Bolvormige poeders
Inhoudsopgave
Bolvormige poeders hebben betrekking op fijne deeltjes met een afgeronde morfologie die gebruikt worden op gebieden zoals additieve metaalpoederproductie, spuitgieten van keramiek en carbiden, farmaceutica en geavanceerde elektronicafabricage. Hun verbeterde stromings- en verpakkingseigenschappen bieden prestatievoordelen ten opzichte van onregelmatig gevormde poeders.
Overzicht van bolvormig poeder
Speciaal ontwikkelde sferische poeders leveren superieure dichtheid, vloeibaarheid, smeerbaarheid, verpakkingsefficiëntie en reologisch gedrag, wat essentieel is voor productieprocessen die homogene en stabiele grondstoffen nodig hebben.
Dankzij de nauwkeurige controle over de verdeling van de deeltjesgrootte, uniformiteit van vorm, chemische zuiverheid, microstructuur en oppervlaktechemie kunnen de prestaties worden afgestemd op veeleisende toepassingen op gebieden zoals:
- Additieve productie
- Metaal spuitgieten
- Thermische spuitcoatings
- Geavanceerde verwerking van keramiek
- Batterijmaterialen
- Katalysatoren
- Cosmetische en tandheelkundige formuleringen
- Chemisch mechanisch polijsten
Zowel submicron- als grotere bolvormige poeders spelen een cruciale rol in opkomende productietechnieken op nanoschaal en in persoperaties met grote volumes.
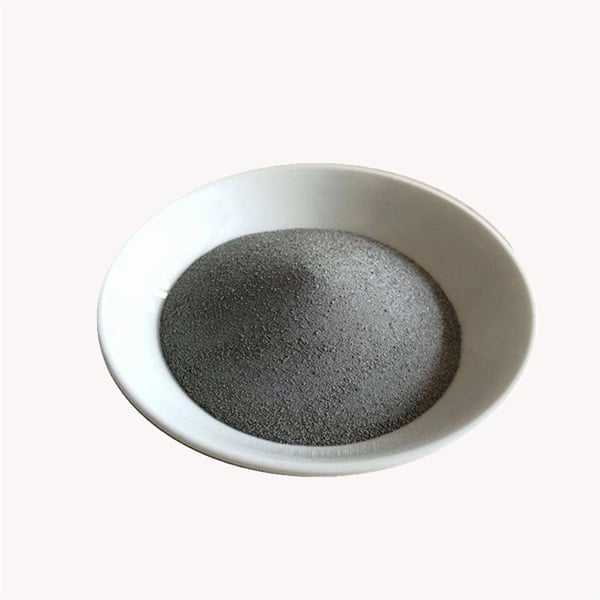
bolvormig poeder Eigenschappen
De sferische morfologie en gladde buitenkant van poederdeeltjes minimaliseert de wrijving tussen de deeltjes en maximaliseert de dichtheid in vergelijking met niet-sferische deeltjes. Dit leidt tot wenselijke eigenschappen.
Verbeterde vloeibaarheid en verpakkingsdichtheid
Afgeronde deeltjes herschikken en glijden gemakkelijker langs elkaar onder invloed van de zwaartekracht, pneumatisch transport of roeren, wat resulteert in betere stroomsnelheden, minder klonteren en eenvoudigere verwerking. Bulkdichtheden die de echte materiaaldichtheid benaderen worden ook bereikt door het minimaliseren van lege ruimtes.
Hierdoor kunnen mallen, matrijzen en bedden sneller worden gevuld, wat essentieel is voor de rendabiliteit van poedergebaseerde processen. Er worden stroomsnelheden van meer dan 15 s/50 g verwacht bij gebruik van een standaard Hall-apparaattest.
Smalle deeltjesgrootteverdelingen
Gecontroleerde productietechnieken maken sferische poederpartijen mogelijk met strakke grootteverdelingen variërend van 10-99% die binnen 5 μm afwijken. Deze consistentie zorgt voor voorspelbaar gedrag tijdens het doseren, mengen, verwarmen en consolideren.
Hoge gesinterde dichtheid
Bolvormige morfologieën zorgen voor een grotere verdichting tijdens sinter- of fusieprocessen met kleinere poriën tussen de deeltjes. Dit maximaliseert de haalbare mechanische eigenschappen in afgewerkte onderdelen. Dichtheden van meer dan 90% van theoretische niveaus zijn typisch.
Verbeterde dispersie
De lagere oppervlakte-volumeverhouding van sferische poeders vermindert aggregatie in vergelijking met onregelmatige vormen wanneer ze gedispergeerd worden in vloeibare middelen voor afzetting via thermisch spuiten, inkjetprinten, slipgieten of andere natte routes. Dit bevordert de uniformiteit en stabiliteit van de coating.
Andere kenmerken
- Beter behoud van vloeibaarheid na blootstelling aan verhoogde temperaturen
- Minder slijtage door schuren en apparatuur na verloop van tijd
- Meer gecontroleerde elektrische weerstanden en defecten
- Uniforme krimp en maatnauwkeurigheid
bolvormig poeder Productie methodes
Door voldoende kinetische energie toe te voegen aan gesmolten materiaalstromen, kunnen deze door oppervlaktespanning uiteenvallen in fijn gedispergeerde druppeltjes die stollen tot poederdeeltjes. Het beheersen van de procesomstandigheden bepaalt de uiteindelijke bolvormige poedereigenschappen.
Gasverneveling
Inerte gasstralen met hoge snelheid botsen op metaalsmelten en verdelen deze in fijne druppeltjes die snel afkoelen tot afgeronde vaste poeders wanneer ze uit de verstuivingskamer komen. Toepasbaar op reactieve legeringen zoals titanium, nikkel en materialen op ijzerbasis.
Waterverneveling
Vergelijkbaar concept, maar met water als smeltbrekend medium. Lagere koelsnelheden dan bij gasmethodes, maar hogere opbrengsten en goedkopere bedrijfskosten zijn beter geschikt voor legeringen met een hoger smeltpunt, zoals staal en superlegeringen, wanneer een lagere poederkwaliteit aanvaardbaar is.
Plasma-roterend elektrodeproces (PREP)
Een vlamboog smelt de uiteinden van roterende draden van hoge zuiverheid die uiteenvallen in bolletjes die worden gekoeld in een inerte gasstroom die in de plasmastraal wordt getrokken. Zeer gecontroleerde omstandigheden maken strakke verdelingen mogelijk. Wordt gebruikt voor reactieve metalen zoals aluminium en magnesium.
Elektrode-inductie smeltgasatomisatie (EIGA)
Combineert het smelten van draadelektroden op inductiespoelen met dicht bij elkaar geplaatste gasmondstukken die zeer snel afkoelen van beginnende druppels mogelijk maken. Het beste voor het produceren van zeer uniforme nano- en submicron-sferische metaalpoeders met op maat gemaakte chemische legeringen.
Solgel verwerking
Via chemische routes kunnen ultrafijne deeltjes worden neergeslagen uit vloeibare precursors die vervolgens worden gecalcineerd en gemalen tot poeders met geoptimaliseerde vorm. Gebruikt voor keramiek, oxiden en carbiden waarvoor zuiverheid en nanoschaalafmetingen nodig zijn.
Andere methoden
Sproeidrogen, condensatiereacties, emulsificatie, cavitatiegebaseerde technologieën, chemische dampdepositie, elektrodepositie en vastestofreacties bieden speciale benaderingen voor sferische metallische, keramische en polymeerdeeltjes.
bolvormig poeder Materialen en maten
De meest voorkomende sferische poedermaterialen zijn metalen, keramiek, polymeren en speciale legeringen, variërend van deeltjes met een nanometerschaal tot deeltjes met een grootte van meer dan 100 micron.
Materiaalklasse | Materialen | Maatbereik |
---|---|---|
Metalen | Roestvrij staal, gereedschapsstaal, superlegeringen, titanium, wolfraam, kobaltchroom, koper, aluminium | 0,5 μm - 150 μm |
Keramiek | Aluminiumoxide, zirkoniumoxide, carbiden zoals WC of SiC | 0,01 μm - 45 μm |
Polymeren | Nylon, PEEK, PEKK, Ultem | 5 μm - 100 μm |
Anderen | Glas, magnetische legeringen, legeringen met vormgeheugen, legeringen met hoge entropie | 0,1 μm - 50 μm |
Duurdere legeringen, keramische en speciale poeders neigen naar kleinere deeltjesafmetingen voor additieve productie met hoge prestaties, terwijl processen met een hogere verwerkingscapaciteit beter werken met grotere verdelingen van bijna enkelvoudige afmetingen.
Grootteklassen
Groep | Bereik deeltjesdiameter |
---|---|
Ultrafijn | < 20 μm |
Prima | 20-45 μm |
Medium | 45-105 μm |
Ruw | 105-150 μm |
De gemiddelde grootte, bolvorm, chemische zuiverheid, morfologie, microstructuur, vloei en tapdichtheid worden bevestigd aan de hand van de toepassingseisen en verwerkingsbehoeften.
bolvormig poeder van Belangrijkste toepassingen
Additieve productie
Selectief lasersmelten, smelten met elektronenstralen en binder jetting zorgen voor ultrafijne sferische poeders met gecontroleerde grootteverdeling en samenstelling, waardoor complexe metalen onderdelen direct vanuit CAD-gegevens geproduceerd kunnen worden.
Metaalspuitgieten (MIM)
Sferische poeders gemengd met bindmiddelen worden gespuitgiet en vervolgens gesinterd om grote volumes kleine ingewikkelde onderdelen te produceren. Dit combineert de bijna netvormige mogelijkheden en afwerking van kunststof spuitgieten met de hoogwaardige eigenschappen van materialen zoals roestvrij staal, gereedschapsstaal en superlegeringen.
Thermische spuitcoatings
Als grondstof worden sferische poeders van metaal, carbide, oxide en polymeer door verhitte plasma- of verbrandingssproeiers gevoerd, waardoor coatings ontstaan die bestand zijn tegen corrosie, slijtage en hitte met op maat gemaakte mechanische of diëlektrische eigenschappen.
Geavanceerde keramiek
Sferische keramische poeders met een kleine diameterverdeling dienen als precursors voor de productie van hoogwaardige elektrische, structurele en vuurvaste componenten via koud isostatisch persen, slipgieten, tapeformuleringen en geavanceerde sintertechnieken die geoptimaliseerde poederbedden vereisen.
Andere nichetoepassingen
Cosmetische foundations, tandheelkundige polymeren, soldeerpasta's, katalysatordragende deeltjes, chemische mechanische polijstslurries, poedersmeedgeleiders, precursors voor metaalglas enz. zijn afhankelijk van speciale bolvormige poeders die voldoen aan strenge normen.
Wereldwijde leveranciers van sferisch poeder
Toonaangevende materiaalfabrikanten en poederverwerkers in Noord- en Zuid-Amerika, Europa en Azië leveren sferische poeders voor zowel O&O- als commerciële kopers. De prijzen variëren sterk op basis van zuiverheid, uniformiteit, grootte, samenstelling en inkoopvolume.
Metaal & legering opties
Bedrijf | Plaats |
---|---|
Sandvik | Duitsland |
Rio Tinto metaalpoeders | Canada |
Hogenäs | Zweden |
Mitsubishi materialen | Japan |
BÖHLER Edelstahl | Oostenrijk |
AMETEK | ONS |
Tekna | Canada |
Keramische, carbide en oxide poeders
Bedrijf | Plaats |
---|---|
HC Starck | Duitsland |
Reade Geavanceerde Materialen | ONS |
Inframat geavanceerde materialen | ONS |
Stanford Advanced Materials | ONS |
Nanoshel | ONS |
Andere leveranciers van bolvormig poeder voor farmaceutische toepassingen, polymeren, magnetische materialen, batterijmaterialen, katalysatoren en elektronische precursoren.
bolvormig poeder Kostenanalyse
Metaal- en legeringsferische poeders variëren van $5/kg voor algemeen aluminium en ijzer tot $500/kg voor gespecialiseerde soorten.
De kosten zijn sterk afhankelijk van:
- Basissamenstelling (bijv. roestvast staal kost 2-4x koolstofstaal)
- Productiemethode (gas vs waterverstuiving, plasma vs verbranding)
- Groottedistributie consistentie
- Morfologie en deeltjesstructuur
- Aankoophoeveelheid en gewenste levertijden
- Zuiverheidsniveaus en consistentie
De prijzen van het ceramische/karbide sferische poeder gaan van $50/kg tot $5000/kg gebaseerd op:
- Materiaal (siliciumdioxide vs lithiumaluminaat, WC vs HfC)
- Zuiverheid - Van 98 tot 99,999%
- Deeltjesafmetingen - nanoschaal kost 100x meer
- Bestelvolume
- Oppervlakte
- Mate van branden/vermalen
- Agglomeratietendensen
- Vochtgevoeligheid
Schaalvoordelen zijn van toepassing op bulkorders, terwijl aangepaste batches extra kosten met zich meebrengen. Een lagere poederconsistentie verlaagt ook de kosten.
Normen en specificaties
Technisch samengestelde sferische poeders moeten voldoen aan de toepassingsbehoeften en gestandaardiseerde testmethodes die eigenschappen controleren zoals:
Parameter | Gebruikelijke methoden |
---|---|
Deeltjesgrootteverdeling | Laserdiffractie, sedimentatie, zeven |
Deeltjesvorm | Rasterelektronenmicroscopie, optische evaluatie |
Poeder vloeibaarheid | Hall debietmeter trechter |
Tik op dichtheid | Standaard druppeldichtheidsapparaat |
Verificatie van de samenstelling | ICP-OES/MS, FTIR, XRF, GDMS |
Morfologie | SEM, TEM |
Specifiek oppervlak | BET-stikstofadsorptie |
Dichtheid poederbed | Geometrische metingen |
Thermische analyse | TGA, DSC |
Internationale (ISO), nationale (ASTM) en industriële richtlijnen omvatten aanvaardbare meettechnieken die toepasbaar zijn op metaal, keramiek, elektronica en andere materialen. bolvormige poeders.
Het gebruik van consistente methoden op basis van gestandaardiseerde vereisten garandeert betrouwbare prestaties wanneer ze worden toegepast in strenge productieprocessen en levenskritische toepassingen.
Voordelen versus beperkingen
Voordelen | Nadelen |
---|---|
- Voorspelbaar verpakkings- en stroomgedrag | - Hogere kosten dan gemalen/regelmatig poeder |
- Verbeterde productkwaliteit en procesrendementen | - Beperkte mogelijkheid tot extreem hoge temperaturen voor metalen |
- Betere controle over microstructuur en prestaties | - Agglomeratietendens in bepaalde gevallen |
- Aanpasbare grootteverdelingen | - Risico's op verontreiniging en consistentie |
- Flexibele samenstelling met legeringen | - Inbedding van deeltjes tijdens depositiestappen |
- Hogere haalbare gesinterde dichtheid | - Speciale voorzorgsmaatregelen bij het hanteren |
- Verminderde porositeit | - Zeven of classificeren vaak nodig |
- Toepasbaar op multimateriële componenten | - Uitdagingen voor vormbehoud bij de kleinste maten |
- Geschikt voor kleine afmetingen en fabricage van dunne films |
Weeg de voordelen af tegen de beperkingen op basis van de verwerkingsroute en de beoogde poedertoepassing.
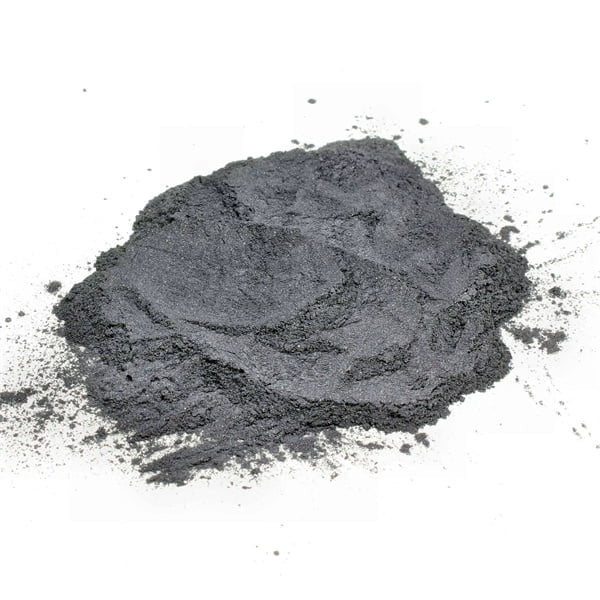
FAQ
V: Wat is het belangrijkste voordeel van bolvormige poeders ten opzichte van onregelmatig gevormde poeders?
A: Bolvormige poeders vloeien veel gemakkelijker door de lagere wrijving tussen de deeltjes, waardoor ze sneller kunnen worden gevuld met mallen, bedrukt, gespoten en verdicht, wat essentieel is voor precisiefabricage, waardoor de productiesnelheid, kwaliteit en betrouwbaarheid toenemen. Hun ronde vorm maakt ook een hogere sinterdichtheid mogelijk.
V: Hoe klein kunnen bolvormige metaalpoeders geproduceerd worden?
A: Met inerte gasverstuivingstechnieken kunnen roestvrijstalen poeders tot 10 micron worden gemaakt, terwijl koperlegeringen met gasverstuiving een diameter van 5 micron kunnen bereiken. Er zijn speciale legeringsmengsels met meerdere componenten gemaakt tot minder dan 20 nm via mini-emulsiechemie.
V: Wat bepaalt de grootteverdeling van sferisch poeder?
A: Het ontwerp van de straalpijp, de dynamica van de gasstroming, de onstabiliteit van de smeltstroom en de snelle afkoelingskinetiek bepalen de druppelvorming en stollingsfysica in gasverstuivingsprocessen - waarvoor modellering en zorgvuldige parametrische tests nodig zijn om de distributie te optimaliseren.
V: Wat is goedkoper - gas- of watervernevelde sferische poeders?
A: Waterverstuiving heeft 5-10x lagere operationele kosten dan gasverstuiving, maar produceert meer onregelmatige poeders die stroomafwaarts bewerkt moeten worden om de bolvorm en distributie te verbeteren. Het kostenvoordeel hangt dus af van het aanvaardbare kwaliteitsniveau voor de toepassing.
V: Kunt u bolvormige poederdeeltjes van één grootte maken?
A: Natte chemische productieroutes maken zeer strakke verdelingen mogelijk tot relatieve standaarddeviaties onder 5% van de gemiddelde deeltjesgrootte, maar overblijvende satellietfracties leiden tot enige spreiding. Gespecialiseerde classificatie of zeven helpt bij het isoleren van primaire modale fracties indien nodig.
Delen op
MET3DP Technology Co, LTD is een toonaangevende leverancier van additieve productieoplossingen met hoofdkantoor in Qingdao, China. Ons bedrijf is gespecialiseerd in 3D printapparatuur en hoogwaardige metaalpoeders voor industriële toepassingen.
Onderzoek om de beste prijs en een op maat gemaakte oplossing voor uw bedrijf te krijgen!
gerelateerde artikelen
Over Met3DP
Recente update
Ons product
NEEM CONTACT MET ONS OP
Nog vragen? Stuur ons nu een bericht! Na ontvangst van uw bericht behandelen wij uw verzoek met een heel team.
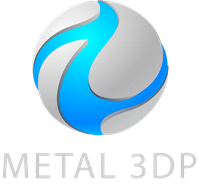
Metaalpoeders voor 3D printen en additieve productie