Custom Heat Sinks for Power Modules via Metal AM
Inhoudsopgave
Introduction: Revolutionizing Thermal Management with Custom 3D Printed Heat Sinks for Power Electronics
The relentless drive towards higher power densities, miniaturization, and increased efficiency in power electronics across industries like automotive, aerospace, and industrial automation presents a significant challenge: effective thermal management. As components shrink and power throughput increases, dissipating the generated heat becomes critical for ensuring reliability, performance, and longevity. Traditional manufacturing methods for heat sinks, often involving extrusion or CNC machining, face limitations in creating the complex geometries needed for optimal thermal performance in space-constrained environments. This is where metal additive manufacturing (AM), or 3d printen, emerges as a transformative technology.
Metal AM enables the fabrication of custom heat sinks with intricate designs, optimized flow paths, and material combinations previously impossible or prohibitively expensive to achieve. By building parts layer by layer directly from metal powder, manufacturers can now create highly customized thermal management solutions tailored to specific power modules and operating conditions. This capability unlocks new levels of design freedom, allowing engineers to integrate cooling features directly into components, optimize shapes for maximum surface area and airflow, and utilize advanced materials like high-conductivity copper alloys. For procurement managers and engineers seeking cutting-edge thermal solutions, understanding the potential of metal AM for custom heat sinks is crucial for staying competitive and pushing the boundaries of power electronic performance. Companies specializing in metaal 3D printen, like Met3dp, offer the expertise and technology to turn complex thermal challenges into efficient, high-performance realities.
This post delves into the world of custom heat sinks for power modules produced via metal AM. We will explore the diverse applications, the compelling advantages over traditional methods, the critical role of material selection (focusing on CuCrZr and AlSi10Mg), design considerations, technical specifications, potential challenges, and how to select the right manufacturing partner. Whether you are developing next-generation electric vehicle (EV) power systems, compact aerospace electronics, or high-power industrial converters, metal AM offers a powerful toolset for creating superior thermal management solutions.
Key Aspects of Metal AM for Heat Sinks:
- Ontwerpvrijheid: Creation of complex internal channels, thin walls, and optimized fin structures (e.g., lattice or gyroid structures) impossible with traditional methods.
- Prestatieverbetering: Improved heat dissipation through optimized geometries and high-conductivity materials.
- Lichtgewicht: Topology optimization allows for material reduction only where structurally needed, crucial for aerospace and automotive applications.
- Deelconsolidatie: Integrating heat sinks with other components or enclosures, reducing assembly steps and potential points of failure.
- Rapid Prototyping & Customization: Faster iteration cycles and ability to produce unique designs cost-effectively, even in low volumes.
As a leader in metal AM equipment and high-performance metal powders, Met3dp leverages advanced powder manufacturing techniques like gas atomization and Plasma Rotating Electrode Process (PREP) to produce materials ideal for demanding thermal applications. Our commitment to quality ensures that the powders used in creating your custom heat sinks meet the stringent requirements for density, purity, and performance.
Applications: Where are Custom Metal AM Heat Sinks Making an Impact?
The ability of metal additive manufacturing to produce highly optimized, custom heat sinks is driving adoption across a range of demanding industries where efficient thermal management is paramount. Traditional cooling solutions often compromise performance due to design limitations imposed by subtractive manufacturing or casting. Metal AM overcomes these constraints, enabling heat sinks specifically tailored for challenging environments and high-power density applications.
Key Industry Applications:
- Automotive (Especially Electric Vehicles – EVs):
- Power Modules (Inverters, Converters): EVs rely heavily on power electronics to manage battery power and drive the electric motor. These modules generate significant heat, particularly during fast charging or high-performance driving. AM allows for compact, highly efficient heat sinks, often incorporating liquid cooling channels, that fit within tight vehicle architectures. Lightweighting via topology optimization also contributes to overall vehicle efficiency.
- On-Board Chargers (OBCs): Efficient cooling is needed to maximize charging speed and component lifespan.
- Battery Pack Cooling: While often using cold plates, AM can create optimized flow channels within these plates or specialized heat sinks for specific battery module hot spots.
- Ruimtevaart en defensie:
- Power Distribution Units: Aircraft and spacecraft utilize complex power systems where reliability is non-negotiable. AM heat sinks offer high performance in compact, lightweight forms, crucial for minimizing payload weight.
- Avionics Cooling: Sensitive electronic components require stable operating temperatures. Custom AM heat sinks can be designed to conform to irregular spaces and provide targeted cooling.
- Radar and Communication Systems: High-power RF components generate substantial heat. AM enables intricate cooling channel designs for liquid or air cooling.
- Industrial Automation and Manufacturing:
- Variable Frequency Drives (VFDs) and Motor Controls: Precise control of industrial motors generates heat in the power electronics. Robust and efficient heat sinks ensure reliability in demanding factory environments.
- Power Supplies and Converters: High-power industrial supplies benefit from optimized thermal management to improve efficiency and lifespan.
- Welding and Laser Equipment: Power sources for these processes require effective cooling solutions, often benefiting from custom AM designs.
- Renewable Energy:
- Solar Inverters: Converting DC power from solar panels to AC power for the grid generates heat. Efficient heat sinks, potentially using passive cooling optimized by AM, improve inverter performance and reliability, especially in harsh outdoor conditions.
- Wind Turbine Converters: Power electronics in wind turbines manage large amounts of power and require dependable cooling. AM can provide robust, optimized solutions.
- Medische hulpmiddelen:
- Imaging Equipment (e.g., MRI, CT Scanners): Power supplies and gradient amplifiers require stable thermal conditions. Compact, custom AM heat sinks can be integrated into space-constrained medical devices.
- Laser Systems: Medical lasers generate heat that must be managed precisely.
- High-Performance Computing (HPC) & Data Centers:
- While often focused on liquid cooling plates, specific high-power processors or custom server designs can benefit from uniquely shaped AM heat sinks for targeted hot spot cooling.
Wholesale and Supplier Considerations:
Procurement managers and wholesale buyers looking for reliable heat sink suppliers should consider metal AM providers who demonstrate expertise in these application areas. A capable supplier, like Met3dp, understands the specific thermal challenges and regulatory requirements (e.g., aerospace certifications, automotive standards) within these sectors. We offer custom heat sink manufacturing services, leveraging our advanced printing technologies and high-quality metal powders to deliver solutions optimized for performance, weight, and integration. Partnering with an experienced thermal solutions provider using AM ensures access to cutting-edge designs and materials tailored for the most demanding power electronic applications.
Table: Application Examples and AM Benefits
Toepassingsgebied | Specific Component | Key Thermal Challenge | How Metal AM Helps | Potential Materials |
---|---|---|---|---|
Automotive (EV) | Power Inverter | High power density, space constraints | Complex liquid cooling channels, lightweight topology-optimized design | AlSi10Mg, CuCrZr |
Lucht- en ruimtevaart | Avionics Power Supply | Weight sensitivity, high reliability | Integrated cooling features, complex thin fins, reduced part count | AlSi10Mg |
Industrieel | Variable Frequency Drive (VFD) | Robustness, high ambient temperature | Optimized air-cooled fins, durable materials, conformal designs | AlSi10Mg, CuCrZr |
Hernieuwbare energie | Solar Inverter | Passive cooling efficiency, longevity | Maximized surface area fins, weather-resistant designs | AlSi10Mg |
Medisch | MRI Gradient Amplifier | Compactness, electromagnetic compatibility | Conformal shapes, non-magnetic materials if needed, integrated cooling | AlSi10Mg, Copper |
High-Power Systems | RF Amplifiers | Extreme heat flux | High-conductivity materials (Copper alloys), optimized liquid micro-channels | CuCrZr, Pure Copper |
Exporteren naar Sheets
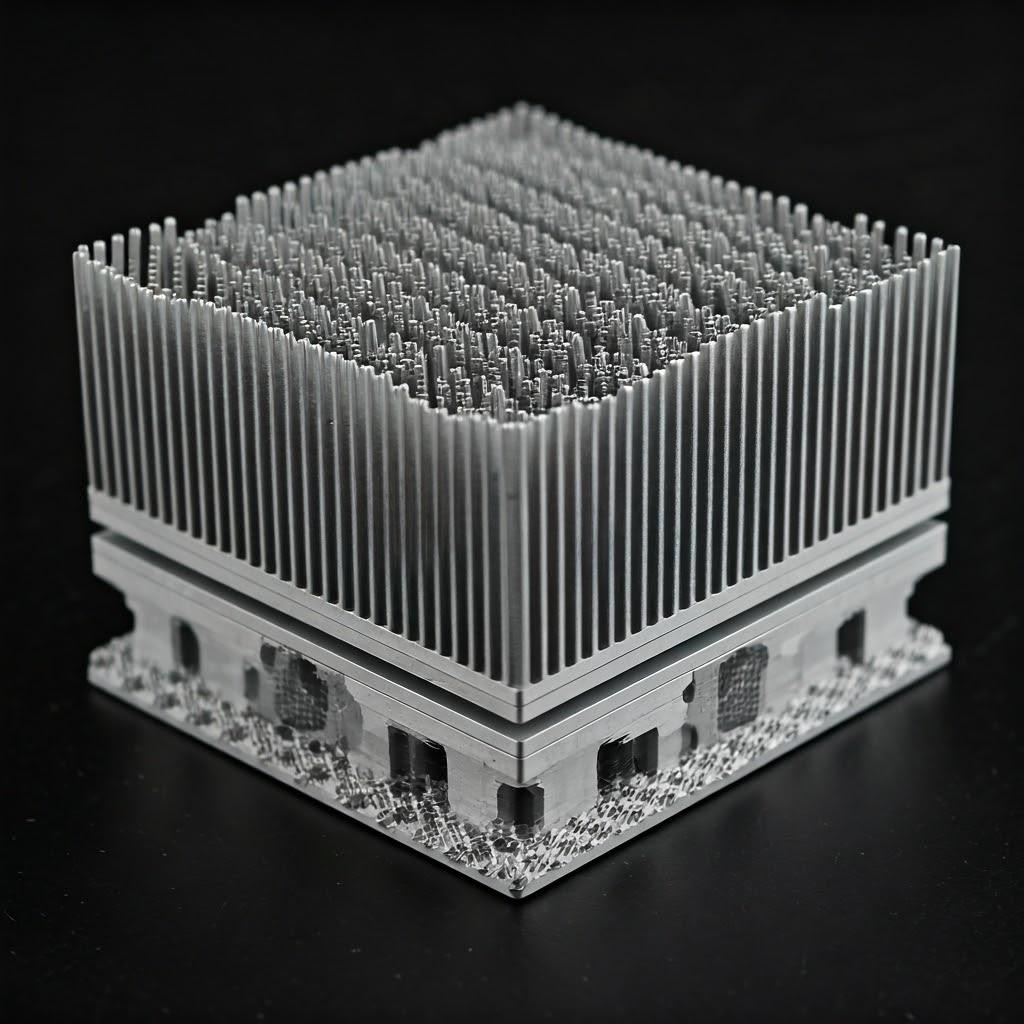
The Additive Advantage: Why Choose Metal 3D Printing for Heat Sink Manufacturing?
While traditional manufacturing methods like extrusion, casting, and CNC machining have long served the purpose of creating heat sinks, they inherently limit design complexity and optimization potential. Metal additive manufacturing fundamentally changes the paradigm, offering significant advantages, particularly for demanding power electronics applications requiring custom solutions. Choosing metal AM isn’t just about a different manufacturing process; it’s about unlocking superior performance, design innovation, and production flexibility.
Key Advantages of Metal AM for Heat Sinks:
- Unparalleled Design Freedom & Complexity:
- Intricate Geometries: AM builds parts layer-by-layer, enabling the creation of highly complex internal structures, such as gyroids, lattices, or conformal cooling channels that precisely follow the contours of heat-generating components. This maximizes surface area and optimizes fluid flow (for liquid cooling) in ways impossible with subtractive methods.
- Topologieoptimalisatie: Software algorithms can determine the most efficient material distribution for thermal performance and structural integrity, removing unnecessary mass. This leads to significantly lighter heat sinks without sacrificing cooling capability – a critical factor in automotive and aerospace.
- Thin Walls & Fine Features: AM processes like Selective Laser Melting (SLM) or Electron Beam Melting (EBM) can produce very thin walls (down to ~0.3-0.5 mm) and intricate fin structures, further increasing surface area for heat dissipation within a given volume.
- Enhanced Thermal Performance:
- Optimized Heat Transfer Paths: Complex geometries allow for more direct and efficient pathways for heat to travel from the source to the cooling medium (air or liquid). Conformal channels minimize thermal resistance.
- Increased Surface Area: Lattice structures or complex fin arrays significantly increase the surface area available for convection, leading to more effective heat removal compared to simple extruded fins of the same volume.
- Material Possibilities: AM allows the use of high-performance materials, including high-conductivity copper alloys (like CuCrZr), which can be challenging or costly to machine into complex shapes traditionally.
- Lichtgewicht:
- As mentioned, topology optimization and lattice structures allow for significant weight reduction compared to solid metal heat sinks produced by traditional methods. This is crucial for applications where every gram counts, such as EVs (range extension) and aircraft (fuel efficiency, payload capacity).
- Deelconsolidatie:
- AM enables the integration of the heat sink directly into other components, such as electronic enclosures, brackets, or fluid connectors. This reduces the number of individual parts, simplifies assembly, lowers weight, and eliminates potential thermal interface resistances between components.
- Snelle prototyping en iteratie:
- Producing functional prototypes of complex heat sink designs is significantly faster with AM than waiting for custom tooling for extrusion or casting. This allows engineers to quickly test multiple design variations, validate performance through simulation and physical testing, and arrive at an optimized solution much faster.
- Customization and Low-Volume Production:
- AM is ideal for producing custom, application-specific heat sinks without the high tooling costs associated with traditional mass production methods. This makes it economically viable for specialized equipment, prototypes, or low-to-medium volume production runs often required by groothandel kopers needing tailored solutions.
- Veerkracht van de toeleveringsketen:
- Digital manufacturing enables localized production, potentially reducing reliance on long, complex supply chains. Designs can be sent digitally to an AM service provider like Met3dp for on-demand manufacturing closer to the point of need.
Comparison Table: Metal AM vs. Traditional Heat Sink Manufacturing
Functie | Metaal Additive Manufacturing (AM) | Traditional (Extrusion, Machining, Casting) | Advantage of AM |
---|---|---|---|
Complex ontwerp | Very High (Internal channels, lattices, conformal shapes) | Limited (Primarily 2.5D shapes, linear features) | Enables optimized geometries for superior thermal performance and integration |
Lichtgewicht | Excellent (Topology optimization, lattices) | Limited (Material removal is subtractive or shape is cast) | Significant weight reduction potential |
Materiaalgebruik | Additive (Uses only necessary material) | Subtractive (Machining creates waste) or Formed (Casting) | More efficient material usage, less waste (though powder reuse is key) |
Kosten gereedschap | None (Direct digital manufacturing) | High (Dies for extrusion, molds for casting, fixtures) | Economical for custom and low-volume production |
Prototyping Speed | Fast (Hours to days) | Slow (Weeks to months for tooling and production) | Rapid design iteration and validation |
Deel Consolidatie | High potential (Integrate features directly) | Low potential (Requires assembly of multiple parts) | Reduced assembly time, weight, and potential failure points |
Materiaal opties | Growing range (Alloys, Copper, Steel, Ti, etc.) | Established range, but complex shapes costly for some materials | Access to high-performance materials like CuCrZr for complex shapes |
Het meest geschikt voor | Custom, high-performance, complex, lightweight, low-medium volume | Standard shapes, high-volume production | Applications requiring maximum performance, customization, or weight savings |
Exporteren naar Sheets
By leveraging these advantages, engineers and procurement managers can overcome the limitations of conventional thermal management solutions and achieve significant improvements in the performance, reliability, and efficiency of power electronic systems. Partnering with an experienced provider like Met3dp ensures access to state-of-the-art afdrukmethoden and materials expertise.
Material Matters: Selecting CuCrZr and AlSi10Mg for Optimal Heat Sink Performance
The choice of material is fundamental to the performance of any heat sink. Metal additive manufacturing broadens the palette of usable materials, allowing for the selection of metals optimized for thermal conductivity, weight, strength, and cost, tailored to the specific application requirements. For demanding power electronics cooling, two materials stand out: Copper-Chromium-Zirconium (CuCrZr) en Aluminum-Silicon-10Magnesium (AlSi10Mg).
Understanding the properties and benefits of these materials is crucial for engineers designing AM heat sinks and for procurement managers sourcing custom heat sink manufacturing services.
Copper-Chromium-Zirconium (CuCrZr): The High-Conductivity Champion
CuCrZr is a precipitation-hardenable copper alloy renowned for its excellent combination of high thermal and electrical conductivity, good mechanical strength (especially at elevated temperatures), and resistance to softening.
- Key Properties & Benefits:
- Hoge thermische geleidbaarheid: Typically in the range of 300-340 W/(m·K) after appropriate heat treatment. This is significantly higher than aluminum alloys and most steels, allowing for very efficient heat transfer away from the power module. This makes it ideal for applications with extremely high heat flux.
- Goede elektrische geleidbaarheid: While thermal performance is primary for heat sinks, its high electrical conductivity (~80% IACS) can be beneficial if the heat sink forms part of an electrical path or needs specific grounding properties.
- Elevated Temperature Strength: Unlike pure copper, CuCrZr retains significant strength at higher temperatures (up to ~450-500°C), preventing deformation or softening in demanding operating conditions.
- Goede corrosiebestendigheid: Offers reasonable resistance to atmospheric corrosion.
- Bedrukbaarheid: While challenging due to copper’s high reflectivity and conductivity (requiring optimized laser parameters), CuCrZr has become increasingly processable via Laser Powder Bed Fusion (LPBF/SLM) with modern machine capabilities.
- Why Use It for AM Heat Sinks?
- When maximum thermal performance is the absolute priority.
- For applications with very high heat densities where aluminum alloys might struggle.
- Where operating temperatures are elevated.
- Ideal for compact, high-power modules in aerospace, high-performance computing, or specialized industrial equipment.
- Overwegingen:
- Kosten: Copper alloys are generally more expensive than aluminum alloys, both in terms of raw powder cost and potentially printing process time/complexity.
- Gewicht: Copper is significantly denser than aluminum (approx. 8.9 g/cm³ vs 2.68 g/cm³). Even with topology optimization, a CuCrZr heat sink will likely be heavier than an equivalent AlSi10Mg one, which might be a limiting factor in weight-sensitive applications.
- Print Parameter Sensitivity: Requires careful control of laser power, speed, and atmosphere during printing to achieve dense, defect-free parts.
Aluminum-Silicon-10Magnesium (AlSi10Mg): The Versatile Lightweight
AlSi10Mg is one of the most common and well-understood aluminum alloys used in metal AM. It’s essentially a casting alloy adapted for powder bed fusion processes, offering a good balance of thermal properties, mechanical strength, low weight, and excellent printability.
- Key Properties & Benefits:
- Goede thermische geleidbaarheid: While lower than CuCrZr, its thermal conductivity (typically 120-150 W/(m·K) as-printed, potentially higher after heat treatment) is excellent for an aluminum alloy and sufficient for a vast range of power electronics cooling applications.
- Uitstekende verhouding sterkte/gewicht: AlSi10Mg offers good mechanical properties (yield strength, tensile strength) combined with very low density (approx. 2.68 g/cm³). This makes it ideal for lightweight heat sinks in automotive, aerospace, and portable devices.
- Superb Printability: It is relatively easy to process using LPBF/SLM, allowing for fine features, thin walls, and complex geometries with high reliability and good surface finish.
- Corrosieweerstand: Exhibits good resistance to corrosion.
- Kosteneffectiviteit: Aluminum powder is generally less expensive than copper alloys, and the printing process is typically faster and more established, leading to lower overall part costs.
- Why Use It for AM Heat Sinks?
- When weight reduction is a primary design goal.
- For applications with moderate-to-high heat loads where the thermal conductivity is sufficient.
- Where cost is a significant driver.
- Ideal for automotive (EVs), aerospace components, drones, and many industrial applications.
- Leverages the full potential of topology optimization and complex, lightweight designs.
- Overwegingen:
- Lower Thermal Conductivity: Not suitable for the most extreme heat flux applications where CuCrZr might be necessary.
- Lower Operating Temperature Limit: Compared to CuCrZr, AlSi10Mg’s mechanical properties degrade more significantly at elevated temperatures (typically limited to applications below 150-200°C, depending on load and duration).
Met3dp: Your Source for High-Quality AM Powders
Choosing the right material is only part of the equation; the quality of the metal powder itself is critical for successful additive manufacturing. Poor powder quality (e.g., inconsistent particle size distribution, irregular morphology, impurities, high oxygen content) can lead to printing defects, porosity, and compromised mechanical and thermal properties in the final heat sink.
Met3dp specializes in producing high-performance metal powders specifically optimized for AM processes like Selective Electron Beam Melting (SEBM) and Laser Powder Bed Fusion (LPBF/SLM).
- Advanced Production: We utilize industry-leading Gas Atomization (GA) and Plasma Rotating Electrode Process (PREP) technologies. Our unique nozzle and gas flow designs ensure high sphericity and excellent flowability – essential characteristics for uniform powder bed spreading and consistent melting.
- Kwaliteitscontrole: Rigorous quality control measures guarantee powder characteristics meet specifications for particle size distribution (PSD), chemical composition, morphology, and purity.
- Materiaal Portfolio: Beyond standard alloys like AlSi10Mg, Met3dp actively researches and manufactures innovative alloys. While we excel in materials like Ti-based alloys and superalloys, our expertise extends to producing high-quality powders suitable for thermal applications, ensuring our clients receive materials optimized for their specific needs. Explore our productaanbod to see our range.
Als metal powders supplier, Met3dp ensures that the foundation of your AM heat sink – the powder – enables the printing of dense, high-quality parts with superior thermal and mechanical properties, consistent with the demands of your application.
Table: Material Comparison for AM Heat Sinks
Eigendom | CuCrZr | AlSi10Mg | Eenheid | Belangrijkste afhaalmaaltijd |
---|---|---|---|---|
Warmtegeleiding | ~300 – 340 (Post Heat Treatment) | ~120 – 150 (As-Printed/Heat Treated) | W/(m-K) | CuCrZr offers significantly higher heat transfer capability. |
Dikte | ~8.9 | ~2.68 | g/cm³ | AlSi10Mg is much lighter, ideal for weight-sensitive applications. |
Max Operating Temp. | Good strength up to ~450-500°C | Strength degrades above ~150-200°C | °C | CuCrZr suitable for higher temperature environments. |
Printability (LPBF/SLM) | Moderate (Requires optimization) | Uitstekend | – | AlSi10Mg is generally easier and faster to print reliably. |
Relatieve kosten (poeder) | Hoger | Lager | – | AlSi10Mg is typically more cost-effective. |
Primary Advantage | Maximum Thermal Performance | Excellent Strength-to-Weight Ratio, Cost | – | Choose based on the most critical design requirement (performance vs weight). |
typische applicaties | Extreme heat flux, high-temp environments | Automotive, Aerospace, General Industrial | – | Application dictates the best material choice. |
Exporteren naar Sheets
By carefully considering these material properties in conjunction with the application demands and the design possibilities offered by AM, engineers can select the optimal material for their custom heat sinks, ensuring efficient and reliable thermal management for critical power electronics.
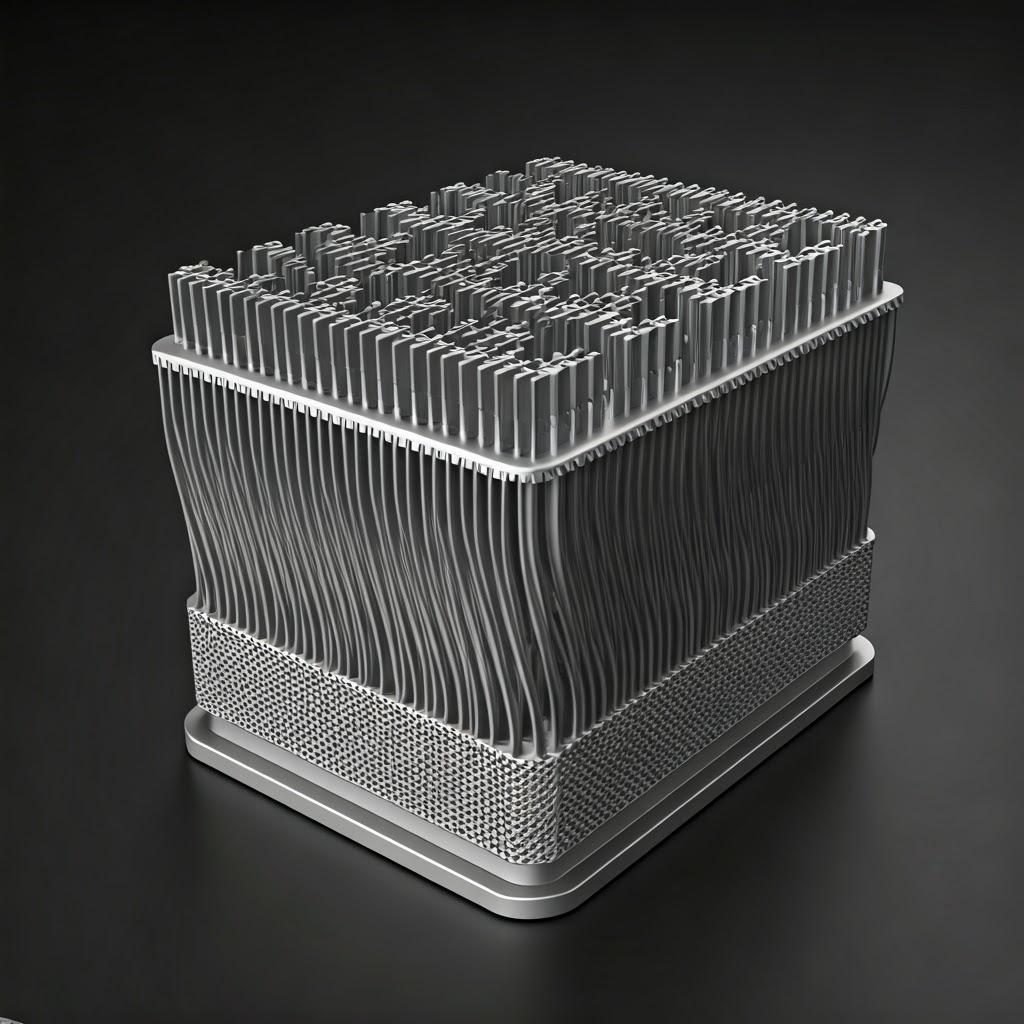
Design for Additive Manufacturing (DfAM): Optimizing Heat Sinks for 3D Printing
Simply replicating a traditionally designed heat sink using additive manufacturing often fails to leverage the technology’s true potential. To unlock the significant advantages in thermal performance, weight reduction, and integration offered by AM, engineers must embrace Ontwerp voor additieve productie (DfAM) principles. DfAM is a mindset and a set of methodologies focused on designing parts specifically for the layer-by-layer fabrication process, considering its unique capabilities and constraints. For heat sinks, this means rethinking geometry to maximize heat transfer efficiency within the given design space.
Key DfAM Considerations for AM Heat Sinks:
- Leveraging Geometric Complexity:
- Lattice and Gyroid Structures: Instead of simple extruded fins, consider complex, periodic structures like lattices or triply periodic minimal surfaces (TPMS) such as gyroids. These offer vastly increased surface area-to-volume ratios, promoting turbulent flow (in liquid cooling) and enhancing convective heat transfer. They also allow for significant lightweighting.
- Conforme koelkanalen: Design liquid cooling channels that precisely follow the contours of the heat-generating components (e.g., power modules, IGBTs). This minimizes the thermal path length and interface resistance, leading to more effective and uniform cooling compared to straight-drilled channels in machined blocks.
- Optimized Fin Shapes: Move beyond simple rectangular fins. AM allows for aerodynamically or hydrodynamically optimized fin shapes (e.g., airfoils, tapered profiles, variable density arrays) to improve airflow or liquid flow characteristics and reduce pressure drop. Generative design tools can assist in discovering non-intuitive, high-performance shapes.
- Topologieoptimalisatie:
- Utilize software tools to define loads (thermal and structural), constraints (keep-out zones, connection points), and objectives (minimize weight, maximize stiffness, optimize thermal path). The software then iteratively removes material from non-critical areas, resulting in organic, lightweight structures that efficiently transfer heat and withstand operational stresses. This is particularly crucial for lightweight thermal solutions in aerospace and automotive sectors.
- Feature Size and Resolution:
- Minimum Wall Thickness: Understand the limits of the chosen AM process (e.g., LPBF) and material. Typically, minimum printable wall thickness is around 0.3-0.5 mm. Designing below this can lead to print failures or incomplete features.
- Fin Spacing and Channel Diameter: Consider the powder particle size and laser beam spot size. Very narrow channels or tightly spaced fins can be difficult to print accurately and, critically, difficult to fully evacuate trapped powder from during post-processing. A balance must be struck between maximizing surface area and ensuring manufacturability and cleanability.
- Aspect Ratio: Tall, thin features can be prone to vibration or distortion during printing. Consider adding bracing or adjusting orientation if high aspect ratios are required.
- Ondersteunende structuren:
- AM processes typically require support structures for overhanging features (usually angles below 45 degrees from the horizontal build plane). Supports add print time, material cost, and require removal in post-processing, which can affect surface finish.
- Minimize Supports: Design parts with self-supporting angles whenever possible. Orient the heat sink strategically on the build plate to minimize the need for supports, especially on critical heat transfer surfaces or in complex internal channels where removal is difficult.
- Support Design: If supports are unavoidable, design them for easy removal (e.g., using tapered contact points) and consider their impact on surface roughness where they attach.
- Deeloriëntatie:
- The orientation of the heat sink on the build platform significantly impacts surface finish (up-facing vs. down-facing surfaces), dimensional accuracy (stair-stepping effect on curved surfaces), support requirements, and build time. Critical surfaces or fine features should ideally be oriented optimally relative to the recoater blade and build direction.
- Thermal Simulation:
- DfAM should be tightly integrated with thermal simulation (Computational Fluid Dynamics – CFD). Simulate the performance of AM-specific features like lattices or conformal channels early in the design process to validate their effectiveness and iterate towards an optimal solution before committing to a physical print. Simulation helps predict temperature distributions, pressure drops, and flow rates.
Integrating DfAM Expertise:
Successfully applying DfAM requires not only the right software tools but also a deep understanding of the AM process capabilities and material behaviors. Partnering with an experienced AM service provider like Met3dp can be invaluable. Our engineers possess expertise in DfAM for thermal management applications and can provide guidance on optimizing designs, selecting appropriate materials (like CuCrZr or AlSi10Mg), and identifying potential manufacturing challenges early on. This collaborative approach ensures that your custom heat sink design is not only innovative but also manufacturable and cost-effective.
Table: DfAM Strategies for Heat Sinks
DfAM Principle | Application to Heat Sinks | Voordeel |
---|---|---|
Complexe Geometrie | Lattices, gyroids, conformal channels, variable density fins | Increased surface area, improved flow mixing, reduced thermal resistance |
Topology Optimization | Minimizing material use while maintaining thermal/structural performance | Significant weight reduction, optimized heat paths |
Feature Size Control | Adhering to min. wall thickness, channel diameter, fin spacing limits | Ensures printability, prevents defects, allows powder removal |
Support Strategy | Designing self-supporting angles, minimizing supports on critical surfaces, easy-removal supports | Reduced post-processing effort, lower cost, better surface finish |
Orientation Planning | Placing critical surfaces optimally, considering build direction | Improved accuracy, better surface finish, reduced support needs |
Simulation Integration | Using CFD to validate complex geometries and thermal performance pre-print | Reduced prototyping iterations, performance prediction, design validation |
Deel Consolidatie | Integrating heat sink with enclosures, brackets, or fluid ports | Reduced part count, simplified assembly, potentially lower weight & cost |
Exporteren naar Sheets
By thoughtfully applying these DfAM principles, engineers can fully exploit the capabilities of metal AM to create next-generation heat sinks that significantly outperform their traditionally manufactured counterparts.
Precision and Finish: Understanding Tolerance, Surface Finish, and Dimensional Accuracy in AM Heat Sinks
While metal additive manufacturing unlocks incredible design freedom, it’s essential for engineers and procurement managers to have realistic expectations regarding the achievable precision, surface finish, and dimensional accuracy of 3D printed heat sinks. These factors directly impact assembly fit, thermal contact resistance, and fluid dynamics (for liquid-cooled designs). Understanding the typical capabilities and influencing factors is crucial for defining specifications and ensuring the final part meets functional requirements.
Maatnauwkeurigheid en toleranties:
- Typical Tolerances: For processes like Laser Powder Bed Fusion (LPBF/SLM), which are commonly used for heat sinks made from AlSi10Mg and CuCrZr, typical dimensional accuracy is often cited in the range of ±0.1 mm to ±0.2 mm for smaller features, or ±0.1% to ±0.2% of the overall dimension for larger parts. However, this can vary significantly based on several factors.
- Beïnvloedende factoren:
- Machinekalibratie: Regular and precise calibration of the AM system (lasers, scanners, powder deposition) is critical.
- Onderdeelgeometrie en -grootte: Larger parts and complex geometries are more susceptible to thermal stresses during the build, which can cause warping or distortion, impacting final accuracy.
- Materiaal: Different materials have different shrinkage rates and thermal properties, affecting distortion.
- Oriëntatie: The orientation on the build plate influences accuracy due to factors like thermal gradients and the “stair-stepping” effect on angled or curved surfaces.
- Ondersteunende strategie: Supports help anchor the part and manage thermal stress but can also influence local accuracy.
- Thermisch beheer: Build plate heating and chamber atmosphere control help mitigate thermal stress.
- Achieving Tighter Tolerances: If specific features require tolerances tighter than the standard AM process capability (e.g., mounting interfaces, surfaces for thermal interface materials – TIMs), post-process machining is typically required. It’s essential to identify these critical dimensions in the design phase and include machining allowances.
Oppervlakteafwerking (ruwheid):
- As-Printed Surface Roughness (Ra): Metal AM parts inherently have a rougher surface finish compared to machined parts. The roughness depends heavily on:
- Proces: LPBF/SLM typically yields Ra values from 8 µm to 25 µm or higher. Electron Beam Melting (EBM) generally produces rougher surfaces.
- Materiaal: Powder particle size and morphology affect the resulting surface.
- Oriëntatie: Up-facing surfaces (facing away from the build plate) are generally smoother than down-facing surfaces (supported surfaces) or vertical walls. Angled surfaces exhibit stair-stepping.
- Parameters: Laser power, speed, and layer thickness influence melt pool dynamics and surface texture.
- Impact on Heat Sinks:
- Thermal Contact Resistance: Rough surfaces create microscopic air gaps when mated with a component, increasing thermal resistance. Smooth surfaces are crucial for efficient heat transfer at interfaces, often requiring post-processing.
- Fluid Dynamics: In liquid-cooled heat sinks, surface roughness inside channels increases friction and pressure drop, potentially affecting flow rate and pumping power requirements.
- Cleanliness: Rough surfaces can be harder to clean thoroughly, potentially trapping residual powder.
- Verbetering van de oppervlakteafwerking: Various post-processing techniques (discussed in the next section) like bead blasting, tumbling, polishing, or electro-polishing can significantly improve the surface finish (reducing Ra) where required.
Managing Expectations:
- Specify Critical Features: Clearly define which dimensions and surfaces require tight tolerances or smooth finishes. Avoid over-specifying the entire part, as this unnecessarily increases cost.
- Consult Your AM Provider: Discuss requirements with your chosen metal AM service bureau, like Met3dp, early in the process. They can provide guidance on achievable tolerances and finishes with their specific afdrukmethoden and materials, recommend design adjustments, and plan necessary post-processing steps.
- Consider Functional Requirements: Determine the level of precision and finish truly needed for the heat sink to function correctly. Is sub-micron Ra needed, or is a standard AM finish acceptable for non-contact surfaces?
Table: Typical LPBF/SLM Precision & Finish
Parameter | Typical Range (As-Printed) | Influenced By | Implications for Heat Sinks | Mitigation / Improvement |
---|---|---|---|---|
Maattolerantie | ±0.1 to ±0.2 mm or ±0.1-0.2% | Machine calibration, part size/geometry, material, orientation, thermal stress | Affects assembly fit, alignment with power modules | Post-process CNC machining for critical dimensions |
Oppervlakteruwheid (Ra) | 8 – 25+ µm | Process, material, orientation (up-skin vs down-skin), parameters | Increases thermal contact resistance, affects fluid flow (pressure drop), powder trapping | Post-processing (blasting, polishing, etc.) |
Minimale grootte | ~0.3 – 0.5 mm (walls/fins) | Process resolution (laser spot, layer thickness), powder size | Limits fin density, minimum channel size | DfAM optimization, process selection |
Warping / Distortion | Variabele | Thermal gradients, residual stress, support strategy, part geometry | Can affect flatness of mounting surfaces, overall dimensional accuracy | Optimized orientation, supports, heat treatment |
Exporteren naar Sheets
By understanding these parameters, designers can create heat sinks that are not only functionally superior due to AM geometries but also meet the necessary standards for integration and performance in their target power electronic systems.

Essential Post-Processing for 3D Printed Metal Heat Sinks
A common misconception about metal additive manufacturing is that parts come out of the printer ready to use. In reality, especially for demanding applications like heat sinks, several post-processing steps are typically required to achieve the desired material properties, dimensional accuracy, surface finish, and overall functionality. Planning for these steps is crucial for accurate cost estimation and lead time prediction when working with an AM contract manufacturer.
Common Post-Processing Steps for AM Heat Sinks:
- Stress Relief / Heat Treatment:
- Doel: The rapid heating and cooling cycles inherent in powder bed fusion processes induce residual stresses within the printed part. These stresses can cause distortion (especially after removal from the build plate) and potentially reduce the part’s fatigue life or mechanical strength. Heat treatment relieves these stresses and can also modify the material’s microstructure to achieve desired properties (e.g., precipitation hardening in CuCrZr to maximize conductivity and strength, or optimizing ductility in AlSi10Mg).
- Proces: Parts are heated in a controlled atmosphere furnace to specific temperatures for defined durations, followed by controlled cooling. The exact cycle depends heavily on the material (CuCrZr and AlSi10Mg have very different requirements) and the desired final properties.
- Noodzaak: Generally considered essential for most functional metal AM parts, particularly those under thermal or mechanical loads, like heat sinks.
- Onderdeel verwijderen van bouwplaat:
- Proces: Parts are typically printed on a thick metal build plate. Removal usually involves wire EDM (Electrical Discharge Machining) or sawing to cut the part away from the plate at the base or support interface.
- Overwegingen: This step needs careful handling to avoid damaging the part.
- Draagstructuur verwijderen:
- Doel: Removing the temporary support structures added during the build process.
- Proces: Can range from simple manual breaking/clipping (for well-designed supports) to more involved methods like CNC machining, grinding, or manual tooling, especially for supports in hard-to-reach areas or made from tough materials.
- Overwegingen: Support removal can leave witness marks or rougher surface patches (“scars”) that may require further finishing. DfAM aims to minimize support needs, especially on critical surfaces.
- Powder Removal / Cleaning:
- Doel: Ensuring all unfused metal powder, especially from internal channels or complex lattice structures, is removed from the heat sink. Trapped powder can impede fluid flow, add weight, and potentially become dislodged during operation.
- Proces: Typically involves compressed air blow-off, bead blasting (which also improves surface finish), ultrasonic cleaning baths, or specialized de-powdering stations. Accessing deep or intricate internal channels can be challenging.
- Noodzaak: Absolutely critical, particularly for heat sinks with internal cooling channels or fine lattice/fin structures.
- Afwerking oppervlak:
- Doel: Improving the as-printed surface roughness (Ra) for various reasons: reducing thermal contact resistance, improving fluid dynamics, enhancing aesthetics, or preparing for coatings.
- Processes:
- Bead Blasting / Sand Blasting: Propels abrasive media at the surface to create a uniform, matte finish, removing loose powder and slightly smoothing the surface.
- Tumbling / Vibratory Finishing: Places parts in a tumbler with media that abrades the surface, effective for smoothing edges and surfaces, especially on batches of smaller parts.
- Polijsten: Manual or automated mechanical polishing using abrasive compounds to achieve very smooth, reflective surfaces (low Ra). Often targeted at specific areas like thermal interface surfaces.
- Electro-polishing: An electrochemical process that removes a microscopic layer of material, resulting in a very smooth and clean surface. Particularly effective for complex shapes and internal channels.
- CNC-bewerking:
- Doel: To achieve tight tolerances, specific flatness, or smooth finishes on critical features that cannot be met by the AM process alone. Common for mounting surfaces, O-ring grooves, or threaded holes.
- Proces: Utilizes traditional subtractive machining (milling, turning, drilling) on the AM part. Requires careful fixture design to hold the potentially complex AM geometry. Design must include machining allowances (extra material) on relevant surfaces.
- Inspection and Quality Control (QC):
- Doel: Verifying dimensional accuracy, checking for defects (cracks, porosity), confirming material properties, and ensuring cleanliness.
- Methoden: Coordinate Measuring Machines (CMM), 3D scanning, CT scanning (for internal geometry and defects), pressure testing (for liquid channels), material testing, visual inspection.
Choosing a Post-Processing Partner:
Veel metal AM service providers, including Met3dp, offer a suite of in-house or closely managed post-processing services. Sourcing from a provider with integrated capabilities simplifies the supply chain for groothandel kopers and ensures accountability throughout the manufacturing process. When evaluating suppliers, inquire about their specific post-processing capabilities relevant to heat sink requirements (e.g., experience with copper heat treatment, precision machining, internal channel cleaning).
Table: Post-Processing Steps & Relevance to Heat Sinks
Post-Processing Step | Purpose for Heat Sinks | Typical Necessity | Material Specific? |
---|---|---|---|
Hittebehandeling | Relieve stress, optimize thermal/mechanical properties (esp. conductivity in CuCrZr) | High (Usually Essential) | Yes (Cycles vary) |
Build Plate Removal | Separate part from build plate | Essentieel | Nee |
Ondersteuning verwijderen | Remove temporary structures | Essential (If supported) | No (But difficulty varies) |
Poeder verwijderen | Ensure cleanliness, prevent blockage (esp. internal channels/lattices) | Essentieel | No (But difficulty varies) |
Oppervlakteafwerking | Reduce Ra (thermal interface, flow), improve aesthetics | Application Dependent | No (Method may vary) |
CNC-bewerking | Achieve tight tolerances/flatness on critical surfaces (e.g., mounting face) | Application Dependent | No (Requires planning) |
QC / Inspection | Verify dimensions, integrity, performance | Essentieel | Yes (Methods may vary) |
Exporteren naar Sheets
Effectively planning and executing these post-processing steps is just as critical as the printing process itself for producing high-quality, reliable metal AM heat sinks.
Overcoming Hurdles: Common Challenges and Solutions in Printing Metal Heat Sinks
While metal additive manufacturing offers transformative potential for heat sink design and performance, the process is not without its challenges. Understanding these potential hurdles and how to mitigate them is crucial for successful implementation. Engineers, procurement managers, and AM suppliers must work collaboratively to navigate these complexities.
Gemeenschappelijke uitdagingen en risicobeperkende strategieën:
- Vervorming en vervorming:
- Uitdaging: The intense localized heating from the laser or electron beam, followed by rapid cooling, creates significant thermal gradients and residual stresses. These stresses can cause the part to warp or distort during the build or after removal from the build plate, affecting dimensional accuracy and flatness, particularly for large or thin structures common in heat sinks.
- Solutions:
- Geoptimaliseerde oriëntatie: Orienting the part to minimize large flat areas parallel to the build plate can help.
- Robust Support Structures: Properly designed supports anchor the part and help dissipate heat, reducing stress accumulation.
- Processimulatie: Build simulation software can predict stress concentrations and deformation, allowing for pre-compensation in the design or optimization of support strategies.
- Thermisch beheer: Using build plate heating and maintaining stable chamber temperatures minimizes thermal gradients.
- Stressverlichtende warmtebehandeling: Post-print heat treatment is essential to relieve residual stresses before part removal or machining.
- Achieving and Verifying Fine Features:
- Uitdaging: Heat sinks often rely on thin fins, narrow channels, or intricate lattice structures to maximize surface area. Printing these features consistently at the limits of the machine’s resolution can be difficult. Ensuring these fine features are fully formed and dimensionally accurate requires precise process control.
- Solutions:
- Parameter Optimization: Fine-tuning laser power, speed, scan strategy, and layer thickness for the specific material and feature size.
- DfAM: Designing features slightly above the absolute minimum printable size for better robustness. Avoiding excessively high aspect ratios.
- High-Resolution AM Systems: Utilizing machines with smaller laser spot sizes or optimized beam control.
- Metrology: Using high-resolution inspection techniques (e.g., CT scanning, microscopy) to verify internal and external feature dimensions.
- Residual Powder Removal:
- Uitdaging: Complex internal cooling channels, narrow fin gaps, and dense lattice structures create geometries where unfused metal powder can become trapped. Incomplete powder removal compromises thermal performance (blocking flow paths), adds weight, and risks contamination during operation.
- Solutions:
- DfAM: Designing channels with sufficient diameter, smooth transitions, and potentially including dedicated drain/access holes for powder removal. Avoiding “dead zones” in lattices where powder can easily settle.
- Geoptimaliseerde oriëntatie: Orienting the part to facilitate powder drainage during the build and post-processing.
- Advanced Cleaning Techniques: Utilizing high-pressure air/gas jets, ultrasonic cleaning, micro-blasting, or chemical flushing methods specifically chosen for the geometry and material.
- Inspectie: Using endoscopy or CT scanning to verify complete powder removal from internal passages.
- Managing Material Properties (Especially Copper Alloys):
- Uitdaging: Materials like CuCrZr have high thermal conductivity and reflectivity, making them more challenging to process consistently with lasers compared to aluminum or steel. Achieving full density without defects (like porosity) and obtaining the desired microstructure (for optimal conductivity post-heat treatment) requires specialized expertise and carefully controlled parameters.
- Solutions:
- Geoptimaliseerde procesparameters: Using higher laser power, specific scan strategies (e.g., pulse shaping), and potentially modified wavelengths (e.g., green lasers) to improve energy absorption.
- Atmosphere Control: Maintaining a high-purity inert gas atmosphere to prevent oxidation.
- Poederkwaliteit: Using high-quality spherical powder with optimized particle size distribution specifically designed for AM (as provided by specialists like Met3dp).
- Heat Treatment Expertise: Precise control over post-print heat treatment cycles is critical for achieving target properties in alloys like CuCrZr.
- Thermal Performance Validation:
- Uitdaging: Ensuring the complex, additively manufactured heat sink performs thermally as predicted by simulations. Factors like as-built surface roughness, slight dimensional deviations, and actual material properties (which can differ slightly from wrought properties) can influence real-world performance.
- Solutions:
- Accurate Simulation Inputs: Using material property data representative of the AM process and incorporating factors like surface roughness effects in CFD models.
- Rigorous Physical Testing: Performing bench tests using calibrated heat sources and temperature sensors to measure thermal resistance (Rth) and pressure drop under realistic operating conditions.
- Iteratief ontwerp: Comparing test results with simulations and iterating on the design or process parameters if performance targets are not met.
Partnering for Success:
Overcoming these challenges requires a deep understanding of materials science, AM process physics, and thermal engineering. This is where partnering with a knowledgeable and experienced metal AM solutions provider becomes invaluable. Met3dp combines expertise in advanced metaalpoederproductie with state-of-the-art printing capabilities and a thorough understanding of post-processing requirements. Our team collaborates with clients to anticipate potential issues, optimize designs for manufacturability, and implement robust process controls and quality checks, ensuring the successful production of high-performance custom heat sinks. We help navigate the complexities, turning potential hurdles into manageable steps towards achieving superior thermal management solutions.
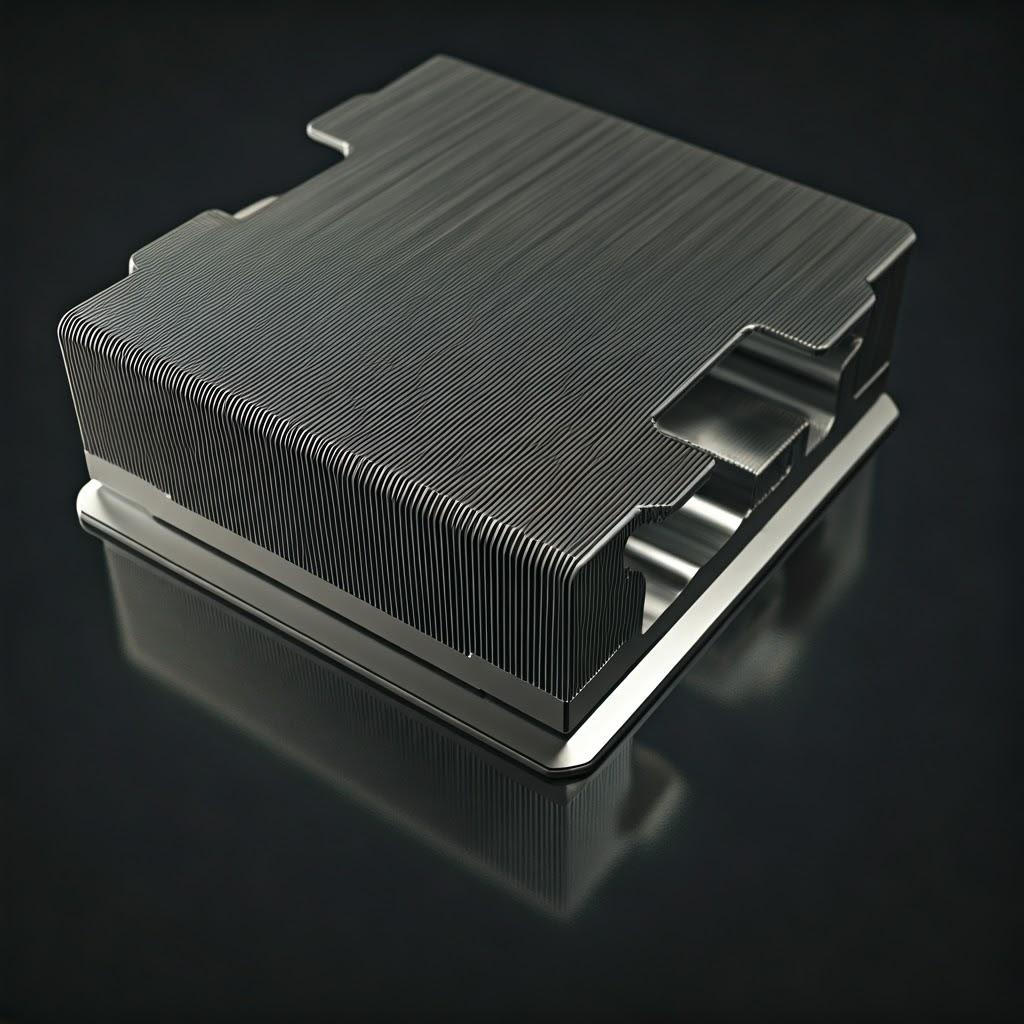
Supplier Selection: Choosing the Right Metal AM Partner for Your Heat Sink Needs
Selecting the right manufacturing partner is as critical as the design and material choice when embarking on producing custom heat sinks via metal additive manufacturing. Not all AM service providers possess the specific expertise, equipment, and quality systems required for demanding thermal management applications, especially when working with materials like high-conductivity copper alloys. For engineers and procurement managers seeking reliable custom heat sink manufacturers, careful evaluation based on relevant criteria is essential.
Key Criteria for Evaluating Metal AM Suppliers for Heat Sinks:
- Material Expertise & Availability:
- Specific Alloys: Does the supplier routinely process the required materials, particularly AlSi10Mg and, crucially, CuCrZr or other copper alloys? Ask for evidence of successful prints and material property data achieved with these metals. Handling copper alloys effectively requires specialized parameter sets and machine capabilities.
- Poederkwaliteit: Inquire about their powder sourcing and quality control. Do they use high-quality, AM-optimized powders? Providers like Met3dp, who manufacture their own high-performance powders using advanced methods like PREP and gas atomization, offer greater control over the entire process chain.
- Machine Capabilities & Technology:
- Process Suitability: Ensure they utilize appropriate AM technology, typically Laser Powder Bed Fusion (LPBF/SLM) for the fine features and material compatibility needed for heat sinks.
- Machine Specifications: Consider build volume (can they accommodate your part size?), laser power (important for reflective materials like copper), and atmosphere control (critical for preventing oxidation).
- Maintenance & Calibration: Well-maintained and regularly calibrated machines are crucial for consistent quality and dimensional accuracy.
- Thermal Design & DfAM Support:
- Engineering Expertise: Does the supplier have engineers experienced in thermal management and Design for Additive Manufacturing (DfAM)? Can they offer constructive feedback on your design to improve performance, reduce weight, enhance manufacturability, and minimize cost? Collaborative design refinement is a significant value-add.
- Mogelijkheden voor nabewerking:
- Integrated Services: Does the supplier offer necessary post-processing in-house or through trusted partners? This includes stress relief/heat treatment (with proper equipment and knowledge for specific alloys), precision CNC machining, support/powder removal (especially for internal channels), and various surface finishing options. An integrated workflow simplifies logistics and quality management.
- Quality Management Systems & Certifications:
- Relevant Certifications: Look for certifications like ISO 9001 (general quality management). Depending on your industry, certifications like AS9100 (aerospace) or ISO 13485 (medical devices) might be required or indicate a higher level of process control and traceability.
- Inspection Capabilities: What metrology equipment do they use (CMM, 3D scanning, CT scanning)? Can they provide comprehensive inspection reports to verify dimensional accuracy and internal integrity?
- Track Record & Praktijkvoorbeelden:
- Relevant Experience: Ask for examples or case studies of similar projects, particularly involving heat sinks, thermal management components, or parts made from your chosen material. This demonstrates proven capability.
- Customer References: Reputable suppliers should be willing to provide references upon request.
- Communication & Project Management:
- Responsiveness: How quickly and thoroughly do they respond to inquiries and technical questions?
- Project Management: Is there a clear point of contact and process for managing your project from quote to delivery? Good communication is vital for complex AM projects.
- Quoting Process & Transparency:
- Detailed Quotes: Ensure quotes clearly break down costs (material, print time, post-processing, NRE) and state lead times. Understand the assumptions behind the quote.
- Fair Pricing: While cost is important, the cheapest option may not offer the necessary expertise or quality for critical components like heat sinks. Balance cost with capability and reliability.
Why Partner with Met3dp?
Met3dp stands out as a comprehensive metal additive manufacturing solutions provider. Our integrated approach, combining advanced metal powder production with state-of-the-art printing technology, offers significant advantages:
- Material Control: As manufacturers of high-quality spherical metal powders, including those suitable for thermal applications, we ensure the optimal starting point for your components.
- Technische expertise: Our team possesses deep knowledge in materials science, AM processes (including SEBM and LPBF), and DfAM, ready to collaborate on optimizing your heat sink design. Learn more over ons and our commitment to innovation.
- Industry Focus: We understand the demanding requirements of industries like aerospace, medical, and automotive, delivering parts with industry-leading accuracy and reliability.
- Comprehensive Solutions: From powder to finished part, including necessary post-processing and quality control, we offer a streamlined manufacturing experience.
Choosing the right partner is an investment in the success of your project. Thoroughly evaluating potential metal AM suppliers based on these criteria will help ensure you receive high-quality, reliable custom heat sinks that meet your performance expectations.
Understanding Investment: Cost Factors and Typical Lead Times for AM Heat Sinks
One of the primary considerations for adopting any new manufacturing technology is understanding the associated costs and production timelines. While metal additive manufacturing offers unique benefits for custom heat sinks, it’s important to recognize the factors that influence pricing and lead times compared to traditional methods, especially for groothandel kopers en procurement teams evaluating total cost of ownership.
Key Cost Drivers for Metal AM Heat Sinks:
- Material Type and Consumption:
- Kosten poeder: The raw material cost varies significantly. High-performance copper alloys like CuCrZr are considerably more expensive per kilogram than common aluminum alloys like AlSi10Mg. The volume of material used directly impacts cost.
- Part Volume/Mass: Larger, denser parts consume more powder and take longer to print, increasing costs. DfAM techniques like topology optimization can significantly reduce material usage and weight, thus lowering costs.
- Afdruktijd:
- Build Height: This is often the most significant factor driving print time. Taller parts require more layers, directly increasing the time the machine is occupied. Printing multiple parts simultaneously (nesting) can improve machine utilization but depends on part geometry and build volume.
- Deel Complexiteit: Highly intricate designs with extensive laser scanning paths or numerous thin features can increase print time per layer.
- Ondersteunende structuren: The volume of support material required adds to both print time and material consumption, as well as post-processing time.
- Machine Usage:
- Uurloon machine: AM service providers factor in the depreciation, maintenance, operation, and energy costs of expensive industrial metal 3D printers into their pricing, often calculated as an hourly rate.
- Setup & Teardown: Time required for preparing the build (loading powder, setting up the file) and removing the part post-build contributes to the overall cost.
- Vereisten voor nabewerking:
- Complexity & Extent: The number and complexity of post-processing steps significantly impact cost. Extensive CNC machining, intricate support removal, high-level surface polishing, or specialized heat treatments add considerable cost compared to basic stress relief and bead blasting.
- Manual Labor: Many post-processing steps (support removal, polishing) involve skilled manual labor, contributing to the cost.
- Quality Assurance & Inspection:
- Level of Inspection: Basic dimensional checks are standard, but more rigorous inspection (e.g., CT scanning for internal channel verification, detailed CMM reports, material testing) adds cost. The level required depends on the criticality of the application.
- Bestelhoeveelheid:
- Schaalvoordelen: While AM avoids tooling costs, some economies of scale exist. Larger batches allow for better machine utilization (nesting parts), potentially distributing setup costs over more units and potentially offering volume discounts from the AM supplier. However, the cost-per-part reduction is generally less dramatic than in traditional high-volume methods like casting or extrusion.
- Non-Recurring Engineering (NRE):
- Design Optimization/Support: If significant DfAM support or design modification is required from the service provider, this may be quoted as a separate NRE cost.
Typical Lead Times:
Lead times for custom AM heat sinks can vary widely based on complexity, quantity, material, and the supplier’s backlog. A rough breakdown might look like this:
- Quoting & Design Finalization: 1-5 business days (assuming a ready design); longer if DfAM consultation is needed.
- Build Preparation & Printing: 2-10+ business days (highly dependent on part size, height, quantity, and material). Printing complex copper parts may take longer than simpler aluminum ones.
- Nabewerking: 3-15+ business days (dependent on the required steps: heat treatment cycles take time, complex machining adds days, extensive polishing is labor-intensive).
- Inspection & Shipping: 1-3 business days.
Total estimated lead time: Gewoonlijk varieert het van 1.5 to 5 weeks, but can be longer for very complex projects or large quantities. It’s crucial to get specific lead time estimates from your chosen supplier based on your final design.
Requesting Quotes (RFQ):
To get accurate pricing and lead times, provide potential suppliers with:
- A 3D CAD model (STEP format preferred).
- A 2D drawing specifying critical dimensions, tolerances, required surface finishes, and material.
- The desired quantity.
- Any specific post-processing or inspection requirements.
Understanding these cost factors and typical timelines allows for better budgeting, project planning, and informed decision-making when considering metal AM for producing high-performance, custom heat sinks.
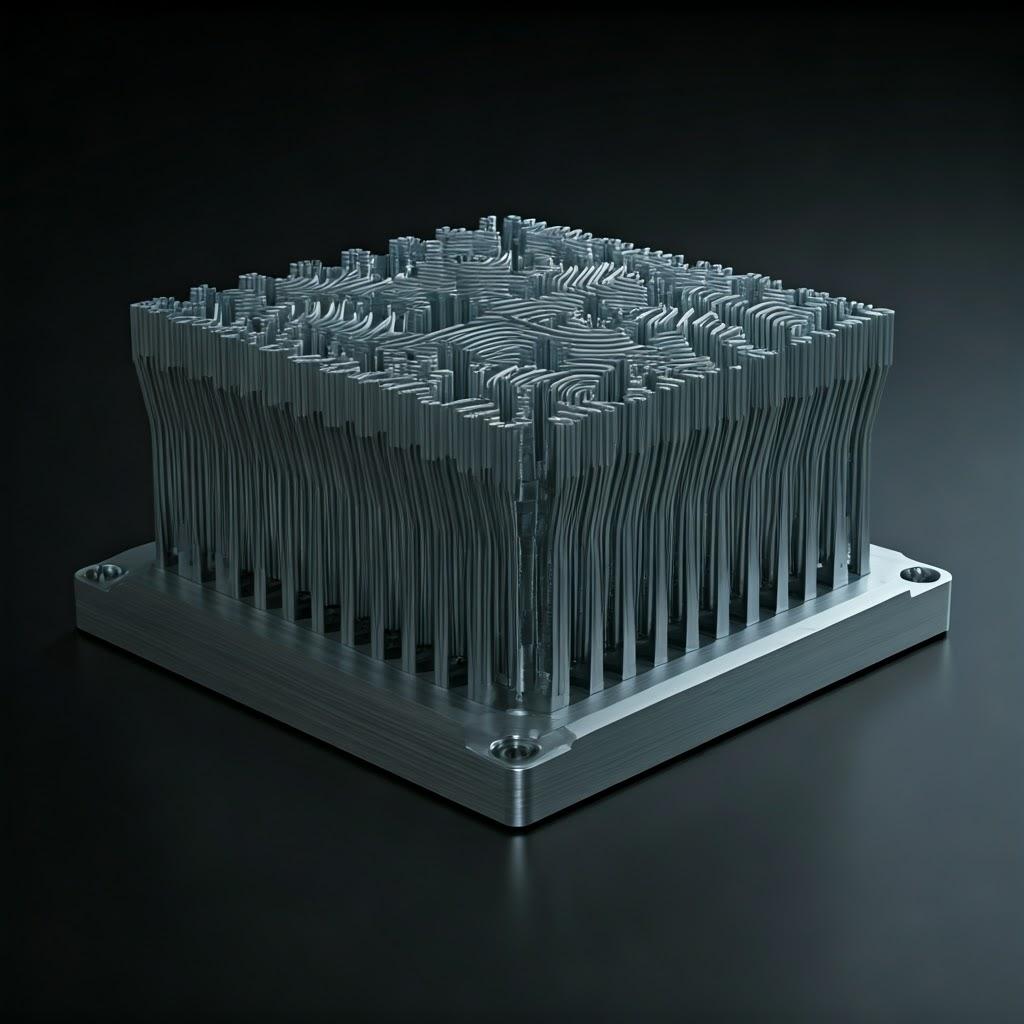
FAQ: Your Questions Answered on Custom Metal AM Heat Sinks
Here are answers to some frequently asked questions about using metal additive manufacturing for custom heat sinks:
- Are 3D printed metal heat sinks actually better than traditional ones (e.g., machined or extruded)?
- Antwoord: They kan be significantly better, but it depends on the application and design. Metal AM allows for highly complex geometries (like internal lattices or conformal channels) and topology optimization that are impossible with traditional methods. This can lead to superior thermal performance (lower thermal resistance), significant weight reduction, and better integration within tight spaces. However, for simple, high-volume heat sink designs where cost is the primary driver and standard performance is adequate, traditional methods like extrusion might still be more economical. The key advantage of AM lies in customization and performance optimization voor veeleisende toepassingen.
- Is metal 3D printing an expensive way to make heat sinks?
- Antwoord: The cost per part for metal AM can be higher than traditional mass production methods, especially for simple designs, due to material costs, machine time, and necessary post-processing. However, AM eliminates tooling costs, making it very cost-effective for prototypes, low-to-medium volume production runs, and highly customized designs. Furthermore, when considering the total system benefit – such as improved performance enabling higher power density, reduced weight saving fuel in vehicles, or part consolidation simplifying assembly – the overall value proposition of AM heat sinks can be highly favorable, justifying the initial part cost. Factors like material choice (CuCrZr vs. AlSi10Mg), complexity, and volume heavily influence the price.
- What is the best material for a 3D printed heat sink: Aluminum (AlSi10Mg) or Copper (CuCrZr)?
- Antwoord: There isn’t a single “best” material; the optimal choice depends on the specific requirements:
- Choose CuCrZr if maximum thermal performance is the absolute priority, especially in high heat flux situations or elevated operating temperatures, and if the higher weight and cost are acceptable.
- Choose AlSi10Mg if laag gewicht, good thermal performance, En kosteneffectiviteit are the primary drivers. It’s suitable for a wide range of applications in automotive, aerospace, and industrial sectors where its thermal conductivity is sufficient.
- Met3dp can help evaluate your application’s needs and recommend the most suitable material from our portfolio of high-quality AM powders.
- Antwoord: There isn’t a single “best” material; the optimal choice depends on the specific requirements:
- How complex can the internal cooling channels or fin structures be in an AM heat sink?
- Antwoord: Metal AM allows for extremely complex internal features, including intricate lattice structures, smoothly curving conformal channels, and very fine, densely packed fins. However, there are practical limits based on the chosen AM process resolution (minimum feature size typically ~0.3-0.5 mm) and, importantly, the ability to remove unfused powder after printing. Designs must incorporate considerations for powder removal (e.g., minimum channel diameters, access ports). DfAM principles and collaboration with your AM provider are key to leveraging complexity effectively while ensuring manufacturability.
- Can Met3dp help me design or optimize my heat sink for additive manufacturing?
- Antwoord: Yes, absolutely. Met3dp offers comprehensive solutions that include application development services. Our team has expertise in DfAM, thermal management principles, and the specific capabilities of our AM processes and materials. We can work with your engineers to review existing designs, suggest optimizations for performance and manufacturability using AM, or assist in developing new concepts that fully leverage the benefits of additive manufacturing for your thermal challenges.
Conclusion: Embracing Additive Manufacturing for Next-Generation Power Electronics Cooling
The relentless push for higher power density, increased efficiency, and component miniaturization across industries places unprecedented demands on thermal management solutions. Traditional manufacturing methods for heat sinks, while effective for standard applications, often fall short when faced with complex geometries, stringent weight targets, and the need for highly customized cooling. Metal additive manufacturing has emerged as a powerful enabler, transforming how engineers approach heat sink design and fabrication for power electronics.
As we’ve explored, metal AM offers compelling advantages:
- Ongeëvenaarde ontwerpvrijheid: Enabling complex internal channels, optimized fin structures, and topology-optimized forms that drastically improve thermal performance and reduce weight.
- Hoogwaardige materialen: Facilitating the use of materials like high-conductivity CuCrZr and versatile, lightweight AlSi10Mg in intricate shapes.
- Customization & Speed: Allowing for rapid prototyping and cost-effective production of bespoke heat sinks tailored to specific power modules and environments.
- Integration Potential: Enabling part consolidation by integrating thermal management features directly into structural components.
From enhancing the range of electric vehicles through lighter, more efficient inverter cooling, to ensuring the reliability of critical aerospace power systems, and enabling more compact industrial drives, the impact of custom AM heat sinks is already significant and continues to grow. While challenges related to design optimization, process control, and post-processing exist, they are readily overcome through expertise and collaboration.
Choosing the right materials, applying DfAM principles, understanding process capabilities, and partnering with an experienced supplier are key to unlocking the full potential of this technology. Met3dp, with its foundation in advanced metal powder manufacturing and state-of-the-art additive manufacturing capabilities, provides comprehensive solutions to meet your most demanding thermal management needs. We are committed to partnering with organizations to implement 3D printing and accelerate digital manufacturing transformations.
Ready to revolutionize your thermal management? Explore the possibilities of custom metal AM heat sinks for your power electronics applications. Contact Met3dp today to discuss your project requirements with our experts and discover how our cutting-edge systems and high-quality powders can power your organization’s additive manufacturing goals.
Delen op
MET3DP Technology Co, LTD is een toonaangevende leverancier van additieve productieoplossingen met hoofdkantoor in Qingdao, China. Ons bedrijf is gespecialiseerd in 3D printapparatuur en hoogwaardige metaalpoeders voor industriële toepassingen.
Onderzoek om de beste prijs en een op maat gemaakte oplossing voor uw bedrijf te krijgen!
gerelateerde artikelen
Over Met3DP
Recente update
Ons product
NEEM CONTACT MET ONS OP
Nog vragen? Stuur ons nu een bericht! Na ontvangst van uw bericht behandelen wij uw verzoek met een heel team.
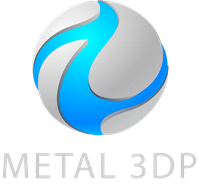
Metaalpoeders voor 3D printen en additieve productie