Spuitgietpoeder
Inhoudsopgave
Spuitgietpoeder verwijst naar een type basismateriaal dat gebruikt wordt bij poederspuitgieten, een industrieel productieproces om complexe metalen onderdelen met hoge precisie te maken. Dit poeder is een mengsel van fijne metaalpoeders en polymeerbindmiddelen die in grote volumes spuitgegoten kunnen worden tot complexe netvormige onderdelen.
Voordelen van het gebruik van spuitpoeder
Voordeel | Beschrijving | Voordeel |
---|---|---|
Complexe geometrieën: Met IMP kunnen ingewikkelde vormen met fijne kenmerken worden gemaakt die met traditionele spuitgiettechnieken moeilijk of onmogelijk te realiseren zijn. Deze ontwerpvrijheid opent deuren voor innovatieve componenten in diverse industrieën. | In tegenstelling tot traditionele vormmaterialen zoals gesmolten kunststof, gebruikt IMP een bindmiddelsysteem dat de poederdeeltjes bij elkaar houdt tijdens het vormproces. Hierdoor kunnen onderdelen met interne kanalen, ondersnijdingen en andere complexe geometrieën worden gemaakt. | |
Materiaalefficiëntie: IMP bevordert bijna-net-vorm productie, waardoor materiaalverspilling wordt geminimaliseerd in vergelijking met subtractieve technieken zoals machinale bewerking. Dit is vooral gunstig voor dure of hoogwaardige materialen. | De nauwkeurige controle over de poederverdeling tijdens het spuitgieten minimaliseert overmatig materiaalgebruik. Bovendien zorgt IMP, in tegenstelling tot traditionele processen waarbij afvalproducten ontstaan tijdens proefruns, voor snellere ontwerpiteraties met minimale materiaalverspilling. | |
Brede materiaalselectie: IMP biedt een breder scala aan materiaalopties in vergelijking met traditioneel spuitgieten. Deze veelzijdigheid maakt het mogelijk om onderdelen te maken met specifieke eigenschappen op maat van de toepassing. | Naast de standaardpolymeren die worden gebruikt bij spuitgieten, kan IMP metaalpoeders, keramiek en zelfs composietmaterialen gebruiken. Dit opent deuren voor het maken van onderdelen met unieke combinaties van sterkte, geleidbaarheid of biocompatibiliteit. | |
Hoogwaardige onderdelen: De mogelijkheid om metaal- en keramiekpoeders te gebruiken in IMP maakt de productie mogelijk van hoogwaardige onderdelen met uitzonderlijke sterkte, hittebestendigheid of slijtage-eigenschappen. | Onderdelen van metaalspuitgieten (MIM) kunnen mechanische eigenschappen bereiken die vergelijkbaar zijn met die van gesmeed (bulk) metaal, waardoor ze geschikt zijn voor veeleisende toepassingen. Op dezelfde manier bieden keramische IMP onderdelen uitstekende slijtvastheid en prestaties bij hoge temperaturen. | |
Potentieel voor massaproductie: De IMP-technologie werd aanvankelijk gebruikt voor prototyping, maar is nu volwassen genoeg om kosteneffectieve massaproductie van complexe onderdelen mogelijk te maken. | De hoge mate van automatisering die mogelijk is bij IMP-processen maakt efficiënte productie van grote hoeveelheden onderdelen van constante kwaliteit mogelijk. Dit maakt het een haalbare optie voor toepassingen met grote volumes. | |
Verbeterde oppervlakteafwerking: Vergeleken met traditionele metaalgiettechnieken kan IMP soms een gladdere afwerking van het oppervlak van de uiteindelijke onderdelen bereiken. | Het gebruik van fijne poeders en het gecontroleerde vormproces kunnen imperfecties aan het oppervlak minimaliseren, waardoor mogelijk uitgebreide nabewerkingsstappen zoals polijsten minder nodig zijn. |
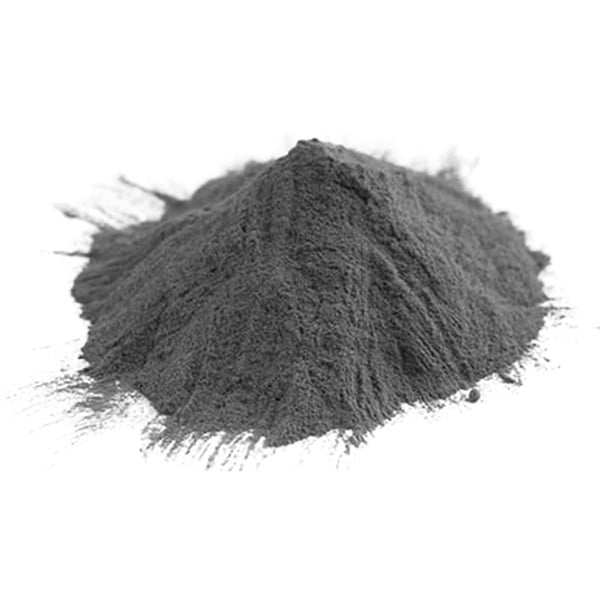
Samenstelling van spuitgietpoeder
Onderdeel | Beschrijving | Functie |
---|---|---|
Basis Poeders | Deze vormen het primaire functionele materiaal van het uiteindelijke onderdeel en kunnen worden onderverdeeld in drie hoofdtypen: Metaalpoeders: Fijn verdeelde metalen deeltjes van verschillende legeringen, zoals roestvrij staal, gereedschapsstaal of superlegeringen. Keramische poeders: Keramische materialen zoals aluminiumoxide, zirkoniumoxide of siliciumnitride in poedervorm. Polymeerpoeder: Thermoplastische polymeren die vaak worden gebruikt bij spuitgieten, zoals nylon of polypropyleen. | De keuze van het basispoeder bepaalt de uiteindelijke eigenschappen van het spuitgietproduct, zoals sterkte, slijtvastheid of thermische prestaties. |
Bindmiddel systeem | Dit is een cruciaal onderdeel dat fungeert als een tijdelijke lijm die de basispoederdeeltjes bij elkaar houdt tijdens het vormproces. Het bindmiddelsysteem bestaat meestal uit: Thermoplastisch polymeer: Een thermoplastisch hars dat smelt tijdens het spuitgieten, waardoor het vloeibaar wordt en hecht aan het basispoeder. * Wassen of additieven: Deze kunnen de vloei-eigenschappen verbeteren, de ontbindingsefficiëntie verhogen of helpen bij de poederdispersie in het bindmiddel. | Het bindmiddelsysteem zorgt ervoor dat het poeder zich gedraagt als een vormbare grondstof tijdens het injecteren en maakt het mogelijk om complexe vormen te creëren. |
Poriënvormers | Dit zijn optionele additieven die tijdelijke poriën creëren in het spuitgietproduct. Dit kunnen zijn: * Organische materialen: Deze verbranden tijdens het ontbinden en laten een netwerk van poriën achter dat het verwijderen van het bindmiddelsysteem vergemakkelijkt. * Chemische uitloogmiddelen: Deze lossen op in een specifiek oplosmiddel tijdens een nabewerkingsstap, waardoor een gecontroleerde poriestructuur ontstaat. | Poriënvormers maken het mogelijk om poreuze structuren te creëren in het uiteindelijke onderdeel, wat gunstig kan zijn voor toepassingen zoals filters of botimplantaten. |
Kenmerken van gebruikte metaalpoeders
Kenmerkend | Beschrijving | Belang in MIM |
---|---|---|
Deeltjesgrootte en -verdeling | De grootte en verdeling van de metaalpoederdeeltjes hebben een grote invloed op de volgende aspecten van MIM: Schimmelvulling & groene sterkte: Fijnere poeders bieden over het algemeen een betere verpakkingsdichtheid en kunnen het vullen van de matrijs tijdens injectie verbeteren. Te fijne deeltjes kunnen echter de vloeibaarheid belemmeren en leiden tot problemen tijdens de verwerking. Een smalle deeltjesgrootteverdeling zorgt voor een consistente pakking en minimaliseert holtes in het spuitgietproduct, wat bijdraagt tot een goede groene sterkte (sterkte van het product vóór het sinteren). Sintergedrag en uiteindelijke eigenschappen: De deeltjesgrootte beïnvloedt het sinterproces, waarbij de deeltjes zich aan elkaar hechten tot een vaste structuur. Poeders met een bredere korrelgrootteverdeling kunnen leiden tot inhomogeen sinteren en mogelijk de uiteindelijke mechanische eigenschappen van het onderdeel beïnvloeden. | Een zorgvuldige selectie van de deeltjesgrootte en -distributie is cruciaal om een goede matrijsvulling, groene sterkte en optimale prestaties in het uiteindelijke gesinterde onderdeel te verkrijgen. |
Deeltjesmorfologie | Dit verwijst naar de vorm van de metaalpoederdeeltjes. Idealiter geven MIM-processen de voorkeur aan poeders met een sferische of bijna-sferische morfologie. | Bolvormige deeltjes vloeien gemakkelijker, wat de vulling van de matrijs en de dichtheid van de verpakking verbetert. Onregelmatig gevormde deeltjes kunnen holtes creëren en de vloeibaarheid belemmeren, wat kan leiden tot defecten in het spuitgietproduct. |
Schijnbare dichtheid & kraandichtheid | Deze eigenschappen vertegenwoordigen de bulkdichtheid van het poeder onder verschillende omstandigheden. Schijnbare dichtheid: Dit verwijst naar de dichtheid van het poeder in rust, rekening houdend met de ruimten tussen de deeltjes. Tikdichtheid: Dit weerspiegelt een dichtere toestand die wordt bereikt door een gestandaardiseerd tapproces. | Een hogere tapdichtheid is over het algemeen wenselijk bij MIM voor efficiënt materiaalgebruik en een goede maatnauwkeurigheid van het uiteindelijke onderdeel. Het draagt ook bij aan een betere pakking tijdens het vormen en minimaliseert krimp tijdens het sinteren. |
Chemische samenstelling | De specifieke elementen of legeringen die in het metaalpoeder worden gebruikt, bepalen de uiteindelijke eigenschappen van het gesinterde onderdeel. | Door de samenstelling van het metaalpoeder te kiezen, kunnen eigenschappen als sterkte, corrosiebestendigheid of slijtvastheid worden aangepast aan de specifieke toepassingseisen. MIM kan verschillende metaallegeringen gebruiken, waaronder roestvast staal, gereedschapsstaal en zelfs hoogwaardige legeringen zoals Inconel. |
Vloeibaarheid | Dit verwijst naar het gemak waarmee het poeder vloeit onder invloed van de zwaartekracht of toegepaste krachten. | Een goede vloeibaarheid is essentieel voor een gelijkmatige poederverdeling tijdens het spuitgieten. Poeders met een slechte vloeibaarheid kunnen leiden tot inconsistenties in verpakkingsdichtheid en mogelijke defecten in het uiteindelijke onderdeel. |
Normen voor metaalpoeders
De gebruikte metaalpoeders moeten voldoen aan de samenstellings- en korrelnormen:
Standaard behuizing | Standaard | Beschrijving | Belang in IMP |
---|---|---|---|
ASTM International (ASTM) | ASTM B930 - Standaardgids voor poederkarakterisering van materiaal voor metaalspuitgieten (MIM) | Deze standaard beschrijft verschillende testmethodes voor het karakteriseren van de eigenschappen van metaalpoeders gebruikt in MIM. | Biedt een kader voor het evalueren van factoren zoals deeltjesgrootteverdeling, morfologie, stroombaarheid en schijnbare dichtheid. Dit zorgt voor consistentie en kwaliteitscontrole in de metaalpoeders die worden gebruikt voor IMP-toepassingen. |
** | ** | * ASTM B783 - Standaardspecificatie voor roestvast staalpoeder voor metaalspuitgiettoepassingen (MIM). | Deze norm definieert specifieke eisen voor de chemische samenstelling, de verdeling van de deeltjesgrootte en de vloeibaarheid van roestvrijstalen poeders gebruikt in MIM. |
** | ** | * ASTM D4000 - Standaardclassificatiesysteem voor het Specificeren van Plastic Materialen. | Hoewel deze norm niet uitsluitend voor gvo geldt, biedt hij een classificatiesysteem voor verschillende soorten kunststofmaterialen, waaronder materialen die mogelijk als bindmiddel in gvo-grondstoffen worden gebruikt. |
Internationale Organisatie voor Standaardisatie (ISO) | * ISO 3095 - Metalen poeders - Bepaling van de stroomsnelheid met behulp van een Hall stromingsmeter | Deze norm specificeert een methode voor het meten van de stroombaarheid van metaalpoeders met behulp van een Hall-stromingsmeter. | Biedt een gestandaardiseerde aanpak voor het beoordelen van de vloeibaarheid, een kritieke eigenschap voor het bereiken van een goede matrijsvulling en consistente productkwaliteit in IMP. |
** | ** | * ISO 4497 - Kunststoffen - Bepaling van het smeltdebiet (MFR) en smeltvolume (MVR) van thermoplasten. | Deze norm beschrijft een methode voor het meten van de smeltsnelheid (MFR) van thermoplastische materialen, die relevant kan zijn voor de bindmiddelcomponent in IMP feedstock. |
Stappen in het productieproces
Het productieproces bestaat uit de volgende belangrijke stappen:
Stap | Beschrijving | Belang |
---|---|---|
1. Poederbereiding en mengen | Het basispoeder (metaal, keramiek of polymeer) wordt zorgvuldig geselecteerd en voorbehandeld op basis van de gewenste uiteindelijke eigenschappen. Additieven zoals poriënvormers of smeermiddelen kunnen worden toegevoegd. Het poeder wordt dan nauwkeurig afgewogen en gemengd met het bindmiddelsysteem om een homogene grondstof te vormen. | Deze stap legt de basis voor de eigenschappen van het uiteindelijke onderdeel. Zorgvuldige selectie en nauwkeurig mengen zorgen voor consistent materiaalgedrag tijdens het verwerken. |
2. Spuitgieten | De bereide grondstof IMP wordt verwarmd tot een half gesmolten toestand en onder hoge druk in een gesloten vormholte geïnjecteerd. De matrijs bootst de gewenste vorm van het uiteindelijke onderdeel na. | Deze fase bepaalt de geometrie van het onderdeel. Een consistente stroom en druk tijdens het inspuiten zijn cruciaal voor het verkrijgen van nauwkeurige productafmetingen en minimale defecten. |
3. Ontbinden | Het spuitgietproduct, ook wel het "groene product" genoemd, ondergaat een ontbindingsproces om het bindmiddelsysteem te verwijderen. Dit kan worden bereikt door: * Ontbinding met oplosmiddelen: Het onderdeel wordt ondergedompeld in een oplosmiddel dat het bindmiddel oplost, waardoor de poederstructuur achterblijft. * Thermisch ontbinden: Het onderdeel wordt blootgesteld aan een gecontroleerde verwarmingscyclus, waarbij het bindmiddel thermisch ontleedt en als gas ontsnapt. | Effectief ontbinden is cruciaal om de uiteindelijke gewenste vorm en porositeit te bereiken zonder de delicate poederstructuur te beschadigen. |
4. Sinteren | Het afgebroken onderdeel wordt onderworpen aan hoge temperaturen in een gecontroleerde atmosfeer (vaak onder vacuüm of inert gas). Dit proces bevordert diffusie en binding tussen de poederdeeltjes, wat resulteert in een solide en bijna netvormig onderdeel. | Sinteren bepaalt de uiteindelijke mechanische eigenschappen van het onderdeel, zoals sterkte, dichtheid en maatvastheid. Nauwkeurige temperatuurregeling en atmosfeerbeheer zijn essentieel. |
5. Nabewerking | Afhankelijk van de toepassingseisen kan het gesinterde onderdeel extra nabewerkingsstappen ondergaan, zoals: * Bewerking of slijpen: Voor het bereiken van nauwkeurige maattoleranties of oppervlakteafwerkingen. * Hittebehandeling: Om specifieke mechanische eigenschappen zoals sterkte of hardheid te verbeteren. * Coating of infiltratie: Om oppervlakte-eigenschappen zoals slijtvastheid of corrosiebestendigheid te verbeteren. | Nabewerkingen kunnen de functionaliteit en esthetiek van het uiteindelijke IMP-onderdeel verder verbeteren. |
Toepassingen van spuitgegoten onderdelen
Spuitgietpoeder kan worden gebruikt om verschillende ingewikkelde en zeer nauwkeurige onderdelen te maken in verschillende industrieën:
Industrie | Toepassingsvoorbeelden | Voordeel van spuitgieten |
---|---|---|
Automobiel | Interieuronderdelen (dashboards, deurpanelen, consoles) Onderdelen onder de motorkap (ventilatorhuizen, inlaatspruitstukken) Functionele onderdelen (tandwielen, kettingwielen) | Productie in grote volumes van complexe vormen met precieze kenmerken. Lichtgewicht onderdelen voor een lager brandstofverbruik. Breed scala aan materiaalopties voor verschillende prestatiebehoeften (duurzaamheid, hittebestendigheid). |
Consumentenelektronica | Elektronische behuizingen (telefoons, laptops, tablets) Aansluitingen en knoppen Interne onderdelen (beugels, tandwielen) | Massaproductie van ingewikkelde onderdelen met hoge maatnauwkeurigheid. Gladde oppervlakteafwerking voor esthetiek en gebruikerscomfort. Verscheidenheid aan kleuren en texturen die bereikt kunnen worden door materiaalkeuze en vormtechnieken. |
Medische apparaten | Chirurgische instrumenten (handgrepen, grepen) Prothetische componenten (kniegewrichten, tandheelkundige implantaten) Medische wegwerponderdelen (spuiten, flacons) | Steriliseerbare materialen voor hygiëne en veiligheid. Biocompatibele materialen voor gebruik in het menselijk lichaam (bepaalde polymeren en metaallegeringen). Complexe geometrieën voor precieze functionaliteit in medische toepassingen. |
Ruimtevaart en defensie | Vliegtuigonderdelen (kanalen, onderdelen van landingsgestellen) Satellietonderdelen (beugels, behuizingen) Defensie-uitrusting (helmen, wapenonderdelen) | Lichtgewicht en zeer sterke materialen voor gewichtsvermindering in luchtvaarttoepassingen. Vlamvertragende of hittebestendige materialen voor specifieke vereisten. Duurzame onderdelen voor ruwe omgevingen en veeleisende bedrijfsomstandigheden. |
Consumentengoederen | Speelgoed en spelletjes Apparaten (behuizingen, knoppen, wijzerplaten) Sportartikelen (helmen, fietsonderdelen) | Rendabele productie voor grote aantallen consumentenproducten. Grote variëteit aan kleuren en afwerkingen voor visuele aantrekkingskracht. Duurzame en functionele onderdelen voor dagelijks gebruik. |
Voordelen van spuitgieten voor de productie van onderdelen
Voordeel | Beschrijving | Voordeel |
---|---|---|
Productie van grote volumes: Spuitgieten blinkt uit in het efficiënt produceren van grote hoeveelheden identieke onderdelen. De automatiseringsmogelijkheden en snelle cyclustijden maken kosteneffectieve massaproductie mogelijk. | Dit is vooral voordelig voor producten die miljoenen eenheden vereisen, zoals consumentenelektronica of auto-onderdelen. Een constante kwaliteit en herhaalbaarheid zijn gegarandeerd tijdens de hele productierun. | |
Ontwerpflexibiliteit: Spuitgieten is geschikt voor een groot aantal geometrische complexiteiten, zoals ingewikkelde vormen, dunne wanden en interne kenmerken. Deze ontwerpvrijheid maakt het mogelijk om functionele en innovatieve onderdelen te maken. | In tegenstelling tot sommige subtractieve productiemethoden is spuitgieten niet beperkt door de geometrie van het gereedschap. Ondersnijdingen, kanalen en andere complexe vormen kunnen rechtstreeks in het onderdeel worden gespuitgiet. | |
Dimensionale nauwkeurigheid en herhaalbaarheid: De nauwkeurige controle over het matrijsontwerp en de injectieparameters zorgt voor consistente en nauwkeurige productafmetingen bij hoge productievolumes. | Dit minimaliseert de noodzaak voor nabewerkingsstappen voor maatcorrectie en zorgt voor uitwisselbare onderdelen voor assemblage. Herhaalbaarheid is cruciaal voor het behouden van een consistente productkwaliteit en functionaliteit. | |
Brede materiaalkeuze: Een groot aantal materialen kan worden gebruikt bij spuitgieten, waaronder thermoplasten, thermoharders, elastomeren en zelfs sommige metaallegeringen (via Metal Injection Molding - MIM). | Dankzij deze veelzijdigheid kan het optimale materiaal worden gekozen op basis van de gewenste eigenschappen, zoals sterkte, hittebestendigheid, chemische weerstand of flexibiliteit. | |
Afwerking en esthetiek van het oppervlak: Spuitgieten kan onderdelen produceren met een gladde oppervlakteafwerking van hoge kwaliteit, waardoor uitgebreide nabewerkingsstappen zoals polijsten vaak overbodig zijn. Bovendien kunnen verschillende kleurstoffen en texturen worden toegevoegd tijdens het spuitgieten. | Dit draagt bij aan de visuele aantrekkingskracht en functionaliteit van het eindproduct. Gladde oppervlakken kunnen essentieel zijn voor de hygiëne van medische apparatuur of voor een gemakkelijke reiniging van consumentengoederen. | |
Materiaalefficiëntie: Spuitgieten bevordert een bijna-netto-vorm productie, waardoor materiaalverspilling tot een minimum wordt beperkt in vergelijking met subtractieve technieken zoals machinale bewerking. Overtollig materiaal, sprue en runners genoemd, kan vaak worden gerecycled en hergebruikt in volgende productieruns. | Dit is gunstig vanuit het oogpunt van kosten en duurzaamheid. Het minimaliseren van afval vermindert ook de milieu-impact van het productieproces. | |
Automatiseringspotentieel: Het spuitgietproces kan in hoge mate geautomatiseerd worden, waarbij minimale menselijke tussenkomst nodig is voor de bediening. Dit zorgt voor een consistente productiekwaliteit en verlaagt de arbeidskosten. | Automatisering is vooral voordelig voor productieruns met grote volumes en zorgt voor een consistente productkwaliteit, ongeacht het vaardigheidsniveau van de operator. |
Beperkingen van het productieproces
Er zijn ook enkele beperkingen:
- Gewicht onderdeel beperkt tot < 400 g
- Wanddikte > 0,4 mm
- Assemblages nodig voor complexe geometrieën
- Duur gereedschap voor mallen
- Dimensionale veranderingen tijdens sinteren
Wereldwijde leveranciers van grondstoffen
Veel internationale bedrijven leveren kant-en-klaar basismateriaal voor spuitgieten:
Bedrijf | Plaats | Materialen |
---|---|---|
BASF | Duitsland | 316L roestvrij staal, titaniumlegeringen |
Sandvik | Zweden | Roestvrij staal, gereedschapsstaal |
GKN | Groot-Brittannië | Aluminium- en magnesiumlegeringen |
Rio Tinto | Australië | Metalen en keramische geïnjecteerde mengsels |
Indicatieve prijzen
Materiaal | Prijsbereik |
---|---|
Roestvrij staal | $50-70 per kg |
Gereedschapstaal | $45-65 per kg |
Zware legering wolfraam | $130-170 per kg |
De prijs is afhankelijk van de bestelvolumes, de aanpassingsbehoeften en economische factoren.
Voor- en nadelen van het gebruik Spuitgietbare poeders
Voordelen | Nadelen |
---|---|
Ingewikkelde en complexe vormen | Beperkte afmetingen en gewicht |
Nauwere toleranties | Duur gereedschap en dure apparatuur |
Fijne oppervlakteafwerking | Dimensionale veranderingen tijdens sinteren |
Gamma materialen | Vaak is nabewerking nodig |
Hoge productie, lage kosten per onderdeel | Broze materialen hebben de neiging te barsten |
Minder afval | Beperkt de materiaalkeuze |
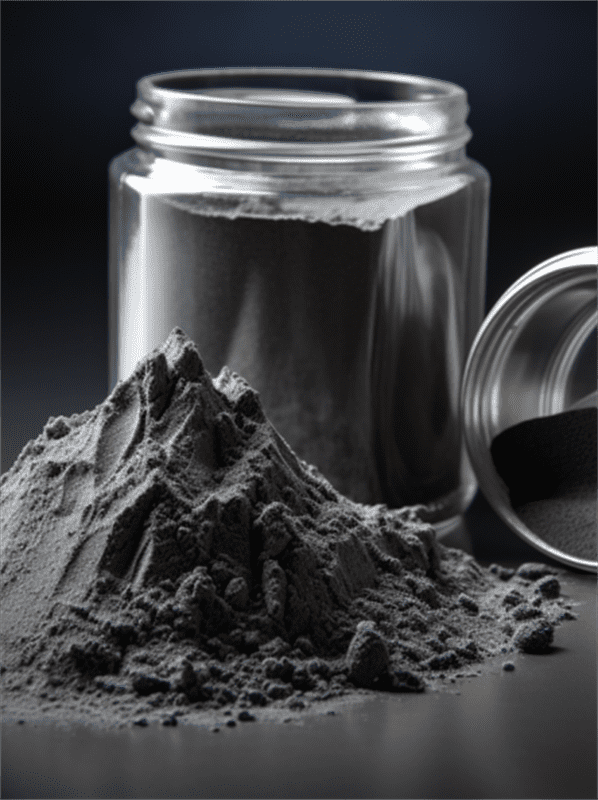
FAQ
V: Wat is de typische samenstelling van spuitgietpoeders?
A: Ze bevatten 80-90% metaalpoeder, 8-20% bindmiddel en 1-2% smeermiddelen per gewicht. Gebruikelijke bindmiddelen zijn was, PP, PE en PEG.
V: Welke grootte worden de poeders gebruikt?
A: Poeders tussen 1-20 micron worden gebruikt. Fijner poeder verbetert de dichtheid, maar kan gevoelig zijn voor agglomeratie.
V: Hoeveel krimp treedt er op tijdens het sinteren?
A: Tot 20% lineaire krimp van onderdelen treedt op tijdens sinteren in vloeibare fase. Hiervoor moet rekening worden gehouden bij het ontwerp van het gereedschap.
V: Wat veroorzaakt scheuren in spuitgegoten onderdelen van gesinterd metaal?
A: Niet-uniforme verwarming in ovens, gebruik van snelle koeling na sinteren, slechte poedermenging en keuze van brosse legeringen.
V: Welke materiaalopties bestaan er voor spuitgietpoeders?
A: Roestvrij staal, gereedschapsstaal, zware wolfraamlegeringen, koperlegeringen, titanium en titaniumlegeringen.
Delen op
MET3DP Technology Co, LTD is een toonaangevende leverancier van additieve productieoplossingen met hoofdkantoor in Qingdao, China. Ons bedrijf is gespecialiseerd in 3D printapparatuur en hoogwaardige metaalpoeders voor industriële toepassingen.
Onderzoek om de beste prijs en een op maat gemaakte oplossing voor uw bedrijf te krijgen!
gerelateerde artikelen
Over Met3DP
Recente update
Ons product
NEEM CONTACT MET ONS OP
Nog vragen? Stuur ons nu een bericht! Na ontvangst van uw bericht behandelen wij uw verzoek met een heel team.
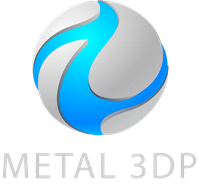
Metaalpoeders voor 3D printen en additieve productie