Lightweight Antenna Feed Horns via Aluminum 3D Printing
Inhoudsopgave
Inleiding
In the rapidly evolving landscape of telecommunications, aerospace, and satellite technology, the demand for high-performance, lightweight components is constantly increasing. Antenna feed horns, critical elements in signal transmission and reception, are no exception. Traditionally manufactured through subtractive methods, these components often face limitations in terms of design complexity and weight optimization. Metal 3D printing, also known as metal additive manufacturing, offers a transformative approach to producing antenna feed horns with enhanced performance characteristics and reduced weight. This blog post explores the significant advantages of utilizing aluminum alloys like AlSi10Mg and Scalmalloy® in metal 3d printen for the fabrication of lightweight antenna feed horns, catering to the needs of engineers and procurement managers seeking innovative solutions. At Metaal3DP, we are at the forefront of providing cutting-edge metal additive manufacturing solutions, including advanced metal powders and state-of-the-art printing equipment, enabling the creation of intricate and high-performance components like antenna feed horns.
What are Lightweight Antenna Feed Horns Used For?
Lightweight antenna feed horns play a crucial role in a variety of applications across diverse industries. Their primary function is to efficiently direct electromagnetic waves to or from the antenna’s radiating element, optimizing signal strength and quality. Here’s a breakdown of their key use cases:
- Lucht- en ruimtevaart: In aircraft and spacecraft, weight is a critical factor. Lightweight antenna feed horns are essential for satellite communication systems, radar systems, telemetry, and navigation. Reduced weight contributes to improved fuel efficiency and payload capacity.
- Telecommunicatie: For ground-based satellite dishes and telecommunication towers, lightweight feed horns facilitate efficient signal transmission and reception for broadcasting, internet services, and mobile communications. Their reduced mass can simplify installation and structural support requirements.
- Verdediging: Military applications, including radar systems, communication arrays, and electronic warfare equipment, benefit significantly from the reduced weight and design flexibility offered by 3D-printed antenna feed horns. This can lead to more agile and efficient systems.
- Automobiel: With the increasing integration of connectivity features in vehicles, lightweight antenna feed horns are utilized in satellite navigation, communication systems, and even emerging technologies like vehicle-to-everything (V2X) communication.
- Wetenschappelijk onderzoek: In radio astronomy and space exploration, lightweight, high-precision antenna feed horns are critical for collecting and analyzing faint signals from distant celestial objects. The design freedom of 3D printing allows for the creation of specialized horn geometries for specific research purposes.
The demand for lightweighting in these applications drives the need for advanced manufacturing techniques like metal 3D printing, which allows for the creation of complex geometries with optimized material distribution. Our metal 3D printing services cater to these demanding requirements, providing customized solutions for various antenna feed horn applications.
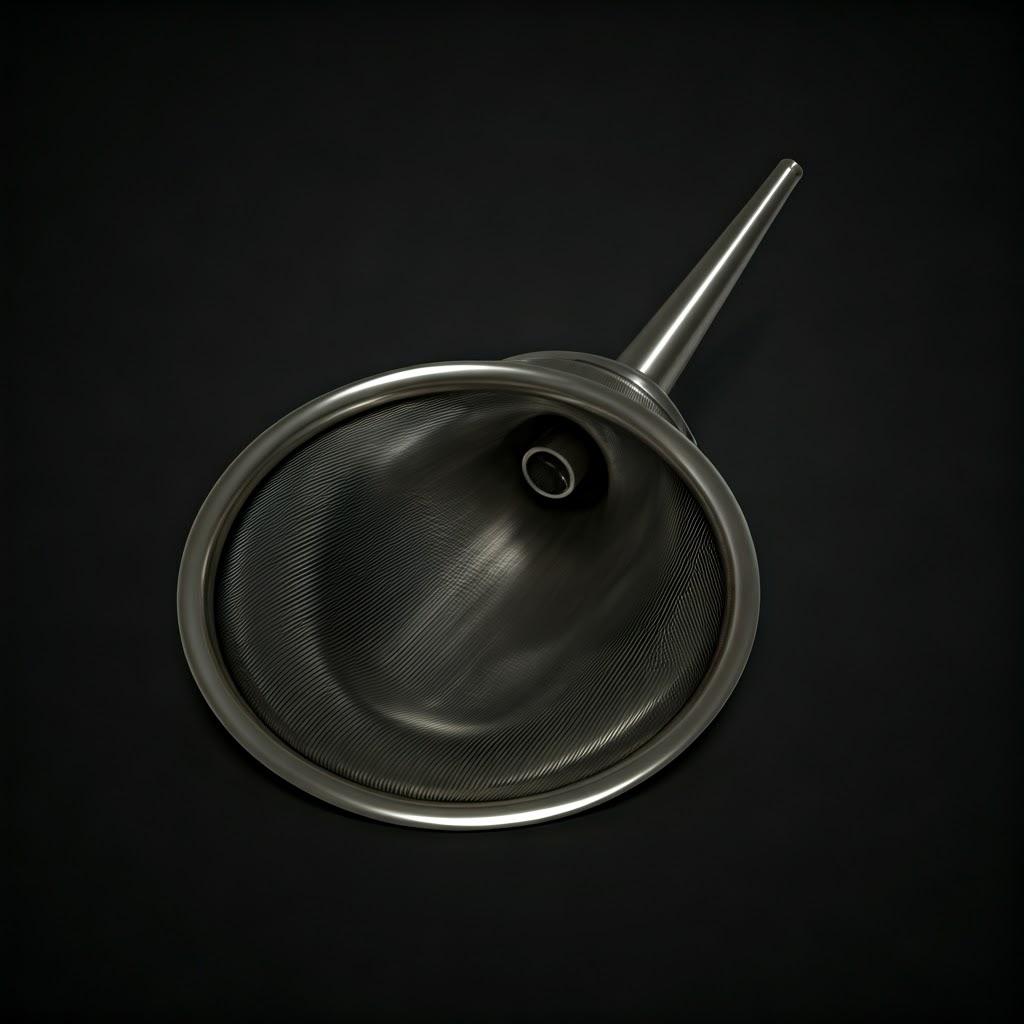
Why Use Metal 3D Printing for Lightweight Antenna Feed Horns?
Opting for metal 3D printing over traditional manufacturing methods for antenna feed horns offers a multitude of compelling advantages, particularly in achieving lightweight designs without compromising performance:
- Ontwerpvrijheid en complexiteit: Additive manufacturing allows for intricate geometries that are difficult or impossible to achieve with traditional methods like machining or casting. This design freedom enables the optimization of the feed horn’s shape for enhanced electromagnetic performance and reduced material usage, directly contributing to weight reduction. Internal lattices and hollow structures can be easily incorporated, further minimizing weight while maintaining structural integrity.
- Materiaalefficiëntie: Unlike subtractive methods that remove material to create the final part, 3D printing adds material layer by layer, significantly reducing material waste. This is particularly beneficial when working with expensive specialty alloys like Scalmalloy®.
- Potentieel lichtgewicht: By enabling complex geometries and internal structures, metal 3D printing facilitates significant weight reduction compared to conventionally manufactured feed horns. This is crucial in weight-sensitive applications like aerospace and portable communication systems.
- Snel prototypen en aanpassen: Metal 3D printing allows for quick iteration of designs and the production of customized feed horns tailored to specific application requirements. This agility in prototyping and customization can significantly reduce development time and costs.
- Integration of Features: Additive manufacturing allows for the integration of multiple components into a single printed part, reducing the need for assembly and additional hardware, which can further contribute to weight savings and improved reliability.
- Productie op aanvraag: 3D printing enables the production of antenna feed horns on demand, eliminating the need for large production runs and associated tooling costs. This is particularly advantageous for low-volume or highly specialized applications.
Op Metaal3DP, our advanced Selective Electron Beam Melting (SEBM) printers and Direct Metal Laser Sintering (DMLS) technology provide the precision and control necessary to manufacture complex, lightweight antenna feed horns with exceptional accuracy and material properties.
Recommended Materials and Why They Matter
The choice of metal powder is paramount in determining the final properties and performance of a 3D-printed antenna feed horn. For lightweight applications, aluminum alloys offer an excellent balance of strength, stiffness, and low density. Here are the recommended powders and their key benefits:
- AlSi10Mg: This aluminum alloy is widely used in metal 3D printing due to its excellent strength-to-weight ratio, good thermal conductivity, and corrosion resistance.
- Lichtgewicht: Aluminum’s low density (approximately 2.7 g/cm³) makes it ideal for reducing the overall weight of the antenna feed horn.
- Mechanische eigenschappen: AlSi10Mg offers good tensile strength and hardness, ensuring the structural integrity of the component under operational loads.
- Thermisch beheer: Its good thermal conductivity helps dissipate heat generated during operation, crucial for maintaining performance and reliability.
- Verwerkbaarheid: AlSi10Mg is well-suited for both DMLS and SEBM processes, allowing for the production of complex geometries with good surface finish.
- Scalmalloy®: This high-performance aluminum-magnesium-scandium alloy offers superior strength-to-weight ratio compared to conventional aluminum alloys.
- Ultra-Lightweighting: Scalmalloy®’s even lower density (around 2.67 g/cm³) and significantly higher strength allow for the creation of even lighter parts without sacrificing structural integrity.
- Uitzonderlijke kracht: Its high tensile strength and yield strength make it suitable for demanding applications where weight savings are critical and high mechanical performance is required.
- Vermoeidheidsweerstand: Scalmalloy® exhibits excellent fatigue resistance, crucial for components subjected to вибрации or cyclic loading.
- Aerospace-Grade Performance: Due to its exceptional properties, Scalmalloy® is increasingly being adopted in aerospace applications where weight and performance are paramount.
Metal3DP’s range of high-quality metal powders includes AlSi10Mg and other advanced aluminum alloys, ensuring that our customers have access to the best materials for their specific antenna feed horn requirements. Our advanced powder making system guarantees high sphericity and flowability, essential for consistent and high-quality 3D printing.
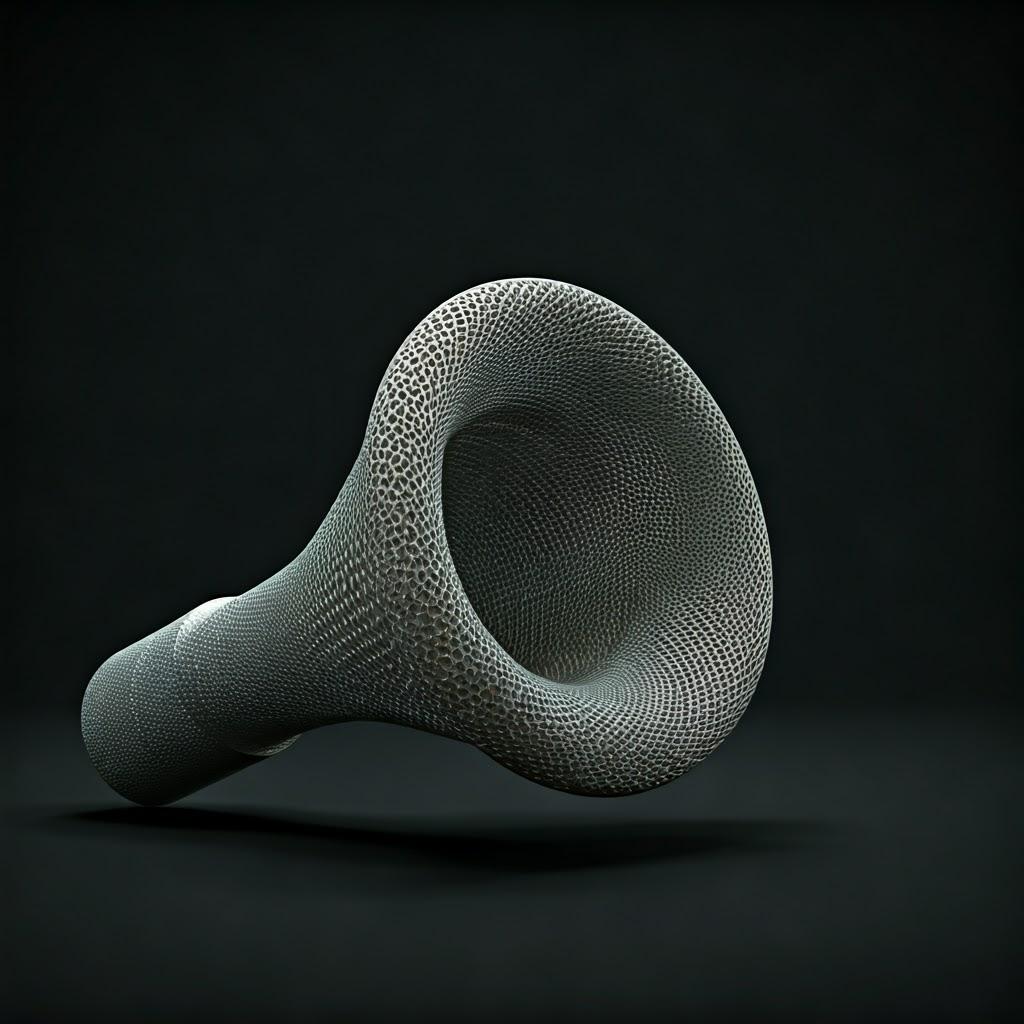
Design Considerations for Additive Manufacturing
Designing antenna feed horns for metal 3D printing requires a different mindset compared to traditional manufacturing. To fully leverage the capabilities of additive manufacturing and achieve optimal lightweighting and performance, several design considerations are crucial:
- Topologieoptimalisatie: This computational method optimizes the material layout within a given design space for a specific set of loads and boundary conditions. By removing material from low-stress areas, topology optimization can lead to significant weight reduction while maintaining or even improving structural performance. Metal 3D printing excels at realizing these complex, organic-like optimized geometries.
- Roosterstructuren: Incorporating lattice structures, which are repeating cellular geometries, within the bulk of the feed horn can dramatically reduce weight without significantly compromising stiffness. Different lattice types (e.g., gyroid, diamond, cubic) offer varying strength-to-weight ratios and can be tailored to specific load requirements.
- Hollow Features and Thin Walls: Metal 3D printing allows for the creation of hollow internal channels and thin-walled structures, further minimizing material usage and weight. Careful consideration of wall thickness and support structures is essential to prevent collapse or distortion during the printing process.
- Surface Finish Optimization: While a smooth surface finish is often desirable for electromagnetic performance, minimizing surface roughness in non-critical areas can reduce the need for extensive post-processing, saving time and cost. Designing with the inherent surface finish capabilities of the chosen 3D printing process in mind is important.
- Orientation and Support Structures: The orientation of the part during printing significantly impacts surface finish, support structure requirements, and the potential for warping. Careful orientation planning and the strategic placement of support structures are crucial for successful printing and minimizing material waste. Support structures should be designed for easy removal without damaging the delicate features of the feed horn.
- Feature Integration: Additive manufacturing allows for the integration of features like mounting interfaces, cooling channels, or alignment features directly into the feed horn design, reducing the need for separate components and assembly steps, which can contribute to overall weight reduction and system simplification.
Our team at Metaal3DP possesses extensive expertise in designing for additive manufacturing. We work closely with our clients to optimize their antenna feed horn designs for lightweighting, performance, and efficient production using our advanced metal 3D printing technologies.
Tolerance, Surface Finish, and Dimensional Accuracy
Achieving the required tolerance, surface finish, and dimensional accuracy is critical for the functional performance of antenna feed horns, as these factors can directly impact their electromagnetic properties. Metal 3D printing offers specific capabilities in these areas:
- Tolerance: The achievable tolerance in metal 3D printing depends on the chosen printing technology, material, and part geometry. Typically, tolerances in the range of ±0.1 to ±0.05 mm can be achieved for critical dimensions. Factors influencing tolerance include thermal gradients during printing, material shrinkage, and the accuracy of the printer’s motion system. At Metaal3DP, our high-precision SEBM and DMLS printers are capable of achieving tight tolerances required for demanding antenna applications.
- Afwerking oppervlak: The as-printed surface finish in metal 3D printing is generally rougher compared to machined surfaces. The surface roughness (Ra) typically ranges from 5 to 20 μm, depending on the powder particle size and printing parameters. For antenna feed horns, a smoother surface finish is often desired to minimize signal loss and scattering. Post-processing techniques like polishing, media blasting, or chemical etching can be employed to achieve smoother surfaces.
- Maatnauwkeurigheid: Dimensional accuracy refers to the ability of the 3D-printed part to match the intended design dimensions. Factors affecting dimensional accuracy include material shrinkage, thermal distortion, and calibration of the printing equipment. Careful process control, optimized build orientation, and appropriate support structure design are essential for achieving high dimensional accuracy. Our quality control processes at Metal3DP ensure that all printed parts meet stringent dimensional requirements.
Functie | Typical Range in Metal 3D Printing | Impact on Antenna Feed Horn Performance |
---|---|---|
Tolerantie | ±0.05 mm – ±0.1 mm | Affects fit, assembly, and potentially electromagnetic properties |
Surface Roughness (Ra) | 5 μm – 20 μm | Can influence signal loss and scattering |
Dimensionale nauwkeurigheid | Varies with geometry and process | Critical for achieving desired electromagnetic characteristics |
Exporteren naar Sheets
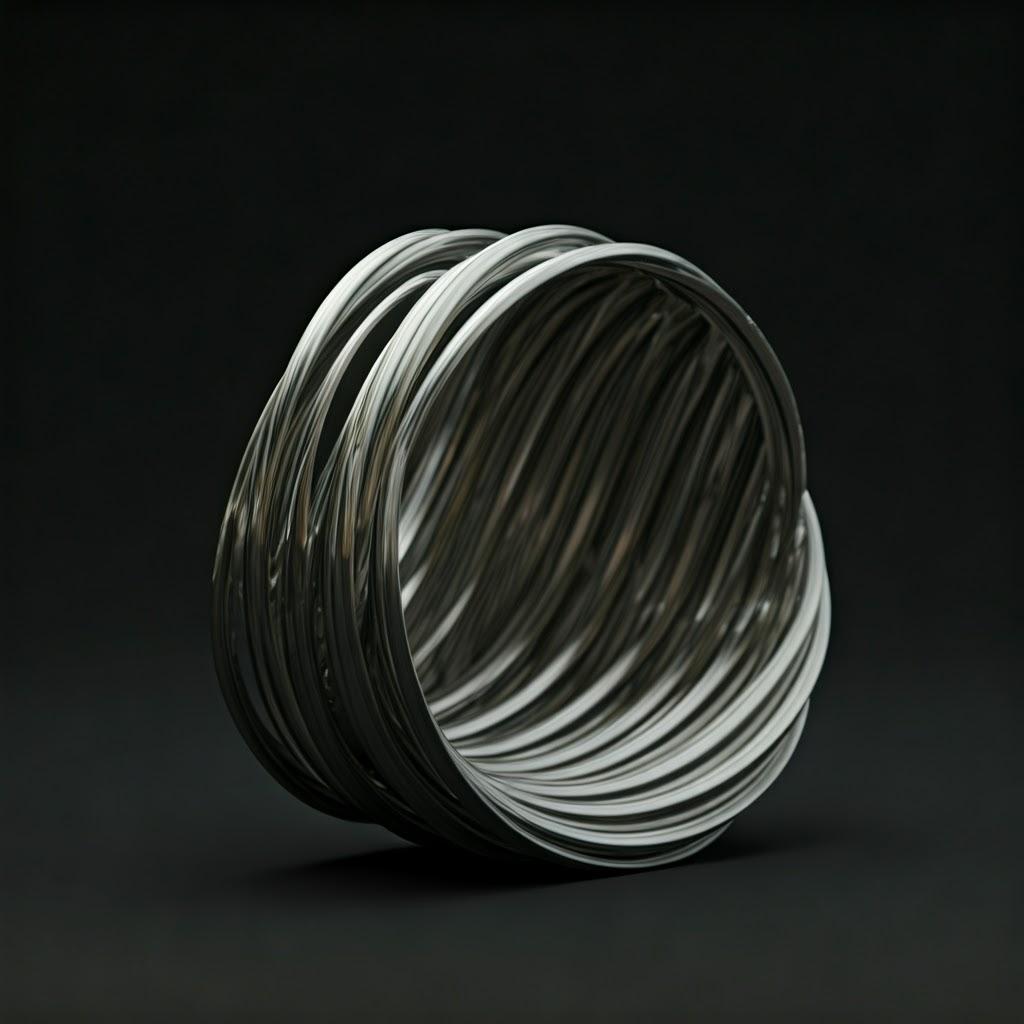
Vereisten voor naverwerking
While metal 3D printing offers significant advantages, post-processing steps are often necessary to achieve the final desired properties and surface finish for antenna feed horns:
- Ondersteuning verwijderen: Support structures are often required during the printing process to prevent part deformation and ensure proper overhangs. These supports need to be carefully removed after printing. The design of the supports and the material used can influence the ease of removal and the potential for surface damage.
- Hittebehandeling: Depending on the material and application requirements, heat treatment may be necessary to relieve internal stresses, improve mechanical properties (e.g., strength, hardness), or achieve specific microstructures. For aluminum alloys like AlSi10Mg, stress relieving or age hardening treatments are common.
- Afwerking oppervlak: As mentioned earlier, post-processing techniques like media blasting, polishing (mechanical or electrochemical), and chemical etching can be used to improve the surface finish of the antenna feed horn, which can be critical for optimizing electromagnetic performance.
- CNC-bewerking: In cases where very tight tolerances are required for specific features, such as mounting interfaces or critical dimensions, CNC machining can be employed as a secondary operation after 3D printing. This hybrid approach leverages the design freedom of 3D printing and the precision of machining.
- Coating: Depending on the operating environment, coatings may be applied to enhance corrosion resistance, improve surface conductivity, or modify the electromagnetic properties of the antenna feed horn. Examples include conductive coatings or protective layers.
- Inspection and Quality Control: Thorough inspection using techniques like coordinate measuring machines (CMM), optical scanners, and non-destructive testing (NDT) methods (e.g., X-ray inspection) is crucial to ensure that the printed antenna feed horns meet the required dimensional accuracy, material integrity, and performance specifications.
Op Metaal3DP, we offer comprehensive post-processing services to ensure that our 3D-printed metal parts meet the highest quality standards and specific application requirements.
Common Challenges and How to Avoid Them
While metal 3D printing offers numerous benefits, certain challenges can arise during the process. Understanding these potential issues and implementing appropriate strategies can help avoid them:
- Vervorming en vervorming: Thermal stresses during the printing process can lead to warping or distortion of the part, especially for large or complex geometries.
- Avoidance: Optimizing part orientation, using appropriate support structures, controlling the build chamber temperature, and employing stress-relieving heat treatments can mitigate warping.
- Poreusheid: The presence of pores or voids within the printed part can compromise its mechanical strength and electromagnetic performance.
- Avoidance: Optimizing printing parameters (laser power, scan speed, powder feed rate), ensuring high-quality metal powder with good flowability, and maintaining a controlled printing environment (e.g., inert atmosphere) can minimize porosity. Our advanced powder making system ensures the high quality of our metal powders, contributing to dense and defect-free prints.
- Support Structure Removal Damage: Improper removal of support structures can damage the surface of the printed part, especially delicate features.
- Avoidance: Designing support structures for easy removal, using appropriate removal tools and techniques, and considering dissolvable support materials (where applicable) can prevent damage.
- Oppervlakteruwheid: As mentioned earlier, the as-printed surface can be rough, which may not be suitable for all antenna applications.
- Avoidance: Optimizing printing parameters to achieve a smoother initial surface finish and employing appropriate post-processing techniques like polishing or media blasting can address this.
- Dimensional Inaccuracy: Deviations from the intended dimensions can occur due to factors like material shrinkage or printer calibration issues.
- Avoidance: Accurate printer calibration, material-specific process parameter optimization, and incorporating shrinkage compensation in the design can improve dimensional accuracy.
By understanding these potential challenges and implementing best practices in design and printing, engineers and procurement managers can effectively leverage metal 3D printing for the successful production of lightweight antenna feed horns.
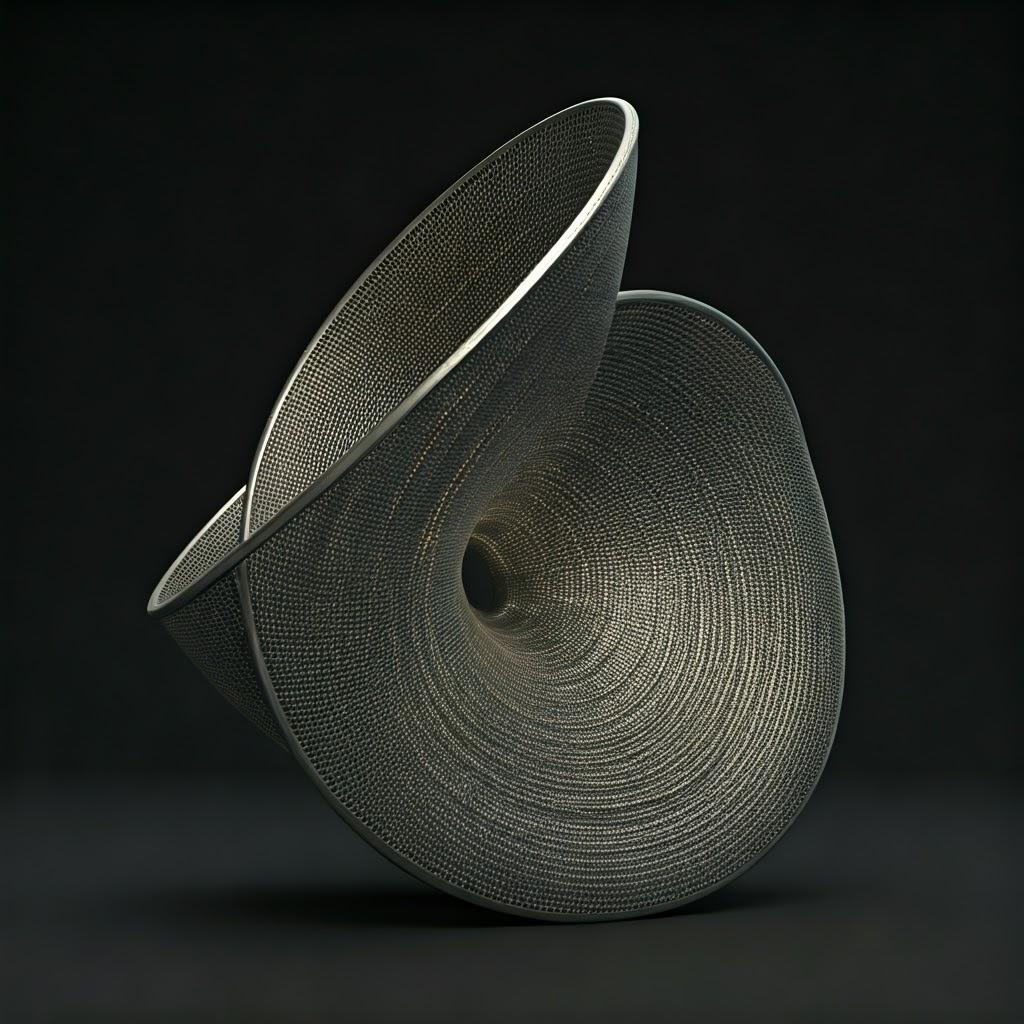
How to Choose the Right Metal 3D Printing Service Provider
Selecting the right metal 3D printing service provider is crucial for ensuring the successful fabrication of high-quality, lightweight antenna feed horns that meet your specific requirements. Here are key factors to consider when evaluating potential suppliers:
- Material Capabilities: Ensure the provider has experience working with the recommended aluminum alloys (AlSi10Mg, Scalmalloy®) and possesses a comprehensive understanding of their properties and processing parameters. Inquire about the range of other materials they offer, as future projects may require different alloys. Metaal3DP specializes in a wide array of high-performance metal powders, including those ideal for lightweighting applications.
- Druktechnologie: Different metal 3D printing technologies (e.g., DMLS, SLM, EBM) have varying strengths and limitations in terms of achievable accuracy, surface finish, build volume, and material compatibility. Understand which technologies the provider utilizes and whether they are suitable for your antenna feed horn’s design complexity and performance requirements.
- Design and Engineering Support: A reputable service provider should offer design for additive manufacturing (DfAM) expertise to help optimize your antenna feed horn design for lightweighting, performance, and efficient printing. Their engineers should be knowledgeable in topology optimization, lattice structures, and other DfAM principles.
- Post-Processing Services: Inquire about the in-house post-processing capabilities, including support removal, heat treatment, surface finishing (polishing, coating), and CNC machining. A provider offering comprehensive post-processing services can streamline the production process and ensure the final part meets your specifications.
- Quality Assurance and Certifications: Verify the provider’s quality management system and any relevant certifications (e.g., ISO 9001, AS9100 for aerospace). Robust quality control processes, including material testing and dimensional inspection, are essential for ensuring the reliability and performance of the printed antenna feed horns.
- Experience and Industry Focus: Look for a provider with a proven track record in metal 3D printing, ideally with experience in your specific industry (e.g., aerospace, telecommunications). Industry-specific expertise can translate to a better understanding of your application requirements and potential challenges.
- Lead Times and Production Capacity: Discuss lead times for prototyping and production, as well as the provider’s capacity to handle your anticipated volumes. Ensure their timelines align with your project schedule.
- Cost Structure and Transparency: Obtain a clear and detailed quotation that outlines all costs, including printing, materials, post-processing, and any additional services. Understand the factors that influence pricing.
- Communication and Customer Support: Effective communication and responsive customer support are crucial for a smooth and successful project. Assess the provider’s responsiveness and willingness to collaborate.
By carefully evaluating these factors, you can select a metal 3D printing service provider like Metaal3DP that can deliver high-quality, lightweight antenna feed horns tailored to your specific needs.
Cost Factors and Lead Time
The cost and lead time for producing lightweight antenna feed horns via metal 3D printing are influenced by several factors:
Kostenfactoren:
- Materiaalkosten: The type and quantity of metal powder used are significant cost drivers. Specialty alloys like Scalmalloy® are typically more expensive than standard aluminum alloys like AlSi10Mg. The complexity of the part design and the efficiency of the printing process (material waste) also impact material costs.
- Afdrukken tijd: The build time on the 3D printer is a key factor. Longer print times, influenced by part size, complexity, and layer height, translate to higher machine operating costs.
- Kosten voor nabewerking: The extent of post-processing required (support removal, heat treatment, surface finishing, machining, coating) significantly affects the overall cost. Complex post-processing workflows will increase expenses.
- Design and Engineering Costs: If you require design optimization or engineering support from the service provider, these services will factor into the total cost.
- Quantity and Volume: Similar to traditional manufacturing, economies of scale can apply to metal 3D printing. Larger production runs may result in lower per-part costs.
- Equipment and Overhead: The service provider’s investment in equipment, facility costs, and operational overhead are reflected in their pricing.
Lead Time Factors:
- Design Complexity and Optimization: Intricate designs requiring significant optimization may have longer initial lead times for design and engineering.
- Beschikbaarheid materiaal: The availability of the chosen metal powder can impact lead times. Less common or specialty alloys may have longer procurement times.
- Afdrukken tijd: As mentioned earlier, the build duration on the 3D printer directly affects the manufacturing lead time.
- Post-Processing Duration: The time required for post-processing steps can add significantly to the overall lead time. Complex heat treatments or extensive surface finishing will take longer.
- Workload and Scheduling: The service provider’s current workload and production schedule will influence the turnaround time.
- Shipping and Logistics: The time required for shipping the finished parts to your location needs to be considered in the overall lead time.
While metal 3D printing can offer faster prototyping compared to traditional methods, production lead times depend on the factors mentioned above. It’s crucial to discuss these aspects in detail with your chosen service provider to establish realistic expectations for both cost and delivery timelines.
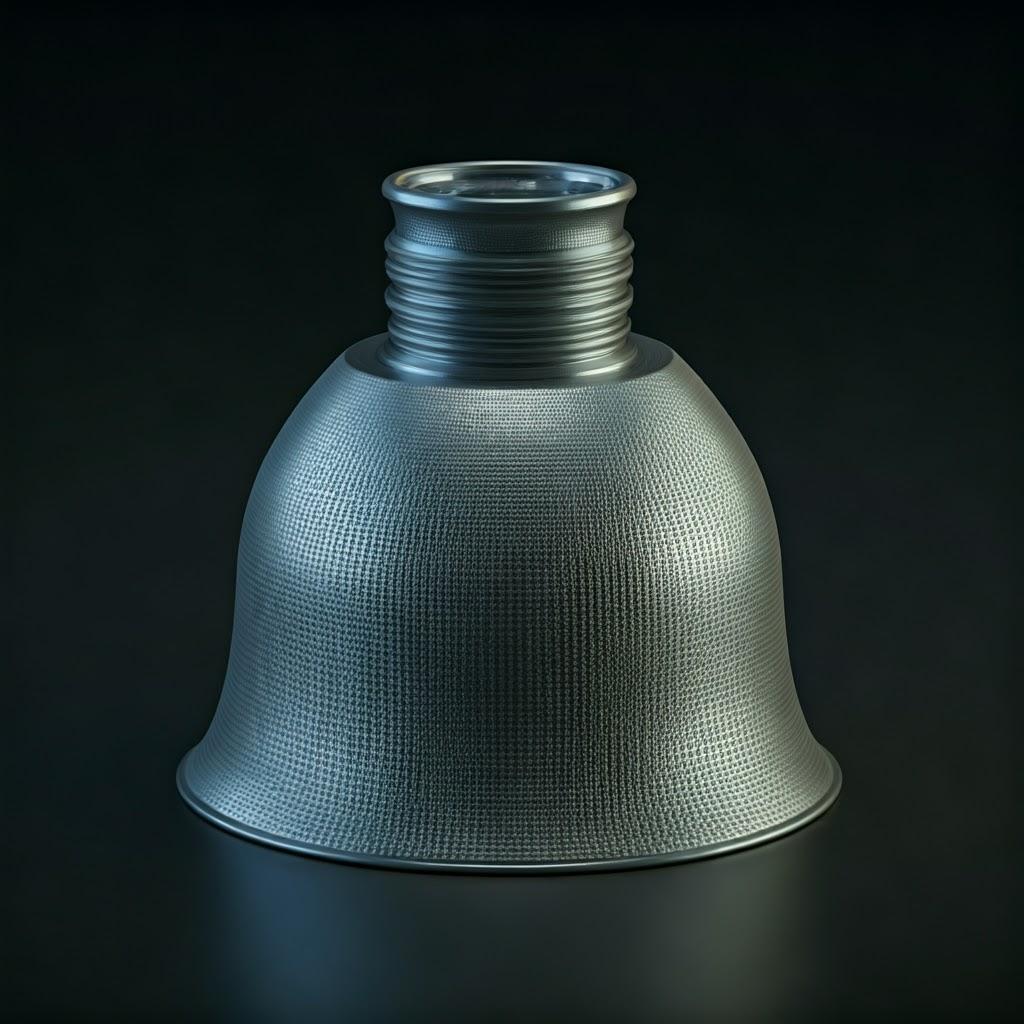
Veelgestelde vragen (FAQ)
- Can metal 3D-printed antenna feed horns achieve the same performance as traditionally manufactured ones? Yes, when designed and manufactured correctly, metal 3D-printed antenna feed horns can meet or even exceed the performance of traditionally manufactured counterparts. The design freedom offered by additive manufacturing allows for optimized geometries that can enhance electromagnetic properties. Material selection and post-processing are also critical factors in achieving desired performance.
- Is metal 3D printing cost-effective for producing antenna feed horns? The cost-effectiveness of metal 3D printing depends on factors such as design complexity, production volume, material choice, and post-processing requirements. For low to medium volumes, complex geometries, and customized designs, metal 3D printing can be more cost-effective than traditional methods that require tooling. As production volumes increase, traditional methods may become more economical for simpler designs.
- What are the typical applications for lightweight 3D-printed aluminum antenna feed horns? Lightweight 3D-printed aluminum antenna feed horns are commonly used in aerospace (satellites, drones), telecommunications (portable systems), defense (radar systems), and specialized scientific equipment where weight reduction is critical for performance and efficiency.
Conclusie
Metal 3D printing, particularly with lightweight aluminum alloys like AlSi10Mg and Scalmalloy®, offers a powerful solution for producing high-performance antenna feed horns with significantly reduced weight. The design freedom, material efficiency, and rapid prototyping capabilities of additive manufacturing provide engineers and procurement managers with unprecedented opportunities to innovate and optimize their systems. By carefully considering design principles for additive manufacturing, understanding the achievable tolerances and surface finishes, and selecting a reputable service provider like Metaal3DP, organizations can leverage the benefits of metal 3D printing to create next-generation, lightweight antenna feed horns for a wide range of demanding applications. Contact Metaal3DP today to explore how our comprehensive metal additive manufacturing solutions can power your organization’s goals.
Delen op
MET3DP Technology Co, LTD is een toonaangevende leverancier van additieve productieoplossingen met hoofdkantoor in Qingdao, China. Ons bedrijf is gespecialiseerd in 3D printapparatuur en hoogwaardige metaalpoeders voor industriële toepassingen.
Onderzoek om de beste prijs en een op maat gemaakte oplossing voor uw bedrijf te krijgen!
gerelateerde artikelen
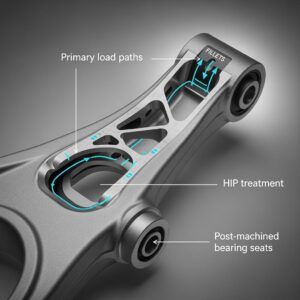
Metal 3D Printing for U.S. Automotive Lightweight Structural Brackets and Suspension Components
Lees verder "Over Met3DP
Recente update
Ons product
NEEM CONTACT MET ONS OP
Nog vragen? Stuur ons nu een bericht! Na ontvangst van uw bericht behandelen wij uw verzoek met een heel team.