3D Printed Inverter Housings for Electric Vehicles
Inhoudsopgave
Introduction – The Rise of 3D Printed Inverter Housings in Electric Vehicles
The electric vehicle (EV) revolution is rapidly transforming the automotive landscape, demanding innovation at every level of vehicle design and manufacturing. One critical component in the powertrain of an EV is the inverter, responsible for converting direct current (DC) from the battery into alternating current (AC) to power the electric motor. The housing that encases and protects this vital electronic assembly plays a significant role in its performance, durability, and overall efficiency. Traditionally manufactured using methods like die casting, EV inverter housings are now increasingly being produced using metal 3D printing, also known as metal additive manufacturing. This shift is driven by the unique advantages that metal 3d printen offers, enabling the creation of complex geometries, lightweight designs, and customized solutions tailored to the specific demands of modern EVs. As the demand for high-performance, efficient, and lightweight EVs continues to surge, the role of innovative manufacturing techniques like metal 3D printing in producing critical components such as inverter housings will only become more pronounced. Companies like Metaal3DP, with their expertise in additive manufacturing solutions and high-performance metal powders, are at the forefront of this evolution, providing cutting-edge technologies to empower the next generation of electric vehicles. You can learn more about Metal3DP’s comprehensive solutions on their website.
What are EV Inverter Housings Used For? Key Applications and Industries
EV inverter housings serve several crucial functions within the electric vehicle. Primarily, they act as a protective enclosure for the sensitive electronic components of the inverter, shielding them from environmental factors such as moisture, dust, and debris. This protection is essential for ensuring the long-term reliability and performance of the inverter. Secondly, the housing often plays a critical role in thermal management. Inverters generate significant heat during operation, and the housing can be designed with integrated cooling channels or fins to dissipate this heat effectively, preventing overheating and maintaining optimal operating temperatures. Lightweighting is another key consideration. Reducing the overall weight of an EV is paramount for improving energy efficiency and range. Metal 3D printing allows for the creation of complex, yet lightweight, housing designs that can contribute to overall vehicle weight reduction. Furthermore, the housing provides structural support for the inverter components and facilitates its mounting within the vehicle chassis.
The applications for advanced EV inverter housings extend across the entire electric vehicle sector, including:
- Battery Electric Vehicles (BEVs): Found in all fully electric cars, SUVs, and trucks.
- Plug-in Hybrid Electric Vehicles (PHEVs): Used in vehicles that combine an electric motor with an internal combustion engine.
- Electric Buses and Commercial Vehicles: Essential for the efficient operation of large electric transportation.
- Electric Motorcycles and Scooters: Providing robust protection and thermal management for their power electronics.
Industries benefiting from advancements in EV inverter housing manufacturing include:
- Automotive OEMs (Original Equipment Manufacturers): Directly integrating these housings into their vehicle production lines.
- Tier 1 Automotive Suppliers: Developing and supplying inverter systems, including housings, to OEMs.
- Electric Powertrain Developers: Innovating and manufacturing complete electric drive systems.
The ability of metal 3D printing to create customized, high-performance inverter housings is particularly valuable in this rapidly evolving industry. Metal3DP’s advanced metal powders and printing technologies cater to the demanding requirements of these applications, enabling the production of intricate and reliable components. Explore the diverse applications of metal 3D printing further on Metal3DP’s metaal 3D printpagina.
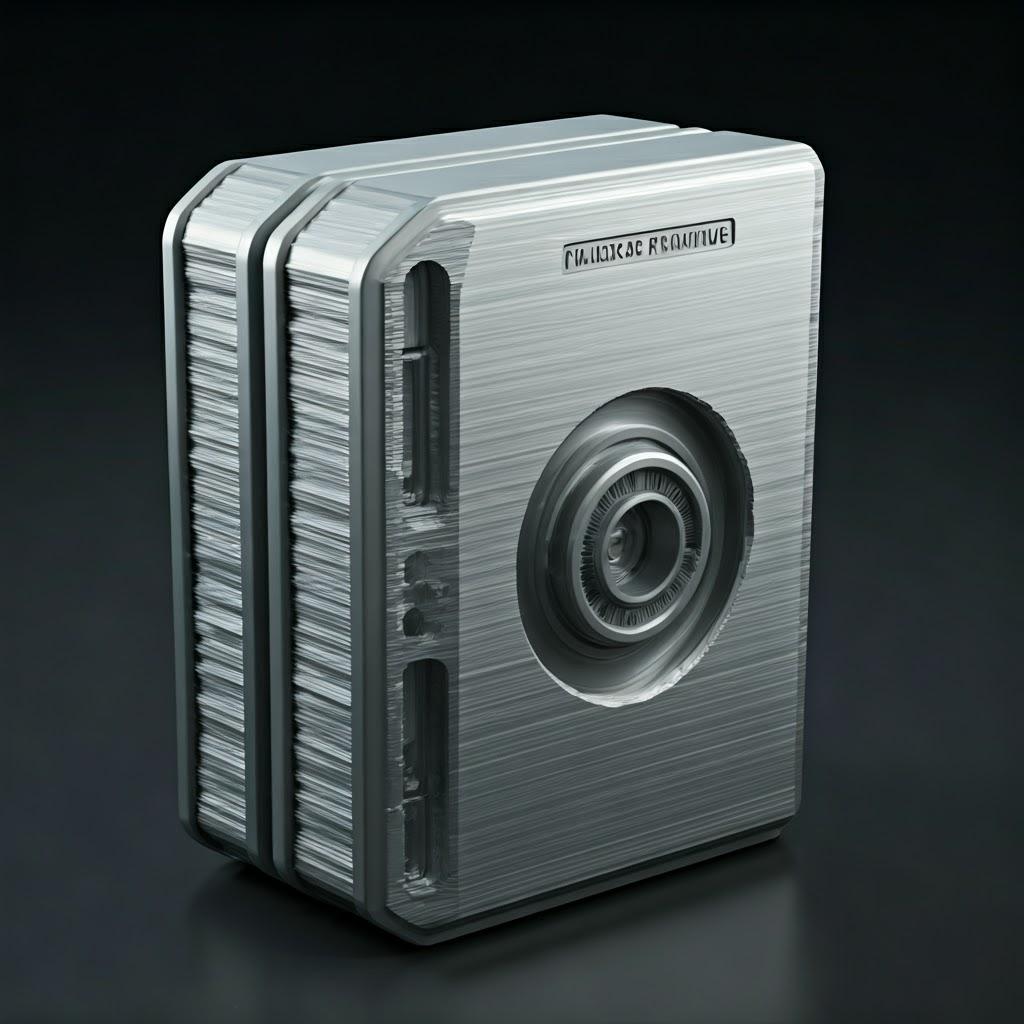
Why Use Metal 3D Printing for EV Inverter Housings? Advantages Over Traditional Manufacturing
Adopting metal 3D printing for the production of EV inverter housings offers a compelling array of advantages compared to traditional manufacturing methods like die casting or machining:
- Ontwerpvrijheid en complexiteit: Metal 3D printing allows for the creation of highly complex geometries that are often impossible or cost-prohibitive to achieve with traditional methods. This includes intricate internal cooling channels, optimized rib structures for lightweighting and stiffness, and integrated mounting features, leading to more efficient and compact designs.
- Lichtgewicht: By enabling topology optimization and the creation of lattice structures, metal 3D printing facilitates the production of significantly lighter housings without compromising structural integrity. This directly contributes to improved energy efficiency and extended range in EVs.
- Snelle prototyping en iteratie: Additive manufacturing significantly accelerates the prototyping process. Design changes can be implemented quickly and new iterations can be produced in a fraction of the time compared to tooling-dependent methods. This agility is crucial in the fast-paced EV market.
- Customization and Low-Volume Production: Metal 3D printing is economically viable for low to medium production volumes and allows for easy customization of designs to meet specific vehicle requirements without the need for expensive tooling modifications.
- Materiaalefficiëntie: Additive manufacturing processes can be more material-efficient as they only use the material needed to build the part, reducing waste compared to subtractive methods like machining.
- Integration of Features: 3D printing enables the integration of multiple functionalities into a single part, reducing the number of components and assembly steps. For example, cooling channels can be directly printed within the housing structure.
- Verbeterde prestatie: Optimized designs made possible by 3D printing can lead to improved thermal management and structural performance of the inverter housing, enhancing the overall reliability and efficiency of the EV powertrain.
Metal3DP’s expertise in Selective Electron Beam Melting (SEBM) and other advanced printing methods, detailed on their afdrukmethoden pagina, further enhances these advantages, providing high-quality, robust solutions for EV inverter housings.
Recommended Materials for 3D Printed EV Inverter Housings and Why They Matter
The choice of material is critical for the performance and durability of 3D printed EV inverter housings. Two recommended metal powders that offer excellent properties for this application are AlSi10Mg en CuCrZr.
AlSi10Mg (Aluminum Silicon Magnesium Alloy):
- Eigenschappen: This aluminum alloy is widely used in additive manufacturing due to its excellent combination of lightweightness, high strength-to-weight ratio, good thermal conductivity, and corrosion resistance. It also exhibits good castability and weldability.
- Benefits for EV Inverter Housings:
- Lichtgewicht: Its low density contributes significantly to reducing the overall weight of the vehicle, improving energy efficiency.
- Thermisch beheer: Good thermal conductivity allows for efficient heat dissipation from the inverter’s electronic components.
- Strength and Stiffness: Provides the necessary structural integrity to protect the sensitive electronics.
- Corrosieweerstand: Ensures long-term reliability in various environmental conditions.
CuCrZr (Copper Chromium Zirconium Alloy):
- Eigenschappen: This copper alloy is known for its high electrical and thermal conductivity, as well as good strength and wear resistance at elevated temperatures. It also possesses good creep resistance.
- Benefits for EV Inverter Housings:
- Uitstekende thermische geleidbaarheid: Crucial for effectively dissipating the significant heat generated by the inverter, leading to improved performance and longevity.
- Good Strength at High Temperatures: Maintains structural integrity even under demanding operating conditions.
- Elektrische geleidbaarheid: Can potentially be used for integrated electrical features within the housing design.
Metaal3DP offers a comprehensive portfolio of high-quality metal powders, including AlSi10Mg and CuCrZr, specifically optimized for additive manufacturing processes. Their advanced powder making system ensures high sphericity and flowability, essential for producing dense and high-performance parts. You can explore Metal3DP’s range of metaalpoeders for various applications. The selection of the appropriate powder depends on the specific performance requirements of the EV inverter housing, with factors like thermal management needs, weight constraints, and cost considerations playing a crucial role in the decision-making process. Sources and related content
Design Considerations for Additive Manufacturing of EV Inverter Housings
Designing for metal 3D printing requires a different mindset compared to traditional manufacturing. To fully leverage the capabilities of additive manufacturing for EV inverter housings, several key design considerations should be taken into account:
- Topologieoptimalisatie: This computational technique can be employed to identify and remove material from non-critical areas of the housing while maintaining structural integrity. By optimizing the material distribution, significant weight reductions can be achieved, leading to improved EV efficiency.
- Roosterstructuren: Incorporating lattice or cellular structures within the housing design can further reduce weight without sacrificing stiffness. These intricate internal geometries are uniquely enabled by metal 3D printing and offer excellent strength-to-weight ratios.
- Integrated Cooling Channels: Unlike traditional manufacturing, 3D printing allows for the creation of complex internal cooling channels that can be tailored to the specific heat-generating components within the inverter. This enables more efficient and targeted thermal management, potentially eliminating the need for separate cooling systems and reducing overall system complexity.
- Feature Integration: Consider integrating features such as mounting points, cable routing channels, and sensor housings directly into the design. This reduces the number of individual parts, simplifies assembly, and can improve the overall robustness of the inverter system.
- Orientation and Support Structures: The orientation of the part during the printing process can significantly impact surface finish, dimensional accuracy, and the need for support structures. Careful consideration of the build orientation is crucial to minimize material usage, post-processing effort, and potential for warping or distortion.
- Wall Thickness and Ribbing: Optimizing wall thicknesses and incorporating rib structures can enhance the stiffness and strength of the housing while minimizing weight. The flexibility of 3D printing allows for the creation of complex rib patterns tailored to the specific load requirements.
- Minimizing Overhangs: Designs with excessive overhangs may require extensive support structures, which can be challenging to remove and may affect surface quality. Designing with self-supporting angles or strategically placed supports is important for efficient printing.
- Material Considerations: The chosen metal powder will influence the design parameters. For example, the minimum feature size, achievable wall thickness, and susceptibility to warping can vary between materials like AlSi10Mg and CuCrZr.
By carefully considering these design aspects, engineers can harness the full potential of metal 3D printing to create high-performance, lightweight, and functionally integrated EV inverter housings. Metal3DP’s application development services can provide valuable expertise in optimizing designs for their advanced metal powders and SEBM printers.
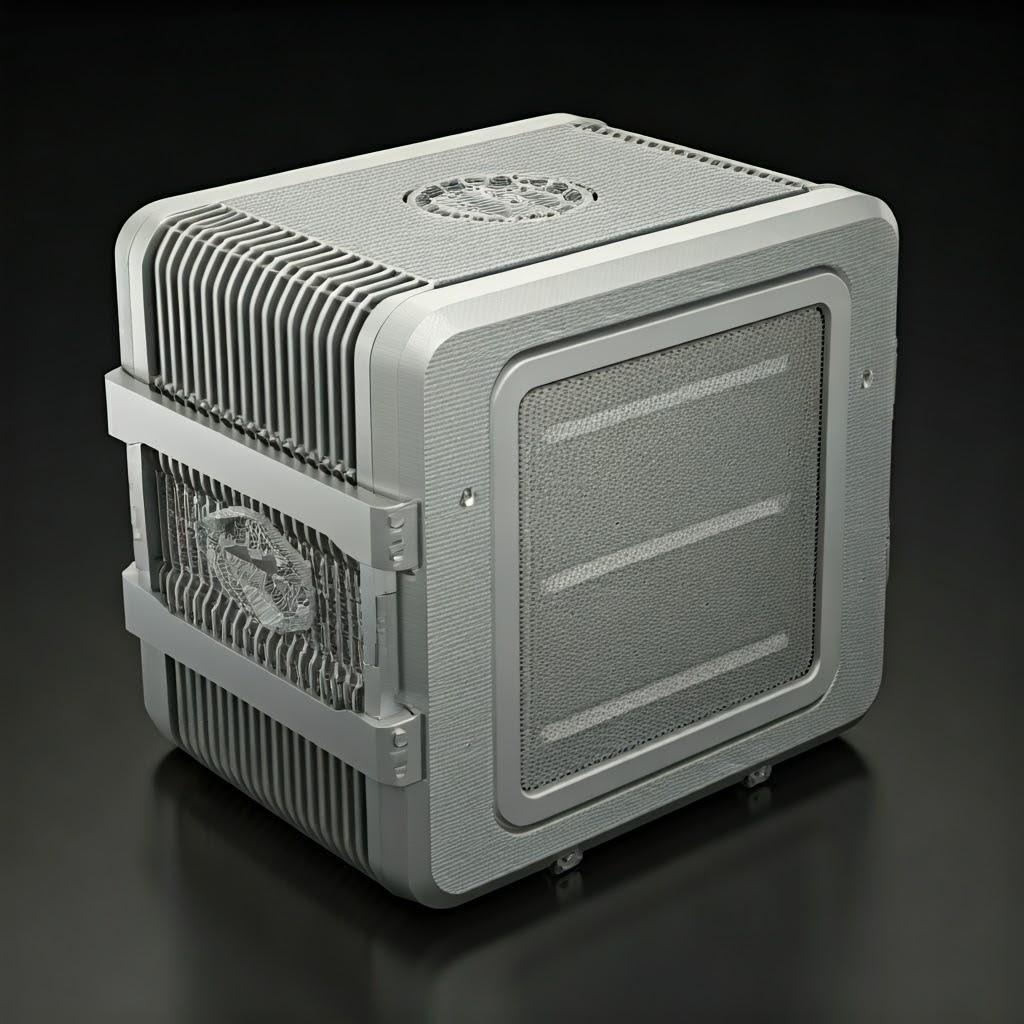
Tolerance, Surface Finish, and Dimensional Accuracy of 3D Printed EV Inverter Housings
Achieving the required tolerance, surface finish, and dimensional accuracy is paramount for the functional integration and reliability of EV inverter housings. Metal 3D printing technologies, particularly Selective Electron Beam Melting (SEBM) as offered by Metaal3DP, are capable of producing parts with tight tolerances and good dimensional accuracy. However, these aspects can be influenced by several factors:
- Druktechnologie: Different metal 3D printing processes (e.g., SEBM, Laser Powder Bed Fusion) have varying inherent accuracy and achievable surface finishes. SEBM, known for its high energy input and vacuum environment, can produce dense parts with good dimensional accuracy and reduced internal stresses.
- Materiaaleigenschappen: The characteristics of the metal powder, such as particle size distribution and flowability, can affect the final part’s accuracy and surface finish. Metal3DP’s high-quality metal powders are engineered to ensure consistent and reliable printing outcomes.
- Build Orientation and Support Structures: As mentioned earlier, the orientation of the part during printing and the use of support structures can impact dimensional accuracy and surface finish, especially on downward-facing surfaces.
- Nabewerking: Depending on the application requirements, post-processing steps like CNC machining, polishing, or surface coating may be necessary to achieve tighter tolerances or smoother surface finishes.
- Machine Calibration and Maintenance: Proper calibration and regular maintenance of the 3D printer are crucial for ensuring consistent accuracy and repeatability. Metal3DP’s industry-leading printers are designed for high accuracy and reliability.
- Design for Manufacturing (DFM): Designing parts with the limitations and capabilities of the chosen 3D printing process in mind is essential for achieving the desired tolerances and surface finish.
Typical achievable tolerances for metal 3D printed parts can range from ±0.1 to ±0.5 mm, depending on the size and complexity of the part, the printing technology, and post-processing. Surface roughness (Ra) values can typically range from 5 to 20 µm as-printed, which can be further improved through post-processing techniques. For critical interfaces or functional surfaces of EV inverter housings requiring tighter tolerances or smoother finishes, machining or other finishing processes can be employed. Metaal3DP can provide guidance on achieving the desired precision and surface quality for specific applications.
Post-Processing Requirements for 3D Printed EV Inverter Housings
While metal 3D printing offers significant advantages in creating complex geometries, post-processing is often required to meet the final specifications and performance requirements of EV inverter housings. Common post-processing steps include:
- Powder Removal: After the printing process, loose or semi-sintered powder needs to be carefully removed from the part’s surfaces and internal channels. This is typically done using compressed air, vacuuming, or blasting techniques.
- Draagstructuur verwijderen: If support structures were necessary during printing, they need to be removed. This can be a manual process involving cutting or breaking away the supports, or it can be automated using specialized tools or chemical dissolution. The design should aim to minimize the need for extensive support structures to simplify this step.
- Hittebehandeling: Stress relief annealing or other heat treatment processes may be required to improve the mechanical properties of the printed part, reduce internal stresses, and achieve the desired microstructure of the material. The specific heat treatment cycle depends on the metal alloy used.
- Afwerking oppervlak: Depending on the application, surface finishing processes may be necessary to improve aesthetics, reduce surface roughness, or prepare the surface for further treatments. Common methods include blasting, grinding, polishing, and vibratory finishing.
- CNC-bewerking: For critical dimensions or features requiring very tight tolerances, CNC machining can be used as a secondary process to achieve the desired precision. This is often applied to mating surfaces or mounting interfaces.
- Coating and Surface Treatments: Coatings, such as corrosion-resistant layers or thermal management coatings, may be applied to enhance the performance and durability of the inverter housing in its operating environment. Examples include anodizing for aluminum alloys or specialized thermal interface materials.
- Inspection and Quality Control: Non-destructive testing methods, such as dimensional metrology, dye penetrant inspection, or X-ray computed tomography, are used to verify the dimensional accuracy, structural integrity, and internal soundness of the printed parts.
The specific post-processing requirements for a 3D printed EV inverter housing will depend on the design, the chosen material, the printing process, and the final application demands. Collaborating with an experienced metal 3D printing service provider like Metaal3DP, who offers comprehensive post-processing capabilities, is crucial for ensuring that the final parts meet the required specifications.
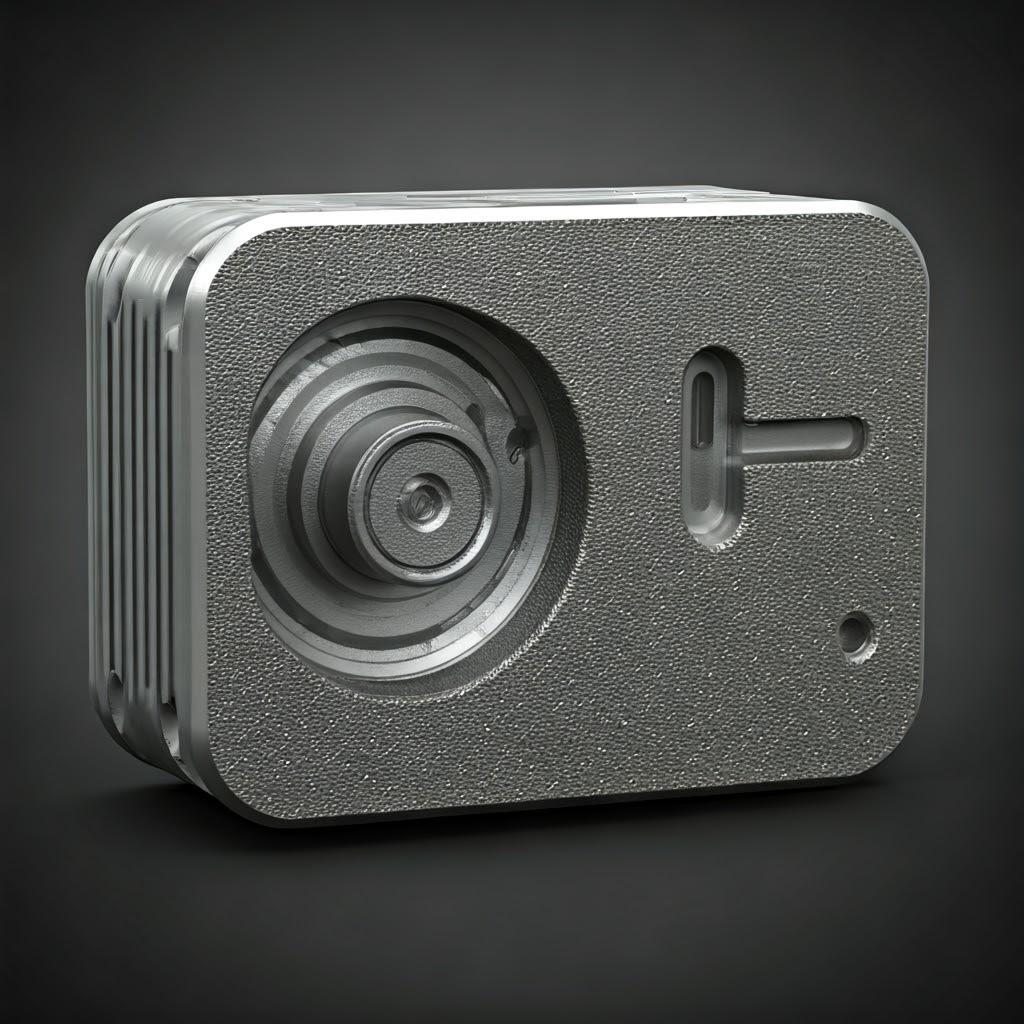
Common Challenges in 3D Printing EV Inverter Housings and How to Avoid Them
While metal 3D printing offers numerous benefits, there are also potential challenges that need to be addressed to ensure successful production of EV inverter housings:
- Vervorming en vervorming: Thermal stresses during the printing process can lead to warping or distortion of the part, especially for large or complex geometries.
- How to Avoid: Optimize part orientation, use appropriate support structures, employ process parameters that minimize thermal gradients, and consider stress relief heat treatment after printing.
- Moeilijkheden bij het verwijderen van de steunstructuur: Intricately designed parts may require complex support structures that can be challenging and time-consuming to remove, potentially damaging the part’s surface.
- How to Avoid: Design parts with self-supporting angles where possible, optimize support structure design for easier removal, and consider using dissolvable support materials if available for the chosen printing technology.
- Porosity and Internal Defects: Insufficient melting or solidification during the printing process can lead to porosity or other internal defects, which can compromise the mechanical strength and thermal conductivity of the housing.
- How to Avoid: Optimize process parameters such as laser power or electron beam current, scan speed, and powder bed temperature. Ensure the use of high-quality metal powders with good flowability, such as those offered by Metaal3DP.
- Oppervlakteruwheid: As-printed metal surfaces can be rough, which may not be suitable for all applications, especially mating surfaces requiring good thermal contact.
- How to Avoid: Optimize printing parameters to minimize surface roughness, and employ post-processing techniques like blasting, grinding, or polishing to achieve the desired surface finish.
- Dimensional Inaccuracy: Achieving tight tolerances can be challenging, especially for complex geometries or large parts.
- How to Avoid: Carefully calibrate and maintain the 3D printer, optimize part orientation, and consider using machining as a secondary process for critical dimensions.
- Material Property Variations: Inconsistent melting or solidification can lead to variations in the mechanical properties throughout the printed part.
- How to Avoid: Utilize well-established and controlled printing processes, optimize process parameters for the chosen material, and perform thorough quality control and testing.
By understanding these potential challenges and implementing appropriate design strategies and process controls, manufacturers can effectively leverage metal 3D printing to produce high-quality EV inverter housings. Partnering with an experienced provider like Metaal3DP, who possesses deep expertise in metal additive manufacturing, can significantly mitigate these risks.
How to Choose the Right Metal 3D Printing Service Provider for EV Inverter Housings
Selecting the right metal 3D printing service provider is crucial for the successful production of high-quality EV inverter housings. Here are key factors to consider when evaluating potential suppliers:
- Technology and Material Capabilities: Ensure the provider has experience with metal 3D printing technologies suitable for your application, such as Selective Electron Beam Melting (SEBM) or Laser Powder Bed Fusion (LPBF). Verify they offer the recommended materials, like AlSi10Mg and CuCrZr, and possess expertise in processing these materials to achieve the desired properties. Metaal3DP offers a range of advanced printing technologies and a portfolio of high-performance metal powders.
- Industry Experience and Expertise: Look for a provider with a proven track record in serving the automotive, aerospace, medical, or industrial manufacturing sectors, ideally with specific experience in EV components. Their understanding of industry-specific quality standards and requirements is essential. Metaal3DP has decades of collective expertise in metal additive manufacturing and partners with organizations across various industries.
- Design and Engineering Support: A strong service provider should offer design consultation and engineering support to optimize your part for additive manufacturing. This includes guidance on topology optimization, lightweighting strategies, and design for manufacturability. Metaal3DP provides comprehensive solutions spanning equipment, materials, and application development services.
- Mogelijkheden voor nabewerking: Evaluate the provider’s in-house post-processing capabilities, including powder removal, support removal, heat treatment, surface finishing, and CNC machining. A comprehensive suite of services can streamline the production process and ensure the final part meets your specifications.
- Quality Assurance and Certifications: Inquire about the provider’s quality management systems, certifications (e.g., ISO 9001, AS9100 for aerospace), and inspection processes. Robust quality control measures are essential for ensuring the reliability and performance of critical components like EV inverter housings.
- Production Capacity and Scalability: Consider the provider’s production capacity and their ability to scale up production if your volumes increase in the future. Understand their lead times for manufacturing and delivery.
- Communication and Customer Support: Effective communication and responsive customer support are vital for a smooth and successful partnership. Assess their responsiveness to inquiries and their willingness to collaborate throughout the project.
- Kostenconcurrentievermogen: While cost should not be the sole determining factor, it’s important to obtain competitive quotes and understand the pricing structure, including any additional charges for design, post-processing, or quality control.
By carefully evaluating these factors, you can select a metal 3D printing service provider that aligns with your specific needs and ensures the successful production of high-quality EV inverter housings. Contact Metaal3DP to explore how their capabilities can power your organization’s additive manufacturing goals.
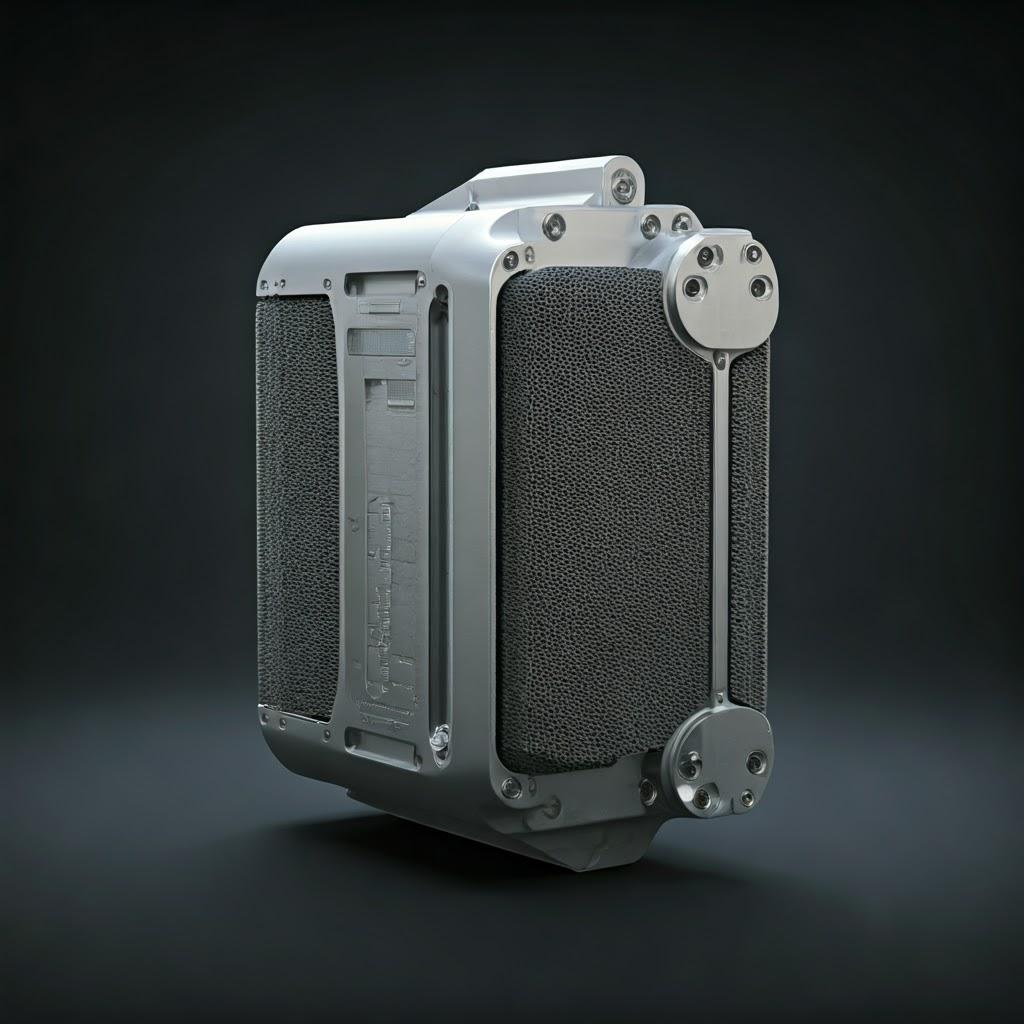
Cost Factors and Lead Time for 3D Printed EV Inverter Housings
The cost and lead time for producing EV inverter housings using metal 3D printing are influenced by several factors:
Kostenfactoren:
- Materiaalkosten: The type and quantity of metal powder used are significant cost drivers. Materials like CuCrZr can be more expensive than AlSi10Mg. Efficient design and optimized build orientation can minimize material usage.
- Bouwtijd: The time it takes to print a part depends on its size, complexity, and the chosen printing parameters (e.g., layer height, scan speed). Longer build times translate to higher machine operating costs.
- Kosten voor nabewerking: The extent of post-processing required (e.g., support removal, heat treatment, machining, coating) will impact the overall cost. Complex post-processing steps can add significantly to the final price.
- Arbeidskosten: The labor involved in design optimization, machine setup and operation, post-processing, and quality control contributes to the overall cost.
- Machine Depreciation and Overhead: The cost of the 3D printing equipment and the operational overhead of the service provider are factored into the pricing.
- Hoeveelheid: While metal 3D printing can be cost-effective for low to medium volumes and customized parts, the cost per part may decrease with larger production runs due to economies of scale in material procurement and process optimization.
Lead Time Factors:
- Design Complexity and Optimization: The time required for design optimization and preparation for 3D printing can vary depending on the complexity of the part.
- Afdrukken tijd: As mentioned earlier, the build time is a significant component of the lead time.
- Post-Processing Time: The duration of post-processing steps can range from a few days to several weeks, depending on the complexity and the number of processes involved.
- Machine Availability and Scheduling: The lead time can be affected by the availability of the 3D printing equipment and the service provider’s production schedule.
- Shipping and Logistics: The time required for shipping the finished parts to the customer needs to be considered.
It’s important to engage in detailed discussions with potential metal 3D printing service providers like Metaal3DP to obtain accurate cost estimates and lead times based on your specific design requirements and production volumes. Providing clear specifications and CAD models will enable them to offer a precise quotation.
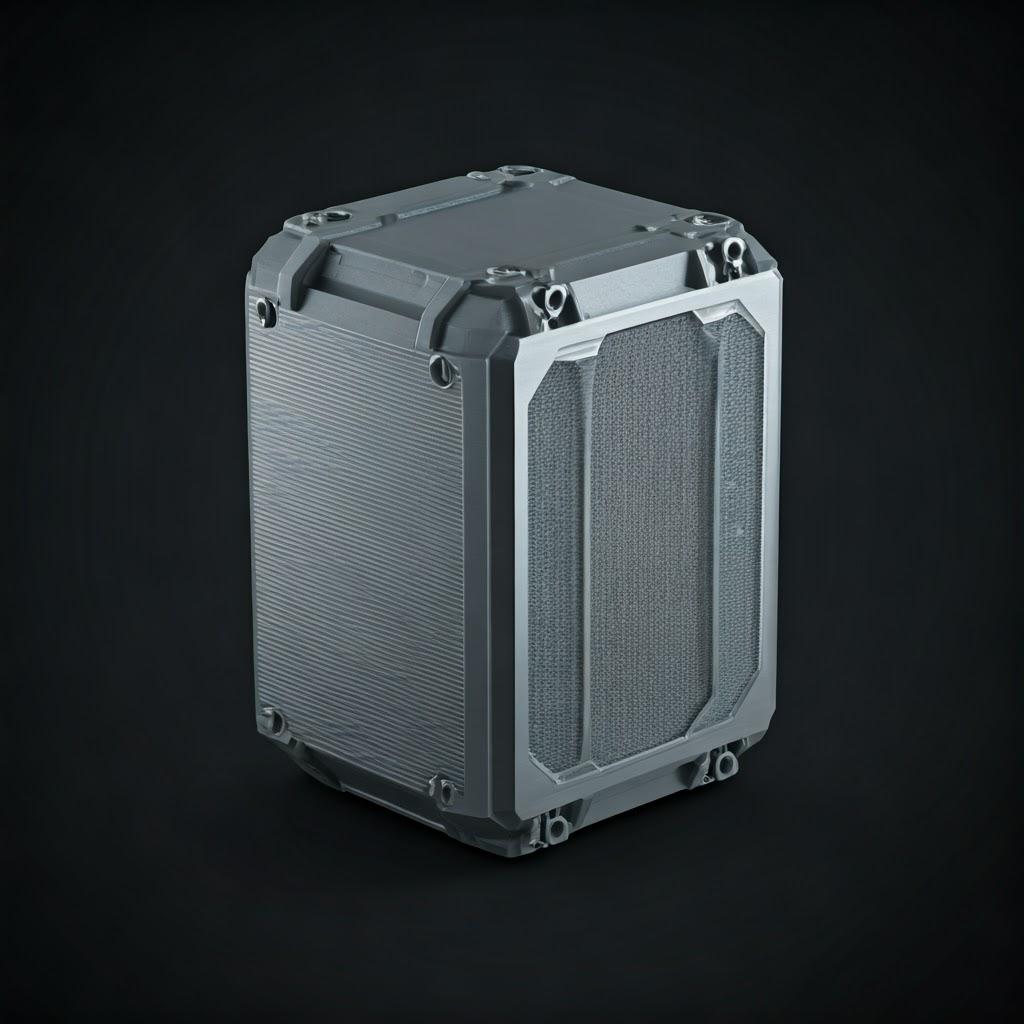
Veelgestelde vragen (FAQ)
What are the typical tolerances achievable with metal 3D printing for EV inverter housings? Typical achievable tolerances range from ±0.1 mm to ±0.5 mm, depending on the part geometry, printing technology, and post-processing. For critical features, CNC machining can be used to achieve tighter tolerances.
Can metal 3D printed inverter housings meet automotive industry standards for durability and reliability? Yes, when the appropriate materials, printing processes, and post-processing are employed, metal 3D printed parts can meet stringent automotive industry standards. It’s crucial to work with experienced providers like Metaal3DP who understand these requirements and have robust quality control processes in place.
Is metal 3D printing cost-effective for mass production of EV inverter housings? While metal 3D printing is highly advantageous for rapid prototyping, low to medium volume production, and complex designs, the cost-effectiveness for mass production depends on factors like part complexity, material costs, and the specific printing technology. For very high volumes, traditional methods like die casting may still be more economical. However, the benefits of design freedom and lightweighting offered by 3D printing can provide overall value.
Conclusion – Embracing Metal 3D Printing for Next-Generation EV Inverter Housings
Metal 3D printing is revolutionizing the design and manufacturing of critical components for electric vehicles, and EV inverter housings are a prime example. The ability to create complex geometries, achieve significant weight reductions, integrate functionalities, and rapidly iterate designs offers compelling advantages over traditional manufacturing methods. Materials like AlSi10Mg and CuCrZr, processed using advanced technologies such as those offered by Metaal3DP, provide the necessary performance characteristics for these demanding applications.
By carefully considering design for additive manufacturing principles, understanding the achievable tolerances and surface finishes, and partnering with an experienced metal 3D printing service provider, the automotive industry can unlock the full potential of this transformative technology. As the demand for innovative and efficient EVs continues to grow, metal 3D printing will play an increasingly vital role in shaping the future of electric mobility. Metaal3DP, with its comprehensive expertise in metal AM equipment, high-quality powders, and application development, stands ready to empower organizations in their journey towards advanced digital manufacturing. Explore the possibilities of metal 3D printing for your EV applications by visiting Metal3DP’s startpagina.
Delen op
MET3DP Technology Co, LTD is een toonaangevende leverancier van additieve productieoplossingen met hoofdkantoor in Qingdao, China. Ons bedrijf is gespecialiseerd in 3D printapparatuur en hoogwaardige metaalpoeders voor industriële toepassingen.
Onderzoek om de beste prijs en een op maat gemaakte oplossing voor uw bedrijf te krijgen!
gerelateerde artikelen
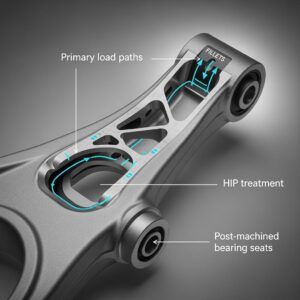
Metal 3D Printing for U.S. Automotive Lightweight Structural Brackets and Suspension Components
Lees verder "Over Met3DP
Recente update
Ons product
NEEM CONTACT MET ONS OP
Nog vragen? Stuur ons nu een bericht! Na ontvangst van uw bericht behandelen wij uw verzoek met een heel team.