Roestvrij staal 316L poeder
Inhoudsopgave
Roestvrij staal 316L poeder is een populaire materiaalkeuze voor veel toepassingen vanwege de uitstekende corrosieweerstand, mechanische eigenschappen en biocompatibiliteit. Deze gids biedt een gedetailleerd overzicht van 316L-poeder, inclusief de eigenschappen, productiemethoden, toepassingen, leveranciers en meer.
Overzicht van roestvrij staal 316L poeder
Roestvrij staal 316L-poeder is een type roestvrijstalen legering die molybdeen bevat voor verbeterde corrosieweerstand. De “L” verwijst naar het lage koolstofgehalte, wat de lasbaarheid verbetert.
Enkele belangrijke eigenschappen en kenmerken van 316L-poeder zijn onder meer:
- Uitstekende corrosiebestendigheid, vooral tegen putcorrosie en spleetcorrosie
- Hoge sterkte en goede ductiliteit
- Uitstekende biocompatibiliteit en geschikt voor medische implantaten
- Niet-magnetische austenitische structuur
- Hoge oxidatie- en kruipweerstand bij verhoogde temperaturen
- Verkrijgbaar in verschillende deeltjesgroottes en morfologieën
316L-poeder kan worden geproduceerd door middel van gasverneveling, waterverneveling en andere methoden. Het poederproductieproces beïnvloedt de poedereigenschappen zoals deeltjesvorm, grootteverdeling, vloeibaarheid en meer.
Hier is een vergelijking van verschillende 316L-poedertypen en hun typische toepassingen:
Poeder soort | Deeltjesgrootte | Morfologie | Toepassingen |
---|---|---|---|
Gas verneveld | 15-150 µm | Bolvormig | Additieve productie, MIM |
Water verneveld | 10-300 µm | Onregelmatig, dendritisch | Metaal spuitgieten |
Plasma verneveld | <100 μm | Bolvormig | Additieve productie |
Elektrolytisch | <150 µm | Dendritisch, stekelig | Additieve productie, persen |
Carbonyl | <10 μm | Bolvormig | Poedermetallurgie, persen |
316L-poeder wordt gewaardeerd vanwege de combinatie van sterkte, corrosieweerstand en biocompatibiliteit. Enkele van de belangrijkste toepassingen zijn:
- Additieve productie – Selectief lasersmelten, direct lasersinteren van metalen, bindmiddelspuiten
- Metaalspuitgieten – Kleine, complexe onderdelen zoals orthopedische implantaten
- Persen en sinteren – Filters, poreuze structuren, zelfsmerende lagers
- Oppervlaktecoating – Om de slijtvastheid en corrosieweerstand te verbeteren
- Solderen en lassen – Als vulmateriaal
Hier is een overzicht van hoe 316L-poeder wordt gebruikt in verschillende productieprocessen:
Productieproces | Hoe 316L-poeder wordt gebruikt |
---|---|
Additieve productie | Het poederbed wordt selectief gesmolten door laser om 3D-onderdelen te bouwen |
Metaal spuitgieten | Poeder vermengd met bindmiddel, gevormd en vervolgens gesinterd |
Pers en sinter | Poeder wordt in vorm geperst en vervolgens gesinterd |
Deklaag | Op het oppervlak gespoten of gesmolten door thermisch spuiten, lasercladding enz. |
Solderen en lassen | Gebruikt als vulmateriaal voor verbindingen |
De ultrafijne korrelstructuur en homogene consistentie verkregen uit poeders maken 316L een ideaal materiaal voor kritische toepassingen in de lucht- en ruimtevaart, medische, chemische verwerking en meer.
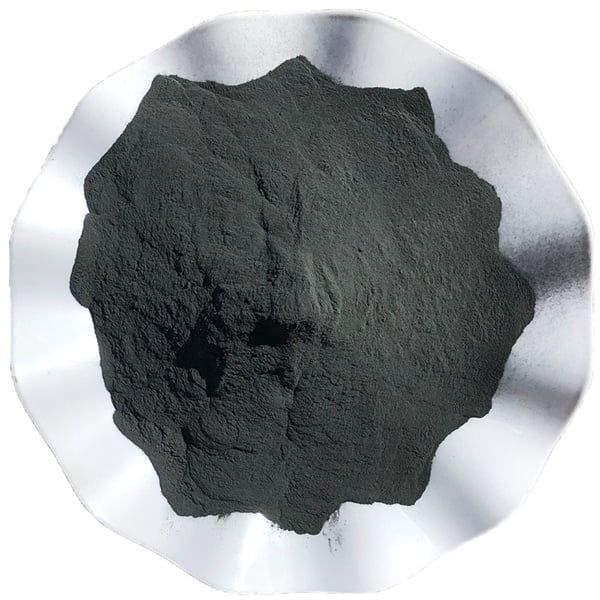
Eigenschappen van 316L roestvrij staalpoeder
Eigendom | Beschrijving | Invloed op bruikbaarheid |
---|---|---|
Chemische samenstelling | Voornamelijk samengesteld uit ijzer (Fe), chroom (Cr) (16-18%), nikkel (Ni) (10-12%), molybdeen (Mo) (2-3%), met kleine toevoegingen van silicium (Si), mangaan (Mn), fosfor (P), zwavel (S), stikstof (N). Laag koolstofgehalte (minder dan 0,03%) | Het hoge chroomgehalte zorgt voor een uitstekende weerstand tegen corrosie, vooral tegen put- en spleetcorrosie. Nikkel verbetert de sterkte en vervormbaarheid, terwijl molybdeen de weerstand tegen plaatselijke aanvallen verbetert, vooral door chloriden. Een laag koolstofgehalte minimaliseert het risico op carbideprecipitatie tijdens lassen of processen bij hoge temperaturen. |
Deeltjesgrootte en -verdeling | Gemeten in micrometers (µm), met een typisch bereik van 15-50 µm. De verdeling van de deeltjesgrootte binnen dit bereik is cruciaal. | Deeltjesgrootte en -distributie hebben een aanzienlijke invloed op de vloeibaarheid, verpakkingsdichtheid en mechanische eigenschappen van het eindproduct. Fijnere deeltjes bieden over het algemeen een betere oppervlakteafwerking, maar kunnen lastig te verwerken zijn vanwege de slechte vloeibaarheid. Een goed gecontroleerde verdeling met een mix van deeltjesgroottes optimaliseert de pakking en minimaliseert holtes in het eindproduct. |
Schijnbare dichtheid & kraandichtheid | Schijnbare dichtheid verwijst naar de dichtheid van het losjes gegoten poeder. De tapdichtheid wordt gemeten na het aftappen van de poedercontainer om een dichtere verpakking te verkrijgen. Eenheden zijn meestal g/cm³. | Het verschil tussen schijnbare dichtheid en tapdichtheid weerspiegelt de vloeibaarheid van het poeder. Een hogere tapdichtheid ten opzichte van de schijnbare dichtheid duidt op betere stromingseigenschappen, wat essentieel is voor het efficiënt creëren van een poederbed in Additive Manufacturing processen. |
Vloeibaarheid | Het gemak waarmee poeder stroomt onder zijn eigen gewicht. Gemeten met technieken zoals de Hall Flowmeter of Carr Index. | Een goede vloeibaarheid zorgt voor een gelijkmatige verspreiding van het poeder en minimaliseert segregatie (scheiding van verschillende deeltjesgroottes) tijdens verwerking en afzetting. Dit vertaalt zich in consistente dichtheid en eigenschappen in het eindproduct. |
Sfericiteit en morfologie | Sfericiteit verwijst naar hoe dicht een deeltje op een perfecte bol lijkt. Morfologie beschrijft de algemene vorm van de deeltjes (bolvormig, hoekig, onregelmatig). | Bolvormige deeltjes stromen doorgaans beter en pakken dichter op dan onregelmatige vormen. Sommige toepassingen kunnen echter baat hebben bij een specifieke deeltjesmorfologie om de gewenste oppervlaktestructuur of in elkaar grijpende deeltjes te verkrijgen. |
Smeltpunt & Bereik | Rond 1400°C (2552°F). Het smelttraject kan licht variëren afhankelijk van de specifieke poedersamenstelling. | Het smeltpunt is cruciaal voor het bepalen van de juiste verwerkingstemperaturen bij technieken zoals sinteren of Additive Manufacturing. |
Warmtegeleiding | Ongeveer 16 W/mK. | Thermische geleidbaarheid beïnvloedt de warmteoverdracht binnen het poederbed tijdens de verwerking. Dit kan factoren beïnvloeden zoals koelsnelheden, restspanningen en de vorming van ongewenste fasen in het eindproduct. |
Sintergedrag | Het vermogen van poederdeeltjes om zich aan elkaar te hechten tijdens een verhittingsproces op hoge temperatuur (sinteren) om een vast object te vormen. | Het sintergedrag hangt af van factoren zoals de verdeling van de deeltjesgrootte, de chemische samenstelling van het poederoppervlak en sinterparameters. Goed gecontroleerd sinteren zorgt voor verdichting van het poederbed, waardoor de gewenste mechanische eigenschappen in het eindproduct worden bereikt. |
Corrosieweerstand | Erft een uitstekende corrosiebestendigheid van zijn bulktegenhanger, 316L roestvrij staal. Biedt weerstand tegen een breed scala aan omgevingen, waaronder oxiderende zuren, reducerende zuren en zoutnevel. | Het molybdeengehalte in 316L poeder zorgt voor een superieure weerstand tegen putcorrosie, vooral in chloridehoudende omgevingen, in vergelijking met 304L roestvast staal poeder. Dit maakt het geschikt voor toepassingen die een hoge corrosiebestendigheid vereisen. |
Productiemethoden voor 316L poeder
Methode | Beschrijving | Deeltjeskenmerken | Voordelen | Nadelen | Toepassingen |
---|---|---|---|---|---|
Gasverstuiving | Gesmolten 316L staal wordt geïnjecteerd in een inerte gasstroom met hoge snelheid, waardoor het in fijne druppeltjes breekt die snel stollen tot bolvormige deeltjes. | - Bolvorm - Strakke grootteverdeling (15-45 micron) - Uitstekende vloeibaarheid - Hoge verpakkingsdichtheid | - Consistente kwaliteit - goed voor Additive Manufacturing (AM) processen zoals Laser Beam Melting (LBM) en Electron Beam Melting (EBM) | - Hoog energieverbruik - Potentieel voor zuurstof- en stikstofopname | - Lucht- en ruimtevaartonderdelen (turbinebladen, warmtewisselaars) - Medische implantaten (vanwege biocompatibiliteit) - Hoogwaardige auto-onderdelen |
Waterverneveling | Vergelijkbaar met gasverstuiving, maar met een waterstraal onder hoge druk om het gesmolten metaal te breken. | - Onregelmatige vorm met enkele satellieten (gesmolten deeltjes) - Bredere grootteverdeling (10-100 micron) - Lagere stroombaarheid vergeleken met gasverstuiving | - Kosteneffectiever dan gasverstuiving - Geschikt voor toepassingen waarbij de bolvorm minder kritisch is | - Hoger zuurstofgehalte door interactie met water - Mogelijk extra nabewerking nodig voor AM | - Wervelbedreactoren (katalysatordragers) - Grondstoffen voor metaalspuitgieten (MIM) |
Plasma-verneveling | Maakt gebruik van een plasmatoorts met hoge temperatuur en hoge snelheid om het 316L staal te smelten en te verstuiven. | - Zeer sferische vorm - Strakke grootteverdeling met fijnere deeltjes mogelijk (tot 5 micron) - Uitstekende vloeibaarheid | - Superieure kwaliteit voor veeleisende AM-toepassingen - Kan fijnere poeders bereiken voor ingewikkelde vormen | - Hoogste energieverbruik van de drie methoden - Vereist gespecialiseerde apparatuur | - Hoogwaardige turbinebladen - Microfluïdische componenten - Biomedische implantaten die een hoge oppervlakteafwerking vereisen |
Mechanisch legeren | Vaste elementaire of voorgelegeerde poeders worden gemengd en samen gemalen in een hoogenergetische kogelmolen om een uniforme 316L samenstelling te verkrijgen. | - Onregelmatige vorm met hoekige facetten - Grote spreiding in grootte - Lagere stroombaarheid | - Zeer aanpasbaar voor het creëren van unieke legeringssamenstellingen die niet haalbaar zijn met andere methoden | - Langere verwerkingstijd vergeleken met verstuivingstechnieken - Kan extra stappen vereisen om de stroombaarheid voor AM te verbeteren | - Gespecialiseerde onderdelen die specifieke materiaaleigenschappen vereisen - Ontwikkeling van nieuwe legeringen voor AM |
Elektrolyse | Een op water gebaseerd proces waarbij een anode van 316L oplost in de elektrolytoplossing en de metaalionen als poeder worden afgezet op de kathode. | - Sferische of dendritische vormen - Grote spreiding in grootte - Kan poreus zijn | - Zeer zuivere poeders haalbaar - Potentieel voor bijna-netvorm productie | - Beperkte productiecapaciteit - Relatief langzaam proces | - Biomedische implantaten die een hoge zuiverheid vereisen - Katalysatordragers - Gespecialiseerde toepassingen die specifieke poedereigenschappen vereisen |
Toepassingen van 316L roestvrij staalpoeder
Industrie | Sollicitatie | Hefboomeffecten | Aanvullende opmerkingen |
---|---|---|---|
Medisch & tandheelkundig | * Implantaten (knie, heup, tand) * Chirurgische instrumenten * Prothesen | * Biocompatibel (veilig voor lichaamscontact) * Uitstekende corrosiebestendigheid * Hoge sterkte * Vormbaarheid voor complexe ontwerpen | * 316L minimaliseert risico op afstoting en infectie. * Poeder maakt poreuze structuren voor botingroei mogelijk. * Kan worden gesteriliseerd voor veilig chirurgisch gebruik. |
Voedselverwerking | * Drukvaten * Buizen * Kleppen * Fittingen * Bevestigingsmiddelen | * Superieure corrosiebestendigheid tegen voedingszuren en pekel * Eenvoudig te reinigen en te onderhouden * Voldoet aan hygiëne- en veiligheidsnormen | * 316L garandeert voedselkwaliteit en voorkomt besmetting. * Gladde oppervlakken minimaliseren de bacteriële broeihaarden. * Bestand tegen herhaalde reinigingscycli. |
Marien | * Schroefassen * Onderdelen voor dieselmotoren * Dekuitrusting | * Uitzonderlijke weerstand tegen zoutwatercorrosie * Hoge mechanische sterkte * Duurzaamheid in ruwe omgevingen | * 316L verlengt levensduur van kritische maritieme componenten. * Behoudt structurele integriteit onder stress en zware belastingen. * Presteert betrouwbaar bij verschillende temperaturen. |
Chemisch & petrochemisch | * Reactievaten * Leidingsystemen * Kleppen * Pompen | * Ongevoelig voor een breed scala aan chemicaliën * Bestand tegen hoge temperaturen * Druktolerantie | * 316L kan agressieve chemicaliën aan zonder degradatie. * Bestand tegen hoge verwerkingstemperaturen voor efficiënte reacties. * Geschikt voor omgevingen met hoge druk in raffinaderijen en fabrieken. |
Lucht- en ruimtevaart | * Vliegtuigmotoronderdelen * Vloeistofregelsystemen * Constructiedelen | * Hoge sterkte-gewichtsverhouding * Uitstekende mechanische eigenschappen bij hoge temperaturen * Corrosiebestendigheid in veeleisende omgevingen | * 316L vermindert gewicht voor verbeterde brandstofefficiëntie. * Behoudt prestaties onder extreme hitte en druk. * Bestand tegen corrosie door vliegtuigbrandstof en andere vloeistoffen voor de ruimtevaart. |
Automobiel | * Uitlaatonderdelen * Motoronderdelen * Sierelementen en decoratieve elementen | * Bestand tegen hoge temperaturen * Vormbaarheid voor complexe vormen * Corrosiebestendigheid voor langere levensduur | * 316L is bestand tegen hete uitlaatgassen zonder krom te trekken. * Kan worden gevormd tot ingewikkelde uitlaatspruitstukken en -pijpen. * Bestand tegen corrosie door strooizouten en barre weersomstandigheden. |
Consumentengoederen | * Horloges * Sieraden * Bestek * Huishoudelijke apparaten | * Esthetische aantrekkingskracht door gepolijste afwerking * Hoge sterkte en slijtvastheid * Corrosiebestendigheid voor eenvoudige reiniging en hygiëne | * 316L biedt een gestroomlijnde, luxueuze look voor hoogwaardige producten. * Gebruiksvoorwerpen en apparaten behouden hun scherpte en duurzaamheid. * Eenvoudig te onderhouden, schoon en hygiënisch oppervlak. |
Bouw | * Bouwkundige bekleding * Bevestigingsmiddelen * Leuningen * Hardware | * Corrosiebestendigheid voor buitentoepassingen * Hoge sterkte en weerbestendigheid * Esthetische aantrekkingskracht voor moderne ontwerpen | * 316L is bestand tegen zware weersomstandigheden zonder te roesten. * Behoudt structurele integriteit en functionaliteit na verloop van tijd. * Biedt een strakke, eigentijdse look voor architecturale elementen. |
Specificaties en normen
De samenstelling, kwaliteit en eigenschappen van 316L-poeder worden bepaald door verschillende internationale specificaties en normen.
ASTM-normen
- ASTM A240 – Standaard voor chroom- en chroom-nikkel roestvrijstalen platen, platen en strippen voor drukvaten en algemene toepassingen. Definieert samenstellingslimieten en mechanische eigenschappen voor 316L-legering.
- ASTM B822 – Standaard testmethode voor de deeltjesgrootteverdeling van metaalpoeders en verwante verbindingen door lichtverstrooiing. Wordt gebruikt om de poedergrootteverdeling te karakteriseren.
- ASTM F3055 – Standaardspecificatie voor additieve productie van nikkellegeringspoeder bedoeld voor gebruik in poederbedfusietoepassingen. Definieert strenge eisen voor AM-nikkellegeringspoeder, inclusief 316L.
- ASTM F3049 – Gids voor het karakteriseren van eigenschappen van metaalpoeders die worden gebruikt voor additieve productieprocessen. Biedt richtlijnen voor het meten van kenmerken zoals stroming, dichtheid, morfologie enz.
Andere normen
- ISO 9001 – Kwaliteitsmanagement voor de productie van metaalpoeders
- ISO 13485 – Kwaliteitsmanagement voor metaalpoeders voor medische toepassingen
- ASME Ketel- en drukvatcode – Materiaalvereisten voor drukvattoepassingen
Gerenommeerde leveranciers van 316L-poeder beschikken over kwaliteitssystemen die zijn gecertificeerd volgens ISO- en ASTM-normen. Traceerbaarheid van partijen en uitgebreide tests worden gehandhaafd om naleving te garanderen.
Leveranciers van 316L-poeders
Enkele toonaangevende wereldwijde leveranciers van 316L roestvrij staalpoeder zijn onder meer:
Bedrijf | Productie methodes | Poeder soorten | Deeltjesgrootte |
---|---|---|---|
Sandvik | Gasverneveling | Visarend® 316L | 15-45 µm |
LPW-technologie | Gasverneveling | LPW316L | 15-63 μm |
Timmerman | Gasverneveling | Timmerman 316L | 15-150 µm |
Hogenäs | Waterverneveling | 316L | 10-45 µm |
CNPC | Gas-, waterverneveling | 316L | 10-150 µm |
Pometon | Gas-, waterverneveling | 316L | 10-150 µm |
ATI | Gasverneveling | 316L | 10-63 μm |
De prijs van 316L-poeder is afhankelijk van factoren zoals:
- Poederkwaliteit, samenstelling, deeltjesgrootte en morfologie
- Productie methode
- Bestelhoeveelheid en lotgrootte
- Niveau van kwaliteitscontrole en testen
- Verpakkings- en leveringsvereisten
De indicatieve prijs voor gasverstoven 316L-poeder ligt tussen $50-100 per kg voor standaardbestellingen. Aangepaste bestellingen met speciale vereisten kunnen meer kosten.
Bij het selecteren van een 316L-poederleverancier zijn enkele belangrijke overwegingen:
- Poedereigenschappen – deeltjesgrootteverdeling, morfologie, vloeibaarheid enz. moeten overeenkomen met de toepassingsbehoeften
- Consistente kwaliteit en samenstelling volgens specificaties
- Betrouwbare supply chain en logistiek
- Naleving van internationale normen en certificeringen
- Technische expertise en klantenservice
- Prijzen en minimale bestelhoeveelheid
Toonaangevende 316L-poederfabrikanten hebben tientallen jaren ervaring in het produceren van poeders die zijn afgestemd op AM-, MIM- en andere toepassingen met strenge kwaliteitscontroles.
Ontwerpoverwegingen voor 316L-poeder
Ontwerpoverwegingen voor 316L roestvast staal poeder
Aspect | Overweging | Invloed op afgedrukt onderdeel | Aanbevelingen |
---|---|---|---|
Wanddikte | De minimale dikte moet 0,8-1 mm zijn | Onderdelen met dunnere wanden kunnen zwak zijn en vatbaar voor scheuren. | * Ontwerp wanden van minstens 1 mm dik voor optimale sterkte. * Overweeg het gebruik van interne ribben of roosters voor versterking in dunne doorsneden. * Voor onderdelen die een minimale wanddikte vereisen, onderzoek alternatieve AM processen met een hogere resolutie. |
Overstekken en hoeken | Scherpe hoeken en overhangen zonder ondersteuning kunnen leiden tot kromtrekken en delaminatie. | * Minimaliseer scherpe hoeken door hoeken en rondingen in te bouwen. * Ontwerp overstekken met hoeken tussen 30-45 graden voor betere ondersteuning. * Gebruik strategisch geplaatste ondersteunende structuren tijdens het printen om doorhangen te voorkomen. | |
Oppervlakteafwerking en oriëntatie | Poederkenmerken en laagoriëntatie kunnen de oppervlaktestructuur beïnvloeden. | * Begrijpen hoe poedergrootte en morfologie oppervlakteruwheid beïnvloeden. * Overweeg de oriëntatie van het onderdeel om de zichtbaarheid van lagen op kritieke oppervlakken te minimaliseren. * Nabewerkingstechnieken zoals polijsten of parelstralen kunnen de oppervlakteafwerking verbeteren. | |
Porositeit | Luchtbellen in het onderdeel kunnen de mechanische eigenschappen aantasten. | * Optimaliseer printparameters zoals laservermogen en scansnelheid om een hoge dichtheid te bereiken. * Verken technieken zoals Hot Isostatic Pressing (HIP) om porositeit verder te minimaliseren. * Ontwerp interne kanalen of ontluchtingsgaten om poederverwijdering tijdens het printen te vergemakkelijken. | |
Stressmanagement | Restspanningen van het printproces kunnen leiden tot kromtrekken of barsten. | * Maak strategisch gebruik van ondersteuningsstructuren om spanningsconcentratiepunten te minimaliseren. * Ontwerp elementen zoals vullingen en geleidelijke overgangen om spanningsopbouw te verminderen. * Overweeg warmtebehandeling na het printen voor spanningsontlasting door gloeien. | |
Dimensionale nauwkeurigheid | De verdeling van de poedergrootte en krimp tijdens het sinteren kunnen de uiteindelijke afmetingen beïnvloeden. | * Rekening houden met krimpsnelheden (meestal rond 20%) bij het ontwerpen van het model. * Gebruik de principes van design for additive manufacturing (DfAM) om de printbaarheid te optimaliseren en maatafwijkingen te minimaliseren. * Print testonderdelen om de printparameters te kalibreren en de maatnauwkeurigheid te garanderen. | |
Ondersteunende structuren | Tijdelijke structuren die nodig zijn voor complexe geometrieën kunnen sporen achterlaten. | * Ontwerp ondersteuningsstructuren met een minimaal contactoppervlak om verwijderingssporen te minimaliseren. * Onderzoek oplosbare ondersteuningsmaterialen voor eenvoudigere nabewerking. * Optimaliseer het ontwerp van de ondersteuningsstructuur voor efficiënt materiaalgebruik en eenvoudige verwijdering. | |
Poeder verwijderen | Niet verwijderd poeder in holtes kan de functionaliteit beïnvloeden. | * Ontwerp interne kanalen of drainagegaten om de poederverwijdering te vergemakkelijken. * Gebruik hoekige elementen en ontluchtingsstrategieën om poederinsluiting te voorkomen. * Optimaliseer de printparameters om het vastplakken van poeder te minimaliseren en de vloeibaarheid te verbeteren. |
Naverwerking van 316L-onderdelen
Nabewerking van 316L roestvrijstalen onderdelen
Proces | Beschrijving | Voordelen | Overwegingen |
---|---|---|---|
Ondersteuning verwijderen | Tijdelijke structuren verwijderen die tijdens het afdrukken zijn gebruikt. | * Essentieel voor het bereiken van de uiteindelijke geometrie van het werkstuk. * Geeft toegang tot interne functies. | * De keuze van de verwijderingsmethode hangt af van het type dragermateriaal (handmatig, mechanisch, chemisch oplossen). * Zorgvuldige behandeling is vereist om beschadiging van het onderdeel te voorkomen. |
Hittebehandeling | * Stressvrij gloeien: Vermindert restspanningen van het printen om de maatvastheid te verbeteren en scheuren te voorkomen. * Oplossing ontharden: Verfijnt de microstructuur voor betere mechanische eigenschappen en corrosiebestendigheid. | * Optimaliseert de prestaties en de levensduur van het onderdeel. * Maakt conformiteit met specifieke materiaalspecificaties mogelijk. | * Vereist nauwkeurige regeling van temperatuur en tijd op basis van de geometrie van het onderdeel en het gewenste resultaat. * Voor gloeien in oplossing kunnen snelle koeltechnieken zoals afschrikken nodig zijn. |
Shot Peening | Het oppervlak bombarderen met kleine metalen bolletjes om een drukspanningslaag te creëren. | * Verbetert de vermoeiingssterkte en slijtvastheid. * Verbetert de weerstand tegen spanningscorrosie. | * De keuze van straalmiddelen en straalparameters hangt af van de gewenste oppervlakteafwerking en de diepte van het effect. * Overmatig stralen kan oppervlakteruwheid introduceren. |
Beitsen en passiveren | Chemisch reinigingsproces om oppervlakteverontreinigingen te verwijderen en de corrosiebestendigheid te verbeteren. | * Essentieel voor onderdelen die worden blootgesteld aan zware omstandigheden. * Creëert een passieve oxidelaag voor verbeterde corrosiebescherming. | * De keuze van beits- en passiveeroplossingen hangt af van de materiaalsoort en de oppervlaktegesteldheid. * Onjuiste omgang met chemicaliën vereist de juiste veiligheidsmaatregelen. |
Bewerking en afwerking | Traditionele subtractieve technieken om precieze afmetingen, toleranties en oppervlakteafwerkingen te bereiken. | * Maakt het mogelijk om eigenschappen te creëren die niet mogelijk zijn met AM. * Verbetert de esthetiek en functionaliteit van oppervlakken. | * Vereist extra deskundigheid en apparatuur voor machinale bewerking. * Kan warmte en spanning introduceren die verdere nabewerking noodzakelijk maken. |
Polijsten | Mechanische of chemische methoden om een glad, reflecterend oppervlak te verkrijgen. | * Verbetert de esthetische aantrekkingskracht voor decoratieve toepassingen. * Verbetert de oppervlaktehygiëne voor medische hulpmiddelen. * Vermindert oppervlakteruwheid voor verbeterde slijtvastheid. | * De keuze van de polijstmethode hangt af van het gewenste afwerkingsniveau. * Overmatig polijsten kan materiaal verwijderen en de afmetingen van het onderdeel veranderen. |
Galvanisch verzinken | Een dunne laag van een ander metaal op het oppervlak aanbrengen voor verbeterde eigenschappen. | * Verbetert de elektrische geleiding, slijtvastheid of corrosiebestendigheid. * Biedt decoratieve afwerkingen zoals verchromen of vergulden. | * Vereist gespecialiseerde apparatuur en expertise voor galvaniseerbaden. * De dikte van het galvaniseren moet zorgvuldig gecontroleerd worden om delaminatie te voorkomen. |
Veelvoorkomende defecten in 316L-onderdelen
Defect | Beschrijving | Oorzaak | Invloed | Matigingsstrategieën |
---|---|---|---|---|
Porositeit | Luchtzakken in het onderdeel tijdens het printen. | * Suboptimaal laservermogen of scansnelheid. * Ontoereikende poederstroom. * Onjuiste gasreiniging. | * Verminderde mechanische sterkte, vermoeiingslevensduur en corrosiebestendigheid. * Kan lekken veroorzaken in vloeistoftoepassingen. | * Printparameters optimaliseren voor de juiste smelt en dichtheid. * Het poederbed voorverwarmen om de stroming te verbeteren. * Maak gebruik van purgen met inert gas om ingesloten lucht te minimaliseren. * Overweeg nabewerkingstechnieken zoals Hot Isostatic Pressing (HIP) voor verdere verdichting. |
Gebrek aan fusie | Onvolledig smelten tussen aangrenzende poederlagen. | * Onvoldoende dichtheid van het laservermogen. * Inconsistente dikte van de poederlaag. * Verontreiniging op het poederoppervlak. | * Zwakke hechting tussen de lagen, wat kan leiden tot scheuren en mislukken van onderdelen. | * Lasersterkte en scansnelheid kalibreren voor de juiste smeltdiepte. * Zorg voor een consistente dikte van de poederlaag door de juiste overspuitmechanismen. * Zorg voor een schoon poederbed zonder vocht of verontreinigingen. |
Balloneren | Gesmolten metaal dat zich ophoopt in grote parels op het bovenoppervlak. | * Te hoge dichtheid van het laservermogen. * Onjuiste scansnelheid. * Onjuiste poedergrootteverdeling. | * Ruwe oppervlakteafwerking met slechte esthetiek. * Potentieel voor spatten en procesinstabiliteit. | * Verminder het laservermogen of verhoog de scansnelheid om oververhitting te voorkomen. * Scanpatronen optimaliseren om overmatige verblijftijd op een enkel gebied te voorkomen. * Gebruik een meer uniforme verdeling van de poedergrootte voor consistent smeltgedrag. |
Scheuren | Breuken in het onderdeel door restspanningen of thermische schokken. | * Snelle afkoeling tijdens het printen. * Onvoldoende spanningsontlasting na verwerking. * Scherpe hoeken of ontwerpkenmerken die spanning concentreren. | * Gecompromitteerde structurele integriteit en kans op defecten. | * Langzamere koelsnelheden toepassen tijdens het printen om thermische gradiënten te minimaliseren. * Voer spanningsarmgloeien uit om restspanningen te verminderen. * Ontwerp elementen met vloeiende overgangen en vermijd scherpe hoeken. |
Kromtrekken | Vervorming van het onderdeel ten opzichte van de bedoelde geometrie. | * Ongelijkmatige thermische uitzetting en inkrimping tijdens het printen. * Ongeschikte ondersteuningsstructuren voor complexe geometrieën. * Restspanningen in het onderdeel. | * Maatonnauwkeurigheden en kans op defecten. | * Printparameters optimaliseren om thermische gradiënten te minimaliseren. * Gebruik strategisch geplaatste ondersteuningsstructuren voor de juiste ondersteuning tijdens het printen. * Stress reliëfgloeien implementeren om kromtrekken te verminderen. |
Delaminatie | Scheiding van lagen binnen het onderdeel. | * Zwakke tussenlaagbinding door gebrek aan fusie. * Te hoog vochtgehalte in het poeder. * Verontreiniging op het poederbed. | * Verlies van structurele integriteit en kans op delaminatie van onderdelen. | * Zorgen voor een goede samensmelting tussen lagen door de drukparameters te optimaliseren. * Behoud een laag vochtgehalte van het poeder door juiste opslag en verwerking. * Gebruik een schoon poederbed zonder verontreinigingen. |
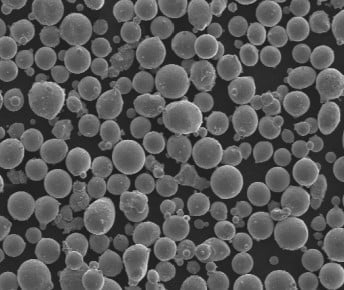
Hoe u een 316L-poederleverancier kiest
Hier vindt u een stapsgewijze handleiding voor het selecteren van een leverancier voor 316L roestvrij staalpoeder:
Stap 1: Bepaal de toepassingsvereisten
- Bedenk welk productieproces zal worden gebruikt – AM, MIM enz.
- Identificeer de kritische poedereigenschappen die nodig zijn, zoals deeltjesgrootte, vorm, zuiverheid enz.
- Houd rekening met de onderdeelspecificaties – mechanische eigenschappen, nauwkeurigheid, oppervlakteafwerking enz.
Stap 2: Onderzoek potentiële leveranciers
- Zoek naar toonaangevende 316L-poederfabrikanten met lange ervaring
- Controleer de mogelijkheden – productiemethoden, poedervariëteiten, QC-testen enz.
- Bekijk casestudy's en klantbeoordelingen die relevant zijn voor uw toepassing
Stap 3: Evalueer de technische mogelijkheden
- Kunnen ze 316L-poeder aanpassen aan uw toepassingsbehoeften?
- Hebben ze expertise in AM, MIM of andere poedertechnologieën?
- Wat is hun niveau van verticale integratie en kwaliteitscontrole?
Stap 4: Beoordeel het serviceaanbod
- Technische ondersteuning tijdens poederselectie, applicatieontwikkeling
- Monstertesten, proefdiensten
- Reactie op vragen, flexibiliteit in de doorlooptijd
Stap 5: Controleer certificeringen en naleving
- Internationale kwaliteitscertificeringen – ISO 9001, ISO 13485 enz.
- Naleving van poedersamenstellingsnormen zoals ASTM
- Traceerbaarheid van partijen, uitgebreide tests en documentatie
Stap 6: Vergelijk prijzen
- Prijs per kg voor gewenste deeltjesgrootte, kwaliteitsniveau, hoeveelheid
- Minimale bestelhoeveelheid en vereisten voor partijgrootte
- Verzend-/logistiekkosten
Stap 7: Controleer beschikbaarheid en betrouwbaarheid
- Stabiel aanbod op voorraad en het vermogen om aan schommelingen in de vraag te voldoen
- Volgen en monitoren van bestellingen, transparante doorlooptijden
- Bewezen tijdige leveringsrecord
Het selecteren van een leverancier met toepassingsexpertise, consistente productkwaliteit en responsieve service zorgt voor een soepele inkoopervaring.
Hoe u 316L-poeder voor AM kunt optimaliseren
Zorg ervoor dat de deeltjesgrootte overeenkomt met het AM-proces
- Gebruik deeltjes van 10-45 μm voor poederbedfusie zoals DMLS, SLM
- Optimaliseer de maatverdeling – te breed kan verpakkingsproblemen veroorzaken
- Fijnere deeltjes van 1-10 μm zijn beter geschikt voor het spuiten van bindmiddelen
Bereik een hoge bolvormigheid en vloeibaarheid
- De vloeibaarheid heeft rechtstreeks invloed op de poederspreiding en de uniformiteit van de lagen
- Gasverneveling produceert bolvormige, vrij stromende poeders
- Test de poederstroom volgens de ASTM B213-norm
Minimaliseer satellietdeeltjes
- Gebruik zeven en classificatie om satellieten en boetes te verwijderen
- Satellieten kunnen agglomeratie en defecten veroorzaken
Controle samenstellingstolerantie
- Controleer de elementaire samenstelling strak binnen het door ASTM gespecificeerde bereik
- Beperk onzuiverheden zoals O, N, C die de eigenschappen beïnvloeden
Verminder de porositeit
- Optimaliseer procesparameters en scanpatronen
- Gebruik heet isostatisch persen om de porositeit te minimaliseren
- Handhaaf een dichtheid van >99% voor hoge prestaties
Minimaliseer restspanningen
- Optimaliseer thermische gradiënten in het bouwproces
- Gebruik geschikte warmtebehandelingen om spanningen te verlichten
Behaal de beoogde mechanische eigenschappen
- Oplossingsgloeien en veroudering verbeteren de sterkte
- Behoud uniforme eigenschappen in alle bouwrichtingen
Zorgvuldige poederkarakterisering, parameteroptimalisatie en nabewerking zijn essentieel om defectvrije 316L-onderdelen te bereiken met behulp van AM.
FAQ
Vraag: Waar wordt 316L roestvrij staalpoeder doorgaans voor gebruikt?
A: 316L-poeder wordt het meest gebruikt voor additieve productie, metaalspuitgieten en pers- en sintertoepassingen vanwege de uitstekende corrosieweerstand in combinatie met goede mechanische eigenschappen en biocompatibiliteit. Veel voorkomende toepassingen zijn onder meer implantaten, ruimtevaartcomponenten, auto-onderdelen, biomedische apparaten en gereedschappen.
Vraag: Welke deeltjesgrootte wordt aanbevolen voor lasergebaseerde AM-processen?
A: Een deeltjesgroottebereik van 10-45 micron wordt doorgaans aanbevolen voor laserpoederbedfusieprocessen zoals DMLS en SLM. Fijnere deeltjes onder de 10 micron kunnen problemen met de stroming en verspreiding veroorzaken. De deeltjesgrootteverdeling moet ook goed worden gecontroleerd.
Vraag: Hoe beïnvloedt de poedermorfologie de eigenschappen?
A: Zeer bolvormig, vrijstromend poeder is wenselijk voor AM-toepassingen. Onregelmatig, stekelig poeder is geschikt voor pers- en sintermethoden. Satellietdeeltjes en fijne deeltjes hebben een negatieve invloed op de poederstroom en kunnen defecten veroorzaken. Het beheersen van de poedermorfologie is de sleutel voor optimale prestaties.
Vraag: Wat zijn enkele belangrijke verschillen tussen gasverstoven versus waterverstoven 316L-poeder?
A: Gasverstoven 316L-poeder heeft een meer bolvormige morfologie en een betere vloeibaarheid. Met water verneveld poeder vertoont meer onregelmatige vormen, maar biedt een hogere samendrukbaarheid die gewenst is voor pers- en sintertoepassingen. Gasverstoven poeder heeft een lager zuurstofgehalte.
Vraag: Welke nabewerkingsmethoden worden gebruikt op 316L AM-onderdelen?
A: Veel voorkomende nabewerkingen omvatten warmtebehandeling, heet isostatisch persen, oppervlakteafwerking door middel van slijpen/bewerking, coating en kwaliteitscontroletests. Dit helpt bij het bereiken van doeleigenschappen, maatnauwkeurigheid, esthetiek en defectdetectie.
Vraag: Wat zijn enkele veelvoorkomende defecten aan het 316L-poeder en hoe kunnen deze worden vermeden?
A: Mogelijke defecten zijn porositeit, scheuren, slechte oppervlakteafwerking, gebrek aan versmelting en restspanningen. Zorgvuldige optimalisatie van procesparameters, controle van de poederkwaliteit, bouworiëntatie en nabewerking kunnen deze defecten in 316L-onderdelen minimaliseren.
Vraag: Welke normen zijn van toepassing op 316L-poeder voor AM en andere toepassingen?
A: De belangrijkste normen zijn ASTM F3055 voor AM-poeders, ASTM B822 voor poederkarakterisering, ASTM A240 voor legeringssamenstelling en ISO-normen voor kwaliteitsmanagement. Toonaangevende leveranciers van 316L-poeder zijn gecertificeerd volgens deze normen.
Vraag: Welke factoren bepalen de prijs voor 316L-poeder?
A: De belangrijkste factoren die van invloed zijn op de prijsstelling van 316L-poeder zijn kwaliteitsniveau, deeltjesgrootte en distributie, productiemethode, bestelhoeveelheid, kopersvereisten voor testen/QC, verpakking en levering. Strengere eisen verhogen de prijzen.
Vraag: Hoe kan de corrosieweerstand van 316L AM-onderdelen worden geoptimaliseerd?
A: Oplossingen omvatten het beheersen van onzuiverheidsniveaus door middel van nauwe toleranties voor de chemische samenstelling, het gebruik van heet isostatisch persen om de dichtheid te verhogen en de porositeit te verminderen, het toepassen van passivatiebehandelingen en oplossingsgloeien om de corrosieweerstand te verbeteren.
Delen op
MET3DP Technology Co, LTD is een toonaangevende leverancier van additieve productieoplossingen met hoofdkantoor in Qingdao, China. Ons bedrijf is gespecialiseerd in 3D printapparatuur en hoogwaardige metaalpoeders voor industriële toepassingen.
Onderzoek om de beste prijs en een op maat gemaakte oplossing voor uw bedrijf te krijgen!
gerelateerde artikelen
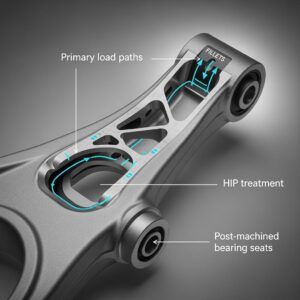
Metal 3D Printing for U.S. Automotive Lightweight Structural Brackets and Suspension Components
Lees verder "Over Met3DP
Recente update
Ons product
NEEM CONTACT MET ONS OP
Nog vragen? Stuur ons nu een bericht! Na ontvangst van uw bericht behandelen wij uw verzoek met een heel team.