alloys like A7075 are generally more expensive per kilogram than more common alloys like AlSi10Mg.
- Volume Used: The total amount of powder consumed, which includes the part volume plus the volume of support structures, directly impacts cost. Efficient DfAM and support optimization can significantly reduce material consumption.
- Efficiënt recyclen: The cost may be influenced by the provider’s ability to efficiently recycle unused powder, although high recycling rates are standard practice. Virgin powder is always more expensive.
- Machinetijd: This is often the largest single cost component in metal AM.
- Build Height: Print time is primarily driven by the number of layers required, meaning taller parts take longer, regardless of how many are nested on the build plate (up to the plate limits). Optimizing orientation to minimize Z-height is critical for cost reduction.
- Part Volume/Density: While height is primary, the actual volume of material being melted per layer (related to part cross-sectional area and density) influences the time spent scanning each layer. More complex geometries do not necessarily cost more to print than simpler ones if they have the same height and volume.
- Machine Depreciation & Operating Costs: The hourly rate charged for machine time reflects the high capital investment in industrial metal AM systems, plus costs for energy, inert gas (for PBF-LB), maintenance, and specialized facilities.
- Arbeid: Skilled labor is required throughout the AM workflow.
- Setup: Preparing the build file, loading the machine with powder, setting up the build plate.
- Monitoring: While largely automated, builds require some level of monitoring.
- Build Removal: Removing the build plate, separating parts from the plate (e.g., sawing).
- Arbeid na het verwerken: This can be significant – manual support removal, surface finishing (blasting, tumbling, polishing), inspection, part handling between steps. Machining labor adds further cost.
- Post-Processing Steps: Each additional step adds cost.
- Hittebehandeling: Furnace time, energy consumption, potential use of controlled atmospheres or fixtures.
- Bewerking: CNC machine time (milling, turning), programming, fixturing, tooling costs.
- Afwerking: Labor and consumables for blasting, peening, polishing, coating (anodizing, painting).
- NDO-inspectie: Costs associated with equipment and certified personnel for CT scanning, DPT, etc.
- Kwaliteitscontrole en inspectie:
- Metrology: Time for CMM measurements, 3D scanning, report generation.
- Testen: Costs for destructive testing of sample coupons if required.
- Documentatie: Generating compliance reports and traceability documentation demanded in B2B transactions.
- Order Volume (Economies of Scale):
- Setup Afschrijving: Fixed setup costs (build preparation, machine setup) are spread over more parts in larger batches, reducing the per-part cost.
- Nesting Efficiency: Printing multiple parts simultaneously in a single build (nesting) optimizes machine utilization, significantly reducing the machine time cost per part compared to printing single pieces.
- Material Purchasing: Potential for bulk discounts on powder for very large orders.
- Post-Processing Efficiency: Batch processing in heat treatment, finishing, and machining can sometimes yield efficiencies. Wholesale buyers and those placing bulk B2B orders generally achieve significantly lower per-part costs than for single prototypes.
- Ontwerpoptimalisatie (DfAM): A well-designed part optimized for AM (minimal supports, reduced volume via topology optimization, minimized height) will inherently be cheaper to produce than a poorly optimized design. Investing in DfAM expertise pays dividends.
Estimating Lead Times
Lead time – the total time from order placement to part delivery – varies widely depending on several factors:
- Prototyping vs. Series Production: Prototypes often receive priority scheduling and may skip some extensive post-processing or QC steps, leading to faster turnaround (typically days to 1-3 weeks). Series production requires more rigorous process control, batch processing, full post-processing, and comprehensive QC, leading to longer lead times (typically weeks to months, highly dependent on volume and complexity).
- Design Complexity and Print Time: Build height is the primary driver of print time. Very tall or large volume parts naturally take longer to print (can range from hours to many days for a single build).
- Vereisten voor nabewerking: Each step adds time: stress relief/heat treatment (hours to days, including furnace cycles and cooling), support removal (hours), machining (hours to days depending on complexity), finishing/coating (days), NDT (hours to days). The cumulative time for extensive post-processing can often exceed the print time itself.
- Provider’s Queue Times and Capacity: The service provider’s current workload significantly impacts when a job can be started. Communicate required delivery dates early.
- Shipping and Logistics: Time required for packaging and shipping to the customer’s location.
Total Cost of Ownership (TCO) Considerations
When comparing AM to traditional methods, it’s crucial to look beyond the simple per-part manufacturing cost. A TCO analysis should consider:
- Toolingkosten: AM eliminates the need for expensive molds, dies, or complex fixtures required for casting, forging, or stamping, offering huge savings, especially for low-to-medium volumes or frequent design changes.
- Assembly Costs: Part consolidation achieved through AM reduces the number of components to assemble, lowering labor costs and potentially improving reliability.
- Weight Savings Benefits: The value of lightweighting (improved fuel/energy efficiency, better performance, potential for downsizing other components) should be factored in over the vehicle’s lifetime.
- Time-to-Market: AM’s ability to rapidly produce prototypes and iterate designs can significantly shorten the vehicle development cycle, providing a competitive advantage.
- Inventory Costs: On-demand manufacturing potential with AM can reduce the need for large inventories of spare parts.
While the direct manufacturing cost of an AM part might sometimes be higher, the overall TCO can be significantly lower when these factors are considered, particularly for complex, lightweight, or low-volume components like specialized shock mounts.
Requesting Quotes: Information Needed for Accurate Pricing
To obtain accurate quotes from AM service providers like Met3dp, B2B clients should provide comprehensive information:
- CAD Model: A 3D CAD file in a standard format (e.g., STEP, STL – though STEP is preferred for dimensional accuracy).
- Material Specification: Clearly defined alloy (e.g., A7075-T6 requirements, AlSi10Mg as-printed + stress relieved).
- Tolerances: Clearly marked drawings (e.g., PDF) specifying all critical dimensions, GD&T callouts, and required surface finishes (Ra values) for specific features. Indicate which features require post-machining.
- Hoeveelheid: Number of parts required (for prototypes and estimated production volumes).
- Vereisten voor nabewerking: Specify required heat treatments, surface finishes, coatings, and any NDT inspection needs.
- Required Delivery Date: Target timeline for receiving the parts.
- Testing/Certification Needs: Any specific material testing or certification documentation required.
Providing detailed information upfront enables suppliers to generate accurate quotes and realistic lead time estimates, facilitating smoother B2B procurement processes.
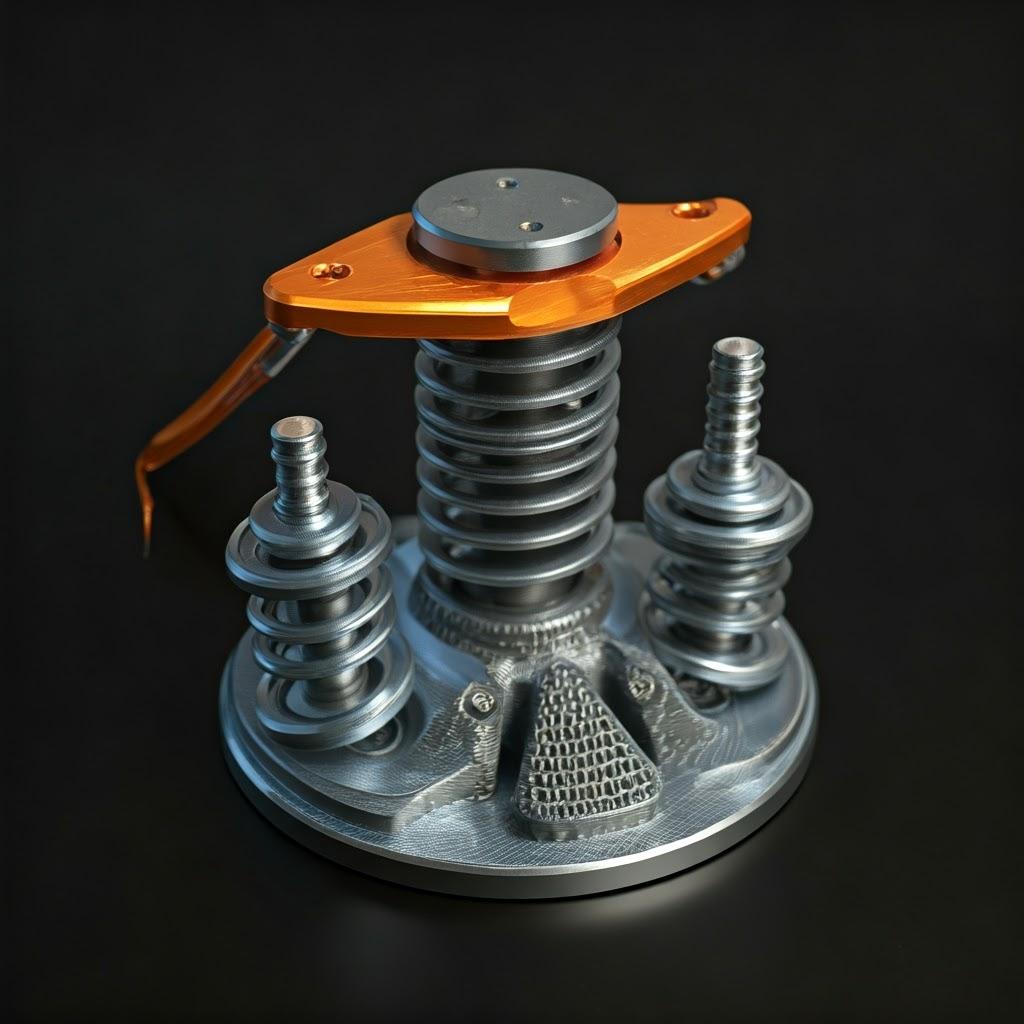
Frequently Asked Questions (FAQ) about 3D Printed Automotive Shock Mounts
As metal additive manufacturing becomes more prevalent in the automotive industry, engineers, designers, and procurement managers often have questions about the capabilities, limitations, and practicalities of using this technology for structural components like shock tower mounts. Here are answers to some common questions:
Q1: Are 3D printed aluminum shock mounts strong enough for automotive use?
A: Yes, absolutely, provided they are designed, manufactured, and validated correctly. High-performance aluminum alloys like A7075 (when heat-treated to T6 condition) and AlSi10Mg (especially when appropriately processed) offer excellent mechanical properties suitable for demanding automotive loads. Metal AM processes, when properly controlled by experienced providers like Met3dp using high-quality powders, can produce fully dense parts (>99.5% density, potentially ~100% with HIP) with strength, stiffness, and fatigue resistance comparable or even superior to cast components, particularly when leveraging topology optimization for efficient material usage. The key lies in:
- Correct Material Selection: Choosing the alloy that best matches the load requirements (e.g., A7075 for very high strength needs).
- Appropriate DfAM: Designing the part specifically for AM, managing stress concentrations, and ensuring manufacturability.
- Geoptimaliseerde procesparameters: Using validated machine parameters to achieve dense, defect-free parts.
- Correct Post-Processing: Implementing necessary stress relief and heat treatments (like T6 for A7075) to achieve target properties.
- Rigorous Testing & Validation: Performing thorough testing (material coupon tests, component rig tests, vehicle tests) to verify performance against requirements, just as with any conventionally manufactured critical component.
Q2: How does the cost of 3D printing shock mounts compare to CNC machining from billet or casting?
A: The cost comparison is nuanced and depends heavily on volume, complexity, and design:
- Prototypen: Metal AM is often significantly faster and cheaper for producing one-off or very small batches (e.g., 1-10) of functional prototypes compared to creating prototype tooling for casting or the extensive setup and material waste involved in CNC machining complex geometries from billet.
- Low-to-Medium Volume Production (Tens to Thousands):
- vs. CNC Machining: AM can be cost-competitive or even cheaper than multi-axis CNC machining for highly complex, topology-optimized geometries where machining would require extensive setup, complex fixturing, long cycle times, and generate significant material waste. For simpler geometries easily machined, CNC might remain cheaper per part.
- vs. Casting: AM typically has a higher per-part cost than traditional high-pressure die casting or even sand casting once production volumes justify the high upfront tooling investment for casting. However, AM eliminates tooling costs, making it potentially more economical for lower volumes or where design flexibility is needed.
- High Volume Production (Tens of Thousands+): Traditional methods like casting and stamping currently remain more cost-effective for mass-market volumes due to their established infrastructure and high throughput rates. AM is generally not competitive at this scale maar for components like standard shock mounts.
Key Consideration: Always factor in the Total Cost of Ownership (TCO), including tooling elimination, assembly reduction (part consolidation), and the value of lightweighting, which can make AM economically viable even if the per-part price seems higher initially.
Q3: What kind of testing is required to validate 3D printed shock mounts for automotive applications?
A: Validation follows similar principles to conventionally manufactured parts but with added focus on AM process consistency. Typical validation steps include:
- Material Property Verification: Printing test coupons alongside the actual parts and performing destructive tests (tensile tests for strength/ductility, fatigue tests, hardness tests) to confirm the material meets specifications after all processing (including heat treatment). Microstructural analysis might also be performed.
- Dimensionale inspectie: Using CMMs or 3D scanners to verify that all critical dimensions, tolerances, and GD&T requirements are met on the final part.
- Niet-destructief onderzoek (NDT): Employing methods like CT scanning (highly recommended for internal integrity checks), Dye Penetrant Testing (for surface cracks), or Ultrasonic Testing to ensure parts are free from critical defects like porosity or cracks.
- Component Rig Testing: Subjecting the shock mount (often assembled with mating parts) to simulated operational loads on a test rig. This includes static strength tests (push/pull), durability/fatigue tests (applying cyclic loads representing lifetime usage), and potentially impact tests.
- On-Vehicle Testing: Installing the parts on prototype or test vehicles and subjecting them to real-world driving conditions (test tracks, specific maneuvers, durability runs) while monitoring performance and inspecting for wear or failure.
The specific test plan depends on the OEM’s standards, the criticality of the part, and whether it’s for motorsport, niche vehicles, or potentially broader applications.
Q4: Can existing shock mount designs be directly 3D printed?
A: Generally, no. Attempting to directly print a design optimized for casting or machining is usually inefficient and fails to leverage the key benefits of AM. Such designs often have thick, bulky sections, lack optimized load paths, and may contain features difficult or impossible to print effectively (e.g., unsupported internal cavities, features requiring extensive support structures). To realize the advantages of lightweighting, part consolidation, and performance optimization, redesigning the component using DfAM principles is almost always necessary. This involves topology optimization, lattice structure integration (if applicable), designing for self-support, and ensuring features are suitable for the layer-by-layer AM process.
Q5: What production volumes are feasible for metal 3D printed shock mounts with providers like Met3dp?
A: Metal AM technology is rapidly evolving, and production capabilities are increasing. Currently, it is highly feasible and often advantageous for:
- Prototypen: Single parts to small batches (1-20 units).
- Low Volume Production: Niche vehicles, motorsport applications, aftermarket parts (tens to hundreds of units per year).
- Medium Volume Production: Premium vehicles, specialized EV components, potentially some series production (hundreds to low thousands of units per year). Providers like Met3dp, with multiple industrial machines and streamlined workflows, can support these volumes.
While AM is continuously improving in speed and cost-effectiveness, it is not yet typically suitable for mass-market production volumes (tens of thousands to millions per year) where traditional methods like high-pressure die casting or stamping offer significantly lower per-part costs due to established economies of scale. However, for the right applications focusing on performance, customization, and moderate volumes, AM is a viable and increasingly attractive production method supported by capable B2B suppliers.
Conclusion: Driving the Future of Automotive Design with Metal Additive Manufacturing
The journey through the design, materials, manufacturing, and validation of 3D printed automotive shock tower mounts reveals the transformative impact of metal additive manufacturing on the automotive industry. This technology is no longer confined to rapid prototyping; it has matured into a powerful tool for producing highly optimized, lightweight, and complex end-use components that meet the demanding performance and efficiency goals of modern vehicles.
We’ve explored how AM unlocks unprecedented design freedom, enabling topology optimization and part consolidation strategies that strip unnecessary weight while enhancing structural integrity – benefits simply unattainable through traditional casting or machining. The resulting lightweight shock mounts contribute directly to improved vehicle dynamics, increased fuel efficiency or EV range, and allow for more innovative packaging solutions.
The successful implementation relies heavily on selecting the right geavanceerde materialen, such as high-strength A7075 or the versatile and highly printable AlSi10Mg. Equally critical is the quality of the powder feedstock and the precision of the AM process itself, demanding expertise in areas like Ontwerp voor additieve productie (DfAM), thermal management, and meticulous post-processing, including heat treatment, machining, and surface finishing. Addressing potential challenges like distortion, porosity, and achieving tight tolerances requires deep process knowledge and robust quality control systems.
Choosing the right manufacturing partner is paramount. Automotive companies need B2B-leveranciers who offer not just printing capacity but a comprehensive suite of services: material expertise, DfAM support, advanced printing technologies (like PBF-LB and SEBM), integrated post-processing, rigorous quality assurance backed by relevant certifications, and the ability to scale from prototypes to series production.
Met3dp embodies this comprehensive approach. With our foundation in advanced metal powder production using Gas Atomization and PREP technologies, our fleet of industry-leading metal 3D printers including SEBM systems, and our dedicated team of engineers and technicians, we provide end-to-end solutions tailored to the automotive sector. We partner with our clients to push the boundaries of design and manufacturing, enabling the creation of next-generation components that drive automotive innovation.
Metal additive manufacturing is fundamentally changing how vehicles are designed and built. For components like shock tower mounts, it offers a clear pathway to enhanced performance, reduced weight, and accelerated development cycles. As the technology continues to evolve, its role in shaping the future of automotive engineering will only grow.
Ready to explore how metal AM can revolutionize your next automotive project? Contact Met3dp today to discuss your lightweight component needs and learn more about our advanced Metaal 3D-printen services and capabilities. Let us be your partner in driving the future of automotive design.
Delen op
MET3DP Technology Co, LTD is een toonaangevende leverancier van additieve productieoplossingen met hoofdkantoor in Qingdao, China. Ons bedrijf is gespecialiseerd in 3D printapparatuur en hoogwaardige metaalpoeders voor industriële toepassingen.
Onderzoek om de beste prijs en een op maat gemaakte oplossing voor uw bedrijf te krijgen!
gerelateerde artikelen
Over Met3DP
Recente update
Ons product
NEEM CONTACT MET ONS OP
Nog vragen? Stuur ons nu een bericht! Na ontvangst van uw bericht behandelen wij uw verzoek met een heel team.
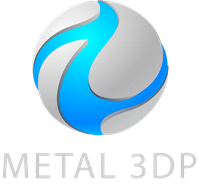
Metaalpoeders voor 3D printen en additieve productie