Mounting Brackets for EV Powertrain Systems: Leveraging Metal 3D Printing for Automotive Innovation
Inhoudsopgave
The electric vehicle (EV) revolution is transforming the automotive landscape, demanding innovative approaches to design, manufacturing, and supply chain management. Central to this transformation are the powertrain systems – the heart of any EV – encompassing batteries, electric motors, power electronics, and gearboxes. Securely mounting these critical components while optimizing for weight, performance, and packaging space presents significant engineering challenges. Mounting brackets, seemingly simple components, play a crucial role in the structural integrity, safety, and overall efficiency of electric vehicles. As automotive manufacturers and their Tier 1 suppliers push the boundaries of EV performance and range, traditional manufacturing methods for these brackets, such as casting or machining from billet, are increasingly being challenged by the capabilities of additieve vervaardiging van metaal (AM), commonly known as metal 3d printen. This technology offers unprecedented design freedom, enabling the creation of highly optimized, lightweight, and complex brackets that were previously impossible or prohibitively expensive to produce. For procurement managers, engineers, and designers in the automotive sector, understanding the potential of metal AM for producing EV powertrain brackets is essential for staying competitive and driving innovation. This article delves into the specifics of using metal 3D printing for EV powertrain mounting brackets, exploring applications, benefits, material choices, design considerations, and how to partner with the right B2B manufacturing service provider, like Met3dp, a leader in additieve productieoplossingen.
Introduction: The Critical Role of Powertrain Brackets in Electric Vehicles and the Manufacturing Shift
Electric vehicle powertrains are sophisticated assemblies of high-value components. Unlike internal combustion engine (ICE) vehicles with a single engine block, EVs often feature distributed components – battery packs spanning the vehicle floor, one or more electric motors driving the axles, inverters converting DC to AC power, and associated control units. Each of these elements requires robust mounting solutions, or brackets, to:
- Securely Position Components: Brackets rigidly hold powertrain elements in their designated locations within the vehicle chassis or subframes, preventing movement during operation, acceleration, braking, cornering, and potential impacts.
- Manage Loads and Vibrations: They must withstand static loads (component weight) and dynamic loads (vibrations from the road and powertrain operation, torque reactions, inertial forces). Effective vibration damping is crucial for passenger comfort and component longevity.
- Ensure Structural Integrity: Brackets contribute to the overall stiffness and structural integrity of the vehicle, transferring loads between the powertrain components and the vehicle body.
- Facilitate Assembly and Maintenance: Well-designed brackets simplify the assembly process on the production line and allow for easier access during servicing or component replacement.
- Optimize Packaging: In the tightly packed environment of a modern EV, brackets must often conform to complex shapes and fit within minimal available space.
- Contribute to Thermal Management: In some cases, brackets can be designed to aid in heat dissipation from components like motors or power electronics.
The shift towards electrification introduces unique challenges for bracket design and manufacturing. Key amongst these is lichtgewicht. Reducing vehicle mass is paramount for extending driving range, improving handling dynamics, and offsetting the significant weight of battery packs. Every gram saved contributes to overall efficiency. Furthermore, the rapid pace of EV development necessitates shorter design cycles and faster prototyping capabilities, areas where traditional manufacturing methods, often reliant on expensive tooling (like casting molds), can create bottlenecks.
The B2B automotive supply chain is adapting to these demands. Suppliers are sought not just for cost-effective production but for their ability to offer innovative solutions that address weight reduction, complexity integration, and speed to market. This is where metal additive manufacturing enters the picture. AM processes, particularly laser powder bed fusion (L-PBF) techniques like Selective Laser Melting (SLM) or Direct Metal Laser Sintering (DMLS), build parts layer by layer directly from 3D CAD data using high-power lasers to fuse fine metal powders. This approach eliminates the need for traditional tooling, unlocks complex geometries, and enables the production of highly optimized structural components. Companies like Met3dp, with their expertise in both advanced metal powders and industrial-grade 3D printing systems, are pivotal in enabling automotive manufacturers and suppliers to harness the full potential of AM for critical components like EV powertrain brackets. Their focus on industry-leading print volume, accuracy, and reliability makes them a strategic partner for businesses navigating the transition to electric mobility and seeking advanced manufacturing solutions.
What Are EV Powertrain Mounting Brackets Used For? Key Functions and Applications
EV powertrain mounting brackets serve diverse functions, tailored to the specific component they support and their location within the vehicle architecture. Understanding these applications highlights the versatility required from both the design and the manufacturing process. Key applications within the EV ecosystem include:
- Elektromotorsteunen: These brackets secure the electric motor(s) to the chassis or subframe. They must handle significant torque reaction forces during acceleration and regenerative braking, manage motor vibrations to prevent transfer into the cabin, and withstand dynamic loads from road imperfections. Designs often need to be compact yet robust, integrating features for alignment and assembly. Metal AM allows for topology-optimized designs that place material precisely where needed to handle stress paths, drastically reducing weight compared to traditional cast or fabricated mounts.
- Battery Pack Brackets and Supports: Supporting the heavy battery pack requires numerous brackets and structural members. These components are critical for crash safety, ensuring the battery remains secure during impacts. They also contribute to the overall torsional rigidity of the chassis. Brackets might secure the battery tray to the vehicle body, support individual modules within the pack, or mount associated cooling system components. AM enables complex shapes that conform to the battery pack’s form factor and integrate mounting points for sensors or wiring harnesses, potentially consolidating multiple parts into one.
- Power Electronics Housing and Mounts: Inverters, converters (DC-DC), and on-board chargers (OBCs) need secure mounting. These brackets often need to accommodate complex shapes and provide clearance for high-voltage cabling and cooling lines. In some cases, the bracket itself can be designed with integrated cooling channels using AM, improving thermal management efficiency – a critical factor for power electronics performance and lifespan. The design freedom of AM is particularly beneficial here, allowing for optimized airflow or liquid cooling integration directly into the mounting structure.
- Gearbox and Differential Mounts: In EVs with reduction gearboxes or differentials, mounting brackets perform functions similar to motor mounts, managing torque, vibration, and loads. They ensure precise alignment between the motor and the drivetrain components. AM can produce stiff, lightweight brackets tailored to the specific gearbox design and vehicle packaging constraints.
- Ancillary Component Brackets: Various other powertrain-related components, such as pumps for cooling systems, high-voltage junction boxes, or charging port assemblies, also require dedicated brackets. While potentially less structurally demanding than motor or battery mounts, using AM for these parts can still offer benefits in terms of weight reduction, part consolidation, and rapid design iteration, especially during vehicle development phases.
Industry Relevance:
The primary industry for these components is overwhelmingly Automobiel, specifically within the Electric Vehicle (EV) segment. This includes:
- Passenger Cars (OEMs and Startups)
- Electric Commercial Vehicles (Vans, Trucks, Buses)
- Electric Performance Vehicles and Motorsport
- Electric Off-Highway Vehicles (Construction, Agriculture)
- Specialty Electric Vehicles (e.g., autonomous shuttles)
Key Functional Requirements Addressed by AM:
- Structural Integrity & Load Bearing: AM with high-strength aluminum alloys like A7075 or optimized AlSi10Mg provides strength comparable or superior to traditional materials.
- Vibration Damping: Complex geometries and lattice structures enabled by AM can be designed to actively damp vibrations.
- Thermal Management Integration: Conformal cooling channels can be built directly into brackets for power electronics or motors.
- Deelconsolidatie: AM allows designers to combine multiple traditionally separate parts (e.g., a bracket, a heat sink, and a mounting plate) into a single, complex component, reducing assembly time, weight, and potential points of failure. This is a significant advantage for automotive bracket suppliers looking to offer value-added solutions.
- Complex Geometries & Packaging: AM excels at producing organic shapes that fit into tight spaces, routing around other components – essential in modern EVs.
By leveraging metal 3D printing, manufacturers and suppliers can produce EV powertrain brackets that are not just functional but highly optimized for the unique demands of electric mobility.
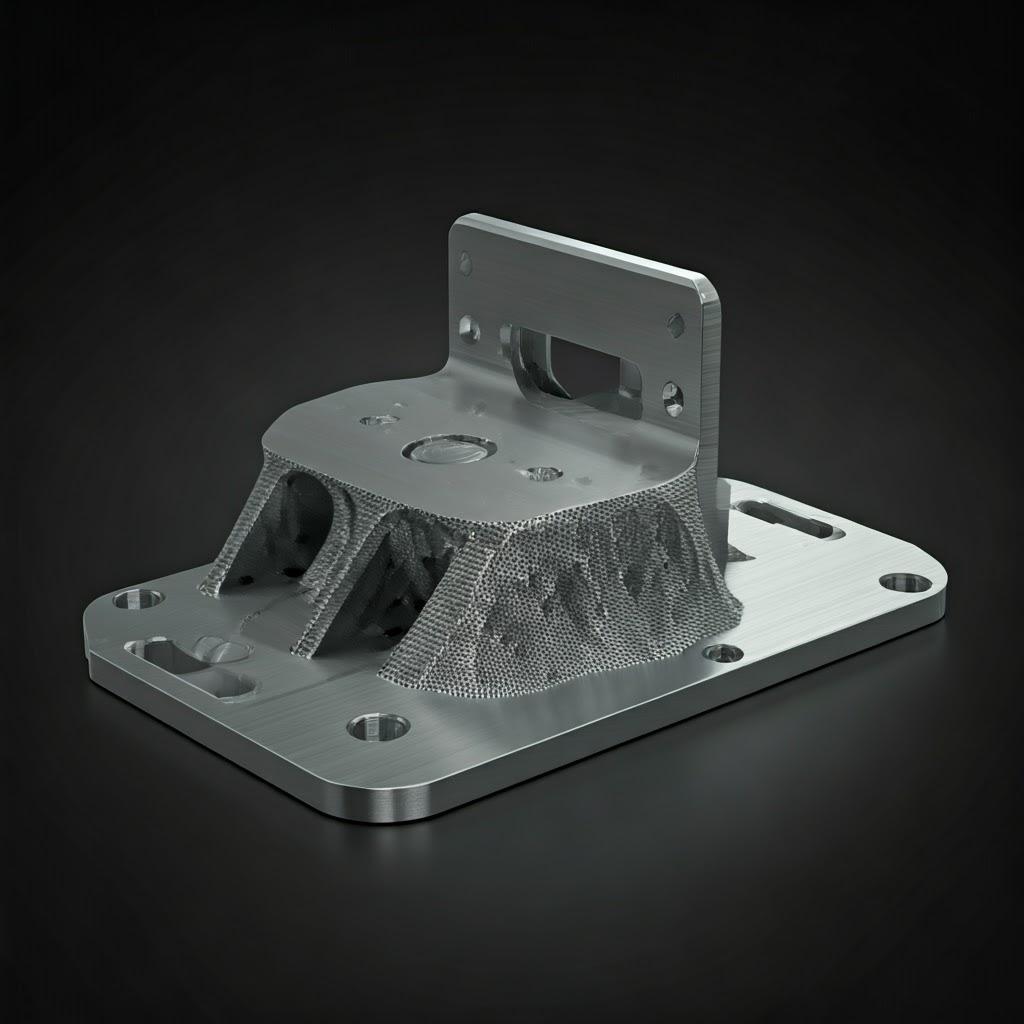
Why Use Metal 3D Printing for EV Powertrain Brackets? Advantages Over Traditional Manufacturing
While traditional manufacturing methods like casting (die casting, sand casting) and CNC machining from billet have long been the standard for producing automotive brackets, metal additive manufacturing offers compelling advantages, particularly for the challenges and opportunities presented by electric vehicles. For engineers aiming for optimal performance and procurement managers focused on total cost of ownership and supply chain agility, understanding these benefits is key.
Here’s a breakdown of why Metaal 3D printen is a transformative technology for EV powertrain brackets:
- Unmatched Design Freedom & Complexity:
- Traditional: Casting requires draft angles, uniform wall thicknesses, and avoids undercuts, limiting geometric complexity. Machining is subtractive, making complex internal features difficult or impossible and potentially wasteful.
- Metal AM: Builds parts layer-by-layer, enabling highly complex, organic shapes, internal channels (e.g., for cooling), thin walls, and intricate lattice structures. This allows for topologie optimalisatie, where software algorithms remove material from low-stress areas, resulting in parts that are perfectly tailored to their load paths. This capability is ideal for creating strong yet ultra-lightweight brackets.
- Aanzienlijk potentieel voor lichtgewicht:
- Traditional: Weight reduction often involves using lighter materials (like aluminum instead of steel) or complex, multi-stage machining, which can be costly. Casting designs are often bulkier than necessary due to process limitations.
- Metal AM: Topology optimization and the ability to create internal lattice structures allow for dramatic weight reductions (often 20-60% or more) compared to traditionally manufactured counterparts, without compromising strength or stiffness. This directly translates to increased EV range and improved vehicle dynamics.
- Rapid Prototyping and Accelerated Iteration:
- Traditional: Creating prototypes via casting requires expensive and time-consuming tooling (molds or patterns). Machining prototypes can be faster but still takes time for programming and setup. Design changes necessitate new tooling or reprogramming.
- Metal AM: Prototypes can be printed directly from CAD data in days, without tooling. This allows engineers to quickly test multiple design iterations, validate performance, and shorten the overall vehicle development cycle – crucial in the fast-evolving EV market. Changes are easily implemented by modifying the CAD file.
- Deelconsolidatie:
- Traditional: Complex assemblies often require multiple individual brackets, fasteners, and joining processes.
- Metal AM: The design freedom allows engineers to consolidate multiple components into a single, integrated 3D printed part. For example, a mounting bracket could incorporate features for cable management, sensor mounting, or fluid routing, reducing part count, assembly time, weight, and potential failure points. This offers significant advantages for B2B manufacturing solutions focused on streamlining production.
- Materiaalefficiëntie en minder afval:
- Traditional: Machining is inherently wasteful, often removing significant amounts of material from a solid block. Casting produces waste through sprues, runners, and risers.
- Metal AM: It’s an additive process, using only the material necessary to build the part and its supports. While some support material is used and waste powder exists, it’s generally much more material-efficient than subtractive methods, especially for complex parts. Unused powder can often be recycled and reused, further improving sustainability.
- On-Demand Manufacturing and Low-Volume Production:
- Traditional: Casting is typically cost-effective only at high volumes due to tooling costs. Machining can be viable for low volumes but can be slow and expensive for complex parts.
- Metal AM: Eliminates tooling costs, making it economically viable for low-to-medium volume production runs, customization, spare parts, or niche vehicle applications. This supports agile manufacturing strategies and distributed production models favored by modern B2B supply chains.
- Tool-Less Production:
- Traditional: Requires significant investment in molds, dies, jigs, and fixtures.
- Metal AM: Requires only the 3D printer and digital design files, reducing capital expenditure on tooling and storage space.
Comparison Table: Metal AM vs. Traditional Methods for EV Brackets
Functie | Metal Additive Manufacturing (L-PBF) | Traditionele gieterij | Traditionele CNC-bewerking |
---|---|---|---|
Complex ontwerp | Very High (Internal channels, lattices) | Moderate (Draft angles, uniform walls) | High (Limited by tool access) |
Lichtgewicht | Excellent (Topology optimization) | Good (Material choice) | Moderate (Subtractive limits) |
Prototyping Speed | Zeer snel (dagen) | Slow (Weeks/Months – tooling) | Moderate (Days/Weeks) |
Kosten gereedschap | Geen | Hoog | Low (Fixturing) / None |
Deel Consolidatie | Uitstekend | Beperkt | Beperkt |
Materiaal Afval | Low (Additive, powder recycling) | Moderate (Sprues, runners) | High (Subtractive) |
Ideaal volume | Prototypes, Low-to-Medium | High Volume | Prototypes, Low-to-Medium |
Lead Time (Production) | Gematigd | Long (Tooling) -> Fast (Per Part) | Gematigd |
Cost (Low Volume) | Competitief | Heel hoog | Hoog |
Cost (High Volume) | Hoger | Laagste | Moderate-to-High |
Exporteren naar Sheets
While metal AM may have a higher cost per part in very high-volume scenarios compared to established casting methods, its advantages in design optimization, speed-to-market for new designs, and ability to produce complex, lightweight structures make it an increasingly strategic choice for demanding EV powertrain bracket applications. Partnering with a knowledgeable service provider like Met3dp ensures access to the right technology and expertise to capitalize on these benefits.
Recommended Materials for 3D Printed EV Brackets: AlSi10Mg & A7075 Deep Dive
Selecting the right material is fundamental to the success of any 3D printed component, especially for structurally critical parts like EV powertrain brackets. The choice depends heavily on the specific application’s requirements, including strength, stiffness, weight, operating temperature, durability, and cost. For aluminum brackets produced via Laser Powder Bed Fusion (L-PBF), two alloys stand out: AlSi10Mg and high-strength 7000-series alloys like A7075 (often referred to as AA7075).
Met3dp, leveraging its expertise and geavanceerd poederproductiesysteem utilizing gas atomization and PREP technologies, ensures the availability of high-quality, spherical metal powders crucial for reliable additive manufacturing. Their portfolio includes a range of alloys suitable for demanding industrial applications. Let’s examine the recommended aluminum powders for EV brackets:
1. AlSi10Mg:
- Beschrijving: AlSi10Mg is one of the most widely used aluminum alloys in additive manufacturing. It’s essentially a casting alloy composition adapted for L-PBF processes. It contains approximately 9-11% Silicon (Si) and 0.2-0.45% Magnesium (Mg).
- Belangrijkste eigenschappen:
- Goede verhouding sterkte/gewicht: Offers respectable mechanical properties suitable for many structural applications.
- Uitstekend printbaar: Relatively easy to process using L-PBF with well-established parameters, leading to dense, reliable parts.
- Good Thermal Properties: Suitable for applications requiring moderate heat dissipation.
- Goede corrosiebestendigheid: Performs well in typical automotive environments.
- Lasbaarheid: Can be welded if necessary, although AM often aims to eliminate such secondary processes through part consolidation.
- Warmtebehandelbaar: Mechanical properties can be significantly improved through heat treatments like T6 (solution heat treatment followed by artificial aging), boosting yield strength and tensile strength.
- Why it Matters for EV Brackets:
- Veelzijdigheid: Suitable for a wide range of brackets, from moderately loaded structural components to housings and supports where extreme strength isn’t the primary driver.
- Kosteneffectiviteit: Generally more cost-effective to print than higher-strength alloys due to established process parameters and lower raw material cost.
- Prototypen: Excellent choice for functional prototypes due to its good balance of properties and printability, allowing for rapid design validation.
- Established Performance: Well-understood behavior and extensive data available on its performance in AM.
2. A7075 (AA7075):
- Beschrijving: A7075 is a high-performance, zinc-alloyed aluminum known for its exceptional strength, often comparable to some steels but at significantly lower density. It’s traditionally used in aerospace and high-stress structural applications. Adapting it for L-PBF has been more challenging but offers significant performance gains.
- Belangrijkste eigenschappen:
- Zeer hoge sterkte: Possesses significantly higher tensile and yield strength than AlSi10Mg, especially after appropriate heat treatment (e.g., T6 or T73).
- Uitstekende verhouding sterkte/gewicht: Ideal for applications where minimizing weight while maximizing strength is critical.
- Goede vermoeiingssterkte: Performs well under cyclic loading conditions.
- Lower Corrosion Resistance (compared to AlSi10Mg): May require surface treatments (like anodizing or painting) for protection in harsh environments.
- Challenging Printability: More susceptible to issues like cracking and porosity during L-PBF compared to AlSi10Mg. Requires tightly controlled process parameters, specific machine capabilities (like platform heating), and potentially specialized powder compositions or post-processing like Hot Isostatic Pressing (HIP).
- Why it Matters for EV Brackets:
- High-Load Applications: The primary choice for highly stressed brackets, such as main motor mounts or critical suspension interface points, where the strength of AlSi10Mg may be insufficient.
- Ultimate Lightweighting: Enables the design of components with minimal material usage due to its superior mechanical properties.
- Performance Edge: Suitable for performance EVs, motorsport applications, or situations demanding the highest possible structural efficiency.
- Vereist expertise: Successfully printing A7075 requires a service provider with proven experience and process control for this specific alloy, highlighting the importance of partnering with specialists like Met3dp who focus on hoogwaardige metaalpoeders and advanced AM processes.
Material Property Comparison (Typical Values after Heat Treatment):
Eigendom | AlSi10Mg (T6-voorwaarde) | A7075 (T6 Condition – AM*) | Eenheid | Opmerkingen |
---|---|---|---|---|
Dikte | ~2.67 | ~2.81 | g/cm³ | A7075 is slightly denser. |
Yield Strength (Rp0.2) | 230 – 300 | 450 – 520 | MPa | A7075 significantly stronger. |
Tensile Strength (Rm) | 330 – 430 | 500 – 570 | MPa | A7075 significantly stronger. |
Elongation at Break (A) | 6 – 10 | 5 – 10 | % | Similar ductility ranges achievable. |
Hardheid | ~100 – 120 | ~150 – 170 | HV / HB | A7075 is moeilijker. |
Bedrukbaarheid | Uitstekend | Uitdagend | – | Requires specialized process control. |
Corrosieweerstand | Goed | Gematigd | – | May need protection for A7075. |
Exporteren naar Sheets
*Note: Properties for AM A7075 can vary significantly based on powder quality, print parameters, build orientation, and heat treatment specifics. Achieving optimal properties requires expertise.
Choosing Between AlSi10Mg and A7075:
- For most standard EV brackets, functional prototypes, and cost-sensitive applications: AlSi10Mg is often the preferred choice due to its excellent balance of properties, printability, and cost.
- For highly loaded components, safety-critical parts, or applications demanding maximum lightweighting: A7075 offers superior performance but requires careful consideration of its processing challenges and potential need for surface protection. The higher performance comes at a higher manufacturing complexity and cost.
Consulting with an experienced metal AM service provider like Met3dp is crucial. They can help evaluate the specific requirements of your EV powertrain bracket, recommend the most suitable material, and leverage their expertise in process parameter optimization and powder quality control to ensure the production of high-performance, reliable components tailored to your B2B automotive needs.
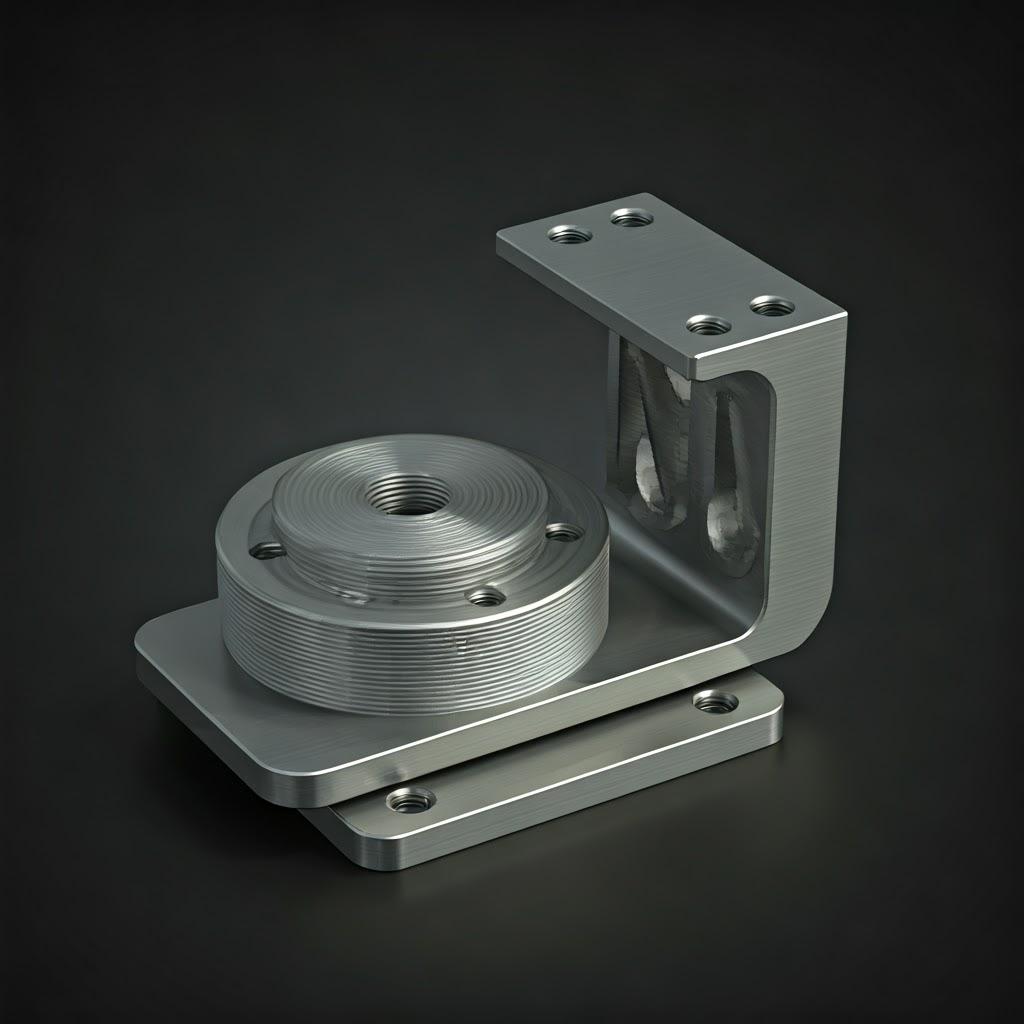
Design Considerations for Additive Manufacturing (DfAM) of EV Brackets
Simply replicating a design intended for casting or machining rarely unlocks the full potential of metal additive manufacturing. To truly leverage the benefits of AM for EV powertrain brackets – particularly lightweighting, performance enhancement, and part consolidation – engineers must embrace Ontwerp voor additieve productie (DfAM) principles. DfAM involves rethinking the design approach to suit the layer-by-layer building process and capitalize on its unique capabilities. For B2B suppliers and automotive OEMs, mastering DfAM is crucial for developing next-generation, optimized EV components.
Key DfAM considerations for EV powertrain brackets include:
- Topologieoptimalisatie:
- Concept: Using specialized software (e.g., Altair Inspire, Ansys Discovery, nTopology) to computationally determine the most efficient material distribution within a defined design space, based on applied loads, constraints, and performance targets (e.g., maximize stiffness, minimize mass).
- Toepassing: Ideal for structural brackets like motor mounts or battery supports. The software generates organic, often bone-like structures that precisely follow stress paths, removing unnecessary material while maintaining or even increasing strength and stiffness. This is the primary driver for significant weight reduction in AM parts.
- Voordeel: Achieves maximum lightweighting potential, leading to improved EV range and performance.
- Lattice Structures and Infill:
- Concept: Incorporating internal lattice structures (repeating geometric unit cells like cubic, octet-truss, gyroid) instead of solid material. These can be tailored for specific properties like high stiffness-to-weight ratio, energy absorption (for crashworthiness), or vibration damping. Variable density lattices can further optimize material usage.
- Toepassing: Can be used within bracket bodies or specific sections to reduce mass while maintaining structural support or adding functional properties.
- Voordeel: Further weight reduction beyond surface topology optimization, potential for enhanced vibration damping or crash performance.
- Orientation and Support Structures:
- Concept: The orientation of the part on the build platform significantly impacts print time, surface finish, dimensional accuracy, required support structures, and potentially mechanical properties (due to anisotropy). Metal L-PBF processes require support structures for overhanging features (typically beyond 45 degrees from the horizontal) to prevent collapse and anchor the part to the build plate, managing thermal stresses.
- Toepassing: Designers must consider orientation early. Aim to minimize steep overhangs and the volume of support material needed. Design features like chamfers or fillets on downward-facing surfaces can turn steep overhangs into self-supporting angles.
- Voordeel: Reduces print time, material consumption (supports are waste), and post-processing effort (support removal). Improves surface finish on critical downward-facing surfaces.
- Minimum Feature Size and Wall Thickness:
- Concept: AM processes have limitations on the smallest features (e.g., pins, holes) and thinnest walls they can reliably produce. This depends on the machine resolution, laser spot size, and powder characteristics. Typical minimum wall thicknesses for L-PBF are often around 0.4-0.8 mm.
- Toepassing: Ensure walls and features are designed above the process minimums to guarantee successful printing and structural integrity.
- Voordeel: Prevents print failures, ensures part robustness.
- Hole Design:
- Concept: Small horizontal holes often require internal supports, which can be very difficult or impossible to remove. Vertical holes generally print well. Teardrop shapes (elongated vertically) can often make horizontal holes self-supporting.
- Toepassing: Orient critical holes vertically whenever possible. If horizontal holes are necessary, consider designing them as self-supporting shapes or plan for post-machining. For tapped holes, it’s often best to print a pilot hole and machine the threads afterward for accuracy and strength.
- Voordeel: Avoids trapped support material, improves accuracy of critical bores.
- Part Consolidation Strategy:
- Concept: Actively look for opportunities to combine multiple adjacent parts (e.g., bracket + heat sink + fastener boss) into a single, complex AM component.
- Toepassing: Analyze assemblies around the powertrain bracket. Can mounting points for wiring harnesses, sensors, or cooling lines be integrated? Can separate reinforcing elements be merged into the main bracket design?
- Voordeel: Reduces part count, weight, assembly time, inventory management, and potential points of failure (like bolted joints). Offers significant value proposition for B2B suppliers.
- Stress Concentrations:
- Concept: Sharp internal corners act as stress risers, potentially leading to fatigue failure under load.
- Toepassing: Apply generous fillets and radii to internal corners and transitions, similar to good design practice for traditional methods, but even more crucial when optimizing aggressively for weight.
- Voordeel: Improves fatigue life and overall durability of the bracket.
- Designing for Post-Processing:
- Concept: Consider how post-processing steps like support removal, machining, and surface finishing will be performed.
- Toepassing: Ensure support structures are accessible for removal tools. Add extra material (machining allowance) on surfaces requiring high precision or specific finishes that will be achieved via CNC machining. Avoid complex internal lattices if powder removal is critical and difficult.
- Voordeel: Streamlines the post-processing workflow, reduces cost and lead time.
Embracing DfAM requires a shift in mindset and often collaboration between design engineers and AM specialists. Service providers like Met3dp, with deep expertise in various afdrukmethoden and materials, can offer invaluable B2B design services and consultation to help clients optimize their EV bracket designs for additive manufacturing, ensuring they fully realize the technology’s benefits in terms of performance, weight, and cost-efficiency.
Tolerance, Surface Finish, and Dimensional Accuracy in 3D Printed EV Brackets
For functional automotive components like powertrain brackets, achieving the required dimensional accuracy, tolerances, and surface finish is critical for proper fit, assembly, and performance. Procurement managers and engineers need realistic expectations about what metal additive manufacturing, specifically L-PBF, can achieve “as-built” (directly after printing and stress relief) and what typically requires secondary post-processing. Understanding these aspects is vital for effective B2B sourcing and quality control.
1. Dimensional Accuracy:
- Definitie: How closely the final printed part conforms to the dimensions specified in the original 3D CAD model.
- Typical L-PBF Values: As-built accuracy is generally good but not as high as precision machining. Typical values often fall within the range of ±0.1 mm to ±0.2 mm for smaller features, or ±0.1% to ±0.2% of the overall dimension for larger parts.
- Beïnvloedende factoren:
- Machinekalibratie: Regular calibration of the printer’s scanners and optics is crucial.
- Materiaaleigenschappen: Thermal expansion and contraction during printing vary by alloy.
- Onderdeelgeometrie en -grootte: Larger parts and complex geometries are more prone to thermal distortion.
- Bouwrichting: Affects thermal gradients and potential shrinkage/warping.
- Ondersteunende strategie: Inadequate supports can allow distortion.
- Thermisch beheer: Platform heating (if available) and consistent process temperatures help.
- Verlichting van stress: Proper heat treatment after printing is essential to relieve internal stresses that can cause distortion upon removal from the build plate.
- Achieving High Accuracy: For critical dimensions, mating surfaces, or interfaces requiring tight tolerances (e.g., bearing bores, precise mounting faces), post-print CNC machining is typically employed. Reputable service providers like Met3dp emphasize process control and machine reliability to maximize as-built accuracy.
2. Tolerances:
- Definitie: The allowable variation in a dimension. Tolerances are specified on engineering drawings (e.g., using ISO standards).
- As-Built Tolerances: Standard achievable tolerances directly from L-PBF are often around ISO 2768-m (medium) or sometimes -f (fine) for certain features, but this is highly dependent on the factors listed above. Achieving tighter tolerances generally requires machining.
- Design Implications: Designers should only specify tight tolerances where functionally necessary. Over-tolerancing increases the likelihood of needing extensive post-machining, driving up costs and lead times. Clearly distinguish critical features requiring machining from less critical surfaces acceptable in their as-built state.
3. Surface Finish (Roughness):
- Definitie: The measure of the texture of a surface, typically quantified by the arithmetic average roughness (Ra).
- As-Built L-PBF Values: The as-built surface finish of L-PBF parts is inherently rougher than machined surfaces due to the layer-by-layer fusion of powder particles. Typical Ra values range from 6 µm to 20 µm (micrometers), sometimes higher on downward-facing or heavily supported surfaces.
- Beïnvloedende factoren:
- Laagdikte: Thinner layers generally result in a smoother finish but increase print time.
- Poeder Deeltjesgrootte: Finer powders can lead to smoother surfaces.
- Laser Parameters: Melting conditions affect surface texture.
- Deeloriëntatie: Surfaces built parallel to the build direction (vertical walls) tend to be smoother than angled or horizontal surfaces (“stair-stepping” effect). Downward-facing surfaces requiring supports are often the roughest after support removal.
- Verbetering van de oppervlakteafwerking: If a smoother finish is required for functional reasons (e.g., sealing surfaces, reducing friction, aesthetics), various post-processing methods are used:
- Stralen (parelen/zandstralen): Common method to achieve a uniform matte finish (Ra typically 3-10 µm).
- Tuimelende/vibrerende afwerking: Uses media to smooth surfaces and edges, effective for batches of smaller parts.
- Polijsten: Manual or automated polishing for mirror-like finishes (Ra < 0.8 µm).
- Bewerking: Provides the best control over surface finish for specific features.
- Anodizing/Coating: Can provide a smoother feel and added corrosion protection, though may not significantly reduce measured Ra depending on the initial surface.
Quality Control in Automotive AM:
Achieving consistent tolerance, accuracy, and finish requires rigorous quality control throughout the AM workflow. This includes:
- Powder Quality Management: Ensuring consistent powder characteristics.
- Process Monitoring: In-situ monitoring of the melt pool and layer deposition.
- Post-Print Metrology: Using CMM (Coordinate Measuring Machines), 3D scanners, or traditional gauges to verify dimensions.
- Material Testing: Validating mechanical properties meet specifications.
B2B procurement for automotive components demands suppliers with robust quality management systems (e.g., ISO 9001, potentially IATF 16949 awareness or compliance for production parts) and the metrology capabilities to verify conformance. Companies like Met3dp, focused on high-accuracy, reliable printing systems and comprehensive solutions, understand the stringent requirements of the automotive industry.
Summary Table: As-Built vs. Post-Processed Capabilities
Parameter | As-Built L-PBF (Typical) | Achievable with Post-Processing | Opmerkingen |
---|---|---|---|
Dimensionale nauwkeurigheid | ±0,1 tot ±0,2 mm / ±0,1-0,2% | Down to ±0.01 mm (Machining) | Depends heavily on feature size and process control. |
Tolerance Class | ISO 2768-m / -f (approx.) | ISO 2768-f / -c (Machining) | Specify tight tolerances only where needed. |
Oppervlakteafwerking (Ra) | 6 – 20 µm+ | < 0.8 µm (Polishing/Machining) | Varies significantly with orientation and supports. |
3 – 10 µm (Blasting) | Blasting provides uniform matte finish. |
Exporteren naar Sheets
Understanding these capabilities allows engineers and procurement managers to make informed decisions about design specifications, post-processing needs, and supplier selection for 3D printed EV powertrain brackets.
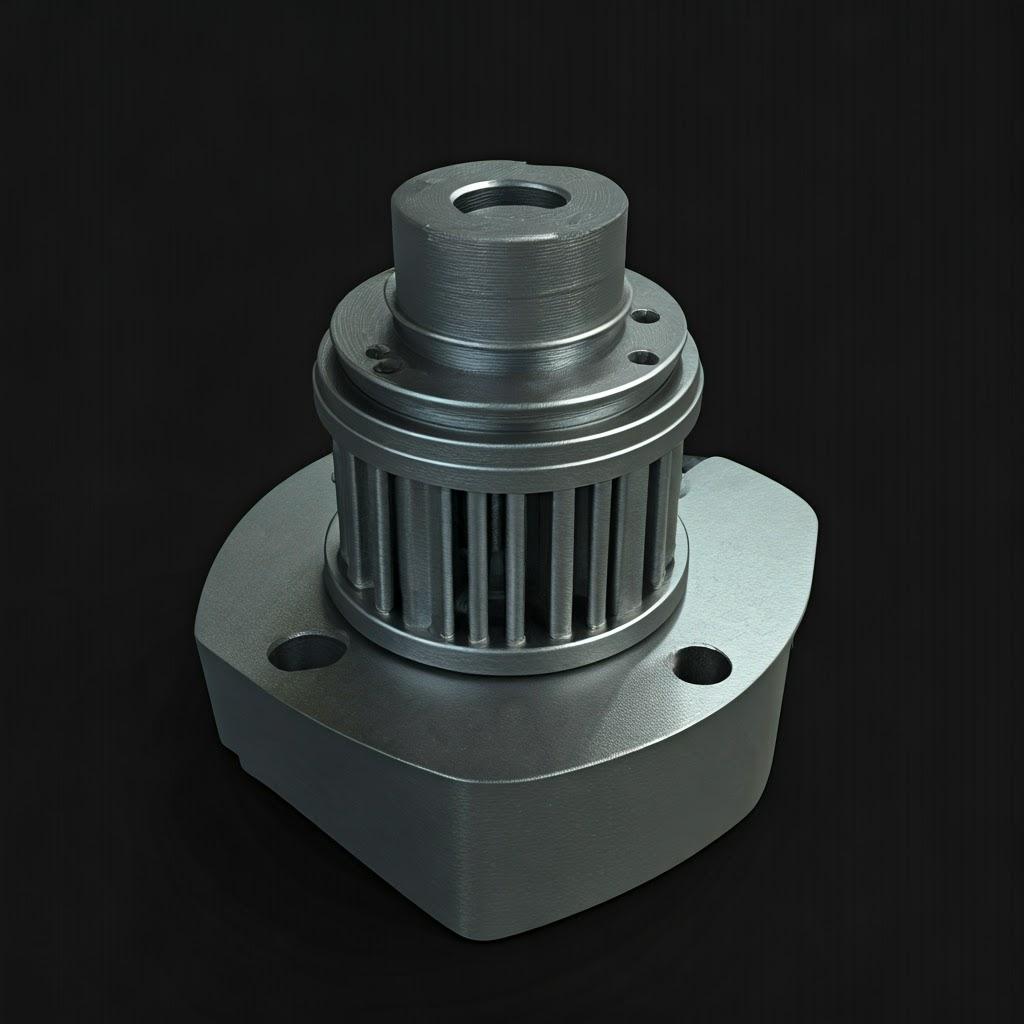
Post-Processing Requirements for Metal 3D Printed EV Brackets: From Print to Part
A common misconception about metal 3D printing is that parts come out of the machine ready to use. In reality, nearly all metal AM parts, especially functional components like EV powertrain brackets, require several crucial post-processing steps to achieve the desired final properties, dimensions, and surface finish. These steps add to the overall lead time and cost but are essential for ensuring the part meets engineering specifications. B2B post-processing services are an integral part of the AM supply chain.
Common post-processing steps for L-PBF printed aluminum EV brackets (AlSi10Mg, A7075) include:
- Powder Removal:
- Proces: After the build is complete and cooled, the build chamber is unpacked, and loose, unfused powder surrounding the parts must be meticulously removed. This is often done manually with brushes and vacuum systems or using automated de-powdering stations. Internal channels or complex lattice structures can make powder removal challenging.
- Belangrijk: Ensures no loose powder remains, which could interfere with subsequent steps or the final application. Allows for powder recovery and recycling.
- Stressverlichtende warmtebehandeling:
- Proces: Parts are typically left attached to the build plate and undergo a thermal cycle in a furnace. This involves heating the parts to a specific temperature (below the melting point, e.g., ~300°C for AlSi10Mg) for a set duration, followed by controlled cooling.
- Belangrijk: The rapid heating and cooling during the L-PBF process induce significant internal stresses within the material. Stress relief is crucial to reduce this residual stress, preventing distortion or cracking when the parts are later removed from the build plate or during machining. It also stabilizes the microstructure.
- Verwijdering van bouwplaat:
- Proces: Once stress-relieved, parts are separated from the metal build plate. This is commonly done using wire EDM (Electrical Discharge Machining) or a band saw.
- Belangrijk: Frees the individual parts for further processing.
- Draagstructuur verwijderen:
- Proces: The support structures required during printing must be removed. This can be done manually (using pliers, cutters, grinders), via CNC machining, or sometimes using wire EDM for delicate or hard-to-reach supports. The ease of removal depends heavily on how well supports were designed (DfAM).
- Belangrijk: Supports are non-functional and must be removed. This step significantly impacts the final surface finish in supported areas.
- Solution Heat Treatment and Aging (e.g., T6 Temper for Al alloys):
- Proces: For alloys like AlSi10Mg and A7075, a full heat treatment cycle is often required to achieve the desired final mechanical properties (strength, hardness, ductility). This typically involves:
- Oplossing Behandeling: Heating to a higher temperature (e.g., ~500-540°C for Al alloys) to dissolve alloying elements into the aluminum matrix.
- Afschrikken: Rapid cooling (often in water) to lock the elements in solution.
- Artificial Aging: Re-heating to a lower temperature (e.g., 150-190°C) for an extended period to precipitate fine particles that strengthen the alloy.
- Belangrijk: Absolutely critical for developing the full strength potential of heat-treatable aluminum alloys. Without proper heat treatment, the bracket will not meet its design strength requirements. Specific cycles (T6, T73, etc.) are chosen based on the desired balance of strength, toughness, and stress corrosion resistance.
- Proces: For alloys like AlSi10Mg and A7075, a full heat treatment cycle is often required to achieve the desired final mechanical properties (strength, hardness, ductility). This typically involves:
- Afwerking oppervlak:
- Proces: As discussed previously, various techniques are used to improve the as-built surface finish based on requirements:
- Abrasive Blasting (Bead, Sand, etc.): Standard step for a uniform, clean, matte finish. Removes minor imperfections.
- Tuimelende/vibrerende afwerking: For deburring edges and smoother finishes on batches.
- Polijsten: For achieving very smooth, reflective surfaces.
- Belangrijk: Improves aesthetics, can enhance fatigue performance by removing surface defects, prepares surfaces for coating, or meets specific functional requirements (e.g., sealing).
- Proces: As discussed previously, various techniques are used to improve the as-built surface finish based on requirements:
- CNC-bewerking:
- Proces: Using milling machines, lathes, or grinders to achieve tight tolerances on specific features, create precise mating surfaces, drill and tap holes, or improve surface finish on critical areas.
- Belangrijk: Essential when the as-built accuracy or surface finish of AM is insufficient for functional requirements. Often required for interfaces with other powertrain components.
- Inspection and Quality Assurance (QA):
- Proces: Final dimensional inspection (CMM, scanning), surface roughness measurement, material testing (tensile tests on representative samples), NDT (Non-Destructive Testing) like CT scanning (Computed Tomography) to check for internal porosity or defects, and final visual inspection.
- Belangrijk: Verifies that the finished bracket meets all design specifications and quality standards before shipment. Crucial for safety-critical automotive components.
Workflow Considerations:
The specific sequence and necessity of these steps depend on the bracket’s design, material, and application requirements. Partnering with a full-service provider like Met3dp, offering both advanced printing and comprehensive post-processing capabilities (either in-house or through qualified partners), simplifies the supply chain for B2B customers. They can manage the entire workflow from CAD file to finished, inspected part, ensuring quality and consistency throughout. Procurement managers should clarify which post-processing steps are included in quotations and ensure the supplier has the necessary expertise and equipment.
Common Challenges in 3D Printing EV Brackets and How to Mitigate Them
While metal additive manufacturing offers significant advantages, producing high-quality, reliable EV powertrain brackets via L-PBF is not without its challenges. Understanding these potential issues and how experienced service providers mitigate them is crucial for successful implementation and managing expectations within the B2B supply chain.
1. Warping and Distortion:
- Uitdaging: The intense, localized heat of the laser followed by rapid cooling creates steep thermal gradients, inducing residual stresses. These stresses can cause parts (especially large, flat, or thin-walled ones) to warp during the build or distort after removal from the build plate.
- Mitigation:
- Geoptimaliseerde oriëntatie: Selecting a build orientation that minimizes large flat surfaces parallel to the build plate and manages heat buildup.
- Robust Support Strategy: Using well-designed supports to anchor the part firmly and counteract thermal stresses.
- Optimalisatie van procesparameters: Fine-tuning laser power, speed, and scanning strategy to minimize stress induction (requires material-specific expertise).
- Platform Heating: Using printers with heated build platforms can reduce thermal gradients.
- Effective Stress Relief: Performing a proper stress relief heat treatment cycle voor removing the part from the build plate is critical.
2. Poreusheid:
- Uitdaging: Small voids or pores can form within the printed material due to trapped gas (from powder or atmosphere) or incomplete fusion between layers (lack-of-fusion porosity). Porosity can significantly degrade mechanical properties, particularly fatigue strength.
- Mitigation:
- Hoogwaardig poeder: Using spherical powder with low internal porosity and controlled particle size distribution, like those produced using Met3dp’s advanced atomization techniques. Proper powder handling and storage are also essential to prevent moisture absorption.
- Optimized Print Parameters: Developing and validating robust parameter sets (laser power, speed, layer thickness, hatch spacing) specific to the alloy and machine to ensure full melting and fusion.
- Inert Atmosphere Control: Maintaining a high-purity inert gas environment (Argon or Nitrogen) in the build chamber to minimize oxidation and gas pickup.
- Heet isostatisch persen (HIP): A post-processing step involving high temperature and high-pressure gas to close internal pores. Often used for critical applications or challenging materials like A7075 to achieve near-full density and improve fatigue properties.
3. Ondersteuning bij verwijderingsproblemen:
- Uitdaging: Supports can be difficult, time-consuming, and costly to remove, especially internal supports or those on complex geometries. Poor removal can damage the part or leave undesirable surface artifacts.
- Mitigation:
- DfAM for Support Minimization: Designing parts with self-supporting angles and features where possible. Orienting parts to reduce the need for supports on critical surfaces.
- Geoptimaliseerd steunontwerp: Using support structures (e.g., block, cone, tree supports with appropriate tooth geometry) that provide adequate anchoring but are designed for easier detachment (e.g., using smaller contact points, perforations). Software tools offer advanced support generation strategies.
- Toegankelijkheidsplanning: Ensuring supports are physically accessible for manual or automated removal tools.
- Appropriate Removal Techniques: Using the right tools (manual, CNC, EDM) for the specific support type and location.
4. Cracking (Especially with High-Strength Alloys):
- Uitdaging: High-strength aluminum alloys like A7075 are more susceptible to solidification cracking or liquation cracking during the rapid heating/cooling cycles of L-PBF due to their wide freezing range and thermal stresses.
- Mitigation:
- Alloy Modification (Powder Chemistry): Sometimes minor modifications to powder chemistry can improve printability.
- Specialized Parameters: Developing highly specific laser parameters (e.g., pulsed laser strategies, specific scan patterns) tailored to mitigate cracking tendencies.
- Platform Pre-heating: Using significant build platform heating (sometimes several hundred degrees C) reduces thermal gradients and cracking risk.
- Optimized Heat Treatments: Carefully designed stress relief and subsequent heat treatment cycles are critical.
5. Achieving Consistent Mechanical Properties:
- Uitdaging: Mechanical properties (strength, ductility, fatigue life) can be influenced by process variations, build location, orientation (anisotropy), and the effectiveness of post-processing heat treatments. Ensuring consistent properties across batches and parts is vital for automotive applications.
- Mitigation:
- Rigorous Process Control: Implementing strict quality control over powder, machine parameters, and atmosphere.
- Proceskwalificatie: Thoroughly validating the printing and heat treatment process for each specific alloy and application.
- Homogenization Heat Treatments: Specific thermal cycles can help reduce microstructural variations.
- Routine Testing: Regularly testing witness coupons printed alongside parts to verify mechanical properties meet specifications.
- Partnering with Experts: Working with service providers like Met3dp, who possess deep materials science knowledge and process expertise, is key to consistently achieving desired properties for demanding materials. Their focus on industry-leading reliability helps ensure dependable results.
By understanding these challenges and partnering with experienced metal AM providers who employ robust mitigation strategies, automotive companies can confidently adopt additive manufacturing for producing high-performance, reliable EV powertrain brackets, accelerating innovation within their B2B supply chains.
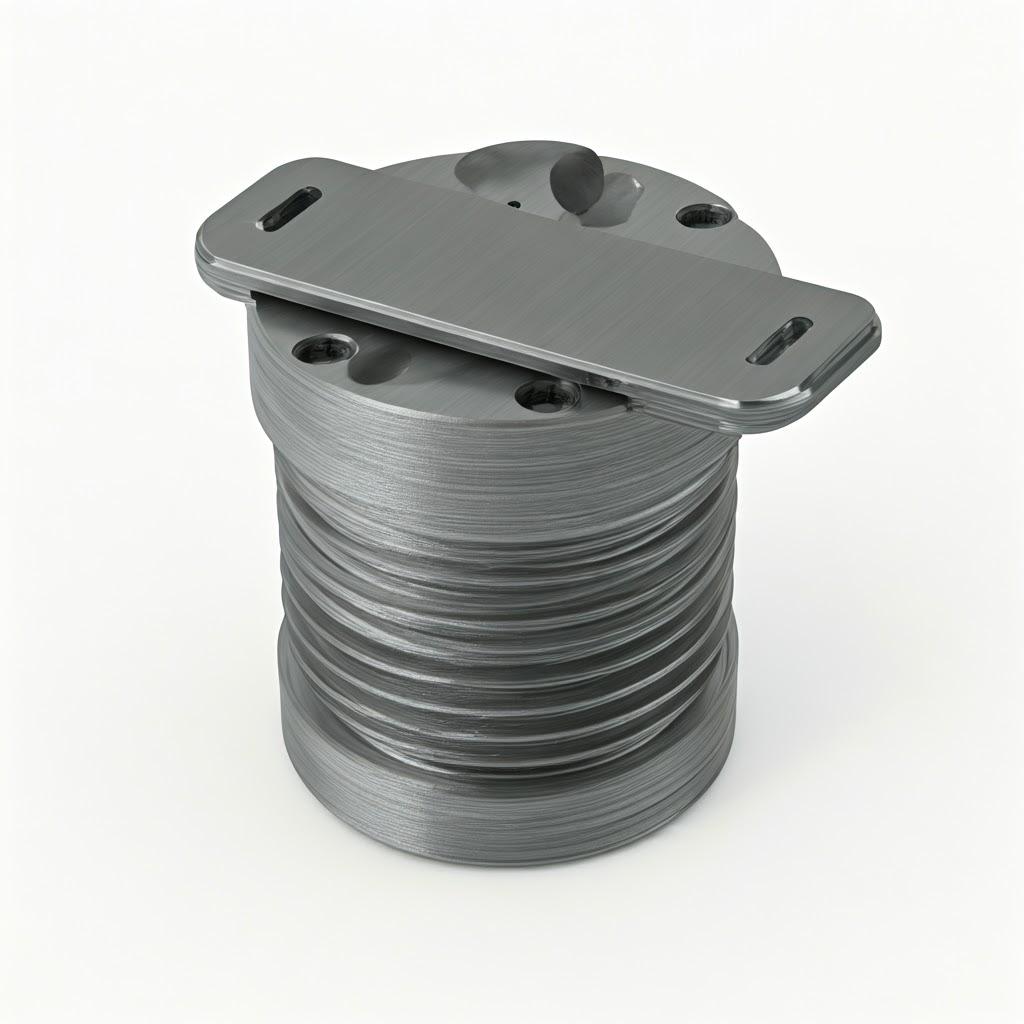
How to Choose the Right Metal 3D Printing Service Provider for EV Components
Selecting the right additive manufacturing partner is as critical as the design and material selection for your EV powertrain brackets. The quality, reliability, cost-effectiveness, and timely delivery of your components depend heavily on the capabilities and expertise of your chosen service provider. For procurement managers and engineering teams involved in B2B sourcing for automotive AM, evaluating potential suppliers requires careful consideration of several key factors.
Here’s a guide on what to look for when selecting a metal 3D printing service provider for demanding EV applications:
- Proven Expertise and Experience:
- Automotive Focus: Does the provider have demonstrable experience working with automotive clients and understanding the industry’s stringent requirements (quality, traceability, performance)? Look for case studies or references specific to automotive or EV components.
- Material Specialization: Do they have deep expertise in printing the specific alloys you need (e.g., AlSi10Mg, A7075)? Successfully printing challenging materials like high-strength aluminum requires specialized knowledge.
- Application Knowledge: Do they understand the functional requirements of powertrain brackets (load bearing, vibration, thermal management)?
- Technology and Equipment:
- Appropriate AM Process: Ensure they utilize suitable L-PBF (SLM/DMLS) machines known for quality and reliability in producing metal parts.
- Machinemogelijkheden: Consider build volume (can they accommodate your part size?), laser power, platform heating (especially important for alloys like A7075), and process monitoring capabilities. Providers like Met3dp emphasize their toonaangevend printvolume, nauwkeurigheid en betrouwbaarheid, which are key indicators of advanced equipment.
- Machine Maintenance & Calibration: Regular maintenance and calibration are essential for consistent results.
- Material Capabilities and Quality:
- Powder Portfolio: Do they offer the specific certified metal powders required? Can they source or handle custom alloys if needed?
- Kwaliteitscontrole poeder: What processes are in place for powder sourcing, testing, handling, storage, and traceability? Consistent powder quality is paramount. Companies like Met3dp, which manufacture their own high-quality metal powders using advanced atomization, often have better control over this critical input.
- Material Certifications: Can they provide material certificates conforming to relevant standards (e.g., ASTM, ISO)?
- Quality Management System (QMS) and Certifications:
- ISO 9001: A fundamental certification indicating a robust QMS.
- AS9100 (Aerospace): While aerospace-specific, this certification often indicates very high levels of process control and traceability, which benefits automotive clients.
- IATF 16949 (Automotive): The gold standard for automotive suppliers. While not all AM providers hold this (especially for prototyping), awareness or compliance with its principles is a significant advantage for production parts.
- Traceerbaarheid: Ensure they have systems for tracking parts and materials throughout the entire production process.
- In-House Post-Processing Capabilities:
- Comprehensive Services: Does the provider offer the necessary post-processing steps in-house (stress relief, heat treatment, support removal, basic surface finishing)? This can streamline the workflow and improve turnaround time.
- Managed Services: If certain steps (e.g., complex CNC machining, specialized coatings, HIP) are outsourced, how well do they manage these external partners and ensure quality?
- Expertise: Do they have metallurgical expertise for heat treatment and appropriate equipment for finishing and machining?
- Engineering and DfAM Support:
- Consultative Approach: Can their engineers provide guidance on Design for Additive Manufacturing (DfAM) to optimize your bracket design for weight, performance, and printability?
- Simulatiemogelijkheden: Do they offer FEA (Finite Element Analysis) or topology optimization services?
- Problemen oplossen: Are they proactive in identifying potential manufacturing issues based on your design?
- Capacity and Lead Time:
- Schaalbaarheid: Can they handle your required volumes, from prototypes to potentially low-volume production?
- Quoted Lead Times: Are their quoted lead times realistic and consistently met? Understand their production scheduling process.
- Responsiveness: How quickly do they respond to inquiries and provide quotes?
- Cost and Transparency:
- Clear Quotations: Is the pricing structure clear, detailing costs for printing, material, supports, and each post-processing step?
- Waardepropositie: Consider the total value, including quality, expertise, reliability, and support, not just the price per part.
- Location and Logistics:
- Verzending: Consider shipping costs and logistics, especially for international B2B suppliers. Ensure they have experience with appropriate packaging for delicate AM parts.
Why Met3dp Stands Out: Met3dp positions itself as a strong contender based on these criteria. As a company specializing in both 3D printing equipment and high-performance metal powders, they possess end-to-end expertise. Their focus on industry-leading accuracy and reliability, advanced powder manufacturing systems (Gas Atomization, PREP), a diverse materials portfolio (including specialty alloys), and decades of collective expertise in metal AM make them a valuable partner for companies seeking comprehensive solutions for demanding applications like EV powertrain brackets. Exploring their capabilities further can reveal how they align with your specific B2B procurement needs.
Choosing the right partner is an investment in the quality and success of your EV project. Thoroughly vetting potential suppliers against these criteria will help ensure you select a provider capable of meeting the demanding requirements of the automotive industry.
Cost Factors and Lead Time Analysis for 3D Printed EV Powertrain Brackets
Understanding the factors that influence the cost and lead time of metal 3D printed components is essential for accurate project planning, budgeting, and managing B2B supply chain expectations. While AM offers unique benefits, it comes with its own set of economic and scheduling drivers compared to traditional manufacturing.
Key Cost Factors:
- Material Type and Consumption:
- Alloy Choice: High-performance alloys like A7075 are typically more expensive per kilogram than standard alloys like AlSi10Mg due to raw material costs and processing complexity. Specialty alloys (Ti-based, superalloys) are significantly more expensive.
- Part Volume & Weight: The actual amount of material used to print the part directly impacts cost. Larger, denser parts cost more.
- Support Structure Volume: Material used for support structures adds to the cost, as it’s essentially waste material that also requires time to print and remove. Efficient DfAM minimizes support needs.
- Part Complexity and Design:
- Geometric Complexity: Highly intricate designs may require more complex support strategies and potentially longer print times, slightly influencing cost. However, AM handles complexity well – the primary driver is volume/time.
- Wall Thickness & Features: Very thin walls or fine features might require slower print speeds or specialized parameters, potentially increasing machine time.
- Build Time (Machine Time):
- Part Height (Z-Height): This is often the most significant driver of print time, as the machine builds layer by layer. Taller parts take longer, regardless of their footprint.
- Part Volume & Density: Larger solid volumes take longer to scan with the laser.
- Number of Parts per Build: Nesting multiple parts efficiently onto a single build plate reduces machine setup time per part and can lower costs (economies of scale).
- Layer Thickness & Parameters: Thinner layers improve finish but increase build time; faster parameters may reduce time but require careful validation.
- Vereisten voor nabewerking:
- Hittebehandeling: Stress relief and full T6 (or similar) heat treatment cycles require furnace time and energy, adding cost.
- Ondersteuning verwijderen: Labor-intensive manual removal or machine time (EDM/CNC) adds cost. Complex/internal supports increase this significantly.
- CNC-bewerking: Machining specific features for tolerance or finish is often one of the more significant post-processing costs, requiring machine time, programming, and setup.
- Afwerking oppervlak: Costs vary widely depending on the method (blasting is relatively low; extensive polishing is high).
- Inspectie: Advanced inspection like CT scanning adds cost but may be necessary for critical parts.
- Quantity and Order Volume:
- Schaalvoordelen: While AM has no tooling costs, some economies of scale exist. Larger batches allow for more efficient build plate utilization, potentially reduced setup time per part, and volume discounts on materials or services. B2B procurement often involves negotiating pricing for recurring orders or larger quantities.
- Arbeid en expertise:
- Skilled labor is required for machine operation, DfAM consultation, post-processing, and quality control. The expertise needed, especially for complex parts or materials, factors into the overall cost.
Lead Time Factors:
- Quoting and Design Review: Initial file preparation, DfAM checks, and quotation generation take time (typically 1-3 days).
- Machine Scheduling: Availability of the appropriate printer. High demand or maintenance can create queues (variable, can be days to weeks).
- Afdruktijd: Determined by part height, volume, and parameters (can range from hours for small parts to several days for large/complex builds).
- Cooling and De-powdering: Time for the build plate to cool before unpacking and subsequent powder removal (hours to a day).
- Nabewerking: This often contributes significantly to the total lead time:
- Stress Relief/Heat Treatment: Furnace cycles take hours to days, including ramp-up and cool-down.
- Support Removal & Basic Finishing: Highly variable depending on complexity (hours to days).
- CNC Machining: Dependent on complexity and machine availability (days).
- External Processes (HIP, Coating): Can add days or weeks depending on vendor scheduling.
- Quality Assurance & Inspection: Dimensional checks, material testing (if required), documentation (hours to days).
- Verzending: Transit time to the customer’s location.
Typical Lead Time Ranges:
- Prototypes (Simple, minimal post-processing): Often 5-10 business days.
- Functional Prototypes (with heat treatment, basic finishing): Typically 10-15 business days.
- Low-Volume Production Parts (requiring machining, full QA): Can range from 3 to 6+ weeks, highly dependent on complexity and batch size.
Getting Accurate Estimates: The best way to determine cost and lead time for a specific EV bracket is to submit a 3D CAD model and detailed requirements (material, tolerances, finish, quantity) to reputable service providers like Met3dp for a formal quotation. Clear communication about critical features and required post-processing is essential for accurate B2B sourcing.
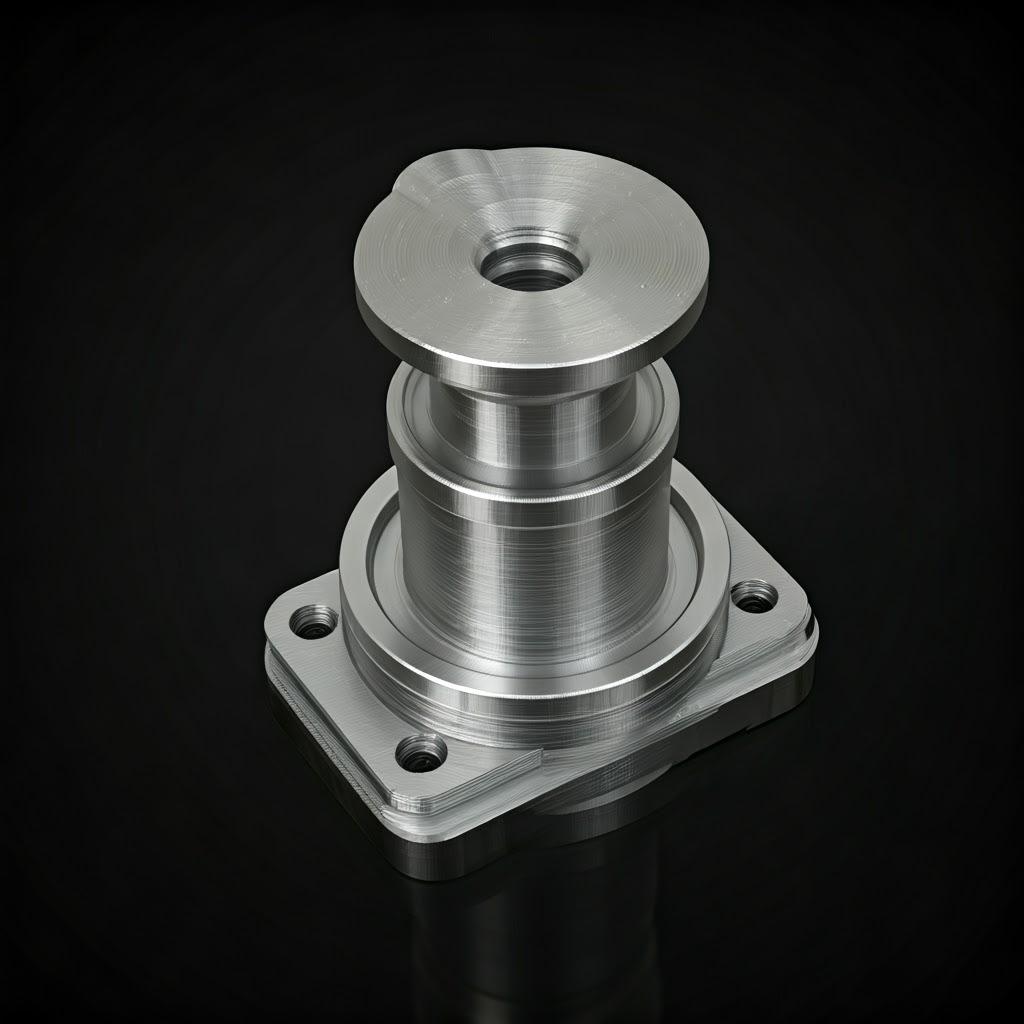
Frequently Asked Questions (FAQ) about 3D Printed EV Brackets
Here are answers to some common questions engineers and procurement managers have about using metal additive manufacturing for EV powertrain brackets:
Q1: Is 3D printed aluminum (like AlSi10Mg or A7075) strong enough for demanding powertrain bracket applications?
A: Absolutely. When processed correctly and subjected to appropriate post-processing heat treatments (like T6 tempering), 3D printed aluminum alloys offer excellent mechanical properties.
- AlSi10Mg (T6): Provides strength comparable to or exceeding typical aluminum casting alloys, making it suitable for many moderately loaded brackets. Its strength-to-weight ratio is very good.
- A7075 (T6/T73): Offers exceptionally high strength, often approaching that of some steels but at roughly one-third the density. This makes it ideal for highly stressed components where maximum strength and minimal weight are critical. The key is proper material selection based on load requirements, validated process parameters, and rigorous quality control, including necessary heat treatments. Additively manufactured brackets, especially those using topology optimization, can often outperform traditionally manufactured counterparts in terms of stiffness-to-weight ratio.
Q2: How does the cost of 3D printed EV brackets compare to traditional casting or CNC machining?
A: The cost comparison depends heavily on part complexity, volume, and design optimization:
- Prototypes & Low Volumes (<50-100 units): Metal AM is often highly cost-competitive or even cheaper than casting (due to high tooling costs) and complex CNC machining (due to material waste and machine time).
- Medium Volumes (Hundreds of units): The comparison becomes closer. AM may still be competitive if the design complexity is high, allows for significant part consolidation, or enables substantial lightweighting not achievable otherwise.
- High Volumes (Thousands+ units): Traditional die casting typically becomes the most cost-effective method per part, assuming the design is suitable for casting. However, AM might still be used for specific niche applications or where its unique benefits (complexity, lead time for design changes) outweigh the per-part cost difference.
- Complexity Factor: For highly complex geometries that are difficult or impossible to cast or machine efficiently, AM can remain competitive even at higher volumes.
- Total Cost of Ownership (TCO): Consider factors beyond per-part price, such as reduced assembly costs (due to part consolidation), lower inventory needs (on-demand production), and the performance benefits of lightweighting (improved EV range/efficiency).
Q3: What is the typical lead time for obtaining prototype EV brackets using metal 3D printing?
A: Lead times for prototypes are one of AM’s major advantages. Typically, you can expect:
- Simple Prototypes (minimal post-processing): 5-10 business days.
- Functional Prototypes (requiring heat treatment, basic finishing): 10-15 business days. Factors influencing this include provider capacity/scheduling, part size/complexity (determining print time), and the extent of required post-processing. Always confirm lead times when requesting quotes. This rapid turnaround is invaluable for accelerating EV development cycles.
Q4: Can functional features like cooling channels or threaded holes be integrated directly into 3D printed brackets?
A: Yes, this is another significant benefit of metal AM:
- Cooling Channels: AM allows for the creation of complex, conformal cooling channels directly within the bracket structure. This is highly advantageous for managing heat from adjacent components like power electronics or motors, potentially eliminating the need for separate heat sinks and improving thermal efficiency.
- Threaded Holes: While threads can sometimes be printed directly, their quality and strength might not be optimal, especially for smaller threads. The common best practice is to design and print pilot holes and then use traditional CNC tapping/threading in post-processing to achieve accurate, strong, and standardized threads.
- Other Features: Mounting bosses, cable routing guides, snap-fit features (with careful design), and complex mating surfaces can all be integrated, supporting part consolidation efforts.
Conclusion: Accelerating Electric Vehicle Innovation with Advanced Metal Additive Manufacturing
The relentless drive towards lighter, more efficient, and higher-performing electric vehicles necessitates a paradigm shift in how critical components like powertrain brackets are designed and manufactured. Metal additive manufacturing, particularly Laser Powder Bed Fusion using advanced aluminum alloys like AlSi10Mg and A7075, offers a powerful solution to meet these challenges head-on.
As we’ve explored, the benefits are compelling: unparalleled design freedom enabling topology optimization and part consolidation; significant lightweighting potential crucial for extending EV range; rapid prototyping capabilities that accelerate development cycles; and the ability to produce complex geometries unachievable with traditional methods. While considerations around tolerances, surface finish, post-processing, and choosing the right manufacturing partner are vital, the strategic advantages AM offers are transforming automotive engineering.
By embracing DfAM principles and leveraging the capabilities of advanced metal powders and printing systems, automotive manufacturers and their B2B suppliers can create EV powertrain brackets that are not merely functional but truly optimized for the unique demands of electric mobility. Overcoming challenges requires expertise and robust process control, underscoring the importance of collaboration with knowledgeable service providers.
Met3dp, with its comprehensive portfolio spanning high-performance metal powders, industry-leading 3D printing equipment, and deep application expertise, stands ready to support the automotive industry’s transition. Their commitment to quality, reliability, and innovation provides the foundation needed to harness the full potential of metal AM.
To explore how metal additive manufacturing can revolutionize your EV component production and address your specific powertrain bracket needs, we encourage you to engage with experts in the field. Contacteer Metal3DP to discuss your project requirements and discover how their cutting-edge systems and advanced materials can power your organization’s journey towards next-generation electric vehicle manufacturing. The future of automotive innovation is being built layer by layer – ensure you have the right partner to help you build it better.
Delen op
MET3DP Technology Co, LTD is een toonaangevende leverancier van additieve productieoplossingen met hoofdkantoor in Qingdao, China. Ons bedrijf is gespecialiseerd in 3D printapparatuur en hoogwaardige metaalpoeders voor industriële toepassingen.
Onderzoek om de beste prijs en een op maat gemaakte oplossing voor uw bedrijf te krijgen!
gerelateerde artikelen
Over Met3DP
Recente update
Ons product
NEEM CONTACT MET ONS OP
Nog vragen? Stuur ons nu een bericht! Na ontvangst van uw bericht behandelen wij uw verzoek met een heel team.
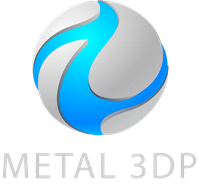
Metaalpoeders voor 3D printen en additieve productie
BEDRIJF
PRODUCT
contact informatie
- Qingdao-stad, Shandong, China
- [email protected]
- [email protected]
- +86 19116340731