DED voor autoproductie
Inhoudsopgave
De auto-industrie is voortdurend in beweging, gedreven door een niet aflatende vraag naar lichtere, sterkere en zuinigere voertuigen. Maak kennis met Directed Energy Deposition (DED), een revolutionaire technologie voor additive manufacturing (AM) die de manier waarop auto's worden gebouwd zal veranderen. Stel je een proces voor waarbij complexe metalen onderdelen laag voor laag worden gemaakt, met ongeëvenaarde ontwerpvrijheid en maatwerk. Dat is de magie van DED, en het verandert snel het spel voor autofabrikanten wereldwijd.
DED: Een metalen wonder
DED, ook bekend als Laser Metal Deposition (LMD) of Cold Metal Transfer (CMT), werkt als een hightech beeldhouwer. Een geconcentreerde energiebron, meestal een laserstraal, smelt metaalpoeder dat in de machine wordt ingevoerd. Dit gesmolten metaal wordt nauwkeurig afgezet op een platform, waarbij het gewenste onderdeel laag voor laag wordt opgebouwd.
Zie het als het maken van een 3D metalen schets met een laserpen, maar dan op industriële schaal, met ongelooflijke precisie en controle. In tegenstelling tot traditionele productiemethoden zoals machinaal bewerken of gieten, is er bij DED geen complex gereedschap nodig en is de ontwerpruimte veel groter.
Maar wat zijn die metaalpoeders precies die DED gebruikt om deze wonderen voor auto's te bouwen? Zet je schrap, want we duiken in de fascinerende wereld van DED-metaalpoeders:
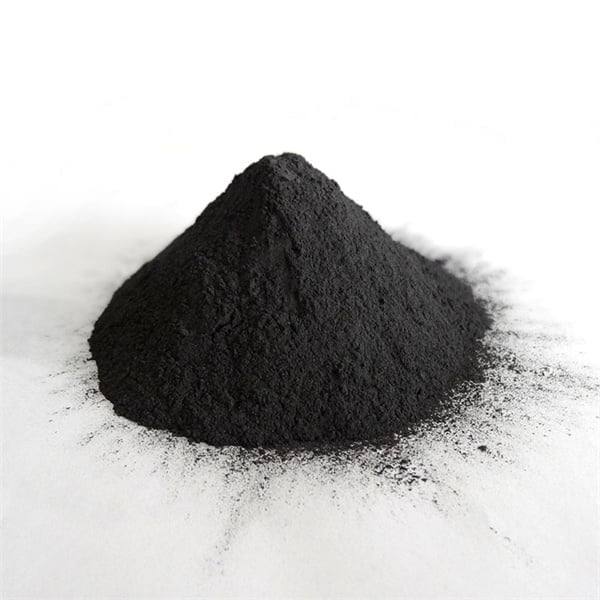
Metaalpoeders voor DED: Een materiële menagerie
Het succes van DED hangt af van het specifieke metaalpoeder dat gebruikt wordt. Verschillende poeders hebben unieke eigenschappen, waardoor ze geschikt zijn voor uiteenlopende toepassingen in de auto-industrie. Hier volgt een blik op enkele van de meest gebruikte DED metaalpoeders en hun eigenschappen:
Metaalpoeder | Samenstelling | Eigenschappen | Toepassingen in autoproductie |
---|---|---|---|
Roestvrij staal 316L | Fe (ijzer), Cr (chroom), Ni (nikkel), Mo (molybdeen) | Uitstekende corrosiebestendigheid, goede mechanische sterkte, biocompatibel | Uitlaatspruitstukken, carrosseriepanelen (vooral voor hoogwaardige sportauto's die superieure corrosiebestendigheid vereisen), onderdelen van medische apparatuur die in ambulances worden gebruikt |
Inconel 625 | Ni (Nikkel), Cr (Chroom), Mo (Molybdeen), Fe (IJzer) | Uitzonderlijke prestaties bij hoge temperaturen, goede weerstand tegen oxidatie | Turbinebladen, uitlaatcomponenten, hitteschilden |
Aluminium Si7Mg0,3 | Al (Aluminium), Si (Silicium), Mg (Magnesium) | Hoge sterkte-gewichtsverhouding, goed lasbaar, uitstekende corrosiebestendigheid | Lichtgewicht ophangingscomponenten, remklauwen, structurele componenten die een balans tussen sterkte en gewicht vereisen |
Titaan Ti-6Al-4V | Ti (titanium), Al (aluminium), V (vanadium) | Hoge sterkte-gewichtsverhouding, uitstekende biocompatibiliteit | Krachtige motoronderdelen zoals drijfstangen en zuigers, prothetische ledematen die worden gebruikt in speciale voertuigen voor mensen met een handicap |
Nikkellegering 718 | Ni (Nikkel), Cr (Chroom), Fe (IJzer), Mo (Molybdeen), Nb (Niobium) | Hoge sterkte, goede kruipweerstand bij verhoogde temperaturen | Tandwielen, assen, ruimtevaartonderdelen die vaak worden gebruikt in raceauto's met hoge prestaties |
Kobaltchroom CoCrMo | Co (Kobalt), Cr (Chroom), Mo (Molybdeen) | Hoge slijtvastheid, biocompatibel | Heupprotheseonderdelen die worden gebruikt in speciale voertuigen voor mensen met een handicap, snij- en slijtgereedschappen |
Gereedschapsstaal H13 | Fe (ijzer), Cr (chroom), Mo (molybdeen), V (vanadium) | Hoge hardheid, goede slijtvastheid | Stempels en matrijzen voor het stempelen en vormen van auto-onderdelen |
Koper Cu | Cu (Koper) | Uitstekende thermische en elektrische geleidbaarheid | Koellichamen voor hoogwaardige elektronica gebruikt in elektrische voertuigen, elektrische rails |
Inconel 718C | Ni (Nikkel), Cr (Chroom), Fe (IJzer), Mo (Molybdeen), Nb (Niobium) | Vergelijkbare eigenschappen als Inconel 718, maar met verbeterde scheurvastheid | Kritische motoronderdelen in high-performance en racetoepassingen |
Maragingstaal 1.2379 | Fe (IJzer), Ni (Nikkel), Mo (Molybdeen), Co (Kobalt), Ti (Titanium) | Hoge sterkte, uitstekende taaiheid | Kritieke veiligheidsonderdelen zoals fusees en ophangingsarmen |
Dit is slechts een tipje van de sluier van de diverse wereld van DED-metaalpoeders. Naarmate de DED-technologie zich verder ontwikkelt, kunnen we verwachten dat er een nog breder scala aan poeders zal worden ontwikkeld voor nog meer gespecialiseerde toepassingen in de auto-industrie.
DED in actie: Transformatie van de autoproductie
Nu we de fascinerende wereld van DED-metaalpoeders hebben verkend, laten we eens kijken hoe deze technologie zich vertaalt naar echte toepassingen in de auto-industrie. DED biedt een groot aantal voordelen ten opzichte van traditionele productiemethoden, waardoor het een game-changer wordt voor autofabrikanten:
- Ongeëvenaarde ontwerpvrijheid: In tegenstelling tot traditionele methoden die beperkt worden door gereedschapsbeperkingen, maakt DED het mogelijk om complexe geometrieën en interne kenmerken in ontwerpen op te nemen. Stelt u zich eens lichtgewicht componenten voor met ingewikkelde rasterstructuren voor een optimale verhouding tussen sterkte en gewicht, of geïntegreerde koelkanalen in motorblokken voor een beter thermisch beheer. DED maakt deze ontwerpdromen werkelijkheid.
- Lichtgewichtrevolutie: De auto-industrie is op een meedogenloze zoektocht om kilo's te verliezen. DED, dat in staat is lichtgewicht maar toch robuuste structuren te bouwen met materialen als aluminium en titanium, is een belangrijk wapen in deze strijd om gewichtsbesparing. Lichtere voertuigen leiden tot een efficiënter brandstofverbruik, minder uitstoot en uiteindelijk tevreden klanten die zich zorgen maken over het milieu.
- Snelle prototyping en productie op aanvraag: Stel je voor dat je een op maat gemaakt onderdeel nodig hebt voor een prototype van een voertuig - traditioneel zou dit langdurige bewerkingsprocessen met zich meebrengen. DED biedt een snellere en flexibelere oplossing. Met DED kunnen complexe prototypes snel en efficiënt worden gemaakt, waardoor de ontwikkelingscyclus wordt versneld en innovatieve nieuwe auto's sneller op de markt komen. Bovendien maakt DED de productie van reserveonderdelen op aanvraag mogelijk, vooral voor oudere of uit productie genomen voertuigen, waardoor stilstand tot een minimum wordt beperkt en auto's op de weg blijven.
- Reparatie en revisie: Bij DED gaat het niet alleen om het maken van nieuwe onderdelen; het is ook een krachtig hulpmiddel voor het repareren en opnieuw maken van bestaande onderdelen. Stel je een gebarsten motorblok voor of een versleten tandwiel - traditioneel zouden deze onderdelen worden vervangen. DED biedt een duurzamere en kosteneffectievere oplossing. Door selectief materiaal op beschadigde gebieden aan te brengen, kan DED versleten onderdelen nieuw leven inblazen, hun levensduur verlengen en afval verminderen.
Hier volgen enkele specifieke voorbeelden van hoe DED de autofabricage nu al transformeert:
- DED kan worden gebruikt om geïntegreerde transmissiebehuizingen te maken: Traditioneel zijn transmissiebehuizingen complexe samenstellingen uit meerdere onderdelen. Met DED kan een enkele, lichtgewicht behuizing worden gebouwd met ingewikkelde interne kanalen en functies, waardoor de efficiëntie wordt verbeterd en het gewicht wordt verlaagd.
- DED kan worden gebruikt om lichtgewicht ophangingscomponenten te maken: Door DED te gebruiken met aluminium of titanium poeders kunnen autofabrikanten ophangingscomponenten maken die zowel sterk als licht zijn, wat bijdraagt aan een betere wegligging en brandstofefficiëntie.
- DED kan worden gebruikt om hoogwaardige motorcilinderblokken te maken: Met DED kunnen complexe koelkanalen in motorblokken worden gemaakt, wat leidt tot een efficiënter warmtebeheer en betere motorprestaties, vooral bij toepassingen voor hoge prestaties en races.
- DED kan worden gebruikt om aangepaste onderdelen voor prototypevoertuigen te maken: Dankzij de snelle prototypingmogelijkheden van DED kunnen autofabrikanten experimenteren met innovatieve ontwerpen en nieuwe voertuigen sneller op de markt brengen.
- DED kan worden gebruikt om kritieke auto-onderdelen te repareren en opnieuw te maken: Van gebarsten motorblokken tot versleten tandwielen, DED biedt een kosteneffectieve en duurzame oplossing voor het repareren en verlengen van de levensduur van kritieke auto-onderdelen.
Dit zijn slechts enkele voorbeelden en naarmate de DED-technologie zich verder ontwikkelt, kunnen we nog meer innovatieve toepassingen verwachten, die een revolutie teweegbrengen in de manier waarop auto's worden gebouwd.
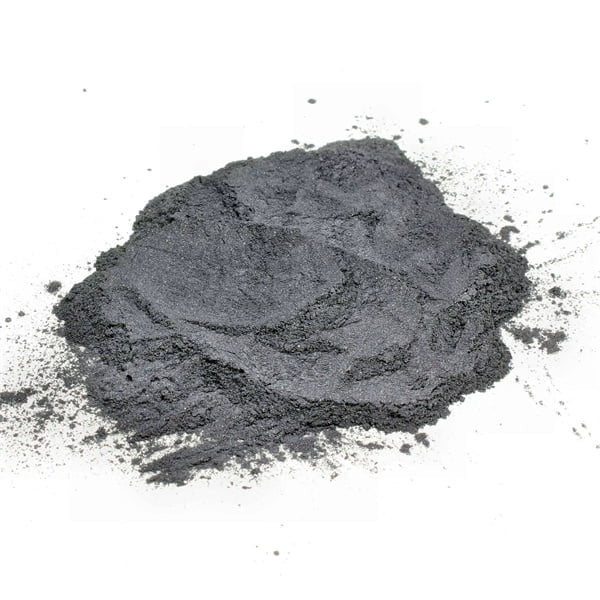
Voordelen en beperkingen van DED in autoproductie
Voordelen:
- Ongeëvenaarde ontwerpvrijheid: Creëer complexe geometrieën en integreer elementen die onmogelijk zijn met traditionele methoden.
- Lichtgewicht: Bouw sterke maar lichte onderdelen voor een efficiënter brandstofverbruik.
- Snelle prototyping: Versnel ontwikkelingscycli door snel en efficiënt prototypes te maken.
- Productie op aanvraag: Aangepaste onderdelen produceren als dat nodig is, zodat er zo min mogelijk voorraad nodig is.
- Reparatie en revisie: Verleng de levensduur van kritieke onderdelen en verminder afval.
Beperkingen:
- Kosten: DED-systemen en metaalpoeders kunnen duur zijn in vergelijking met traditionele methoden.
- Bouwsnelheid: DED kan langzamer zijn dan sommige traditionele productietechnieken voor grote volumes.
- Afwerking oppervlak: Voor DED-onderdelen kan extra nabewerking nodig zijn voor een gladde afwerking.
- Procesbeheersing: DED vereist een zorgvuldige controle van de parameters om de kwaliteit en consistentie van het product te garanderen.
De toekomst van DED in de autoproductie
De toekomst van DED in de autofabricage is rooskleurig. Naarmate de DED-technologie zich verder ontwikkelt, kunnen we het volgende verwachten:
- Lagere kosten: Vooruitgang in DED-systemen en metaalpoeders zal de technologie meer kostenconcurrerend maken ten opzichte van traditionele methoden.
- Hogere bouwsnelheden: Snellere DED-processen maken de technologie geschikt voor productieruns in grotere volumes.
- Verbeterde oppervlakteafwerking: Geavanceerde DED-technieken zullen onderdelen produceren met een gladdere afwerking, waardoor er minder nabewerking nodig is.
- Breder scala aan materialen: Er zullen nieuwe DED-metaalpoeders worden ontwikkeld voor een breder spectrum van toepassingen in de auto-industrie.
DED: Overwegingen voor materiaalselectie
We hebben eerder een aantal verschillende DED metaalpoeders onderzocht, maar het kiezen van de juiste voor jouw specifieke toepassing vereist een zorgvuldige afweging. Hier zijn enkele belangrijke factoren om in gedachten te houden:
- Gewenste onderdeeleigenschappen: Dit is de meest cruciale factor. Stem de eigenschappen van het poeder (sterkte, corrosiebestendigheid, gewicht, enz.) af op de behoeften van het uiteindelijke onderdeel. Als je bijvoorbeeld een lichtgewicht ophangingsonderdeel bouwt, is aluminium Si7Mg0.3 een goede keuze vanwege de hoge sterkte-gewichtsverhouding. Omgekeerd, als je een turbineblad bouwt dat bestand moet zijn tegen extreme temperaturen, is Inconel 625 een betere optie vanwege de uitzonderlijke prestaties bij hoge temperaturen.
- Compatibiliteit met het DED-systeem: Niet alle DED-systemen zijn gelijk. Zorg ervoor dat het poeder dat je kiest de juiste korrelgrootteverdeling en vloeibaarheid heeft voor optimale prestaties in je specifieke DED-machine. Raadpleeg de fabrikant van je machine voor aanbevolen poeders of compatibele poedereigenschappen.
- Kosten: DED metaalpoeders kunnen aanzienlijk in prijs variëren. Houd rekening met de kosten van het poeder zelf, maar ook met eventuele extra verwerkingskosten voor het gekozen materiaal. Sommige exotische poeders zoals Maraging Steel 1.2379 kunnen bijvoorbeeld superieure sterkte bieden, maar zijn duurder dan de meer gangbare opties zoals Stainless Steel 316L.
- Invloed op het milieu: Duurzaamheid is een groeiend aandachtspunt in de auto-industrie. Houd rekening met de ecologische voetafdruk van de productie en recyclebaarheid van het poeder. Sommige poeders, zoals aluminium en titanium, worden gemakkelijker gerecycled dan andere, wat bijdraagt aan een duurzamer productieproces.
- Beschikbaarheid: Zorg ervoor dat het poeder dat je kiest direct verkrijgbaar is bij een gerenommeerde leverancier. Productievertragingen door poedertekorten kunnen je productieproces verstoren.
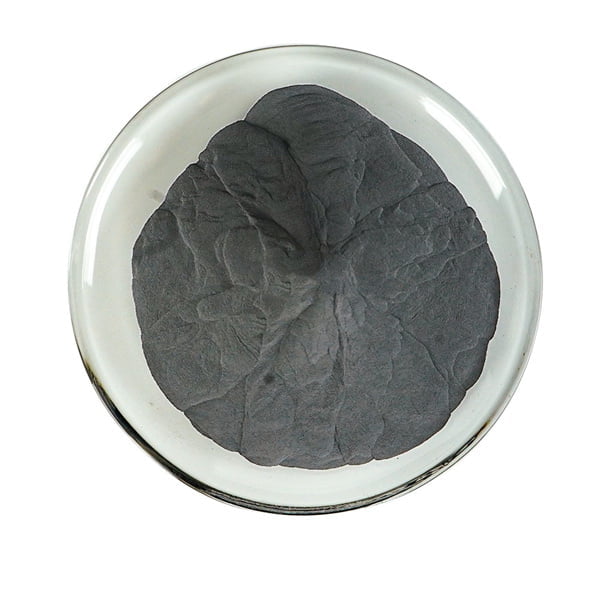
Hier is een tabel met enkele belangrijke overwegingen voor verschillende typen DED metaalpoeders:
Gewenste Onderdeeleigenschap | Potentiële DED-metaalpoeders | Overwegingen |
---|---|---|
Hoge sterkte-gewichtsverhouding | Aluminium Si7Mg0,3, Titaan Ti-6Al-4V | Beschikbaarheid, kosteneffectiviteit |
Uitstekende prestaties bij hoge temperaturen | Inconel 625, Inconel 718 | Compatibiliteit met DED-systeem |
Goede corrosiebestendigheid | Roestvrij staal 316L, Aluminium Si7Mg0,3 | Milieu-impact |
Hoge slijtvastheid | Kobaltchroom CoCrMo, gereedschapsstaal H13 | Eisen aan oppervlakteafwerking |
Biocompatibiliteit | Roestvrij staal 316L, Titanium Ti-6Al-4V | Gebruikt in speciale voertuigen voor mensen met een handicap |
Onthoud dat het kiezen van het juiste DED metaalpoeder een kritieke stap is om het succes van je project te garanderen. Door de bovenstaande factoren zorgvuldig in overweging te nemen, kunt u het ideale poeder kiezen dat aan uw specifieke behoeften voldoet en optimale resultaten oplevert.
FAQ
Hier zijn enkele veelgestelde vragen (FAQ's) over DED in de autoproductie, gepresenteerd in een duidelijke en informatieve tabel:
Vraag | Antwoord |
---|---|
Wat zijn de belangrijkste voordelen van het gebruik van DED bij autofabricage? | DED biedt ongeëvenaarde ontwerpvrijheid, maakt lichtgewicht voertuigen mogelijk, maakt snelle prototyping en productie op aanvraag mogelijk en maakt reparatie en herfabricage van kritieke onderdelen mogelijk. |
Wat zijn enkele beperkingen van DED? | DED-systemen en metaalpoeders kunnen duur zijn in vergelijking met traditionele methoden. De opbouwsnelheid kan lager zijn voor grote volumes, de oppervlakteafwerking kan nabewerking vereisen en het proces vereist een zorgvuldige controle voor een consistente productkwaliteit. |
Welke soorten metaalpoeders worden vaak gebruikt in DED voor toepassingen in de auto-industrie? | Roestvrij staal 316L, Inconel 625, aluminium Si7Mg0,3, titanium Ti-6Al-4V, nikkellegering 718 en nog veel meer, elk met specifieke eigenschappen die geschikt zijn voor verschillende toepassingen. |
Is DED geschikt voor massaproductie? | Hoewel DED momenteel niet ideaal is voor massaproductie van eenvoudige onderdelen, wordt het steeds haalbaarder voor kleinere series, hoogwaardige onderdelen of onderdelen met complexe geometrieën. |
Hoe beïnvloedt DED de toekomst van de auto-industrie? | DED zal naar verwachting een belangrijke rol spelen in de toekomst van de autofabricage, door lichtere, zuinigere voertuigen, snellere ontwikkelingscycli en duurzamere fabricagepraktijken mogelijk te maken. |
Door het potentieel en de beperkingen van DED te begrijpen, evenals de fijne kneepjes van de selectie van DED-metaalpoeder, kunnen autofabrikanten deze transformatieve technologie gebruiken om de volgende generatie voertuigen te creëren.
Delen op
MET3DP Technology Co, LTD is een toonaangevende leverancier van additieve productieoplossingen met hoofdkantoor in Qingdao, China. Ons bedrijf is gespecialiseerd in 3D printapparatuur en hoogwaardige metaalpoeders voor industriële toepassingen.
Onderzoek om de beste prijs en een op maat gemaakte oplossing voor uw bedrijf te krijgen!
gerelateerde artikelen
Over Met3DP
Recente update
Ons product
NEEM CONTACT MET ONS OP
Nog vragen? Stuur ons nu een bericht! Na ontvangst van uw bericht behandelen wij uw verzoek met een heel team.
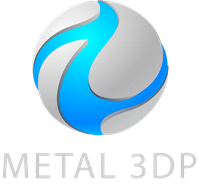
Metaalpoeders voor 3D printen en additieve productie