3D Printed Exhaust Manifolds for Marine Engines
Inhoudsopgave
The relentless pursuit of performance, efficiency, and reliability in the marine industry demands continuous innovation in design and manufacturing. From high-speed racing boats cutting through waves to robust commercial vessels navigating global trade routes, every component plays a critical role. Among these, the exhaust manifold, often subjected to extreme temperatures, corrosive environments, and complex flow dynamics, stands out as a vital element of engine performance and longevity. Traditionally produced through casting or fabrication, these components face limitations in design complexity, material options, and production lead times. However, the advent of metal additive manufacturing (AM), commonly known as metal 3d printen, is charting a new course, offering unprecedented possibilities for creating highly optimized, durable, and customized marine exhaust manifolds. This technological shift is not merely an alternative production method; it represents a fundamental change in how critical marine components can be conceived, designed, and manufactured, promising significant advantages for engine builders, boat manufacturers, and aftermarket suppliers alike.
This exploration delves into the world of 3D printed exhaust manifolds specifically for marine applications. We will examine their function, the compelling reasons to adopt metal AM over conventional methods, and the advanced materials, such as Inconel 625 (IN625) and Copper-Nickel alloys (like CuNi30Mn1Fe), that make this revolution possible. For engineers striving for optimal engine tuning, naval architects seeking weight reduction and enhanced packaging, and procurement managers looking for reliable, high-performance component sourcing solutions, understanding the capabilities of metal 3D printing is becoming increasingly crucial. Companies specializing in this field, particularly those with deep expertise in both advanced printing systems and high-performance material science, are pivotal in bringing these benefits to the marine sector. A prime example is Met3dp, a leading metal additive manufacturing company known for its state-of-the-art equipment and production of specialized metal powders tailored for demanding industrial applications, including the harsh conditions faced at sea. As we navigate through the specifics of this technology, we will uncover how it addresses the unique challenges of the marine environment, paving the way for next-generation propulsion systems.
Introduction: Revolutionizing Marine Performance with 3D Printed Exhaust Manifolds
The exhaust manifold is an unsung hero of the internal combustion engine, particularly in the demanding context of marine propulsion. Its primary role is seemingly simple: collect hot exhaust gases from multiple engine cylinders and funnel them safely out, typically through a wet exhaust system where seawater is injected to cool the gases and muffle sound. However, the conditions under which it operates are anything but simple. Marine exhaust manifolds endure:
- Extreme temperaturen: Rapid cycling from ambient temperatures to potentially hundreds of degrees Celsius during engine operation.
- Corrosieve omgevingen: Constant exposure to hot, acidic exhaust gases internally and, critically, exposure to raw seawater (saltwater) externally or within cooling jackets/wet exhaust sections. This saline environment is notoriously aggressive towards many metals.
- Vibration and Stress: Continuous vibration from the engine and hull movements, imposing mechanical stress on the manifold structure and its mounting points.
- Complex Flow Dynamics: The need to manage exhaust pulses from different cylinders efficiently to minimize backpressure, which directly impacts engine power, torque, and fuel efficiency. Poor flow characteristics can significantly hinder performance.
Traditionally, manufacturers have relied on casting (often using cast iron or specialized stainless steels/bronzes) or fabricating manifolds by welding together pipes and flanges. While effective to a degree, these methods present inherent limitations:
- Casting: Often results in heavy parts with relatively thick walls. Achieving complex internal geometries for optimal flow or integrated cooling can be difficult and expensive due to mold complexity. Porosity can also be a concern. Material choices are limited to those readily castable.
- Fabrication: Allows for more customization but involves multiple welds, which can be potential points of failure or corrosion initiation, especially in saltwater. Achieving perfectly smooth internal transitions for optimal flow can be challenging and labor-intensive. Complex, integrated cooling designs are difficult to implement efficiently.
This is where metal additive manufacturing enters the picture, offering a paradigm shift. By building the manifold layer by layer directly from a digital design file using high-performance metal powders, AM technologies like Laser Powder Bed Fusion (LPBF – encompassing Selective Laser Melting (SLM) and Direct Metal Laser Sintering (DMLS)) enable the creation of parts previously considered impossible or prohibitively expensive.
The AM Advantage in Marine Exhausts:
- Ongekende ontwerpvrijheid: Engineers can design manifolds with organically flowing internal channels optimized via computational fluid dynamics (CFD) to minimize backpressure and maximize engine breathing. Complex cooling jackets, following the exact contours of the hot exhaust passages, can be integrated directly into the part structure, improving cooling efficiency and reducing thermal stress.
- Advanced Material Utilization: AM excels at processing high-performance alloys like Nickel-based superalloys (e.g., Inconel 625) renowned for their exceptional strength at high temperatures and outstanding corrosion resistance in aggressive environments like saltwater. Copper-Nickel alloys (e.g., CuNi30Mn1Fe), famed for their resistance to seawater corrosion and biofouling, can also be effectively processed, offering tailored solutions for specific parts of the exhaust/cooling system. These materials are often difficult or costly to shape using traditional methods.
- Gewichtsvermindering: Through topology optimization algorithms and the ability to create intricate internal structures or thinner, precisely placed walls, AM allows for significant weight reduction compared to cast counterparts, contributing to better vessel performance and fuel economy.
- Deelconsolidatie: Complex assemblies involving multiple cast or fabricated pieces, flanges, and connectors can often be redesigned and printed as a single, monolithic part. This reduces assembly time, eliminates potential leak paths at joints, and simplifies inventory management – a key benefit for wholesale boat parts distributors and manufacturers.
- Customization & Rapid Prototyping: Need a unique manifold for a custom engine build, a racing application, or a prototype? AM allows for rapid iteration and production of bespoke designs without the need for expensive tooling, drastically shortening development cycles.
The emergence of 3D printed exhaust manifolds, leveraging materials like IN625 and CuNi alloys, signifies a major leap forward in marine engine technology. It empowers engineers and designers to overcome the constraints of traditional manufacturing, unlocking new levels of performance, durability, and efficiency. For procurement specialists and B2B buyers in the marine industry, understanding the capabilities and sourcing options for these advanced components is essential for staying competitive and equipping vessels with the best possible technology. Partnering with experienced AM providers who possess both cutting-edge printing technology and deep materials expertise, such as Met3dp with its focus on high-quality powder production and industrial-grade printing solutions, is key to successfully implementing this transformative technology.
What Are 3D Printed Boat Exhaust Manifolds Used For? Applications and Industries
The core function of any exhaust manifold, whether traditionally manufactured or 3D printed, remains the same: to serve as the critical interface between the engine’s cylinders and the exhaust system. It efficiently collects the high-temperature, high-pressure exhaust gases produced during combustion from each cylinder outlet and directs them into a single collector pipe (or sometimes dual pipes in V-engines) which then leads to the rest of the exhaust system (risers, elbows, mufflers, and overboard discharge). Efficient performance of this function is vital for:
- Engine Performance: Minimizing exhaust gas flow restriction (backpressure) allows the engine to “breathe” more easily, improving volumetric efficiency, horsepower, and torque output across the RPM range.
- Fuel Efficiency: Reduced backpressure means the engine doesn’t have to work as hard to expel exhaust gases, leading to improved fuel economy.
- Duurzaamheid: Effectively managing heat and preventing leaks ensures the longevity of the engine and surrounding components.
- Veiligheid: Containing and directing hot, potentially toxic exhaust gases safely away from occupied areas of the vessel.
While the fundamental function is consistent, the specific demands and optimization goals vary significantly across different segments of the marine industry, making metal 3D printing an attractive solution for a wide range of applications:
1. High-Performance Racing Boats:
- Need: Maximum power output, minimal weight, extreme durability under high stress and temperatures.
- AM Advantage: 3D printing allows for highly optimized flow paths, CFD-verified designs to scavenge cylinders effectively, minimal backpressure, significant weight savings through topology optimization, and the use of high-strength, high-temperature superalloys like IN625. Custom designs tailored to specific engine tuning and hull constraints are easily achievable. Part consolidation reduces failure points under intense vibration.
2. Luxury Yachts:
- Need: Smooth, quiet operation, reliability, corrosion resistance for longevity, complex packaging solutions in often tight engine rooms.
- AM Advantage: Integrated water jackets designed using AM can provide superior cooling and sound dampening compared to traditional add-on jackets. The ability to use highly corrosion-resistant alloys like IN625 or potentially CuNi ensures longevity even with constant saltwater exposure. Complex geometries can be realized to fit constrained spaces, and part consolidation improves reliability by minimizing joints. Surface finishing options can provide an aesthetically pleasing appearance if required.
3. Commercial Vessels (Ferries, Workboats, Fishing Vessels):
- Need: Extreme reliability, long service life, fuel efficiency, resistance to harsh operating conditions (including potential impacts or rough handling), ease of maintenance, minimizing downtime.
- AM Advantage: Durability and corrosion resistance offered by materials like IN625 translate directly to longer service intervals and reduced maintenance costs. Optimized flow for fuel efficiency provides significant operational cost savings over the vessel’s lifetime. While initial cost might be higher, total cost of ownership can be lower. The potential for digital inventory and on-demand printing of spares reduces the need for extensive physical stock, which benefits fleet operators and marine component suppliers.
4. Naval Applications:
- Need: High shock resistance, specific acoustic signatures (or reduction thereof), extreme reliability, adherence to stringent material and manufacturing specifications, often requiring specialized alloys.
- AM Advantage: Metal AM allows for the production of robust components capable of withstanding demanding operational requirements. The ability to work with specialized alloys and achieve complex internal structures (e.g., for noise dampening or specific thermal signatures) is highly valuable. Part consolidation enhances structural integrity. Traceability and process control inherent in quality AM production meet stringent military requirements.
5. Custom Engine Builds and Repowers:
- Need: Bespoke exhaust solutions for unique engine configurations, restorations, or engine swaps where off-the-shelf manifolds are unavailable or unsuitable.
- AM Advantage: Additive manufacturing eliminates the need for expensive custom tooling or complex fabrication jigs. Designs can be tailored precisely to fit the specific engine and engine bay constraints, ensuring optimal performance and packaging for one-off or low-volume projects. Rapid prototyping allows for quick design validation.
Addressing B2B Needs:
- Marine Engine Manufacturers: Can leverage AM for prototyping new engine designs, offering high-performance options, or developing integrated exhaust/turbocharger solutions. Partnering with an AM supplier like Met3dp provides access to advanced materials and manufacturing capabilities.
- Boat Builders: Can benefit from weight savings, improved packaging options in engine rooms, and enhanced performance/reliability characteristics offered by AM manifolds, contributing to a higher quality end product.
- Aftermarket Suppliers & Wholesale Distributors: Can utilize AM for producing high-performance upgrades, replacements for obsolete cast manifolds, or customized solutions. The concept of a “digital warehouse” where manifold designs are stored and printed on demand offers significant inventory management advantages, reducing capital tied up in stock and allowing for a wider range of specialized parts to be offered. Sourcing these components from a reliable metal AM manufacturer ensures consistent quality for their customer base.
In essence, 3D printed boat exhaust manifolds are not confined to a niche application. Their utility spans the breadth of the marine industry, offering tailored solutions that address the specific performance, durability, packaging, and customization needs of various vessel types and operational profiles. The ability to integrate complex features like optimized flow paths and conformal cooling channels, combined with the use of superior materials, makes them a compelling choice for anyone seeking to push the boundaries of marine engine performance and reliability.
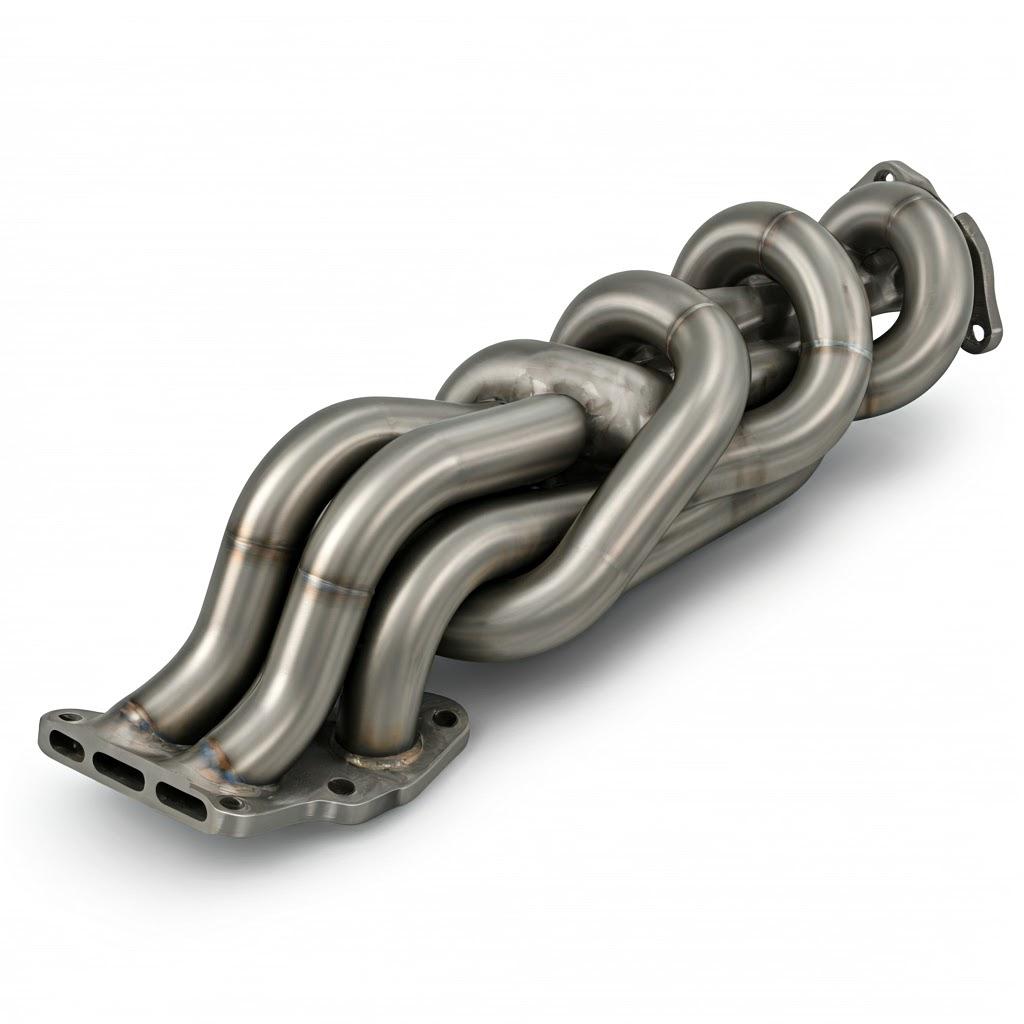
Why Use Metal 3D Printing for Marine Exhaust Manifolds? Advantages Over Traditional Methods
The decision to adopt a new manufacturing technology, especially for critical components like marine exhaust manifolds, requires a clear understanding of its advantages over established methods. While casting and fabrication have served the industry for decades, metal additive manufacturing offers a compelling suite of benefits that address many of the inherent limitations of these traditional processes, particularly when dealing with complex designs and high-performance materials needed for harsh marine environments. Let’s break down the key advantages:
1. Unmatched Design Freedom & Complexity:
- Traditionele beperkingen: Casting is limited by mold design (draft angles, core complexity, minimum wall thickness). Fabricating complex curves and internal features requires skilled labor, multiple steps, and often results in compromises. Integrated features like intricate cooling channels are extremely difficult or impossible to achieve efficiently.
- AM Advantage: AM builds parts layer by layer, freeing designers from many traditional constraints. This enables:
- Optimized Flow Paths: Internal passages can be designed with smooth, organic curves, variable diameters, and CFD-optimized geometries to minimize turbulence and backpressure, directly improving engine performance. Features like pulse-separating dividers within the manifold can be easily incorporated.
- Integrated Cooling Channels: Complex, conformal cooling channels that precisely follow the path of the hot exhaust gases can be designed directly into the manifold’s structure. This leads to far more effective and uniform cooling compared to bolt-on water jackets, reducing thermal stress, increasing part longevity, and potentially lowering engine bay temperatures.
- Feature Integration: Sensor ports, mounting bosses, brackets, and other features can be incorporated directly into the single printed part, reducing assembly complexity.
Comparison Table: Design Freedom
Functie | Gieten | Fabricage | Metal AM (LPBF) |
---|---|---|---|
Internal Geometry | Limited by core complexity, draft angles | Limited by pipe bending, cutting, welding | Highly complex, organic shapes possible |
Cooling Channels | Simple external jackets, limited internal | Very difficult/impractical to integrate | Complex conformal channels easily integrated |
Wanddikte | Relatively thick, less uniform | Determined by pipe/plate stock, weld limits | Optimized, variable thickness possible |
Feature Integration | Limited, requires post-machining | Requires welding/bolting separate parts | High degree of integration possible |
Exporteren naar Sheets
2. Superior Material Properties & Utilization:
- Traditionele beperkingen: Material choices are often limited to those easily cast (cast iron, some bronzes, stainless steels) or readily weldable. High-performance alloys like Nickel-based superalloys (IN625) are notoriously difficult and expensive to cast or machine extensively.
- AM Advantage: AM, particularly LPBF, excels at processing a wide range of advanced metal powders, including:
- Inconel 625 (IN625): Offers an exceptional combination of high strength at elevated temperatures, excellent fatigue resistance, and outstanding resistance to corrosion and oxidation in aggressive marine environments (including chloride pitting and crevice corrosion). Ideal for the hot, corrosive conditions inside an exhaust manifold.
- Copper-Nickel (CuNi30Mn1Fe): Provides unparalleled resistance to general seawater corrosion, stress corrosion cracking, and biofouling, making it suitable for sections potentially exposed to raw water or integrated cooling systems.
- Other Alloys: Potential for using stainless steels (like 316L, though IN625 is generally superior for this application), titanium alloys (for extreme weight saving, though cost is higher), or custom alloys developed for specific needs.
- Hoogwaardige poeders: The final part quality is heavily dependent on the powder quality. Leading providers like Met3dp utilize advanced techniques like gas atomization and PREP (Plasma Rotating Electrode Process) to produce highly spherical metal powders with controlled particle size distribution and high purity. This ensures good flowability in the printer, consistent melting, and results in dense, high-integrity final parts with superior mechanical properties.
3. Significant Weight Reduction:
- Traditionele beperkingen: Cast parts are often bulky with overly thick walls to ensure structural integrity and casting feasibility. Fabricated parts are limited by standard pipe/plate thicknesses.
- AM Advantage:
- Topologieoptimalisatie: Software tools can analyze stress distributions and remove material from non-critical areas, creating lightweight yet strong structures.
- Roosterstructuren: Internal lattice or honeycomb structures can be incorporated to provide stiffness while drastically reducing mass.
- Optimized Wall Thickness: Walls can be designed with precise, variable thickness, adding material only where needed for strength or heat management.
- Result: Weight savings of 30-50% or even more are achievable compared to cast counterparts, contributing to improved vessel handling, potentially higher speeds, and better fuel efficiency.
4. Rapid Prototyping, Customization & On-Demand Production:
- Traditionele beperkingen: Creating prototypes via casting requires expensive tooling (molds, patterns) with long lead times. Customization is often prohibitively expensive for low volumes. Manufacturing relies on established supply chains and minimum order quantities.
- AM Advantage:
- Gereedschapsloze productie: Parts are printed directly from CAD data, eliminating the need for molds or specific tooling.
- Fast Iteration: Design changes can be implemented quickly in CAD and a new prototype printed in days, not weeks or months. This accelerates development cycles for new engine platforms or performance upgrades.
- Cost-Effective Customization: Ideal for one-off parts (custom builds, restorations) or small batch production runs where tooling costs would dominate traditional methods.
- Distributed Manufacturing & Digital Inventory: Designs can be sent electronically to AM service providers globally for local production. Spare parts can be stored as digital files and printed on demand, reducing physical inventory needs and associated costs – a major benefit for global marine operators and parts suppliers.
5. Part Consolidation & Reduced Assembly:
- Traditionele beperkingen: Complex exhaust systems often involve multiple components (manifold sections, collectors, flanges, brackets) bolted or welded together. Each joint represents a potential leak path, a point of stress concentration, and requires assembly labor and additional fasteners/gaskets.
- AM Advantage: AM allows designers to consolidate multiple components into a single, integrated part.
- Voordelen: Reduced part count, simplified assembly, elimination of joints (improving reliability and reducing potential leak paths), lighter overall weight, and potentially lower overall system cost when assembly labor and components are factored in.
Supply Chain & B2B Implications:
For procurement managers and wholesale buyers, the advantages translate into tangible benefits:
- Kortere doorlooptijden: Especially for prototypes and custom parts.
- Veerkracht van de toeleveringsketen: On-demand printing capability reduces reliance on potentially fragile traditional supply chains and large inventory holdings.
- Access to Advanced Technology: Allows offering customers cutting-edge components with superior performance and durability.
- Totale gebruikskosten: While the initial piece price might sometimes be higher than simple castings, the benefits of longer life, reduced maintenance, improved fuel efficiency, and simplified assembly can lead to a lower total cost of ownership.
In summary, metal 3D printing offers a technologically superior approach for manufacturing marine exhaust manifolds, particularly for high-performance, high-value, or customized applications. The ability to combine complex, optimized designs with advanced, corrosion-resistant materials like IN625 and CuNi alloys provides a level of performance and durability that is difficult, if not impossible, to achieve cost-effectively using traditional casting or fabrication methods. Partnering with a knowledgeable AM provider equipped with robust machinery and high-quality materials is key to realizing these significant advantages.
Recommended Materials for 3D Printed Marine Exhausts: IN625 and CuNi30Mn1Fe Deep Dive
Choosing the right material is paramount for the success of any marine component, especially one subjected to the dual attack of high temperatures and corrosive seawater like an exhaust manifold. While various metals can be 3D printed, two alloys stand out for their exceptional suitability in this demanding application: the nickel-based superalloy Inconel 625 (IN625) and specific Copper-Nickel (CuNi) alloys like CuNi30Mn1Fe (often referred to by UNS C71500 or similar designations, though powder metallurgy grades may have specific compositions). Understanding their properties and why they are favored is crucial for engineers and procurement managers sourcing these advanced components. Furthermore, the quality of the metal powder used directly impacts the final part’s integrity, emphasizing the importance of sourcing from reputable suppliers like Met3dp, who leverage advanced powder production technologies.
1. Inconel 625 (IN625 / Alloy 625 / UNS N06625): The High-Performance Champion
Inconel 625 is a nickel-chromium-molybdenum-niobium superalloy renowned for its incredible combination of high strength, toughness, thermal stability, and outstanding corrosion resistance across a vast range of temperatures and environments. It is often the go-to choice for the most demanding sections of marine exhaust systems.
- Key Properties & Benefits for Marine Exhausts:
- Uitzonderlijke corrosiebestendigheid: IN625 exhibits superb resistance to uniform corrosion, pitting, and crevice corrosion in seawater and brackish water. Its high chromium and molybdenum content provide excellent protection against chloride ion attack, a major threat in marine environments. It also resists corrosion from acidic exhaust condensates.
- High Temperature Strength: Maintains significant strength and resists oxidation and scaling at elevated temperatures (up to ~980°C / 1800°F), well within the operating range of marine exhaust manifolds.
- Excellent Fatigue Strength: Crucial for withstanding the vibrations and thermal cycling inherent in engine operation.
- Resistance to Stress Corrosion Cracking (SCC): Highly resistant to chloride-induced SCC, a common failure mode for less robust alloys (like some stainless steels) in marine applications.
- Weldability/Printability: While traditionally known for good weldability, IN625 is also well-suited for processing via Laser Powder Bed Fusion (LPBF). Optimized parameters are needed to manage its susceptibility to solidification cracking, but experienced AM providers can reliably produce dense, high-integrity parts.
- Processing via LPBF:
- IN625 powder is typically processed using SLM or DMLS machines.
- Requires careful control of laser power, scan speed, layer thickness, and build chamber atmosphere (usually Argon) to achieve full density (>99.5%) and minimize defects like porosity or cracking.
- Post-processing, particularly stress relief heat treatment (typically around 870°C / 1600°F) followed by potential solution annealing or aging depending on specific property requirements, is crucial to optimize mechanical properties and ensure dimensional stability.
- Typical Marine Applications:
- Primary exhaust manifold sections directly attached to cylinder heads.
- Exhaust collectors and turbocharger housings.
- High-performance exhaust risers and elbows, especially where high temperatures persist.
- Components requiring maximum durability and longevity in corrosive, high-temperature conditions.
- Sourcing Considerations:
- Poederkwaliteit: Procuring high-quality, spherical IN625 powder with low oxygen content and consistent particle size distribution is vital for successful printing. Suppliers utilizing advanced atomization techniques (like Gas Atomization or PREP, as employed by Met3dp) are preferred. Lot-to-lot consistency is critical for reliable production.
- Expertise leverancier: Partnering with an AM service provider experienced in printing IN625 is essential. They should have validated process parameters and robust quality control measures. Ask for material certifications and part qualification data. B2B buyers should look for IN625 powder suppliers or AM service providers with a proven track record in demanding industries.
Table: Inconel 625 (IN625) Properties Overview (Typical Wrought Values for Reference)
Eigendom | Typische waarde | Significance for Marine Exhaust |
---|---|---|
Dikte | ~8.44 g/cm³ (0.305 lb/in³) | Relatively dense; weight saving achieved through optimized design |
Smeltpunt | ~1290-1350 °C (2350-2460 °F) | High melting point suitable for exhaust temperatures |
Treksterkte (gegloeid) | ~830-1000 MPa (120-145 ksi) | High strength for structural integrity |
Yield Strength (Annealed) | ~415-620 MPa (60-90 ksi) | Resists permanent deformation under load |
Corrosieweerstand | Excellent in seawater, acids, alkalis | Key advantage for longevity in harsh marine environment |
Max Operating Temp. | Up to ~980°C (1800°F) for structural use | Withstands high exhaust gas temperatures |
Thermal Expansion Coeff. | ~12.8 µm/m·°C (7.1 µin/in·°F) @ 20-100°C | Factor in design for thermal stress management |
Exporteren naar Sheets
2. Copper-Nickel Alloy (e.g., CuNi30Mn1Fe / UNS C71500 / “90/10” or “70/30” Variants): The Seawater Specialist
Copper-Nickel alloys, particularly the 70/30 (approx. 70% Cu, 30% Ni with Fe and Mn additions) and 90/10 variants, are famed for their outstanding resistance to seawater corrosion and biofouling (resistance to marine growth attachment). While not possessing the high-temperature strength of IN625, they are excellent choices for components primarily exposed to raw seawater cooling or lower-temperature sections of a wet exhaust system. CuNi30Mn1Fe specifically aligns closely with the 70/30 composition.
- Key Properties & Benefits for Marine Applications:
- Excellent Seawater Corrosion Resistance: Forms a stable, protective surface film in seawater, providing long-term resistance to general corrosion, pitting, and crevice attack. Superior to many stainless steels and bronzes in this regard.
- Weerstand tegen biofouling: Copper ions naturally deter the settlement of marine organisms, keeping surfaces clean and maintaining flow efficiency in cooling channels or seawater pipes.
- Good Ductility and Toughness: Generally ductile materials, though properties can vary based on AM processing.
- Matige sterkte: Lower strength than IN625, limiting its use in highly stressed, very high-temperature primary manifold sections, but often sufficient for risers, elbows, and integrated cooling jackets.
- Goede thermische geleidbaarheid: Higher than IN625, which can be advantageous for heat exchange components.
- Processing via LPBF:
- Printing copper alloys can be challenging due to their high reflectivity and thermal conductivity, requiring higher laser power and careful parameter optimization compared to steels or nickel alloys.
- Maintaining powder quality (low oxygen) is critical, as copper readily oxidizes.
- Achieving full density requires validated process parameters specific to the CuNi alloy being used.
- Post-print heat treatments may be necessary depending on the desired properties.
- Typical Marine Applications:
- Exhaust elbows and risers in wet exhaust systems (especially where seawater injection occurs).
- Integrated seawater cooling jackets or channels within manifolds (potentially as part of a multi-material design, though complex).
- Seawater piping components associated with the exhaust system.
- Heat exchanger components related to engine cooling.
- Sourcing Considerations:
- Specialized Material: CuNi powders for AM are less common than IN625 or stainless steels. Sourcing may require specialized powder suppliers or AM service providers with proven experience in printing copper alloys. Look for CuNi alloy distributors with AM powder expertise.
- Process Validation: Ensure the AM provider has successfully printed the specific CuNi alloy required and can provide data on achieved density and mechanical properties.
Table: Copper-Nickel (CuNi30Mn1Fe – 70/30 Type) Properties Overview (Typical Wrought Values for Reference)
Eigendom | Typische waarde | Significance for Marine Exhaust/Cooling |
---|---|---|
Dikte | ~8.94 g/cm³ (0.323 lb/in³) | Similar density to IN625 |
Smeltpunt | ~1170 °C (2140 °F) | Lower than IN625, suitable for lower temp sections |
Treksterkte (gegloeid) | ~380-450 MPa (55-65 ksi) | Moderate strength, sufficient for many cooling/wet exhaust parts |
Yield Strength (Annealed) | ~140-170 MPa (20-25 ksi) | Lower yield strength than IN625 |
Corrosieweerstand | Outstanding in seawater, resists biofouling | Primary advantage for seawater contact components |
Max Operating Temp. | Limited by strength reduction at high temp | Generally used in lower temp (< 300°C / 570°F) applications |
Warmtegeleiding | ~29 W/m·K | Better heat transfer than IN625, good for cooling |
Exporteren naar Sheets
Material Selection Criteria:
The choice between IN625 and a CuNi alloy (or potentially another material) depends on a careful analysis of the specific operating conditions and requirements:
- Maximum Temperature: If temperatures routinely exceed ~300-400°C, IN625 is generally required for strength retention.
- Primary Failure Mode Concern: If high-temperature strength and resistance to hot exhaust gas corrosion are paramount, IN625 is preferred. If resistance to raw seawater corrosion and biofouling is the main driver (e.g., for a wet elbow), CuNi is a strong contender.
- Structural Loads: For highly stressed components, the superior strength of IN625 is advantageous.
- Weight Sensitivity: Both are dense; weight savings come from AM design optimization, not material choice alone (though Titanium could be considered for extreme cases if cost permits).
- Budget: IN625 powder is generally more expensive than CuNi alloys or stainless steels.
- Supplier Capability: Availability of quality powder and proven printing expertise for the chosen alloy is critical.
Conclusion on Materials:
IN625 and CuNi alloys like CuNi30Mn1Fe represent the pinnacle of material choices for 3D printed marine exhaust components, offering tailored solutions for different parts of the system. IN625 provides unparalleled high-temperature strength and broad corrosion resistance, ideal for the hottest manifold sections. CuNi excels where superior seawater corrosion and biofouling resistance are needed in lower-temperature, raw-water-cooled areas. Leveraging these advanced materials through metal AM requires high-quality powders, such as those produced using Met3dp’s advanced gas atomization processes, and expert printing capabilities to unlock the full potential of performance, durability, and design freedom for next-generation marine exhaust systems. Consulting with material scientists and experienced AM providers is essential for making the optimal selection for your specific application.
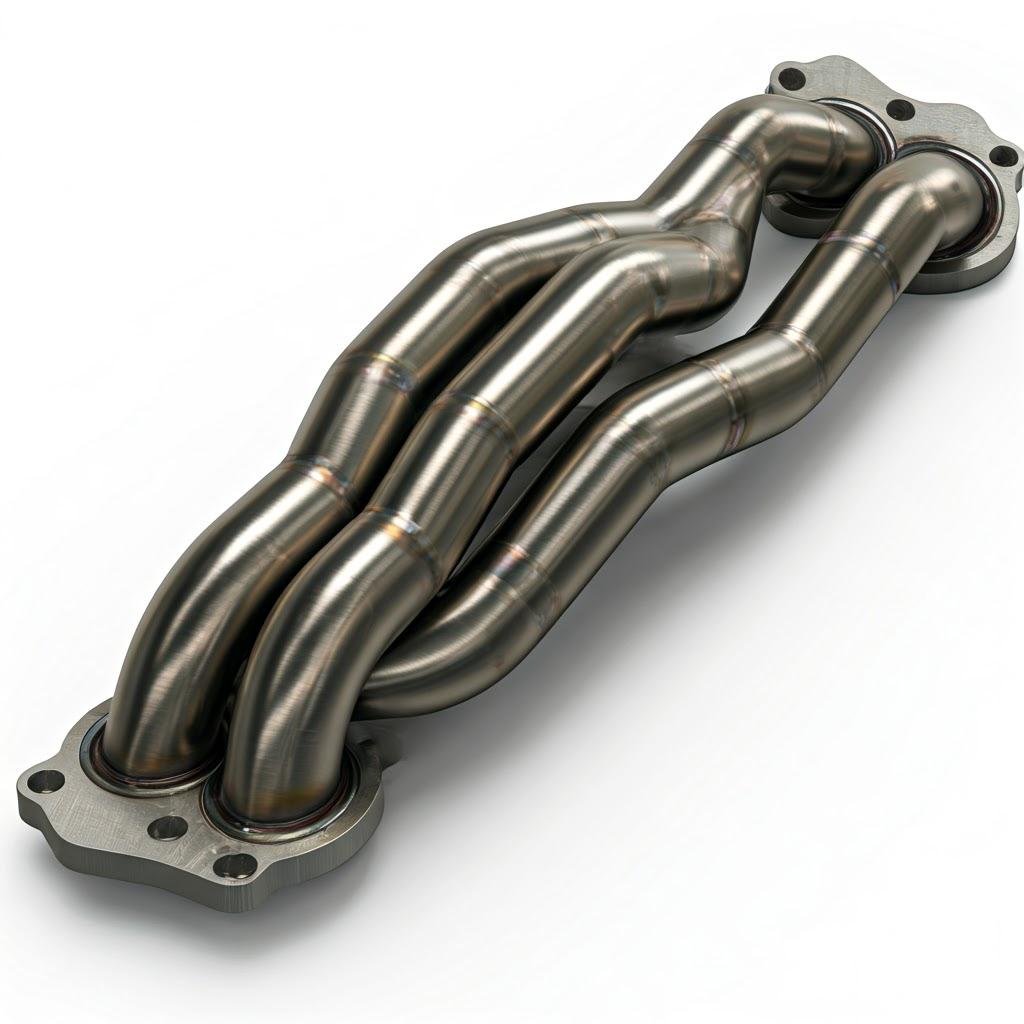
Design Considerations for Additively Manufactured Marine Exhaust Manifolds
The true potential of metal additive manufacturing for marine exhaust manifolds is unlocked not just by the process itself, but by fundamentally rethinking the component’s design. Simply replicating a cast or fabricated design for 3D printing often yields suboptimal results and fails to leverage the unique capabilities of AM. Instead, embracing Design for Additive Manufacturing (DfAM) principles allows engineers to create manifolds that are lighter, stronger, more efficient, and better integrated than ever before. This requires a collaborative approach between marine engineers, who understand the engine and vessel requirements, and AM specialists, who understand the nuances of the printing process and materials. For businesses looking to source high-performance marine components, partnering with an AM provider offering strong engineering support is crucial for maximizing the benefits of this technology.
Here are key design considerations specific to additively manufactured marine exhaust manifolds:
1. Leveraging Design Freedom for Fluid Dynamics:
- Goal: Minimize exhaust backpressure, improve scavenging, and enhance overall engine performance.
- DfAM Approach:
- Organic Flow Paths: Replace sharp bends and abrupt transitions common in fabricated manifolds with smooth, sweeping curves and optimized converging angles (Y-pipes) where cylinder banks merge. Computational Fluid Dynamics (CFD) simulation is invaluable here to model gas flow, identify high-pressure zones, and iteratively refine the internal geometry for minimal resistance.
- Variable Cross-Sections: Design internal passages with continuously varying cross-sectional areas to manage gas velocity and pressure pulses effectively.
- Pulse Tuning Features: Incorporate internal dividers or specific runner lengths (within packaging constraints) to leverage exhaust pulse energy for better cylinder scavenging, particularly in high-performance applications. AM allows these complex internal features to be built monolithically.
- Smooth Internal Surfaces: While as-built AM surfaces have some roughness (discussed later), design choices can minimize features that drastically increase turbulence. Aim for gradual transitions.
2. Integrating Conformal Cooling Channels:
- Goal: Provide highly efficient and uniform cooling to manage thermal stress, increase part longevity, and potentially reduce engine bay heat load. Critical for handling high EGTs (Exhaust Gas Temperatures) and corrosive seawater coolants.
- DfAM Approach:
- Channels Following Hot Spots: Design cooling channels that precisely follow the contours of the hottest exhaust passages, rather than just a simple external jacket. This ensures coolant is directed exactly where needed most.
- Optimized Channel Geometry: Design channel shapes (e.g., teardrop, optimized cross-sections) and internal features (e.g., turbulators, fins – if manufacturable) to maximize heat transfer efficiency from the manifold wall to the coolant.
- Leak-Proof Design: Ensure sufficient wall thickness between exhaust passages and cooling channels. AM allows for complex internal structures, but careful design and process control are needed to guarantee integrity. Pressure testing post-print is essential.
- Inlet/Outlet Ports: Integrate coolant inlet and outlet ports seamlessly into the design, considering standard fitting sizes and accessibility for maintenance.
3. Topology Optimization and Lightweighting:
- Goal: Reduce manifold weight without compromising structural integrity, improving vessel performance and potentially fuel efficiency.
- DfAM Approach:
- Stress Analysis: Use Finite Element Analysis (FEA) to understand the stress distribution under thermal and vibrational loads.
- Material Removal: Employ topology optimization software to automatically remove material from low-stress regions, leaving behind an organic, load-bearing structure.
- Roosterstructuren: Infill sections of the manifold (where structurally appropriate) with lightweight lattice structures instead of solid material. This can significantly reduce mass while maintaining stiffness. Different lattice types (e.g., gyroid, diamond) offer varying properties.
- Optimized Wall Thickness: Instead of uniform thick walls common in casting, design walls with variable thickness, adding material only where needed for pressure containment, heat management, or structural support. Minimum wall thickness will depend on the material (e.g., IN625 vs. CuNi), pressure requirements, and AM process capabilities (typically >0.5mm, but thicker is often needed for robustness).
4. Designing for Manufacturability (DfAM Specifics):
- Goal: Ensure the part can be reliably and cost-effectively printed and post-processed.
- DfAM Approach:
- Minimize Support Structures: Supports are often needed in LPBF to anchor the part to the build plate and support overhanging features. However, they add print time, material cost, and require removal (which can be difficult in internal channels).
- Zelfdragende hoeken: Design overhangs to be below the critical angle (typically around 45 degrees from the horizontal, but process/material dependent) whenever possible.
- Orientation Optimization: Consider the optimal build orientation early in the design phase to minimize the need for supports in critical areas like internal channels or sealing faces.
- Internal Channel Design: Design internal channels with teardrop or diamond shapes rather than purely circular ones to make the upper surfaces self-supporting.
- Accessible Supports: If supports are unavoidable in internal areas, design access ports or pathways for their removal. Sometimes, soluble or easily breakable support structures can be designed.
- Thermisch beheer: Consider heat accumulation during the build. Large solid sections can lead to excessive stress. Incorporating hollow features or lattices can help. Avoid sharp internal corners which can act as stress concentrators.
- Minimum Feature Size: Be aware of the minimum wall thickness, hole diameter, and feature resolution achievable with the chosen AM process and material.
- Powder Removal: Ensure internal cavities and channels have adequate drainage holes for removing unfused powder after the build.
- Minimize Support Structures: Supports are often needed in LPBF to anchor the part to the build plate and support overhanging features. However, they add print time, material cost, and require removal (which can be difficult in internal channels).
5. Integration of Flanges, Ports, and Mountings:
- Goal: Ensure seamless and reliable integration with the engine head, turbocharger (if applicable), exhaust piping, sensors, and vessel structure.
- DfAM Approach:
- Flange Design: Integrate robust flanges designed for proper sealing (consider gasket type). Ensure flange faces are oriented favorably for printing or designate them for post-machining to achieve required flatness and surface finish. Add sufficient material for machining if needed.
- Sensor Ports: Integrate threaded or smooth ports for oxygen sensors, EGT probes, pressure sensors, etc., directly into the manifold body at optimal locations identified through analysis or engine requirements.
- Bevestigingspunten: Design integrated mounting bosses or brackets, ensuring they are robust enough to handle engine vibration and thermal expansion stresses. Consider accessibility for fasteners. FEA is useful for validating mounting point strength.
Collaboration is Key:
Achieving an optimal design for a 3D printed marine exhaust manifold is rarely a solo effort. It requires close collaboration between:
- Marine Engineers: Provide performance targets, packaging constraints, engine interface requirements, operating conditions (temperatures, pressures, coolant type).
- AM Design Specialists: Provide expertise on DfAM principles, material properties (as-printed), process limitations, support strategies, and cost implications of design choices. Companies like Met3dp often have application development teams dedicated to assisting customers in optimizing designs for their specific metaal 3D printen processes and materials.
- Simulation Experts: Conduct CFD and FEA to validate flow performance and structural integrity iteratively throughout the design process.
By considering these factors early and leveraging the expertise of AM partners, manufacturers and suppliers can develop marine exhaust manifolds that truly harness the transformative power of additive manufacturing. This iterative design process, although potentially more involved initially, pays dividends in final part performance, reliability, and potentially lower lifecycle costs, providing a competitive edge for B2B suppliers offering these advanced components.
Achievable Tolerance, Surface Finish, and Dimensional Accuracy in Metal AM Manifolds
While metal additive manufacturing offers incredible design freedom, it’s crucial for engineers and procurement managers to have realistic expectations regarding the achievable precision of 3D printed marine exhaust manifolds. Factors like tolerance, surface finish, and overall dimensional accuracy are critical for ensuring proper fitment, sealing, performance, and interchangeability – key concerns for B2B customers requiring consistent, high-quality parts. While AM may not always match the ultra-high precision of CNC machining in its as-built state, it offers remarkable capabilities, and understanding these nuances is key to successful implementation.
1. Dimensional Tolerances:
- Definitie: Tolerance refers to the permissible range of variation in a dimension of a part.
- Typical AM Capabilities (LPBF): For well-controlled LPBF processes (SLM/DMLS) using materials like IN625 or CuNi alloys, typical achievable tolerances are often cited in the range of:
- ±0.1 mm to ±0.2 mm (±0.004″ to ±0.008″) for smaller features (e.g., up to 25-50 mm).
- ±0.1% to ±0.2% of the nominal dimension for larger features.
- Factors Influencing Tolerance:
- Machinekalibratie: Regular, precise calibration of the AM system (laser spot size, scanner accuracy, Z-axis movement) is fundamental. Providers like Met3dp emphasize the accuracy and reliability of their printers for mission-critical parts.
- Bouwrichting: The orientation of the part on the build plate affects dimensional accuracy due to factors like layer stepping effects on angled surfaces and potential thermal distortion.
- Thermal Stress & Distortion: Residual stresses built up during the layer-wise heating and cooling cycles can cause warping or distortion, impacting final dimensions. This is managed through optimized build strategies, support structures, and post-print heat treatment.
- Poederkwaliteit: Consistent powder particle size, shape (sphericity), and chemistry contribute to stable melting behavior and predictable shrinkage, impacting dimensional control. High-quality powders from sources utilizing advanced atomization are beneficial.
- Nabewerking: Stress relief heat treatment can cause minor dimensional changes that need to be accounted for. Machining operations will achieve much tighter tolerances on specific features.
- Comparison to Traditional Methods:
- Casting: Sand casting typically has much looser tolerances (e.g., ±1 mm or more is common). Investment casting offers better accuracy, potentially approaching AM tolerances in some cases but often still less precise on complex features.
- Fabrication: Tolerances depend heavily on jigging and welding skill, often less precise than AM for complex overall shapes but potentially tighter on specific machined interfaces.
- CNC-bewerking: Offers the highest precision, easily achieving tolerances of ±0.01 mm to ±0.05 mm or better on critical features.
2. Oppervlakteafwerking (ruwheid):
- Definitie: Surface finish, often quantified by Ra (average roughness), describes the texture of a part’s surface. Lower Ra values indicate smoother surfaces.
- Typical As-Built AM Surfaces (LPBF):
- Top Surfaces: Generally the smoothest, potentially Ra 5-10 µm.
- Vertical Walls: Often exhibit layer lines, resulting in Ra values typically ranging from 10-20 µm.
- Upward-Facing Sloped Surfaces: Can be relatively smooth.
- Downward-Facing (Overhang) Surfaces: Tend to be the roughest due to the nature of supporting partially melted powder or contact with support structures. Ra values can exceed 20-30 µm or more.
- Interne kanalen: Surface finish depends heavily on orientation and whether supports were required. Can be challenging to achieve very smooth internal surfaces without post-processing.
- Implications for Manifolds:
- Fluid Flow: Rougher internal surfaces can increase friction and turbulence, potentially impacting exhaust flow efficiency, though the effect depends on the scale of roughness relative to the channel dimensions.
- Sealing: As-built surfaces on flanges are generally too rough for effective metal-to-metal or even standard gasket sealing without post-machining.
- Corrosion: Rougher surfaces have higher surface area and can potentially trap contaminants or create sites for crevice corrosion initiation, although the inherent corrosion resistance of IN625/CuNi is a major mitigating factor.
- Esthetiek: Depending on the application (e.g., luxury yacht), visual appearance might be a factor.
- Verbetering van de oppervlakteafwerking: Post-processing steps like bead blasting, tumbling, abrasive flow machining (for internal channels), electropolishing, or CNC machining are used to achieve smoother finishes where required (detailed in the next section).
3. Ensuring Dimensional Accuracy:
- Importance for B2B: Procurement managers and engineers need assurance that supplied parts consistently meet specifications for reliable assembly and function. This requires robust quality control from the AM service provider.
- Maatregelen voor kwaliteitscontrole:
- Process Monitoring: In-situ monitoring during the build (e.g., melt pool monitoring) can help detect anomalies.
- Dimensionale inspectie: Post-print, parts are typically measured using CMMs (Coordinate Measuring Machines), 3D scanners, or traditional metrology tools to verify critical dimensions against the CAD model and drawing specifications.
- Materiaalcertificering: Ensuring the powder used meets chemical specifications and that the final part properties are as expected (often verified through testing witness coupons built alongside the part).
- Clear Specifications: Providing clear drawings with critical dimensions and tolerances clearly defined is essential for the AM provider to meet expectations. Specify which features require as-built tolerances and which will be post-machined.
Key Takeaways for Engineers and Procurement:
- Specify Critical Tolerances: Clearly identify which dimensions are critical for function (e.g., flange interfaces, port diameters, mounting locations) and define the required tolerances. Assume non-critical dimensions will fall within standard AM process capabilities unless otherwise specified.
- Plan for Post-Machining: For surfaces requiring high precision (e.g., < ±0.1 mm) or very smooth finishes (e.g., Ra < 3.2 µm) for sealing or specific flow requirements, plan for post-print CNC machining of those features. Design the part with sufficient stock material in those areas.
- Discuss Surface Finish Needs: Communicate requirements for internal channel smoothness or external aesthetics with the AM provider to determine appropriate post-processing steps.
- Supplier Evaluation: Choose an AM service provider with robust quality management systems (e.g., ISO 9001 certification), well-maintained and calibrated equipment (like Met3dp’s industrial printers), and experience with the specific material and application. Request sample parts or case studies demonstrating their capabilities.
By understanding the inherent capabilities and limitations of metal AM regarding precision, and by planning for necessary post-processing steps, businesses can confidently leverage 3D printing to produce marine exhaust manifolds that meet demanding fitment and performance requirements.
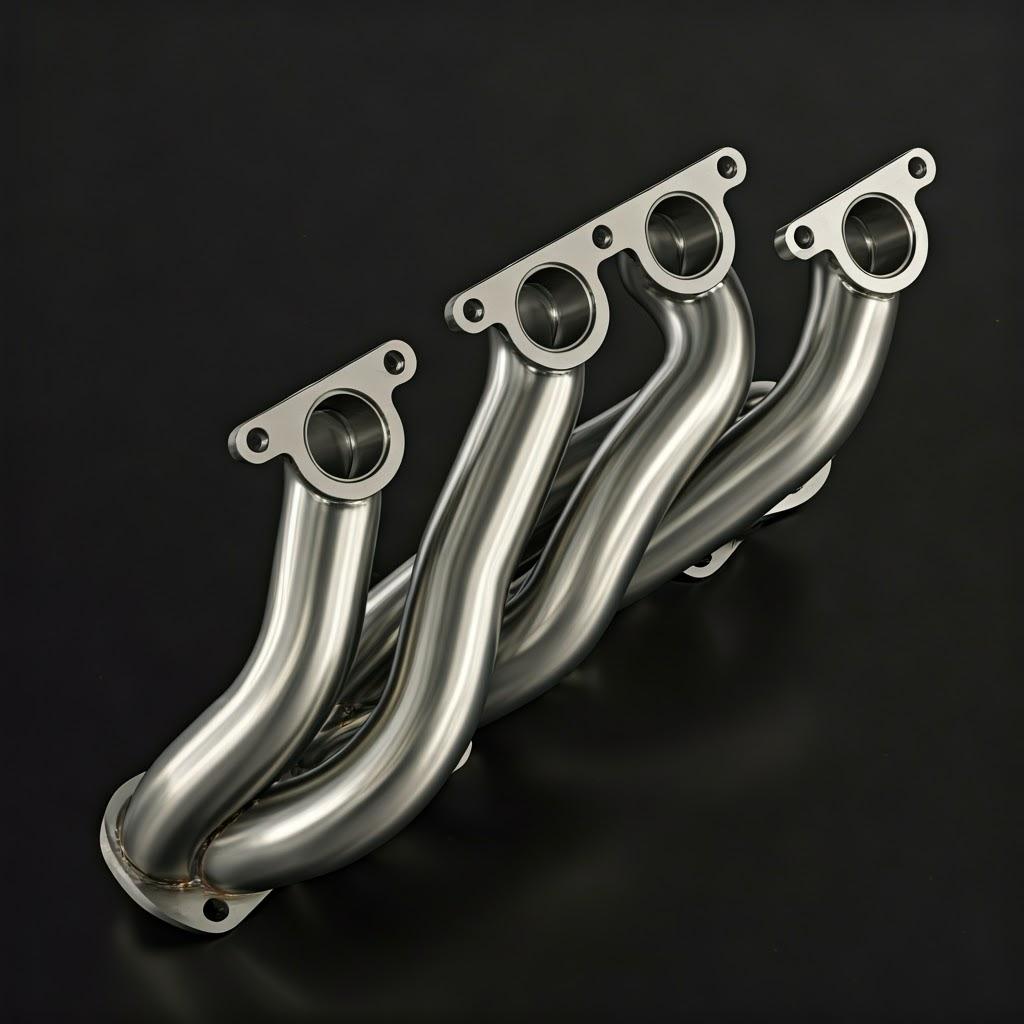
Post-Processing Requirements for 3D Printed Marine Exhaust Manifolds
Obtaining a finished, functional marine exhaust manifold rarely ends when the 3D printer stops. The “green” part emerging from the machine requires several crucial post-processing steps to achieve the desired mechanical properties, dimensional accuracy, surface finish, and overall quality. These steps are an integral part of the additive manufacturing workflow and significantly impact the final cost, lead time, and performance of the component. Understanding these requirements is essential for engineers specifying the part and procurement managers sourcing AM services, as capabilities and costs associated with post-processing can vary between suppliers.
Here’s a breakdown of common post-processing requirements for 3D printed IN625 or CuNi marine exhaust manifolds:
1. Stressverlichting / Warmtebehandeling:
- Doel: To relieve internal stresses built up during the rapid heating and cooling cycles of the LPBF process, improve mechanical properties (ductility, fatigue life), and ensure dimensional stability. Residual stresses can lead to distortion during subsequent machining or cracking in service if not addressed.
- Proces:
- Stress Relief (Common): Typically involves heating the part (often while still attached to the build plate) in a controlled atmosphere furnace (vacuum or inert gas like Argon) to a specific temperature below the aging or annealing temperature, holding it for a set duration, and then cooling slowly. For IN625, this is often around 870-900°C (1600-1650°F). Specific cycles for AM IN625 may vary based on desired properties.
- Solution Annealing / Aging (Less Common for Manifolds, Application Dependent): For IN625, full solution annealing (higher temperatures, e.g., 1100-1150°C / 2000-2100°F) followed by aging treatments can further modify microstructure and mechanical properties (e.g., increase strength), but may not always be necessary or desirable for exhaust manifolds where ductility and stress relief are primary concerns. Heat treatment for AM CuNi alloys is less standardized and depends heavily on the specific alloy composition and desired properties.
- Belangrijk: Considered mandatory for most critical metal AM parts, especially those made from nickel superalloys like IN625, to ensure performance and prevent premature failure.
- Supplier Capability: Ensure the AM service provider has in-house or tightly controlled access to appropriate vacuum/inert atmosphere furnaces and expertise in heat treating the specific alloy.
2. Onderdeel verwijderen van de bouwplaat:
- Doel: To separate the printed manifold(s) from the metal base plate onto which they were built.
- Proces: Typically done using wire EDM (Electrical Discharge Machining) or a bandsaw. Wire EDM generally provides a cleaner cut with less mechanical stress on the part.
- Overwegingen: The interface layer between the supports/part and the build plate needs to be cut cleanly. Access for the cutting tool must be considered.
3. Draagstructuur verwijderen:
- Doel: To remove the temporary support structures required during the build process to anchor the part and support overhangs.
- Proces: This can be one of the most labor-intensive and challenging post-processing steps, especially for complex internal geometries.
- Handmatig verwijderen: Supports are often designed to be relatively easy to break off manually using pliers, chisels, or hand tools.
- Bewerking/Slijpen: More stubborn supports or support interfaces may need to be removed using CNC machining, grinding, or other mechanical methods.
- Toegankelijkheid: Removing supports from deep internal channels or complex geometries can be extremely difficult. This strongly reinforces the DfAM principle of minimizing supports or designing them for easy removal.
- Uitdagingen: Risk of damaging the part surface during removal. Ensuring all support material is removed, especially from internal channels where it could obstruct flow or detach later.
- B2B Impact: Complex support removal significantly adds to labor costs and lead time. Designs optimized to minimize supports are highly preferred.
4. Oppervlakteafwerking:
- Doel: To improve the as-built surface roughness (Ra) for aesthetic reasons, to enhance fluid flow, improve fatigue life, or prepare the surface for subsequent coatings or sealing.
- Common Processes:
- Bead Blasting / Shot Peening: Propelling abrasive media (glass beads, ceramic shot) at the surface. Removes partially melted particles, creates a uniform matte finish, can improve fatigue life (shot peening induces compressive stress). Relatively low cost and widely used. Ra values typically improve but remain relatively high (e.g., Ra 5-10 µm).
- Tumbling / Vibratory Finishing: Placing parts in a machine with abrasive media that vibrates or tumbles. Good for deburring edges and providing a uniform finish on external surfaces, less effective for complex internal channels. Various media types allow for different levels of aggressiveness.
- Abrasive Flow Machining (AFM) / Extrude Hone: Forcing abrasive-laden putty through internal channels under pressure. Effective for smoothing internal passages but requires specialized equipment and can be costly.
- Elektrolytisch polijsten: An electrochemical process that removes a thin layer of material, resulting in a very smooth, bright, and clean surface. Excellent for improving corrosion resistance and cleanability. Can be effective on complex shapes but requires appropriate electrolytes for IN625 or CuNi.
- Manual Polishing: Using hand tools or powered polishers with abrasive compounds. Labor-intensive and typically reserved for specific critical areas or achieving mirror finishes for aesthetic reasons.
- Selectie: The choice depends on the required final Ra value, which surfaces need treatment (internal vs. external), part geometry, material, and cost constraints.
5. CNC Machining:
- Doel: To achieve tight tolerances, specific flatness, or smooth surface finishes on critical features that cannot be achieved reliably by the AM process alone.
- Common Applications on Manifolds:
- Flange Faces: Machining the mating surfaces where the manifold connects to the engine head, turbocharger, or exhaust pipes to ensure flatness and a proper seal.
- Sensor Ports: Machining threads or precise bores for sensor installation.
- Bevestigingspunten: Machining locating features or critical mounting surfaces.
- Proces: Utilizes standard CNC milling or turning centers. Requires proper fixtures to hold the potentially complex AM part securely without distortion. Sufficient stock material must be included in the AM design for these machining operations.
- Supplier Integration: Some AM service providers offer in-house CNC machining, providing a streamlined workflow. Others may require parts to be sent to a third-party machine shop. Integrated services can reduce lead times and logistical complexity for B2B customers.
6. Inspection and Quality Control (QC):
- Doel: To verify that the finished part meets all dimensional, material, and structural integrity requirements before shipping.
- Common Methods:
- Dimensionale inspectie: Using CMMs, 3D scanners, calipers, gauges.
- Niet-destructief onderzoek (NDT):
- Visuele inspectie: Checking for obvious defects, incomplete support removal.
- Dye Penetrant Testing (DPT): Detects surface-breaking cracks or porosity.
- X-ray / Computed Tomography (CT) Scanning: Reveals internal voids, porosity, inclusions, cracks, and allows for internal dimensional verification. Increasingly important for critical AM parts.
- Pressure Testing: Essential for manifolds with integrated cooling channels to ensure leak-tightness between exhaust and coolant passages, and to verify overall structural integrity under pressure.
- Material Verification: Checking material certifications, potentially destructive testing of witness coupons built alongside the part (tensile tests, hardness tests, microstructure analysis).
- Belangrijk: Robust QC is non-negotiable for critical marine components. B2B customers should inquire about the AM provider’s standard QC procedures and any additional testing required for their specific application.
7. Coating (Optional):
- Doel: To provide additional protection against extreme heat, corrosion, or for specific thermal barrier properties.
- Options: Ceramic coatings are sometimes applied to exhaust components to reduce heat radiation and improve thermal management. Other specialized coatings might be considered for unique environmental challenges.
- Overwegingen: Generally applied after all other machining and surface finishing steps. Compatibility with the base material (IN625/CuNi) and the operating environment is crucial.
Conclusion on Post-Processing:
Post-processing is an essential, multi-step phase in producing high-quality 3D printed marine exhaust manifolds. It transforms the raw printed part into a functional, reliable component. Engineers must design with post-processing in mind (e.g., support access, machining stock), and procurement managers must factor these steps into the overall cost and lead time calculations when evaluating quotes from AM service providers. A supplier offering comprehensive, well-controlled post-processing capabilities provides significant value and reduces risk for the customer.
Common Challenges in 3D Printing Marine Exhausts and How to Overcome Them
While metal 3D printing offers significant advantages for marine exhaust manifolds, the technology is not without its challenges. Successfully manufacturing complex, high-performance parts like these requires careful planning, process control, and often, iterative refinement. Understanding potential pitfalls and implementing strategies to mitigate them is crucial for both the AM service provider and the end-user. Addressing these challenges proactively ensures higher quality parts, reduces delays, and manages costs effectively – key considerations for B2B transactions involving advanced manufacturing.
Here are some common challenges encountered when 3D printing marine exhaust manifolds using LPBF with materials like IN625 and CuNi alloys, along with strategies to overcome them:
1. Warpage and Distortion:
- Cause: Significant thermal gradients occur during the LPBF process as localized areas are rapidly heated by the laser and then cool. This creates internal stresses within the part. If these stresses exceed the material’s yield strength at elevated temperatures, the part can warp or distort, especially large or geometrically complex parts like manifolds.
- Matigingsstrategieën:
- Optimized Build Strategy: Careful selection of scan patterns (e.g., island scanning, sector-based scanning) helps distribute heat more evenly. Managing the time between scanning layers can also influence thermal gradients.
- Robust Support Structures: Supports do more than just hold up overhangs; they act as heat sinks and anchor the part firmly to the rigid build plate, resisting distortion forces during the build. Strategic placement and design of supports are critical.
- Thermal Simulation: Using simulation software prior to printing can predict areas of high stress concentration and potential distortion, allowing designers to modify the part geometry or build setup proactively.
- Passende warmtebehandeling: Post-build stress relief heat treatment is essential to relax residual stresses and stabilize the part’s dimensions. Performing this while the part is still attached to the build plate can sometimes help maintain overall geometry.
- Onderdeelontwerp: Avoiding very large, flat sections or abrupt changes in thickness can help minimize stress buildup. Incorporating ribs or optimized structures can add stiffness.
2. Poreusheid:
- Cause: Small voids or pores within the printed material. Can arise from several sources:
- Poreusheid gas: Trapped gas (e.g., Argon from the build chamber atmosphere, or dissolved gases within the powder) that doesn’t escape the melt pool before solidification.
- Poreusheid door smelting: Insufficient energy input (laser power too low, scan speed too high) leads to incomplete melting and bonding between powder particles or successive layers, leaving voids.
- Sleutelgat Porositeit: Excessive energy input can create a deep, unstable vapor depression (keyhole) in the melt pool, which can collapse and trap gas, forming pores.
- Poederkwaliteit: Irregularly shaped powder, hollow powder particles, or contamination can contribute to porosity.
- Invloed: Porosity reduces the effective cross-sectional area, degrading mechanical properties (strength, fatigue life) and potentially creating leak paths, especially critical for pressure-containing manifolds.
- Matigingsstrategieën:
- Optimized Print Parameters: Precise control over laser power, scan speed, hatch spacing, and layer thickness is crucial. These parameters must be validated specifically for the material (IN625, CuNi) and machine being used. Reliable AM providers invest heavily in process development.
- Hoogwaardig poeder: Using high-purity, spherical powder with low internal gas content and controlled particle size distribution is fundamental. Sourcing from reputable suppliers like Met3dp, who utilize advanced methods like gas atomization and stringent quality control via their geavanceerd poederproductiesysteem, minimizes powder-related porosity risks.
- Proper Powder Handling: Preventing moisture absorption and contamination during storage and loading is vital.
- Process Monitoring: Real-time monitoring systems can help detect process instabilities that might lead to porosity.
- Post-Processing (HIP): Hot Isostatic Pressing (HIP) involves subjecting the part to high temperature and high inert gas pressure simultaneously. This can effectively close internal pores (except surface-connected ones), significantly improving density and mechanical properties. However, it adds cost and lead time and may not always be necessary if process control is sufficient.
- NDO-inspectie: CT scanning is highly effective for detecting internal porosity.
3. Support Removal Complexity:
- Cause: Additive manufacturing often requires supports, and for complex internal geometries like the flow paths and cooling channels in a manifold, removing these supports completely can be extremely difficult, time-consuming, and risks damaging the part.
- Matigingsstrategieën:
- DfAM for Support Minimization: Design parts with self-supporting angles (>45°), orient the part strategically on the build plate, use internal channel shapes (e.g., teardrop) that minimize overhangs.
- Geoptimaliseerd steunontwerp: Use support structures that are strong enough during the build but designed for easier removal (e.g., smaller contact points, specific support types like tree supports where applicable).
- Designing for Access: If internal supports are unavoidable, design access ports or openings specifically for support removal tools or processes like abrasive flow machining. These may need to be plugged or welded shut later if necessary.
- Hybride productie: Consider printing features that are easy to support and then using CNC machining to create more complex internal features where access allows.
- Specialized Removal Techniques: Utilizing techniques like AFM or chemical etching (if compatible and safe) for internal support removal in some cases.
4. Material Contamination:
- Cause: Introducing foreign particles or cross-contaminating metal powders during handling, loading, printing, or powder recycling can compromise the alloy’s purity and properties. Oxygen pickup is a particular concern for reactive metals.
- Matigingsstrategieën:
- Dedicated Equipment: Ideally, using machines dedicated to specific material types (e.g., one for Nickel alloys, one for Copper alloys) minimizes cross-contamination risk.
- Strikte poederbehandelingsprotocollen: Implementing rigorous procedures for powder storage (sealed containers, controlled environment), sieving, loading, and reclaiming/recycling unfused powder.
- Atmosphere Control: Maintaining a high-purity inert gas atmosphere (Argon) in the build chamber is critical to prevent oxidation during printing.
- Regular Machine Cleaning: Thorough cleaning of the build chamber, powder handling systems, and sieving equipment between different material runs or even periodically for the same material.
5. Cost Management:
- Cause: Metal AM can have high costs associated with expensive machinery, specialized metal powders (especially IN625), relatively slow build rates compared to mass production methods, and intensive post-processing requirements.
- Matigingsstrategieën:
- Ontwerpoptimalisatie: Use topology optimization and DfAM not just for performance but also to minimize material usage and build time (e.g., reducing volume, minimizing supports).
- Nesting: Printing multiple parts simultaneously on the build plate can improve machine utilization and reduce cost per part for small to medium batch sizes.
- Procesefficiëntie: Working with providers who have optimized their afdrukmethoden and workflow for efficiency.
- Realistic Specification: Avoid over-specifying tolerances or surface finishes for non-critical features, as this drives up post-processing costs.
- Lifecycle Cost Analysis: For B2B procurement, evaluate the total cost of ownership, considering the longer life, reduced maintenance, and improved performance of AM parts compared to potentially cheaper but less durable traditional alternatives.
6. Ensuring Watertightness / Gastightness:
- Cause: Potential for micro-porosity, incomplete fusion, or cracks (if process control is poor) could lead to leaks between exhaust passages and integrated cooling channels, or leaks to the atmosphere.
- Matigingsstrategieën:
- Robust Process Control: Ensuring validated parameters that achieve >99.5% density.
- Design for Integrity: Ensuring sufficient wall thickness between critical passages. Avoiding sharp internal corners that act as stress risers.
- Nabewerking: HIP can close internal porosity. Stress relief minimizes cracking risk.
- Rigorous Testing: Implementing mandatory pressure testing (hydrostatic or pneumatic) of finished manifolds, especially those with integrated cooling, to validate leak-tightness according to specified standards. Dye penetrant or other NDT methods can help identify potential leak paths.
Overcoming these challenges requires a combination of smart design (DfAM), high-quality materials, precise process control, thorough post-processing, and rigorous quality assurance. Partnering with an experienced and well-equipped metal AM service provider, who understands the specific demands of marine applications and materials like IN625 and CuNi, is the most effective way for marine engineers and procurement managers to navigate these potential issues and successfully implement high-performance 3D printed exhaust manifolds.
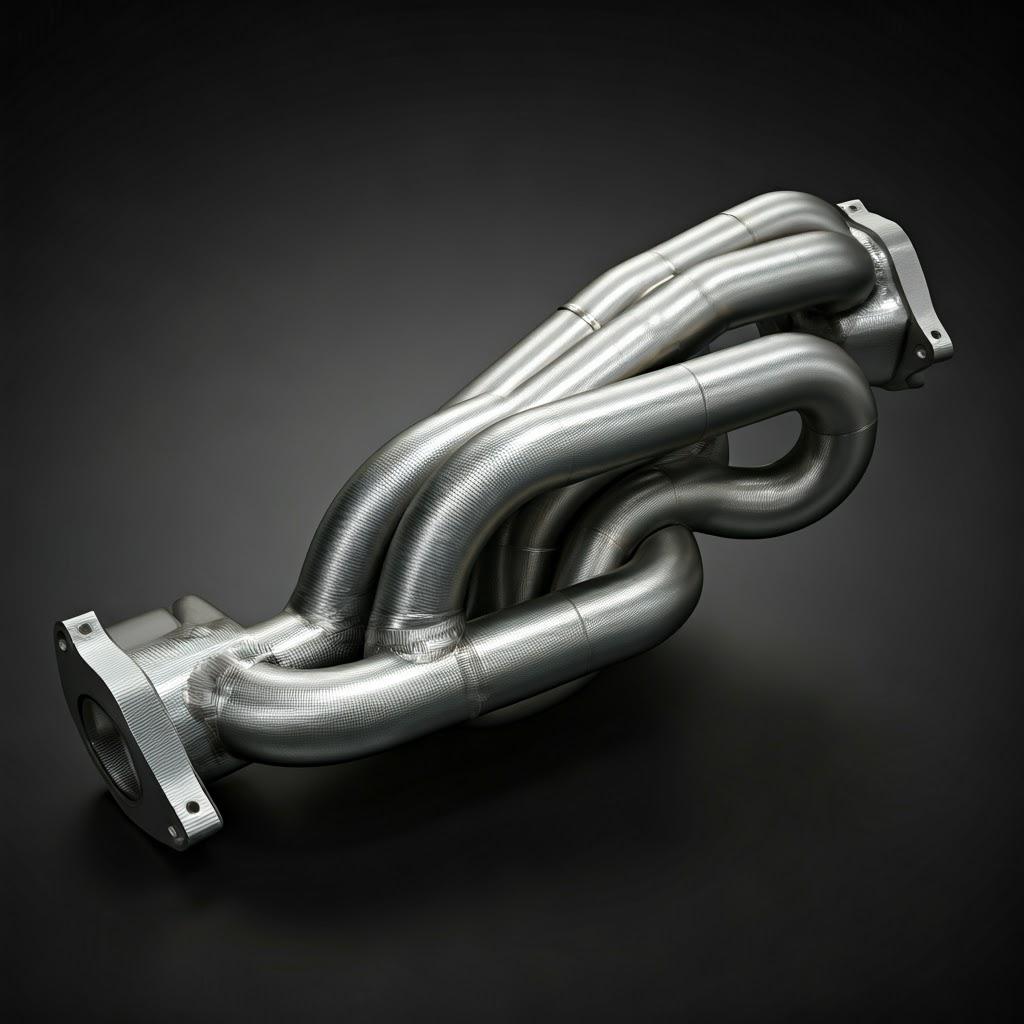
How to Choose the Right Metal 3D Printing Service Provider for Marine Components
Selecting the right additive manufacturing partner is as critical as the design and material choices when implementing 3D printed marine exhaust manifolds. The quality, reliability, and performance of the final component depend heavily on the expertise, equipment, processes, and quality control systems of the service provider. For procurement managers, engineers, and B2B buyers in the marine sector, navigating the landscape of AM suppliers requires a structured evaluation process focused on specific capabilities relevant to demanding marine applications and materials like Inconel 625 and Copper-Nickel alloys. Choosing wisely ensures not only high-quality parts but also reliable delivery schedules and valuable technical support.
Here’s a comprehensive guide to evaluating and selecting the ideal metal AM service provider for your marine exhaust manifold project:
1. Proven Expertise with Marine Applications and Relevant Materials:
- Requirement: The provider should demonstrate experience not just in metal AM, but specifically with components subjected to harsh marine environments. Crucially, they must have validated processes for printing IN625 and/or CuNi alloys, understanding their unique metallurgical behaviors during printing and required post-processing.
- Evaluation:
- Ask for case studies or examples of similar marine or high-temperature, corrosive environment projects they have completed.
- Inquire about their experience level specifically with IN625 and CuNi powders – how many builds, common applications, typical properties achieved.
- Discuss their understanding of marine corrosion mechanisms and how their process controls mitigate risks.
- Assess the technical depth of their sales and engineering teams during initial discussions.
2. Material Capabilities, Quality Control & Sourcing:
- Requirement: The provider must use high-quality metal powders specifically characterized and optimized for additive manufacturing. They need robust systems for powder handling, storage, testing, and traceability to ensure material integrity and consistency – critical for part reliability.
- Evaluation:
- Powder Sourcing: Do they produce their own powder (like Met3dp with its advanced atomization) or source it from qualified third parties? If sourced, who are their suppliers?
- Kwaliteitscontrole poeder: What are their procedures for incoming powder inspection (e.g., chemistry analysis, particle size distribution (PSD), morphology, flowability)? How do they manage powder reuse/recycling to maintain quality?
- Materiaal Portfolio: Do they offer the specific grade of IN625 or CuNi alloy you require? What supporting data (datasheets, typical properties) can they provide for parts printed with these materials on their machines? Met3dp, for example, offers a range of hoogwaardige metaalpoeders optimized for AM, including superalloys.
- Material Certifications: Can they provide material certifications (e.g., conforming to ASTM or other relevant standards) for the powder batch used for your parts?
3. Equipment, Technology & Capacity:
- Requirement: The provider should operate well-maintained, industrial-grade AM systems suitable for the required materials and part size. Their available technology (typically LPBF/SLM/DMLS for these applications) and overall capacity must align with your project’s needs, whether for prototypes or potential serial production for wholesale distributors.
- Evaluation:
- Printer Technology: Confirm they use LPBF machines known for reliability and quality with IN625/CuNi. Inquire about the specific machine models they operate. Met3dp highlights its industry-leading print volume, accuracy, and reliability.
- Bouwvolume: Ensure their printers’ build chambers can accommodate the size of your exhaust manifold design.
- Machine Calibration & Maintenance: Ask about their calibration frequency and maintenance protocols to ensure consistent performance.
- Capacity & Redundancy: How many suitable machines do they have? What is their typical machine utilization rate? Can they handle urgent orders or scale production if needed? Do they have redundancy in case of machine downtime?
4. Certifications and Quality Management System (QMS):
- Requirement: A robust QMS is essential for ensuring repeatable processes and traceable parts. Relevant certifications provide external validation of these systems.
- Evaluation:
- ISO 9001: This is a baseline certification indicating a documented QMS.
- Industry-Specific Certifications: While marine-specific AM certifications are less common, certifications relevant to demanding industries like aerospace (e.g., AS9100) can indicate a higher level of process control and rigor, often beneficial for critical marine components.
- Quality Manual: Request information about their quality manual, inspection procedures, and non-conformance handling processes.
5. Engineering and Design Support (DfAM Expertise):
- Requirement: An ideal partner doesn’t just print files; they offer DfAM consultation to help optimize your design for additive manufacturing, improving performance, reducing cost, and ensuring manufacturability.
- Evaluation:
- Consultation Services: Do they offer DfAM review services? Can their engineers provide feedback on your design regarding support minimization, feature optimization, orientation strategy, and potential cost savings?
- Simulatiemogelijkheden: Do they utilize simulation tools (thermal, structural) to predict and mitigate potential build issues like distortion?
- Collaborative Approach: Are they willing to work collaboratively with your engineering team to achieve the best outcome? Met3dp emphasizes providing comprehensive solutions, including application development services.
6. Comprehensive Post-Processing Capabilities:
- Requirement: As discussed previously, post-processing is crucial. A provider with extensive in-house capabilities (heat treatment, support removal, machining, surface finishing, NDT) offers a more streamlined, controlled, and often faster workflow.
- Evaluation:
- In-House vs. Outsourced: What post-processing steps do they perform in-house? Which are outsourced? In-house capabilities generally allow for better quality control and potentially shorter lead times.
- Specific Equipment: Do they have the necessary furnaces (vacuum/inert atmosphere), CNC machines, surface finishing equipment, and NDT tools (e.g., CMM, potentially CT scanning, pressure testing rigs)?
- Expertise: Does their team have expertise in the specific post-processing required for IN625/CuNi (e.g., correct heat treatment cycles, appropriate machining techniques)?
7. Lead Times, Communication & Transparency:
- Requirement: The provider should offer realistic lead times, communicate proactively throughout the production process, and be transparent about potential challenges or delays. This is vital for project planning and supply chain management for B2B customers.
- Evaluation:
- Quoting Process: Is their quoting clear, detailed, and timely? Does it break down costs?
- Stated Lead Times: Are their quoted lead times competitive and realistic given the complexity of the part and post-processing? How do they track and manage production scheduling?
- Communicatie: Who is your primary point of contact? How often will you receive updates? How do they handle issues or required design clarifications?
- Transparantie: Are they open about their processes, capabilities, and limitations?
8. Track Record, References & Financial Stability:
- Requirement: You need a reliable partner for the long term, especially for ongoing production or critical spare parts supply.
- Evaluation:
- Case Studies & References: Ask for relevant case studies and be sure to check references from other customers, preferably in related industries.
- Company History & Stability: Consider the provider’s time in business and general reputation. For significant B2B partnerships, assessing financial stability might be necessary.
Supplier Evaluation Checklist (Summary Table):
Criteria | Sleutelvragen | Ideal Response Indicator |
---|---|---|
Marine/Material Expertise | Experience with marine parts? Validated IN625/CuNi processes? Understanding of corrosion? | Demonstrated success stories, deep material knowledge, relevant technical discussion |
Material Quality & Control | Powder source? QC procedures (chemistry, PSD, reuse)? Material certs available? | High-quality powder (e.g., advanced atomization), documented QC, full traceability |
Equipment & Capacity | Suitable LPBF machines? Build volume? Calibration/maintenance? Capacity for your needs (proto/production)? | Industrial-grade, well-maintained machines, sufficient capacity & redundancy |
Certifications & QMS | ISO 9001? Other relevant certs (AS9100)? Documented QMS procedures? | Relevant certifications, clear evidence of robust quality system |
Engineering Support (DfAM) | Offer DfAM review? Simulation capabilities? Collaborative approach? | Proactive design feedback, problem-solving orientation, experienced engineering team |
Nabewerkingsmogelijkheden | In-house capabilities (heat treat, machining, NDT)? Expertise with specific materials? | Comprehensive in-house services covering required steps, proven expertise |
Lead Time & Communication | Realistic lead times? Clear quotes? Proactive updates? Transparent communication? | Competitive & reliable lead times, clear & frequent communication, problem transparency |
Track Record & Stability | Relevant case studies? Customer references available? Company history/reputation? | Positive references, proven track record in demanding applications, stable business |
Exporteren naar Sheets
By systematically evaluating potential metal AM service providers against these criteria, marine engineers and procurement managers can forge strong partnerships, mitigate risks, and ensure they receive high-quality, reliable 3D printed exhaust manifolds that meet the demanding requirements of the marine environment.
Cost Factors and Lead Time Analysis for 3D Printed Exhaust Manifolds
While the technical advantages of 3D printed marine exhaust manifolds are compelling, understanding the associated costs and lead times is crucial for project budgeting, procurement decisions, and supply chain planning. Metal additive manufacturing involves different cost drivers and timelines compared to traditional methods like casting or fabrication. A clear analysis helps B2B buyers make informed decisions and accurately compare the total value proposition.
Key Cost Drivers for 3D Printed Manifolds:
The final price of a 3D printed marine exhaust manifold is influenced by a combination of factors:
- Materiaalkosten:
- Alloy Choice: High-performance alloys like Inconel 625 are significantly more expensive per kilogram than stainless steels or even Copper-Nickel alloys. The raw material cost is a major component of the final price.
- Poederkwaliteit: High-quality, highly spherical powders optimized for AM typically command a premium but are essential for reliable printing and superior part properties.
- Material Density: Both IN625 and CuNi are relatively dense materials.
- Part Volume & Mass:
- Direct Proportionality: The amount of material used directly impacts cost. Larger or more massive parts consume more expensive powder. DfAM techniques like topology optimization and lattice structures are key to minimizing volume while maintaining performance, directly reducing cost.
- Bouwtijd:
- Uurloon machine: AM machines represent a significant capital investment, and their operating time is a major cost factor. Build time is influenced by:
- Part Height (Z-axis): Printing taller parts takes longer as more layers are required.
- Part Volume & Cross-Sectional Area: The total volume to be sintered and the area scanned per layer affect the time needed.
- Complexiteit: Intricate features might require slower scan speeds or specific strategies that increase time.
- Ondersteunende structuren: Printing supports adds time and consumes material. Minimizing supports through DfAM reduces build time and cost.
- Nesting: Printing multiple parts simultaneously in one build (nesting) can significantly improve machine utilization and reduce the cost per part, especially beneficial for batch production sought by wholesale buyers or manufacturers.
- Uurloon machine: AM machines represent a significant capital investment, and their operating time is a major cost factor. Build time is influenced by:
- Support Structure Requirements:
- Materiaalverbruik: Supports use powder that often cannot be fully reclaimed.
- Afdruktijd: As mentioned, printing supports adds to the overall build time.
- Removal Labor: Removing supports, especially complex internal ones, is often a manual, labor-intensive process that adds significant cost.
- Post-Processing Intensity:
- Hittebehandeling: Costs associated with furnace time, energy consumption, and inert gas/vacuum requirements.
- Support Removal & Manual Finishing: Labor costs for manual support removal, grinding, or blending.
- Afwerking oppervlak: Costs vary significantly depending on the method (e.g., simple bead blast vs. complex AFM or electropolishing).
- CNC-bewerking: Machine time, tooling, and programming costs for achieving tight tolerances on specific features. This can be a substantial cost component if extensive machining is needed.
- Inspection & NDT: Costs associated with dimensional inspection (CMM, scanning) and non-destructive testing (DPT, CT scanning, pressure testing). More stringent QC requirements increase costs.
- Engineering & Setup:
- Initial Setup: Costs associated with preparing the build file, programming the machine, and setting up the build layout. Usually amortized over larger batches.
- DfAM Consultation: If significant design support is required from the AM provider, this may involve separate engineering fees.
- Custom Tooling/Fixtures: Costs for any specific fixtures needed for post-processing or inspection.
- Order Quantity (Economies of Scale):
- Prototype vs. Production: One-off prototypes typically have the highest cost per part due to setup overheads.
- Batchgrootte: As order quantity increases, setup costs are amortized, machine utilization improves through nesting, and powder purchasing might become more efficient, leading to a lower cost per part. This is a key consideration for B2B procurement aiming for serial production or stocking inventory.
Comparing AM Costs vs. Traditional Costs:
- Initial Piece Price: For simple designs producible by casting in high volumes, the initial cost per part for AM might be higher due to material and process costs. However, for complex designs, low volumes, or materials difficult to cast/fabricate (like IN625), AM can be competitive even on initial price because it avoids high tooling costs (molds, jigs).
- Toolingkosten: AM eliminates the need for expensive molds or complex fabrication jigs required for traditional methods. This makes AM highly cost-effective for prototyping, customization, and low-to-medium volume production.
- Lifecycle Costs (Total Cost of Ownership): This is where AM often shines for high-performance marine components. The superior durability and corrosion resistance of AM parts made from IN625/CuNi can lead to longer service life, reduced maintenance, less downtime, and potentially improved fuel efficiency (due to optimized design/weight). These lifecycle benefits can outweigh a potentially higher initial purchase price, offering better value for vessel operators and fleet managers.
Typical Lead Time Analysis:
Lead time refers to the total time from order placement to part delivery. For 3D printed marine exhaust manifolds, it typically comprises several stages:
- Design & File Preparation (if applicable): 1-5 days (depending on complexity and required DfAM iterations).
- Order Processing & Queue Time: 1-10 days (highly variable depending on supplier workload and capacity).
- Printing (Build Time): 1-7 days (highly dependent on part size, complexity, nesting, and number of parts). A large, complex manifold could take multiple days to print.
- Cooling & Depowdering: 0.5-1 day (allowing the build chamber and parts to cool, removing unfused powder).
- Nabewerking:
- Heat Treatment (including furnace time, heating/cooling ramps): 1-3 days.
- Part Removal & Support Removal: 0.5-3 days (highly variable based on complexity).
- CNC Machining (if required): 1-5 days (depends on complexity and machine shop availability).
- Surface Finishing: 0.5-2 days.
- Quality Control & Inspection: 1-3 days (depending on required NDT and documentation).
- Verzending: 1-7 days (depending on location and shipping method).
Estimated Total Lead Time: Gewoonlijk varieert het van 2 tot 6 weken for a prototype or small batch, but can be longer for very complex parts, large orders, or if extensive post-processing or specific QC requirements are involved.
Factors Influencing Lead Time:
- Complexiteit en omvang van het onderdeel: Directly impacts print time and post-processing effort.
- Supplier Capacity & Workload: Availability of machines and personnel.
- Vereisten voor nabewerking: Extensive machining or specialized finishing adds significant time.
- QC Requirements: Complex NDT or documentation needs increase time.
- Bestelhoeveelheid: Larger batches take longer to print and process.
- Communication & Approvals: Delays in design approvals or clarifications can impact the schedule.
Getting Accurate Quotes:
To receive accurate cost and lead time estimates from AM service providers, ensure you provide:
- A clear 3D CAD model (e.g., STEP file).
- A 2D drawing specifying critical dimensions, tolerances, required surface finishes, and material designation (IN625, CuNi alloy type).
- Clearly defined post-processing requirements (heat treatment specifics, machining needs, finishing type).
- Required quality control checks (NDT methods, testing standards, certifications).
- Desired order quantity and required delivery date.
By understanding the intricate factors driving cost and lead time in metal AM, marine industry stakeholders can better budget for projects, manage procurement processes, and appreciate the comprehensive value offered by high-performance 3D printed components beyond just the initial purchase price.
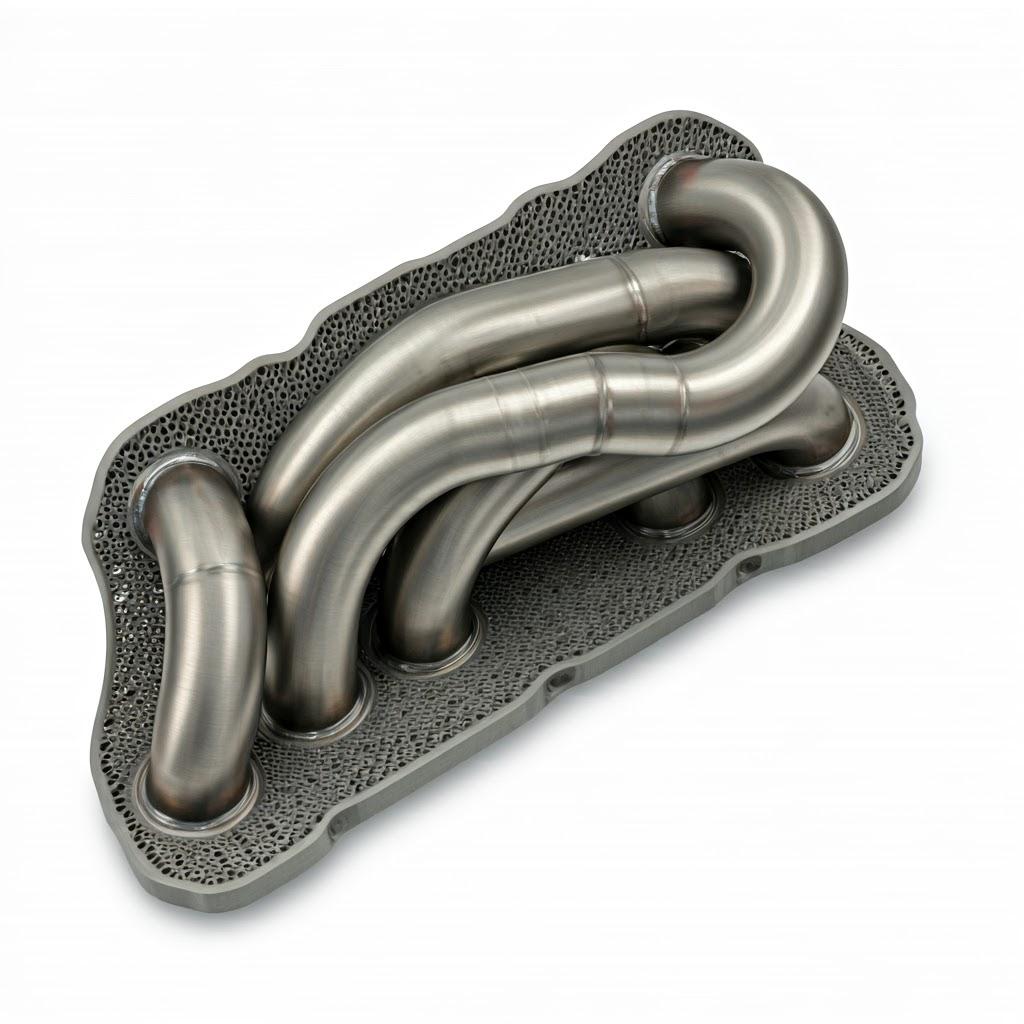
Frequently Asked Questions (FAQ) about 3D Printed Marine Exhaust Manifolds
As metal additive manufacturing becomes more prevalent in the marine industry, engineers, designers, boat builders, and procurement managers often have questions about the practicality, reliability, and cost-effectiveness of 3D printed components like exhaust manifolds. Here are answers to some frequently asked questions:
1. Are 3D printed metal exhaust manifolds durable enough for harsh marine environments?
- Antwoord: Absolutely, provided the correct materials and processes are used. Manifolds printed from high-performance alloys like Inconel 625 (IN625) offer exceptional resistance to high temperatures, thermal cycling, vibration, and, crucially, aggressive saltwater corrosion (including pitting and crevice corrosion). For components primarily dealing with raw seawater cooling, Copper-Nickel (CuNi) alloys offer outstanding resistance to seawater corrosion and biofouling. The additive manufacturing process itself, when properly controlled by experienced providers using high-quality powders, produces fully dense parts (>99.5%) with mechanical properties often comparable or even superior (in some aspects, like fatigue life due to optimized design) to traditionally manufactured counterparts. Rigorous post-processing (like stress relief) and quality control (including NDT and pressure testing) further ensure the durability and reliability required for demanding marine service.
2. How does the cost of a 3D printed manifold compare to a traditionally manufactured one?
- Antwoord: The cost comparison depends heavily on several factors:
- Complexiteit: For highly complex designs with integrated cooling or optimized flow paths, AM can be surprisingly cost-competitive, even at lower volumes, because it avoids the extreme costs of complex molds or intricate fabrication needed for traditional methods.
- Volume: For very simple designs produced in high volumes (thousands), traditional casting might have a lower initial piece price due to established economies of scale. However, AM eliminates tooling costs, making it highly advantageous for prototypes, custom parts, and low-to-medium volume production (dozens to hundreds).
- Materiaal: Printing with expensive superalloys like IN625 will naturally cost more than casting in basic iron or aluminum bronze.
- Totale gebruikskosten: It’s crucial to consider lifecycle costs. A 3D printed IN625 manifold might have a higher upfront cost but could last significantly longer, require less maintenance, and contribute to better fuel efficiency due to optimized design, resulting in a lower total cost of ownership over the vessel’s life.
3. What is the typical turnaround time for obtaining a custom 3D printed marine exhaust manifold?
- Antwoord: Typical lead times generally range from 2 tot 6 weken. This timeframe encompasses design finalization (if needed), file preparation, potential queue time at the service provider, the actual printing process (which can take several days for a complex manifold), cooling, extensive post-processing (heat treatment, support removal, machining, finishing), and quality control/inspection. Factors influencing this timeframe include part size and complexity, the specific material, the provider’s current workload, the extent of required post-processing (especially CNC machining), and the level of quality assurance mandated. For urgent needs or prototypes, expedited services might be available at a premium cost.
4. Can existing manifold designs originally made for casting or fabrication be easily converted for 3D printing?
- Antwoord: While it’s technically possible to print a design originally intended for casting or fabrication, simply doing so often fails to leverage the key advantages of additive manufacturing and may even result in a suboptimal or unnecessarily expensive part. To truly benefit from AM, designs should be reviewed and likely redesigned using Ontwerp voor additieve productie (DfAM) principles. This involves optimizing the geometry for flow and cooling, reducing weight through topology optimization or lattices, minimizing support structures, and consolidating parts – features often not feasible with traditional methods. Collaboration with an AM service provider’s engineering team is highly recommended to adapt or create designs that maximize the benefits of 3D printing.
5. What quality assurance processes are used for these critical components?
- Antwoord: Reputable AM service providers employ rigorous quality assurance processes for critical components like marine exhaust manifolds. This typically includes:
- Material Traceability: Documenting the specific powder batch used for each part.
- Process Monitoring: Utilizing machine sensors to monitor the build process in real-time where possible.
- Dimensionale inspectie: Using CMMs or 3D scanners to verify critical dimensions against drawings and specifications.
- Post-Heat Treatment Verification: Confirming heat treatment cycles were completed correctly.
- Niet-destructief onderzoek (NDT): Common methods include Dye Penetrant Testing (DPT) for surface defects and potentially Computed Tomography (CT) scanning for internal integrity checks (detecting porosity or voids).
- Pressure Testing: Essential for validating the leak-tightness of manifolds, especially those with integrated cooling channels.
- Documentatie: Providing material certifications, certificates of conformity, and inspection reports as required by the customer.
Choosing a supplier with a strong QMS (e.g., ISO 9001 certified) and proven experience in demanding applications ensures these QA steps are performed diligently.
Conclusion: Navigating the Future of Marine Propulsion with Additive Manufacturing
The marine industry stands at the cusp of a manufacturing evolution, and metal additive manufacturing is steering the course towards unprecedented levels of performance, customization, and durability for critical components. As we’ve explored, 3D printed exhaust manifolds, particularly those crafted from advanced materials like Inconel 625 and Copper-Nickel alloys, represent a significant leap beyond the constraints of traditional casting and fabrication. They offer marine engineers and naval architects the freedom to design highly optimized geometries for superior fluid dynamics and integrated cooling, leading to tangible benefits in engine efficiency, power output, and component longevity.
The ability to leverage topology optimization for weight reduction contributes to better vessel performance and fuel economy. The elimination of tooling costs democratizes customization, enabling rapid prototyping and cost-effective production of bespoke manifolds for specialized applications, from high-performance racing to unique repower projects. Furthermore, part consolidation achieved through AM enhances reliability by minimizing joints and potential failure points, while the potential for digital inventories and on-demand production offers transformative supply chain advantages for manufacturers, suppliers, and fleet operators alike.
While challenges related to design complexity, process control, and post-processing exist, they are effectively navigated through adherence to DfAM principles, meticulous process validation, rigorous quality assurance, and, crucially, collaboration with expert additive manufacturing partners. Choosing a service provider with proven expertise in marine applications, deep knowledge of materials like IN625 and CuNi, state-of-the-art equipment, robust quality systems, and comprehensive post-processing capabilities is paramount to success.
Bedrijven zoals Met3dp are at the forefront of this technological wave, providing not only industry-leading metal AM systems known for their accuracy and reliability but also specializing in the production of high-quality, spherical metal powders essential for printing dense, high-performance parts. Their commitment to comprehensive solutions, spanning equipment, advanced materials, and application development support, positions them as a valuable partner for organizations looking to harness the power of additive manufacturing.
For engineers seeking to push the boundaries of marine engine performance, and for procurement managers aiming to source durable, high-value components while optimizing supply chains, the time to explore metal 3D printing is now. The advantages are clear, the technology is mature, and the potential impact on the future of marine propulsion is immense. We encourage you to engage with knowledgeable AM providers, discuss your specific challenges and requirements, and discover how additive manufacturing can propel your next marine project to new horizons. The journey towards lighter, faster, more efficient, and more reliable marine vessels is increasingly being built, layer by layer, with metal additive manufacturing.
Delen op
MET3DP Technology Co, LTD is een toonaangevende leverancier van additieve productieoplossingen met hoofdkantoor in Qingdao, China. Ons bedrijf is gespecialiseerd in 3D printapparatuur en hoogwaardige metaalpoeders voor industriële toepassingen.
Onderzoek om de beste prijs en een op maat gemaakte oplossing voor uw bedrijf te krijgen!
gerelateerde artikelen
Over Met3DP
Recente update
Ons product
NEEM CONTACT MET ONS OP
Nog vragen? Stuur ons nu een bericht! Na ontvangst van uw bericht behandelen wij uw verzoek met een heel team.
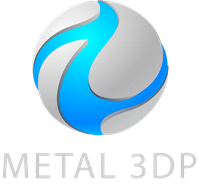
Metaalpoeders voor 3D printen en additieve productie