Power Distribution Plates for EVs via Metal 3D Printing
Inhoudsopgave
Introduction: Revolutionizing EV Power Distribution with Metal Additive Manufacturing
The electric vehicle (EV) revolution is rapidly reshaping the automotive landscape, driven by a global push towards sustainability, reduced emissions, and enhanced energy efficiency. At the heart of every EV lies a complex network of electrical and electronic systems, managing everything from propulsion and battery charging to infotainment and safety features. Central to this intricate architecture is the Power Distribution Unit (PDU), often realized as a sophisticated Power Distribution Plate or Box. This critical component acts as the central nervous system for the vehicle’s high-voltage power flow, ensuring safe, reliable, and efficient delivery of energy from the battery pack to all essential systems. As EV technology advances, pushing the boundaries of performance, range, and charging speed, the demands placed on these power distribution components are escalating dramatically. Engineers face mounting pressure to develop solutions that are not only electrically robust but also lightweight, compact, and thermally efficient – often within tightly constrained packaging envelopes. Traditional manufacturing methods, such as casting, stamping, forging, and machining complex assemblies from multiple parts, are increasingly hitting limitations in meeting these multifaceted requirements, especially when rapid innovation cycles and design flexibility are paramount.
Enter metal additive manufacturing (AM), more commonly known as metal 3D printing. This transformative technology is rapidly moving beyond prototyping and into the realm of functional part production across demanding industries, including aerospace, medical, and, increasingly, automotive. Metal AM offers a paradigm shift in how complex components like EV power distribution plates can be designed and manufactured. By building parts layer by layer directly from digital models using high-performance metal powders, AM unlocks unprecedented design freedom. This allows engineers to create highly optimized, intricate geometries that were previously impossible or prohibitively expensive to produce. Features like integrated cooling channels, complex internal structures for optimized current flow, and topology-optimized lightweight designs become feasible, directly addressing the core challenges of modern EV development. The ability to consolidate multiple functions and components into a single, monolithic printed part further reduces weight, assembly complexity, potential points of failure, and overall system cost.
This technological leap is particularly relevant for materials crucial to EV power distribution, namely lightweight aluminum alloys like AlSi10Mg and high-conductivity copper alloys such as CuCrZr. Metal AM processes, such as Laser Powder Bed Fusion (L-PBF) and Selective Electron Beam Melting (SEBM), can effectively process these materials, enabling the creation of PDUs with tailored properties – balancing structural integrity, weight savings, and superior electrical and thermal performance. This blog post delves into the specifics of utilizing metal 3D printing for the production of advanced EV power distribution plates. We will explore the critical functions of these components, detail the compelling advantages offered by additive manufacturing, examine the key characteristics of recommended materials like AlSi10Mg and CuCrZr, and provide insights into design considerations, achievable precision, post-processing requirements, and potential challenges. Furthermore, we will guide you on selecting the right manufacturing partner and understanding the cost implications. As a leader in metal AM equipment and materials, Met3dp provides cutting-edge systems and high-quality powders, including advanced gas atomization and PREP technologies for superior powder characteristics, positioning us as an ideal partner to accelerate your organization’s journey into the next generation of EV component manufacturing. Join us as we explore how metal AM is not just an alternative but a powerful enabler for innovation in electric vehicle power distribution.
What are EV Power Distribution Plates and Their Critical Functions?
An Electric Vehicle Power Distribution Plate, often integrated within a larger Power Distribution Unit (PDU) or Junction Box, serves as the primary hub for managing and distributing high-voltage (HV) direct current (DC) power throughout the vehicle. Think of it as the main electrical switchboard or circuit breaker panel specifically designed for the demanding environment and unique requirements of an EV. Its fundamental role is to take the high-voltage energy stored in the main traction battery pack (typically operating between 400V and 800V, or even higher in future architectures) and safely route it to the various high-power consumers within the vehicle.
The key functions and responsibilities of an EV power distribution plate are multifaceted and critical for vehicle operation, safety, and longevity:
- High-Voltage Power Routing: This is the primary function. The plate incorporates conductive pathways, typically in the form of integrated busbars or heavy-gauge conductors, to channel the high currents (often hundreds of amperes) from the battery terminals to components such as:
- Traction Inverter: Converts DC power from the battery to AC power for the electric motor(s).
- On-Board Charger (OBC): Manages the charging process when connected to an AC power source.
- DC-DC Converter: Steps down the high voltage from the traction battery to power the vehicle’s lower-voltage (e.g., 12V or 48V) auxiliary systems (lights, infotainment, control units).
- Electric Climate Control: Powers the high-voltage electric compressor for air conditioning and the PTC heater for cabin heating.
- Battery Thermal Management System: Provides power to pumps and fans responsible for maintaining the battery pack within its optimal temperature range.
- Fast Charging Interface: Manages the connection and high-power flow during DC fast charging.
- Circuit Protection: Safety is paramount in high-voltage systems. The PDU plate integrates critical protective devices to prevent damage from overcurrents, short circuits, or other electrical faults. These typically include:
- Fuses: High-voltage fuses designed to interrupt the circuit safely under fault conditions. These can range from traditional fusible links to advanced pyro-fuses or contactor-integrated fuses for faster response times.
- Contactors (Relays): Electrically operated switches that connect or disconnect the high-voltage battery from the rest of the vehicle system. Main contactors are essential for powering up/down the vehicle and isolating the battery during emergencies or servicing. Pre-charge contactors and resistors are also often included to manage inrush current when the system is first energized.
- Current and Voltage Sensing: Accurate monitoring of the electrical system is crucial for battery management, efficiency calculations, and diagnostics. PDUs often incorporate:
- Current Sensors (Shunts or Hall Effect Sensors): Measure the flow of current through various branches of the HV system.
- Voltage Sensors: Monitor voltage levels at key points, including the main battery connection. This data is fed back to the Vehicle Control Unit (VCU) and Battery Management System (BMS).
- Electrical Isolation and Safety: The design must ensure robust electrical isolation between high-voltage circuits, the low-voltage domain, and the vehicle chassis to prevent electrical shock hazards and ensure electromagnetic compatibility (EMC). This involves careful consideration of creepage and clearance distances, use of appropriate insulating materials where necessary, and secure grounding strategies.
- Thermisch beheer: Distributing high currents inevitably generates significant heat (I²R losses) within the conductive elements (busbars, connections). The PDU plate itself often plays a role in dissipating this heat. Its design must prevent overheating of components like fuses, contactors, and connection points, which could lead to premature failure, increased electrical resistance, or even fire hazards. Efficient thermal management ensures component longevity and reliable system performance under demanding operating conditions (e.g., fast charging, high-power acceleration).
- Mechanical Integration and Packaging: The PDU plate must securely mount all the necessary electrical components (fuses, contactors, sensors, connectors) and provide robust connection points for the high-voltage cables. It needs to fit within the allocated space in the vehicle, often competing with other components, and withstand the harsh automotive environment, including vibrations, shocks, temperature fluctuations, and potential exposure to moisture or contaminants.
- System Interconnection: It provides the physical interface points (e.g., bolted connections, high-voltage connectors) for the large, shielded cables connecting the battery pack and the various HV loads. Ensuring low-resistance, reliable connections is critical to minimize power loss and heat generation.
Traditionally, these plates have been manufactured using methods like stamping and forming copper or aluminum busbars, machining insulating base plates (often from high-performance polymers), and then assembling these multiple components together with fasteners. This often results in bulky, heavy assemblies with numerous connection points that can be sources of resistance and potential failure. The complexity of integrating cooling features, optimizing current paths for minimal losses, and reducing weight and volume using these conventional techniques presents significant challenges, paving the way for innovative solutions like metal 3D printing.
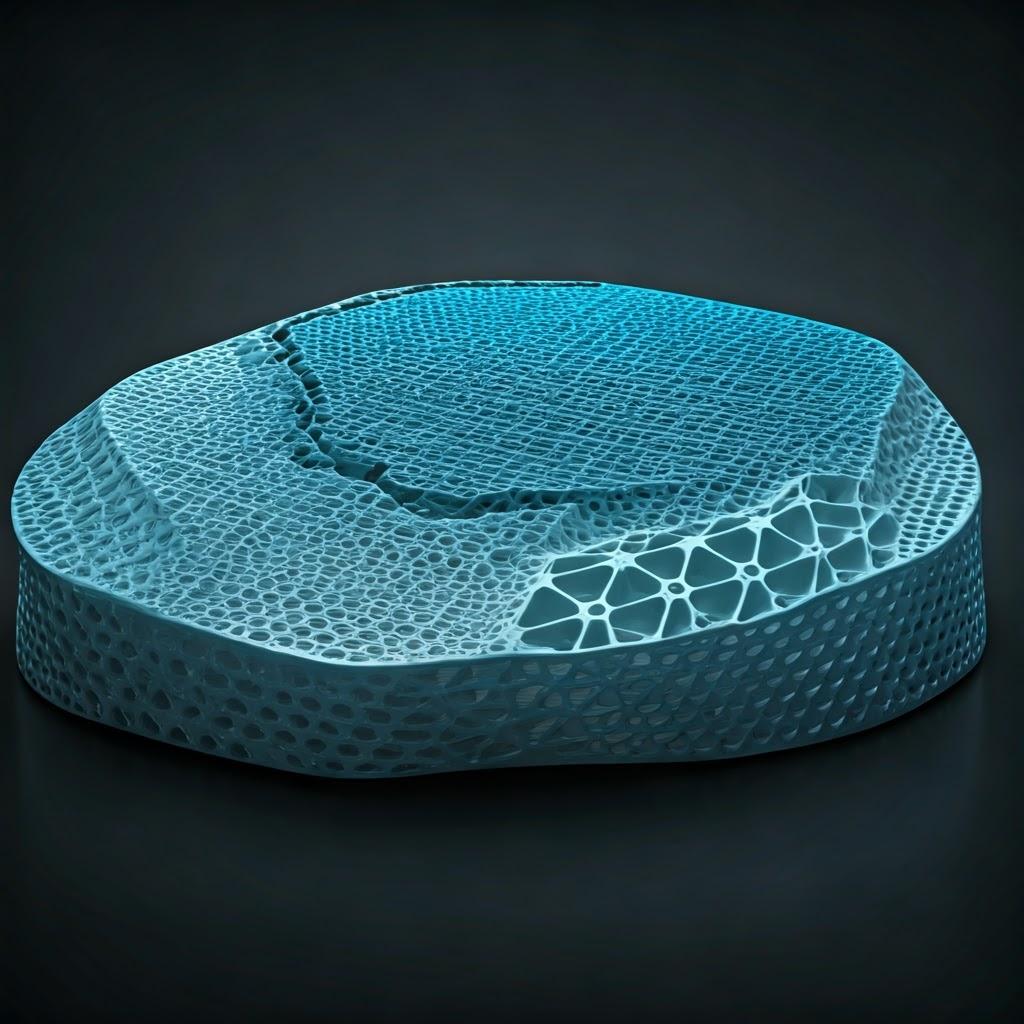
Why Choose Metal 3D Printing for EV Power Distribution Plates?
The demanding requirements of modern electric vehicles – particularly concerning power density, efficiency, weight reduction, and rapid development cycles – often push traditional manufacturing methods to their limits when producing components like power distribution plates. Metal additive manufacturing emerges as a compelling alternative, offering a suite of advantages that directly address these challenges and unlock new possibilities in PDU design and performance. Opting for metal AM, particularly technologies like Laser Powder Bed Fusion (L-PBF) or Selective Electron Beam Melting (SEBM), for EV power distribution plates offers tangible benefits for engineers, procurement managers, and ultimately, the end-user.
Here’s a breakdown of the key reasons why metal 3D printing is increasingly being adopted for these critical components:
- Unmatched Design Freedom and Complexity:
- Uitdaging: Traditional manufacturing methods are often constrained by tooling limitations (molds, dies, cutting tools), making it difficult or impossible to create highly complex, organically shaped geometries. Integrating features like internal cooling channels directly into a busbar assembly is often impractical.
- AM Solution: Metal AM builds parts layer-by-layer, freeing designers from many traditional constraints. This allows for the creation of intricate internal structures, optimized current pathways that minimize length and resistance, and the seamless integration of functional features. For a PDU, this means:
- Conforme koelkanalen: Liquid or air cooling channels can be designed to precisely follow the contours of high-heat areas (e.g., connection points, fuse locations), providing far more effective thermal management than externally attached heat sinks.
- Optimized Busbar Geometries: Conductors can be shaped to manage current density distribution more effectively, potentially reducing hot spots and overall resistance.
- Integrated Sensor Housings: Mounts or enclosures for current and voltage sensors can be built directly into the PDU structure.
- Aanzienlijk potentieel voor lichtgewicht:
- Uitdaging: Every kilogram saved in an EV contributes to increased range and/or improved performance. Traditional PDUs, often assembled from solid metal bars and plates, can be surprisingly heavy.
- AM Solution: Metal AM enables advanced lightweighting strategies:
- Topologieoptimalisatie: Software algorithms can analyze the stress and current load paths within the PDU structure and remove material from non-critical areas, resulting in a functionally optimized, skeletal-like structure that meets all performance requirements with minimum mass.
- Roosterstructuren: Internal lattice or honeycomb structures can be incorporated into non-load-bearing or non-conductive sections of the PDU housing (if printed as part of a consolidated assembly) to drastically reduce weight while maintaining stiffness.
- Materiaalefficiëntie: AM uses material only where needed, minimizing waste compared to subtractive methods like machining, which start with a solid block.
- Part Consolidation and Reduced Assembly:
- Uitdaging: Conventional PDUs are typically assemblies of numerous individual parts: busbars, insulators, brackets, fasteners, connectors, heat sinks. Each part adds weight, requires assembly steps, introduces potential failure points (e.g., loose connections), and complicates the supply chain.
- AM Solution: Metal AM allows designers to consolidate multiple components into a single, monolithic printed part. For instance, a PDU plate could potentially integrate:
- Multiple busbars with complex routing.
- Mounting features for fuses and contactors.
- Structural supports or brackets.
- Integrated cooling structures (channels or fins).
- This consolidation drastically reduces assembly time and labor, simplifies inventory management, improves reliability by eliminating mechanical joints, and often contributes significantly to weight and volume reduction.
- Enhanced Thermal Management:
- Uitdaging: Efficiently removing heat generated by high currents is critical for PDU reliability and performance. Attaching conventional heat sinks adds complexity and may not provide optimal thermal contact or cooling efficiency.
- AM Solution: As mentioned under design freedom, the ability to embed conformal cooling channels directly within the PDU structure is a major advantage. This allows coolant (liquid or air) to flow in close proximity to heat sources, leading to significantly lower operating temperatures for critical components like fuses, contactors, and connection interfaces. This can enable higher current carrying capacity, improve component lifespan, and enhance overall system safety. Even passive cooling can be enhanced by printing complex fin geometries optimized for airflow within the PDU enclosure.
- Snelle prototyping en ontwerpiteratie:
- Uitdaging: Developing and validating new PDU designs using traditional methods involves lead times for tooling (molds, dies) or complex machining setups. Iterating on a design can be slow and expensive.
- AM Solution: Metal 3D printing allows engineers to move directly from a CAD model to a physical metal prototype, often within days rather than weeks or months. This dramatically accelerates the design-build-test cycle. Different design variations for improved performance, weight reduction, or packaging can be quickly manufactured and evaluated, fostering innovation and reducing the overall development time for new EV models or system upgrades.
- Viability for Customization and Low-to-Mid Volume Production:
- Uitdaging: Traditional mass production techniques often require high initial investments in tooling, making them less economical for lower production volumes or customized designs (e.g., for niche vehicles, performance variants, or specialized applications).
- AM Solution: Metal AM is a tool-less manufacturing process. The cost per part is less dependent on volume compared to methods requiring dedicated tooling. This makes it economically viable for:
- Producing parts during the early stages of vehicle production ramps.
- Manufacturing customized PDUs for specific vehicle models or configurations.
- Serving the needs of low-volume EV manufacturers or specialty vehicle converters.
- Producing spare parts on demand.
- Flexibiliteit van het materiaal:
- Uitdaging: Achieving the optimal balance of conductivity, strength, weight, and cost often requires careful material selection. Traditional methods might limit the choice or combination of materials in an integrated design.
- AM Solution: Metal AM allows for the use of specialized alloys tailored for specific requirements. For PDUs, this means readily utilizing materials like AlSi10Mg for lightweight structural elements or heat sinks, and high-conductivity CuCrZr for critical current paths, all within the same technology platform. Companies like Met3dp offer a wide range of qualified metaalpoeders, enabling the selection of the optimal material for the application. While printing multi-material parts in a single build is still an emerging area, AM provides the flexibility to choose the best single material for a consolidated, high-performance design.
In summary, metal 3D printing offers a powerful combination of design flexibility, performance enhancement (lightweighting, thermal management), and manufacturing agility that directly addresses the evolving needs of EV power distribution systems. While challenges remain, the compelling advantages make it an increasingly attractive option for automotive engineers seeking to push the boundaries of electric vehicle technology.
Material Focus: AlSi10Mg and CuCrZr for Optimal EV Performance
The performance, reliability, and safety of an EV power distribution plate are fundamentally dependent on the materials used in its construction. The unique capabilities of metal additive manufacturing allow for the use of advanced alloys that offer specific advantages tailored to the demanding requirements of high-voltage, high-current applications. Among the most promising candidates processed via metal AM for PDUs are aluminum-silicon-magnesium alloys, specifically AlSi10Mg, and copper-chromium-zirconium alloys, notably CuCrZr. Each material brings a distinct set of properties to the table, making them suitable for different aspects or types of PDU designs. Understanding their characteristics is crucial for optimizing the component’s function, weight, and thermal behavior.
AlSi10Mg: The Lightweight Workhorse
AlSi10Mg is one of the most widely used aluminum alloys in metal additive manufacturing, particularly via Laser Powder Bed Fusion (L-PBF). It’s essentially an aluminum casting alloy adapted for AM processes, known for its excellent printability and versatile properties.
- Belangrijkste eigenschappen:
- Lage dichtheid: With a density of approximately 2.67,g/cm3, it’s significantly lighter than copper (approx. 8.9,g/cm3) and steel (approx. 7.8,g/cm3). This is a major advantage for lightweighting EV components.
- Goede verhouding sterkte/gewicht: After appropriate heat treatment (typically stress relief followed by T6 solutionizing and aging), AlSi10Mg achieves good mechanical strength and hardness, suitable for structural components within the PDU.
- Goede thermische geleidbaarheid: While not as conductive as pure aluminum or copper alloys, AlSi10Mg offers respectable thermal conductivity (around 120−140,W/(mcdotK) after heat treatment), sufficient for many heat dissipation tasks within a PDU, such as integrated heat sinks or housing elements.
- Uitstekende corrosiebestendigheid: Aluminum alloys naturally form a passive oxide layer, providing good resistance to atmospheric corrosion.
- Good Weldability/Printability: It is relatively easy to process using L-PBF, allowing for fine features and complex geometries with good density (>99.5%).
- Applications in EV PDUs:
- Structural Housings: The main body or enclosure of the PDU, where lightweighting and structural integrity are key, but electrical conductivity is not the primary requirement.
- Integrated Heat Sinks: Leveraging AM’s design freedom, complex fin structures or liquid cooling channels can be printed directly onto or as part of the housing using AlSi10Mg to manage heat from components like contactors or fuses.
- Mounting Brackets: Consolidating mounting features directly into the PDU structure.
- Busbars (Lower Current Applications): In scenarios where currents are moderate and weight saving is critical, AlSi10Mg busbars might be considered, although copper alloys are generally preferred for high-current pathways due to lower resistive losses.
- Met3dp Capabilities: Met3dp possesses extensive experience in processing aluminum alloys like AlSi10Mg using advanced powder bed fusion techniques. Our understanding of process parameters and post-processing heat treatments ensures that components achieve the desired mechanical properties and dimensional accuracy. Our high-quality gas atomized AlSi10Mg powders contribute to consistent build quality and part performance.
CuCrZr: The High-Conductivity Champion
When maximum electrical and thermal conductivity is paramount, copper alloys are the material of choice. CuCrZr (Copper-Chromium-Zirconium) is a precipitation-strengthened copper alloy that offers an excellent combination of high conductivity and relatively good mechanical strength, particularly at elevated temperatures compared to pure copper.
- Belangrijkste eigenschappen:
- Excellent Electrical Conductivity: Typically achieves >80% IACS (International Annealed Copper Standard), significantly higher than aluminum alloys. This minimizes resistive losses (I²R losses) and heat generation in high-current carrying conductors.
- Hoge thermische geleidbaarheid: With thermal conductivity often exceeding 300,W/(mcdotK), CuCrZr is extremely effective at dissipating heat, making it ideal for thermal management features directly integrated with current paths.
- Good Mechanical Strength: While not as strong as steels, precipitation hardening provides significantly better strength and resistance to softening at higher temperatures compared to pure copper. This is important for maintaining structural integrity and connection clamping force.
- Good Wear Resistance: Offers reasonable resistance to wear.
- Challenges in AM: Printing copper alloys like CuCrZr using laser-based systems (L-PBF) presents challenges due to copper’s high reflectivity and thermal conductivity. It reflects much of the laser energy and rapidly conducts heat away from the melt pool, requiring high laser power and careful process parameter control to achieve stable melting and dense parts. Electron Beam Melting (EBM), like Met3dp’s SEBM technology, can be advantageous for copper due to better energy absorption in a vacuum environment. Sourcing high-quality, spherical copper alloy powders with good flowability, like those produced via Met3dp’s advanced PREP (Plasma Rotating Electrode Process) or specialized gas atomization techniques, is also critical for successful printing.
- Applications in EV PDUs:
- High-Current Busbars: The primary application, leveraging its high conductivity to minimize energy loss and heat generation while carrying hundreds of amperes. AM allows for complex routing and integration within the PDU.
- Terminals and Connectors: Ensuring low-resistance connection points for high-voltage cables.
- Integrated Cooling Features for Conductors: Printing conformal cooling channels directly within or alongside CuCrZr busbars for ultra-efficient thermal management in high-power density applications.
- Fuse Holders/Contacts: Where high current transfer and heat dissipation are critical.
- Met3dp Expertise: Met3dp has invested significantly in developing processes and capabilities for challenging materials like copper alloys. Our advanced powder manufacturing systems, including gasverstuiving en PREP-technologieën, produce high-sphericity, high-flowability CuCrZr powders optimized for AM. Our expertise extends to process parameter development for both L-PBF and our core SEBM (Selective Electron Beam Melting) technology, enabling the production of dense, high-conductivity CuCrZr components for demanding applications like EV power distribution.
Material Selection Matrix (Simplified Comparison):
Eigendom | AlSi10Mg | CuCrZr | Relevance to EV PDU |
---|---|---|---|
Dikte | Low (~2.67,g/cm3) | High (~8.9,g/cm3) | Lightweighting (Advantage: AlSi10Mg) |
Elektrische geleiding | Moderate (~30-40% IACS) | Very High (>80% IACS) | Minimizing power loss in busbars (Advantage: CuCrZr) |
Warmtegeleiding | Good (~120−140,W/mK) | Excellent (>300 W/mK) | Heat dissipation efficiency (Advantage: CuCrZr) |
Mechanische kracht | Good (esp. after T6) | Moderate (Good for Copper) | Structural integrity, connector clamping (Application Dep.) |
High Temp Performance | Gematigd | Good (resists softening) | Reliability under load (Advantage: CuCrZr) |
Printability (L-PBF) | Generally Easier | More Challenging | Manufacturability, Cost |
Cost (Powder) | Lager | Hoger | Overall component cost |
Primary Use Case | Housings, Heat Sinks, Struct. | High-Current Busbars, Conn. | Optimal material for specific function within the PDU |
Exporteren naar Sheets
Conclusion on Materials:
The choice between AlSi10Mg and CuCrZr, or potentially designing a PDU that strategically utilizes components made from both materials (manufactured separately and assembled, or explored via future multi-material AM), depends heavily on the specific requirements of the application.
- Voor maximum electrical efficiency and thermal dissipation in the primary current pathways, CuCrZr is the superior choice, despite its higher density, cost, and printing challenges.
- Voor structural components, housings, and integrated heat sinks where weight saving is paramount and conductivity requirements are less extreme, AlSi10Mg offers an excellent balance of properties and manufacturability.
Metal 3D printing provides the unique capability to effectively process both of these materials, enabling designers to create highly optimized EV power distribution plates that leverage the best properties of each alloy, pushing the boundaries of performance and integration in electric vehicle design. Partnering with a knowledgeable provider like Met3dp, equipped with both advanced powder manufacturing and diverse printing technologies (SEBM and L-PBF), ensures access to the expertise needed to successfully implement these advanced materials.
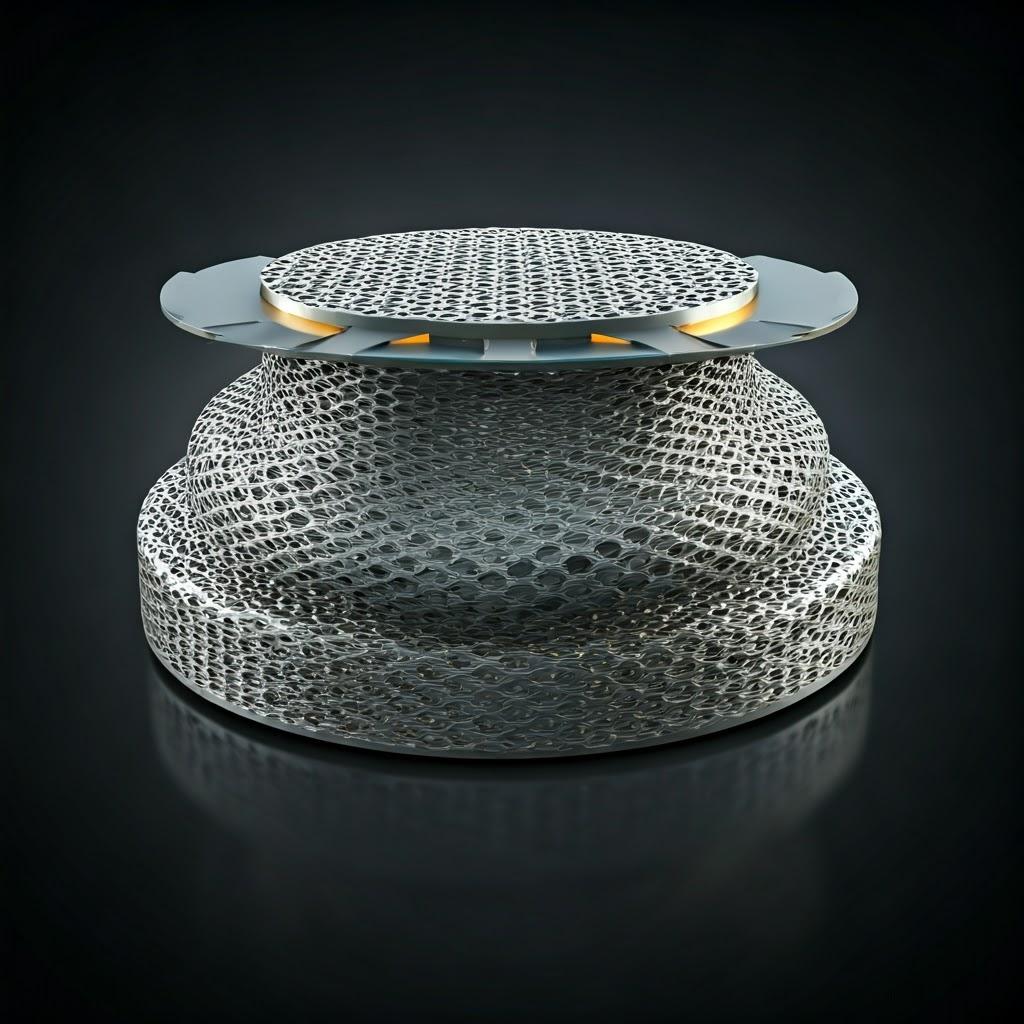
Design Optimization Strategies for 3D Printed Power Distribution Plates
One of the most profound impacts of adopting metaal 3D printen for components like EV power distribution plates lies in the liberation from traditional design constraints. Additive Manufacturing doesn’t just offer a new way to make existing designs; it unlocks the potential to fundamentally rethink how a component is designed to achieve optimal performance, weight, and integration. To truly harness the power of AM, engineers must embrace Design for Additive Manufacturing (DfAM) principles. DfAM is not merely about ensuring a part kan be printed; it’s about actively leveraging the unique capabilities of the layer-by-layer process to create superior components that were previously unimaginable. For EV PDUs, this translates into opportunities for significant advancements in thermal management, lightweighting, electrical efficiency, and system simplification.
Here are key design optimization strategies specifically relevant for 3D printed EV power distribution plates:
- Topology Optimization for Radical Lightweighting:
- Concept: Topology optimization software uses Finite Element Analysis (FEA) to simulate the structural loads, thermal loads, and potentially even current flow paths within a given design space. It then iteratively removes material from areas experiencing low stress or contributing little to the required function, leaving behind an optimized, often organic-looking structure that meets all performance criteria with the absolute minimum amount of material.
- Application for PDUs:
- Structural Elements: The housing or mounting features of the PDU can be topology optimized based on mechanical loads (vibration, mounting forces) and mass targets. This can lead to weight reductions of 30-50% or more compared to traditional designs, directly contributing to increased vehicle range.
- Busbars (Carefully Applied): While the primary path needs sufficient cross-section for conductivity, supporting structures or sections of busbars carrying lower currents could potentially be optimized, balancing weight reduction against electrical resistance increases.
- Overwegingen: Requires specialized software and expertise. The resulting organic shapes can be complex to model initially but are readily manufacturable via AM. Validation through simulation and physical testing is crucial.
- Integration of Conformal Cooling Channels:
- Concept: AM allows the creation of complex internal channels that precisely follow the contours of heat-generating components or high-current pathways. This “conformal cooling” is far more effective than traditional methods like attaching external heat sinks or drilling straight cooling lines.
- Application for PDUs:
- Direct Busbar Cooling: Liquid or air cooling channels can be embedded directly within or alongside high-current CuCrZr busbars, targeting hotspots at connection points or areas of high current density. This allows for higher current ratings within the same footprint or reduces operating temperatures for enhanced reliability.
- Component Cooling: Channels can be routed beneath mounting locations for fuses, contactors, or power resistors to actively draw heat away.
- Optimized Flow Paths: Internal channel geometries can be designed with features like turbulators or complex paths to maximize heat transfer efficiency between the component and the coolant.
- Overwegingen: Requires careful CFD (Computational Fluid Dynamics) analysis to optimize flow rates and heat transfer. Ensuring complete powder removal from these intricate channels during post-processing is critical (more on this later). Wall thickness must be sufficient to contain coolant pressure and prevent leakage.
- Leveraging Lattice Structures:
- Concept: Lattice structures are repeating unit cells (like honeycombs, cubic lattices, or more complex gyroids) that create a component that is mostly empty space but retains significant structural stiffness or other functional properties.
- Application for PDUs:
- Housing/Structural Lightweighting: Sections of the PDU housing not subjected to primary loads can be filled with lattice structures instead of solid material, offering extreme weight savings while maintaining necessary rigidity.
- Vibration Damping: Certain lattice geometries can possess excellent energy absorption properties, potentially helping to dampen vibrations experienced in the automotive environment, protecting sensitive electrical components.
- Enhanced Passive Cooling: Open-cell lattice structures can increase surface area for improved convective heat transfer if integrated into external surfaces or combined with airflow paths.
- Overwegingen: Requires specialized design software. Selection of unit cell type and density depends on the required properties (stiffness, permeability, surface area). Ensuring powder removal from complex lattices can be challenging.
- Part Consolidation for Simplification and Reliability:
- Concept: AM’s ability to create complex, monolithic parts allows designers to combine multiple, previously separate components into a single printed entity.
- Application for PDUs: This is a major driver for using AM. Examples include:
- Integrated Busbar Assembly: Printing multiple busbars with their complex 3D routing, connection points, and potentially even mounting features as one single piece, eliminating numerous bolted or welded joints.
- Housing + Busbars + Cooling: Printing a PDU housing (e.g., in AlSi10Mg) that incorporates integrated CuCrZr busbar sections (potentially requiring advanced multi-material AM or a hybrid approach) and embedded cooling channels.
- Bracket + Heat Sink + Housing: Combining mounting brackets, passive cooling fins, and the main PDU structure into one part.
- Voordelen: Reduced part count, simplified supply chain, faster assembly, lower assembly labor cost, elimination of potential failure points (loose connections, interface resistances), often significant weight and volume reduction.
- Designing for Optimal Print Orientation and Support Minimization:
- Concept: How a part is oriented on the build plate significantly impacts print time, surface finish, dimensional accuracy, required support structures, and ultimately, cost. DfAM involves designing parts with AM in mind from the start.
- Application for PDUs:
- Zelfdragende hoeken: Designing overhangs and angled features to be below the critical angle (typically around 45 degrees from the horizontal for L-PBF, though material and parameters influence this) to avoid the need for support structures.
- Accessible Supports: Where supports are unavoidable (e.g., for large flat undersides, specific features), designing them in locations where they can be easily accessed and removed during post-processing without damaging the part. Avoid supports in critical internal channels if possible.
- Leveraging Process Strengths: Understanding the specific capabilities and limitations of the chosen AM process (e.g., L-PBF vs. Met3dp’s SEBM) regarding feature resolution, minimum wall thickness, and support requirements. SEBM, for instance, often requires fewer supports due to the powder cake providing some inherent stability.
- Overwegingen: Requires close collaboration between the designer and the AM service provider (like Met3dp) who understands the nuances of their machines and processes. Simulation tools can help predict support requirements and optimal orientation.
- Incorporating Functional Surfaces and Features:
- Concept: Designing features directly into the print that aid in assembly, identification, or function.
- Application for PDUs:
- Text/Labels: Part numbers, connection identifiers, or logos can be embossed or engraved directly onto the surface.
- Alignment Features: Pins, slots, or keyways can be integrated to aid in the correct assembly of mating components or connectors.
- Textured Surfaces: Specific surface textures can be designed to enhance grip, improve adhesion for potting compounds, or optimize thermal radiation.
By thoughtfully applying these DfAM strategies, engineers can move beyond simply replicating traditionally manufactured PDU designs and instead create next-generation components that are lighter, more thermally efficient, more reliable, and better integrated into the complex EV architecture. This requires a shift in mindset and often collaboration with AM experts, like the team at Met3dp, who can provide guidance on leveraging the full potential of the technology.
Achievable Tolerances, Surface Finish, and Dimensional Accuracy in Metal AM
While metal additive manufacturing offers unparalleled design freedom, it’s crucial for engineers and procurement managers to understand the levels of precision, surface quality, and dimensional consistency achievable with current technologies like Laser Powder Bed Fusion (L-PBF) and Selective Electron Beam Melting (SEBM). These factors directly impact the functionality, assembly, and performance of EV power distribution plates, particularly at critical interfaces for electrical connections, sealing, and mounting. While AM parts often require some level of post-processing for final tolerances, understanding the as-built capabilities is essential for effective design and cost estimation.
Key Definitions:
- Maatnauwkeurigheid: How closely the dimensions of the printed part conform to the nominal dimensions specified in the CAD model.
- Precision/Repeatability: How consistently the same dimension can be achieved across multiple parts produced in the same or different builds.
- Tolerance: The permissible range of variation for a given dimension. Tighter tolerances generally mean higher manufacturing costs.
- Oppervlakteafwerking (ruwheid): Measured typically as Ra (arithmetical mean roughness), it describes the texture of the part’s surface. Lower Ra values indicate smoother surfaces.
Typical As-Built Capabilities:
The achievable accuracy and surface finish depend heavily on several factors:
- AM Technology:
- L-PBF: Generally offers finer feature resolution and better surface finish compared to SEBM due to smaller laser spot sizes and thinner layers. Typical Ra values might range from 6,mum to 15,mum on upward-facing or side surfaces, while downward-facing surfaces (supported) are rougher. Dimensional accuracy is often in the range of pm0.1 mm to pm0.2 mm or pm0.1 to pm0.2 of the dimension, whichever is greater, although tighter tolerances are possible with careful process control.
- SEBM (selectief smelten met elektronenbundels): Often operates at higher temperatures with thicker layers, typically resulting in rougher surfaces (Ra often > 20,mum) but potentially lower residual stresses, especially in materials like titanium alloys. Dimensional accuracy might be slightly lower than L-PBF, perhaps in the range of pm0.2 mm to pm0.4 mm, but Met3dp’s advanced SEBM systems strive for industry-leading precision through meticulous calibration and process control. The powder cake in SEBM provides inherent support, potentially simplifying some geometries.
- Materiaal: Different metal powders behave differently during melting and solidification, affecting surface tension, shrinkage, and achievable finish. For instance, printing copper alloys can be more challenging for achieving fine details and smooth surfaces compared to aluminum or titanium alloys. Met3dp’s focus on producing high-quality, spherical powders with optimized particle size distribution through advanced gasverstuiving en PREP-technologieën is crucial for achieving consistent melt pool behavior and better surface quality.
- Part Geometry and Size: Large, complex parts are more prone to thermal distortion and deviation from the intended geometry. Internal features are generally harder to control precisely than external ones.
- Bouwrichting: The orientation of a surface relative to the build direction significantly impacts its roughness. Top surfaces are typically smoothest, vertical walls are intermediate, and downward-facing (supported) surfaces are roughest due to contact with support structures or partially sintered powder.
- Laagdikte: Thinner layers generally lead to better surface finish and accuracy but increase build time and cost. Typical layer thicknesses range from 20,mum to 100,mum.
- Machine Calibration and Process Parameters: Accurate machine calibration, optimized laser/electron beam parameters (power, speed, focus), and controlled atmosphere are essential for achieving consistent results. Reputable providers like Met3dp invest heavily in process monitoring and quality control.
Tolerances and Surface Finish Requirements for EV PDUs:
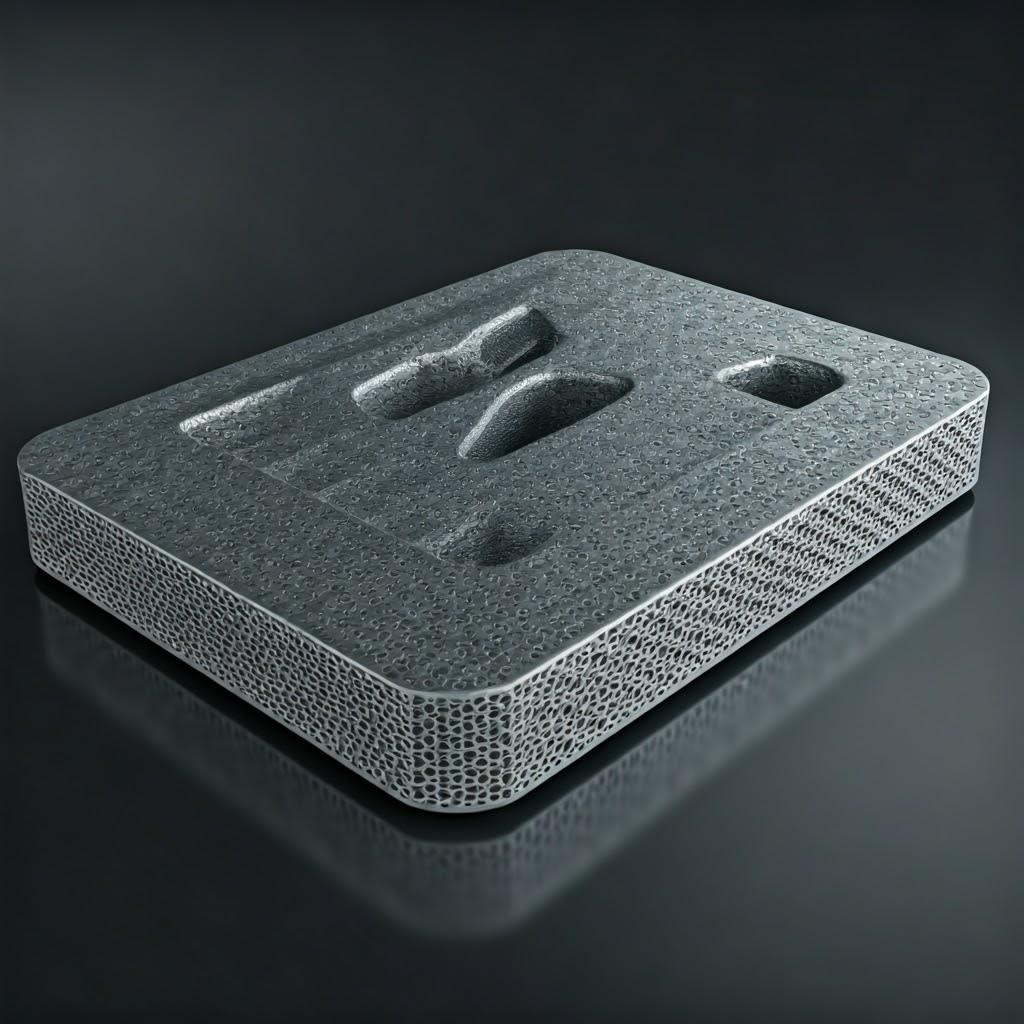
EV power distribution plates have specific areas where tight tolerances and defined surface finishes are critical:
- Electrical Connection Interfaces: Surfaces where busbars connect to each other, to fuses/contactors, or to external cables require flatness and controlled roughness to ensure low contact resistance and prevent overheating. These often require tolerances in the range of pm0.05 mm to pm0.1 mm and smooth finishes (potentially Ra < 3.2,mum), typically achieved through post-machining (milling or grinding).
- Oppervlakken afdichten: If the PDU requires sealing against moisture or contaminants (e.g., O-ring grooves), these surfaces need controlled dimensions and a smooth finish (often Ra < 1.6,mum) to ensure effective sealing. Post-machining is almost always necessary.
- Mounting Holes and Surfaces: Locations where the PDU mounts to the vehicle chassis or where components like contactors are bolted on need accurate positioning and flatness to ensure proper alignment and load distribution. Tolerances might be in the pm0.1 mm range, achievable either as-built (for less critical mounts) or via drilling/milling.
- Component Interfaces: Precise location features for aligning fuses, sensors, or connectors.
Achieving Required Precision:
- As-Built: For less critical features or overall part shape, the as-built accuracy of high-quality AM systems may be sufficient.
- Post-Machining: For critical tolerances and smooth surface finishes, post-process CNC machining is standard practice. Parts are often designed with extra material (“machining stock”) in critical areas specifically for this purpose. The AM process creates the complex near-net shape, and machining provides the final precision where needed.
- Hybride productie: Combining AM with machining in a single setup or process chain.
- Kwaliteitscontrole: Utilizing advanced metrology tools like CMMs (Coordinate Measuring Machines) and 3D scanners to verify dimensions against the CAD model and ensure tolerances are met.
Met3dp’s Commitment to Accuracy: Our company, Met3dp, understands the critical nature of dimensional accuracy and surface finish for functional industrial parts. We employ industry-leading SEBM printers known for their reliability and accuracy, coupled with rigorous process control and quality assurance protocols. Our expertise extends to advising on design for manufacturability, including tolerance expectations and planning for necessary post-machining steps to ensure your EV power distribution plates meet all functional requirements. We work closely with clients to define critical dimensions and develop a manufacturing plan that balances the benefits of AM’s design freedom with the need for precision in key areas.
In conclusion, while metal AM may not achieve the ultra-fine tolerances of precision machining directly “out of the printer,” modern systems offer remarkable accuracy. By understanding the capabilities and limitations, designing accordingly, and incorporating targeted post-machining where necessary, engineers can confidently utilize metal 3D printing to produce highly functional and complex EV power distribution plates that meet stringent automotive standards.
Essential Post-Processing Steps for Functional EV Power Distribution Plates
Producing a dimensionally accurate near-net shape is just the first step in creating a functional metal 3D printed EV power distribution plate. The as-built part, fresh from the printer, requires a series of essential post-processing steps to remove it from the build plate, eliminate support structures, relieve internal stresses, achieve the final desired material properties, meet critical tolerances and surface finish requirements, and ensure it’s clean and ready for assembly. These steps are integral to the manufacturing workflow and must be considered during the design phase and cost estimation. The specific sequence and intensity of post-processing depend on the chosen material (AlSi10Mg or CuCrZr), the complexity of the design, and the specific performance requirements of the PDU.
Here’s a breakdown of common and essential post-processing stages:
- Depowdering / Powder Removal:
- Doel: To remove all residual, unfused metal powder trapped within the part (especially in internal channels, cavities, or lattice structures) and loose powder adhering to the surface.
- Importance for PDUs: This is absolutely critical. Trapped powder in cooling channels will obstruct flow and ruin thermal performance. Loose conductive powder particles elsewhere could cause short circuits or interfere with electrical connections.
- Methoden:
- Manual Brushing/Vacuuming: For easily accessible surfaces.
- Compressed Air / Inert Gas Jetting: Blowing powder out of channels and features.
- Vibration: Shaking the part to dislodge trapped powder.
- Bead Blasting (Gentle): Can help remove adhered powder (using appropriate media to avoid contamination).
- Ultrasonic Cleaning: Using ultrasonic baths with appropriate solvents (if compatible with the material).
- Thermal Cycling / Chemical Methods: Specialized techniques sometimes used for very complex internal geometries, although chemical methods need careful consideration regarding material compatibility and environmental impact.
- Verificatie: Often involves weighing the part, visual inspection (borescopes for internal channels), or even CT scanning for critical applications to ensure complete powder removal.
- Stressverlichtende warmtebehandeling:
- Doel: To reduce internal stresses built up in the part during the rapid heating and cooling cycles inherent in the powder bed fusion process. High residual stresses can lead to part distortion (especially after removal from the build plate) or reduced fatigue life.
- Importance for PDUs: Ensures dimensional stability after subsequent processing steps (like machining) and improves the overall robustness and longevity of the component under operational loads and thermal cycling.
- Methode: Heating the part in a controlled atmosphere furnace to a specific temperature below the material’s critical transformation points, holding it for a period, and then cooling it slowly. Parameters vary significantly based on the material (AlSi10Mg vs. CuCrZr) and part geometry. This is often performed while the part is still attached to the build plate to minimize distortion during the treatment itself.
- Onderdeel verwijderen van bouwplaat:
- Doel: To separate the printed part(s) from the metal build plate they were fused to during the printing process.
- Methoden:
- Wire EDM (elektrisch vonken): Precise method, often used for delicate parts or when a clean cut near the part base is needed.
- Bandzagen: Faster method for less critical separations, leaving more material to be machined off later.
- Frezen: Machining the part off the plate.
- Draagstructuur verwijderen:
- Doel: To remove the temporary support structures that were printed to anchor the part to the build plate and support overhanging features during the build.
- Importance for PDUs: Supports are often needed for complex busbar routing, overhangs in housings, or large flat surfaces parallel to the build plate. Their complete removal is necessary for functionality and aesthetics.
- Methoden:
- Manual Breaking/Clipping: Supports are often designed with weaker connection points for easier manual removal.
- CNC Machining (Milling, Grinding): For supports in difficult-to-reach areas or where a smooth surface finish is required after removal.
- Wire EDM: Can be used for intricate support removal.
- Uitdagingen: Accessing internal supports can be difficult (emphasizing DfAM for support minimization). Removal can leave witness marks or rough surfaces requiring further finishing.
- Solution Annealing and Aging (Hardening Heat Treatment – esp. for AlSi10Mg):
- Doel: To achieve the desired final mechanical properties (strength, hardness, ductility). For precipitation-hardening alloys like AlSi10Mg, this typically involves a T6 temper. CuCrZr also benefits from specific aging treatments to optimize its strength and conductivity balance.
- Method (Example: AlSi10Mg T6):
- Oplossing Behandeling: Heating to a high temperature (e.g., ~530°C) to dissolve alloying elements (Si, Mg) into the aluminum matrix.
- Afschrikken: Rapidly cooling (usually in water) to trap the elements in a supersaturated solid solution.
- Artificial Aging: Reheating to a lower temperature (e.g., ~160-180°C) for several hours to allow controlled precipitation of strengthening phases (Mg₂Si).
- Importance for PDUs: Ensures the PDU structure can withstand mechanical loads, vibrations, and stresses from bolted connections without failure. Optimizes material properties for the specific application.
- Afwerking oppervlak:
- Doel: To achieve the desired surface texture for functional or aesthetic reasons.
- Methoden:
- Media Blasting (Sand, Bead, Shot Peening): Creates a uniform matte finish, removes minor surface imperfections, can clean surfaces. Shot peening can also induce compressive residual stresses, improving fatigue life.
- Tuimelende/vibrerende afwerking: Using abrasive media in a rotating or vibrating bowl to deburr edges and smooth surfaces (suitable for batches of smaller parts).
- Grinding/Polishing: Achieving very smooth surfaces (low Ra) for specific requirements like sealing or, in some cases, potentially improving electrical contact (though surface cleanliness is often more critical than extreme smoothness for conductivity).
- Importance for PDUs: Improves appearance, can prepare surfaces for coatings, and ensures uniform texture. Critical for sealing surfaces.
- CNC-bewerking:
- Doel: To achieve tight tolerances, critical dimensions, flat surfaces, and smooth finishes in specific areas that cannot be met by the as-built AM process.
- Importance for PDUs: Absolutely essential for:
- Connection interfaces: Ensuring flatness and parallelism for low contact resistance.
- Sealing grooves: Precise dimensions for O-rings or gaskets.
- Mounting holes/surfaces: Accurate positioning and flatness.
- Component mating features: Ensuring precise fit for fuses, contactors, sensors.
- Methode: Using milling, drilling, turning, or grinding operations to remove material precisely according to the design specifications. Requires careful fixture design to hold the often complex AM part securely.
- Cleaning and Inspection:
- Doel: Final cleaning to remove any machining fluids, debris, or fingerprints. Comprehensive inspection to verify all dimensions, tolerances, and requirements are met.
- Methoden: Aqueous or solvent cleaning, visual inspection, CMM measurements, 3D scanning, potentially NDT (Non-Destructive Testing) like CT scanning to verify internal integrity or powder removal if required by application criticality.
- Optional Coatings/Treatments:
- Doel: To add specific functional properties not inherent in the base material.
- Examples for PDUs:
- Insulating Coatings: Applying dielectric coatings to specific areas to enhance electrical isolation.
- Conductivity Enhancement: Plating surfaces (e.g., silver plating on connection points) to further reduce contact resistance, although often careful cleaning and proper clamping force are sufficient for Al and Cu alloys.
- Corrosiebescherming: Although AlSi10Mg and CuCrZr have inherent corrosion resistance, specific environments might warrant additional protective coatings.
Successfully navigating these post-processing steps requires expertise, the right equipment, and careful planning. Integrating these considerations early in the design phase (DfAM) can significantly reduce complexity and cost. Partnering with a full-service provider or a company like Met3dp, which understands the entire process chain from powder to finished part, is crucial for ensuring that your 3D printed EV power distribution plates are not only innovative in design but also fully functional and reliable in application.
Navigating Common Challenges in 3D Printing EV Power Components
While metal additive manufacturing offers transformative potential for producing advanced EV power distribution plates, the technology is not without its challenges. Successfully implementing AM for these critical, high-performance components requires a deep understanding of potential issues and the strategies needed to mitigate them. Awareness of these challenges allows engineers and manufacturers to proactively address them through design choices, process optimization, and rigorous quality control, ensuring the final parts meet the demanding standards of the automotive industry.
Here are some of the common challenges encountered when 3D printing EV power components like PDUs using materials such as AlSi10Mg and CuCrZr:
- Thermal Management During Printing (Warping, Distortion, Residual Stress):
- Uitdaging: The very high temperatures involved in melting metal powders, followed by rapid cooling, create significant thermal gradients within the part and between the part and the build plate. This leads to internal stresses. If these stresses exceed the material’s yield strength at elevated temperatures, it can cause warping (parts lifting off the plate), distortion (deviation from intended geometry), and potentially even cracking. This is particularly pronounced in large, flat PDU plates or complex geometries.
- Matigingsstrategieën:
- Geoptimaliseerde scanstrategieën: Using specific laser or electron beam scanning patterns (e.g., island scanning, alternating hatches) to distribute heat more evenly and reduce localized stress buildup.
- Build Plate Heating: Pre-heating the build plate (common in both L-PBF and especially SEBM) reduces the thermal gradient between the part and the plate, lowering stress.
- Robust Support Structures: Well-designed supports anchor the part securely to the build plate, resisting warping forces during the build.
- Thermal Simulation: Using process simulation software to predict areas of high stress and potential distortion, allowing for design modifications or optimized orientation/supports before printing.
- Post-Build Stress Relief: Performing a stress relief heat treatment (often while still on the build plate) is crucial to relax internal stresses before part removal and machining. Met3dp utilizes optimized parameters and thermal cycles tailored to specific materials and geometries.
- Porositeitscontrole:
- Uitdaging: Porosity refers to small voids or pores within the printed material. These can arise from gas trapped during powder atomization or melt pool solidification (gas porosity) or from incomplete fusion between powder particles or layers (lack-of-fusion porosity). Porosity can significantly degrade mechanical properties (strength, fatigue life), reduce thermal conductivity, and potentially compromise electrical performance or dielectric strength in critical areas.
- Matigingsstrategieën:
- Hoogwaardig poeder: Using powders with low internal gas content, controlled particle size distribution, and good sphericity/flowability is paramount. Met3dp’s investment in advanced powder production techniques like gasverstuiving en PREP directly addresses this, ensuring powder quality optimized for dense printing.
- Geoptimaliseerde procesparameters: Developing and precisely controlling parameters (laser/beam power, scan speed, layer thickness, hatch spacing, atmosphere control) specific to the material (AlSi10Mg, CuCrZr) and machine to ensure complete melting and fusion.
- Heet isostatisch persen (HIP): A post-processing step involving high temperature and high pressure inert gas to close internal pores. While effective, it adds cost and lead time and may not be necessary if process optimization achieves sufficient density (>99.5% or higher).
- Niet-destructief onderzoek (NDT): Using methods like X-ray computed tomography (CT scanning) to detect and quantify internal porosity in critical parts.
- Printing High-Conductivity / High-Reflectivity Materials (Copper Alloys):
- Uitdaging: Copper and its alloys (like CuCrZr) pose unique challenges, especially for laser-based systems (L-PBF):
- High Reflectivity: Copper reflects a significant portion of the infrared laser energy typically used in L-PBF, making efficient and stable melting difficult without very high laser power.
- Hoge thermische geleidbaarheid: Heat is conducted away from the melt pool very rapidly, requiring precise energy input control to avoid incomplete fusion or excessive vaporization (spatter).
- Gevoeligheid voor oxidatie: Copper readily oxidizes, requiring excellent control of the inert gas atmosphere within the build chamber.
- Matigingsstrategieën:
- Higher Power Lasers / Green Lasers: Using lasers with higher power or shorter wavelengths (like green lasers) which are absorbed more efficiently by copper.
- Geoptimaliseerde procesparameters: Developing specific parameter sets (higher power density, adjusted scan strategies) tailored to copper’s properties.
- Electron Beam Melting (EBM/SEBM): EBM technology, like that used by Met3dp, often shows advantages for copper. The electron beam couples energy more efficiently into reflective materials, and the process operates under a high vacuum, minimizing oxidation risk.
- Poederkwaliteit: Using highly spherical powders with appropriate surface characteristics enhances energy absorption and flowability.
- Uitdaging: Copper and its alloys (like CuCrZr) pose unique challenges, especially for laser-based systems (L-PBF):
- Powder Removal from Internal Geometries:
- Uitdaging: While AM enables complex internal channels for cooling or lightweighting, ensuring complete removal of unfused powder from these tortuous paths after printing can be extremely difficult. Any trapped powder compromises the intended function (e.g., blocking coolant flow, adding dead weight, potential source of contamination).
- Matigingsstrategieën:
- DfAM for Depowdering: Designing internal channels with accessible entry/exit points, minimum diameters, smooth transitions, and avoiding features that create powder traps. Incorporating specific “depowdering holes” that can be sealed later.
- Advanced Depowdering Techniques: Utilizing optimized combinations of vibration, controlled gas flow, potentially specialized solvents or flow systems designed for internal channel cleaning.
- Verificatie: Rigorous inspection using methods like borescopes, airflow tests, or CT scanning to confirm channels are clear.
- Achieving Consistent Material Properties:
- Uitdaging: Ensuring that the mechanical, electrical, and thermal properties of the AM part are consistent throughout the component and repeatable from build to build is crucial for reliable performance, especially in demanding automotive applications. Properties can be influenced by minor variations in powder characteristics, machine calibration, or process parameters.
- Matigingsstrategieën:
- Robust Quality Control: Implementing strict quality control for incoming powder (chemistry, particle size, flowability), rigorous machine calibration and maintenance schedules, in-process monitoring (melt pool monitoring, thermal imaging), and post-build material testing (tensile tests, conductivity measurements on sample coupons).
- Standardized Procedures: Adhering to documented and validated procedures for printing and post-processing.
- Traceerbaarheid: Maintaining detailed records linking specific parts to powder batches, machine parameters, build data, and post-processing steps. Met3dp emphasizes comprehensive quality management systems throughout its operations.
- Surface Finish and Tolerances:
- Uitdaging: As discussed previously, the as-built surface finish and tolerances of AM parts may not meet the stringent requirements of all PDU features, necessitating post-processing like machining, which adds cost and complexity.
- Matigingsstrategieën: DfAM to minimize reliance on critical as-built tolerances where possible, designing for efficient machining access, and realistic tolerance specification based on functional needs.
Navigating these challenges successfully requires a combination of advanced technology, materials science expertise, process control discipline, and often, close collaboration between the component designer and the additive manufacturing provider. Companies like Met3dp, with deep expertise in both SEBM technology and high-performance metal powders, are well-positioned to help customers overcome these hurdles and leverage the full benefits of metal AM for innovative EV components like power distribution plates.
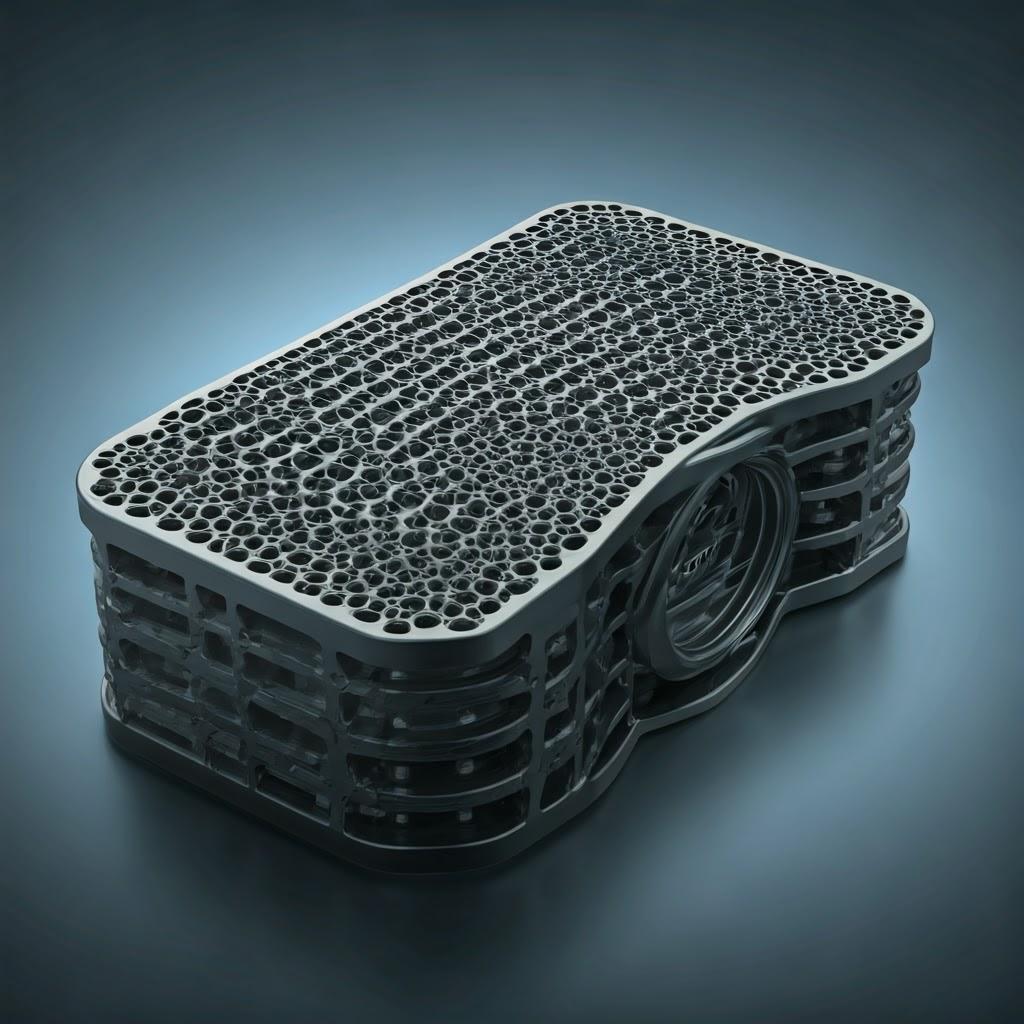
Selecting the Ideal Metal 3D Printing Partner for Automotive Applications
Choosing the right manufacturing partner is as critical as perfecting the design when implementing metal additive manufacturing for demanding applications like EV power distribution plates. The automotive industry operates under stringent requirements for quality, reliability, traceability, and cost-effectiveness. Not all metal AM service providers are equipped to meet these demands. Selecting a partner with the right blend of technical expertise, robust processes, industry experience, and capacity is paramount to ensure project success, from prototype validation to potential series production. For procurement managers and engineers evaluating potential suppliers for 3D printed EV PDUs, a thorough assessment based on several key criteria is essential.
Here’s a guide to selecting the ideal metal 3D printing partner for automotive applications:
- Quality Management Systems and Certifications:
- ISO 9001: This is the foundational requirement for any reputable manufacturing partner, demonstrating a commitment to documented processes, quality control, and continuous improvement.
- IATF 16949: While finding an AM-focused service provider fully certified to IATF 16949 (the global automotive quality standard) might still be challenging, inquire about their alignment with its principles. Look for partners who understand automotive requirements like Production Part Approval Process (PPAP), Failure Modes and Effects Analysis (FMEA), traceability, and stringent process control. Providers serving the aerospace industry (AS9100 certified) often have highly mature quality systems applicable to automotive needs.
- Met3dp Approach: Met3dp Technology Co., LTD operates with rigorous quality management systems governing its powder production and printing processes, ensuring consistency and reliability for industrial applications. We understand the quality expectations of demanding sectors.
- Technical Expertise and Engineering Support:
- Material Science Knowledge: Deep understanding of the specific materials being used (AlSi10Mg, CuCrZr), including their behavior during printing, required heat treatments, achievable properties, and potential failure modes. Look for partners with metallurgists or materials scientists on staff. Met3dp’s roots in both powder manufacturing and printing equipment provide a profound understanding of material-process interactions.
- Design for Additive Manufacturing (DfAM) Expertise: The ideal partner should offer more than just printing services. They should be able to provide expert DfAM consultation, helping optimize your PDU design for printability, performance, support minimization, and cost-effectiveness.
- Process Simulation Capabilities: Experience with simulation tools to predict thermal stresses, distortion, and optimal orientations can de-risk the manufacturing process, especially for complex PDU geometries.
- Post-Processing Know-How: Understanding the nuances of stress relief, heat treatment protocols specific to AM parts, machining strategies for hybrid parts, and effective powder removal techniques is crucial.
- Technology and Equipment:
- Appropriate AM Technology: Ensure the partner possesses the right technology (L-PBF, SEBM) best suited for your material and application. For instance, Met3dp’s specialization in Selectief smelten met elektronenstralen (SEBM) offers distinct advantages for certain materials like titanium alloys and potentially copper alloys due to the vacuum environment and energy coupling characteristics. They should also have capabilities in L-PBF if that’s the preferred route for materials like AlSi10Mg.
- Machine Park: Assess the number, type, and build volume of their machines. Sufficient capacity ensures reasonable lead times and provides redundancy. Look for modern, well-maintained equipment from reputable manufacturers. Met3dp designs and builds its own SEBM printers, ensuring deep system knowledge and control.
- Powder Handling and Management: Strict protocols for storing, handling, sieving, and recycling metal powders are essential to maintain powder quality and prevent cross-contamination. Met3dp’s expertise extends to its own advanced powder manufacturing system, ensuring quality control from the source.
- Process Control and Quality Assurance:
- Gedocumenteerde procedures: Manufacturing processes, from build setup to post-processing and inspection, should be clearly documented and strictly followed.
- Material Traceability: Robust systems for tracking powder batches from supplier through production to the final part are critical for automotive applications.
- Procesbewaking: Advanced partners may utilize real-time monitoring tools (e.g., melt pool monitoring, thermal imaging) to detect potential anomalies during the build process.
- Metrology Capabilities: Access to appropriate inspection equipment, such as Coordinate Measuring Machines (CMMs), 3D scanners, and potentially NDT equipment (CT scanning), to verify dimensional accuracy and internal integrity.
- Industry Experience and Track Record:
- Automotive/EV Experience: Has the provider worked on similar projects within the automotive sector, particularly with EV components? Understanding the specific challenges and requirements of the industry is invaluable.
- Case Studies/References: Ask for examples of relevant projects and client references.
- Experience with Demanding Applications: Success in other high-stakes industries like aerospace or medical often indicates a mature quality and process control environment. Met3dp proudly serves mission-critical applications in aerospace, medical, and automotive fields.
- Capacity, Lead Time, and Scalability:
- Current Capacity: Can the provider meet your required volumes within acceptable lead times?
- Scalability Plan: If you anticipate moving from prototypes to low or medium volume production, does the partner have a credible plan for scaling up capacity to meet future demand?
- Communication and Project Management: Clear communication channels and effective project management are essential for a smooth partnership.
- Location and Logistics:
- Shipping Expertise: Experience in packaging and shipping sensitive, high-value metal AM parts.
- Proximity: While not always the deciding factor, regional proximity can sometimes simplify logistics and communication. Met3dp, headquartered in Qingdao, China, serves a global clientele with robust logistics capabilities.
Evaluation Checklist Summary:
Criteria | Belangrijke overwegingen | Met3dp Strength Highlight |
---|---|---|
Kwaliteitssystemen | ISO 9001, IATF/AS9100 awareness/alignment, PPAP understanding | Rigorous industrial quality management |
Technische expertise | Material science, DfAM support, Simulation, Post-processing know-how | Deep material & process understanding (powder + printers), comprehensive solutions |
Technologie en apparatuur | Appropriate AM tech (L-PBF/SEBM), Build volume, Capacity, Powder handling | Specialization in SEBM, In-house printer design, Advanced powder manufacturing |
Process Control & QA | Documented procedures, Traceability, In-process monitoring, Metrology capabilities | Emphasis on process control, comprehensive QA |
Industriële ervaring | Automotive/EV projects, Demanding applications (Aerospace, Medical) | Proven track record in mission-critical sectors including automotive |
Capacity & Scalability | Current capacity, Lead time estimates, Future scaling potential | Geared for industrial applications, partnership approach for growth |
Communication & Logistics | Project management clarity, Shipping experience | Global reach, responsive customer support |
Exporteren naar Sheets
Selecting the right partner is an investment in mitigating risk and ensuring the successful adoption of metal AM for your critical EV components. A thorough evaluation based on these criteria will help identify a supplier like Met3dp that possesses the necessary technical prowess, process discipline, and automotive understanding to deliver high-quality, reliable power distribution plates.
Understanding Cost Drivers and Lead Times for 3D Printed EV PDUs
While metal additive manufacturing enables the creation of highly optimized and complex EV power distribution plates, understanding the factors that influence production cost and lead time is crucial for project planning, budgeting, and evaluating its economic viability compared to traditional methods, especially as volumes increase. Unlike mass production techniques where tooling amortization dominates low-volume costs, AM costs are more directly tied to material consumption, machine time, and labor-intensive post-processing.
Key Cost Drivers for Metal AM:
The final cost of a 3D printed EV power distribution plate is a composite of several factors:
- Materiaalkosten:
- **Powder Price ($/kg):** This varies significantly between materials. High-performance copper alloys like CuCrZr are typically considerably more expensive than common aluminum alloys like AlSi10Mg. Specialized or customized alloy powders will also command a premium. Met3dp’s efficient powder production helps optimize material costs, but inherent alloy differences remain. * **Part Volume & Density:** The actual amount of material fused to create the part. Topology optimization and lattice structures directly reduce this. * **Support Structures:** Material used for supports adds to consumption, though it’s often recycled. * **Powder Waste/Recycling Efficiency:** Some powder degradation occurs during handling and printing. The efficiency of the service provider’s powder recycling process impacts overall material cost attribution. 2. **Machine Time:** * **Build Time:** Often the largest single cost component. It’s primarily driven by: * **Part Height:** The number of layers determines the minimum time (each layer takes a recoating and exposure cycle). Printing parts flatter but wider can sometimes be faster than printing them tall and narrow. * **Part Volume/Area per Layer:** The time required for the laser or electron beam to scan and fuse the cross-sectional area of the part(s) on each layer. * **Complexity:** Highly intricate features or numerous disconnected sections within a layer can increase scanning time. * **Number of Parts per Build (Nesting):** Efficiently packing multiple parts onto a single build plate utilizes the machine time more effectively and reduces cost per part. * **Machine Depreciation & Operating Costs:** The cost of acquiring, maintaining, and operating expensive industrial metal AM systems (including energy, gas consumption) is factored into the hourly machine rate. Met3dp’s reliable SEBM printers are designed for industrial uptime. 3. **Labor Costs:** * **Build Preparation:** CAD file processing, build layout optimization, machine setup. * **Post-Processing Labor:** This can be significant and includes: * Depowdering (can be time-consuming for complex parts). * Part removal from the build plate. * Manual support removal. * Setup and operation for heat treatment cycles. * Setup and operation for CNC machining (if required). * Manual finishing, cleaning, and inspection. * **Skilled Labor:** Experienced technicians and engineers are required for DfAM, process optimization, quality control, and operating the equipment. 4. **Post-Processing Costs:** * **Heat Treatment:** Furnace time, energy consumption, controlled atmosphere costs. * **Machining:** Costs associated with CNC machine time, tooling, fixtures, and programming, particularly if complex multi-axis machining is needed for critical tolerances. * **Surface Finishing:** Costs of media blasting, tumbling, polishing, or specialized coatings. * **Consumables:** Machining fluids, blasting media, cleaning agents. 5. **Quality Assurance and Inspection:** * **Standard Inspection:** Dimensional checks (CMM, scanning), visual inspection. * **Advanced NDT:** Costs associated with non-destructive testing like CT scanning if required for critical internal feature verification or porosity analysis. * **Documentation:** Time associated with generating quality reports and traceability documentation (e.g., for PPAP-like requirements). 6. **Design and Development Costs:** * While not strictly a production cost per part, the initial investment in DfAM, simulation, and prototyping iterations should be considered in the overall project economics. Partnering with an experienced provider like Met3dp can streamline this phase. **Cost Factors Summary Table:** | Cost Category | Primary Drivers | Impact Level | Mitigation/Optimization Strategies | | :—————— | :——————————————————————————- | :—————- | :—————————————————————— | | **Material** | Powder type ($/kg), Part volume, Support volume, Recycling efficiency | High (esp. Copper)| DfAM (Topology Opt.), Material Selection, Efficient Recycling | | Machinetijd | Part height, Volume/Area per layer, Nesting efficiency, Machine rate | Very High | DfAM (Orientation, Complexity), Build Plate Packing, Fast Machines | | Werk | Setup time, Post-processing intensity (Depowdering, Supports, Machining), Skill | High | DfAM (Support Min.), Automation (future), Skilled Workforce | | Nabewerking | Heat treatment cycles, Machining complexity, Finishing needs, Consumables | Medium to High | DfAM (Minimize Machining), Process Optimization | | Quality/Inspection| Required tolerance checks, NDT needs, Documentation level | Low to Medium | Risk-based inspection plan, Standardized Reporting |
Doorlooptijden:
Lead times for metal AM parts can vary significantly based on similar factors to cost:
- Prototypen: Typically the fastest, ranging from a few days to 2-3 weeks, depending on complexity, material availability, and immediate machine availability.
- Productie van kleine volumes: Usually ranges from 3 to 8 weeks, accounting for scheduling, potentially multiple build runs, full post-processing sequences, and quality assurance.
Factors Influencing Lead Time:
- Beschikbaarheid machine: The service provider’s current workload and queue for the specific machine/material required.
- Bouwtijd: Can range from hours to several days for large or tall builds.
- Post-Processing Complexity: Extensive machining, complex heat treatments, or difficult depowdering add significant time.
- Hoeveelheid: Larger batches may require multiple builds and more extensive post-processing coordination.
- Quality Requirements: Stringent inspection and documentation requirements add time.
- Supply Chain: Availability of specific powder batches or external services (e.g., specialized coatings).
Managing Costs and Lead Times:
- Engage Early with AM Partner: Discuss design concepts with providers like Met3dp early to leverage DfAM expertise, get realistic cost/lead time estimates, and identify potential optimizations.
- Optimize Design for AM: Focus on minimizing volume/mass, reducing build height, designing for support-free features where possible, and simplifying post-processing needs.
- Realistic Tolerancing: Specify tight tolerances only where functionally necessary to avoid excessive machining costs.
- Materiaalkeuze: Carefully weigh the performance benefits of more expensive materials (like CuCrZr) against cost implications. Could AlSi10Mg suffice for certain parts of the PDU?
- Clear Requirements: Provide clear drawings, specifications, and quality requirements upfront to avoid delays and misunderstandings.
By understanding these cost and lead time drivers, stakeholders can make informed decisions about utilizing metal AM for EV power distribution plates, balancing the technology’s unique advantages with the project’s budget and timeline constraints.
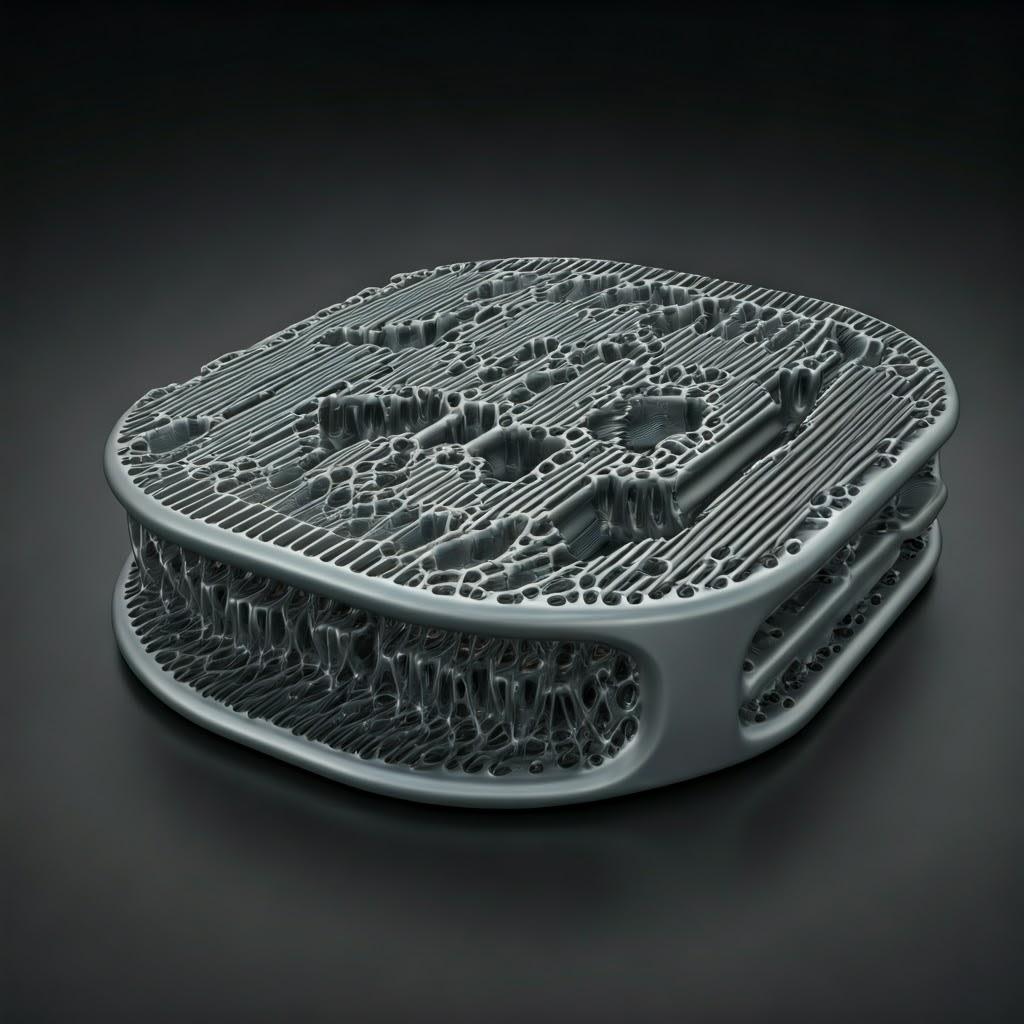
Frequently Asked Questions (FAQ) about 3D Printed EV Power Distribution Plates
As metal additive manufacturing becomes increasingly viable for functional automotive components, engineers and procurement managers often have specific questions regarding its application for critical parts like EV power distribution plates. Here are answers to some frequently asked questions:
1. How does the electrical and thermal conductivity of 3D printed AlSi10Mg or CuCrZr compare to traditional wrought or cast materials?
- Algemene vergelijking: Metal AM parts can achieve conductivity values very close to, but often slightly lower than, their wrought or cast counterparts. This slight reduction is typically attributed to the unique microstructure formed during the rapid solidification process, potential presence of micro-porosity (even in high-density >99.5% parts), and the influence of alloying elements.
- AlSi10Mg: As-printed AlSi10Mg has lower conductivity. After appropriate T6 heat treatment, its electrical conductivity typically reaches around 30-40% IACS (International Annealed Copper Standard), and thermal conductivity is around 120−140,W/(mcdotK). These values are generally suitable for structural components and heat sinks but lower than pure aluminum or conductivity-focused aluminum alloys.
- CuCrZr: The goal for 3D printed CuCrZr is to maximize conductivity while retaining strength. Depending on the print parameters and post-processing (aging treatments), electrical conductivity often reaches >80% IACS, with some processes achieving >90% IACS. Thermal conductivity is similarly high, often >300,W/(mcdotK). These values are excellent for high-current busbars, making AM CuCrZr highly competitive with traditionally manufactured copper components, especially when complex geometries are needed.
- Key Factor: Achieving these high conductivity values in AM parts relies heavily on optimized printing parameters to ensure high density (>99.8%+) and appropriate post-process heat treatments. Partnering with experts like Met3dp who specialize in powder quality and process optimization is crucial. Furthermore, the design of connection interfaces (surface preparation, clamping force) is often more critical for minimizing overall resistance than minor differences in bulk material conductivity.
2. How is high voltage insulation managed in a 3D printed metal PDU? Isn’t the whole part conductive?
- Metal AM Parts are Conductive: Yes, the 3D printed PDU structure made from AlSi10Mg or CuCrZr is electrically conductive. Metal AM does not print the insulators.
- Insulation by Design: High voltage insulation is managed through careful electro-mechanical design, integrating the conductive AM structure with traditional insulating principles and materials:
- Air Gaps (Clearance): Maintaining sufficient distance through the air between conductive elements at different potentials and between conductive elements and the chassis/ground. AM allows complex shapes to optimize these gaps within tight spaces.
- Surface Distance (Creepage): Maintaining sufficient distance along insulating surfaces between conductive elements to prevent tracking currents, especially in potentially contaminated environments.
- Integration with Insulating Materials: Designing the metal PDU plate to interface correctly with separate insulating components made from high-performance polymers (e.g., PBT, PA, PPS). This could involve printing precise mounting features, channels, or pockets for press-fitting or overmolding insulating elements.
- Potting/Encapsulation: After assembly of electrical components (fuses, contactors) onto the printed plate, the entire assembly or critical parts might be potted with a dielectric compound to provide robust insulation and environmental protection. AM can create features to effectively contain and anchor the potting material.
- Coatings: Applying dielectric coatings to specific areas of the metal PDU can provide supplementary insulation, though primary insulation typically relies on gaps and solid insulators.
- AM Advantage: Metal AM allows designers to create more optimized conductive structures (e.g., busbars with integrated mounting) that facilitate cleaner integration with necessary insulating elements, potentially leading to more compact and reliable overall PDU designs compared to traditional assemblies.
3. Is metal AM suitable for high-volume automotive production of PDUs?
- Current State: Currently, metal AM is primarily used for prototyping, tooling, and low-to-mid volume production (hundreds to potentially low thousands of parts per year) in the automotive sector. For very high-volume components (tens or hundreds of thousands per year), traditional methods like stamping, casting, and high-speed machining generally remain more cost-effective due to lower cycle times and established infrastructure.
- Challenges for High Volume:
- Bouwsnelheid: While improving, AM build speeds are still significantly slower than traditional mass production processes.
- Cost per Part: Machine time and powder costs can make the per-part cost higher than conventional methods at large scales.
- Nabewerking: Many manual or semi-automated post-processing steps add time and cost.
- Standardization & Qualification: Industry standards and qualification processes for AM automotive parts are still evolving.
- Future Trends & Niche Applications:
- Faster Machines: Development of multi-laser systems, larger build platforms, and potentially new AM processes promise higher throughput.
- Automatisering: Increased automation in powder handling, build removal, and post-processing will reduce labor costs.
- Kostenbesparing: Decreasing powder costs and improved machine efficiency will make AM more competitive.
- High-Value Niches: AM is likely to be adopted first in high-volume for components where its unique advantages (complexity, consolidation, performance) provide such significant value that it outweighs the higher piece price. Complex PDUs with integrated liquid cooling for high-performance EVs could be such an application.
- Conclusie: While not yet replacing traditional methods for most high-volume parts, metal AM is a viable and rapidly growing solution for moderate volumes and highly complex PDUs where performance and integration benefits are paramount. Its role is expected to expand as the technology matures.
4. What are the typical failure modes for 3D printed PDUs, and how are they addressed?
- Potential Failure Modes: Similar to traditionally manufactured components, but with some AM-specific considerations:
- Electrical Connection Failure: High resistance at bolted joints leading to overheating. Addressed by proper surface preparation (machining), adequate clamping force design, and potentially plating.
- Fatigue Cracking: Due to vibration or thermal cycling, potentially initiating at stress concentrations or internal defects (porosity). Addressed by DfAM (reducing stress risers), topology optimization, robust process control (minimizing porosity), appropriate heat treatments (stress relief, optimizing microstructure), and potentially shot peening.
- Overheating: Insufficient heat dissipation leading to component degradation or failure. Addressed by DfAM (integrated cooling channels), material selection (CuCrZr for high heat loads), thermal simulation, and validation testing.
- Structural Failure: Yielding or fracture under mechanical load. Addressed by proper material selection, DfAM (topology optimization for load paths), appropriate heat treatment for strength, and process control for material integrity.
- Internal Channel Blockage: Incomplete powder removal leading to cooling system failure. Addressed by DfAM (design for depowdering), rigorous cleaning procedures, and verification (airflow test, CT scan).
- Corrosion: Addressed by material selection (AlSi10Mg, CuCrZr have good inherent resistance) and potential coatings if the environment is particularly harsh.
- Mitigation: A combination of robust DfAM, careful material selection, tightly controlled manufacturing processes (like those at Met3dp), appropriate post-processing, and thorough validation testing (thermal, vibration, electrical load cycling) is key to ensuring reliability.
5. Can integrated sensing features be incorporated into 3D printed PDUs?
- Yes, Indirectly and Increasingly Directly:
- Housing/Mounting for Sensors: Metal AM readily allows the design and printing of precise mounting features, housings, or pathways for conventional sensors (e.g., temperature sensors, Hall effect current sensors, voltage sense taps). This integration can be more optimized and compact compared to attaching separate sensor modules.
- Channels for Fiber Optics: Internal channels can be designed into the printed structure to route fiber optic sensors (e.g., for distributed temperature sensing), protecting them while placing them close to critical areas.
- Embedded Structures (Research): Research is ongoing into embedding conductive traces or even functional electronic components within metal AM parts during the build process, but this is not yet commercially widespread for demanding applications like HV PDUs.
- Strain Sensing: The geometry itself can sometimes be designed such that measurable strain in specific locations (using external strain gauges) corresponds to electrical load or temperature, although this is complex.
- Conclusie: While directly printing the sensors themselves within the metal PDU is largely experimental, metal AM provides significant advantages in designing optimized structures for the seamless integration en packaging of separate sensing elements, contributing to smarter and more data-rich power distribution systems.
Conclusion: Accelerating EV Innovation with Advanced Metal 3D Printing
The relentless drive for innovation in the electric vehicle sector demands continuous improvements in power density, efficiency, thermal management, and system integration. The EV power distribution plate, a critical nexus for high-voltage energy flow, stands as a prime example where conventional manufacturing approaches are increasingly challenged to meet the complex, multifaceted requirements of next-generation vehicle architectures. Metal additive manufacturing has emerged not merely as an alternative, but as a powerful enabling technology, offering solutions that directly address these challenges and unlock significant performance and design advantages.
Throughout this discussion, we’ve explored how metal AM technologies like Laser Powder Bed Fusion and Selective Electron Beam Melting allow engineers to fundamentally rethink PDU design. The ability to utilize advanced materials like lightweight, high-strength AlSi10Mg for structural elements and highly conductive, thermally efficient CuCrZr for current pathways opens new avenues for optimization. Key benefits include:
- Ongekende ontwerpvrijheid: Creating complex, topology-optimized geometries, integrated conformal cooling channels, and consolidated assemblies that are impossible or impractical with traditional methods.
- Verbeterde prestatie: Achieving superior thermal management through direct cooling integration, minimizing electrical losses with optimized conductive paths, and improving overall system efficiency.
- Aanzienlijk lichter maken: Reducing component mass through topology optimization and part consolidation, contributing directly to increased vehicle range and performance.
- Accelerated Development: Enabling rapid prototyping and design iteration, shortening development cycles for new EV platforms and components.
- Manufacturing Agility: Providing a viable path for customized designs and low-to-mid volume production runs without the heavy investment in traditional tooling.
While challenges related to process control, post-processing, cost, and scalability exist, they are being actively addressed through technological advancements, materials development, and growing industry expertise. The key lies in understanding both the capabilities and limitations of metal AM and partnering with knowledgeable providers who possess the right equipment, materials expertise, and process discipline.
Met3dp stands at the forefront of this technological wave, offering comprehensive oplossingen voor additieve metaalproductie. With our industry-leading SEBM printers delivering exceptional accuracy and reliability, our advanced in-house powder manufacturing capabilities producing high-quality spherical powders (including AlSi10Mg, CuCrZr, and innovative alloys like TiNi, TiTa, TiAl), and decades of collective expertise, we provide end-to-end support for demanding industrial applications. We partner with organizations in the automotive, aerospace, medical, and industrial sectors to implement 3D printing and accelerate their digital manufacturing transformations.
The journey towards fully optimized electric vehicles requires leveraging cutting-edge manufacturing techniques. Metal 3D printing offers a compelling pathway to create lighter, more efficient, and more reliable power distribution systems, paving the way for the next generation of EVs.
Are you ready to explore how metal additive manufacturing can revolutionize your EV component design? Contact Metal3DP today to discuss your specific challenges and discover how our cutting-edge systems, advanced metal powders, and application development services can power your organization’s additive manufacturing goals and accelerate your path to innovation.
Delen op
MET3DP Technology Co, LTD is een toonaangevende leverancier van additieve productieoplossingen met hoofdkantoor in Qingdao, China. Ons bedrijf is gespecialiseerd in 3D printapparatuur en hoogwaardige metaalpoeders voor industriële toepassingen.
Onderzoek om de beste prijs en een op maat gemaakte oplossing voor uw bedrijf te krijgen!
gerelateerde artikelen
Over Met3DP
Recente update
Ons product
NEEM CONTACT MET ONS OP
Nog vragen? Stuur ons nu een bericht! Na ontvangst van uw bericht behandelen wij uw verzoek met een heel team.
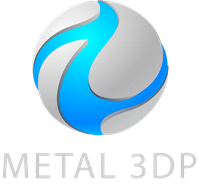
Metaalpoeders voor 3D printen en additieve productie