Metaalspuitgieten (MIM) begrijpen
Inhoudsopgave
Metaal spuitgieten (MIM) is een productieproces dat wordt gebruikt om kleine, complexe metalen onderdelen met nauwe toleranties te produceren. MIM combineert de veelzijdigheid van kunststofspuitgieten met de sterkte en integriteit van bewerkte metalen. Dit artikel biedt een gedetailleerd overzicht van MIM-technologie, toepassingen, apparatuur, processen, ontwerpoverwegingen en meer.
Overzicht van metaalspuitgieten
Metaalspuitgieten is een poedermetallurgisch proces dat de productie van kleine, nauwkeurige metalen componenten in grote hoeveelheden mogelijk maakt met behulp van spuitgiettechnieken.
Hoe MIM werkt
Het MIM-proces omvat het mengen van fijn metaalpoeder met een bindmiddel om een grondstof te creëren die in mallen kan worden geïnjecteerd. De gegoten delen, ook wel groene delen genoemd, worden vervolgens gesinterd om het bindmiddel te verwijderen en het metaalpoeder tot een vaste structuur te consolideren. De basisstappen zijn:
- Mengen – Fijn metaalpoeder wordt gemengd met bindmiddelen om een homogene grondstof te creëren
- Spuitgieten – De grondstof wordt gesmolten en in de mal geïnjecteerd om groene delen te vormen
- Ontbinding – Het bindmiddel wordt verwijderd door middel van oplosmiddel-, thermische of katalytische ontbinding
- Sinteren – De losgemaakte delen worden gesinterd om de metaalstructuur te verdichten en te versterken
- Secundaire operaties – Extra afwerkingsstappen zoals verspanen, boren, tappen etc.
Voordelen van MIM
MIM biedt verschillende voordelen vergeleken met andere productietechnieken:
- Productie in grote volumes met lage kosten per onderdeel
- Complexe geometrieën met nauwe toleranties
- Verscheidenheid aan materialen zoals roestvrij staal, titanium, wolfraam, kobaltchroom enz.
- Minimale schrootverliezen en materiaalverspilling
- Fabricage in de buurt van netvorm, waardoor bewerkingen worden verminderd
- Kleine onderdelengroottes van 0,005 lbs tot 0,5 lbs
- Consolidatie van onderdelen door samenstellingen te combineren
- Gladde oppervlakken en goede afwerking
Beperkingen van MIM
Enkele beperkingen van het spuitgieten van metaal zijn onder meer:
- Hoge opstart- en gereedschapskosten
- Beperkt maatbereik voor onderdelen
- Gespecialiseerde apparatuur vereist
- Meerstapsproces met langzamere productie
- Dimensionale beperkingen gebaseerd op poedereigenschappen
- Beperkingen op onderdeelgeometrie gebaseerd op poederstroom
Toepassingen van MIM
MIM wordt veel gebruikt voor het vervaardigen van kleine, complexe onderdelen met nauwe toleranties in verschillende sectoren, zoals:
- Medisch – orthopedische implantaten, tandheelkundige implantaten, chirurgische instrumenten
- Automotive – motoronderdelen, kleppen, tandwielen
- Lucht- en ruimtevaart – turbinebladen, waaiers, straalpijpen
- Elektronica – connectoren, microversnellingen, afscherming
- Vuurwapens - trekkers, hamers, beveiligingen
- Horloges – horlogekasten, armbanden, kroon
- Industrieel – knoppen, bevestigingsmiddelen, snijgereedschappen
MIM concurreert met andere processen zoals investeringsgieten, machinaal bewerken en stempelen voor de productie van metalen onderdelen.
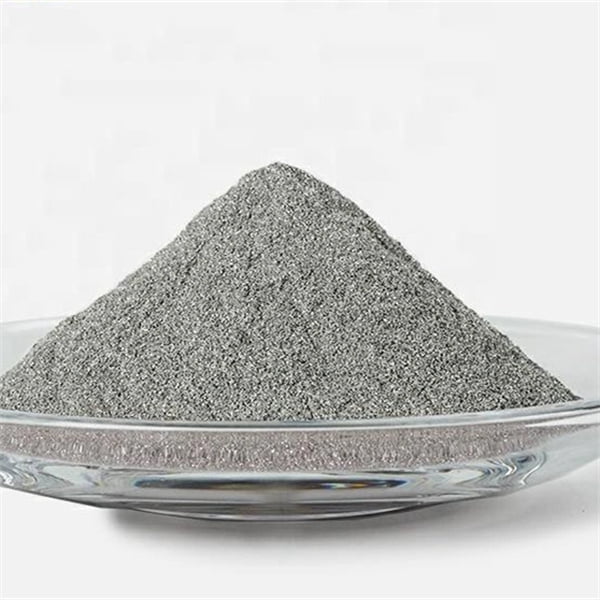
Apparatuurgids voor spuitgieten van metaal
Voor elke fase van het MIM-proces is gespecialiseerde apparatuur vereist. Dit zijn de belangrijkste typen MIM-apparatuur:
Apparatuur | Functie |
---|---|
Poedervoeders | Doseer nauwkeurig fijne poeders |
Mengers | Meng poeder en bindmiddel homogeen |
Granulatoren | Vorm de grondstof tot korrels voor het vormen |
Spuitgietmachines | Vorm de grondstof in de gewenste vormen |
Ontbindingsovens | Verwijder het bindmiddel van vormdelen |
Sinterovens | Verdicht en versterk de metalen structuur |
Slijpmachines | Verwijder hekken, lopers en gladde oppervlakken |
Bewerkingscentra | Boren, draaien, freeselementen tot gesinterde onderdelen |
Geavanceerde automatisering, handlingsystemen en bedieningselementen worden gebruikt om het proces te integreren en de productiviteit te maximaliseren. De apparatuur moet zorgvuldig worden geselecteerd op basis van factoren als materiaal, onderdeelgrootte, productievolume en kwaliteitseisen.
metaalspuitgietproces Stap voor stap
MIM-verwerking omvat meerdere stappen om fijn metaalpoeder om te zetten in volledig compacte componenten voor eindgebruik.
Stap 1 – Mengen
- Het metaalpoeder en het bindmiddel worden grondig gemengd in een mixer om een homogene grondstof te produceren
- Poederdeeltjesgrootte, vorm, distributie beïnvloeden vormbaarheid en sinteren
- Bindmiddelen zorgen voor vloei en hechting tijdens het spuitgieten
- Wassen, thermoplastische materialen zoals PP, PE, PVC en polymeren die als bindmiddel worden gebruikt
- Mengen gebeurt met behulp van Sigma Blade, Z-blade, dubbele planeetmengers
Stap 2 – Granulatie
- Het grondstofmengsel wordt gegranuleerd tot kleine pellets voor spuitgieten
- Verbetert de materiaalstroom en voorkomt segregatie in het vat
- Granulatoren gebruiken roterende messen om de grondstof in uniforme korrels te snijden
- De vorm en grootte van de korrels beïnvloeden de pakkingsdichtheid en de vormbaarheid
Stap 3 – Spuitgieten
- De grondstofkorrels worden in de gewenste vorm en grootte van het onderdeel gegoten
- Maakt gebruik van aangepaste spuitgietmachines met gecontroleerde temperatuur en druk
- Belangrijk om de vormparameters te optimaliseren om defecten te minimaliseren
- As-gegoten onderdelen, groene onderdelen genoemd, hebben vorm gegeven maar geen kracht
Stap 4 – Ontbinden
- Het bindmiddel wordt via oplosmiddel, thermische of katalytische middelen uit de groene delen geëxtraheerd
- Het ontbinden van oplosmiddelen maakt gebruik van capillaire werking om het bindmiddel op te lossen
- Bij thermische ontbinding wordt het bindmiddel in een oven ontleed
- Katalytische ontbinding versnelt de verwijdering van bindmiddel met een katalysator
- Bij het ontbinden ontstaan bruine delen met een poreuze structuur van metaaldeeltjes
Stap 5 – Sinteren
- Bruine delen worden gesinterd in een oven met gecontroleerde atmosfeer
- Bindingen tussen metaaldeeltjes worden gevormd door diffusie en massatransport
- Bijna volledige dichtheid tot 96-99% bereikt tijdens het sinteren
- Sfeer, temperatuur en tijd geoptimaliseerd om defecten te voorkomen
- Tijdens het vormen wordt rekening gehouden met sinterkrimp
Stap 6 – Secundaire bewerkingen
- Extra metaalbewerkingsstappen zoals gloeien, machinaal bewerken, boren, plateren
- Gloeien verlicht interne spanningen door sinteren
- CNC-bewerking verwijdert aanspuitingen, maakt oppervlakken glad en voegt functies toe
- Plating en verf aangebracht voor verbetering of bescherming tegen corrosie
Het MIM-proces maakt complexe metalen onderdelen met hoge precisie mogelijk door de voordelen van kunststofspuitgieten en poedermetallurgie te combineren.
Ontwerpoverwegingen voor MIM-onderdelen
MIM maakt geometrische vrijheden mogelijk die niet mogelijk zijn bij machinale bewerking, maar vereist bepaalde ontwerpoverwegingen:
- Wanddikte – Typisch bereik van 0,3 – 4,0 mm, waarbij sommige poeders muren tot 6 mm ondersteunen
- Oppervlakteafwerking – Gladdere afwerking dan gieten, maar niet zo fijn als machinaal bewerken; Een Ra-waarde van 1 – 4 μm is typisch voor MIM
- Dimensionale toleranties – ±0,1% tot ±0,5% gebaseerd op onderdeelgeometrie met enige nauwkeurigheid op micronniveau mogelijk
- Dikte – Volledige dichtheid tot 99% kan worden bereikt met geoptimaliseerd sinteren
- Geometrie – Het vermijden van opgesloten poeders en het laten ontsnappen van bindmiddel is van cruciaal belang
- Diepgang hoeken – Taps toelopende wanden met een trekhoek van 1-3° om het uitwerpen van onderdelen te vergemakkelijken
- Radii en filets – Geleidelijke overgangen verdienen de voorkeur boven scherpe hoeken
- Gaten en holtes – Minimale diameters van 0,25 – 0,5 mm voor doorlopende gaten
- Draden – Kan worden gegoten, maar vaak machinaal bewerkt na het sinteren voor een betere nauwkeurigheid
- Oppervlaktedetails – Beperk fijne details om schimmelslijtage te verminderen; post-molding-processen kunnen verbeteren
MIM-ontwerp moet zich richten op geometrie die de prestaties maximaliseert in plaats van op fabricagegemak. Het proces maakt consolidatie van uit meerdere delen bestaande assemblages tot één onderdeel mogelijk, met aanzienlijke kosten- en gewichtsbesparingen.
Materialen die worden gebruikt bij het spuitgieten van metaal
MIM kan onderdelen produceren uit een breed scala aan metalen, legeringen en keramiek in diverse industrieën.
Materiaal | Toepassingen | Eigenschappen |
---|---|---|
Roestvrij staal | Medisch, vuurwapens, marine | Corrosiebestendigheid, sterkte |
Laaggelegeerd staal | Automobiel, industrieel | Magnetische respons, bewerkbaarheid |
Zachte magnetische legeringen | Sensoren, actuatoren | Hoge permeabiliteit |
Legeringen van harde metalen | Snijgereedschappen | Slijtvastheid, hardheid |
Koperlegeringen | Elektronica, thermisch | Elektrische geleiding |
Aluminium legeringen | Elektrisch, thermisch | Lichtgewicht, geleidbaarheid |
Titanium legeringen | Lucht- en ruimtevaart, automobiel | Sterkte, biocompatibiliteit |
Wolfraam legeringen | Stralingsafscherming | Hoge dichtheid |
Cermets | Elektronica, optica | Oxidatie weerstand |
Factoren zoals de functie van het onderdeel, de kosten, de nabewerkingsstappen en de compatibiliteit van de legeringen bepalen de ideale MIM-materiaalkeuze.
MIM-leveranciers en apparatuurfabrikanten
Veel bedrijven bieden wereldwijd MIM-materialen, -diensten, -productie en -apparatuur aan. Hier zijn enkele van de belangrijkste MIM-leveranciers in de waardeketen:
Bedrijf | Producten en diensten |
---|---|
BASF | Grondstoffen, bindmiddelen |
Sandvik Visarend | Metaalpoeders |
Hogenäs | Metaalpoeders |
CNPC-poeder | Metaalpoeders |
Indo-Mim | MIM-producten, diensten |
MPP | MIM-producten, diensten |
ARC-groep | MIM-producten, diensten |
Atlas geperste metalen | Productie van MIM-onderdelen |
Epson Atmix | MIM-apparatuur |
Milacron | Spuitgietmachines |
Elnik | Sinterovens |
TCN | Ontbindings-, sinterovens |
Er zijn ook veel kleinere regionale spelers betrokken in de MIM-toeleveringsketen. Eindgebruikers die MIM willen adopteren, kunnen samenwerken met materiaalleveranciers en contractfabrikanten, afhankelijk van de vereiste capaciteiten.
Kostenanalyse van MIM-onderdelen versus alternatieven
Hier is een vergelijking van de geschatte kosten voor het produceren van 1000 onderdelen met behulp van verschillende productieprocessen:
Proces | Kosten instellen | Machinekosten | Gereedschapskosten | Onderdeelkosten | Totaal (1000 onderdelen) |
---|---|---|---|---|---|
CNC-bewerking | Laag | $100,000 | $2,000 | $50 | $52,000 |
Investeringscasting | Hoog | $500,000 | $40,000 | $20 | $60,000 |
Metaal spuitgieten | Hoog | $750,000 | $100,000 | $15 | $115,000 |
Stempelen | Hoog | $1,000,000 | $150,000 | $10 | $160,000 |
- CNC-bewerkingen hebben lage volumes, hoge onderdeelkosten en beperkte complexiteit
- Investeringsgieten is beter voor volumes tot 10.000 eenheden
- MIM heeft voordelen voor middelgrote tot hoge volumes met complexe geometrie
- Stempelen heeft zeer hoge gereedschapskosten, maar de laagste onderdeelprijs bij grote volumes boven de 100.000 onderdelen
Het kruispunt waarop MIM economischer wordt dan andere processen, hangt af van volumes, complexiteit en omvang.
Een MIM-leverancier of -partner kiezen
Het selecteren van een competente MIM-leverancier of productiepartner is cruciaal voor een kosteneffectieve productie van onderdelen. Dit zijn de belangrijkste overwegingen:
- Technische expertise – Eerdere ervaring met vergelijkbare MIM-onderdelen, materialen, industrie
- Kwaliteitssystemen – ISO 9001-certificering, kwaliteitscontrolepraktijken
- Productiecapaciteit – Mogelijkheid om te voldoen aan de huidige en toekomstige volumevereisten
- Secundaire processen – Bewerking, stempelen, plateren, schilderen
- Optimalisatie van onderdelen – Ontwerp voor MIM-ondersteuning om de voordelen te maximaliseren
- Prototyping – Snelle prototypingdiensten om ontwerpen te valideren
- Gereedschapsmogelijkheden – Bij voorkeur ontwerp en fabricage van gereedschappen in eigen huis
- Toegang tot grondstoffen – Aanvoerkanalen voor grondstoffen opgezet
- R&D-mogelijkheden – Voortdurend onderzoek en ontwikkeling op het gebied van geavanceerde materialen en productietechnieken
- Klantgerichtheid – Responsiviteit op behoeften en samenwerkingsaanpak
- Kostenstructuur – Prijsmodel en concurrentievermogen voor voorspelde volumes
- Logistiek – Mogelijkheid om onderdelen betrouwbaar te leveren en tegelijkertijd te voldoen aan de doorlooptijdvereisten
Door deze factoren prioriteit te geven, kunt u de juiste strategische MIM-partner voor een bepaalde toepassing identificeren.
MIM-apparatuur installeren
Voor bedrijven die MIM-mogelijkheden intern installeren, is een goede installatie van apparatuur van cruciaal belang. Dit zijn de belangrijkste overwegingen:
- Vloeroppervlak van ongeveer 2000 – 5000 vierkante meter nodig voor de MIM-lijn
- Stabiele stroomvoorziening met een capaciteit van 200-600 kVA vereist
- Persluchtleidingen geschikt voor een druk van 100 psi
- Afzuigventilatie voor warmte, emissies en stofopvang
- Nutsvoorzieningen zoals stikstof, proceswater en gasvoorziening
- Temperatuur- en vochtigheidsregeling van ongeveer 20±3 °C, 50±20%
- Tussenverdiepingen, platforms voor het installeren van aanvullende apparatuur
- Materiaaltransportsystemen zoals takels, vorkheftrucks, bakken
- Controlekamer, computersystemen voor monitoring
- Opleiding van personeel op het gebied van procesveiligheid en bediening van apparatuur
- Processimulaties, testruns om de installatie te valideren
- Kalibratie- en preventieve onderhoudsschema's
Voldoende ruimte, voorzieningen en gecontroleerde omstandigheden zijn essentieel voor een soepele werking van MIM-apparatuur. Grondig testen en trainen bereidt u voor op echte productie.
Onderhoud van MIM-apparatuur
Consistent onderhoud verbetert de uptime en prestaties van MIM-productieapparatuur. Sleutelaspecten:
- Gedocumenteerd preventief onderhoudsschema voor elke machine
- Dagelijks opruimen van gemorst materiaal, lekken, stof en puin
- Vloeistofniveaus controleren, lekkages, ongebruikelijke geluiden, trillingen
- Bewaking van drukken, temperaturen en energieverbruik
- Testen van verwarmings-, koeling- en regelsystemen
- Vervanging van slijtagedelen zoals zeven, schroeven, vaten
- Inspecties op vermoeidheid van componenten, schade, uitlijning
- Regelmatige verbouwingen en revisies op basis van bedrijfsuren
- Bijhouden van onderhoudslogboeken voor analyse
- Opslag van reserveonderdelenvoorraad voor kritische componenten
- Training over de juiste bediening en veiligheid van apparatuur
- Tijdige service en ondersteuning van apparatuurleveranciers
Goed opgeleid personeel en samenwerking met leveranciers van apparatuur helpen de productiviteit van MIM-apparatuur te maximaliseren en de downtime tot een minimum te beperken.
Simulatiesoftware voor metaalspuitgieten
Simulatiesoftware wordt gebruikt om het MIM-proces digitaal te modelleren vóór de daadwerkelijke productie. Voordelen zijn onder meer:
- Voorspelling van matrijsvulpatronen en optimalisatie van poortlocaties
- Identificeren van laslijnen en luchtafsluitingen om defecten te voorkomen
- Het bestuderen van thermische gradiënten en stolling in complexe geometrieën
- Simuleren van ontbindings- en sinterprofieleffecten op de uiteindelijke vorm
- Valideren van gereedschapsontwerpen vóór fabricage
- Verlaging van de proefkosten door middel van virtuele prototyping
- Trainen van personeel door middel van visuele representaties
Sommige commerciële MIM-simulatiepakketten omvatten:
- MIMSIM – Geïntegreerde simulatie voor het vormen door sinteren
- Sigma Zacht – 3D FEM-analyse van matrijsvulling en vervorming
- Netzsch MIMPre – Modellering van de reologische eigenschappen van MIM-grondstoffen
- Simufact-additief – Multifysica-simulatie van AM-processen
- EOS PSW – Simulatie gericht op sinteren en warmtebehandeling
Het gebruik van MIM-software verbetert de procesconsistentie, optimaliseert de kwaliteit van de onderdelen en verlaagt de kosten voor fysieke prototypes. Een geïntegreerde simulatie-naar-productieworkflow heeft de voorkeur.
Problemen oplossen met veelvoorkomende MIM-defecten
Enkele typische defecten in MIM-onderdelen en mogelijke hoofdoorzaken zijn:
Defect | Oorzaken |
---|---|
Korte opnames | Lage injectiedruk, voortijdige stolling |
Flash | Oververpakte mallen, schimmelschade |
Kromtrekken | Niet-uniforme koeling, problemen met de binder |
Scheuren | Snel sinteren, hoog bindmiddelgehalte |
Porositeit | Slechte homogenisatie, opgesloten gassen |
Verontreiniging | Kruisbesmetting, ovenatmosfeer |
Dimensionale variaties | Problemen met de grondstoffen, schimmelslijtage, krimp |
Oppervlaktedefecten | Gasporositeit, verbrossing van vloeibare metalen |
Insluitsels | Verontreinigde grondstoffen, verstopte spuitmonden |
Er moet een systematische methodologie voor defectanalyse worden gebruikt om procesparameters te isoleren die defecten veroorzaken en corrigerende maatregelen te nemen, zoals het aanpassen van de formulering van de grondstoffen, vormparameters, ontbindings- en sinterprofielen.
Voordelen van MIM-technologie
MIM biedt aanzienlijke voordelen ten opzichte van andere productiemethoden voor metalen onderdelen:
- Complexiteit – Ingewikkelde 3D-geometrieën mogelijk, consolideert samenstellingen
- Samenhang – Zeer herhaalbaar proces met lage onderdeelvariatie
- Efficiëntie – Fabricage in de buurt van netvormen met minder grondstofverspilling
- Automatisering – Sterk geautomatiseerd proces vermindert arbeid
- Flexibiliteit – Breed scala aan materialen zoals metalen, keramiek, composieten
- Kwaliteit – Goede oppervlakteafwerking en mechanische eigenschappen
- Productiviteit – Hoge volumeproductie met lage kosten per onderdeel
- Miniaturisatie – Microcomponenten met details tot 10 μm
- Duurzaamheid – Energie-efficiëntie vergeleken met verspanen
- Kosten – Lagere totale kosten voor middelgrote tot hoge productievolumes
De unieke mogelijkheden van MIM stimuleren de acceptatie in diverse sectoren, zoals de automobielsector, de lucht- en ruimtevaart, de medische sector en de elektronica.
Beperkingen van metaalspuitgieten
Ondanks de vele voordelen heeft MIM bepaalde beperkingen:
- Hoge initiële investering in gereedschap
- Beperkt maatbereik, doorgaans minder dan 65 gram
- Lagere nauwkeurigheid dan CNC-bewerking
- Porositeit brengt het risico met zich mee dat procescontroles nodig zijn
- Beperkte materiaalkeuzes op basis van poedereigenschappen
- Veiligheidsrisico's van fijne poeders
- Beperkingen van de onderdeelgeometrie gerelateerd aan vormbaarheid
- Potentiële variabiliteit van partij tot partij
- Lagere mechanische eigenschappen dan gesmeed materiaal
- Beperkte productie van prototypes in lagere volumes
- Vereiste voor secundaire bewerking in veel toepassingen
- Gespecialiseerde apparatuur en getrainde operators zijn nodig
Voor zeer hoge precisie of grotere metalen onderdelen die in kleine volumes worden geproduceerd, kunnen andere processen beter geschikt zijn dan MIM.
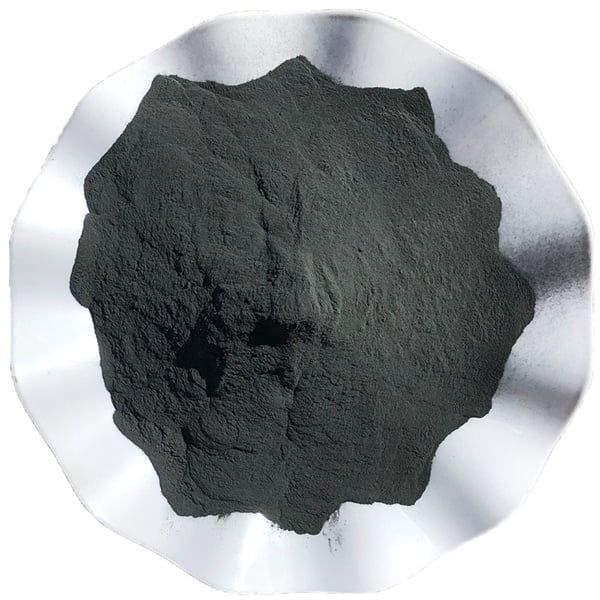
De toekomst van metaalspuitgieten
Er wordt verwacht dat MIM een sterke aanhoudende groei zal zien naarmate de technologie en materialen blijven verbeteren:
- Nieuwe bindmiddelsystemen om de vormbaarheid en groene sterkte te verbeteren
- Nieuwe grondstofformuleringen met behulp van nanocomposieten
- Grotere onderdelen overschrijden de huidige limieten
- Verhoogde acceptatie van keramiek en wolfraamlegeringen
- Sterke groei van de vraag in de medische en elektronische sectoren
- Gebruik van additive manufacturing om MIM-tools te maken
- Automatisering met behulp van robotica en Industrie 4.0-integratie
- Meer toepassingen in extreme omgevingen
- Convergentie met 3D-printen van metaal met behulp van gebonden metaalafzetting
Met meer R&D en eenvoudiger adoptie zal het MIM-gebruik de komende jaren snel groeien in diverse toepassingen.
Delen op
MET3DP Technology Co, LTD is een toonaangevende leverancier van additieve productieoplossingen met hoofdkantoor in Qingdao, China. Ons bedrijf is gespecialiseerd in 3D printapparatuur en hoogwaardige metaalpoeders voor industriële toepassingen.
Onderzoek om de beste prijs en een op maat gemaakte oplossing voor uw bedrijf te krijgen!
gerelateerde artikelen
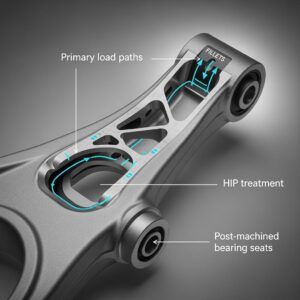
Metal 3D Printing for U.S. Automotive Lightweight Structural Brackets and Suspension Components
Lees verder "Over Met3DP
Recente update
Ons product
NEEM CONTACT MET ONS OP
Nog vragen? Stuur ons nu een bericht! Na ontvangst van uw bericht behandelen wij uw verzoek met een heel team.