Apparatuur voor metaalpoederverneveling
Inhoudsopgave
Verneveling van metaalpoeder is een techniek voor het verkleinen van de deeltjesgrootte die wordt gebruikt om fijne metaalpoeders te produceren met geoptimaliseerde eigenschappen voor industriële toepassingen. Bij dit proces wordt gesmolten metaal door een mondstuk geperst om het te desintegreren in uniforme druppeltjes die snel stollen tot poederdeeltjes.
Verneveling maakt controle mogelijk over de deeltjesgrootteverdeling, morfologie, zuiverheid en andere eigenschappen die van cruciaal belang zijn voor hoge prestaties bij het 3D-printen van metaal, de productie van poedermetallurgische onderdelen, metaalcoatingprocessen en meer. Dit artikel geeft een uitgebreid overzicht van verschillende soorten vernevelingsapparatuur, werkingsprincipes, ontwerpoverwegingen, toepassingen, voordelen en beperkingen.
Overzicht van het metaalpoedervernevelingsproces
Metaalpoederverneveling zet vloeibaar metaal in bulk om in fijne bolvormige poeders met gecontroleerde eigenschappen. Dit wordt bereikt door een stroom gesmolten metaal op te breken in fijne druppeltjes met behulp van een gas- of vloeistofstraal. De druppeltjes stollen snel tot poederdeeltjes terwijl ze afkoelen.
De belangrijkste stappen in dit proces zijn:
- Metaal smelten – De ruwe metaallading wordt gesmolten met behulp van een inductieoven, boogsmelten of andere technieken. Gebruikelijke metalen die worden verstoven zijn onder meer aluminium, titanium, nikkel, ijzer, kobalt, koper enz.
- Levering van gesmolten metaal – Het vloeibare metaal wordt op een optimale temperatuur gehouden en via trechters, smeltkroezen of pompen naar de vernevelingszone geleid.
- Verneveling – De stroom gesmolten metaal valt uiteen in druppeltjes door interactie met gas of vloeistof met hoge snelheid. Er worden verschillende vernevelingsmethoden gebruikt.
- Poederinzameling – Het vernevelde metaalpoeder wordt gekoeld en verzameld voor verdere bewerkingen. Zeef-, magnetische scheidings- en uitgloeiprocessen kunnen worden toegepast.
- Karakterisering van poeder – De deeltjesgrootteverdeling, morfologie, dichtheid, vloeibaarheid en microstructuur van het poeder worden geanalyseerd.
Een goede controle over procesparameters zoals metaalsamenstelling, temperatuur, vernevelingsvloeistofsnelheid en verstuiverontwerp is van cruciaal belang om de gewenste poedereigenschappen te bereiken.
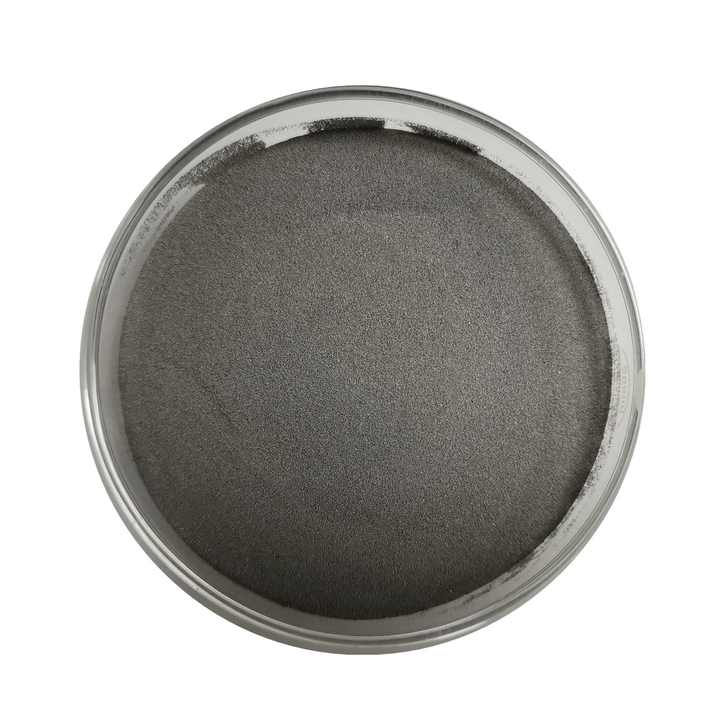
Soorten verstuivingsapparatuur
Vernevelingssystemen kunnen worden gecategoriseerd op basis van het medium dat wordt gebruikt om het gesmolten metaal in druppeltjes te desintegreren:
Gasverstuiving
Bij gasverneveling versnelt de kinetische energie van gas onder hoge druk snel en verspreidt de stroom vloeibaar metaal in fijne druppeltjes. Op basis van het gasleveringsontwerp kan het verder worden geclassificeerd in:
- Drukgasverstuiving – Maakt gebruik van nauw gekoppelde mondstukken om perslucht of inert gas zijwaarts op de vloeibare metaalstroom te leveren.
- Gasverneveling met twee vloeistoffen – Coaxiale mondstukken introduceren het vernevelingsgas met hoge snelheid rond een metalen binnenbuis.
- Gasverneveling met meerdere mondstukken – Maakt gebruik van een reeks convergerende en divergerende mondstukken om supersonische gasstralen op de smeltstroom af te leveren.
Met gas vernevelde poeders hebben een kleinere deeltjesgrootte, een meer uniforme morfologie en een hogere zuiverheid vergeleken met met water vernevelde poeders. Maar het proces is energie-intensief en duur.
Waterverneveling
Bij waterverneveling valt de stroom gesmolten metaal uiteen door de impact ervan met waterstralen onder hoge druk. Er worden druppeltjes gevormd met een bredere grootteverdeling. Waterverneveling heeft lagere kapitaal- en bedrijfskosten vergeleken met gasverneveling.
Op basis van het ontwerp kan waterverneveling gebruik maken van:
- Kortgekoppelde waterverneveling – Waterstralen botsen rechtstreeks op het vloeibare metaal dat de trechter verlaat.
- Vrije valwaterverneveling – Vallende stroom gesmolten metaal wordt onderschept door waterstralen onder de trechter.
Watervernevelde poeders hebben meer onregelmatige deeltjesvormen en een bredere verdeling, ideaal voor persen en sinteren. Maar water introduceert vervuiling.
Centrifugale verneveling
Bij centrifugale verneveling wordt gesmolten metaal in een met hoge snelheid draaiende schijf of beker gegoten of gepompt. Het metaal vormt een dunne film op de omtrek die door centrifugaalkrachten uiteenvalt in fijne druppeltjes.
Voordelen zijn onder meer een eenvoudig ontwerp, een laag gasverbruik en eenvoudige opschaling. Maar het groottebereik is relatief hoger dan gasverneveling. Wordt gebruikt voor de productie van bolvormige poeders van metalen met een laag smeltpunt, zoals tin, lood, zink enz.
Ultrasone gasverneveling
Combineert gasverneveling met een ultrasone generator gekoppeld aan het mondstuk. De hoogfrequente trillingen bevorderen de desintegratie en verspreiding van metaal in fijnere druppeltjes, waardoor submicronpoeder ontstaat.
Zeer effectief om nanokristallijne en amorfe poedermorfologieën te genereren. Maar duur en onderhoudsintensief. Gebruikt voor gespecialiseerde toepassingen.
Vonkerosie-verneveling
Bij deze elektrische vernevelingstechniek wordt een gepulseerde vonkontlading met hoge stroomsterkte toegepast tussen het gesmolten metaal en een elektrodepunt, waardoor plasma ontstaat dat het metaal uiteenvalt in ultrafijn bolvormig poeder.
Maakt zeer fijne, zeer bolvormige metaalpoederproductie mogelijk. Maar lage productiesnelheid en hoge kosten. Meestal gebruikt voor edele metalen zoals goud, platina, palladium.
Verstuivercomponenten en ontwerp
Verstuivers bestaan uit een verscheidenheid aan componenten die zijn ontworpen om het metaalpoeder effectief te smelten, gieten, verstuiven, koelen en verzamelen.
Metaalsmelt- en gietsysteem
- Inductiefornuis – Meestal gebruikt voor het smelten van metalen zoals staal. Zorgt voor een goede temperatuurregeling en een lage smeltverontreiniging.
- Kroezen – Vuurvaste keramische potten bevatten vroeger een metaallading. Kan in een aparte oven worden verwarmd en handmatig worden gegoten of direct in het vernevelingssysteem worden opgenomen.
- Tunisch – Tussenreservoir voor gesmolten metaal dat de gietsnelheid in het vernevelingsgedeelte regelt.
- Regenpijp – Leidt nauwkeurig de stroom gesmolten metaal naar de vernevelingszone. Gemaakt van vuurvast metaal zoals wolfraam om hoge temperaturen te weerstaan.
- Pompen – Wordt gebruikt om de drukgevoede afgifte van gesmolten metaal in bepaalde verstuiverconfiguraties te regelen.
Afdeling Atomisatie
- Verstuivend mondstuk – Gespecialiseerde hogedruk- en temperatuurbestendige mondstukken die worden gebruikt om gas- of waterstralen voor verneveling te creëren.
- Spuitmondarrays – Meerdere gespecialiseerde spuitmonden strategisch gepositioneerd om de druppelvorming te optimaliseren.
- Draaiende componenten – Schijven en kopjes die worden gebruikt bij centrifugale verneveling draaien met zeer hoge snelheden – 10.000 tot 50.000 tpm, aangedreven door een elektromotor.
- Ultrasone generator – Zet elektrisch signaal om in hoogfrequente mechanische trillingen in het mondstukgebied. Gebruikt bij ultrasone verneveling.
- Stroomvoorziening – Levert de hoge stroom om een elektrische boog te genereren voor verneveling door vonkerosie.
Poederbehandelingssysteem
- Cyclonenscheiders – Scheid fijn poeder van de procesgas- of waterstromen met behulp van centrifugaalkrachten.
- Zakkenfilters – Verzamel zeer fijn poeder dat niet in cyclonen wordt gescheiden. Moet regelmatig worden vervangen.
- Schermclassificaties – Grootte-indeling van poeder in verschillende fracties met behulp van gaaszeven.
- Magnetische scheiders – Verwijder alle vuile metalen uit het poeder.
- Transportbanden – Transporteert poeder tussen apparatuur. Gebruikte schroef-, riem- en triltransporteurs.
- Hoppers – Slaat poeder op voor verdere verwerking of verpakking.
- Stofzuigen – Verwijdert gemorst poeder van apparatuur en oppervlakken. Cruciaal voor reactieve metaalpoeders.
Instrumentatie en bedieningselementen
- Temperatuursensoren – Cruciaal voor het monitoren en controleren van oven/smelt- en mondstuktemperatuur voor optimale verneveling.
- Druksensoren – Controleer de gas- en waterdruk in de sproeiers om een goede verneveling te behouden.
- Stroommeter – Meten en regelen van de stroomsnelheden van vernevelingsvloeistof en smelten.
- Toerentellers – Bewaakt de rotatiesnelheid van centrifugale verstuivingsschijven.
- Niveausensoren – Zorg voor optimale smeltniveaus in belangrijke vaten. Voorkomt overstroming.
- Noodstop – Vereist voor het snel en veilig uitschakelen van machines in geval van problemen.
- Controle systeem – Geautomatiseerde computerbesturing optimaliseert de coördinatie van parameters en verbetert de herhaalbaarheid.
Metaalpoedervernevelingsprocesparameters
Een juiste selectie van procesparameters is de sleutel tot het verkrijgen van poeders met de gewenste eigenschappen. De onderstaande tabel vat de belangrijkste variabelen samen en hun invloed op de poedereigenschappen:
Parameter | Effect op poedereigenschappen |
---|---|
Temperatuur van gesmolten metaal | Hogere temperaturen verminderen de viscositeit en verbeteren de verneveling. Maar kan de oxidatie en het verdampingsverlies vergroten. |
Vernevelende gasdruk | Een hogere gasdruk verbetert de deeltjesgrootteverdeling en verlaagt de gemiddelde grootte. Maar verhoogt het gasverbruik. |
Vernevelingsgasstroomsnelheid | Een hoger debiet verbetert de reductie van de deeltjesgrootte. Maar verhoogt het gasverbruik. |
Vernevelingsvloeistofsnelheid | Een hogere snelheid verbetert de reductie van de deeltjesgrootte. Afhankelijk van het mondstukontwerp. |
Mondstukontwerp | gespecialiseerde spuitmonden creëren fijnere druppels en poeder. |
Smeltgietsnelheid | Hogere gietsnelheden verhogen de opbrengst bij continu gebruik, maar kunnen de deeltjesgrootte verkleinen. |
Smelt oververhitting | Neemt toe naarmate de giettemperatuur boven het smeltpunt stijgt. Verbetert de vloeibaarheid. |
Smeltfiltratie | Verwijdert insluitsels en verontreinigingen. Verbetert de zuiverheid van het poeder. |
Vernevelingsafstand | Een langere vrije valafstand zorgt voor meer tijd voor druppelvorming. Vermindert de vorming van satellieten. |
Smelt samenstelling | Legeringselementen kunnen de viscositeit en oppervlaktespanning veranderen, waardoor het verstuivingsgedrag en de poedereigenschappen worden beïnvloed. |
Karakterisering van verstoven metaalpoeder
De eigenschappen en kwaliteit van het vernevelde poeder bepalen de prestaties in stroomafwaartse toepassingen. De belangrijkste geëvalueerde kenmerken zijn:
Deeltjesgrootteverdeling
De verdeling van poederdeeltjes over fracties van verschillende grootte, gewoonlijk weergegeven als D10-, D50- en D90-percentielen. Gasverneveling kan minder dan 20 micron bereiken, terwijl waterverneveling grover poeder produceert.
Deeltjesvorm en morfologie
Gasverstoven poeder heeft zeer bolvormige deeltjes, terwijl waterverstoven poeder onregelmatiger is. Satellietdeeltjes duiden op een gebrek aan optimale verneveling. Afgerond poeder heeft een betere vloei en pakkingsdichtheid.
Chemische samenstelling
De elementaire en fasesamenstelling uit testen. Bepaalt de legeringskwaliteit. Gasverneveling produceert een hoge zuiverheid, terwijl water reactieve metalen zoals titanium en aluminium kan vervuilen.
Schijnbare dichtheid en tikdichtheid
Indicator voor de efficiëntie van het verpakken van poeder. Een hogere dichtheid verbetert de producteigenschappen bij het persen en sinteren. Maar kan de poederstroom beïnvloeden. Waarden typisch 40-65% van materiaaldichtheid.
Stroomkenmerken
Belangrijk voor handling en downstream-verwerking. Beïnvloed door factoren zoals deeltjesvorm, grootteverdeling en oppervlaktestructuur. Verbeterd door gloeien, oppervlaktebehandeling.
Microstructuur
Interne poederstructuur onthuld door microscopie. Met gas verneveld poeder heeft fijne korrels en defecten door snelle stolling, terwijl verneveld water grover is. Bepaalt het sintergedrag.
Toepassingen van metaalpoederverneveling
Verstoven metaalpoeders vinden een breed scala aan toepassingen in geavanceerde productie, waardoor de productkwaliteit en prestaties verbeteren ten opzichte van conventionele metaalverwerking:
Additieve productie
- 3D-printen – Vernevelde bolvormige poeders met gecontroleerde grootteverdeling zijn ideaal voor poederbedfusietechnieken. Aluminium-, titanium- en nikkel-superlegeringen worden vaak gebruikt.
- Metaalspuitgieten – Fijnere roestvrijstalen, titanium- en aluminiumpoeders verbeteren het sinterproces en de componentdichtheid.
Poeder-Metallurgie
- Press and Sinter – Onregelmatig, grover waterverneveld ferropoeder dat wordt gebruikt voor de hoge productie van P/M-onderdelen met goede mechanische eigenschappen.
- Zachte en harde magneten – Fijne kristallijne NdFeB- en SmCo-poeders produceren hoogwaardige gebonden en warmgeperste magneten.
- Wrijvingsmaterialen – Waterverneveld koperpoeder verbetert de prestaties van remblokken en koppelingsvoeringen.
Oppervlaktecoatings
- Thermische spray – Bolvormig poeder met gecontroleerde grootteverdeling, belangrijk voor uniforme, dichte coatings via plasma- of HVOF-spray. WC-Co, nikkellegeringspoeder gebruikt.
- Vapour Deposition – Ultrafijne superlegeringspoedergrondstof die wordt gebruikt bij fysieke dampafzetting met elektronenbundels voor turbinecoatings met verbeterde bescherming.
Ander
- Metaalspuitgieten – Fijne roestvrijstalen, titanium- en aluminiumpoedergrondstoffen kunnen kleine, complexe componenten produceren.
- Soldeerpasta's - Verstoven zilver-, goud- en koperlegeringen die worden gebruikt bij de vervaardiging van soldeerverbindingen bij hoge temperaturen.
- Vonkerosie – Ultrafijn bolvormig poeder dat wordt gebruikt als diëlektrisch medium verbetert de precisie en snelheid van EDM-bewerking.

Voordelen van metaalpoederverneveling
Vergeleken met conventionele metaalverwerkingsroutes zijn de belangrijkste voordelen van het gebruik van verstoven poeders:
- Verbeterde mechanische eigenschappen – Fijne, homogene microstructuur door snelle stolling verhoogt de vloeigrens, de vermoeiingslevensduur en de ductiliteit.
- Nauwkeurige dimensionale controle – Consistent, bolvormig poeder maakt fabricage met hoge dichtheid en nauwkeurige netvorm mogelijk. Vermindert machinale bewerking.
- Hogere productiviteit – Componenten kunnen via metaalpoederverwerking sneller in massa worden geproduceerd dan subtractieve methoden.
- Grotere ontwerpvrijheid – Er kunnen complexe geometrieën worden vervaardigd die onmogelijk zijn door gieten of machinaal bewerken.
- Minimaliseert afval – Het vermogen tot bijna netvorm vermindert schrootverlies ten opzichte van de metallurgie van blokken. Ongebruikt poeder kan worden gerecycled.
- Lager energieverbruik – Het poederproces vereist een lagere temperatuur en energie dan de productie uit bulkmetaal.
- Aangepaste legeringen – Gespecialiseerde samenstellingen kunnen worden verstoven die moeilijk via blokken te produceren zijn.
- Hoge zuiverheid – Reactieve elementen zoals titanium kunnen worden verneveld met minder vervuiling dan conventionele praktijken.
Beperkingen van metaalpoederverneveling
- Er zijn hoge kapitaalinvesteringen nodig voor verstuivingsapparatuur en poederbehandelingssystemen in vergelijking met bulkmetaalverwerking.
- Er zijn aanvullende stroomafwaartse processen zoals verdichting, sinteren enz. nodig om producten uit poeders te maken. Het totale productietraject is complex.
- Het realiseren van ultrafijn poeder op nanoschaal kan een uitdaging en duur zijn met lagere doorvoersnelheden.
- Potentieel voor verontreiniging bij gebruik van waterverneveling, vooral voor reactieve metalen.
- Poeder kan zuurstof en vocht adsorberen, wat een beschermende opslag en hantering vereist.
- Er bestaan veiligheidsproblemen in verband met stofexplosies, brandgevaar en toxiciteit voor bepaalde poedersamenstellingen en morfologieën.
- Variabiliteit in de eigenschappen van de uiteindelijke componenten vergeleken met bewerkte producten. Defecten gerelateerd aan poeder kunnen zich manifesteren na consolidatie.
- Recycling en hergebruik van metaalpoeder is beperkt in vergelijking met bulkmetaalvormen. Materiaal wordt na 1-2 hergebruikcycli weggegooid.
- Het gebrek aan industriële normen voor nieuwe metaalpoeders op het gebied van kenmerken, testmethodologie, kwaliteitscontrole en certificering creëert barrières voor acceptatie.
Een metaalpoedervernevelingssysteem selecteren
Het kiezen van de juiste vernevelapparatuur voor een toepassing hangt af van factoren zoals:
Productie volume
- Lage productie – verstuivers op laboratorium- en pilotschaal. Centrifugale of drukgasvernevelingssystemen.
- Middelmatige productie – Continue verstuivers met een poederopbrengst tot 3 ton/uur.
- Hoge productie – Op maat gemaakte grootschalige systemen met een capaciteit van meer dan 10 ton/uur.
Poedermateriaal
- Niet-reactieve metalen zoals staal en nikkellegeringen kunnen waterverneveling gebruiken.
- Watergevoelige legeringen zoals aluminium en titanium hebben verneveling met inert gas nodig.
- Vuurvaste metalen zoals wolfraam vereisen gespecialiseerde verstuivingsmedia en bescherming.
Poeder eigenschappen
- Gasverneveling voor fijner poeder onder 30 micron met bolvormige morfologie.
- Waterverneveling voor grover, onregelmatig poeder voor het persen.
- Gespecialiseerde verneveling voor nanokristallijn of amorf metaalpoeder.
Product applicatie
- Additieve productie maakt gebruik van zeer fijn, gecontroleerd deeltjesverdeelpoeder afkomstig van gasverneveling.
- Poederspuitgieten vereist fijn, bolvormig poeder met een goede vloei.
- Thermische spuitcoatings hebben een dicht, bolvormig poeder nodig dat goed verpakt is.
Kapitaal- en bedrijfskosten
- Waterverneveling heeft lagere apparatuur- en bedrijfskosten, maar kan de poederkwaliteit in gevaar brengen.
- Gasverneveling brengt 10x hogere kapitaalkosten met zich mee, maar levert superieur poeder op. Bedrijfskosten ook hoger.
- Centrifugale verneveling is economisch, maar heeft beperkingen in grootte en vorm.
Installatie-integratie
- Vereist voldoende infrastructuur voor smeltvoorbereiding, poederbehandeling, opslag en transport.
- Beveiligingssystemen voor reactieve metalen zoals inerte gasatmosfeer.
- Geautomatiseerde controles en gegevensmonitoring verbeteren de processtabiliteit.
Toonaangevende fabrikanten van metaalpoederverstuivers
Verschillende bedrijven bieden gestandaardiseerde en op maat gemaakte metaalpoedervernevelingssystemen en componenten:
Gasverstuivingssystemen
- Praxair – marktleider in hogedrukgasvernevelingsapparatuur. Biedt systemen op laboratorium-, pilot- en productieschaal.
- AP&C – Gespecialiseerd in kortgekoppelde gasverstuivers voor reactieve en vuurvaste metalen. Wordt veelvuldig gebruikt voor titanium- en aluminiumpoeders.
- ALD Vacuum Technologies – Ontwerpt gasverstuivers met meerdere mondstukken voor gemiddelde tot hoge productie. Eigendom van Oerlikon Metco.
Waterverneveling
- Gasbarre – Biedt kortgekoppelde waterverneveling en vrije val-waterverneveling voor middelgrote tot grote volumes.
- Sheffield Atomising Systems – Al meer dan 50 jaar gespecialiseerd in vrije valwatervernevelingstechnologie.
Centrifugale verneveling
- ABB – Grote wereldwijde leverancier van apparatuur. Biedt centrifugale verstuivingssystemen op lab- tot volledige productieschaal.
- Ferrum AG – Toonaangevende leverancier van horizontale en verticale centrifugaalverstuivers, gevestigd in Zwitserland.
Ultrasone verstuiving
- Tekna – Biedt ultrasone gasverstuiversystemen aan op basis van hun gepatenteerde gekoppelde dubbeldraads inductiegeleidingstechnologie
- Ultramet – Biedt speciale ultrasone verstuivingsapparatuur met vloeibaarmakingstechnologie op hoge temperatuur
Vonkerosie-verneveling
- PyroGenesis – Biedt het Plasma Atomization System (PAS) voor de productie van ultrafijne bolvormige metaalpoeders.
- Plasma Innovations – Levert de roterende elektrodeproces (REP) vonkerosie-verstuivingssystemen.
Kostenanalyse van metaalpoederverstuivers
De kosten van de verstuiver zijn afhankelijk van de schaal, de productiesnelheid, het automatiseringsniveau en het poedermateriaal dat wordt verwerkt. Typische schattingen van de kapitaalkosten:
Grote productiegasverstuiver | Gebouw op maat | 1000 | 10 miljoen |
---|---|---|---|
Kleine productiewaterverstuiver | Trailer/containersysteem | 100 | 750,000 |
Waterverstuiver met gemiddelde productie | Onderdak systeem | 500 | 2 miljoen |
Grote productiewaterverstuiver | Gebouw op maat | 2000 | 5 miljoen |
Pilot centrifugale verstuiver | Skid gemonteerd | 50 | 400,000 |
Middelgrote centrifugale verstuiver | Onderdak systeem | 500 | 1,5 miljoen |
Lab ultrasone verstuiver | Tafelblad | 5 | 250,000 |
Pilot ultrasone verstuiver | Skid gemonteerd | 20 | 1000000 |
Vonk-erosie verstuiver | Containersysteem | 10 | 2 miljoen |
Operatie kosten
- De belangrijkste kosten zijn energie, arbeid, onderhoud en gebruik van inert gas.
- Het stroomverbruik bij gasverneveling bedraagt ~500-800 kWh per ton poeder. Gasverbruik 5-10 m3 per kg poeder.
- Energieverbruik bij waterverneveling lager: ~200-400 kWh per ton poeder. Maar hogere arbeid en onderhoud.
- Stroomverbruik door centrifugale verneveling ~300-500 kWh per ton poeder. Lager verbruik van inert gas.
- Verbruiksonderdelen zoals mondstukken en filterzakken moeten regelmatig worden vervangen.
Mogelijkheden voor kostenbesparing
- Het vergroten van de productieschaal en de poederproductie verlaagt de kapitaalkosten per kg poeder.
- Een hogere mate van automatisering en monitoring verbetert de arbeidsproductiviteit.
- Het recyclen en hergebruiken van procesgassen, water en restwarmte verlaagt de bedrijfskosten.
- Preventieve onderhoudsprogramma's minimaliseren stilstand en onderhoudskosten.
- Lokale levering van energie, gassen, water en ondersteunende diensten verlagen de logistieke kosten.
- Het kopen van herbouwde/gebruikte verstuivingssystemen vermindert de kapitaaluitgaven voor kleine producenten.
Apparatuur voor metaalpoederverneveling – Veelgestelde vragen
Vraag: Wat is het typische deeltjesgroottebereik dat wordt bereikt bij gasverneveling?
A: Gasverneveling kan poeders produceren met een deeltjesgrootte van 1 micron tot meer dan 100 micron. Typische D50-waarden zijn 10-45 micron voor de meeste legeringen. Fijner poeder onder de 10 micron is mogelijk met geoptimaliseerde spuitmonden en hoge gassnelheden.
Vraag: Hoeveel kan een klein gasverstuiversysteem jaarlijks produceren?
A: Een gasverstuiver op pilotschaal met een output van 10 kg/uur en een werking van 5000 uur/jaar kan ~50.000 kg poeder per jaar produceren. Een klein productiesysteem met een capaciteit van 50 kg/uur kan bij volledige productie ~250.000 kg per jaar produceren.
Vraag: Welke soorten metalen kunnen tot poeder worden verneveld?
A: De meeste commerciële legeringssystemen zijn verneveld, inclusief roestvrij staal, gereedschapsstaal, nikkellegeringen, titaniumlegeringen, aluminiumlegeringen, superlegeringen, kobaltlegeringen enz. Vuurvaste metalen zoals wolfraam en molybdeen vormen een uitdaging en vereisen gespecialiseerde vernevelingssystemen.
Vraag: Wat is de beste vernevelingsmethode voor reactieve metalen zoals titanium?
A: Gasverneveling met een inert gas zoals argon of stikstof heeft de voorkeur voor reactieve metalen zoals titanium en aluminium. Dit voorkomt oxidatie en vervuiling in vergelijking met waterverneveling.
Vraag: Hoe fijn kan de deeltjesgrootte worden bereikt met ultrasone verneveling?
A: Ultrasone gasverstuivers kunnen, indien geoptimaliseerd, metaalpoeder op submicron- en nanoschaal genereren met een gemiddelde grootte van minder dan 100 nanometer. Maar de poederproductiesnelheid is laag.
Vraag: Kan metaalpoeder worden gerecycled na gebruik bij additieve productie?
A: Ja, ongebruikt poeder kan worden hergebruikt in AM-processen. Maar het poeder kan slechts 1-2 keer worden gerecycled voordat de eigenschappen achteruitgaan. Het poeder moet vervolgens opnieuw worden verneveld voor voortgezet hergebruik.
Vraag: Wat is de beste manier om fijn reactief poeder te verwerken?
A: Gebruik inerte handschoenendozen, sluit poedercontainers af en vermijd blootstelling aan lucht/vocht. Sommige reactieve materialen vereisen mogelijk een oppervlaktebehandeling. Met water verneveld aluminiumpoeder wordt doorgaans gecoat om oxidatie te voorkomen.
Vraag: Waarom is inert gas met een hoge zuiverheid belangrijk voor gasverneveling?
A: Hoge zuiverheid minimaliseert verontreiniging. Vocht en zuurstof kunnen reactieve legeringen oxideren tijdens verneveling. Landgassen kunnen in het poeder terechtkomen, waardoor defecten in de eigenschappen van de uiteindelijke onderdelen ontstaan.
Vraag: Hoe gemakkelijk is het om een gasverstuiver te onderhouden en te repareren?
A: Routineonderhoud is eenvoudig. Maar grote reparaties, zoals het vervangen van spuitmondjes, kunnen dagen duren en vereisen personeel met een gespecialiseerde opleiding. Extra spuitmondconstructies moeten als reserve worden bewaard voor een snelle vervanging.
Vraag: Welke veiligheidsproblemen zijn er bij de productie van metaalpoeder?
A: Het hanteren van fijne poeders brengt altijd het risico van stofexplosies met zich mee. Andere problemen zijn de gevaren van gas onder druk, elektriciteit met hoge spanning, verhoogde temperaturen en het hanteren van gesmolten metaal waarvoor beschermende uitrusting en training nodig zijn.
Delen op
MET3DP Technology Co, LTD is een toonaangevende leverancier van additieve productieoplossingen met hoofdkantoor in Qingdao, China. Ons bedrijf is gespecialiseerd in 3D printapparatuur en hoogwaardige metaalpoeders voor industriële toepassingen.
Onderzoek om de beste prijs en een op maat gemaakte oplossing voor uw bedrijf te krijgen!
gerelateerde artikelen
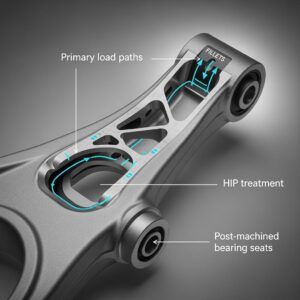
Metal 3D Printing for U.S. Automotive Lightweight Structural Brackets and Suspension Components
Lees verder "Over Met3DP
Recente update
Ons product
NEEM CONTACT MET ONS OP
Nog vragen? Stuur ons nu een bericht! Na ontvangst van uw bericht behandelen wij uw verzoek met een heel team.