3D Printed Frames for Thermal Interface Modules
Inhoudsopgave
Introduction: Revolutionizing Thermal Management with 3D Printed Interface Frames
In the relentless pursuit of smaller, faster, and more powerful electronic devices and systems, managing the generated heat has become a paramount engineering challenge. From densely packed server racks and high-performance computing clusters to advanced power electronics in electric vehicles (EVs) and critical aerospace systems, efficient thermal management is no longer just a design consideration – it’s a fundamental requirement for reliability, performance, and longevity. Excessive heat can degrade component performance, shorten operational lifespans, and lead to catastrophic failures. Traditional cooling solutions, while effective to a point, often face limitations when dealing with complex geometries, high heat fluxes, or stringent space and weight constraints. This is where the concept of the Thermal Interface Frame (TIF) becomes crucial, acting as a structural and thermal bridge between heat-generating components (like CPUs, GPUs, power modules) and heat dissipation elements (like heat sinks or cold plates). Now, imagine enhancing these critical components using the transformative capabilities of additieve vervaardiging van metaal (AM)ook bekend als metaal 3d printen. This synergy is paving the way for 3D printed frames for thermal interface modules, offering unprecedented design freedom and performance potential in electronics cooling and broader oplossingen voor thermisch beheer.
A thermal interface frame is more than just a simple bracket; it often serves multiple functions. Structurally, it provides precise mounting and alignment for components, ensuring consistent contact pressure for Thermal Interface Materials (TIMs). Thermally, it must efficiently conduct heat away from the source towards the cooling system, minimizing thermal resistance. Traditionally, these frames are manufactured using methods like CNC machining or die casting, often using materials like aluminum or copper alloys. However, these methods can be restrictive. Machining complex internal structures or conformal channels designed to follow the heat source contours can be difficult, time-consuming, and generate significant material waste. Casting, while suitable for high volumes, requires expensive tooling and offers less design flexibility, often resulting in heavier parts than necessary or suboptimal thermal pathways.
Metal additive manufacturing fundamentally changes the paradigm. Technologies like Selective Laser Melting (SLM) and Electron Beam Melting (EBM) build parts layer by layer directly from metal powder, guided by a digital CAD model. This process liberates designers from many traditional manufacturing constraints. For thermal interface frames, this translates to the ability to:
- Create Complex Geometries: Integrate intricate internal cooling channels, lattice structures for weight reduction while maintaining stiffness, and organic shapes that conform perfectly to component layouts.
- Optimize Thermal Pathways: Design non-linear, direct heat paths that minimize thermal resistance, potentially incorporating features impossible to machine or cast.
- Consolidate Parts: Combine the frame with features traditionally part of the heat sink or other components, reducing assembly complexity and potential points of thermal resistance.
- Enable Rapid Prototyping and Iteration: Quickly produce and test different frame designs without the need for expensive tooling changes, accelerating development cycles.
- Geavanceerde materialen gebruiken: Effectively process high-performance alloys like Copper-Chromium-Zirconium (CuCrZr) or specialized aluminum alloys (like AlSi10Mg) optimized for thermal conductivity and structural integrity.
The implications for industries reliant on cutting-edge thermal management are profound. Engineers can now design thermal interface frames not just as passive structural elements, but as active contributors to the cooling solution, tailored precisely to the application’s unique thermal and mechanical demands. This level of customization and performance optimization is critical for pushing the boundaries in fields demanding extreme warmteafvoer capabilities. Companies seeking robust B2B thermal solutions and reliable thermal component suppliers are increasingly turning to AM service providers who possess the expertise and equipment to deliver these advanced components.
At Met3dp, we stand at the forefront of this technological shift. Leveraging decades of collective expertise in metal additive manufacturing, we provide comprehensive solutions, from our advanced SEBM (Selective Electron Beam Melting) printers known for their toonaangevend printvolume, nauwkeurigheid en betrouwbaarheid to our high-performance metal powders produced using state-of-the-art gas atomization and PREP technologies. We understand the critical interplay between material properties, process parameters, and design intricacies required to produce high-quality, high-performance 3D printed thermal interface frames. Whether you are an engineer designing next-generation power modules or a procurement manager seeking a dependable supplier for wholesale thermal frames, Met3dp offers the capabilities and partnership approach to help you harness the full potential of additive manufacturing for your thermal management challenges. We specialize in materials like CuCrZr and AlSi10Mg, ideal for these demanding applications, ensuring optimal warmteafvoer and structural integrity.
This article will delve deep into the world of 3D printed thermal interface frames. We will explore their core applications, detail the compelling advantages of using metal AM, discuss critical material selection criteria (focusing on CuCrZr and AlSi10Mg), provide essential design guidelines (DfAM), examine achievable precision levels, outline necessary post-processing steps, address common challenges, guide you in selecting the right AM service provider, analyze cost factors, and answer frequently asked questions. Join us as we explore how metal 3D printing is revolutionizing the design and manufacture of these vital thermal management components.
Core Applications: Where are 3D Printed Thermal Frames Making an Impact?
The versatility and performance benefits of 3D printed thermal interface frames (TIFs) make them increasingly sought after across a diverse range of demanding industries. Their ability to provide tailored thermal pathways, complex geometries for enhanced surface area or fluid flow, and structural support in compact spaces addresses critical needs where conventional manufacturing falls short. Procurement managers seeking wholesale thermal solutions and engineers designing cutting-edge systems are finding significant value in leveraging AM for these components. Let’s explore the key sectors where these innovative frames are making a tangible impact:
1. Power Electronics: This is arguably one of the most significant application areas. Power modules (IGBTs, MOSFETs, SiC devices) used in industrial drives, renewable energy inverters (solar, wind), power supplies, and traction systems for EVs generate substantial amounts of heat in concentrated areas.
- Uitdaging: Efficiently extracting heat from these high-power density devices while ensuring electrical isolation and mechanical stability is critical for reliability and preventing thermal runaway. Space is often limited, and minimizing thermal resistance is paramount.
- AM Solution: 3D printed TIFs, often made from high-conductivity copper alloys like CuCrZr, can be designed with:
- Conforme koelkanalen: Internal channels that precisely follow the layout of the heat-generating chips, allowing direct liquid cooling integration for maximum heat extraction.
- Optimized Base Structures: Topology-optimized designs that minimize material usage and weight while maximizing stiffness and heat spreading.
- Integrated Features: Combining the frame with spreader plates or preliminary heat sink structures to reduce thermal interface layers and assembly complexity.
- B2B Relevance: Manufacturers of power modules, EV components, and renewable energy systems require reliable thermal component suppliers capable of producing custom TIFs in volume, meeting stringent thermal and mechanical specifications.
2. Electric Vehicles (EVs) and Automotive: Beyond power electronics in the drivetrain and charging systems, thermal management is crucial for batteries, onboard computers, sensors (LiDAR, radar), and advanced driver-assistance systems (ADAS).
- Uitdaging: Managing heat from multiple distributed sources within the confined and vibration-prone environment of a vehicle. Weight reduction is also a constant goal to improve range and efficiency.
- AM Solution: Lightweight AlSi10Mg or high-conductivity CuCrZr TIFs can be employed for:
- Battery Pack Cooling: Frames integrating microchannels or complex surfaces to interface between battery modules and cooling plates.
- ECU/Sensor Cooling: Compact, custom-shaped frames that fit into tight spaces around electronic control units or sensor packages, ensuring reliable operation.
- Component Mounting & Cooling: Combining structural mounting for sensitive electronics with efficient thermal pathways in a single, weight-optimized component.
- B2B Relevance: Automotive Tier 1 suppliers and OEMs need partners for EV thermal management components, requiring high-volume production capabilities, automotive quality standards (e.g., IATF 16949), and cost-effective solutions.
3. Aerospace and Defense: Aircraft, satellites, and military equipment feature densely packed avionics, radar systems, and power distribution units operating in harsh environments with limited cooling options (often relying on conduction or limited airflow).
- Uitdaging: Ensuring reliable operation under extreme temperatures, vibrations, and G-forces. Weight is a critical design driver, and components must meet stringent reliability and qualification standards.
- AM Solution: Additive manufacturing enables:
- Highly Complex Geometries: Creating TIFs that fit within highly constrained spaces in avionics bays or around complex hardware.
- Lichtgewicht ontwerpen: Utilizing topology optimization and lattice structures (often with AlSi10Mg) to significantly reduce component weight without compromising structural integrity or thermal performance.
- Materiaalprestaties: Employing materials certified for aerospace use, capable of handling wide temperature ranges and providing efficient heat transfer.
- B2B Relevance: Aerospace manufacturers require contract manufacturing thermal parts providers with specific certifications (e.g., AS9100), proven experience with aerospace materials and processes, and rigorous quality control systems.
4. High-Performance Computing (HPC) and Data Centers: Servers, CPUs, GPUs, and specialized processors in data centers and HPC clusters generate immense heat loads. Efficient cooling is essential for performance and preventing costly downtime.
- Uitdaging: Cooling extremely high heat fluxes from processors within dense server blades or racks. Air cooling is often insufficient, pushing the need for advanced liquid cooling solutions.
- AM Solution: 3D printed TIFs facilitate advanced cooling strategies:
- Microchannel Integration: Frames designed as part of sophisticated cold plates, featuring intricate microchannels optimized for liquid coolants, placed directly over hotspots.
- Custom Shapes for Dense Packing: Creating frames that allow for maximum component density while ensuring effective thermal contact and coolant flow distribution.
- Direct Integration: Combining the TIF with manifolds or flow distributors for liquid cooling systems.
- B2B Relevance: Data center operators and HPC system builders seek innovative electronics cooling solutions and partners who can deliver high-performance, custom thermal components reliably and potentially in large quantities.
5. Industrial Equipment and Manufacturing: Lasers, welding equipment, automation systems, and process control machinery often incorporate sensitive electronics or components that require precise temperature control for optimal performance and longevity.
- Uitdaging: Providing robust cooling solutions in potentially harsh industrial environments (dust, vibration, temperature fluctuations). Customization is often needed for specific machine configurations.
- AM Solution: Additively manufactured TIFs offer:
- Rugged Designs: Frames built from durable alloys capable of withstanding industrial conditions.
- Tailored Solutions: Custom-designed frames for unique equipment geometries or thermal loads, enabling optimized performance for specialized machinery.
- Rapid Replacement/Upgrades: Ability to quickly produce replacement frames or improved designs without traditional tooling lead times.
- B2B Relevance: Industrial equipment manufacturers require flexible thermal component suppliers who can provide both standard and custom solutions with reasonable lead times and industrial-grade reliability.
Summary Table: Applications and AM Benefits for TIFs
Industrie | Belangrijkste uitdagingen | AM Solution Examples | Relevant Keywords |
---|---|---|---|
Power Electronics | High heat density, space constraints, reliability | Conformal cooling channels (CuCrZr), topology-optimized bases, integrated spreaders | Power module cooling, IGBT thermal management, wholesale thermal solutions |
EV / Automotive | Distributed heat, weight reduction, vibration | Battery cooling frames, ECU/Sensor cooling (AlSi10Mg/CuCrZr), integrated mounting | EV thermal management, automotive electronics cooling, Tier 1 supplier solutions |
Ruimtevaart en defensie | Extreme environments, weight critical, reliability | Complex geometries for tight spaces, lightweight lattices (AlSi10Mg), certified materials | Aerospace components, AS9100 certified supplier, defense electronics cooling |
HPC / Data Centers | Very high heat flux, component density | Microchannel cold plate integration, custom shapes for density, manifold integration | High-performance computing cooling, data center thermal solutions, liquid cooling |
Industriële apparatuur | Harsh environments, customization needs, robustness | Rugged designs, tailored solutions for specific machines, rapid replacement parts | Industrial heat exchangers, laser cooling, custom thermal component supplier |
Exporteren naar Sheets
The breadth of these applications underscores the transformative potential of metal 3D printing in thermal management. By enabling optimized designs and leveraging advanced materials, 3D printed thermal interface frames are not just replacements for traditionally manufactured parts; they are enablers of next-generation performance and efficiency across critical industries. Companies like Met3dp, with their deep expertise in both AM processes and high-performance metaalpoeders, are crucial partners in realizing this potential.
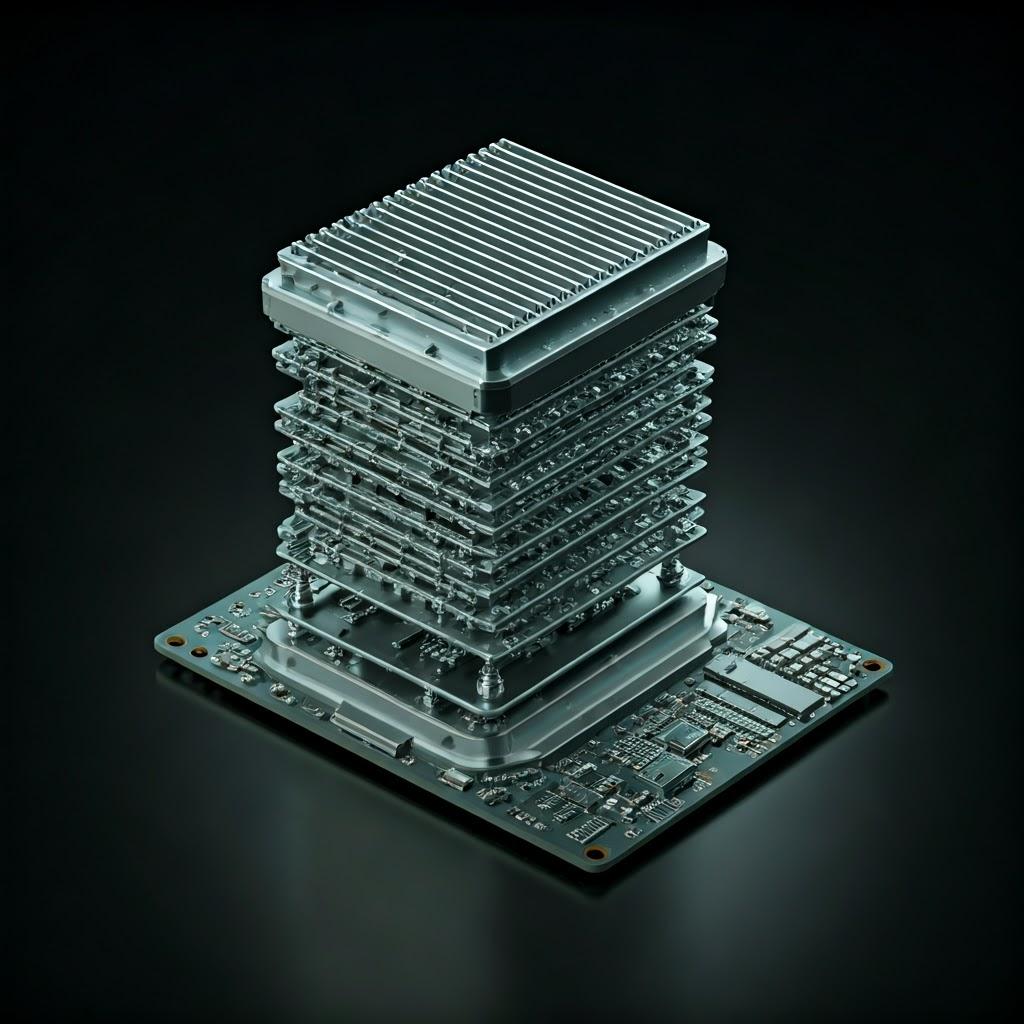
The Additive Advantage: Why Choose Metal 3D Printing for Thermal Interface Frames?
While traditional manufacturing methods like CNC machining and die casting have long served the purpose of creating thermal interface frames (TIFs), they inherently carry limitations that metal additive manufacturing (AM) can overcome, offering compelling advantages, particularly for complex and high-performance applications. For engineers and procurement managers evaluating procurement thermal solutions, understanding these benefits is key to making informed decisions and unlocking superior performance, faster development cycles, and potentially lower total costs in certain scenarios. Let’s dissect the specific advantages AM brings to the table compared to conventional approaches:
1. Unmatched Design Freedom (Geometric Complexity):
- Traditional Limits: CNC machining struggles with internal features, undercut geometries, and highly complex curves. Access for cutting tools is a major constraint. Die casting requires draft angles, avoids complex internal coring where possible, and necessitates expensive, fixed tooling, making intricate designs costly or impossible.
- AM Advantage: Layer-by-layer construction removes many geometric barriers. This allows for:
- Internal Cooling Channels: Sophisticated, non-linear channels that conform precisely to heat sources or follow optimal flow paths for liquid coolants can be directly integrated into the frame structure. This is virtually impossible or prohibitively expensive with machining.
- Roosterstructuren: Lightweight yet stiff structures can be incorporated to reduce material usage and weight (critical for aerospace and automotive) while maintaining mechanical integrity and potentially enhancing surface area for convective cooling.
- Topologieoptimalisatie: Algorithmic design processes can generate highly organic, efficient shapes that distribute material only where structurally or thermally needed, minimizing mass and maximizing performance. These shapes are often unmanufacturable traditionally.
- Deelconsolidatie: Features previously requiring multiple parts (e.g., frame, spreader, small manifold) can potentially be combined into a single printed component, reducing assembly time, weight, and potential thermal contact resistance points.
2. Enhanced Thermal Performance:
- Traditional Limits: Thermal pathways are often constrained by manufacturing feasibility (e.g., straight drilled holes for cooling, uniform thickness). Optimizing heat spreading or minimizing resistance across complex interfaces can be challenging.
- AM Advantage: Design freedom directly translates to thermal benefits:
- Conformal Cooling: Channels that mirror the topography of the heat source (e.g., power module layout) ensure more uniform and efficient heat extraction compared to flat cold plates or simple frames.
- Optimized Heat Spreading: The ability to vary wall thickness locally or incorporate internal structures allows designers to guide heat more effectively towards the ultimate heat sink.
- Reduced Thermal Interface Resistance: Part consolidation eliminates physical interfaces (and the TIMs required between them), which inherently add thermal resistance. Integrated designs offer more direct thermal paths.
- Increased Surface Area: Lattice structures or complex external fins can be integrated into the frame design to enhance convective heat transfer if exposed to airflow.
3. Rapid Prototyping and Accelerated Development:
- Traditional Limits: Creating prototypes via CNC machining can be time-consuming, especially for complex parts. Creating casting tooling is expensive and slow, making design iterations costly and hindering development speed.
- AM Advantage: AM operates directly from digital CAD files without dedicated tooling.
- Snelheid: Functional metal prototypes can often be produced in days rather than weeks or months.
- Iteratie: Multiple design variations can be printed and tested concurrently or sequentially much faster and more cost-effectively than iterating with traditional tooling. This allows for quicker design validation and optimization cycles.
- Reduced Risk: Problems can be identified and rectified early in the design phase before committing to expensive mass-production tooling.
4. Material Flexibility and Optimized Use:
- Traditional Limits: Machining generates significant waste material (swarf), especially for complex parts starting from billets. Casting is material-efficient but limited in alloy choices compared to the wide range of powders available for AM. Joining dissimilar metals effectively can be challenging.
- AM Advantage:
- Materiaalefficiëntie: AM is an additive process, using primarily only the material needed for the part and necessary supports, significantly reducing waste compared to subtractive machining.
- Geavanceerde legeringen: AM processes, particularly Powder Bed Fusion (SLM/EBM), can effectively process advanced alloys like high-conductivity CuCrZr or specialized aluminum and titanium alloys that might be difficult or impossible to cast or machine effectively. Met3dp, for instance, utilizes advanced gas atomization and PREP technologies to produce high-sphericity, high-flowability powders crucial for achieving dense, high-quality parts from these advanced materials.
- Potential for Multi-Material (Future): While still emerging, research into multi-material metal AM could eventually allow different properties (e.g., high conductivity in one area, high strength in another) within a single frame component.
5. Suitability for Customization and Low-to-Medium Volume Production:
- Traditional Limits: Die casting is only economical for very high volumes due to tooling costs. CNC machining can be costly for highly complex parts, even at lower volumes, due to long machining times.
- AM Advantage: AM is highly cost-effective for:
- Custom Parts: Producing one-off or highly customized TIFs tailored to specific, unique applications without tooling investment.
- Low-to-Medium Volumes: For production runs where tooling costs for casting are not justified, or where machining complexity drives up costs significantly, AM can be the more economical choice.
- Bridge Production: AM can be used to produce parts while waiting for high-volume tooling to be completed, shortening time-to-market.
Comparison Table: AM vs. Traditional Methods for TIFs
Functie | Metaal Additive Manufacturing (AM) | CNC-bewerking | Spuitgieten |
---|---|---|---|
Geometrische complexiteit | Very High (Internal channels, lattices, organic shapes) | Moderate (Limited by tool access, undercuts difficult) | Low-Moderate (Requires draft angles, simpler forms) |
Ontwerpvrijheid | Hoog | Gematigd | Low (Tied to tooling) |
Internal Channels | Easily Integrated | Very Difficult / Impossible | Very Difficult / Requires complex tooling |
Deel Consolidatie | High Potential | Beperkt | Beperkt |
Thermal Optimization | High (Conformal cooling, topology opt., varied thickness) | Moderate (Constrained by machinability) | Low (Constrained by casting process) |
Prototyping Speed | Fast (Days) | Moderate (Days/Weeks) | Slow (Weeks/Months due to tooling) |
Kosten gereedschap | Geen | Low (Fixturing) | Heel hoog |
Materiaal Afval | Low (Additive process) | Hoog (subtractief proces) | Low (Recyclable runners/gates) |
Materiaalkeuze | Wide range of powders (incl. advanced alloys like CuCrZr) | Wide range of machinable stock materials | More limited (Specific casting alloys) |
Ideaal volume | Low-to-Medium, Custom | Low-to-High (Depending on complexity) | Heel hoog |
Lead Time (Production) | Moderate (Print + Post-processing) | Moderate-to-High (Depending on complexity) | Moderate (After tooling completion) |
Exporteren naar Sheets
While AM offers significant advantages, it’s crucial to acknowledge that it’s not always the superior choice. For very simple frame geometries produced in extremely high volumes, die casting might remain more cost-effective. Similarly, for basic frames requiring very tight tolerances on all surfaces achievable directly through machining, CNC might be preferred if complexity isn’t a factor. However, for applications demanding maximum thermal performance, weight reduction, intricate designs, customization, or faster development cycles for complex thermal interface frames, the additive advantage provided by metal 3D printing, especially when partnered with an expert provider like Met3dp utilizing optimized afdrukmethoden, presents a compelling and often transformative solution.
Material Matters: Selecting CuCrZr and AlSi10Mg for Optimal Thermal Performance
Choosing the right material is arguably one of the most critical decisions when designing any component, but it takes on heightened importance for thermal interface frames (TIFs) where both thermal conductivity and mechanical properties are paramount. While metal additive manufacturing opens the door to a wide array of alloys, two materials stand out as particularly well-suited for 3D printed TIFs due to their excellent balance of thermal performance, processability, and mechanical characteristics: Copper-Chromium-Zirconium (CuCrZr) en Aluminum-Silicon-Magnesium (AlSi10Mg). Understanding their properties and why they are recommended is crucial for engineers designing high-performance thermal solutions and for procurement managers engaging with leveranciers van metaalpoeder or AM service providers.
Copper-Chromium-Zirconium (CuCrZr – UNS C18150): The High-Conductivity Champion
Copper alloys are renowned for their exceptional thermal and electrical conductivity. Pure copper offers the highest conductivity, but it’s relatively soft and has poor mechanical strength, especially at elevated temperatures. CuCrZr is a precipitation-hardening copper alloy designed to retain a significant portion of copper’s conductivity while offering substantially improved strength, hardness, and resistance to softening at higher temperatures.
- Belangrijkste eigenschappen:
- Hoge thermische geleidbaarheid: Typically in the range of 300-340 W/(m·K) after appropriate heat treatment, significantly higher than aluminum alloys or steels, allowing for very efficient heat transfer.
- Hoge elektrische geleidbaarheid: Often exceeding 80% IACS (International Annealed Copper Standard). While less critical for TIFs than thermal conductivity, it can be relevant if the frame also serves an electrical grounding function.
- Good Mechanical Strength: Achieves moderate to high strength and hardness through precipitation hardening (solution treatment followed by aging). Yield strengths can reach 350-450 MPa, much higher than pure copper.
- Excellent Resistance to Softening: Retains its strength and hardness at moderately elevated temperatures (up to ~450-500°C), crucial for applications involving power electronics or high-temperature environments.
- Goede corrosiebestendigheid: Similar to copper, offers good resistance in many environments.
- Why it Matters for TIFs:
- Maximum Heat Transfer: Its primary advantage is minimizing the thermal resistance of the frame itself, ensuring heat is conducted away from the source as efficiently as possible. This is critical for high heat flux applications (e.g., cooling powerful IGBTs or CPUs).
- Structurele integriteit: Provides the necessary mechanical strength to securely mount components and withstand clamping forces without deformation, especially when combined with its high-temperature stability.
- Enabling Complex Designs: When processed via AM (typically SLM), intricate internal cooling channels can be created from this high-conductivity material, maximizing the benefit of liquid cooling designs.
- AM Processing Considerations:
- Copper alloys have high reflectivity and thermal conductivity, making them challenging for Laser Powder Bed Fusion (LPBF/SLM). It requires high laser power, careful parameter optimization (scan speed, layer thickness, hatch spacing) to achieve dense, defect-free parts. Green or blue lasers are sometimes preferred over standard infrared lasers due to better absorption.
- Requires post-print heat treatment (solutionizing and aging) to achieve the desired combination of strength and conductivity. Stress relief is also common.
- Support structures are necessary and require careful design for successful printing and removal.
Aluminum-Silicon-Magnesium (AlSi10Mg): The Lightweight All-Rounder
AlSi10Mg is one of the most common and well-understood aluminum alloys used in metal AM, particularly SLM. It’s essentially a casting alloy adapted for additive manufacturing, known for its excellent processability, good strength-to-weight ratio, and decent thermal properties.
- Belangrijkste eigenschappen:
- Goede thermische geleidbaarheid: Typically around 120-180 W/(m·K), depending on the post-processing heat treatment. While significantly lower than CuCrZr, it’s still considerably better than steels or titanium alloys and sufficient for many thermal management applications.
- Lage dichtheid: Approximately 2.67 g/cm³, roughly one-third the density of copper alloys. This makes it ideal for weight-sensitive applications (aerospace, automotive).
- Good Mechanical Properties: Offers a good balance of strength and ductility, especially after heat treatment (T6). Yield strengths can range from 230-300 MPa.
- Uitstekende verwerkbaarheid in AM: Melts and solidifies reliably with standard infrared lasers used in SLM, making it relatively easy to process compared to copper. It allows for fine features and complex geometries.
- Goede corrosiebestendigheid: Forms a passive oxide layer, providing good protection in many environments.
- Kosteneffectief: Generally less expensive powder cost compared to CuCrZr.
- Why it Matters for TIFs:
- Gewichtsvermindering: Its low density is a major advantage where minimizing mass is critical (e.g., aircraft, EVs, portable devices).
- Balance of Properties: Offers a practical combination of reasonable thermal conductivity, good strength, and excellent manufacturability via AM.
- Complexe geometrieën: Its ease of processing allows for intricate designs, including thin walls, fine lattices, and complex internal features, enabling topology optimization for maximum weight savings.
- Cost Efficiency: Lower material and processing costs can make it a more economical choice for applications where the absolute highest thermal conductivity of copper is not strictly necessary.
- AM Processing Considerations:
- Well-established parameters exist for SLM processing, leading to reliable and repeatable results.
- Typically requires heat treatment (stress relief and potentially T6 aging) to optimize mechanical properties and stabilize the microstructure. Stress relief is crucial to prevent distortion.
- Support structures are needed, particularly for overhangs and bridges.
Material Selection Guide: CuCrZr vs. AlSi10Mg for TIFs
Functie | CuCrZr | AlSi10Mg | Selectiecriteria |
---|---|---|---|
Warmtegeleiding | Excellent (~320 W/m·K) | Good (~150 W/m·K) | Choose CuCrZr for highest heat flux, lowest $\Delta$T requirements. |
Dikte | High (~8.9 g/cm³) | Low (~2.67 g/cm³) | Choose AlSi10Mg for weight-critical applications (aerospace, automotive). |
Mechanische kracht | Good, esp. at high temps | Goed | Both are generally sufficient; CuCrZr better for high-temp strength retention. |
AM Verwerkbaarheid | More Challenging (Reflectivity, Power Req.) | Excellent (Well-understood, reliable) | AlSi10Mg allows easier processing, potentially finer features. |
Nabewerking | Heat Treat (Solution + Age) Required | Heat Treat (Stress Relief / T6) Recommended | Both require heat treatment for optimal properties. |
Relatieve kosten (poeder) | Hoger | Lager | AlSi10Mg is more cost-effective material-wise. |
Primary Advantage | Max Thermal Performance | Lightweight & Balanced Properties | Match advantage to primary design driver (thermal performance vs. weight/cost). |
Typical Use Cases | High-power electronics, CPU/GPU cooling | Aerospace frames, EV components, general use | Application dictates the priority. |
Exporteren naar Sheets
The Met3dp Advantage in Materials:
Successfully 3D printing thermal interface frames relies heavily on the quality of the metal powder feedstock. Poor powder quality (e.g., irregular shapes, satellites, internal porosity, poor flowability) can lead to defects in the final part, compromising both thermal and mechanical performance.
Met3dp addresses this critical aspect directly. Our company employs industry-leading gas atomization and PREP (Plasma Rotating Electrode Process) technologies to research and manufacture high-quality 3D printing metallic powders.
- Verstuiving van gas: Our equipment utilizes unique nozzle and gas flow designs optimized to produce metallic spheres with high sphericity and excellent flowability – essential characteristics for uniform layer spreading and dense packing in powder bed fusion processes.
- High-Quality Portfolio: Met3dp manufactures a wide range of metal powders optimized for laser (SLM) and electron beam (SEBM) powder bed fusion, including standard alloys like AlSi10Mg and specialized materials like CuCrZr. Our portfolio extends to innovative alloys such as TiNi, TiTa, TiAl, TiNbZr, CoCrMo, stainless steels, and superalloys, showcasing our broad materials expertise.
By controlling the powder production process, Met3dp ensures a consistent, high-quality input for our AM services, translating to superior final part quality for demanding components like thermal interface frames. Partnering with a provider like Met3dp, who possesses deep knowledge spanning materials science, powder production, and additive manufacturing processes, ensures that your TIFs are built from the best possible materials using optimized techniques, achieving the performance required for your critical applications. Choosing between CuCrZr and AlSi10Mg depends heavily on the specific requirements of the application, balancing the need for supreme thermal conductivity against constraints like weight and cost.
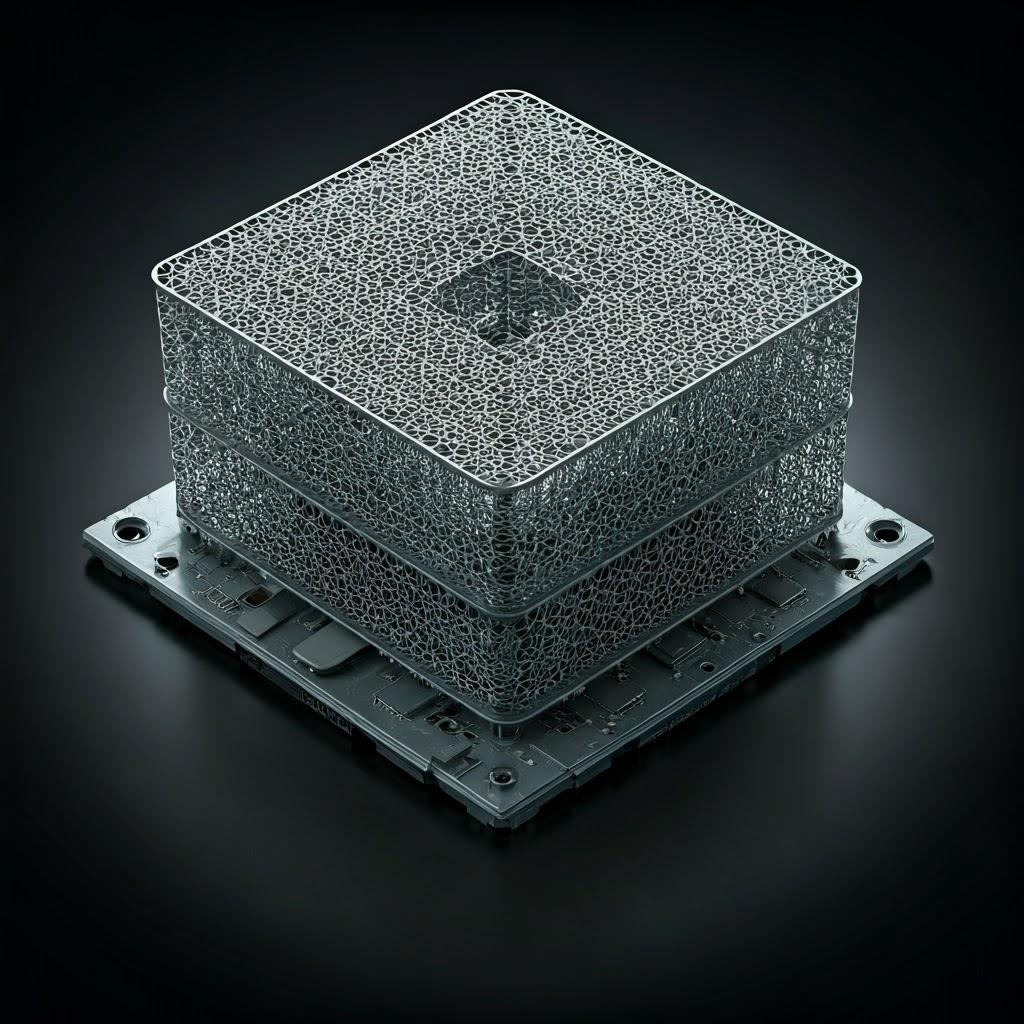
Design for Additive Manufacture (DfAM): Optimizing Thermal Frame Geometry
Simply taking a design intended for CNC machining or casting and sending it to a metal 3D printer rarely yields optimal results, either in terms of performance or cost-effectiveness. To truly harness the power of additive manufacturing for thermal interface frames (TIFs), designers must embrace Design for Additive Manufacture (DfAM) principles. DfAM involves tailoring the geometry of the part specifically to leverage the strengths and accommodate the constraints of the chosen AM process (like SLM or EBM) and material (like CuCrZr or AlSi10Mg). This proactive approach is essential for maximizing thermal performance, minimizing weight, reducing print time and cost, and ensuring manufacturability, especially when considering wholesale thermal frames where production efficiency matters. Let’s explore key DfAM considerations for optimizing TIF geometry:
1. Leveraging Geometric Freedom for Thermal Enhancement:
- Conforme koelkanalen: This is perhaps the most potent thermal advantage offered by AM. Instead of straight, drilled holes, design internal channels that precisely follow the contours of the heat-generating components mounted to the TIF.
- Design Rules: Consider minimum achievable channel diameter (often ~0.5-1.0 mm, depending on process and powder), ensure smooth bends to minimize pressure drop, and crucially, design accessible inlet/outlet ports for coolant connection and internal powder removal after printing. Consider teardrop or diamond shapes for horizontally oriented channels to make them partially self-supporting.
- Voordeel: Maximizes heat transfer efficiency by bringing the coolant closer to the heat source and ensuring more uniform temperature distribution compared to traditional cold plate approaches integrated with frames.
- Topologieoptimalisatie: Utilize specialized software (e.g., Altair Inspire, nTopology, Siemens NX) to define load cases (mechanical clamping forces, vibration profiles) and thermal loads, then let the algorithm remove material from non-critical areas.
- Proces: Define design spaces, keep-out zones (for mounting holes, component interfaces), and optimization goals (e.g., minimize mass subject to stiffness constraints, minimize thermal resistance).
- Outcome: Often results in organic, bone-like structures that are highly efficient in terms of material usage and structural performance. These shapes are typically impossible to manufacture conventionally but are ideal for AM. Requires careful translation into manufacturable CAD geometry (smoothing, ensuring minimum feature sizes).
- Voordeel: Significant weight reduction (vital for aerospace/automotive) while maintaining or even improving structural integrity and potentially creating beneficial thermal pathways.
- Roosterstructuren: Incorporate internal or external lattice structures (strut-based or TPMS – Triply Periodic Minimal Surfaces) within the frame’s volume.
- Types & Uses: Strut lattices are good for lightweighting and stiffness. TPMS lattices (like Gyroid) offer high surface area-to-volume ratios, potentially beneficial for enhancing heat transfer if integrated with fluid flow or even passive air cooling, while also providing good structural support. Density can often be graded across the structure.
- Overwegingen: Minimum strut diameter/wall thickness, ensuring powder removability from internal cells (access points are critical), understanding the anisotropic thermal conductivity of certain lattice types.
- Voordeel: Further weight reduction compared to solid topology optimization, potential for enhanced convective cooling surface area, tunable stiffness.
2. Accommodating AM Process Constraints:
- Minimum Wall Thickness: Each AM process/material combination has a limit on the thinnest stable wall that can be reliably printed. Typically ranges from 0.3mm to 0.8mm. Designing below this limit can lead to print failures or poor feature definition. Consider thicker walls for structural integrity or heat spreading requirements.
- Overhangs and Support Structures: Metal AM processes generally require support structures for features angled below a certain threshold relative to the build plate (often ~45 degrees). Supports anchor the part, prevent warping, and conduct heat away during printing.
- DfAM Strategy: Minimize the need for supports, as they consume extra material, add print time, and require post-processing removal (which can damage surfaces or be difficult in confined areas).
- Technieken: Orient the part strategically on the build plate, use chamfers or fillets instead of sharp horizontal edges on down-facing surfaces, design self-supporting angles (e.g., >45 degrees), utilize self-supporting shapes like diamonds or teardrops for horizontal holes. Where supports are unavoidable, design them for easy access and removal (e.g., using minimal contact points).
- Eigenschap Resolutie: Understand the minimum size of features (holes, slots, pins, text) that can be accurately produced. This depends on laser/beam spot size, powder particle size, and process parameters. Fine, sharp internal corners can be difficult to fully consolidate or clean. Using fillets is generally recommended.
- Powder Removal: For TIFs with internal channels or complex lattice structures, ensuring complete removal of unfused metal powder after printing is critical. Trapped powder adds weight and can compromise thermal or fluid flow performance.
- Design Strategy: Include strategically placed access holes or drainage channels in the design, ensure internal passages are large enough for powder to flow out, avoid dead-end cavities, and orient the part to facilitate drainage during breakout and cleaning.
3. CAD Modeling Best Practices for AM:
- Avoid Sharp Internal Corners: These act as stress concentrators, potentially leading to cracking during printing (due to thermal stress) or in operation. Use fillets generously.
- Consider Shrinkage/Distortion: Metal AM involves significant thermal cycles, leading to internal stresses and potential distortion. While service providers like Met3dp use simulation and optimized parameters to mitigate this, designers can help by avoiding large, flat, unsupported sections and incorporating features that add stiffness. Advanced users might pre-deform the CAD model slightly to compensate for predicted shrinkage.
- Design Tolerances Appropriately: Understand the typical achievable tolerances of the AM process (see next section) and design accordingly. Avoid specifying unnecessarily tight tolerances on non-critical features, as this drives up post-processing costs (machining). Clearly indicate critical dimensions and surfaces requiring tighter control.
- Model Format: Provide high-quality, watertight STL files or, preferably, step/native CAD files to the AM service provider. Poor quality input models can lead to printing errors.
DfAM Summary Table for TIFs:
DfAM Principle | Key Technique(s) | Benefit(s) for TIFs | Overwegingen |
---|---|---|---|
Thermal Enhancement | Conformal Channels, Topology Opt., Lattice Structures | Improved Heat Transfer, Reduced $\Delta$T, Weight Reduction, Increased Surface Area | Min. Channel Size, Powder Removal, Software Needs, Manufacturability Checks |
Support Minimization | Orientation, Self-Supporting Angles, Chamfers/Fillets | Reduced Print Time/Cost, Easier Post-Processing, Better Surface Finish | Max. Self-Supporting Angle (~45°), Sacrificial Features |
Feature Definition | Min. Wall Thickness, Min. Feature Size, Fillets | Part Printability, Structural Integrity, Reduced Stress Concentration | Process/Material Limits (e.g., 0.3-0.8mm wall), Avoid Sharp Corners |
Poeder verwijderen | Access Holes, Drainage Paths, Avoid Dead Ends | Complete Powder Evacuation, Ensure Channel Flow, Reduce Part Weight | Channel Size vs. Powder Size, Cleaning Method Access |
Structural Integrity | Topology Opt., Fillets, Avoid Large Flat Areas | Stiffness, Reduced Distortion Risk, Improved Fatigue Life | Load Case Definition, Simulation Needs |
Kostenefficiëntie | Support Min., Topology Opt., Appropriate Tolerances | Lower Print Cost, Less Material Usage, Reduced Post-Processing Time | Balance Performance with Manufacturability |
Exporteren naar Sheets
By integrating these DfAM principles from the outset, engineers can design 3D printed thermal interface frames that are not only functional but truly optimized for performance, weight, and cost-effective production via additive manufacturing. Collaborating closely with an experienced AM service provider like Met3dp during the design phase can provide invaluable feedback on manufacturability and help unlock the full potential of AM for your thermal management needs.
Precision and Finish: Understanding Tolerances and Surface Quality in AM Thermal Frames
When designing and procuring critical components like thermal interface frames (TIFs), especially those interfacing with expensive electronics or forming part of a precise thermal stack-up, understanding the achievable precision and resulting surface finish is vital. Metal additive manufacturing, while offering incredible design freedom, produces parts with inherent characteristics regarding dimensionale nauwkeurigheid en surface roughness (Ra) that differ significantly from traditional methods like high-precision CNC machining. Managing expectations and planning for necessary post-processing steps are key considerations for both engineers and B2B additive manufacturing procurement specialists.
Dimensional Accuracy in Metal AM:
Metal AM processes like Selective Laser Melting (SLM) and Electron Beam Melting (EBM) build parts layer by layer, and while highly controlled, the process involves rapid melting and solidification, leading to thermal stresses and potential micro-scale variations.
- Typical Tolerances: As a general guideline, for well-controlled processes and medium-sized parts, achievable tolerances for metal AM often fall within the range of:
- +/- 0.1 mm to +/- 0.3 mm for smaller dimensions (e.g., up to 100 mm).
- +/- 0.1% to +/- 0.2% of the nominal dimension for larger features.
- This often corresponds to tolerance classes like ISO 2768-m (medium) of soms ISO 2768-f (fijn) for certain features, but it’s highly dependent on the specific geometry, material, machine calibration, and build orientation.
- Factoren die de nauwkeurigheid beïnvloeden:
- Machinekalibratie: Regular calibration of the laser/electron beam positioning system, powder deposition mechanism, and build platform is crucial.
- Thermische effecten: Residual stresses built up during the print can cause warping or distortion, affecting final dimensions. This is managed through support strategies, optimized scan patterns, and post-print stress relief.
- Onderdeelgeometrie en -grootte: Larger parts and complex geometries with varying thicknesses are more prone to distortion.
- Bouwrichting: The orientation of the part on the build plate affects support needs, thermal history, and potential stair-stepping effects on angled surfaces, all impacting accuracy.
- Materiaaleigenschappen: Different materials (e.g., CuCrZr vs. AlSi10Mg) have different thermal expansion coefficients and melting behaviors, influencing final dimensions.
- Nabewerking: Heat treatments can cause slight dimensional changes (shrinkage/growth), and support removal might affect surface accuracy. Machining is often required for very tight tolerances.
- Met3dp’s Commitment: At Met3dp, we recognize the importance of precision. Our printers are engineered to deliver industry-leading accuracy and reliability, essential for mission-critical parts in demanding fields like aerospace, medical, and automotive. We employ rigorous process controls and quality checks, detailed further on our Over ons pagina, to ensure components meet the specified dimensional requirements.
Surface Roughness (Ra) in Metal AM:
The layer-wise nature of AM inherently results in a surface texture different from the smooth finish typically achieved by machining or polishing.
- As-Built Surface Roughness: The typical surface roughness (Ra – arithmetic average height deviation) for as-built metal AM parts often ranges from 8 µm to 25 µm (or higher).
- Vertical Walls: Generally exhibit lower Ra values within this range, influenced by powder particle size and melt pool characteristics.
- Angled/Curved Surfaces: Show a “stair-stepping” effect due to the layer geometry, leading to higher Ra values.
- Top Surfaces: Can be smoother but sometimes show slight variations from the final laser passes.
- Down-Facing Surfaces (Supported): Tend to have the highest roughness due to contact with support structures.
- Impact on TIF Performance: Surface roughness is particularly critical for TIFs at interfaces where Thermal Interface Materials (TIMs) are applied.
- Thermal Contact Resistance (TCR): Rough surfaces create microscopic air gaps when mating with another component or TIM, significantly increasing TCR and hindering heat transfer. A smoother surface allows for better wetting and thinner bond lines with TIMs, reducing resistance.
- TIM Interaction: Very rough surfaces might require thicker, more compliant TIMs (pastes, pads) to fill the voids effectively. Smoother surfaces (< 3-5 µm Ra) are generally preferred for optimal TIM performance, especially with thinner, high-performance materials.
- Fluid Sealing: If the TIF incorporates fluid channels, rough surfaces might pose challenges for achieving reliable sealing with gaskets or O-rings.
- Gladdere afwerkingen bereiken: Since as-built AM surfaces are often too rough for critical thermal interfaces, post-processing is essential:
- CNC-bewerking: The most common method to achieve smooth (Ra < 1 µm, or even lower), flat surfaces on specific faces (e.g., the TIM contact area, mounting pads).
- Polishing/Lapping: Can achieve very smooth, mirror-like finishes if required, though often more expensive and time-consuming.
- Bead Blasting / Tumbling: Can provide a more uniform matte finish and remove loose particles but generally doesn’t significantly reduce the Ra value compared to machining or polishing. It can slightly improve Ra on very rough supported surfaces.
Verification and Quality Control:
Ensuring that the final TIF meets the required dimensional and surface specifications is crucial.
- Dimensionale inspectie: Coordinate Measuring Machines (CMMs) provide high-accuracy point measurements for critical dimensions, hole locations, and flatness. 3D scanning offers a comprehensive comparison of the entire part geometry against the original CAD model, useful for complex shapes and identifying overall distortion.
- Meting van oppervlakteruwheid: Profilometers are used to measure Ra and other surface texture parameters on specified surfaces, ensuring they meet requirements for TIM application or sealing.
Summary Table: Precision & Finish in AM TIFs
Parameter | Typical As-Built AM Range | Factors Influencing | Impact on TIFs | Mitigation / Improvement |
---|---|---|---|---|
Dimensionale nauwkeurigheid | +/- 0.1-0.3 mm or +/- 0.1-0.2% | Machine, Thermal, Geometry, Material | Fit, Alignment, TIM Bond Line Thickness | Process Control, Simulation, Post-Machining |
Oppervlakteruwheid (Ra) | 8-25+ µm | Orientation, Supports, Parameters | Thermal Contact Resistance (TCR), TIM Wetting, Sealing | Post-Machining, Polishing, Blasting/Tumbling |
Exporteren naar Sheets
In summary, while metal AM provides unparalleled design freedom, designers must account for its inherent tolerances and surface finish. Specify tight tolerances and smooth finishes alleen where functionally necessary (e.g., TIM interfaces, critical mounting points) and plan for post-processing steps like machining to achieve these requirements. Partnering with a quality-focused AM provider who understands these nuances is key to obtaining functional, reliable 3D printed thermal interface frames.
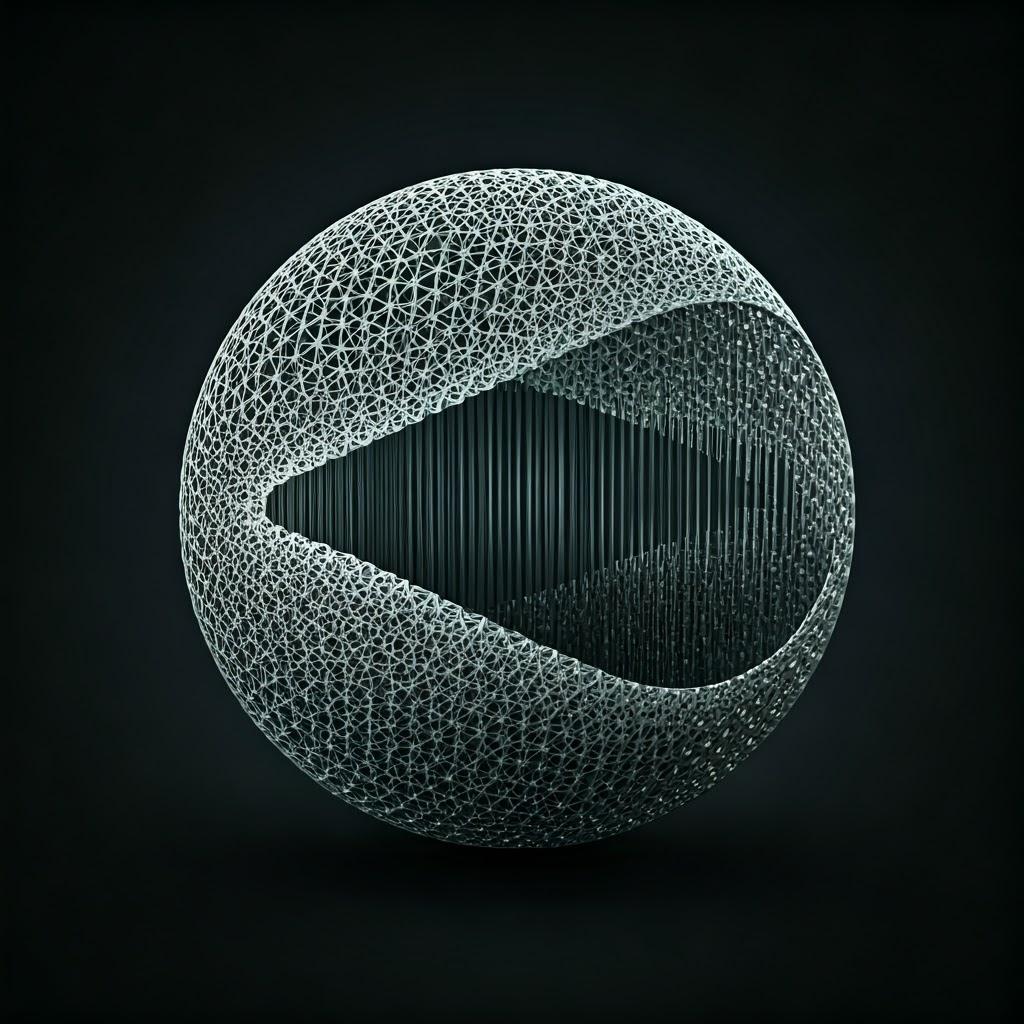
Beyond Printing: Essential Post-Processing for 3D Printed Thermal Frames
The journey of a 3D printed thermal interface frame (TIF) doesn’t end when the printer stops. The “as-built” part, fresh off the build plate, requires several crucial nabewerking steps to transform it into a functional, reliable component ready for integration. These steps are vital for relieving internal stresses, achieving the desired material properties (especially for alloys like CuCrZr), ensuring dimensional accuracy, attaining the necessary surface finish for thermal interfaces, and removing residual powder and support structures. Understanding these processes is essential for accurately estimating final part cost, lead time, and performance capabilities. For businesses sourcing contract manufacturing thermal parts, ensuring the provider has robust post-processing capabilities is as important as the printing itself.
1. Heat Treatment (Stress Relief & Property Optimization):
This is often the first and one of the most critical post-processing steps, particularly for metal AM parts susceptible to residual stress.
- Doel:
- Verlichting van stress: The rapid heating and cooling cycles during layer-by-layer fusion create significant internal stresses within the printed part. These stresses can cause warping/distortion after removal from the build plate or later in the component’s life, and can potentially reduce fatigue strength. Heating the part to an elevated temperature allows the material’s atoms to rearrange slightly, relieving these stresses without significantly altering the microstructure (for simple stress relief).
- Microstructure Homogenization & Property Enhancement: For certain alloys, specific heat treatment cycles are required to achieve the desired final mechanical and thermal properties. This involves controlled heating and cooling phases to modify the grain structure, dissolve phases, and/or precipitate strengthening particles.
- Material-Specific Cycles:
- AlSi10Mg: Commonly undergoes a stress relief cycle (e.g., 2 hours at 300°C) shortly after printing, often while still attached to the build plate, to minimize distortion during removal. For improved strength and ductility, a T6 heat treatment (solutionizing followed by artificial aging) might be applied, though this can sometimes slightly reduce thermal conductivity. The optimal treatment depends on the application’s balance between mechanical and thermal requirements.
- CuCrZr: Requires a precipitatieharding treatment to achieve its high strength and conductivity. This typically involves:
- Oplossing Behandeling: Heating to a high temperature (~950-1000°C) to dissolve Chromium and Zirconium into the Copper matrix, followed by rapid quenching (water).
- Veroudering: Reheating to a lower temperature (~450-500°C) for a specific duration (e.g., 2-4 hours) to allow Cr and Zr particles to precipitate finely within the matrix, significantly increasing strength and hardness while restoring high conductivity. Careful control of temperature and time is critical.
- Uitrusting: Requires calibrated furnaces capable of maintaining precise temperatures and potentially controlled atmospheres (e.g., vacuum or inert gas like Argon) to prevent oxidation, especially for copper alloys at high temperatures.
2. Onderdeel verwijderen van de bouwplaat:
Once stress-relieved (if done on the plate), the part needs to be separated from the metal build plate it was printed on.
- Methoden: Commonly done using wire Electrical Discharge Machining (EDM), bandsawing, or sometimes intentionally designed weak points in the support interface allow it to be manually broken off. Wire EDM provides a clean cut with minimal force on the part.
3. Draagstructuur verwijderen:
The support structures necessary during printing must be removed.
- Methoden: Depending on the design and material:
- Handmatig verwijderen: Supports designed with small contact points can sometimes be broken off by hand or with simple tools (pliers, cutters). Care must be taken not to damage the part surface.
- Bewerking: Supports in accessible areas can be milled or ground away.
- Wire EDM: Can be used for precise removal, especially near delicate features.
- Uitdagingen: Accessing supports within complex internal geometries or channels can be difficult. Residual marks or “nubs” may be left at support contact points, potentially requiring further finishing. This highlights the importance of DfAM to minimize support needs and design them for easy removal.
4. Machining for Critical Tolerances and Surfaces:
As discussed previously, as-built AM parts rarely meet the tight tolerances or smooth surface finish requirements for critical interfaces.
- Doel: To achieve precise dimensions, flatness, parallelism, and low Ra values on specific features.
- Common Areas on TIFs:
- TIM interface surfaces (contacting the heat source and the heat sink/cold plate).
- Mounting holes (for precise alignment).
- Sealing surfaces (if applicable).
- Proces: Typically involves CNC milling or turning. Requires careful setup and fixturing of the AM part. Can be considered a form of hybride productie, combining the geometric freedom of AM with the precision of subtractive machining.
5. Surface Finishing and Cleaning:
Depending on the application requirements, additional surface treatments may be applied.
- Bead Blasting / Sand Blasting: Propels abrasive media (glass beads, aluminum oxide) at the surface. Creates a uniform, matte finish, removes loose powder particles, and can blend minor imperfections. Does not significantly improve dimensional accuracy or drastically reduce Ra.
- Tumbling / Vibratory Finishing: Parts are placed in a machine with abrasive media and vibrated or tumbled. Good for batch processing, deburring sharp edges, and achieving a more uniform finish on complex shapes, but less precise than machining.
- Polishing / Lapping: Mechanical or chemical-mechanical processes to achieve very smooth, reflective surfaces (Ra << 1 µm). Usually reserved for specific optical or ultra-high-performance thermal interface requirements.
- Coating / Plating: Applying coatings for:
- Corrosiebescherming: Especially if the TIF operates in a harsh environment.
- Electrical Insulation: If required between the frame and components.
- Slijtvastheid: For surfaces subject to repeated contact or friction.
- Enhanced Emissivity: For improved radiative cooling (less common for TIFs).
- Schoonmaken: Thorough cleaning is vital to remove all loose and trapped metal powder, especially from internal channels or lattice structures, as well as any residues from machining fluids or blasting media. Methods include compressed air, ultrasonic cleaning baths (often with specific solvents), and visual/borescope inspection. CT scanning can sometimes be used to verify internal cleanliness non-destructively.
Summary Table: Post-Processing Steps for AM TIFs
Post-Processing Step | Doel | Typical Methods | Belangrijke overwegingen |
---|---|---|---|
Hittebehandeling | Stress Relief, Property Optimization | Furnace Treatment (Vacuum/Inert), Specific Cycles | Material type (CuCrZr vs AlSi10Mg), Prevents warping, Achieves specs |
Part Removal | Separate part from build plate | Wire EDM, Bandsaw, Manual Break | Clean cut, Minimize force |
Ondersteuning verwijderen | Remove temporary printing supports | Manual, Machining, Wire EDM | Access, Avoid part damage, DfAM for ease of removal |
CNC-bewerking | Achieve tight tolerances & smooth critical surfaces | Milling, Turning | TIM interfaces, Mounting holes, Flatness/Parallelism |
Oppervlakteafwerking | Improve Ra, Aesthetics, Add Functionality | Blasting, Tumbling, Polishing, Coating/Plating | Application needs (thermal, corrosion, electrical) |
Cleaning & Inspection | Remove residual powder, fluids; Verify requirements | Compressed Air, Ultrasonic Bath, Inspection (Visual/CT) | Internal channels, Final QC check |
Exporteren naar Sheets
Each post-processing step adds time and cost to the production of a 3D printed TIF. Therefore, optimizing the design (DfAM) to minimize complex supports and specifying tight tolerances or special finishes only where absolutely necessary are crucial for managing the overall project budget and timeline. Working with a full-service provider like Met3dp, equipped with comprehensive in-house or tightly managed external post-processing capabilities, ensures seamless integration of these essential steps and delivery of finished, functional thermal interface frames.
Navigating Challenges: Overcoming Hurdles in Metal AM for Thermal Components
While metal additive manufacturing offers transformative possibilities for thermal interface frames (TIFs), it’s not without its challenges. Achieving consistent, high-quality results requires deep process understanding, meticulous control, and often, advanced troubleshooting. Engineers designing TIFs and procurement managers selecting Leveranciers van metaal 3D-printdiensten should be aware of potential hurdles and the strategies employed to overcome them. Successfully navigating these challenges is key to realizing the full benefits of AM for demanding thermal applications.
1. Warping and Distortion (Residual Stress):
- Uitdaging: The intense, localized heating and rapid cooling inherent in powder bed fusion processes (SLM/EBM) generate significant thermal gradients. As layers cool and contract, stresses build up within the part. These residual stresses can cause the component to warp, distort, or even crack, especially after removal from the supportive build plate. Large, flat sections and sharp transitions in thickness are particularly susceptible.
- Solutions:
- Simulation-Driven Design & Orientation: Specialized AM simulation software (e.g., Ansys Additive Suite, Simufact Additive) predicts thermal stresses and distortion based on geometry, material, and process parameters. This allows optimizing part orientation on the build plate and modifying the design to minimize stress accumulation.
- Optimized Support Strategy: Supports do more than just hold up overhangs; they act as anchors to the build plate, restraining the part and providing pathways for heat dissipation, thus reducing stress buildup. Simulation helps determine the optimal placement, type, and density of supports.
- Optimalisatie van procesparameters: Fine-tuning laser/beam power, scan speed, scan strategy (e.g., checkerboard patterns, island scanning), and layer thickness can influence the thermal history and reduce stress. Met3dp leverages extensive process knowledge to optimize parameters for materials like CuCrZr and AlSi10Mg.
- Post-Print Stress Relief: Performing a stress relief heat treatment cycle (as described in the previous section), often before removing the part from the build plate, is the most common and effective way to significantly reduce internal stresses and ensure dimensional stability.
2. Porosity Control:
- Uitdaging: Porosity refers to small voids or pores within the printed material. It can negatively impact both mechanical properties (reducing strength and fatigue life) and thermal conductivity (as voids impede heat flow). Common types include:
- Poreusheid gas: Caused by gas trapped within the molten pool (e.g., dissolved gases in the powder or shielding gas). Usually spherical.
- Poreusheid door smelting: Irregularly shaped voids caused by insufficient melting and fusion between layers or adjacent scan tracks, often due to incorrect energy input (too low power or too high speed).
- Solutions:
- High-Quality Metal Powders: Using powders with low internal gas content, high sphericity, good flowability, and controlled particle size distribution is fundamental. Met3dp’s advanced powder production systems are designed precisely for this, ensuring optimal powder characteristics.
- Strict Process Parameter Control: Maintaining the correct energy density (a function of power, speed, hatch spacing, layer thickness) is critical to ensure complete melting and fusion without excessive vaporization. This requires rigorous machine calibration and validated parameter sets for each material.
- Optimized Shielding Gas Flow: In SLM, ensuring proper flow of inert shielding gas (e.g., Argon, Nitrogen) removes metal vapor and spatter from the build zone, preventing contamination and ensuring consistent laser interaction. EBM uses a vacuum environment, eliminating this specific concern but requiring control over vacuum levels.
- Heet isostatisch persen (HIP): For critical applications demanding near-100% density, an optional post-processing step called HIP can be employed. It involves subjecting the part to high temperature and high isostatic pressure (using an inert gas like Argon) simultaneously. This collapses internal voids, effectively eliminating most porosity.
3. Support Structure Removal Difficulties:
- Uitdaging: While necessary, removing support structures, especially from complex internal geometries like conformal cooling channels or dense lattice structures within a TIF, can be time-consuming, labor-intensive, and risk damaging the part. Leaving support remnants can obstruct flow or create stress concentrations.
- Solutions:
- DfAM for Support Reduction: The best approach is proactive design – orienting the part to minimize overhangs, using self-supporting angles, and employing design features that reduce reliance on supports (see DfAM section).
- Geoptimaliseerd steunontwerp: Utilizing specialized AM software to generate supports with minimal contact points, easily breakable interfaces, or using specific types like tree supports that are easier to access and remove. Material choice also matters; some support materials are designed to be chemically dissolved (less common in metal AM).
- Advanced Removal Techniques: Employing careful manual removal with specialized tools, targeted machining, or Wire EDM for precise cutting in difficult-to-reach areas.
4. Trapped Powder Removal:
- Uitdaging: Ensuring all unfused metal powder is removed from internal channels, cavities, and intricate lattice structures is crucial. Trapped powder adds dead weight, can impede fluid flow in cooling channels, and may sinter together during heat treatment, causing blockages.
- Solutions:
- DfAM for Drainage: Designing parts with adequate access holes, drainage paths, and avoiding dead-end voids. Internal channels should be large enough relative to the powder particle size to allow flow.
- Thorough Cleaning Procedures: Utilizing a combination of methods like compressed air blow-outs, vibration tables, specialized vacuum systems, and ultrasonic cleaning baths with appropriate fluids immediately after printing and de-powdering.
- Inspectie: Using borescopes for visual inspection of internal channels and, for highly critical parts, non-destructive testing like CT scanning to verify complete powder removal.
5. Achieving Consistent Material Properties:
- Uitdaging: Ensuring that the mechanical and thermal properties of the AM part are consistent throughout its volume and repeatable from build to build is essential for reliable performance, especially for certified components in aerospace or medical fields. Variations can arise from inconsistent melt pool dynamics, thermal gradients, or powder characteristics.
- Solutions:
- Robust Process Validation: Developing and strictly adhering to validated process parameters (power, speed, hatching, layer thickness, gas flow, etc.) for each specific material and machine combination.
- Machine Calibration & Maintenance: Regular calibration of laser/beam systems, scanners, and powder handling mechanisms ensures consistent energy delivery and layer deposition.
- Powder Quality Management: Using high-quality powder from reliable suppliers (like Met3dp’s own production) with consistent batch-to-batch characteristics (chemistry, particle size distribution, flowability) and proper storage/handling to prevent contamination or degradation.
- In-Process Monitoring (Advanced): Some advanced AM systems incorporate sensors to monitor melt pool temperature, size, or layer uniformity in real-time, allowing for potential closed-loop control adjustments, although this is still evolving.
- Post-Build Material Testing: Performing regular destructive testing (tensile tests, hardness measurements) and microstructural analysis on witness coupons printed alongside actual parts to verify that material properties meet specifications.
Successfully producing high-performance 3D printed thermal interface frames requires navigating these potential challenges through a combination of smart design (DfAM), meticulous process control, high-quality materials, appropriate post-processing, and rigorous quality assurance. Partnering with an experienced and well-equipped service provider like Met3dp, who understands these intricacies and possesses the tools and expertise to mitigate risks, is crucial for achieving reliable and optimal results for your critical thermal management components.
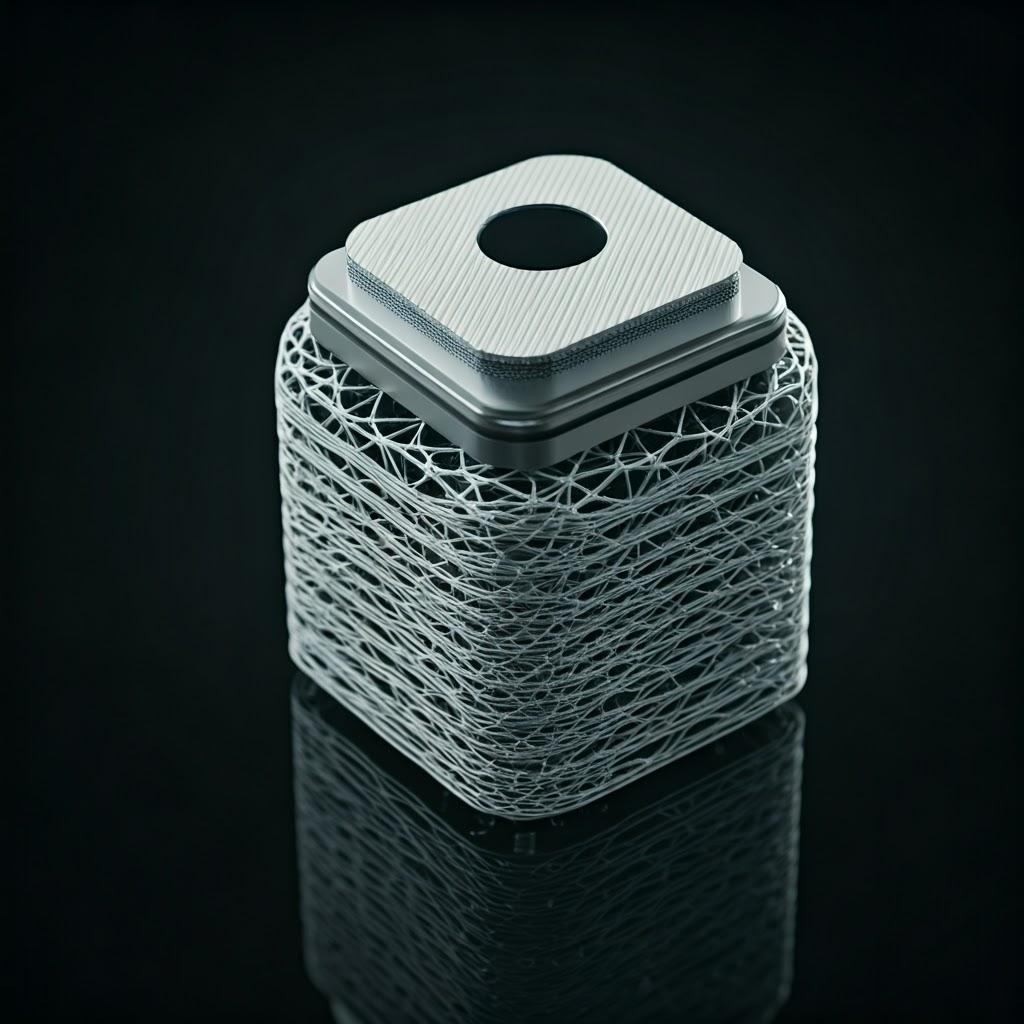
Supplier Selection: Choosing the Right Partner for Metal 3D Printed Thermal Frames
The success of your 3D printed thermal interface frame (TIF) project hinges not only on a well-optimized design and correct material choice but significantly on the capabilities and expertise of your chosen metal 3D printing service provider. Selecting the right partner is a critical decision, especially for businesses seeking reliable B2B additive manufacturing solutions for demanding applications in aerospace, automotive, medical, or industrial sectors. The ideal supplier acts as more than just a printer; they are a collaborative partner offering technical guidance, robust quality control, and dependable production. Here’s a comprehensive guide to evaluating potential partners for your TIF manufacturing needs:
1. Material Expertise and Powder Quality:
- Specific Alloy Experience: Does the supplier have proven, documented experience printing with the specific alloys required for your TIF, particularly the challenging high-conductivity CuCrZr or the common AlSi10Mg? Ask for sample parts or case studies involving these materials.
- Powder Sourcing & Quality Control: Where does the supplier source their metal powders? Do they have stringent quality control measures for incoming powder batches (e.g., checking particle size distribution, morphology, flowability, chemistry)? Suppliers who produce their own powder, like Met3dp with its advanced gas atomization and PREP capabilities, offer a distinct advantage in controlling feedstock quality, which directly impacts final part density, properties, and consistency. Ensure they understand the specific requirements for thermal application powders.
2. Machine Capabilities and Technology:
- Passende technologie: Do they operate the right type of machine for your needs? Selective Laser Melting (SLM/LPBF) is common for AlSi10Mg and increasingly for CuCrZr. Selective Electron Beam Melting (SEBM), like the systems developed by Met3dp, offers advantages for certain materials (like titanium alloys or crack-prone materials) due to its vacuum environment and higher build temperatures, potentially reducing residual stress. Ensure their machine’s build volume is adequate for your frame size.
- Machine Maintenance & Calibration: Are their machines regularly maintained and calibrated? Consistent performance relies on well-maintained equipment. Ask about their calibration schedules and procedures.
- Eigenschap Resolutie: Can their machines achieve the minimum feature sizes, wall thicknesses, and channel diameters specified in your design?
3. Technical Expertise and Engineering Support:
- DfAM Consultation: Does the supplier offer Design for Additive Manufacture (DfAM) support? Can their engineers review your design and provide feedback to optimize it for printability, performance, and cost-effectiveness? This collaborative approach is invaluable.
- Simulatiemogelijkheden: Can they perform build simulation (thermal, stress) to predict potential issues like distortion and optimize build orientation and support structures?
- Application Knowledge: Do they understand the specific challenges and requirements of thermal management components? Experience in your industry (e.g., power electronics, aerospace) is a significant plus. Met3dp, for instance, provides comprehensive solutions spanning printers, powders, and applicatieontwikkelingsdiensten, partnering with organizations to implement 3D printing effectively.
4. Quality Management System (QMS) and Certifications:
- Robust QMS: Does the supplier operate under a certified QMS like ISO 9001? This demonstrates a commitment to consistent processes and quality control.
- Industry-Specific Certifications: For specific sectors, look for relevant certifications:
- Lucht- en ruimtevaart: AS9100 is typically required, indicating adherence to stringent aerospace quality standards.
- Automobiel: IATF 16949 may be necessary for suppliers involved in automotive production supply chains.
- Medisch: ISO 13485 applies to medical device manufacturing.
- Traceerbaarheid: Ensure they have systems for full material and process traceability, crucial for critical components.
5. Post-Processing Capabilities:
- In-House vs. Managed Services: Does the supplier handle essential post-processing steps (heat treatment, support removal, machining, finishing, cleaning, inspection) in-house, or do they manage a network of qualified subcontractors? In-house capabilities often lead to better control and potentially shorter lead times.
- Equipment & Expertise: Verify they have the necessary equipment (calibrated furnaces, CNC machines, CMMs, surface measurement tools, cleaning systems) and skilled personnel for the required post-processing steps for your specific TIF design and material.
6. Track Record, Experience, and B2B Focus:
- Bewezen ervaring: Ask for case studies, references, or examples of similar thermal components they have produced. How long have they been working with metal AM?
- Reputatie in de sector: Check reviews, testimonials, or industry standing.
- B2B Reliability: Are they geared towards serving industrial clients? Do they understand the requirements for wholesale 3D printing orders, including consistent quality, reliable delivery schedules, and professional communication? Can they handle potential bulk additive manufacturing needs if your project scales up?
7. Communication, Responsiveness, and Location:
- Clear Communication: Is the team responsive, easy to communicate with, and transparent about their processes and capabilities?
- Quoting Process: Is their quoting process clear, detailed, and timely?
- Location & Logistics: While not always the primary factor, proximity can sometimes simplify logistics, site visits, and communication, though reputable suppliers operate globally. Consider shipping costs and potential import/export requirements if applicable. Met3dp, headquartered in Qingdao, China, serves a global clientele, leveraging its expertise in both equipment and materials.
Supplier Evaluation Checklist Summary:
Criteria | Key Questions to Ask | Why It Matters for TIFs | Met3dp Alignment (Example) |
---|---|---|---|
Materiële expertise | Experience with CuCrZr/AlSi10Mg? Powder source & QC? | Ensures correct material properties (thermal/mechanical), density, consistency. | Produces own high-quality powders (CuCrZr, AlSi10Mg+), deep materials science knowledge. |
Machine Capabilities | Right tech (SLM/EBM)? Build volume? Calibration? Resolution? | Ensures part can be printed accurately and reliably. | Offers advanced SEBM printers, focus on accuracy/reliability. |
Technical/Eng. Support | DfAM review? Simulation? Application knowledge? | Optimizes design for performance & cost, mitigates risks. | Provides comprehensive solutions including application development services. |
Kwaliteitssysteem/certificaten | ISO 9001? AS9100/IATF/ISO 13485 (if needed)? Traceability? | Guarantees process control, consistency, meets industry requirements for critical parts. | Committed to high standards (inquire for specific current certifications). |
Nabewerking | In-house capabilities (Heat treat, CNC, finish, inspect)? Equipment? | Ensures all steps are handled correctly for final part function. | Offers/manages necessary post-processing for complete solutions. |
Track Record / B2B Focus | Similar parts? Case studies? Experience? Handle volume orders? Reliability? | Demonstrates capability and reliability as a long-term B2B partner. | Decades of collective expertise, focused on industrial applications & partnerships. |
Communication/Logistics | Responsive? Clear quoting? Location implications? | Ensures smooth project management and delivery. | Global provider with professional communication channels (Contact Met3dp). |
Exporteren naar Sheets
Choosing the right supplier is an investment in the quality and reliability of your thermal interface frames. Conduct thorough due diligence, ask detailed questions, and prioritize partners like Met3dp who demonstrate a deep understanding of materials, processes, quality, and the specific demands of thermal management applications.
Cost Dynamics and Lead Times: Planning Your Metal AM Thermal Frame Project
While the technical advantages of 3D printed thermal interface frames (TIFs) are compelling, practical implementation requires a clear understanding of the associated costs and expected lead times. Unlike traditional mass production methods like casting, the cost structure of additive manufacturing is different, heavily influenced by factors beyond just material volume. Accurately estimating budgets and timelines is crucial for project planning, especially for wholesale 3D printing procurement and integrating AM into production schedules.
Factors Influencing Metal AM Cost:
The final price per part for a 3D printed TIF is a complex calculation involving several key elements:
- Materiaalkosten:
- Prijs poeder: This is a significant driver. High-performance powders like CuCrZr are substantially more expensive (often 5-10x or more) than common alloys like AlSi10Mg due to raw material costs and specialized production processes.
- Material Volume: The total volume of the part, including any necessary support structures, directly impacts the amount of powder consumed. DfAM techniques like topology optimization and lattice structures can significantly reduce this.
- Powder Recycling/Refresh: While unfused powder can often be sieved and reused, there are limits. Some powder inevitably degrades or becomes contaminated, requiring replenishment (“refreshing”) with virgin powder, adding to the effective material cost per part.
- Machine Time (Print Duration):
- Part Volume & Height: Larger volumes and taller parts naturally take longer to print. Print time is often more dependent on height than footprint, as each layer takes a certain amount of time to process regardless of the area being scanned in that layer.
- Complexity & Features: Intricate details, thin walls, and complex internal channels require more precise scanning and potentially slower speeds, increasing print time. Dense support structures also add significantly to build time.
- Layer Thickness & Parameters: Thicker layers print faster but result in lower resolution and potentially poorer surface finish. Optimized parameters balance speed and quality.
- Machine Amortization & Operation: The cost of running sophisticated metal AM machines (purchase price, maintenance, energy, inert gas/vacuum) is factored into an hourly machine rate, which contributes significantly to the part cost. Nesting multiple parts efficiently in a single build helps amortize setup and machine time costs.
- Arbeidskosten:
- Voorbewerking: Engineering time for DfAM review, build preparation (orientation, support generation, slicing, nesting), and simulation.
- Werking van de machine: Skilled technicians are needed to set up, monitor, and unload the machines.
- Nabewerking: This can be a major cost component. Manual labor is required for de-powdering, build plate removal, support removal (often time-consuming), heat treatment setup, CNC machining setup and operation, manual finishing/polishing, cleaning, and quality inspection. Labor rates vary significantly by region.
- Complexity and Design:
- As mentioned, complex geometries influence machine time but also heavily impact post-processing labor (support removal, cleaning internal channels, complex machining setups).
- Quality and Finishing Requirements:
- Tolerances: Specifying tighter tolerances necessitates more extensive post-machining and inspection, increasing costs.
- Afwerking oppervlak: Requirements for very smooth finishes (polishing, lapping) add significant cost compared to standard bead blasting or as-machined finishes.
- Inspection & Testing: Basic dimensional checks are standard, but requirements for advanced NDT (like CT scanning for internal integrity), material certification testing, or extensive CMM reports add cost.
- Order Quantity (Volume):
- Setup Afschrijving: Fixed costs associated with build setup are spread over more parts in larger batches, reducing the cost per part.
- Nesting Efficiency: Larger orders allow for more efficient packing of parts within the build volume, maximizing machine utilization.
- Procesoptimalisatie: For ongoing production, processes can be further optimized for efficiency.
- Wholesale Pricing: Suppliers typically offer tiered pricing or discounts for bulk 3D printing of wholesale orders, reflecting these efficiencies. However, the cost reduction per part is often less dramatic than with traditional tooling-based methods like casting.
Factors Influencing Lead Times:
The time from placing an order to receiving finished parts involves several stages:
- Offerte en orderbevestiging: (Typically 1-5 days) Depending on complexity and supplier responsiveness.
- Engineering Review & Build Prep: (Typically 1-3 days) File check, DfAM feedback (if needed), simulation (if needed), final build file generation and scheduling.
- Machine Queue: (Variable: days to weeks) Parts must wait for an appropriate machine to become available. This is often a major variable depending on the supplier’s current workload.
- Afdrukken tijd: (Variable: hours to several days or even weeks for very large/complex builds) Depends on factors discussed under machine time costs.
- Cool Down & De-powdering: (Typically 0.5-1 day) Allowing the build chamber and parts to cool safely before careful removal of unfused powder.
- Nabewerking: (Variable: days to weeks) This often takes longer than the printing itself.
- Hittebehandeling: Furnace cycles can take hours or even days, plus setup/cooling time.
- Support Removal & Machining: Highly dependent on complexity and required precision.
- Finishing & Cleaning: Variable based on requirements.
- Inspectie: Time depends on the level of inspection needed.
- Verzending: (Variable: 1 day to weeks) Depending on location and shipping method.
Indicative Lead Time Ranges:
- Prototypes (1-5 parts): Often 1-3 weeks, depending heavily on machine availability and post-processing complexity.
- Low Volume Production (10s-100s parts): Typically 3-8 weeks, allowing for optimized nesting and batch post-processing, but still subject to queues and complexity.
Cost & Lead Time Summary Table:
Factor | Invloed op kosten | Impact on Lead Time | Considerations for TIFs |
---|---|---|---|
Materiaalkeuze | High (CuCrZr >> AlSi10Mg) | Minor | Balance thermal needs vs. budget. |
Part Volume/Size | High (Material + Machine Time) | High (Print Time) | DfAM (topology opt., lattices) is key to reduce. |
Complexiteit | Moderate-High (Print Time + Post-Processing Labor) | Moderate-High (Print Time + Post-Processing) | Simplify where possible without sacrificing function; design for manufacturability (DfAM). |
Ondersteunende structuren | Moderate (Material + Print Time + Removal Labor) | Moderate (Print Time + Removal Time) | Minimize via DfAM (orientation, self-supporting features). |
Tolerances/Finish | High (Post-Machining/Finishing Labor & Time) | High (Post-Processing Time) | Specify tight requirements only where functionally necessary (e.g., TIM interfaces). |
Hoeveelheid | Moderate Reduction per Part (Setup Amort., Nesting, Wholesale Price) | Can Increase Total Time (if serial production) or Optimize (Batching) | Discuss volume breaks with supplier; plan for batch processing efficiencies. |
Quality/Inspection | Moderate-High (Labor, Equipment Time) | Moderate (Inspection Time) | Define necessary QC level early. |
Supplier Queue/Capacity | Indirect (Affects supplier overhead rates) | Potentially High (Waiting time) | Discuss expected queue times; build buffer into project schedule. |
Exporteren naar Sheets
Effectively managing metal 3D printing cost and lead time for TIFs requires careful planning, realistic expectations, and close collaboration with your chosen AM service provider. Optimize the design using DfAM, clearly define requirements, get detailed quotes breaking down costs, and discuss lead times upfront, including potential bottlenecks like machine queues and post-processing.
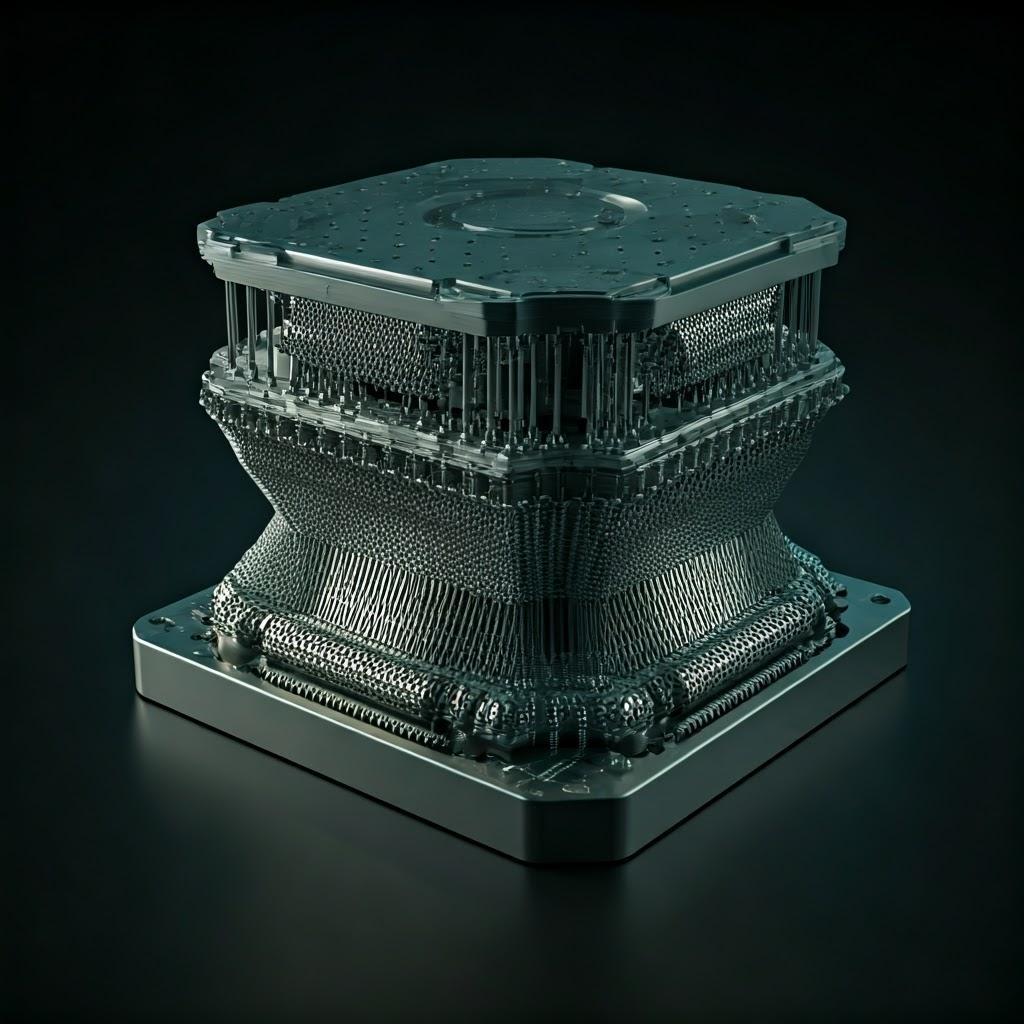
Frequently Asked Questions (FAQ) about 3D Printed Thermal Interface Frames
As metal additive manufacturing becomes more prevalent for producing complex thermal components like Thermal Interface Frames (TIFs), engineers and procurement specialists often have pertinent questions. Here are answers to some frequently asked questions:
1. How does the thermal performance of a 3D printed CuCrZr TIF compare to a traditionally machined pure copper (e.g., C110) frame?
- Geleidbaarheid: Pure copper (like C11000) has higher bulk thermal conductivity (~390-400 W/m·K) than precipitation-hardened CuCrZr (~300-340 W/m·K after heat treatment). So, for a frame of identical simple geometry, the pure copper one would have slightly lower thermal resistance.
- System Performance: De overall system thermal performance can often be significantly betere with the 3D printed CuCrZr frame. This is because AM allows for conformal cooling channels integrated directly into the frame, placing coolant much closer to the heat source and improving heat transfer efficiency far more than the slight difference in bulk conductivity. Additionally, CuCrZr offers much higher strength and resistance to softening at elevated temperatures compared to pure copper, ensuring structural integrity under load and heat.
- Conclusie: While pure copper has higher bulk conductivity, AM-enabled designs (like conformal cooling) using CuCrZr often lead to superior real-world thermal management performance in complex applications, combined with better mechanical properties.
2. Is 3D printing TIFs generally more or less cost-effective than CNC machining?
- It depends heavily on complexity and volume.
- Simple Geometries: For basic, blocky frame designs with minimal features, CNC machining from standard stock material is often more cost-effective, especially at higher volumes where machining setups are amortized.
- Complexe geometrieën: For TIFs with intricate internal channels, topology-optimized structures, lattice infill, or highly curved surfaces, metal AM becomes increasingly cost-competitive or even cheaper. Machining such features would require multiple complex setups, specialized tooling, and generate significant material waste, driving up CNC costs substantially.
- Volume: CNC machining benefits more from economies of scale for simple parts. AM is highly competitive for low-to-medium volumes (prototypes, custom parts, 10s to 1000s of units) of complex parts, where the tooling costs of casting are prohibitive and machining complexity is high. For very high volumes (many thousands) of simpler designs, casting might be cheapest, but lacks design flexibility.
- Conclusie: AM wins on cost for low-to-medium volumes of highly complex TIF designs where its unique geometric capabilities provide significant value. For simple designs in higher volumes, CNC may be cheaper. Always compare quotes based on your specific geometry and volume needs.
3. Can you achieve the same smooth surface finish on critical areas of an AM TIF as you can with machining?
- Not as-built: As discussed previously, the native surface finish of metal AM parts (SLM/EBM) is relatively rough (typically 8-25 µm Ra or higher).
- Post-Machining Required: To achieve the smooth, flat surfaces (typically Ra < 1-3 µm) required for optimal performance with Thermal Interface Materials (TIMs) or for sealing surfaces, post-process CNC machining of those specific critical faces is almost always necessary.
- Achievable Result: With post-machining, the final surface finish on those critical areas can absolutely match or even exceed typical machined finishes. The key is to only specify and machine the smoothness where it’s functionally required, leaving non-critical surfaces as-built or bead-blasted to save cost.
4. What are the main design limitations when creating internal cooling channels in 3D printed TIFs?
- Minimumdiameter: There’s a practical limit to how small channels can be reliably printed and, more importantly, de-powdered (typically ~0.5-1.0 mm minimum).
- Powder Removal Access: Channels must have clear inlets and outlets, and pathways must be designed to allow unfused powder to be completely removed after printing. Avoid dead-end pockets.
- Zelfdragende hoeken: Horizontal or low-angle channels often require internal supports during printing, which can be extremely difficult or impossible to remove. Designing channels with self-supporting shapes (teardrop, diamond) or orienting the part carefully can mitigate this.
- Wanddikte: Channel walls must meet minimum printable thickness requirements.
- Pressure Drop: Complex, narrow, or sharp-bending channels can increase coolant pressure drop, which needs to be considered in the overall system design.
5. What quality certifications are most important when selecting a supplier for aerospace or automotive TIFs?
- Lucht- en ruimtevaart: AS9100 certification is the standard, demonstrating a quality management system tailored to the stringent demands of the aviation, space, and defense industries.
- Automobiel: IATF 16949 certification is typically required for suppliers providing production parts directly or indirectly to automotive OEMs, focusing on process control, risk management, and continuous improvement.
- Baseline: ISO 9001 certification provides a fundamental baseline of quality management practices applicable across industries.
6. How does the durability and strength of 3D printed metal TIFs compare to traditionally manufactured ones (cast/machined)?
- Materiaaleigenschappen: Metal AM parts, when produced using optimized parameters and high-quality powder (like Met3dp’s), can achieve densities exceeding 99.5%.
- Vergelijking:
- vs. Castings: AM parts often exhibit superior mechanical properties (strength, ductility, fatigue life) compared to equivalent cast alloys due to the fine-grained microstructure formed during rapid solidification.
- vs. Wrought (Machined): Wrought materials generally have the highest strength and ductility due to their processing history. However, heat-treated AM parts (especially after HIPing, if used) can approach or sometimes meet certain wrought properties. AM materials can sometimes exhibit anisotropy (properties differing slightly depending on build direction).
- Conclusie: Properly processed 3D printed TIFs using materials like AlSi10Mg or CuCrZr are highly durable and can meet or exceed the mechanical requirements met by castings, offering reliable performance for demanding structural and thermal loads. Careful design and process control are key.
7. What key information does an AM supplier like Met3dp need to provide an accurate quote for a TIF?
- CAD Geometry: A 3D model, preferably in STEP format (or other neutral formats like IGES, Parasolid). STL is acceptable but less preferred for detailed analysis.
- Material Specification: Clearly state the desired alloy (e.g., CuCrZr, AlSi10Mg) and any specific material standard if applicable.
- Critical Dimensions & Tolerances: Clearly indicate on drawings or models which dimensions are critical and their required tolerances. Specify required surface finishes (Ra values) for critical faces (e.g., TIM interfaces).
- Hoeveelheid: Number of parts required (for prototyping, low volume, or potential future production).
- Vereisten voor nabewerking: Specify necessary heat treatments (e.g., stress relief, T6, CuCrZr aging), required finishing (e.g., bead blast, machining specifics), and any special cleaning needs.
- Application Context (Optional but helpful): Briefly describing the application helps the supplier understand functional requirements and potentially offer DfAM suggestions.
- Required Certifications/Testing: List any necessary quality certifications (ISO 9001, AS9100) or specific testing/inspection requirements (e.g., CMM report, material certs).
8. Does Met3dp offer design assistance or consultation for developing 3D printed TIFs?
- Yes, Met3dp provides comprehensive solutions that extend beyond just printing. We offer applicatieontwikkelingsdiensten en DfAM consultation. Our team has deep expertise in metal AM processes, materials science, and the capabilities of our metaal 3D printen systems. We can partner with your engineering team to review designs, suggest optimizations for thermal performance and manufacturability, and help you leverage the full potential of additive manufacturing for your thermal management challenges.
Conclusion: The Future is Cool – Embracing AM for Advanced Thermal Interface Frames
The challenge of managing heat in ever-more powerful and compact electronic systems is relentless. Thermal Interface Frames (TIFs), the critical link between heat sources and cooling solutions, demand innovation beyond the constraints of traditional manufacturing. As we’ve explored, additieve metaalproductie offers a powerful, often transformative approach to designing and producing TIFs that deliver superior performance, reduced weight, and unprecedented design flexibility.
By leveraging AM technologies like SLM and EBM, engineers can now:
- Unlock Unparalleled Design Freedom: Create TIFs with integrated conformal cooling channels, intricate lattice structures, En topology-optimized geometries previously impossible to manufacture, leading to breakthroughs in thermal efficiency.
- Enhance Thermal Performance: Minimize thermal resistance through optimized heat paths, direct cooling integration, and reduced interface layers via deelconsolidatie.
- Geavanceerde materialen gebruiken: Effectively employ high-performance alloys like high-conductivity CuCrZr for maximum heat transfer or lightweight AlSi10Mg for weight-critical applications, processed using high-quality powders.
- Accelerate Development Cycles: Rapidly prototype and iterate on complex TIF designs without the time and expense associated with traditional tooling.
- Achieve Lightweighting: Significantly reduce component weight, crucial for industries like aerospace and automotive, without compromising structural integrity.
However, realizing these benefits requires a holistic approach. Success depends on embracing Design for Additive Manufacture (DfAM) principles from the outset, carefully selecting the appropriate material, understanding the achievable tolerances and surface finishes, planning for essential nabewerking steps like heat treatment and machining, and navigating potential manufacturing uitdagingen through robust process control.
Crucially, partnering with the right metaal 3D printen leverancier is paramount. Look for providers with deep material expertise, advanced and well-maintained equipment, comprehensive post-processing capabilities, rigorous quality systems (including relevant certifications like ISO 9001 or AS9100), and a collaborative approach to engineering support.
Met3dp embodies this integrated approach. With our foundation in producing hoogwaardige metaalpoeders using industry-leading technologies and manufacturing advanced SEBM printing systems, we possess end-to-end expertise. Our commitment extends to providing comprehensive application development services, helping clients optimize designs and implement AM solutions effectively. Whether you need high-conductivity CuCrZr frames for power electronics or lightweight AlSi10Mg structures for aerospace, Met3dp delivers cutting-edge systems, advanced materials showcased on our Product page, and the partnership needed to enable next-generation manufacturing.
The future of high-performance thermal management is undeniably linked to the capabilities of additive manufacturing. For engineers and procurement managers striving to push the boundaries of electronics cooling and system efficiency, 3D printed thermal interface frames offer a compelling pathway forward.
Ready to explore how metal AM can revolutionize your thermal management solutions? Contact Met3dp today to discuss your specific TIF requirements and discover how our additive manufacturing capabilities can power your innovation.
Delen op
MET3DP Technology Co, LTD is een toonaangevende leverancier van additieve productieoplossingen met hoofdkantoor in Qingdao, China. Ons bedrijf is gespecialiseerd in 3D printapparatuur en hoogwaardige metaalpoeders voor industriële toepassingen.
Onderzoek om de beste prijs en een op maat gemaakte oplossing voor uw bedrijf te krijgen!
gerelateerde artikelen
Over Met3DP
Recente update
Ons product
NEEM CONTACT MET ONS OP
Nog vragen? Stuur ons nu een bericht! Na ontvangst van uw bericht behandelen wij uw verzoek met een heel team.
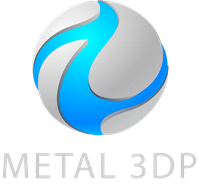
Metaalpoeders voor 3D printen en additieve productie